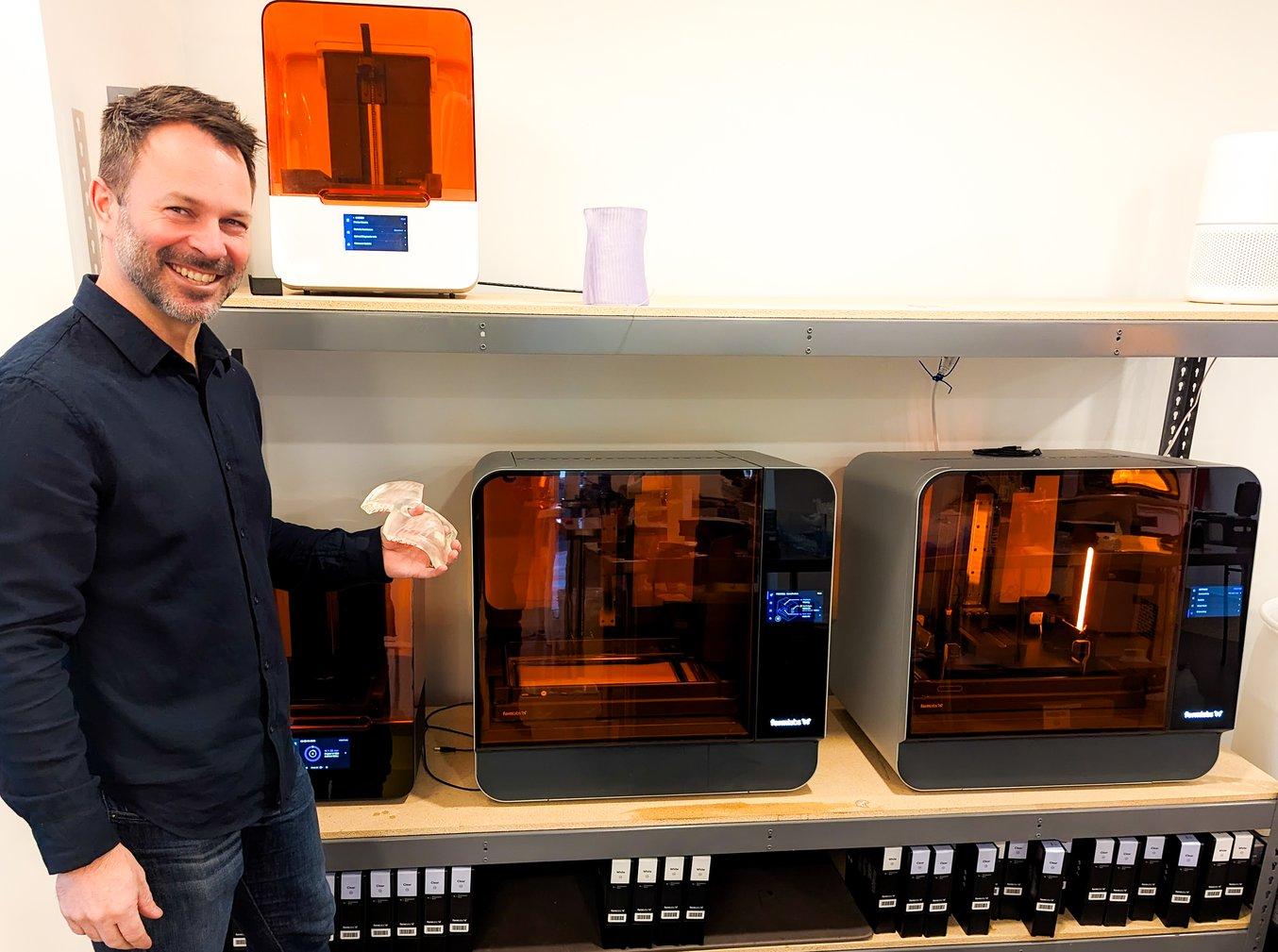
By 2040, global cancer cases are expected to rise to 29.5 million a year. As cases increase, healthcare professionals are working to develop more effective treatments. Currently, multiple options for treatment are leveraged by medical professionals in the fight against cancer, with surgery, chemotherapy, and radiation therapy used alone or in combination depending on the case.
Technological advancements play a key role in the development of improved treatment options with efficiency, level of care, patient experience, and clinical outcomes among the main considerations.
When it comes to radiation therapy for cancer, Adaptiiv is one company leveraging technology to advance treatment options. Their regulatory-cleared software is utilized by radiologists to design patient-specific bolus devices and surface brachytherapy applicators for the treatment of cancer. Once designed, Adaptiiv manufactures the devices through its Adaptiiv On Demand service and ships them to the hospital. 3D printing and biomedical materials are key, enabling the creation of customized, patient-specific devices for enhanced clinical precision and improved operational efficiency.
Conventional Bolus Devices for Radiation Therapy
According to the World Health Organization (WHO), more than 50% of cancer patient treatment plans utilize radiation therapy (RT). This includes some of the most common types of cancer including breast, lung, colorectal, and skin cancer.
Radiation therapy uses high-energy radiation to destroy cancer cell DNA. Radiation therapists fit patients with RT accessory devices while radiation is being delivered, most commonly for skin cancer and superficial tumors. These RT devices optimize dose delivery or shield healthy tissues from radiation. RT devices include:
- Conventional bolus devices to improve dose distribution
- Immobilization devices to reduce patient movement during treatment and aid procedure setup
- Electron apertures to shield healthy tissues from the radiation
- Surface brachytherapy applicators to enable the delivery of small radiation sources through positioned catheters.
A conventional bolus used in external beam radiation therapy (photon and electron) might be a flat piece of rubbery material placed on a patient’s skin to ensure the correct dose of radiation reaches the tumor. Conventional bolus devices are often cobbled together, which can cause air gaps for some patients, potentially resulting in the underdosing of the tumor or overdosing of healthy tissue.
Surface brachytherapy applicators are placed on the skin over the treatment area and utilize catheters as channels for radioactive sources that deliver the radiation. This manual process is time-consuming and radiologists often undertake a two to six day process to try and create a personalized device. Additional challenges to surface brachytherapy applicators include optimizing catheter placement for patient anatomy. If catheters aren’t well placed, patients may receive suboptimal treatment.
Challenges of Manually Creating a Traditional Device
For radiation therapists, creating a traditional bolus is a messy and time-consuming process. Common traditional materials including heated dental wax and Superflab (a rubbery sheet) are difficult to manipulate. The process and materials are variable and lack standardization.
The creation of brachytherapy applicators involves additional manual measurements and catheter placement, leaving significant room for error.
If the device is determined to have a poor fit, refabrication is likely necessary, requiring a repetition of the mold making and casting process. This means further work for the radiation therapist, additional materials, and more patient appointments.
Manually creating traditional bolus devices is an inefficient use of both time and material resources, with the resulting device often compromising treatment accuracy. These frustrations have driven many to seek out alternative workflows.
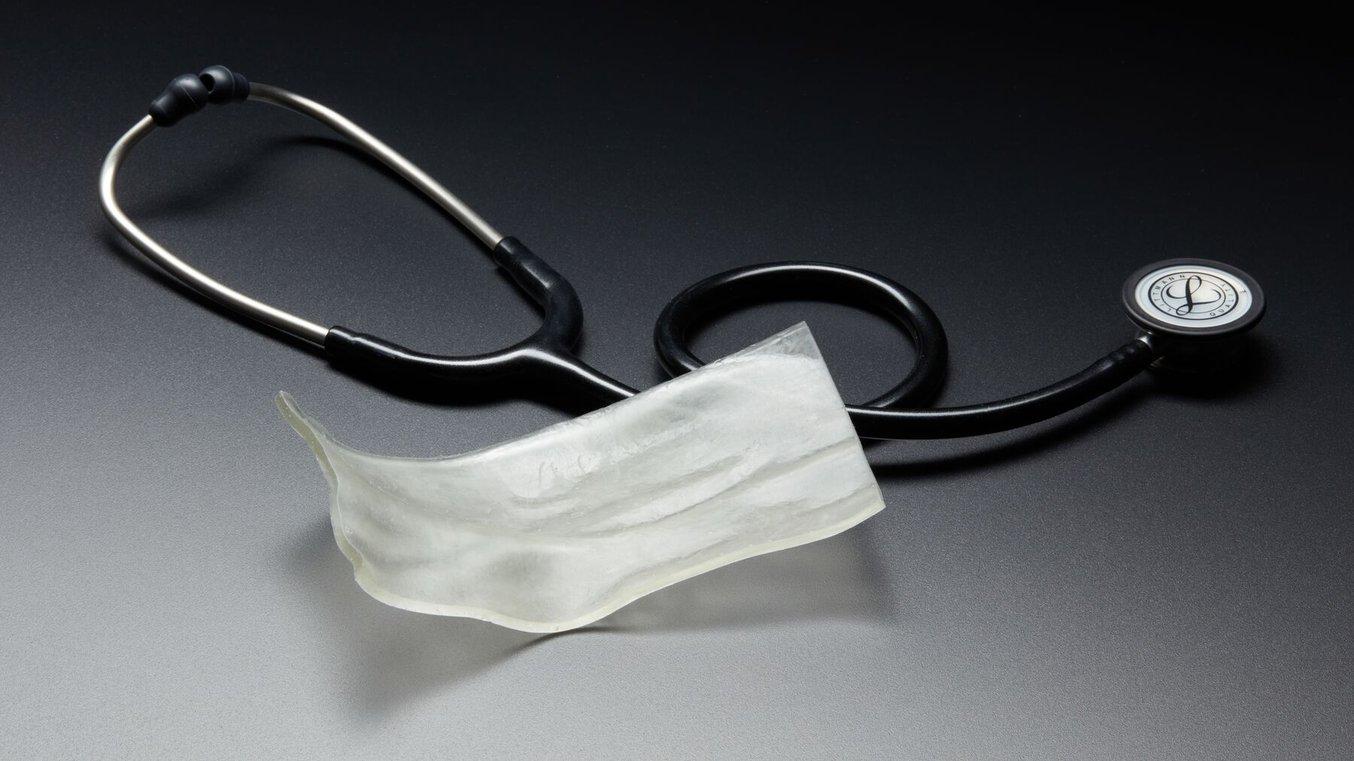
Unlock Patient-Specific Solutions for Radiation Therapy Using Formlabs 3D Printing
Learn how Formlabs 3D printing is democratizing patient-specific solutions from radiation oncology experts at Memorial Sloan Kettering Cancer Center, Centre Hospitalier de l'Université de Montréal (CHUM), and USF Health.
The Adaptiiv Advantage
Time, resources, patient comfort, and device accuracy are top of mind for healthcare providers. Dr. James Robar, Professor and Chief of Medical Physics at the Department of Radiation Oncology at Dalhousie University, has spent his career in radiation oncology. Robar found that while the planning, equipment, and technology for radiation oncology were state-of-the-art, the bolus devices being used were diminishing the effectiveness of treatments.
Robar compared a 3D printed bolus versus a standard vinyl gel sheet bolus for post-mastectomy chest wall radiation therapy and published a paper on the topic in 2017, leading him to connect with Alex Dunphy. Together, the two founded Adaptiiv, seeking to “digitize the last mile of radiation therapy cancer treatment and empower clinicians to deliver the plan they designed,” says Dunphy.
Robar’s career working with status quo materials led him to develop Adaptiiv’s digital workflows. Adaptiiv now works with cancer centers across the USA and around the world, continually testing and expanding their offerings.
Digital Workflows for Bolus Devices
Adaptiiv first developed regulatory cleared (FDA, CE) software in 2017 for use in the clinic and validated printers for in-house manufacturing. With Adaptiiv software, clinicians could design patient-specific bolus devices and then print them in-house.
When COVID hit, cancer centers were hit as well. For many, this meant lacking the resources to print in-house. Additionally, Dunphy says, “We realized, over time, that cancer centers wanted to treat cancer, not be micro-manufacturers. So Adaptiiv created Adaptiiv On Demand, a service that allowed cancer centers to design their parts in Adaptiiv software and then order them through Adaptiiv’s regulatory cleared solution, Adaptiiv On Demand.”
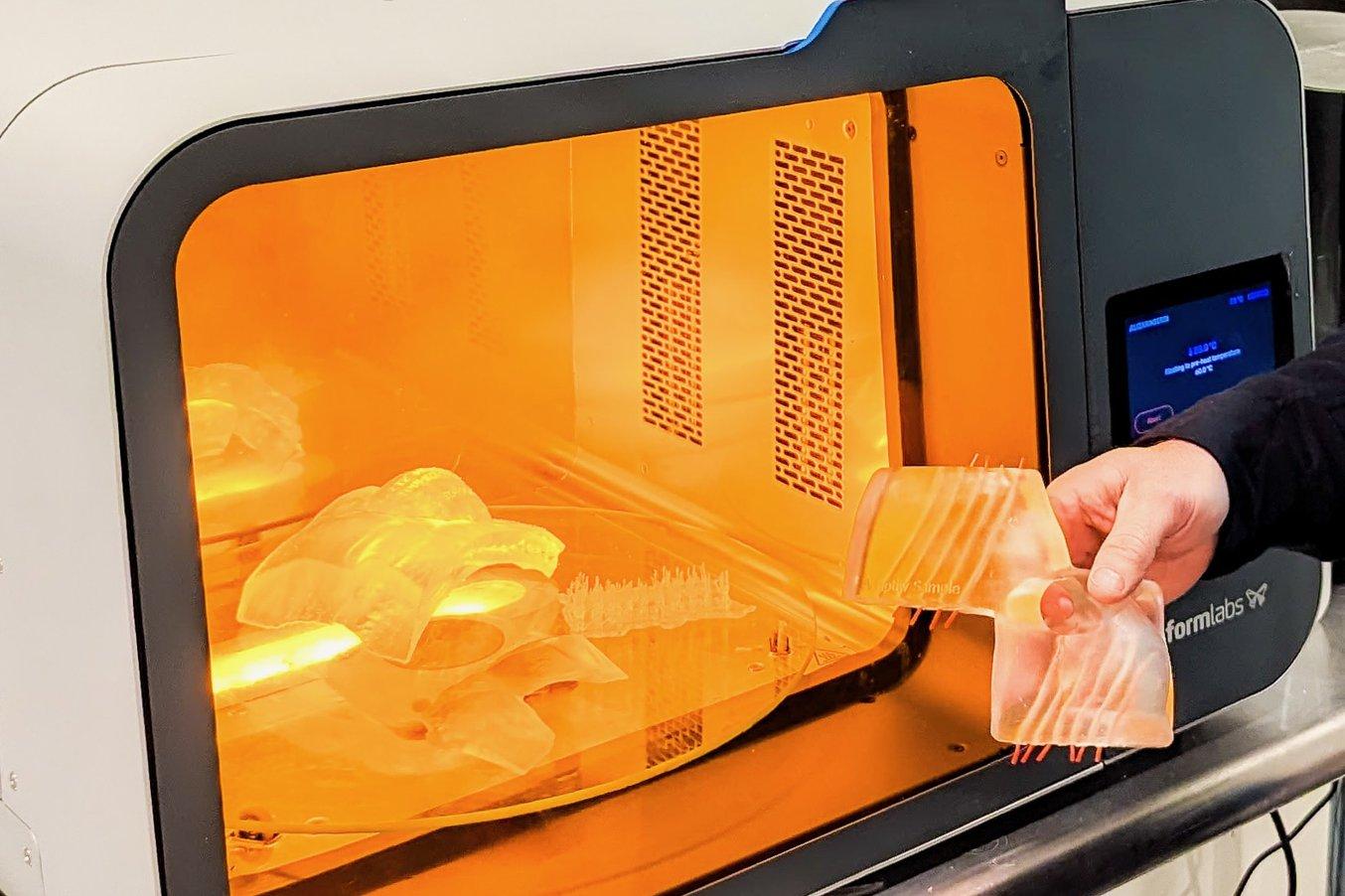
Post-curing SLA 3D printed parts helps them reach their maximum mechanical properties and achieve peak dimensional accuracy. The Form Cure L fits large prints or multiple prints for higher throughput.
With this solution, clinicians design a bolus utilizing Adaptiiv’s software and then send Adaptiiv the file. With this workflow, Adaptiiv has enabled the complete digitization of the mold room. Adaptiiv’s manufacturing facility then prints and mails the custom bolus device to the hospital, empowering clinicians to focus on patient care rather than the fabrication process.
“As we stepped into manufacturing we recognized the need for a printer that was capable of printing all of our solutions. In addition, we needed high output with low downtime. Formlabs has high quality control on their printers, exceptional customer support, and a regulatory focus.”
Alex Dunphy, Chief Executive Officer and Co-Founder, Adaptiiv
Adaptiiv works with Formlabs’ Form 3B+ stereolithography (SLA) 3D printer for healthcare applications to print the patient-specific HDR surface brachytherapy applicators designed utilizing their proprietary software. The Form 3B+ has a compact footprint and access to a library of high-performance resins, including biocompatible, sterilizable materials manufactured in Formlabs’ FDA-registered, ISO 13485 certified facility.
With the in-house manufacturing enabled by 3D printing, Adaptiiv On Demand can produce custom devices with a three to five day manufacturing turnaround, drastically cutting the timelines and improving the effectiveness of traditional bolus devices.
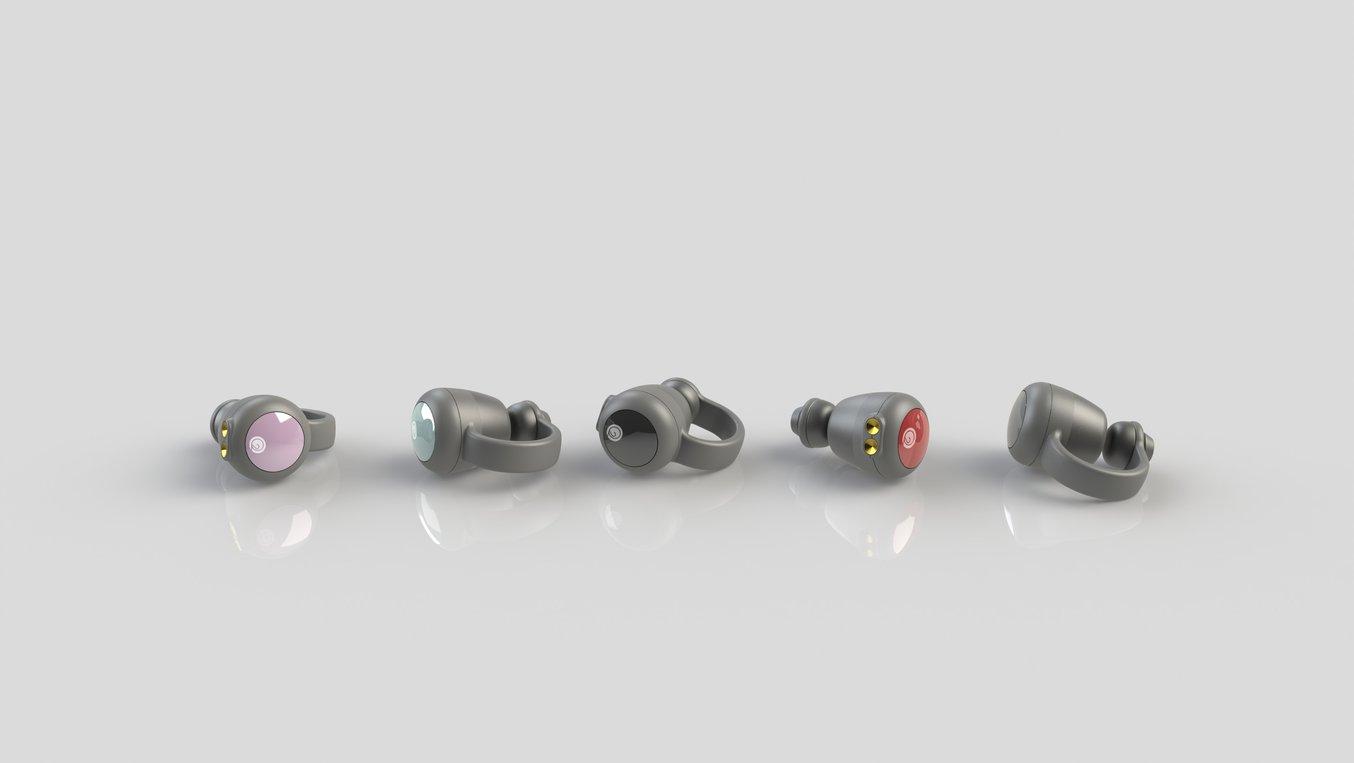
Building a New Medical Device Company with Formlabs Additive Manufacturing
Hear from three inspiring startup companies about their experiences building a brand-new business and simultaneously launching their first medical device. They’ll give us some insight into why they chose Formlabs to be a part of that process and how additive manufacturing was used.
Regulatory Clearance
Medical device manufacturing requires a number of regulatory hurdles. For Adaptiiv, this required the clearance of software, manufacturing platforms, and materials. This is a lengthy process requiring multiple tests and master files. Adaptiiv does all the validation of their parts in-house, including material validation.
When Adaptiiv moved into surface brachytherapy, they realized they required a clear material to visualize the tunnels within. As Dunphy says, “Intracavitary and interstitial brachytherapy require a material that can be safely inserted into the human body.” This meant finding a material that was both biocompatible and clear.
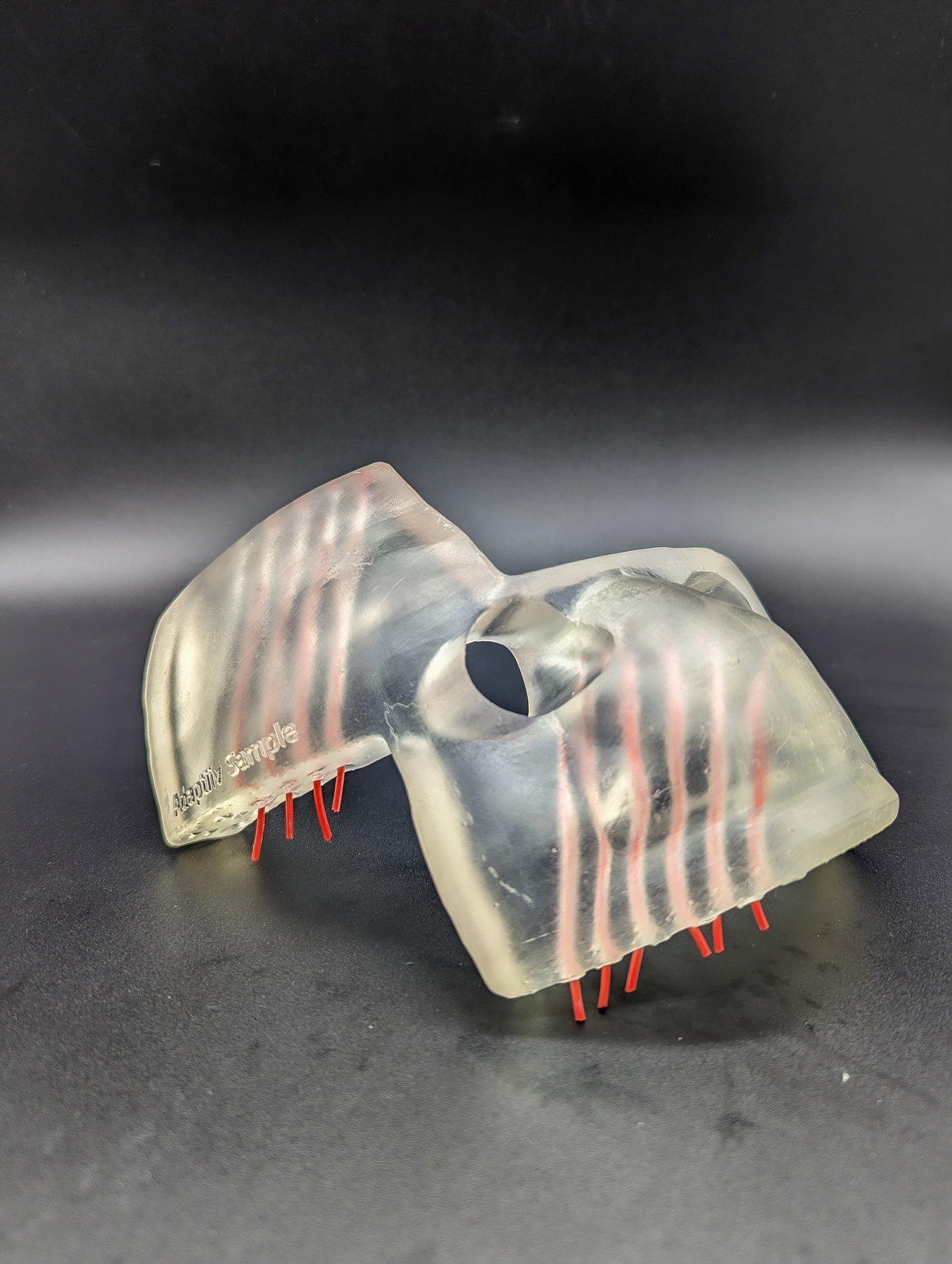
3D printed brachytherapy devices are printed to fit an individual patient for a custom fit.
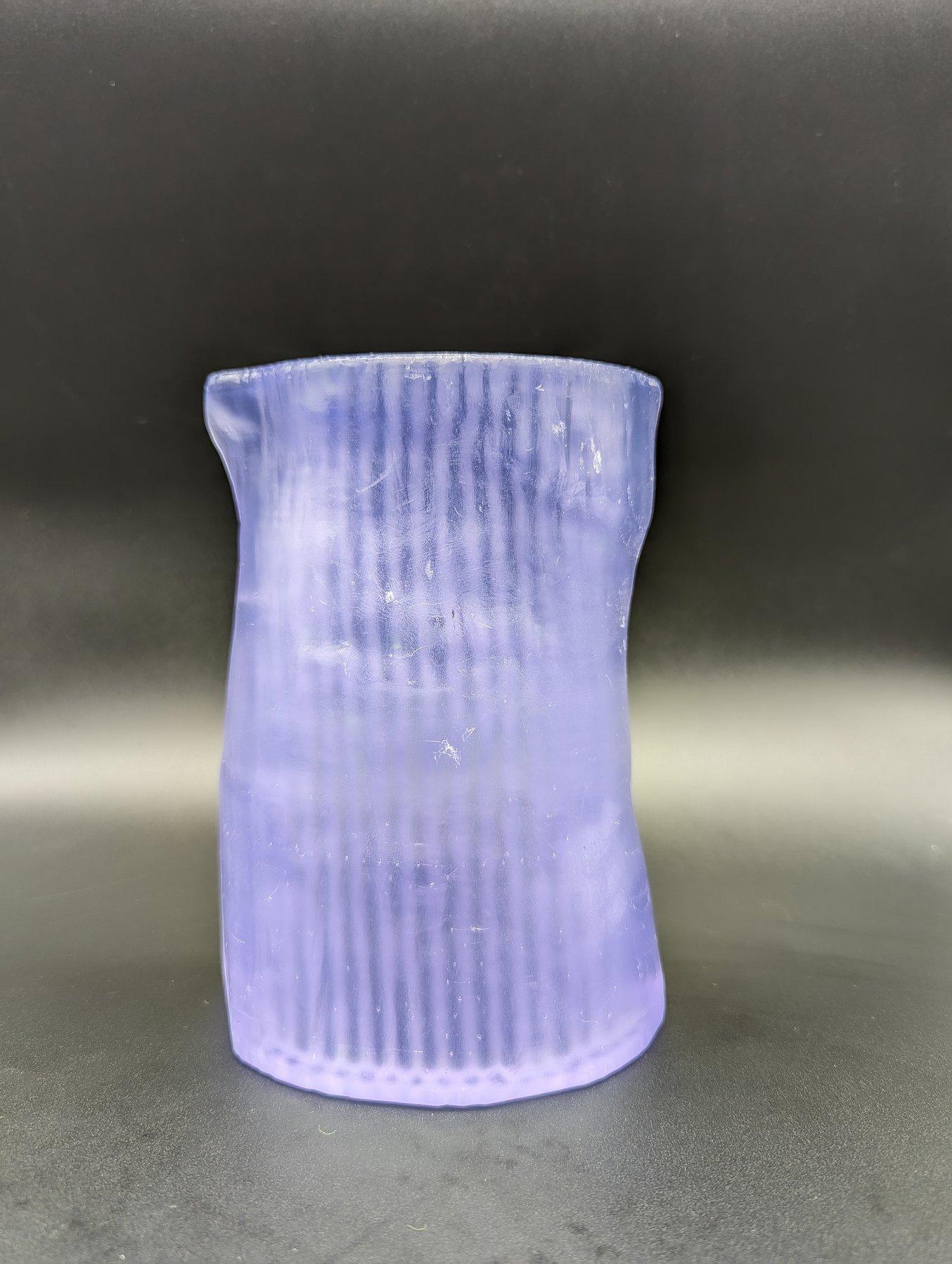
Tight tolerances make it possible to 3D print the channels in this brachytherapy applicator.
“Formlabs was the only creator of material that fit those needs. While that started that conversation, it evolved into recognizing that Formlabs 3D printers are the most consistent printers available on the market and are a pioneer in materials for 3D printing.”
Alex Dunphy, Chief Executive Officer and Co-Founder, Adaptiiv
For surface brachytherapy applications, clear resin is utilized. Formlabs Clear Resin is a rigid material that polishes to near optical transparency. It prints with a high resolution and a smooth surface finish. Transparent and rigid, it’s ideal for showcasing internal features, a requirement of brachytherapy tunnels. For intracavitary interstitial brachytherapy applicators, BioMed Clear Resin, a USP Class VI certified material that can be used for biocompatible applications requiring long-term skin or mucosal membrane contact, is used.
Dunphy notes that one of the benefits of printing with Formlabs SLA printers is the library of materials that can be utilized. “Formlabs’ commitment to new materials and resins in addition to their existing suite of regulatory cleared resins made the decision [to work with Formlabs] that much more logical.” From elastic resins to biocompatible and clear, resins are available in a range of material properties, empowering Adaptiiv to deliver the optimal product to their customers.
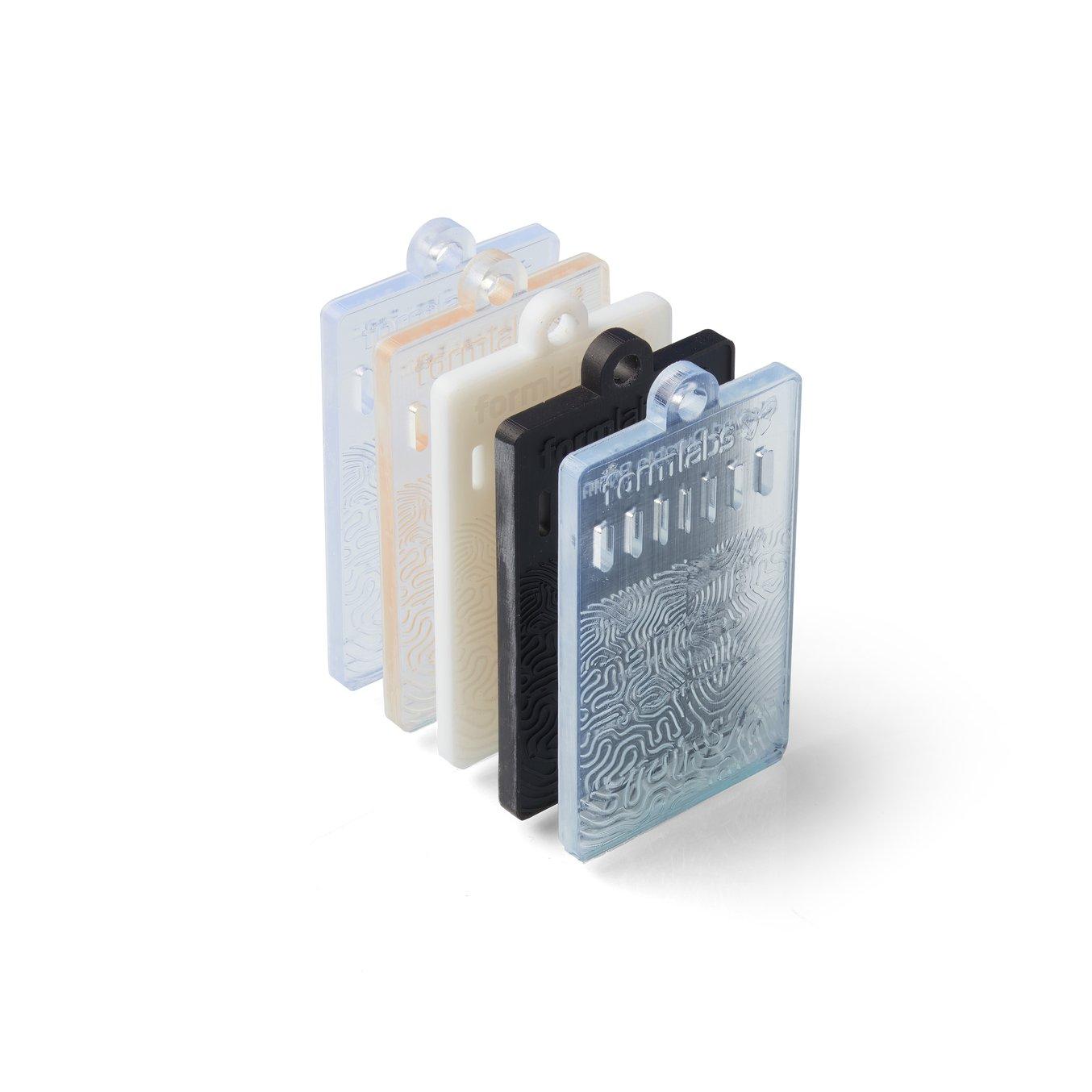
BioMed Resin Swatches
Each BioMed Resin swatch features embossed and debossed designs, 0.5-2.0 mm cutout thicknesses, as well as regulatory information unique to that resin.
Focused on Patient Care
Improving patient outcomes and experience are top of mind for Adaptiiv. A radiation team in Puerto Rico treating a nine-month-old patient was at a loss, unable to find a pediatric brachytherapy applicator that would come even close to fitting their patient. Looking for a solution, they reached out to Varian, A Siemens Healthineers Company, who referred them to Adaptiiv.
Adaptiiv was able to use their software platform to design five samples of applicators that could be used to modify an existing delivery device. Manufacturing utilizing 3D printing, the team was able to deliver biocompatible and sterilizable devices that were perfect for the patient’s anatomy.
The patient-personalization enabled by 3D printing makes treatment more accessible and effective. As Dunphy says, “we're providing access to personalization to the market, which without special skills and tools and budgets, they wouldn't be able to do themselves in a regulated way. What we're providing is access to personalization at scale.”
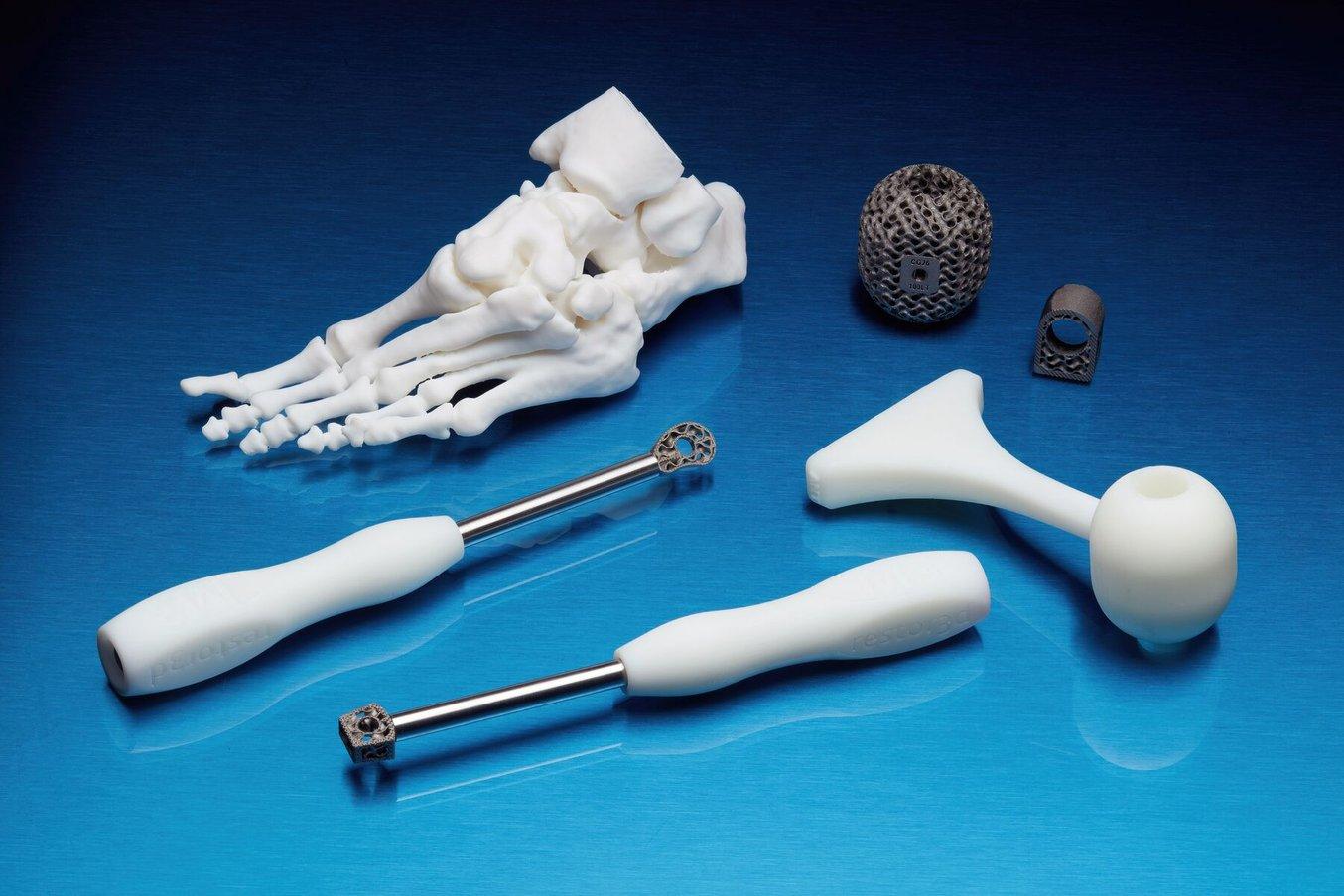
Proven Uses of Additive Manufacturing by Leading Medical Device Companies
Learn how medical device companies use additive manufacturing over traditional processes in this panel discussion with Enovis Surgical and restor3d.
The Bolus of the Future Is Here
Adaptiiv’s On Demand software platform can be used to design patient-specific devices which are then 3D printed for a customized solution. They are actively working on expanding their offerings, too, utilizing digital methods and 3D printing to bring new, unique technologies to healthcare professionals.
“Adaptiiv is committed to releasing new innovative solutions and having a partner like Formlabs who is committed to innovative materials, processes, and printers is a perfect synergy.”
Alex Dunphy, Chief Executive Officer and Co-Founder, Adaptiiv
Customized, patient-specific medical devices empower healthcare providers to deliver the best care. Learn how 3D printing can be used to manufacture medical devices or talk to a 3D printing expert about how Formlabs can help you meet your goals.