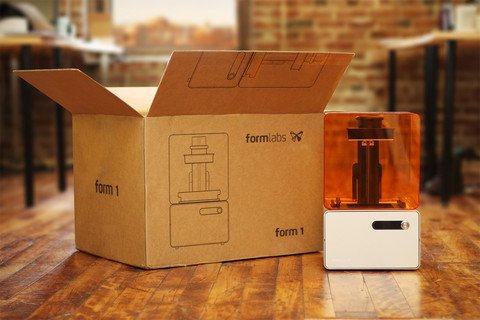
When we first began plans for the Form 1, we received some advice: “don’t leave packaging to the last minute.” We thank those wise advisors. Here’s some things that went into packaging:
10+ cushioning iterations
Many unlucky Form 1 prototypes suffered cracks, bruises, and breaks thanks to numerous drop tests (performed by our tallest team member, Jason). Designs ranged from foam-filled boxes to bolting the Form 1 to a piece of plywood. In the end we settled on what turned out to be the most reliable protection and (luckily) most visually appealing. Two inserts with sheets of tough plastic create a cushioned bed, allowing you to see through to the Form 1 at rest.
5 graphic design reviews
The packaging team (which borrows members from almost every other team in the company) focused on every detail to create graphic assets that would reflect each component of the Form 1 experience, ranging from the printer to the accessory kit.
~20% more BOM items
Stickers, labels and packaging added 20% more line items to the Form 1 bill of materials (BOM). Each new item requires individual design attention as well as vetting and coordinating more suppliers. These include the boxes as well as labels (like the resin tank fill line) and shipping stabilizers to better protect the delicate orange cover.
This effort is why the Form Team was beyond excited to receive our first production line test units from across the country in official packaging. We thought we’d share a few photos of what many of you can expect in the coming weeks.