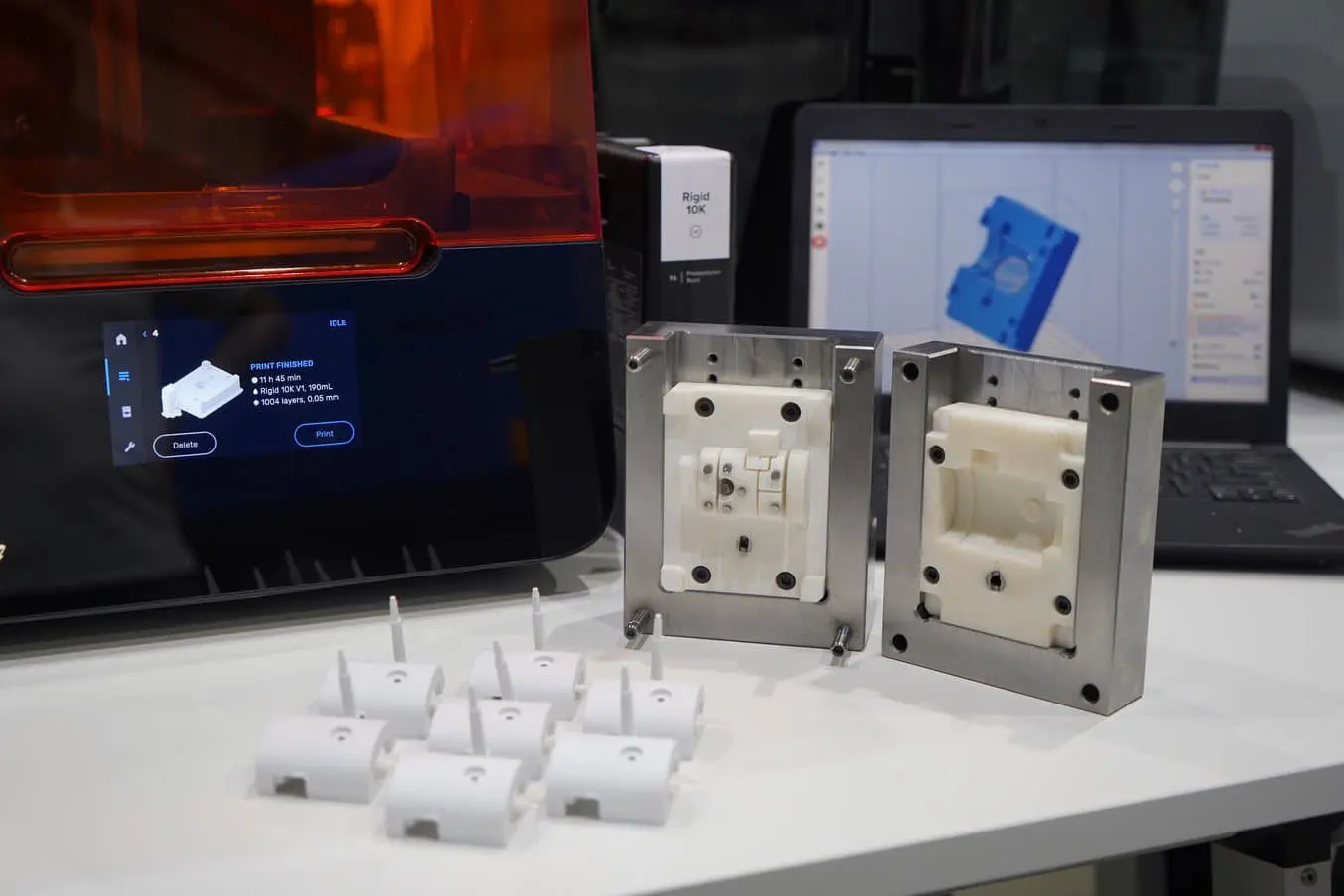
Obwohl der Spritzguss traditionell als ein Fertigungsprozess angesehen wird, der aufgrund seiner hohen Werkzeugausstattungskosten nur für die Massenproduktion ist, kann die Ausnutzung des 3D-Drucks zur Herstellung von Spritzgussformen Sie befähigen, diesen Prozess zu nutzen, um hochqualitative und reproduzierbare Teile für die Prototypenerstellung und Kleinserienproduktion herzustellen.
In diesem umfangreichen Leitfaden lernen Sie, wie Sie Spritzgussformen aus dem 3D-Drucker sowohl mit Benchtop- als auch industriellen Geräten nutzen können, um effizient und erschwinglich Hunderte funktionsfähiger Prototypen und Teile zur Beschleunigung der Produktentwicklung herzustellen, die Kosten und Durchlaufzeiten zu reduzieren und bessere Produkte auf den Markt zu bringen.
Spritzguss für Kleinserien im Vergleich zu traditionellem Spritzguss
Das Spritzgießen ist eines der führenden Verfahren zur Fertigung von Kunststoffteilen. Es ist eine kostengünstige und extrem reproduzierbare Technologie zur Produktion hochwertiger Teile in Großserien. Deshalb findet es breiten Einsatz zur Massenherstellung von Teilen mit minimalen Fertigungstoleranzen.
Das Spritzgießen ist ein schneller, intensiver Prozess, bei dem geschmolzenes Material unter großer Hitze und Druck in eine Form gespritzt wird. Das geschmolzene Material hängt von dem Umfang des Fertigungsprojekts ab. Die beliebtesten Materialien sind verschiedene Thermoplaste wie ABS, PS, PE, PC, PP oder TPU, aber auch Metalle und Keramiken können über Spritzguss injiziert werden. Die Form besteht aus einem Hohlraum, der für das injizierte, geschmolzene Material geeignet ist und so konzipiert ist, dass er die finalen Eigenschaften des Teils widerspiegelt.
Die Formen werden üblicherweise durch CNC-Bearbeitung oder Funkenerodieren (EDM) aus Metall hergestellt. Dies sind kostenintensive industrielle Verfahren, für die spezielle Geräte, hochwertige Software und hochqualifizierte Arbeitskräfte erforderlich sind. Daher dauert die Herstellung einer Metallform üblicherweise vier bis acht Wochen, bei Kosten zwischen 2000 bis 100 000 $, in Abhängigkeit von der Form und der Komplexität des Teils. Werden Formen aus üblichen Werkzeugmetallen und mit üblichen Herstellungsmethoden hergestellt, ist der Kosten- und Zeitaufwand hoch, zudem sind dabei spezielles Gerät und Fachwissen erforderlich. Für die Kleinserienfertigung ist der Spritzguss daher häufig keine Option. Es gibt jedoch Alternativen zur spanenden Fertigung von Formen aus Metall. Durch die betriebsinterne Herstellung von Spritzgussmodellen via 3D-Druck lassen sich Prototypen für die Kleinserienproduktion dagegen deutlich kosten- und zeitsparender erstellen als mit Metallformen. Zudem zeichnen sich die so produzierten Teile durch hohe Qualität aus und sind problemlos wiederholbar.
Für dieses Video haben wir uns mit dem Spritzgussdienstleister Multiplus zusammengetan, um Ihnen die Schritte des Spritzgussprozesses unter Einsatz 3D-gedruckter Formen näherzubringen.
Der Desktop-3D-Druck ist eine leistungsstarke Lösung zur raschen und kostengünstigen Herstellung von Spritzgussformen. Er stellt geringe Anforderungen an die Geräte und ermöglicht Einsparungen bei CNC-Zeiten und qualifizierten Arbeitskräften, die für andere anspruchsvolle Aufgaben genutzt werden können. Die Hersteller profitieren von der Geschwindigkeit und Flexibilität des betriebsinternen 3D-Drucks zum Erstellen von Formen und kombinieren diesen mit der Leistungsfähigkeit des Spritzgießens, um Serien aus herkömmlicher Thermoplaste in wenigen Tagen zu liefern. Dabei können sogar komplexe Formen hergestellt werden, die mit der herkömmlichen Fertigung nur schwer erzielbar sind, was den Entwicklungsteams eine höhere Gestaltungsfreiheit bietet. Diese können sowohl mit Desktop- als auch mit industriellen Spritzgießmaschinen verwendet werden. Außerdem profitiert die Produktentwicklung von der Möglichkeit, mehrere Versionen zu entwickeln und das Material für die Endverwendung zu testen, bevor in ein Metallwerkzeug investiert wird.
Wenngleich also im 3D-Druck hergestellte Formen bei sachgerechter Anwendung derartige Vorteile bieten, gibt es auch einige Grenzen, die man kennen sollte. So sollte von einer im 3D-Druck hergestellten Polymerform nicht die gleiche Leistung wie von einer herkömmlichen Metallform erwartet werden. Kritische Abmessungen sind schwerer einzuhalten, die Abkühlzeit ist aufgrund der langsameren Wärmeübertragung in Kunststoff länger und gedruckte Formen können unter Hitze und Druck leichter brechen. Dennoch setzen branchenweit Unternehmen 3D-gedruckte Formen in ihren Kurzzeit-Arbeitsabläufen im Spritzguss ein, was es ihnen ermöglicht, schnell Hunderte bis Tausende Teile herzustellen. Vom Entwurf funktionsfähiger Prototypen aus Endverwendungsmaterialien, über die Fertigung von Teilen während der Pilotproduktion bis zur Herstellung von personalisierten oder in Kleinserien produzierten Endverbrauchsteilen sind 3D-gedruckte Spritzgussformen eine kostengünstige und schnelle Möglichkeit, Teile in begrenzter Stückzahl zu produzieren.
Die Stereolithografie (SLA)-3D-Drucktechnologie ist eine ausgezeichnete Wahl für die Formenherstellung. Sie zeichnet sich durch eine glatte Oberflächenbeschaffenheit und die hohe Präzision aus, die von der Form auf das endgültige Teil übertragen wird und auch das Entformen erleichtert. Mit dem Stereolithografie (SLA)-Verfahren hergestellte 3D-Drucke verfügen über chemische Bindungen, die für Dichte und Isotropie sorgen. So entstehen funktionsfähige Formen in einer Qualität, die mit dem Schmelzschichtungs (FDM)-3D-Druck nicht erreicht wird. Desktop-SLA-Drucker, wie die von Formlabs angebotenen, können nahtlos in jeden Spritzguss-Arbeitsprozess integriert werden, dank ihrer einfachen Implementierung, Bedienung und Wartung.
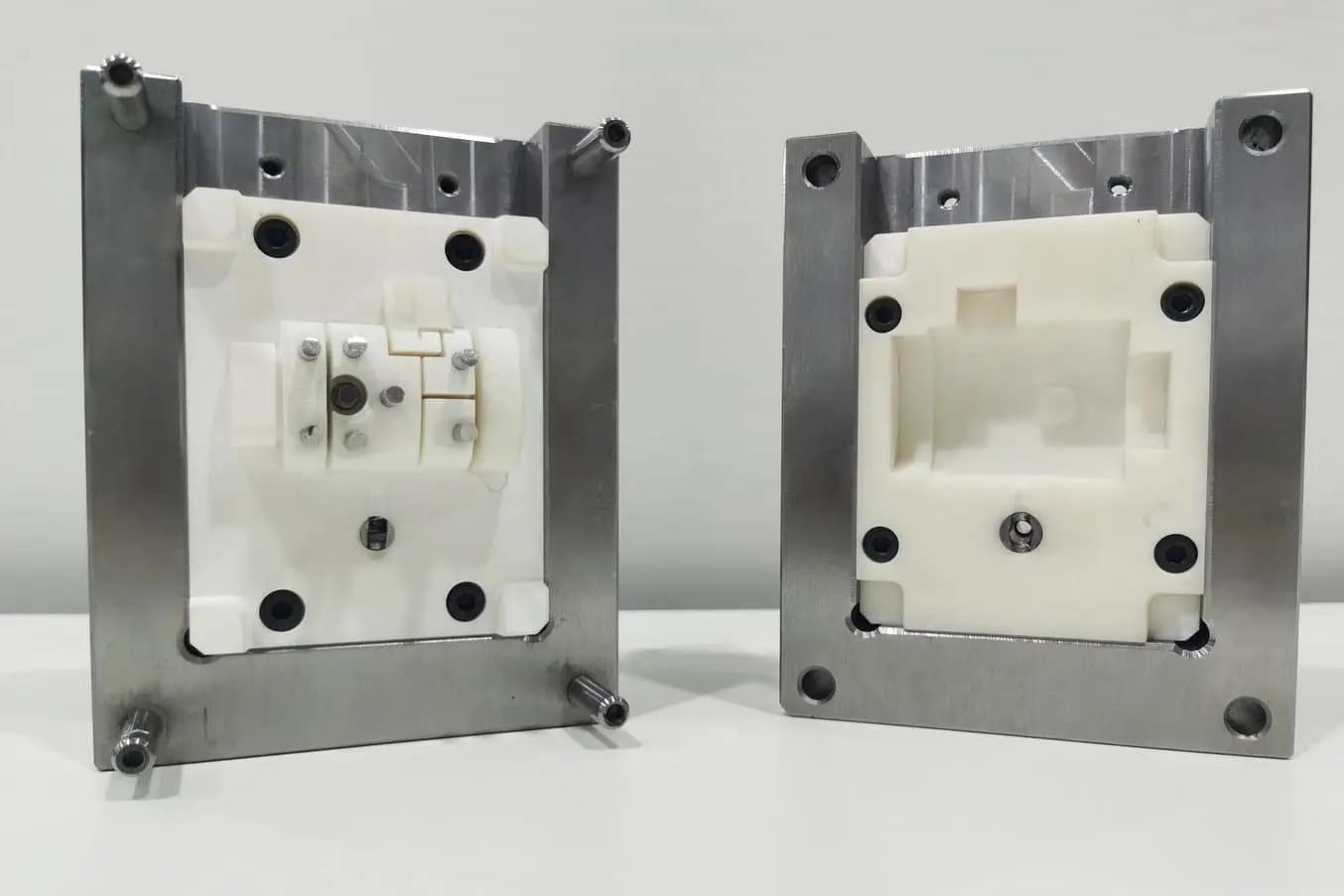
Ein 3D-gedruckter Spritzgussformenkern, hergestellt mit einem metallenen Formgehäuse.
Gespante Formen aus Aluminium können als Alternative für mittelgroße Produktionsvolumen von 500 bis 10 000 Teilen verwendet werden und reduzieren die Fixkosten der Formenfertigung. Zerspantes Aluminium ist fünf- bis zehnmal schneller als Stahl und verursacht weniger Verschleiß an den Werkzeugen, was kürzere Durchlaufzeiten und niedrigere Kosten bedeutet. Aluminium leitet auch Hitze schneller als Stahl, was eine geringere Notwendigkeit für Kühlkanäle zur Folge hat und Herstellern ermöglicht, den Formenentwurf zu vereinfachen, während kurze Zyklen eingehalten werden können.
Hier ist ein zusammenfassender Überblick der verschiedenen Spritzgussmethoden und der Formentypen, die zum effizientesten Prozess und den niedrigsten Kosten pro Teil führen, abhängig vom Produktionsvolumen.
Spritzguss für kleine Volumen | Spritzguss für mittelgroße Volumen | Spritzguss für große Volumen | |
---|---|---|---|
Methode | Betriebsinterne(r) Spritzgussproduktion und Formenbau | Ausgelagerte(r) Spritzgussproduktion und Formenbau | Ausgelagerte(r) Spritzgussproduktion und Formenbau |
Erforderliche Geräte | 3D-Drucker, Desktop-Spritzgießmaschine | - | - |
Form | 3D-gedrucktes Polymer | Bearbeitetes Aluminium | Bearbeiteter Stahl |
Formenkosten | < 100 $ | 2000–5000 $ | 10 000–100 000 $ |
Durchlaufzeit bis zum Endprodukt | 1–3 Tage | 3–4 Wochen | 4–8 Wochen |
Ideales Produktionsvolumen | < 500 | 500–10 000 | 5000 oder mehr |
Anwendungen | Rapid Prototyping individualisierter Spritzguss Spritzguss mit kurzer Laufzeit | Spritzguss mit kurzer Laufzeit | Massenproduktion |
Die Art der Spritzgießmaschine hat keinen wesentlichen Einfluss auf den Spritzgussprozess für Kleinserienfertigung. Auch traditionelle, große Spritzgießmaschinen können mit den 3D-gedruckten Spritzgussformen verwendet werden. Diese Maschinen sind jedoch teuer, haben strenge Anforderungen an die Anlage und erfordern geschulte Arbeitskräfte. Aus diesem Grund haben die meisten Unternehmen mittelgroße bis große Produktionsvolumen an Dienstleister und Vertragshersteller ausgelagert.
Wenn Sie in das Spritzgießen einsteigen und es mit begrenztem Investitionsaufwand testen möchten, könnte eine manuelle Benchtop-Spritzgießmaschine wie die Holipress oder die Galomb Model-B100 eine gute Option sein. Automatische Spritzgießmaschinen zur Kleinserienfertigung, wie das Desktop-Gerät von Micromolder oder das Hydraulikgerät Babyplast 10/12, sind eine gute Alternative für die mittelgroße Serienproduktion von kleinen Teilen.
Sind Sie neugierig geworden, was die verschiedenen Faktoren sind, die die Gesamtkosten für den Spritzguss ausmachen? Lesen Sie unseren umfangreichen Leitfaden.
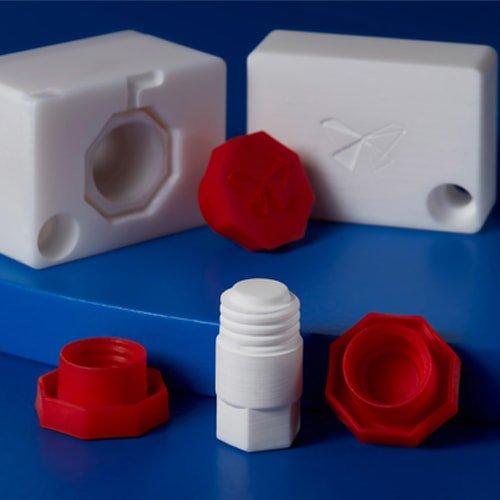
Schnelles Spritzgießen von Kleinserien mit Formen aus dem 3D-Drucker
Laden Sie dieses Whitepaper herunter und erfahren Sie mehr über die Methoden und Richtlinien zur Herstellung 3D-gedruckter Spritzgussformen, um die Kosten zu senken und Lieferzeiten zu verkürzen. Es enthält Fallstudien aus der Praxis von Braskem, Holimaker und Novus Applications.
Schritt-für-Schritt-Arbeitsablauf für den Spritzguss von Kleinserien
Der Arbeitsablauf für den Spritzguss von Kleinserien umfasst die folgenden sieben Schritte:
1. Design der Form
Erstellen Sie die Form Ihres Teils anhand der CAD-Software Ihrer Wahl. Beachten Sie dabei sowohl die allgemeinen Designregeln für additive Fertigung als auch für Spritzgussformen. Designempfehlungen speziell für den 3D-Druck von polymerbasierten Formen finden Sie in unserem Whitepaper.
Uploaden Sie Ihr Design in die Formlabs-Druckvorbereitungssoftware PreForm. Bereiten Sie den Druck vor, und senden Sie ihn an Ihren Formlabs-3D-Drucker.
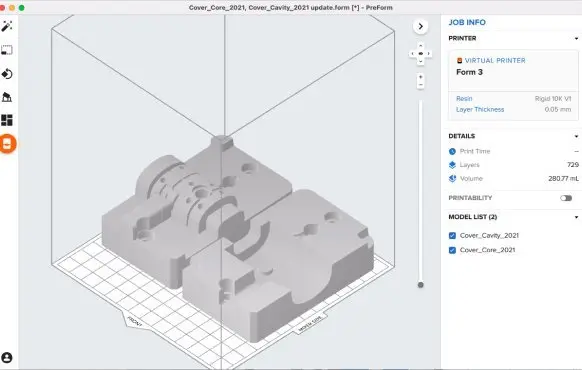
2. 3D-Druck der Formen
Wählen Sie ein Material für den 3D-Druck aus, und starten Sie den Druckvorgang. Rigid 10K Resin , gedruckt bei einer Schichthöhe von 50 Mikrometern, bildet aufgrund seiner hohen Festigkeit, Steifigkeit und Temperaturbeständigkeit das Kunstharz der Wahl für die meisten Spritzgussformen.
Es wird empfohlen, die Form nach Möglichkeit flach und direkt auf der Konstruktionsplattform aufliegend ohne Stützstrukturen zu drucken. Auf diese Weise wirken Sie einem Verziehen der Form entgegen.
Nach dem Waschen und Nachhärten ist die 3D-gedruckte Form bereit für den Einsatz im Spritzguss.
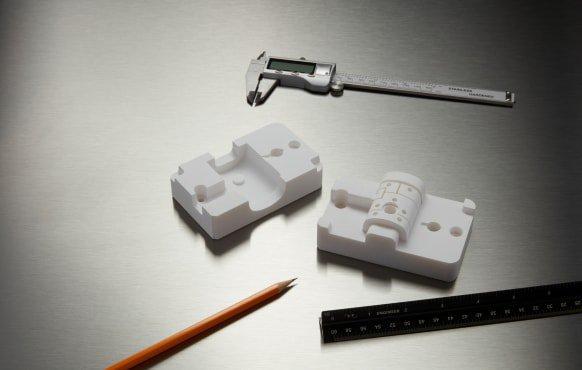
3. Zusammenbau der Formen
Vor dem Zusammenbau sollten Sie die Form ggf. durch manuelles Schleifen, Desktop-Fräsen oder CNC-Bearbeitung nachbehandeln, damit sie kritische Abmessungen erfüllt.
Es wird empfohlen, die gedruckte Form in einen Standard-Metallrahmen oder Master Unit Die zu platzieren, um sie widerstandsfähiger gegenüber starkem Druck zu machen und ihre Lebensdauer zu erhöhen. Schieben Sie die 3D-gedruckte Form dazu vorsichtig in den Metallrahmen. Fügen Sie bei Bedarf außerdem Auswerferstifte, Einsätze, Seitenschieber und andere ggf. benötigte Komponenten hinzu.
Platzieren Sie die Form in Ihrer Spritzgießmaschine.
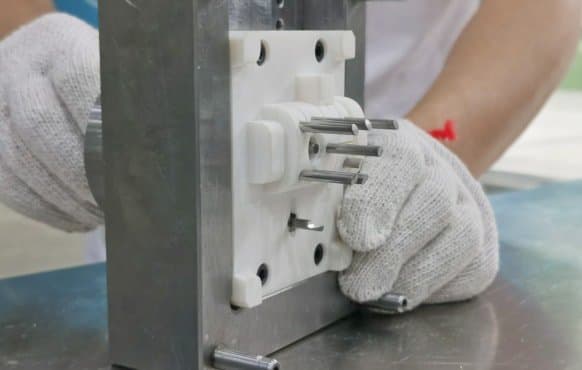
4. Einspannen der Formen
Füllen Sie das Kunststoffgranulat ein, stellen Sie alles Nötige ein, und legen Sie mit der Produktion los. Sofern die Form nicht durch einen Metallrahmen geschützt ist, sollten Sie die Klemmkraft beim Einspannen geringer halten.
Mit 3D-gedruckten Formen kann eine breite Palette an Thermoplasten verarbeitet werden, darunter PP, PE, TPE, TPU, POM oder PA.
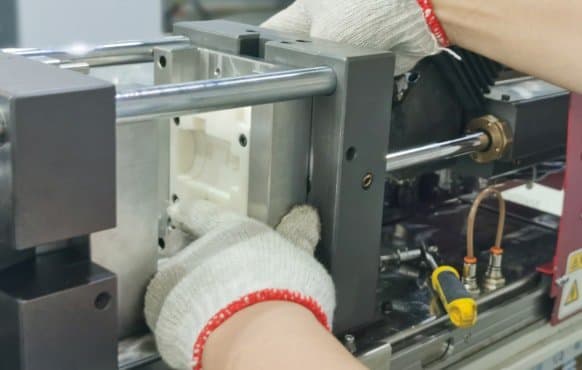
5. Einspritzung
Auf dem Weg zu idealen Verfahrensbedingungen werden Sie womöglich einige Versuche benötigen, da hierbei die Druckgeometrie, die Wahl des Kunststoffs, die Temperaturen und der Druck beim Einspritzen und andere Parameter mit hineinspielen.
Versuchen Sie, Einspritzdruck und -temperatur so gering zu halten wie möglich.
Formlabs-Nutzer fertigen bei Verwendung einfach zu verarbeitender Kunststoffe wie TPE, PP und PE unter Temperaturen bis 250 °C in der Regel mit einer einzelnen gedruckten Form mehrere Hundert Teile. Kommen Kunststoffe wie PA zum Einsatz, die höhere Einspritztemperaturen erfordern, kann die Lebensdauer der 3D-gedruckten Form kürzer ausfallen.
In unserer Dokumentation zu Verfahrensbedingungen finden Sie Testergebnisse hierzu sowohl für Desktop- als auch für industrielle Spritzgießmaschinen.
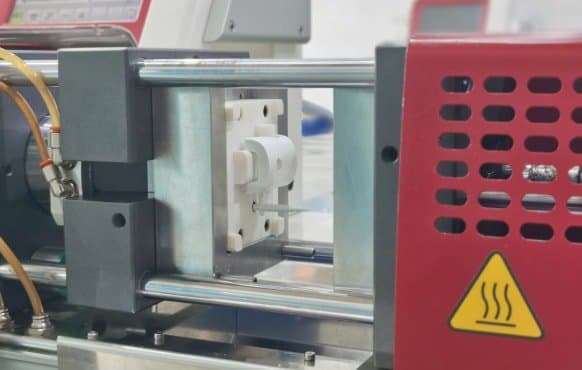
6. Abkühlen
Bei polymerbasierten Formen ist die Abkühlzeit länger als bei Metallformen, da die Wärmeübertragung in Kunststoffen langsamer erfolgt als in Metallen. Daher ist generell davon abzuraten, beim Drucken der Form Kühlkanäle einzubringen.
Stattdessen kann das Abkühlen der Form durch Druckluft oder die Verwendung von austauschbaren Stapeln beschleunigt werden.
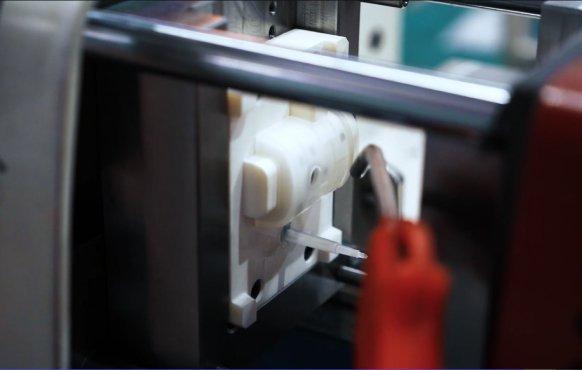
7. Entformen
Entformen Sie die Teile entweder von Hand oder automatisch über Auswerferstifte. Bei Thermoplasten mit hoher Viskosität ist ein Trennmittel zu verwenden. Formentrennmittel sind auf dem Markt weithin erhältlich. So bieten etwa die Hersteller Slide oder Sprayon Silikon-Trennmittel, die mit Formlabs-Kunstharzen kompatibel sind.
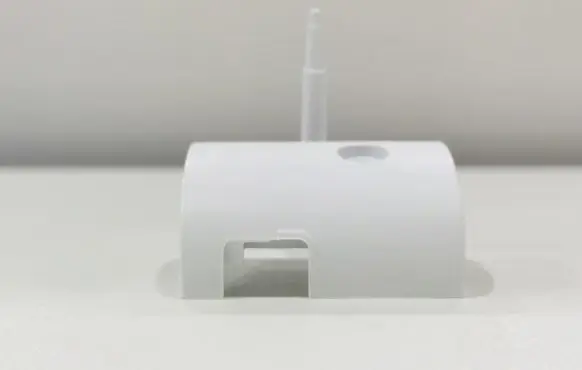
Anwendungen für den Spritzguss von Kleinserien
Die drei primären Anwendungen für den Spritzguss von Kleinserien sind das Rapid Prototyping, das Spritzgießen mit kurzer Laufzeit und individueller Spritzguss auf Abruf.
Rapid Prototyping With Injection Molding
Rapid Prototyping ermöglicht es Unternehmen, Ideen in realistische Konzeptnachweise zu verwandeln, diese Konzepte zu Prototypen mit hoher Originaltreue weiterzuentwickeln, die wie Endprodukte aussehen und funktionieren, und Produkte durch eine Reihe von Validierungsphasen zur Massenproduktion zu führen.
Im Allgemeinen ist der 3D-Druck die typischste Art, schnelle Prototypen zu produzieren. Aber in den späteren Phasen des Entwicklungsprozesses ist es oftmals notwendig, etwas größere Volumen identischer Prototypen mit denselben Materialien und Produktionsprozessen wie für die Endprodukte zu produzieren. Diese Prototypen können für Anwendungen wie Betaversionen oder Feldtests verwendet werden. 3D-gedruckte Formen mit dem Spritzguss zu kombinieren, ermöglicht es Herstellern, schnell und effizient funktionsfähige Prototypen zu entwickeln und den Produktentwicklungsprozess zu beschleunigen.
Zum Beispiel entwickelt das französische Start-up Holimaker eine manuelle Spritzgießmaschine, die Ingenieuren und Produktdesignern die Möglichkeit bietet, Kunststoffteile auf ihrem Desktop für die Herstellung von geringen Mengen an Prototypen, Pilot-Produktionen oder auch limitierten Reihen von Endverbrauchsteilen zu verwenden.
Das Unternehmen offeriert seinen Kunden Machbarkeitsstudien unter Einsatz 3D-gedruckter Formen, die für einen schnellen und erschwinglichen Durchsatz verwendet werden. Auf diese Weise lassen sich in der Pilotproduktionsphase einer neuen Produkteinführung schnell und erschwinglich Prototypen erstellen, um auf deren Basis die Endbedingungen für die Fertigung zu validieren.
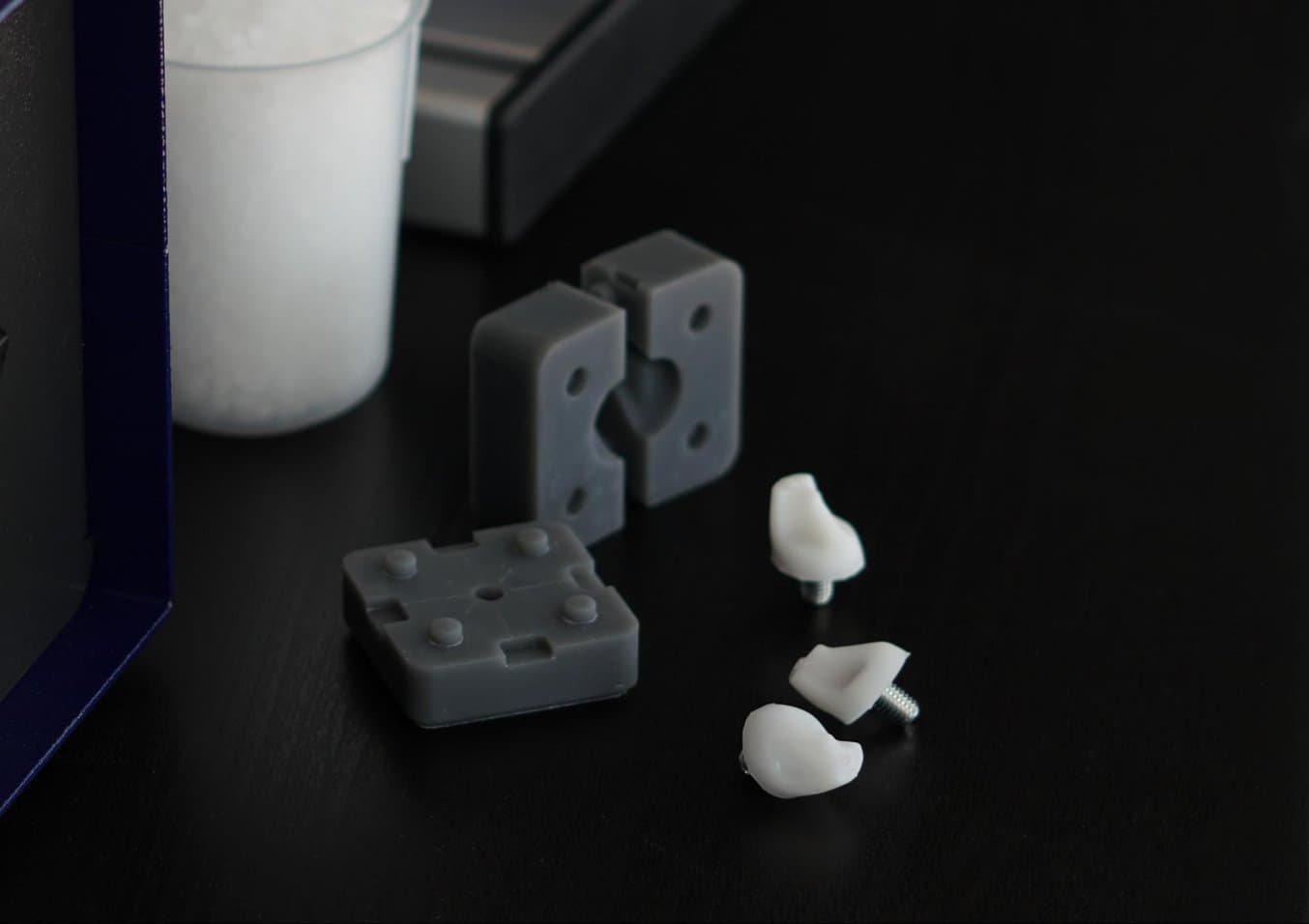
Die Vorproduktionsprototypen dieser Stollen wurden in 3D-gedruckten Formen mit drei unterschiedlichen Thermoplasten spritzgegossen, nämlich POM (180 °C), PA 6.6 (270 °C) und PP (210 °C).
Durch die Verwendung derselben Fertigungsmethode, einschließlich des Entwurfs und der Materialien der Form, können diese Teile in der Praxis getestet und dabei deren Tauglichkeit für die Massenproduktion sichergestellt werden. Die 3D-gedruckten Formentwürfe können dann während der Massenproduktion einfach an den Werkzeugstahl angepasst werden.
Mithilfe der 3D-gedruckten Formen hat es Holimaker geschafft, die Durchlaufzeit für die Formenherstellung für den Spritzgussprozess auf 24 Stunden zu verkürzen, und es verwendet in 80 bis 90 % seiner derzeitigen Projekte 3D-gedruckte Spritzgussformen.
Spritzguss mit kurzer Laufzeit
Spritzguss mit kurzer Laufzeit bietet Herstellern ein Mittel, kleinere Serien von Endverbrauchsteilen herzustellen, für Produkte, die nur in begrenzter Menge produziert werden, oder Pilotserien eines Produkts zur Markterprobung, bevor zu viel Kapital in das Projekt gesteckt wird.
Die Nutzung von Spritzguss zur Kleinserienfertigung bietet die Möglichkeit, akkurate und wiederholbare Endverbrauchsteile herzustellen, ohne die hohen Fixkosten des traditionellen Spritzgussprozesses.
Multiplus ist ein Spritzgusslösungsanbieter mit Unternehmenssitz in Shenzhen, der den gesamten Produktionszyklus abdeckt, vom Entwurf bis zur Herstellung von Kunststoffprodukten, und jedes Jahr mehr als 250 Kunden, darunter auch einer Reihe von Fortune-500-Unternehmen, seine Dienstleistungen anbietet. Manche davon geben eher kleine Chargen in Auftrag. Die Produktion solcher Chargen mittels Spritzguss ist mit traditionellen Methoden kostspielig und zeitaufwändig, aufgrund der Komplexität der Fertigungsprozesse harter Werkzeugausstattung.
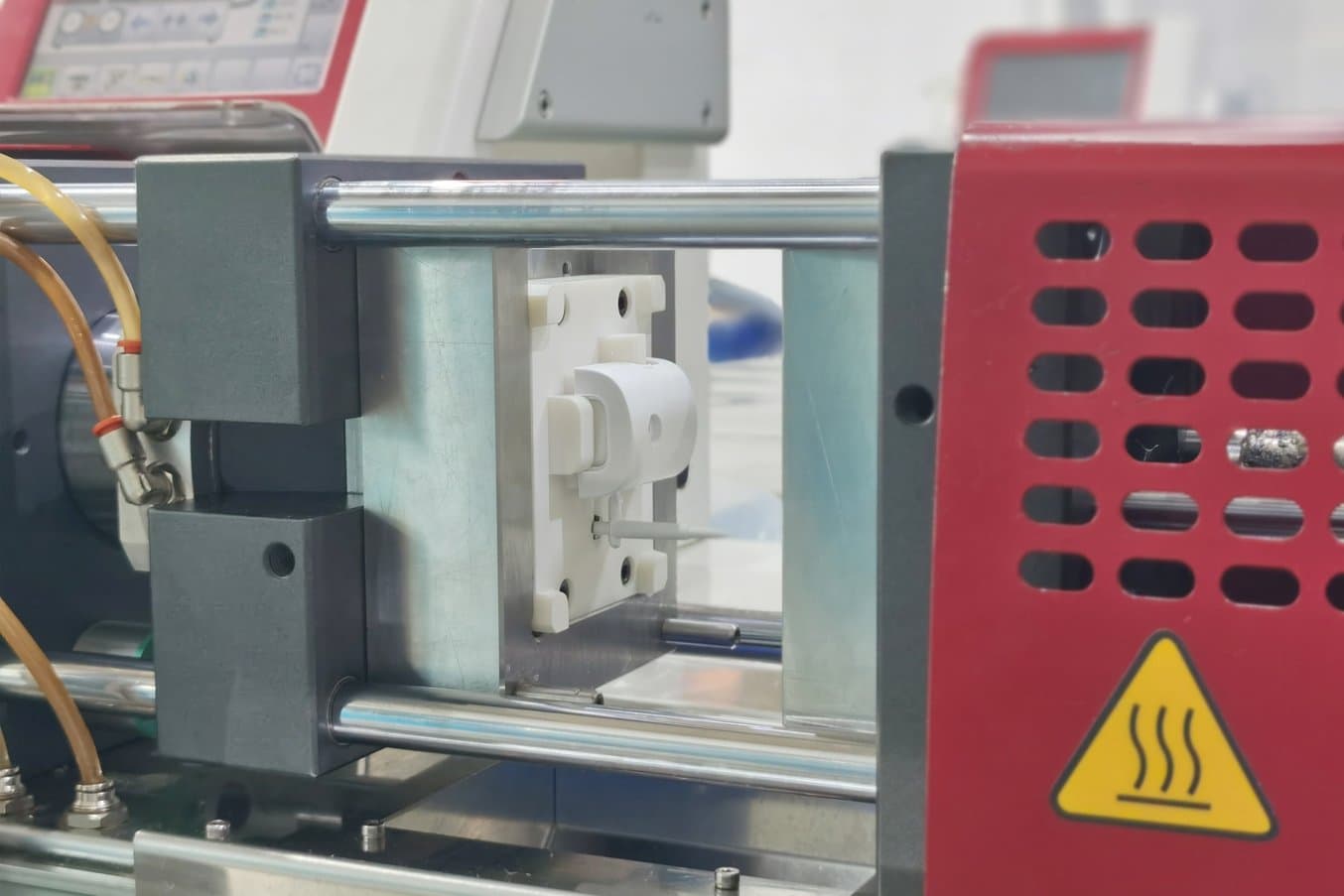
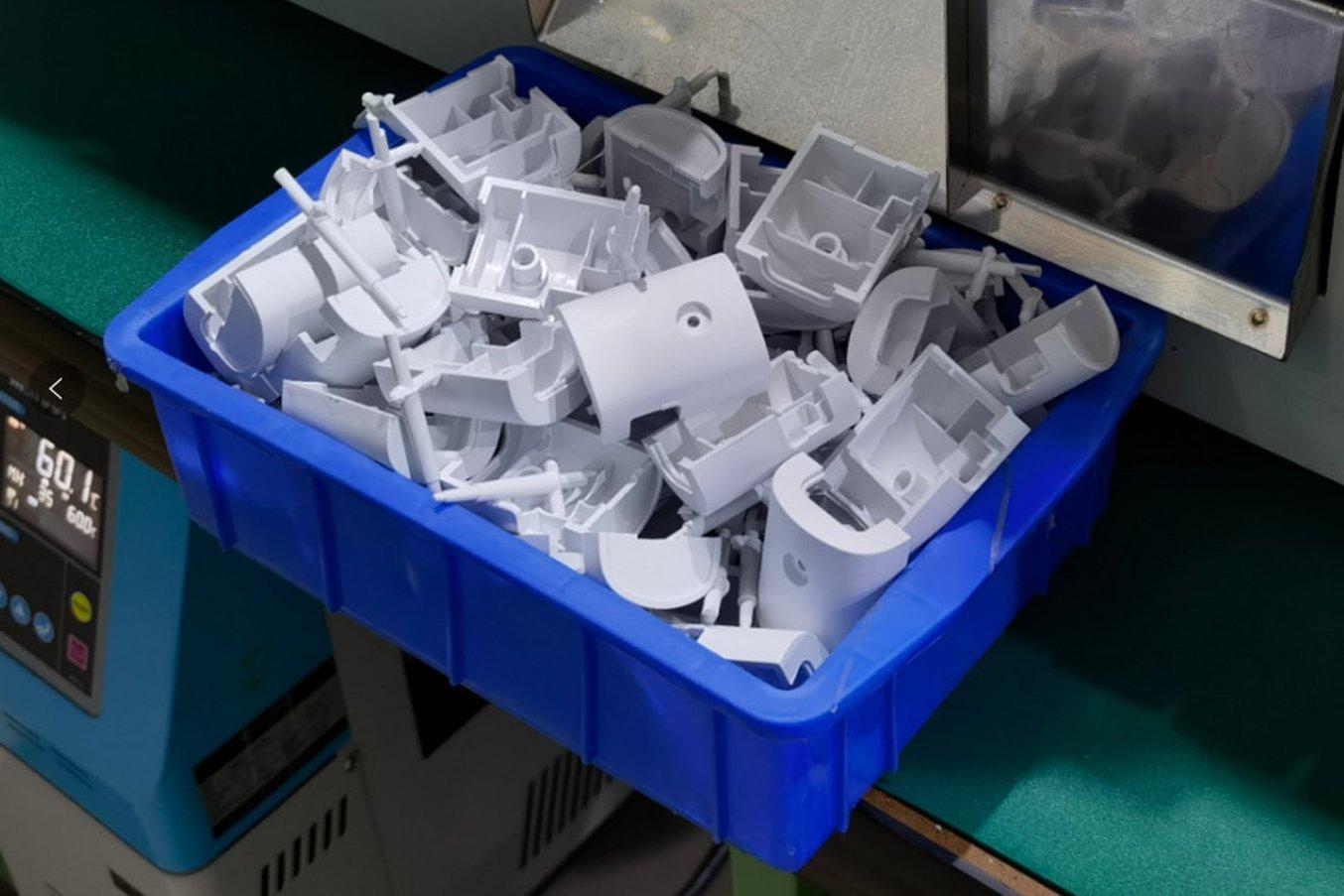
ABS-Gehäuseteile für Bedienelementkästen, aus 3D-gedruckten Spritzgussformen, frisch aus der Spritzgussproduktion
Mit steigender Nachfrage nach der Produktion von Kleinserien hat sich Multiplus dem 3D-Druck zugewandt. So wollte man verschiedene Materialien kennenlernen, um schließlich die kostengünstigste Methode für die Produktion von Kunststoffformen für kleinere Aufträge und Pilotproduktionsdurchläufen zu finden. Durch die Fertigung von Spritzgussformen in Kleinserie mit Formlabs-3D-Druckern konnte im Vergleich zur Bearbeitung von Aluminiumformen der Kosten-, Arbeits- und Zeitaufwand gesenkt werden. Zudem ließ sich das Verfahren nahtlos in Verbindung mit den von Multiplus eingesetzten industriellen Spritzgießmaschinen von Babyplast verwenden.
Individueller Spritzguss auf Abruf
Individueller oder schneller Spritzguss auf Abruf kann die Herstellung von personalisierten Endverbrauchsteilen zu bestimmten Zwecken erfordern, z. B. humane Faktoren, Anwendungen oder Ereignisse, und das oftmals mit beschleunigtem Zeitplan. Das begrenzte Volumen und/oder die kurze Durchlaufzeit bedeutet, dass traditionelles Spritzgießen mit Werkzeugen weder effizient noch durchführbar ist. In diesem Fall ist das Spritzgießen von Kleinserien mit 3D-gedruckten Formen eine ideale Lösung, um den Vorgang zu beschleunigen und Sonderanfertigungen zu liefern.
Im Beispiel von Braskem, einem der weltweit führenden petrochemischen Unternehmen, wird der Fall hervorgehoben, wie 3D-gedruckte Formen verwendet werden, um schnelle Bestellungen auf Abruf zu bedienen. Während der ersten Welle der COVID-19-Pandemie musste das Unternehmen Tausende von Maskenhalterungen produzieren, um seine weltweit vertretenen Mitarbeiter zu schützen. Braskem fand heraus, dass der Spritzguss die ideale Methode für die Herstellung der Teile war, aber ohne Zugang zu 3D-Druck hätte es eine teure Metallform auslagern müssen, die das Team Geld und wertvolle Zeit gekostet hätte.
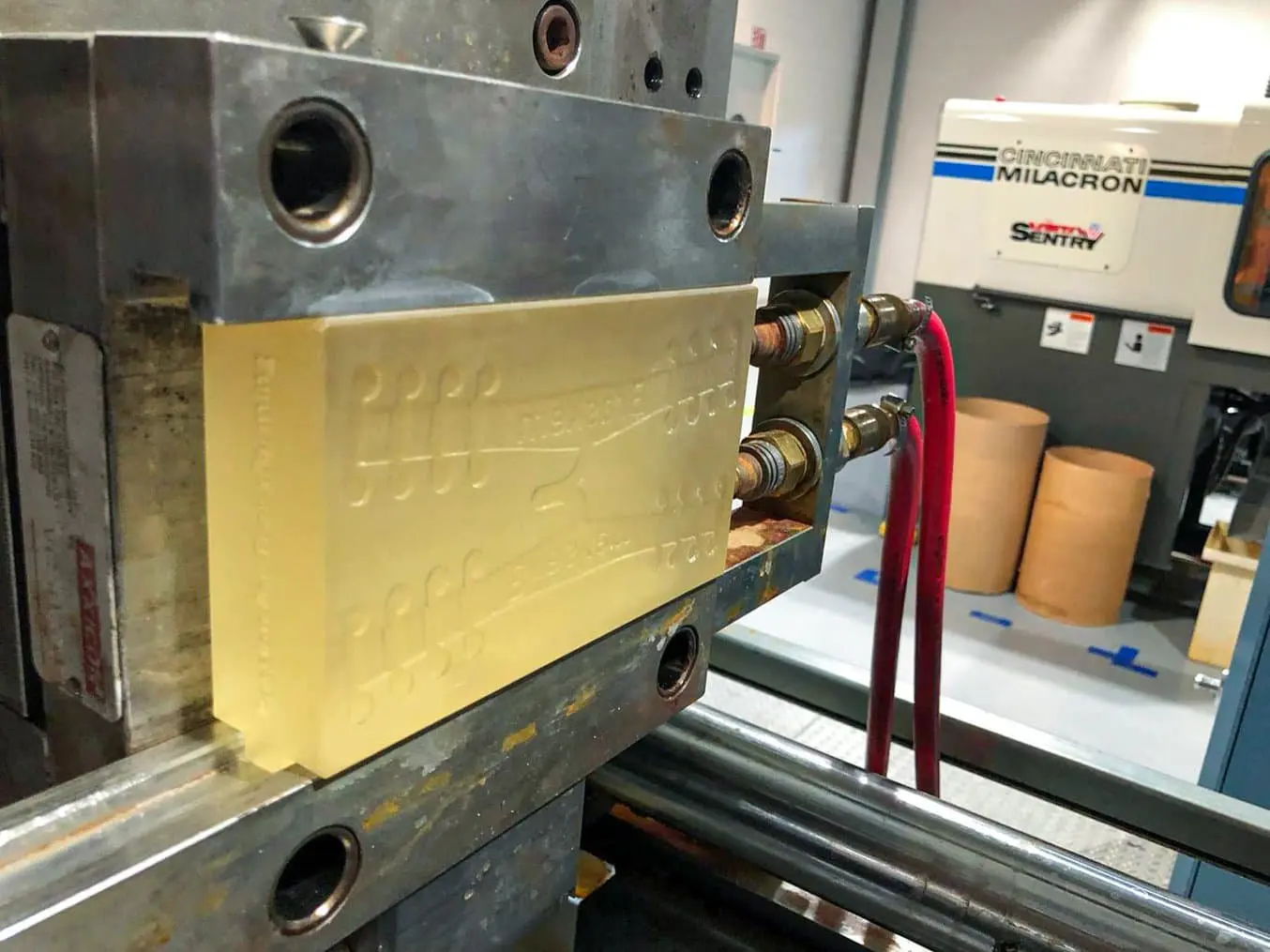
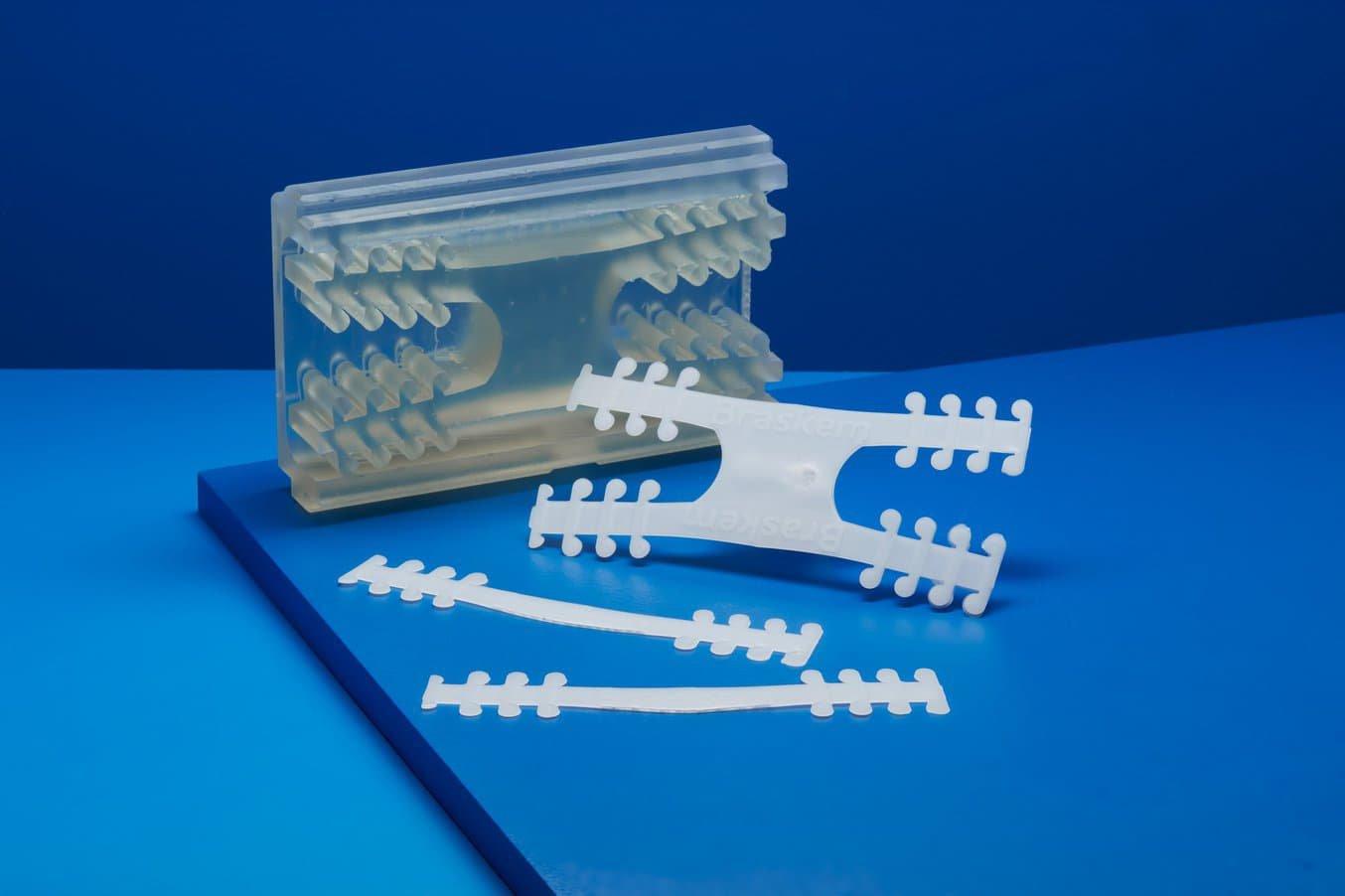
Braskem verwendete eine 3D-gedruckte Form zusammen mit einer traditionellen, industriellen Spritzgießmaschine, um die Maskenhalterungen schnell über Spritzguss herzustellen.
Das Team von Braskem nutzte den Spritzguss, indem es einen Form 3 von Formlabs verwendete, um die Form für seine Halterungen zu drucken, und die vollelektrische Spritzgießmaschine Cincinnati Milacron 110 Ton Roboshot, um die Halterungen zu entwickeln.
Durch die Nutzung von 3D-Druck konnte das Team innerhalb einer Woche nach dem Eingang der E-Mail des VP Tausende Halterungen fertigen und sie für die Auslieferung an Niederlassungen auf der ganzen Welt vorbereiten.
Steigen Sie in den Spritzguss für Kleinserien ein
Beschleunigen Sie die Produktentwicklung, senken Sie die Kosten und Durchlaufzeiten und bringen Sie bessere Produkte auf den Markt, indem Sie Ihren Entwicklungsprozess mit dem 3D-Druck und Spritzguss von Kleinserien bereichern.