Brose, fornitore di accessori per il settore automobilistico a livello mondiale, si serve della stampa 3D SLS per produrre parti per uso finale
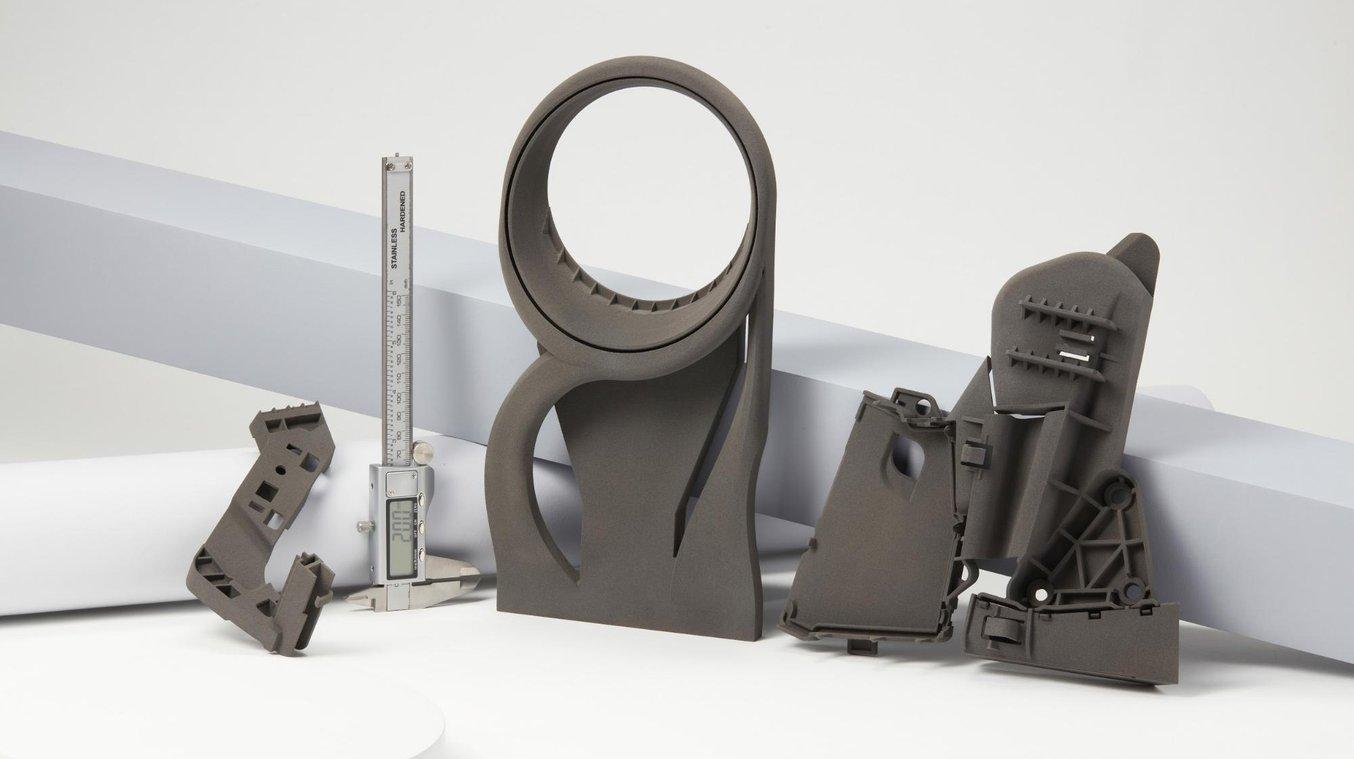
Siamo sicuri che, se siete mai saliti su un'automobile, avete interagito con almeno uno dei prodotti di Brose. Con 25 000 dipendenti in 24 paesi, quest’azienda a gestione familiare è uno dei più grandi fornitori di primo livello del settore automobilistico. Collabora con 80 marchi automobilistici, oltre 40 fornitori e 50 produttori di biciclette elettriche.
A livello globale, circa la metà dei veicoli nuovi in commercio contiene almeno un prodotto Brose, tra cui vari componenti e sistemi meccatronici, come le strutture dei sedili, i componenti delle portiere e diversi comandi e motori elettrici.
Brose, tra le più innovative aziende tedesche, è in un'ottima posizione per integrare la produzione additiva nei prodotti e nel workflow di produzione. L'azienda utilizza varie tecnologie di produzione additiva per prototipi, strumenti e fissaggi. Il prossimo obiettivo è quello di inserirla nella produzione in serie. La nuova arrivata nella flotta di stampanti di Brose, la Fuse 1, la prima stampante 3D a sinterizzazione laser selettiva (SLS) da banco di Formlabs, è tra gli strumenti che accompagneranno l'azienda in questo percorso.
Continua a leggere per scoprire l'esperienza con il nuovo dispositivo di Christian Kleylein, tecnologo per la produzione in serie di parti polimeriche tramite produzione additiva di Brose, e come l'azienda progetta di utilizzare la stampa 3D per la produzione in serie.
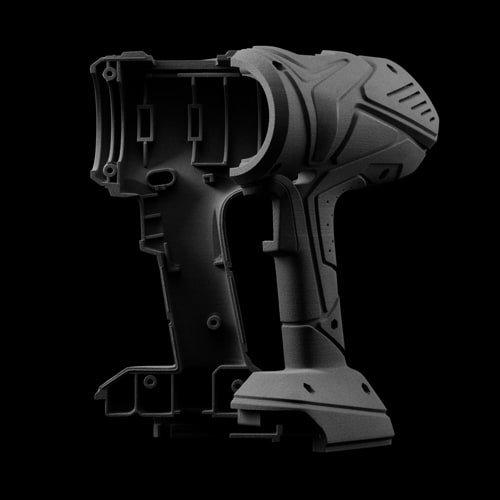
Introduzione alla stampa 3D tramite sinterizzazione laser selettiva (SLS)
Stai cercando una stampante 3D per creare parti robuste e funzionali? Scarica il nostro whitepaper per scoprire come funziona la stampa SLS e perché è un processo di stampa 3D molto diffuso per la prototipazione funzionale e la produzione per l’utilizzo finale.
Utilizzo della Fuse 1 in un contesto industriale
La produzione additiva è uno dei più recenti tra i settori di competenza principali di Brose. La produzione additiva è uno dei più recenti tra i settori di competenza principali di Brose.
Brose ha acquistato la sua prima stampante 3D FDM oltre dieci anni fa, ma presto si è aperta a quasi tutti gli altri processi di produzione additiva presenti sul mercato, dalla stereolitografia (SLA) ai processi a getto, fino alla sinterizzazione laser selettiva e a grandi parchi macchine di stampanti 3D per il metallo.
La flotta di stampanti 3D di Brose è dotata di vari sistemi di stampa 3D SLS, dai piccoli apparecchi desktop fino alle più grandi stampanti industriali tradizionali. Hanno una lunga esperienza con questa tecnologia e sono stati una delle prime aziende in Europa a sperimentare la Fuse 1.
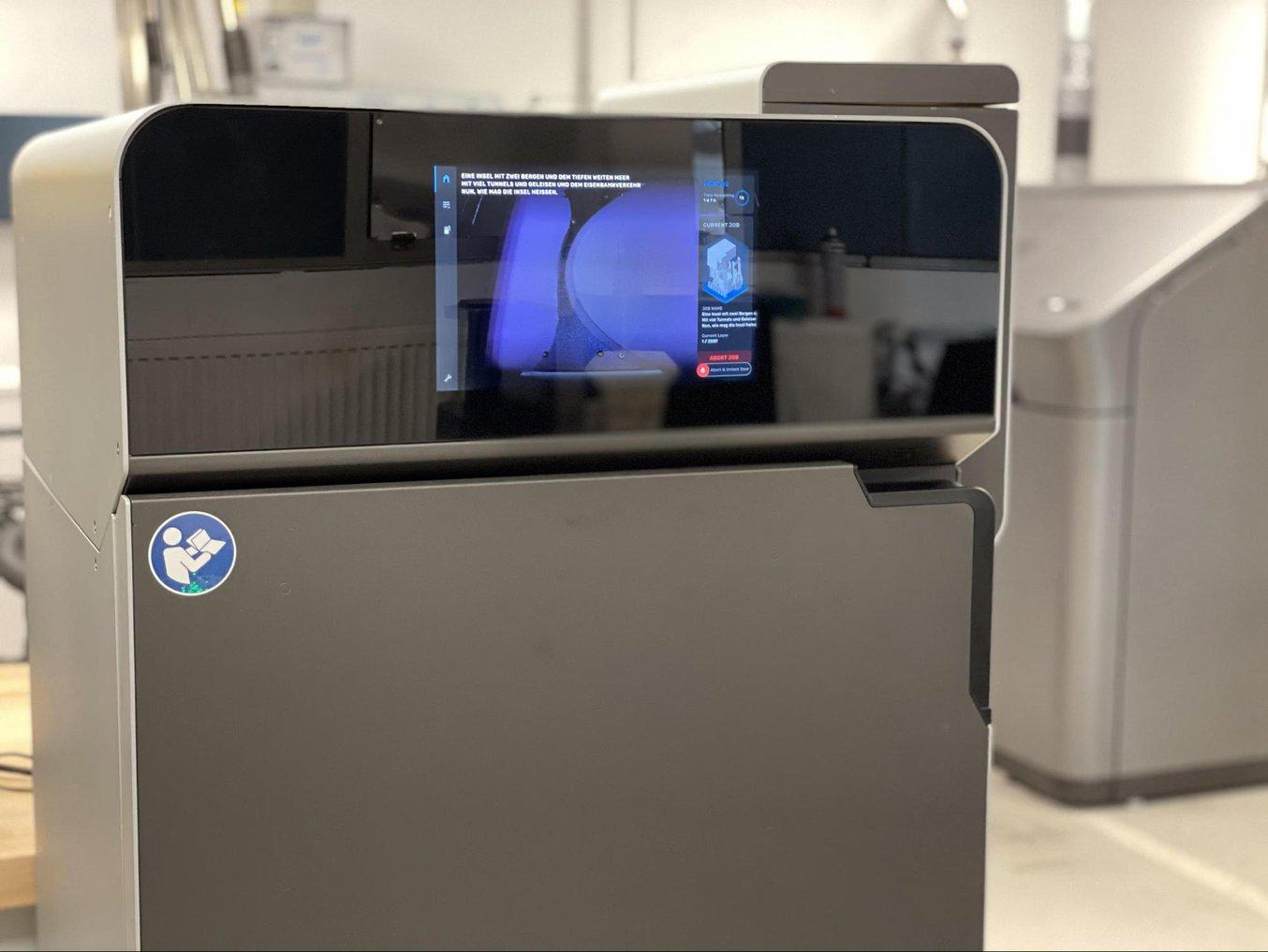
Il centro di produzione additiva di Brose comprende quasi tutti i processi di stampa 3D presenti sul mercato, tra cui la nuova arrivata, la Fuse 1.
Considerando che l’installazione e la messa in funzione di una delle macchine più grandi può richiedere una settimana, Kleylein è rimasto colpito dalla velocità del processo di installazione della Fuse 1.
"Installarla è molto semplice. Se avete una stanza chiusa con un sistema di aria condizionata, siete pronti. Non richiede molto spazio, e questo è un grande vantaggio. Non è necessaria alcuna fase di calibrazione; basta solo assicurarsi che sia in piano. Una volta collegata la stampante alla corrente, potete avviare la procedura di impostazione e stampare il giorno della consegna" afferma Kleylein.
"La curva di apprendimento è rapida. Ci sono ottime probabilità che la prima stampa vada a buon fine. Poi puoi fare degli aggiustamenti e prendere confidenza con l'apparecchio."
Christian Kleylein
"Abbiamo sottoposto la Fuse 1 a molti test. Abbiamo stampato un gran numero di parti con lo spessore minimo, e altre dal design molto sottile e allungato. Da queste sperimentazioni abbiamo riscontrato che anche quando c'era un errore nelle dimensioni, le parti variavano sempre nello stesso modo. Quindi una volta ottimizzato il processo, si riescono a ottenere parti finali molto precise dal punto di vista dimensionale" sostiene Kleylein.
Il team ha eseguito molte stampe sulla Fuse 1 per testarne i limiti, da cicli notturni di circa 12 ore a camere di stampa riempite al massimo della capacità con più di 1000 piccole parti, per un tempo totale di quattro giorni.
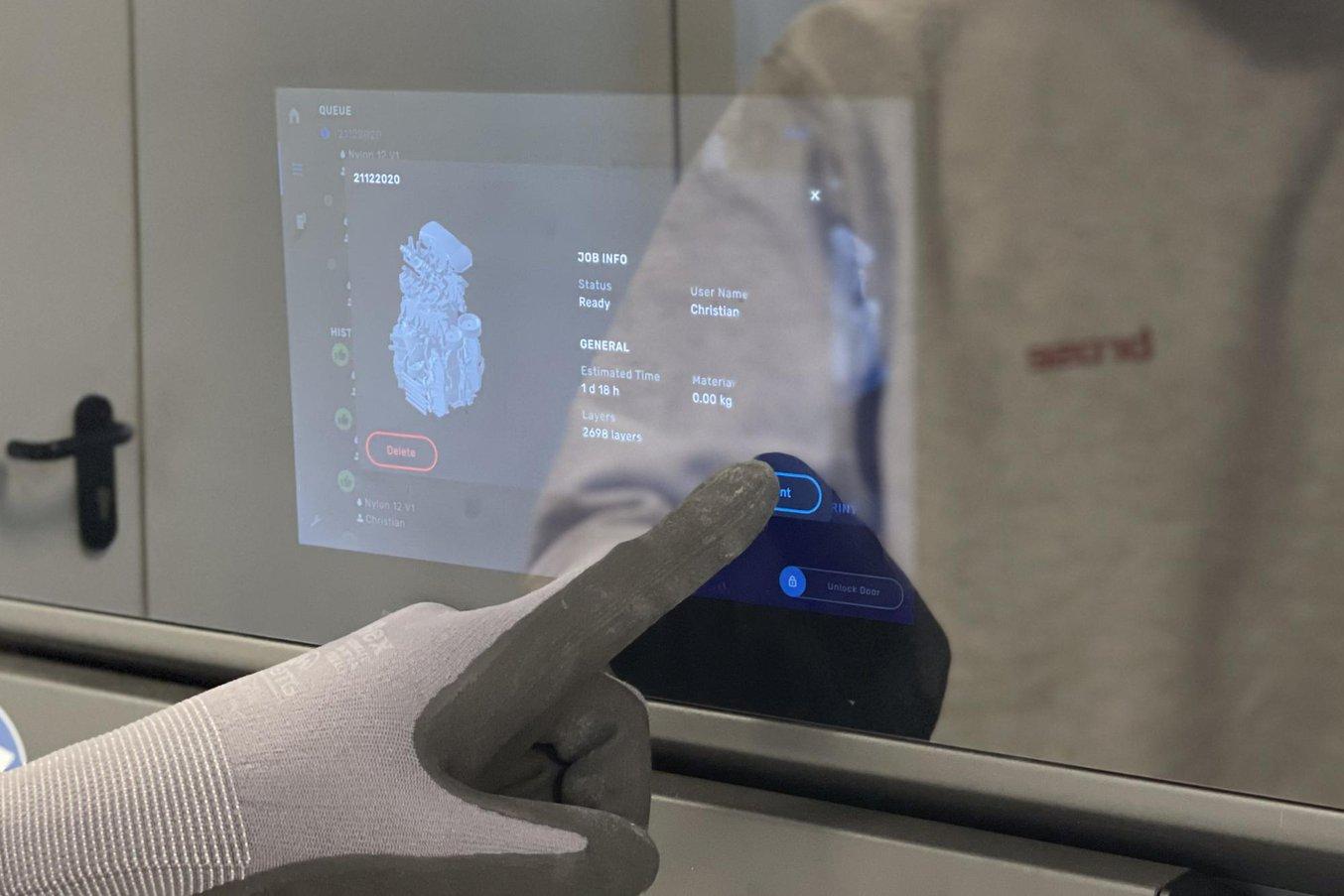
La sinterizzazione laser selettiva non richiede strutture di supporto, perché durante la stampa le parti sono circondate da polvere non sinterizzata. È possibile posizionare le parti con una densità elevata in modo da massimizzare lo spazio di stampa.
"La finitura superficiale è ottima, molto liscia, con pochissimi strati visibili. In questo modo le parti possono essere usate subito dopo essere state estratte dalla stampante e ripulite dai residui di polvere. Si possono realizzare molti dettagli precisi. Ad esempio, se vuoi stampare degli ingranaggi, otterrai delle belle parti rotonde" afferma Kleylein.
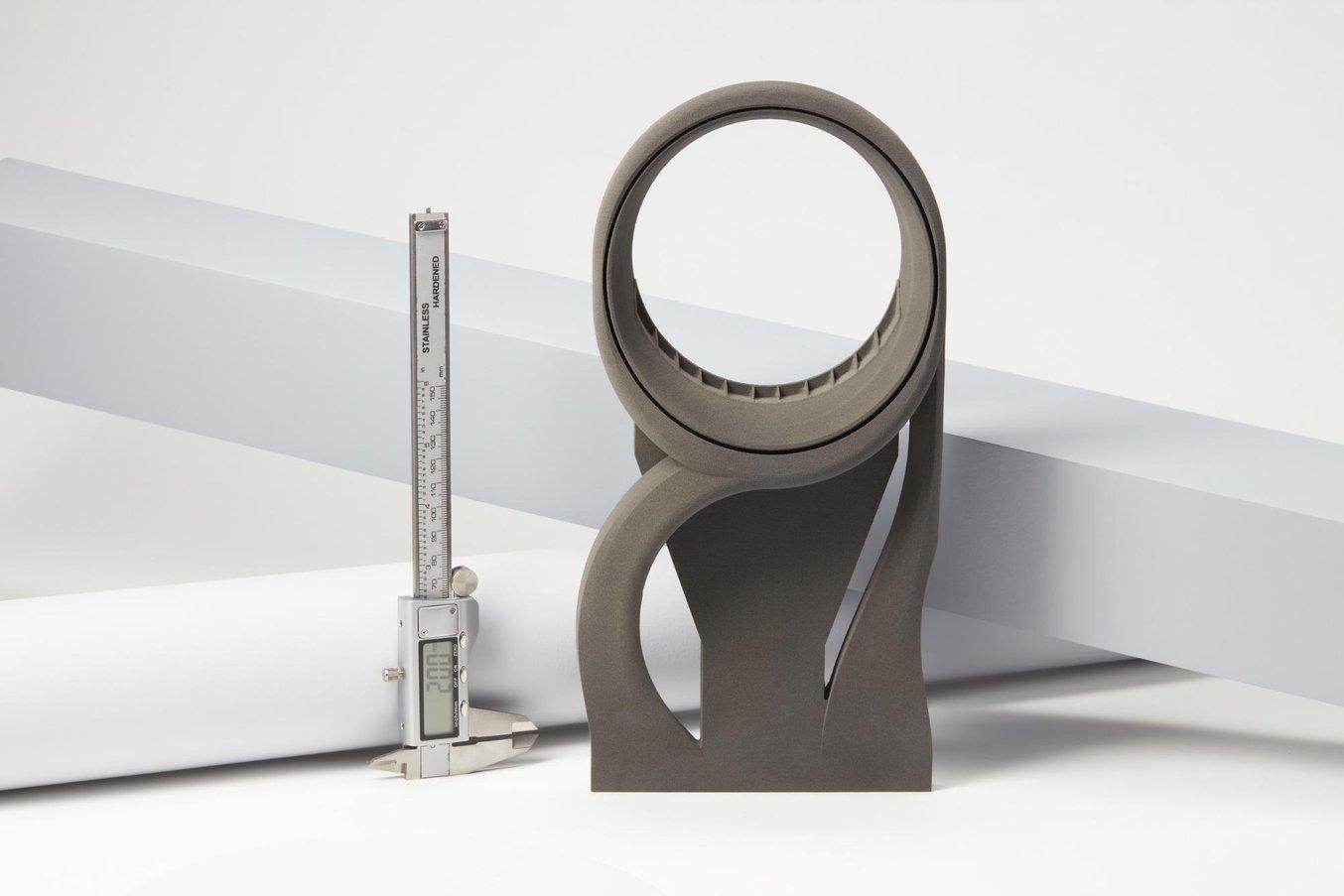
Attrezzatura per i test di fine linea per gli apparecchi Brose durante l'assemblaggio.
Con la Fuse 1, Formlabs punta a superare il divario tra stampanti SLS tradizionali e stampanti a basso costo di piccolo formato offrendo alta qualità, ingombro ridotto e flusso di lavoro completo e semplificato a un prezzo di gran lunga inferiore rispetto a quello dei sistemi SLS tradizionali.
"È più simile alle stampanti industriali che a quelle da banco. Con il laser a fibra, Formlabs ha sviluppato un sistema di scansione ottica tutto suo, e il fascio laser viene deviato nel modo corretto" sostiene Kleylein.
"È una macchina. Non ha niente di simile a un giocattolo: è uno strumento di lavoro vero e proprio. Ha l'aspetto di un apparecchio industriale, e funziona in modo perfetto. Noi del team di collaudo siamo molto soddisfatti. Si può usare molto facilmente in un contesto industriale."
Christian Kleylein
Si potrebbe pensare che per le parti del settore automobilistico siano più adatte stampanti di maggiori dimensioni, ma secondo Kleylein in volume di stampa della Fuse 1 è sufficiente per la maggior parte dei design di Brose.
"L'80% delle parti che stampiamo hanno all'incirca le dimensioni di un pugno, al massimo. Quindi possiamo realizzarle con la Fuse 1. Ci sono alcune parti che sono una via di mezzo e poi ci sono quelle davvero grandi" afferma Kleylein.
"La velocità di stampa è buona, e dopo l'ottimizzazione probabilmente aumenterà ancora. Ma come punto di partenza si ha una buona velocità di stampa e il giusto spazio per determinate applicazioni" sostiene Kleylein.
La Fuse 1 è inoltre accompagnata dalla Fuse Sift, una postazione di post-elaborazione che combina in un solo dispositivo l’estrazione delle parti, nonché il recupero, la conservazione e la miscelazione della polvere.
"In passato, con alcune macchine, l'attrezzatura di post-elaborazione non era inclusa. Bisognava progettarla da soli, pensando persino alla miscelatura. La Fuse Sift invece offre un ottimo sistema integrato. Ci sono ventole per estrarre la polvere, che permettono la riduzione al minimo delle attrezzature di sicurezza personali più limitanti. Setaccia la polvere, così le particelle troppo grandi per essere filtrate vengono raccolte per essere riciclate. La polvere viene miscelata e così puoi controllare il tuo tasso di rigenerazione. Se ti servono delle proprietà specifiche, puoi stampare con polvere nuova al 100% o polvere usata al 100%. Basta inserirla nel miscelatore e la polvere viene distribuita correttamente" afferma Kleylein.
Kleylein ha riscontrato che produrre parti SLS con la Fuse 1 generalmente non richiede interventi, ma soltanto tempi e sforzi ridotti per la preparazione delle nuove stampe, la manutenzione della stampante e la post-elaborazione delle parti.
"Si può posizionarla in un piccolo laboratorio, e a una persona basterà solo un quarto del suo tempo per completare tutte le operazioni necessarie. Il software gratuito è efficiente e il processo di stampa è paragonabile a quello delle stampanti più grandi, quindi è veloce da preparare" sostiene Kleylein.
"È molto semplice, molto ben concepita. La stampante può essere riavviata in soli 30 minuti."
Christian Kleylein
"È una stampante molto adatta ai parchi stampanti. Si presta molto bene alla pianificazione e funziona senza pause. Il fatto di poter stampare 24 ore su 24, 7 giorni su 7 è un grande vantaggio. Non abbiamo momenti di inattività. Può capitare solo se il lavoro di stampa non è abbastanza pieno e si interrompe durante il fine settimana" afferma Kleylein.
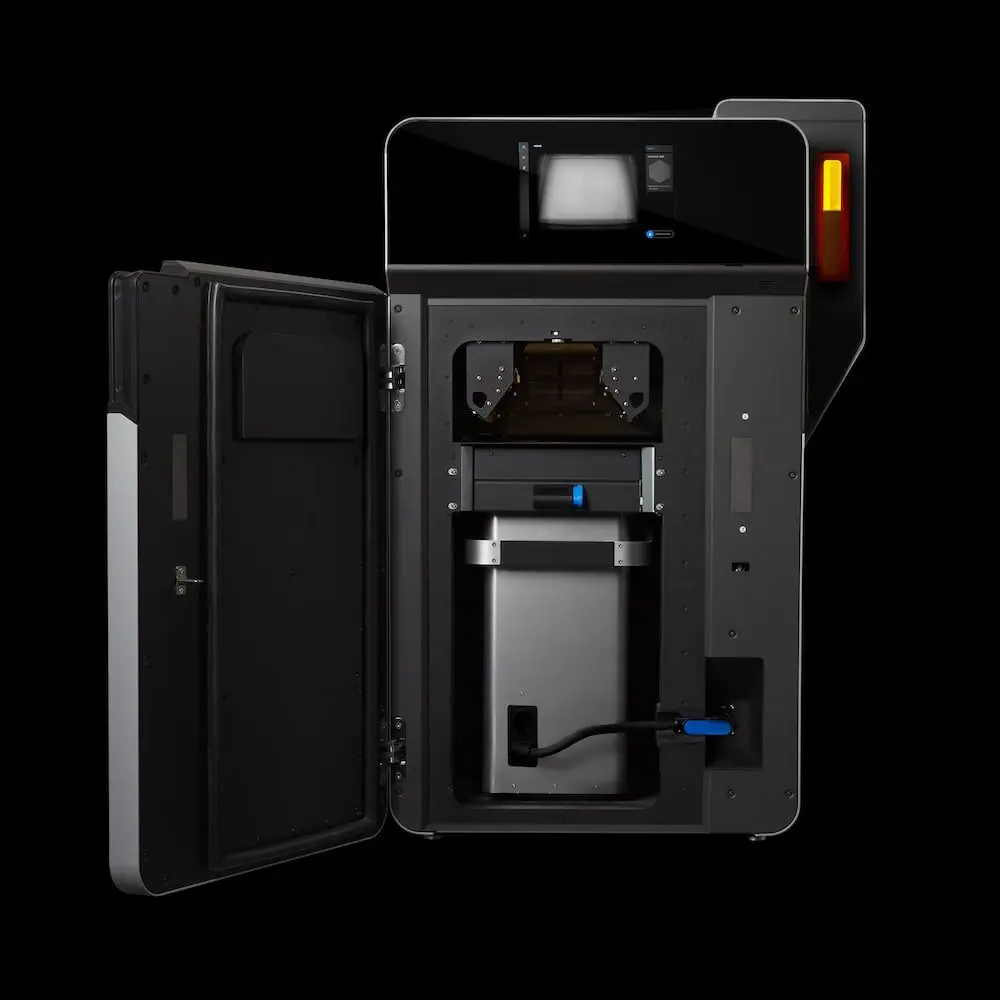
Dimostrazione di prodotto della Fuse 1
Guarda la nostra dimostrazione di prodotto per un’introduzione alla Fuse 1 e alla stampa 3D SLS svolta dagli esperti di Formlabs.
Applicazioni della sinterizzazione laser selettiva per utilizzo finale: parti di ricambio e parti per prodotti alla fine del ciclo di vita
Inizialmente Brose prevede di utilizzare la Fuse 1 per la prototipazione funzionale così da trarre vantaggio dai tempi di produzione rapidi e dal materiale, la Nylon 12 Powder, che offre proprietà simili a quelle dei materiali attualmente impiegati dall'azienda per la produzione. Ma il team di Kleylein sta già validando parti e studiando casi specifici per le prime applicazioni per utilizzo finale, e i principali candidati sono le parti di ricambio e quelle alla fine del ciclo di vita.
Quando un modello di automobile non è più in commercio, i fornitori hanno comunque l'obbligo di fornire parti di ricambio. Di solito questo significa cercare di stimare quante parti di ricambio occorreranno, iniettarle tutte per lo stampaggio e poi conservarle in magazzino.
"Questo è un grande spreco di risorse, di spazio e di denaro. Stampando le parti in 3D non avremo bisogno di conservare gli stampi a iniezione e le parti per i successivi 15 anni. C'è molta richiesta di parti di ricambio e parti alla fine del ciclo di vita, perché questi prodotti si esauriscono, e abbiamo molte parti in plastica realizzate tramite stampaggio a iniezione. Se riusciamo a conservarle correttamente e arrivare a un'alta densità, abbiamo un buon rapporto costi-benefici" spiega Kleylein.
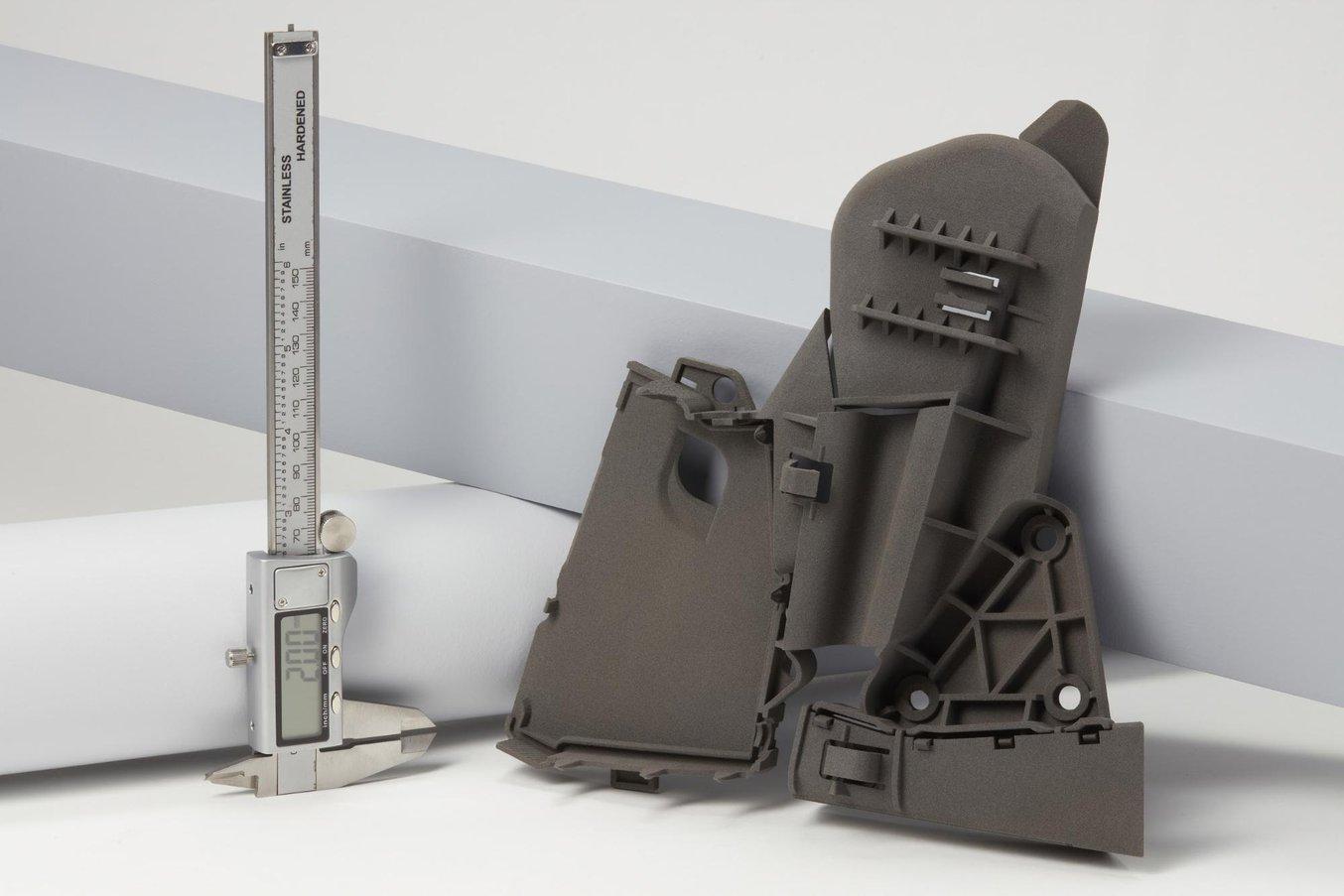
Una parte di ricambio per il modulo di una maniglia per portiera stampato in 3D che viene solitamente realizzato tramite stampaggio a iniezione.
"Nel settore automobilistico è importante offrire la più alta qualità possibile al miglior prezzo. Al momento qualsiasi quantità sotto le 10 000 parti l'anno potrebbe essere stampata mediante la sinterizzazione laser selettiva."
Christian Kleylein
La sinterizzazione laser selettiva è una tecnologia ideale per la produzione sotto molti punti di vista:
-
È in grado di creare parti di alta qualità con proprietà simili a quelle delle parti realizzate tramite stampaggio a iniezione.
-
Può essere implementata in un ambiente di produzione.
-
È uno dei processi di produzione additiva più puliti e con meno sprechi, cosa che sta diventando sempre più importante nella produzione.
"Si possono usare polimeri tecnici per produrre parti tecniche, e non servono supporti. Anche la post-elaborazione è molto pulita, e le parti hanno pochissima polvere residua, anche prima della sabbiatura" sostiene Kleylein.
"Alcuni dei clienti di Brose sono molto favorevoli a questa tecnica: apprezzano il nostro tentativo di stampare praticamente senza sprechi. Possiamo riutilizzare la polvere, così non dobbiamo buttarla via. E non ci sono altre sostanze chimiche da riciclare. Entro la fine dell'anno puntiamo a ridurre a zero gli sprechi per tutte le nostre macchine a sinterizzazione laser selettiva" conclude Kleylein.
Il futuro della sinterizzazione laser selettiva nella produzione in serie
Naturalmente l'obiettivo finale è quello di utilizzare la sinterizzazione laser selettiva per realizzare in serie parti per prodotti automobilistici di nuova generazione, che secondo Christian arriveranno in un futuro molto vicino.
"Prototipi e parti di ricambio: ora li puoi realizzare. Al momento, a giudicare dagli sviluppi tecnici, credo che potremo pensare alla produzione in serie tra quattro o cinque anni."
Christian Kleylein
Per raggiungere questo obiettivo sono necessari due cambiamenti fondamentali: la presa in considerazione della produzione additiva durante lo sviluppo di prodotto a partire dalla fase di design e un ulteriore calo del costo dei materiali e degli apparecchi.
"Il maggiore ostacolo è fare in modo che i designer di prodotto siano davvero consapevoli delle possibilità fornite dalla stampa 3D e prendano la decisione di stampare in 3D le parti. Non si avrà mai un buon rapporto costi benefici con componenti progettati per lo stampaggio a iniezione. Bisogna progettare in funzione del processo" prosegue Kleylein.
"Occorre valutare la quantità di pezzi che si progetta di stampare e l'efficienza dei sistemi di produzione tradizionali. Una volta che la proposta di valore è corretta, produrremo una parte con il sistema di produzione più efficiente possibile. Non ci serviremo a tutti i costi della stampa 3D, ma se è il modo migliore per produrre una determinata parte, approfitteremo di questa tecnologia" afferma Kleylein.
Abbassando la barriera di ingresso per la stampa 3D SLS, la Fuse 1 svolgerà un ruolo fondamentale nel rendere possibile questa svolta nella produzione. Brose ha già pianificato di continuare a espandere rapidamente le sue capacità di stampa 3D. Il loro secondo laboratorio per la produzione additiva di plastiche è in costruzione negli Stati Uniti, e presto riceverà la prima Fuse 1.
"Abbiamo ancora molte sfide davanti a noi, ma se guardo la Fuse 1, vedo un prodotto con grande potenziale a un prezzo davvero competitivo."
Christian Kleylein