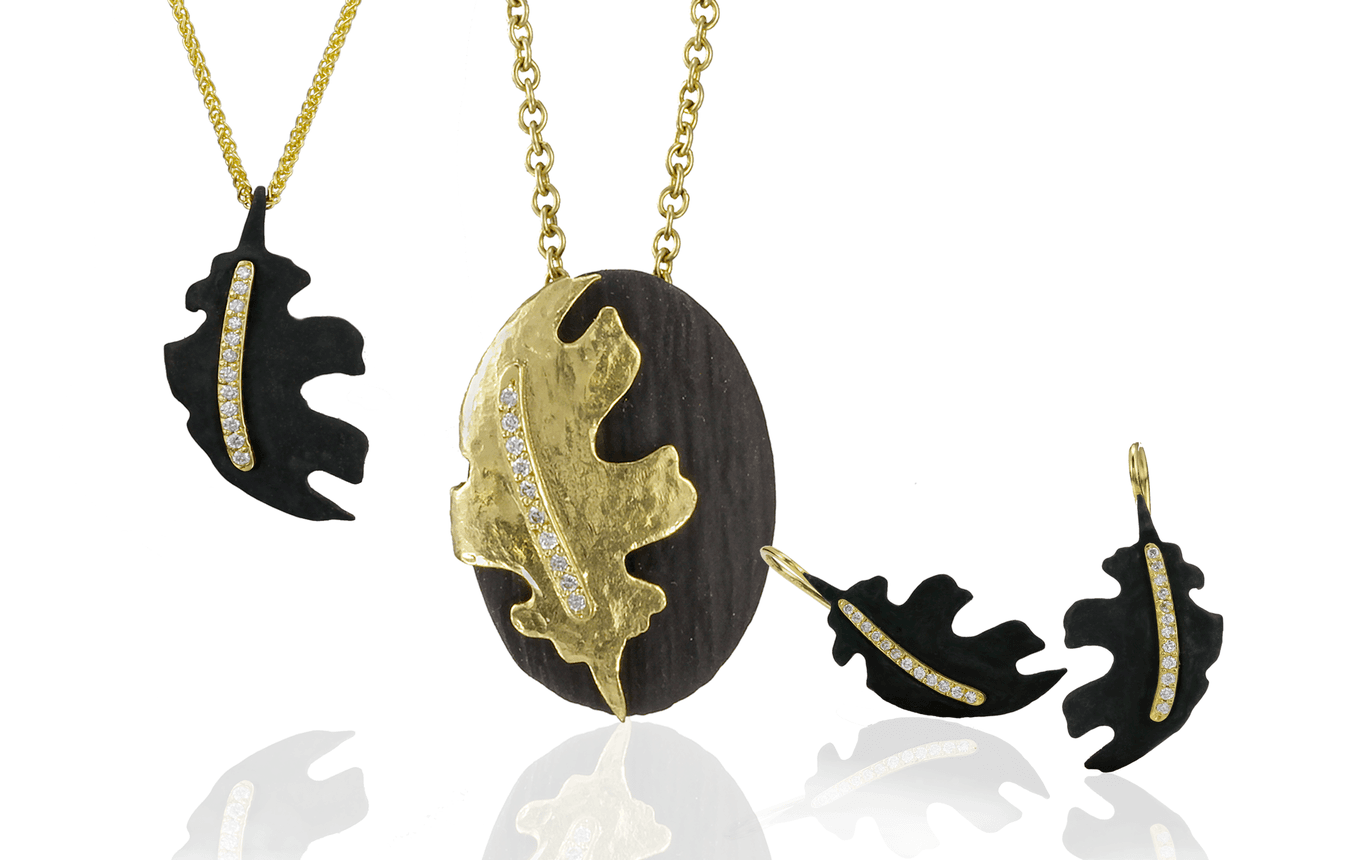
Sarah Graham’s use of unique materials and organic forms has gained her a reputation as one of the most innovative designers in the fine jewelry industry. She continues to break convention by using the Form 1+ SLA 3D printer to create highly-detailed jewelry, inspired by nature. Each piece is a work of art, composed of multiple interlocking pieces that rely on precise detail and rich textures to tell their story. Formlabs offered a first look at Sarah’s latest collection, ‘Oak Leaf’, at our booth during MJSA Expo New York.
We spoke to Sarah about her latest collection, how the Form 1+ 3D printer has changed her design process, and the future of desktop 3D printing for the fine jewelry industry.
How did Oak Leaf come about?
I grew up in central California with an enormous Oak Tree in our front yard. I have such fond memories of long, hot, summers playing in the shade of this tree, and the beautiful shape of the leaves is permanently imprinted in my mind. I was recently leafing through an Andrew Goldsworthy book and one of his designs using leaves and stones and water caught my eye and reminded me of another childhood memory - the rains. My father was a farmer, and waiting for the rains was always a topic of conversation. When they finally came, everyone was in a good mood, and I will always associate the memory of wet oakleaves plastered over the rocks and on the pavement as I walked to school with happy times.
What was the process like? Can you tell us more about the details of your pieces?
The challenge was to capture two important aspects of my memories in the metal - the wetness of the leaves, and the wrapping effect. This meant playing with lots of textures and making lots of adjustments to the position of the leaves as they wrapped around the stone. I printed my ideas every day for three weeks until I got the effect I was going for.
How long have you used the Form 1+? What was your experience like?
I started using a Form 1+ in November 2014, and the first thing I printed was a fingerprint ring. I felt confident the printer would be really helpful in allowing me to do lots of ‘practice prints’ that let me see what I am designing in CAD in general, but that I would still need to send my final files to a service bureau for high resolution printing. I started with a fingerprint ring though, just to see what it could do. I was shocked when it finished - the detail (and you need a LOT of detail to print a fingerprint!) was just as good as what I had been getting from my service bureau, which uses very expensive 3d printers.
Do you think high-resolution 3D printing will change the workflow process of jewelry design?
It certainly has changed mine. I play and tweak and experiment with new design ideas way more than I did when I had to pay for each print. It is also broadening my horizons in a bigger sense - I have a collection of stacking rings with stones set on top - there are over 100,000 permutations available, and when a customer orders a set of rings, we position the stones so that they nestle nicely together. In effect, each ring is a one of a kind, and requires us to solder on each stone individually. But with an inexpensive desktop printer, it should now be possible for us to add the bezels to the shank in CAD and print the complete ring with the bezels attached. This could save us a lot of time and money and would transform how I manufacture the best selling item in my inventory. I see this printer greatly reducing, if not eventually eliminating, the need for making molds and shooting waxes.