Mapping the Mind: How OpenBCI Turns Brainwaves Into Physical Reality With 3D Printing

Ten years ago, as Formlabs founders were getting excited to release the Form 1+, there was another founder who was also visualizing a tool that could take ideas and turn them into physical reality.
Conor Russomanno wanted to find a way to map the mind, to turn brain power into our common modern language — computer code. But mapping a world that hasn’t been fully explored, let alone categorized and codified, required years of intensive testing, research, and collaboration.
OpenBCI recently announced that their commercially shippable product, Galea, was ready. The OpenBCI team has leveraged an incredible network of open-source collaborators for software development to reach that milestone. But to stay apace with their software development the team had to find the right hardware solution. The Form 3 and Form 3L stereolithography (SLA) printers have helped them map the mind and create the Galea headset that can turn that brainwaves into action. The possibilities for Galea are nearly limitless — OpenBCI is already working with innovators across every industry, from biomedical research to consumer goods manufacturing, and beyond.
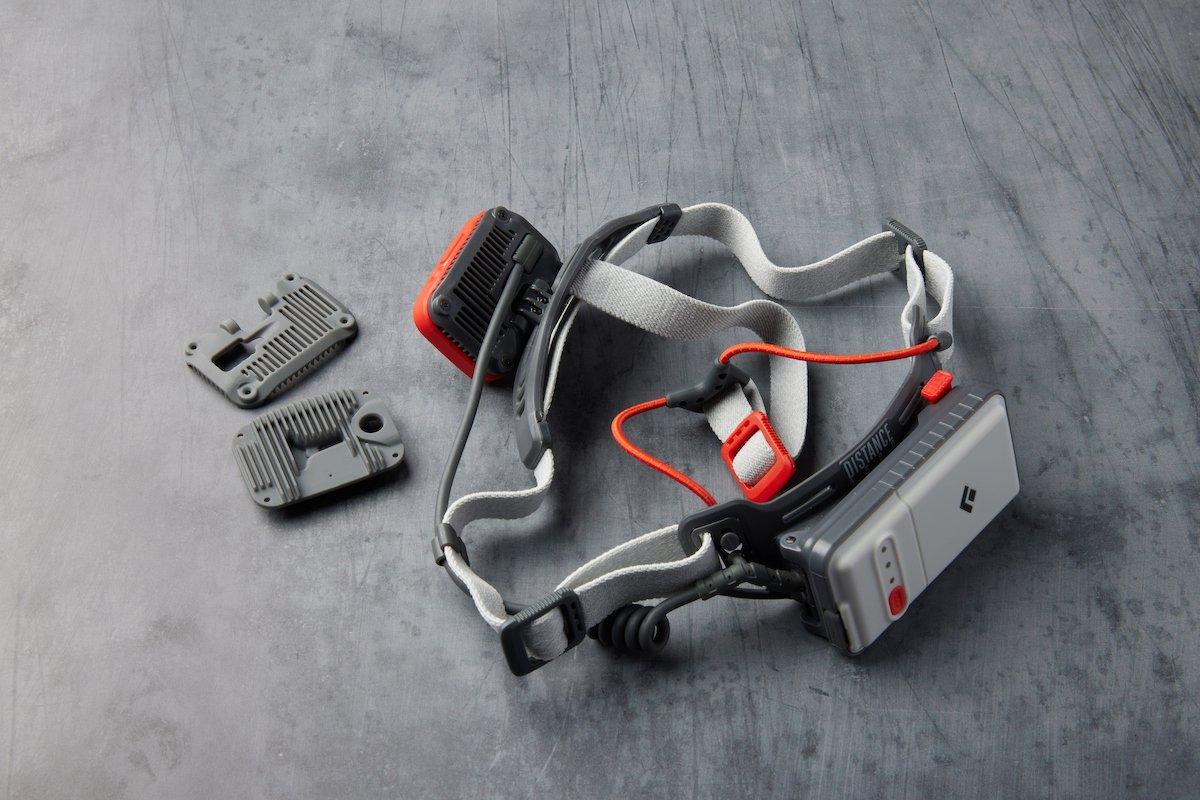
Guide to Rapid Prototyping for Product Development
In this guide, you’ll learn how rapid prototyping fits into the product development process, its applications, and what rapid prototyping tools are available to today’s product development teams.
Building a Tool With Purpose
For years, even the most advanced medical researchers have used some form of EEG sensors wired together into a helmet-like shape to gather data from the brain. But there were no tools built to look at the system holistically and put brainwaves in the context of the body.
Russomano and the OpenBCI team started experimenting with ways to measure electrical waves from the brain alongside using biosensing amplifiers that could take inputs from heart rate, skin temperature, eye movements, and so much more. “By combining a multi-modal sensor system with the immersion of augmented and virtual reality, Galea gives researchers, developers, and creators a powerful new tool for understanding and augmenting the human mind and body,” says Russomano.
Precursors to Galea were the Ultracortex and Cyton, two biosensing products used in countries and communities all over the world that needed access to this kind of information. OpenBCI’s mission has always included an open-source component so that shared information, free guidance, and constant collaboration could push innovation forward.
Collaboration for TED: Christian Bayerlein’s Contribution
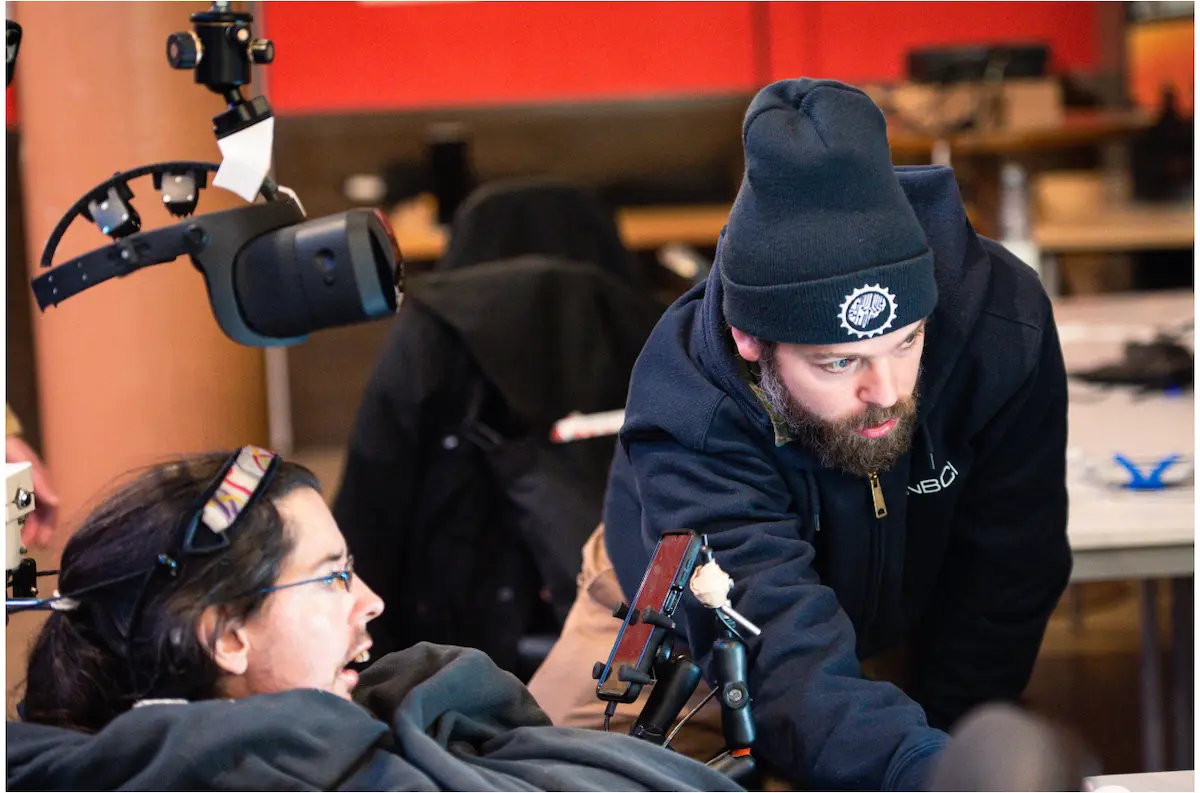
Christian Bayerlein and Conor Russomanno working on NeuroFly (photo: Björn Lubetzki)
One result of that collaboration is a partnership between OpenBCI and Christian Bayerlein, a German technologist and disabled rights activist, who worked together to demonstrate something truly remarkable at the TED2023 conference.
Using Open BCI’s NeuroFly technology and an earlier version of the Galea hardware, Bayerlein flew a drone using a ‘digital joystick’ that gathered data from residual muscle activity throughout Bayerlein’s body and translated it into electrical commands to the drone.
Bayerlein, who is living with spinal muscular atrophy (SMA), a genetic disease that affects the motor neurons controlling voluntary movement, said, “I see it as a way to experience a sense of freedom and independence that is often limited by my disability. I’ve always been fascinated by aviation and the feeling of soaring through the air, and being able to pilot a drone using my brain signals was an incredible experience that I will never forget.”
Human-Scale Hardware Development Poses Difficulties
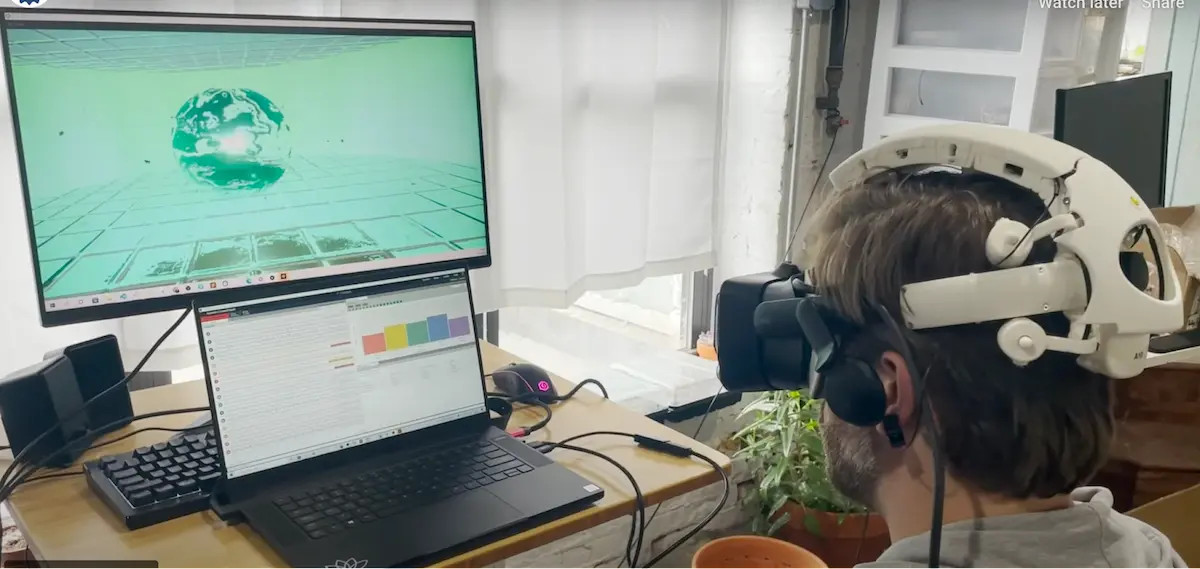
There are applications for OpenBCI’s technology across all industries; Galea can be used in almost any interaction between us and the digital world — a nearly constant relationship in today’s society.
Though data analysis and so many other integral parts of the Galea interface could be worked on through open-source software from people all over the world, the Galea interface is, at its core, an effort to combine the virtual and physical worlds. So Blake Larkin, OpenBCI’s Mechanical Engineer, had to find a tool that could create a new type of product, one that would be iterated daily and accurate enough to record even the smallest shift in electrical information, all while being used on subjects of varied shapes and sizes.
After joining OpenBCI in 2022, Larkin added Formlabs printers as they advanced through their own iterations — first the Form 3, then Form 3+, and now both desktop and benchtop SLA with the Form 3L, Wash L, and Cure L. “The printers have been great. The phrase, 'just print it'— it’s not just something people say,” Larkin said.
The quality of OpenBCI’s data, and thus the whole interface, is dependent on how well the biosensors can measure the brain and body outputs. Each tester headset has to be adjusted for the unique anatomy of the test subject, iterated constantly to reach a design that could be adjustable for different head shapes, and consistently measure multiple inputs without interruption or interference.
“When you’re trying to create something that works with all types of people, you have to really fine tune everything, which is when 3D printing shows its biggest benefit — the ability to change millimeters — everyone’s different in different ways,” says Larkin.
The Form 3L has allowed them to prototype on a human scale, and increase their iterative speed even with larger prints. “We need many of the components to be one piece, like the face mask. On the Form 3L you have more control over your print orientation for large parts,” says Larkin.
Because these parts will be used in early production runs of the Galea, superior surface finish is important, and layer lines, support marks or other visual imperfections cannot be part of the final part. The large build volume of the Form 3L means that Larkin can optimize the part layout to achieve the smoothest possible surface finish and avoid extra post-processing. “The Form 3L saves a lot of time, the post-processing is streamlined, and we can get cosmetically perfect parts. With what we’re using, I don’t think anyone would be able to tell the final parts are 3D printed.”
Material Scope Provides Confidence for Manufacturing
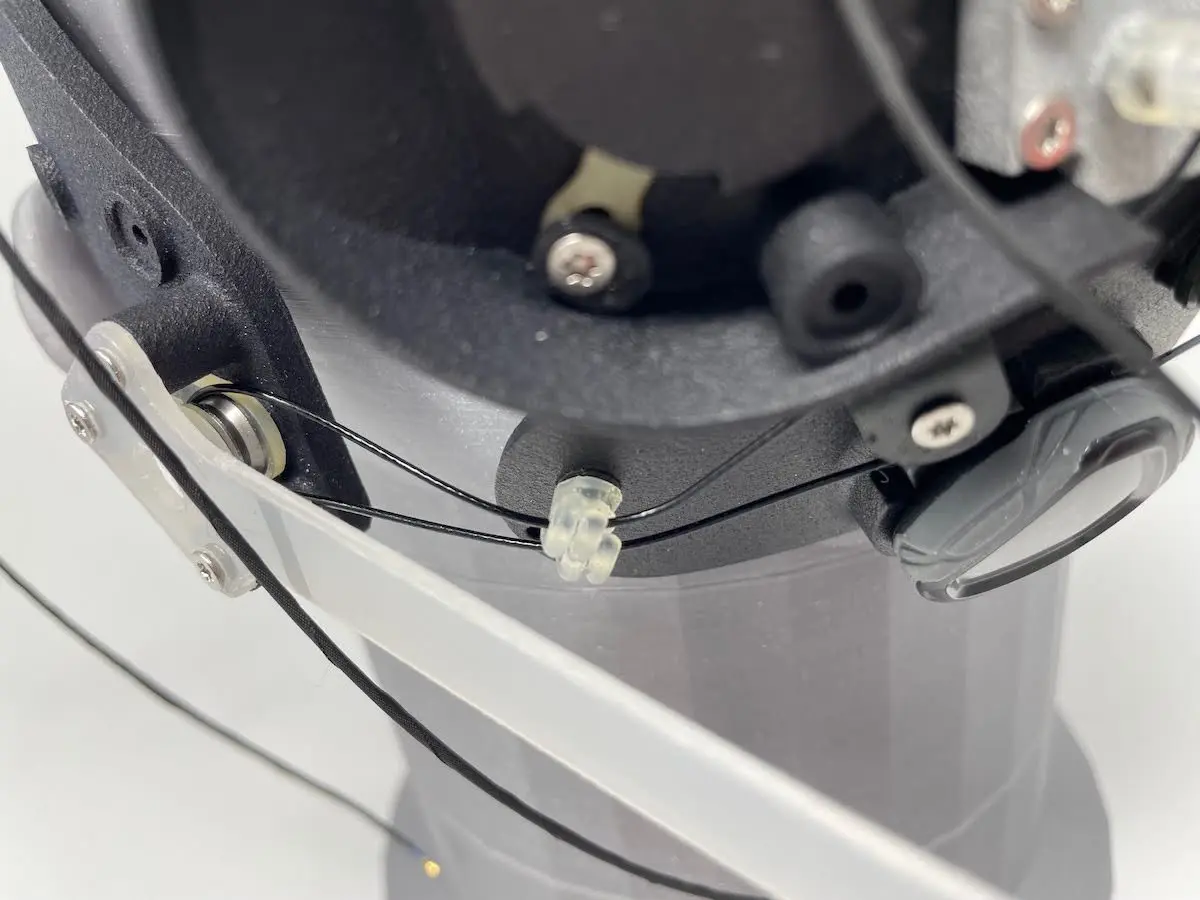
Larkun uses Durable Resin for high-friction components that need to let wires and cables slide through them repeatedly. These components have intricate internal geometries that prevent the wires and cables from coming undone.
The Galea headset is made up of several components with different purposes, such as cushioning, securing the headset to the head, or functioning as a frame for the sensors. These components all have to assemble together smoothly, and many have to be adjustable, with various levels of stiffness, flexibility, or strength needed. Larkin had to try multiple materials, sometimes switching between projects and resins daily.
The extensive Formlabs material catalog and the Form 3 Series platform made it possible to try new processes and resins. “We don’t have to compromise on the material properties themselves. Tough 1500 Resin, Tough 2000 Resin, Clear Resin, Durable Resin, Flexible 80A Resin, they’re all being used. With SLA, you can pick different material properties, that’s important,” Larkin says.
Using Durable Resin has helped them develop the headset’s belt component, and allowed Larkin to iterate quickly and avoid a complicated multi-step process.
“If I couldn’t 3D print this belt, I’d have to combine different ways of fabricating it — buying flat sheet plastic, cutting it, attaching, and testing. If we went into production, I’d have lower confidence that it would match the finished material perfectly. Something cool about Formlabs is that you can get closer to the manufacturing workflow, so you have more confidence in the testing stages.”
Blake Larkin, Mechanical Engineer
3D Printed Rapid Tooling for Foam Molds
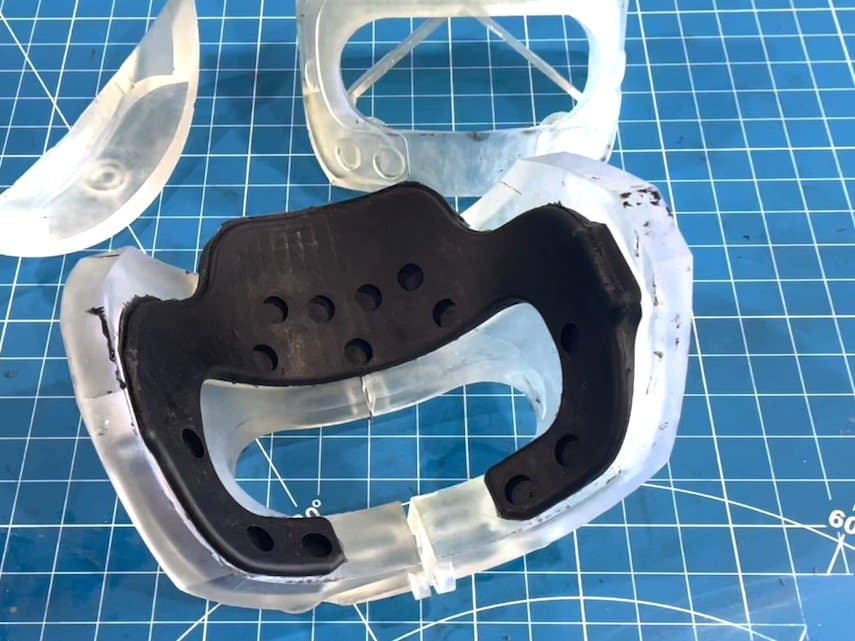
The Clear Resin mold allows Larking to monitor the injection of the green silicone material and ensure that it’s spreading evenly throughout the mold during pressurization.
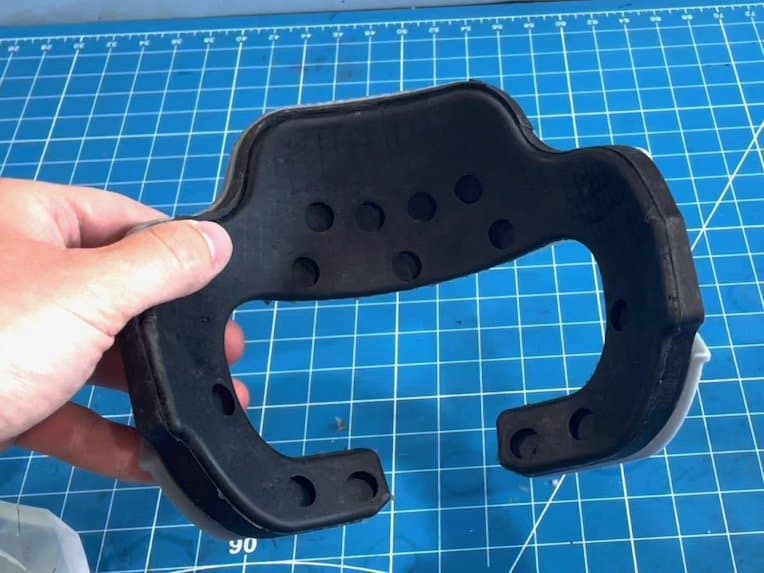
3D printing rapid tooling can improve iterative timelines as well as provide solutions for low-volume end-use production.
For one cushioning component on the headset, the team wanted to try out different kinds of foam material. Typically inexpensive and widely available, ordering foam is easy — unless you’re not sure which kind will work best for your application. Before locking themselves into a single manufacturer or foam type, the team designed their own tooling using the Form 3L and Clear Resin. Larkin printed a two-part mold and then injected green 30A Shore durometer silicone to create a master before finishing with silicone foam. Being careful of support connection points and vent holes, Larkin was able to create 1 mm diameter vent holes that were quite long. “It would be basically impossible on an FDM printer, and Clear Resin is helpful because you can get a better understanding of where vents, supports, and curves are,” says Larkin.
Being able to 3D print tooling for other materials and keep the entire workflow in-house helps keep the team focused on the headset design, without getting bogged down in the logistics of vendors, quoting, lead times, and logistics.
“It’s great because you can change not only the shape of the part but when you combine 3D printing with other workflows, you can create versatile geometries with a range of material properties. With in-house 3D printing I gain two months. I can print infinite molds theoretically, then make the decision to keep that workflow or outsource for higher volumes,” says Larkin.
The design flexibility and supply chain protection that comes with in-house 3D printing means that OpenBCI can continue their supercharged development schedule, even if a global pandemic, raw materials shortages, or logistics breakdowns would threaten another company. With their open-source software development community working constantly across the world, their hardware development had to keep pace and avoid being the bottleneck. With in-house 3D printing, they could make anything they needed on hand, keeping laser-focused on the product and not the fabrication process.
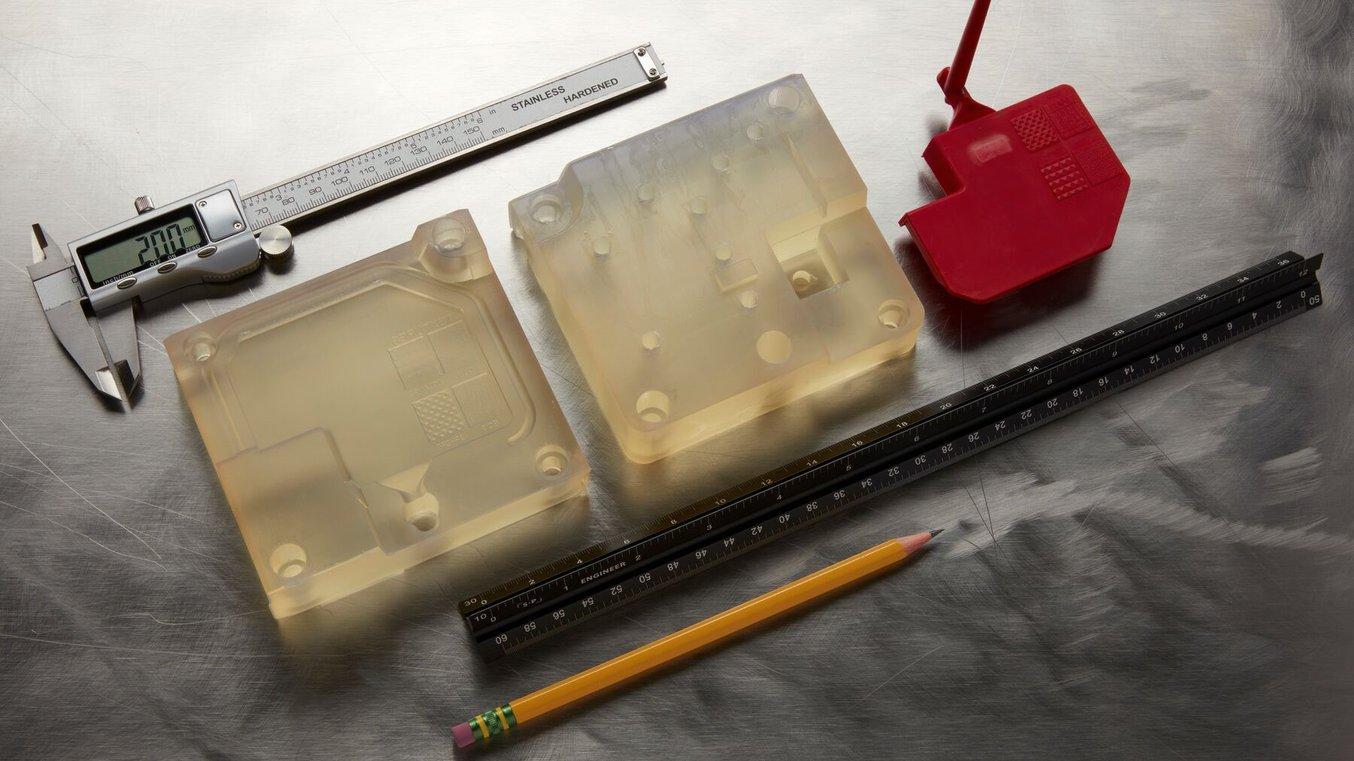
Leverage 3D Printing at Every Stage of Product Development
Discover how 3D printing reduces time and costs at every stage of the product development process - from ideation to manufacturing and beyond.
Durable Resin Belt Guides
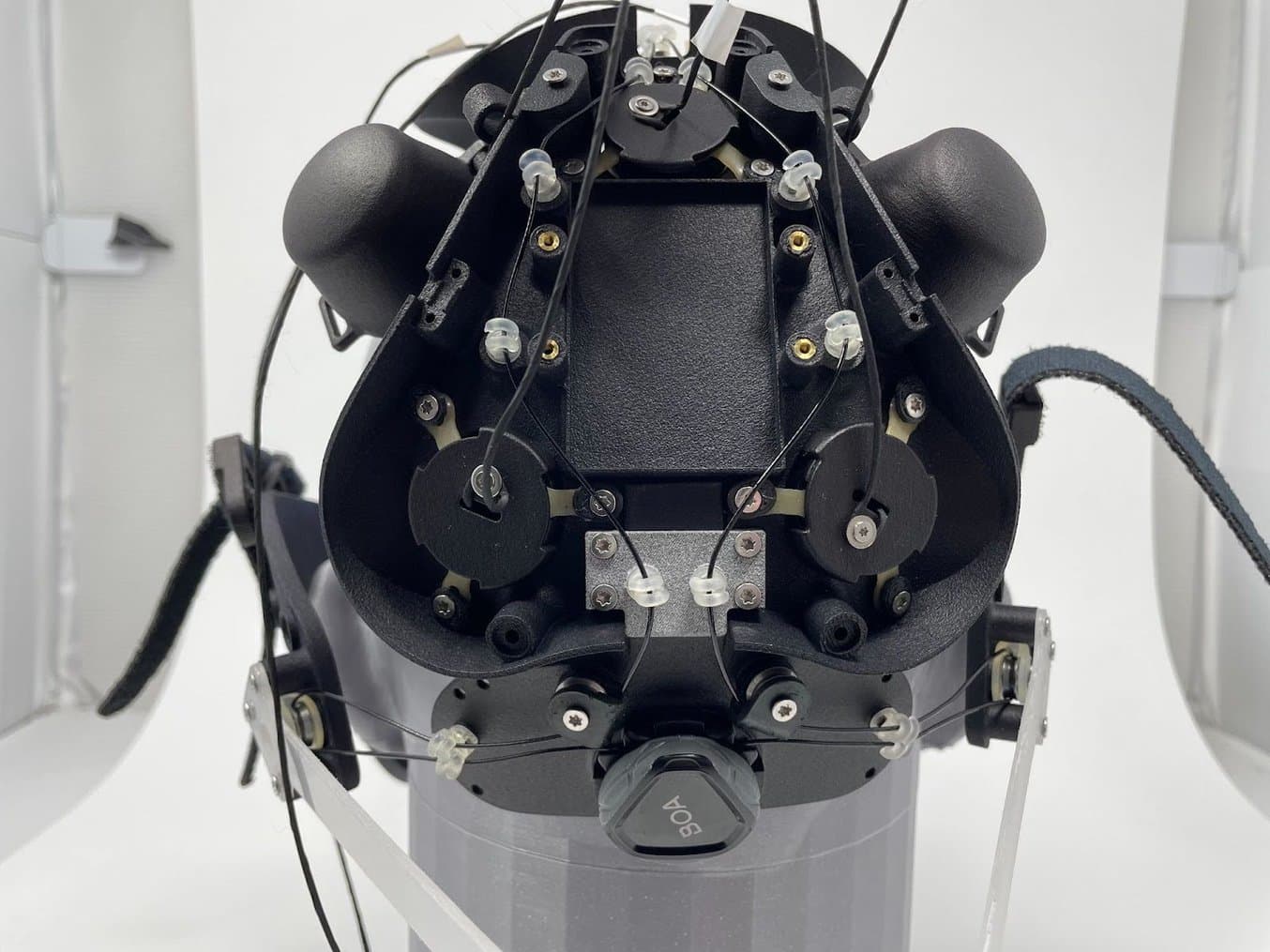
3D printing enables complex geometries like internal channels that keep wires secure without completely restricting movement.
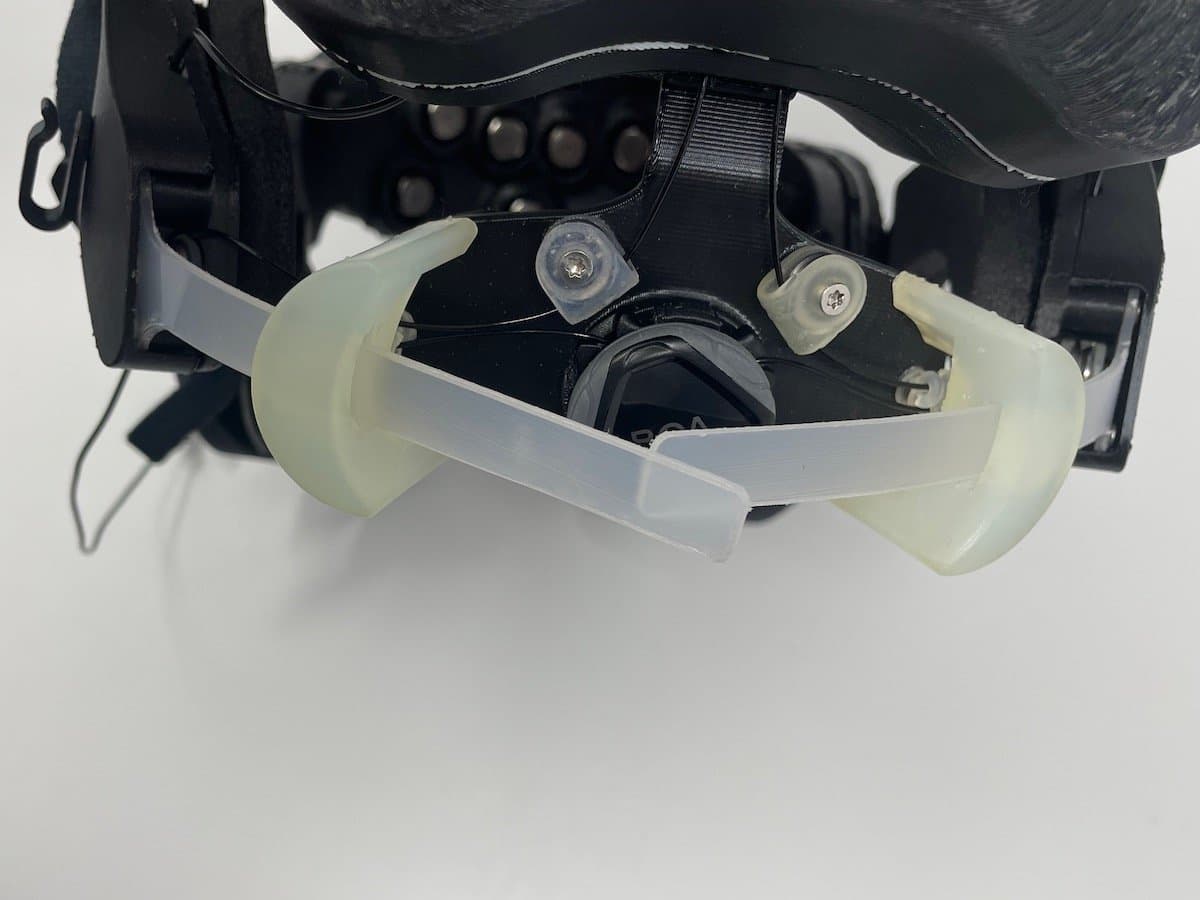
For components with high friction, like this belt guide, Durable Resin is a perfect choice: it allows the belt to glide smoothly back and forth without catching or snagging on the internal channel.
Combining traditionally manufactured parts with 3D printed parts isn’t always easy, but the range of mechanical properties available to Larkin and the team meant that they could find a resin that interacted smoothly with a belt that would eventually be made through a CNC or waterjet cutting process. The belt helps adjust the size and fit of the headset but needs a sort of guiding fixture to keep it in place. The guide has internal features, an internal channel shaped like an hourglass to make sure the belt can’t move accidentally. Traditional manufacturing for the guide would be almost impossible. “We wouldn’t have been able to make it out of one part with traditional manufacturing — an internal channel with a weird shape it would have to be made in two parts. That’s another thing we’d have to rethink,” says Larkin.
3D printing offers a way to manufacture these guides in one piece, and Durable Resin provides the right amount of ‘slide’ for the belt to move back and forth when necessary. “We don't have to worry so much about how we’re going to be making it. We can really focus on the design. Anything that has a moving surface, we do in Durable Resin,” says Larkin.
Skin Safe Tough 1500 Resin for Ear Clips
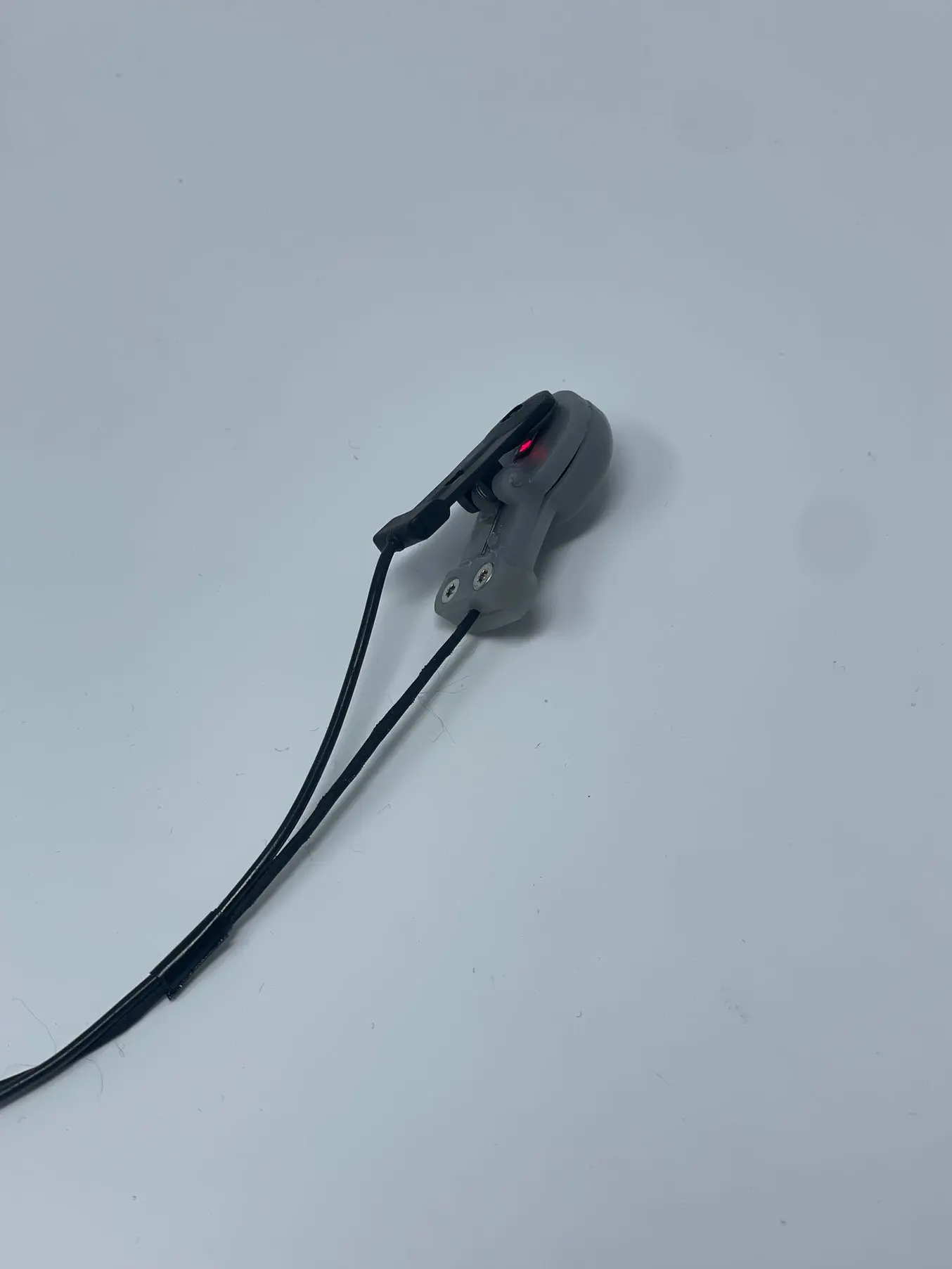
Tough 1500 Resin is certified as skin-safe for applications like wearables, including this ear clip that takes biometric data from the wearer's earlobe.
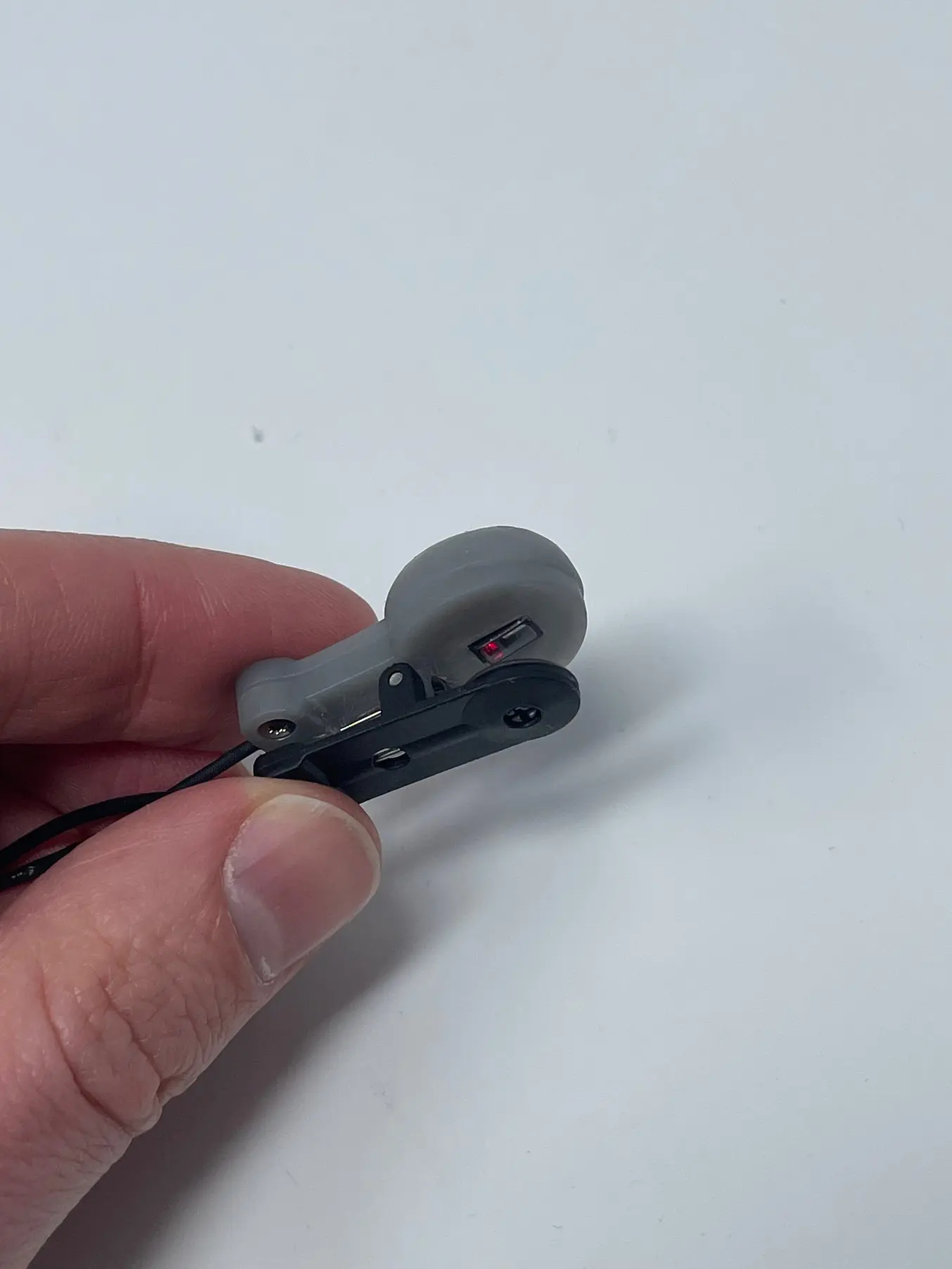
These parts need to have high dimensional accuracy in order to mate with existing biometric measurement components and function as a multi-piece electrical assembly.
Tough 1500 Resin’s skin-safe certification opens up opportunities for the team to create end-use components that interface directly with users’ skin. An ear clip component that measures the heart rate taken at your ear lobe has a tiny infrared sensor, an off-the-shelf component that Larkin modified to add a grounding feature. He took off the back half and printed a new mating component to ground the device. “Material variability is very helpful. Once you have a machine, the cost to try a new material is negligible compared to retooling something, so we tried out Tough 1500 because it’s skin-safe,” says Larkin.
Production Volume and Galea’s Future
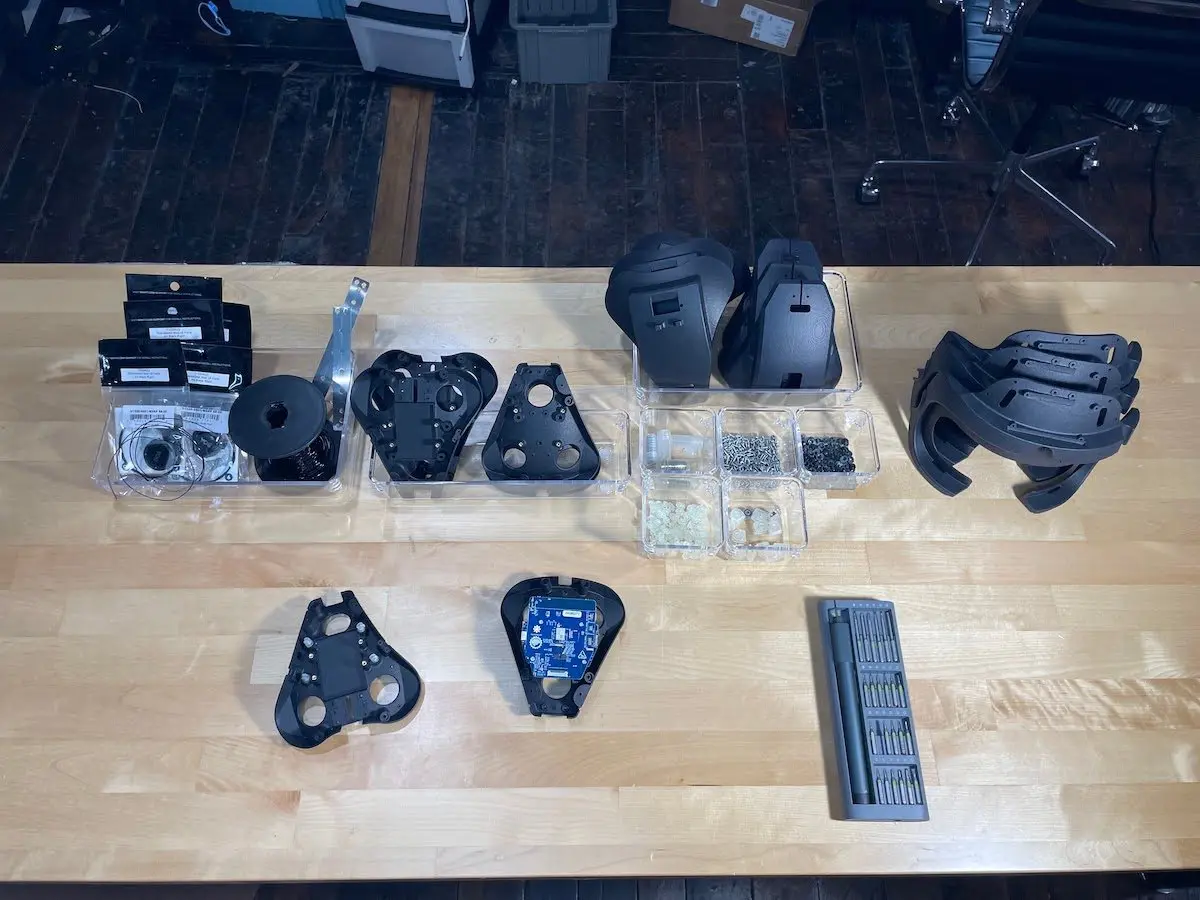
Larkin prints multiple components at low to mid-volume for production on the Form 3+ and Form 3L utilizing multiple resins, including Tough 1500 Resin for skin-safe parts and Durable Resin for high-friction components.
Russomamno premiered Galea at Slush, a conference held annually in Helsinki, Finland. The first production run of Galea headsets, will have multiple 3D printed components, so that OpenBCI can stay responsive and change their design after having more feedback, without sinking resources into expensive tooling.
With the Form 3+ and Form 3L, Larkin and the OpenBCI hardware team can make tiny adjustments that lead to big improvements in capturing and analyzing high-quality data. 3D printing allows the team to focus on the design of the components and their function, not the ease with which they could be molded, or the quantities they should be predicting for.
“It’s part of our strategy. We don't have to say, ‘Now we have the design, let’s spend three months making it again for injection molding,’” says Larkin. “We can fully focus on the design and testing it.”
Forecasting demand and calculating the costs of tooling can be obstacles to innovation. 3D printing and open-source software have enabled OpenBCI to move past those obstacles and focus on the design of a potentially life-changing device. Their unique development and production model will help fast-track production, and get Galea into the hands of collaborative users who can continue improving the product.