Formlabs' Form 4 resin 3D printer and its biocompatible version, Form 4B, are powered by our next-generation Low Force Display™ (LFD) Print Engine that turns liquid resin into printed parts.
LFD Print Engine features six advanced subsystems to set the new standard for blazing fast speed, unmatched reliability, stunning print quality, and performance materials.
What Is Low Force Display™ Technology?
Form 4 is powered by our next-generation Low Force Display™ (LFD) Print Engine. LFD redefines the industry performance standard and delivers unmatched reliability, print speed, print quality, dimensional accuracy, and materials versatility in one printer.
LFD is built on Formlabs’ previous Low Force Stereolithography™ (LFS) Print Engine. Since 2011, over 50,000 companies have relied upon more than 130,000 Formlabs 3D printers to produce over 400 million performance parts.
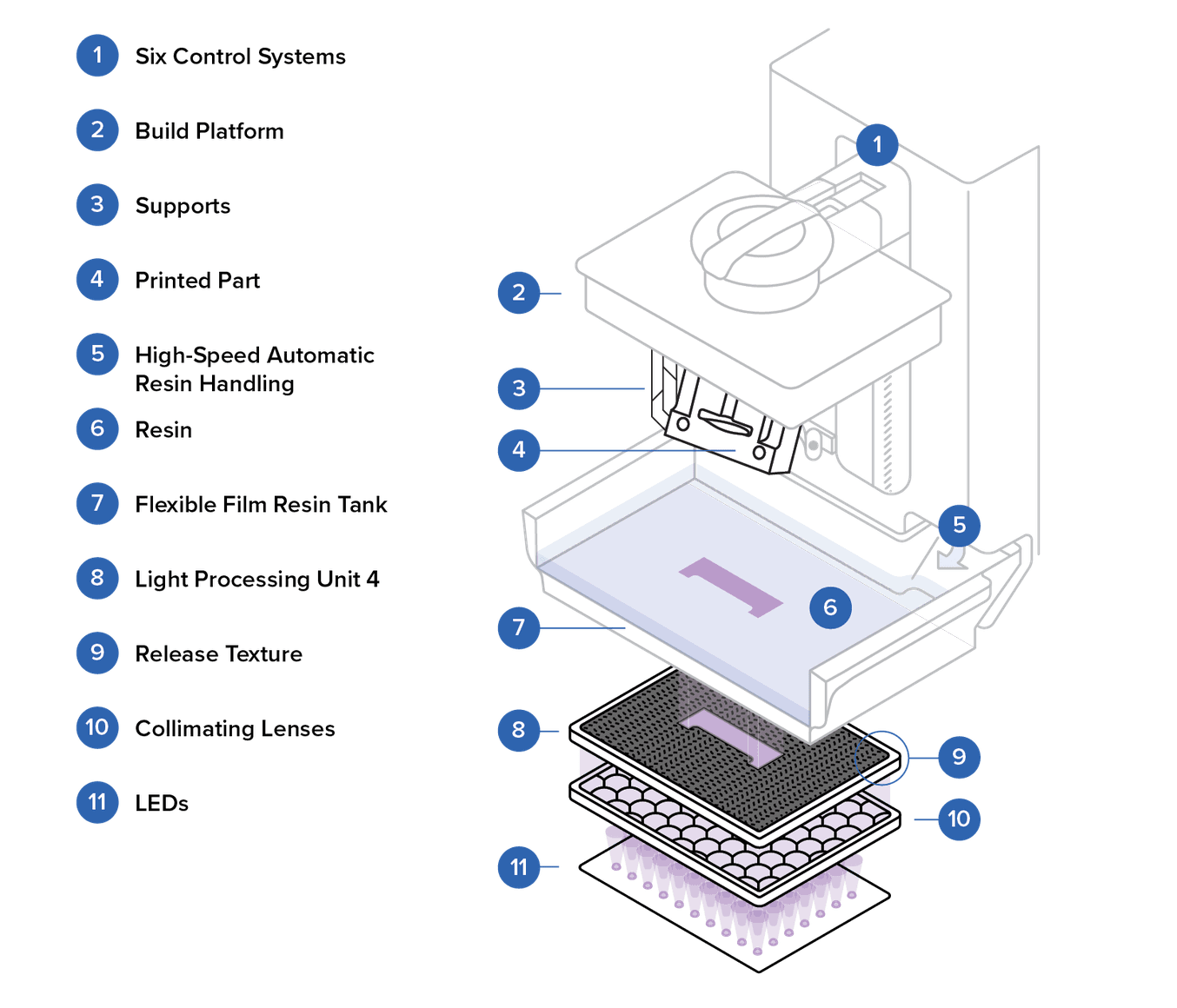
SLA was patented by scientist Chuck Hull in 1984 as the world’s first commercial 3D printing technology, and opened the door to professional-quality rapid prototyping, revolutionizing the design process for companies like Apple, Boeing, and Ford. However, its reach was limited to the likes of Fortune 500 companies due to printer cost, size, complexity, and material limitations.
Formlabs brought SLA printing to the desktop for the first time in 2011, with the Form 1, empowering a whole new community of engineers and designers with professional tools for in-house prototyping and production.
In 2015, Form 2 introduced new advancements to desktop SLA printing and professionals, including automated resin dispensing, hassle-free materials switching, 40% larger build volume, touch-screen controls, Wi-Fi connectivity, reliability, and a wider range of performance materials.
In 2019, Form 3 and Form 3B (for biocompatible 3D printing) were released, powered by LFS. LFS is a form of stereolithography that leverages a flexible tank and linear illumination to revolutionize print quality and printer reliability, enabling smoother surface finishes and light-touch supports thanks to lower peel forces.
Recently, many manufacturers have switched from laser-based SLA to DLP or LCD as these optical systems have led to substantial improvements in print speed, but often at the cost of surface finish, reliability, resolution, or hardware longevity. Form 4's LFD Print Engine was developed to address these challenges and deliver the speed, reliability, and part quality that professionals need, all in a single printer. LFD introduces several new advanced subsystems including a backlight unit, light processing unit, release texture, and integrated camera, and significant improvements with updates to the flexible film tank, resin cartridge, automatic resin handling, and intelligent control systems.
Form 4 | Form 3/B/+ | |
---|---|---|
Technology | Masked Stereolithography (MSLA) | Stereolithography (SLA) |
Printer engine | Low Force Display™ (LFD) | Low Force Stereolithography™ (LFS) |
Key components of the print engine | Backlight Unit Light Processing Unit 4 (LPU 4) Release Texture Redesigned Flexible Film Resin Tank Intelligent Control Systems High-Speed Automatic Resin Handling | Laser Light Processing Unit (LPU) Flexible Film Resin Tank Automatic Resin Handling |
Light source | Backlight Unit (LEDs) and collimating lenses | Laser |
Light processing unit | LCD and Release Texture | Galvanometer, mirrors, spatial filter |
Build volume | 20.0 x 12.5 x 21.0* cm 7.9 x 4.9 x8.3* in 5.25 liters | 14.5 × 14.5 × 19.3* cm 5.7 x 5.7 x 7.6 in 4.05 liters |
* If you are printing a job that is taller than 19.0 cm (7.5 in) on Form 4/B, or taller than 18.5 cm on Form 3/B/+, you have to remove the resin tank while removing your print. PreForm will warn users when their job is above 19.0 cm on Form 4/B or over 18.5 cm on Form 3/B/+.
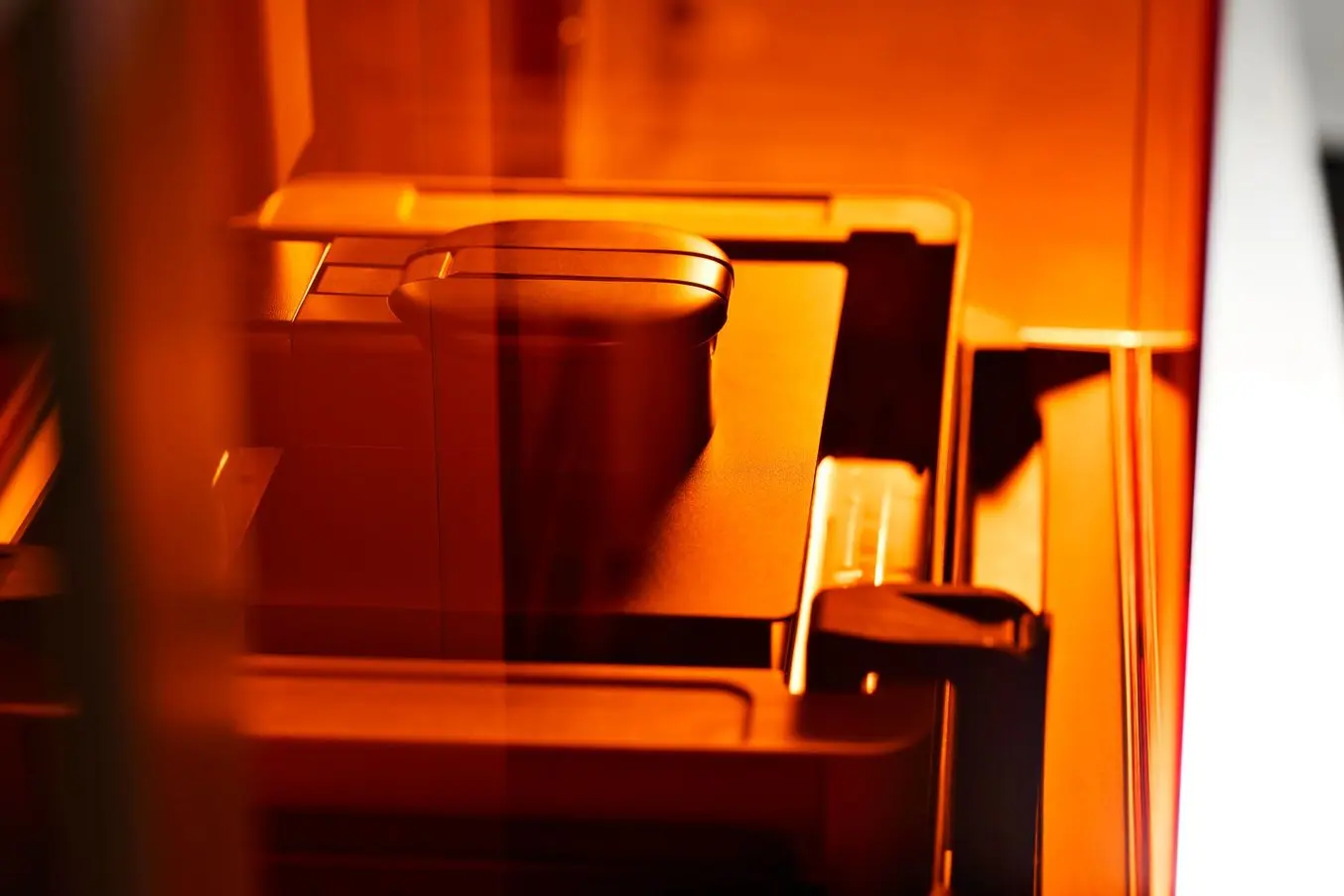
Product Demo: Form 4
See how Form 4 can enable new levels of productivity and innovation through its unmatched speed, accuracy, and reliability.
How Does LFD Work?
At the core of the LFD print engine is the Backlight Unit. This ultra-high power light source uses 60 LEDs, integrated cooling, and collimating lenses, with industry-leading optical power intensity of 16 mw/cm2, to deliver blazing fast print speeds with excellent print quality and accuracy anywhere on the Build Platform.
The Backlight Unit emits a uniform area projection of light, which passes through the lens array, making the light more collimated, or parallel, and more uniform, eliminating dark or bright spots. The custom lens array is made of plano-convex lenses for highly collimated and uniform light even at high power.
From here, the light passes through the Light Processing Unit (LPU) 4, where it is formed into the shape of the printed layer using a series of polarizers, optical coatings, and a custom liquid crystal display. The 50 μm pixel size of the high-resolution LCD and pre-tuned anti-aliasing delivers sharp details, smooth surface finishes, and accurate tolerances. The custom LCD also features high light transmission, delivering maximum optical power to the resin and achieving blazing fast print speed.
Unlike existing LCD-based printers, the LPU 4 is long-lasting, engineered and manufactured to deliver 600,000 - 1,900,000 layers of consistent print performance before replacement, depending on the material and layer height printed. It is also robust to accidental damage, featuring a strong metal frame, scratch-resistant surface coating, and smart software (debris detection and force limits). When replacement is necessary, anyone can easily and quickly replace the LPU 4 at a low cost.
Once the light reaches the liquid resin inside the resin tank, the full liquid layer immediately cures into a solid layer. The Build Platform then rises out of the resin and a precision Z-axis peels away the layer from the bottom of the resin tank.
In the past, peel forces have been a major hurdle for resin 3D printing, forcing users to sacrifice either part quality, reliability, or printing speed when selecting a printer. With Form 4, peel forces are minimized using a new Release Texture and redesigned Flexible Film Resin Tank.
The Release Texture is a proprietary, microtextured optical film that introduces airflow to prevent the resin tank from suctioning to the LPU.
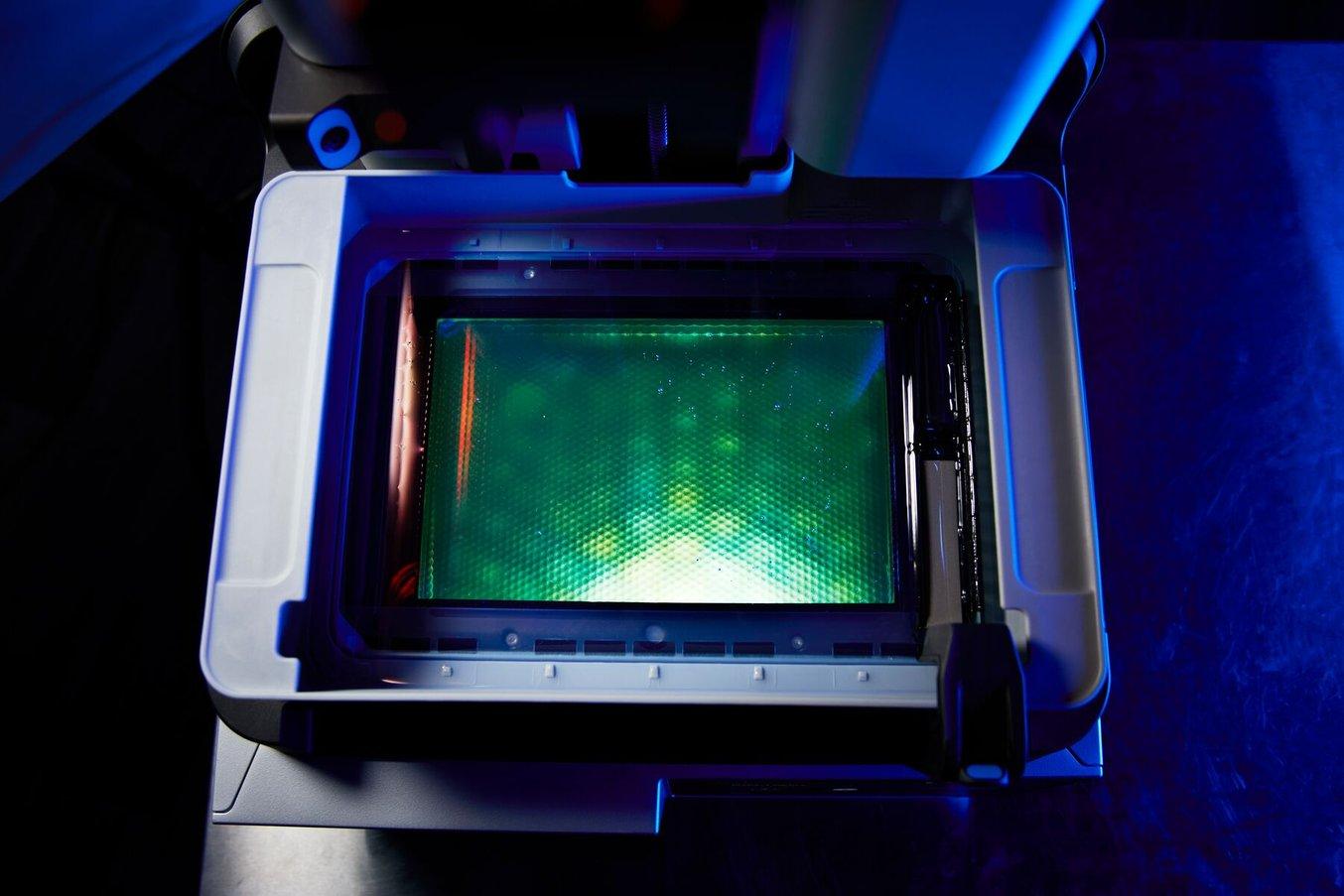
Form 4's custom lens array is made of plano-convex lenses for highly collimated and uniform light even at high power.
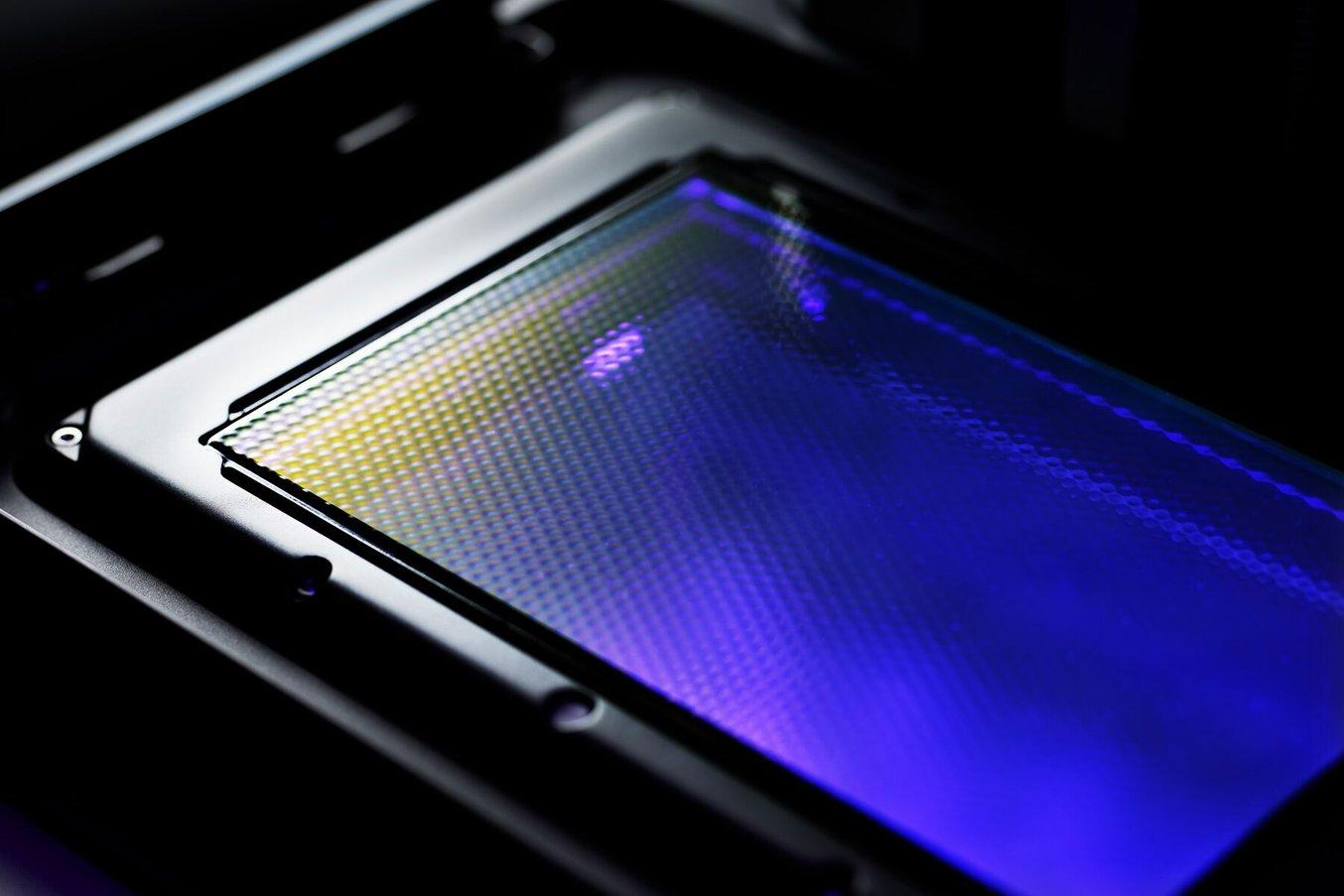
The proprietary Release Texture prevents the resin tank from suctioning to the LPU by introducing airflow.
The new Flexible Film Resin Tank is a long-lasting consumable that holds resin inside the printer and provides a surface for liquid resin to cure against. It features a dual-layer, flexible film that gently separates from the edges of a cured layer, reducing peel forces exerted on the layer.
Together, the Release Texture and Flexible Film Tank significantly reduce forces exerted on a print. As a result, Form 4 can rapidly and reliably produce smooth, detailed parts with light touch supports that rival injection molding, with extreme print speed and reliability.
Upgraded Automated Resin Handling and New Materials
Gone are the days of waiting for resin to heat before printing commences. Form 4 features conduction resin heaters and an infrared temperature sensor, enabling faster heating times and minimal time to start a print. The heater and infrared sensor precisely control resin temperature and unlock higher-viscosity materials.
The dual-layer Flexible Film Resin Tank is designed for a long lifetime, minimizing upkeep costs and waste. It features a top film that is chemically inert and flexible, and a bottom film that is hard and durable to prevent scratches and punctures. Resin tanks are easy to use, with simple latches for printer installation, an easy-pour spout, and an oversized volume (2.3 L when not printing) to protect against accidental spills.
Every resin tank includes a reusable lid and stackable design, making it easy to stack tanks and store resin outside of the machine. With a separate tank for each individual resin color or type, switching materials is as easy as sliding in a new tank.
Resin Tanks are built to last and deliver consistent performance for their entire lifetime. Each resin tank is designed to deliver consistent performance for over 75,000 layers using any Formlabs resin. The Flexible Film Resin Tank also has a 33% lower price than earlier models, making it easier than ever to try out new materials and lower operating expenses.
The high-speed Resin Mixer easily latches to the resin tank and quickly remixes your resin into a homogenous liquid, with near zero impact to print times. This helps ensure excellent print quality and accuracy for any-sized parts, printed anywhere on the build platform. The resin mixer is removable and can be easily reused across resin tanks containing the same material. Therefore, only one resin tank mixer is needed for each material printed on Form 4, reducing waste.
The resin handling system automatically dispenses resin into your printer so you don’t have to. The redesigned valve has a higher flow rate for 5-10 times faster filling than Form 3, depending on the viscosity of the material. Form 4 resin cartridges still contain 1 L of resin, but with 63% less plastic and a 30% smaller footprint than Form 3 cartridges, for less waste and more efficient storage. Once installed in the printer, a cartridge load cell weighs how much resin is in the cartridge, giving a clear picture of how much resin remains so it’s easy to plan ahead on resin quantities.
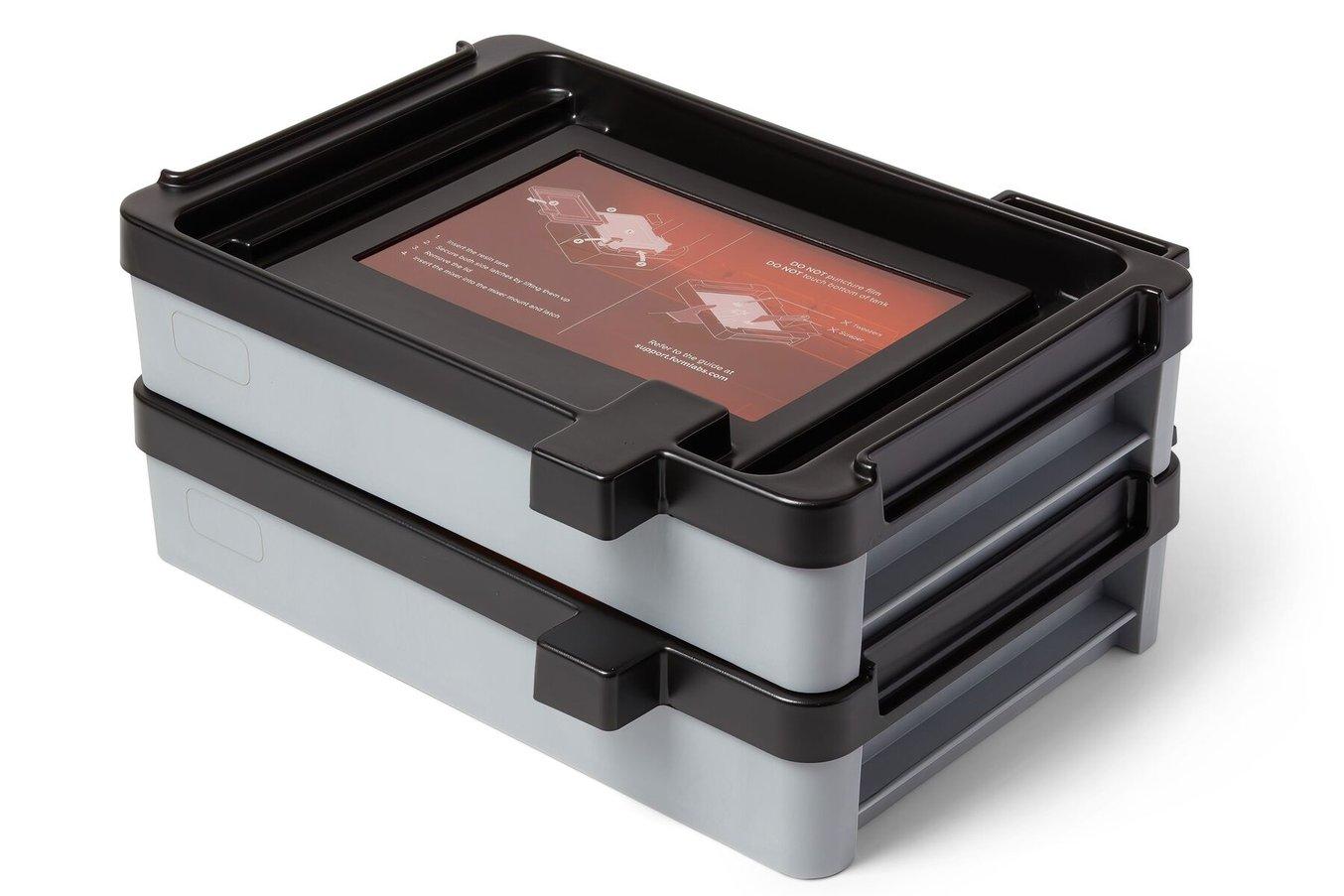
The Form 4 Flexible Film Resin Tank includes a reusable lid that enables stacking for easy storage.
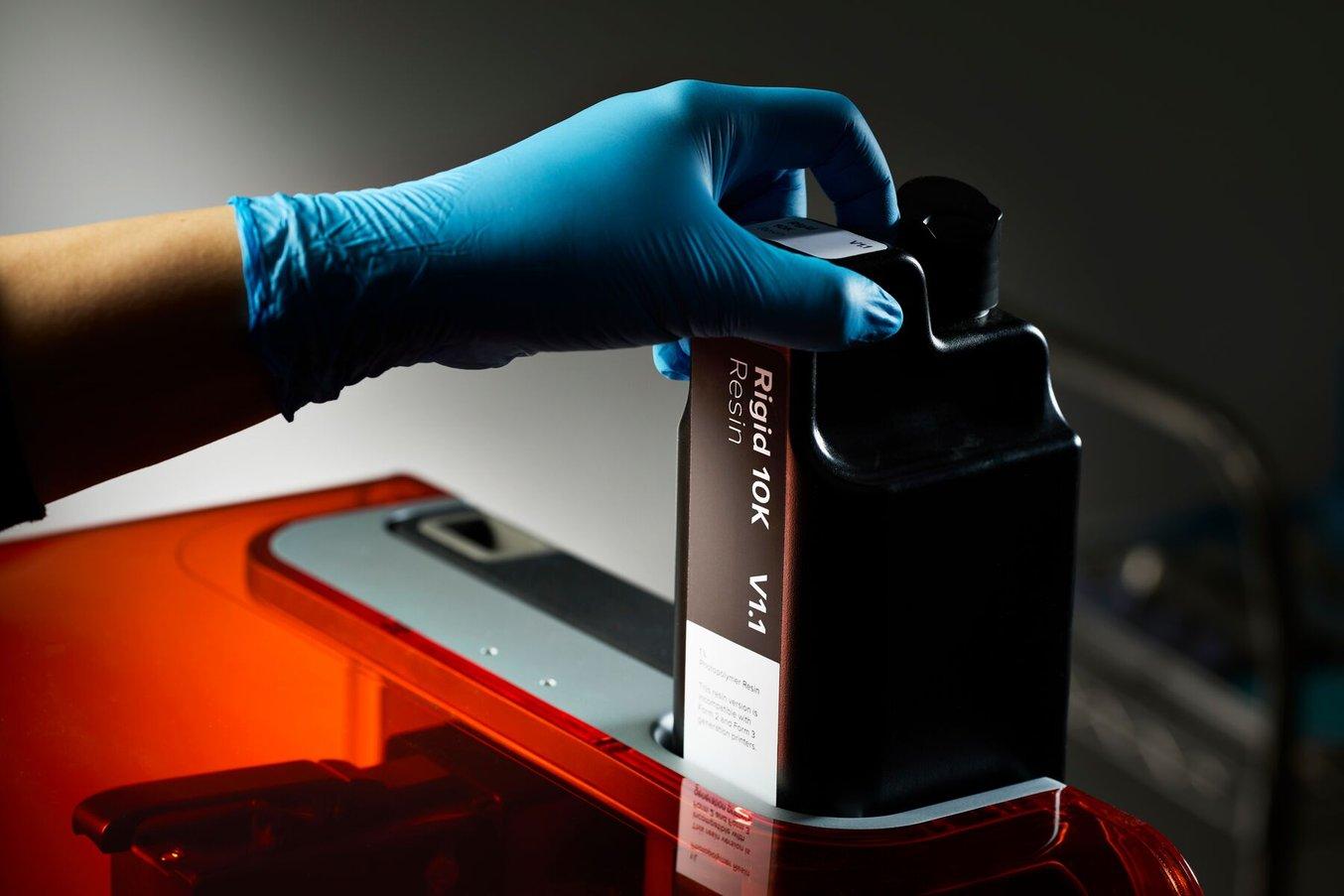
New resin cartridges still contain 1 L of resin, but 63% less plastic and 30% a smaller footprint for less plastic waste and shelf space.
Form 4 is validated to print 23 performance materials from Formlabs’ materials library, including six brand-new resins with improved speed, toughness, accuracy, and appearance:
- General Purpose Resins V5 (Clear, Grey, Black, White) print two to five times faster than Form 3 with improved toughness and color.
- Fast Model Resin, for high-speed prototypes or production of orthodontic models.
- Precision Model Resin, for highly accurate dental models that always fit.
Explore the Formlabs material library to learn more.
Streamlined User Experience
Form 4 builds off the intuitive user experience of Form 3+. With Wi-Fi, ethernet, and USB connectivity, plus power switches, it’s easier than ever to control your printer no matter your business needs. Additional updates mean Form 4 is more autonomous and intelligent, freeing up user time for higher-value tasks.

Form 4's updated UI makes diagnostics and queue management easier on Form 4 — no more post-it notes on printers to establish whose part is printing.
Interact with a more intuitive Touch UI via a seven-inch touchscreen. On-screen preventative maintenance reminders, print status information, and printer readiness information make printing easier and more intuitive than ever before.
Say goodbye to post-it notes on printers with an always-visible printer name and status. After five minutes, a time-out screen will display the name, resin, and printer readiness in larger letters, so you can tell at a glance what the printer is and if it’s ready to go.
Faster preprint times mean you can typically walk away from Form 4 less than a minute after starting. But, if a printer is ready, no printer interaction is necessary, simply send the print to the printer from your computer, and Form 4 will start printing automatically.
On-screen information includes maintenance reminders and diagnostic tools to keep the printer running smoothly. In the event of an issue, error messages display QR codes that lead to support articles to get you back up and running as quickly as possible.
Exciting new features will continue to be added over time through firmware updates, including the release of additional language options.
Intelligent Control Systems and Integrated Camera
Six onboard control systems precisely measure and maintain the temperature, resin level, print forces, and print status inside Form 4. In addition to the cartridge load cell sensor and conduction heating, Form 4 includes a printer leveling sensor, resin level sensor, integrated Z-axis force sensor, and a camera.
Printer Leveling Sensor: When a Form 4 is plugged in and turned on, the touchscreen will automatically walk you through leveling. Simply follow the screen prompts and adjust the legs of the printer with the provided tool. Leveling the printer ensures the Resin Level Sense system can precisely measure the level of liquid resin throughout a Resin Tank, for consistently accurate prints.
Resin Level Sensor: The resin level sensor measures the exact amount of resin in the Resin Tank and controls the automated resin dispensing system, ensuring consistent resin levels and print performance.
Z-Axis Force Sensor: The Z-axis force sensor measures the forces being exerted on every layer during printing and automatically adjusts Z-axis motion to minimize those forces. This delivers optimal speed, quality, and reliability for any part geometry printed in any material.
Camera: A camera inside the build chamber can take a photo or timelapse video of each completed print and upload it into Dashboard, Formlabs’ printer management software, where print status can be viewed from anywhere. This feature makes remote print monitoring and print history traceability easier than ever. For users wishing to opt out of this feature, the camera can easily be turned off, covered, or removed.
Build Platforms
Two different build platforms are available to optimize printing and easy removal of printed parts. A spare build platform can speed up your workflow and allow for nonstop printing.
The Build Platform has a rigid aluminum surface. Build Platform Flex with patented Quick Release Technology has a flexible print surface that allows you to quickly and easily remove parts without tools in seconds. Build Platform Flex eliminates the risk of damaging your part and streamlines your workflow. It is built with a stainless steel print surface ensuring robust, long-term durability. Save material costs and post-processing time by printing parts directly on the Build Platform Flex.
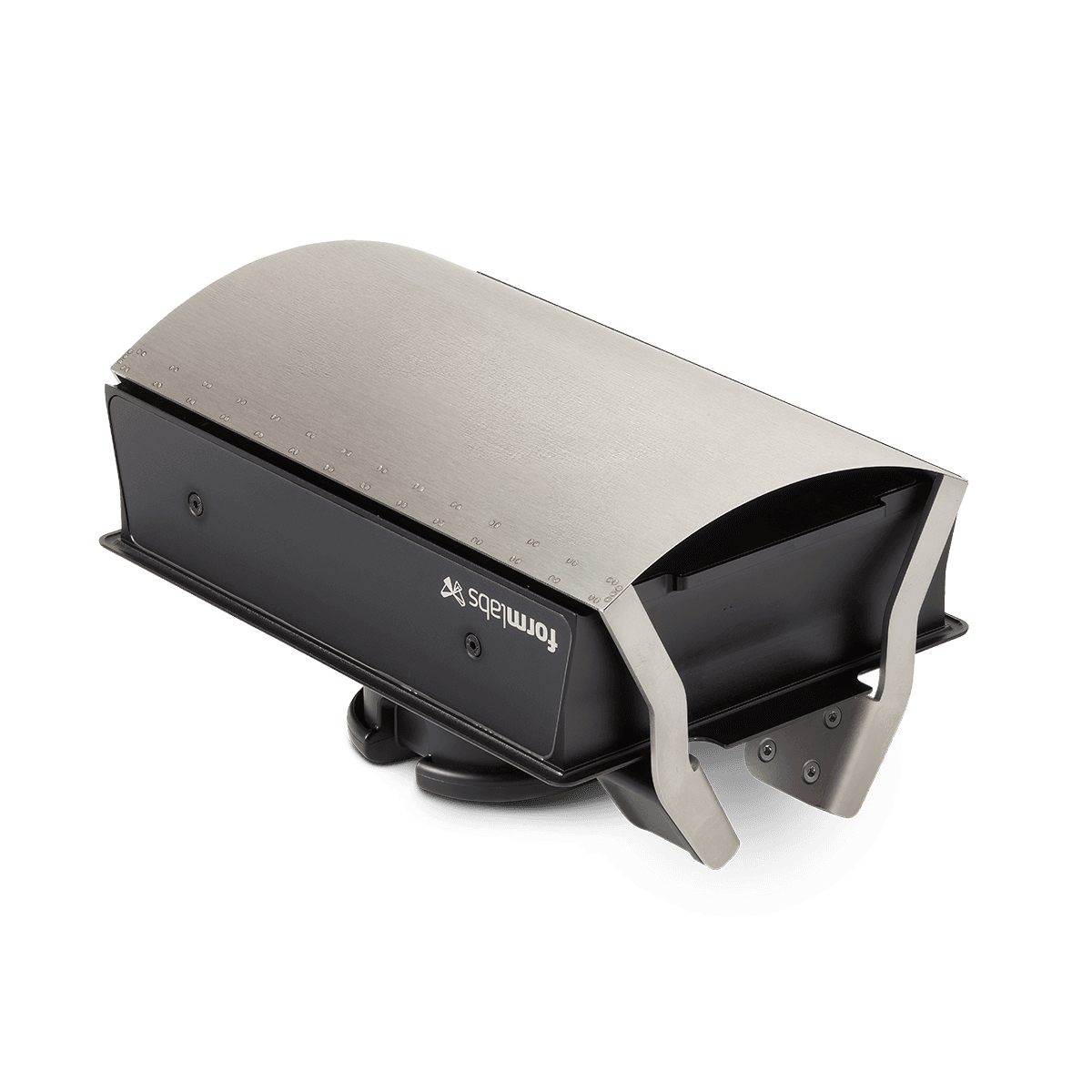
Both Form 4 Build Platform and Build Platform Flex have a printable surface of 20.0 x 12.5 cm (7.9 x 4.9 in), compared to 14.5 x 14.5 cm (5.7 x 5.7 in) of the Form 3 Build Platform and Build Platform 2.
Both Form 4 Build Platform and Build Platform Flex, as well as Build Platform (Form 2, Form 3/B/+) and Build Platform 2 (Form 3/B/+), are compatible with the new Form Wash (2nd generation).
Build Platform | Build Platform Flex | |
---|---|---|
Quick Release Technology | No | Yes |
Resin compatibility | All resins | All resins (parts printed in flexible/elastic materials may not release as reliably with the quick-release functionality, but they can be easily removed with a tool) |
Compatible with Form Wash (2nd generation) | Yes | Yes |
Print Without Compromise
Making things is hard, and every second counts. When Formlabs engineers set out to make Form 4, speed, reliability, accuracy, and materials performance were front of mind. Powering Form 4 is countless hours of research and development, all to create a tool that enables you to go beyond the expected.
Print accurately right out of the box with blazing speed. Order Form 4 or Form 4B now or contact a 3D printing expert to learn how it can help you meet your business goals.