Impression 3D de préhenseurs personnalisés pour un robot de transfert
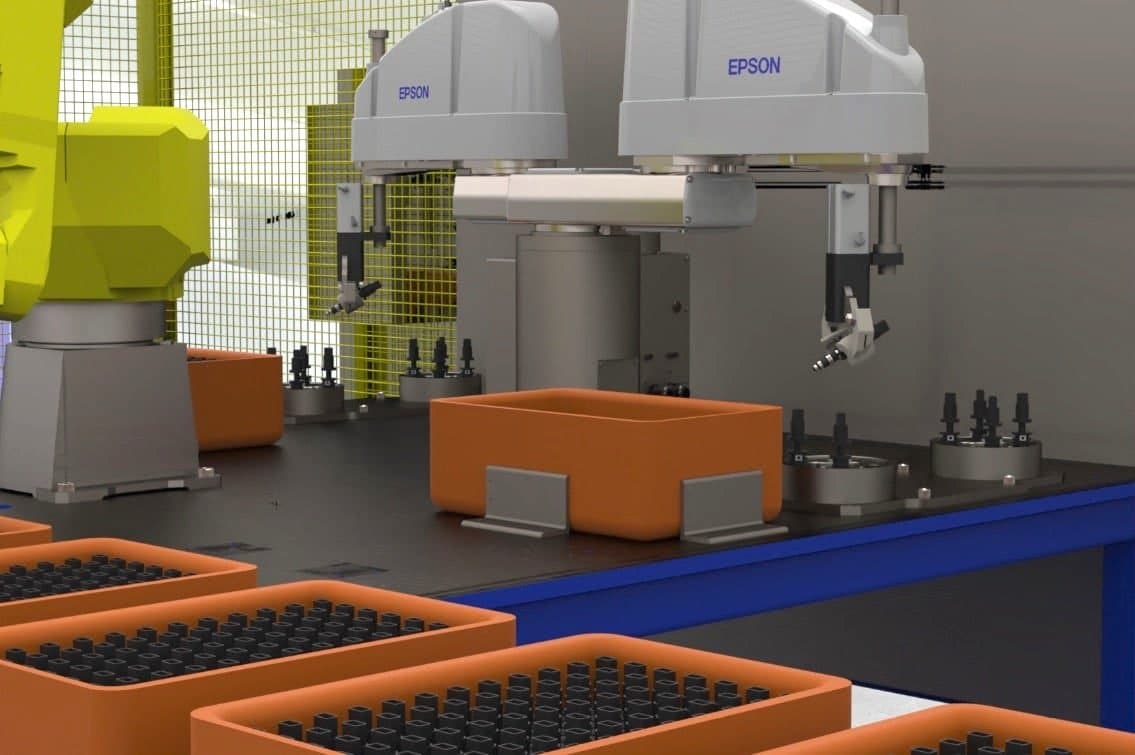
Entreprise basée dans le Wisconsin, STS Technical Group travaille depuis près de 40 ans avec ses clients sur des problèmes de recrutement, de conception technique et d'ingénierie. Avec plus de 250 employés répartis dans différents centres de recrutement aux États-Unis, l'entreprise s'est développée et suit de près l'évolution des technologies de production industrielle, offrant des services nouveaux et innovants au fur et à mesure de leur apparition.
STS utilise les imprimantes 3D Formlabs, car elles sont capables de produire des composants biocompatibles de grande qualité, et proposent de nombreux matériaux adaptés à une utilisation intensive dans un environnement de fabrication.
Dans cette étude de cas, Benjamin Heard, directeur des services d'ingénierie de STS Technical Group, vous montrera comment il a réussi à développer des préhenseurs personnalisés pour saisir et positionner des injecteurs de carburant dans un environnement de fabrication. Vous découvrirez les avantages de l'impression 3D par rapport à des méthodes de production traditionnelles telles que le moulage et l'usinage. M. Heard expliquera également pourquoi les préhenseurs imprimés en 3D sont bien supérieurs à ceux fabriqués avec des méthodes traditionnelles.
Comment choisir une méthode de production pour des composants spécifiques
Pour fabriquer un composant spécifique, de nombreuses méthodes de production doivent être envisagées pendant le développement. Il y a par exemple le moulage, le façonnage, l'usinage et les processus d'impression 3D comme le dépôt de fil fondu (FDM) ou l'impression par stéréolithographie (SLA).
Voici quelques-uns des nombreux avantages qu'offre l'impression 3D pour la fabrication de composants :
-
Un niveau de détail plus grand que le moulage et/ou l'usinage. Une épaisseur de couche d'impression pouvant être de 25 microns à peine.
-
Plus rentable que le moulage, le façonnage ou l'usinage lorsqu'il s'agit de conceptions très détaillées.
-
Des délais de production nettement inférieurs à ceux du moulage, du façonnage ou de l'usinage.
-
Aucun usinage n'est nécessaire après l'impression. Il n'y a donc pas besoin d'un équipement d'usinage coûteux qui nécessite une main-d'œuvre qualifiée et une configuration fastidieuse.
-
Une large gamme de matériaux durables et légers.
-
Les conceptions créées à l'aide d'un logiciel CAO peuvent être sauvegardées et réutilisées au besoin pour remplacer une pièce, sans qu'il soit nécessaire de procéder à un inventaire.
-
Les pièces imprimées en 3D peuvent inclure des matériaux supplémentaires pour les renforcer et faciliter leur installation, ou incorporer des caractéristiques telles que des trous de vis/boulons et des cavités hexagonales.
-
Si une pièce en polymère imprimée en 3D SLA subit un choc violent en cours de fonctionnement, elle se brisera probablement, alors que les pièces métalliques auront tendance à se déformer et à continuer à produire des pièces qui ne répondront pas aux exigences.
-
Coûts de remplacement réduits pour les composants cassés, et accélération des délais de production pour les pièces de rechange.
-
Les pièces imprimées peuvent être peintes ou vernies.
-
Elle permet d'utiliser des matériaux qui ne conviennent pas à l'usinage parce qu'ils fondent, s'écaillent ou se fissurent pendant le processus.
-
Frais d'expédition réduits grâce à un poids plus faible et à une réduction des matériaux d'emballage.
Pour choisir entre le moulage, le façonnage, l'usinage ou l'impression 3D de composants, il faut d'abord tenir compte de la durabilité de la pièce. Si les pièces métalliques produites par des procédés traditionnels offrent une solidité, une durabilité et une résistance à l'usure supérieures, les exigences de nombreux composants peuvent être facilement satisfaites en les imprimant en 3D avec des matériaux techniques spécifiques.
Pour choisir la méthode la mieux adaptée, il faut aussi prendre en compte l'environnement de travail pour s'assurer que le matériau peut résister à la température, aux niveaux d'humidité ou à la présence de corrosifs. L'impression 3D de grands composants peut constituer un défi, mais les imprimantes 3D grand format, telles que la Form 3L, peuvent imprimer des pièces plus volumineuses.
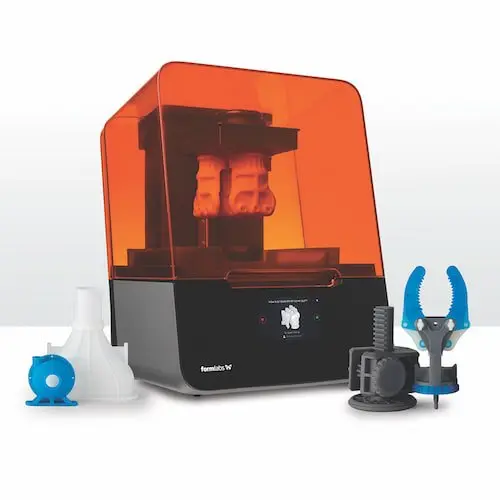
Introduction à l'impression 3D avec la stéréolithographie de bureau (SLA)
Vous cherchez une imprimante 3D pour créer des modèles 3D haute résolution ? Téléchargez notre livre blanc pour découvrir comment fonctionne l'impression SLA et pourquoi elle est tant utilisée pour créer des modèles aux détails incroyables.
Conception et impression 3D de préhenseurs personnalisés pour injecteurs de carburant
De nombreux facteurs doivent être pris en compte pour concevoir des préhenseurs destinés à des opérations de transfert : les matériaux utilisés pour fabriquer le composant saisi et le préhenseur, la force de préhension, la forme du composant saisi, les mouvements radiaux ou linéaires des mâchoires, l'espace environnant et les tolérances requises pour la saisie et le placement.
Le matériau des doigts de préhension est généralement choisi pour être nettement plus résistant et plus dur que la pièce saisie afin d'éviter que les bras ne s'usent pas après des milliers, voire des millions de cycles. Un préhenseur est généralement fabriqué en acier trempé, qui peut laisser des marques sur certaines surfaces molles des pièces saisies. Si la finition de la pièce saisie est délicate, des revêtements ou des patins sont ajoutés au préhenseur. En outre, lorsque les pièces sont placées pour être usinées, un mauvais contact peut entraîner un mauvais positionnement de la pièce et engendrer des défauts d'usinage.
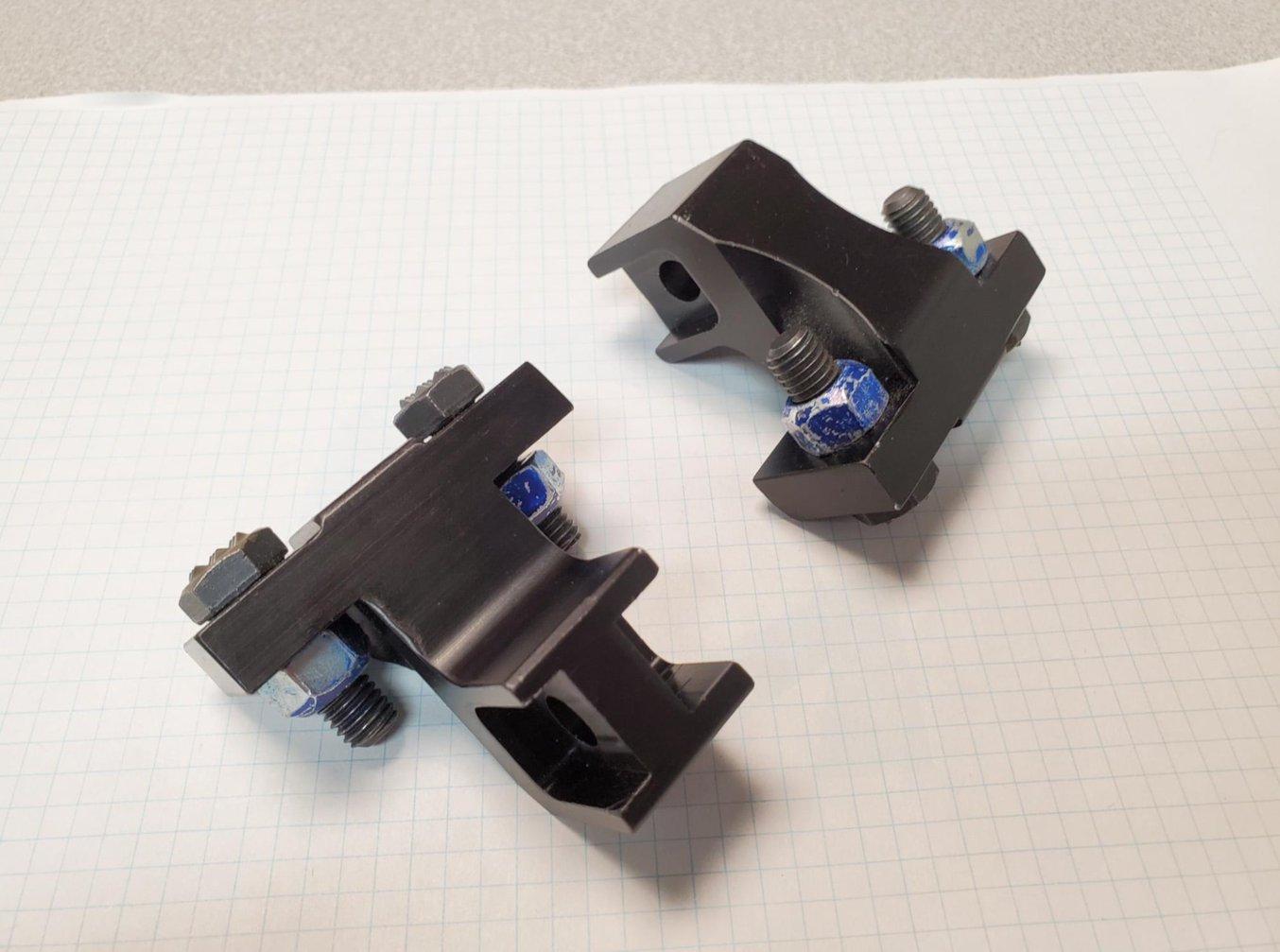
Les préhenseurs génériques qui étaient initialement installés sur le cylindre pneumatique.
En général, les mâchoires du préhenseur sont conçues en forme de « V » pour saisir les objets cylindriques ou ayant des bords non plats. Cette forme offre un contact fiable avec la pièce, qui est doucement saisie de chaque côté. Plus important encore, il s'agit d'une conception simple et rentable qui peut être adaptée à n'importe quel processus.
Les inconvénients de cette conception sont les concentrations de force, qui sont éprouvantes à la fois pour le préhenseur et l'objet saisi, ce qui entraîne une usure du préhenseur. En outre, les préhenseurs en « V » ne peuvent positionner un objet que de manière abstraite, et nécessitent donc un mécanisme de positionnement secondaire pour les processus de fabrication supplémentaires.
Grâce à l'impression 3D, les options de conception augmentent considérablement, et il est possible de produire des préhenseurs bien ajustés qui répartissent la force sur une plus grande surface de contact.
Dans notre exemple, nous avons utilisé un scanneur laser 3D Creaform et le logiciel de modélisation VX Elements pour obtenir un scan 3D virtuel de l'injecteur de carburant, afin de faciliter la conception des préhenseurs. Le scan a permis d'obtenir une image très détaillée, évitant ainsi de devoir mesurer chaque espace, cylindre et ouverture de l'injecteur de carburant. L'image scannée peut ensuite être importée dans un logiciel CAO 3D pour générer une conception extrêmement détaillée à l'aide d'une fonction de moulage du logiciel.
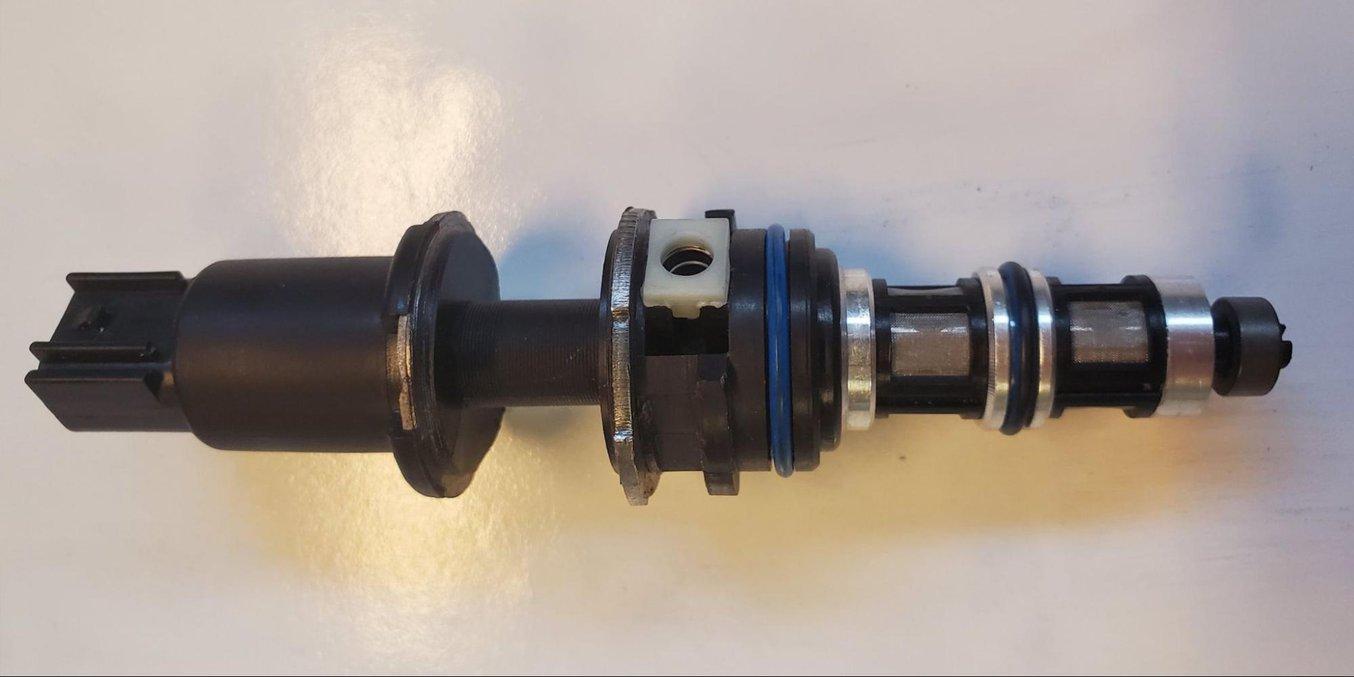
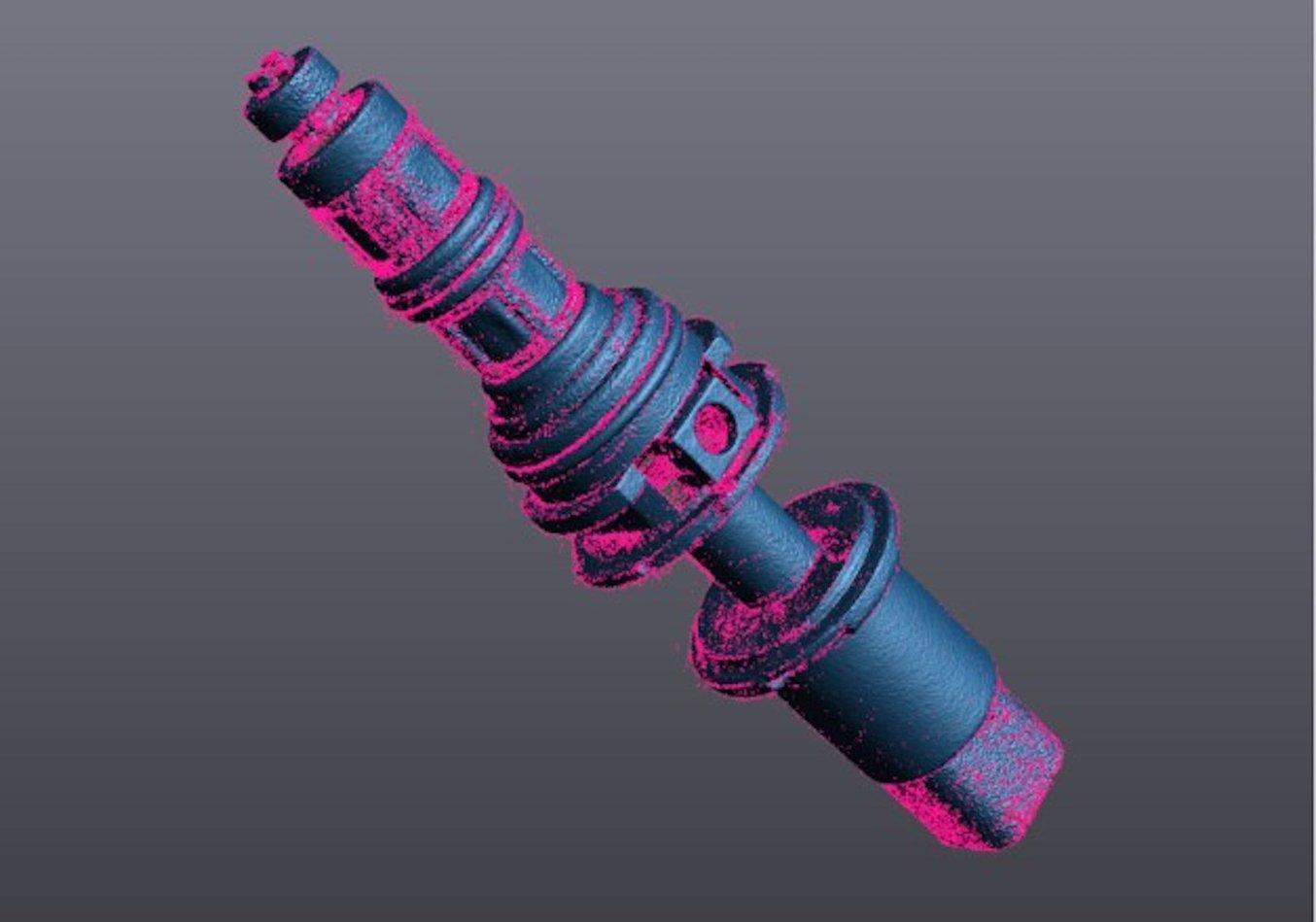
L'injecteur de carburant (en haut) a été scanné en 3D pour créer un modèle (en bas) qui a ensuite pu être utilisé pour créer les préhenseurs personnalisés.
Notre nouvelle conception détaillée de préhenseur radial est ensuite montée sur des bras rotatifs fixés au piston d'un cylindre pneumatique.
Le nouveau préhenseur a été prototypé et fabriqué avec une imprimante 3D SLA Form 3 de Formlabs. Formlabs propose plusieurs matériaux pour le prototypage rapide, tels que Draft Resin. Dans notre cas, Black Resin a été utilisée pour développer le prototype initial. Les deux moitiés du préhenseur ont ainsi pu être imprimées en une seule fois avec la Form 3. Les matériaux peuvent facilement être changés, ce qui accélère le passage de l'idée initiale au produit final.
Le composant final nécessitait un matériau plus durable pour pouvoir supporter l'environnement de production. Rigid 4000 Resin a donc été utilisée pour fabriquer les préhenseurs finaux. Ce matériau polymère extrêmement rigide à charge de verre offre une durabilité et une rigidité élevées, ainsi qu'une belle finition pour les pièces imprimées.
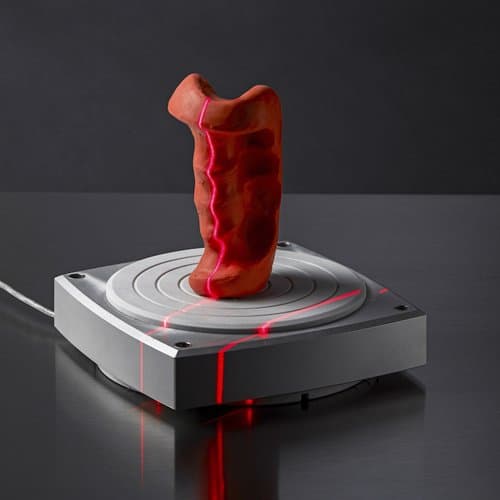
Numérisation 3D pour la rétro-ingénierie, la restauration et la métrologie
La numérisation et l'impression 3D sont utilisables, entre autres, en reproduction, en restauration, en rétro-ingénierie, en métrologie, et bien plus. Téléchargez notre livre blanc ou regardez notre webinaire pour apprendre à utiliser ces technologies et améliorer vos propres processus de conception.
Résultats
Le processus de conception et d'impression 3D des préhenseurs personnalisés a été franc succès, et ils fonctionnent comme prévu. Les capacités des préhenseurs imprimés en 3D sont bien supérieures à celles des préhenseurs précédents.

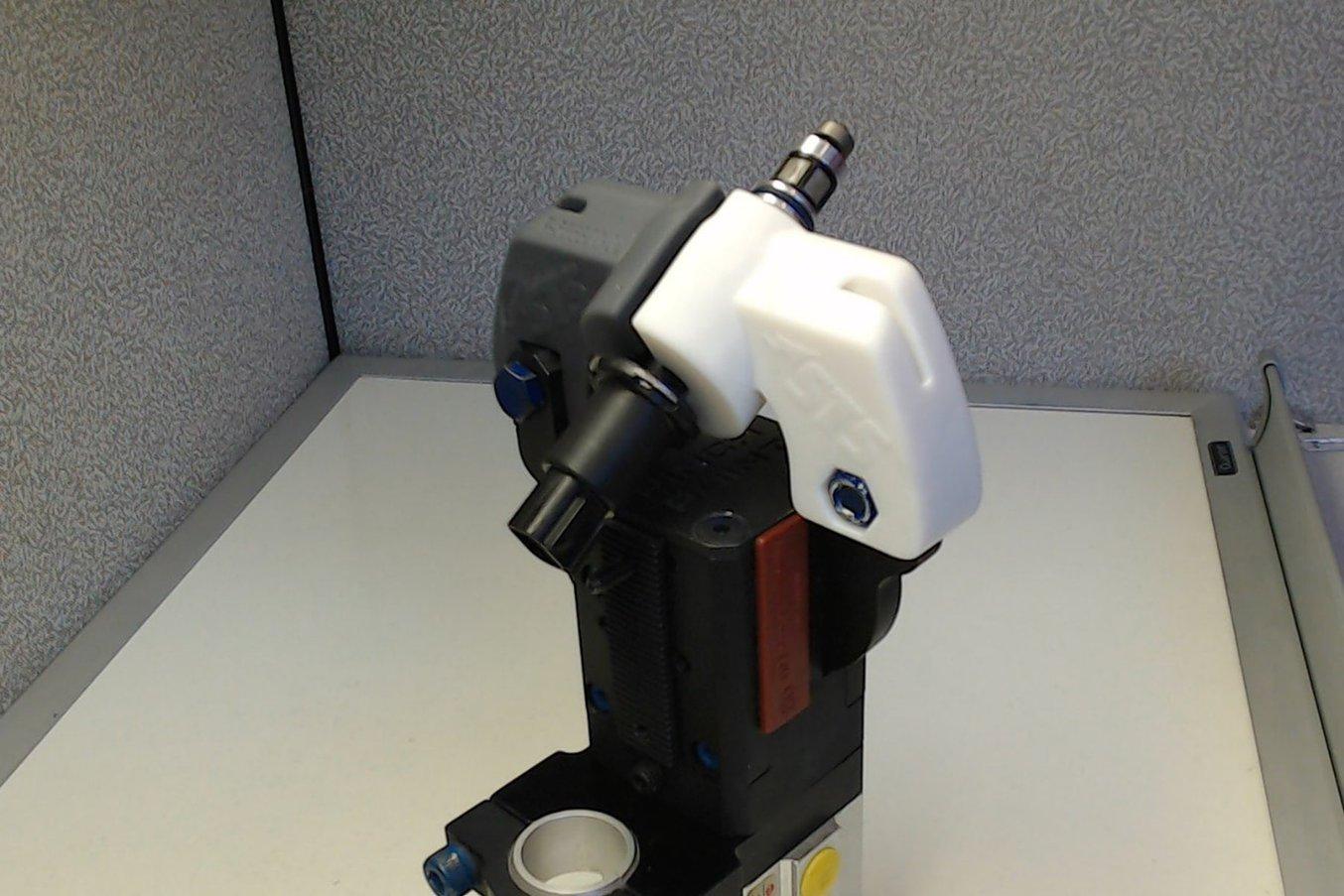
L'assemblage du cylindre pneumatique, avec les préhenseurs imprimés en 3D tenant l'injecteur de carburant.
Les avantages des préhenseurs imprimés en 3D sont les suivants :
-
Une plus grande surface pour saisir l'injecteur de carburant, ce qui permet de réduire les zones de concentration de force qui pourraient endommager ou rayer l'injecteur de carburant et user le préhenseur. Même si le préhenseur subit une usure, sa conception unique lui permettra de fonctionner comme souhaité.
-
Étant donné que les préhenseurs opèrent un mouvement de préhension radial, l'espace sur les bords intérieurs des préhenseurs peut être intégré dans la conception au lieu d'être usiné. Cela enlève les bords carrés dans la cavité de préhension, et permet de saisir et de relâcher uniformément l'injecteur de carburant.
-
Les mâchoires de préhension finement détaillées alignent et orientent l'injecteur de carburant dans la position souhaitée, réduisant ainsi la quantité d'équipements et de postes de fabrication nécessaires pour orienter les pièces saisies.
-
La conception du préhenseur permet de réduire la pression nécessaire pour saisir l'injecteur de carburant, ce qui diminue les besoins en pression pneumatique ou hydraulique de l'équipement de manutention.
-
Les préhenseurs sont conçus pour éliminer les structures de composants plus fines et maximiser la résistance de la résine. Ils incluent également une cavité hexagonale permettant de placer un écrou et de simplifier l'installation.
-
La sérialisation ou l'étiquetage du composant imprimé par SLA se fait pendant le processus d'impression, ce qui évite d'avoir recours à des processus d'estampage ou de gravure.
Conclusion
La Form 3+ de Formlabs est dotée d'une large gamme de matériaux d'impression, et constitue une excellente alternative aux processus traditionnels pour fabriquer des composants personnalisés, tels que des aides à la fabrication.
Les composants imprimés offrent une excellente durabilité et un haut niveau de détail, coûtent beaucoup moins cher, et peuvent être produits et mis en œuvre en bien moins de temps. L'avenir de la production industrielle automatisée, ce sont des produits très détaillés conçus à l'aide de logiciels CAO et imprimés en 3D avec divers matériaux.
Grâce aux imprimantes 3D Formlabs et aux logiciels CAO, STS Technical Group peut concevoir et réaliser des composants personnalisés et très détaillés pour ses clients.