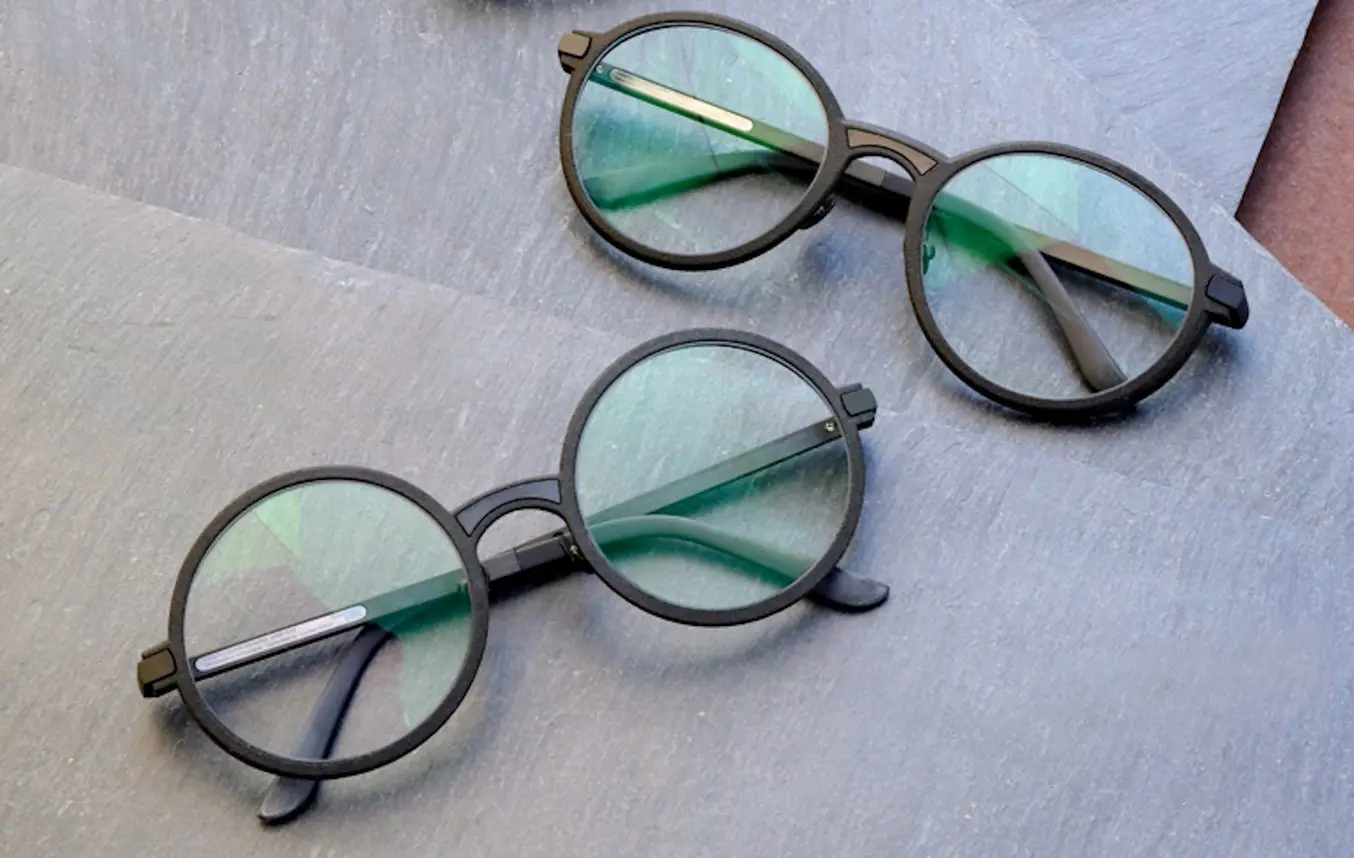
Marcus Marienfeld AGのアイウェアは、高品質でラグジュアリーな材料選定と熟練の職人技、そして革新的なアイデアをデザインに反映し続けることで、従来のアイウェアフレームとは一線を画すものとなっています。
金細工職人として活躍していた頃からMarcus Marienfeld氏は常に、これまでにないアクセサリーのデザインやその製造方法を追い求めてきました。
直近では、スイスの工房にFormlabsのSLS(粉末焼結積層造形)方式の3Dプリンタ Fuse 1を導入してアイウェアフレームを3Dプリントで量産する試みを始め、チタン製のパーツを成形するために3Dプリント製の型を使用する、いわゆるラピッドツーリングを行うようになりました。
本記事では、Marienfeld氏がSLS 3Dプリントの導入に至った背景、カスタムデザインの製品を量産できることの利点、そしてナイロンが材料として最適だった理由などを伺っています。
金細工職人からアイウェアブランドへ
Marcus Marienfeld氏は、現在の拠点であるスイスに金細工職人としてやって来ました。彼はほどなくして、業界で長年当たり前となっていた旧態依然の製造技術に革命を起こす可能性を見い出しました。
彼の使命はジュエリーのデザインだけに留まらず、その製造分野にも新たなテクノロジーを導入することでした。ジュエリーコレクションを開発する会社からスタートしたMarienfeld氏は、ドローイングからモデル製作、生産に至るすべてのプロセスを内製で行い、手仕事の技術に常にこだわってきました。
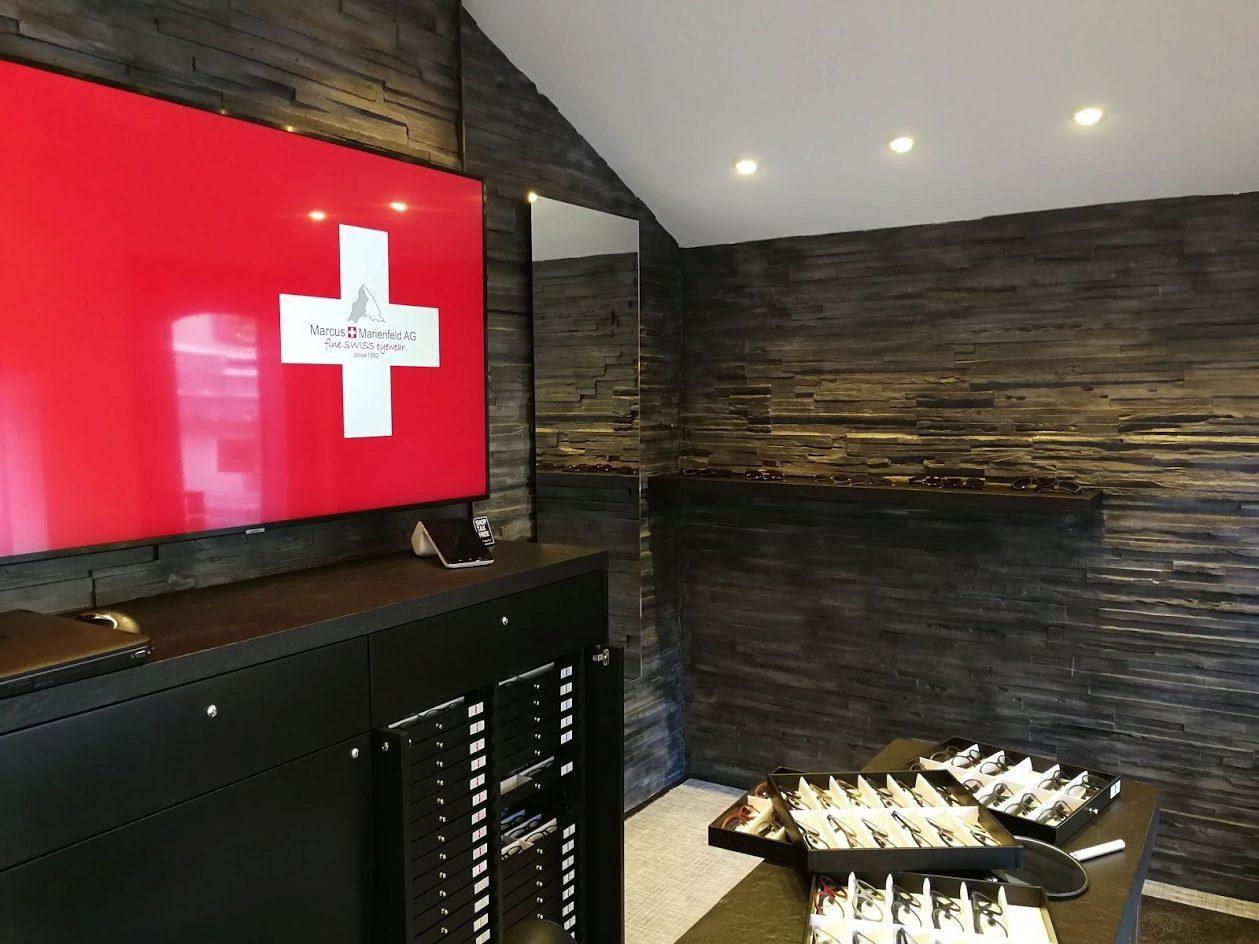
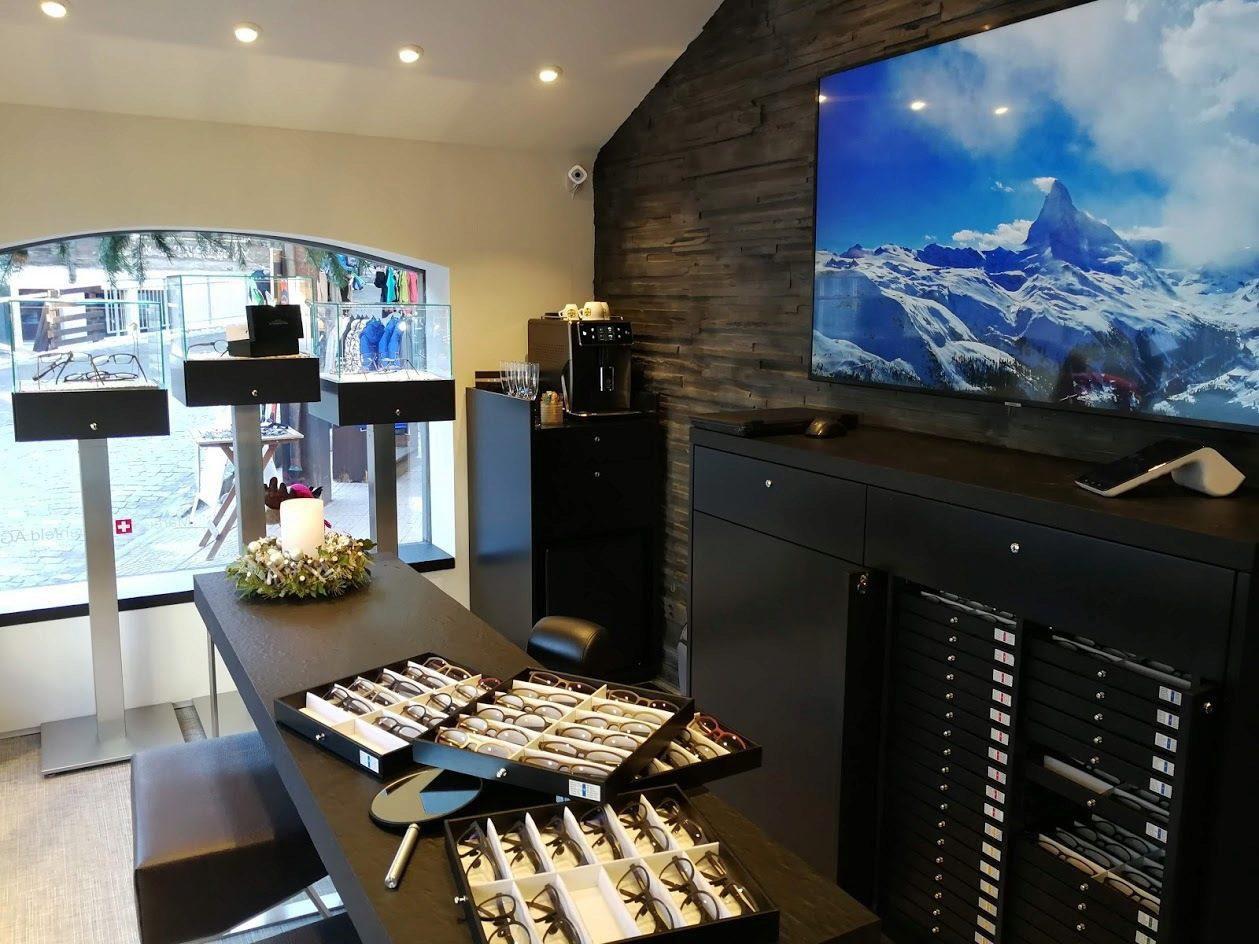
金細工職人だった彼は、ジュエリーやアクセサリーの試作を手早く行う(ラピッドプロトタイピング)目的で、CNC加工機にデザインをプログラムする前段階で、SLA光造形方式の3Dプリンタを活用していました。
現在では、Marienfeld氏は主にSLS 3Dプリンタを彼の専門分野であるアイウェアの製造に使用しています。同社ではNylon 11パウダーをアイウェアフレームに採用し、高品質なフレームを製造しており、SLSプリントで生産用の型も製作しています。
「私は、製造工程における”自給自足”を重視しています。生産工程を外部要因に左右されないように、そして常に柔軟に顧客のニーズに対応できる体制を目指しています。自分のオフィスに持ち込める3Dプリンタは、まさに打ってつけのツールでした。」
Marcus Marienfeld氏
3Dプリント製アイウェアフレームをFuse 1で量産
Marcus Marienfeld AGは2022年から、カーボン、チタン、水牛の角、古いオーク樽の木材など、高級アイウェアに使用するこれらの材料に、SLS 3DプリンタFuse 1を使って、徐々にナイロンを導入しています。
「私たちが作るアイウェアは、世の中にある一般的なものとは別物です。」とMarienfeld氏は言います。
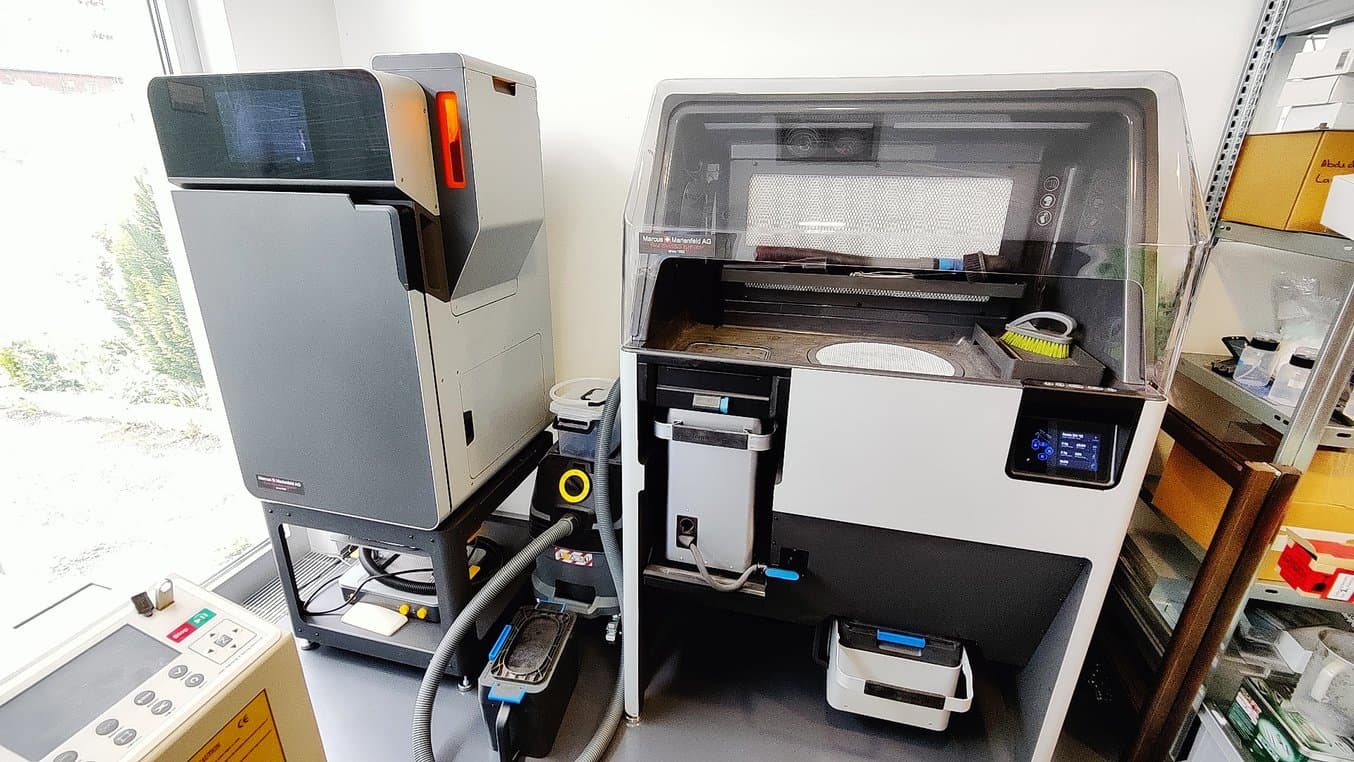
この方針の下、彼はFormlabsのSLS材料、Nylon 11パウダーをアイウェアのデザインに取り入れることを決めました。Marienfeld氏が最初に着手したのは、自身のスタジオでフレームフロントを中心に様々なデザインをFuse 1でプリントし、テストすることでした。直近では、初めてFuse 1でアイウェアフレームの量産を行っています。1回のプリントで80枚のフレームフロントを、およそ1日半で完成させることができています。
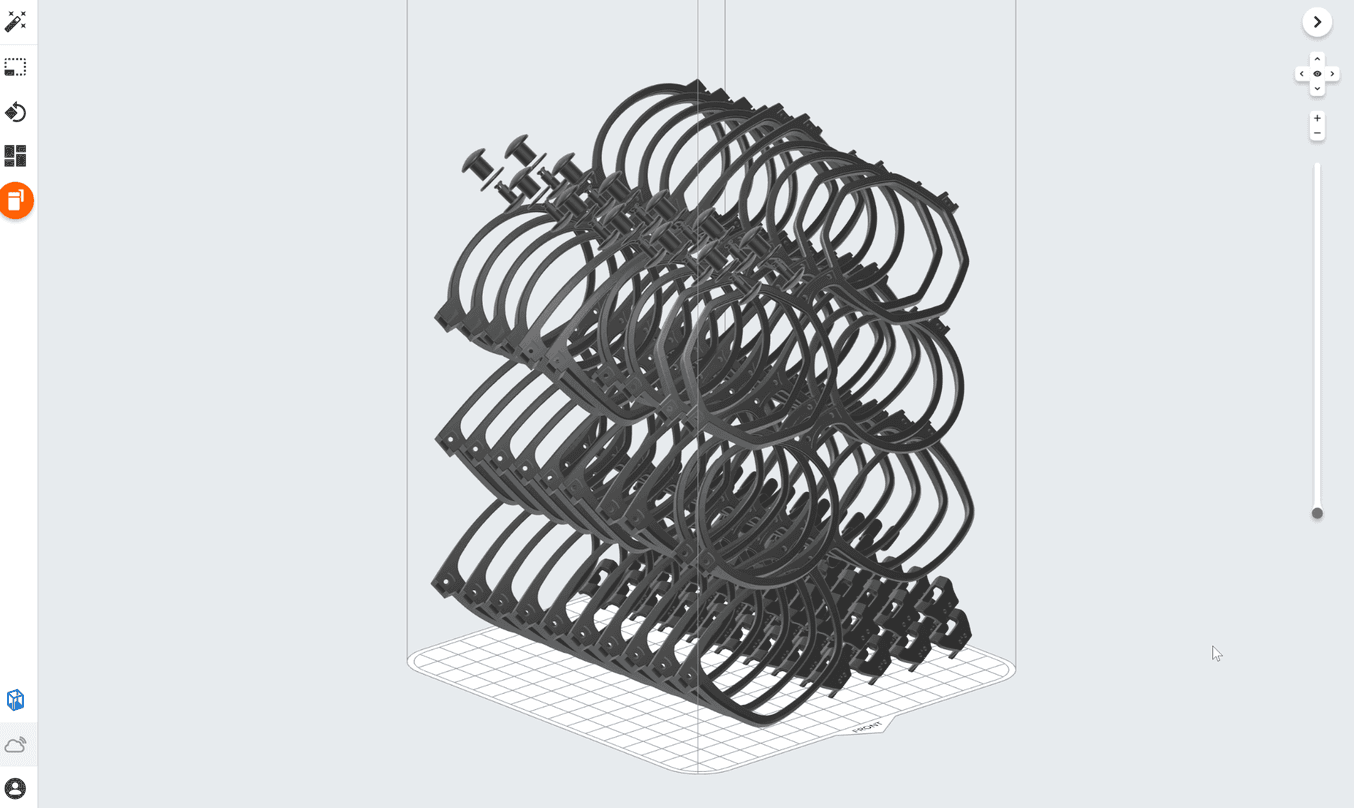
Fuse 1の造形スペースでは、1回のプリントで合計80枚のフレームフロントを造形スペースに配置し、量産を行った。
Fuse 1の粉末焼結積層造形方式は、高精細な造形とサポート材が不要となる特徴により、繊細なデザインや形状がプリントでき、プリント後にさらに精密な加工を施すことも可能です。
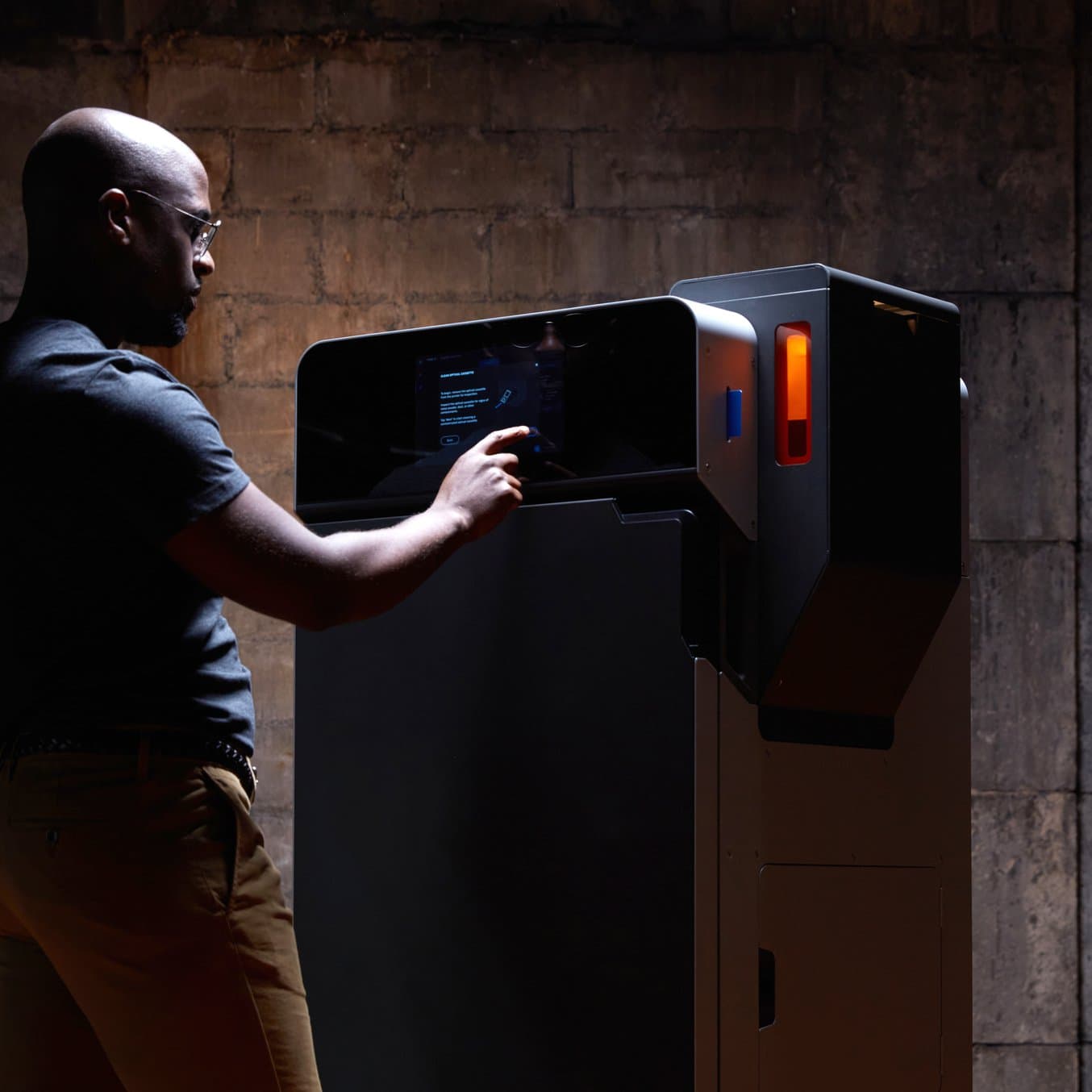
Formlabs SLS製品総合カタログ
本カタログでは、SLS方式とは何か、そしてFormlabsのSLS Fuseシリーズの優位性と特許技術、使用できる材料の紹介、社内検証済みの表面処理や実際の採用事例等、総合的な情報をこれ1冊でご確認いただけます。
「SLS 3Dプリントの利点の一つは、サポート材なしで入れ子状のデザインがプリントできることだと思います。」
Marcus Marienfeld氏
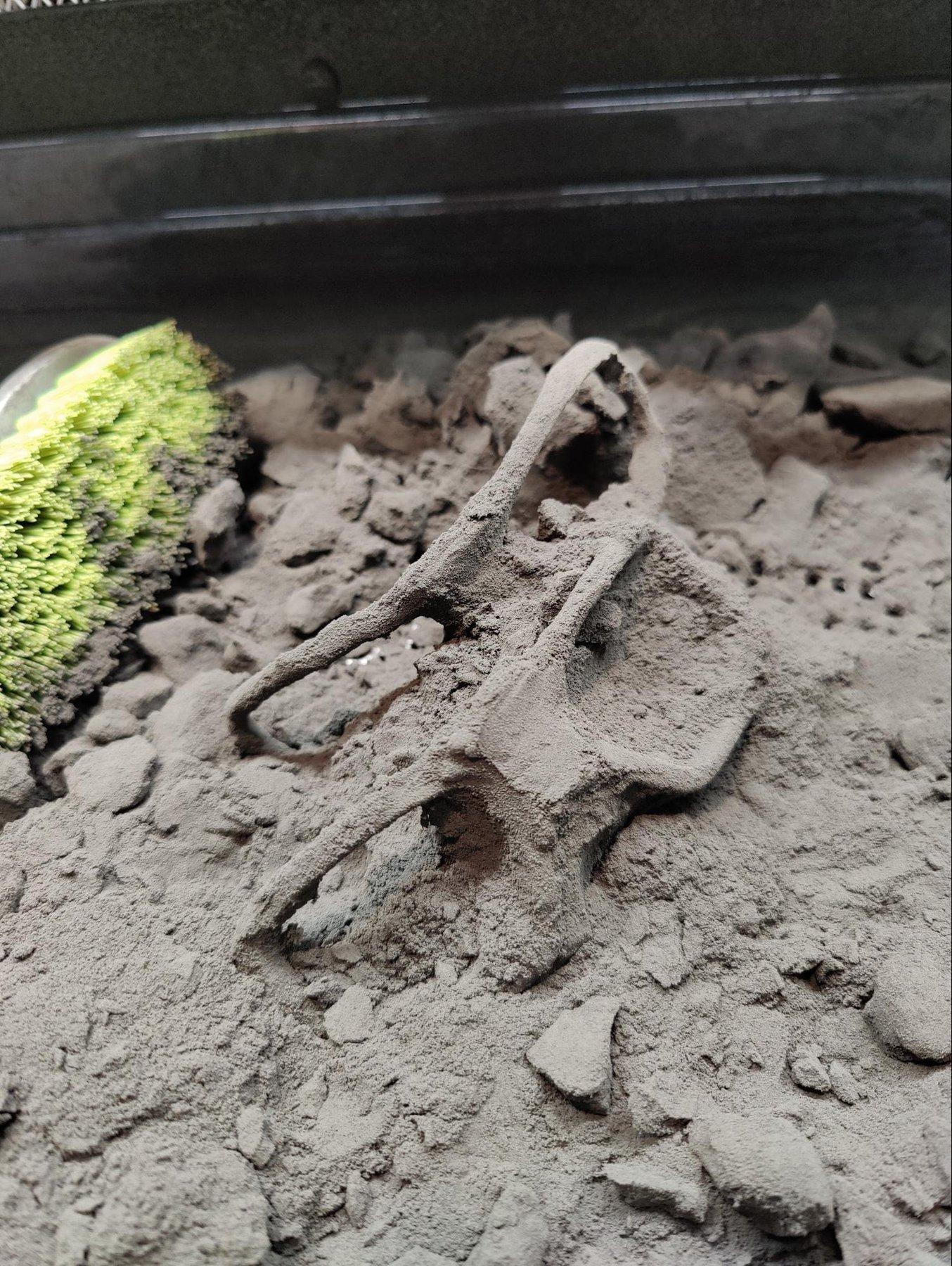
Fuse Siftで粉末除去作業中のNylon 11製のアイウェアフレーム。
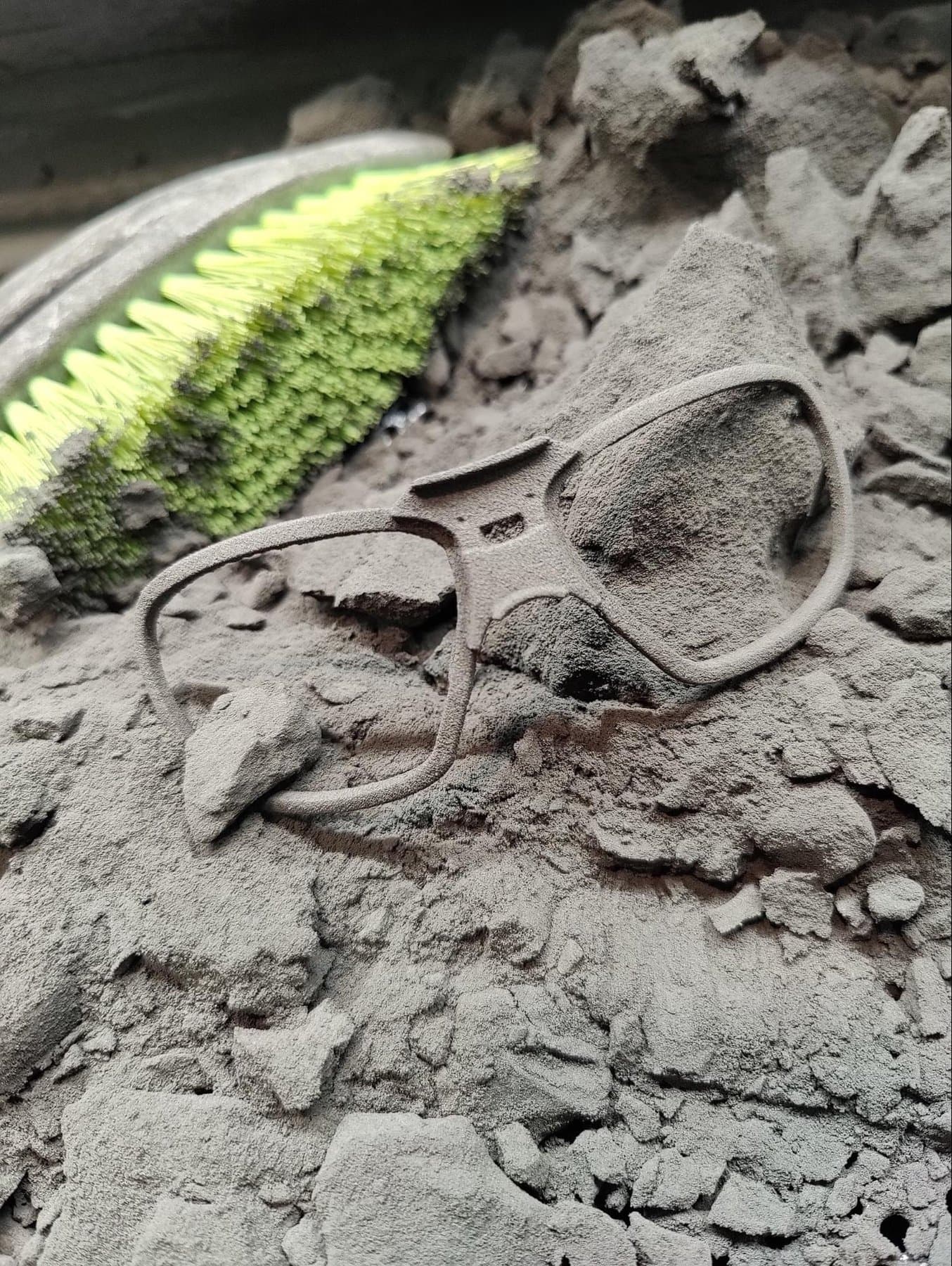
SLS 3Dプリントで量産された最初のアイウェアは、高品質なカーボン製テンプルが装着され、世界中の販売店に共有されます。また、ナイロン材を使用した他のアイウェアプロジェクトもMarienfeld氏の下で進行しており、通気孔をデザインに取り入れたスポーツ用のグラスは、別個にプリントしたパーツをアセンブリして完成するデザインとなっています。
“Fuse 1 is always at 100% in terms of accuracy. That's pretty awesome."
Marcus Marienfeld
Fuse 1のように、サポート材除去後の研磨を気にすることなくデザインしたものが量産できる3Dプリンタの場合、従来の切削や成形のようなデザイン面での制約がほぼ無くなり、非常に自由度の高いデザインを製品化することが可能です。「私たちはただフラットなだけではなく、外側に行くほど厚みを持たせたフレームをデザインしました。ほぼ円錐形状に近いデザインです。こういったものを作る際の最適解は、3Dプリンタを活用することです。他の技術では作ることができない特殊なデザインも、簡単にできてしまいます。」とMarienfeld氏は説明してくれました。
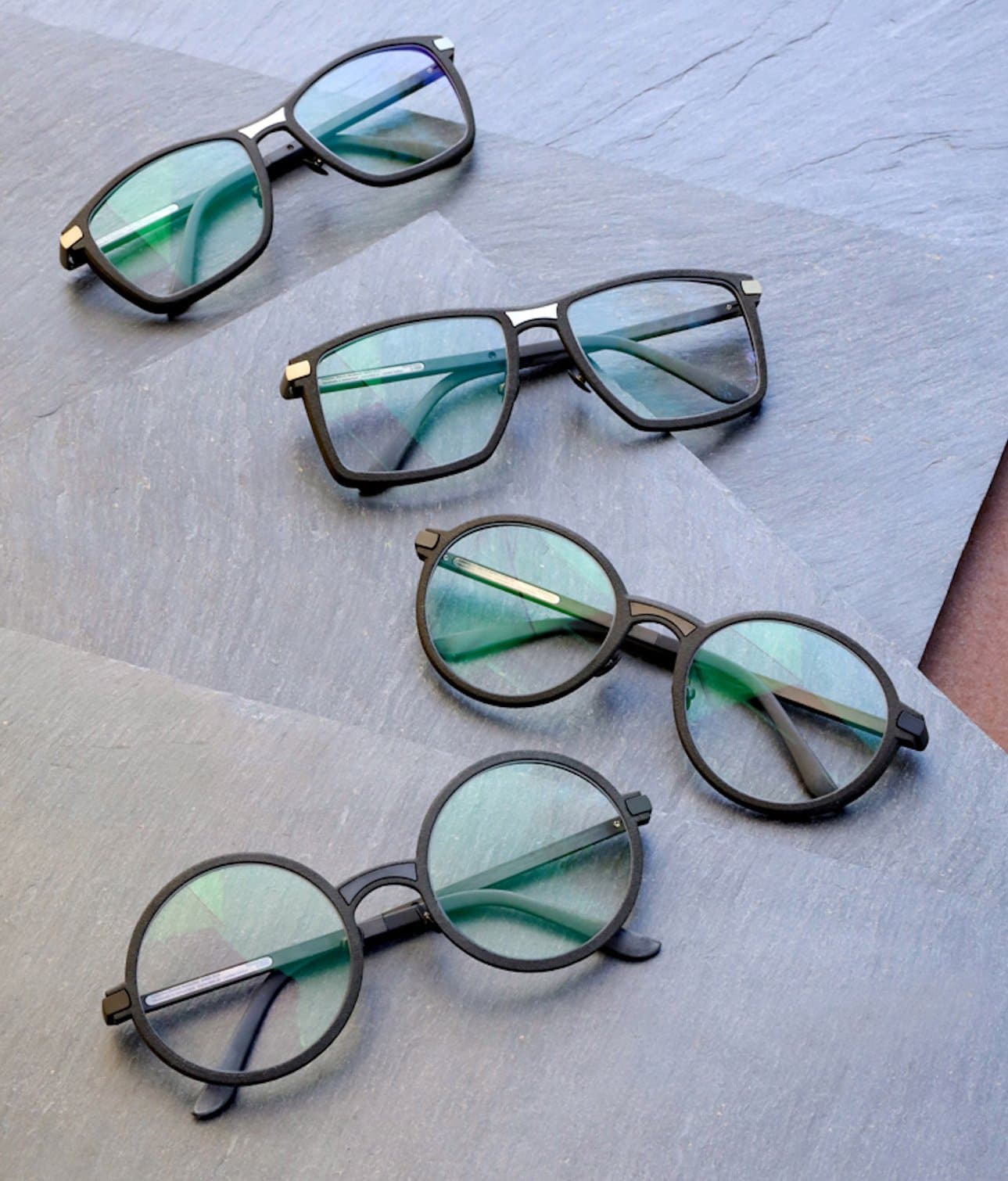
Nylon 11パウダーとカーボンパーツを使用したMarcus Marienfeldのアイウェア。
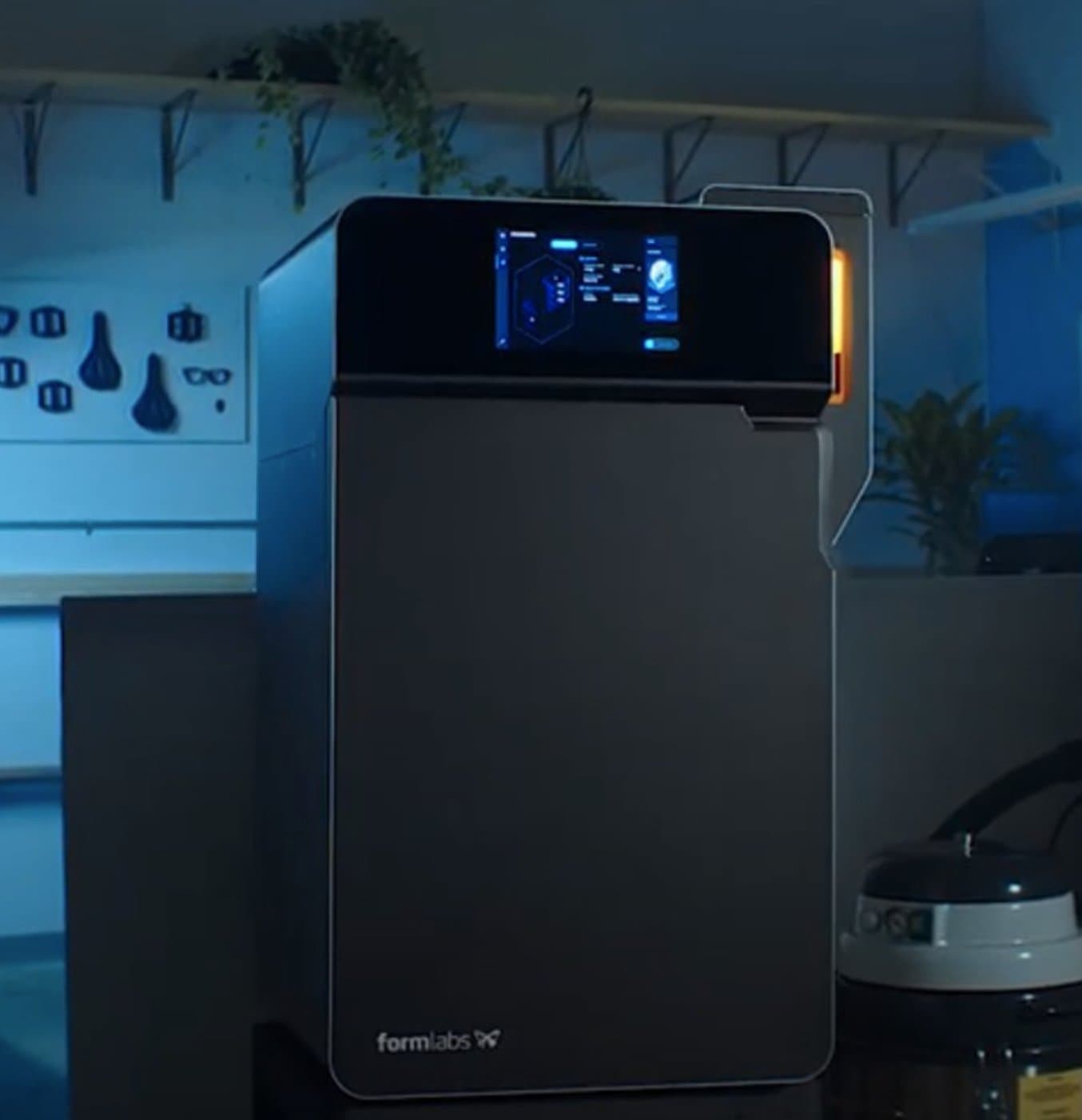
外注か内製か: SLS方式3Dプリントが適するケースとは?
本ホワイトペーパーでは、最近のSLS方式3Dプリンタ市場の概要と、3種の用途に関する6つのケーススタディ等を解説いたします。
耐久性に優れたナイロン材がもつ美しさ
製造業、特に工業分野のFuse 1ユーザーにとっては、強度や耐熱性などの機械的特性がまず重要となりますが、Marienfeld氏は少し違った視点で材料を見ています。
材料選定の際、Marienfeld氏がNylon 11パウダーを選んだのは、その美しさが主な理由でした。
「私はNylon 11パウダーのダークグレーの色味とSLSプリント品の質感を強調したいと思いました。ニュートラルな印象があるので、異素材を組み合わせて遊ぶこともできますし、ジュエリーであればカラフルな要素も取り入れるのも良いんじゃないかと思ったんです。」とMarienfeld氏は言います。
さらに、仕上げ工程を経ても一定のグリップ力を保つセミグロス(半艶)の表面処理は、Nylon 11製アイウェアを販売する上でも、顧客がそれをかける上でも重要なポイントとなっています。
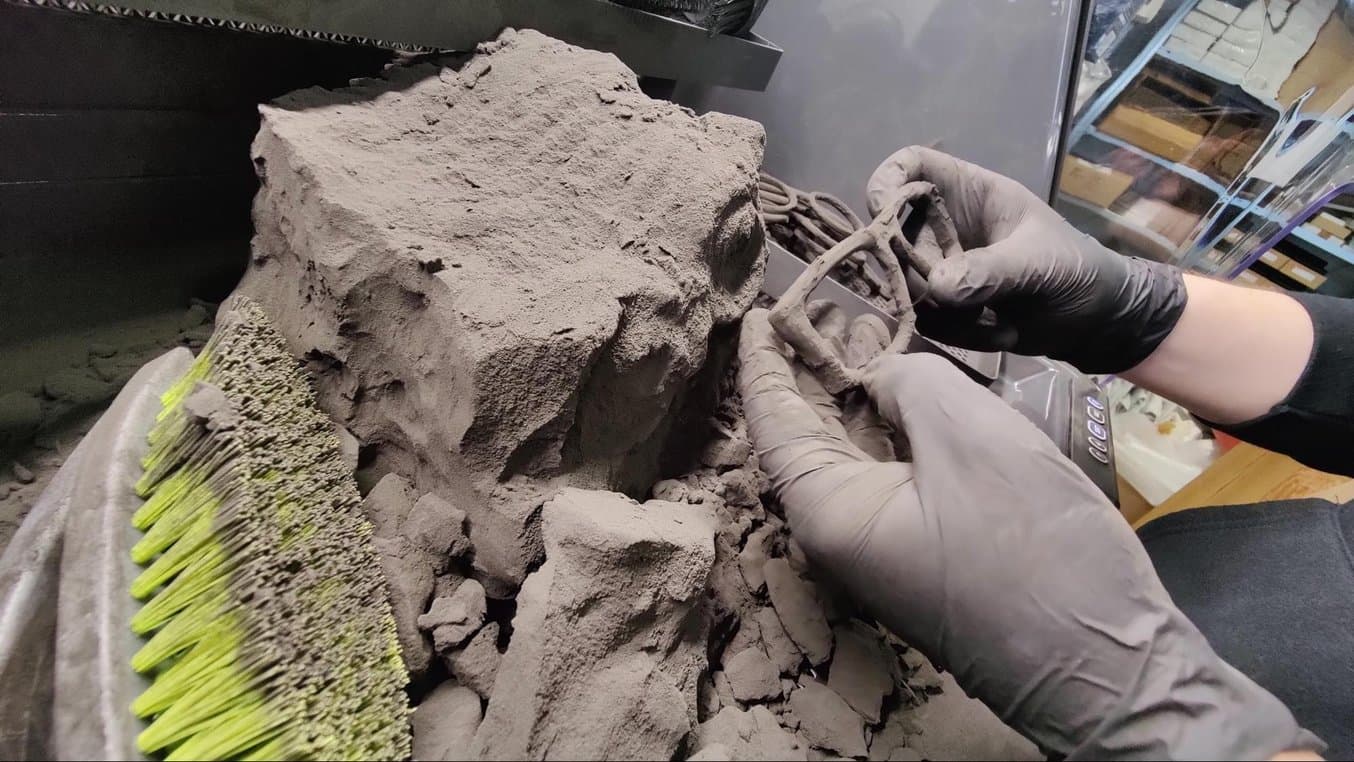
お客様一人一人の思いを実現する3Dプリンタ
Marcus Marienfeld AGでは、以前からアイウェアの製造に多彩な生産技術を導入しているため、3DプリントとCNC加工など、従来型の工程とを比較することもできました。
Marienfeldのカーボングラスは、5軸のCNCマシンで削り出されています。細部の加工はすべてCNCで行いますが、お客様一人一人の顔にぴったり合うアイウェアを作ることはできません。
「でも3Dプリンタなら、すぐにできてしまうんです。CADデザインに慣れている人なら、3Dモデルの微調整も簡単にでき、PreFormでSTLファイルを開けばそのままプリントできます。フライス加工となると、ワークを機械上で固定するために、常にそれ専用の治具を作らないといけないのですが、これは非常にコストがかかってしまいます。」とMarienfeld氏は言います。
例えば、ある登山ガイドからの依頼で、オーダーメイド製品を実現した例があります。3Dプリントの活用により、僅か2週間で登山中の太陽光への特殊な偏光レンズを備えたナイロン製サングラスを提供することができています。
「従来型の製造方法で作らなければいけないカーボン製では、2~3カ月はかかると思います」とMarienfeld氏は説明してくれました。
チタンを成形する金型も3Dプリントで
Marcus Marienfeld AGは、ナイロン材でアイウェアを作るだけでなく、Fuse 1で独自の成形用金型も製作しています。Nylon 11パウダーは、その強度と寸法安定性から、特にチタン製メガネの金型製作にも活用することができます。
「チタンの欠点は、成形、曲げ等の加工が難しいことです。しかし3Dプリント製のNylon 11で作ったプレス金型で試してみるとどうだろうと思い付き、試してみたんです。完璧に成功したんですよ。」
Marcus Marienfeld氏
「アイウェアのフレーム用に曲げ加工を行うためのプレス金型を作っています。メガネのモデルによって曲げのアールを変える必要があります。これまではスチールを切削して金型を作っており、非常に手間がかかっていました。手間がかかるということは、1モデルあたりのコストも高くつくということなんです。」とMarienfeld氏は言います。
そんなNylon 11製の金型は上下2つの型で構成され、工場内のトグルプレス上で90kg程度の圧力に耐えて機能します。Nylon 11の優れた寸法安定性により、高圧でチタンのエッジが接触する箇所でも、金型にくぼみが生じることはありませんでした。
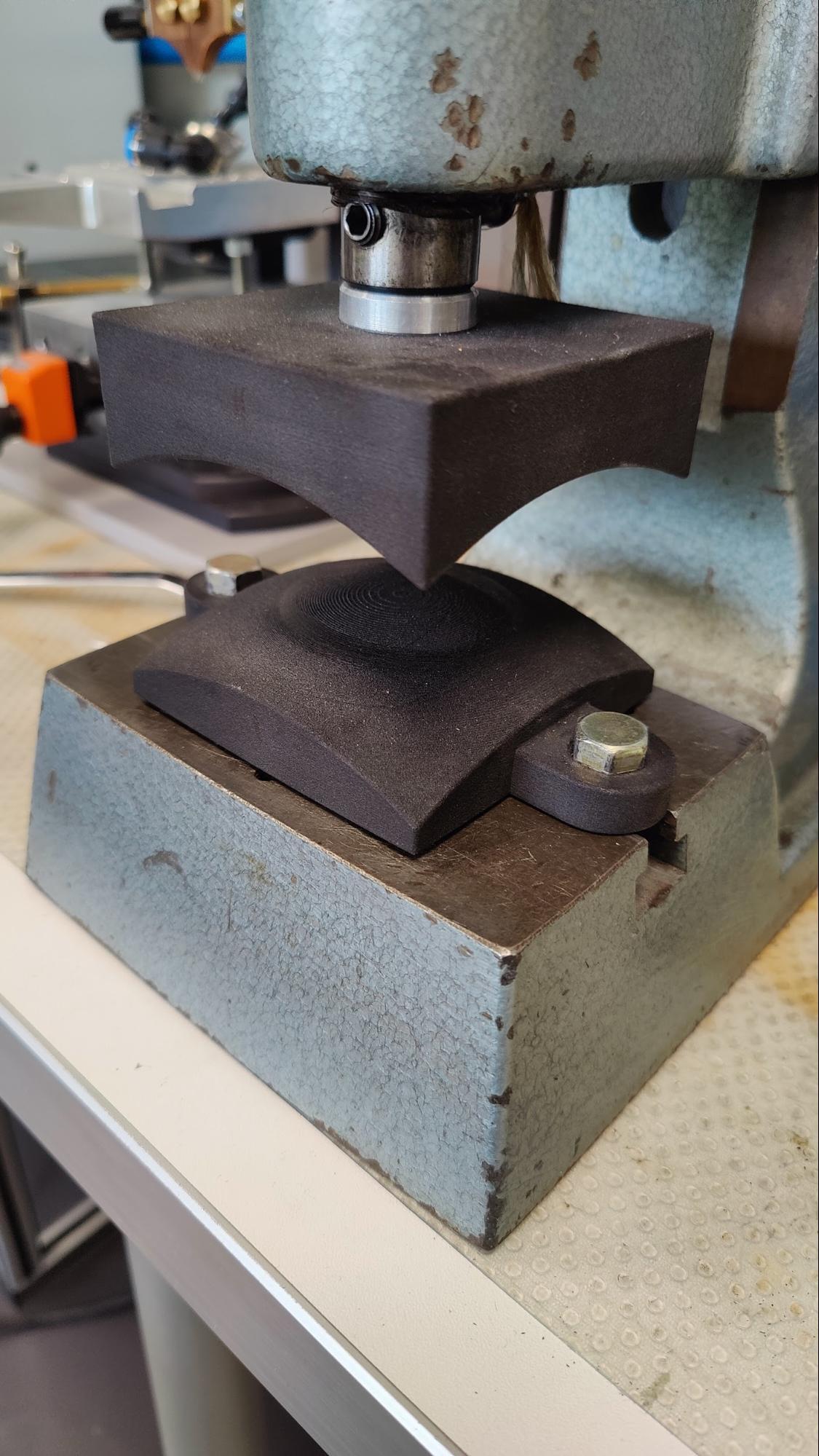
トグルプレス機に設置されたNylon 11による3Dプリント製金型。
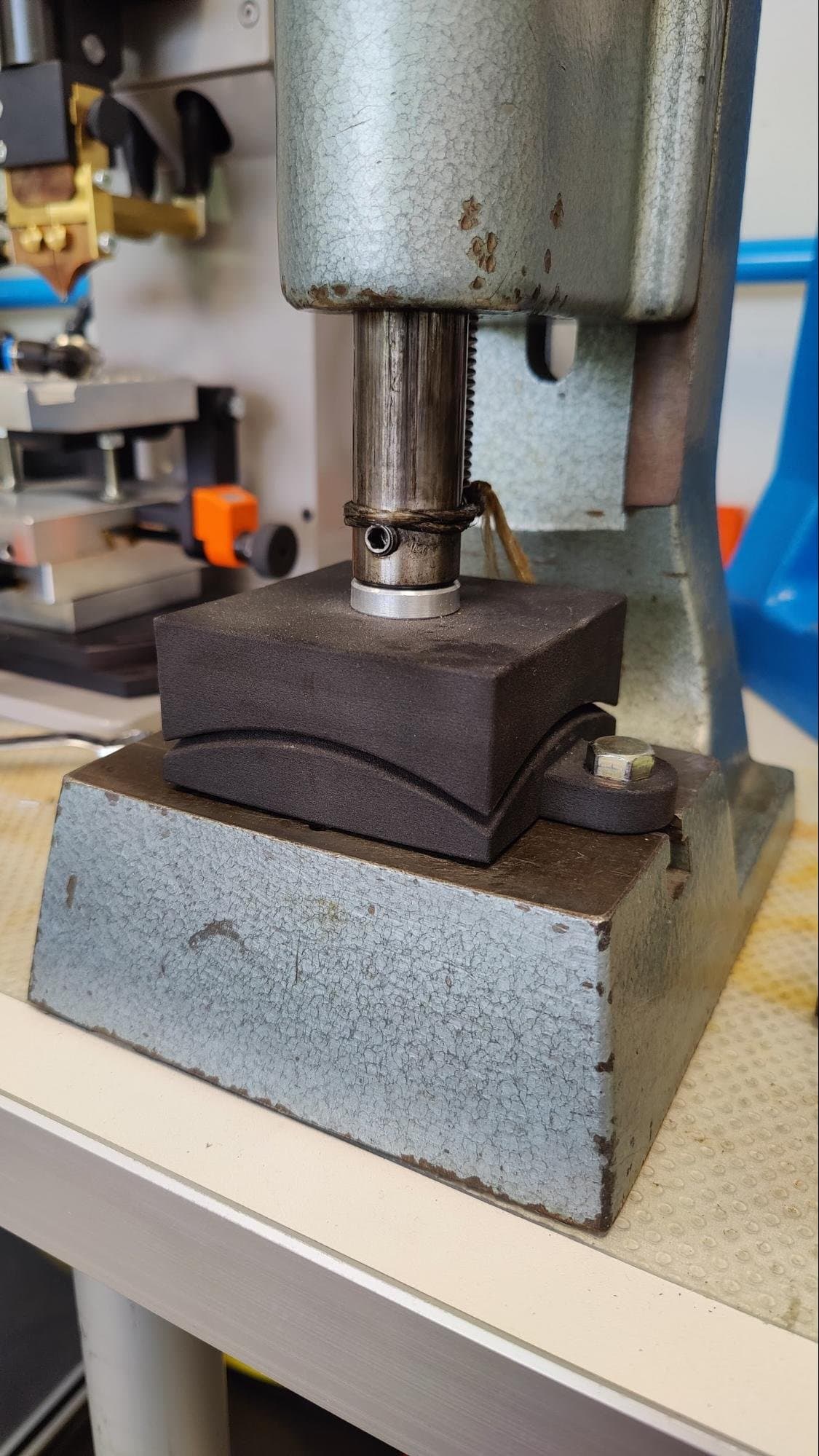
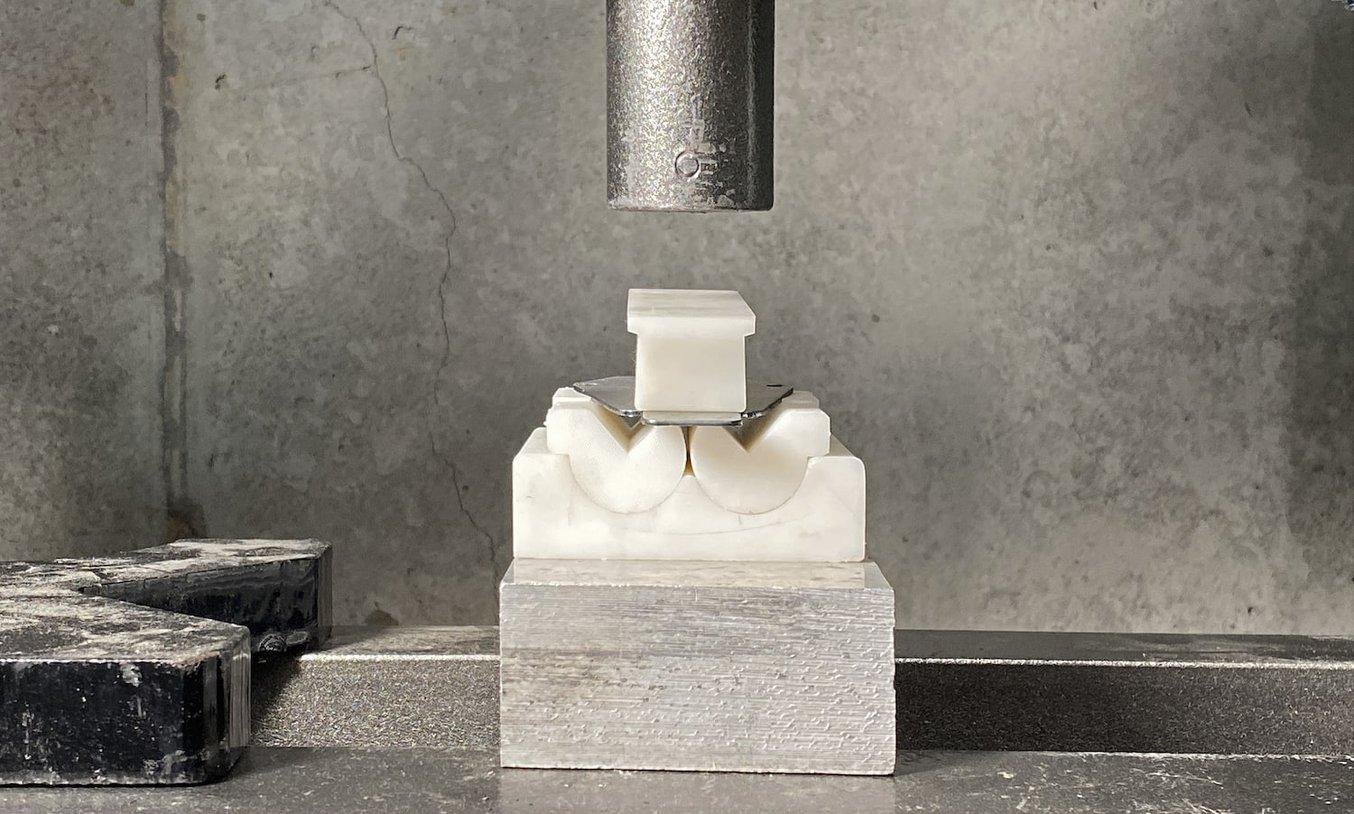
3Dプリント製金型での板金加工でラピッドツーリングを行う
本ホワイトペーパーでは、3Dプリント製の樹脂型で板金加工を行い、金型製作の時間とコストを削減する方法を手順ごとに解説します。
※本資料は現在翻訳中です。近日中のアップデートをお待ちください。資料の内容に関するご質問は[email protected]までお気軽にお問合せください。
3Dプリントの活用で、止まらぬイノベーションを
「私たちの目標は、常に成長を続けることです。規模や販売量ではなく品質とイノベーションにおいて、です。ニッチであり続けたいんです。」と、Marienfeld氏は自身のブランドについて語っています。
Marienfeld氏は、3Dプリンタによって試作品や金型の製作にかかる時間とコストを削減すると同時に、プロダクトデザインやその製造方法を新たに開発し続けることで、常に顧客に刺激を与えられる技術を手にしたと言えるでしょう。
「自社内にFuse 1のような3Dプリンタがあると、想像力が膨らんでもっと工夫できないものかと考えるようになります。普段はトライしないようなことにも、気軽に挑戦できるようになるんです。」
Marcus Marienfeld氏