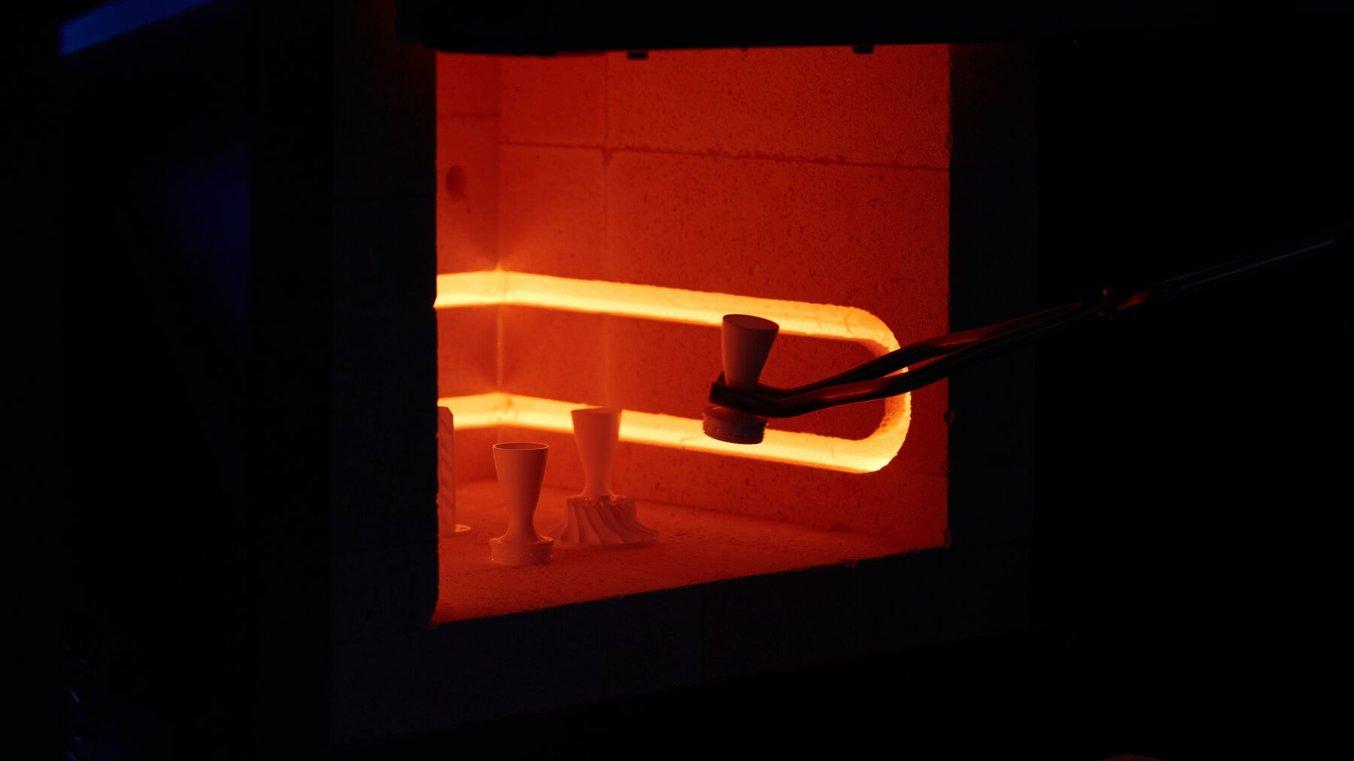
Formlabs introduced the first accessible, affordable, high-performance technical ceramic 3D printing material for stereolithography (SLA) 3D printers. Alumina 4N Resin is a 99.99% purity alumina material that combines the workflow flexibility and design freedom of 3D printing with the industrial and high-performance possibilities of technical ceramics.
When customized or low-volume parts are necessary in these situations, 3D printing with Alumina 4N Resin is a cost-effective, highly accurate, and rapid solution, but does not sacrifice any mechanical properties that technical ceramic users are looking for, even under extreme temperatures.
Formlabs conducted tests to determine the upper bounds of Alumina 4N Resin’s performance in extreme temperature settings so that customers can use the material with confidence in even the most demanding applications. To see the full workflow and results, download the white paper.
Alumina 4N Resin: Technical Ceramic for 3D Printing
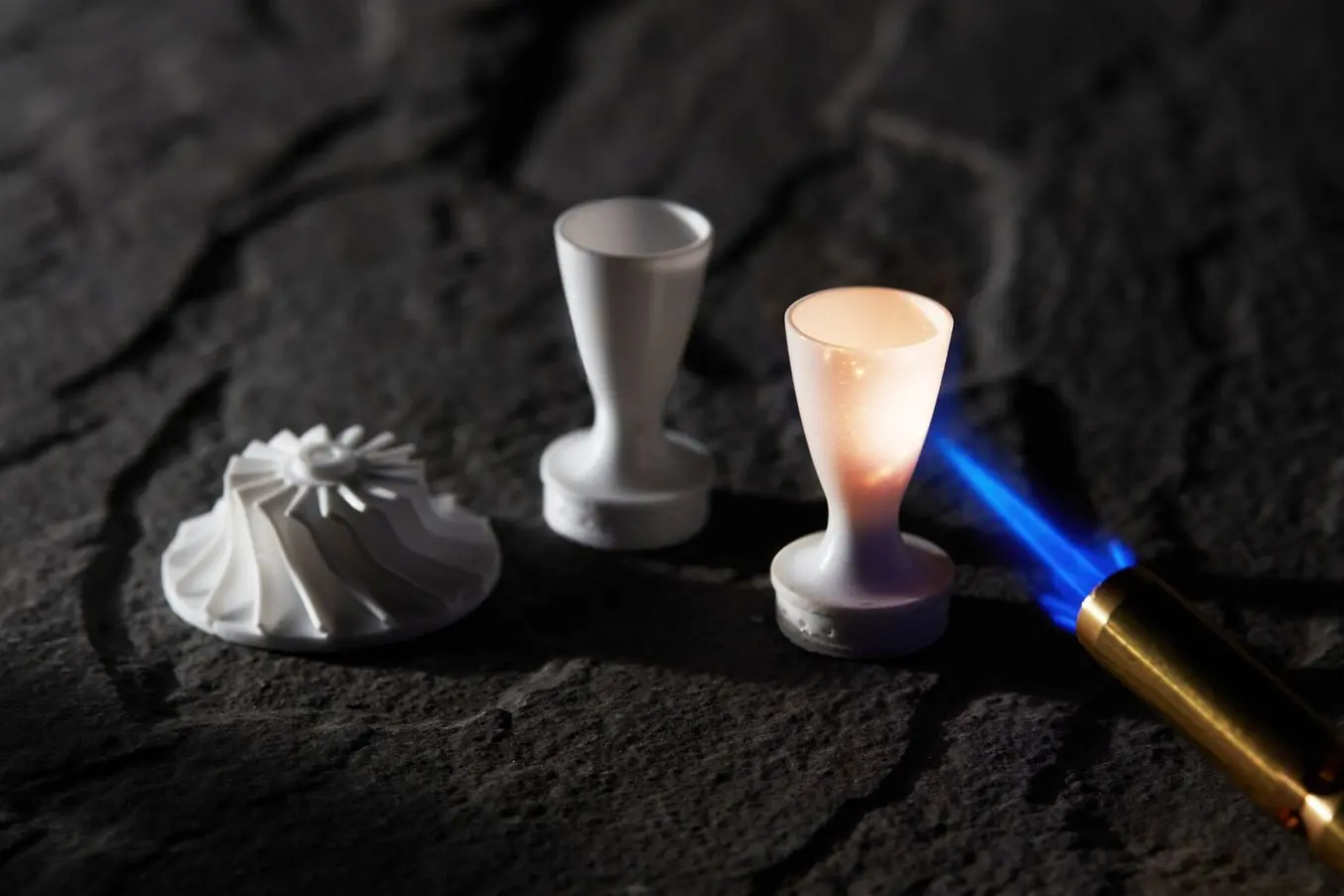
As the results of this testing show, Alumina 4N Resin parts can withstand extreme temperatures without any degradation in material properties.
Formlabs developed Alumina 4N Resin to address the need for a technical ceramic workflow that wasn’t prohibitively expensive and complicated. Previously, ceramics made for 3D printing were often only available for systems that cost upwards of $250,000, and came with complex workflows that limited users’ ability to reliably, consistently, and affordably produce 3D printed ceramic parts.
Alumina 4N Resin answers these challenges by combining the materials science and engineering behind technical ceramic materials with the ease of use, consistency, and affordability of Formlabs’ 3D printers.
Applications for 3D Printing Alumina 4N Resin
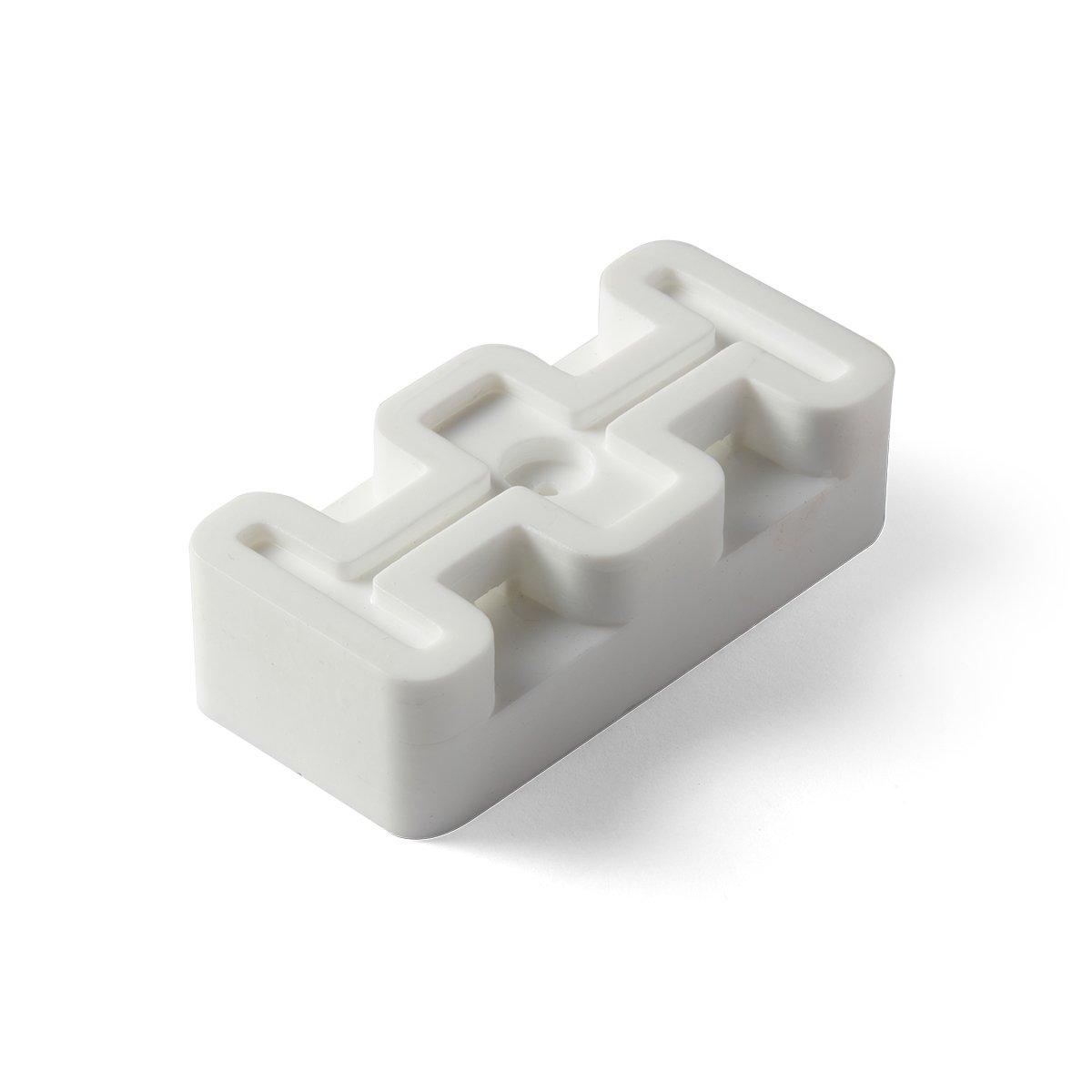
High-Voltage Applications
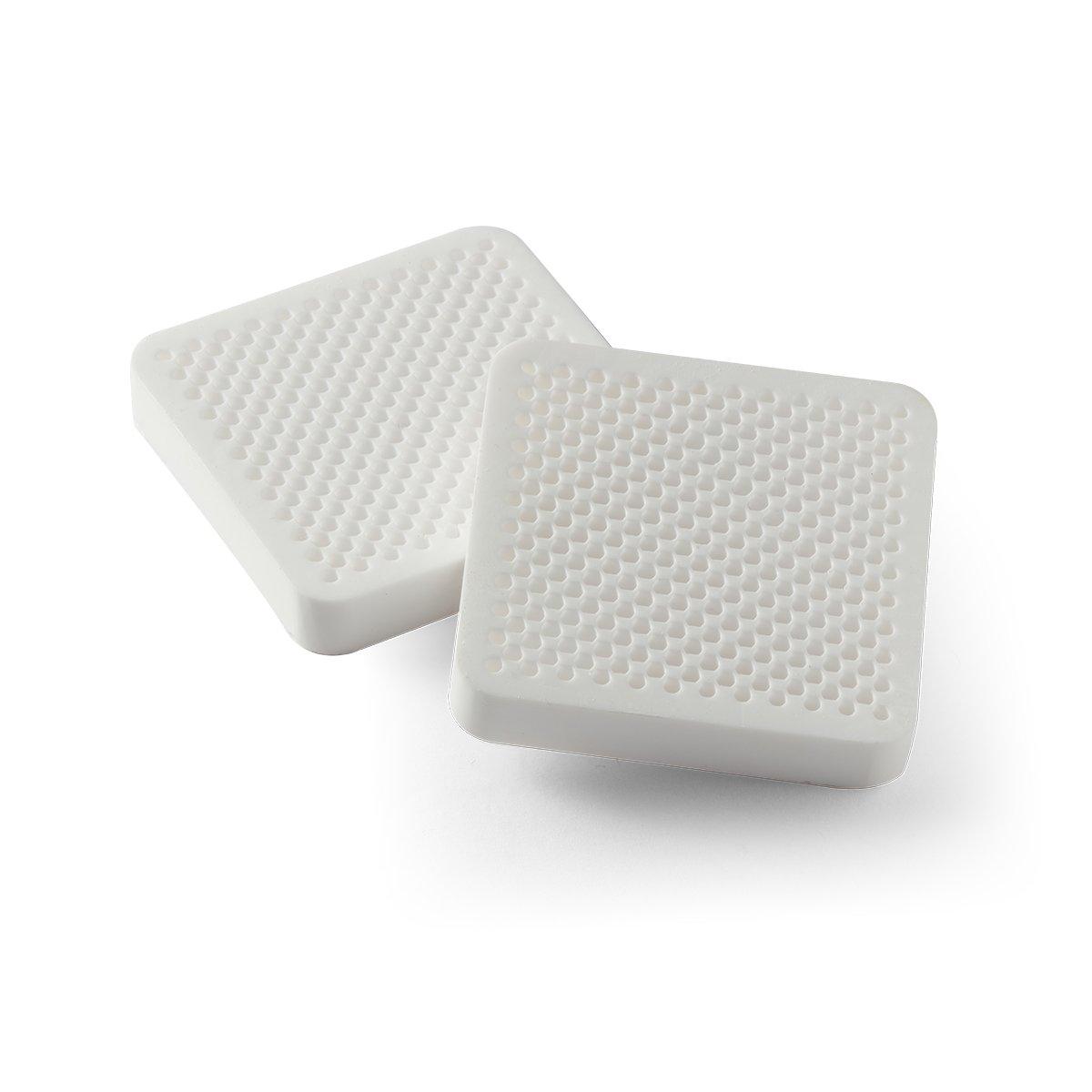
Thermal Protective Parts
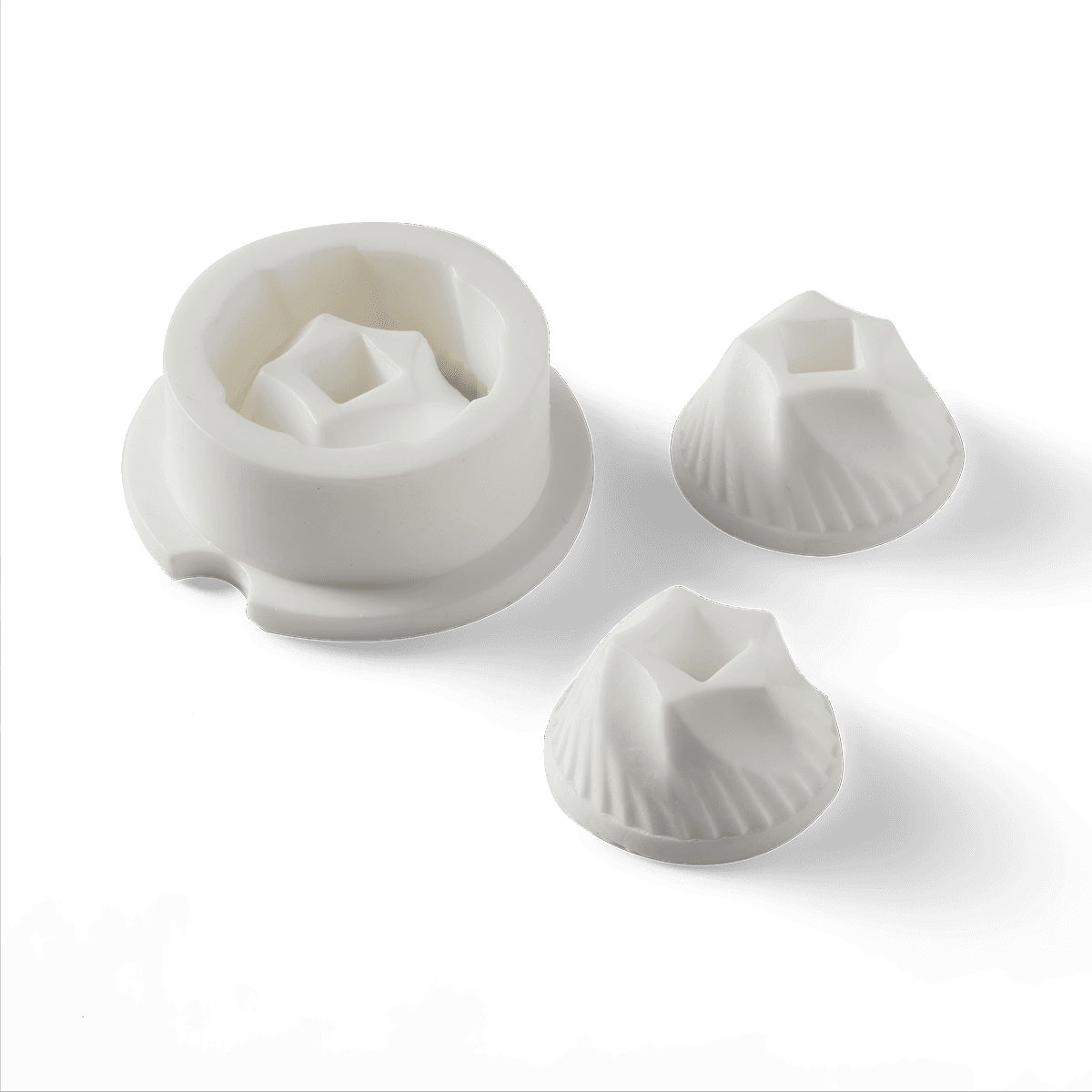
Foundry Tools for Metal Casting
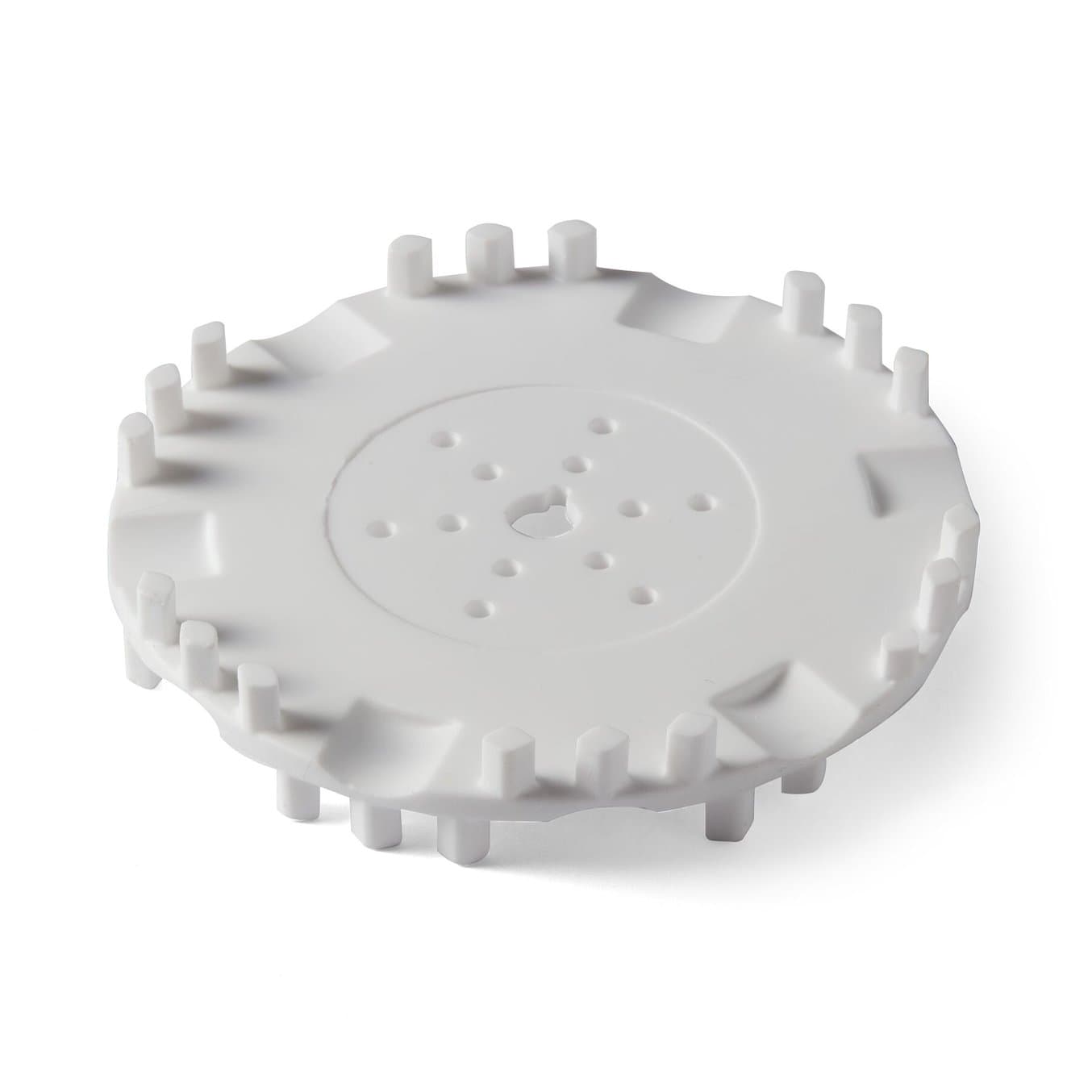
Customized Manufacturing Tools
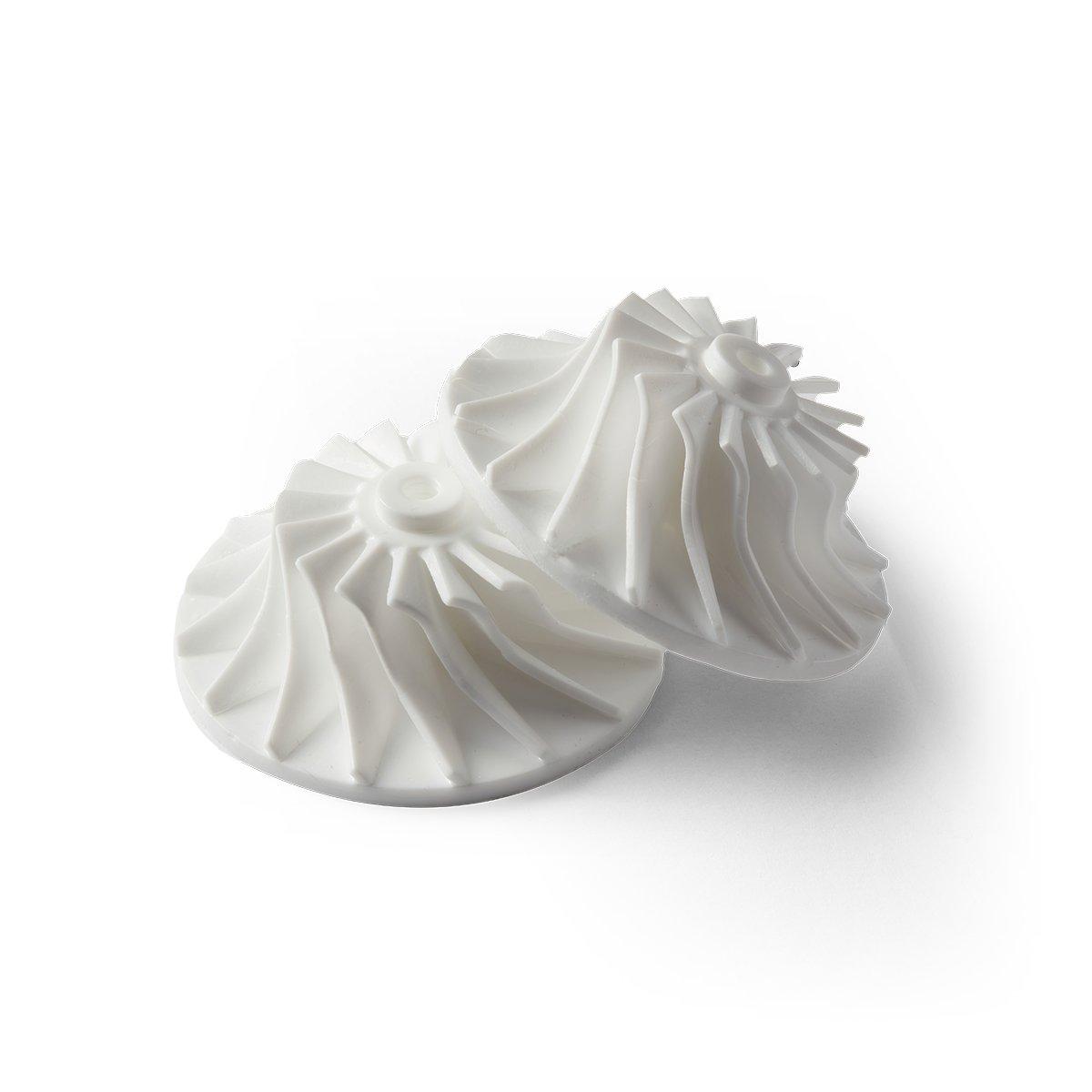
Functional Engineering Prototypes
Extreme Temperature Testing and Results
Alumina, like many ceramics, is used at extremely high temperatures, often exceeding the melting point of most metals, including all steels and even nickel superalloys. Understanding how it behaves at these temperatures is critical, and marks the difference between whether a part will succeed or fail.
The melting point of alumina is over 2000 °C, but the material begins to sag and lose its strength before reaching that point. Formlabs’ TDS recommends a maximum operating temperature of 1500 °C, but this experiment aims to show that, depending on the application, it may be successful at far higher temperatures.
Testing Procedure
The testing was conducted using a standard sag bar setup — a thin, straight bar printed in Alumina 4N Resin was suspended between two fixed points set 90 mm apart, and then heated. Using a height gauge and a granite table, the amount that the bar dropped below the two fixed points was measured and recorded.
The bars were all fired normally based on product recommendations found on Formlabs’ website. The sag testing followed a consistent pattern, heating at 5 °C/min to 400 °C under the target temperature, and then 2 °C/min to the target temperature, holding for 2 hrs.
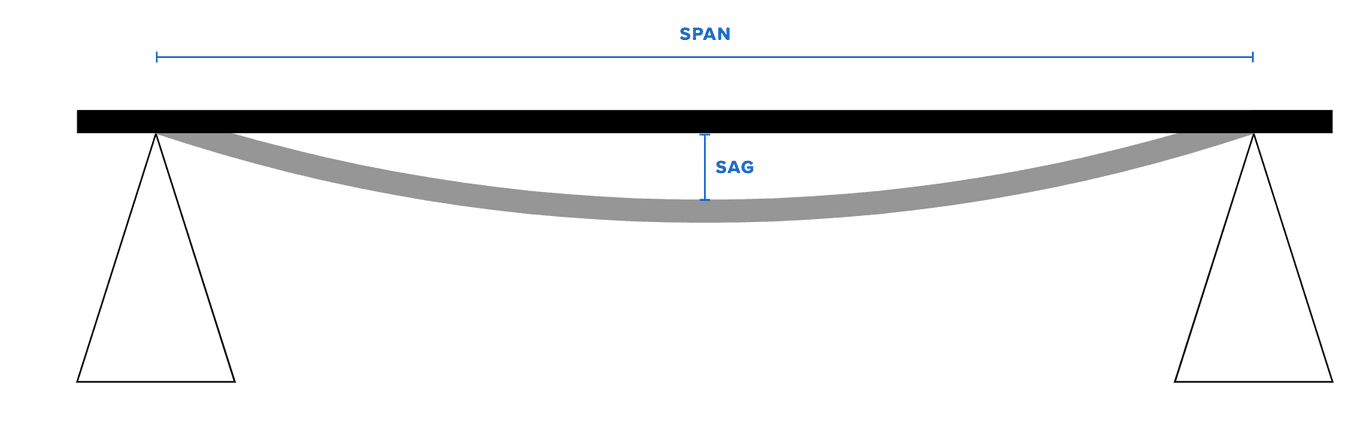
The sag bars were printed on the Form 3+ printer in Alumina 4N Resin and fired according to instructions.
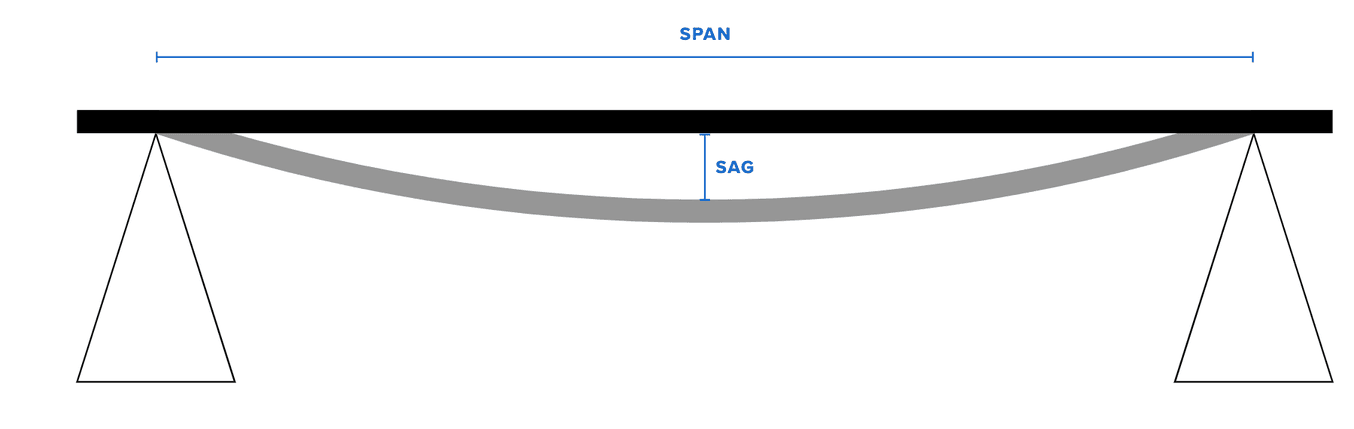
The sag bar was suspended between two fixed points set 90 mm apart before being heated.
Testing Results
The high temperature testing of Alumina 4N Resin shows it to be extremely resistant to sagging. The 2.6 mm part sagged less than 1° at 1600 °C, even on an unsupported span over 30 times as long as the height of the part. To see the full data sets, download the white paper.
For parts operating at extreme temperatures, Alumina 4N Resin is the perfect choice, and at ‘low’ temperatures below 1400 °C, will not sag or deform at all. This, in addition to the other properties of Alumina 4N Resin such as extreme electrical resistance, chemical resistance, and low permeability, make it ideally suited for many engineering applications that previously have been unobtainable for 3D printed parts.
To discuss Alumina 4N Resin for your own application, contact our team of specialists.