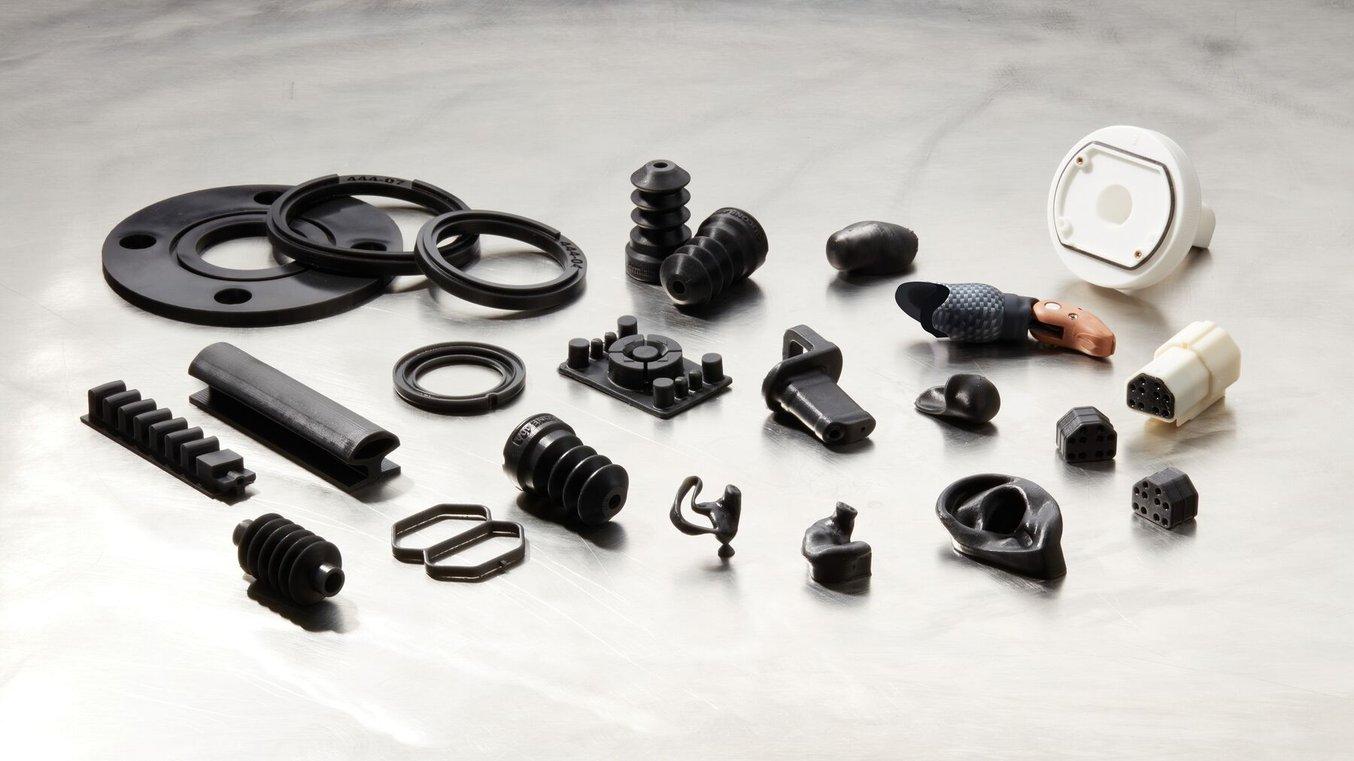
Silicone rubber is a versatile material with mechanical properties including heat-resistance and biocompatibility that make it highly suited for applications in the field of medicine. From custom hearing aids to specialized handles and grips on medical devices, soft anatomical models to prosthetics, silicone is a key material for the healthcare industry.
In this guide, we’ll outline the ways that the Formlabs ecosystem can be used to create true silicone parts for applications in healthcare. To learn the full workflow for both printing with Silicone 40A Resin, and molding silicone using Formlabs stereolithography (SLA) 3D printers, download our white paper.
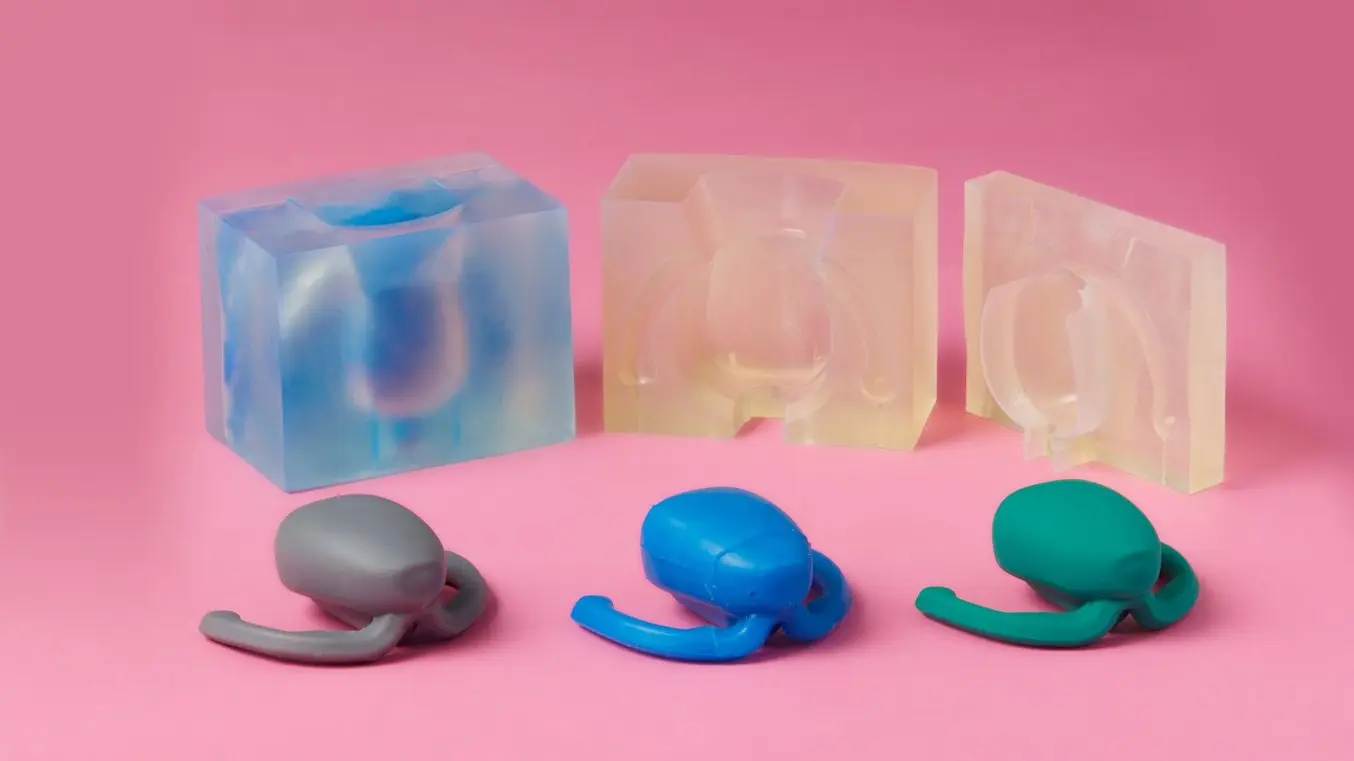
Creating Silicone Medical Devices
This guide aims to help the user decide on the best method of silicone part production for their intended use, and provides step-by-step instructions for both printing with Silicone 40A, and molding silicone using SLA 3D printed tooling (including two-part injection molds, overmolds, and compression molds).
Silicone Part Production
Soft, rubbery parts have applications across healthcare, from soft anatomical models to prosthetics and other wearables. Designers can incorporate robust, bendable, and stretchable true silicone parts into their portfolios using two methods: printing directly with Silicone 40A Resin, and molding silicone using SLA 3D printed tooling.
Silicone is a popular material used to fabricate soft end-use medical devices. It can also be used to produce soft molds for casting rigid materials, a process known as “silicone mold making.” This guide covers only silicone part production, which produces soft, rubbery parts by printing directly with SIlicone 40A Resin, or casting silicone in 3D-printed molds. More information on rigid part production using silicone mold making can be found in our guide.
Our white paper covers examples of silicone part production using a variety of different methods. These include:
-
Direct silicone printing: Silicone parts are produced directly on Form 3/B/+ resin 3D printers with Silicone 40A Resin. This method is best for producing complex geometries that cannot be achieved through molding.
-
Compression molding of silicone putty: A fast-curing silicone putty is packed into two sides of a 3D printed mold, which is clamped together with a benchtop vise. This method is often used for gasket prototypes and closely mimics tooling used in mass production.
-
Injection filled mold for liquid silicone: This is the most common method used to form a single continuous silicone prototype using a two-part or multi-part mold. In many cases the mold is configured such that gravity aids the silicone filling process. Silicone is injected into a channel at the top of the mold, and the mold cavity gradually fills from the bottom. Liquid silicone is finally released through outlets and air channels at the top of the mold.
-
Overmolding for complete or partial silicone encapsulation of hardware: Hardware is suspended in a two-part or multi-part mold. Liquid silicone is then injected into the mold cavity, either completely or partially conforming around the hardware.
-
Eggshell mold for custom silicone goods: The mold is a thin (less than 1 mm) shell that conformally envelopes the target silicone injection cavity. After the silicone is cured, the 3D printed shell-like mold is cracked away to reveal a silicone part. Since this is a sacrificial mold that cannot be reused, this technique is used to create one single custom part. A step-by-step guide on eggshell mold production is outlined in great detail here with regard to silicone ear molds.
Design, printing, and casting methods share fundamental steps even across different industries and applications. For a detailed design example for an injection filled overmold, taking into account advice and best practices provided by featured customers, read the complete white paper.
Types of Silicones
Silicones are a class of polymers that contain the elements silicon and oxygen in their molecular chain, and transform from a gel or liquid to a highly flexible and stretchable solid after curing. They are versatile materials with high-performance properties such as excellent electric insulation, heat resistance, chemical stability, high tear strength, and biocompatibility, making them attractive for highly-demanding industries like healthcare.
Silicone elastomers dominate the market and can be divided into three categories:
-
Liquid silicone rubbers (LSR) are high performance silicones usually employed for producing strong, technical parts with tight tolerances, such as seals or electronic connectors. They are processed at high temperatures, often through liquid injection molding, and are selected for large volume production.
-
High temperature vulcanized (HTV) silicones, also called Heat Cured Rubber (HCR) silicones, offer great temperature and aging resistance ideal for cables or insulators in medical devices. They generally employ a platinum-cure chemistry, and are shaped by extrusion or compression molding with vulcanization under pressure and heat. Discover how the silicone expert SIOCAST forms HTV silicone molds around 3D printed master patterns.
-
Room temperature vulcanized (RTV) silicones are relatively easier to process, with great mechanical and thermal properties for gaskets and medical devices, as well as encapsulation of electrical components and mold making. They are traditionally shaped at room temperature by injection molding, compression molding, or gravity casting.
This report covers the usage of room temperature vulcanized (RTV) silicones. It describes techniques that can be used in-house in any prototyping or product development lab. Some specific forms of RTV silicones include:
-
Silicone 40A Resin: Silicone 40A Resin is a one-part RTV silicone resin that produces 100% silicone parts with excellent elasticity, chemical resistance, and thermal stability. Parts are printed directly on the Form 3/3B and post-processed using a mixture of isopropyl alcohol (IPA) and n-butyl acetate, then water, heat, and UV light.
-
RTV liquid silicone: Liquid-type silicones are typically two-part or single-part with a small amount of catalyst added. There are two general categories that are readily available. Platinum-catalyzed silicones are higher cost but offer superior long-term dimensional stability and very low shrinkage after full cure. Tin-catalyzed silicones are lower cost but less stable over time, and tend to have higher shrinkage rates. Curing time ranges from 10 minutes to several hours.
-
Polydimethylsiloxane (PDMS): PDMS is a chemically distinct type of RTV liquid silicone that contains methyl groups on the silicon-oxygen polymer chain. The liquid polymer is very commonly used as a lubricant or viscous additive in consumer and industrial goods. As a cured rubber, PDMS is used in a number of research applications. Its high optical transparency and ability to capture micro-scale surface textures and channels make it ideal for microfluidics and soft lithography. Many PDMS formulas will cure at room temperature over a period of 48 hours, or cure in less than one hour at elevated temperature.
-
Silicone putty: This is a two-part putty in which components are blended together in equal volumes by hand. The type featured in this report has a durometer rating of Shore 40A (see scale below), or a hardness similar to a pencil eraser. This type of silicone can be purchased from jewelry suppliers as it is commonly used for producing wax masters for metal casting. However, the silicone itself is also a good mimic for compression molded gaskets and seals.
Skin, Mucous Membrane, and Food Safety
Some applications require more sensitivity than others when it comes to contact with the body or contact with food. Always check the material safety data sheet (MSDS) from the silicone manufacturer to make sure the material is safe for your application. Note that two part liquid silicones that are rated for skin safety tend to use a platinum catalyst.
Silicone 40A Resin is currently being evaluated as a skin contacting device in accordance with ISO 10993-1 for the following biocompatibility endpoints: ISO 10993-5:2009, 10993-23-2021:2021, ISO 10993-10:2021.
Durometer Rating Scale
Rubbery materials, including silicone rubbers, can be formulated to a range of hardnesses from extremely soft to extremely firm, as indicated by a specific Shore durometer number. Softer materials are measured on the Shore A scale, and harder materials on the Shore D scale. The table shown below provides a helpful comparison to common household goods.
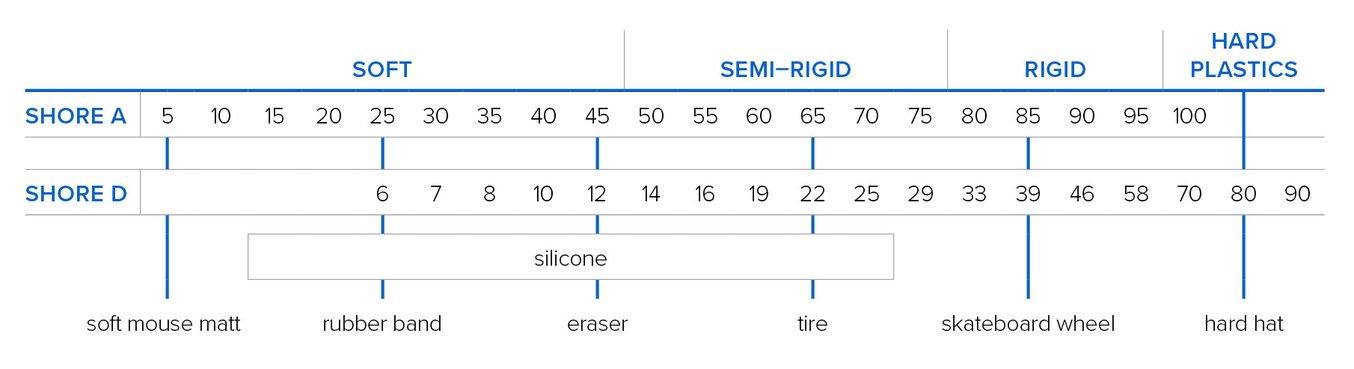
Deciding to Print or Mold
The specific requirements of your application and workflow will dictate whether direct printing or silicone molding is the optimal method. Here are some specifics of each process to consider:
-
Complex geometries: Not all geometries are achievable through molding. Direct printing is preferable for applications requiring complex geometries.
-
Color: Silicone 40A Resin is black. For applications that require clarity or colored parts, silicone molding may be a preferable option.
-
Time: Designing parts for direct printing takes less time than designing molds. Also, the time required to print a single silicone part is significantly less than the time required to print a mold and then fill it with silicone. When time is a concern, direct printing is generally preferred.
-
Scent: Silicone 40A finishes printing with an odor that can take time to dissipate. This process can be expedited by curing your printed part in a mixture of water and Febreze HD, but silicone molding may be preferable for applications where the scent of the material is an immediate concern.
-
Biocompatibility: Different types of silicone have different levels of biocompatibility. Silicone 40A Resin is currently being evaluated for skin contact in accordance with ISO 10993-1. Silicone molding may be preferred for applications requiring more extensive levels of biocompatibility.
-
UV exposure: The mechanical properties of Silicone 40A Resin will degrade after repeated exposure to UV light. For applications where the parts are going to spend lots of time in direct sunlight, silicone molding is likely preferable.
For medical applications requiring rubbery parts where silicone is not a good fit, you may want to consider alternative Formlabs elastomers, such as BioMed Elastic 50A Resin for SLA or TPU 90A Powder for SLS 3D printing.
Material | Printer | Ultimate tensile strength | Stress at 100% elongation | Elongation at break |
---|---|---|---|---|
Formlabs Silicone 40A Resin | Form 3/B/+ | 7.2 MPa | 4.5 MPa | 135% |
BioMed Elastic 50A Resin | Form 3/B/+ | 2.3 MPa | 1.3 MPa | 150% |
TPU 90A Powder | Fuse 1+ 30W | 8.7 MPa (X/Y) 7.2 MPa (Z) | 7.2 MPa (X/Y) 7.0 MPa (Z) | 310% (X/Y) 110% (Z) |
Overview of Printing With Silicone 40A Resin
Silicone 40A Resin utilizes patent-pending Pure Silicone Technology™ and Formlabs’ stereolithography (SLA) ecosystem, enabling the in-house production of 100% silicone parts in a matter of hours. It is ideal for applications requiring pliability, durability, and resistance to repeated stretching, flexing, or compression.
Material Property | Silicone 40A Resin |
---|---|
Shore durometer | 40A |
Elongation at break | 230% |
Tear strength | 12 kN/m |
Rebound resilience | 34% |
Temperature range | -25 °C to 125 °C |
The applications for Silicone 40A Resin are diverse, ranging from rapid prototyping, beta testing, and validation stages in product development to cost-efficient low-volume or custom manufacturing of end-use parts. The material is also suitable for manufacturing medical devices, patient-matched prosthetics, audiology components, and for the production of parts with complex geometries that are challenging to manufacture through traditional methods.
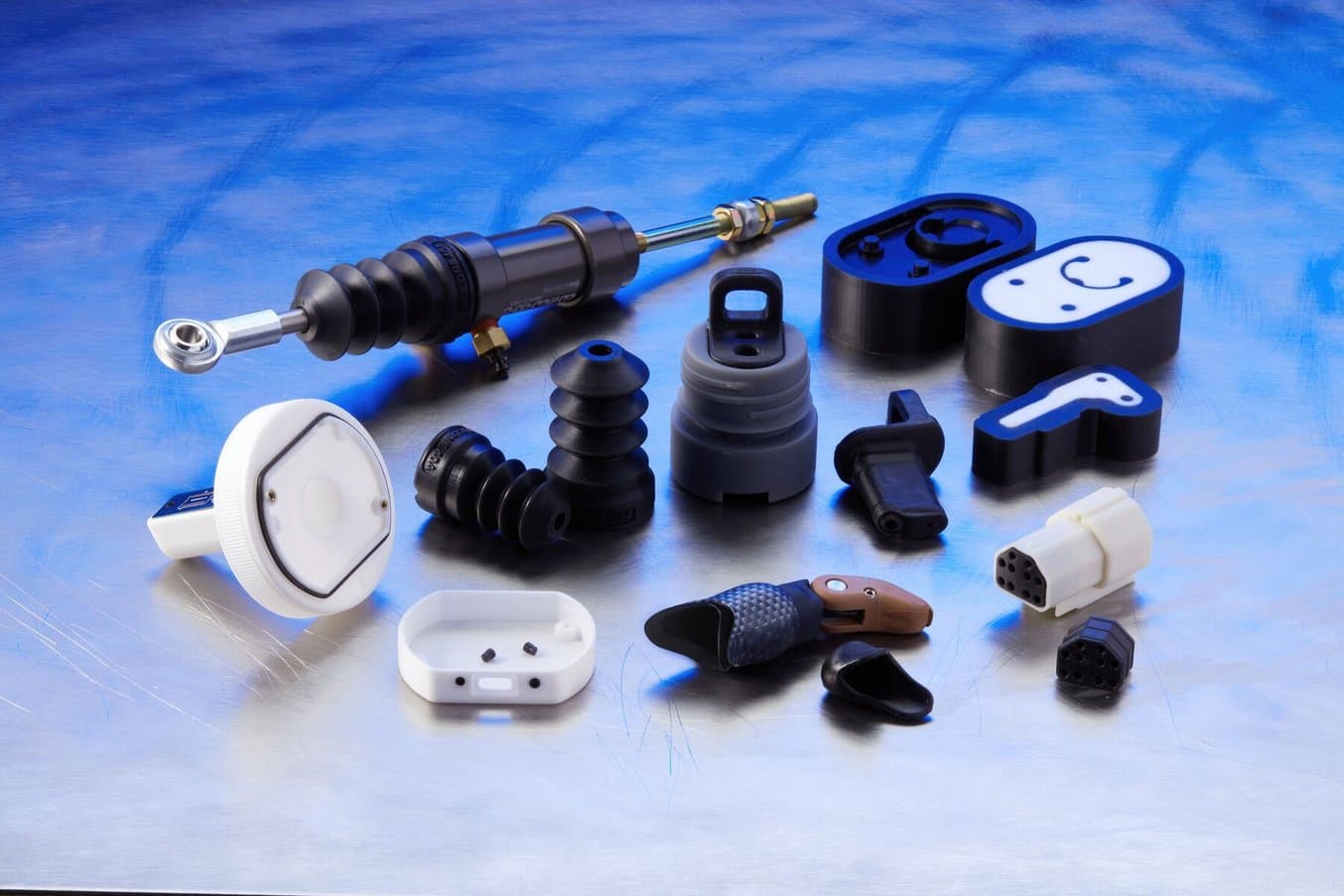
Direct silicone 3D printing with Silicone 40A Resin is ideal for a wide range of applications, from rapid prototyping to manufacturing aids, tooling, and low volume or custom manufacturing.
The introduction of Silicone 40A Resin addresses longstanding challenges associated with traditional silicone 3D printing methods, such as high costs and technical limitations. One-touch printing with Silicone 40A Resin saves time by eliminating the need to design and manufacture molds, and pour and cast silicone. It also opens up design possibilities by enabling the users to create complex geometries that are difficult to achieve using traditional manufacturing methods. This accessible solution allows businesses to create high-quality end-use parts without compromising on price, quality, or speed.
Overview of Silicone Molding 3D Printed Tooling
Traditional molds for silicone part production are CNC machined from blocks of aluminum or steel. These include two-part or multi-part injection molds for liquid silicone rubbers (LSR), or single cavity compression molds used with a heat cured rubber (HCR) silicone sheet that is cured under pressure and high temperature. Normally these types of metal molds are used in mass production. However, when employed for prototyping, lead times of several weeks and upfront tooling costs of hundreds to thousands of dollars limit a designer’s ability to implement and test small changes in a mold design.
Desktop 3D printing is a powerful solution to fabricate tools rapidly and at a low cost. It requires very limited equipment and enables skilled operators to focus attention on other high-value tasks. With in-house 3D printing, manufacturers and product designers can introduce rapid tooling into the product development process to validate design and material choices prior to transitioning to mass production. They can iterate quickly, accelerate product development, and bring better products to market. 3D printed tooling using Formlabs SLA resins offers many advantages to product designers across prototyping, small-scale production runs, and custom part production. Using 3D printed tooling, RTV two-part silicones are injected into a two-part or multi-part mold or an RTV silicone putty is squeezed between sections of a 3D printed compression mold. Using 3D printed tooling, a broad range of tin cure and platinum cure silicones are available to designers, including a wide range of durometer ratings, colors and degrees of transparency, as well as special functions such as skin safety.
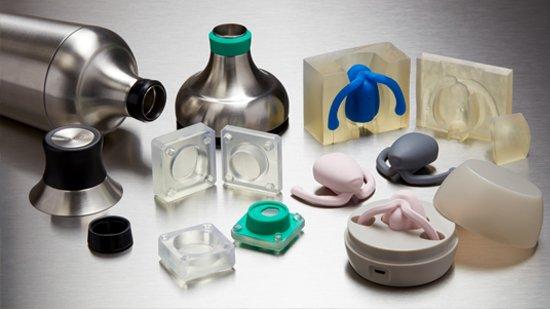
Silicone Part Production With 3D Printed Tools
This report provides a step by step guide on 3D printed tooling for silicone part production, with best practices and customer case studies.
Stereolithography (SLA) 3D printing technology is a great choice for silicone mold tooling. SLA parts are characterized by a smooth surface finish and high precision. RTV silicone rubbers capture fine surface details including defects, so the quality of the tool surface directly translates to the surface quality of the final part. A mold printed with a fused deposition modeling (FDM) printer, for example, would leave visible impressions of printer layer lines in the silicone part.
By contrast, SLA 3D printing with Formlabs BioMed Clear Resin or Clear Resin allows for visualization of the silicone injection process, enabling designers to assess bubble and void formation, and identify areas where corner fillets or additional air vents should be added. SLA 3D printing also offers an advantage for design complexity; a 3D printed mold allows designers to take advantage of undercuts or other complex geometries that may not be possible or would be prohibitively expensive to produce with CNC machining.
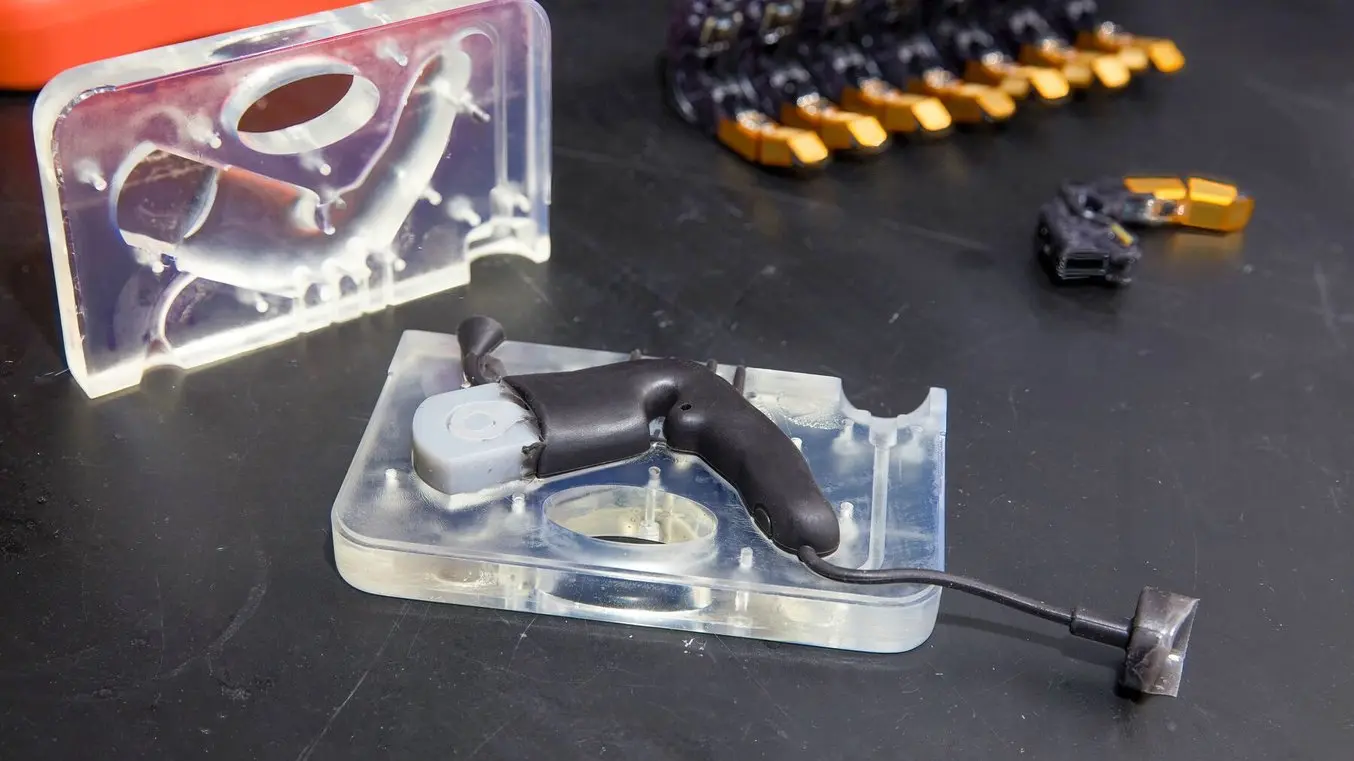
PSYONIC encapsulates the Ability Hand fingers using a silicone overmold configuration. Some molds include a Tough 2000 Resin mold insert to anchor the encapsulated “bone” feature in the mold.
Formlabs BioMed Clear Resin and Clear Resin are also quite versatile in their mechanical performance. The same material can be used for an extremely thin eggshell mold that cracks away easily from a custom silicone part, or for a robust compression mold that is used multiple times to produce gaskets. Finally, using affordable benchtop scale fabrication reduces lead times; a designer can print a mold geometry and start injecting silicone the next day.
When used with 3D printed molds, RTV silicone rubber captures fine surface details, including embossed text. In addition, most castable silicones are not chemically adhesive and will peel away from the mold surface after curing. Mechanical bonding can be achieved by casting onto highly porous surfaces like woven fabric. In some cases, chemical bonding can be promoted with specialized binders.
Because processing RTV silicone does not require high heat or pressure, it can easily be formed with limited equipment in a prototyping lab, reducing the startup cost needed to introduce soft parts to any company's design portfolio. Guidelines for manufacturing silicone parts quickly and affordably at low volume in-house are included in the complete white paper.
Start Creating Silicone Medical Devices
The applications for silicone are diverse, ranging from rapid prototyping, beta testing, and validation stages in product development to cost-efficient low-volume or custom manufacturing of end-use parts. Formlabs' ecosystem makes it possible to 3D print in Silicone 40A Resin and print silicone molds for manufacturing medical devices, patient-matched prosthetics, audiology components, and for the production of parts with complex geometries that are challenging to manufacture through traditional methods.
For the complete guides to both 3D printing silicone molds and silicone printing, download the white paper.