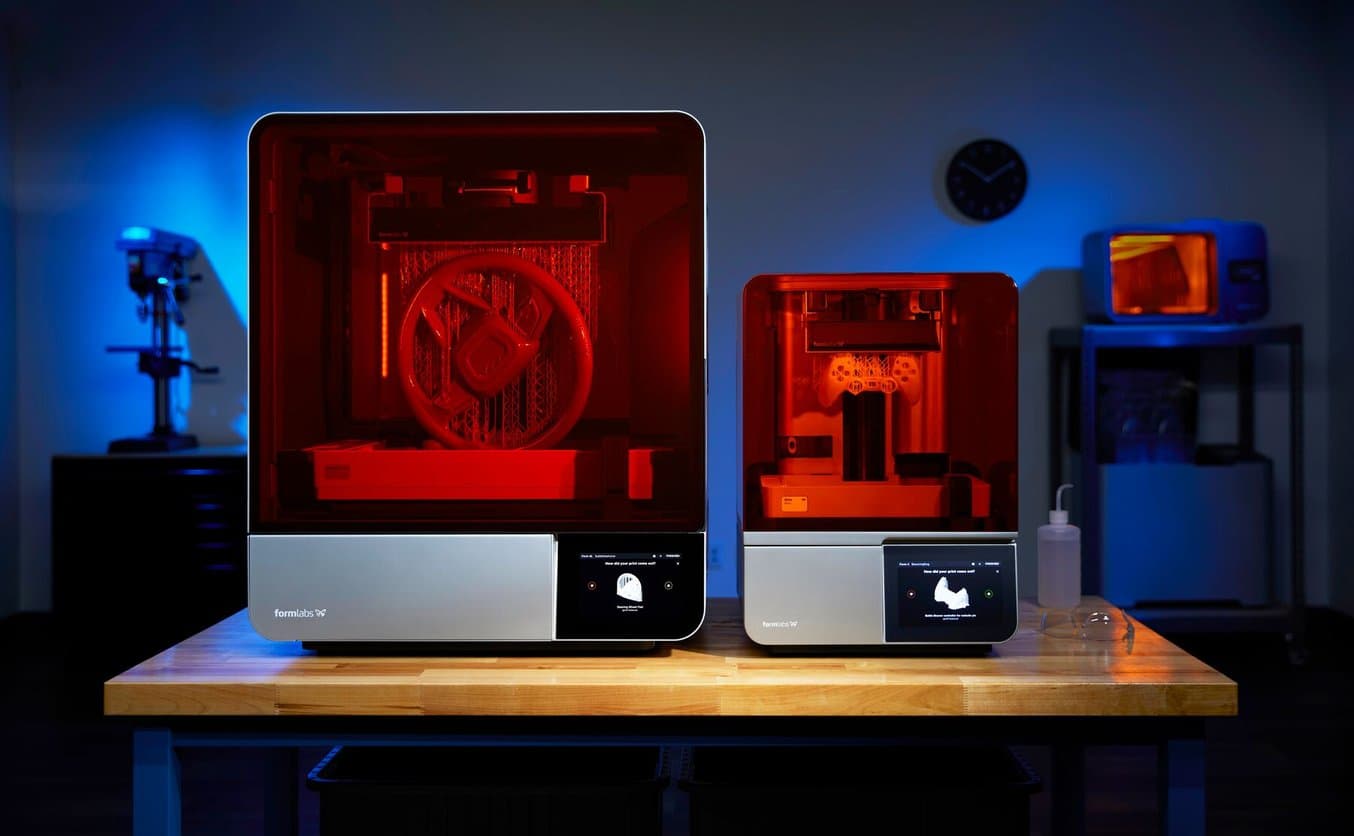
On April 17, 2024, Formlabs announced Form 4, our next-generation resin 3D printer that redefines the industry standard for speed, accuracy, reliability, and material versatility. Six months later, we announced Form 4L, a large-format resin 3D printer built on the same groundbreaking hardware, software, and materials science innovations as Form 4.
Form 4 Series 3D printers, including biocompatible printers Form 4B and Form 4BL, deliver unmatched speed, accuracy, and reliability, redefining the standards of 3D printing. But you don’t have to take our word for it. In this review roundup, we’ll take a look at what 3D printing experts are saying about Form 4 and Form 4L.
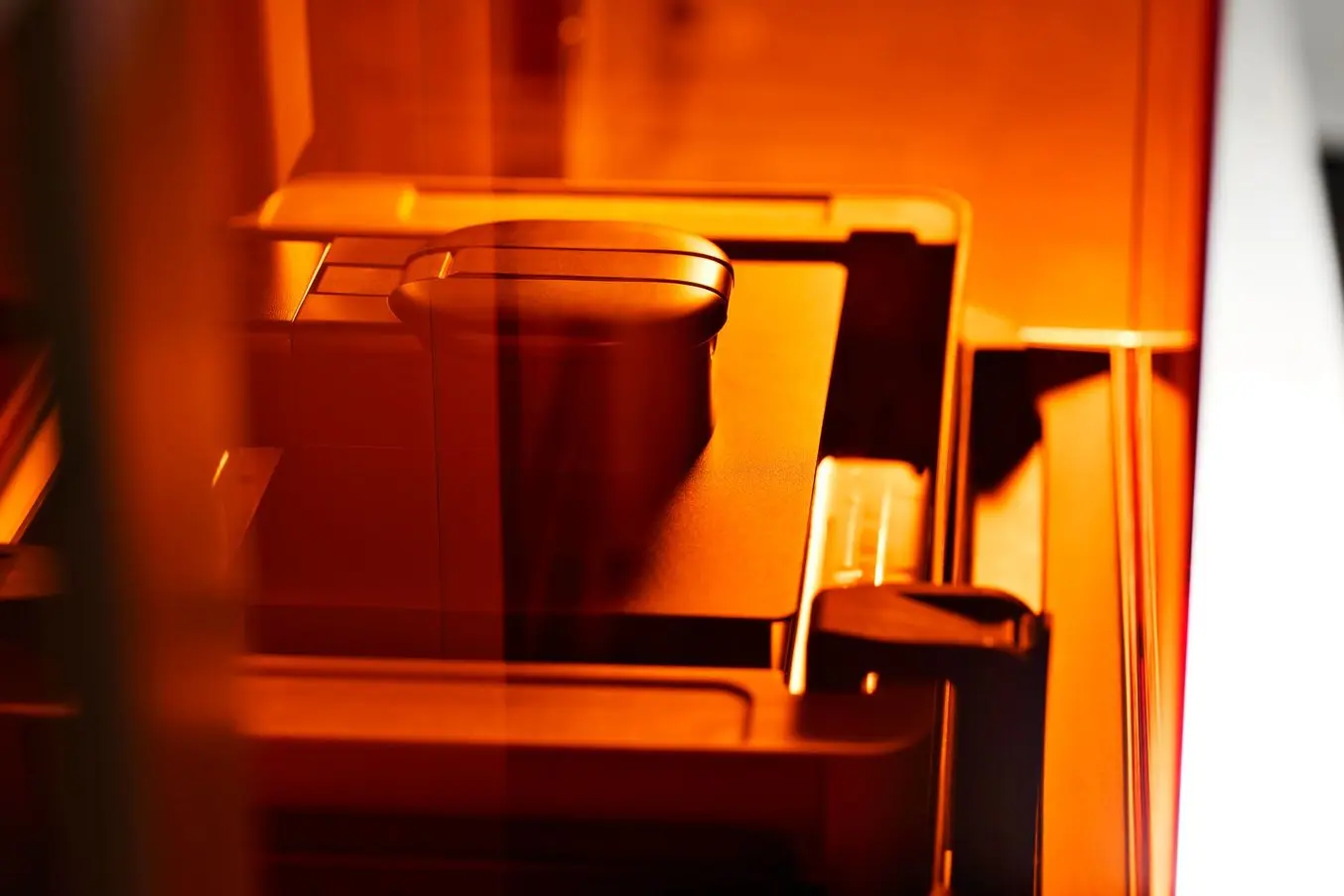
Product Demo: Form 4
See how Form 4 can enable new levels of productivity and innovation through its unmatched speed, accuracy, and reliability.
TechRadar
“An outstanding resin 3D printer that delivers high-end production quality prints in a compact form.”
Alastair Jennings, TechRadar
Alastair Jennings wrote a glowing review of Form 4 for TechRadar. He starts by looking at the entire ecosystem, saying “The vast selection of specialist materials and a high-quality ecosystem that includes wash and cure machines as well as a finishing station make this one of the most complete and user-friendly options on the market.” He also points out the ease of use and flexibility offered by the extensive materials library before breaking down the features.
“The Form 4 impresses with some of the speediest, most accurate, and detailed prints we've seen from any 3D printer yet.”
Alastair Jennings, TechRadar
Jennings details unboxing the Form 4, noting similarities to Form 3+ in terms of look, size, and ease of setup. Moving to testing prints, he found that larger pre-supported models could fail by falling from supports. However, he says that while this issue occurs with many high-speed printers, the advanced sensors of the Form 4 helped to mitigate this issue, and switching to PreForm-generated supports achieved a 100% print success rate.
Jennings pitted Form 4 against the Creality K1C, finding that Form 4 reduces time when running small production runs. Printing nine 3DBenchy models took one hour and 12 minutes on Form 4, while printing the same task on the Creality K1C drastically increased to 15 hours and 47 minutes with supports. Plus, the prints from Form 4 were higher-quality, with better details and easier support removal.
“Print quality and reliability are outstanding, and the overall user experience represents a significant step forward, making this a viable solution for businesses wanting to prototype, model or manufacture on-site.”
Alastair Jennings, TechRadar
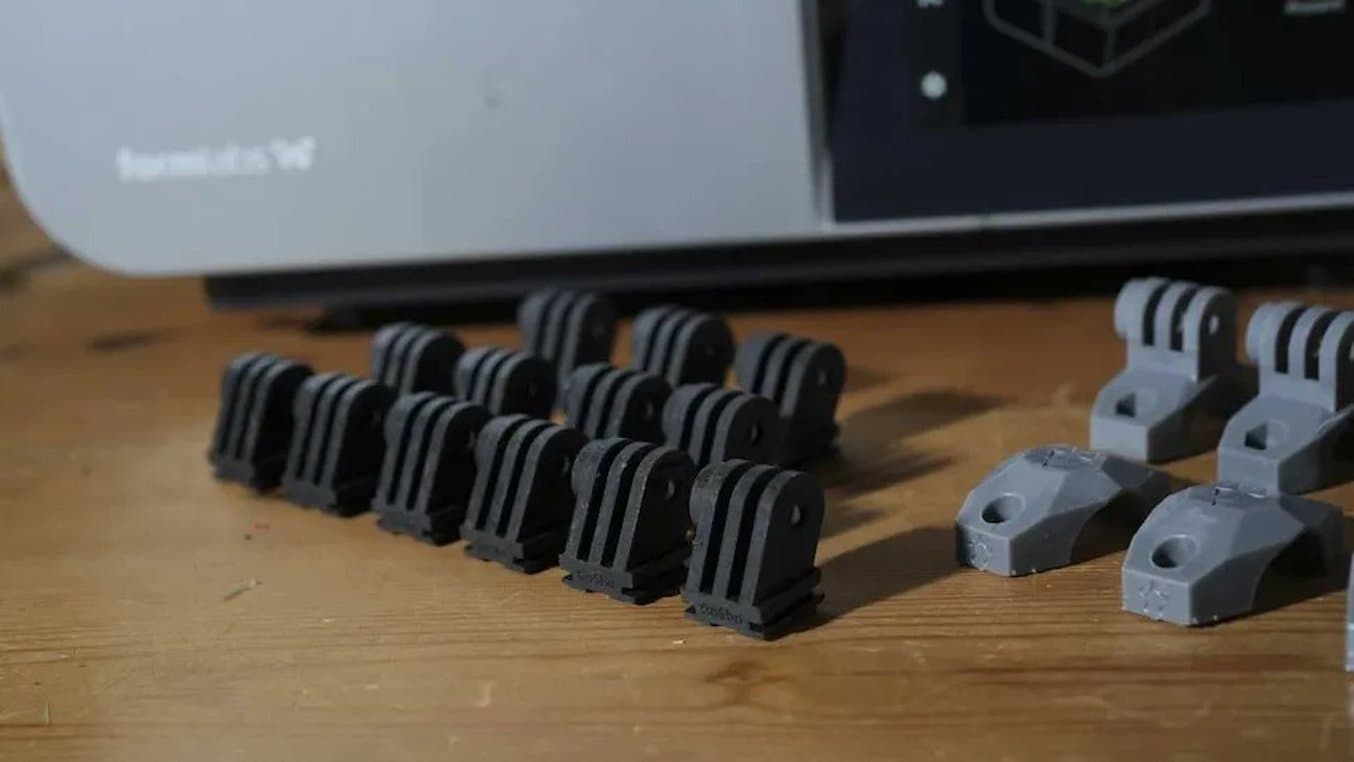
(Image credit: Alastair Jennings)
For post-processing, it was noted that “The Wash and Cure machines, while optional, are nearly essential for achieving the best results and are among the best in their class.”
Ultimately, Jennings says that “the enhanced user experience and additional features make the Form 4 a worthwhile upgrade from the Form 3+” and “For those looking for one of the most reliable, high-quality, and least messy resin 3D printers on the market, the Form 4 has little competition at this price point.”
Scoring Chart From TechRadar
Value | Exceptional quality at a competitive price point. | 4.5 |
---|---|---|
Design | Sleek, user-friendly design with an efficient resin system. | 4.5 |
Features | Packed with innovative features for advanced printing. | 5 |
Performance | Outperforms competitors in speed and precision. | 5 |
Total | An outstanding 3D Printer that sets industry standards. | 5 |
“Form 4 stands out in two particular areas: its accuracy, quality, and reliability for intricate details and complex objects [...] offering unmatched ease of consistency. Throughout testing, 8 liters of resin—clear, grey, and black—were used without a single issue, a stark contrast to some of the best, cheaper printers that often encounter failures.”
Alastair Jennings, TechRadar
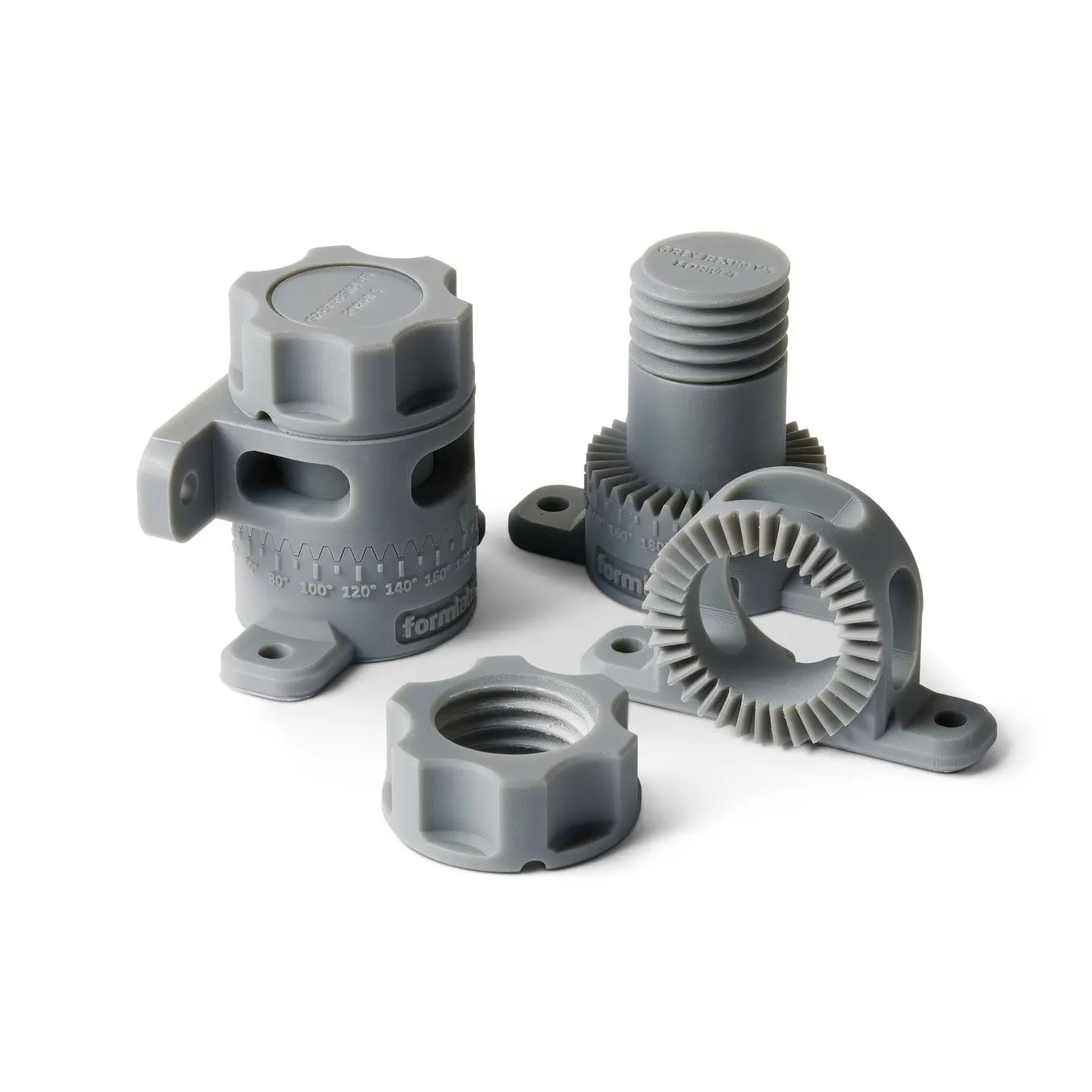
Request a Free Sample Part
See and feel Formlabs quality firsthand. We’ll ship a free 3D printed sample part to your office.
Tom’s Hardware
“The Formlabs Form 4 is a premium 3D printer for people who demand high quality, ease of use, and reliability[…] The company provides a wide range of performance materials for every application, including medical, and we find it to be one of the best resin 3D printers and best 3D printers overall.”
Denise Bertacchi, Tom’s Hardware
In a review titled “Fail Proof Business 3D Printing: Perfect prints are as easy as a game of connect the dots.” Denise Bertacchi walks through Form 4. As someone who never enjoyed resin printing, Bertacchi realizes this is a direct result of the printers she was using.
“Consumer-level resin 3D printers — and their associated wash and cure stations — are not only messy but also require too much guesswork. Formlabs eliminated the guessing game by creating a tightly controlled and thoroughly tested ecosystem. That ecosystem also includes all the tools you need for cleanup and a cleverly designed user interface that reduces the mess.”
Denise Bertacchi, Tom’s Hardware
Bertacchi says that the technology of the tightly-locked Form 4 ecosystem is both its benefit and biggest flaw, as third-party resins require purchasing Open Material Mode and dialing in, yourself, “the perfectly orchestrated chain of events” users experience when printing with Formlabs materials.
“The system is designed for businesses that need a steady flow of perfect prints every time… If you follow the guidelines in the slicer, you will get good parts. Using Formlabs Form 4 is so simple that it can be run by an intern or Bob from accounting.”
Denise Bertacchi, Tom’s Hardware
From the guides and videos on the Formlabs website to the color, on-screen instructions on the Form 4 touchscreen, the ease of the Formlabs ecosystem is evident to Bertacchi. Unlike most printers she’s tested, the printer included what she needed to get started, except isopropyl alcohol (IPA). Even unpacking the printer was easy as it comes fully assembled.
“The Formlabs Form 4 is a beautifully built machine with superior attention to detail,” says Bertacchi, noting the flip-top lid is easy to use and the non-stick surface that prevents the resin tank from getting stuck to the printer.
Moving on to resin handling, Bertacchi highlights automated resin dispensing, easy resin tank storage, quick material changeovers, a resin mixer, debris detection, and RFID tags in both the resin cartridge and tank, eliminating the possibility of accidentally mixing materials. Additionally, the added sensors prevent mess when filling the resin tank, and in the case of print failures.
Additional callouts include:
-
Build Platform Flex, for easy removal of printed parts
-
Form Wash automatic lid opening and automated wash basket lift
-
Integrated camera for both still shots and time-lapse
-
PreForm software with presets for resin, support generation, model hollowing, and advanced settings editor
-
Dashboard to track print history and resin consumption
-
Material clarity
“The Form 4 “only” has 4k resolution, which may sound inferior to the latest batch of consumer-grade printers with double or triple the number of pixels. But this machine proves something I’ve always suspected: sharp details are more about the material than the pixel count. The Form 4 produces crisp, clean prints with an amazing level of detail and accuracy.”
Denise Bertacchi, Tom’s Hardware
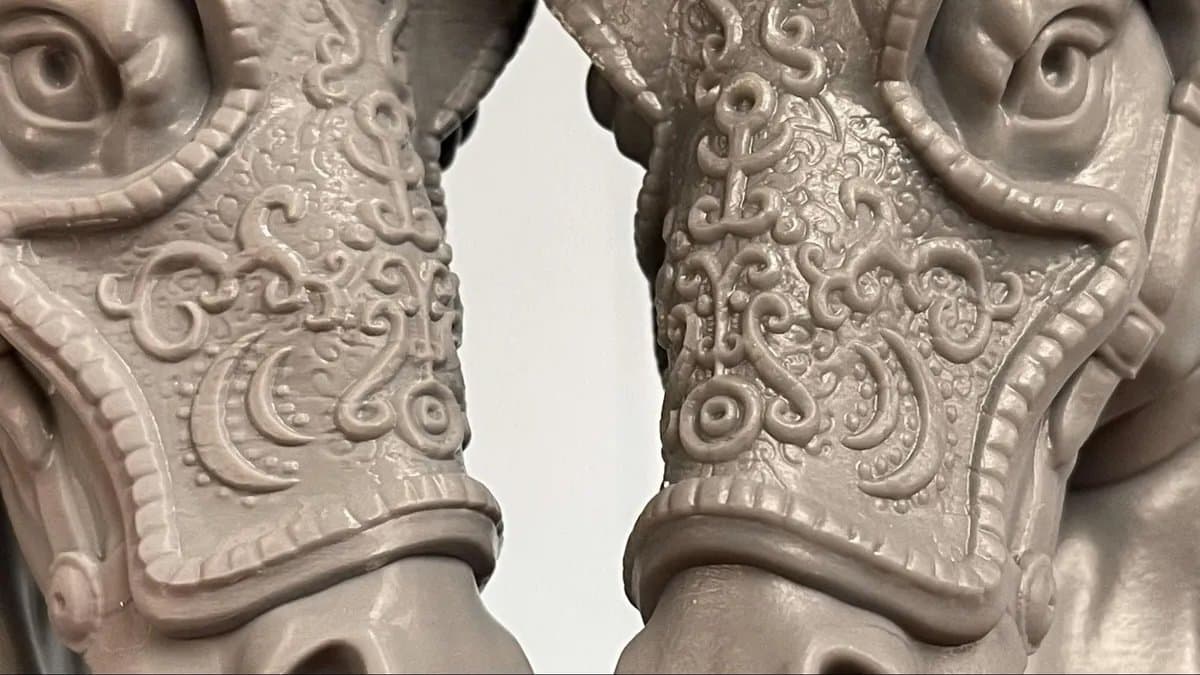
Bertacchi printed the sample on the left with a Phrozen Sonic Mega 8k S, and the one on the right with Form 4. Image credit: Tom's Hardware
“I just can’t get over the clear, crisp details the Form 4 can produce…The Phrozen machine is aimed at the same commercial market, and has a 43 µm resolution – compared to the Form 4’s 50 µm. You can clearly see the Form 4 has cleaner details that appear less blurred.”
Denise Bertacchi, Tom’s Hardware
Bertacchi’s test prints exemplify that resolution is not the defining metric for print detail and quality. Rather, multiple stats and features affect final print quality.
Ultimately, Bertacchi sees Form 4 as “a great tool for businesses who need perfect parts for production or prototyping, and don’t have time to waste on tinkering around with the printer.” And though the price tag pushes it out of the consumer market, “This kind of machine would also be an excellent tool for school and university programs where you want to spend time designing and producing parts. The helpful guides on the user interface and the constant reminders to follow procedures allow makers to concentrate on their design skills and less on their knowledge of chemistry.”
3DPrint.com
Form 4
We shared a Form 4, Form Wash, Form Cure, and General Purpose Resins with Jay Rincher at 3DPrint.com to see what he thought. As someone new to resin 3D printing, he was a little nervous at first, but “found that the workflow is so simple and the slicer so intuitive, I doubt that there is anyone who couldn’t be trained to use one of these machines in about an hour.”
Rincher walks through the entire process of unboxing, setting up, printing, and post-processing. Unboxing and setup proved to be easy, with clear prompts from the printer touchscreen, but he ran into issues sourcing isopropyl alcohol for the Form Wash, which can hold up to 15 liters for the washing of large parts.
While Rincher found PreForm to be intuitive, the biggest issue was with cups on his models, which he could not automatically vent via PreForm’s features. This aside, he says, “the printing process itself is painless. There really is no real learning curve to using this machine. It is as plug-and-play as they come and on-boarding employees unfamiliar with resin printing would be fairly simple.”
“I’ve often heard resin printing described as smelly, messy and hazardous. I’m sure that probably remains the case for the experience with many lower-end devices, but I found the complete opposite with the Form 4. The printing experience was largely smooth, effortless, and consistent."
Jay Rincher, 3DPrint.com
Rincher’s test prints included models, earrings, a fidget toy with working threads, and dental models. He found that components printed in multiples were identical and that the threads on the fidget toy worked in all the materials he tried.
“Any business looking to add high-speed SLA printing to its capabilities would be well advised to see if this machine fits their needs.”
Jay Rincher, 3DPrint.com
Form 4L
“Overall, the Form 4L is a valuable asset for businesses that need a fast, accurate, and versatile 3D printing solution.”
Orville Wright, 3DPrint.com
Wright opens his review with unboxing, finding the packaging to be exceptionally sturdy for protection while shipping white straps made it easy to unbox the printer. Once unboxed, he found Form 4L was made with high quality materials that would make for a durable printer.
Wright’s first test print was a 350 mm tall Eiffel Tower model at 50 µm which he printed in ~13 hours. He writes, “This impressive speed, coupled with the intricate details captured in the Eiffel Tower model, demonstrated the Form 4L’s potential for high-quality, rapid production.”
Diving into the hardware and specs, Wright ultimately says that Form 4L “delivers impressive print speeds, achieving up to 80 mm of print height per hour. This pace, coupled with its generous build volume, makes the Form 4L a highly productive addition to any manufacturing environment.” Additionally, Open Material Mode “enhances the Form 4L’s versatility and adaptability, making it a valuable asset for a diverse range of applications.”
“From beginners to experienced professionals, navigating and utilizing PreForm’s capabilities is intuitive, ensuring a smooth and efficient printing workflow.”
Orville Wright, 3DPrint.com
Wright is effusive in his appreciation of the Form 4L’s camera, which enables the creation of timelapse videos of prints.
Wright runs multiple test prints, including an accuracy test, as well as an evaluation of print speeds and noise levels. He calls out Form 4L’s “exceptional reliability” and base price as a “reasonable entry point for a high-performance production printer.” Wright compares Form 4L to competitors including Nexa and Carbon, noting that the Nexa 3D XiP Pro “comes with a significantly higher price tag” and that Carbon 3D printers are “exclusively available through lease agreements and lack the flexibility of an open material system.”
“At a fraction of the cost of its competitors, the Form 4L presents an exceptional value proposition for production-level 3D printing.”
Orville Wright, 3DPrint.com
Wright dives into a comprehensive production cost comparison using pcbway.com, with quotes for quantities of 1,000 and 10,000 units across CNC machining, selective laser sintering (intentionally not Formlabs’ Fuse 1+ 30W), and injection molding. Ultimately, Wright concludes that, “While the Form 4L may not always be the least expensive option upfront, it offers substantial advantages over outsourcing.” These include flexibility for design changes, the ability to produce intricate details and complex geometries, greater supply chain control, and reduced lead times.
“3D printing with the Form 4L significantly accelerates production compared to traditional manufacturing methods like CNC machining or injection molding. Furthermore, in-house 3D printing empowers businesses to maintain control over their manufacturing process, ensuring consistent quality and facilitating rapid iterations.”
Orville Wright, 3DPrint.com
Tested
Form 4
We sent a Form 4 and resins to Adam Savage’s Tested team. In a 48-minute video, Norm Chan gives an extensive look at Form 4, including:
-
How 3D printing works on resin printers, including different curing systems
-
The masked stereolithography (MSLA) technology of Form 4
-
Setting up Form 4
-
Comparing Form 4 to Form 3+
-
A conversation with Formlabs Technical Program Manager Cole Durbin
-
A conversation with Formlabs Co-founder and CEO Max Lobovsky
-
Experience printing hobby models on Form 4
-
Review of Form 4
Chan breaks down SLA vs. MSLA technology before walking through the entire Form 4 setup process, explaining how each component works, and how it compares to Form 3+, as he sets up the printer. Chan’s experience with Form 3+ is evident, and will provide insights to existing Form 3+ users interested in the updates to the Form 4 technology and consumables.
“The advantages of the Formlabs ecosystem are still here. Things I love [about Form 4]: Quick to print, quick to monitor, reliability, and rock solid quality of their really nice resins.”
Norm Chan, Tested
Chan’s video goes beyond a traditional review, including footage of his visit to Formlabs HQ to dive into the technology of Form 4 with Technical Program Manager Cole Durbin. In an interview with Formlabs co-founder and CEO Max Lobovsky, the two discuss developing products in response to user feedback, including software and materials.
After performing test prints, Chan dives into his experience and printer performance, saying, “First and foremost it’s about speed… The Form 4 is actually about three times faster… using grey resin to test at 100 microns.” Calling out the finer details on printed models, he notes incremental improvement seen via a macro lens and dimensional accuracy for parts that fit.
While Chan is mostly focused on printing hobbyist parts, he says, “What I've learned over the years working with resin prints and working with 3D printing in general, iteration time, workflow time, the rate at which you can cycle a print really matters. And if you’re prototyping, if you're designing, you want to have a balance between how much time you have to spend in your modeling software and how much time you’re spending printing and iterating.”
Ultimately, he says about Form 4, “It’s definitely not a printer made for printing tiny miniatures all day, It’s a printer made for printing engineering parts, your ceramic parts, your silicone parts, all the fancy and exotic materials that you can get in this ecosystem.”
To dive into the details and hear the conversations, watch Chan’s entire Tested review of Form 4.
Form 4L
“It blew my mind away. I mean, we were thinking in terms of weekend or week-long prints…for some of these draft resins, same day prints. [...] This is going to be an invaluable tool added to the Tested 3D Printing Workshop.”
Norm Chan, Tested
We sent a Form 4L and resins to Adam Savage’s Tested team. In a follow up to his review of Form 4, Norm Chan gives a look at Form 4L, with an overview of technology, speed, part size and quality, product engineering, resin usage and savings, and reliability.
Chan opens with the acknowledgement that Form 4L is “meant for industry and professionals, people who are prototyping who need parts that are reliable, consistent,” and who need access to the expansive Formlabs materials library.
In his review of Form 4, Chan dove into what masked stereolithography (MSLA) is and the ins and outs of Formlabs’ Low Force DisplayTM (LFD) Print Engine. Here, he gives a more general overview of MSLA and how the technology of Form 4L differs from Form 3L, specifically noting that on Form 3L, layers were cured by a combination of two laser units, which could cause a little seamline. Chan says, “By changing from the laser-based curing system of the 3L, the 4L also doesn’t have the seam line issue.” Printing with MSLA on Form 4L gives a seamless finish, saving time while preparing and finishing prints.
“On Form 4L, we’re talking much bigger. I mean this is almost like a full miniature model kit that you could print in one go in one piece…the details are incredible,” says Chan, noting that printed parts can be taller than a foot while still achieving fine surface details. And, of course, this all comes at speed.
“With the 3L we were operating in a kind of weekend mindset printing over multiple days…With about a 4-5x increase in speed, the prints here are really more of an overnight print — 12 hours…you can start a print afternoon one day and have it ready the next afternoon or the next morning so you can then work on your next iteration.”
Norm Chan, Tested
Chan printed a life-size model of Adam’s head using Fast Model Resin at 200 μm layer height, a print with about 1,300 layers. “It took an astounding 2 hours and 45 minutes to print — mindblowing.” Doing the math to break down the time to heat up resin, and time per layer to print, Chan says that Form 4L “does reach that 80 mm per hour max speed time that they claim on their website.”
The hardware and consumables, including mixer arm and resin tank, are robust and easy to run and install.
“Things just work, which is a testament to the engineering of this machine.”
Norm Chan, Tested
A major consideration for a large part is that it consumes a lot of resin. The model of Adam’s head took 1.5 L of resin in a printer that holds 2 L of resin (without Resin Pumping System). However, Chan found a solution to this with the latest PreForm update.
“Thankfully, in the PreForm software, Formlabs has introduced features that we’ve been asking for for a long time, namely the ability to hollow prints. With the touch of a button you can determine your wall thickness, how much fidelity you want on the inside of these models. And then a print that would have been 3.5 L if it were solid would only consume 700 mL of resin which is not only a savings in resin, but allows me to use finer touch points for supports so it’s easier to clean up and post-process.”
Norm Chan, Tested
Download PreForm or learn more about hollowing prints here.
While he was setting up his print in PreForm and manually editing the auto-generated supports, Chan mentioned that he liked PreForm's new support raft geometries. Even without a Build Platform Flex, it was easy to pry off rafts from the build platform, with no concerns for gouging. Plus, supports easily popped off prints.
“I haven’t had a single failed print yet on this in the two weeks we’ve been testing…It’s a thing that just works. For professionals who don’t want to be tinkering with machines, who need to have parts to deliver for projects for their clients — that’s why we see these machines in those workshops, in those labs for the companies at that scale.”
Norm Chan, Tested
Ultimately, Chan says that Form 4L is going to be an invaluable tool for professionals, reliably enabling turnover of large prints in under a day.
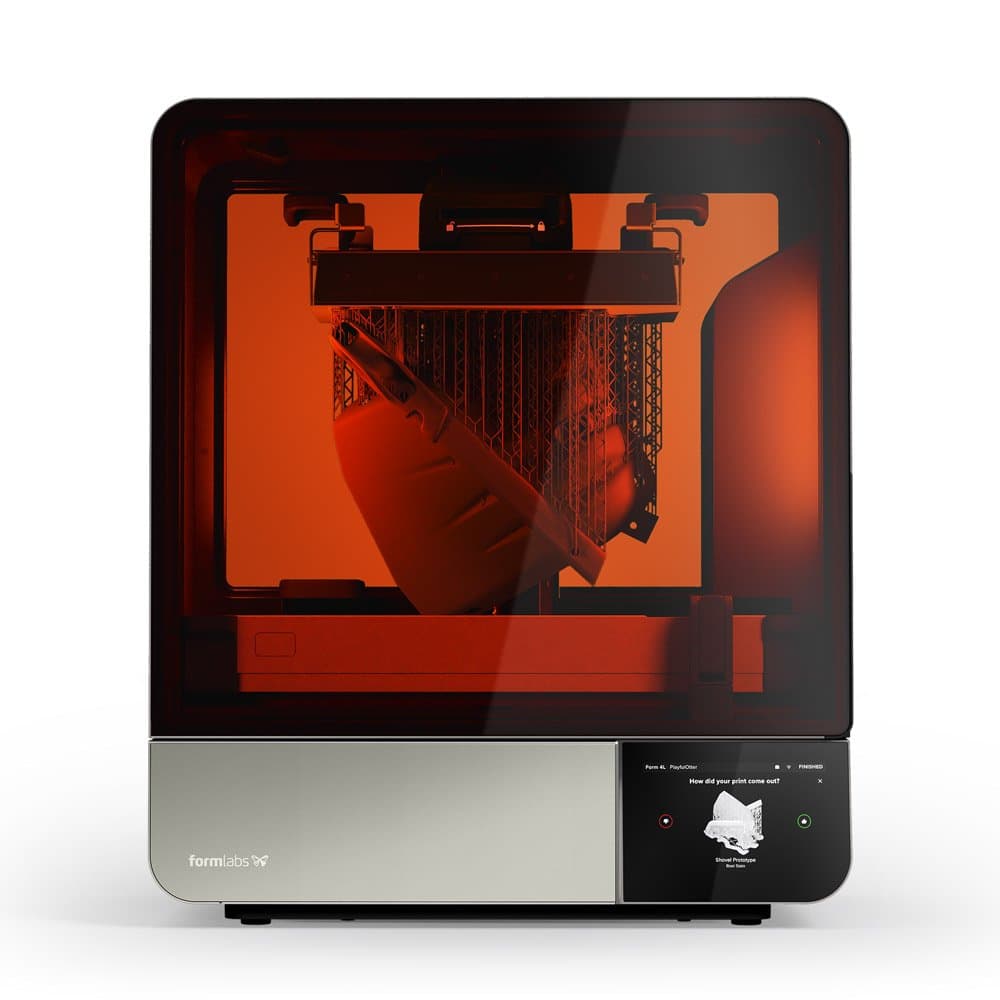
Product Demo: Form 4L
See how Form 4L, our next-generation large-format resin 3D printer, takes the speed, accuracy, and reliability of Form 4 to a completely new scale.
DEVELOP3D
“First impressions of the Form 4’s print performance are dominated by how fast it runs. Because of the layer-by-layer process, there is no time penalty for filling the bed, and you can almost watch the build platform ease its way out of the resin bath.”
Matt Batchelor, DEVELOP3D
Matt Batchelor at DEVELOP3D tested Form 4 and found that “every aspect of its design shaves off time and makes set-up a breeze.” Beginning with unboxing, the printer was well packaged and easy to pull out of the box and set up. Batchelor highlights the ability to turn off the printer to save energy, the big, bright user display, and the dramatic increase in speed. He also notes that parts on Form 4 are 3D printed, including the fume extraction port (Tough 1500 Resin on Form Series printers) and a small tool caddy (Nylon 12 Powder on Fuse Series selective laser sintering (SLS) 3D printers).
Turning to resin and consumables, Batchelor appreciates the redesigned cartridge and larger valve, plus the resin tanks which are more rigid, and have a lid to keep light and dust out of the resins when not in use. Plus, both a new tank and arm together cost less than a Form 3 resin tank and mixer.
When the printer starts, resin “Filling happens so fast that it took us a few prints to figure out when it actually happens – right at the start of the process, semi-obviously,” says Batchelor.
The Form 4 Build Platform is larger and more rectangular, and Build Platform Flex is “much more elegant than trying to pry a print off.” Plus, Form 4 offers a higher maximum build height compared to Form 3.
Form Wash (2nd Generation) offers decreased wash times and more vigorous washing. Batchelor says, “This improved washing workflow is a massive time-saver. It also becomes backward-compatible with the Form 3 build platform by moving the supports inwards, and is able to run only part-filled with solvent for those who never use the full height of the printer’s build envelope.”
Batchelor then offers a basic overview of PreForm and model setup before diving into printing, trying out the camera, and ultimately saying, “The prints were crisp and accurate, in line with Formlabs’ suggested tolerances,” and “the faster cycle time of the Formlabs Form 4 has genuinely changed how we use it… fast enough to turn around some simple parts in a couple of hours or to perform multiple runs in a day for more complex jobs.”
“The Form 4 is a really good machine, built with the needs of professional users clearly in mind. The big selling point of increased speed aside, it manages to make the SLA 3D printing slick and straightforward, allowing users to better use time previously spent messing around on set-up and post-processing tasks.”
Matt Batchelor, DEVELOP3D
3D Printing Industry
2025 Desktop Non-FFF 3D Printer of the Year
In December, 2024, 3D Printing Industry released its 2025 award winners, with Form 4 winning Desktop non-FFF 3D Printer of the Year.
On the occasion of the win, Dávid Lakatos, CPO at Formlabs, said, “We invested years of development into creating Form 4 to usher in a new era of resin 3D printing, with blazing fast speeds and unprecedented reliability. We’re honored that the expert committee and readers at the 2024 3D Printing Industry Awards recognized Form 4’s impact by naming it the Desktop non-FFF 3D Printer of the Year.”
He added that, “The printer’s high speeds and reliability have caught the attention of customers at top brands including NASA, Ford, and Microsoft, and we expect this fast printer to continue to expand 3D printing applications across new industries and use cases. 3D printing has historically never had the speeds and reliability to outpace injection molding, and Form 4 is the first 3D printer that enables innovators, manufacturers, and product designers to reimagine products with flexible design and fast print times at an affordable price.”
View the complete list of award winners here.
Form 4 Review
“The 3D printer’s sizable build volume and compatibility with any 405 nm photopolymer resin support a wide range of applications for professional-grade 3D printing.”
Alex Tyrer-Jones, 3D Printing Industry
On 3D Printing Industry, Tyrer-Jones begins by diving into the technology powering Form 4, highlighting the LFD technology, saying, “This approach minimizes the force applied during 3D printing to enhance part quality and dimensional accuracy.”
The review calls out the print speeds, dimensional tolerance, and reliability, including the "unmatched 3D print success rate exceeding 98.7%, ideal for professionals targeting high-volume production.”
Moving onto setting up Form 4, Tyrer-Jones notes how user-friendly it is, with easy unboxing and set up in 15 minutes. It is a true desktop setup, easy to fit in most workspaces while still having a sizable build volume and offering the “premium, high-quality feel we expect from Formlabs.” He then walks through the features of the resin tank, including the film and over 75,000 layer lifetime, and set up and use of post-processing solutions Form Wash (2nd Generation) and Form Cure (1st Generation), which are plug-and-play.
“We were impressed by the Form Wash, which significantly reduces the need for direct contact with washing solvents. This provides a safer and cleaner alternative to manual wash stations, where users risk inhaling harmful IPA fumes and spilling solvents.”
Alex Tyrer-Jones, 3D Printing Industry
For print setup, Tyrer-Jones says, “PreForm stands out thanks to its intuitive interface and control over essential 3D printing tasks,” noting the ease of slicing, support generation, one-click automated print setup, and a layout function for maximizing the layout of multiple models.
To test Form 4, Tyrer-Jones printed a number of benchmarking prints including a mandibular dental model, a tower, a perimeter test, two models with six overhangs, and a functional M8 nut in Clear Resin which “fit together seamlessly, confirming the Form 4 can print small and precise parts to desired tolerances.”
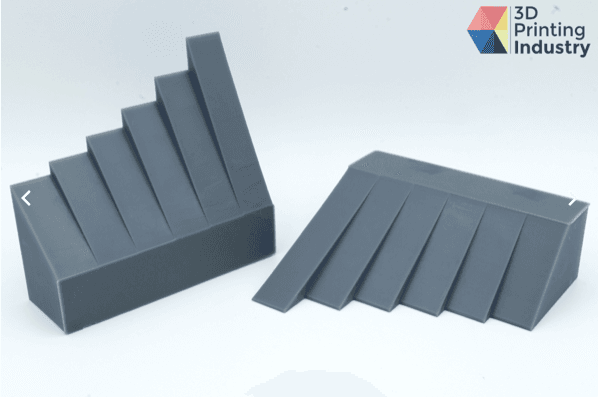
Tests for 3D printing overhangs at angles up to 65°. Photo by 3D Printing Industry
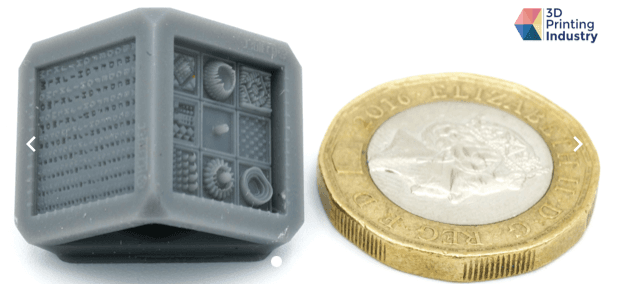
K3D Tech Definition test cube in Grey Resin V5. Photo by 3D Printing Industry
Additional tests included a K3D Tech Definition test cube, for checking intricate and complex designs, and a test model that was printed 12 times to check for repeatability. Tyrer-Jones found that “All twelve test pieces were 3D printed and processed with no significant defects. The measurements ultimately highlighted the strong repeatability of the Form 4. The average deviation came to 0.0477 mm, just below the 0.05 mm benchmark.”
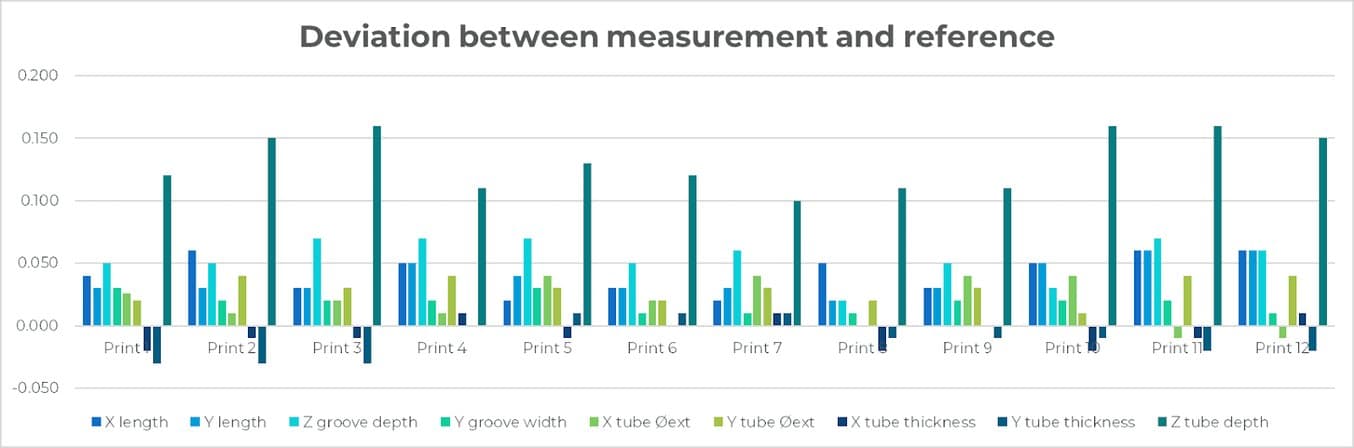
Repeatability differences between the measurement and reference. Image by 3D Printing Industry
Tyrer-Jones tested a number of real-world applications, including a functional motorcycle fuel pump hose clip which is no longer manufactured and miniature models in Grey Resin V5, snorkeling components and sunglasses in Clear Resin V5, parts in Elastic 50A Resin, and more.
“We 3D printed a batch of 24 fuel pump clips, with a total print time of 7 hours. The Form 4 performed exceptionally well here, with all components produced with intricate features perfectly preserved. The surface text was rendered perfectly, rivaling the quality of its injection-molded counterparts.”
Alex Tyrer-Jones, 3D Printing Industry
Of the Clear Resin V5 parts, Tyrer-Jones writes, “The part had an impressive transparent effect, free from the cloudiness often seen in other translucent resins. It also showed no yellowing, which is a common issue with similar clear materials. The high clarity and smooth surface finish eliminated the need for extra post-processing, like polishing or smoothing, and support removal left minimal marks.”
Overall, Tyrer-Jones found Form 4 to be reliable and high-performance, holding up to marketing claims, with particularly impressive repeatability. Additionally, Form Wash and Form Cure (1st Generation) were called out as great options for post-processing.
“The Formlabs Form 4 is a reliable, high-performance resin 3D printer that combines impressive accuracy and versatility with affordability and ease of use. The efficiency and reliability provided by Formlabs’ LFD technology make the Form 4 ideal for professional and industrial-scale users seeking an adept production system at a low price point.”
Alex Tyrer-Jones, 3D Printing Industry
Fabbaloo
“The Form 4L is quite an incredible resin 3D printer. It is a complete system that integrates materials, hardware, and software to produce a truly end-to-end workflow experience that just works. We had not a single print failure, and indeed all prints came out perfectly.”
Kerry Stevenson, Fabbaloo
In an extensive, three-part series, Kerry Stevenson at Fabbaloo reviews Form 4L from unboxing and set up through printing. The full review is worth reading for its exhaustive breakdown of every aspect of the Form 4L process, but the overall takeaway is clear — Stevenson gives Form 4L a perfect 10/10 for production use and deems the printer “...guaranteed to work, is very high speed, and consistently produces high-quality output.”
Part 1
Stevenson opens with a brief background on Formlabs SLA technology before diving into specifications and features including build size, print set up in PreForm, and speed. Stevenson calls out the technological advancements, “all of which add up to a much more convenient experience for operators.”
Stevenson thoroughly outlines unboxing, with images of each step and part that must be assembled, but ultimately says that, “There’s not much physical activity required to get the 4L ready for action."
Part 2
Stevenson started by printing a small test print, before moving to larger models. Printing was done on a standard Form 4L Build Platform L, which meant that parts had to be printed on rafts rather than flat against the build platform. Stevenson notes that having a flexible build platform would solve the few issues he had with layer lines, but that washing, curing, and removing supports were easy.
“Removing support structures is one of the most awful aspects of resin 3D printing. [...] By contrast, supports on the 4L were usually quite easy to remove. This is a feature of the PreForm software that creates support tips that are somehow strong but easily come off. There’s something to be said about perfectly tuned print profiles.”
Kerry Stevenson, Fabbaloo

The Form 4L Build Plate can be hung inside Form 4L so that resin can drip back into the resin tank. [Image source: Fabbaloo]
Particular features of note were the intelligent monitoring on the printer, which alerts to debris, unvented resin cartridges, resin/tank mismatches, resin requirements for prints, and more.
“Formlabs has carefully engineered the entire experience from end to end, and it all just works. We had no print failures after printing quite a few objects, and using the machine was easy.”
Kerry Stevenson, Fabbaloo
Part 3
“The crown jewel of Formlabs is their PreForm software, which is used to prepare jobs for all of their equipment, including the new 4L. It’s exquisitely designed and has the easiest workflow of any resin job software we’ve experienced.”
Kerry Stevenson, Fabbaloo
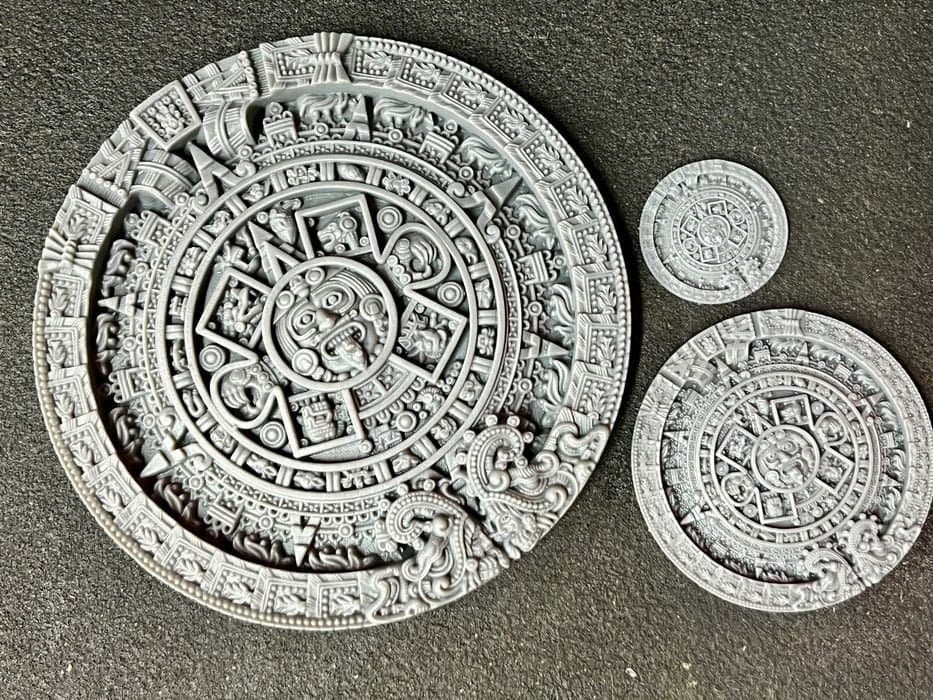
This Mayan Calendar Wheel print shows “an impressible level of fine detail, ideal to show off the capabilities of a machine,” says Stevenson. [Image source: Fabbaloo]
Stevenson did multiple test prints in four resins, finding swapping between resins to be easy and automatic, unlike other printers where recalibration is required. The verdict was that the print quality of Form 4L is very high and consistent, producing parts that fit — including a hinge to test articulated parts. He tested large models and volume production, robust parts and delicate features, finding success with all.
bunnie : studios Teardown
“I’m always impressed by the thoroughness of the Formlabs engineering team. I learn a lot from every teardown, and it’s a pleasure to see the new twists they put on old motifs.”
Andrew Shane Huang, bunnie : studios
We sent two Form 4 printers to Andrew Shane Huang, a researcher who holds a PhD in electrical engineering from MIT, and creator of the blog bunnie : studios. Huang says, “I jumped on the chance to do a teardown of the printer; I’m grateful that I was able to do the same for the Form 1, Form 2, and Form 3 generations. In addition to learning a lot from the process of tearing down a single printer, I am also gaining a unique perspective on how a successful hardware startup matures into an established player in a cut-throat industry.”
In the extensive post, Huang starts by giving background on the SLA 3D printer market before moving onto explaining the evolution of Formlabs’ light processing engines with clear diagrams. On the light processing technology of Form 4, Huang says, “I’m definitely no expert in 3D printing technology – my primary exposure is through doing these teardowns – but from a first-principles perspective I can see many facial challenges around using LCDs as a light modulator for UV, such as reliability, uniformity, and build volume.”
“An hour and change to run the below test print is in net faster than my workflow can keep up with. At this speed, the sum of time I spend on 3D model prep plus print clean and finishing is more than the time it takes to run the print, so for a shop like mine where I’m both the engineer and the operator, it’s faster than I can keep up with.”
Andrew Shane Huang, bunnie : studios
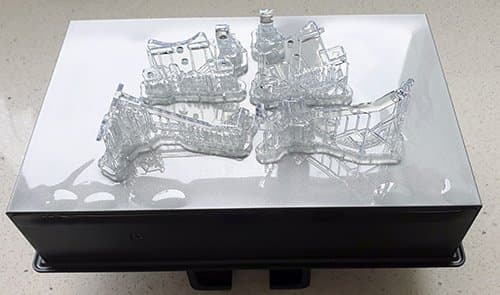
(Image credit: Andrew Shane Huang)
Huang then takes readers through unboxing, setup, and the outwardly-visible features of Form 4 before diving inside. Huang says that, ”Formlabs is walking the walk by using their own printers to fabricate parts for their shipping products.” This includes, “the set of allen keys that come with the printer, hidden inside a nifty 3D printed holder” and a service plug. Huang adds, “Another minor detail I really enjoyed on the LCD panel is the 3D-printed retaining clip for the HDMI cable. I think this was probably made out of nylon on one of Formlabs’ own SLS printers.”
Then, the breakdown commences, with Huang diving into the printer, extensively detailing the hardware inside, including the LCD, light source assembly, drive electronics, and related components. Huang’s review includes both detailed photos and diagrams explaining how components work. For those looking for a technological deep dive other than one from Formlabs, Huang delivers.
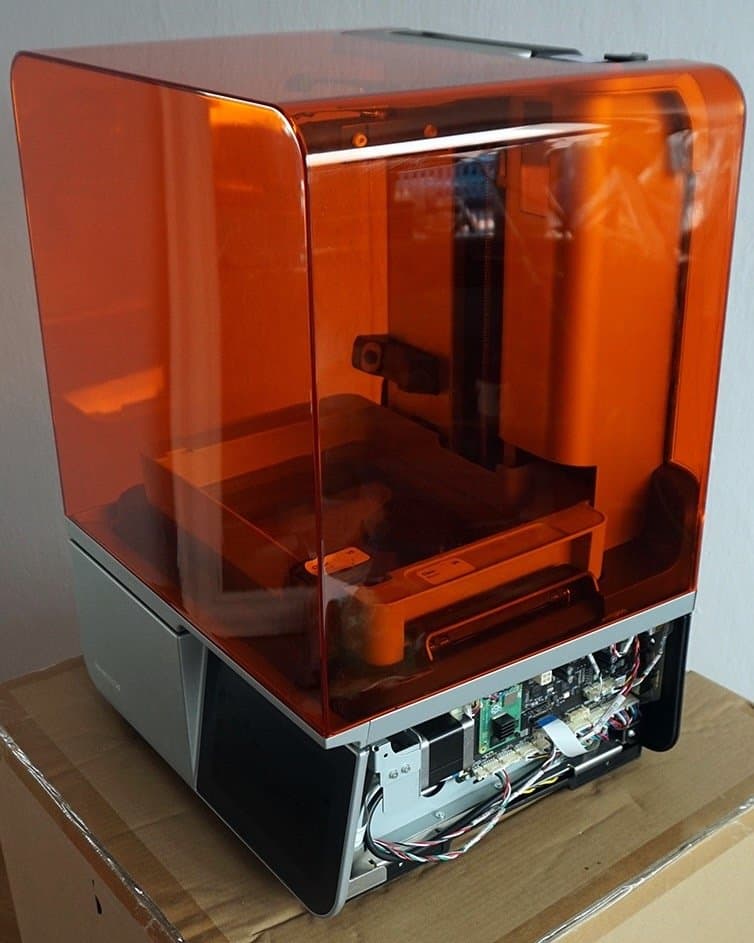
Huang says, “Pulling off the right body panel reveals the motherboard. Four screws and the panel is off – super nice experience for repair!” (Image credit: Andrew Shane Huang)
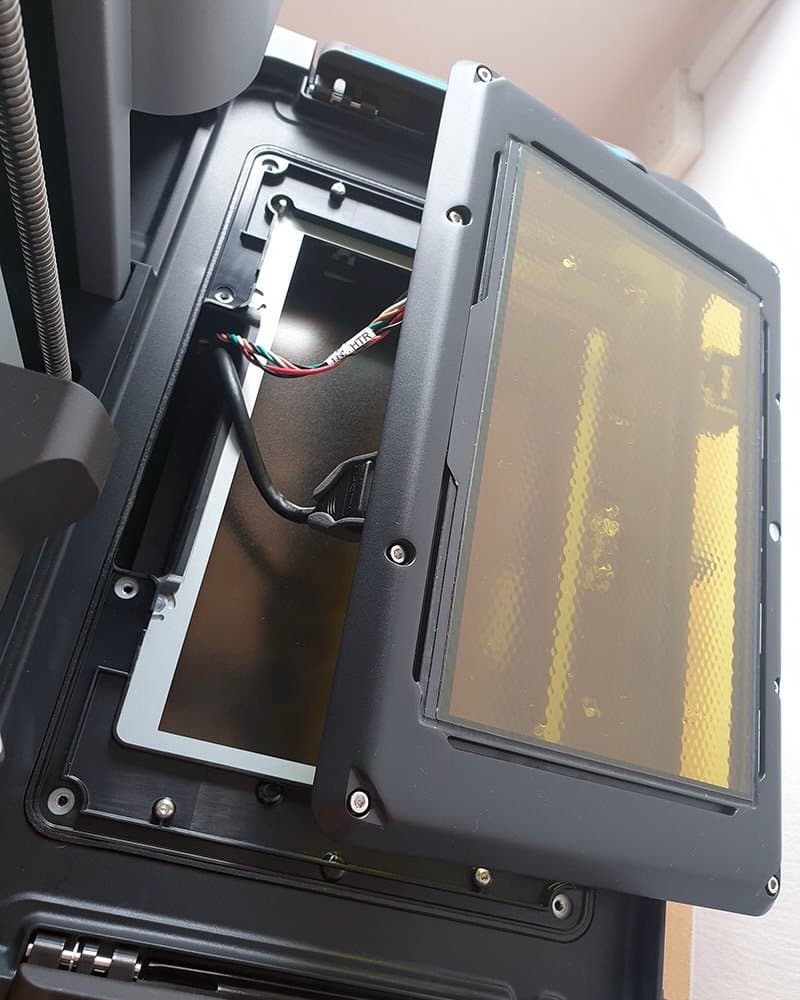
Huang says, “The LCD panel itself is about as easy to repair as the side body panels; just 8 accessible screws, and it’s off.” (Image credit: Andrew Shane Huang)
Huang ends with a few other features of note, saying, “I appreciated the new foam seal on the bottom of the case lid. [...] I have noticed that there is less smell from the printer as it’s running. For a small urban office like mine, the odor of the resin is a nuisance, so this quality of life improvement is appreciated.”
“For me, the dramatically faster print time of the Form 4 and reduced resin odor go a long way towards reducing the barrier to running a 3D print. I look forward to using the Form 4 more.”
Andrew Shane Huang, bunnie : studios
Review Form 4 and Form 4L Yourself
Formlabs is excited to see the overwhelmingly positive response that Form 4 and Form 4L have received, and we're looking forward to seeing what our community accomplishes with the next generation of resin 3D printers. If these reviews have piqued your interest, explore Form 4 Series printers to learn more. To evaluate print quality for yourself, request a free sample part in the material of your choice. And, if you have any questions or would like to discuss how Formlabs resin 3D printers can help you meet your business goals, our experts are here to help.