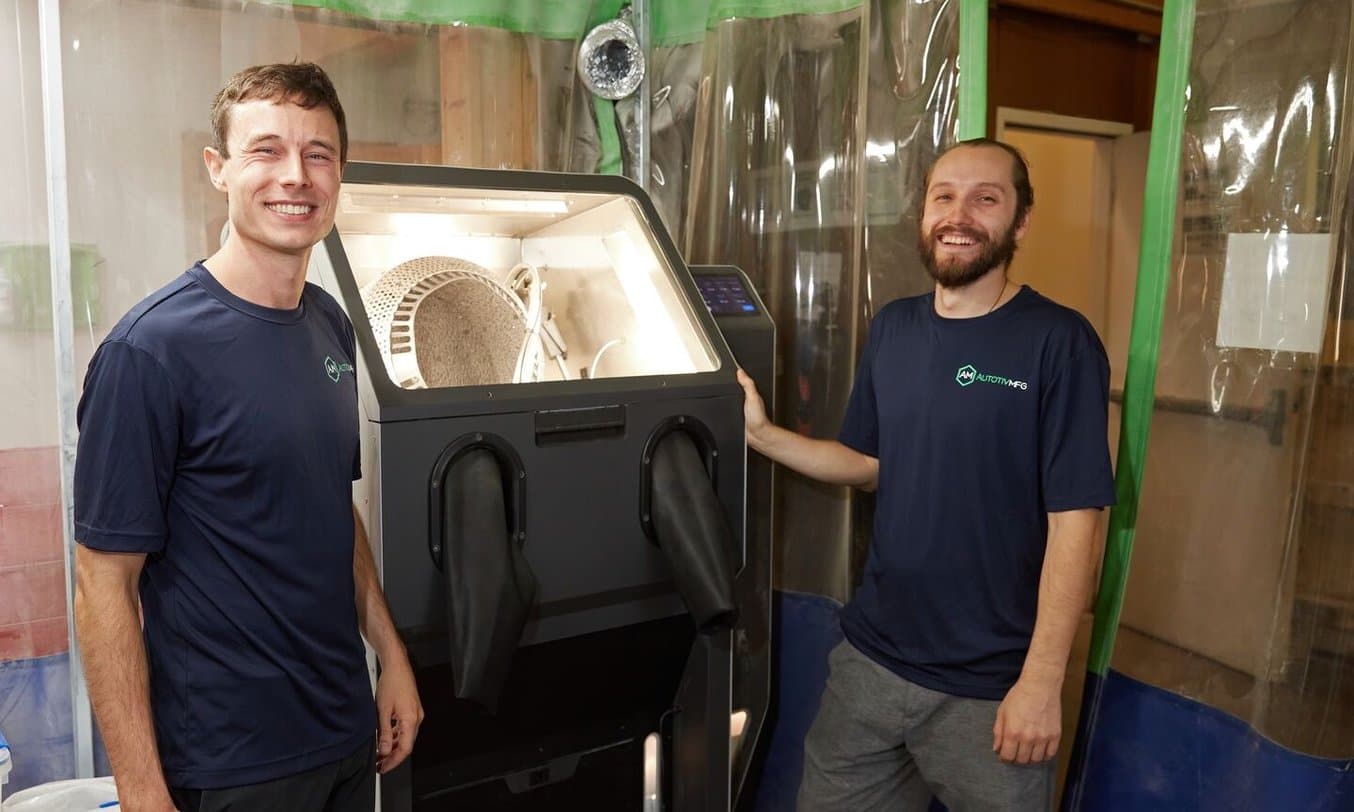
Autotiv CEO and co-founder Evan LaBelle (left) and Operations Lead Chris Haak (right) with their Fuse Blast.
Efficiency is the top priority at Autotiv. The startup, based in Salem, New Hampshire, is a contract manufacturer that specializes in 3D printing and advanced post-processing techniques, and has made it a priority to deliver parts to its customers as quickly as possible. As business has grown this has become more difficult — SLS production can create major bottlenecks in the labor-intensive post-processing stage, creating longer lead times.
To maintain their high standards, even with a steadily increasing volume of SLS orders, the Autotiv team was spending hours, or sometimes full days, manually media blasting SLS parts. With the addition of the Fuse Blast automated powder cleaning system, the team can now spend their time on higher value tasks.
Autotiv CEO and co-founder Evan LaBelle and Operations Lead Chris Haak walked us through their facility, giving us a good look at how they’ve created a lean manufacturing environment by selectively choosing the right tool for the right job and by automating processes where they can.
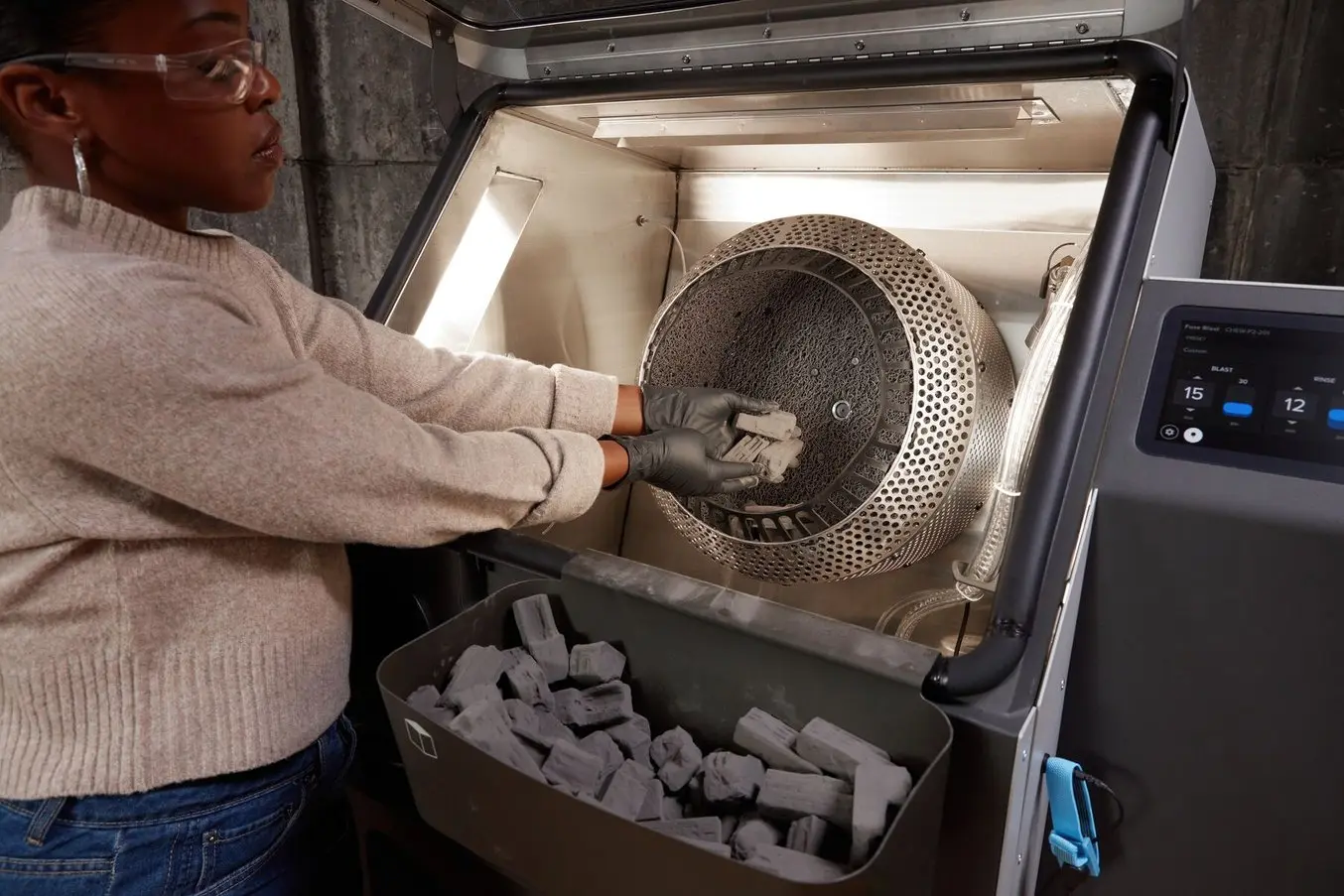
New Automated Post-Processing And Speed Improvement For The Fuse Series SLS 3D Printers
Discover the latest innovations at Formlabs: SLS software improvements for the Fuse Series and the new Fuse Blast, an automated solution that enables hands-free SLS part cleaning and polishing in as little as 15 minutes. Register to watch a 15 minute inroduction and product demo.
Production-Volume SLS and the Blasting Time Sink
Since opening in 2015, Autotiv has relied solely on word-of-mouth and repeat customers to grow their business. “We don’t have marketing people, or sales, it’s just us focusing on printing and post-processing at a high level,” LaBelle told us. That strategy has paid off, and in the last year, Autotiv has seen an uptick in higher production volume orders, including some for up to six thousand parts.
From plug-and-print files that are ready to go, to concepts for prototypes that Autotiv has to consult on, the parts, quantities, industries, and applications change every day. LaBelle estimates that about 60% of their business comes from SLS parts, including both prototyping and production runs. The other 25% is split up between fused deposition modeling (FDM) and stereolithography (SLA) 3D printing, along with post-processing techniques like dyeing or coating.
Ramping Up SLS Production
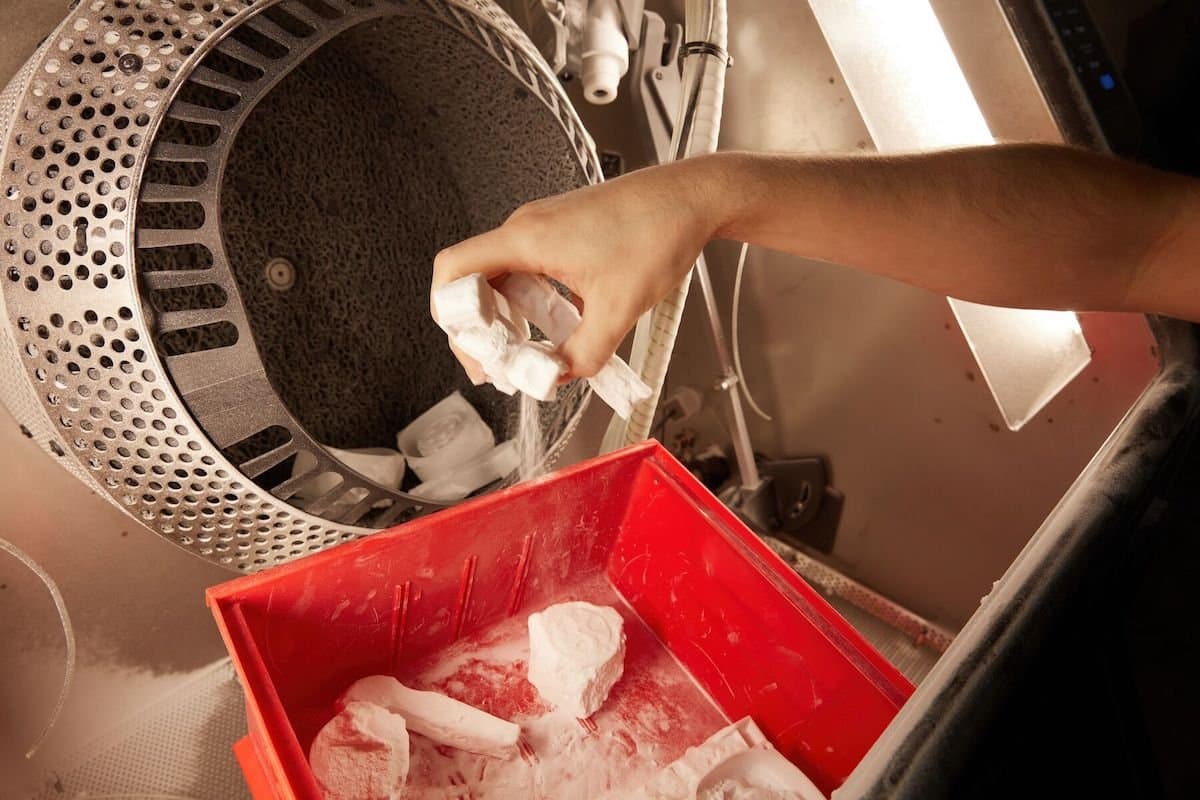
Most of Autotiv’s business comes from SLS production of nylon 12 parts from their large-format SLS printer. Cleaning many small parts like these used to take up a significant portion of Haak’s day.
Two years ago, Autotiv invested in a large-format SLS printer, purchased for about $300,000. The printer has a build volume of 325 x 325 x 425 mm, allowing the team to print large objects easily, or to pack it full for a production run of smaller parts. Because the vast majority of their part requests are for nylon 12 parts, it’s still most efficient to keep their printer running full-time on nylon 12 and use their network of suppliers to provide other materials printed on SLS machines when needed.
As production-level orders increased, the Autotiv team started running into issues with post-processing. Their large-format printer came with a powder management tool, similar to the Fuse Sift, for extracting parts from the powder cake and recycling powder. Cleaning the parts after that, however, was completely up to the Autotiv team, even when it meant hours standing in front of their manual media blaster, painstakingly removing powder from the parts’ surfaces.
“We'd be in there, depending on the workload, around two to three hours a day, maybe a little more. It might be all day and we might swap in and out if we have several hundred or a thousand parts to do. It was definitely a labor sink."
Chris Haak, Autotiv Operations Lead
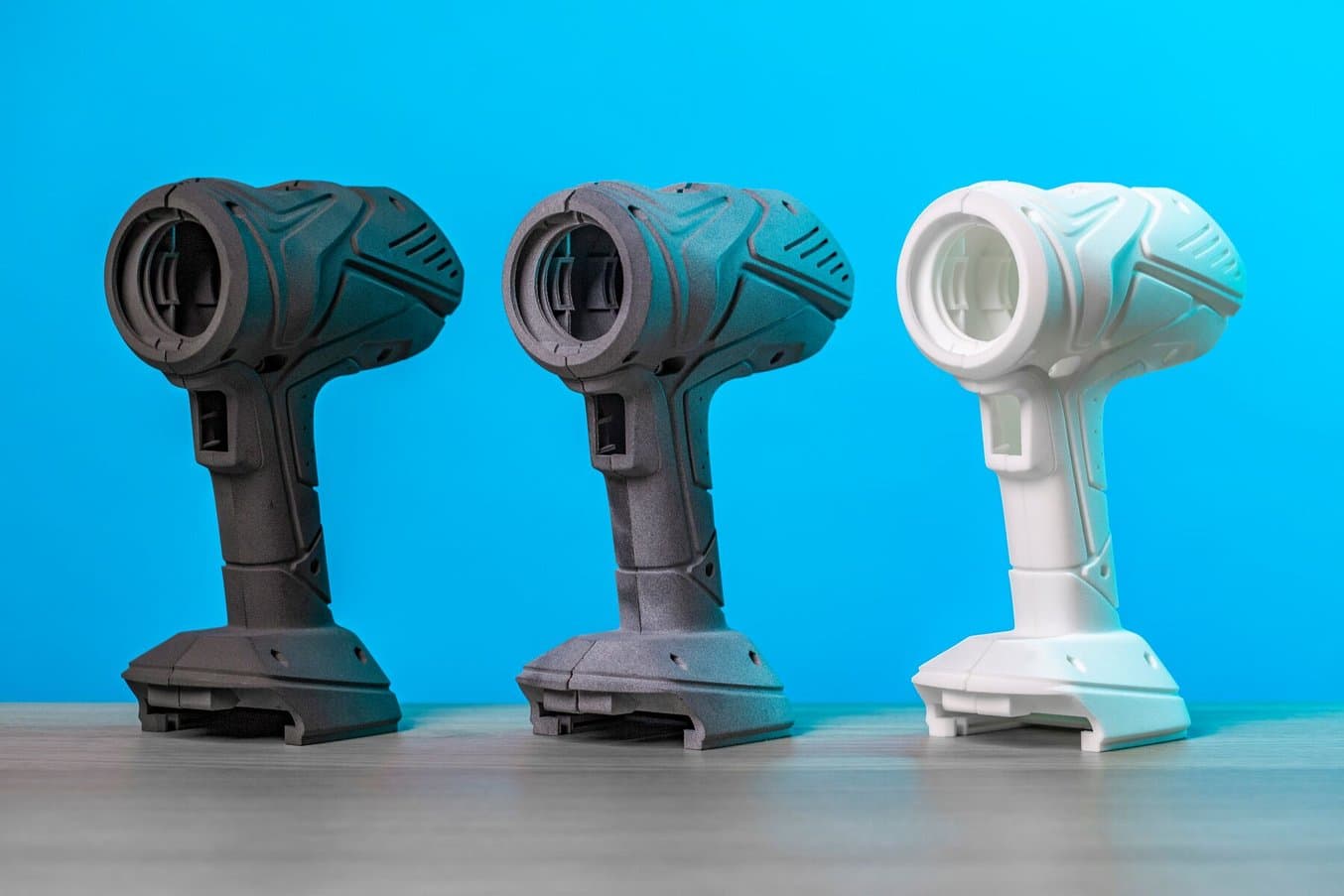
Fuse Series SLS Printers vs. Traditional Powder Bed Fusion Systems
This comparison guide covers the main differences between compact SLS printers such as Formlabs Fuse 1+ 30W that can easily fit into existing office or manufacturing spaces and large footprint machines that require more planning and preparation to integrate into an existing workflow.
Physical Wear and Tear
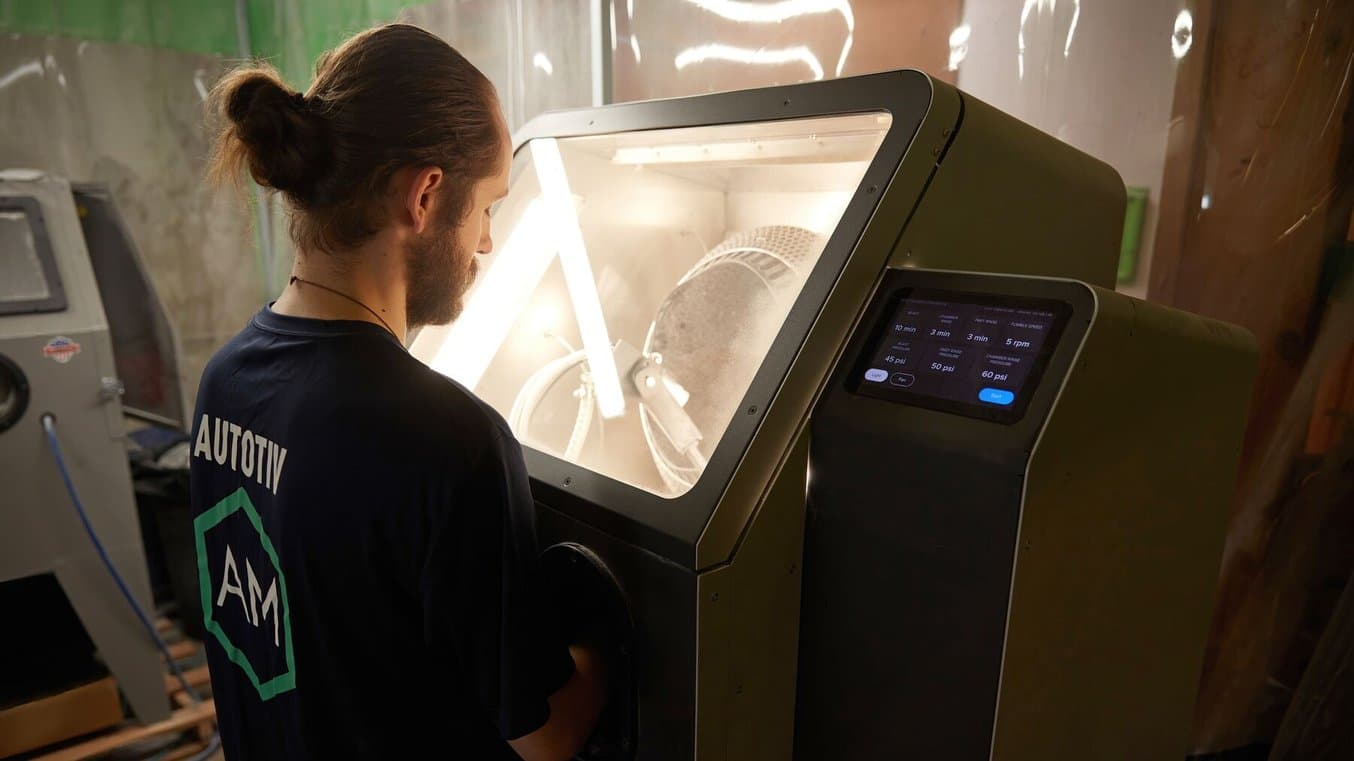
Though Haak still spends some time doing glovebox work for parts that need an extra manual polishing step after dyeing, the vast majority of work is automated, mitigating the physical wear and tear of standing at a media blaster all day.
Autotiv’s commitment to 24-hour turnaround times for some SLS orders means they have a strict, regimented schedule for printing, cleaning, and packaging. Though several orders might get bundled into one large build volume that prints overnight, the team has to keep track of which order has the quickest turnaround. “We had to make sure we were cleaning all the correct parts in the correct order so the orders got out on time,” Haak continued.
That strict schedule means that time spent media blasting was non-negotiable, even if it was physically demanding and difficult for the team. Hours spent handling parts and operating the media blasting nozzle, especially in the close quarters of the media blasting room with constant heat and loud noise, were wearing the team down.
“It was a pretty good chunk of a person’s day having to stand there for hours, not to mention the stress and fatigue on the body and the muscles. We actually had someone have to see the doctor because they were media blasting so much they strained their shoulder.”
Chris Haak, Autotiv Operations Lead
Different Manufacturers for Printing and Blasting
At first, the Autotiv team was apprehensive about integrating a Formlabs post-processing solution into a different OEM’s printing workflow. Haak and LaBelle were familiar with Formlabs SLS parts, and noted that the Autotiv parts’ powder cake required more force to remove than a typical Formlabs Nylon 12 Powder build.
“I had to see for myself, but literally, the first time that we used it, all of that apprehension went away. It will fit well into any production or office environment, it’s pretty versatile in terms of being open to many different types of customers. Either ones that own a smaller Fuse Series system or run a bigger SLS system.”
Chris Haak, Autotiv Operations Lead
Because their large-format SLS printer runs every evening, and throughout the weekend, the Autotiv team needed a blasting solution that could work just as hard. The Fuse Blast was an affordable option that integrated easily into their workflow.
Though their original manual media blaster sat in a tented area to avoid powder contamination throughout the workspace, the Fuse Blast doesn’t have to. The Autotiv team had space for the Fuse Blast near their large-format powder recovery station, and it made sense to keep the two near each other in the contained space. In the future, however, the team could scale up outside of the tented area, since Fuse Blast is self-contained and keeps the environment clean and powder-free.
Automated Blasting Yields Better Part Results
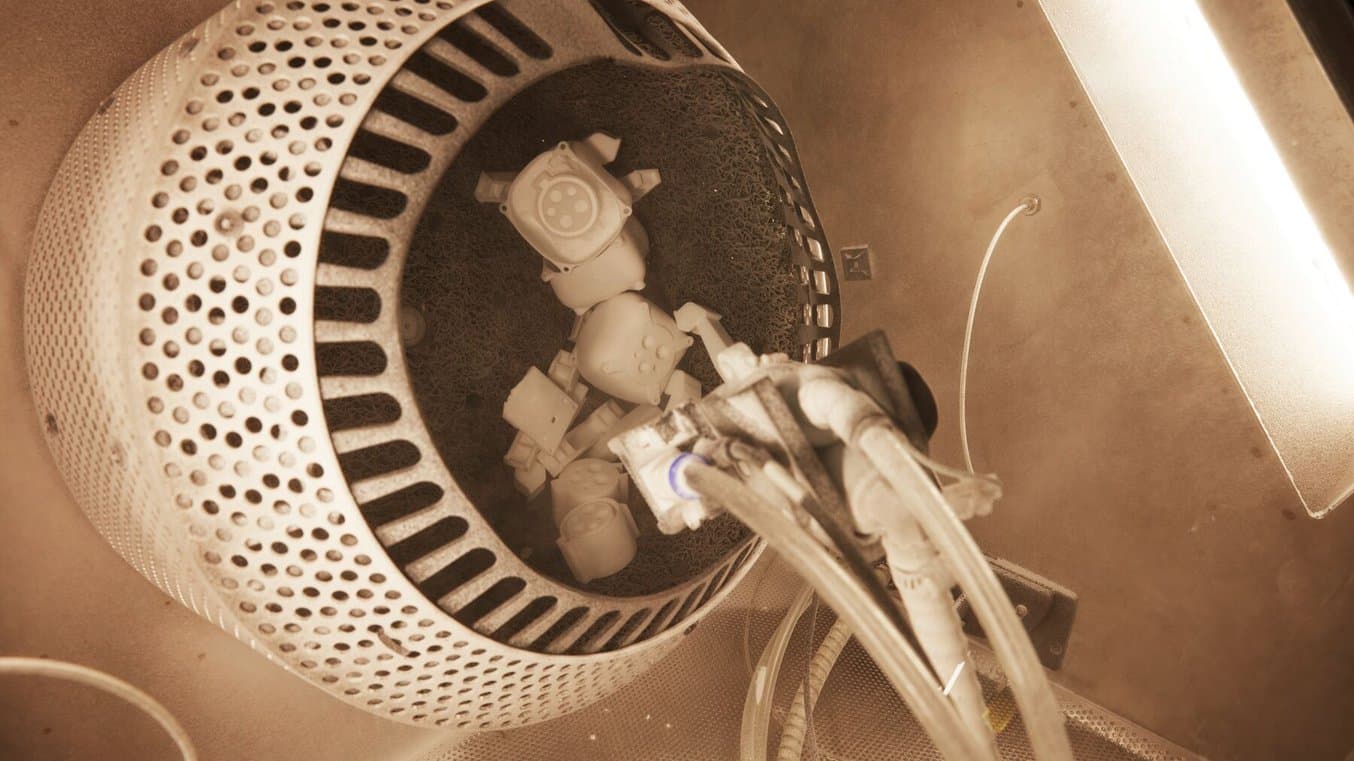
The Fuse Blast does a better job at protecting small parts or fine features than manually blasting parts - the tumbling motion is gentle enough to keep parts safe while the media blasting nozzle eliminates excess powder.
Manually media blasting parts took up valuable time for the Autotiv team while they were hands-on with the parts, but it also created another kind of time-sink: time spent reprinting broken parts. Fatigue and the difficulty of handling the blast nozzle for hours on end sometimes led to small parts jerking out of their hands and snapping against the enclosure.
“Previously, small parts were prone to breaking or flying out of your hand from the blast pressure, and then hitting the back wall of the media blaster and shattering. With the Fuse Blast, that hasn't happened. It's actually a bit safer because it's in a controlled environment and it does have a pretty soft mesh in there as well,” says Haak.
Manually blasting can also lead to parts ‘burning’ or scarring when a blast stream is held in place for too long, which can be a matter of seconds; manually blasting requires a skilled operator familiar with the process, pressure, and needs of the part. The Fuse Blast automates the process and keeps the parts moving at all times with a lower pressure blast stream.
Fewer broken or burned parts means fewer reprints, and more time spent on final polishing, dyeing, and getting orders out the door. Haak and LaBelle have found that the Fuse Blast can actually create a true satin finish when added as an additional step after dyeing. The Autotiv team uses the manual option for a quick few minutes of concentrated media blasting to remove any blotchiness or uneven color on the parts after they come out of the dyeing machine. “We are seeing an improved surface finish because we are constantly tumbling the part. It’s an almost satin-like finish on the black-dyed parts that we are printing, processing, and dyeing,” says Haak.
Small parts and complex geometries are easier to handle now, and the Autotiv team can confidently attend to other tasks while a preprogrammed routine runs. “With manual cleaning, we may miss pockets, holes, and corners, which we’ll need to inspect pre-shipping. With the Fuse Blast, we’re able to inspect much more quickly because we actually have more faith in the machine cleaning the parts than ourselves. It does just as good if not a better job of getting those small features,” says Haak.
In-Line Ionization Creates a White-Glove Effect
Before the Fuse Blast arrived, Haak was manually cleaning parts with pressurized air after the blasting step in an attempt to remove the powdery residue from the parts’ surfaces. “Even then we’d still get the static charge, so after we blasted it and put it in the bin for processing and inspection, it would still collect dust,” says Haak.
An inspection would invariably reveal the dusty surface, so parts would have to go back through post-processing before getting shipped out, wasting valuable time on the Autotiv side and delaying their customers’ projects.
Fuse Blast’s in-line ionizer removes the static charge from parts, and causes powder and media to drop away to the bottom of the chamber.
"The parts come out and they’re just clean to the touch. When you pick them up, you can feel the surface — it’s just the SLS part and there’s nothing else on the surface."
Chris Haak, Autotiv Operations Lead
Less Contamination, Lower Media Costs
The Fuse Blast’s passive media separation feature ensures that media and powder are being filtered continuously, so that the blasting nozzle is only pulling uncontaminated media through, and the parts are cleaned more quickly. The Autotiv team was media blasting every day with their manual solution, and going through about 45 pounds of media every three to four weeks before needing to change out the media supply. With the Fuse Blast, they’ve reduced that by almost half. Autotiv blasts with 45 PSI pressure to process their relatively stiffer powder cake — for users who blast at the recommended 30 PSI, media can be expected to last four to eight times longer than with manual blasting. “We are putting about 25 pounds of media into the Fuse Blast, and changing it out every four weeks. So I would say it effectively doubles the lifespan of our media consumption,” says LaBelle.
Higher Productivity Enables Continued Growth for Autotiv
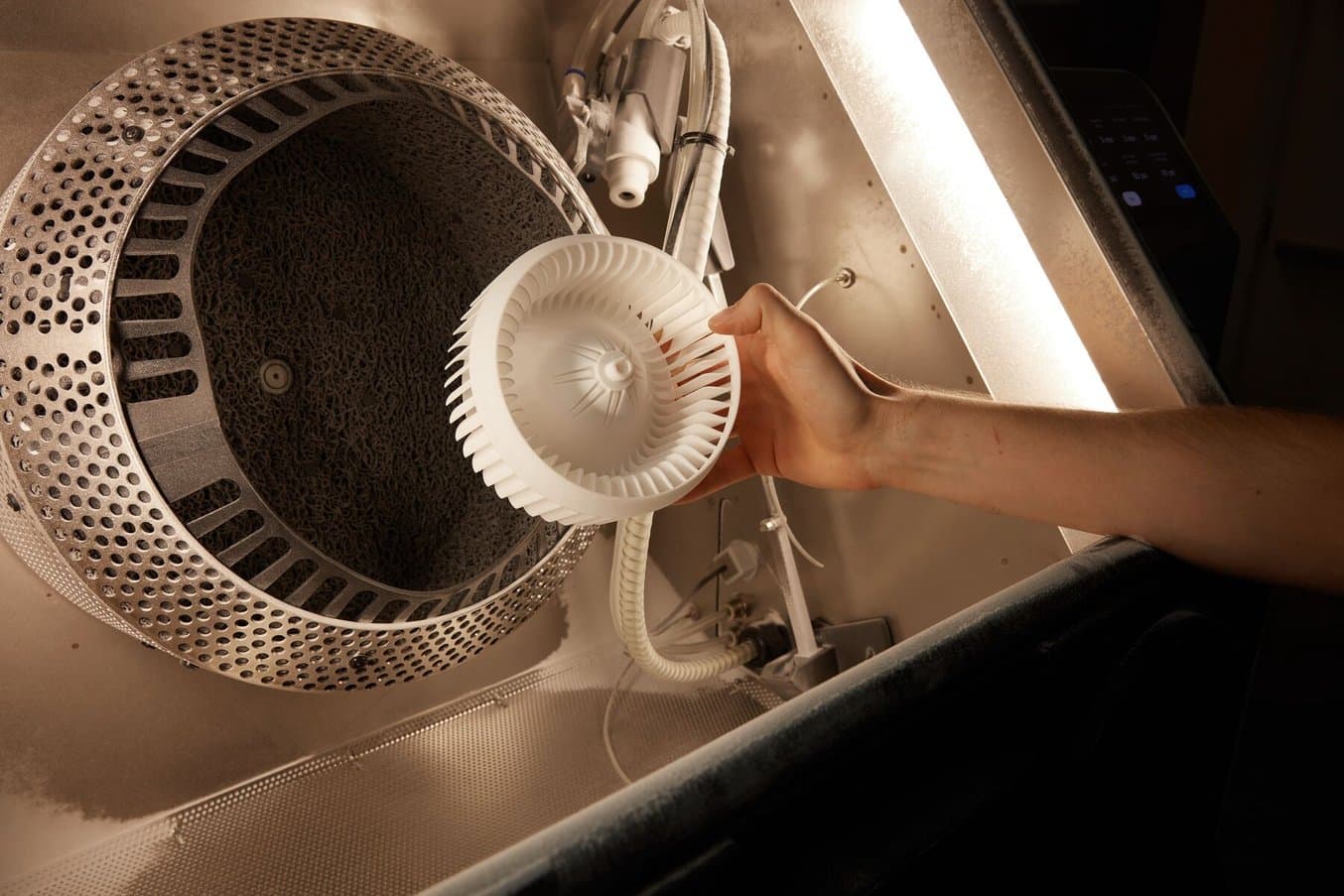
The in-line ionization causes all the powder to fall away from the surface of the part, leaving it clean to the touch.
At Autotiv, it’s all hands on deck. Everyone, from LaBelle to his most recent hire, takes turns when the going gets tough. When they were manually media blasting for hours, or even entire workdays, they shared the workload so no one had to be standing at the machine for too long at once. Now, with Fuse Blast, those hours are free to accomplish the many higher-value tasks that the growing company requires. “The Fuse Blast does greatly improve the amount of time and productivity that the team has to work on other tasks,” says Haak. Despite printing parts with a non-Formlabs printer, the Fuse Blast integrated seamlessly into their workflow.
“It's essentially plug-and-play. There's no tuning to do. You just fill it up with media and you push go, and 10 to 15-minutes later you have clean parts.”
Evan LaBelle, Autotiv CEO and Co-founder
The range of industries currently requesting parts from Autotiv is broad. Everyone, from robotics to automotive to consumer electronics manufacturers, is integrating SLS 3D printing into some stage of their manufacturing and design process. As Autotiv’s business grows in response, the Fuse Blast is helping them handle the increasing volume. “I can see scaling with it,” Haak says.
To learn more about SLS 3D printing or to learn more about the Fuse Blast, contact our SLS team.