作为世界上最大的快速消费品 (FMCG) 公司之一,联合利华始终致力于开发新的日用产品,包括个人护理、家庭护理、营养品等等。鉴于该公司拥有多芬、家净、Cif、Knorr、Axe (Lynx)、Ben & Jerry’s 以及数十个其他全球和本地品牌,现在您的家里就很可能有一种或多种联合利华产品。
在快消行业,消费者的持续需求使竞争日益激烈,因此品牌必须不断创新,调整产品战略。包装是创新的一个重要领域;有时,瓶子的设计和内容物一样,都会影响消费者对产品的感知。诸如联合利华等品牌必须考虑多种包装类型的材料使用、美观性、安全性和可持续性及其所装产品。但对于“简单的”塑料瓶而言,从在电脑屏幕上进行设计到在生产线上进行灌装,传统上需要花费数月时间。
“诸如联合利华等消费品公司必须尽快或抢在竞争对手之前进入市场。并需要在最短的时间内以最优惠的价格向消费者提供最优质的产品。3D 打印技术可以帮助我们加快这一进程。”
Stefano Cademartiri,联合利华 CAD 和原型制造负责人
了解联合利华的 CAD 和原型制造负责人 Stefano Cademartiri 和 Serioplast 全球服务公司的研发设计经理 Flavio Migliarelli 如何携手合作,测试 3D 打印模具在小批量拉伸吹塑成型中的可行性,以加快原型制造和试点测试,将周转时间缩短 6 周,成本降低 90%。
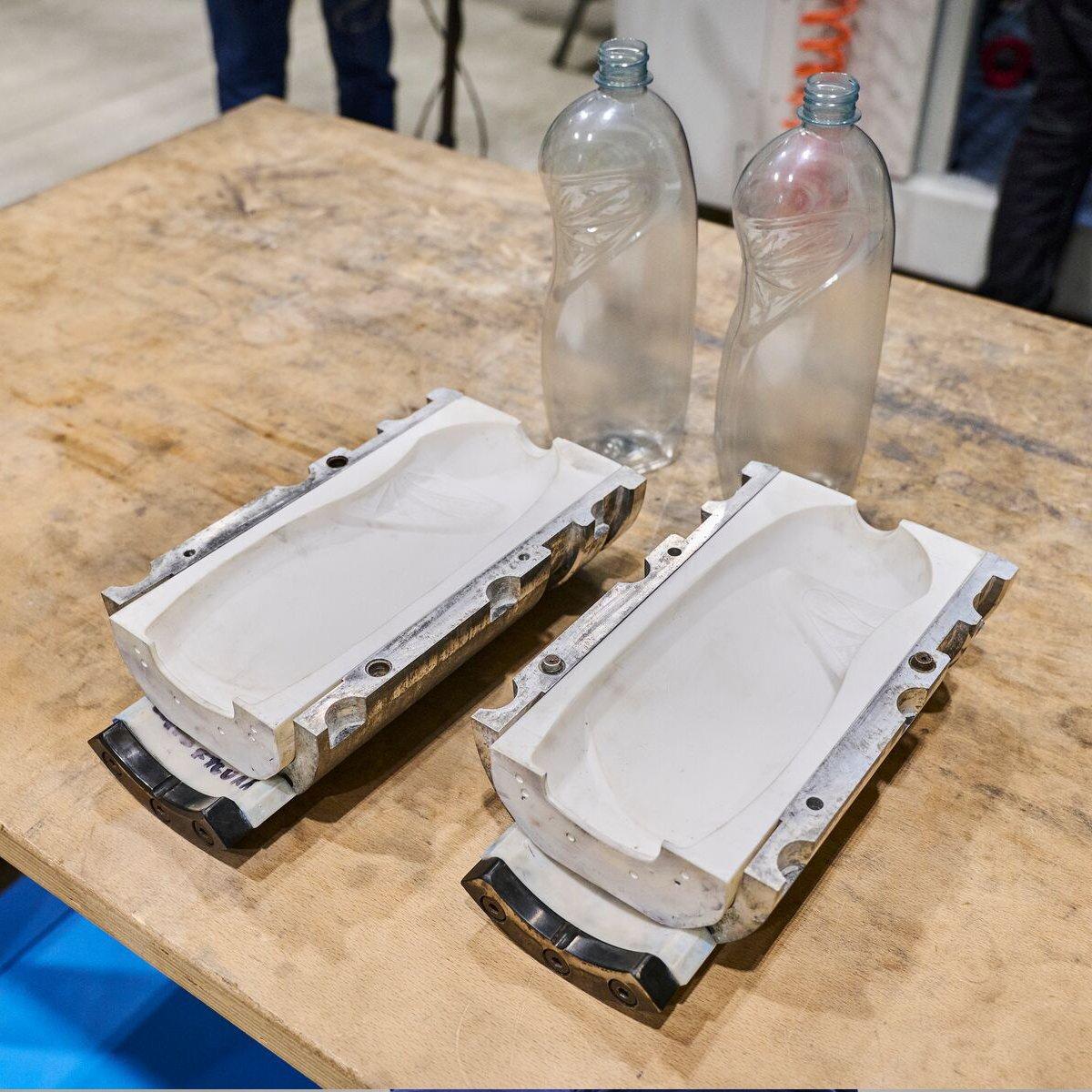
使用 3D 打印模具完成小批量快速拉伸吹塑成型
本白皮书将提供必要的方法和指导,帮助用户在试生产期间将 SLA 3D 打印模具用于 SBM 工艺来降低成本及缩短周转时间。从设计和工作流程考虑因素到成型条件,本文详细介绍了行业专家联合利华和 Serioplast 开展的可行性研究。
开发和测试新瓶子设计的传统工作流程
食品和饮料容器、化妆品包装和医疗包装等塑料产品最常见的生产方法是吹塑成型,该方法长期以来多用于快速批量生产高质量薄壁部件。吹塑成型的周期时间非常短,通常在一到两分钟之间,并且对于大批量生产极具成本效益。该工艺通常用于以较低的单位成本生产数百万个相同的部件。
吹塑的工作原理是在模具内向受热的塑料管(称为型坯或瓶坯)中充气,直至形成所需形状。吹塑成型工艺有三种类型:挤出吹塑成型 (Extrusion Blow Molding, EBM)、注射吹塑成型 (Injection Blow Molding, IBM) 和拉伸吹塑成型 (Stretch Blow Molding, SBM)。SBM 通常用于生产高质量的玻璃透明 PET 容器,如水瓶。
Serioplast 是快消品行业硬质塑料包装的全球生产商,也是联合利华开发和生产家庭及个人护理市场包装的主要合作伙伴之一。“我们每年使用 PET、HDPE 和 PP 材料生产 40 亿个瓶子,”Migliarelli 说道。
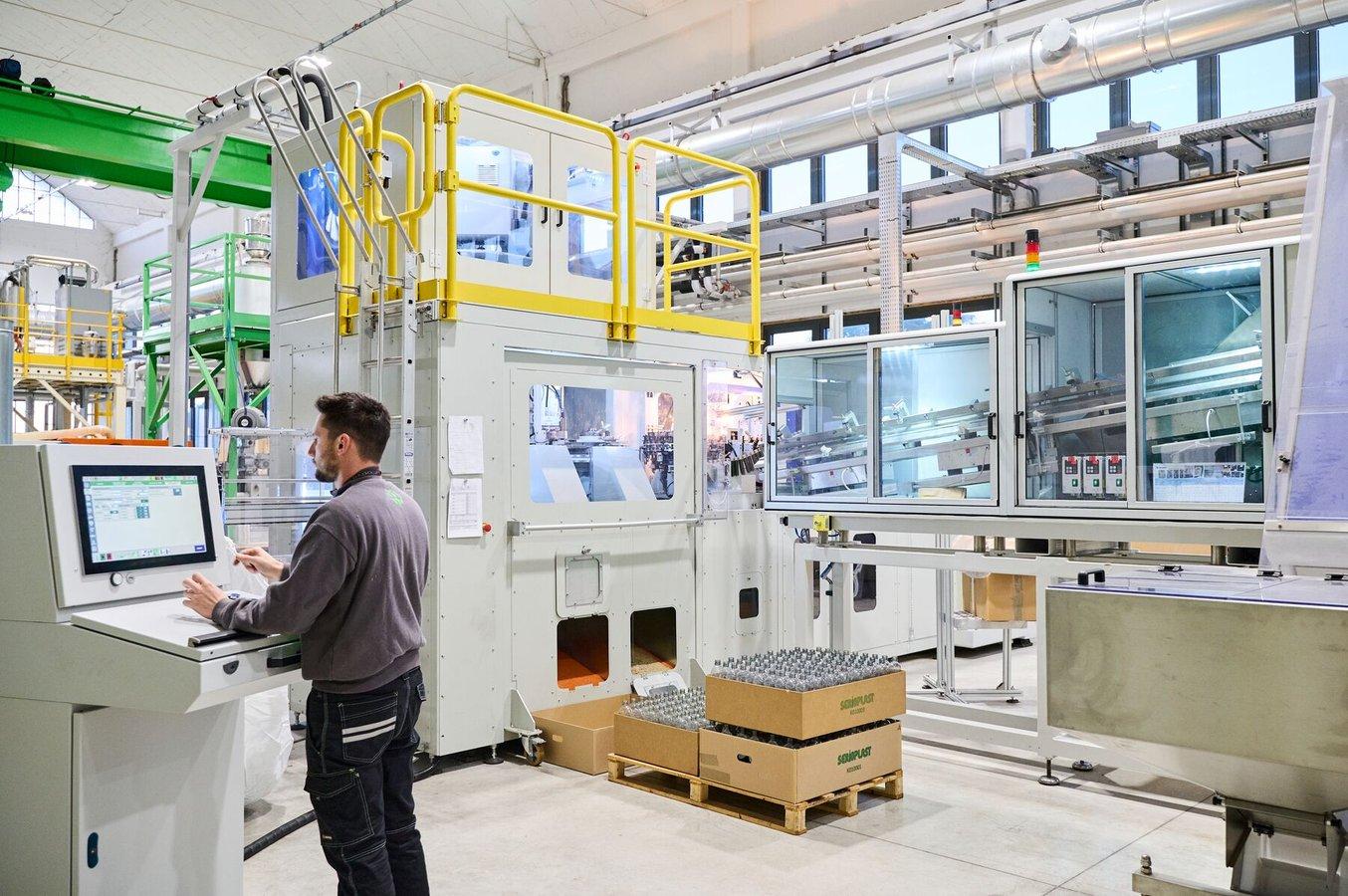
Serioplast 意大利研发机构中的 Seriomac UNIX 4 型腔 SBM 机器。他们与联合利华共同开发了一种全新工作流程,用于在这种大型工业制造设备中使用 3D 打印模具。
通常情况下,Serioplast 可以选择直接使用 3D 打印或通过吹塑成型制作原型模型。传统上,3D 打印模型无法体现合适的触感或透明度,同时可靠性较低,无法发送给消费者。然而,通过 SBM 制作生产级品质的样品部件需要使用昂贵的金属模具,由于工艺复杂和模具生产外包需求,典型的试点测试阶段中则因此增加了为期 6 到 9 周的周转时间。
“我们必须等待 6 到 12 周才能为客户提供真正的样品,所以仅仅是为了尝试瓶子的新设计,我们就浪费了数周时间。这些工作有时费时费力,也很令人沮丧,因为你可能不得不重新开始,”Migliarelli 说道。
SBM 模具传统上由金属通过 CNC 加工制成,此过程需要专业设备、CAM 软件和熟练技术人员。金属模具的生产一般外包给服务供应商,周转时间为 4 到 8 周,成本从 2000 美元到 10 万美元以上不等,具体取决于部件的复杂程度和每个模具制造的部件数量。即使是在公司内部加工金属模具,通常也需要 6 周时间,因为此过程包括数个步骤:订购材料的周转时间、CAM 和机器设置、手动抛光以及等待机器可用的时间。
因此,传统上小批量吹塑成型部件用于原型制造和试点测试在经济上并不可行。联合利华等公司不得不延长计划时间,并根据不同材料的外观性原型做出最终设计决定,这往往导致模具过时和成本损失。
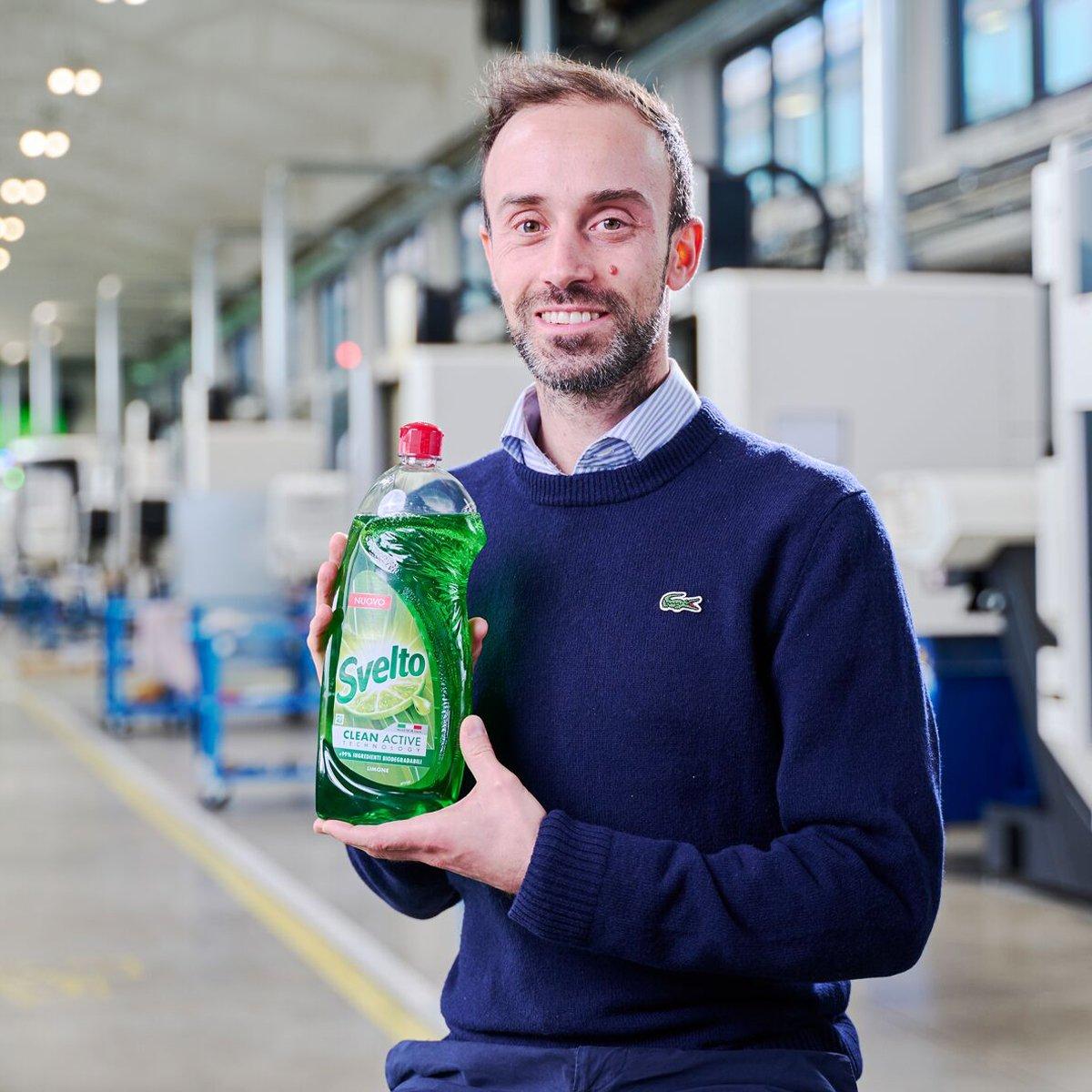
利用快速吹塑技术降低包装试点测试的成本和时间
在本次网络研讨会中,吹塑专家 Flavio Migliarelli 将指导您了解工作流程和逐步方法,并讨论使用 3D 打印模具进行快速拉伸吹塑的主要优势和应用。
将吹塑瓶子成品的速度提高 70% 同时成本降低 90%
3D 打印是以低成本快速制作模具的强大解决方案。该工艺所需设备极少、可以释放 CNC 容量并节省技术操作人员的时间,让制造商将更多时间投入高价值任务。通过内部 3D 打印,制造商和产品设计师可以在产品开发过程中引入快速模具制作,以便在过渡到大规模生产之前验证设计和制造步骤。3D 打印模具早已用于注射成型或热压成型等工艺中,可实现快速迭代、加快产品开发,并将更好的产品推向市场。
对于模具制作而言,立体光固化 (SLA) 3D 打印技术是很好的选择。其特点是得到的打印模具表面光滑且精度高,可转化成最终部件,而且便于脱模。大幅面 SLA 3D 打印机 Form 3L 紧凑小巧、适用于办公室,却可制作大型部件和模具。
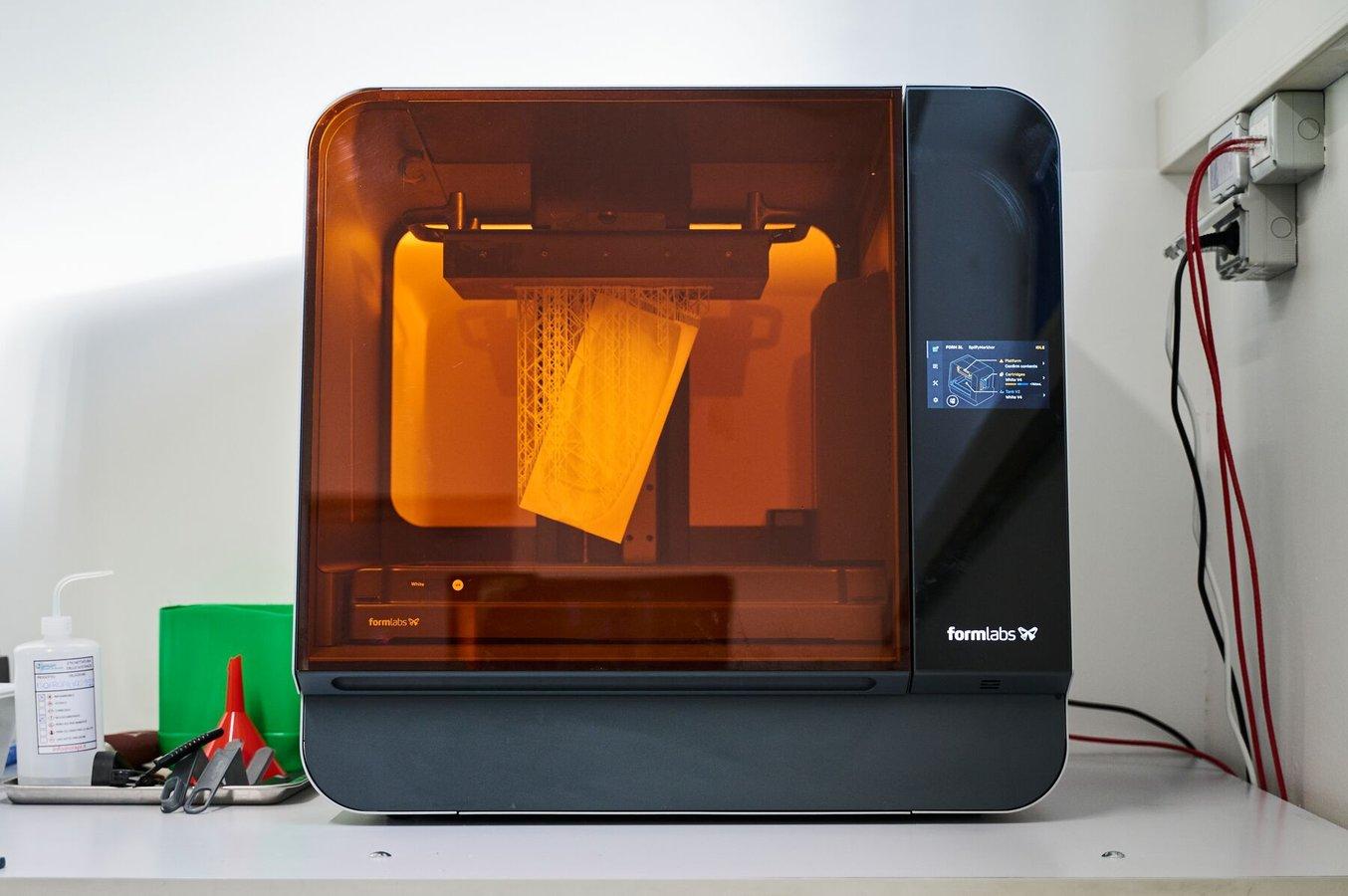
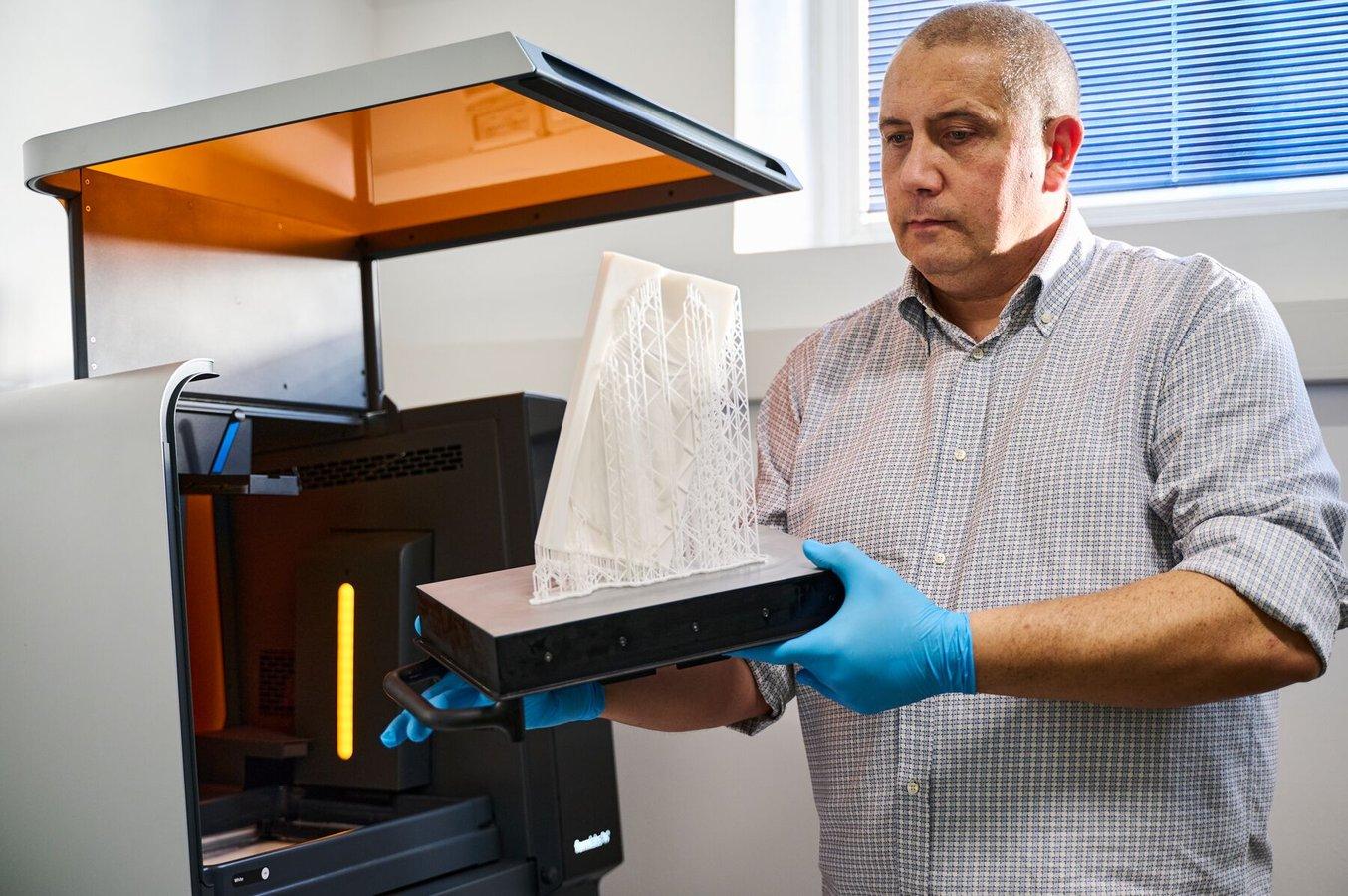
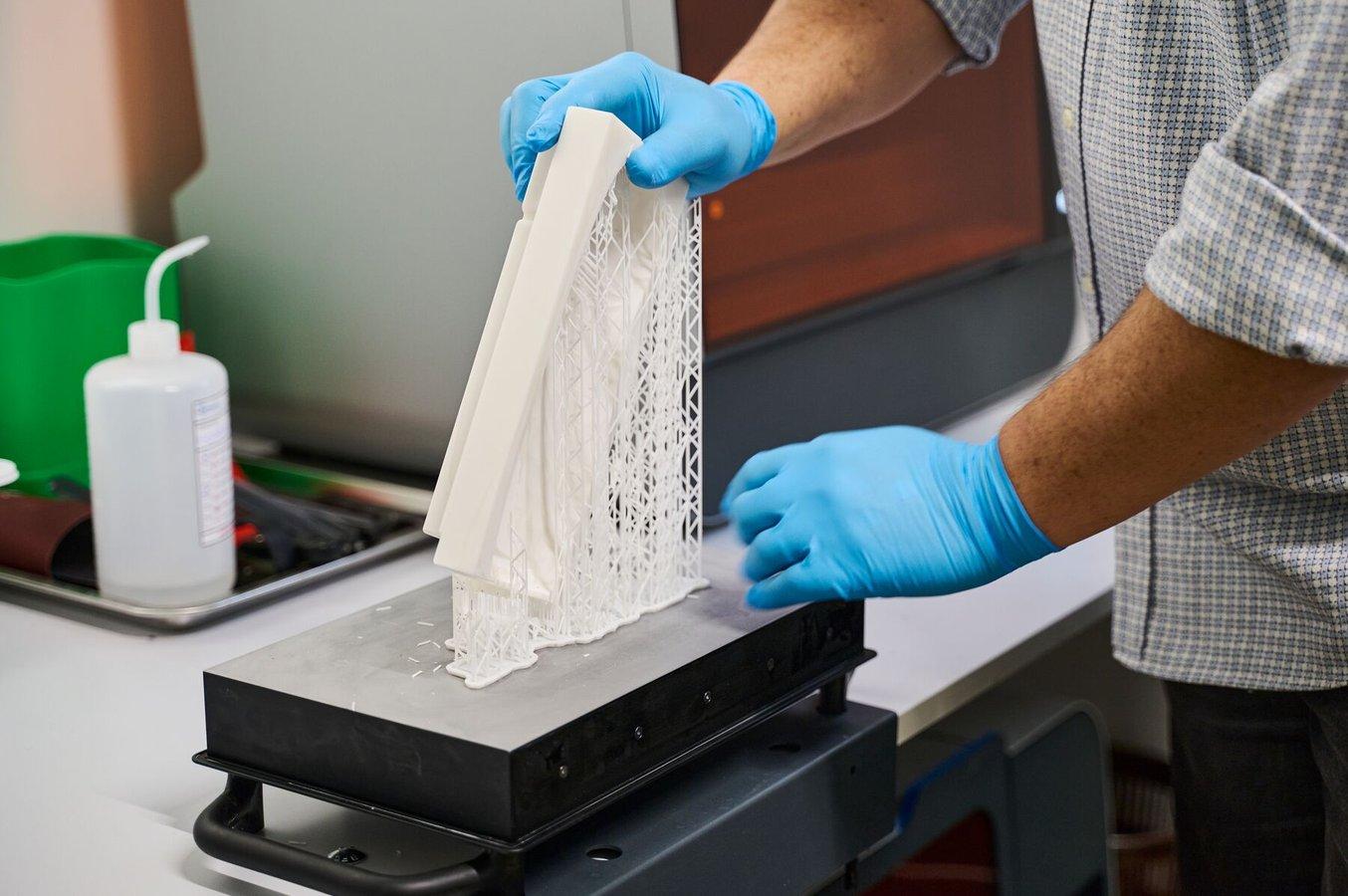
在 Form 3L 中使用 Rigid 10K Resin 正在打印的 3D 打印模具。
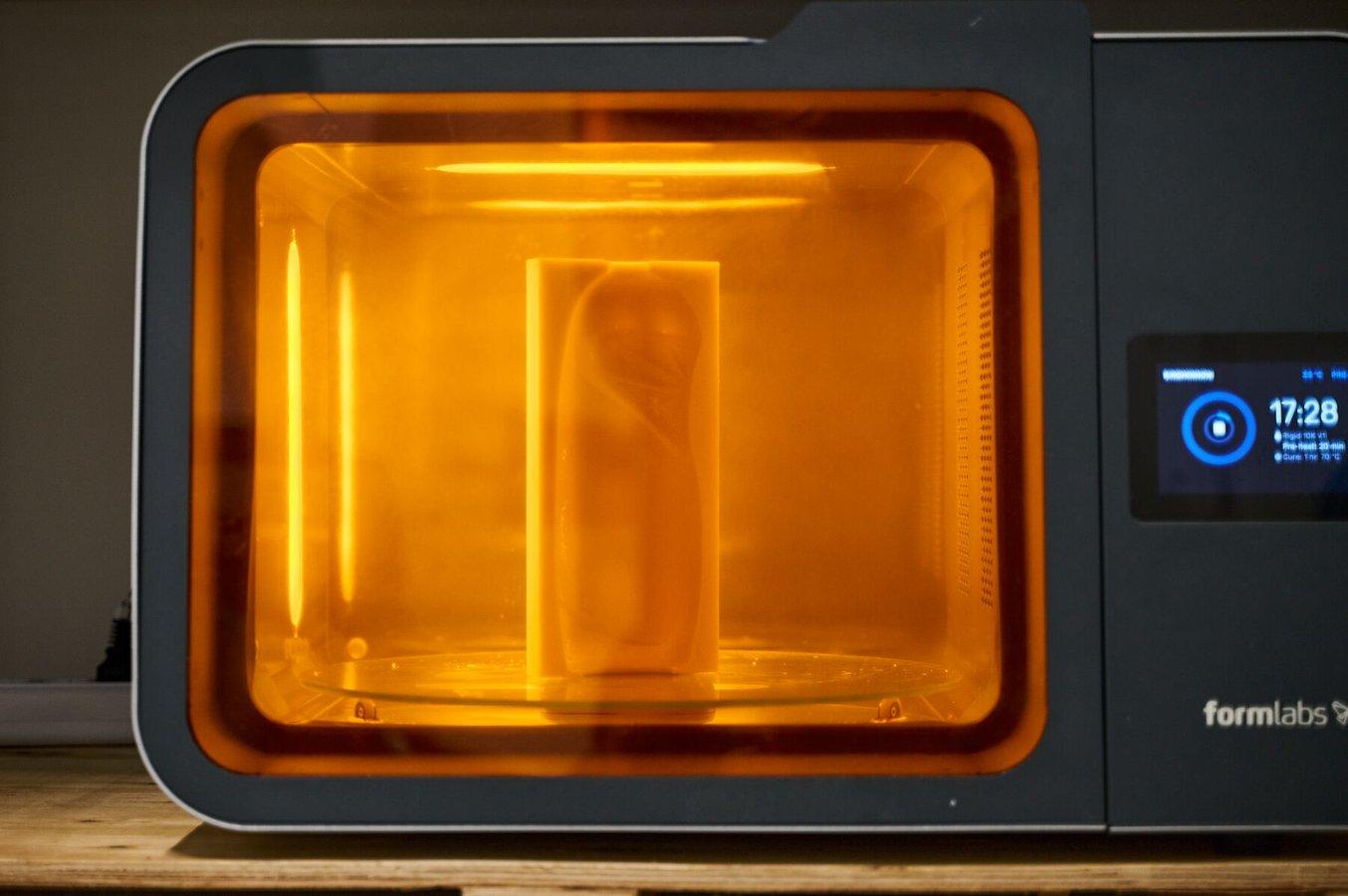
清洗后,移除支撑结构,后固化模具。
材料选择是生产模具的关键。联合利华和 Serioplast 需要一种既能承受 SBM 工艺的内部压力和温度,又能维持良好的尺寸精度和稳定性的材料。
Cademartiri 说道:“在 Formlabs 公司工程师的帮助下,我们确定了一种材料,这种材料可以让我们使用真实材料制作几个瓶子来进行测试。”
Rigid 10K Resin 具备出色的强度、硬度和耐热性,Formlabs 推荐将其用于制造 SBM 模具。这是一种工业级高度玻璃填充材料,在 0.45MPa 条件下的热变形温度为 218°C,拉伸模量为 10000MPa,使用 Rigid 10K Resin 打印的模具具有良好的尺寸稳定性,适用于数百次吹塑成型,重复性高。
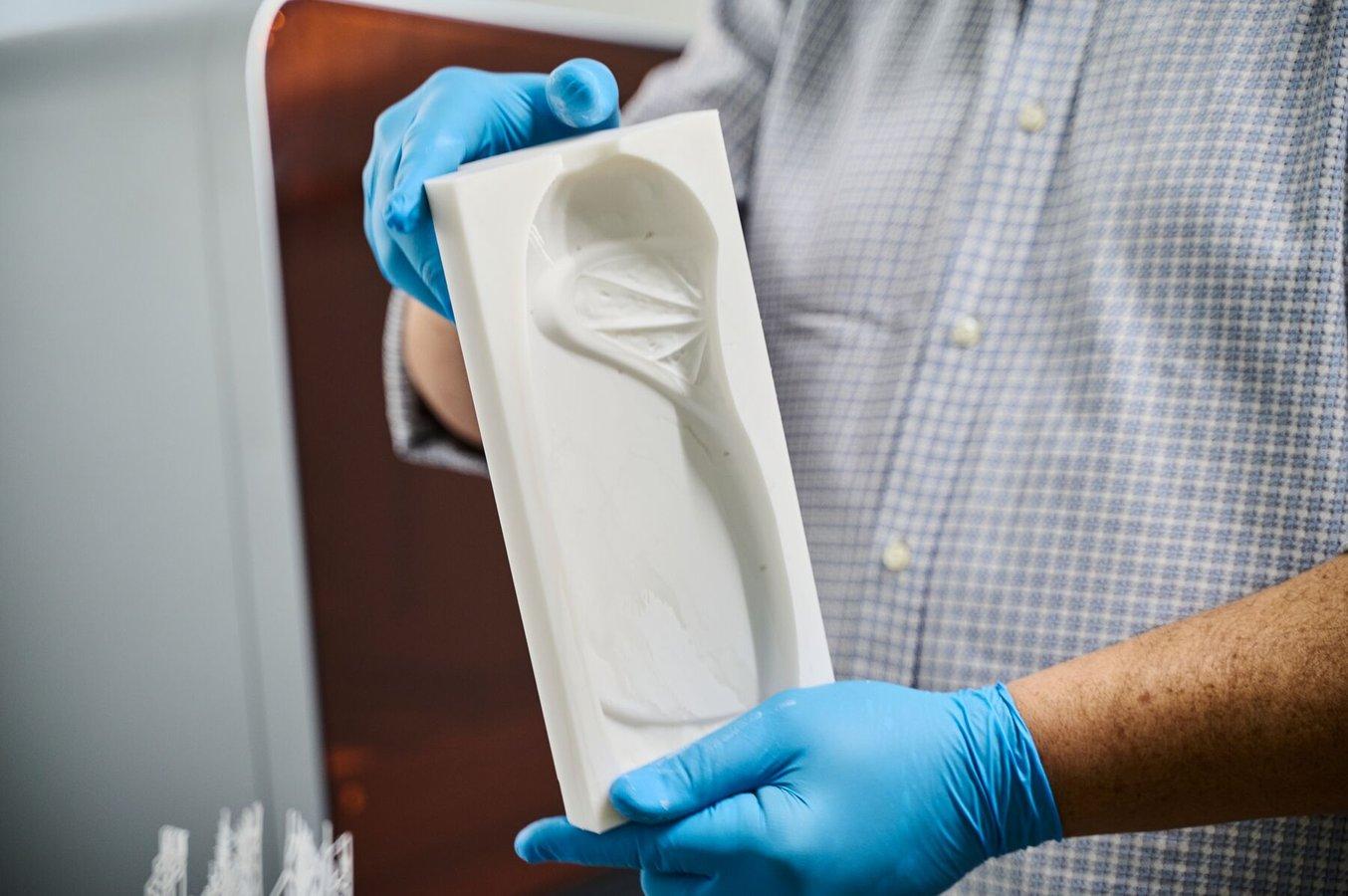
通过使用 Rigid 10K Resin,Serioplast 制作了表面光滑的精密模具,能够整合精细特征,包括 0.5mm 的小孔。他们使用抛光机或手工打磨进行后处理,以满足关键尺寸要求。在模具型腔的 CAD 文件中加入了纹理表面。
Cademartiri 说道:“我们对模具的细节进行了精确微调,特别是对于带有一些徽标或类似柠檬细节的瓶子,这需要很高的精度。Formlabs 机器和 Rigid 10K Resin 为获得极佳细节并将其转移到瓶子成品上提供了可能性。”
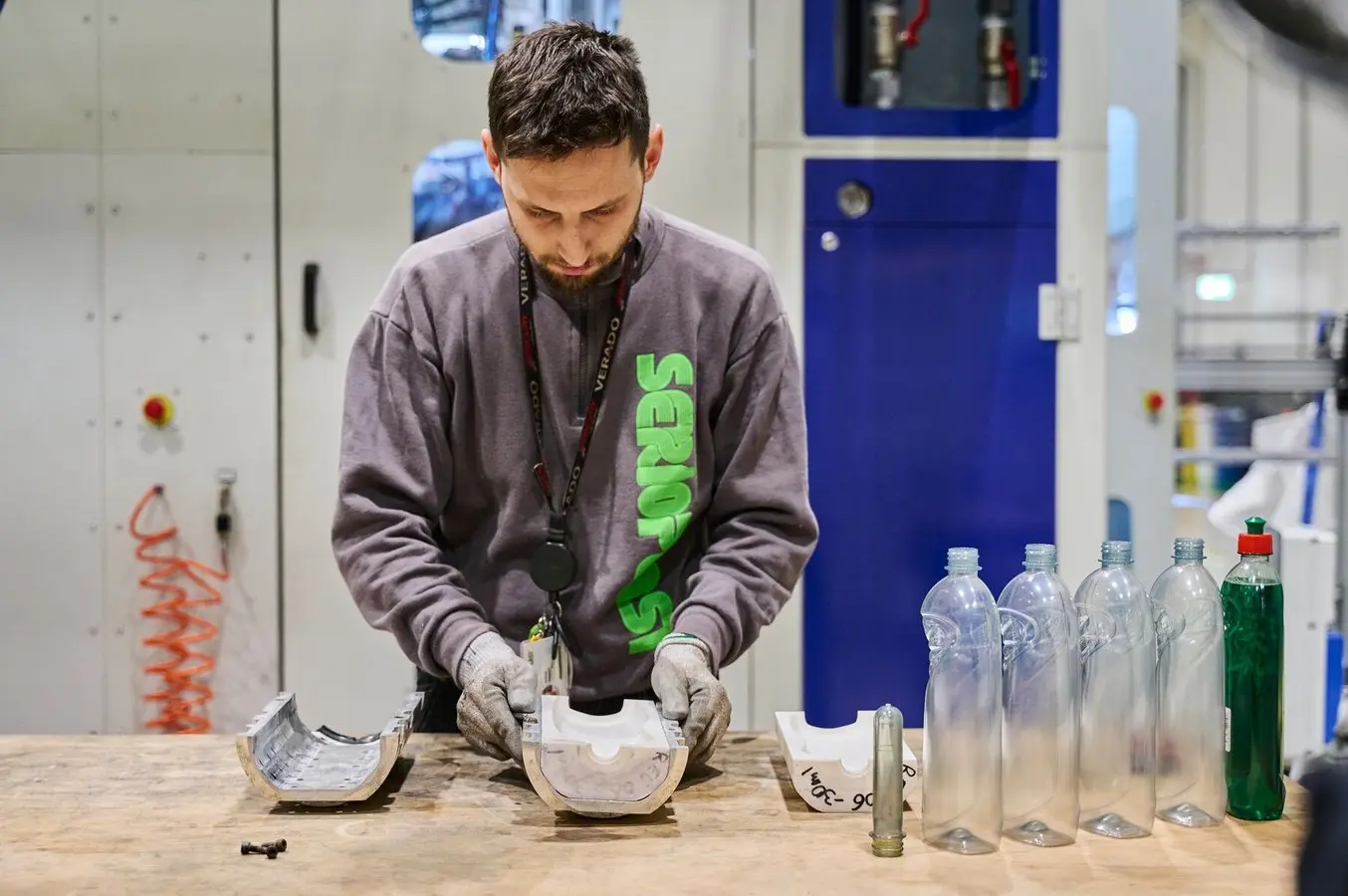
使用 Rigid 10K Resin 通过 3D 打印制造的模具经过手动抛光,然后组装到金属框架中。
使用 SLA 3D 打印技术制作模具只需要两天时间。3D 打印模具可将开始试点测试的周转时间从六周缩短到两周,同时提供接近生产级品质的逼真试生产部件,并使用与最终生产单元相同的材料和机械进行成型。此外,3D 打印模具还支持操作人员同时对多个设计进行试点测试
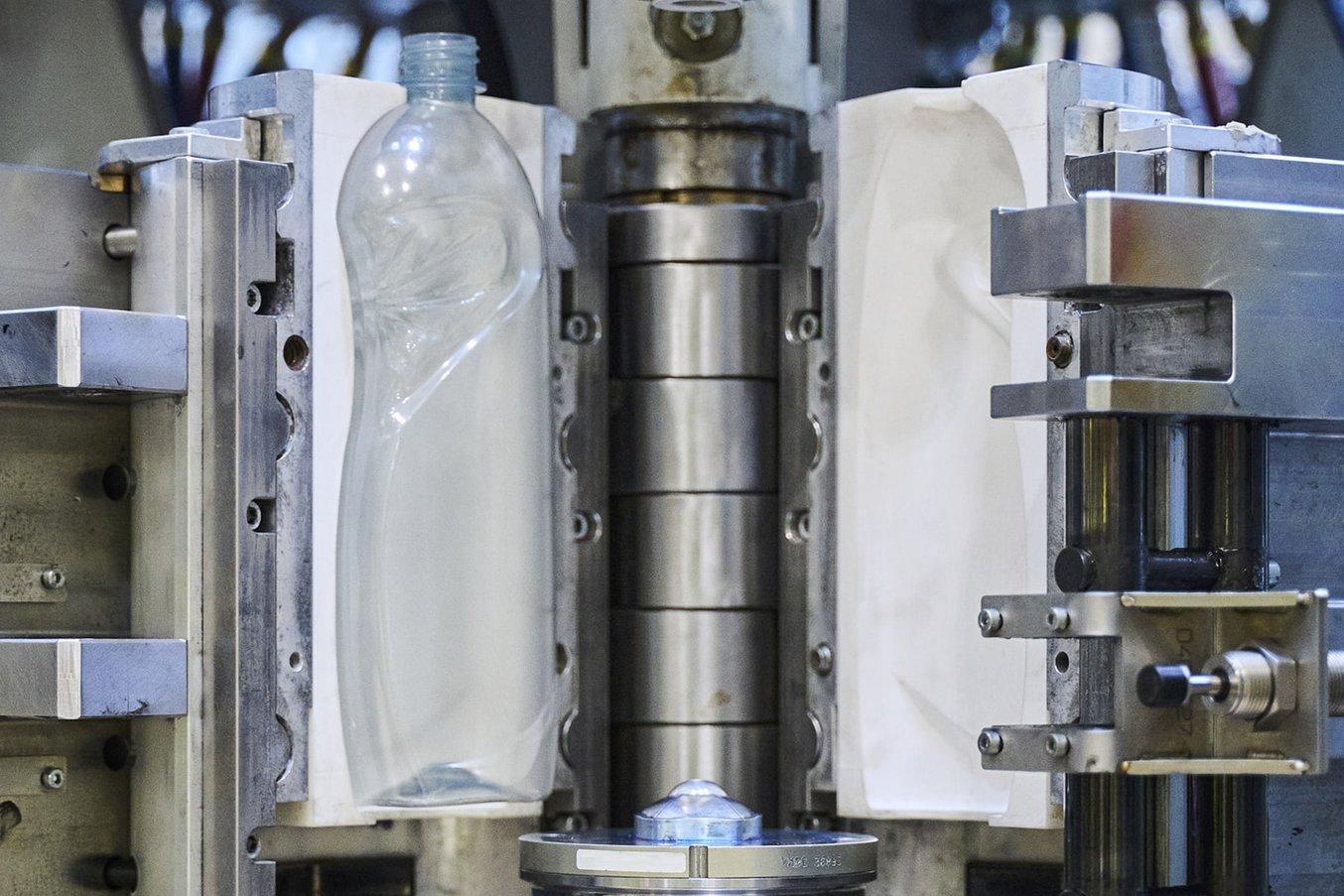
使用 Rigid 10K Resin 经 3D 打印制作的联合利华 Slice 750mL 瓶子模具,安装在机器上的外壳支架上。该团队可以使用与标准试模相同的工艺窗口,从而可靠地测试最终工艺。
“借助 3D 打印模具,我们就可以在吹塑机中放置的外壳支架内使用标准布局。因此,我们在模具设计上节省了大量时间,而且能够非常轻松地管理 3D 打印计划,”Migliarelli 说。
200 个生产单元 | 加工金属模具 | 3D 打印模具 |
---|---|---|
Equipment | 内部 CNC 机器或外包 | Form 3L Rigid 10K Resin |
试点测试周转时间 | 6-8 周 | 2 周 |
模具制作成本 | 2500-10000 美元 | 500-1000 美元 |
“与标准模具相比,使用 3D 打印模具,我们可以节省多达 70% 的时间和 90% 的成本。过去,[客户]仅为一个设计就需要等待长达 12 周,而现在在相同的时间内我们可以进行五次设计。”
Flavio Migliarelli,Serioplast 全球服务公司研发设计经理
使用传统方法进行如此数量的测试几乎不可能。他们需要针对每种设计投资金属模具,却无法获得规模经济效益,同时永远无法收回模具成本。
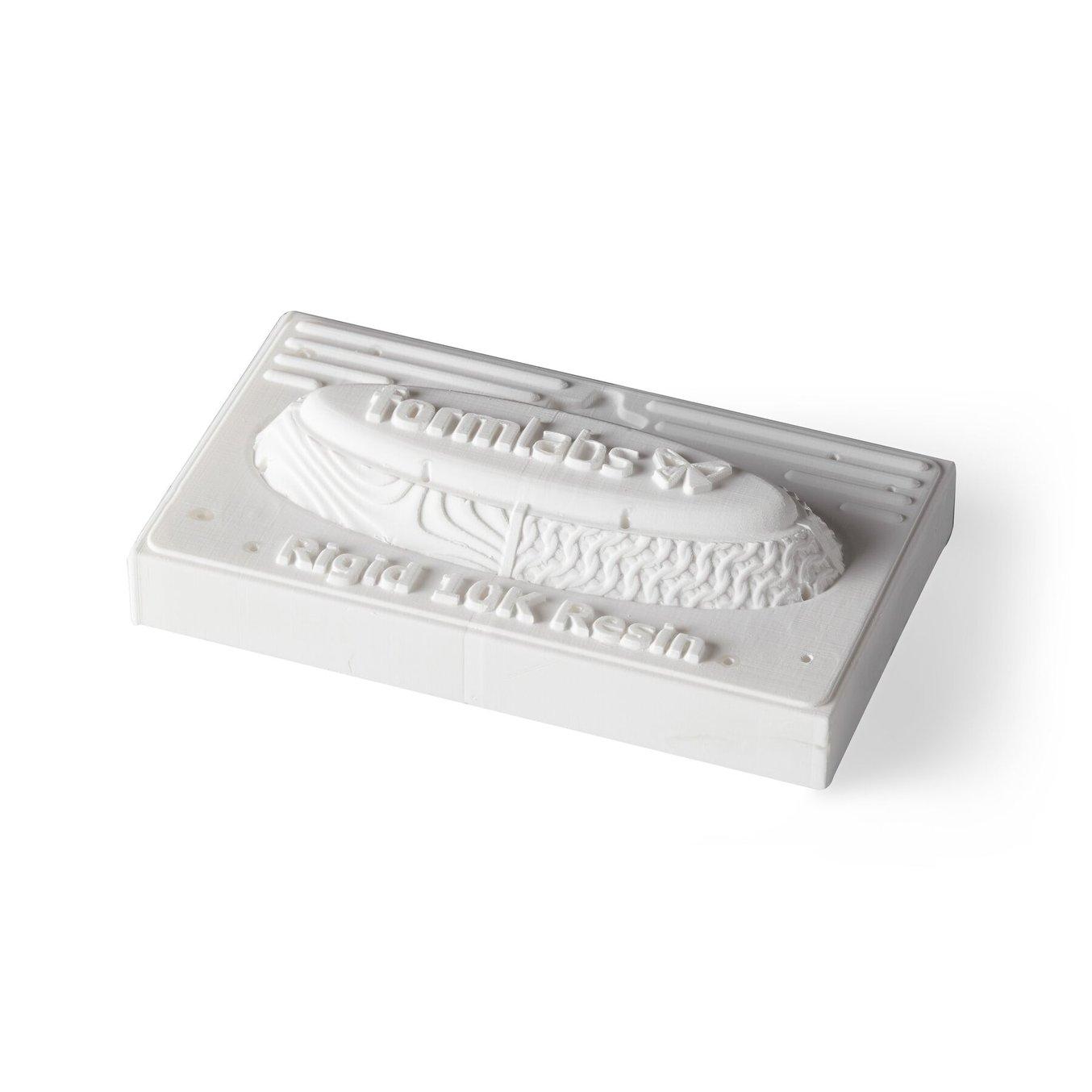
从客户测试到启动生产线
3D 打印模具主要用于生产样品部件,供消费者测试。它们在触感、外观和使用方面都能代表最终产品,在消费者眼中,它们就是真正的产品。
“在制作真正的模具之前,您可以先制作一个瓶子实物,以便立即确定开发方法是否正确,或者是否需要进行更改,以避免出现错误,从而造成更大的损失。”
Stefano Cademartiri,联合利华 CAD 和原型制造负责人
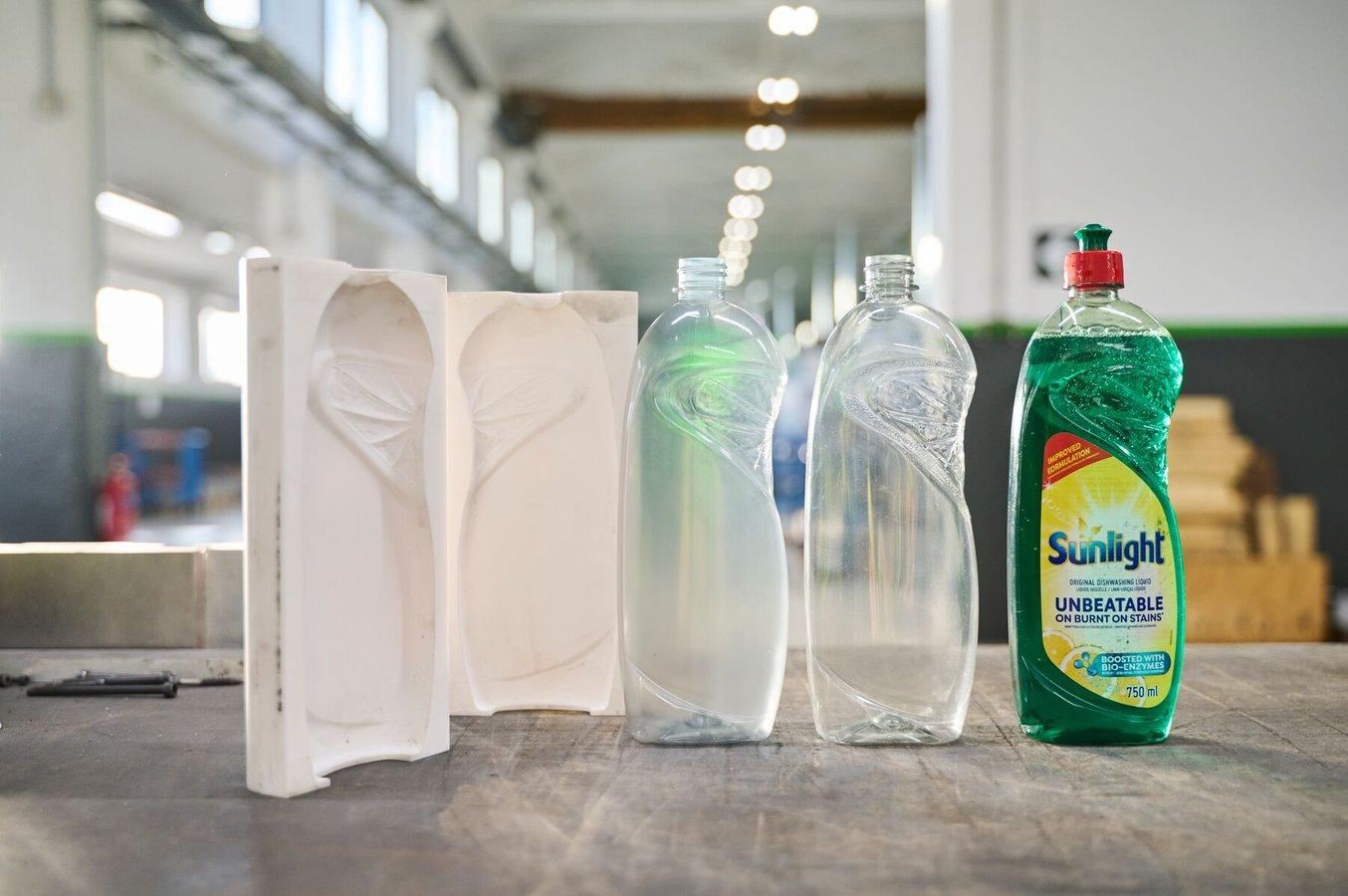
使用 3D 打印模具生产的瓶子与通过传统金属模具工艺生产的最终产品几乎别无二致。从左到右:使用 Rigid 10K Resin 3D 打印的两件式模具、使用 Rigid 10K Resin 3D 打印模具生产的瓶子、使用金属模具生产的瓶子,以及用于客户测试的标签原型瓶。
模块化模具的另一个用途是验证 SBM 工艺以及待吹塑的 PET 瓶坯,以便观察工艺窗口、拉伸比和可行的材料分配。Serioplast 通过注射成型在内部生产瓶坯。虽然有些瓶坯是为特定瓶子量身打造,但他们通常使用用户无法修改的标准化产品。Serioplast 团队希望了解这种库存瓶坯的可用功能范围。这有助于他们在投入生产之前确定给定瓶坯是否适合吹塑特定瓶子。
“我们使用的工艺窗口与标准试模相同。这非常好,因为我们可以测试最终的工艺窗口并观察瓶子的变化。在此过程中,我们采用高达 30 巴的压力。结果非常出色可靠。此外,我们还在 100°C 下对瓶坯进行加热,但这并未对 3D 打印模具的型腔造成任何磨损。我们每天可以轻松生产多达 100、200 个瓶子。随着时间的推移,我们的产量可以达到 1000 瓶,”Migliarelli 说道。
快速生产模具的第三个用途是对生产线的某些方面进行早期测试。由于使用 3D 打印模具成型的瓶子非常接近生产单元,因此可以用于对灌装生产线进行一些初步验证,如生产线的移动、装瓶机星轮的运行、封盖或机器人装箱机的动作。及早对生产线进行试点测试可使工厂提前准备备件、为大规模生产做好准备,并加快产品上市速度。
加速优质产品上市
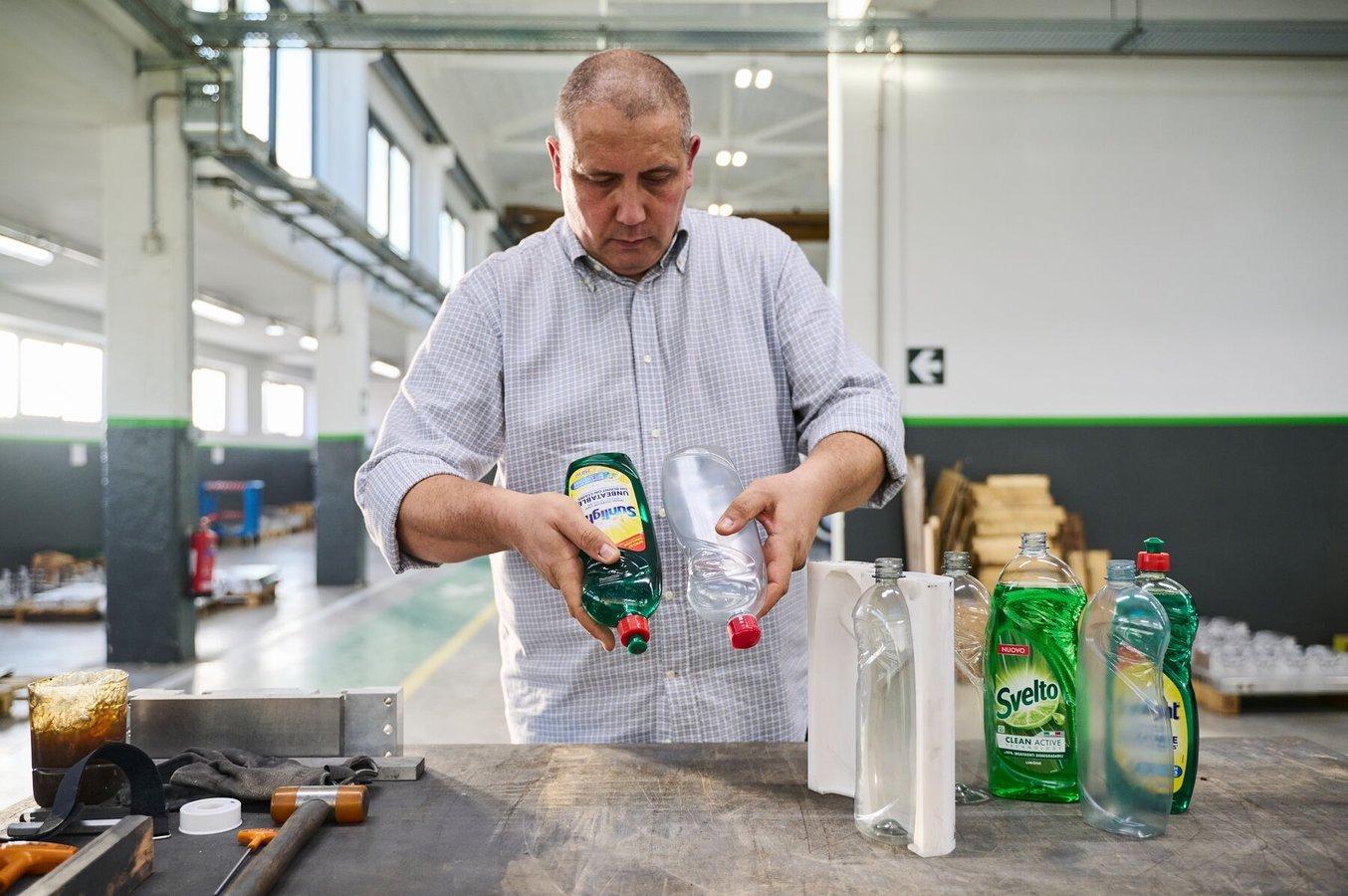
Cademartiri 和 Serioplast 已经使用新工艺测试了大约 15 种不同型号的瓶子。
通过使用 Formlabs SLA 打印机和 Rigid 10K Resin,联合利华和 Serioplast 能够将周转时间缩短 70%,将模具成本降低 90%,仅用两周时间就能试生产 200 个产品。
“Formlabs 是我们的出色合作伙伴,他们不仅销售机器,还支持我们了解这些材料的特性。这种合作伙伴关系有助于我们确定是否可以使用 3D 打印模具,”Cademartiri 说道。
新的工作流程支持联合利华更快地向市场推出更优质的产品,并大幅降低与开发包装相关的风险和成本。
“3D 打印机给我们带来的最大影响就是梦想成真的可能性。只需要数周时间,电脑屏幕上的设计就会出现在你的手中。真实的产品、瓶子、瓶盖和标签,”Cademartiri 说。
您是否还有关于使用 SLA 打印机进行吹塑成型或其他工程和制造应用的问题?请下载我们的白皮书,了解详细的工作流程,联系我们的解决方案专家,或索取使用 Rigid 10K Resin 打印的免费样品部件。