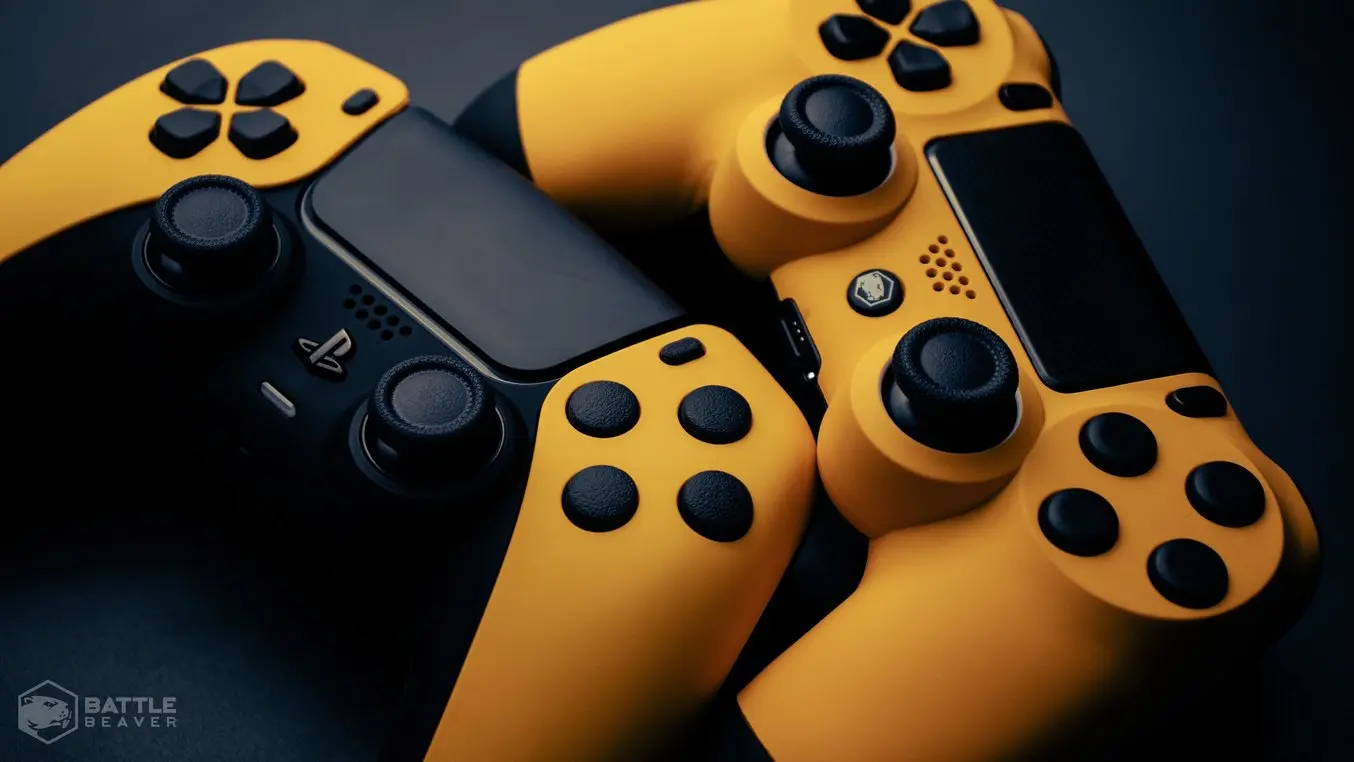
Fuse 1으로 프린팅한 버튼을 사용한 컨트롤러(왼쪽)와 사출 성형으로 제작된 버튼을 사용한 컨트롤러(오른쪽).
배틀 비버 커스텀스(Battle Beaver Customs)는 맞춤형 게임 컨트롤러를 통해 게임을 즐기는 동안 최고의 경험을 제공하는 데 중점을 두고 있습니다. 수정을 끊임없이 반복하여 컨트롤러의 반응성과 경쟁력을 향상하고 플레이어가 게임 잠재력을 높이고 다양한 게임에서 최고의 성능을 발휘할 수 있게 합니다.
배틀 비버 커스텀스는 Form 2 SLA 프린터와 Fuse 1 SLS 프린터로 이뤄진 FDM 장비를 포함하여 인하우스 3D 프린터를 여러 대 갖추고 있습니다. 최근에는 아웃소싱으로 제작하던 컨트롤러 내부 파트를 Fuse 1으로 제작하여 최종 사용 파트를 인하우스 제작으로 충당하기 시작했습니다. 그러자 리드 타임은 몇 주나 단축되었고 배틀 비버 커스텀스는 공급망 문제에서 자유로워졌습니다.
이 글에서는 연구 개발 책임자인 마이클 크루넬(Michael Crunelle)의 이야기로 배틀 비버 커스텀스가 시장을 선도하는 게임 컨트롤러를 계속 출시해낸 방법을 알아보겠습니다.
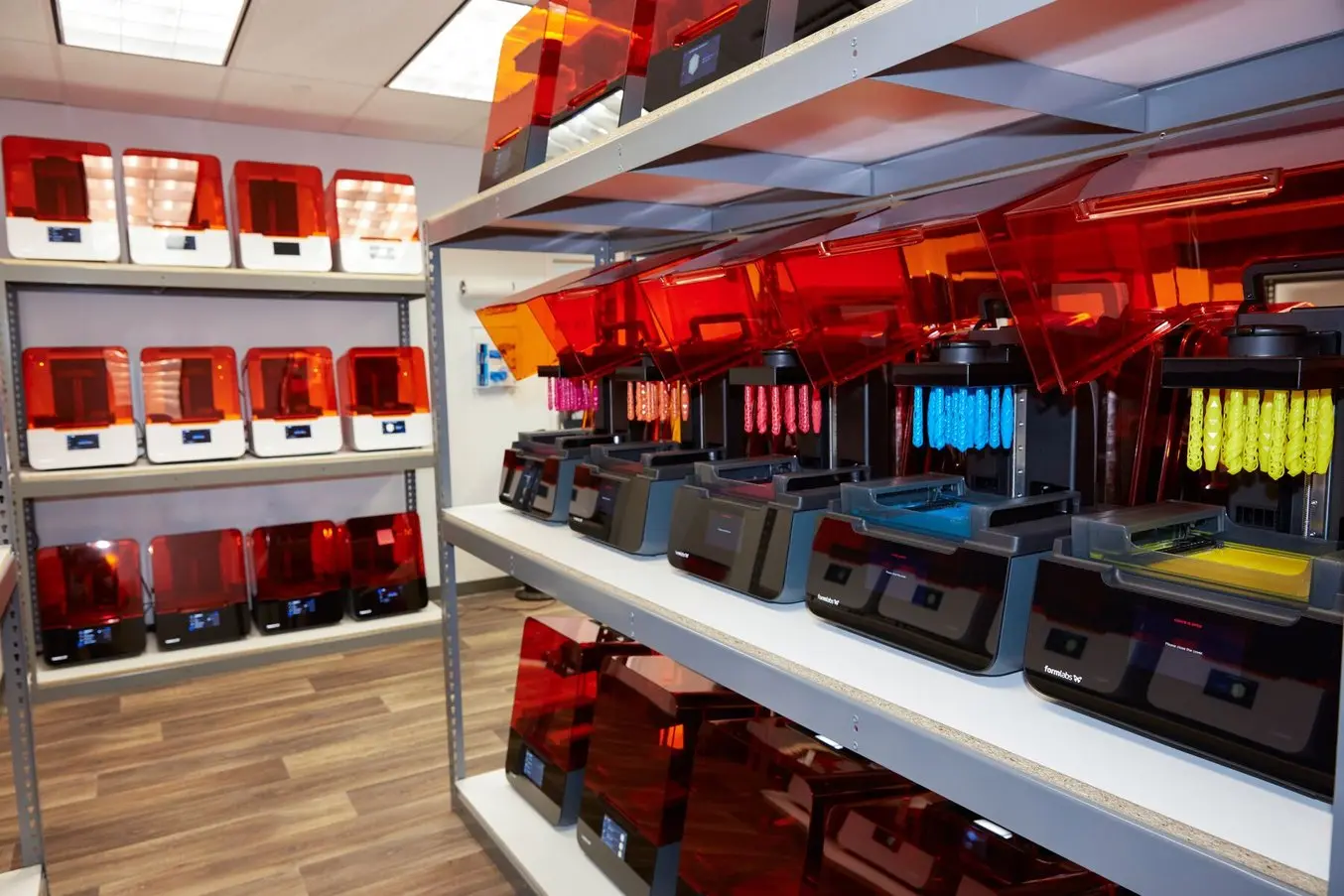
3D 프린팅 최종 사용 파트로 소량 생산과 맞춤형 제작 분야를 개척한 방법
웨비나에서 3D 프린팅을 이용해 맞춤형 생산과 최종 사용 파트 소량 생산을 신속하고 비용효율적으로 진행한 방법을 알아보세요.
시장에서 경쟁자 물리치기
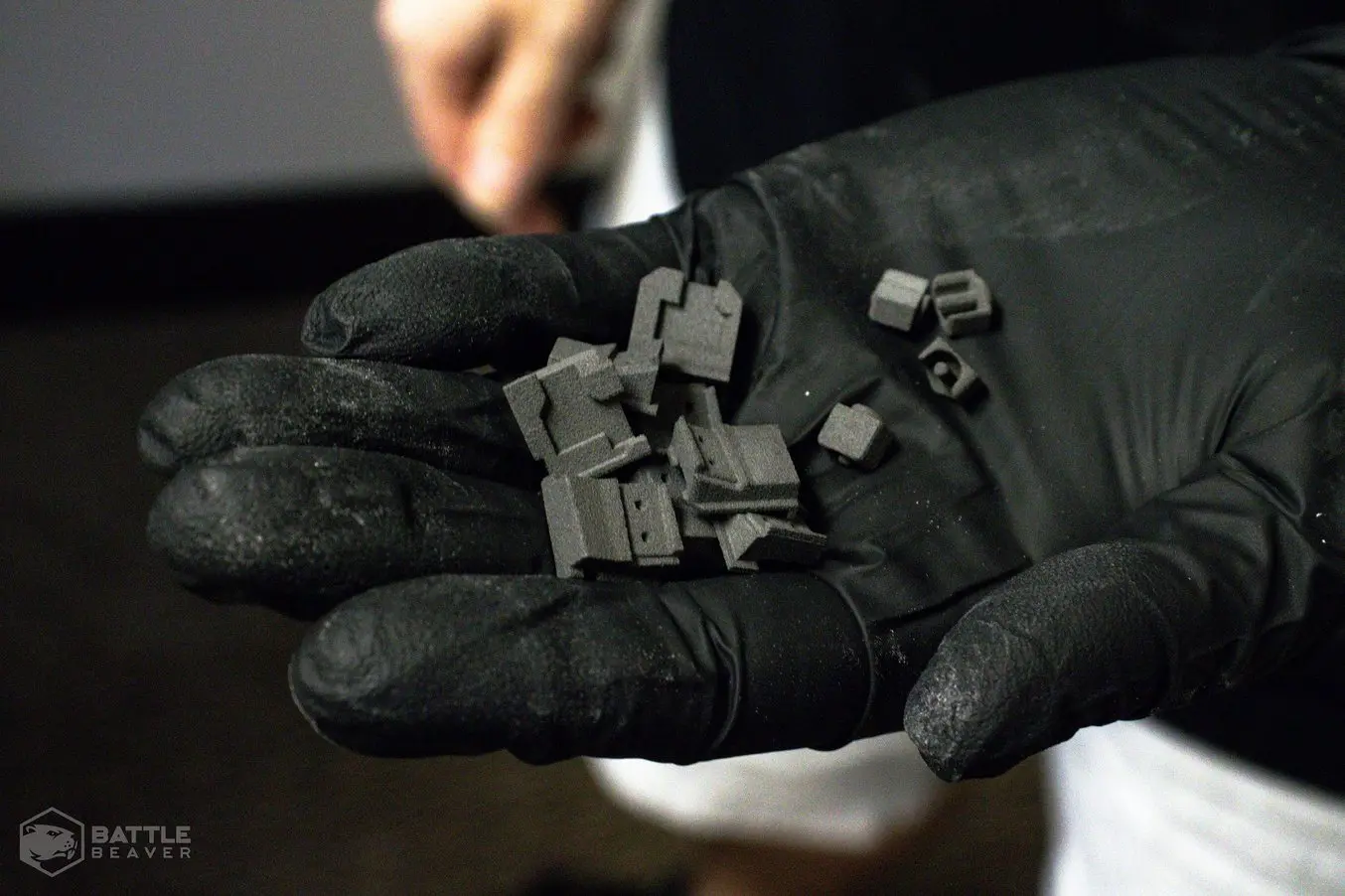
배틀 비버 커스텀스의 고성능 컨트롤러에 사용되는 내장 파트
단일 콘솔 제품 생애 주기를 거쳐온 게임 컨트롤러는 내장 파트의 설계 변화를 여러 번 거치게 되었습니다. 배틀 비버 커스텀스 같은 커스텀 컨트롤러 제작사에는 이런 상황이 두통 유발의 원인이 되었습니다. 그들의 오래된 마운트와 버튼 디자인이 새 컨트롤러와 맞지 않게 되었기 때문입니다.
배틀 비버 커스텀스는 Fuse 1을 이용한 신속 프로토타이핑으로 자사 제품의 마운트와 버튼 디자인을 재빨리 변경할 수 있었습니다. 맞춤형 소비자 제품을 제작할 때 처리 시간이 짧으면 경쟁업체보다 앞서 나가고자 하는 기업에게는 이익이 될 수 있습니다. 크루넬 씨는 "Fuse 1은 컨셉에서 최종 사용품에 이르기까지 각 단계에서 설계를 빠르게 변경하기에 좋은 도구였습니다. 경쟁사에서 따라올 수 없죠."라며 만족감을 드러냈습니다.
최근에 Playstation 5 컨트롤러의 내부 디자인을 재설계할 때, 크루넬은 새 마운트를 설계하는 데 시간을 많이 소비했고 "Playstation 4가 제품 생애 주기를 지내오는 동안 [Sony]가 Playstation 컨트롤러 내부를 4번 정도 다시 설계하는 바람에 Playstation 5 컨트롤러는 이미 두 번째 버전을 맞이 했습니다. 이는 곧 내부 플랫폼 설계를 변경해야 한다는 의미와 같습니다. PlayStation 5 컨트롤러를 생산하려면, 48시간 안에 새 플랫폼을 설계하고 프린팅하여 소니의 수정 사항이 작동하도록 해야 했습니다. 이런 작업은 일반적으로 몇 주 또는 몇 달이 걸리는 일이지만 지금은 문제 없이 처리할 수 있죠”라며 당시를 회상했습니다.
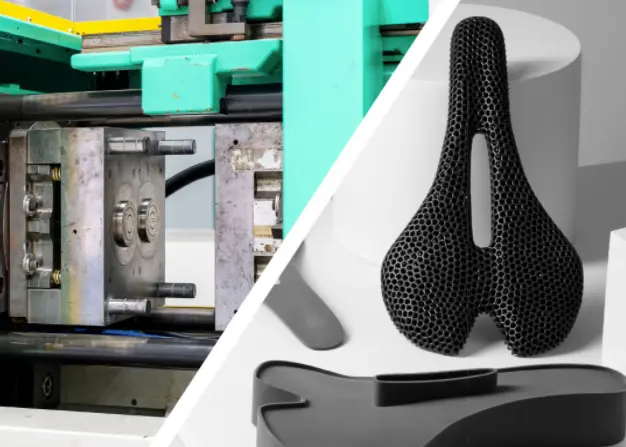
SLS 3D 프린팅 vs. 사출 성형: 사출 성형을 3D 프린팅 방식으로 전환해야 하는 시점
본 백서에서는 실제 사용 사례의 비용 역학과 SLS 3D 프린팅, 사출 성형 또는 두 가지 모두를 함께 사용하는 데 필요한 지침을 제시합니다.
합리적인 인하우스 SLS 프린팅을 이용한 (외주제작) 사출 성형 대체
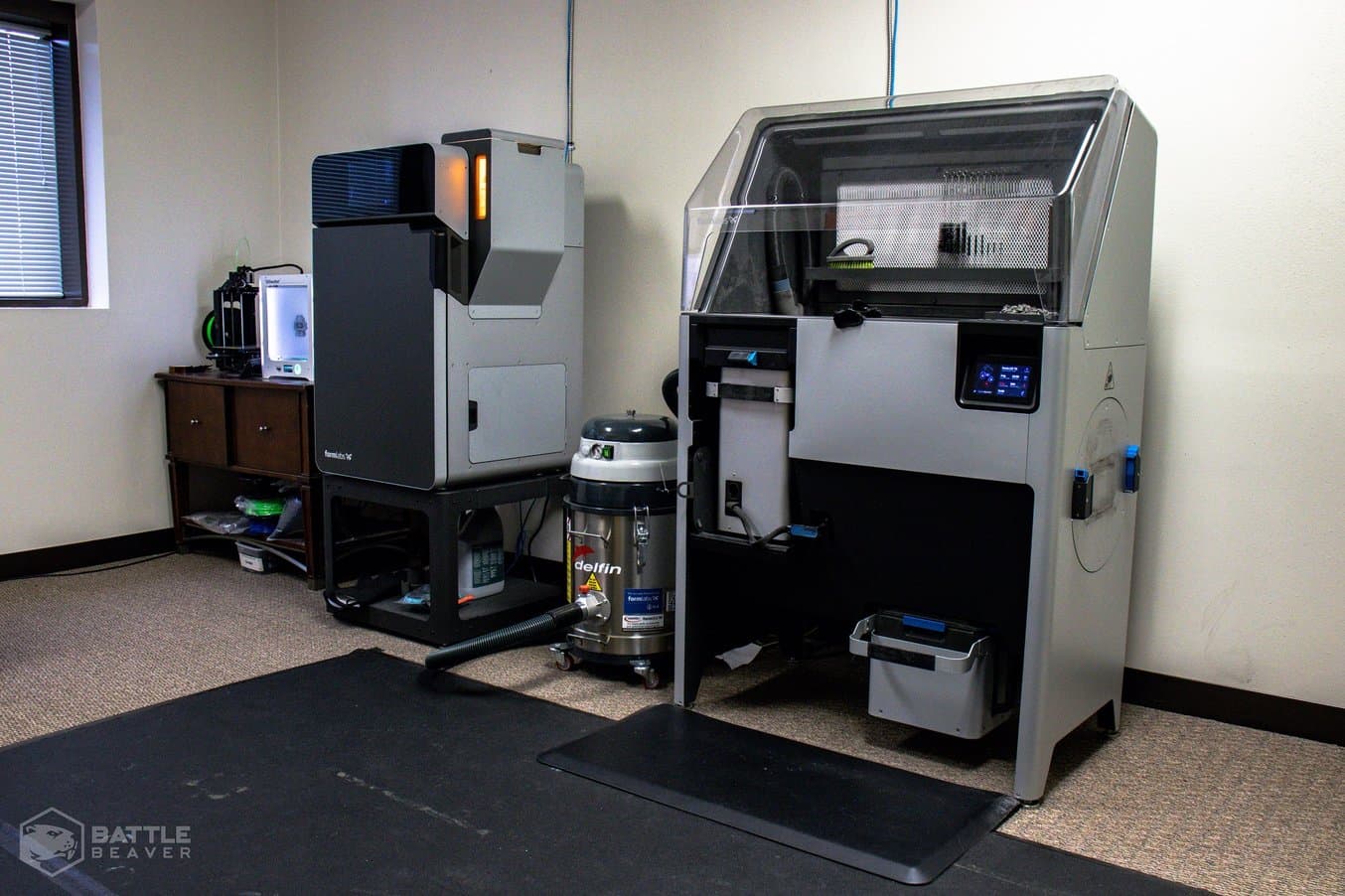
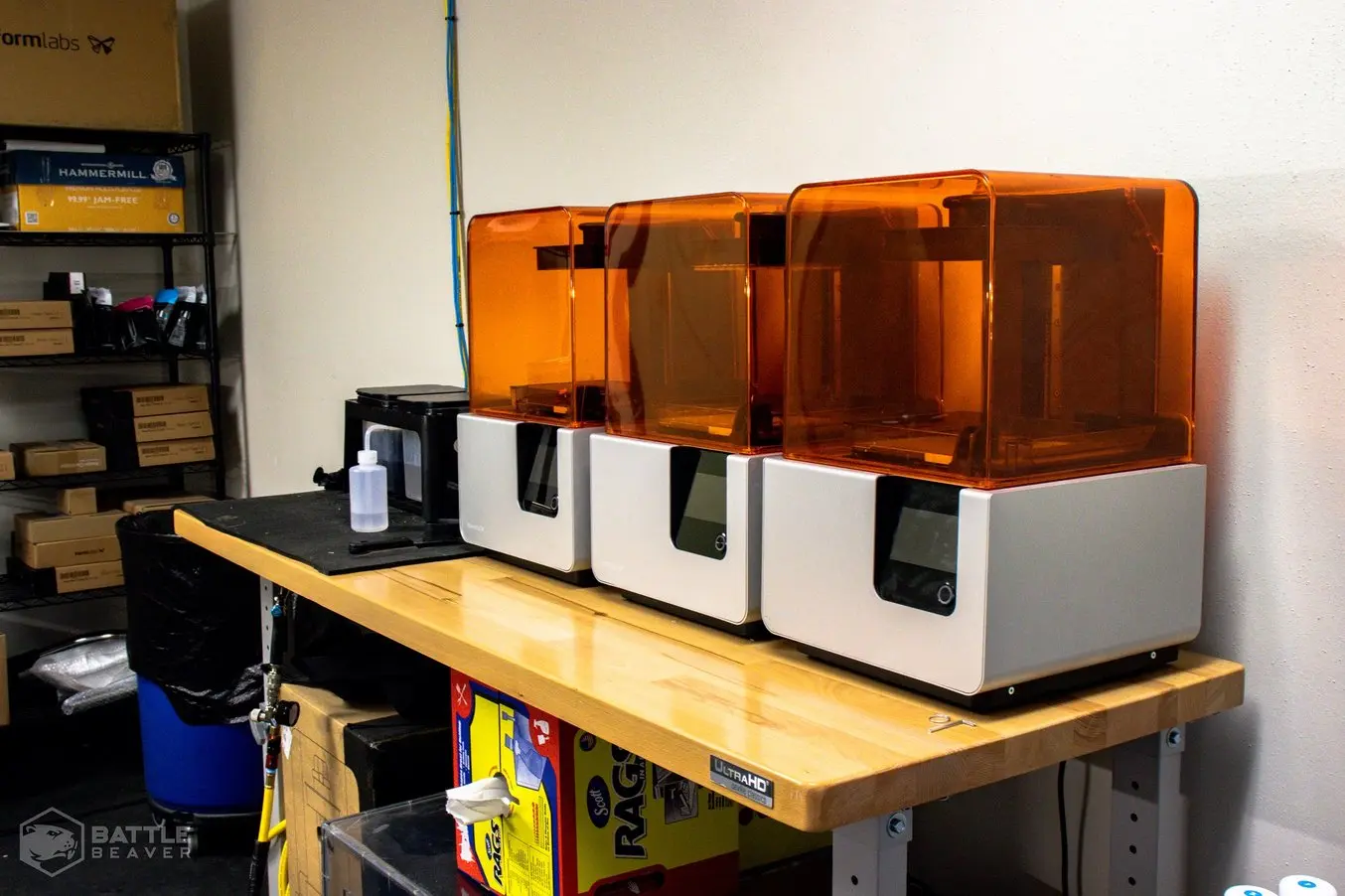
팀은 생산 물량의 대부분을 Fuse 1으로 이전했지만 프로토타입 제작과 일부 최종 사용 파트는 Form 2 SLA 프린터 플릿으로 생산합니다.
시작은 크루넬이 eBay에서 구매한 Form 1+ 한 대였지만 Form 2 프린터 세 대로 이뤄진 플릿으로 업그레이드하는 데까지 이르게 된 것입니다.
크루넬에 따르면, SmartPad의 d-패드 교체품과 표면 마감이 매끄러워야 하는 외장 파트를 제작하는 데는 여전히 Form 2를 이용하고 있다고 합니다. 한편, 나일론은 기타 물성덕분에 내장 파트 수정을 선도하는 역할을 하고 있습니다. 크루넬은 "레진과 비교하면 나일론 분말을 사용했을 때 에폭시와 글루 사용이 편리합니다. 내열성이 우수한 점 또한 큰 부분을 차지하고 있죠. 철제 팁을 용접하다보면 나일론 파트와 가까워질 수 있지만 녹지 않아요."라고 설명합니다.
배틀 비버 커스텀스는 Fuse 1 덕분에 내장 마운트와 파트 전부를 인하우스 생산으로 전환할 수 있었습니다. 이전에는 사출 성형으로 제작한 파트를 중국에서 미국으로 배송 받아야 했습니다. Fuse 1의 빌드 챔버에서는 500~800 파트를 한 번에 제작할 수 있으므로 팀은 파트를 주문형으로 일괄 생산하고 있으며 Fuse 1 한 대만으로eh 외주 제작 물량을 전부 생산하고 있습니다.
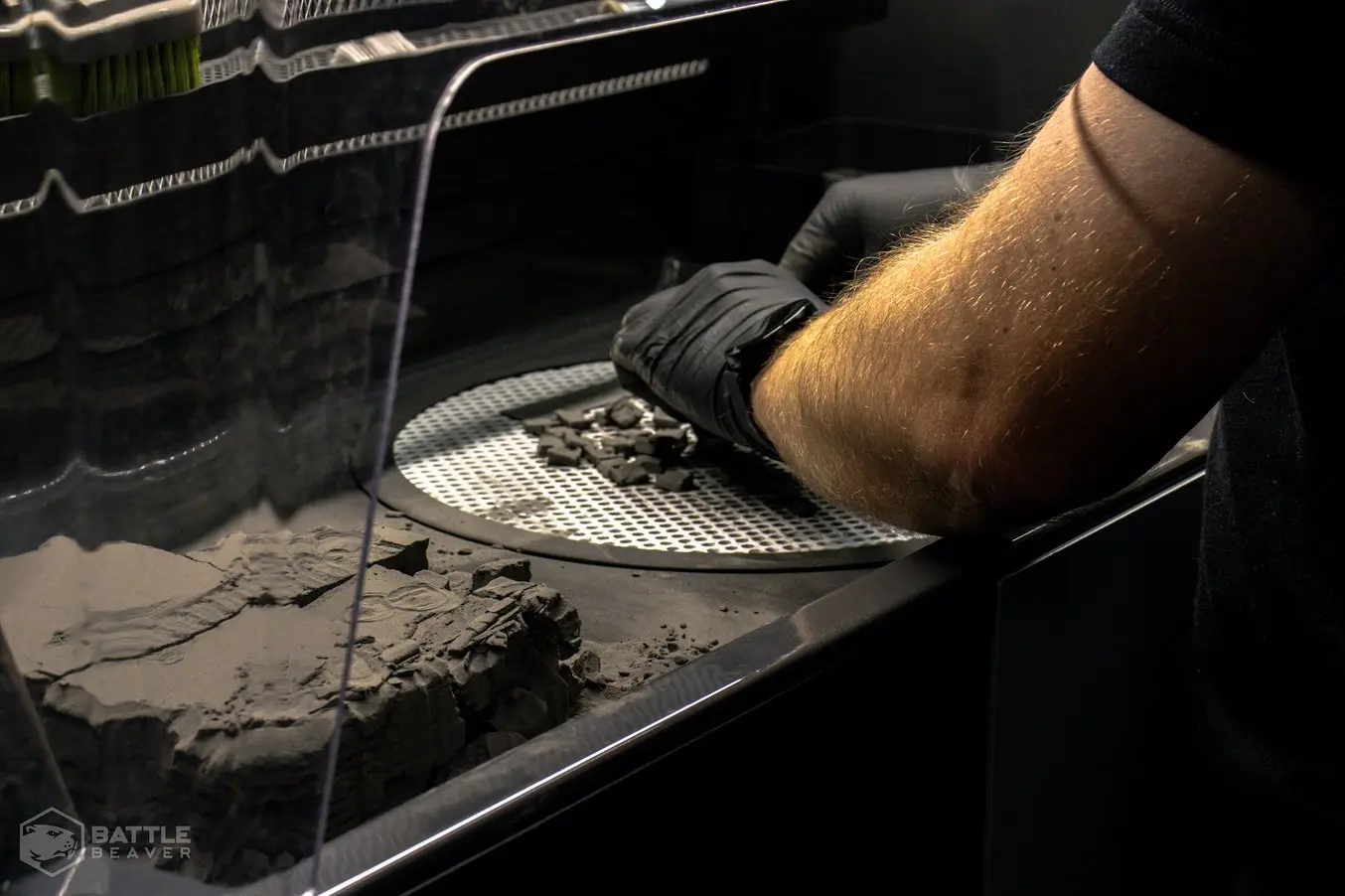
프린팅이 끝난 파트는 Fuse Sift로 옮긴 후 미디어 블라스팅을 거친 후에 사용합니다.
팀이 인하우스 3D 프린팅 역량을 갖추자 리드 타임이 몇 주나 줄어들고 공급망 문제와 오래 걸리던 리드타임이 해결되었습니다. 새로운 내장 파트의 시장 출시 기간이 6개월에서 며칠로 단축되자 신제품을 제작하는 데 수반되는 위험이 줄어들었고 혁신과 다양한 제품 확보의 가능성이 늘어났습니다.
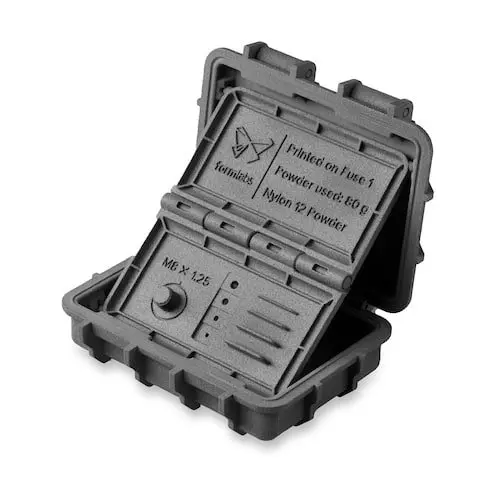
기존 파트의 주문형 생산
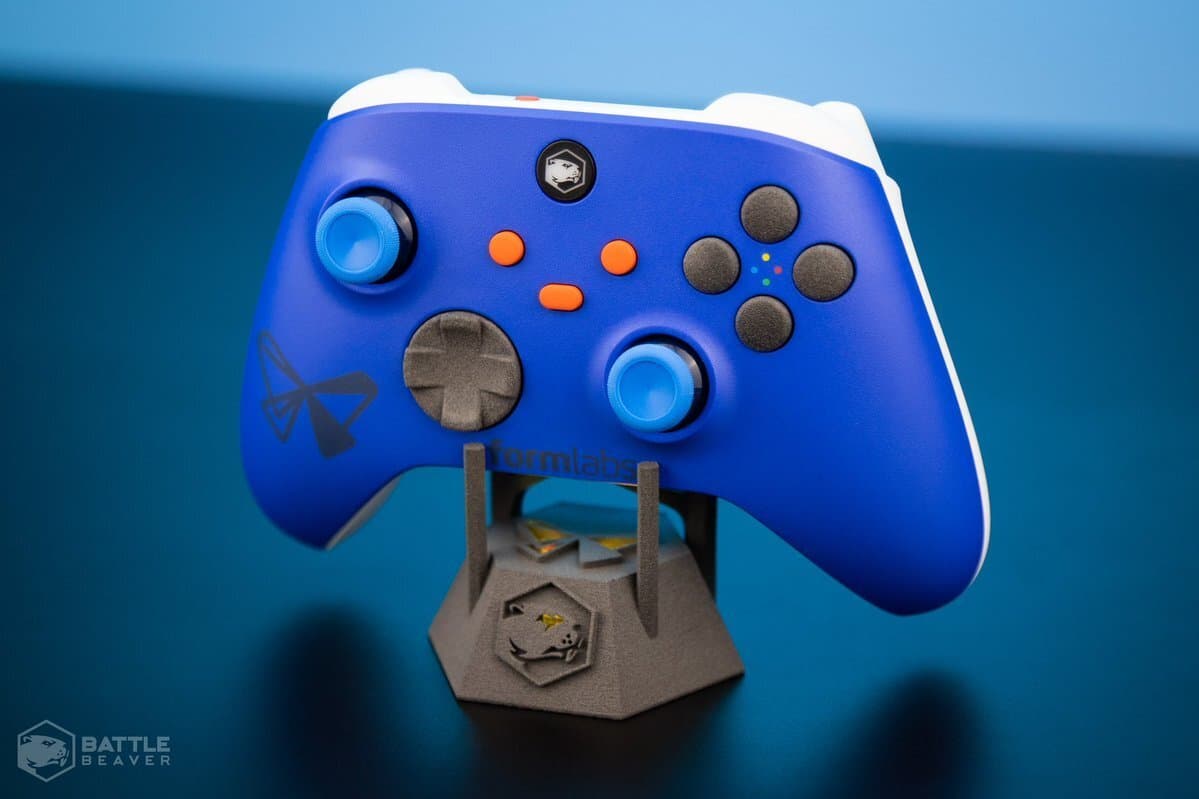
Fuse 1으로 제작한 SLS 파트를 사용한 Formlabs의 커스텀 XBOX 컨트롤러.
더욱이 컨트롤러의 생산 물량이 늘어나자 오래된 파트까지도 인하우스 3D 프린팅을 이용해 소량 일괄 생산할 수도 있게 되었습니다. 고객이 구버전 컨트롤러를 개조하고 싶어하면 적당한 STL 파일을 로드하여 파트를 프린팅한 뒤 배송하면 됩니다. 오래된 파트를 재고로 관리하는 데 드는 비용을 절감할 수 있으니 제품을 더 폭넓게 구비할 수 있습니다. 크루넬은 “Fuse 1으로 다양한 구조를 프린팅할 수 있는 자유를 얻자 필요에 따라변경할 수 있고 변경할 때마다 공구 제작에 드는 비용을 걱정할 필요가 없습니다.”라며 만족감을 드러냈습니다. 이전에는 비용과 생산 시간 때문에 배틀 비버 커스텀스가 지원할 수 있는 레거시 컨트롤러 모델이 한정적이었습니다.
최종적으로 인하우스 SLS 3D 프린팅 덕분에 예상치 못한 프로젝트에서 다양성을 확장하게 된 점은 기대하지 않았던 장점입니다. 배틀 비버 커스텀스의 일괄 생산 규모가 파트 500개를 넘어선다는 점을 고려하면 생산 과정에서 시간이 많이 걸리는 작업은 미디어 블라스팅입니다. 크루넬은 커스텀 스탠드를 제작하는 데 Fuse 1을 사용했고 블라스팅 유닛에 들어가는 모터를 구매했습니다. 그러자 파트는 20분간을 혼자 회전하게 되었고 후처리 과정에 드는 시간을 상당히 절약할 수 있었습니다.
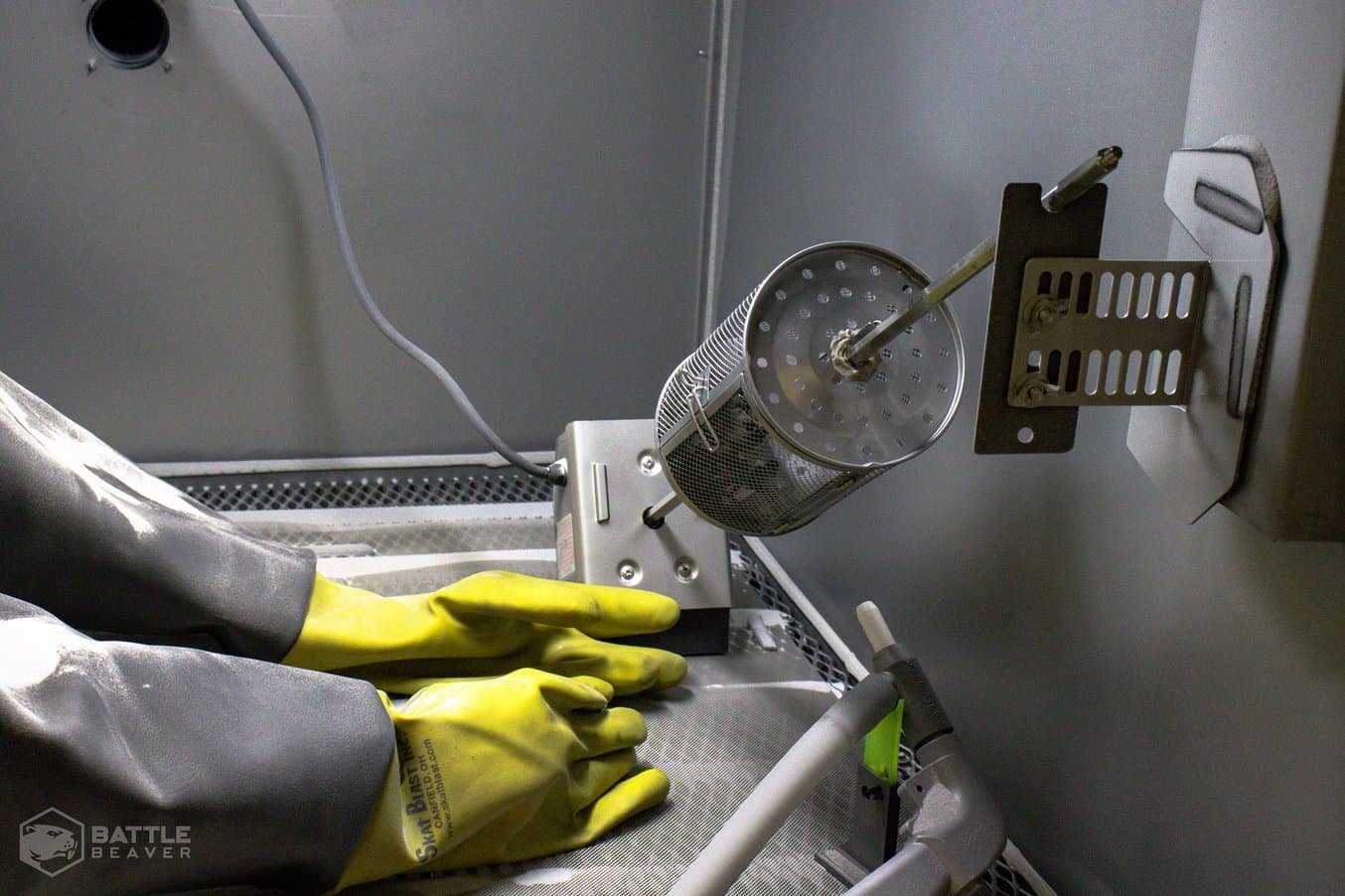
팀이 미디어 블라스팅 과정을 자동화하는 데 사용할 랙을 직접 제작한 것입니다.
크루넬은 Fuse 1을 가장 먼저 사용해 본 사람에 속합니다. 그 프린터를 워크플로에 완전히 통합한 것은 거의 12개월 후였고 "거의 1년을 프린팅해 본 지금에 와서야 도구 목록에 완전히 자리 잡은 새 도구가 되었다"고 전합니다.
배틀 필드 커스텀스에 관해 자세히 알아보시려면 Twitter에서 팔로우해 주세요.