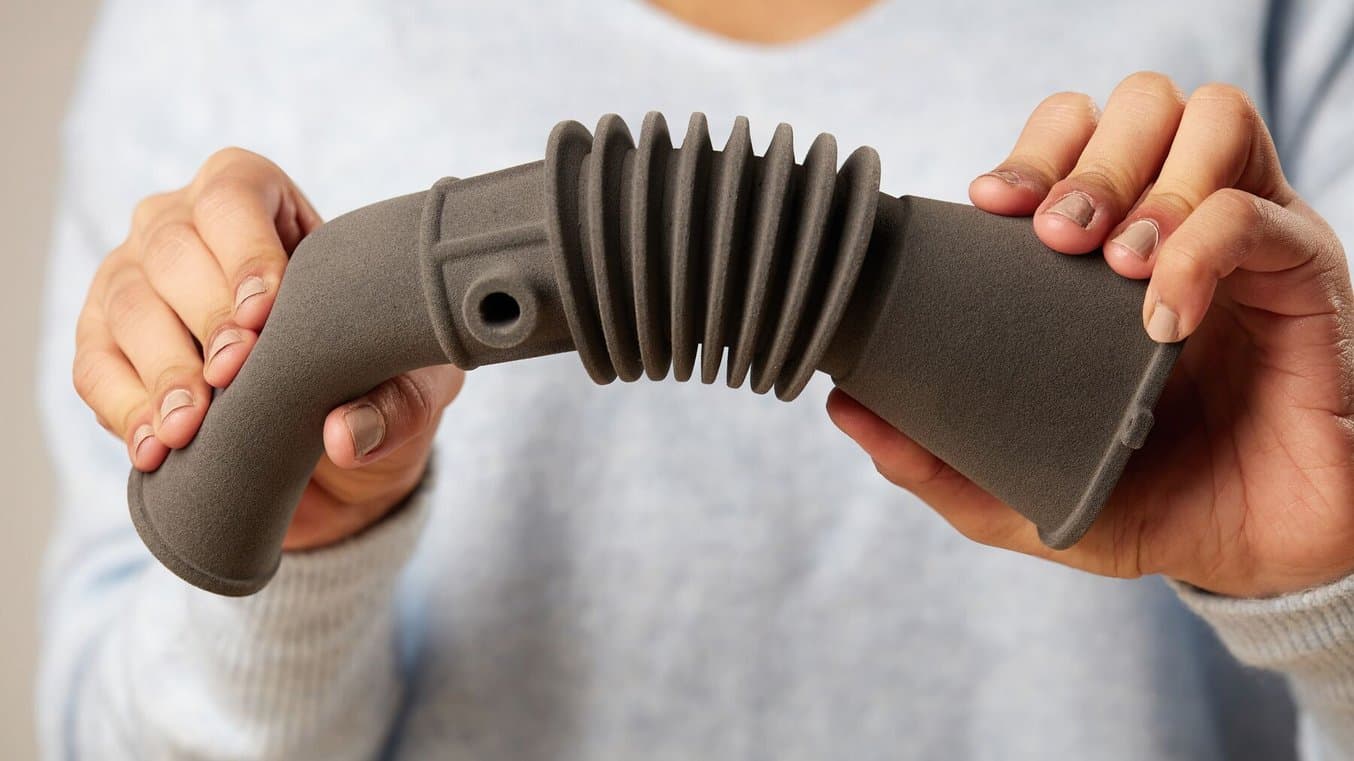
TPU란 무엇인가요?
TPU, 즉 열가소성 폴리우레탄은 자동차, 운송, 항공우주, 스포츠 용품, 의료기기 제조업계에서 흔히 사용되는 열가소성 엘라스토머(TPE)에 속합니다. 플라스틱의 우수한 연성과 고무의 탄성이 결합된 TPU는 반복적으로 굽히거나 압력을 가해야 하는 응용 분야에 사용하기에 좋습니다.
그 탄성 덕분에 헬멧, 보호용 포장재, 진동 방지 제품, 개스킷 또는 씰 같은 제품에 사용되는 충격 보강재로 사용되는 것을 자주 볼 수 있는 소재입니다. TPU는 내마모성도 우수하여 마찰이 심하거나 자동차 인테리어 또는 전기 케이블 및 절연체 제작에서 전적으로 사용되는 소재입니다. 유분이 도처에 널려 있는 업계의 응용 분야에서도 대부분 TPU를 사용하는데, 이는 기름 자국도 잘 남지 않기 때문입니다.
TPU 파트는 어떻게 제작되나요?
TPU 제품은 일상 생활 어디서나 존재합니다. 인기가 워낙 좋아 대량 생산에 자주 사용되고 가장 흔하게는 전통적인 사출 성형 공정에서 자주 눈에 띕니다. 우리가 고무라고 생각하는 제품 중 다수가 사실은 TPU입니다.
사출 성형은 물량이 큰 부품을 비용 효율적으로 생산할 수 있는 방법이지만 기하학적 유연성이나 맞춤화 가능성 면에서는 제한이 있습니다. 사출 성형으로 제작된 부품은 수십만 개에서 수백만 개까지 대량으로 생산할 수 있도록 표준화되어 있어 의료 기기 제조나 스포츠 용품 등을 취급하는 업계에서는 소량 생산이나 맞춤화에 더 적합한 대안이 절실합니다.
대량 생산은 또한 소규모 업장과 스타트업이 자사의 제품을 빠르게 출시하는 데 걸림돌로 작용하기도 합니다. 대형 산업 사출 성형기를 사용하려면 거의 외주 작업에 의지해야 하기 때문입니다.
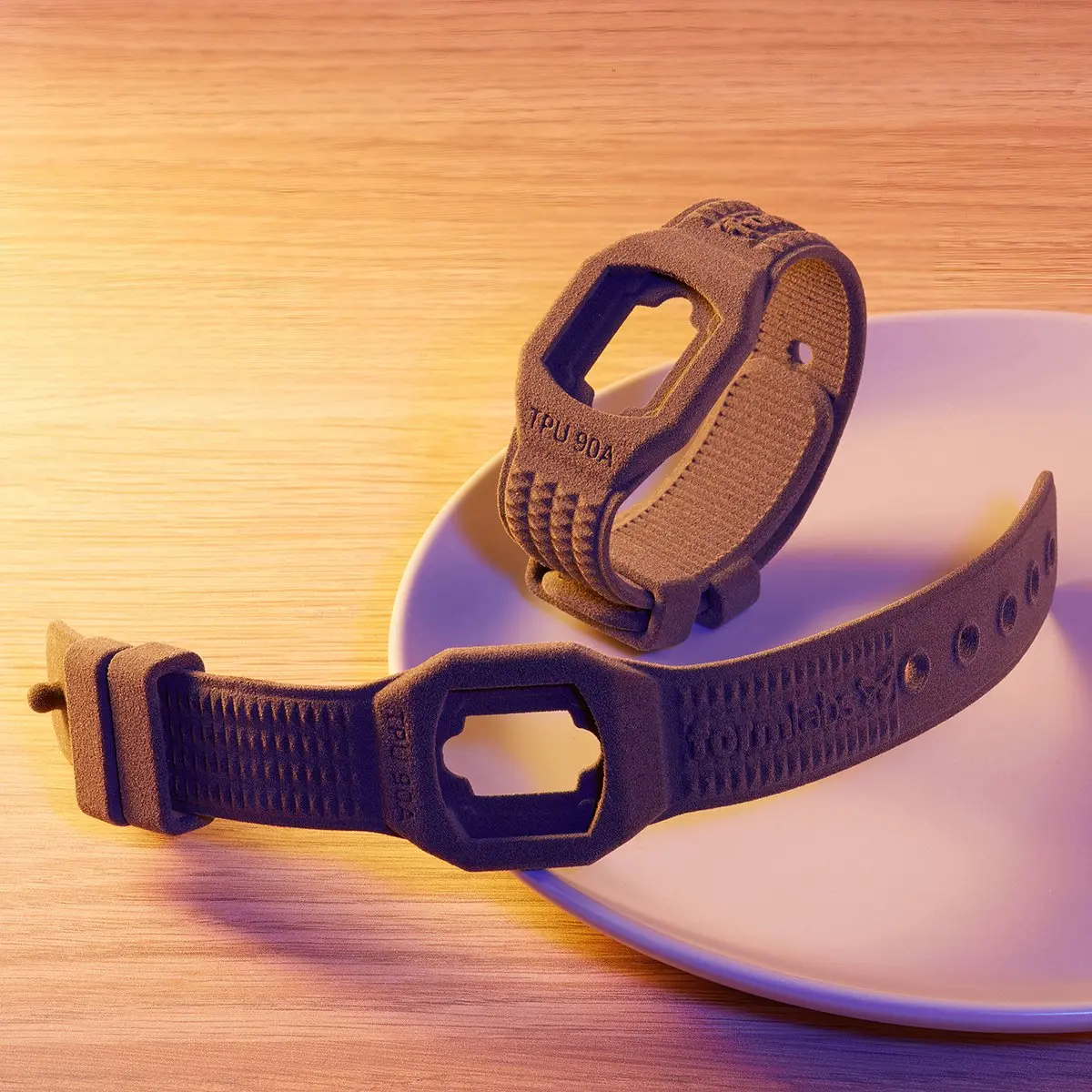
플렉서블하고 질기며 피부에도 안전한 SLS 파트용 TPU 90A Powder 소개
웨비나에서 TPU 90A Powder가 어떻게 도움이 될지 확인해보세요. 말랑말랑한 고무 파트를 Fuse 시리즈 3D 프린터로 자체 제작하는 방법을 알려드립니다.
3D 프린팅에 TPU를 사용하는 이유는 무엇인가요?
TPU와 TPE 소재를 3D 프린팅하게 되면 기존 워크플로에서 벗어나 극도로 복잡한 기하학적 형상과 개인화 또는 맞춤화 디자인을 실현하고, 반복 설계와 디자인이 더 신속해지며, 소량 생산을 더욱 비용 효율적으로 처리할 수 있는 가능성이 열립니다.
TPU 3D 프린팅에는 용융 적층 모델링 방식(FDM)과 선택적 레이저 소결 방식(SLS) 외에도 다양한 기술 방식이 있습니다. 지금까지 3D 프린팅 기술과 소재는 진보해왔고, 3D 프린팅 워크플로를 자사의 기존 공정에 도입하는 제조업체의 수는 기하급수적으로 늘어나고 있습니다t.
TPU 3D 프린팅을 도입하면 신속 프로토타이핑 응용 분야의 반복 설계 주기가 짧아질 뿐만 아니라 엔드 유즈 파트를 맞춤화하는 역량도 갖출 수 있습니다. 제품 개발 공정에서 단계 하나를 기존 외주 제작(대개는 대량 생산 단계)으로 처리하는 산업에서는 3D 프린팅으로 엔드투엔드 워크플로를 수직 통합하여 공정 전체를 개선할 수 있습니다.
TPU 3D 프린팅을 이용해도 제조사가 맞춤화 및 개인화 물품에 대한 수요를 충족하는 데 도움이 됩니다. 딜로이트(Deloitte) 연구에 따르면 일부 카테고리에서는 50%가 넘는 소비자가 개별 맞춤된 제품 또는 서비스를 구매하는 데 관심을 표현했으며 이들 중 대다수가 맞춤형 제품 또는 서비스에 비용을 더 부담할 의향이 있는 것으로 나타났습니다. 헬멧이나 교정기, 인솔(깔창) 같은 보호 장비같이 TPU와 고무가 흔히 사용되는 응용분야에서는 헬멧 패딩, 보조기, 스포츠 장비, 고글, 헤드셋, 테크 제품의 인체공학적 손잡이 컴포넌트의 대량 맞춤화에 3D 프린팅 TPU가 마치 맞춤옷처럼 잘 어울립니다.
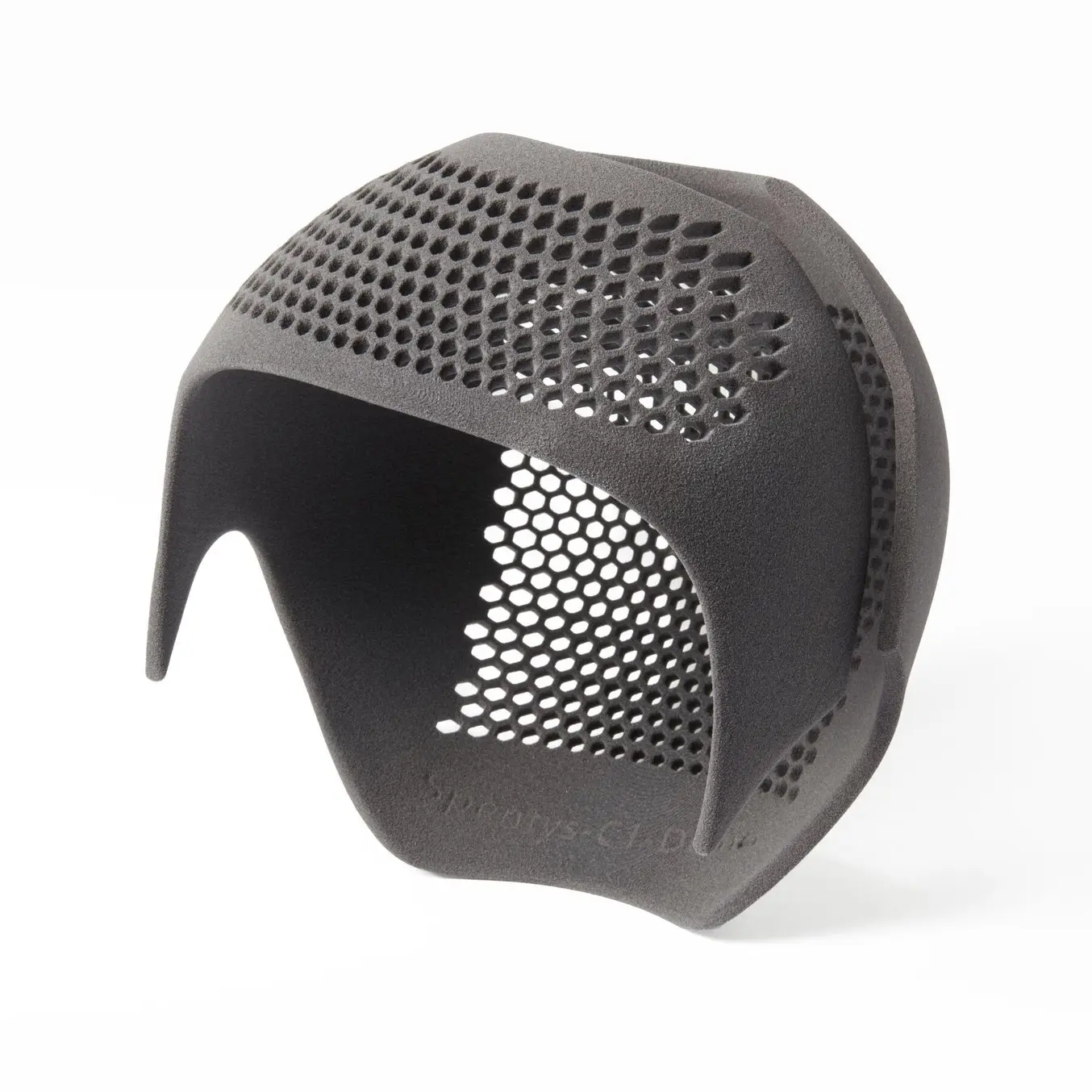
Formlabs의 TPU 90A Powder를 이용하면 이 개인용 머리 보호대 같은 응용 분야에서 신체계측 자료에 따라 맞춤화 작업을 할 수 있습니다.
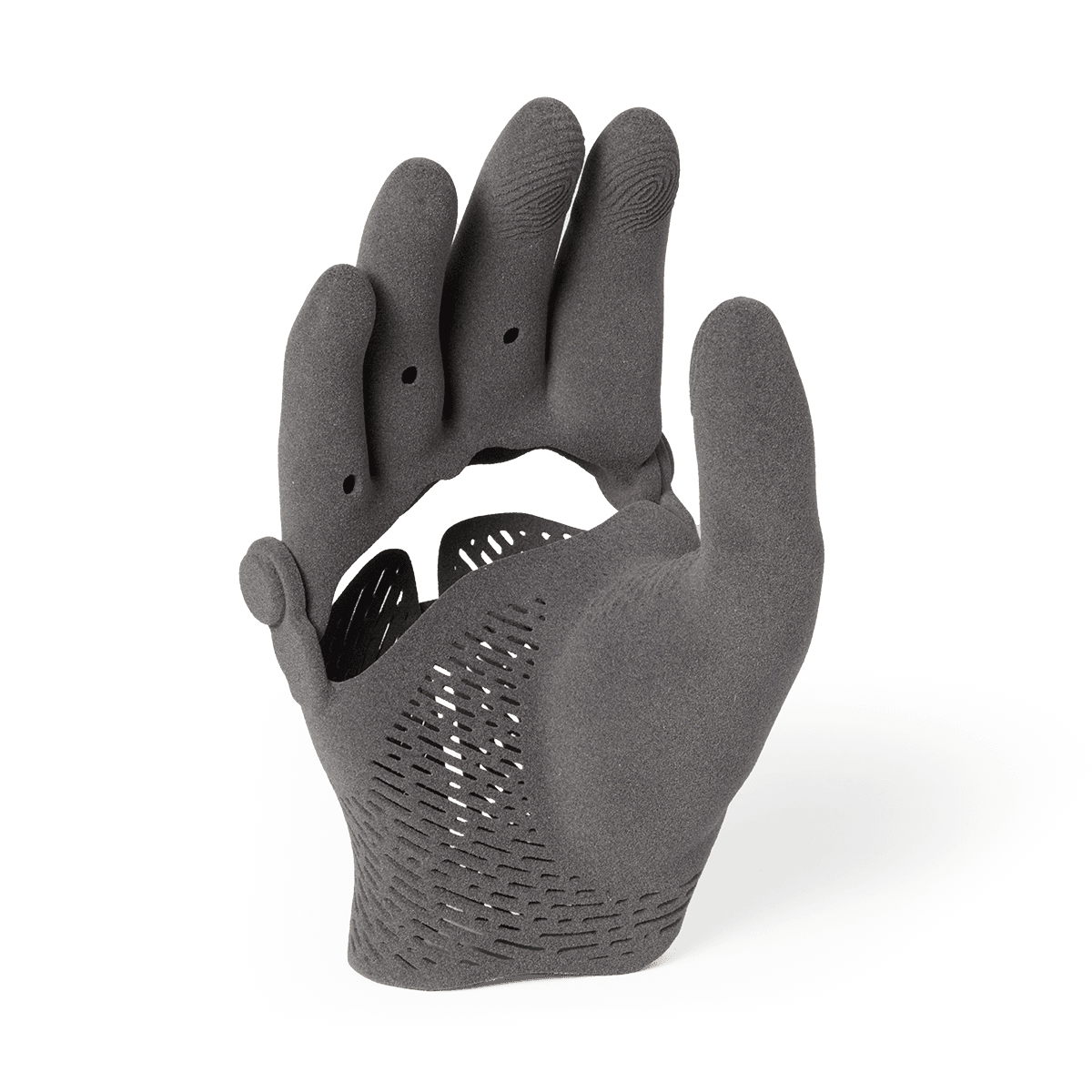
TPU 90A Powder로 프린팅한 이 의수 보호대는 유연하고 튼튼하며 내구성이 좋습니다.
TPU 3D 프린팅 방법
TPU는 FDM이나 SLS 방식 3D 프린터로 프린팅할 수 있습니다. 각 기술에는 고유한 장점이 있으므로 기술 방식을 선택하기 전에 워크플로와 비즈니스 니즈에 따라 가장 적합한 방식을 선택하는 것이 중요합니다.
FDM TPU 3D 프린팅 | SLS TPU 3D 프린팅 | |
---|---|---|
소재의 기능적 강도 | ★★☆☆☆ | ★★★★★ |
해상도 | ★★☆☆☆ | ★★★★☆ |
정확도 | ★★★★☆ | ★★★★★ |
표면 마감 | ★★☆☆☆ | ★★★★☆ |
처리량 | ★★☆☆☆ | ★★★★★ |
복잡한 디자인 | ★★☆☆☆ | ★★★★★ |
사용 편리성 | ★★★★★ | ★★★★☆ |
장점 | 소비자용 장비와 소재의 실용적 가격 단순하고 작은 파트를 빠르고 쉽게 수급 | 파트의 기능성, 강도, 등방성 실생산 수준의 생산 물량 자가 서포트 설계 우수한 설계 자유도 |
단점 | 파트가 비등방성이며 수밀성과 기능적 강도 없음 설계 자유도 빈약 | 표면 마감이 약간 거칠거칠함 |
응용 분야 | 저비용 신속 프로토타입 제작 기본 개념 증명 모델 | 기능성 프로토타입 자동차 개스킷, 씰, 매니폴드, 소비재, 신발, 의족, 의수, 보조기 같은 최종 사용 파트의 소량 생산 |
FDM 방식의 TPU 3D 프린팅
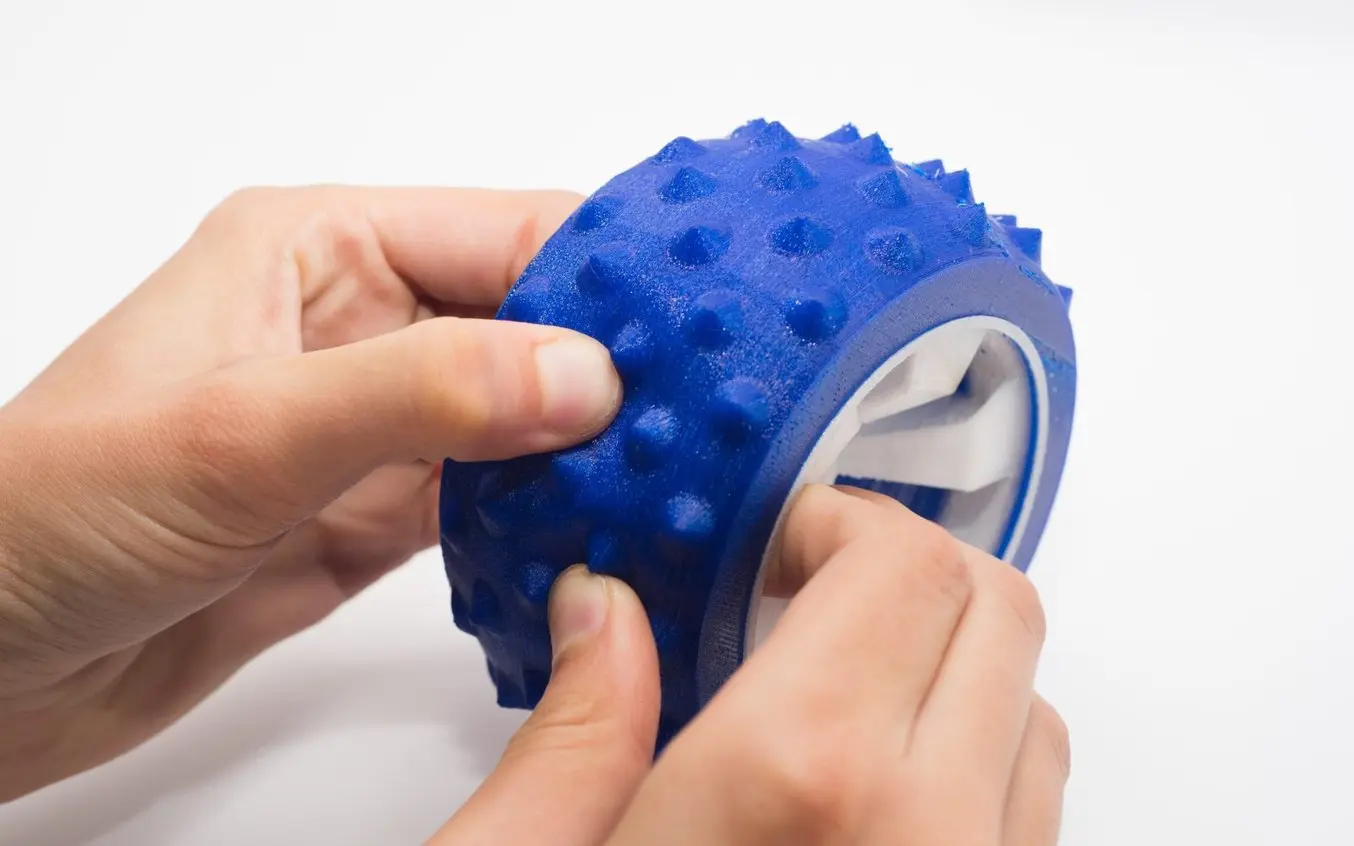
FDM 프린터를 이용한 TPU 3D 프린팅은 훌륭한 진입 옵션이 될 수 있지만, 3D 프린팅에 사용 가능한 소재를 구하기가 어렵고 설계에도 제약이 있습니다. (이미지 출처: Hubs)
TPU를 3D 프린팅해 보려는 기업의 입장에서는, 저가의 FDM 프린터가 진입 단계 워크플로에 좋은 옵션이 될 수 있습니다. FDM TPU 필라멘트는 가격이 저렴하며 특히 기존의 사출 성형 방법을 이용한 대량 성형을 최종 목표로 할 때 디자인 컨셉과 스타일 목업을 제작하여 평가하기에 좋은 방법이 될 수 있습니다.
그렇지만, FDM 프린터로 3D 프린팅하기에는 TPU가 까다로운 소재일 수 있습니다. 부드럽고 잘 늘어나는 필라멘트가 압출기에서 쉽게 뭉쳐져 기술 문제가 발생하고 프린트 성공률이 좋지 못하기 때문입니다. 또한 FDM 프린터에서 TPU를 3D 프린팅하면 설계 자유도에 제약이 있고 치수 정확도가 낮으며 레이어 라인이 확연히 드러나 보이기도 합니다.
FDM 방식으로 프린팅한 TPU 파트에 응력을 가하면 축과 평면의 위치에 따라 받는 스트레스가 달라진다는 의미입니다. 즉, FDM 방식으로 프린팅한 TPU 파트에 한 방향으로 힘을 가하면 같은 크기의 힘을 다른 방향에서 가했을 때와 그 효과가 서로 달라진다는 의미입니다. 자주 잡아당기고 늘리고 압축하고 비틀어야 하는 TPU 파트라면 이런 비등방성 때문에 기능을 갖춰야 할 파트 중 어떤 것으로도 사용하기가 부담스러울 수 있고 심지어 프로토타입 단계에서조차 실제품과 다른 양상을 보일 수 있습니다.
FDM 프린터용 TPU 필라멘트
FDM 프린터와 소재 물성이 다양한 소재를 공급하는 제조사가 많습니다. FDM TPU 필라멘트는 일반적으로 약간 단단한 탄성 소재이며 쇼어 경도가 약 95A지만 프린트 매개변수나 설계를 약간 변경하여 조정할 수 있습니다.
SLS 방식의 TPU 3D 프린팅
SLS 3D 프린팅기술은 생산 물량이 크고 기능적인 분야에 잘 어울리고, 보조기, 헬멧 패딩, 웨어러블 같은 맞춤형 최종 사용 물품의 테스트나 소량 생산 같은 분야에 안성맞춤입니다. SLS 3D 프린터를 보유하면 TPU의 뛰어난 강도와 유연성을 활용해 제품을 단시간에 출시하거나 의료 분야에서는 환자 케어에 사용할 수 있습니다. 인열 강도가 우수한 TPU를 사용하면 튼튼하고 내구성 좋은 엘라스토머 파트가 만들어지고 Fuse 시리즈 같은 벤치톱 SLS 시스템의 우수한 접근성을 이용하면 파트당 비용이 저렴해집니다. 게다가 리프레시 비율이 낮아 시스템의 실용성과 확장성은 더욱 커집니다. 리프레시 비율이 낮으면 사용했던 분말을 대부분 재사용할 수 있어 분말 사용의 효율성이 늘어나고 새 소재를 구매하는 데 드는 비용이 줄어들기 때문입니다
SLS 3D 프린팅으로 제작한 TPU 파트는 복잡한 기하학적 형상을 구현해야 하거나 그러한 형상이 성능 향상에 도움이 되는 응용 분야에 꼭 맞습니다. SLS 기술의 자가 서포팅 특성은 별도의 서포트 구조가 필요하지 않으며 내부 채널, 격자, 매니폴드 유형의 아코디온 구조가 포함된 정교한 형상을 구현할 수 있다는 의미입니다. 보호용 하드웨어나 풋웨어용 인솔과 보조기, 고무 같은 격자 구조 같은 응용 분야에서 압력 강도를 높여 제품의 효율성을 향상할 수 있습니다.
SLS 프린터용 TPU 소재
TPU 분말 소재를 사용할 수 있는 선택적 레이저 소결 방식(SLS) 시스템에는 여러 가지가 있습니다. 이들 시스템 중 다수가 환기 시스템, 넓은 설치 공간, 복수의 회로와 전기적 요구 사항 등 복잡한 기반 시설을 필요로 하는 대형 산업용 장비입니다. Formlabs의 Fuse 시리즈같이 접근하기가 쉬운 SLS 시스템을 사용하면, 분말 베드 시스템에서 TPU를 더 쉽고 경제적으로 3D 프린팅할 수 있습니다.
Formlabs의 TPU 90A Powder는 피부에 안전하여 안전 규제에 따라 사용할 수 없는 3D 프린팅 파트가 많은 웨어러블과 의료 장비 분야에 진출할 기회를 얻을 수 있습니다. TPU 90A Powder를 이용하면 3D 프린팅의 설계 자유도, 고무의 우수한 인열강도와 연신율, 기존 성형 방법에서 얻을 수 있는 열가소성 플라스틱의 피부 안전성까지, 모두 단일 워크플로에서 활용할 수 있습니다.
Formlabs의 TPU 90A Powder와 Fuse 시리즈 SLS 프린터를 이용한 3D 프린팅 공정은 간단하므로 기존 SLS 워크플로에 쉽게 통합할 수 있고 처음 시도해보는 SLS 소재하고 해도 무리가 없습니다. 소재는 대기 환경에서 프린팅할 수 있으며 일부 SLS 소재가 그런 것처럼 비활성 기체가 필요하지 않습니다.
또한 Fuse 시리즈 프린터에서 TPU로 제작된 파트는 Surface Armor(단단하게 굳은 분말 파트 주변에 반소결 쉘 생성)를 사용하지 않으므로 Fuse Sift 후처리 장비로 아주 간단하게 여분의 분말을 제거할 수 있습니다. TPU 90A Powder에는 Surface Armor기술을 이용하지 않지만 미디어 블라스팅으로 파트에서 여분의 분말을 깔끔하게 제거하시기를 권해드립니다. 그렇게 하면 보다 청결하고 작업하기 쉬운 환경을 조성할 수 있습니다. 전용 Fuse Sift와 빌드 챔버를 사용하시는 편이 좋지만 기존의 Fuse 시리즈 프린터에서도 당연히 TPU 90A Powder 소재를 프린팅하실 수 있습니다.
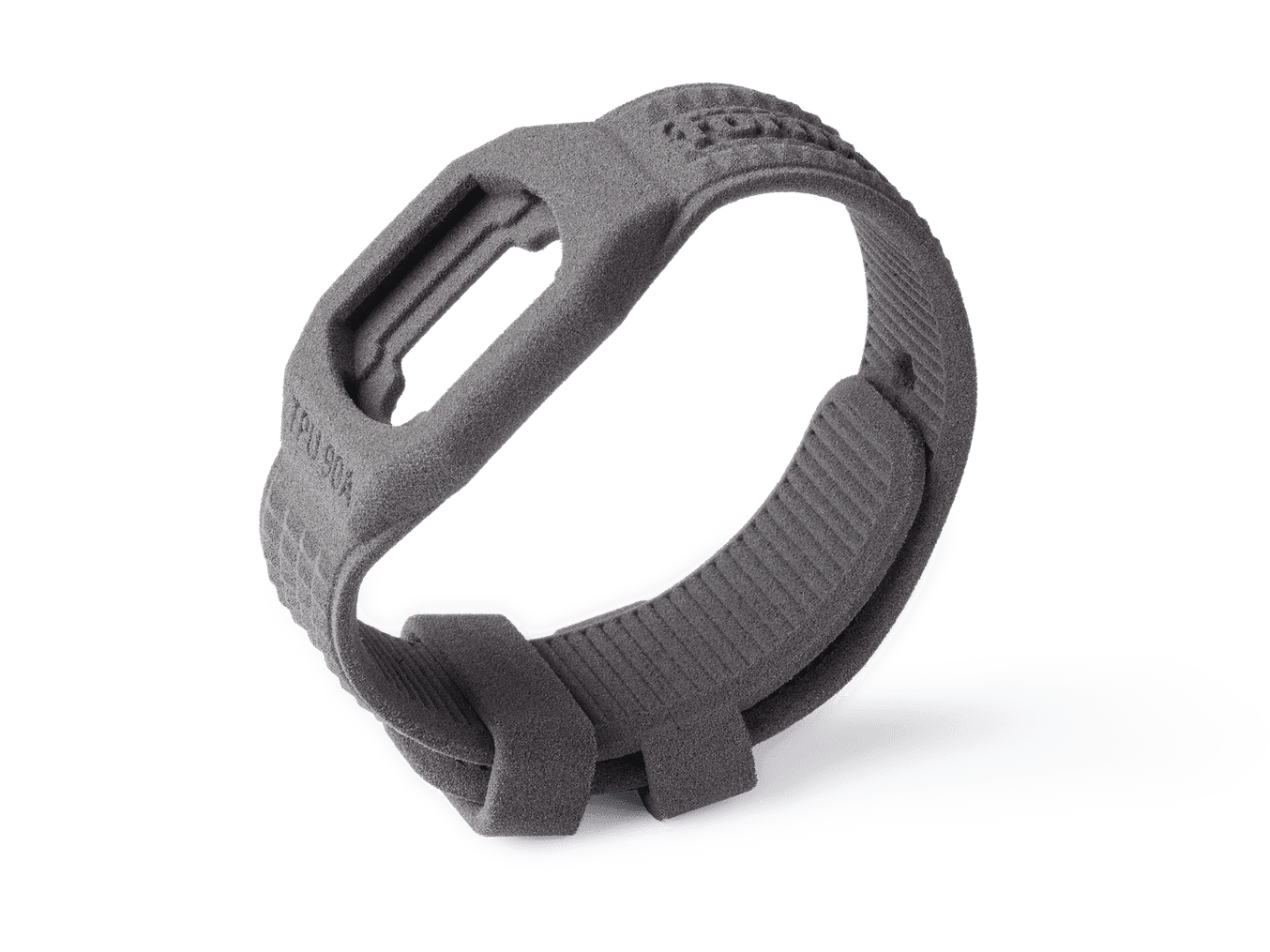
TPU 90A: Formlabs의 유연한 SLS 분말
당사 최조의 유연성 SLS 소재, TPU 90A Powder로 프린팅한 무료 샘플 워치 스트랩을 요청하세요.
TPU 3D 프린팅 응용 분야
기존의 TPU 파트 제작 방식에는 입증된 워크플로가 있으며 이들 워크플로는 고무 제품 대량 생산에 꼭 맞습니다. 그렇지만, 3D 프린팅 TPU는 다양한 분야, 이를 테면, 속도나 사용 편의성이 필요한 분야, 신속한 프로토타입 제작, 주문형 제조 보조 도구, 맞춤화가 필요한 분야에서 훌륭한 대안이 될 수 있습니다. 빠르게 프로토타입을 제작해야 하는 설계 초기 단계에서 최종 사용 파트를 확인해야 하는 설계 마지막 단계까지, 심지어 대량 맞춤형 소비재 제작에도 3D 프린팅 TPU를 사용하면 워크플로의 속도와 효율성은 상승하고 기계적 물성이나 설계 충실도는 변함 없는 결과물을 얻을 수 있습니다.
신속 프로토타이핑
TPU를 3D 프린팅하면 프로토타입 제작 역량을 자사 내에서 제어할 수 있으며 리드 타임은 단축하고 이전에 대행 업체나 기계 가공 업체에 지불하던 비용은 절감할 수 있습니다.
예를 들어, 스포츠 헬멧을 프로토타입으로 제작하려면 단단한 외피와 내부의 부드러운 쿠션까지 제작할 수 있는 능력이 필요합니다. 혁신적인 기업들은 이러한 쿠션에 새로운 격자 구조와 충격 방지 기술을 설계하기 위해 노력하고 있으며 TPU는 그런 용도에 완벽한 소재입니다.
그러나 새로운 설계와 형상을 실험하려면 기존의 툴링 방법으로는 비용이 엄청나게 들어서 접근하기가 어렵고 설계 외주 업체에 아웃소싱하는 데는 몇 주가 걸릴 수 있습니다. 단단한 외피와 부드러운 내부 쿠션을 제작하는 데 하나의 워크플로와 한 가지 유형의 기술을 사용할 수 있다면 이러한 혁신 기업들이 훨씬 더 빠른 속도로 설계 변경을 반복할 수 있을 것입니다. 이 헬멧은 광범위한 물리적 테스트를 거쳐야 하므로 단일 회차 테스트에 10개의 쿠션 패드가 필요합니다. 그 정도의 물량은 쿠션 표면을 세심하게 손으로 제작하기에는 너무 많지만 기존 TPU 성형을 비용 효율적으로 이용하기에는 너무 적습니다. 해답은 인하우스 3D 프린팅에 있습니다.
Fuse 시리즈 3D 프린터를 이용하면 TPU 90A Powder로 다양한 고무 격자 구조를 손쉽게 프린팅할 수 있으며 설계를 미세하게 변형하여 각기 다른 디자인을 테스트할 수도 있습니다. 벽 두께 같은 파트 자체 디자인을 변경하여 서로 다른 응용 분야에 사용할 수 있도록 다양한 강도의 파트를 생산하거나 테스트 후에 설계 변경을 반복할 수도 있습니다.
Fuse 시리즈의 워크플로는 기계적 성질이 광범위한 다양한 소재를 사용할 수 있으며 이들 소재를 전부 사내에 보관하고 하나의 기술로 다양한 컴포넌트의 설계를 관리할 수 있습니다. TPU 90A Powder 덕분에 신뢰할 수 있는 Fuse 시리즈 플랫폼에서 3D 프린팅으로 직접 프로토타입을 제작하고 생산까지 동일한 플랫폼에서 하는, 완전히 새로운 유형의 제품이 탄생할 수 있게 되었습니다.
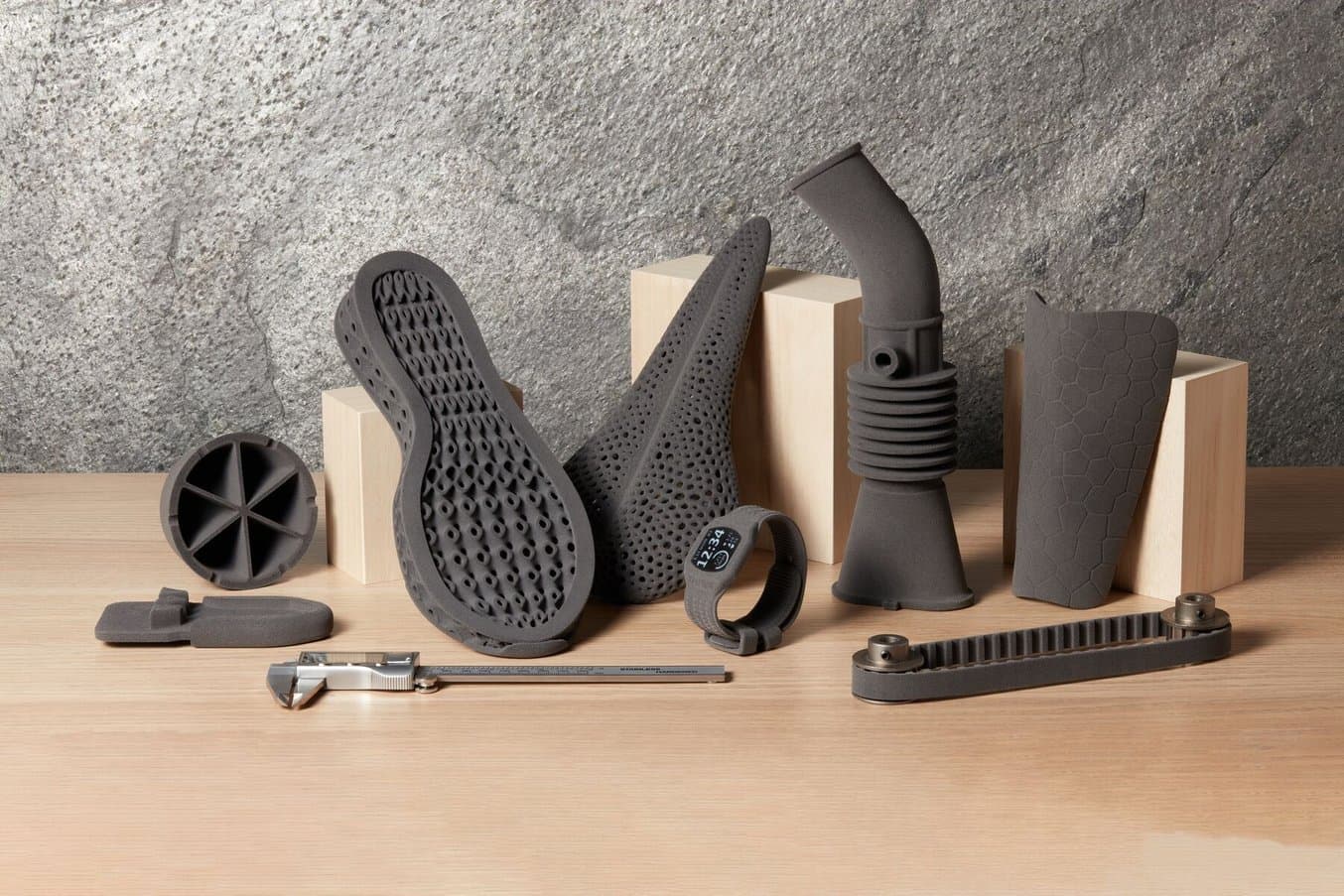
TPU 90A Powder는 피부에 안전한 웨어러블, 고성능 스포츠 장비 또는 신발 안창과 같이 유연성이 필요한 파트의 기능적 프로토타입을 제작하기에 제격인 소재입니다.
제조 보조 도구
귀사가 제조 분야의 기업에 속하지 않는다면, 제조 보조 도구의 유형 사이의 차이점을 알아채기가 어려울 수 있습니다. 그러나 지그, 브래킷, 인클로저를 이야기하든, 기타 기계 장비를 한데 고정할 수 있는 수많은 공구 중 하나를 이야기 하든, 그 공구가 정말 절실하게 필요하다는 점에는 기본적으로 차이가 없습니다. TPU는 많은 제조업체가 직면한 문제, 즉 백만 달러나 되는 고가의 제조 장비가 너무 많이 마모되는 것을 방지할 해결책이 될 수 있습니다.
소프트 터치 제조 보조 도구는 특정 충격을 완충하거나 완벽한 모양의 그리퍼 역할을 하여 중장비의 수명을 연장하는 데 도움이 될 수 있습니다. 씰이나 개스킷이 수년간의 반복 사용 후 찢어지면 작업자가 즉시 교체품을 프린팅할 수 있으며 새 파트가 도착할 때까지 며칠 또는 몇 주를 기다리지 않고도 몇 시간 만에 제조 라인을 재가동할 수 있습니다.
가용 소재가 늘어난다는 것이 제조 업체에는 보험과도 같아서 고장난 파트나 결함이 있는 장비로부터 제조 업체를 보호할 수 있습니다. 인하우스에서 더 많은 기계적 물성을 활용할수록 공급망 지연과 OEM의 치솟는 수리 비용으로부터 자사를 보호할 수 있습니다. 고무로 된 3D 프린팅 파트를 사용하면, 이제 완전히 새로운 장비 구성품 하위 집합체를 필요에 따라 수리하거나 교체할 수 있습니다. 공장 작업 라인이나 공정의 가동중지를 피할 수 있다면 하루에 수천 달러를 절약할 수 있습니다.
TPU는 자동차 및 항공 우주 업계의 테스트용 진동 댐퍼뿐만 아니라 형태가 고유한 파트의 열성형과 같은 산업 공정에 필요한 지그를 제작하는 데 사용할 수 있습니다. 자동차 공장에서는 구부리고 회전해야 하는 갠트리에서 대형 로봇 시스템이 작동합니다. 맞춤형 쿠션과 부드러운 인클로저를 사용하면 이러한 기계 사이의 마찰을 피하고 수명을 연장하는 데 도움이 될 수 있습니다.
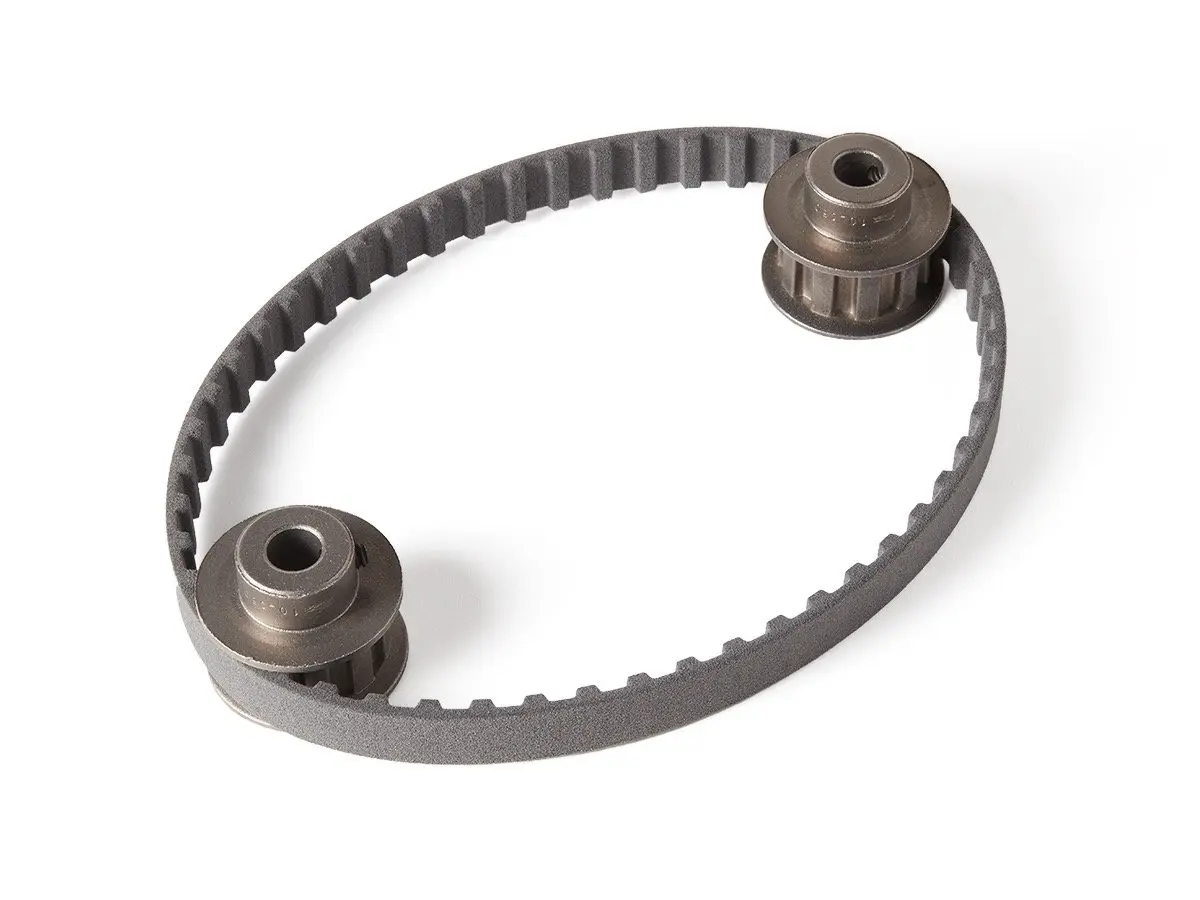
TPU 소재를 보유하고 있다는 것은 유연한 교체용 파트와 제조 보조 도구를 당일에 설계하고 프린팅할 수 있으므로 생산을 중단할 필요가 없다는 것을 의미합니다.
소량 및 맞춤형 기성 제품
스포츠, 패션 및 웨어러블 기술 산업에서 시장 점유율을 더 높이고자 하는 브랜드는 필수적으로 개인화 옵션을 제공해야 합니다. 진입 장벽이 낮은 3D 프린팅의 세계가 열리기 전까지는 툴링과 관련된 비용이 고가여서 소량 또는 일회성 생산은 거의 불가능했습니다.
더욱이 TPU가 출시되기 전까지는 3D 프린팅 소재 대부분이 스포츠 용품이나 웨어러블 시장에 사용하기에는 너무 단단했습니다. 사람의 정확한 족적과 체중 분포에 맞게 맞춤화할 수 있는 신발 밑창부터 충격 방지용으로 설계된 축구 헬멧, 손목에 맞게 성형된 시계 밴드에 이르기까지 가능성은 무한합니다.
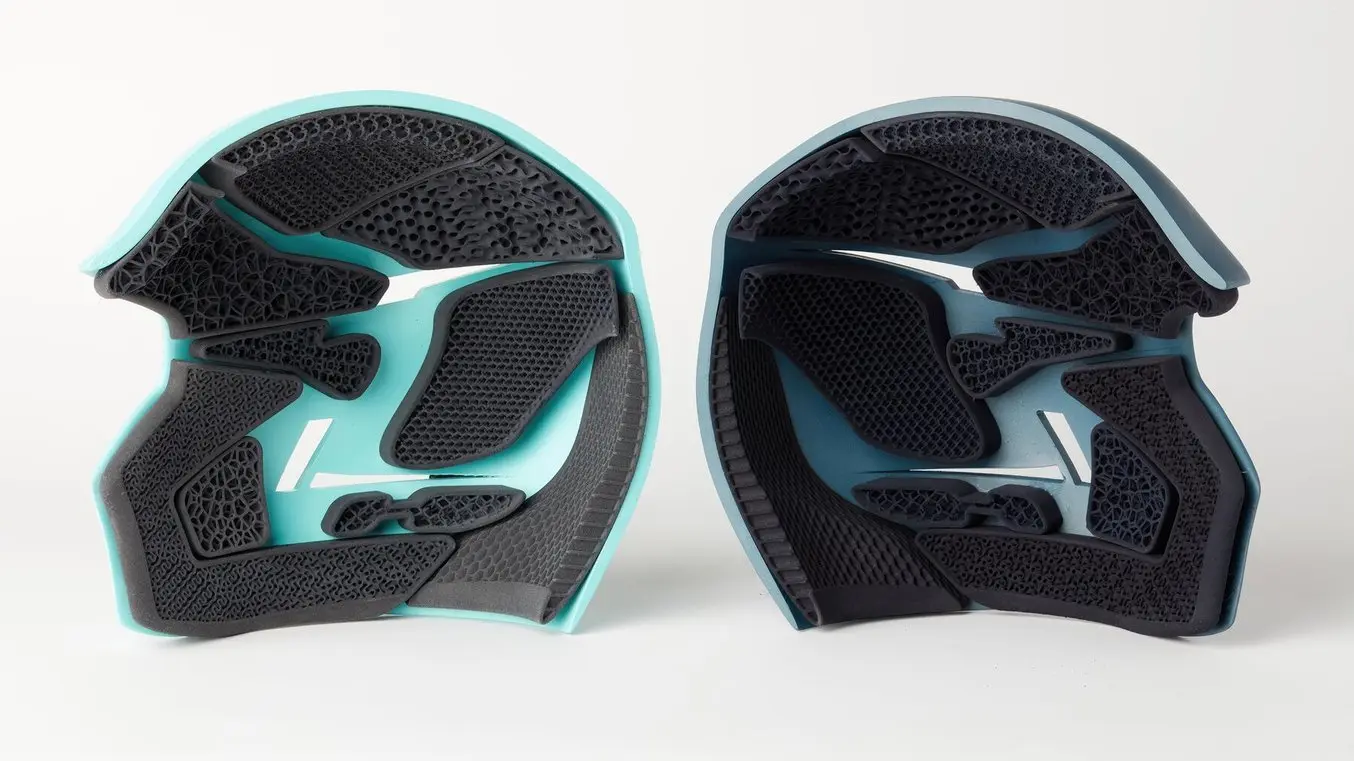
Fuse 시리즈 SLS 3D 프린터에서 TPU를 프린팅하여 제작한 맞춤형 패딩을 사용한 미식 축구 헬맷
의료 장치
내구성과 인성이 탁월한 3D 프린팅 TPU는 보철물, 보조기, 환자 맞춤형 장치, 의료 기기 제작에 가장 적절한 소재입니다. 의료 전문가가 유연하고 튼튼한 최종 사용 파트를 3D 프린팅할 역량을 갖추게 되면 고무 소재의 우수한 인열 강도 및 파단 신율과 SLS 3D 프린팅의 디자인 자유도 및 내구성을 결합하여 새로운 분야를 개척할 수 있습니다.
TPU는 유연한 엘라스토머로 다음과 같은 의료용 파트를 3D 프린팅하기에 좋습니다.
-
의료 기기 프로토타입 및 최종 사용 의료 기기 및 부품
-
교정 패드 및 보철 라이너
-
웨어러블, 씰, 범퍼 및 튜브
-
부목, 두상 교정모
-
선수용 및 교정용 인솔
의료 분야의 3D 프린팅은 급성장하고 있는 분야이지만 엄격한 재료 요구 사항으로 인해 안전 인증은 물론 강도와 기계적 물성도 모두 갖춰야 하는 제약이 있습니다. 3D 프린팅 TPU는 도구 상자에 담긴 또 하나의 도구로서 의료 분야에서 다양한 응용 분야에 진출할 수 있는 기회를 열어 줍니다.
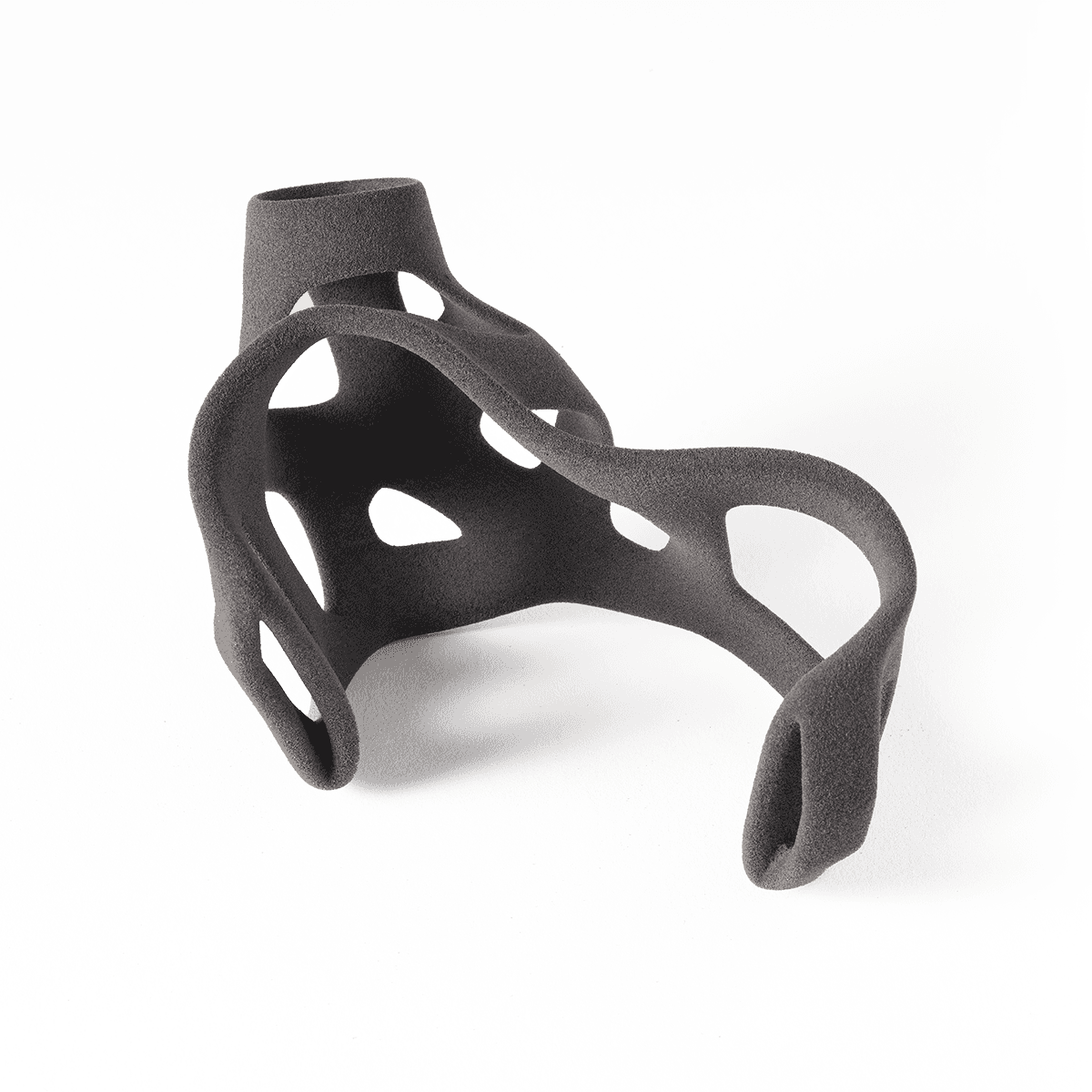
맞춤형으로 제작된 엄지 손가락 지지용 보호대로 기존 보호대보다 유연성과 제어 범위가 향상되어 지지력이 좋고 부상이 확대되지 않도록 방지할 수 있습니다.
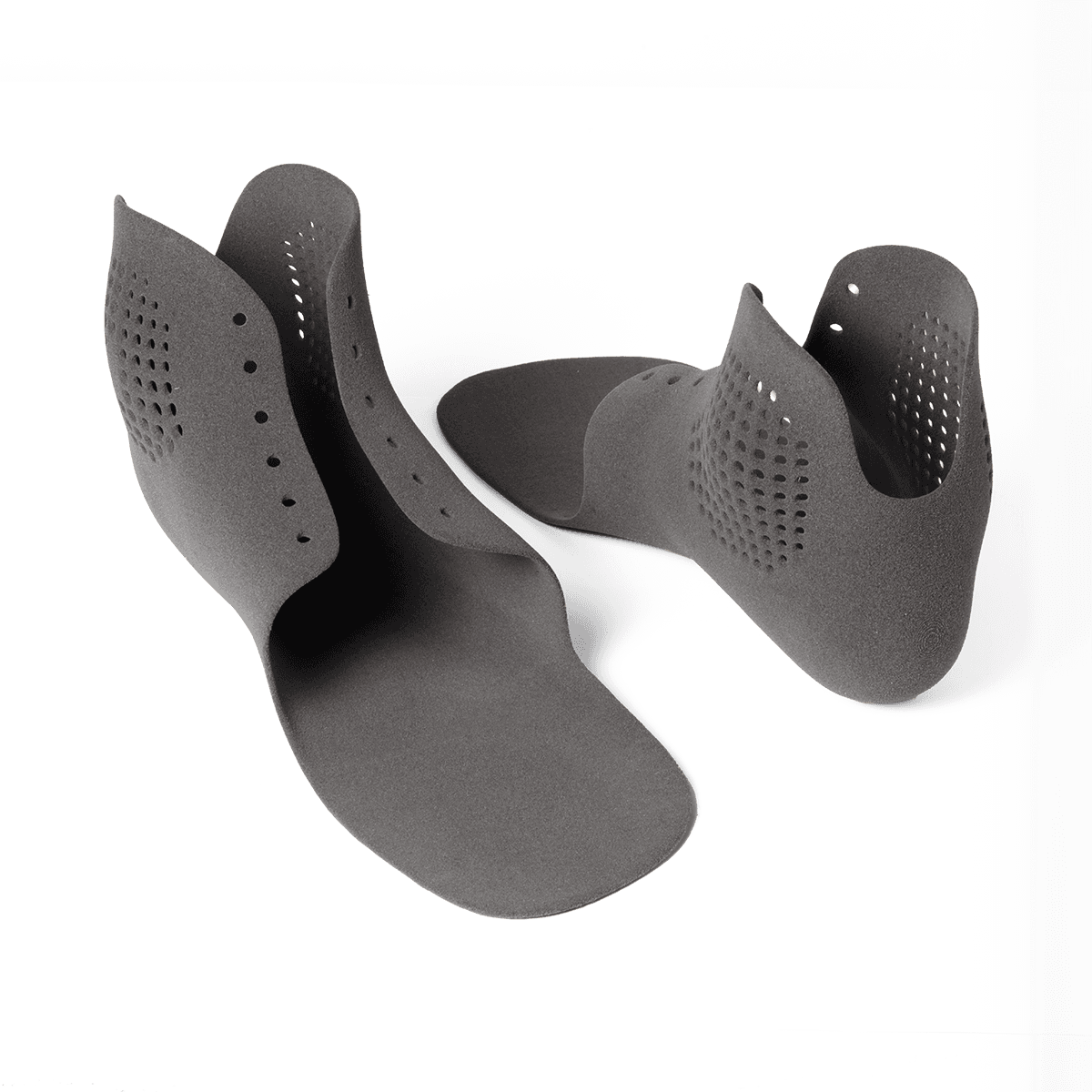
TPU는 발 교정용 깔창이나 선수용 인솔과 교정용 인솔 등 다양한 신체 교정용 장치를 제작하는 데 꼭 맞는 소재입니다.
사례 연구
하이델베르그의 글로벌 프린팅 프레스의 보호용 장비 컴포넌트
하이델베르거 드럭마치넨(Heidelberger Druckmaschinen) AG는 오프셋 인쇄기 제조의 선두 주자로, 170여 개국에서 약 10,000명의 직원을 두고 있습니다. 하이델베르거는 가장 크고 빠른 최첨단 프린팅 프레스부터 재단 및 접기 장비에 이르기까지 인쇄 가치 사슬 전체를 아우르는 광범위한 도구와 자동화 솔루션을 생산합니다.
이들은 픽 앤 플레이스 로봇용 경량 파트, 접지기용 신규 부속품, 이전에는 강철로 제작하던 장비 부속품에 들어가는 교체용 파트까지 기계용 컴포넌트 제작에 Fuse 1+ 30W SLS 3D 프린터를 사용합니다. TPU 90A Powder를 이용하면 충격에 견디며 기존의 강성이 우수한 장비에 맞출 수 있을 만큼 잘 구부러지는, 유연성이 좋은 파트를 생산할 수 있습니다.
교체용 파트나 제조 보조 도구는 기존의 로봇 시스템에 끼워 맞춰야 하므로 이상하고 복잡한 형태를 띠는 경우가 종종 있습니다. 이런 파트는 적용 시 받아야 할 응력과 힘을 구체적으로 고려하여 개발하므로 반복적인 마모 시험을 거치게 됩니다. 3D 프린팅 부품은 종종 금속 베어링이나 테프론 코팅 부품과 같이 마찰 방지 역할을 수행하는 다른 부품과 결합해서 사용하기도 합니다. 어떤 부품은 비교적 복잡도가 낮지만 고도의 정확도와 섬세한 표현은 여전히 필요합니다.
유연성 있는 TPU 파트는 감염 방지, 날카로운 모서리 방폐, 센서 보호, 마모 방지의 목적으로 사용됩니다. TPU 90A Powder를 SLS 방식으로 3D 프린팅하는 워크플로는 이런 유형의 파트를 제작하는 데 완벽한 공정이 될 수 있으며, 이런 파트는 형태가 무궁무진하게 다양한 기계 장비를 거칠게 사용함으로써 생기는 손상으로부터 보호할 수 있습니다.
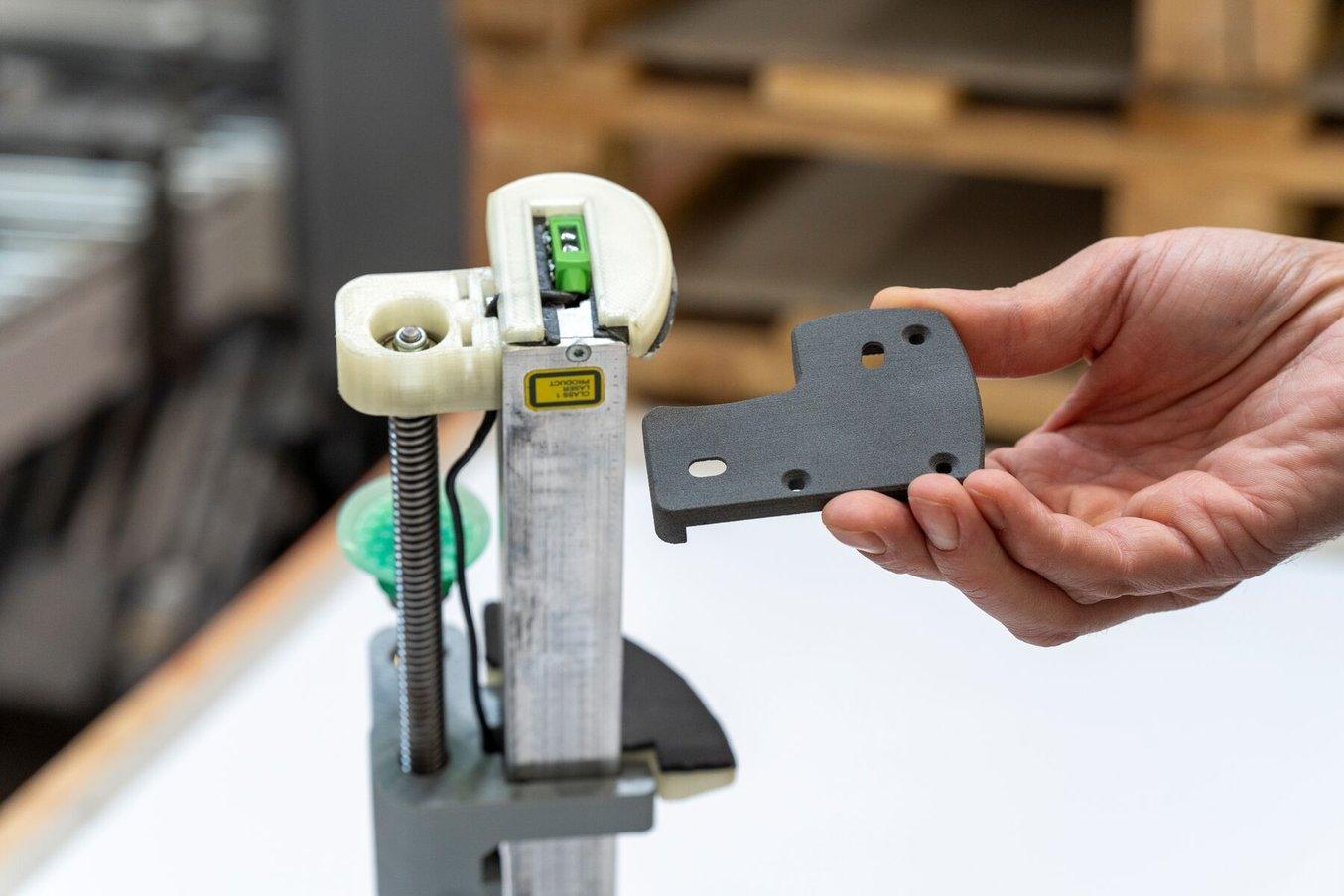
TPU 90A Powder로 프린팅한 유연한 파트, 센서와 기타 종단팔 공구를 보호합니다.
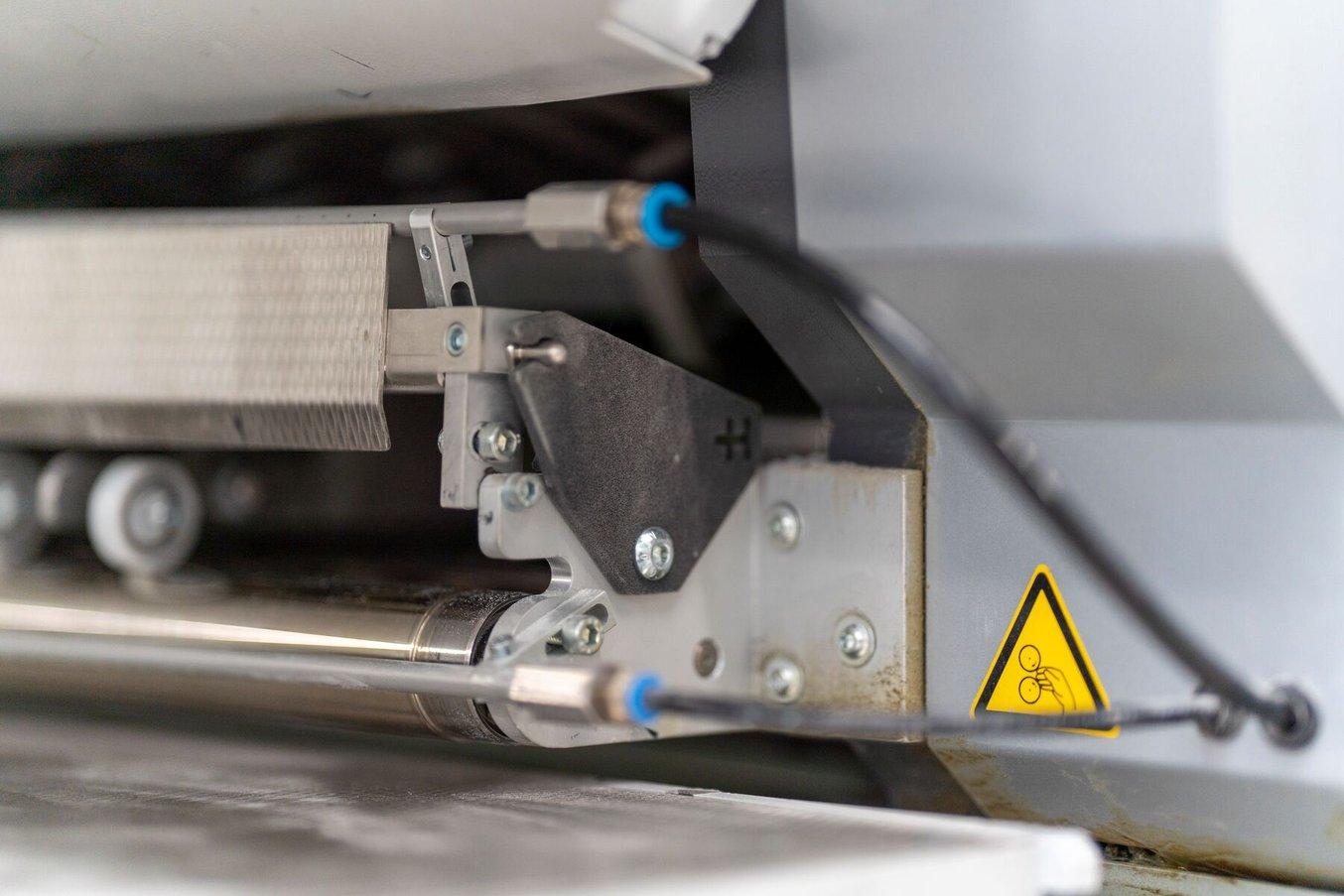
탄성이 있는 파트는 스냅핏 컴포너트를 제작하기에 안성맞춤입니다. 날카로운 모서리를 차폐하면 작업자도 보호할 수 있습니다.
구제척으로 TPU 90A Powder로 프린팅한 케이블 가이드 컴포넌트는 전기 케이블이 고도의 마찰로 마모되는 것을 방지하여 케이블의 수명을 연장하고 가동 중단 시간을 최소한으로 단축할 수 있습니다. 이러한 케이블 중 하나라도 끊어지거나 닳아서 작동이 멈추면 교체품을 주문하여 설치할 때까지 전체 기계를 사용할 수 없습니다. 이 케이블 가이드와 같은 기계 보호용 컴포넌트는 공장이 계속 운영되는 데 도움이 될 수 있습니다.
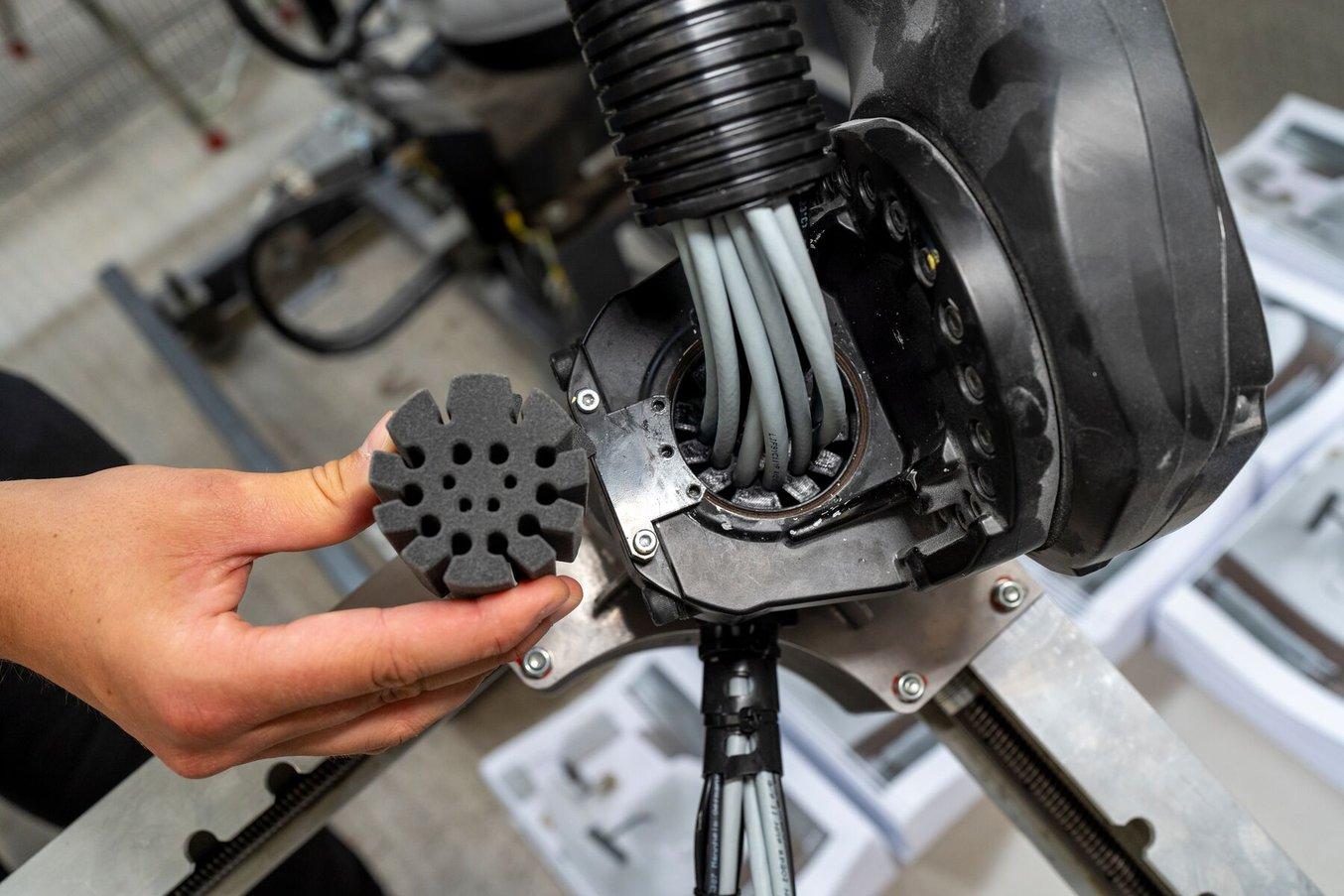
Fuse 시리즈 SLS 3D 프린터로 생산된 탄성 케이블 가이드를 사용하자 복잡한 설계도 문제 없이 구현하여 장기 내구성 솔루션으로 케이블이 마모되는 것을 보호할 수 있었습니다.
Fuse 시리즈와 TPU 90A Powder는 접근성도, 또 경제성도 우수하여 기업이 공급망과 유지 관리 필요성을 자체적으로 제어할 수 있는 활로를 개척하는 데 도움이 됩니다. TPU 90A Powder로 제작된 파트는 기계 장비 보호와 컴포넌트 수명 개선에 안성맞춤이며 궁극적으로는 이런 특성이 운영비 절감과 다운타임 단축 효과로 이어집니다.
도이치반이 열차 운행을 지속하는 데 TPU 제조 보조 도구를 사용한 방법
노이뮌스터에 위치한 도이치반의 차량 유지 관리 지점은 독일의 대중 교통인 열차의 정비와 유지 관리를 담당하고 있으며 이런 업무를 최대한 효율적으로 진행하기 위해 3D 프린팅의 도움을 받고 있습니다. 도이치반은 3D 프린팅을 업무 흐름에 통합한 결과, 수백만 유로의 비용을 절감하고 운행 중인 열차가 다시 선로로 복귀하는 데 걸리는 리드 타임을 단축할 수 있었습니다.
제조 엔지니어 겸 적층 가공 전문가 카스텐 볼프그램(Carsten Wolfgramm) 씨는 Fuse 1+ 30W SLS 3D 프린터 두 대를 감독하고 있는데, 한 대는 Nylon 12 Powder를, 나머지 한 대는 TPU 90A Powder를 프린팅합니다. 볼프그램 씨는 “Formlabs의 장비를 사용하는 이유는 가격 대비 성능이 뛰어나기 때문입니다. 특히 SLS 프린터는 안정적이고 플러그 앤 플레이 방식으로 사용할 수 있죠. 파트를 끊임 없이 반복 설계할 때는 작업이 훨씬 더 쉬워집니다. 연중무휴 24시간, 주 7일, 매일 작동하니까요."라고 설명합니다.
일반적인 유지 관리 작업 중에는 기술 인력이 짐 받침대를 분리하여 기차 차량 벽을 다시 칠하고 호일을 다시 붙이는 작업이 있습니다. 랙을 이리저리 옮기면서 벽이 손상되는 일이 잦았고, 유지관리팀이 방금 한 모든 작업이 헛수고로 돌아갔습니다. 벽을 보호해야 했던 담당 팀은 랙용 맞춤형 커버를 디자인하고 TPU 90A Powder로 3D 프린팅했습니다. 이렇게 제작된 커버를 랙 위로 밀어 올려 가장자리를 완충 처리하면 랙을 제거 및 교체 중에 새로 칠해진 기차 내부에 손상을 입히지 않을 수 있습니다.
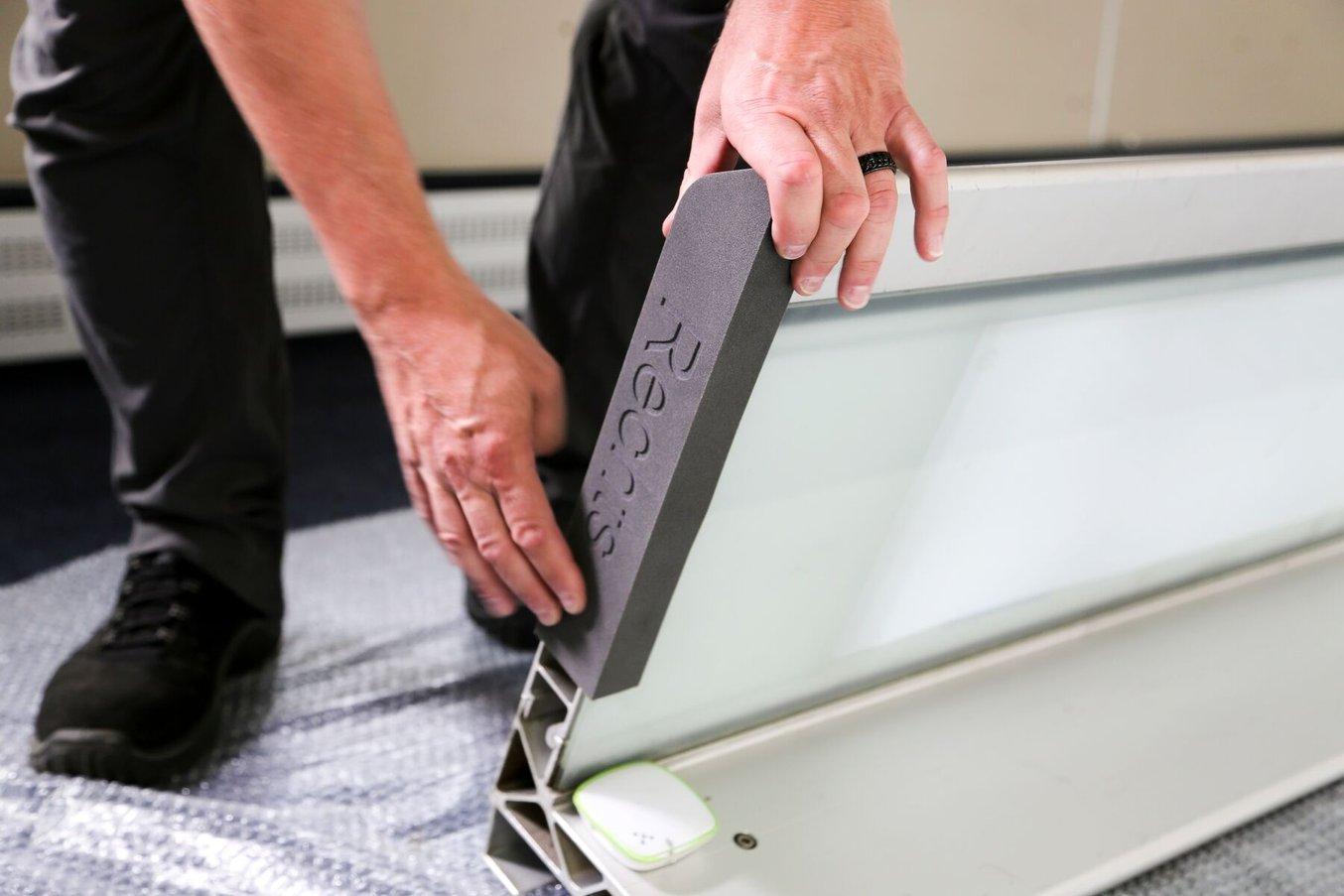
스크래치와 충격 보호용으로 유연성이 있는 TPU 90A Powder를 사용했습니다.
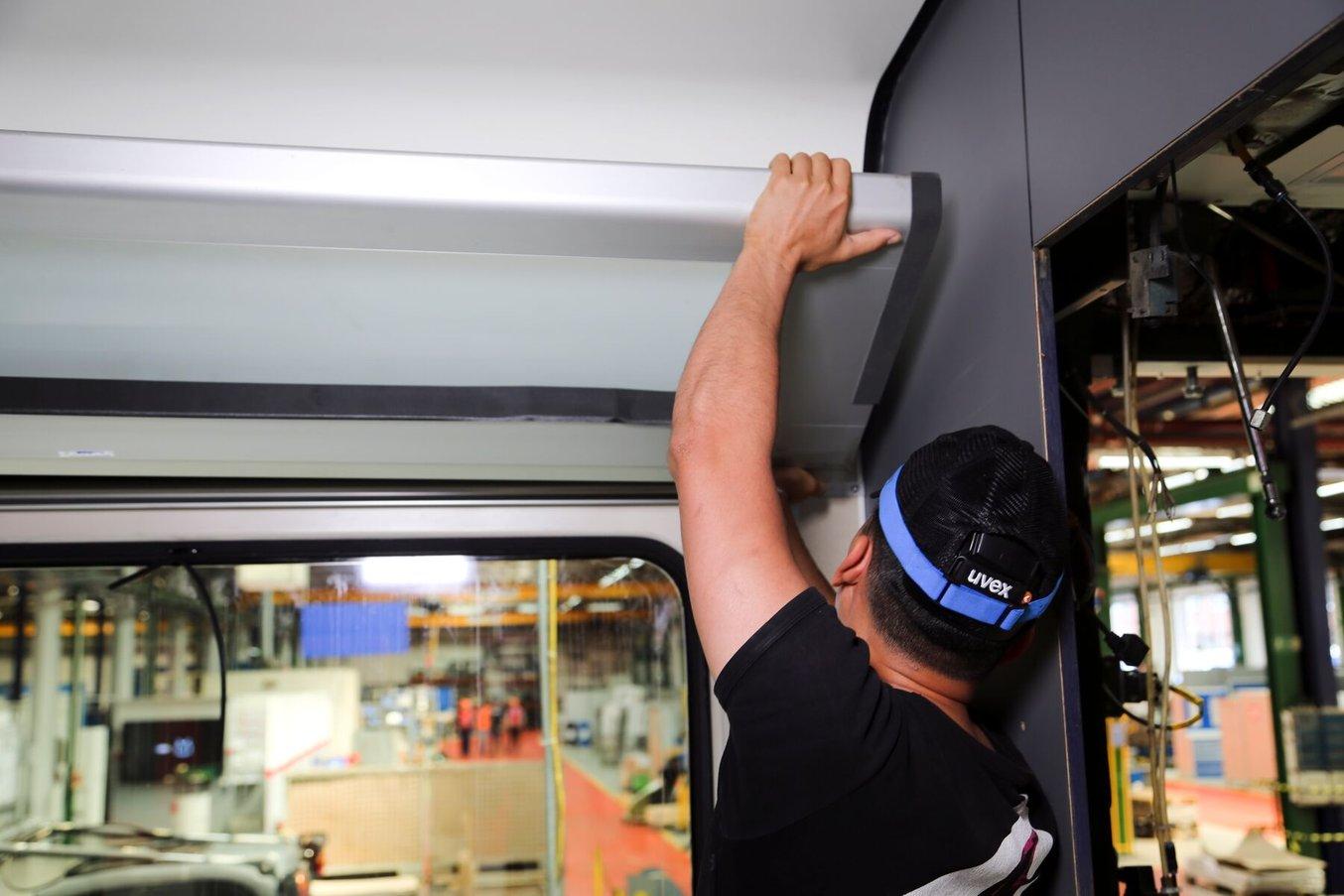
SLS 3D 프린팅을 사용하면 수하물 선반과 벽 사이에 끼워 넣을 수 있는 슬림한 디자인을 제작할 수 있습니다.
볼프그램 씨는 “스크래치 방지용 피처를 개발하여 3D 프린팅하기 전에는 동료들이 항상 뽁뽁이나 이와 유사한 도구를 뒤집어 씌웠지만 결과물이 늘 좋았던 것은 아닙니다. 마침내 스크래치가 하나도 생기지 않게 할 수 있었던 것은 이번이 처음입니다. 새로운 TPU 파트 덕분이죠.”라고 합니다.
카스텐 볼프그램(Carsten Wolfgramm), 제조 엔지니어 겸 적층 가공 전문가, 도이치반
도이치반은 이렇게 3D 프린팅으로 제작된 MRO 파트를 채택하여 비용 절감과 노동 시간 단축을 실현함으로써 대규모 운송 회사가 3D 프린팅을 업무 흐름에 통합하는 청사진을 제시하고 있습니다. 이 보호용 커버 같이 유연성 있는 맞춤형 3D 프린팅 파트를 인하우스 방식으로 제작할 수 있는 역량을 갖춘 도이치반은 프로세스는 더 효율적으로, 기차는 더 빨리 선로에 복귀시킬 수 있게 되었습니다.
미국의 완구 및 e-바이크 회사인 라디오플라이어(Radio Flyer)의 프로토타이핑 작업과 TPU
100년 이상 미국의 가정에서 신뢰하고 사랑해온 라디오 플라이어는 상징성 짙은 Original Little Red Wagon®의 제작사이며 해당 제품은 장난감 명예의 전당에 오른 유명한 제품입니다. 라디오 플라이어는 세계 최고의 승용 장난감 생산업체로서 대중문화의 선두 주자이자 모든 어린이의 크리스마스 선물 목록에서 일 순위를 차지해온 기업으로 이들이 생산해 온 웨건, 스쿠터, 세발자전거, 고카트, 전기 자전거를 비롯한 혁신적인 제품은 가족이 가는 곳이라면 어디서든 빠지지 않고 따라다닙니다.
3D 프린팅은 라디오 플라이어의 개발 프로세스에서 큰 부분을 차지하며 TPU 90A Powder를 사용해 본 디자인 엔지니어 아고스티노 로벨로(Agostino Lobello)는 해당 소재로 제작한 프로토타입이 정말 최종 제품처럼 작동할 수 있다는 사실을 알게 되었습니다. 로벨로는 “제가 사용해 본 다른 3D 프린팅 TPE/TPU와 비교해 볼 때 하이그립의 표면 마감은 독특합니다. 그런 관점에서 사출 성형 TPE/TPU와 더 흡사하게 느껴지고 이점은 프로토타입 응용 분야에서는 획기적이죠. 현재 이 프로세스에 이용할 수 있는 3D 프린팅을 제외한 차선책은 프로토타입 도구에 실제 TPE나 다른 우레탄을 주입하는 것이므로 3D 프린팅 쪽이 비용과 시간 모두 더 효율적인 방법입니다.”라고 설명합니다.
"이 소재를 타이어 트레드, 핸드 그립, 범퍼, 시트 쿠션에 사용할 예정인데다 특정 탄성률을 가진 TPE 스프링의 프로토타입 소재로 사용할 수 있다는 점에 몹시 기대됩니다.”
아고스티노 로벨로(Agostino Lobello), 설계 엔지니어
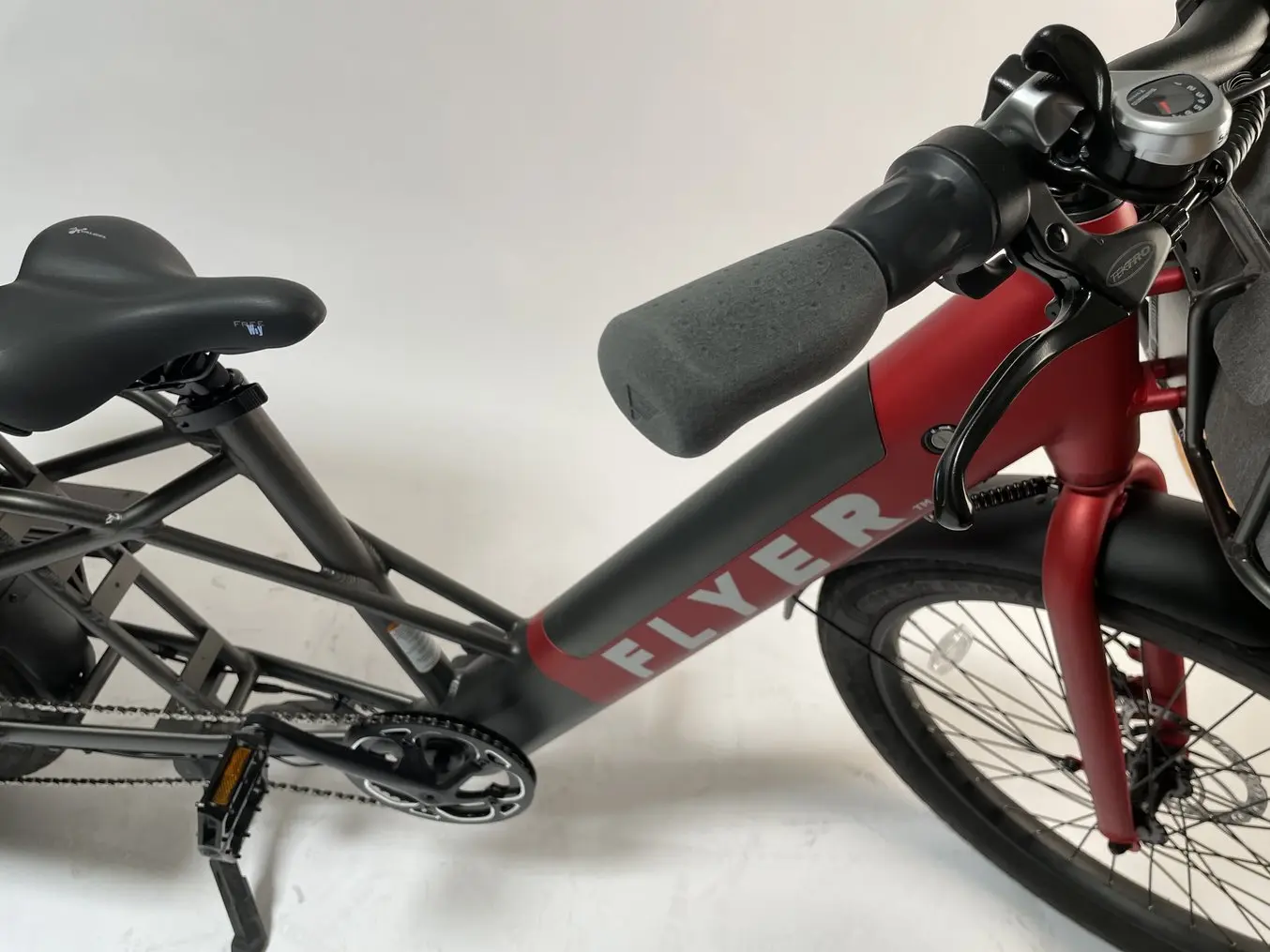
TPU 90A Powder를 Fuse 시리즈 프린터에서 사용한 라디오플라이어는 Flyer™ L885 Family Cargo eBike의 소프트 그립 핸들 바와 기능적으로 동일한 프로토타입 파트를 제작할 수 있었습니다.
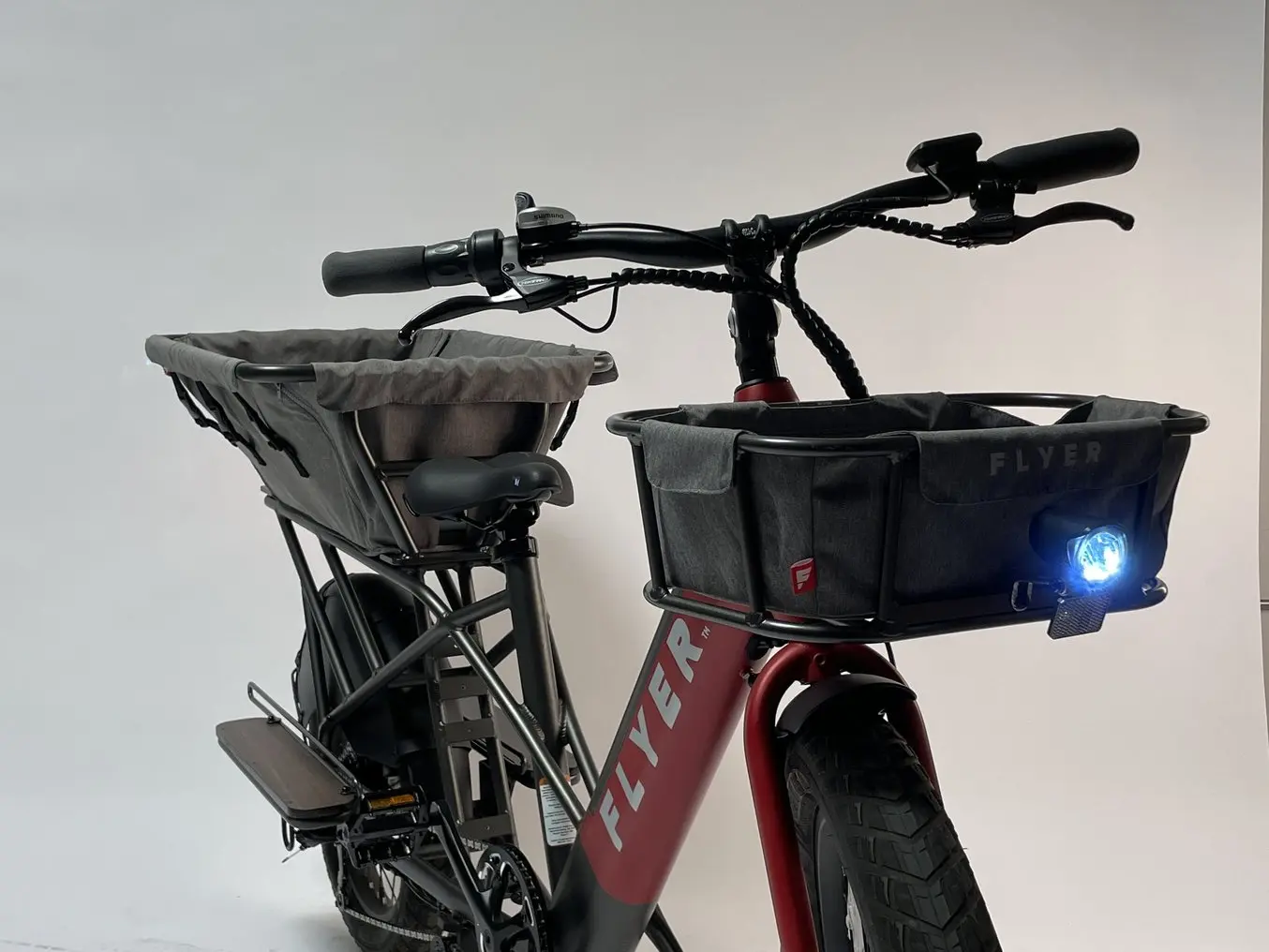
Fuse 시리즈에서 TPU 소재 3D 프린팅하기
접근성이 우수한 SLS 3D 프린팅 워크플로와 TPU 분말은 고품질 반복 설계 프로토타입 제작을 이용한 설계 프로세스 개선이나 맞춤화 최종 사용 파트 생산으로 제조 업체의 가능성을 활짝 열어주었습니다.
프린터와 Fuse Sift가 포함된 Fuse SLS 에코시스템은 컴팩트하고 경제적이며 접근성이 우수합니다. Formlabs TPU 90A Powder의 출현으로 이전에는 성형으로 제작해야 했던 튼튼하고 유연하며 등방성까지 갖춘 파트의 제작을 통해 새로운 응용 분야를 개척하고 워크플로를 간소화할 수 있게 되었습니다. 고무와 유사한 파트를 인하우스 방식으로 생산할 역량을 갖추게 되면 설계와 제조 공정을 더 폭넓게 제어할 수 있으며 이런 효과는 어떤 분야의 제품을 생산하고 어떤 업계에 속해 있어도 동일합니다. Formlabs의 TPU 90A Powder는 피부 안전 등급을 획득하여 헬스 케어와 웨어러블 업계의 가능성을 활짝 열었습니다.
Formlabs SLS 워크플로를 이용한 3D 프린팅 TPU 파트의 생산 공정을 자세히 알아보려면 TPU 90A Powder 샘플 파트를 무료로 요청하거나 당사 영업팀에게 귀사의 독특한 응용 분야를 상담해 보세요.