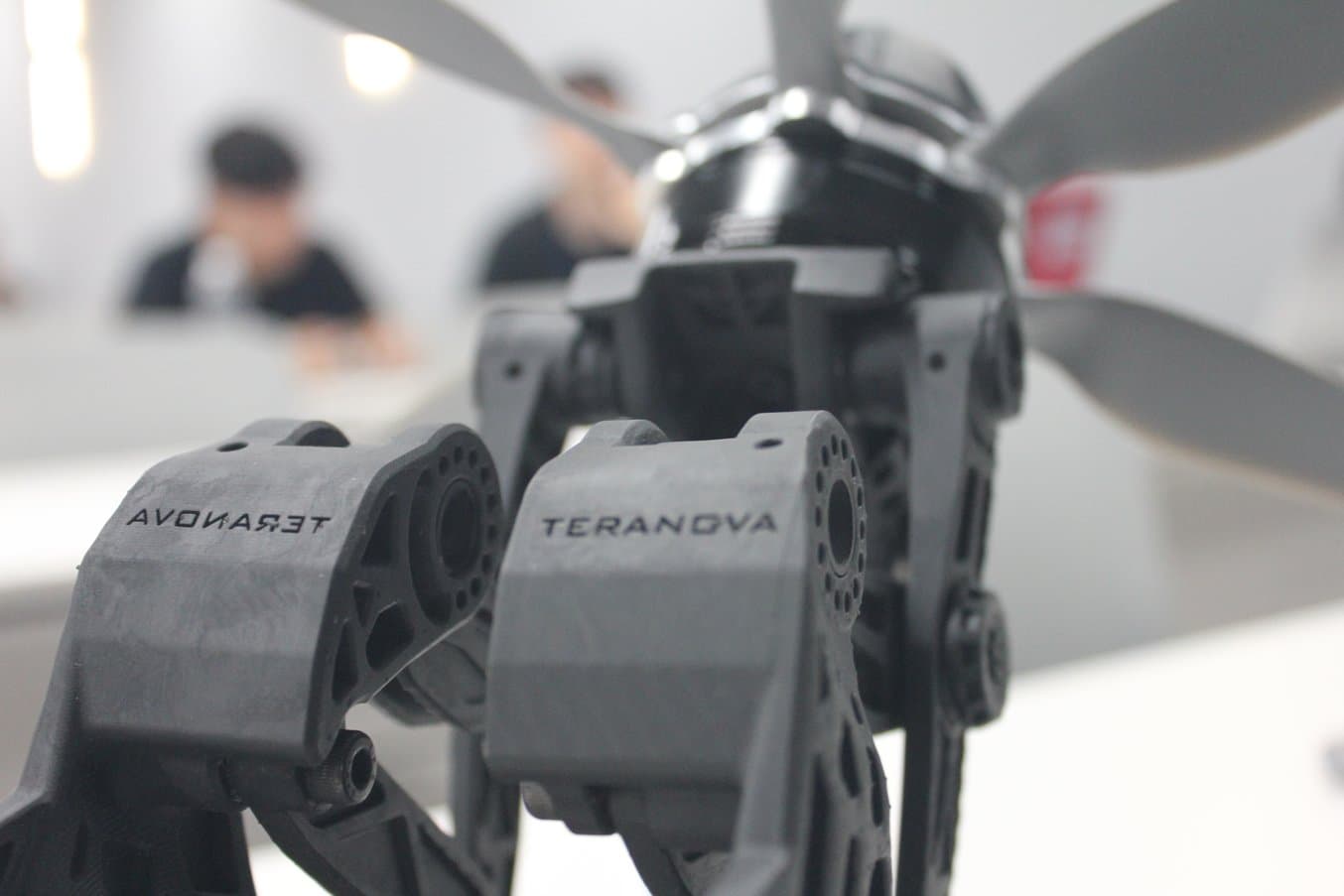
최대 1톤 화물 배송을 위한 테라노바의 도전, 3D 프린터는 필수
테라노바는 도심 항공 모빌리티(Urban Air Mobility, UAM) 기체 제작사입니다. UAM은 도심 상공에서 사람이나 화물을 운송하는 항공교통 수단인데, 기체 개발과 인프라, 플랫폼, 서비스, 유지보수 등 관련 사업을 모두 포괄하는 개념입니다. 테라노바가 현재 비즈니스 모델로 삼은 사업 하나는 물류 배송입니다. 테라노바는 새로운 모터 기술을 개발하는 등, 시제품을 계속 만들어내야 해서 3D 프린터를 매우 많이 가동해야 하는 입장입니다. ‘최대 1 톤의 화물 배송’이라는 목표를 세우고, 이에 맞춰 기체를 개발 중이라고 전합니다. 새로운 기술에 민감하고, 제품을 많이 만들어 비교해야 하는 테라노바는 3D 프린터를 필수적으로 사용해야 했습니다.
테라노바도 처음에는 비용 등을 이유로 3D 프린터 중 FDM 방식을 먼저 사용하기 시작했습니다. 그런데 FDM 방식으로 만든 시제품은 출시가 어려운 외형을 가졌습니다. 출력 속도도 느리고 소재도 다양하지 않아서 모양만 볼 수 있을 뿐, 실질적인 개발에 활용하기 어려웠습니다. 결정적인 SLA 프린터 사용 계기는 후가공 처리 방식 문제입니다. 결이 얼마나 보이는지, 후가공이 얼마나 필요한지 여부도 중요했습니다. SLA 프린터는 외형을 만드는 기술, 출력 속도 등 문제에서 확실히 더 나은 선택입니다. 그런데 레진에서 특유의 화학 약품 냄새가 심하게 난다는 점이 곤란한 점이 있는데요. 그래서 주로 외형을 아름답게 해야하는 경우, 제품 모양을 섬세하게 결정할 수 있는 SLA를 적극 사용하고 기계적인 구조물은 FDM 방식을 사용했습니다.
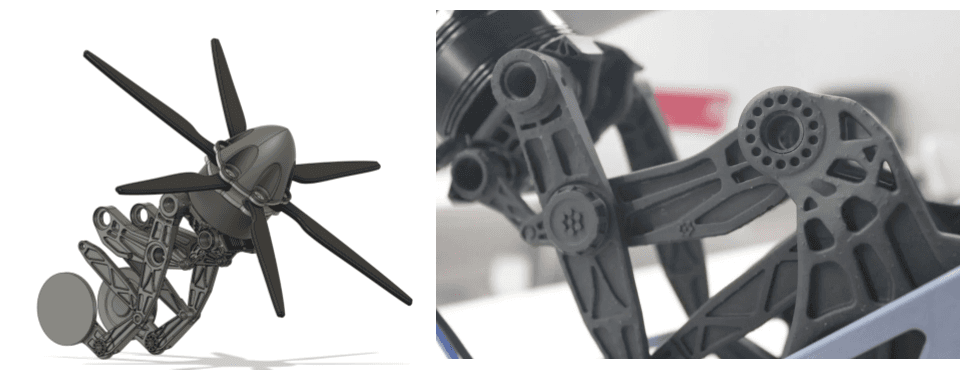
편리하고 빠르고 견고하다, Form 4가 보여준 신세계
Form 4를 사용하기 시작한 첫 번째 계기는 이전 사용하던 3D 프린터의 출력 실패율이 너무 높아졌기 때문입니다. 출력시간, 가격, 퀄리티를 전부 고려하니 답이 나왔습니다. 처음 사용했을 때 놀란 부분은, 레진 화학 약품 특유의 냄새가 전혀 나지 않는다는 부분이었습니다. 이전 사용했던 SLA 프린터의 몇 안되는 문제점 중 하나인데 바로 해결이 되었습니다. 그 다음엔 인터페이스와 기능에 감탄했습니다.
가장 놀라운 점은 출력 성공률이 타사 레진 3D 프린터 대비 매우 높다는 것 이었습니다. 테라노바에서는 A사 레진 3D 프린터를 사용중이었는데, 해당 프린터로 출력할 경우 출력 성공률이 약 70% 정도 밖에 안되었습니다. 처음 Form 4 사용 할때도 비슷하지 않을까 생각했었는데 놀랍게도 현재까지 출력 성공률은 90% 이상으로 집계 되었습니다. 비록 몇 번 출력 실패한 적이 있었지만, 해당 부분은 설정에서 실수하거나, 잘 못 설정된 부분으로 인한 실패여서, 기기 자체의 출력 성공율은 100%에 가깝다고 얘기해주었습니다. 높은 출력 성공률로 인하여 재료 낭비가 줄어들었고, 부품 생산 속도는 빨라졌기 때문에 프로젝트를 진행하는 속도가 높아졌다고 합니다.
터치 화면이 큰 편이라 사용자 친화적이었고, 프린터를 어디에 설치해도 기계 수평을 잡아주는 기능이 활성화되어서 편리했습니다. 대시보드도 필요한 데이터를 직관적으로 표기해주고, 온도도 알아서 다 맞춰주는 시스템이라 모든 작업이 황당할 정도로 간편하게 이루어졌습니다. 기계, 부품 세척과 레진을 믹싱하는 과정도 Form 4에서는 대폭 축소되었습니다. 모든 과정이 자동화로 진행되는데 퀄리티 또한 놓치지 않았습니다. 체크리스트와 경고창으로 세심하게 확인을 시켜줘서 작은 실수도 일어나지 않도록 방어해주었습니다. 이전에는 빌드 플랫폼에서 출력물을 제거 하지 않아서, 출력을 실패한 경험도 가지고 있었는데, Form 4는 해당 과정을 일일히 알림으로 보여주니 셋팅 과정에서의 실수도 많이 줄었습니다. 도심 항공 교통수단은 불량품 문제에 매우 민감하므로, 이런 요소 하나 하나가 귀중한 기능이었습니다.
처음에는 Form 4가 사용한다는 LFD 작동 방식이 생소했다는 감상이 있었습니다. LFD 프린트는 백라이트 장치를 활용하여 강도 높은 빛을 균일하게 쏘는 작동 방식입니다. 여기서 빛이 광처리 장치(Light Processing Unit, LPU) 4를 통과하여 일련의 편광판, 광학 코팅 및 맞춤형 액정 디스플레이를 사용하면 프린팅된 층의 모양으로 형성됩니다. 고해상도 LCD와 사전 튜닝된 안티 애일리어싱 기능으로 날카로운 디테일과 매끈한 표면 마감, 정확한 공차까지 얻을 수 있다는 것이 장점입니다. 그래서 매우 간단하게 제품을 제작하는 3D 프린터인데 경도와 퀄리티 면에서도 완벽했습니다.
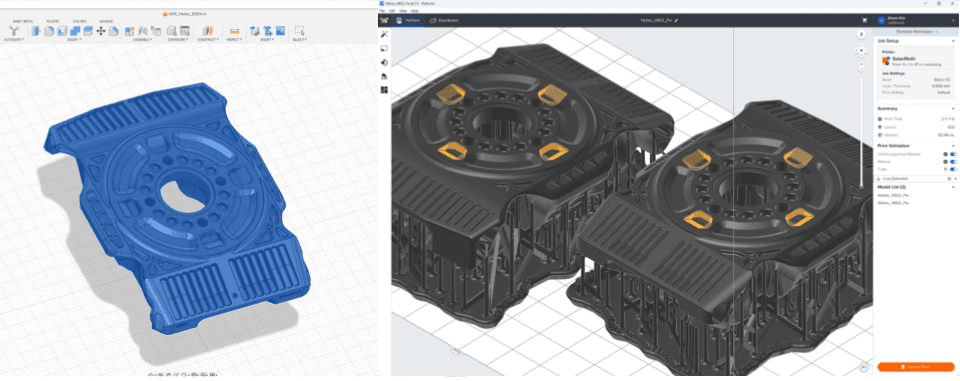
Form 4는 편리한 기능 만큼이나 표면 품질과 내구성이 뛰어난 제품을 생산해냅니다. 좋은 제품이 출력되는 비결은 프린터의 자체 기능 뿐 아니라 우수한 재료 품질 덕분입니다. 테라노바는 Form 4의 재료로 Black Resin V5와 Tough 2000 Resin를 사용했습니다. 검은색 범용 레진은 Black Resin V5인데, 변형이 적고 튼튼합니다. 사출 성형되는 표면 마감은 제품을 최대한 의도대로 제작할 수 있게 해줍니다. Form 4 에코시스템을 활용하면 Black Resin V5으로는 이전 버전보다 세 배 더 빠르게 프린팅할 수 있습니다. Tough 2000 Resin은 그 이름만큼 가장 강하고 경도가 높은 소재입니다. Tough 2000 Resin은 쉽게 휘어지지 않아서, 강하고 견고한 프로토타입 파트를 프린트하기에 적절합니다
완벽한 재료가 완벽한 제품을 만든다
Form 4는 편리한 기능 만큼이나 표면 품질과 내구성이 뛰어난 제품을 생산해냅니다. 좋은 제품이 출력되는 비결은 프린터의 자체 기능 뿐 아니라 우수한 재료 품질 덕분입니다. 테라노바는 Form 4의 재료로 Black Resin V5와 Tough 2000 Resin를 사용했습니다. 검은색 범용 레진은 Black Resin V5인데, 변형이 적고 튼튼합니다. 사출 성형되는 표면 마감은 제품을 최대한 의도대로 제작할 수 있게 해줍니다. Form 4 에코시스템을 활용하면 Black Resin V5으로는 이전 버전보다 세 배 더 빠르게 프린팅할 수 있습니다. Tough 2000 Resin은 그 이름만큼 가장 강하고 경도가 높은 소재입니다. Tough 2000 Resin은 쉽게 휘어지지 않아서, 강하고 견고한 프로토타입 파트를 프린트하기에 적절합니다.
김지환, Tech / CTO
“체크리스트로 착오 없이 제품 생산, 안정적이고 단단한 LFD 기술. 정확함이 생명인 기체 제작에는 반드시 필요했죠. “
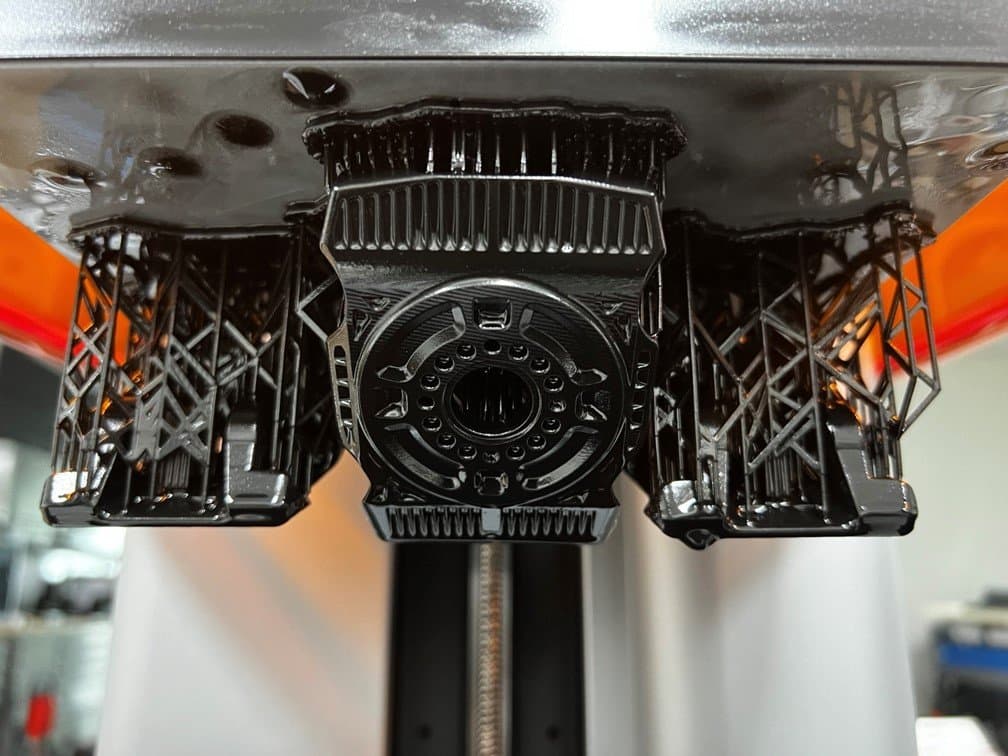
정확도가 생명, Form 4와 나아갈 테라노바의 미래
라노바의 목표는 언제나 하늘을 바라보는 기업답게 다양하고 높습니다. 연구부터 개발, 설계, 제조를 직접 수행하는 수직 계열화를 구축하고 단계별 세부 추진 전략을 통해 2026년까지 시제기 출시가 목표입니다. PAV, AAM 등 항공기와 조종성 평가 시뮬레이터와 원격 조종 관제 시스템을 개발 및 판매 중이기 때문에 제품의 안정성과 품질이 특히 중요합니다. 테라노바에서는 목표는 3D 프린팅을 이용하여 좋은 기체를 제작하는 것이 목표입니다.
테라노바에서는 앞으로 Formlabs 제품 사용 비중이 늘어날 것으로 보고 있습니다. 테라노바는 기존의 제품을 사용하는 것이 아니고 자체적으로 부품을 개발하고 생산하므로, 3D 프린팅을 이용하여 부품을 생산을 준비하고 있습니다. 그 중에서 Rigid 10 레진을 이용하여 몰드를 제작하고, 제작하는 몰드를 사출 생산 또한 현재 고려중인 상태이고, 시험기를 3D 프린팅을 통해서 생산을 준비중에 있습니다.
앞으로 Form 4 뿐만 아니라 Fuse 1+로도 도입할 예정이라고 합니다. Fuse 1+를 통해서 자체적으로 부품을 생산하는 것도 현재 고려중인 상태 입니다. Fuse 1+로는 기체 중 landing에 들어가는 랜딩기어용 부품을 제작하고자 고려하고 있습니다.
고도로 발달한 기술을 다루고, 무엇보다도 오류 없는 개발과 생산이 중요한 테라노바. 테라노바가 높은 하늘 위에서도 안심하고 믿고 맡길 수 있는 3D 프린터가 되기 위하여, Form 4를 시작으로 확실한 파트너가 되어주리라 기대해봅니다.
이번 사례는 폼랩 공인 파트너 '에이엠플러스' 의 고객사례입니다.