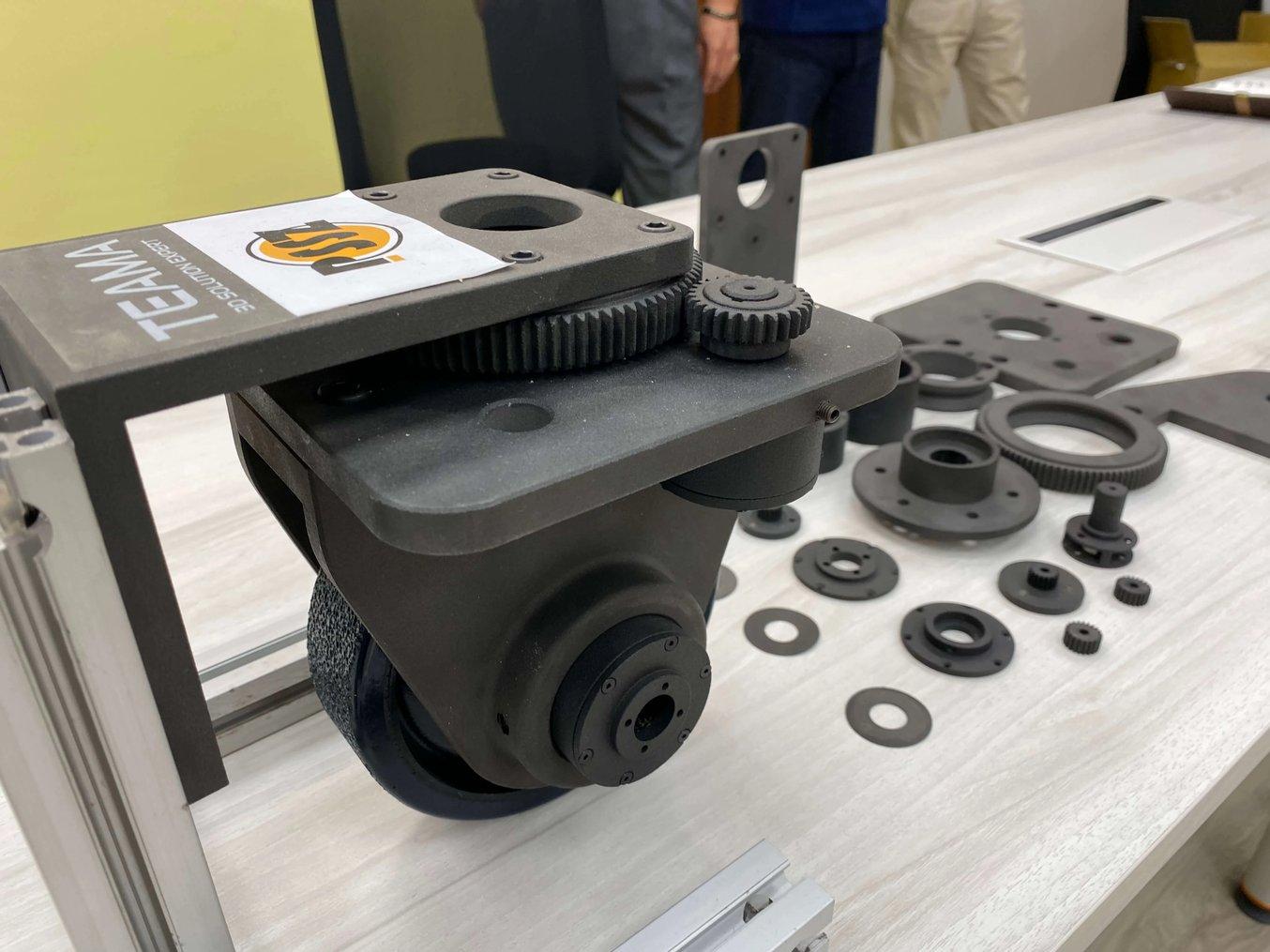
In recent years, the development of robots has changed the operating model of society. Led by Professor Huang Zhongqin from the Department of Electrical Engineering of the National Taiwan University of Science and Technology, a dynamic team comprising students Wu Yidao, He Jiaxiang, and Cai Shaoxiang embarked on an impactful industry-academic collaboration with a domestic company. Their objective? Pioneering the creation and deployment of an innovative guidance system for a steering wheel-type autonomous mobile robot, complete with a unique screw-lifting function.
Traditionally, the journey from concept to prototype in robotics involved significant time and cost investments, particularly in the realm of mould creation. However, the team utilized the Formlabs Selective Laser Sintering (SLS), Fuse 1 3D Printer and Nylon 12 material to prototype steering wheel components, they slashed both costs and production timescales, reducing mold creation from a typical two to three months down to just one week.
The genesis of the steering wheel-type autonomous mobile robot stemmed from the company's vision to innovate steering wheel structures and associated control systems. Leveraging the students' expertise in unmanned vehicle construction, the collaboration bore fruit as the two entities synergized their efforts to complete the project. One steering wheel contains two motors, which drive the steering gear and the wheel to move forward and backward respectively. The built-in lifting system with unmanned vehicles as the main body, combined with motor control, power management, limit switches, environment map creation, and action logic judgment, can complete the transportation of goods and expand the use of automation in factories.
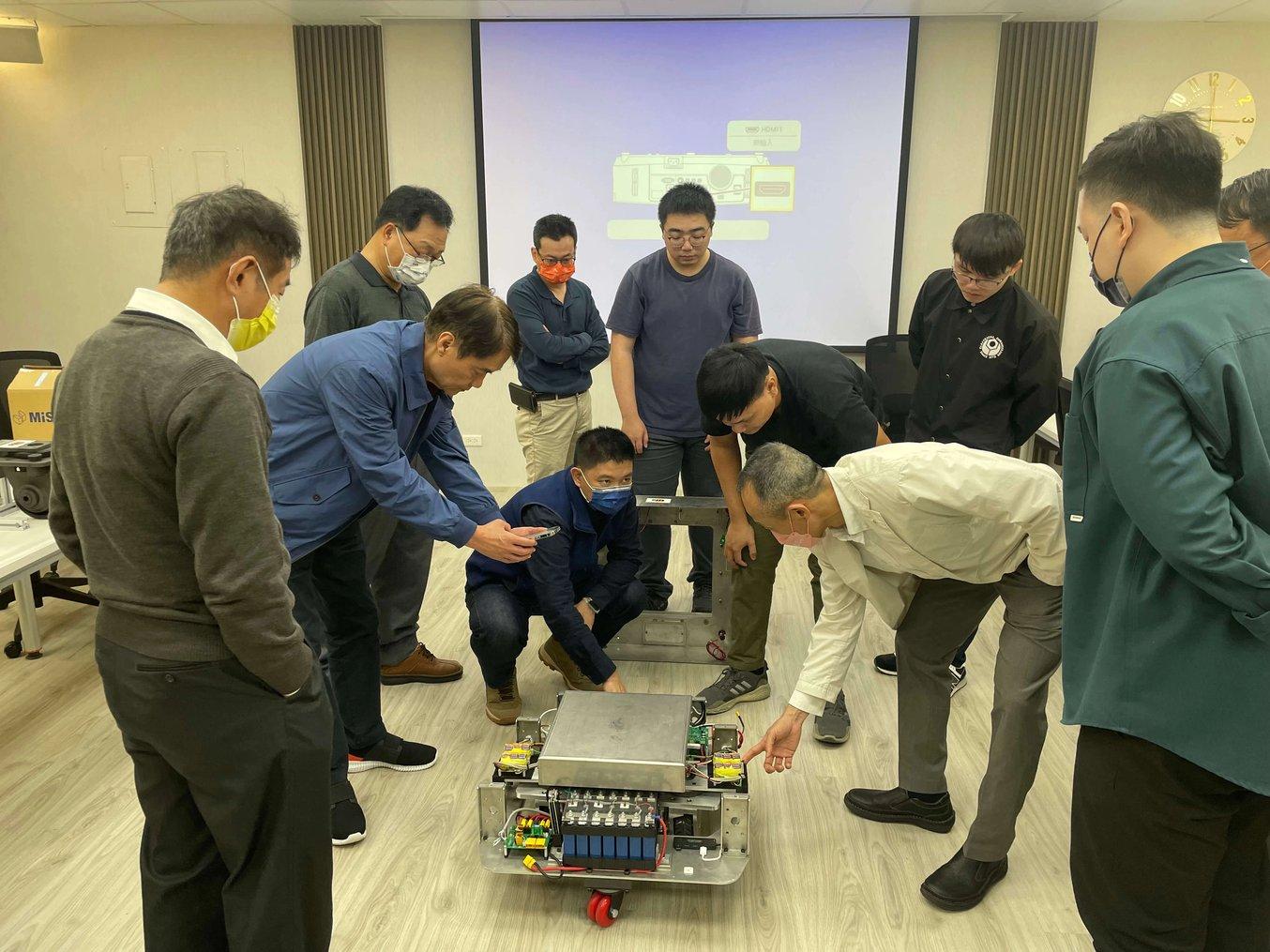
A steering wheel-type autonomous mobile robot developed by a team of Taiwan University of Science and Technology students through industry-university cooperation
The entire manufacturing process, from initial design to finished product, unfolded over eight months. Collaborating closely, the student team and the company jointly developed the program, seamlessly integrating software and hardware components. Employing 3D printing, they meticulously scrutinized the robot's appearance and functionality, continuously refining and iterating throughout the process. Student He Jiaxiang highlighted the indispensable role of 3D printing, stating, "Without it, we might not have achieved such rapid progress." Traditionally, the creation of a metal mold would demand a substantial two to three-month timeframe, exacerbating timelines with the need for reiterations. However, the revelation of the 3D printed prototype, crafted with the Fuse 1 printer using Nylon 12 Powder, exceeded expectations.
In utilizing Formlabs' Nylon 12 Powder, renowned for its remarkable balance between strength and intricate detail, the team ensured the production of highly functional prototypes. This versatile material not only facilitated the rapid iteration of complex assemblies but also endowed the final product with exceptional durability and environmental stability, further underlining the pivotal role of advanced materials in the project's success.
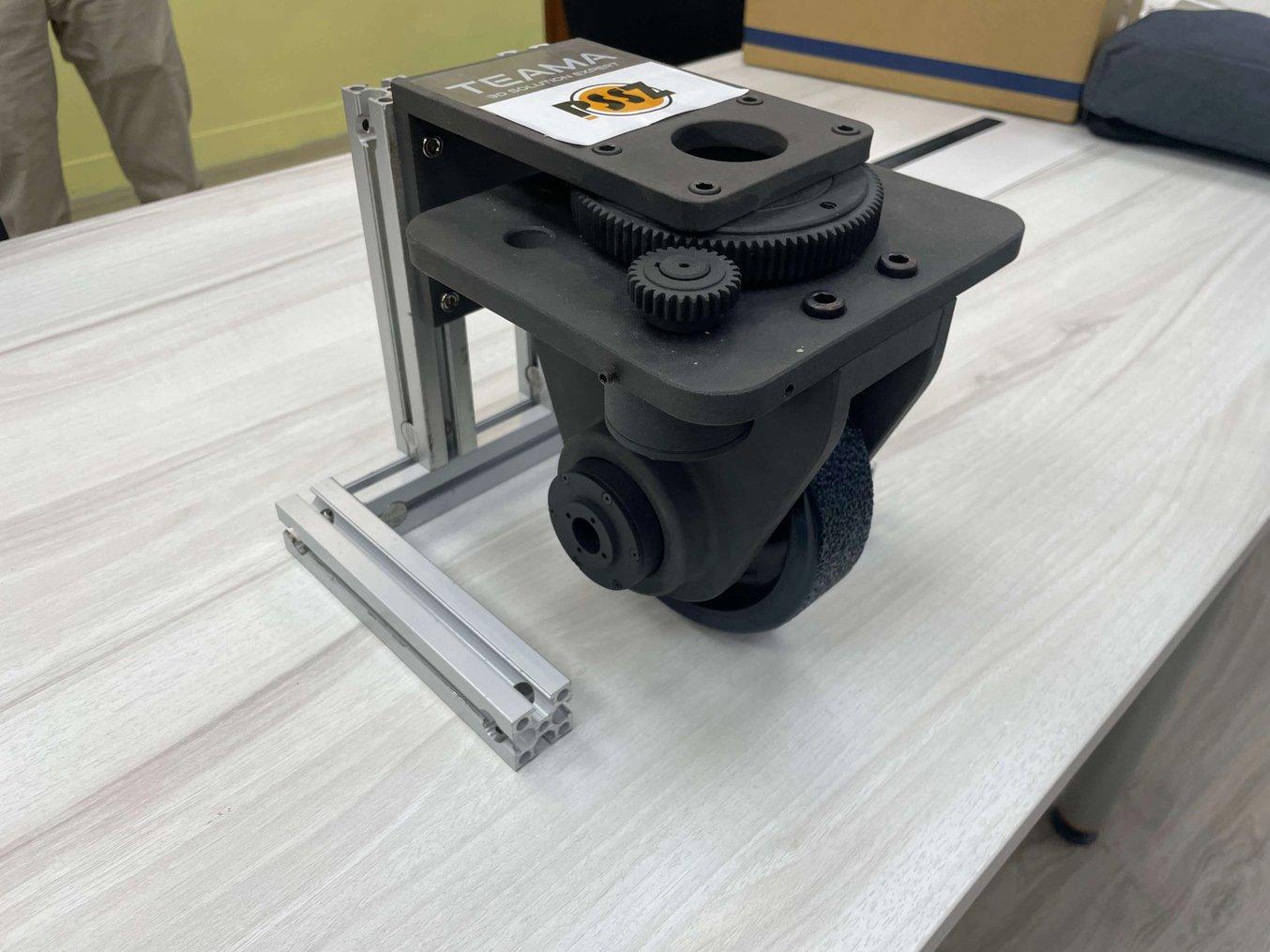
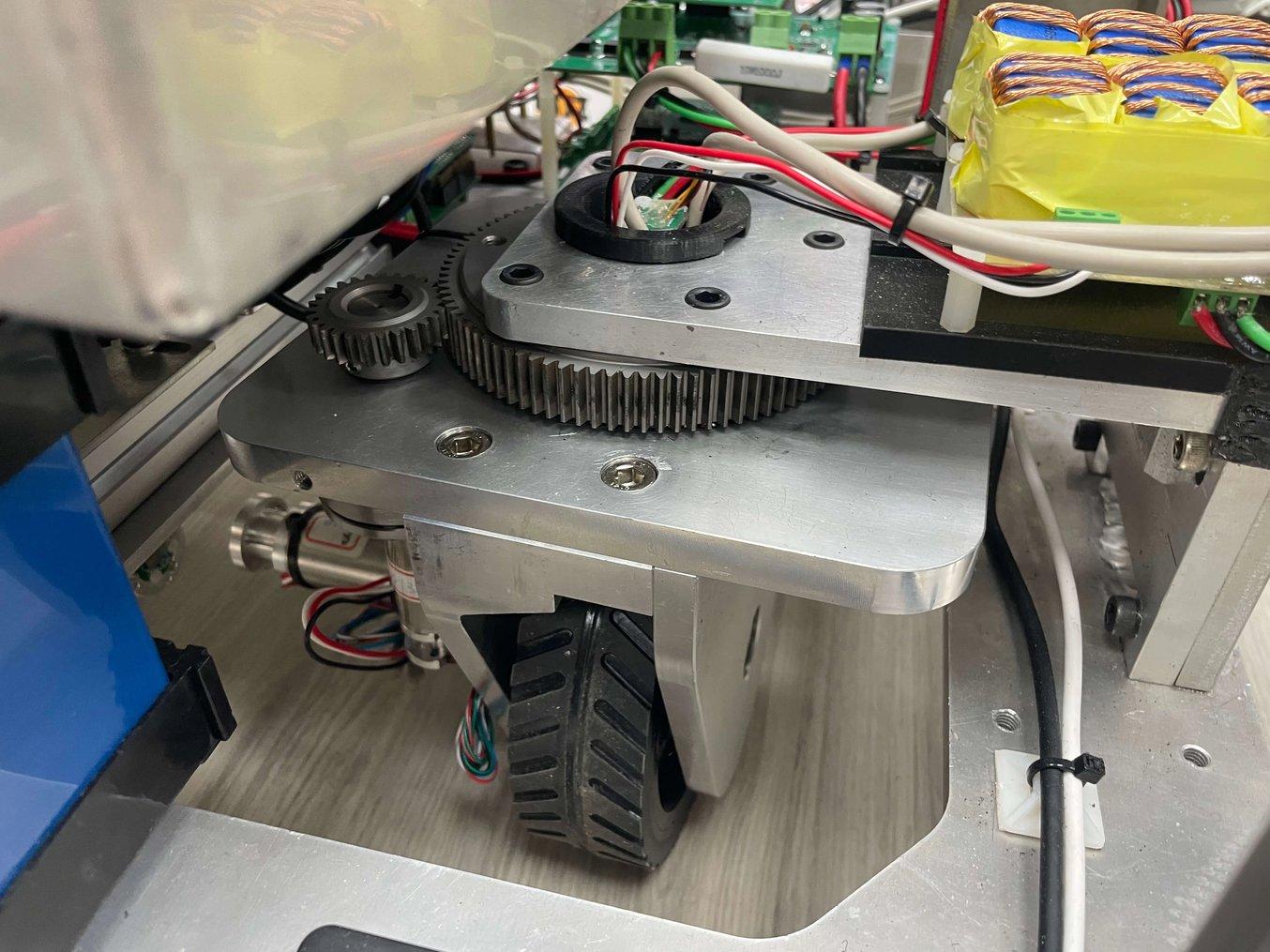
Before creating the finished product, the team utilized the Fuse 1 laser sintering 3D printer with Nylon 12 Powder to verify both appearance and function.
Institutional director Zhang Hongren and engineer Lai Zhenghe, integral to the mechanism design, emphasized their reliance on 3D printing to ensure the feasibility of the robot design. They praised the technology's precision and efficiency, acknowledging its transformative impact on the project's development.
"What surprises me most about 3D printing is that it can control the size to 0.3 mm. As a designer, the more precise the control can be, the better," he emphasized.
"The traditional machine industry requires a lot of time to process parts, while 3D printing can complete the same task in a week. Therefore, time efficiency is significantly improved, and costs are reduced. This is 3D printing. The advantages of 3D printing."
Zhang Hongren, Director of Organization
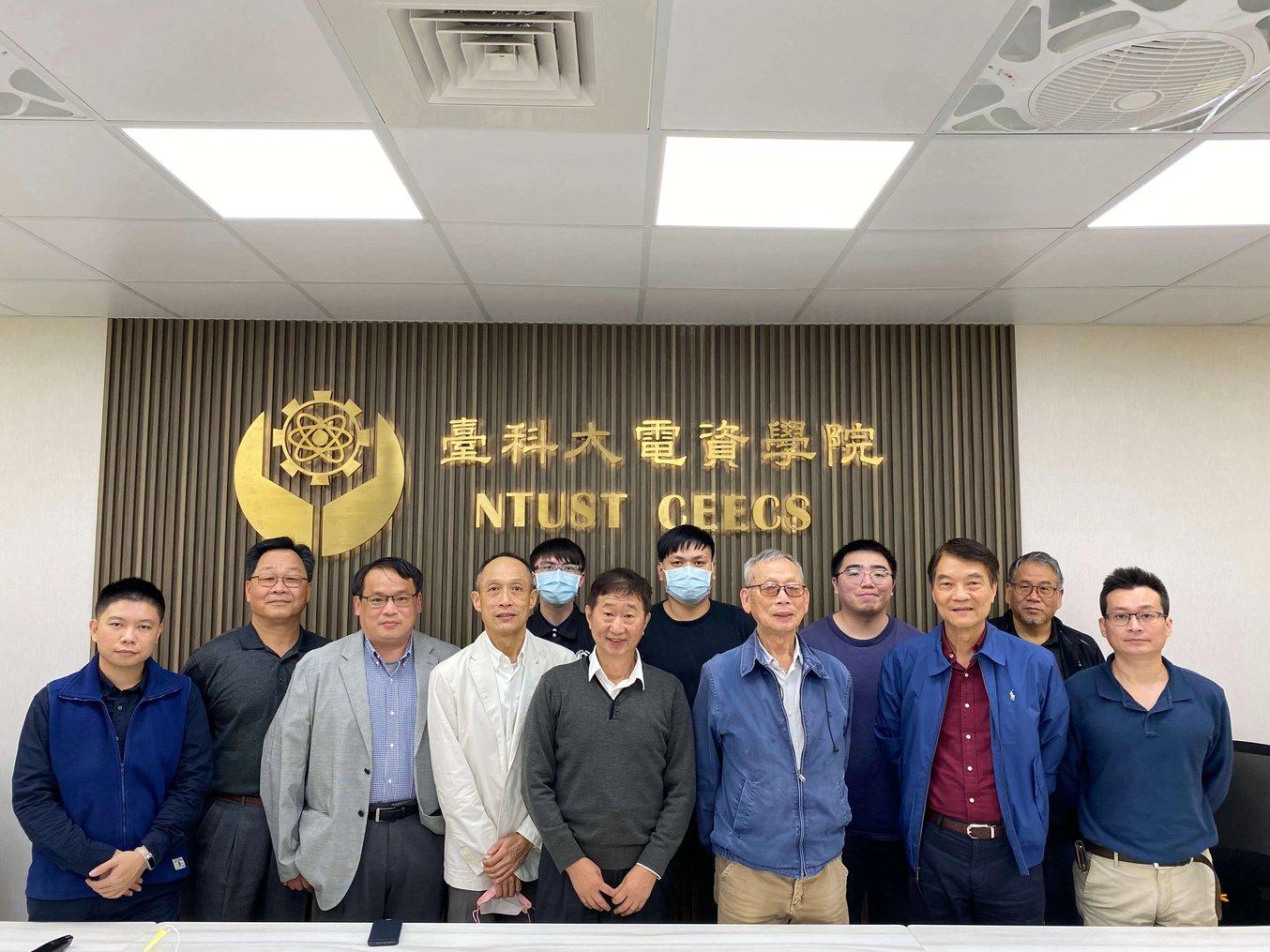
Professor Huang Zhongqin of the National Taiwan University of Science and Technology, a student team and representatives from industry-academy cooperation company.
General Manager Dr Huang Yingyao highlighted the operational advantages offered by 3D printing, enabling accelerated product development and verification, and facilitating rapid adjustments in response to market changes. He expressed pride in the student team's accomplishments, recognizing the collaborative efforts of academia and industry in realizing this innovative milestone. While acknowledging the ongoing refinement needed before market readiness, Dr. Huang commended the dedication and ingenuity displayed by all involved parties, underscoring the transformative potential of collaborative ventures.