Formlabs is focused on offering an intuitive and efficient 3D printing experience, starting with our print preparation software. In recent PreForm versions, you can experiment with Adaptive Layer Thickness—a public beta feature that varies layer thickness throughout a print depending on part geometry.
Through the use of stereolithography (SLA) technology, Formlabs has consistently provided its customers with high quality 3D printing. Depending on the type of resin, you can choose between layer heights ranging from 25 to 200 microns, selecting thin layers for better resolution or thick layers for faster prints. To optimize the benefits of both options, Formlabs has introduced a new feature, adaptive layer thickness.
What is Adaptive Layer Thickness?
Adaptive Layer Thickness is an advanced print mode that analyzes the geometry of parts imported into PreForm and assigns layer heights throughout the sliced model to maximize print speeds while preserving fine detail. Adaptive Layer Thickness is now available for select materials on the Form 3 and Form 3B printer.
Depending on the shape of a design, layer thickness can drastically change the surface finish of a part. For example, in areas with steeply angled or curved walls, layer lines are more pronounced and can affect the smoothness of the printed surface. In areas with walls perpendicular to the build platform, layer lines are less pronounced.
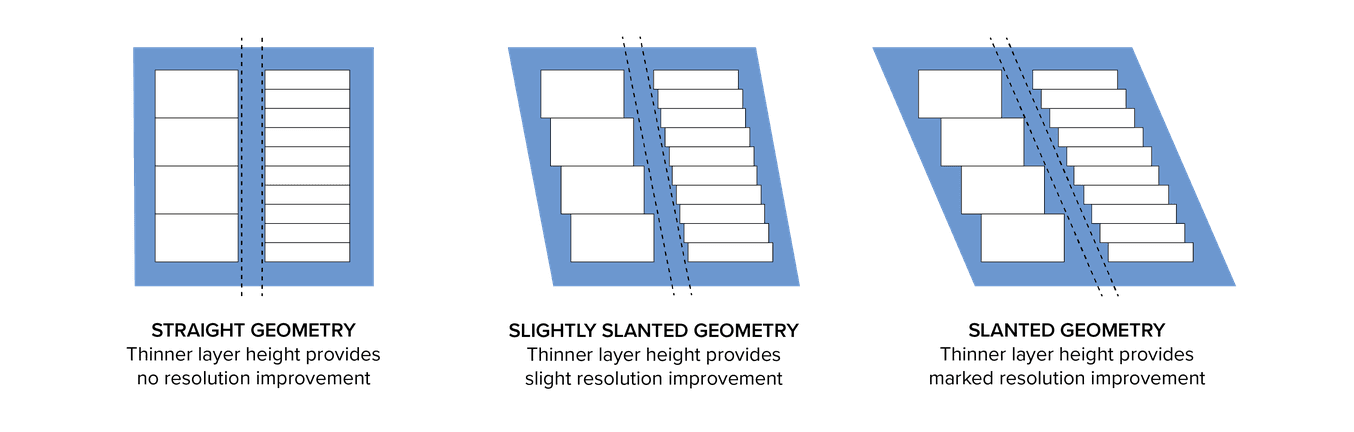
Adaptive Layer Thickness determines which areas of the print require thinner layer heights for high resolution and which areas of the print can use thicker layer heights to decrease printing times. For example, the nozzle below prints with thinner layers in the bottom section for higher detail in the threading and knurling, and thicker layers in the top section where the nozzle is smooth and uniform.
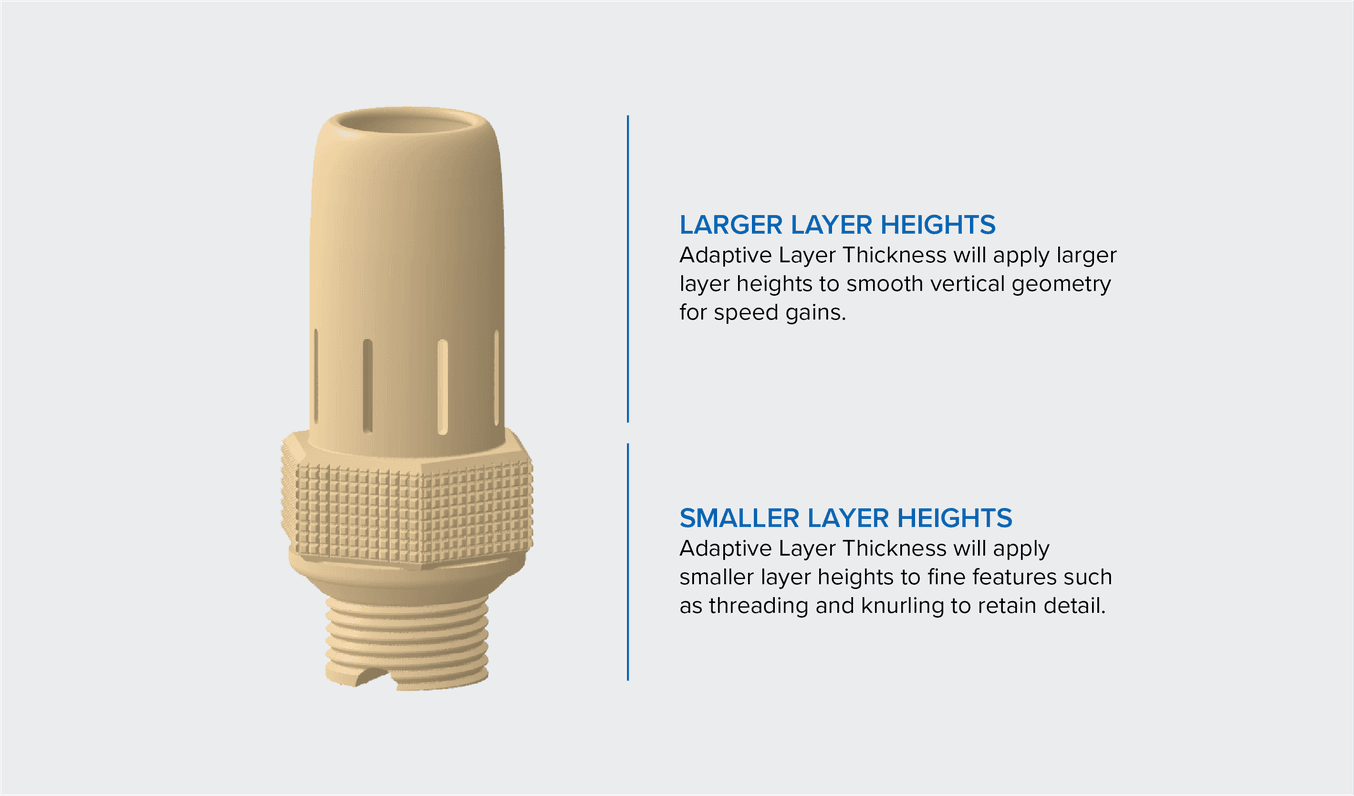
Learn how 3D printer resolution affects your prints and how it differs between SLA, FDM, and DLP printers.
When to Use Adaptive Layer Thickness
This feature helps create detailed prototypes and high impact concept models. However, it's still a new feature and there are some applications better suited to choosing constant layer thickness throughout your print.
Adaptive Layer Thickness works best for:
- Parts with gradual changes in slope and/or organic curves
- Models with concentrated detail in some areas and little to no detail in other areas
- Creating prototypes with higher fidelity
Adaptive Layer Thickness should not be used for:
- Parts that require high accuracy. Adaptive Layer Thickness is still in beta and is not yet validated for accuracy
- Parts that require precise detail throughout the entire print (e.g. fine jewelry)
- Printing different models on the same build platform. Adaptive Layer Thickness will not work effectively since the feature is intended to generate the optimal layer settings for a specific model
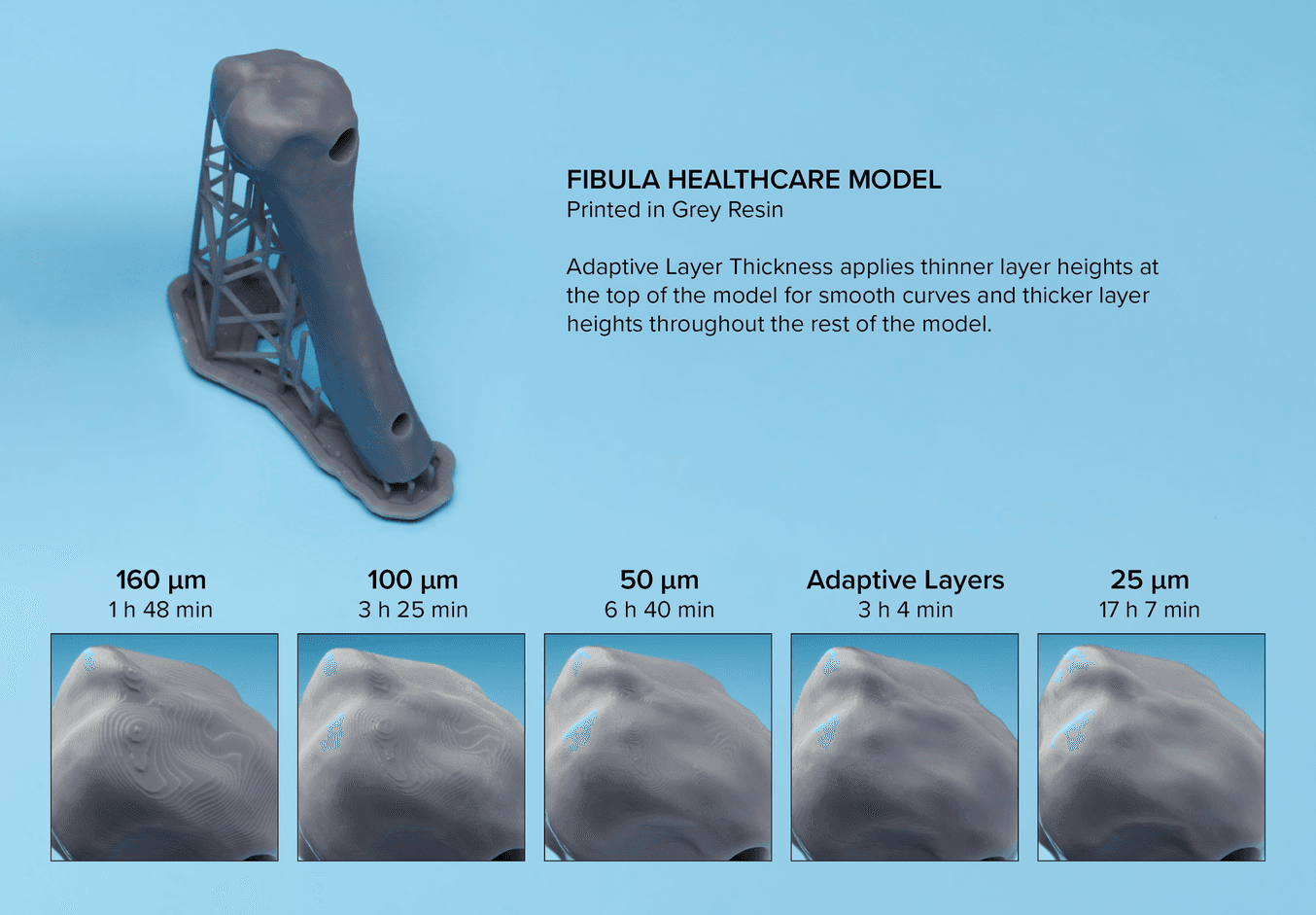
Just looking for fast print speed? Draft Resin prints 4x Faster than Standard Resins.
Orienting Parts for Adaptive Layer Thickness
To optimize the efficiency of this feature, orient parts in preform to increase uniform vertical geometry and concentrate fine details in the vertical direction. The former allows for larger layer heights while the latter minimizes the number of thinner layers printed.
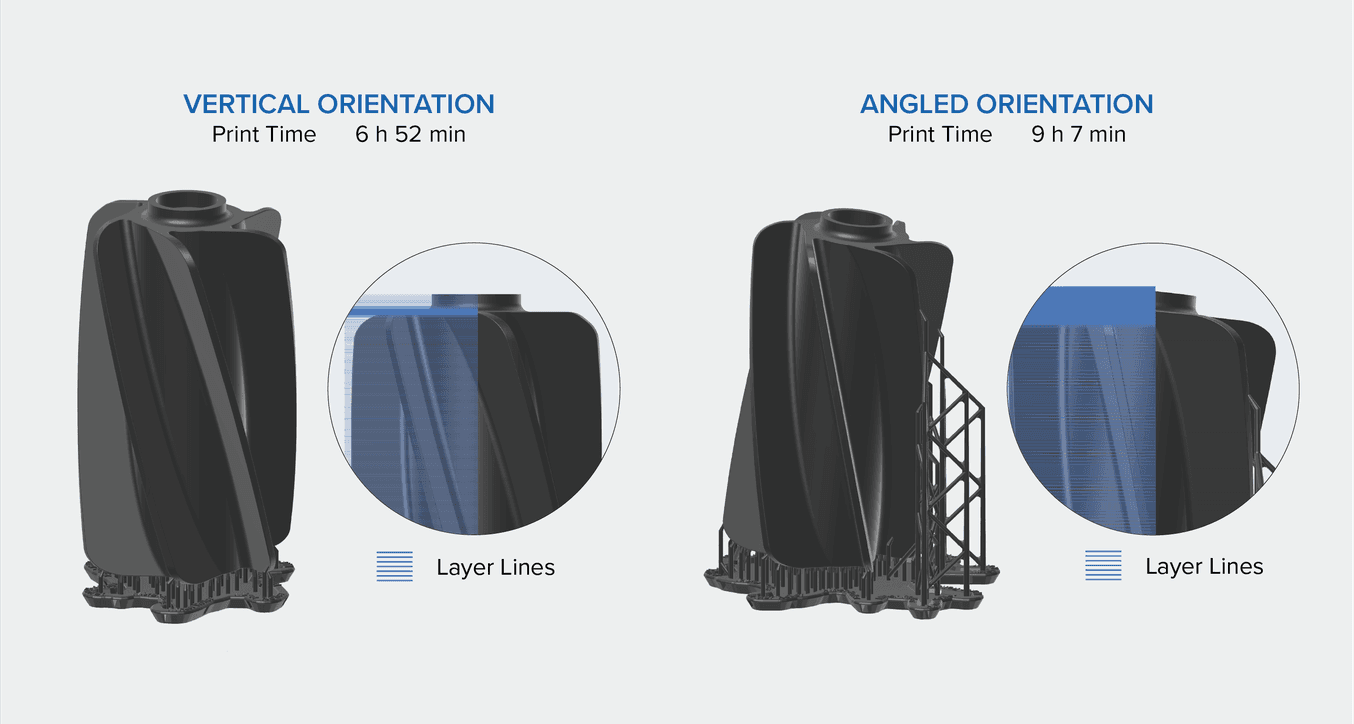
In the example above, the roller prints up to 2 hours faster when positioned perpendicular to the build platform rather than at an angle. Using Black Resin with the roller oriented vertically, Adaptive Layer Thickness assigns a layer thickness of 100 microns for the majority of the print, using thinner layers sparingly at the top and bottom of the roller. In contrast, ALT uses thinner layers for a larger portion of the print when the roller is oriented as an angle because the fine features are spread out in the z direction.
Learn More
At Formlabs, we’re constantly innovating to expand the capabilities of 3D printing. To watch a presentation about our new software updates from the Formlabs User Summit, click here.