How Figure Engineering Developed an Advanced SLA Material for the Department of Defense
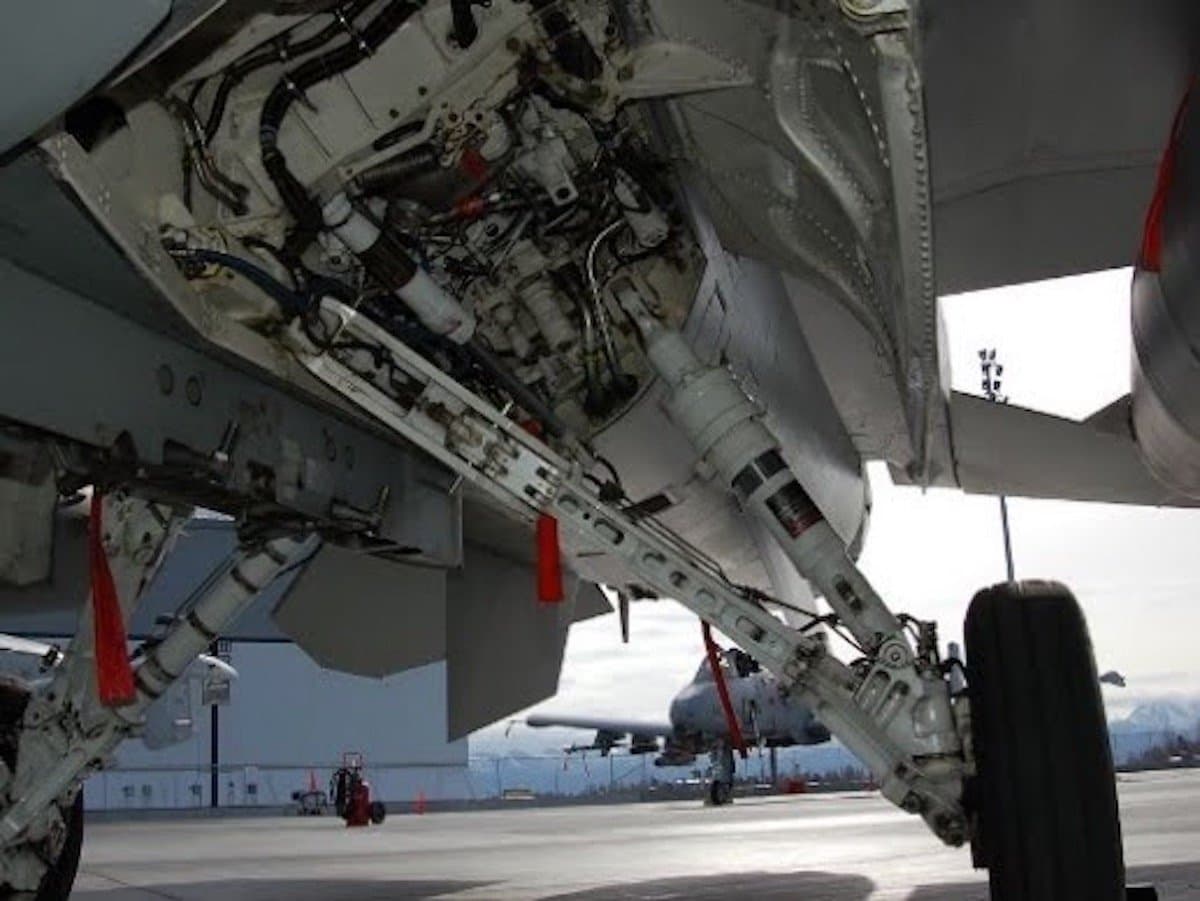
For every one hour of flight time on a jet operated by the United States Department of Defense (DoD), there are about 12 hours of maintenance completed. Though maintenance, repair, and overhaul (MRO) operations are necessary to ensure that each aircraft is operating safely and at the highest possible level of performance, they are often lengthened by the manual nature and traditional processes employed.
The Department of Defense is always searching for ways to improve these operations and make the workflow more efficient — Figure Engineering, through utilizing Formlabs’ new open ecosystem, has developed an innovative and affordable solution to do so.
Figure Engineering has leveraged the speed of Formlabs’ Form 4 stereolithography (SLA) 3D printer to develop a new material made specifically for masking and tooling used in the electroplating process. Print Settings Editor and Open Material Mode have made it possible for Figure Engineering’s co-founder Jonathon McDaniels and his team to tune their material development process and find a new solution for a multi-million dollar problem.
Dirty, Dull, Dangerous: Primed for an Advanced Solution
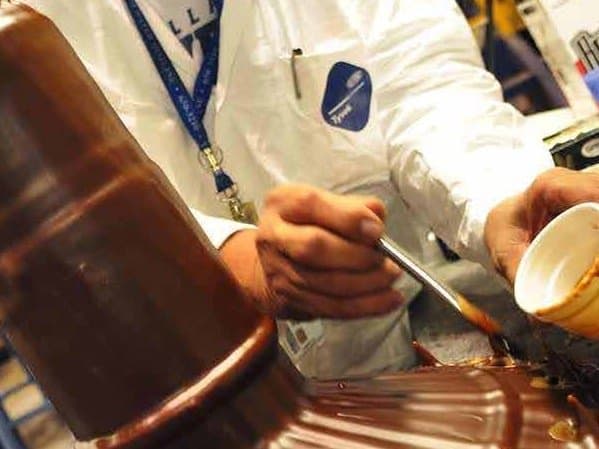
Hand painting lacquers for masking parts that will be electroplated can be dangerous if the materials used are toxic, and when operators reach their exposure limits, the whole project has to halt, potentially grounding aircraft for longer.
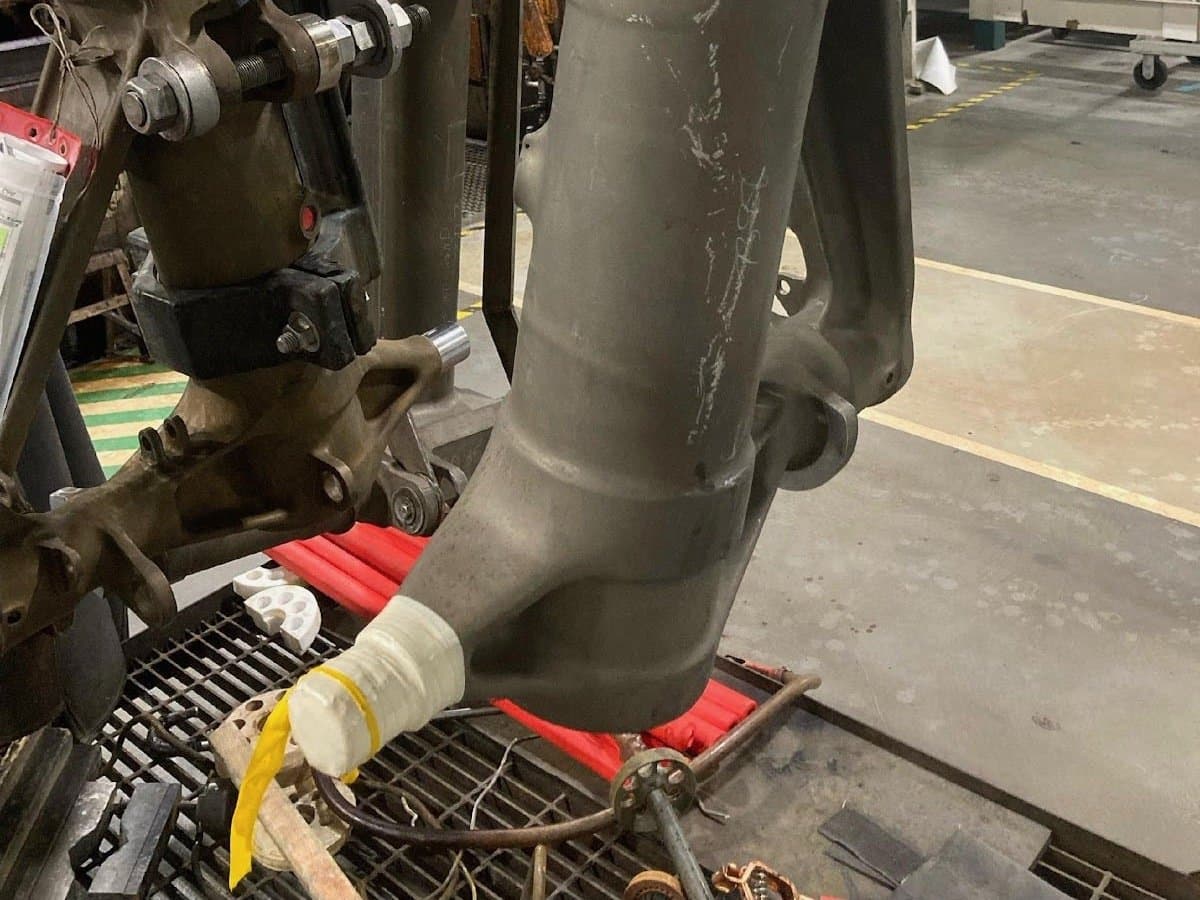
Applying tape by hand to mask certain areas during the electroplating process is time-consuming and labor-intensive, and must be repeated for each part, leading to excessive labor costs.
Figure Engineering develops advanced manufacturing and sustainment solutions, primarily as a contractor for the different branches of the DoD, but also for private enterprises. In the case of aircraft operated by the United States Air Force, Navy, and Army as well as commercial airline operators, Figure Engineering was called in to target areas that get overlooked in the maintenance process: abrasive blasting, painting, plating, and coating.
These operations are categorized informally as the ‘three D’s,’ meaning they’re dirty, dull, and dangerous. That designation means they’re less visible and understood than processes like engine replacement or new wing-tip innovations, but they can be just as important to overall aircraft performance. If the processes take too long because of inefficient workflows, it can impact military readiness, add substantial operating costs, and, because they often involve toxic chemicals, can affect the safety of the MRO operators.
Figure Engineering specializes in finding innovative solutions to make these processes more safe and efficient, and has been working with depot shops in the US Air Force for years. “The best solutions require a lot of collaboration with the owner of the process. They’re going to know their challenges best. For the electroplating process, they were saying, ‘I can’t get this plane out fast enough, and we are generating a lot of waste,” says McDaniels.
The Problem: The Aircraft Electroplating Workflow
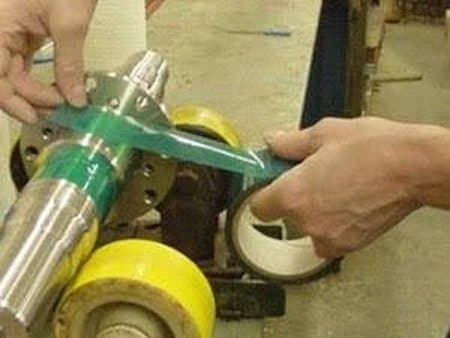
Applying tape by hand.
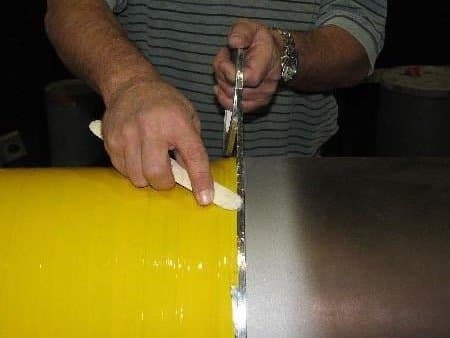
Trimming tape by hand.

Masked parts are submerged into the electroplating bath.
One of the most difficult and time-consuming aircraft MRO processes is electroplating large landing gear components. The workflow includes harsh, extremely aggressive chemical baths and hours of laborious manual work masking areas that won’t be plated by hand-painting a removable lacquer or taping off sections.
“The amount of hands-on work that is necessary to get the coating where you want it to go, and away from where you don’t want it to go is labor intensive, tedious, and expensive. The repair depots wanted a way to reduce that hands-on time, and instead develop masks that you could clamp or bolt on,” says McDaniels.
However, when Figure Engineering began to design and prototype masks for electroplating, they ran into a complex set of problems. “What we found when we did the initial studies, there was nothing that could withstand the rigors of the electroplating process. The material needed to have a high chemical resistance and be very tough — they’re dropped all the time or hit with hammers, so they need to be quite impact resistant,” says McDaniels.
Beyond material, choosing the right printing hardware was also a challenge. “Initially, everything was on the table. We needed to find a printer that would be easy to use and reliable, as well as a known name so we could get widespread support from the different depots,” says McDaniels.
After trying several parts from fused deposition modeling (FDM) and selective laser sintering (SLS) 3D printers, the team realized they needed completely dense, non-porous parts. The chemicals used in the electroplating process were able to seep into the FDM and SLS 3D printed parts, and when they were removed from the bath, they continued to leak the toxic chemicals from their surfaces. Resin printing was the answer, and though Figure Engineering tried multiple 3D printers, one stood out from the rest.
“It became pretty obvious early on that Formlabs was the company I wanted to work with. The lower cost for the higher quality equipment, the fact that the printers are highly reliable, and the fact that it’s a very well-known name made it the best choice.”
Jonathon McDaniels, Co-founder at Figure Engineering
McDaniels started with Form 3+, tweaking print settings and iterating a custom formulation with Open Material Mode. When Form 4 came out, the iterative process got supercharged, and development for their custom resin formulation sped up.
“When Form 4 came out, a lot of the problems we had went away overnight. Form 4 was so much of a game changer as far as the ability to print these really difficult-to-print materials. We’re pushing the boundaries of what’s possible in polymer additive manufacturing to get these materials to stand up to the plating process,” says McDaniels.
Developing Unique Materials With Formlabs' Open Ecosystem
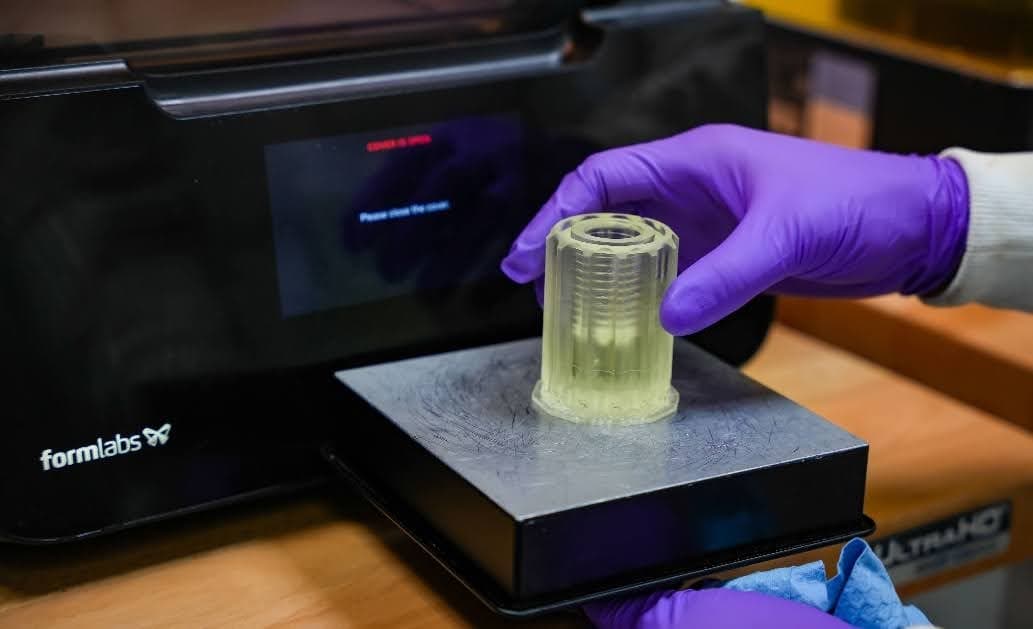
Form 4 gave Figure Engineering the boost they needed — tripling the number of iterations they could try each day gave them faster feedback and allowed them to try more print parameters in a shorter timeframe to find the perfect settings.
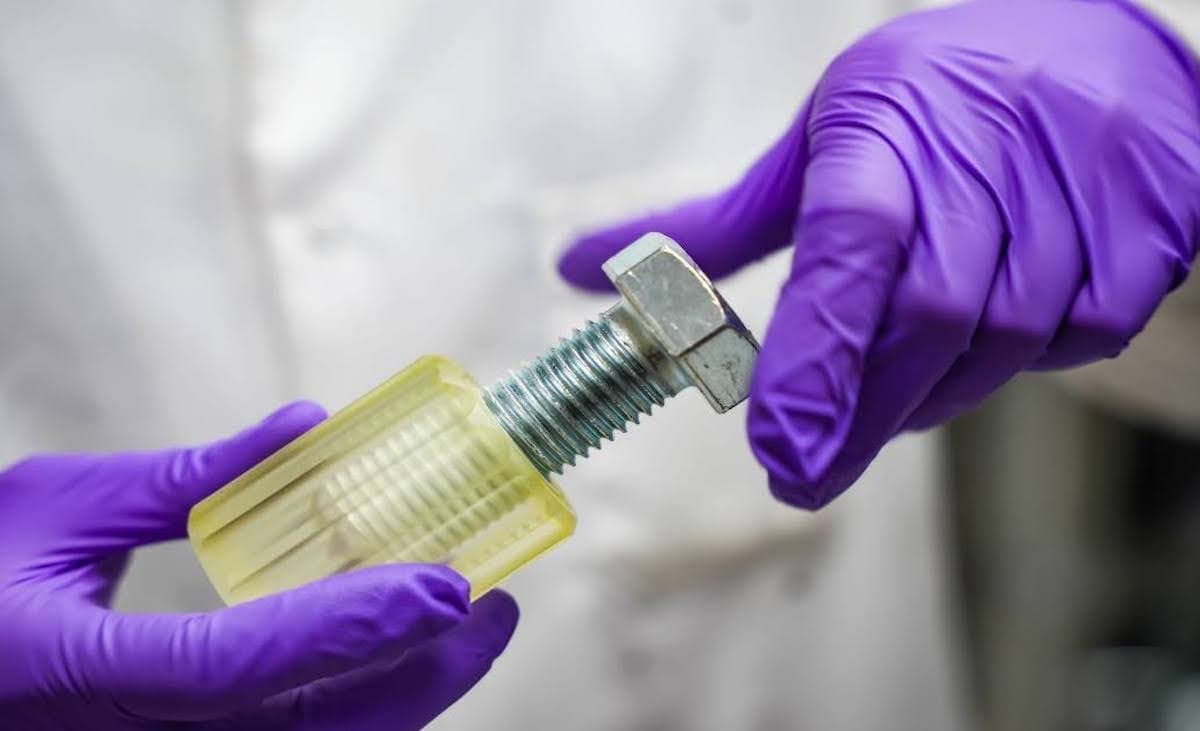
Figure Engineering's custom-developed material enables the creation of highly chemical-resistant, strong, and reusable masking tools, like this tool that can screw directly onto a large bolt that requires electroplating.
The fast print speed on Form 4 let the Figure Engineering team do more than double the number of tests they were able to before, but it was the access to printer settings that made creating a new, fully functional, and technically advanced material possible.
“We wouldn’t have been able to get off the ground without Open Material Mode and editing print settings,” says McDaniels. Developing new materials and tuning printer settings requires an understanding of the effect each setting has on the outcome. McDaniels’ background in chemical engineering proved helpful as he worked with Formlabs’ team to fine-tune certain processes. “Editing the print settings was pretty straightforward. Understanding how the printer works, how resin fills in and supports the first layer, and things like that — there was guidance on those things. You get your numbers to come into the right range, and then things start printing the way they should. Once you understand that, the use of settings becomes easy,” says McDaniels.
Reducing Labor and Costs
Developing a resin for electroplating masking parts required unique material characteristics, ones that weren’t available on any existing system. Formlabs offered a platform for Figure Engineering to use as a base for their research — a fast, reliable 3D printer, access to print settings and software, and an involved team that was ready to support and collaborate with McDaniels and the team.
The custom formulation developed by Figure Engineering has been rolled out to one US Air Force MRO depot already. Once the masking parts are designed and printed, their implementation in the masking process drastically reduces the time it takes to prepare aircraft components for electroplating. “The whole goal is to get operators to spend less hands-on time in this process, and away from the chemical baths as much as possible,” says McDaniels.
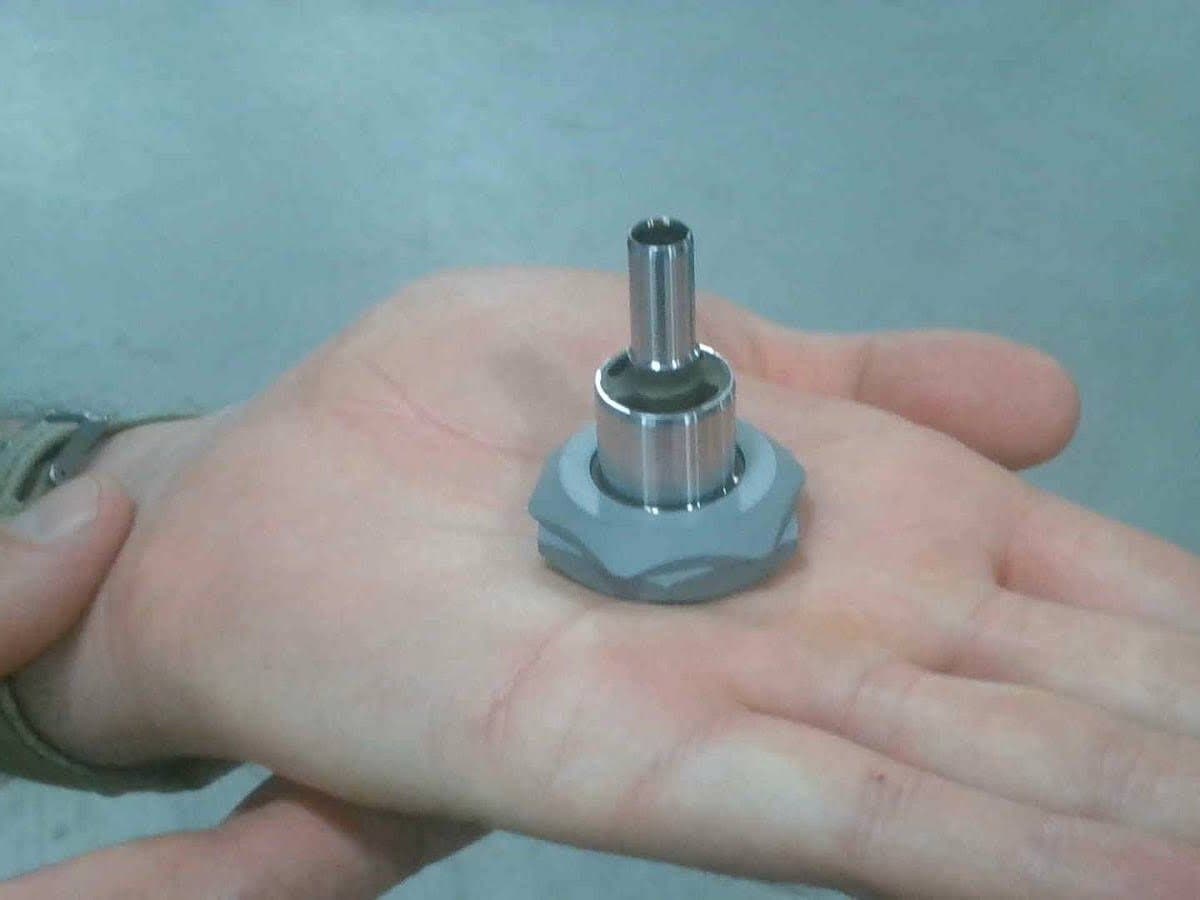
Creating a mask by hand for this metal bolt cost about $250 each, while printing them with screw threading features inside in Resist™ cost just 5$ each.
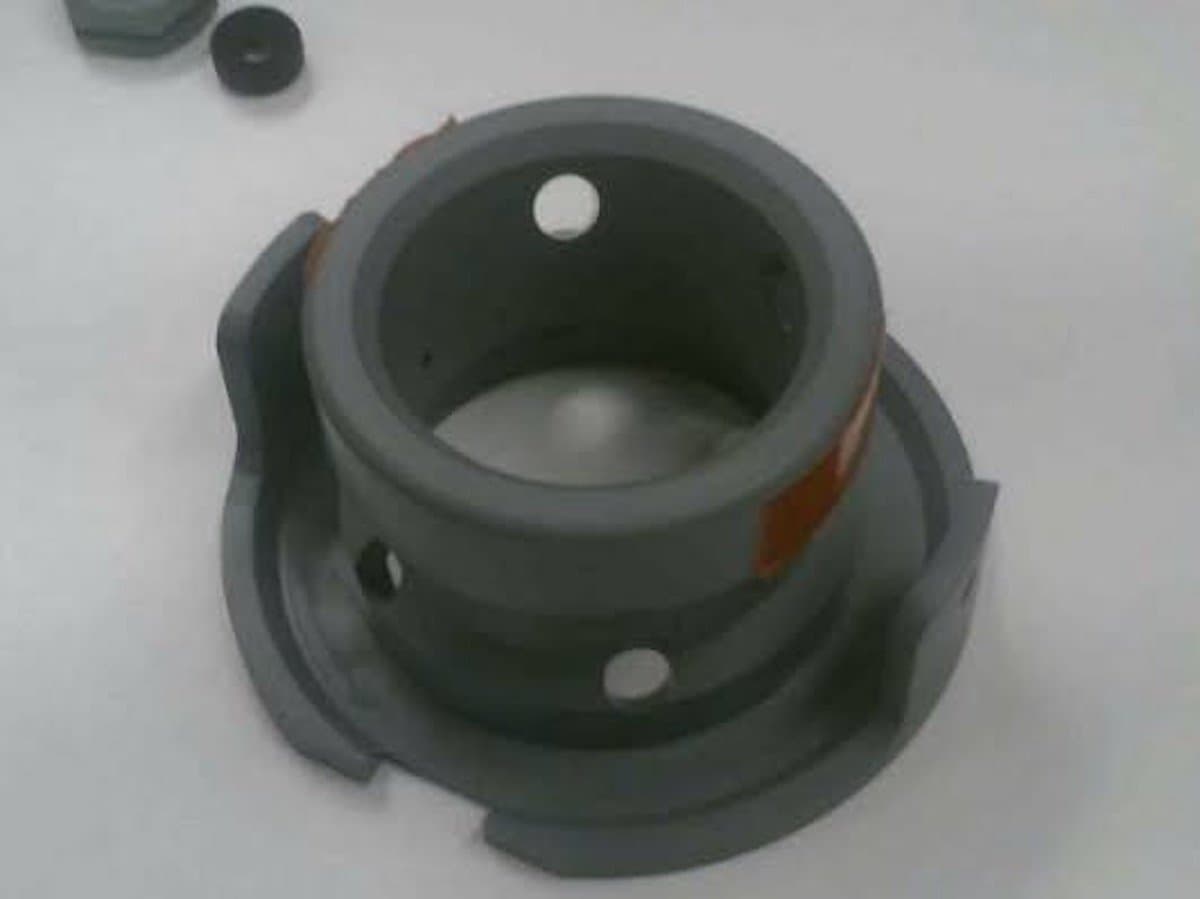
This large part costs about $550 of materials and labor during application, while the traditional hand-masking process costs between $2000 and $4000.
Each 3D printed part can be reused for up to 20 electroplating cycles; compared to lacquers and tapes, which are single-use — plating shops go through millions of dollars of lacquer and tape annually. Though design, printing, and post-processing for 3D printing can take time, that design can be shared between departments, depots, or even branches of the armed forces, so that any aircraft with a component that needs to be electroplated could potentially use the same design and print it on-demand. In addition, 3D printed masks can be batch produced, and stored until needed. Masking is a major bottleneck in the electroplating process, and switching to 3D printed masks eliminates that bottleneck.
Sky’s the Limit
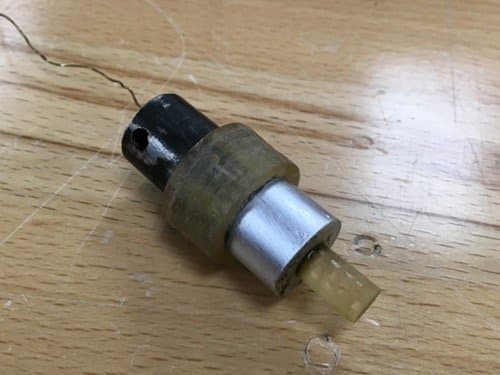
Phase 1: Feasibility
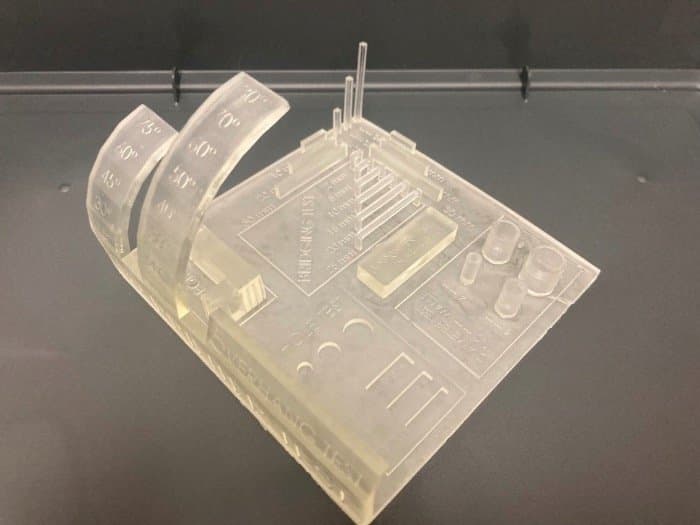
Phase 2: Development
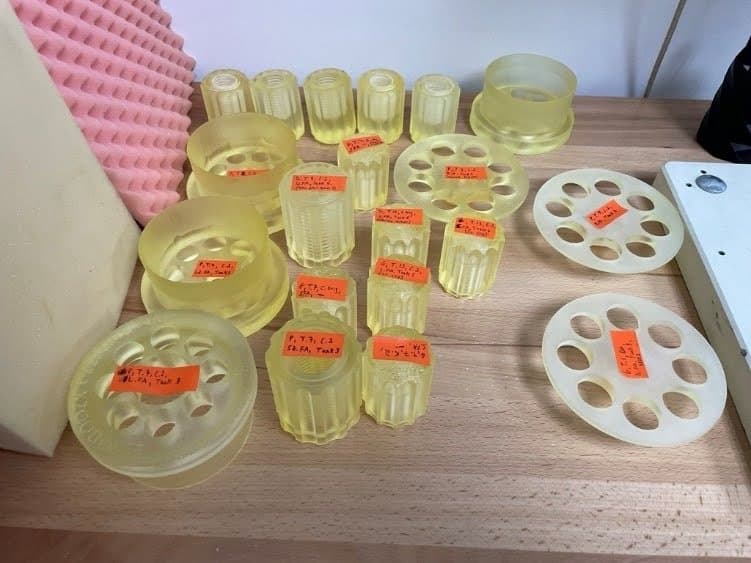
Phase 3: First article demonstration
The partnership between Figure Engineering and Formlabs has demonstrated that the solutions to big, complex problems can be found fastest through collaboration. Figure Engineering’s chemical engineering expertise and deep understanding of the problem at hand were key, but they needed more than just a 3D printer to arrive at the right solution — they needed access and support within a powerful 3D printing platform.
Formlabs' open ecosystem and Open Material Mode have enabled McDaniels and his team to create an entirely new material and workflow for the DoD, potentially saving them millions of dollars in materials and labor and improving safety for technicians in MRO depots across the country. “Our work wouldn’t have been possible with Open Material Mode,” says McDaniels. “It’s actually changed the way we think about new projects moving forward. This will not be the last 3D printing material we make. We’re working with other DoD departments and even commercial, private airlines. Open Material Mode is our path to getting those opportunities.”
Learn more about Formlabs' open ecosystem or request a free sample part to see Form 4’s quality for yourself.