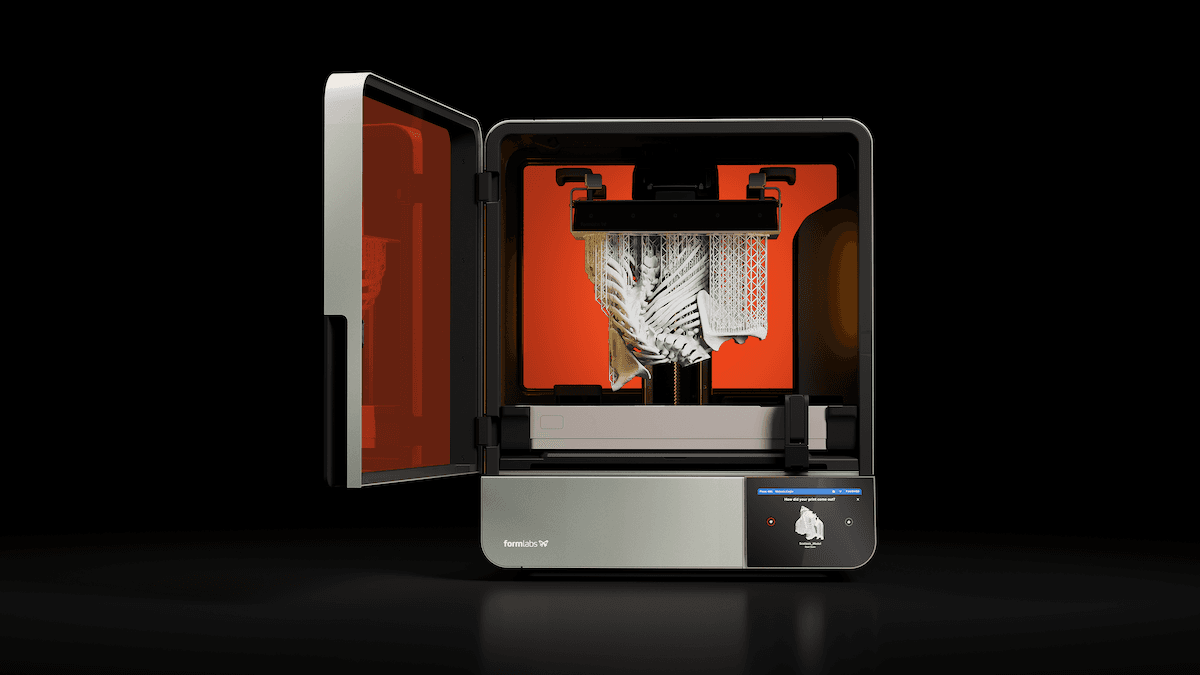
There are many ways to distinguish between 3D printer manufacturers — resin, powder, or filament; hobbyist or professional; desktop, benchtop, or industrial — but for many 3D printing customers, one of the biggest differentiators is: open or closed?
Since our beginnings in 2011, Formlabs has strived to create a 3D printing solution — hardware, software, and versatile materials — that delivers exceptional parts consistently while being easy to use, so that anyone can turn their ideas into reality. We’ve created a platform that works every time you need it to, but we know that there are applications and challenges for which we haven’t created specific workflows. That’s why we’re opening the Formlabs ecosystem, so that you can use our printers, software, and materials as a launchpad to solve your unique challenges.
Formlabs' open ecosystem encompasses three powerful tools that will enable our users to solve complex problems on their own terms, while still accessing the advanced, reliable, and highly-engineered Form Series SLA and Fuse Series SLS printers:
- Open Material Mode: Available for a one-time fee per printer, Open Material Mode enables expert users to use any third-party material on Form 3/+, Form 3B/+, Form 4, Form 4B, Form 4L, Form 4BL, Fuse 1, and Fuse 1+ 30W.
- PreForm Print Settings Editor: Free access through PreForm for any user who wishes to adjust print settings and tailor print performance for both Formlabs’ proprietary and Certified Materials on Form 3/+, Form 3B/+, Form 4, Form 4B, Form 4L, Form 4BL, Fuse 1, and Fuse 1+ 30W.
- Formlabs Certified Materials: Enables a curated selection of certified best-in-class third-party materials with pre-tuned print settings for seamless use on Formlabs’ SLA and SLS printers.
Open Material Mode: Innovate Outside the Box
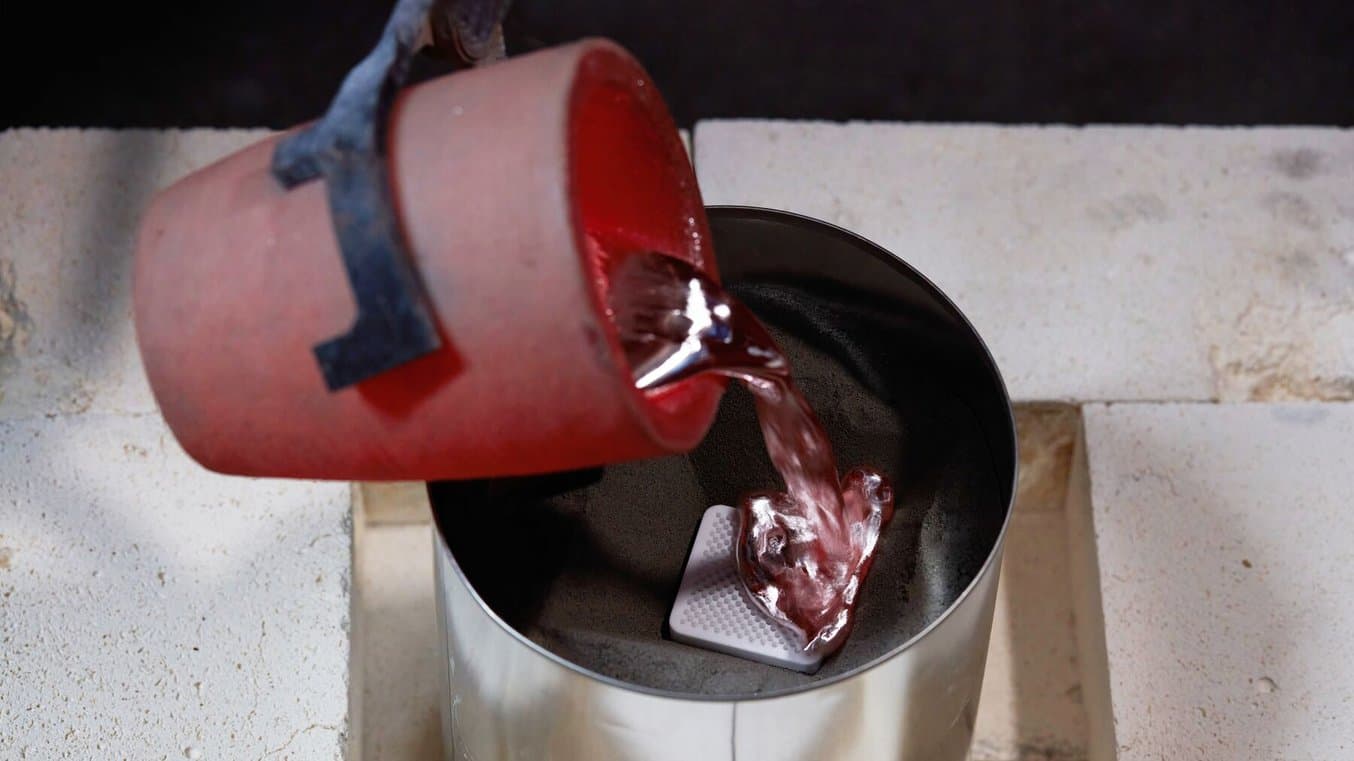
For specialized applications, Open Material Mode enables users to find the right material for their unique workflow, while still leveraging the reliability, ease-of-use, and consistent dimensional accuracy of Formlabs' SLA and SLS 3D printers. Before we released Alumina 4N Resin and enabled true technical ceramic 3D printing, many researchers were using a version of this feature for applications like metalwork, shown above.
Formlabs has prided ourselves on our best-in-class material engineering team, who have developed over 45 materials spanning a full range of applications and mechanical properties. But we know that the existing library of resins and powders doesn’t answer every question or solve every problem our customers could have.
Opening up our SLA and SLS ecosystems to third-party materials means that customers can take matters into their own hands. With Open Material Mode, customers can take any 405 nm resin or 1064 nm powder and create new workflows. Formlabs printers should be tools to get where you need to go, not a bottleneck to creativity and innovation. OMM opens up the doors for developing new, specialized materials that are purpose-built for your unique challenges. Leverage the proven reliability of our SLA or SLS printers so that you can focus on engineering new materials, without worrying about the hardware.
Open Material Mode is for our expert users to take their innovation to the next level, who know what they need and how to get there. These customers can purchase lifetime open access for a one-time fee per printer and, from there, continuously try new resins or powders. Our partnerships with customers like Figure Engineering have shown us that small changes in material properties can have groundbreaking effects on innovation.
Reducing Costs and Improving Safety for Aircraft MRO Operations
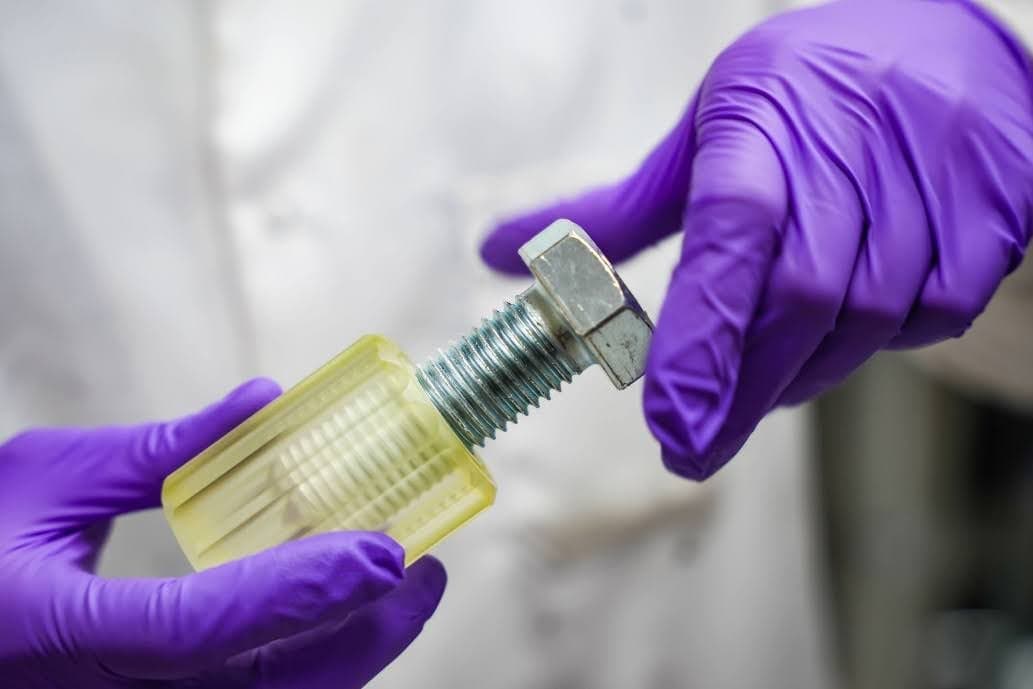
After successfully formulating their new resin, Resist™, Figure Engineering is working with the United States Air Force to create strong, chemically-resistant masking and tooling for the electroplating process of large metal landing gear components for aircraft.
One of the most difficult and time-consuming aircraft maintenance, repair, and overhaul (MRO) processes is electroplating large landing gear components. The workflow includes harsh, extremely abrasive chemical baths and hours of laborious manual work masking areas that won’t be plated by hand-painting a removable lacquer or taping off sections. Figure Engineering is a contractor brought in by the United States Department of Defense to find ways of making this process more efficient and safe.
However, when they began to design and prototype masks for electroplating, they ran into a complex set of problems. “What we found when we did the initial studies, there was nothing that could withstand the rigors of the electroplating process. The material needed to have a high chemical resistance and be very tough — they’re dropped all the time or hit with hammers, so they need to be quite impact resistant,” says Figure Engineering’s co-founder and technical lead Jonathon McDaniels.
After evaluating different 3D printing technologies, McDaniels and the team started working with Formlabs printers and Open Material Mode to experiment with new resins and develop their own formulation for a high-strength, chemically resistant material that had the durability to be used for multi-cycle masking parts.
“Editing the print settings was pretty straightforward. You get your numbers to come into the right range, and then things start printing the way they should. Once you understand that, the use of settings becomes easy,” says McDaniels.
After successfully formulating their new resin, Resist™ Figure Engineering is working with the United States Air Force to eventually deploy the 3D printing workflow at maintenance depots across the country.
“Our work wouldn’t have been possible without Open Material Mode. It’s actually changed the way we think about new projects moving forward. This will not be the last 3D printing material we make.”
Jonathon McDaniels, Co-founder at Figure Engineering
To learn more about how Figure Engineering developed their material, read the full story.
PreForm Print Settings Editor
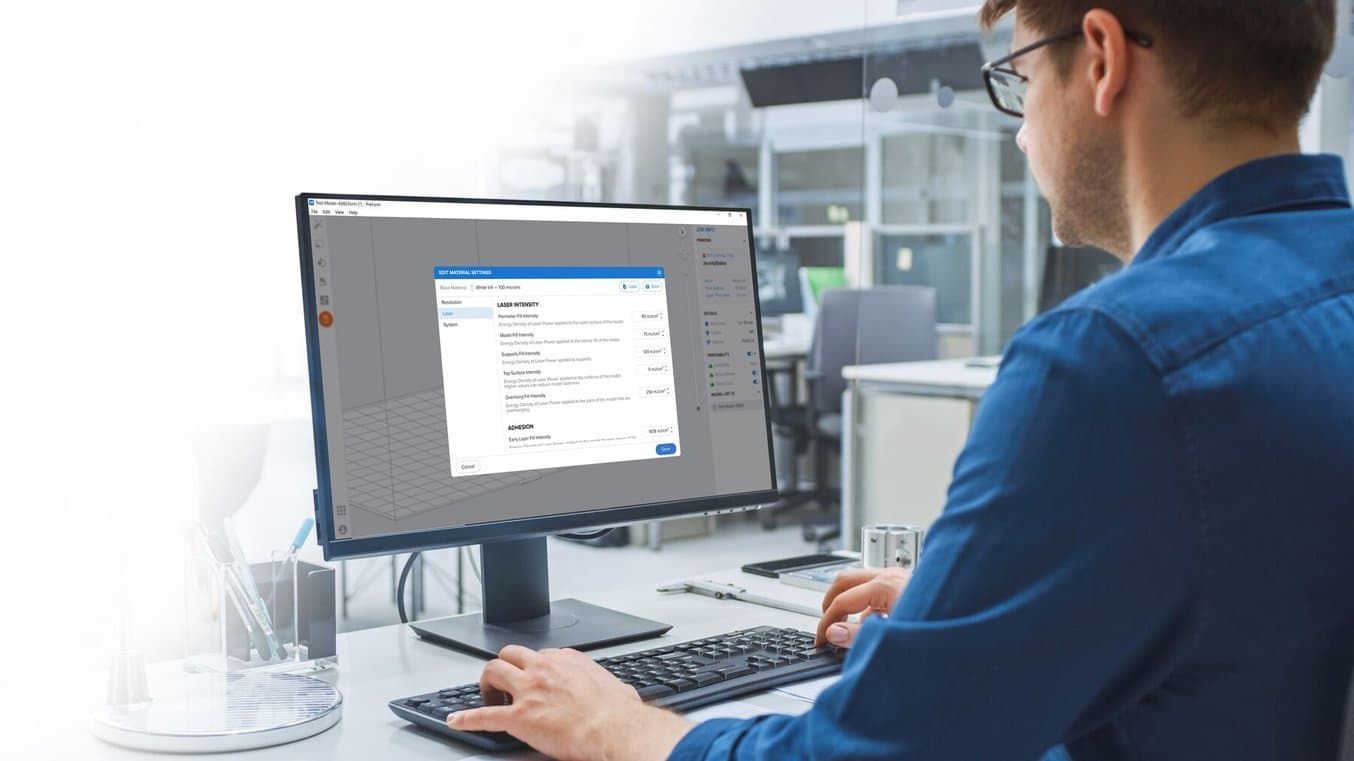
Print Settings Editor enables users to customize print parameters in PreForm, so that they can create their own workflows and perfect printing environments for unique, optimized results.
Formlabs SLA and SLS 3D printers are globally best-selling professional 3D printers for a reason — they deliver parts that solve problems reliably. Maybe that means delivering very accurate parts consistently, very strong parts overnight, or even highly detailed parts in just the right color.
We’ve spent years dialing in print parameters like resin tank wiper speed, layer height, exposure, heating, and more, but we know that we’ve been dialing them in to work for the majority and that there are fringe cases where something specific, if tweaked, could be a ‘eureka’ moment.
Print Settings Editor is ideal for customers who have been using our validated resins and powders and like the results, but have one small area where they know a quick fix could change everything. Print Settings Editor enables customers to make those tweaks, giving you the power to solve your unique problems while still leveraging the proven reliability, affordability, and accessibility of the Form Series or Fuse Series.
Putting Print Settings Editor Into Action
At Stryker, one of the largest medical device manufacturers in the world, a microfluidics part was giving engineers some issues — channels weren’t resolving in expected ways consistently enough for them to choose Form 4 as the primary tool. After working with our team, they diagnosed an easy fix and created a customized print setting solution to optimize the print process for small channels.
At another medical device manufacturer, Abbot, microbubbles in Clear Resin parts weren’t appropriate for the surface-level finish and transparency the team was shooting for. Another easy fix — resin tank wiper speed — could be adjusted slightly to eliminate any bubbles in the final part. With Print Settings Editor, the Abbot team could slow the wiper down just a bit, enough to adequately stir the resin and prevent settling while still avoiding the creation of microbubbles.
Why wouldn’t Formlabs make this setting permanent, given that microbubbles in a clear material are inherently undesirable? Though we’ve worked to try to eliminate them altogether, slowing down the wiper doesn’t work in every situation, every time, so we chose the path that works best for the majority. Abbot now has a tool that lets them customize their experience while still taking advantage of the qualities of Clear Resin and the reliability, speed, and accuracy of Form 4.
Formlabs Certified Materials: Leveraging Others’ Expertise
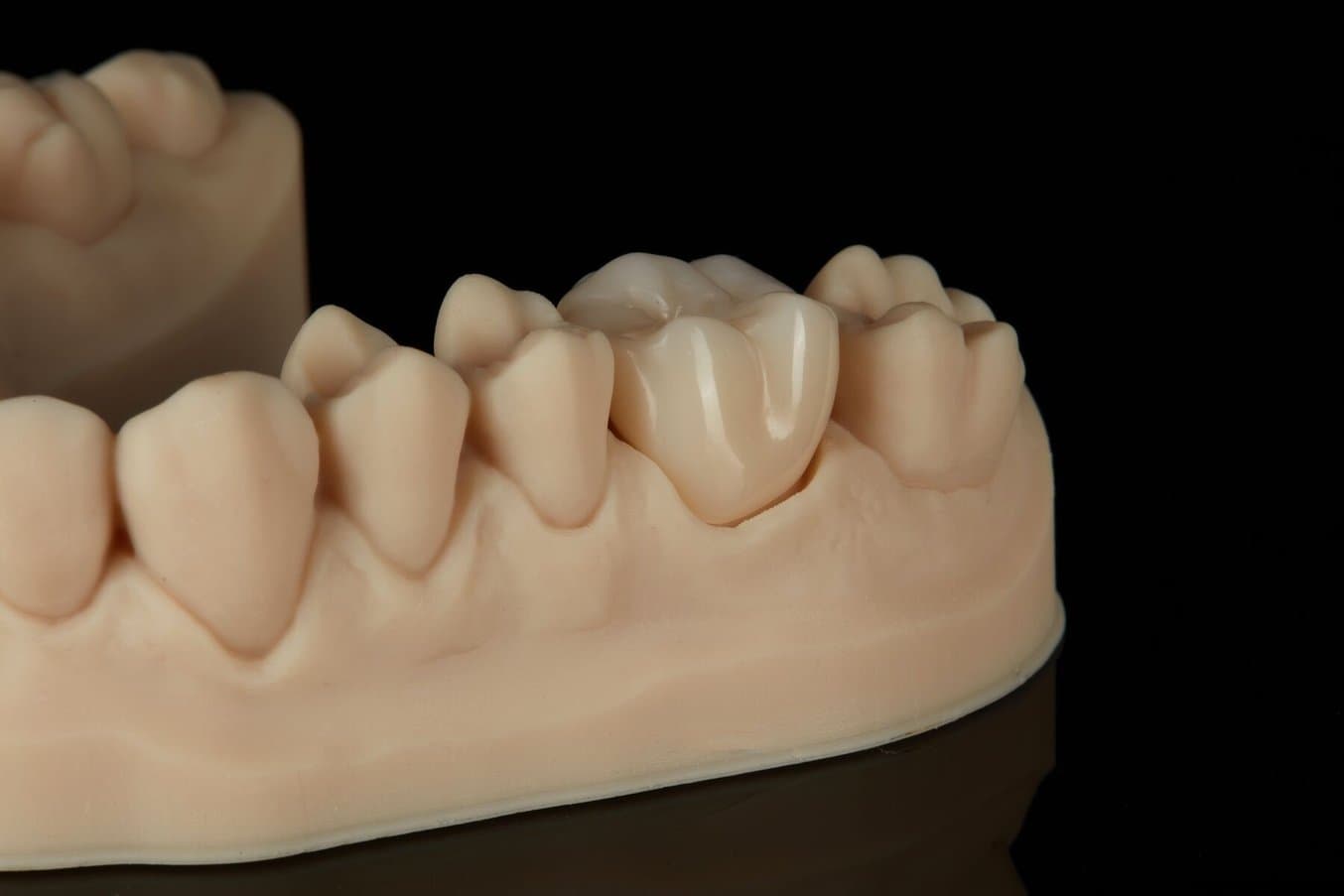
BEGO™ VarseoSmile® TriniQ® Resin is an example of a Formlabs Certified Material. BEGO's materials is best-in-class and has been rigorously tested on the Formlabs ecosystem for a smooth, efficient workflow. Combining the exceptional material engineering of BEGO and the power of Form 4B, the Certified Materials workflow delivers on all fronts.
Formlabs’ materials library has over 45 custom resins and powders that have been precisely engineered and exhaustively validated for specific applications. While we will always strive to continue increasing our material versatility, sometimes collaboration is the best, fastest way to reach a solution. With the addition of Certified Materials, our printers become a platform for other material manufacturers to leverage as they help customers reach their goals.
Using a Formlabs Certified Material with our ecosystem is ideal for customers in a specialized industry or application, such as medical device manufacturing, where certain material regulations and approvals are of paramount importance, and the current Formlabs’ material library offerings don’t meet the requirements. For permanent dental restorations, BEGO created an ideal solution in their dental material, which is now certified for use on Form 3B, Form 3B+, Form 3L, and Form 4.
Certified Materials have huge advantages, and with an open 3D printing ecosystem, you can get the best of both worlds — a highly specialized resin or powder as well as a powerful, best-in-class 3D printer.
Formlabs API and Integrations
Streamlining is the name of the game with an open ecosystem. As with Certified Materials, we want to make things easier for customers, so that they can spend more of their time dreaming up new ideas, and less time switching between systems, materials, or methods.
By opening up Formlabs’ API, we want to reach a place where the majority of customers are starting prints outside of PreForm. Customers and partners can build integrations in other applications and automate those workflows, so you can go from design to printed part effortlessly. Many great design programs are available, and creating integrations for all of them would be impossible, so we’re putting that power in the hands of our partners and developers, who can use our provided Software Development Kit (SDK) to access the API and create functionality. Reducing the time spent in the pre-print process is just one way we can help you bring your ideas into reality, faster.
Becoming More Than a Tool
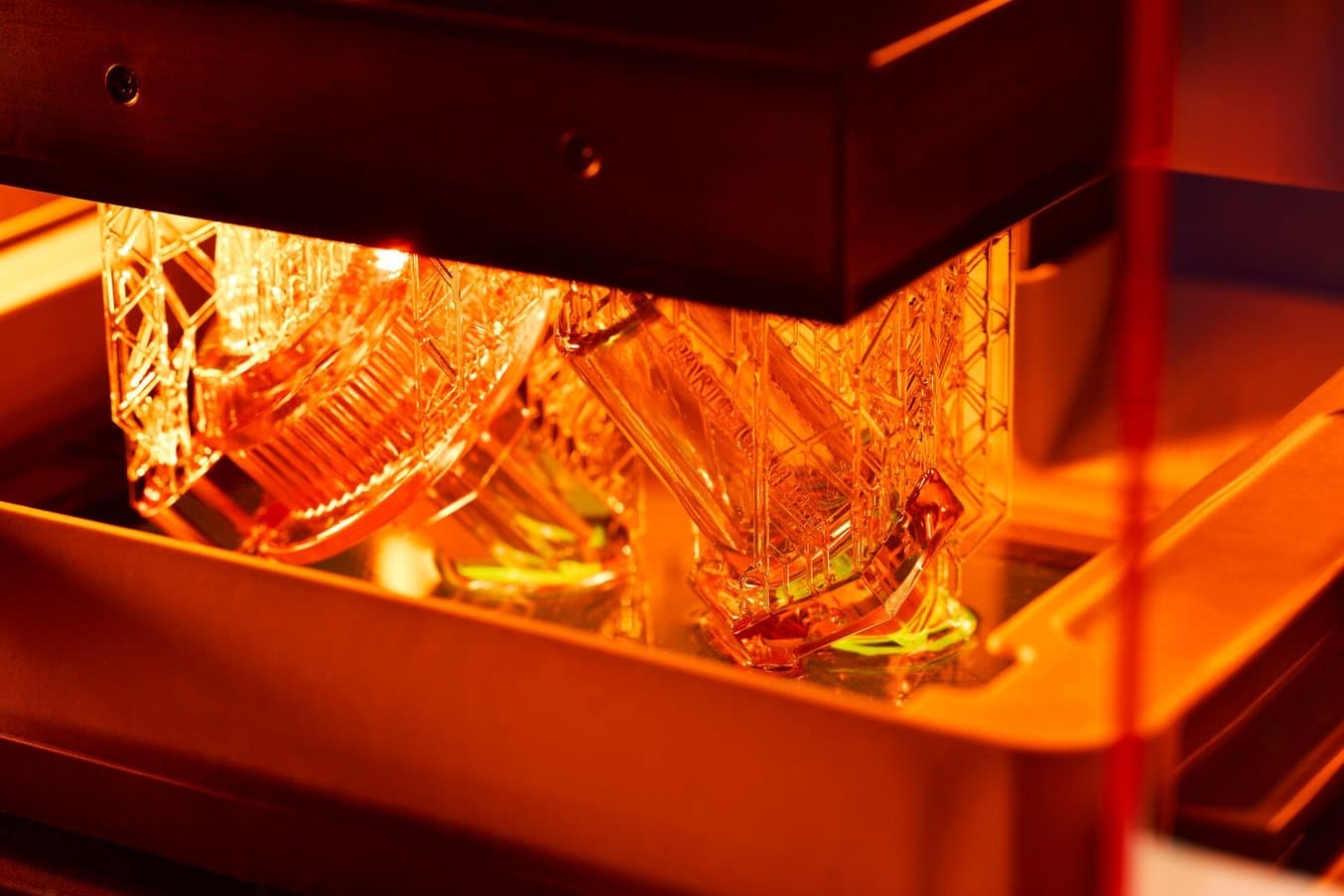
We've developed printers, software, and materials that have made 3D printing more powerful and accessible than ever, but for what comes next? We're so excited to see how the Formlabs community takes these proven SLA and SLS workflows and makes them their own.
Though Formlabs’ mission is to build tools that bring customers’ ideas to life, the opening of the Formlabs ecosystem represents a shift to becoming more than just manufacturers of tools — we’re creating a platform for innovation.
At its core, that platform contains powerful 3D printers like Form 4, Form 4L, and the Fuse 1+ 30W, but we know that true innovation happens when our customers add layers. By bringing in expert-made materials, hyper-charging a new resin development process, tweaking small settings that make a big difference, or making workflows more collaborative, Formlabs’ customers are taking the tools we’ve manufactured and making them so much more.
We can’t wait to see what’s in store with Formlabs' open ecosystem. To speak to an expert who can walk you through how to leverage these new features to optimize your workflow, contact our team.