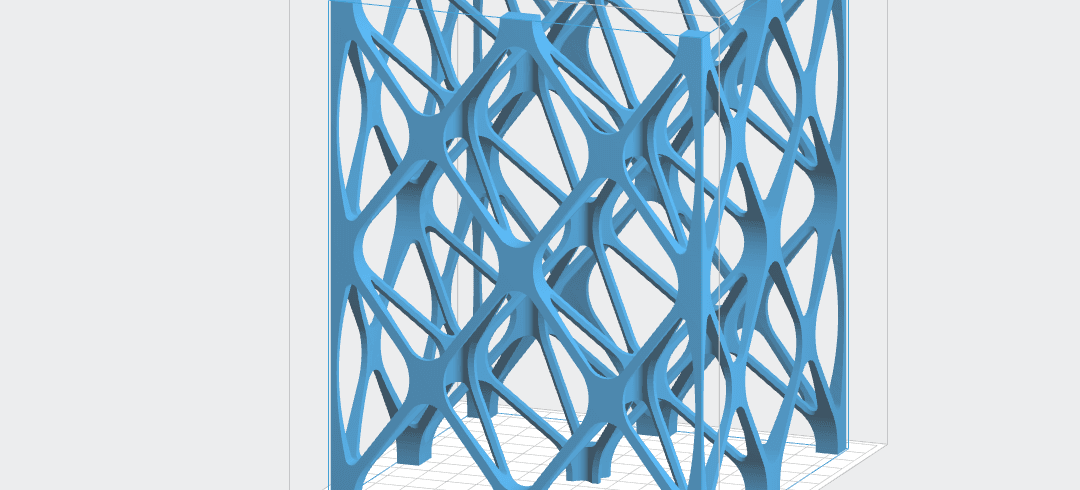
Part 1: The Right Way to Orient Parts
The technology behind your 3D printer makes a world of difference. If you’re used to working with Fused Deposition Modeling (FDM), then stereolithography (SLA) seems both alien and familiar. On paper it seems simple enough: an SLA 3D printer fires a laser beam at photoreactive resin, turning liquid into solid, building your part layer by layer. Yet there are key differences between these methods in every step from software to finishing. Thankfully, moving from FDM to SLA isn’t difficult — it just calls for a bit of knowledge before you take the leap.
Learning how to orient your part is the first step. Orienting SLA parts takes a few more considerations. In SLA machines, the resin system can cause compression and suction because of the hydrodynamic effects of pressing a solid into a pool of liquid. Finding the right orientation drastically improves the quality of your prints and reduces print failures.
Suction

Make sure that concave surfaces face toward the build platform.
On an FDM machine, the nozzle moves down, pushes out filament, and deposits each layer. With SLA, the laser hardens resin on the bottom of the build plate, which peels that layer from the previous one. When the peel process is complete and the build plate moves up for the wiper to move across (or, on some machines, when it lifts after the peel process), there is a slight suction effect. It’s similar to when you take a cupped dome (like a toilet plunger) and put it into a pool of liquid, then feel the resistance when you try and lift it. This suction effect in a resin system can cause several issues: the recently-formed layer could stick to the build plate, or the force of the pull could yank the print apart. Either issue will cause a print failure.
Thankfully, there are ways to orient your part to avoid this suction effect. Make sure that concave surfaces face toward the build platform. If you have a part with interior cavities, you should either add a hole for pressure relief or arrange the part so that cupped areas are minimized.
Drainage

Place drainage holes at the very lowest point (local minimum) of a hollow part.
Another SLA consideration is drainage. When printing with FDM, any support left inside the part (such as a closed sphere) is not an issue. However, with SLA, when you have a liquid resin and “trap” that resin inside your part, the resin inside will remain uncured in liquid form. The easiest way to avoid this issue is to add a drainage hole or two to the part. Orient it so that those holes are at the very lowest point (local minimum) of it. That way, when liquid resin gets enclosed, it has a place to go.
Peel Forces

Orient parts with flat surfaces at an angle toward the build platform.
On an FDM 3D printer, the head or platform moves to the next layer without creating peeling forces. With SLA, the wiper moves left and right between each layer, which can cause strain along the XY axis and lead to warping. Flat surfaces that are oriented parallel to the build platform are especially susceptible to peel forces. To counteract this issue, all you need to do is orient parts with flat surfaces at an angle toward the build platform.
SLA 3D printers take a few more considerations than FDM machines, but the results are dramatically different. FDM simply can’t produce the intricate details and smooth surfaces of SLA parts. With the right orientation, you can achieve professional SLA parts in no time.
Read our in-depth guide about FDM vs. SLA 3D printers to learn how they compare in terms of print quality, materials, applications, workflow, speed, costs, and more.