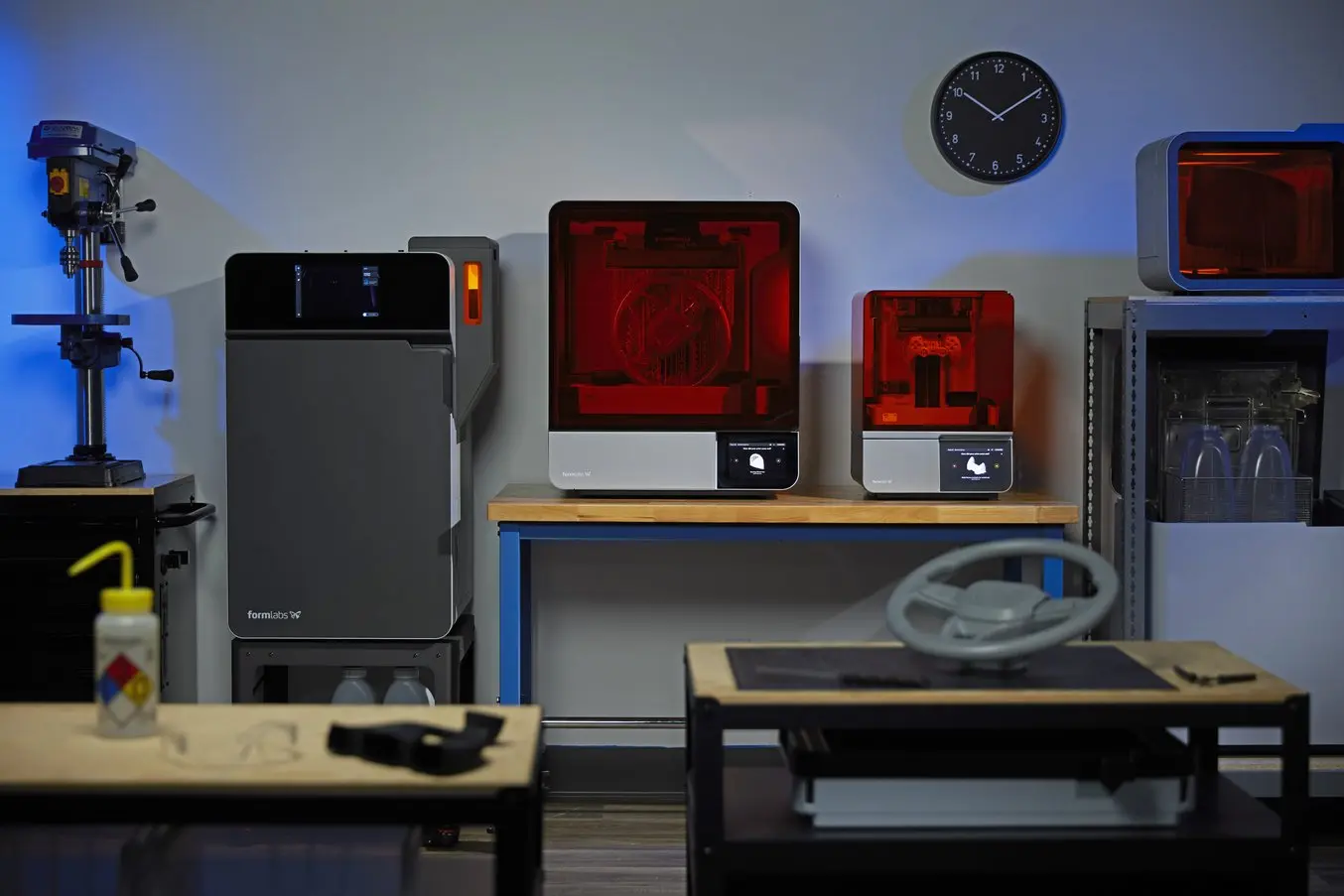
The 3D printing industry went through its most striking hype cycle during the early 2010s, when promoters claimed that the technology would find broad usage in consumer applications. Away from the frothy consumer 3D printing market, however, additive manufacturing technologies continued to advance rapidly.
Industrial 3D printing technologies have been rapidly maturing in many concrete ways, crossing critical thresholds in print quality, reliability, and cost structure. Recent advances in machinery, materials, and software have made 3D printing accessible to a wider range of businesses, enabling more and more companies to use tools previously limited to a few high-tech industries.
Today, industrial 3D printers accelerate innovation and support businesses in various industries including engineering, manufacturing, dentistry, healthcare, education, entertainment, jewelry, and audiology.
An industrial 3D printer can revolutionize a business, as well as lower production costs and lead times. Here’s how to pick one that best suits your company’s needs.
Industrial 3D Printing Processes
Industrial 3D printing is available to businesses for a variety of applications, from prototypes to production parts. These technologies include fused deposition modeling (FDM), stereolithography (SLA), selective laser sintering (SLS), material jetting, and metal 3D printing.
A common theme across many of these technologies is the recent appearance of highly capable, but more compact and accessible industrial 3D printers, which helped lower the initial investment costs from $100,000 - $200,000 to often below $10,000.
Fused Deposition Modeling (FDM)
FDM, also known as fused filament fabrication (FFF), is a printing method that builds parts by melting and extruding thermoplastic filament, which a printer nozzle deposits layer by layer in the build area.
FDM is the most widely used form of 3D printing at the consumer level, fueled by the emergence of hobbyist 3D printers. Industrial FDM 3D printers are, however, also popular with professionals.
-
Advantages of FDM Industrial 3D Printers
FDM works with an array of standard thermoplastics, such as ABS, PLA, and their various blends. This results in a low price of entry and materials. FDM best suits basic proof-of-concept models and the low-cost prototyping of simpler parts.
-
Disadvantages of FDM Industrial 3D Printers
FDM has the lowest resolution and accuracy when compared to other industrial 3D printing technologies for plastics such as SLA or SLS, which means that it is not the best option for printing complex designs or parts with intricate features. Higher-quality finishes require labor-intensive and lengthy chemical and mechanical polishing processes. Some industrial FDM 3D printers use soluble supports to mitigate some of these issues and offer a wider range of engineering thermoplastics, but they also come at a steep price. With large parts, FDM industrial 3D printers also tend to be slower than SLA or SLS.
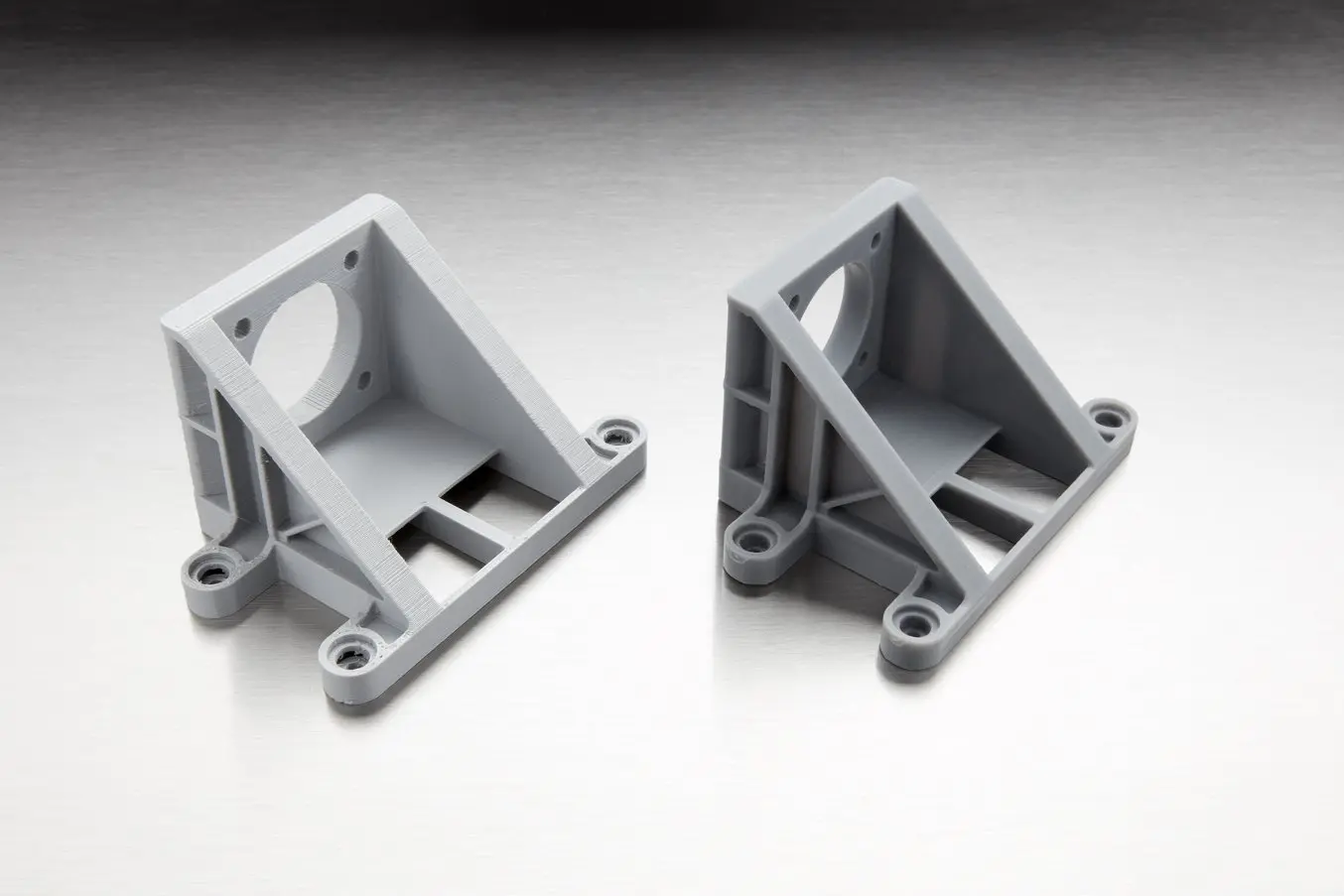
FDM printers (left) are ideal for simple shapes, but struggle with complex designs or parts with intricate features, compared to other processes like SLA printers (right).
Stereolithography (SLA)
SLA printers use a laser to cure liquid resin into hardened plastic in a process called photopolymerization. SLA is one of the most popular processes among professionals due to its high resolution, precision, and material versatility.
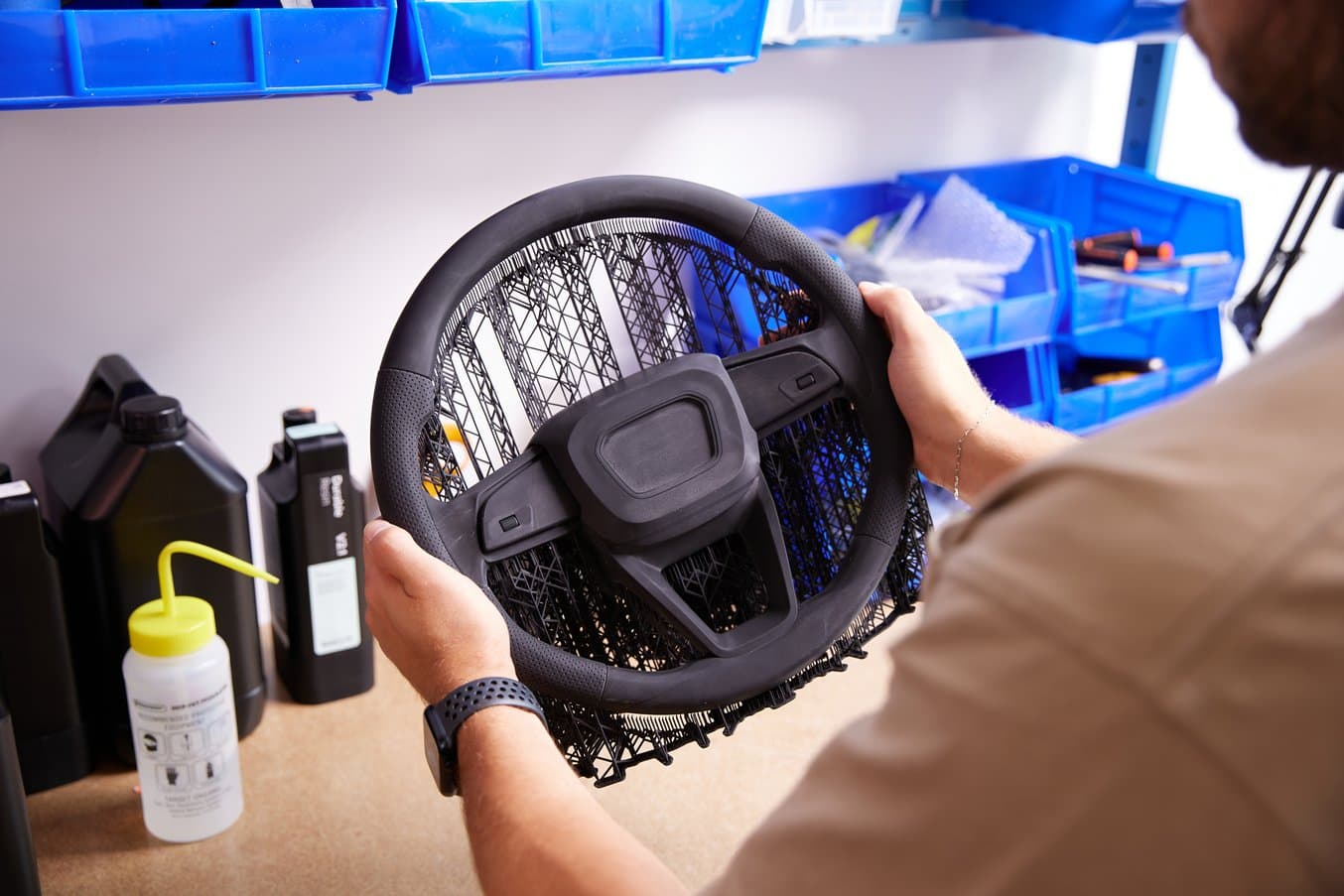
Form 4L, a large-format SLA 3D printer from Formlabs, is capable of 3D printing large prototypes the size of a steering wheel.
While SLA technology used to be available only in large, complex industrial 3D printers that cost more than $200,000, the process has become much more accessible. With the Formlabs Form 4 printer, businesses now have access to industrial-quality blazing fast SLA 3D printing for just $4,499. Large-format SLA with the Form 4L starts at just $9,999.
-
Advantages of SLA Industrial 3D Printers
SLA parts have the highest resolution and accuracy, the clearest details, and the smoothest surface finish of all plastic 3D printing technologies. The main benefit of SLA lies in its versatility; SLA resin formulations offer a wide range of optical, mechanical, and thermal properties to match those of standard, engineering, and industrial thermoplastics. MSLA 3D printers, like Formlabs' Form 4 and Form 4L are also the fastest options for 3D printing large parts, up to 10X faster than FDM.
SLA is a great option for highly detailed prototypes requiring tight tolerances and smooth surfaces, as well as molds, tooling, patterns, medical models, and functional parts. It also offers the material with the highest heat deflection temperature of 238 °C @ 0.45 MPa — which makes it an ideal choice for certain engineering and manufacturing applications — as well as the widest selection of biocompatible materials for dental and medical applications.
-
Disadvantages of SLA Industrial 3D Printers
SLA’s wide versatility comes with a slightly higher price tag than FDM, but it is still more affordable than all other industrial 3D printing processes. SLA resin parts also require post-processing after printing, which includes washing the parts and post-curing.
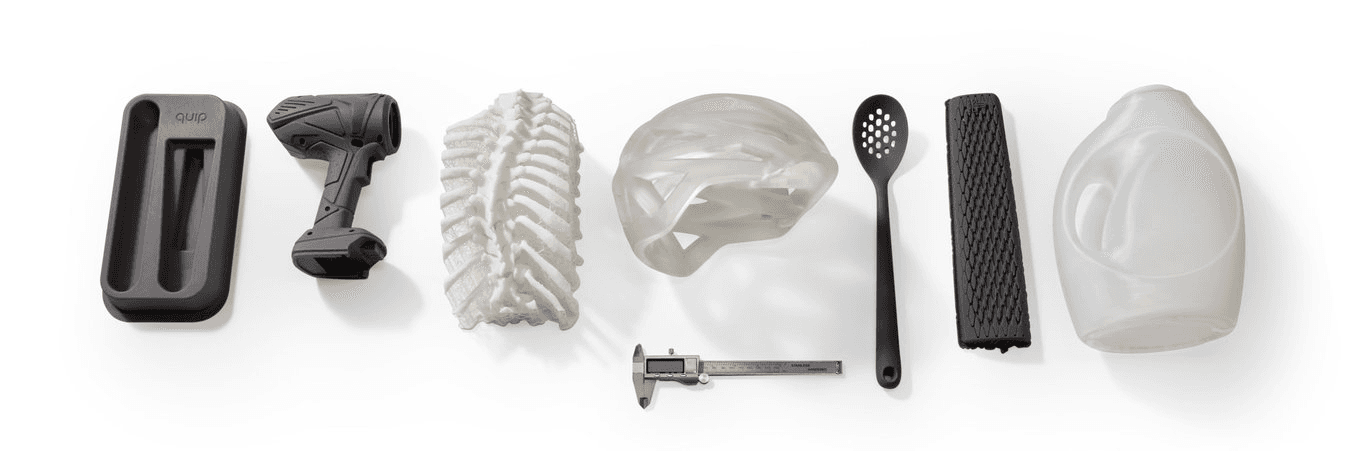
Some examples of large 3D printed parts manufactured on the Form 4L.
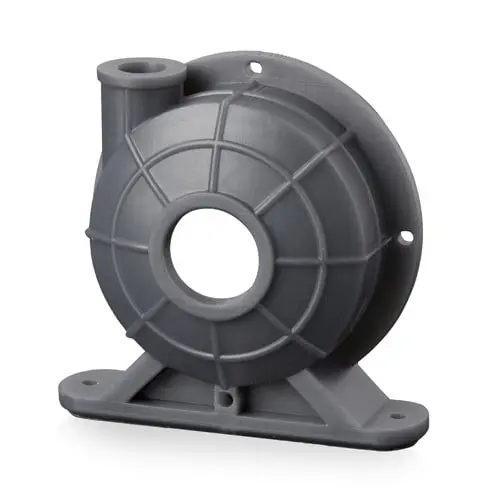
Request a Free Sample Part
See and feel Formlabs quality firsthand. We’ll ship a free sample part to your office.
Selective Laser Sintering (SLS)
SLS printers use a high-powered laser to fuse small particles of polymer powder. The unfused powder supports the part during printing and eliminates the need for dedicated support structures, making SLS a particularly effective choice for complex mechanical parts.
Its ability to produce parts with excellent mechanical capabilities makes SLS the most common polymer additive manufacturing technology for industrial applications.
Just like SLA, SLS used to be only available in large-format, complex 3D printing systems starting at about $200,000. With Formlabs’s Fuse Series SLS printers, businesses can now access industrial SLS starting just under $30,000 with a 30 x 16.5 x 16.5 cm build volume.
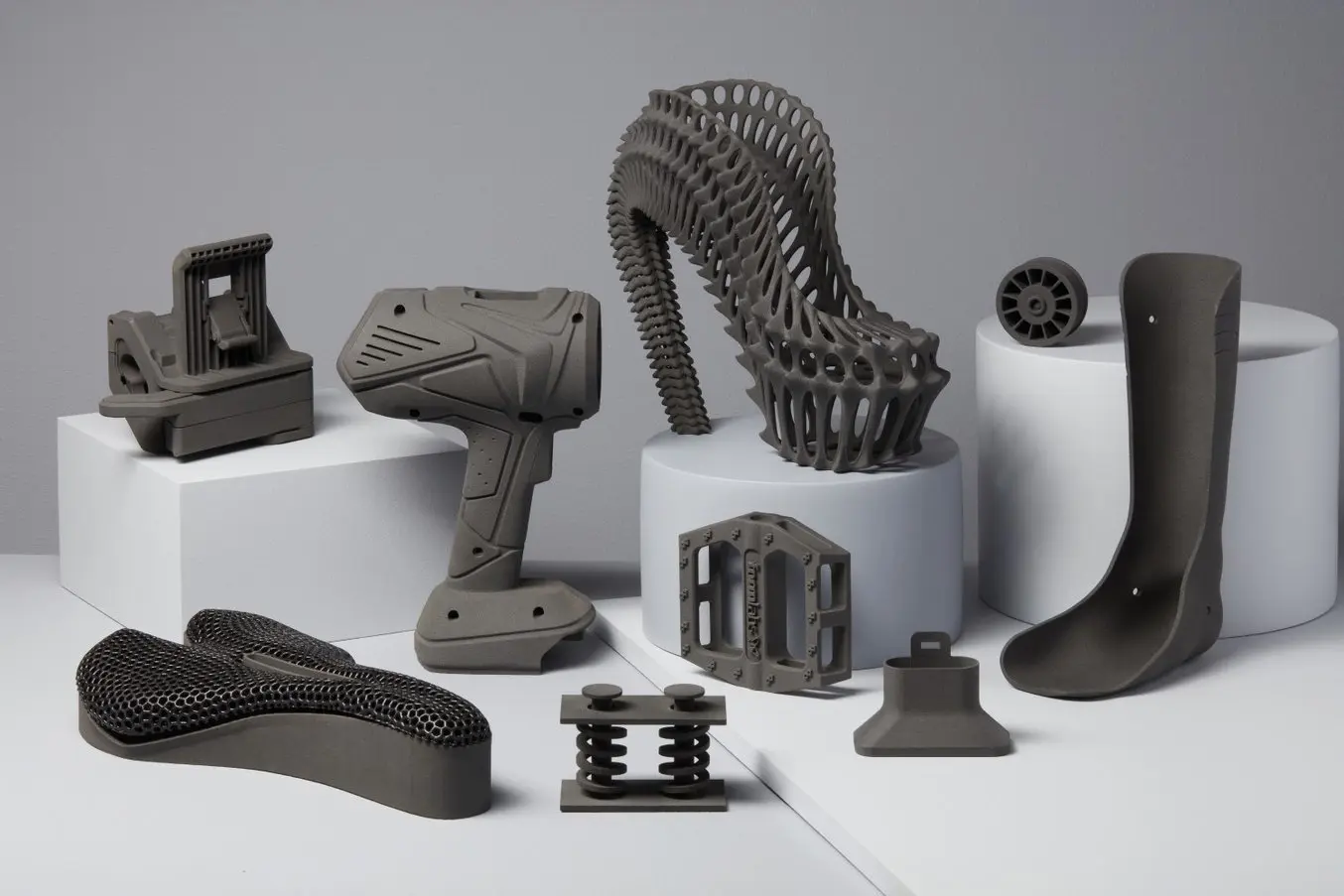
Parts printed on the Fuse 1 SLS 3D printer.
-
Advantages of SLS Industrial 3D Printers
Since SLS printing doesn’t require dedicated support structures, it’s ideal for complex geometries, including interior features, undercuts, thin walls, and negative features. Parts produced with SLS printing have excellent mechanical characteristics, with strength resembling that of injection-molded parts.
The most common material for SLS is nylon, a popular engineering thermoplastic with excellent mechanical properties. Nylon is lightweight, strong, and flexible, as well as stable against impact, chemicals, heat, UV light, water, and dirt.
The combination of low cost per part, high productivity, and established materials make SLS a popular choice among engineers for functional prototyping, and a cost-effective alternative to injection molding for limited-run or bridge manufacturing.
-
Disadvantages of SLS Industrial 3D Printers
SLS has a higher entry price than FDM or SLA technologies. While nylon is a versatile material, material selection for SLS is also more limited than for FDM and SLA. Parts come out of the printer with a slightly rough surface finish and require media blasting for a smooth finish.
Material Jetting
Material jetting 3D printers use a print head, similar to those in traditional inkjet printers, to deposit and cure droplets of photopolymer material, which harden under ultraviolet light. Some more advanced material jetting printers can also create parts from multiple materials.
-
Advantages of Material Jetting Industrial 3D Printers
Material jetting results in a finished product that is precise and has a smooth finish. The overall accuracy, combined with the fact that it is one of the only printing processes that offers multi-material and full-color printing, makes it an ideal option for realistic prototypes, such as full-color prototypes or anatomical models.
-
Disadvantages of Material Jetting Industrial 3D Printers
Material jetting printers can only operate with materials that have a low viscosity, which limits material options. The finished products tend to be brittle, photosensitive, and sensitive to heat. Their gradual deterioration makes them less suitable as functional prototypes. For resin 3D printing, SLA offers a wider range of functional materials, including resins that contain particles like wax and glass to imbue them with certain properties.
Metal 3D Printing
Beyond plastics, there are multiple industrial 3D printing processes available for metal 3D printing.
-
Metal FDM
Metal FDM printers work similarly to traditional FDM printers, but use extrude metal rods held together by polymer binders. The finished “green” parts are then sintered in a furnace to remove the binder.
-
Selective Laser Melting (SLM) and Direct Metal Laser Sintering (DMLS)
SLM and DMLS printers work similarly to SLS printers, but fuse metal powder particles together layer by layer using a laser instead of polymers. SLM and DMLS 3D printers can create strong, accurate, and complex metal products, making this process ideal for aerospace, automotive, and medical applications.
While the prices of metal 3D printers have also begun to decrease, with costs ranging from $100,000 to $1 million, these systems are still not accessible to most businesses.
Alternatively, SLA 3D printing is well-suited for casting workflows that produce metal parts at a lower cost, with greater design freedom, and in less time than traditional methods.
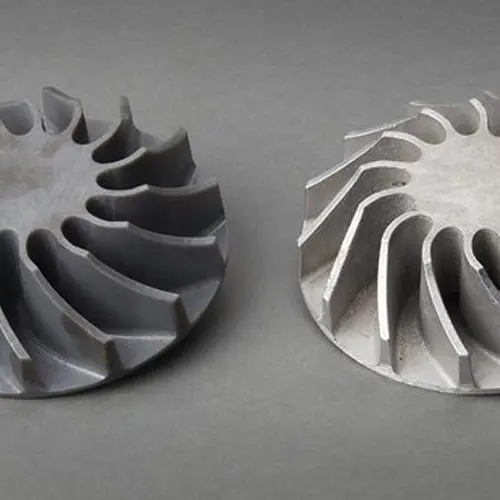
Fabricating Metal Parts With 3D Printing
Get design guidelines for creating 3D printed patterns, walk through the step-by-step direct investment casting process, and explore guidelines for indirect investment casting and sand casting.
Compare Industrial 3D Printing Processes
FDM, SLA, SLS, material jetting, and metal 3D printing have unique advantages and disadvantages across different applications.
Fused Deposition Modeling (FDM) | Stereolithography (SLA) | Selective Laser Sintering (SLS) | Material Jetting | Metal 3D Printing (Metal FDM, DMLS, SLM) | |
---|---|---|---|---|---|
Build volume | Up to 300 x 300 x 600 mm (desktop and benchtop 3D printers) | Up to 353 x 196 x 350 mm (desktop and benchtop 3D printers) | Up to 165 x 165 x 300 mm (benchtop industrial 3D printers) | Up to 300 x 200 x 150 mm (benchtop industrial 3D printers) | Up to 300 x 200 x 200mm (metal FDM), 400 x 400 x 400 mm (large industrial DMLS/SLM) |
Price range | Professional desktop FDM printers range from $2,000 to $8,000, and industrial systems are available from $15,000. | Professional SLA 3D printers are in the $2,500 to $10,000 range, and large-format resin 3D printers are in the $5,000 to $25,000 range. | Benchtop industrial SLS 3D printers start just under $30,000 for the printer and $60,000 for the entire ecosystem, including powder management and cleaning stations. Traditional industrial SLS printers start at around $200,000. | Starting from $20,000 (multi-material starting from $100,000) | Starting from $100,000 |
Materials | Standard thermoplastics, such as ABS, PLA, and their various blends. | Varieties of resin (thermosetting plastics). Standard, engineering (ABS-like, PP-like, silicone-like, flexible, heat-resistant, rigid), castable, dental, and medical (biocompatible). | Engineering thermoplastics, typically nylon and its composites (nylon 12 is biocompatible + compatible with sterilization). | Varieties of resin (thermosetting plastics). | Stainless steel, tool steel, titanium, cobalt chrome, and aluminum. |
Ideal applications | Basic proof-of-concept models, low-cost prototyping of simple parts. | Highly detailed prototypes requiring tight tolerances and smooth surfaces, molds, tooling, patterns, medical models, and functional parts. | Complex geometries, functional prototypes, short-run or bridge manufacturing. | Highly detailed prototypes, including multi-material and full-color realistic prototypes. | Strong, durable parts with complex geometries; ideal for aerospace, automotive, and medical applications. |
Disadvantages | Lowest resolution and accuracy; not ideal for complex designs or parts with intricate features. | Some materials are sensitive to long exposure to UV light. | Slightly rough surface finish, limited material options. | Limited material options. Finished products tend to be brittle and photosensitive; less suitable for functional prototypes. | High costs and complexity, stringent facility requirements. |
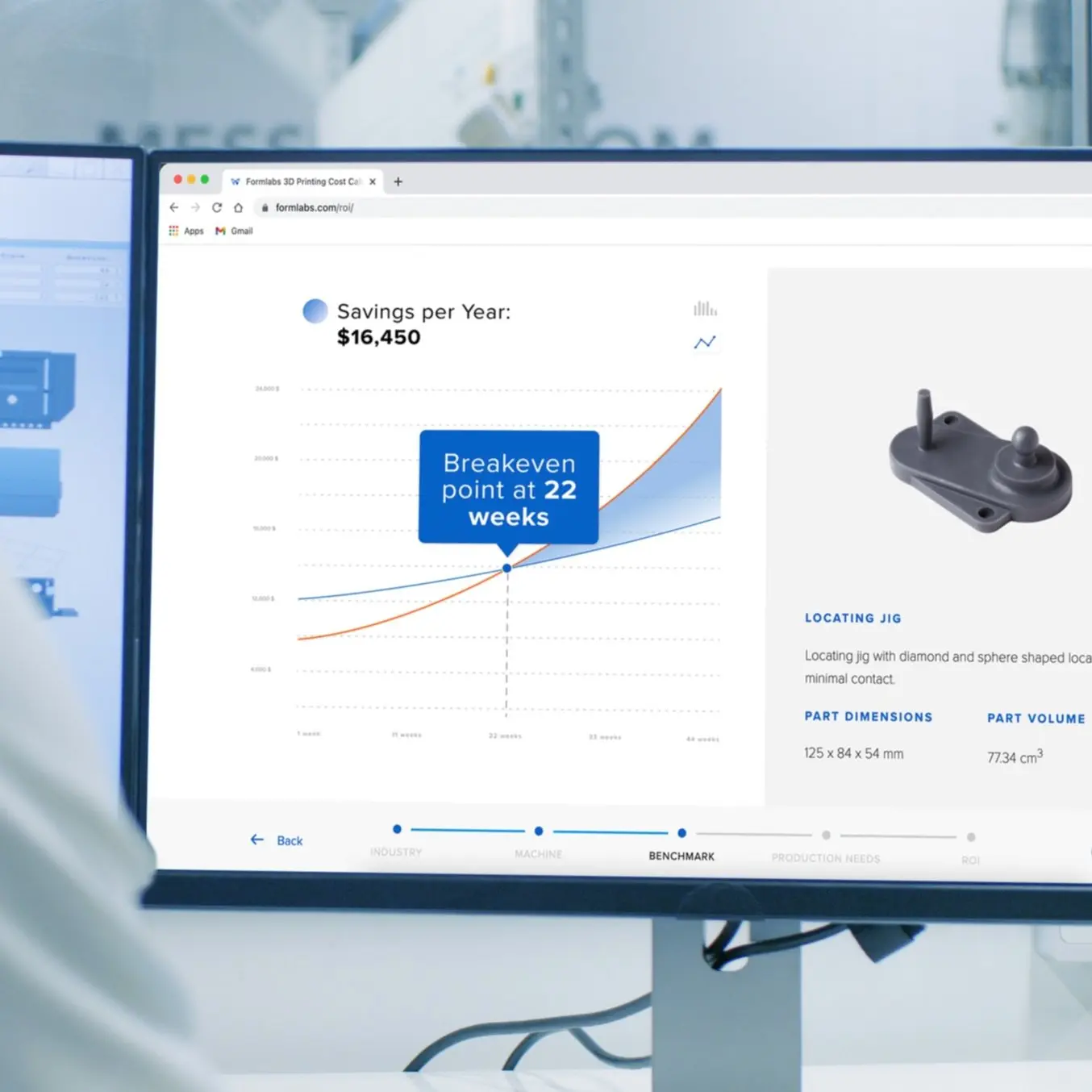
Calculate Your Time and Cost Savings
Try our interactive ROI tool to see how much time and cost you can save when 3D printing on Formlabs 3D printers.
Applications of Industrial 3D Printers
There are several applications that capitalize on industrial 3D printers, such as prototyping, hybrid manufacturing, and production.
Rapid Prototyping
With rapid prototyping, designers and engineers can create prototypes directly from CAD data faster than ever before, and execute quick and frequent revisions of their designs based on real-world testing and feedback.
Because these parts or assemblies are usually constructed using additive fabrication techniques as opposed to traditional subtractive methods, the phrase has become synonymous with additive manufacturing and 3D printing.
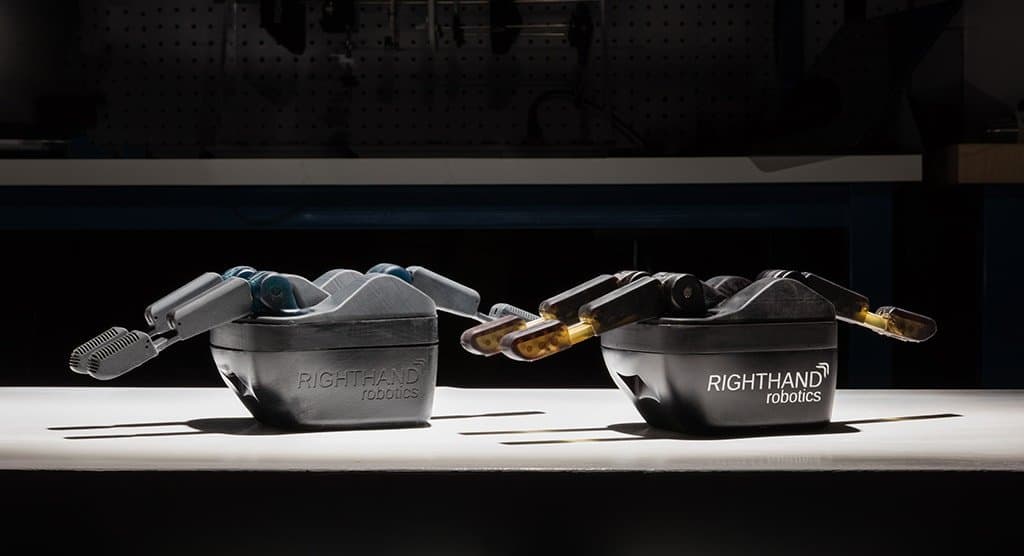
A rapid prototype of a robot hand next to the final end-use product.
Additive manufacturing is a natural match for prototyping. It provides almost unlimited form freedom, doesn’t require tooling, and can produce parts with mechanical properties closely matching various materials made with traditional processes.
With in-house industrial 3D printers, engineers and designers can produce realistic and functional prototypes quicker and at a lower cost than any other production method to quickly iterate between digital designs and physical prototypes. It is now possible to create prototypes within a day and carry out multiple iterations of design, size, shape, or assembly based on results of real-life testing and analysis. Ultimately, the rapid prototyping process helps companies get better products to market faster than their competition.
Hybrid Manufacturing
Hybrid manufacturing combines 3D printing with traditional manufacturing processes like injection molding, thermoforming, or casting. It enhances the production process by improving its flexibility, agility, scalability, and cost-efficiency. As a result, it enables manufacturers to meet changing business needs quickly.
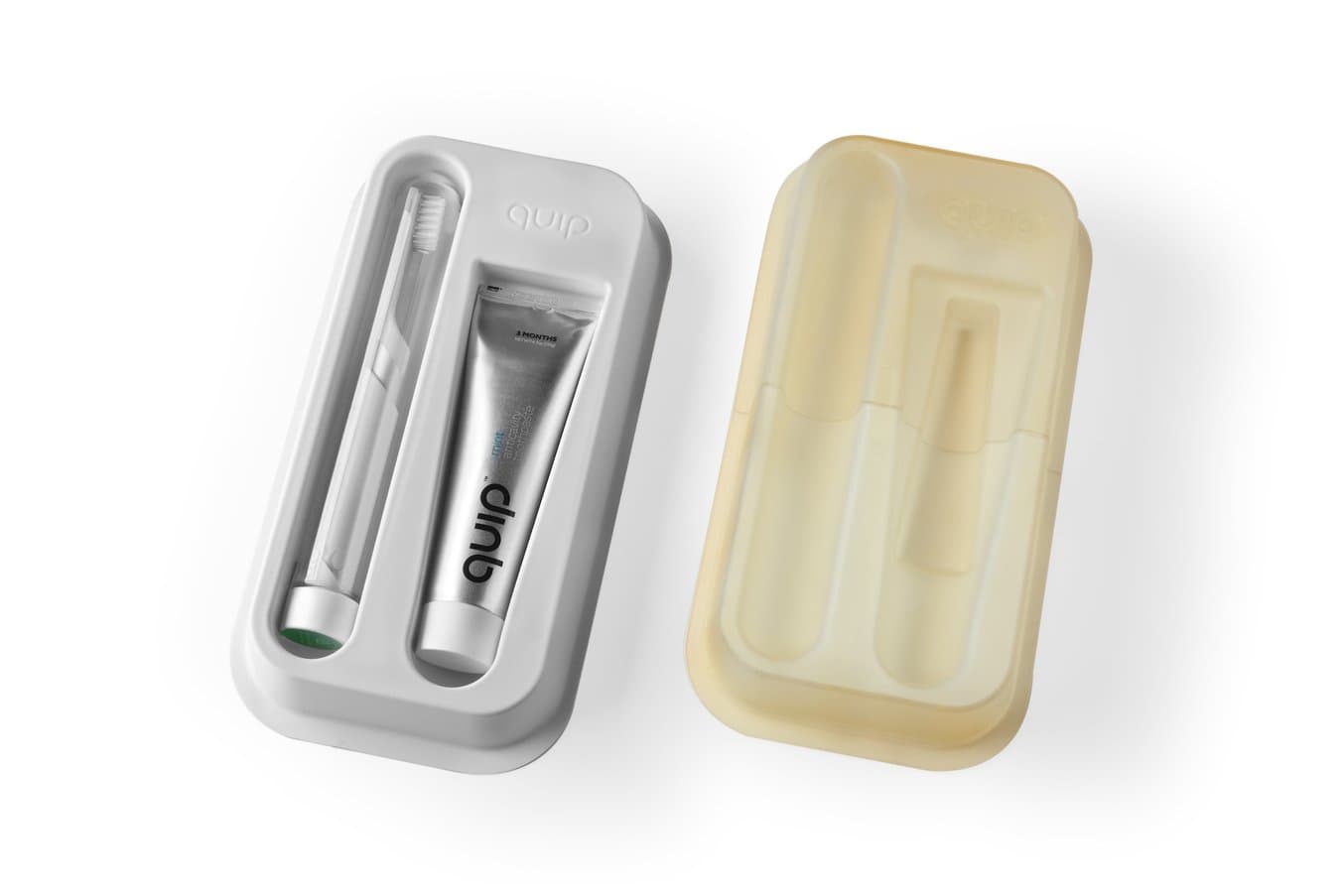
A 3D printed mold for vacuum forming product packaging.
Industrial 3D printers empower the rapid, cost-effective production of jigs, fixtures, and tooling in-house to save days or weeks of lead time, improve operational agility, and dramatically reduce costs versus outsourcing parts to an external vendor to machine from a solid billet of plastic or metal.
-
Tooling
Build custom tooling that stands up to the rigors of the factory floor, and can help solve the toughest manufacturing challenges. Validate manufacturing processes, solve DFM issues, and increase flexibility by direct printing of tooling for applications ranging from injection molding to CNC tube bending.
-
Jigs and fixtures
Reduce costs and increase agility by bringing jig and fixture production in-house with no minimum order quantities, no toolpath programming, wide material selection, and low capital equipment costs. Continuously improve products and respond quickly and effectively to issues on your manufacturing line with jigs and fixtures that improve assembly or QA processes.
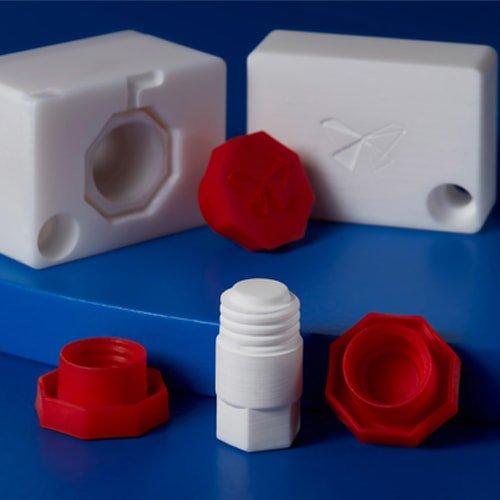
Low-Volume Rapid Injection Molding With 3D Printed Molds
Download our white paper for guidelines for using 3D printed molds in the injection molding process to lower costs and lead time and see real-life case studies with Braskem, Holimaker, and Novus Applications.
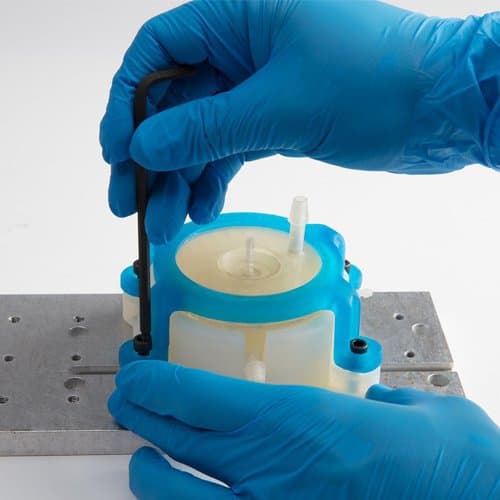
Designing Jigs & Fixtures with 3D Printing
Download the white paper reducing the cost and lead time of producing jigs and fixtures.
Production
As the economics of 3D printing are improving, and the cost-per-part threshold is moving: it’s becoming practical to use the technology in incrementally lower-value, higher-volume applications. Fueled by technology innovation and improving material properties, additive manufacturing is bound to further expand beyond rapid prototyping toward end-use parts and mass production.
Several industries have already incorporated 3D printed materials into their manufacturing processes for creating molds and casting patterns, or even printing end-use parts.
-
Mass Customization
Without the need to invest in costly tooling, use 3D printing to manufacture a variety of complex designs with no more time, energy, or material than producing simple parts. Automated 3D printing solutions can help to scale personalized products for mass-market opportunities such as patient-specific models in healthcare to consumer products like shoes, and earbuds.
-
Short Run Production
Short run production with 3D printing provides flexibility to change designs without sinking high costs into tooling, and a cost-effective manufacturing alternative for producing end-use parts in the tens and hundreds.
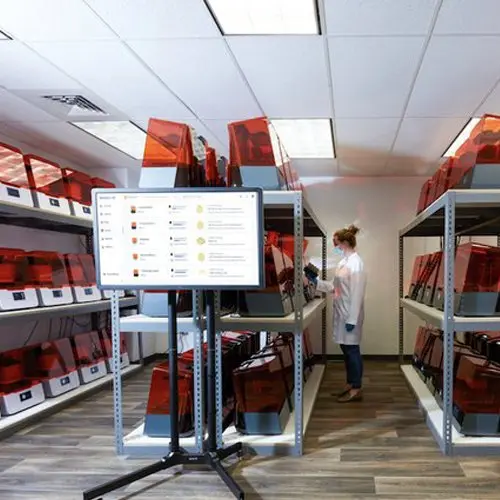
Introducing Factory Solutions
In this briefing, Formlabs’ Global Business Development Lead Dan Recht will show you how to identify, assess, and benefit from opportunities to use additive manufacturing as a production technology.
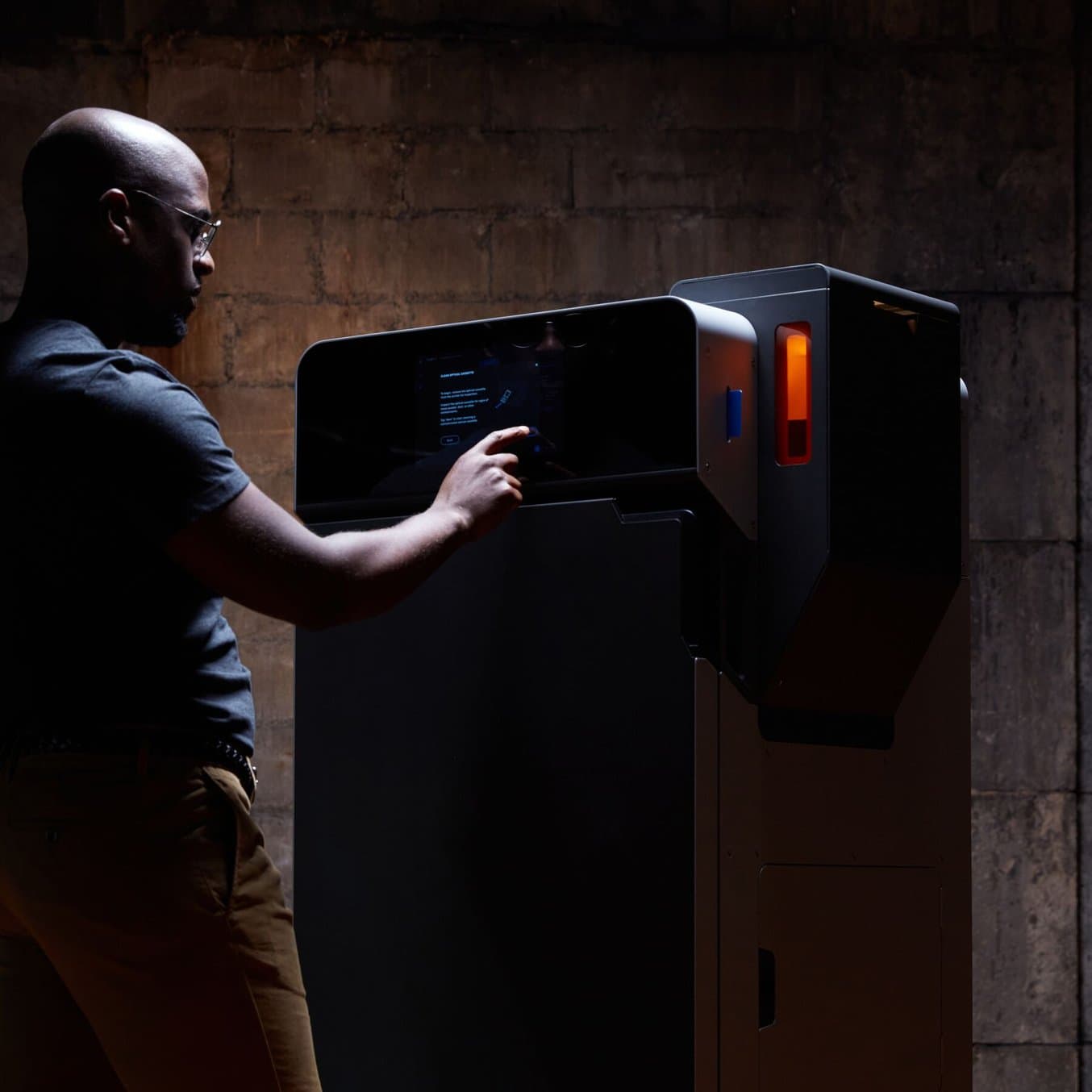
Outsourcing vs. In-House: When Does it Make Sense to Bring SLS 3D Printing In-House?
In this white paper, we evaluate the value proposition of bringing SLS 3D printers in-house, in comparison with outsourcing SLS parts from a service bureau.
Get Started With Industrial 3D Printing
The latest generation of industrial 3D printers have made manufacturing prototypes and end-use parts faster and much more affordable, opening the doors for almost any company to use 3D printing to improve product development and production.
With a line-up of accessible SLA and SLS 3D printers, Formlabs strives to revolutionize industrial 3D printing. If you’re ready to leverage 3D printing in your business, find the right Formlabs 3D printer for your needs today.