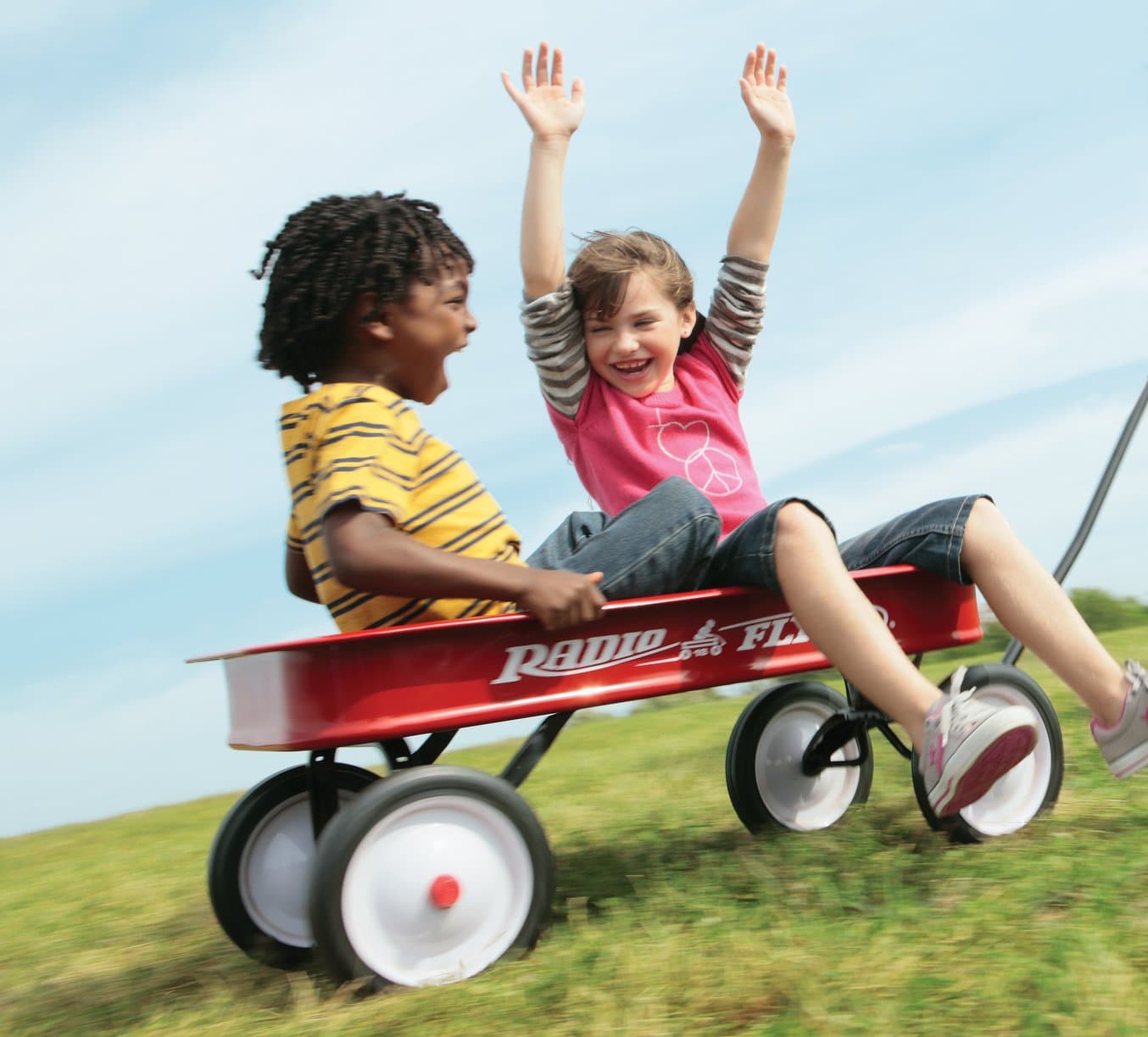
Radio Flyer’s most famous product, the iconic Original Little Red Wagon®, may conjure up images of American mid-century traditionalism, but the Chicago-based company is far from stuck in the past — to lead an industry for over a century requires a commitment to new technologies and innovative ideas. 3D printing is a huge part of how the company continues to be the world’s leading producer of ride-ons including wagons, scooters, tricycles, go-karts, electric bikes, and more.
Radio Flyer’s product development team is 3D printing all day, every day. Their Prototype Shop relies on Formlabs’ Fuse selective laser sintering (SLS) 3D printers as well as large-format stereolithography (SLA) printers to help them hit design deadlines and create products that bring smiles and create warm memories that last a lifetime.
We spoke with Radio Flyer product design engineer Agostino LoBello, who supports the evaluation and integration of new technologies for their machine shop. The new Form 4L large-format resin 3D printer has shortened timelines for high-fidelity vendor approval parts and increased throughput for next-day, human-scale prototypes. Combined with their 24/7 production of functional prototypes on their Fuse Series printers, Form 4L helps the shop produce hundreds of parts each month.
“One of the first things we printed on the 4L as soon as we got it was a seat for the Stingray Ride-On, and we used that exact 3D print in a vendor meeting. The speed and dimensional accuracy have made a big difference in our shop. Right now, we’re successfully printing a box the full size of the build volume – when we tried to print that size on Form 3L, the box and its lid wouldn’t match up. Before Form 4L we would rather CNC it on our router or piece it together with SLS.”
Agostino LoBello, Product Design Engineer, Radio Flyer
Fuse Lends Strength and Functionality for Family Testing
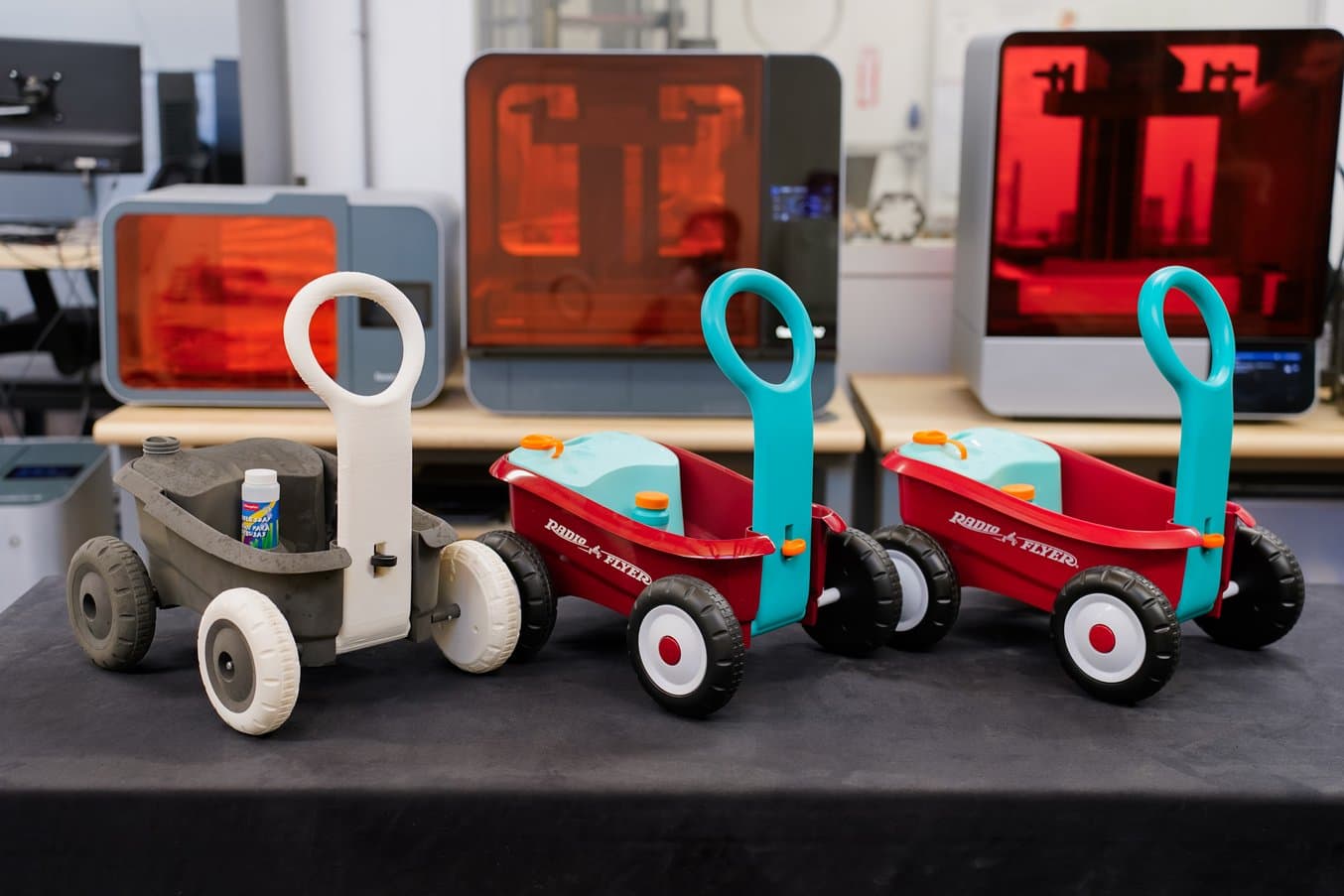
The original SLS printed prototype (left), SLA 3D printed and painted Roadshow Prototype (center) and final Production Bubble Buddy Walker Wagon.
Beloved toys can experience years of play, lasting generations. Radio Flyer builds products to last and is committed to making products of the highest quality and safety.
The secret behind that durability is the intensive prototyping process every component goes through. Since adding their first Fuse 1 in 2022 and the Fuse 1+ 30W in 2023, Radio Flyer’s Prototype Shop has been able to produce fast, functional prototypes for seats, ball bearings, handlebar grips, and more, in Nylon 12 Powder for the engineers and designers.
“It’s really the only printer we trust if we are building a new wagon or tricycle. We use it for functional caster pods and wheel assemblies, brake assemblies, and more. The Fuse printed parts solve a need for functional, end-use parts that we feel good about sending home with a family for testing.”
Agostino LoBello, Product Design Engineer, Radio Flyer
Families are some of the hardest consumers to please, and where children’s safety is concerned, durability is a top priority. Printing parts on the Fuse Series gets products past initial prototyping stages faster, so that they can confidently conduct several rounds of testing without the need to print new parts.
Relying on Dimensional Accuracy
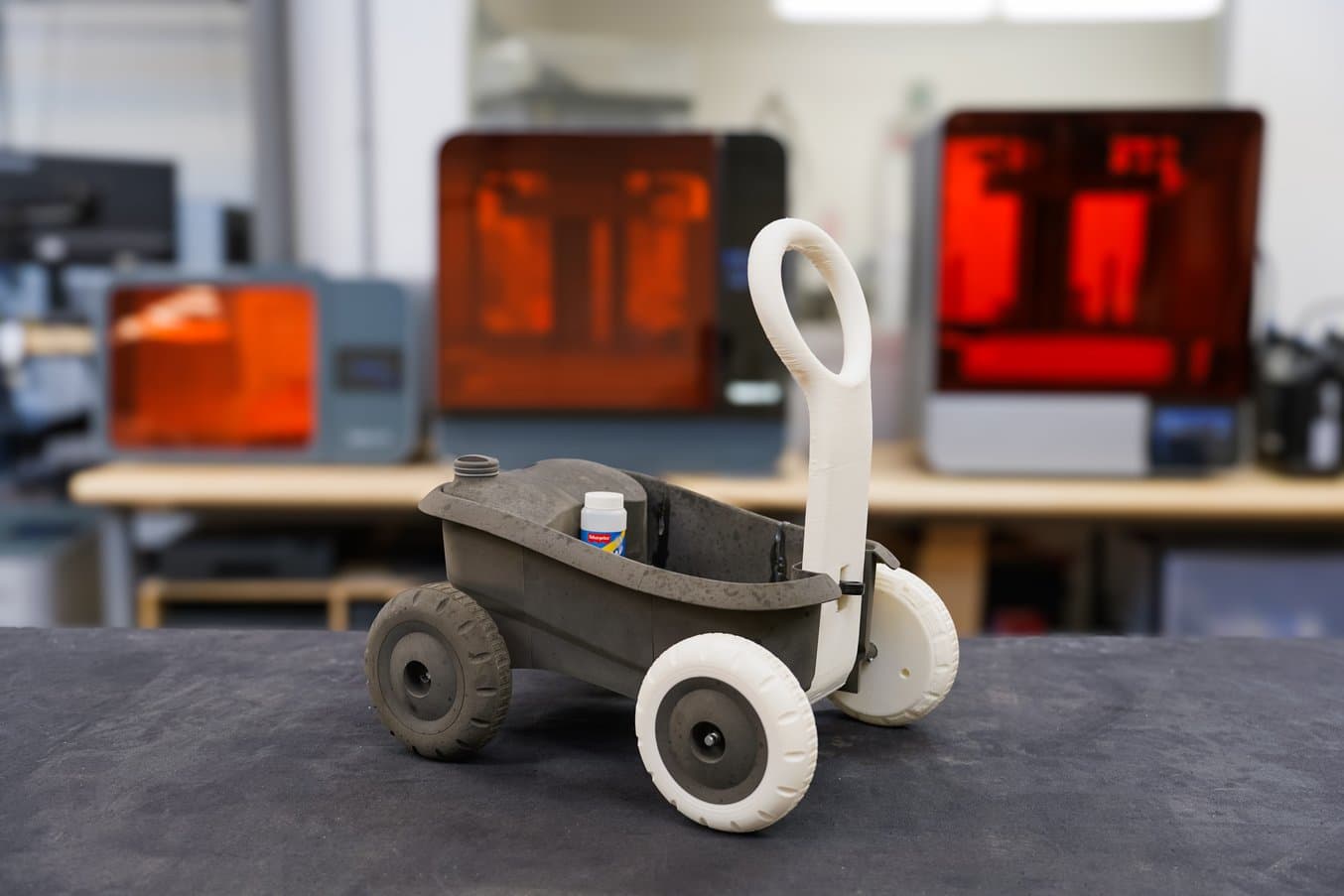
The Bubble Buddy Walker Wagon® was prototyped on Radio Flyer’s Fuse 1+ 30W SLS 3D printer in Nylon 12 Powder, shown here as a multi-part assembly prototype.
Even though Radio Flyer’s products are sized for children, they’re still quite a bit bigger than the average 3D printer’s build volume, including the Fuse Series. Prototypes are often split into multiple parts to fit within the 3D printer’s build volume and assembled. The self-supporting print bed on SLS 3D printers makes it possible to nest multiple parts together within one build, so even if the requestors need to fit parts together after the print is done, they’re able to get them all at once, and large parts don’t have to slow down the iterative process.
“Another advantage of the Fuse is that when we have to break large parts up to fit on the Fuse, they need to line up. Even if we’re printing one today and one tomorrow, we need to rely on it to have the same dimensional accuracy every time. Parts printed on different days still fit perfectly together,” says LoBello.
The Fuse Series printers have delivered accurate parts so consistently that the design and engineering teams have grown to trust the technology more and more. They had used an FDM 3D printer in the past, but the Fuse has given them a higher fidelity result — they’re able to learn more from parts without factoring in supports or anisotropic geometries before they go to tooling.
“The team views Fuse parts as they would production injection molded parts. We have faith that what we send to the printer is what we’ll get out of it for functional, end-use quality parts.”
Agostino LoBello, Product Design Engineer, Radio Flyer
Speed and Throughput With SLS 3D Printing
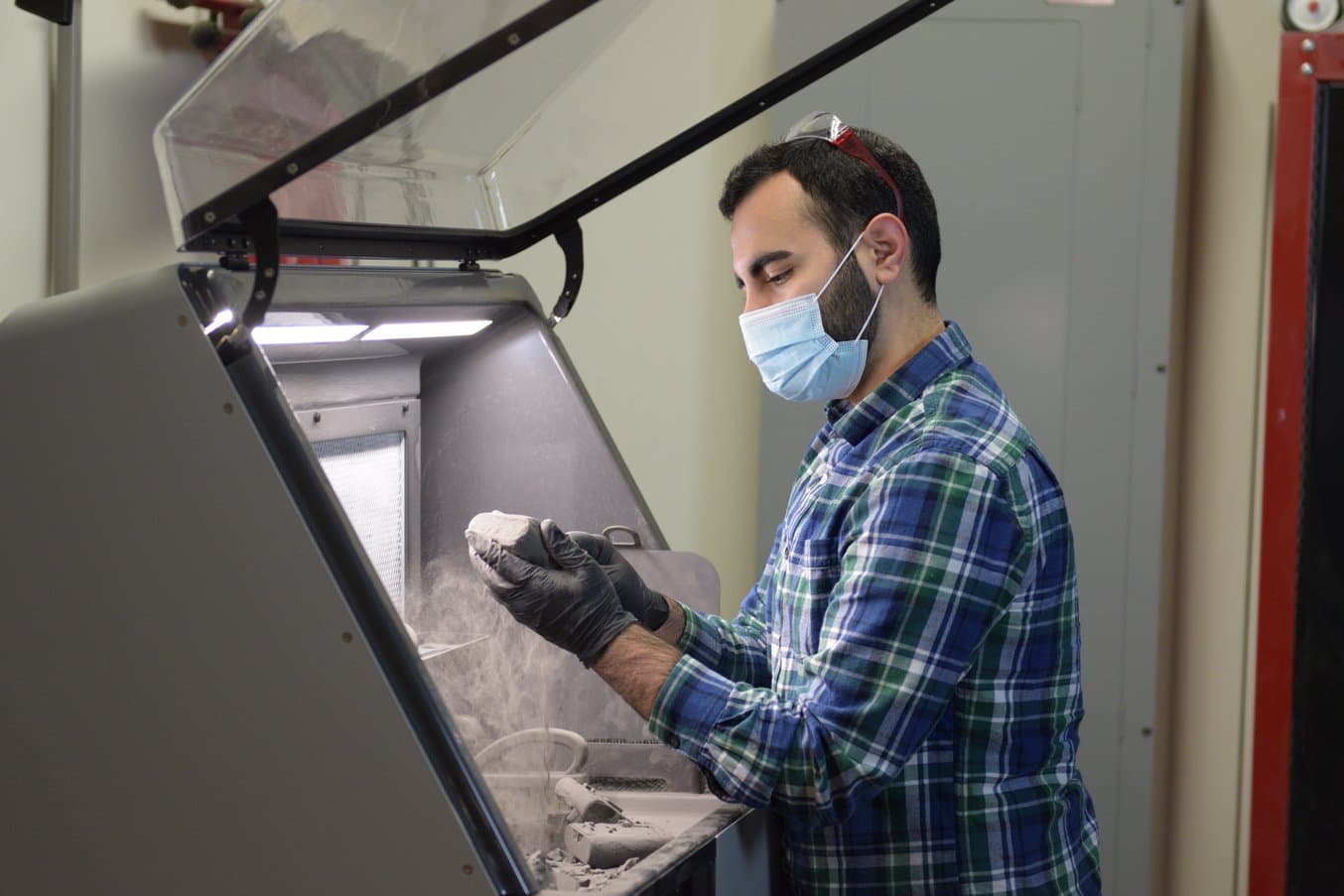
During summer — the busiest time of the year — Radio Flyer’s two Fuse Series printers will run nonstop, often going through over 20 kg of Nylon 12 Powder each month.
Each Radio Flyer product category, such as wagons, e-bikes, or scooters, has multiple products and components within it, so new development projects are happening all the time. SLS parts are used at each stage, from early proof of concepts to final-stage models that get sent to potential buyers and partners. Injection molding doesn’t make sense until customer orders and quantities are completely locked in, so Radio Flyer leverages the low cost per part and high throughput of the Fuse Series printers to get them to that point quickly and affordably.
“The Fuse printers are running 24/7, always one build every day and sometimes two if they’re a bit shorter. Throughout the busiest time in the summer, when we’re getting multiple iterations of different concepts every day, we’ll go through 20 to 30 kilograms of powder a month,” says LoBello.
Adding SLS capability has shifted some of Radio Flyer’s workflow from FDM and outsourcing. They’re able to get farther along in the product development cycle before needing to go to tooling because they’re confident in the Fuse printed parts’ ability to replicate what they’ll eventually get from an injection molded component. “It’s sped our workflow up. We’re not needing to send as much out of house, and from an engineering and product development perspective, we need fewer rounds of tuning and dialing in specs before sending designs to the factory,” says LoBello.
Closing the Gap With Form 4L
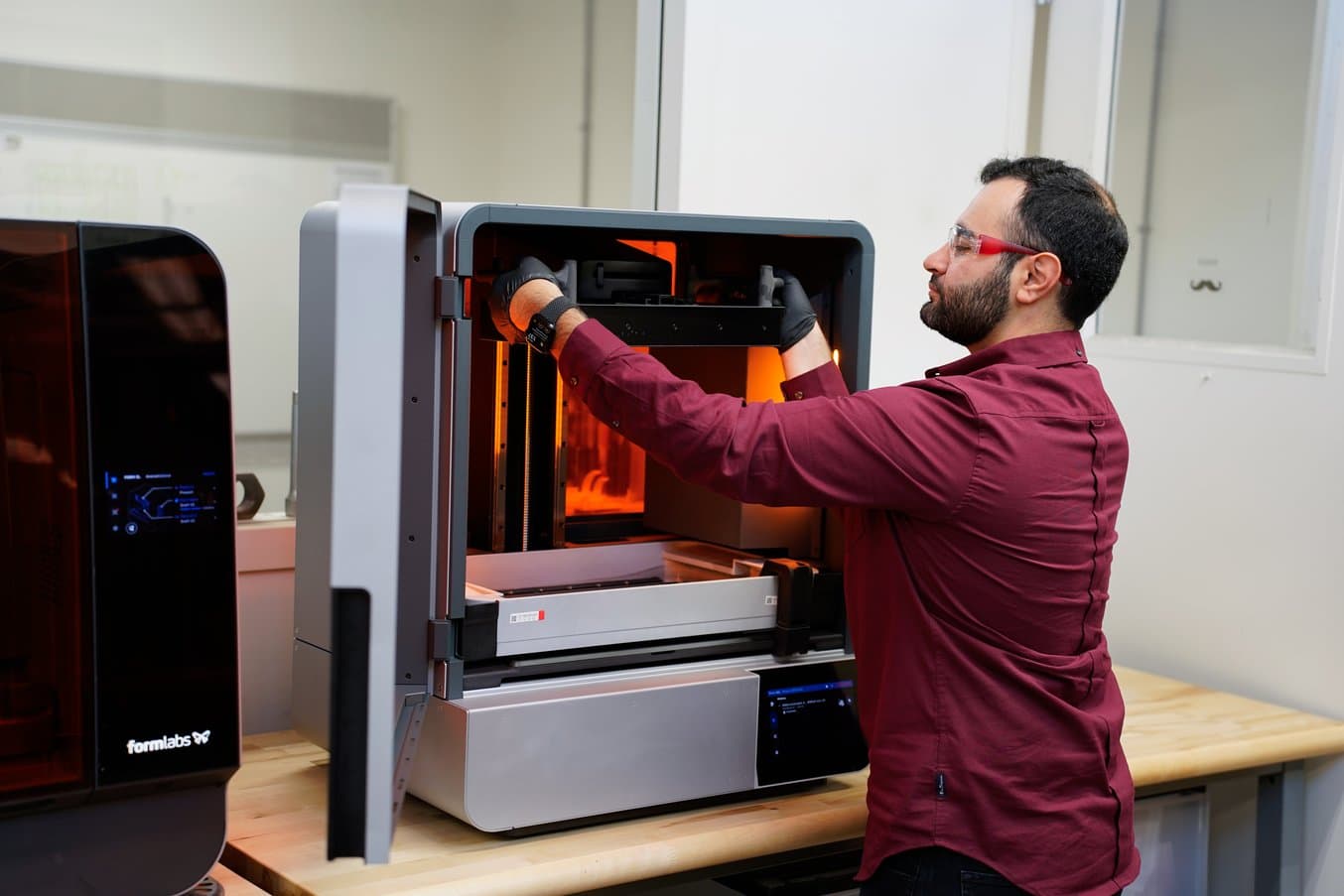
Form 4L has helped Radio Flyer print large parts fast, so design and engineering teams can meet critical deadlines with confidence knowing they’ve been able to iterate and test all of their ideas.
The Radio Flyer developmental workflow has come to rely on SLS 3D printing. Their previous large-format SLA 3D printer, the Form 3L, wasn’t getting many requests from the team. But with the arrival of Form 4L, that’s started to change.
“We often need quick turnarounds for design reviews. Previous large-format options couldn’t to get parts done fast enough, and it’s that quick turnaround where I think Form 4L has closed the gap. It’s fast enough that our 3D printing tech is running multiple builds a day,” says LoBello.
Faster print times and more print cycles each day led to more fully fleshed-out ideas and a deeper understanding of how each product fulfills a specific need. “We spend a lot of time focusing on the design of our products and all the foreseeable uses. We ask, ‘How are people going to use this? What would they want to add to it?’” says LoBello. Fast, powerful 3D printing is one way to pursue every possible answer to these questions.
“Having the ability to prototype our ideas quickly because we can generate more versions and test those ideas quickly with Form 4L has allowed us to bring concepts further, faster. We can integrate new features into products that would have been difficult to before.”
Agostino LoBello, Product Design Engineer, Radio Flyer
Accuracy and Reliability Improvements
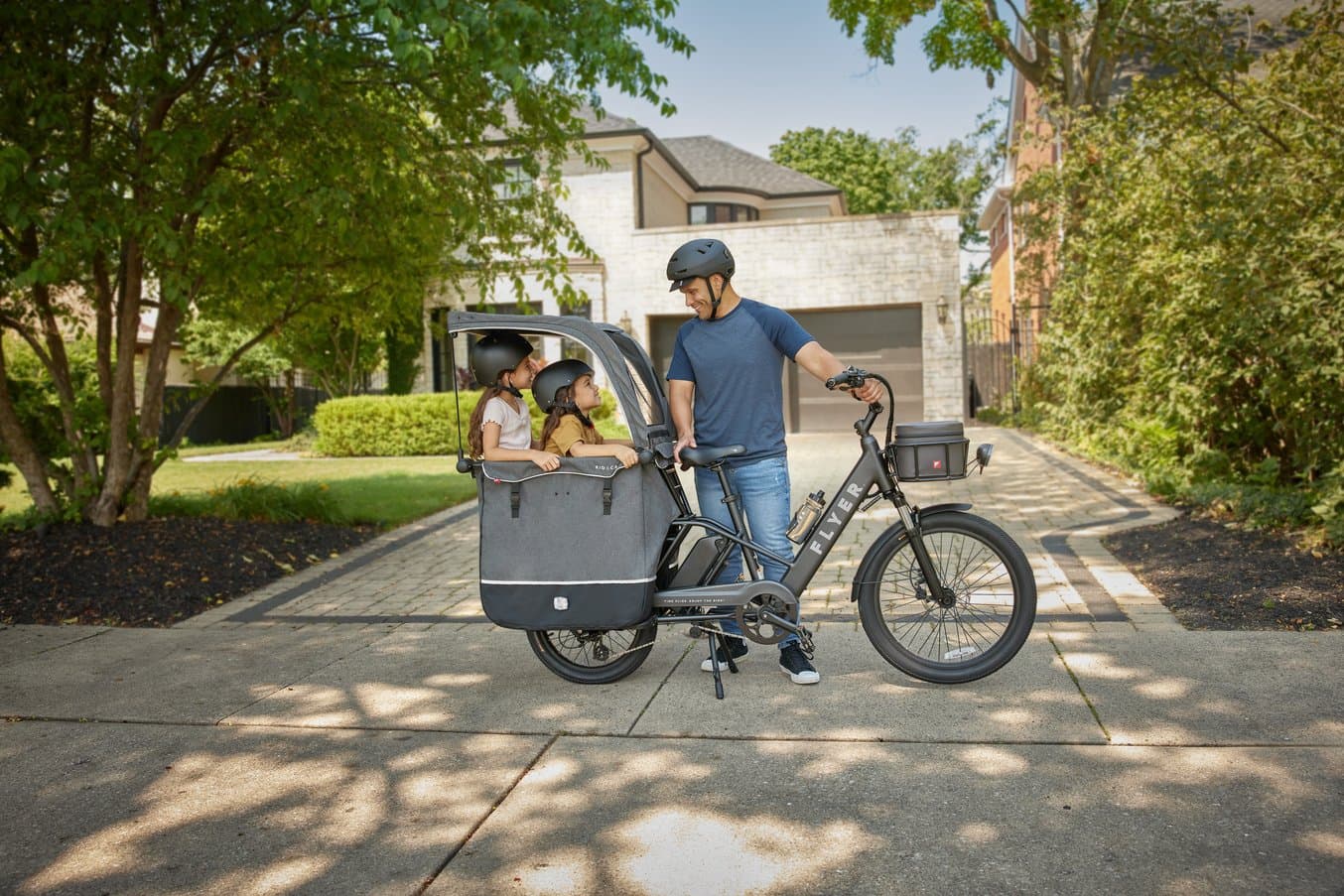
New product prototypes for e-bikes and e-bike accessories were often being sent to the Fuse Series printers before Radio Flyer brought Form 4L in-house. Now, Form 4L’s improved reliability and dimensional accuracy have given teams confidence that their parts will come out accurate and easy to post-process for final approval prototypes.
Before adding Form 4L, The Prototype Shop's team hadn’t gotten many large-format SLA requests because the product design teams had become frustrated with a lack of dimensional accuracy. “When we’re assembling a prototype, the different components have to fit seamlessly together, otherwise it’s distracting and doesn’t let us learn as much as we can from a design review,” says LoBello.
To request a part in-house rather than go with a tried and tested outsourcing CNC machinist or expensive industrial 3D printing service bureau, the product team must have complete confidence they’ll get what they’re looking for, especially with limited timeframes if something goes wrong. “That’s the big improvement over Form 3L. We have a lot higher degree of confidence that Form 4L will give us parts that will work for what we’re trying to do,” says LoBello.
The team has started getting more and more requests for SLA parts now that Form 4L is an option. For roadshows, where Radio Flyer’s product development and sales team will meet with retail buyers to demonstrate their new products and ideas, the team needs parts that are nearly indistinguishable from injection molded surface finishes.
“These parts must be precise because we’re using them to demonstrate to retailers what they’ll be buying. To the untrained eye, they need to be mistaken for a final manufactured product, and Form 4L parts are helping us get there,” says LoBello.
Timeless, Elegant Products Require Extra Testing
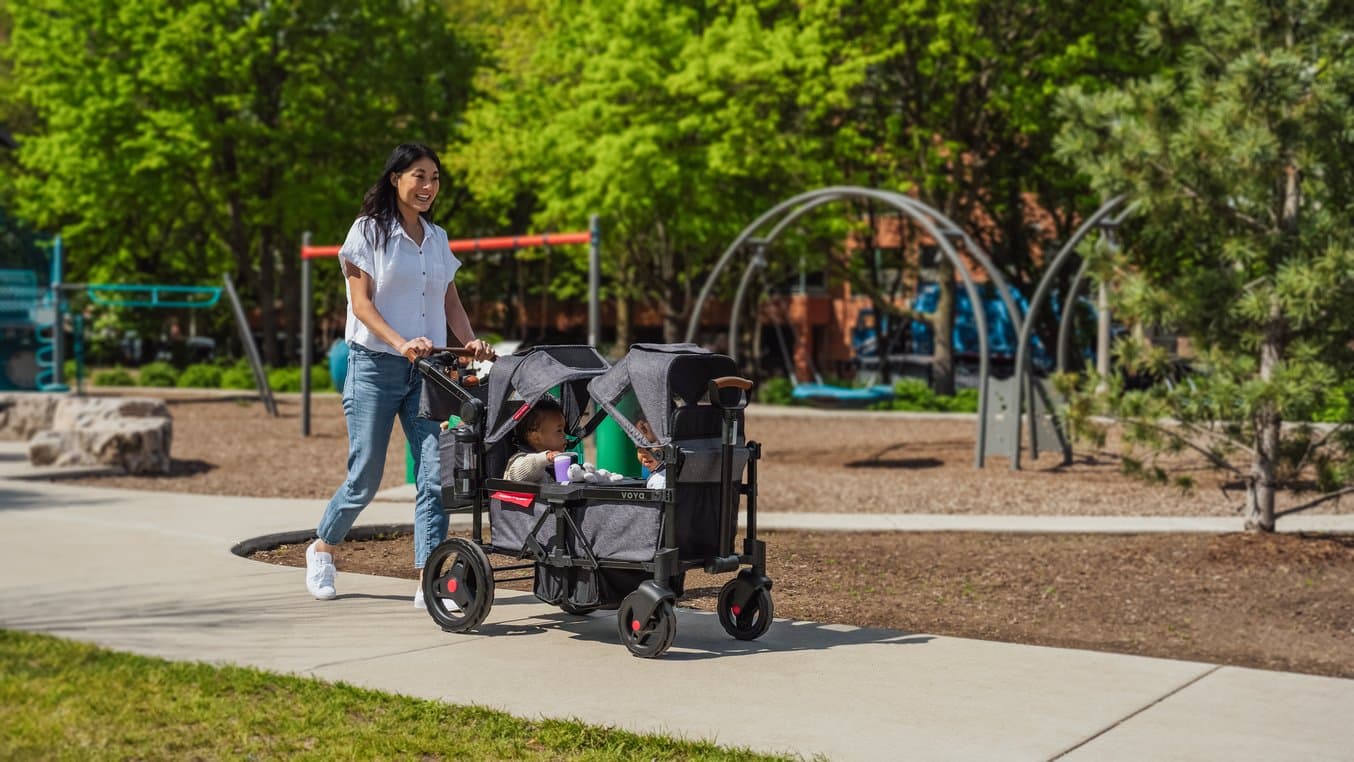
Fast, reliable prototyping with both SLA and SLS 3D printing has helped Radio Flyer create new evolutions of iconic toys and family products, delivering the tools for families to make life-lasting memories.
Trusted and loved by families for over 100 years, Radio Flyer has built a legacy of innovative, high-quality products that have delighted generations of families. Combining beautiful product design with function and safety requires intensive iteration and real feedback from families — 3D printing makes that process possible for Radio Flyer.
By bringing industrial-quality 3D printers like the Fuse Series and Form 4L in-house, their design teams can try new things, tweak small features, and rely on their prototypes to act like the real thing.
Adding Form 4L has opened up capacity in their Prototype Shop to do what it couldn’t before — produce high-fidelity models that can be nearly indistinguishable from an injection molded piece in less than a day. The speed, accuracy, and reliability of Form 4L helps Radio Flyer do what they do best — approach tradition through the lens of modern technology to create toys that combine the best of both worlds.
To learn more about the Fuse Series or Form 4L, visit our pages.