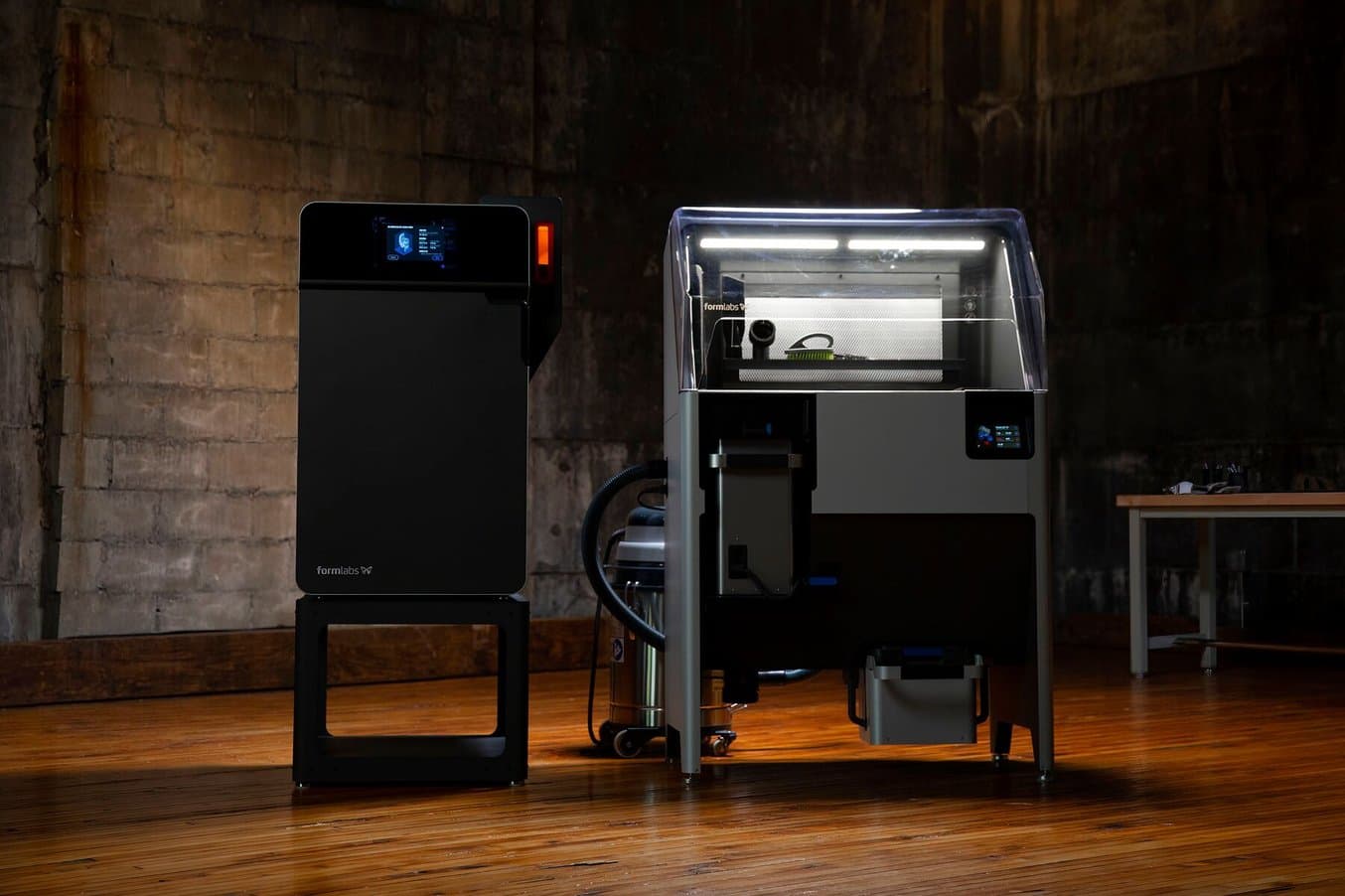
The Formlabs Fuse 1+ 30W selective laser sintering (SLS) 3D printer
Since its invention in the 1980s, selective laser sintering (SLS) 3D printing has been used by large manufacturers for prototyping and small batch production. Only recently, however, have SLS 3D printer prices become affordable for small to medium manufacturers. The growing number of SLS 3D printers deployed globally speaks to the high part quality, low cost per part, and production readiness of this technology.
SLS 3D printing is an additive manufacturing technology in which a thin layer of plastic powder particles is sintered by a high-powered laser in the shape of a cross-section of the 3D file. The printer then spreads another thin coat of these particles across the build chamber, and the laser sinters that, gradually building these layers into the final part. In plastic powder bed fusion 3D printers, the powder bed supports the parts as they’re being constructed, eliminating the need for the support structures necessary in most other forms of 3D printing, and enabling complex constructions with overhangs, internal channels, and interlocking features. The lack of support structures also means that post-processing parts is easier and less labor-intensive, enabling parts to be produced consistently at a larger scale.
Because the SLS technology requires a high-powered laser, a high level of precision, and tight control throughout the printing process, even the cheapest SLS printer is more expensive than most fused deposition modeling (FDM) and many stereolithography (SLA) printers. But even with these higher initial costs, bringing an SLS 3D printer in-house can result in a positive ROI within just a few months thanks to the high productivity and the lower costs of new industrial benchtop solutions.
In this article, we’ll compare the prices of different SLS 3D printers, and provide a complete overview of the cost of selective laser sintering printing, from initial purchase price to ongoing maintenance, material purchases, and more.
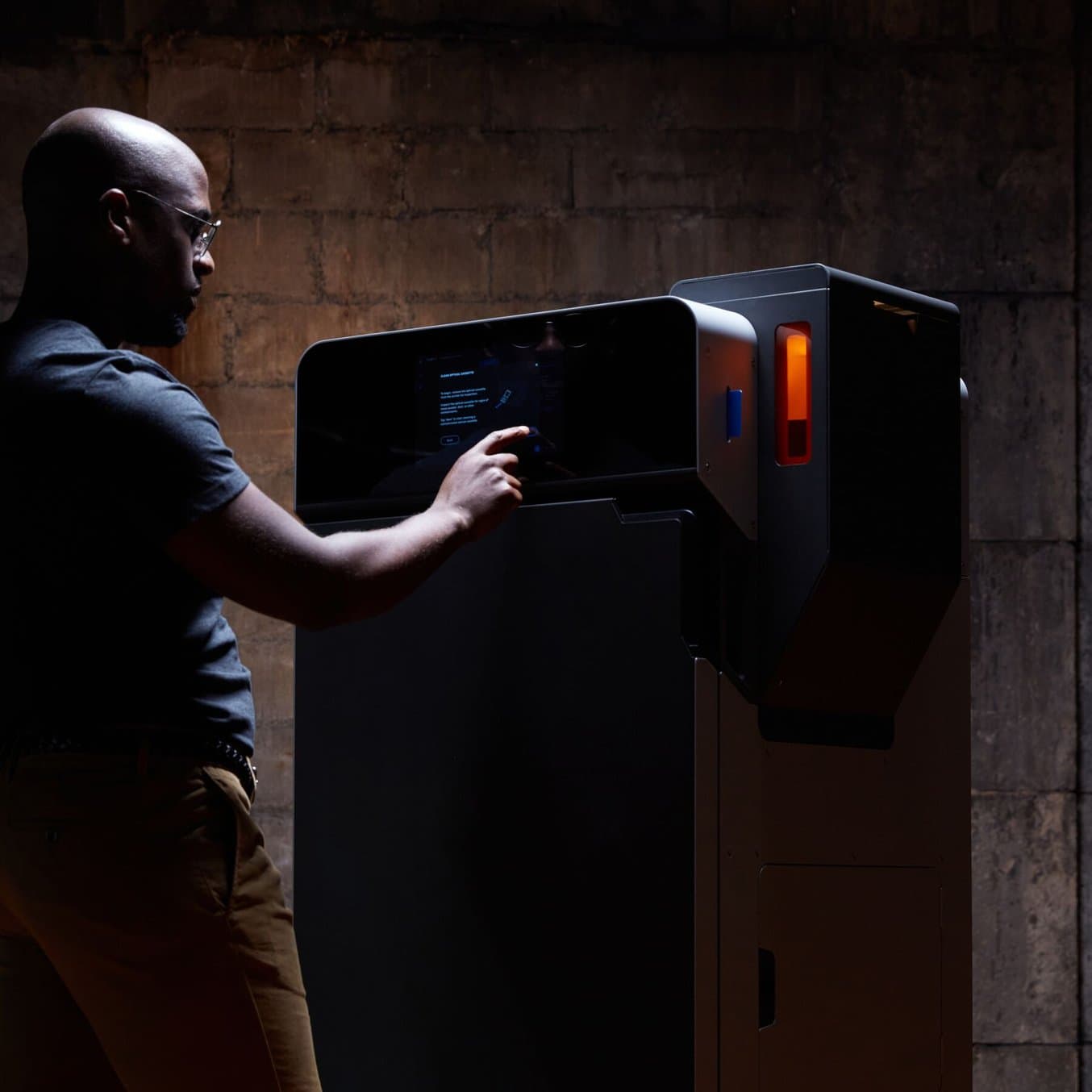
Outsourcing vs. In-House: When Does it Make Sense to Bring SLS 3D Printing In-House?
In this white paper, we evaluate the value proposition of bringing SLS 3D printers in-house, in comparison with outsourcing SLS parts from a service bureau.
SLS 3D Printer Prices: Benchtop vs. Industrial Printers
Historically, SLS printers were complex, bulky, and expensive systems, only accessible for industrial giants with large manufacturing facilities. In the last five years have benchtop options made it possible for small and medium manufacturers to access the power and productivity that SLS 3D printing provides.
When comparing benchtop SLS solutions like the Fuse Series to traditional industrial options, there are several factors to take into account, namely purchase price, size, ease of use, infrastructure requirements, and ongoing costs. In the following table, we cover these factors in a comparison between benchtop industrial SLS (the Formlabs Fuse 1+ 30W) and traditional SLS (based on EOS’s and 3D System’s product range).
Fuse Series: Benchtop Industrial SLS 3D Printers | Traditional Industrial SLS 3D Printers | |
---|---|---|
Price | Starting at $28,989 for the Fuse 1+ 30W | $200,000-$500,000+ |
Print Volume | Up to 165 x 165 x 300 mm | Up to 550 x 550 x 750 mm |
Pros | Affordable High-quality parts High throughput Multiple material options Simplified workflow Small footprint Low maintenance | Large build volume High-quality parts High throughput Multiple material options |
Cons | Smaller build volume | Expensive machinery Large footprint Facility requirements High maintenance Requires a dedicated operator |
What Goes Into SLS 3D Printing Cost
Equipment Ownership
The cost of SLS ownership is not limited to only the printer hardware itself — there are also the accessory systems, maintenance, and service to consider. Printers themselves can range from around $10,000 for DIY cheap SLS printers to $500,000+ for the most expensive large-format industrial printers.
Formlabs was the first manufacturer to make industrial-quality printing available at the affordable end of the spectrum; the Fuse 1+ 30W starts at $28,989, while delivering parts of comparable quality to traditional industrial SLS options. However, regardless of which print engine is purchased, there are post-print steps that must be completed for usable parts.
SLS 3D printers provide the benefit of supportless printing, and though this eliminates the need for painstaking removal of support structures, there is still a removal step for the layer of unsintered powder coating the parts. For this step, an accessory system is integral. Almost every SLS manufacturer supplies a post-processing and powder recovery station, which itself can vary greatly in price, from $999 for Formlabs' Fuse Depowdering Kit, an affordable, all-in-one manual post-processing kit, to $9,999 for the Fuse Sift for a compact and efficient powder management station, to $50,000 for EOS’s solutions.
After basic cleaning, media blasting (also called sand blasting) is recommended to fully depowder SLS parts. Manual media blasting cabinets are available for less than $500, while Fuse Blast is the first affordable, automated media blasting solution that can drastically reduce labor time and cost for $10,999.
For the entire ecosystem capable of producing industrial-quality parts, including the Fuse 1+ 30W SLS 3D printer, powder recycling and cleaning with Fuse Sift and Fuse Blast, to be available for under $60,000 is revolutionary, and has opened up opportunities for small businesses, individuals, and educational institutions to bring powerful powder bed fusion 3D printing in-house for the first time.
For all SLS printers on the market, there are options for service plans and maintenance contracts, some voluntary, others mandatory. For traditional industrial machines, most service contracts are priced at around 10% of the machine cost — enough to purchase a Fuse Series printer each year. Additionally, industrial printer service plans often have a mandatory renewal every year, creating yet another ongoing cost.
Materials and Consumables
The most popular material for SLS 3D printing is nylon, a rugged engineering thermoplastic used for strong, lightweight functional parts, as their main material option. Nylon composites are also very common, and some manufacturers also offer more flexible options like TPU. The cost of these materials varies between manufacturers, but most price their nylon materials at around $100/kg, with discounts available at larger volumes.
Though prices for raw materials are similar across different manufacturers, the ongoing cost of using those materials can change based on the efficiency of the workflow. This efficiency depends on two factors: packing density and refresh rate.
Packing densities of benchtop SLS printers like the Fuse Series, can often reach 30%, leading to a zero waste printing workflow. The zero waste printing workflow relies on an equilibrium between packing density and refresh rate. Refresh rate refers to the amount of fresh powder necessary for each new build. Most SLS refresh rates are between 30%-50%, though some industrial systems have refresh rates of only 20%.
What matters most for ongoing consumables cost, however, is not refresh rate alone, but the balance of refresh rate and packing density. When they are equal or when the latter is higher, only sintered powder needs to be replaced by fresh powder, and all powder eventually gets used, leading to zero waste and the most efficient use of funds.
Labor
The self-supporting nature of powder-bed printing eliminates the laborious process of removing supports from parts printed on FDM or SLA machines, but there is still hands-on labor involved, as the parts must be depowdered in some type of post-processing set-up. Some solutions are also highly complex, requiring maintenance and a long list of workflow steps between each print.
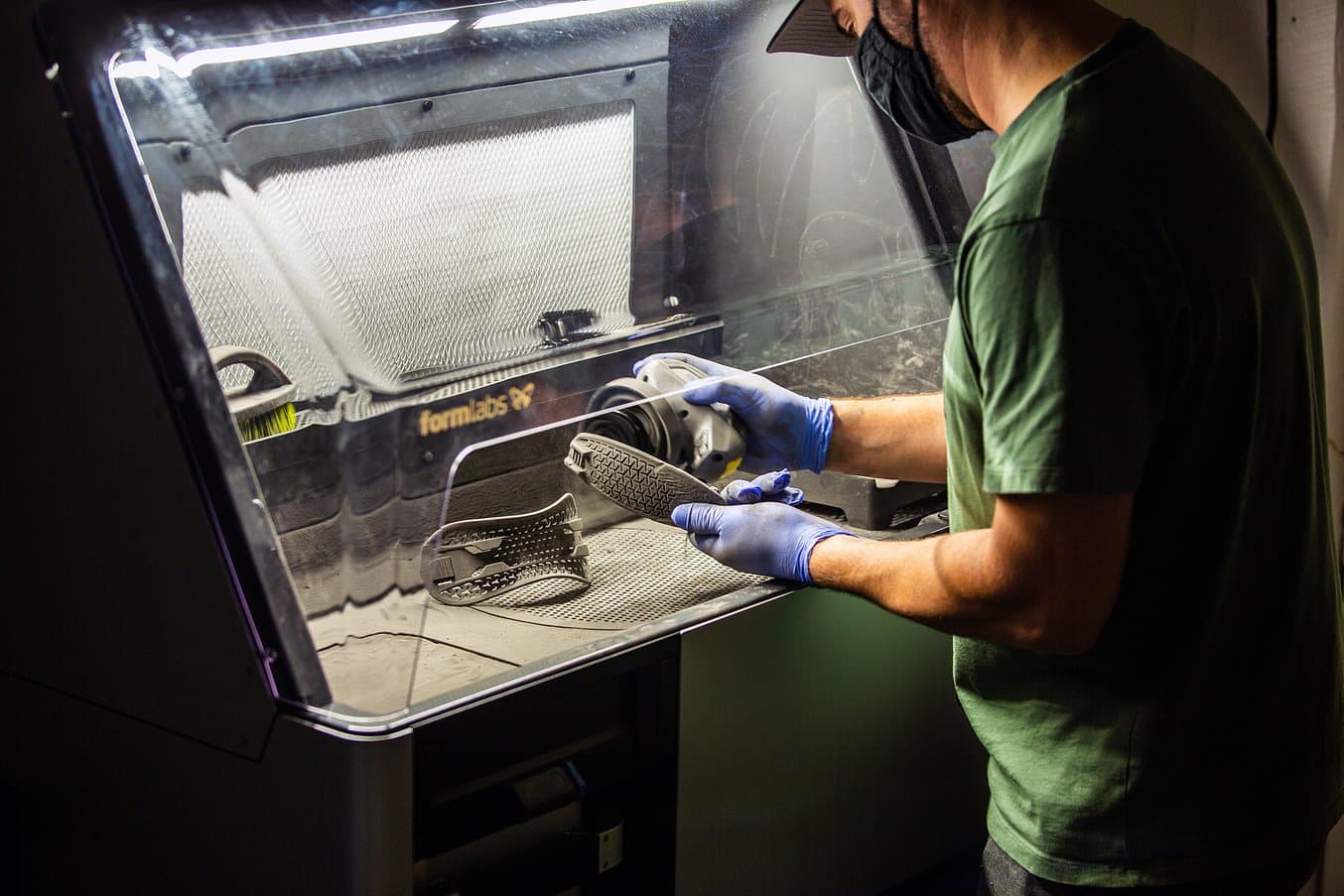
The Fuse Sift machine simplifies the powder removal, recycling, and mixing workflows.
For large traditional SLS systems, the printer and post-processing machine require a dedicated technician to operate them, and in some cases, additional units are needed for powder recycling steps. For these traditional SLS systems, both printer and post-processing machine also require at least a full working day of cleaning and depowdering before switching to a new type of powder. Cost calculations should factor in both the additional labor time as well as the loss in potential production during the downtime necessary for cleaning. The Formlabs Fuse Series system requires only four hours when switching between Nylon 12 Powders and Nylon 11 Powders, and half that when switching between materials using the same base component, e.g. between Nylon 12 Powder and Nylon 12 GF Powder.
Low-cost SLS options, like some DIY solutions, have no post-processing accessories, and thus require much more time spent by an operator on depowdering, mixing, recycling, and labor. Their less intuitive workflows also create many ongoing manual tasks.
The Formlabs Fuse Series printers combine the streamlined workflow of traditional SLS with the manageable footprint of less expensive options. The Fuse Series printers and Fuse Sift can slot in easily to an existing workspace, and the Fuse Sift makes depowdering, recycling, all powder management tasks easy and intuitive, freeing up time for more important tasks.
SLS 3D Printing ROI Calculator
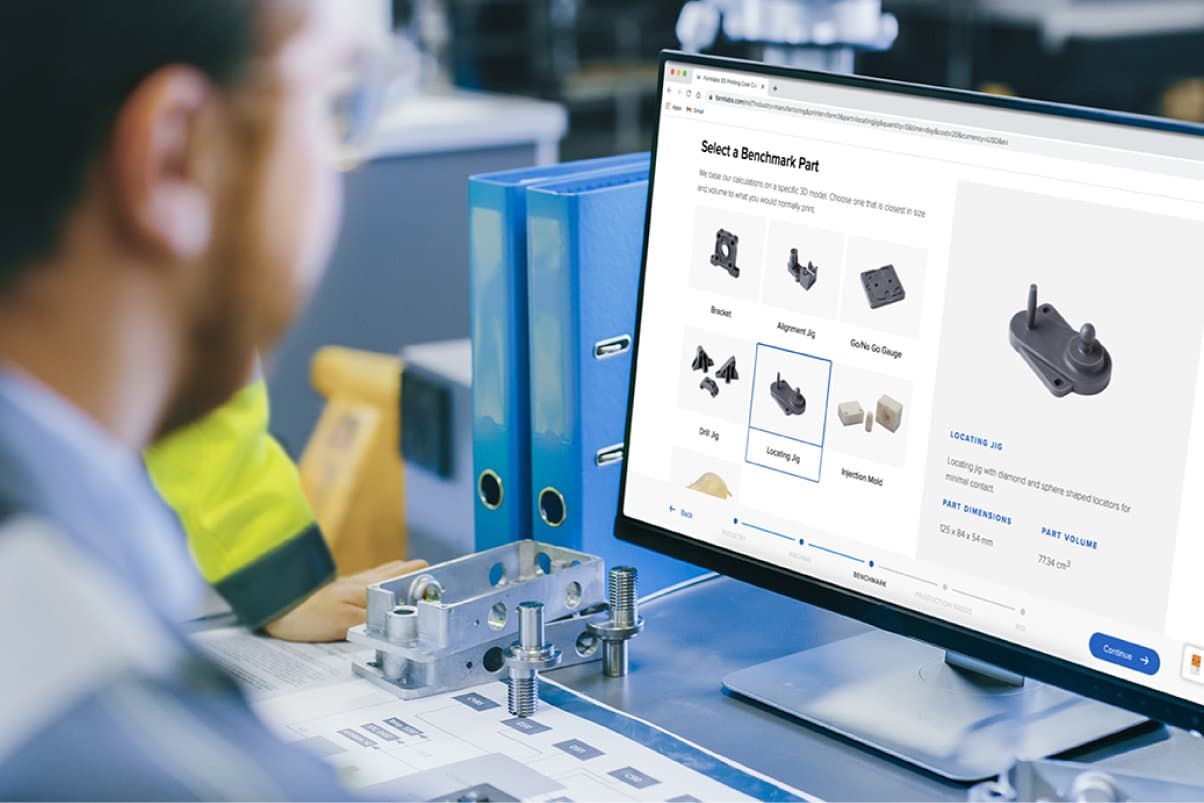
The Formlabs ROI calculator makes budgeting for an SLS 3D printer easy by breaking down the purchase price of hardware, materials, labor, and all other costs, and calculating the cost per part based on a certain production volume. You can also use the tool to compare time and cost savings with SLS 3D printing versus alternatives like outsourcing or other production methods.
SLS 3D printing: In-House vs. Outsourcing
SLS is an ideal way to prototype functional, strong, and industrial-quality parts quickly and inexpensively, and to manufacture low volume or custom end-use parts. Many manufacturers, engineers, and product designers are already relying on SLS parts, whether they produce them in-house or through a service bureau.
For the majority of the time that the technology has been available, outsourcing was the only way to get SLS parts for most businesses—it was simply too expensive to afford an in-house unit for all but the largest manufacturers. And even now, outsourcing SLS 3D printing can be advantageous in certain scenarios, namely for one-off parts or when a new company simply does not have enough funding to purchase a powerful SLS 3D printer. Service bureaus can provide a stopgap solution for prototyping or even very low volume production. But now that in-house, high-quality SLS is within reach, it’s worth looking into the cost of SLS 3D printing for small and medium manufacturers as well.
An in-house Fuse 1+30W printer can be purchased for one-tenth the cost of traditional SLS systems, creating an opportunity to gain control of more of the manufacturing process. Once established in-house, Fuse Series printers often deliver a positive ROI in as little as five weeks for production cases, and two to three months for prototyping. Businesses can eliminate their reliance on outsourcing, speed up their prototyping or low-volume production, and reduce variables like shipping time in their timelines. In a recent whitepaper, we analyzed six different prototyping and production scenarios to determine exactly how quickly businesses can pay off the cost of the Fuse 1+ 30W by printing in-house, such as the following:
Prototype: Power Drill Casing
Material: Nylon 12
Build: Two parts for each assembly, four total parts
Fuse 1+ 30W In-House | Service Bureau SLS | |
---|---|---|
Print Time | 13h 10m | |
Cooling | 13h 45m | |
Sift Time (labor time for post-processing) | 40m | |
Total Time | 27h 35m | 7-10 business days |
Materials Cost | $50 | |
Labor Cost | $11.22 | |
Total Cost | $61.22 | $752.50 |
Cost Per Part | $15.31 | $188.13 |
The total time required to produce these prototypes would allow in-house SLS users to run five full production runs each week, printing ten iterations of the two-part drill casing assembly. Compared to a single iteration every two weeks when outsourcing, an in-house SLS printer opens up opportunities for true iteration. Each new model could have a different aesthetic, alternatives for the grip’s design, or screw threads placed in different spots, and then be presented physically to an approval team the very next day.
The savings when compared to a service bureau are close to $700, which equals over 90% savings for each round, meaning a Fuse 1+ 30W user could achieve positive ROI in just over three months and a little over one year if it’s used just once a week.
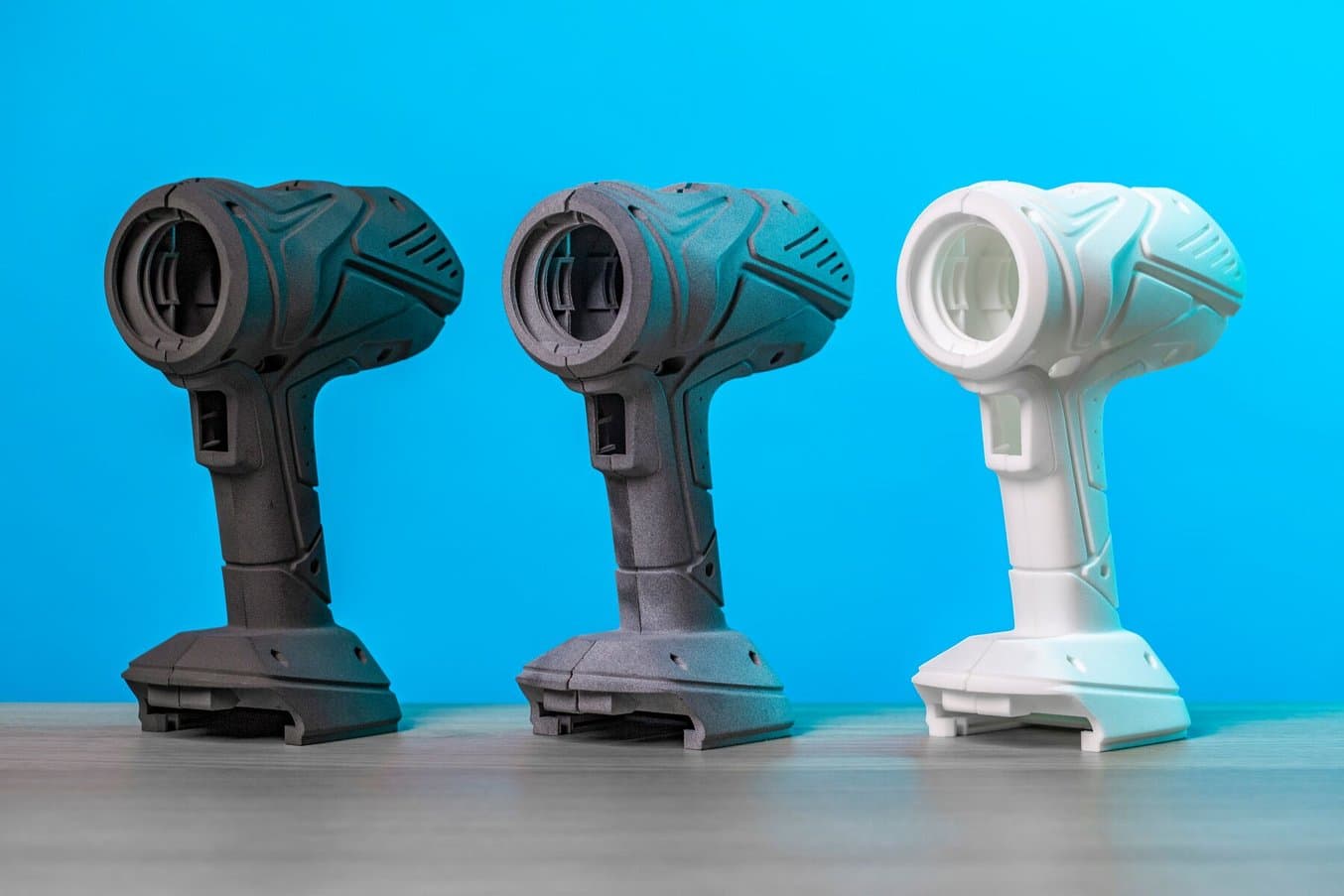
The prototype drill, printed on an in-house Fuse 1+ 30W printer (left), and ordered from a service bureau with an MJF (HP) printer (center), and an SLS (EOS) printer (right).
However, not only rapid prototyping applications created such fast positive ROI. In our whitepaper we also analyzed the savings created by in-house low volume end-use parts and manufacturing aids, finding that the savings created by making these in-house paid off the cost of the printer in similarly quick timelines.
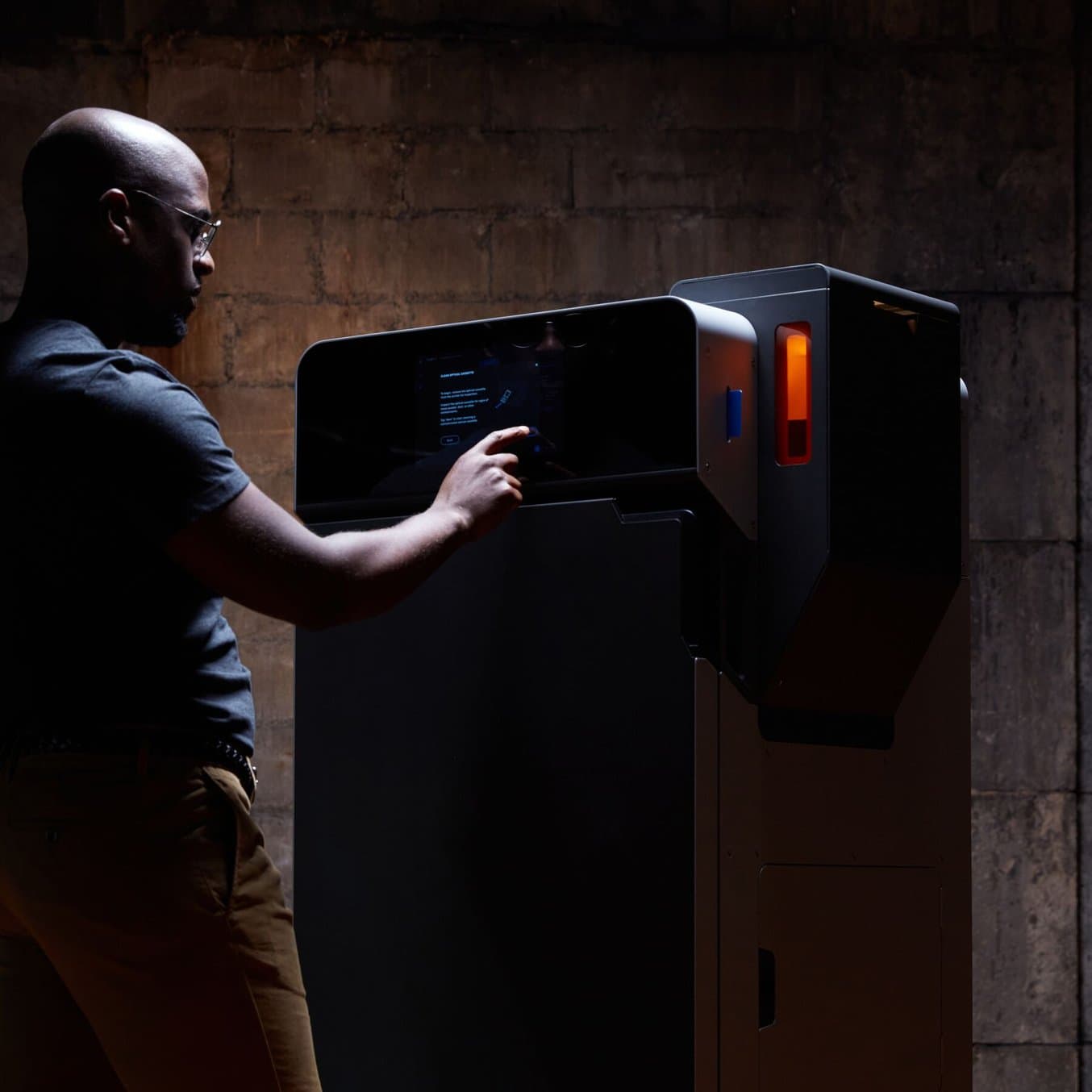
Outsourcing vs. In-House: When Does it Make Sense to Bring SLS 3D Printing In-House?
In this white paper, we evaluate the value proposition of bringing SLS 3D printers in-house, in comparison with outsourcing SLS parts from a service bureau.
Conclusion
SLS 3D printing used to be too expensive for most businesses to bring in-house—both due to the cost of the hardware itself as well as the ongoing costs of materials, service plans, and maintenance needs.
Now, SLS in-house is within reach, with accessible hardware costs, and streamlined workflows that reduce continued operating costs. While it’s still a more expensive technology than FDM or SLA, SLS 3D printers have enormous potential for manufacturers to create value. The high throughput and outstanding part quality enable businesses to shorten the time to market through rapid iteration and low-volume production, and reduce reliance on external manufacturers for tooling and replacement parts. Fast, efficient, and high-quality 3D printing can pay back the cost of the printer quickly, especially when compared to other solutions like outsourcing.
The Formlabs Fuse Series printers produce parts of comparable quality as traditional large SLS machines, with affordable prices, similar material selections, and more efficient powder recycling systems. Both in terms of upfront printer price and ongoing costs, Fuse Series printers are the most accessible way to bring high-quality, industrial-grade parts in-house.