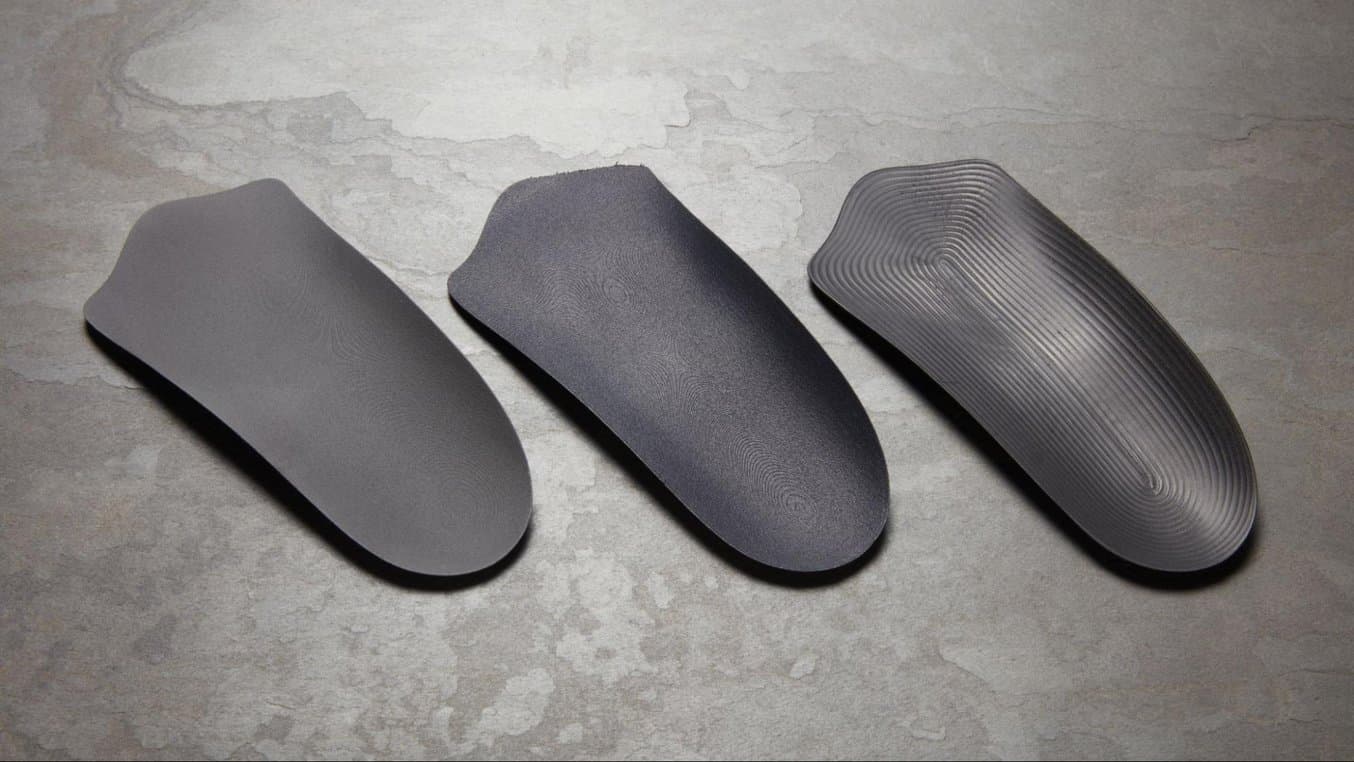
Insole shell samples used in external mechanical property testing. From left to right: Formlabs Nylon 11 Powder, HP PA 11, CNC’d polypropylene.
The Fuse 1+ 30W and Nylon 11 Powder lend themselves particularly well to manufacturing the custom rigid shell layer of orthotic insoles. In order to learn how our manufacturing method compares to other industry options, and confirm that our material exceeds the demands of daily wear, we conducted a series of mechanical property tests.
External testing was conducted by the Orthopaedic Innovation Centre and included a Static 3-Point-Bending test, a Dynamic 3-Point-Bending test, and a Ross Flex test. The same tests were also conducted on insole shells CNC machined from polypropylene and 3D printed in PA 11 using an HP multi-jet fusion (MJF) machine. Internally, we also challenged the durability of our angled prints with a series of 180° hand flexion tests.
Read on for a quick overview of the testing and the results and download our mechanical performance analysis white paper for the detailed results.
Overview of Testing Methods
Per the recommendation of industry professionals, we decided to do Static and Dynamic 3-Point Bend testing, and Ross Flex testing. The Orthopaedic Innovation Centre (OIC) conducted these tests on our samples, as well as two other samples; PA 11 from HP and CNC’d polypropylene.
-
Static 3-Point Bend Testing was conducted to 60° of flexion (approximately 40 mm of displacement), far exceeding the expected 20-30° of flexion expected for normal use. This test produces data on the relative arch stiffness of the insole shell.
-
Dynamic 3-Point Bend Testing was chosen to model harsh daily use and give an idea of overall durability by repeatedly displacing each insole shell by 5 mm. For comparison purposes, the non-Formlabs samples were tested up to 2 million cycles (a standard tested by HP in previous testing with OIC). The Formlabs samples were tested up to 4 million cycles to model significantly above-average usage over the course of one year.
-
Ross Flex Testing was used to demonstrate the insole’s flexural endurance by bending it 1.5 million times between 0° and 90°- another value far exceeding expected use.
In addition to formal testing at OIC, Formlabs conducted internal flexion tests to 180° by hand on sample insole shells printed at angles 0°-50° from the build volume floor. This test aimed to demonstrate that rigid insole shells printed within this recommended range of angles can reliably withstand forces far greater than expected for daily use.
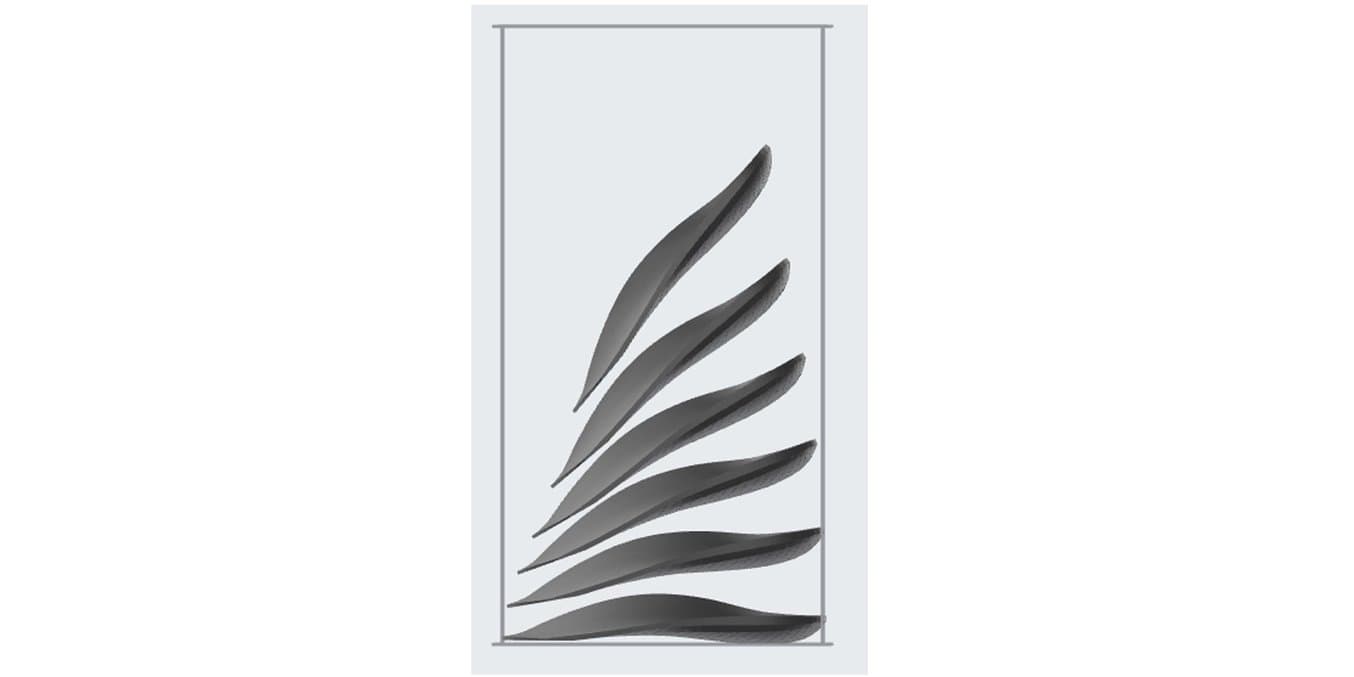
Insole shells angled from 0°-50° from the floor of the build chamber in PreForm.
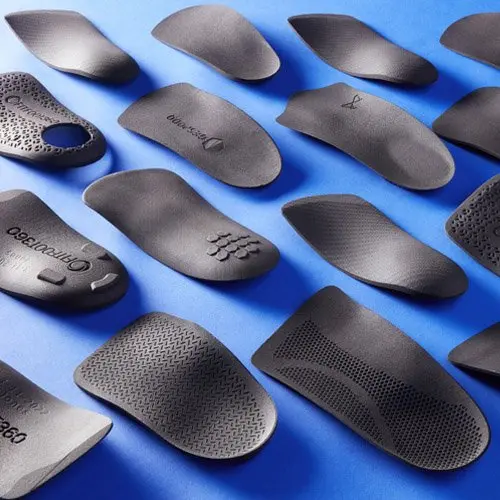
3D Printing Rigid Insole Shells
Learn how to produce strong, ductile insole shells exceeding 4 million bend cycles with Formlabs’ compact, affordable SLS ecosystem. This comprehensive guide will help you hit the ground running with insole shell production on the Fuse 1+ 30W.
Results Overview
Static 3-Point Bend
No insoles failed upon displacing 40 mm. The ranking of most to least flexible is as follows: Formlabs, HP, and Polypropylene. Having the highest ranking of flexibility means that the Formlabs samples are the most durable of those tested, and the least likely to be damaged by heavy use.
40 mm displacement of Formlabs sample.
Dynamic 3-Point Bend
All samples survived displacement of 5 mm to 2 million cycles. The Formlabs sample survived an additional 2 million cycles (4 million total) with no signs of damage, representing durability far exceeding the physical demands of daily wear over the course of one year, even for a particularly active individual taking 10,000 steps per day.
Ross Flex Test
All samples survived 90° flexion more than 1.5 million times. The Formlabs samples demonstrated greater energy return than the HP samples, indicating greater comfort for the patient.
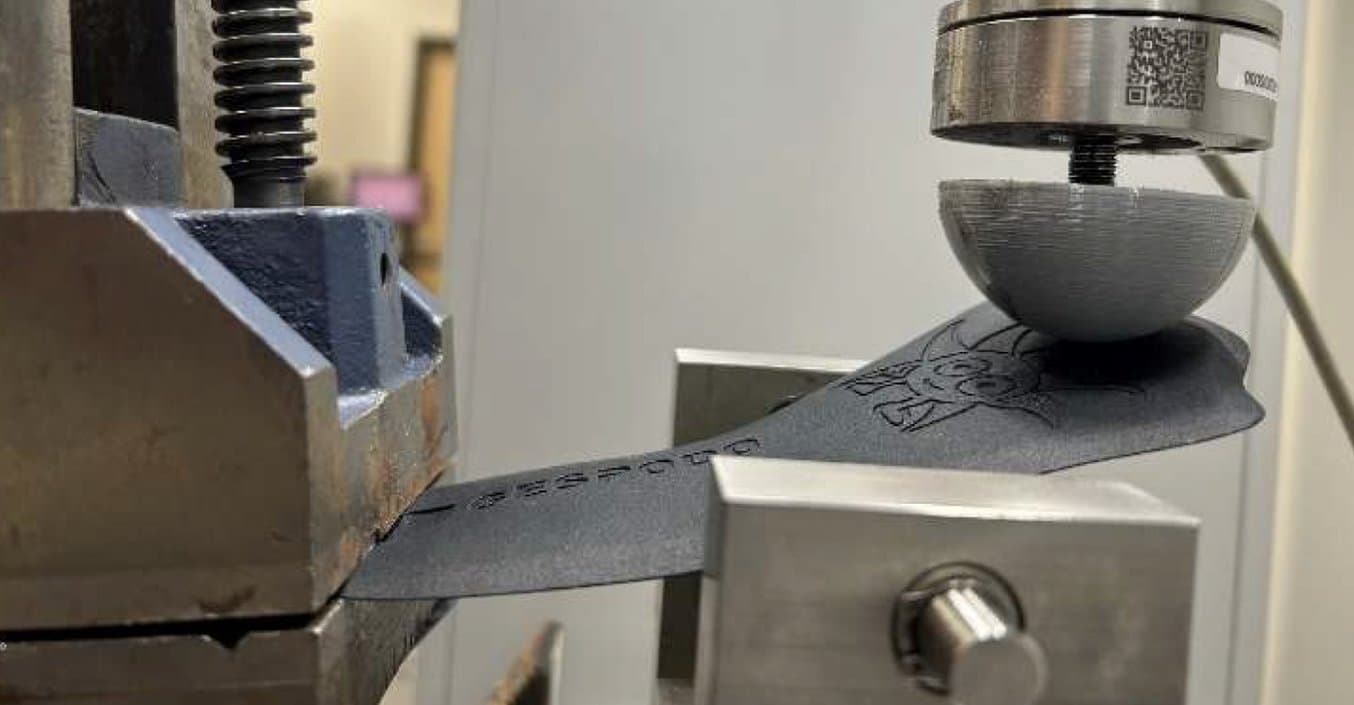
Cyclical 90° bend of Formlabs sample.
Flexion Test
All samples printed within 0°-50° from the build volume floor survived rigorous bending to 180° and back by hand. These results demonstrate the durability of prints completed at 50° or less.
Samples exposed to 70% humidity for 24 hours prior to testing performed no different than samples exposed only to ambient air (30-50% at our testing location).
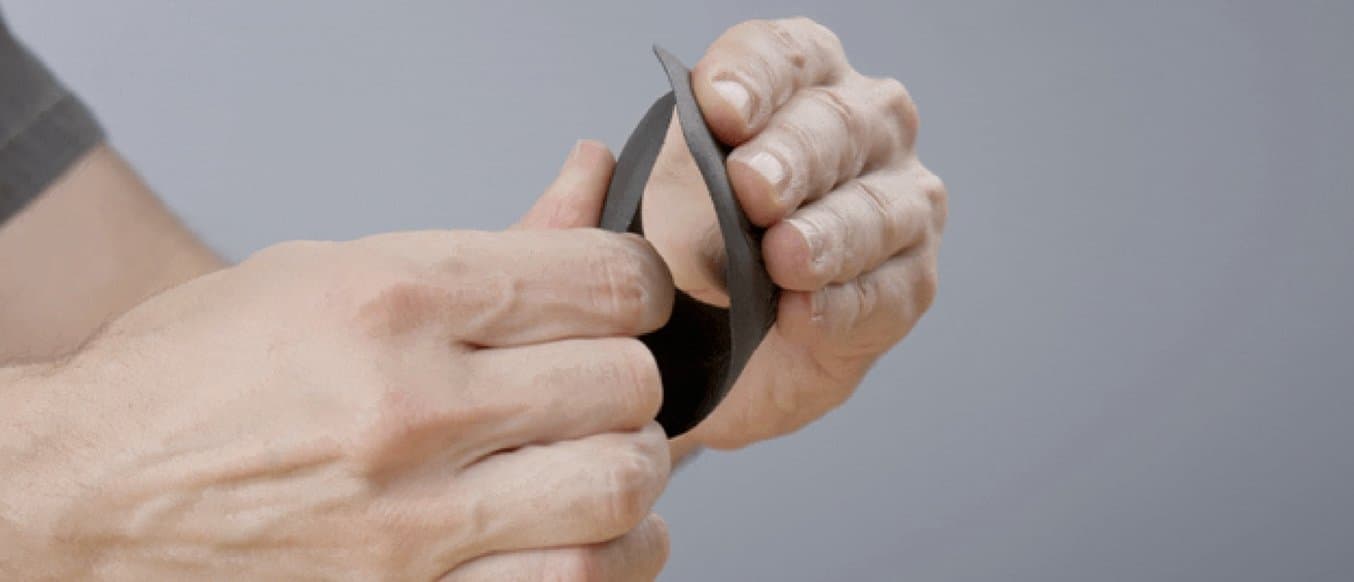
180° flexion of a sample printed at 50° from the build volume floor.
Get Started With 3D Printed Insoles
Download our mechanical performance analysis white paper for the detailed results or contact our medical 3D printing experts if you have any questions about 3D printing insoles using Formlabs’ 3D printing solutions.