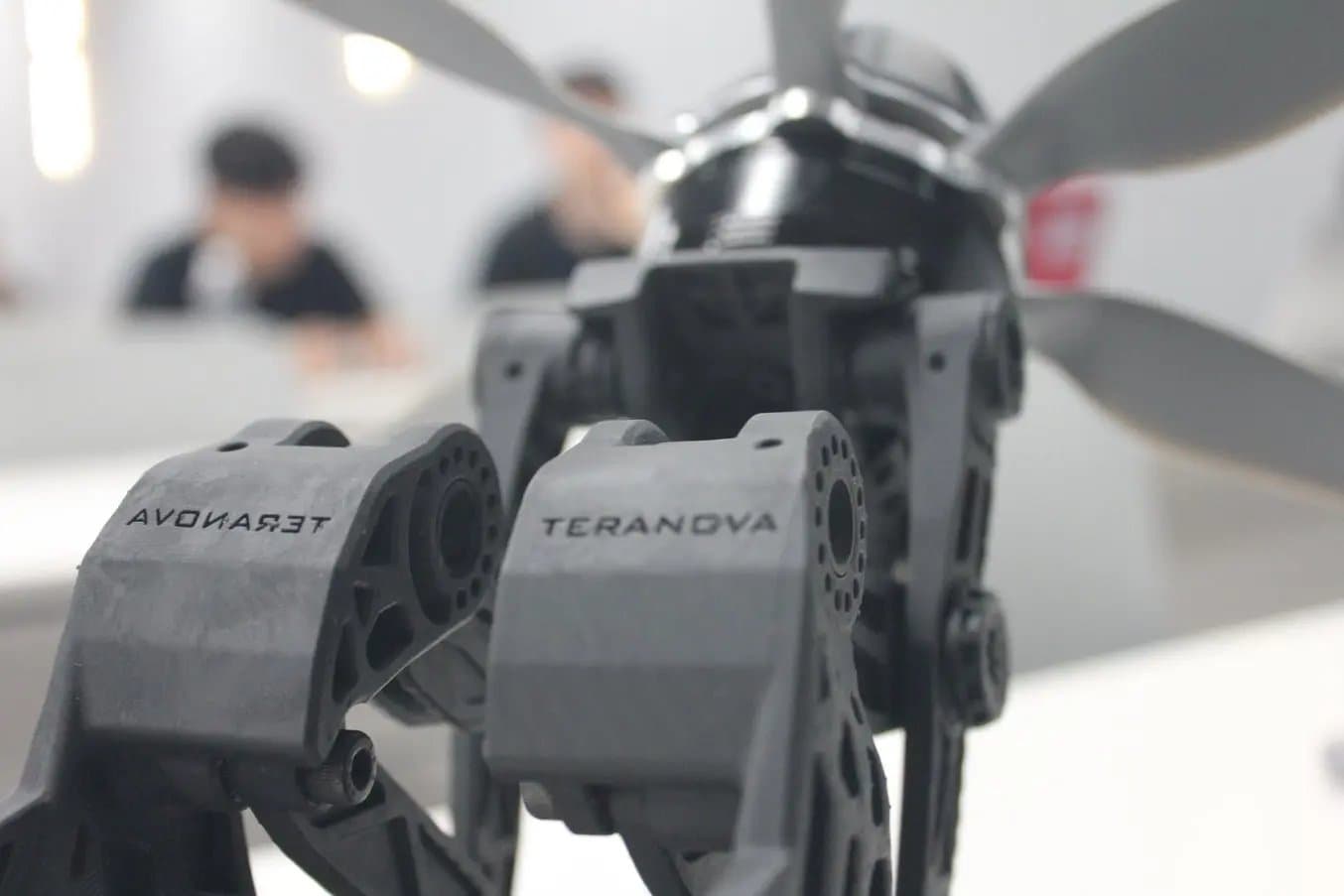
How 3D Printing Powers Teranova's Mission to Deliver Up to 1 Ton of Cargo
Based in Incheon, South Korea, Teranova is leading the charge in urban air mobility (UAM), a transformative transportation system that moves people and cargo above cityscapes while encompassing vehicle development, infrastructure, platforms, services, and maintenance. Among its innovative pursuits, logistics delivery has emerged as a cornerstone of its business model. To bring this vision to life, Teranova relies heavily on 3D printing technology to produce prototypes and develop advanced motor technologies. The company has set its sights on delivering up to 1 ton of cargo via UAM vehicles, a goal that demands constant prototyping and iteration. By embracing 3D printing as a critical tool, Teranova has ensured it stays at the forefront of technological innovation.
Initially, the company used FDM (Fused Deposition Modeling) printers for their cost-effectiveness, but these printers fell short in delivering market-ready prototypes due to limitations in speed, material variety, and surface finish quality. The adoption of SLA (Stereolithography) printers marked a turning point, offering significant advantages in aesthetics, precision, and speed. Teranova ultilized SLA printers for intricate designs and refined appearances, optimizing its prototyping process and driving innovation in UAM logistics.
Form 4, Redefining 3D Printing with Speed, Durability, and Convenience
When Teranova’s previous FDM and SLA 3D printers began delivering high failure rates, the company needed a solution that could balance speed, cost, and quality. Enter the Form 4. Its intuitive interface and advanced functionality provided a seamless user experience, leaving a lasting impression on Teranova’s team.
One of the Form 4’s standout features was its exceptional success rate. Teranova’s previous resin printer struggled with a 70% success rate, but the Form 4 achieved an impressive 90%, with the few failures largely due to user errors rather than hardware issues. This leap in reliability reduced material waste and accelerated part production, enabling faster project completion. The printer’s large touch screen and built-in leveling system made setup effortless, while automated systems like dashboards and temperature control streamlined every stage of the printing process. Even traditionally time-consuming tasks, such as cleaning and resin mixing, were simplified without compromising quality, making the Form 4 a game-changer for urban air mobility applications where precision and reliability are critical.
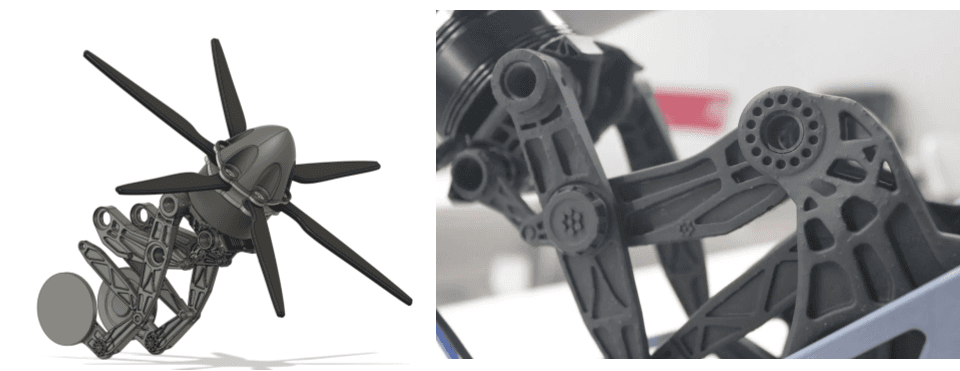
The Power of LFD Technology and Advanced Materials
Initially, Teranova approached the Form 4’s Low Force Stereolithography (LFD) technology with curiosity, but it quickly became clear how revolutionary it was. Using a backlight device, LFD projects a high-intensity, uniform beam of light through a Light Processing Unit (LPU) equipped with polarizers, optical coatings, and a custom LCD. This process results in layers with exceptional detail, smooth finishes, and precise tolerances. Combined with high-resolution LCD technology and anti-aliasing, the Form 4 delivers flawless prints with outstanding surface quality and durability.
The Form 4’s capabilities were further enhanced by its advanced materials. Teranova utilized Black Resin V5 and Tough 2000 Resin to create robust prototypes. Black Resin V5 provided excellent durability and low distortion, enabling injection-molded finishes that closely matched design intentions. With the Form 4 ecosystem, printing with Black Resin V5 was three times faster than with earlier versions. Tough 2000 Resin lived up to its name by offering unmatched strength and rigidity, making it ideal for producing resilient and long-lasting parts. These materials, combined with the Form 4’s advanced features, empowered Teranova to consistently exceed expectations in quality and performance.
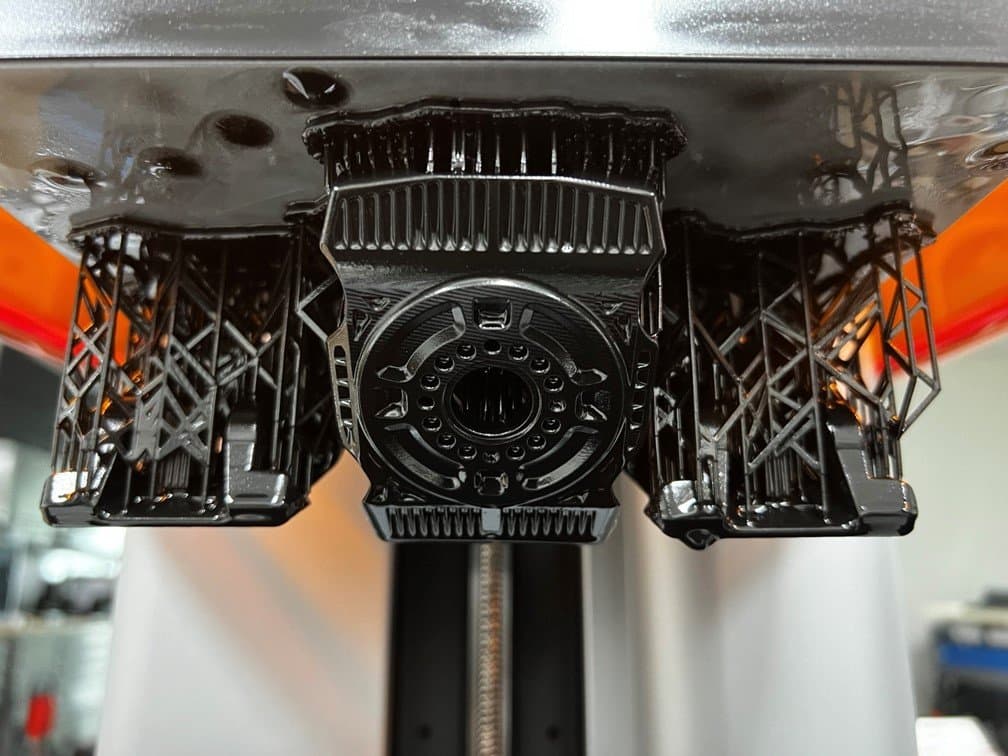
Teranova’s Vision for the Future: Harnessing 3D Printing for Aerospace Innovation
Teranova’s ambitions are as lofty as the skies it seeks to conquer. As a forward-thinking aerospace company, it has established vertical integration, managing everything from research and development to design and manufacturing. With a meticulous step-by-step approach, the company is targeting the launch of its prototype aircraft by 2026. Focused on advancing Personal Air Vehicles (PAV) and Advanced Air Mobility (AAM), as well as developing simulators for flight evaluation and remote control systems, Teranova prioritizes the stability and quality of its products. To achieve these high standards, the company has embraced 3D printing as a cornerstone of its production process, enabling the creation of superior aircraft components.
Looking ahead, Teranova plans to expand its use of Formlabs products to support its innovative designs. Unlike companies that rely on off-the-shelf parts, Teranova develops and manufactures its own components, making 3D printing an essential part of its strategy. One of its key initiatives is using Rigid 10K resin to produce molds, which will later be utilized for injection molding production. Additionally, the company is preparing to manufacture testing devices through advanced 3D printing techniques, further streamlining its development process.
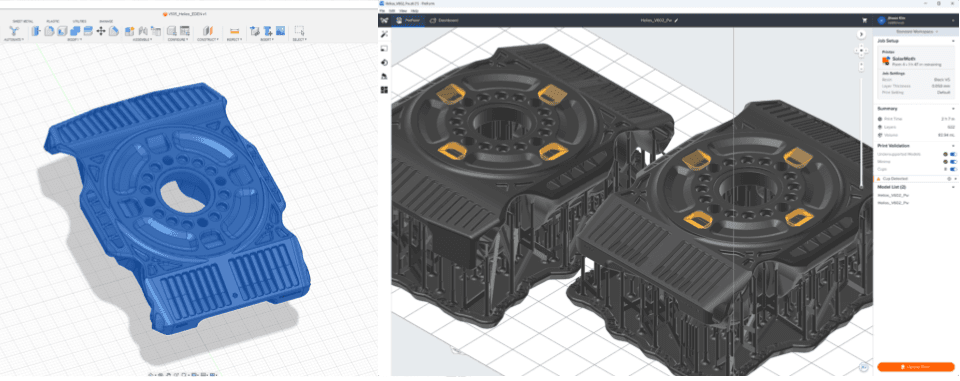
Kim CTO, Teranova
"LFD technology has been a game-changer for us, delivering stable and reliable performance. In aircraft manufacturing, where precision is everything, it ensures error-free production every time."
Teranova’s commitment to innovation doesn’t stop there. The company is preparing to integrate the Fuse 1+ 30W system into its production line. This cutting-edge 3D printer will allow Teranova to independently produce critical components, such as landing gear parts, showcasing its dedication to precision and reliability. By bringing more of its manufacturing capabilities in-house, Teranova is solidifying its position as a leader in aerospace innovation.
Handling complex, cutting-edge technologies requires an unwavering focus on error-free development and production. By partnering with reliable 3D printing solutions like the Form 4, Teranova ensures consistent quality and performance, even in the most demanding applications. With these advanced tools, the company is poised to achieve its ambitious goals, building a future where precision-engineered aircraft take to the skies with confidence.
This user story was provided by Formlabs’ authorized partner, AM Plus.