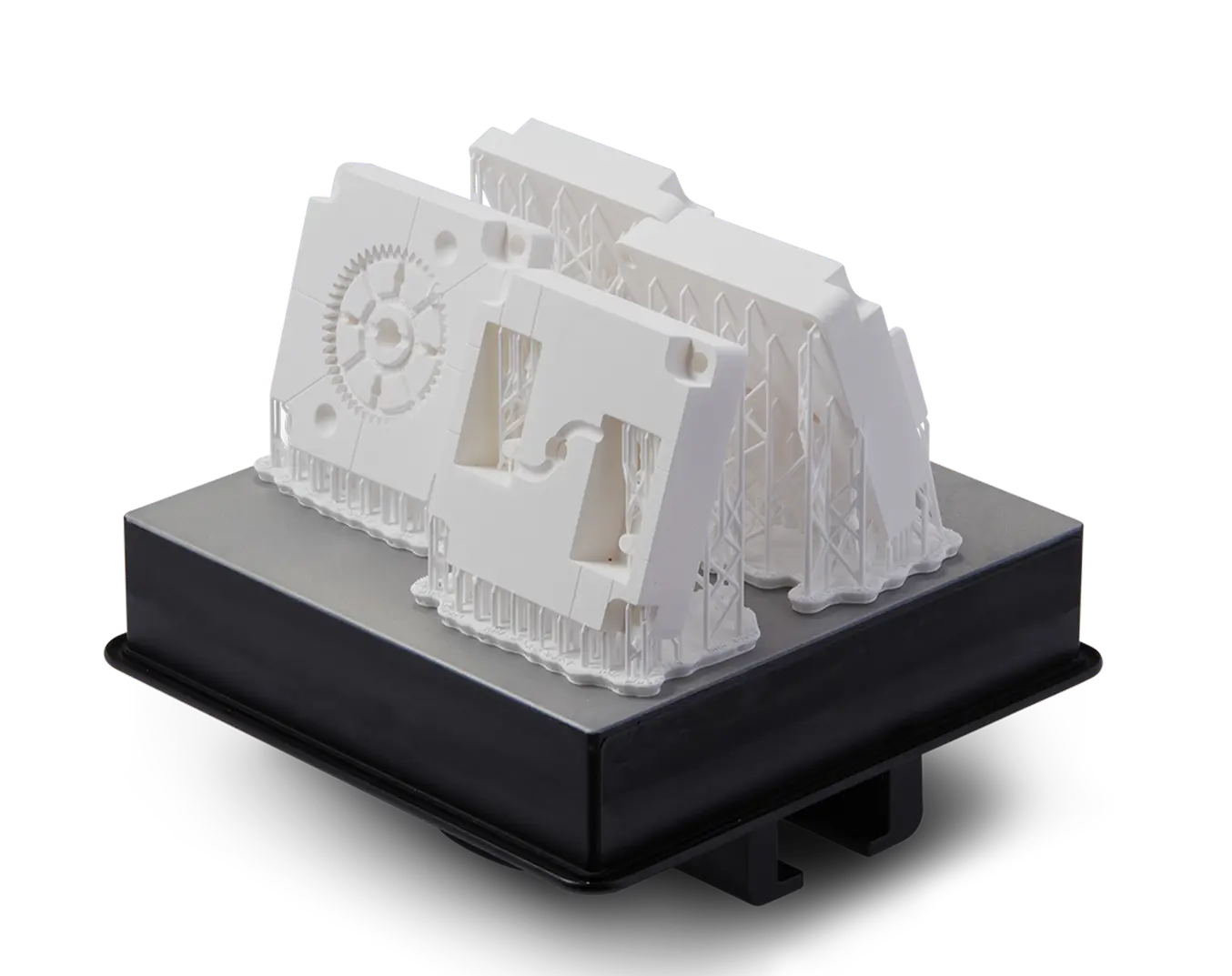
Why Choose Rigid 10K Resin?
Rigid 10K Resin is a high performance material that is strong, completely stiff, and stable.
Extremely Stiff
Resistant to deformation under a variety of forces, pressures, and torques.
High Thermal and Chemical Resistance
Withstands high temperatures and a variety of chemicals.
Precise
Produce strong, detailed, and accurate molds or models.
Incredible Surface Quality
Exhibits a smooth matte finish.
Applications
Rigid 10K Resin is ideal for creating rigid, strong, industrial-grade prototypes. Rigid 10K Resin can be faster and easier to print compared to milling aluminum and steel.
Consider Rigid 10K Resin for:
Material Properties*
Rigid 10K Resin
Ultimate Tensile Strength
Tensile Modulus
Elongation
Flexural Modulus
Notched Izod
Heat Deflection Temp. @ 0.45 MPa
Thermal Expansion, 0-150 °C
* Data was obtained from parts printed Form 3, 100 µm and post-cured with a Form Cure for 60 minutes at 70°C.
Post-Processing
Form Wash Settings
10 minutes + 10 minutes in IPA
Rigid 10K Resin contains glass particles, which strengthens printed parts. Maintain separate wash buckets to prevent glass particles adhering to parts printed with other resins. Parts with two wash times require two wash cycles. For the second wash cycle, use clean solvent. The first wash cycle removes the bulk of the resin, while the second cycle fully cleans the parts.
Form Cure Settings
60 min
70 °C
For parts printed in an engineering-focused resin (such as those in the Rigid, Tough & Durable, and Flexible & Elastic families), post-curing ensures that the parts reach their optimal mechanical properties and can function as designed. There is only one recommended post-curing time for Rigid 10K Resin V1. Optionally, after post-curing, heat the printed part in a non-food oven at 90 °C for 125 minutes for a higher heat deflection temperature.