How Sirris Transformed Custom Electric Dirt Bike Suspensions With Form 4L and Tough 1500 Resin V2
In 2024, for the first time, the 120-mile Mint 400 race was open to electric dirt bikes, and Sirris, a pioneering manufacturer specializing in high-performance suspension for electric dirt bikes, needed to upgrade the fork guards on their bikes to withstand the unforgiving desert terrain. With limited time to prototype and manufacture, they turned to 3D printing.
“What truly sets this project apart is the remarkably fast transition from concept to execution. While similar projects might take 6-12 months for other companies, this entire journey — from idea to race — was completed in just a matter of weeks.”
Josh Doolittle, Creative Director, Sirris
Combining the robust Tough 1500 Resin V2 and Form 4L stereolithography (SLA) 3D printer, Sirris was able to prototype and manufacture end-use parts in time for the Mint 400 race without investing in expensive tooling.
“We can now bridge the gap between prototyping and full production, allowing us to deliver functional parts to customers without waiting for tooling.”
Jon Howard, Co-Founder and Operations, Sirris
Faster Prototyping With Form 4L
Dirt bikes require precision-engineered suspension systems to handle aggressive terrain, jumps, and impacts. Fork guards protect stanchions from debris, which could cause oil leaks and ultimately result in suspension failure. These guards need to be robust, withstanding flying rocks, debris, and impact.
Sirris began experimenting with fused deposition modeling (FDM) for prototyping, and has also used selective laser sintering (SLS) 3D printing in the past. However, SLS and FDM-printed parts can’t withstand functional testing on an off-road dirt bike. Unlike FDM parts, SLA 3D printed parts are isotopic, meaning there is no difference between X, Y, or Z planes. Additionally, tough, robust materials that can withstand functional prototyping are available for SLA 3D printing.
“3D printing provides instant access to functional prototypes. Our products need to withstand harsh off-road conditions, being able to iterate based on real-world testing — within days rather than weeks — is invaluable.”
Jon Howard, Co-Founder and Operations, Sirris
Form 4L, Formlabs’ large-format SLA 3D printer, has the build volume to print a pair of fork guards, and the speed to enable two to three iterations a day that can then be tested on actual bikes. This rapid speed enabled Sirris to 3D print robust, functional prototypes that could be tested off-road.
“With the Form 4L, we’re just scratching the surface of what’s possible. The ability to customize and iterate quickly gives us a significant edge in the market.”
Jon Howard, Co-Founder and Operations, Sirris
Rugged Enough to Race: Tough 1500 Resin V2
“Tough 1500 Resin V2 has the right balance of impact resistance and flexibility, making it durable enough for real-world use.”
Jon Howard, Co-Founder and Operations, Sirris
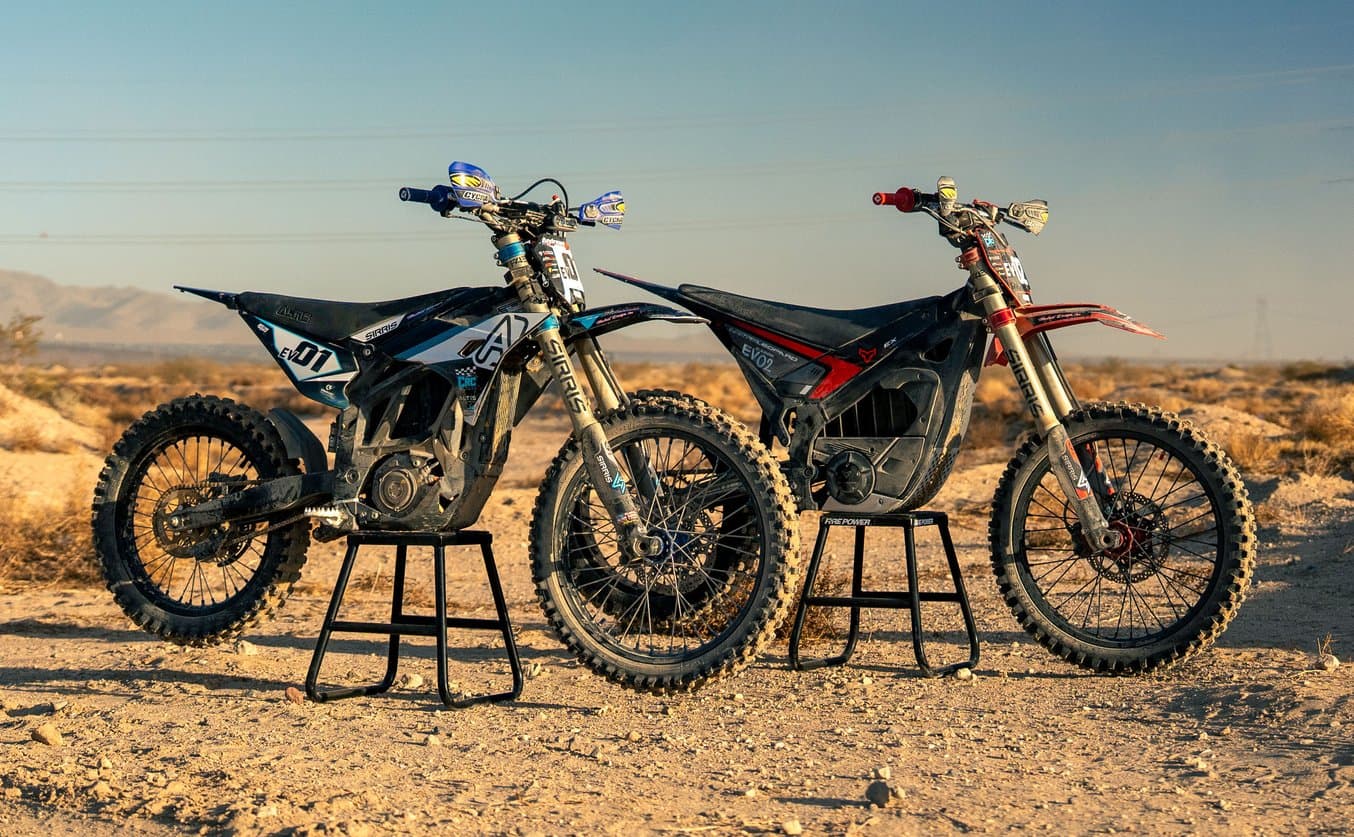
3D printed parts were put to the test by riders.
Sirris initially began printing functional prototypes with Tough 1500 Resin V1. However, with the launch of Tough 1500 Resin V2 in March 2025, they transitioned to the tougher material. Tough 1500 Resin V2 rivals the mechanical properties of polypropylene, with a 10x higher work of fracture than Tough 1500 Resin V1 and a 3x higher Gardner impact strength, making it well-suited for Sirris’ rigorous demands.
With such a durable material, Sirris can not only 3D print functional prototypes, but also produce custom or low volumes of end-use parts.
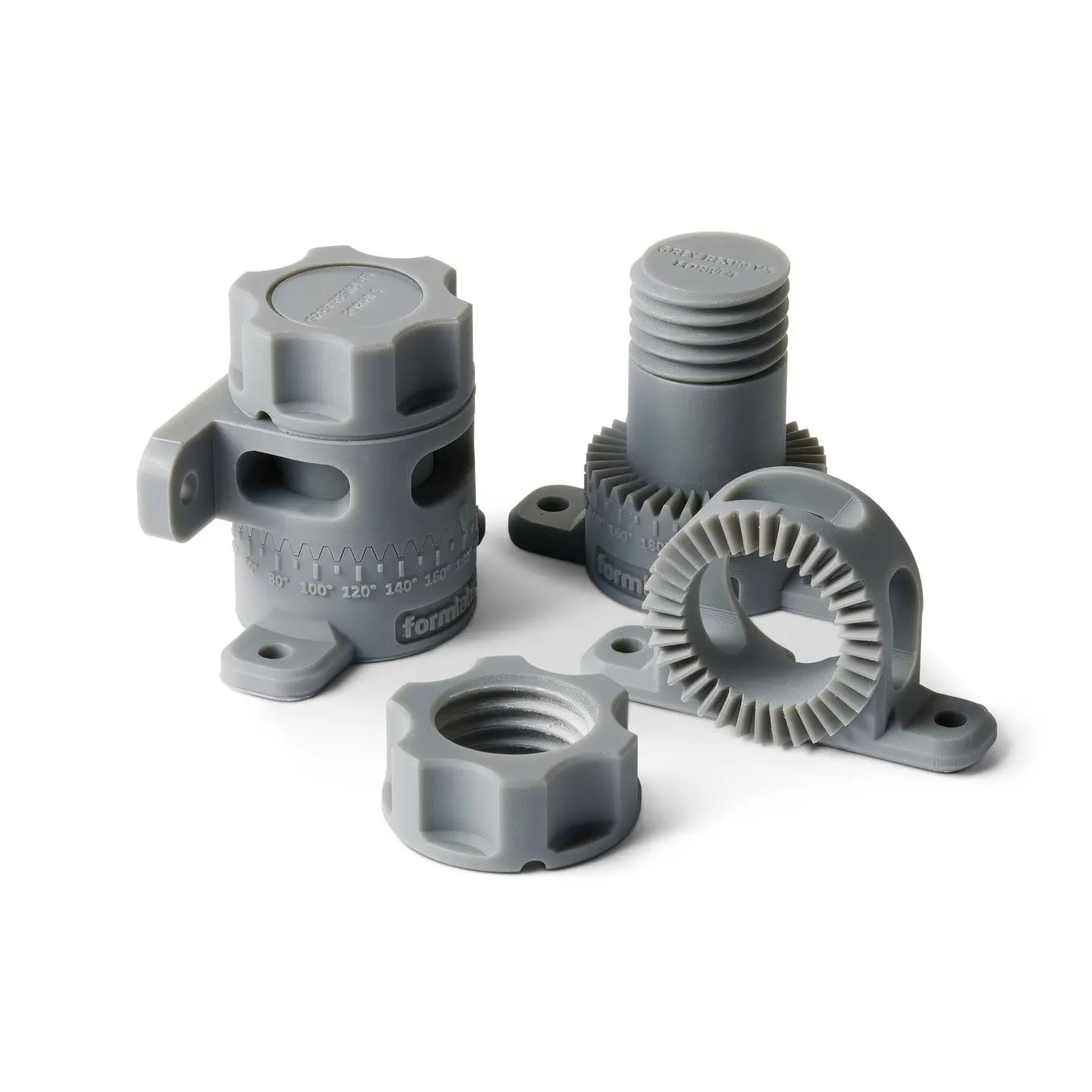
Request a Free Sample Part
See and feel Formlabs quality firsthand. We’ll ship a free 3D printed sample part to your office.
Producing End-Use Parts That Podium
Injection molding requires significant upfront tooling costs — from $6,000-$28,000 depending on the part complexity — plus lengthy production cycles and minimum orders. Sirris needed to produce 50 fork guards per week, with the potential to make adjustments as they continued to optimize the design.
Lead Time | Modifications | Material | |
---|---|---|---|
3D Printing With Form 4L | One day | Yes, from print to print | Tough 1500 Resin V2 |
Injection Molding | ~8-10 weeks | Difficult, expensive, or not possible | Polypropylene |
“With 3D printing, we can produce guards on demand with no tooling delays. A single batch can be printed in ~13 hours, meaning we can fulfill low-volume production needs in days instead of weeks.”
Jon Howard, Co-Founder and Operations, Sirris
Manufacturing fork guards with 3D printing is less costly than injection molding for short timelines and when adjustments may still be needed. As Howard says, “Since the E-Moto market is evolving rapidly, our ability to quickly test new concepts, validate fitment, and assess durability gives us a competitive edge.” Only once the design is locked in and larger production runs are required does it make sense to manufacture with injection molding.
Racing 120 Miles: The Mint 400 Test
The Mint 400 is one of America’s toughest off-road races, spanning 120 miles of grueling desert terrain. In a historic first, electric dirt bikes competed, including some equipped with custom Sirris F43 suspension forks and 3D printed fork guards.
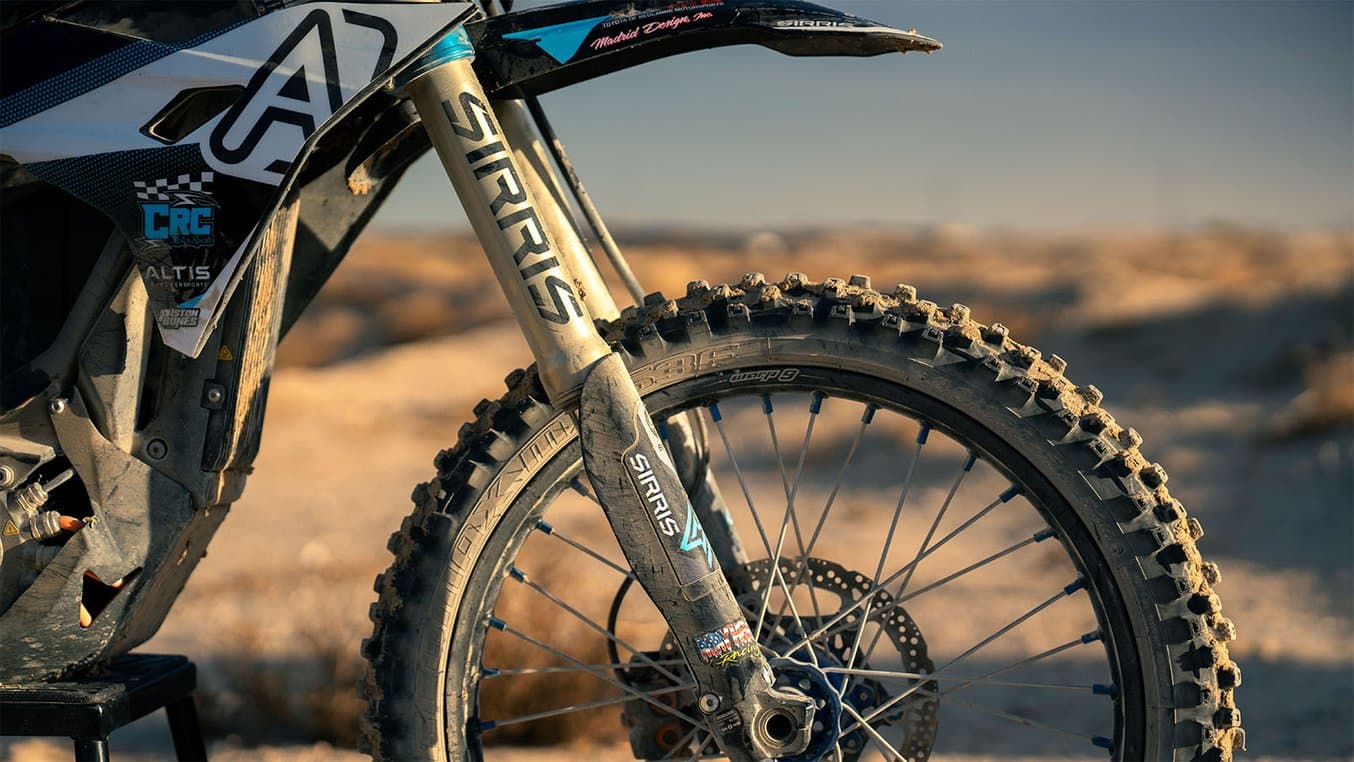
The 3D printed fork guards held up to the rugged desert conditions of the Mint 400 race.
Upon examination post-race, the guards showed no wear from their 120 miles of racing, the Tough 1500 Resin V2 parts withstanding the rigors of the desert course.
“Formlabs’ cutting-edge 3D printing technology enabled the creation of custom plastic fork guards, a key component that not only helped the motorcycles compete but also ensured their successful finish in this landmark race.”
Jon Howard, Co-Founder and Operations, Sirris
Looking Ahead: Future Innovations and Expansion
With the success of the custom suspension parts printed on Form 4L, Sirris is expanding their custom options, exploring selective laser sintering (SLS) 3D printed parts using Nylon 12 Tough Powder with Fuse 1+ 30W. Additionally, they plan to investigate 3D printed molds in Rigid 10K Resin for low-volume productions, offering even greater flexibility and efficiency in their manufacturing processes.
Explore Form 4L to start printing or contact sales to learn more. To evaluate Formlabs materials for yourself, request a sample part.