Rowing 9,000 Miles Across the Pacific With 3D Printed Parts: The Journey of the Maclean Brothers
Somewhere in the Pacific, the Maclean brothers are rowing into history. But to survive the 9,000-mile voyage completely unsupported, they had to re-engineer their boat for speed, safety, and comfort — with the help of a Form 4 3D printer and the Formlabs material library.
“Ocean rowing is a really interesting sport because it's relatively new. Not many people have rowed across an ocean and there's loads of room for innovation, there's loads of problems that haven't been solved.”
Ewan Maclean, Engineer
After rowing across the Atlantic and setting multiple world records, brothers Ewan, Jamie, and Lachlan Maclean are rowing across the Pacific Ocean to raise money for clean water projects. Taking lessons from their trans-Atlantic journey, Ewan, an engineer at Dyson, designed and 3D printed ~50 custom parts for their boat, the Rose Emily.
Customization With Form 4
The Maclean brothers constantly write down ideas for making their trans-Pacific journey safer and more comfortable. As an engineer who has used 3D printing for his work for a decade, Ewan is fascinated by the way things work, and how they can be optimized.
“Ocean rowing is a sport of marginal gains, so to improve a fraction of a percent of efficiency through the day in any area means less frustration.”
Ewan Maclean, Engineer
The complex geometries, need for lightweight parts, and tight timeline meant 3D printing was the optimal method of producing custom, end-use parts. For some parts, the only other option for fabrication would be welding, which would be too heavy and difficult for producing the optimal geometries. Ewan has worked with Formlabs 3D printers in the past and knew stereolithography (SLA) would be an optimal method for producing the variety of parts he needed for the Rose Emily.
“One of the best things about a Formlabs printer: they literally work out of the box. You set them up, follow the straightforward process, stick the resin in, and you’ve got prints coming off straight away. It’s been so easy for us.”
Ewan Maclean, Engineer
Ewan takes the ideas he and his brothers generate to develop sketches and make a 3D model before uploading the model into PreForm, Formlabs’ free print-preparation software, for printing.
“I can just upload it to PreForm and then send it to the printer, and I can be confident that the part that comes off the machine is exactly the shape I want it to be and that everything fits. The quality of prints — it's quite amazing. Formlabs, these machines are literally the best."
Ewan Maclean, Engineer
Strong and Tough Materials
“The thing that's amazed me most is where the new engineering resins have got to. The strength is really quite impressive and is not far off from what you’d see in a production part.”
Ewan Maclean, Engineer
Three different resins were used to create parts for the Rose Emily: Tough 2000 Resin, Durable Resin, and Clear Resin V5. Tough 2000 Resin is stiff, sturdy, and robust, used for creating parts that go on the exterior of the boat and are exposed to the elements, like the Starlink mount, which is used to attach a vital shipboard system to the boat at an optimal angle. Clear Resin V5 was used to make molds for silicone parts that had to be flexible and durable.
“It’s amazing how strong these parts are, how detailed they are. I wouldn’t have trusted any other printing process.”
Ewan Maclean, Engineer
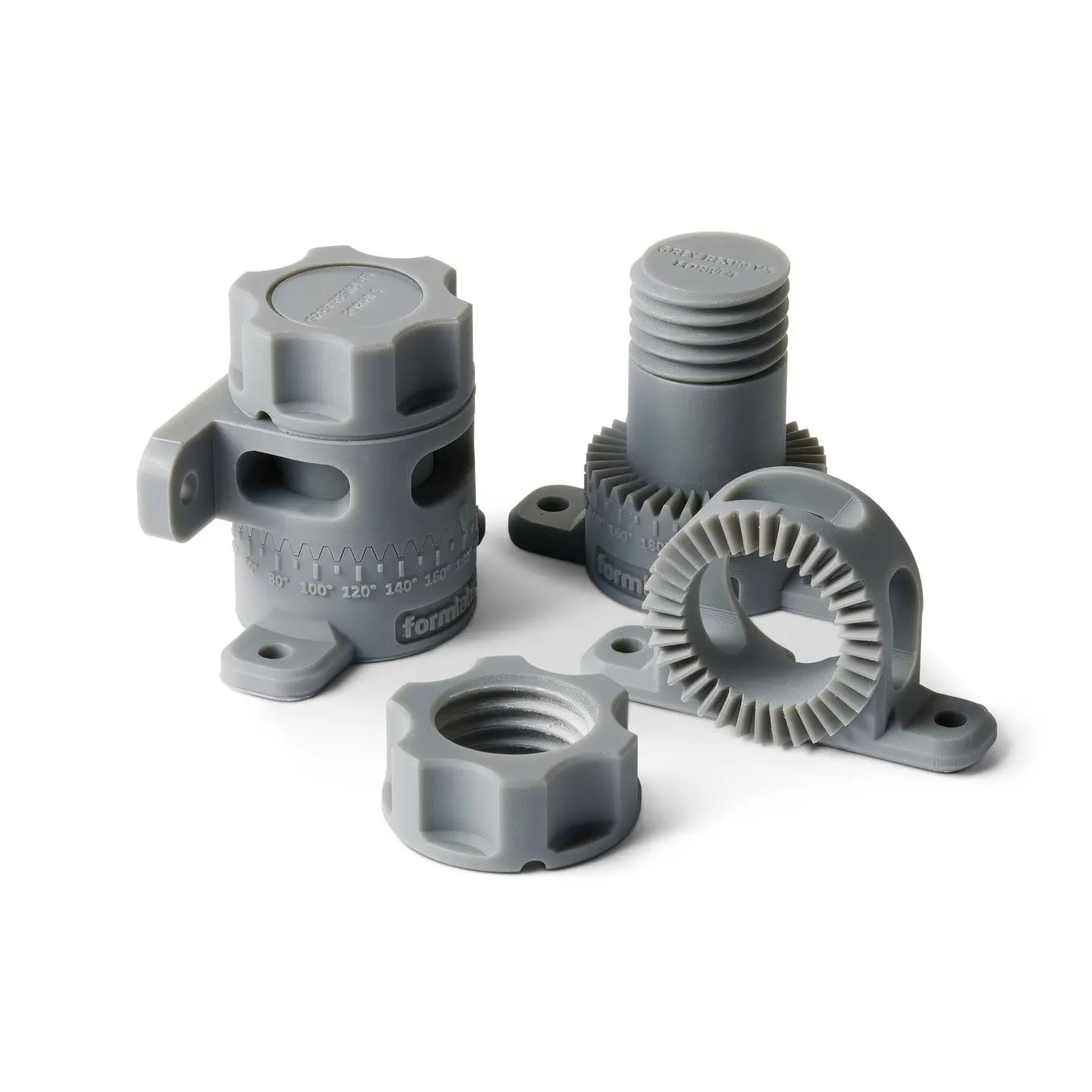
Request a Free Sample Part
See and feel Formlabs quality firsthand. We’ll ship a free 3D printed sample part to your office.
A Little Part That Makes a Big Difference
Ewan designed and printed 40-50 parts for the Rose Emily. These include ergonomic parts shaped to each brother’s body, parts that simply don’t exist, and parts with complex geometries that need to be shaped to the hydrodynamic and aerodynamic curves of the Rose Emily.
Starlink Mount
The Starlink, which provides the brothers with satellite communication, needs to be in a very specific position to get reception and ensure there’s no water buildup. Additionally, the mount must withstand the waves crashing into the back of the boat, and exposure to salt and UV.
Gimbal for a Jetboil
The gimbal was a last-minute addition to keep the Jetboil level while boiling water, printed 12 hours before the brothers left for their trip.
Removable Bed
Made of 3D printed connectors and carbon poles, the bed can be installed in the rear position so that the person on break can stretch and sleep without going into the hot, cramped cabin.
Ergonomic Seats
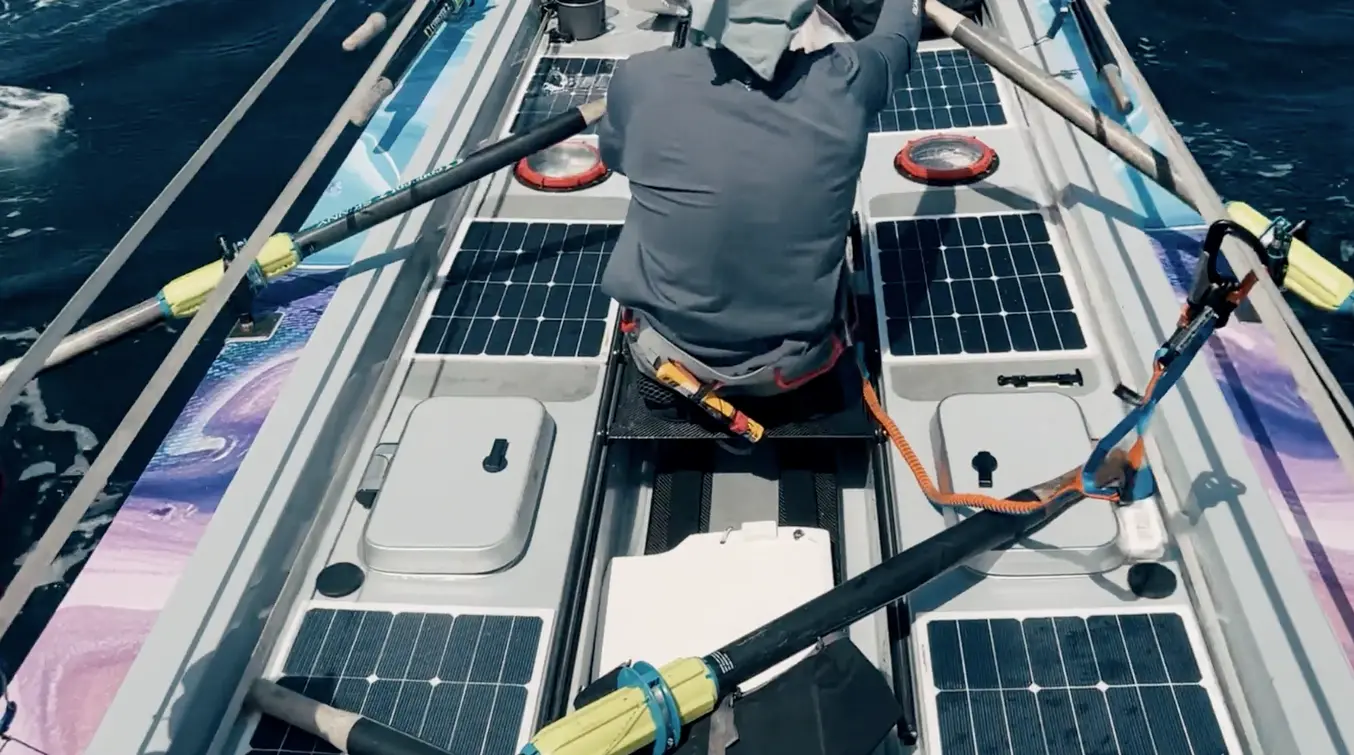
During their time at sea, the brothers will lose muscle mass, including their glutes, making the seats for rowing more uncomfortable. To combat this, the brothers made impressions of their anatomy and 3D scanned them to create custom seat molds that were then cast in silicone.
Oar Holders
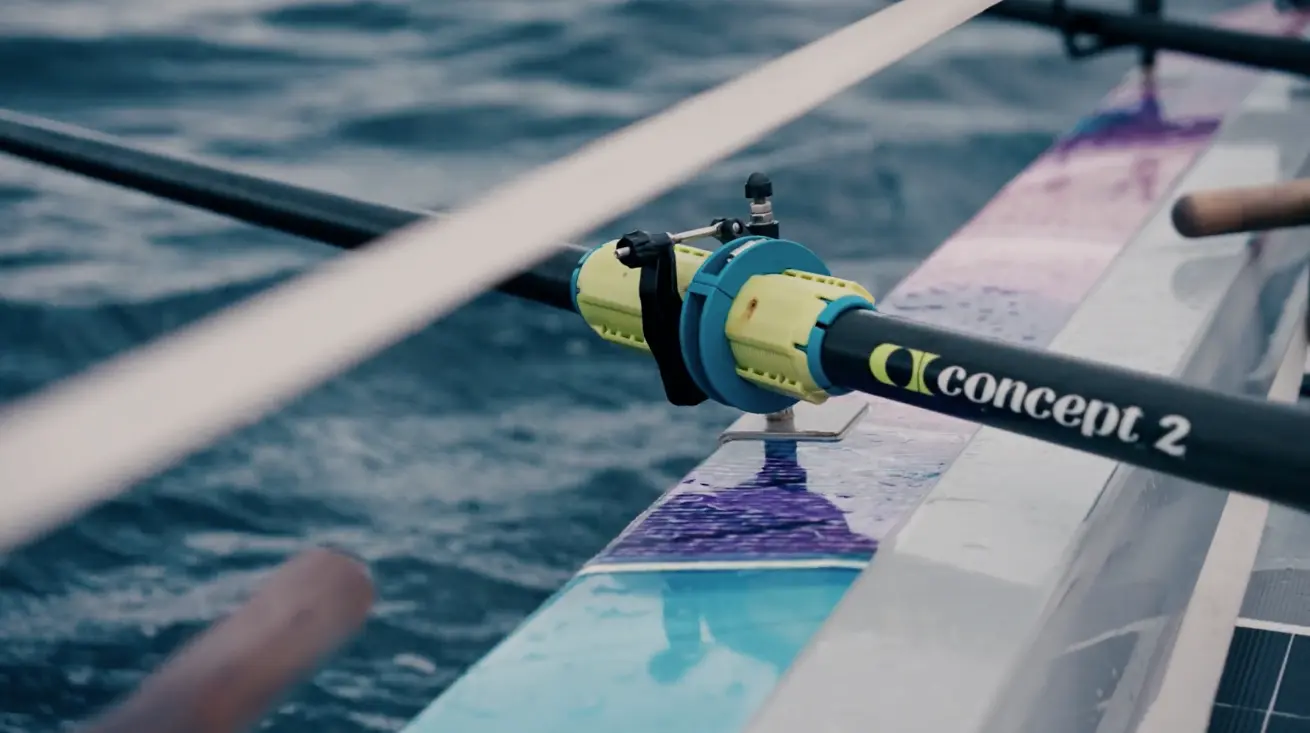
The oar holders ensure that oars aren’t an impediment to the other rowers whenever a hand is taken off of them.
The True Test: Rowing the Pacific
“You can put these parts that you get off the printer into the field. And there couldn't be much more of a test for the quality of a part than rowing across an ocean: 120 days in a pretty harsh environment of salt, weather, UV exposure, and repeated use.”
Ewan Maclean, Engineer
The Maclean brothers are currently rowing across the Pacific Ocean, where they and their boat are being put to the test in harsh conditions. For both the brothers and their boat, the ocean is a testing ground as all are subjected to sun, sea, salt, storms, and weather.
Follow the Maclean brothers’ journey through live tracking and updates as they work toward their mission to raise £1,000,000 for clean water projects for clean water projects in Madagascar.
To start printing your own custom parts, explore Form 4 or contact sales to discuss your unique application.