International trade has never been as expensive and hotly contested as it is today — every factor that could potentially impact shipping costs is under intense scrutiny. Nakai Robotics, a company founded by Yair Tamir and Aviv Melman, has developed an advanced robotic solution that can reduce costs for large shipping companies, like Maersk or MSC, that have thousands of freight vessels at sea at any given time.
Nakai’s robots are autonomous cleaning vehicles that remove biofouling — a buildup of algae, vegetation, and animal life — in order to help ships run more efficiently while adhering to stringent port regulations around cleaning processes.
Tamir has been 3D printing since 2005 — 3D printers were part of his everyday workflow, and he learned how to leverage on-demand design and production technologies to solve problems quickly. At Nakai, when it came time to ramp up design and production, the team turned to accessible SLS. They’ve ramped up to three Fuse Series printers as well as the Form 3L and Form 3B SLA printers.
“For us, parts that get printed on the SLS 3D printers are production-volume worthy and final product quality.”
Yair Tamir, Nakai Robotics Co-Founder
The Costs of Biofouling
Nakai Robotics started when Melman approached Tamir with an observation and an idea. As a recreational diver, Melman had seen the undersides of ships coming into port harbors and been amazed by the accumulated sludge on their hulls. “We spent a year learning about the effect of biofouling on the environment at ports and fuel costs for ships, and realized we could develop a solution that could improve both profits and environmental safety,” says Tamir.
Biofouling impacts shipping costs mainly because it slows ships down — the buildup of organic and inorganic matter sticking to the ship’s hull creates enormous drag. Ships have to burn more fuel to keep on schedule, and their costs go up accordingly. A clean hull can have a drastic impact on efficiency — Nakai estimates their robots lead to a 10% to 15% reduction in fuel costs.
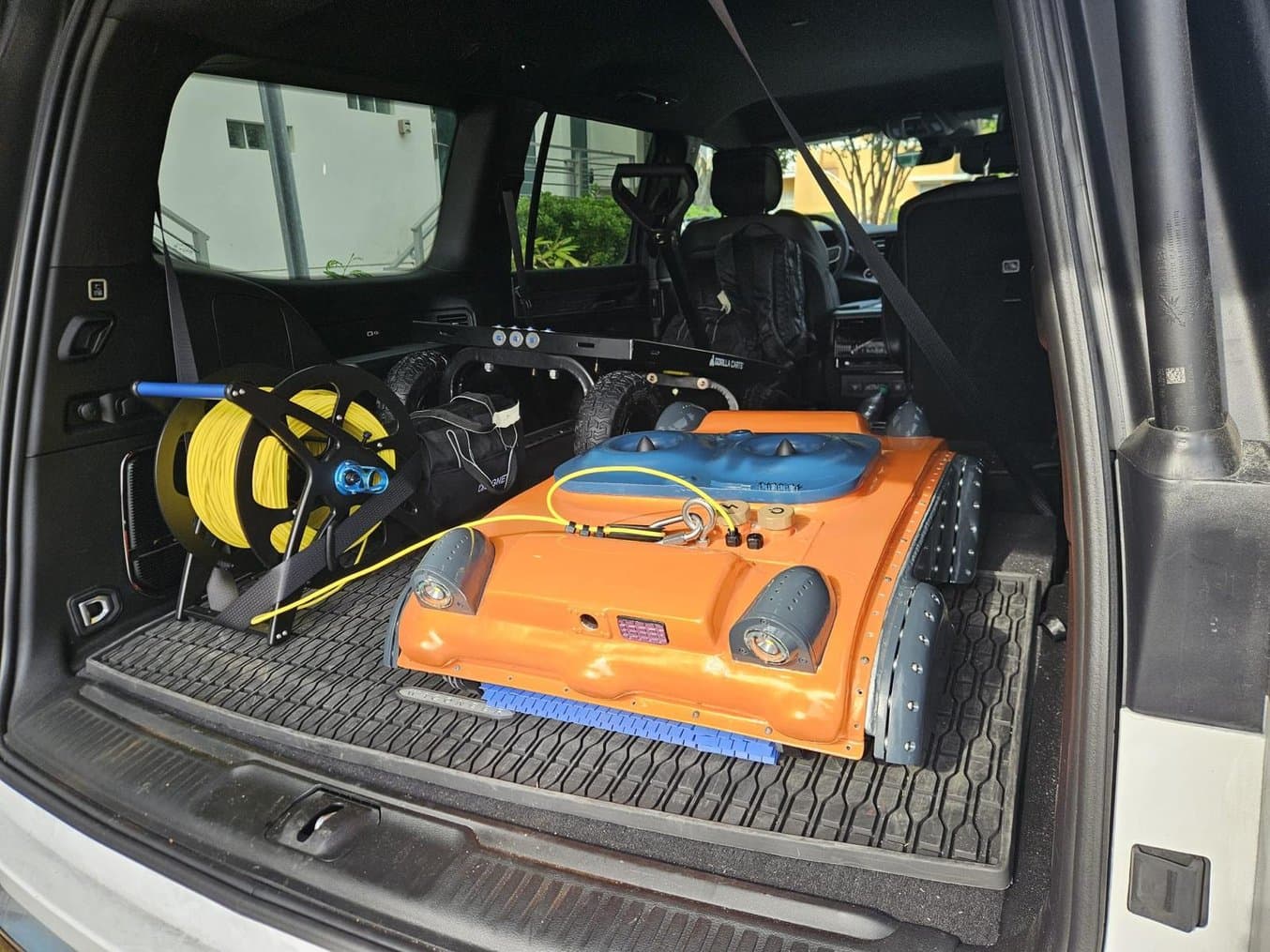
Nakai Robotics' PLECOS robot leverages years of engineering and development, as well as hundreds of distinct components. 3D printed end-use parts, as well as molded and machined components, contribute to the durability and efficiency of the PLECOS.
Some local governments with stringent policies won’t even allow ships into the harbor if they don’t pass a hull check beforehand. One Australian cruise ship was held outside the Sydney harbor for over a week before they could get it cleaned and brought in — a massive cost for the cruise company and the guests on board.
Beyond costs, biofouling presents a huge problem for the delicate ecosystem balance in the shoreline environments of ports. When ships come into harbor, the already fragile shoreline ecosystem endures an influx of foreign matter and invasive species that come off naturally from the ship’s hull. If a ship has to be cleaned (typically by a remote-controlled vehicle or a human diver), that foreign material has to be discarded. In some less regulated countries, they allow it to be dumped directly in that nation’s waters, which can lead to environmental effects like local species extinction, coral bleaching, and invasive species proliferation.
Nakai has two platform solutions. The first, PLECOS, operates in ports. It has a proprietary filter and collection tank to ensure no debris is discarded in local waters. The second, GOBY, travels with the ship in the open ocean and continuously removes new biofouling accumulation as it builds up, thereby mitigating any environmental impact and helping ship operators comply with regulatory policies.
“Biofouling harms the environment tremendously, it has a bad effect on the ocean as well as the costs for fuel. Though there are companies that provide cleaning, it’s hard to comply with strict port regulations while you’re within the maritime borders of certain countries. So we needed a way to develop something that could withstand the forces of deep sea travel or collect whatever it removed,” says Tamir.
Fixing the Foul: Deep Sea Robotics Development
3D printing was part of the solution right from the beginning. Tamir had already been using 3D printers for twenty years by the time Nakai was founded and was familiar with every technology and major 3D printing manufacturer on the market. For this project specifically, he needed a solution that allowed the team to develop functional parts quickly, with precise tolerances so they would fit easily into a very complex, multi-material assembly. “We are printing all the time, it’s 24/7, non-stop development,” says Tamir.
Overall, the Nakai robots include 1,500 different components, and 300 of them are 3D printed for end-use in the final versions of the robots. Not only does their 3D printing solution need to print high volumes, it needs to be consistent, repeatable, and accurate, with a material that can withstand intense external forces. With 300 end-use 3D printed components, Nakai needs a solution that can also produce high volumes to have as back-stock as new orders come in.
“We chose the Fuse Series because of the repeatable quality. I want to send a part to the printer, take it out, and have it be ready, I don’t want to play with it. I have a lot of people working here, and don’t want to have to teach each one of them to calibrate a printer.”
Yair Tamir, Nakai Robotics Co-Founder
SLS 3D Printing for End-Use Robotic Components
Tamir had started with Formlabs’ large format SLA printer, Form 3L, and the biocompatible. desktop version, Form 3B, for a separate medical device venture. The range of materials available for the SLA line made it possible for them to easily switch between resins for different projects. They were able to experiment quickly with molds for the high-performance carbon fiber shell of the robots by utilizing Formlabs resins, and even create flexible parts for a seal. “Our go-to SLA material is Tough 1500 Resin for pretty much everything, even molds,” says Tamir.
When it came time to create end-use parts, however, Tamir brought on the Fuse 1 with Nylon 12 GF Powder, a glass fiber-reinforced material with extremely high stiffness and dimensional accuracy.
“We chose Nylon 12 GF Powder for its excellent tensile strength. That was the biggest driver. We needed something that could mimic steel or other metals, in a way. ”
Yair Tamir, Nakai Robotics Co-Founder
To produce the thousands of SLS components necessary for the end-use robots, the Nakai team is running their printers all day, every day. “With over 300 SLS parts on each robot, that’s a commercial enterprise level of production,” says Tamir. With that commercial volume, they need to rely on the accuracy and consistency of those parts as well, so that each robot assembles and functions the same as the next. Even after years of printing with the Fuse Series, Tamir and his production team have found that their parts deliver consistent dimensional accuracy.
“Everyone talks about SLA being the best for small features, but when you need percentage tolerances, you need SLS. The SLS can do it again and again and again. Every time, you get the same results, with no deformation.”
Yair Tamir, Nakai Robotics Co-Founder
Ensuring Underwater Performance With Cerakote
Building an autonomous robot is hard enough, but building one that needs to operate underwater and with intense forces acting against it is an entirely next-level challenge. The technology that keeps the GOBY robot adhered to the side of the ship’s hull is proprietary, though Nakai shares that they use the force of the oncoming water to power the robot and keep it attached securely to the ship.
The outer shell of the robot is made from carbon fiber, fabricated through a carbon pre-preg process. But for all the end-use SLS components, Tamir needed to find a solution that could keep the 3D printed parts waterproof and functional even after months underwater.
The team tested SLS 3D printed parts in salt baths and with salt spraying to determine the corrosive effects of ocean water. After long periods of exposure, the SLS 3D printed components would start to show signs of corrosion, and Tamir began to explore different coating methods. After testing different ways of plating and coating the parts, they settled on Cerakote. “We tested post-processing treatments and solutions that we thought could protect the parts, but then we started to use Cerakote, and it just worked. We now Cerakote our SLS parts in-house, and they withstand the salt spray and the underwater immersion well,” says Tamir.
Cerakote is a thin, high-performance ceramic coating developed by NIC Industries that provides numerous mechanical and aesthetic advantages. For end-use SLS products and assemblies, Cerakote can elevate their functionality, extending the lifetime and weatherability of 3D printed parts.
Expansion, Full Steam Ahead
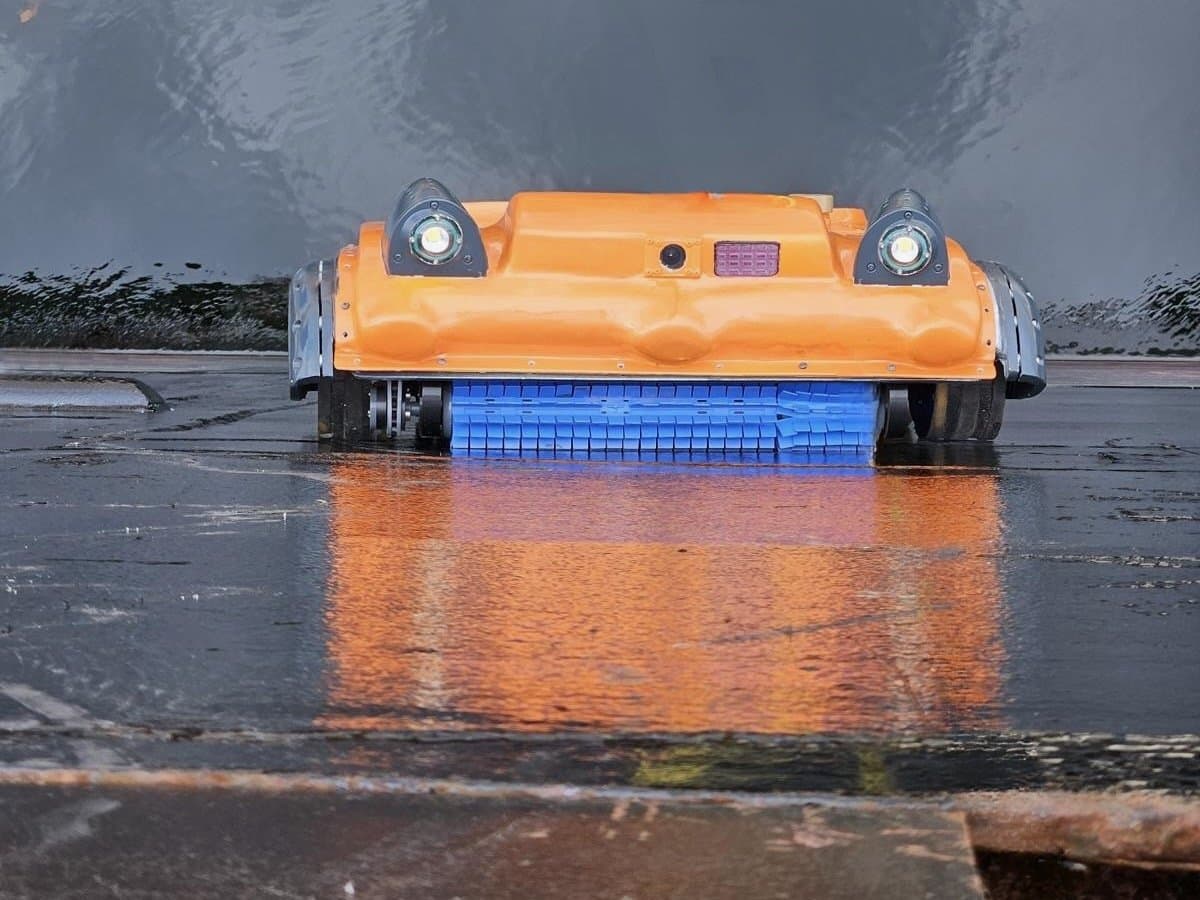
The PLECOS can stay attached and untethered, removing biofouling from the ship's hull and making passage more efficient.
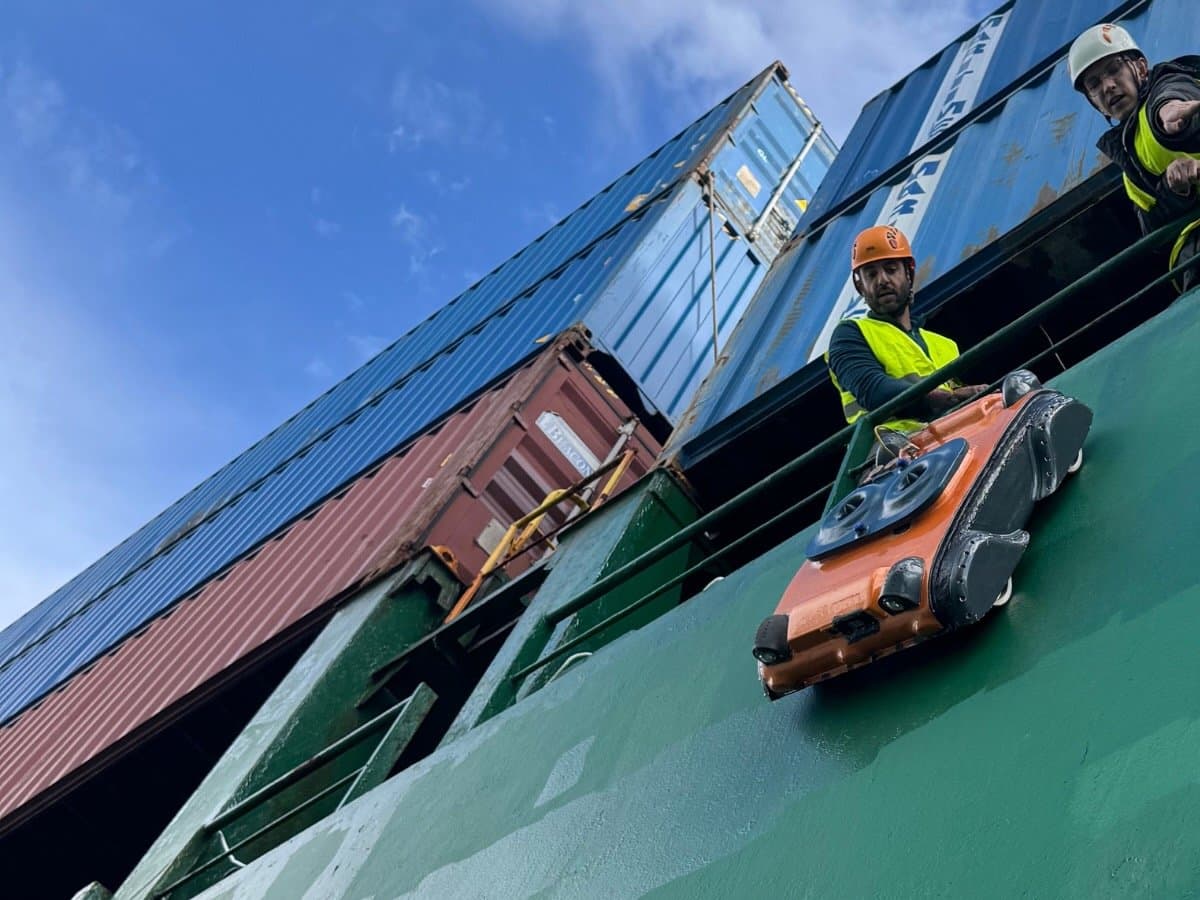
Nakai's team deploys the PLECOS for large freight vessels, an example of the fast growing 'drones as a service' sector of the overall drones and robotics industry.
With life cycle testing done and beta testing successful, Nakai has been able to get end-use robots out onto multiple ships crossing the world. As word gets out, demand for this energy-saving, economical solution is growing; nearly every type of shipping solution, from freight cargo to cruise ships, faces regulatory concerns over biofouling, and without exception, everyone would like their fuel to get them farther. “If our robots are cleaning the ship, we’re saving you money, we’re saving you carbon credits. Even for wind or electric, friction still exists, and cleaning the biofouling solves it,” says Tamir.
3D printing is a big part of Nakai’s expansion plan — after reaping the benefits of a fast, agile development timeline, Tamir knows that 3D printing can help them retain their lead over an increasingly competitive industry. “Our next stage in the company is scale. Getting bigger, more support, more products. I plan to buy more 3D printers and do it here,” says Tamir.
Between the Form Series and the Fuse Series, the Nakai team has been able to both rapidly iterate as well as create thousands of end-use parts for robots in some of the harshest environments out there: highly pressurized, cold, salty water that’s moving fast. “We chose Formlabs because of the repeatable quality. I want to send something, I want to take it out, and it's ready. I don't want to play with it,” says Tamir.
As more customers and partners come on board, Nakai’s set to expand with both SLA and SLS 3D printing. To learn more about Formlabs technology, explore end-use applications and materials.