“Often ideas are born because you learn about the potentiality of technologies you work with daily. If we didn’t have access to 3D printers, NOVA Foot wouldn’t have even been born. Having access to the Fuse 1+ 30W led me to think that I could create something truly functional and accessible to everyone, that could revolutionize the everyday life of amputees.”
Marco Garano, CEO, C.P.T.
NOVA Foot is a high energy return custom prosthetic foot available in six sizes. Developed by Marco Garano, CEO of C.P.T. (Custom Precision Technology), NOVA Foot was prototyped, tested, and is now produced with Formlabs 3D printers. Without access to 3D printing, this prosthetic wouldn’t exist, as any alternative method of production would be prohibitively costly and inefficient. NOVA Foot is sold through Protosystem, a C.P.T. spin-off, opened with the aim of creating functional and accessible products in the orthopedic field.
“Thanks to 3D printing, which has allowed us to significantly contain production costs, NOVA Foot is accessible to all foot amputees in Italy, and is entirely covered by the NHS.”
Valentina Garano, Sales & Marketing Manager, Protosystem
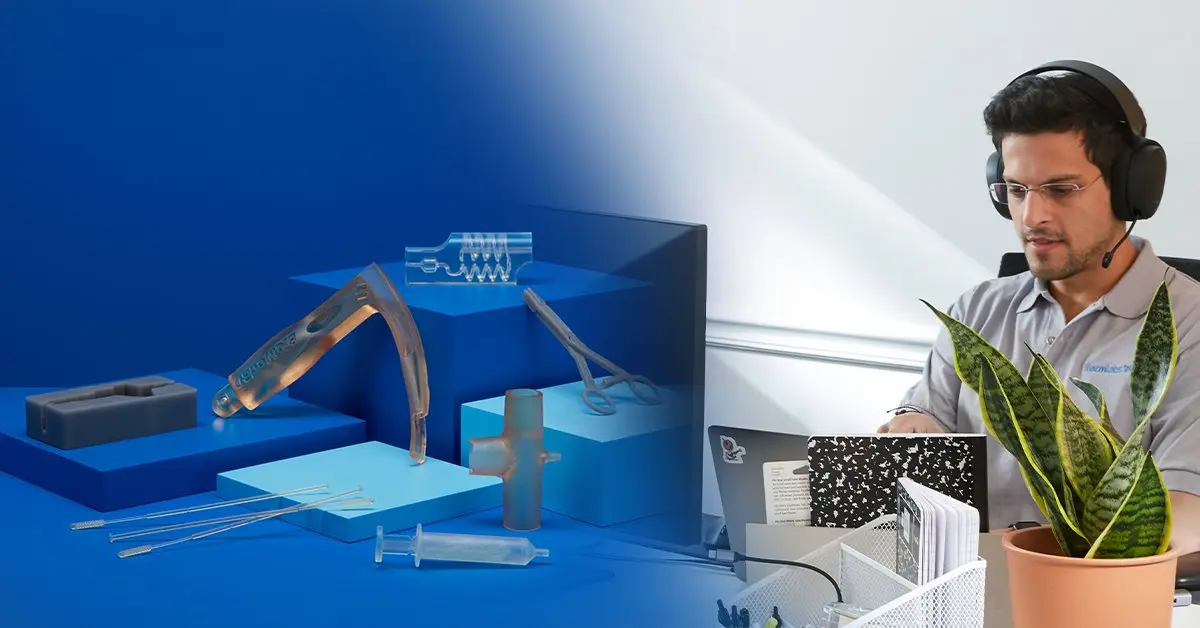
Talk to Our Medical Sales Team
Whether you need to make patient-matched surgical tools or are prototyping for a cardiac medical device, we’re here to help. Formlabs Medical team are dedicated specialists who know exactly how to support you and your company's needs.
NOVA Foot: Customizable for Improved Comfort
Most prosthetic feet involve extensive adaptation by the patient. The goal behind the NOVA Foot was for it to adapt to the patient, and guarantee comfort and stability during daily use.
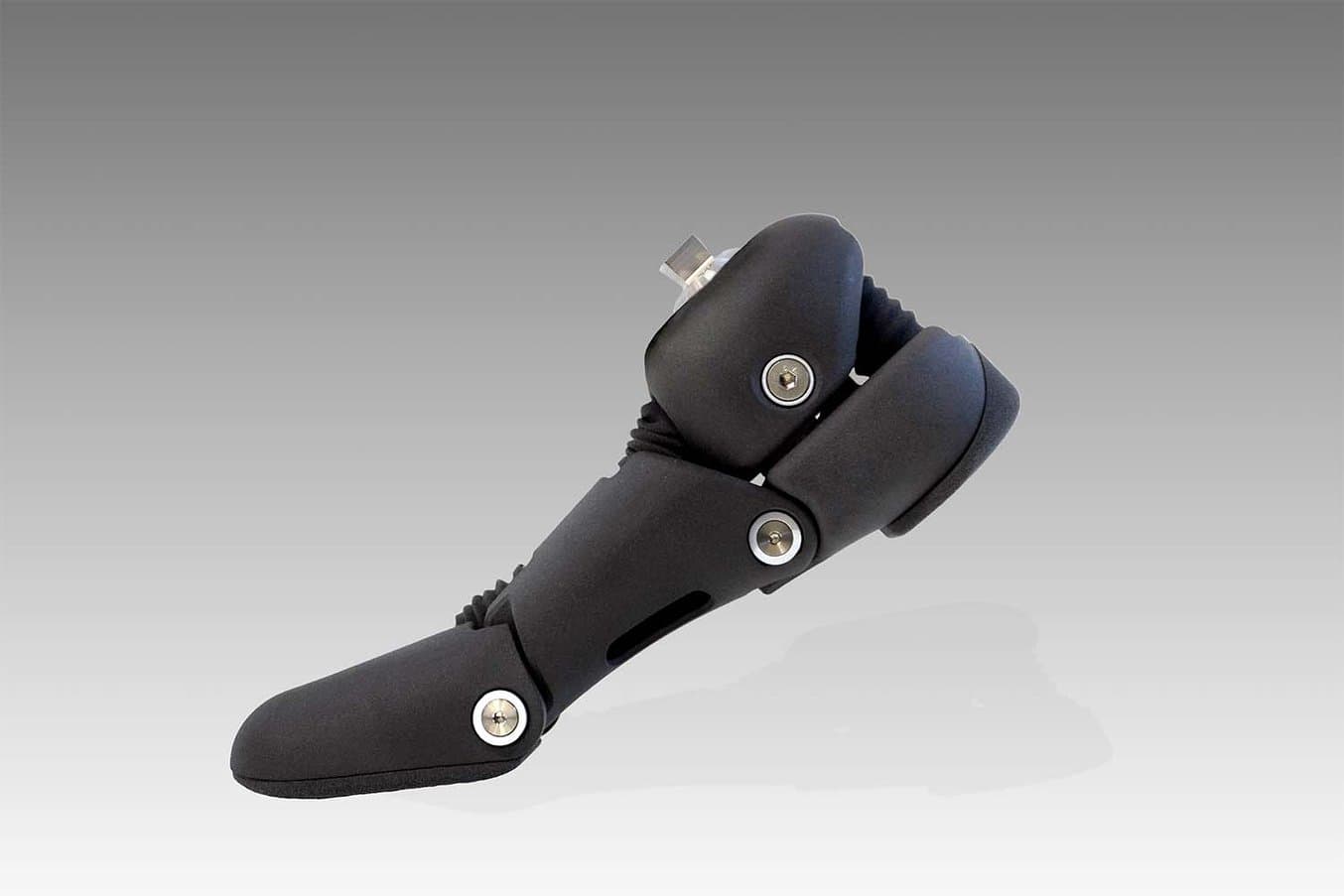
NOVA Foot is 3D printed on Formlabs Fuse 1+ 30W with additional components printed on Form 3B+.
NOVA Foot is composed of multiple sections for the forefoot, midfoot, heel, and ankle. Each segment of the foot can be customized based on a patient’s needs. These highly customizable sections are printed on the Fuse 1+ 30W selective laser sintering (SLS) 3D printer. Additional soles at the toe and heel, also printed on Fuse 1+ 30W, are completely waterproof and offer traction and stability in wet environments, such as a shower.
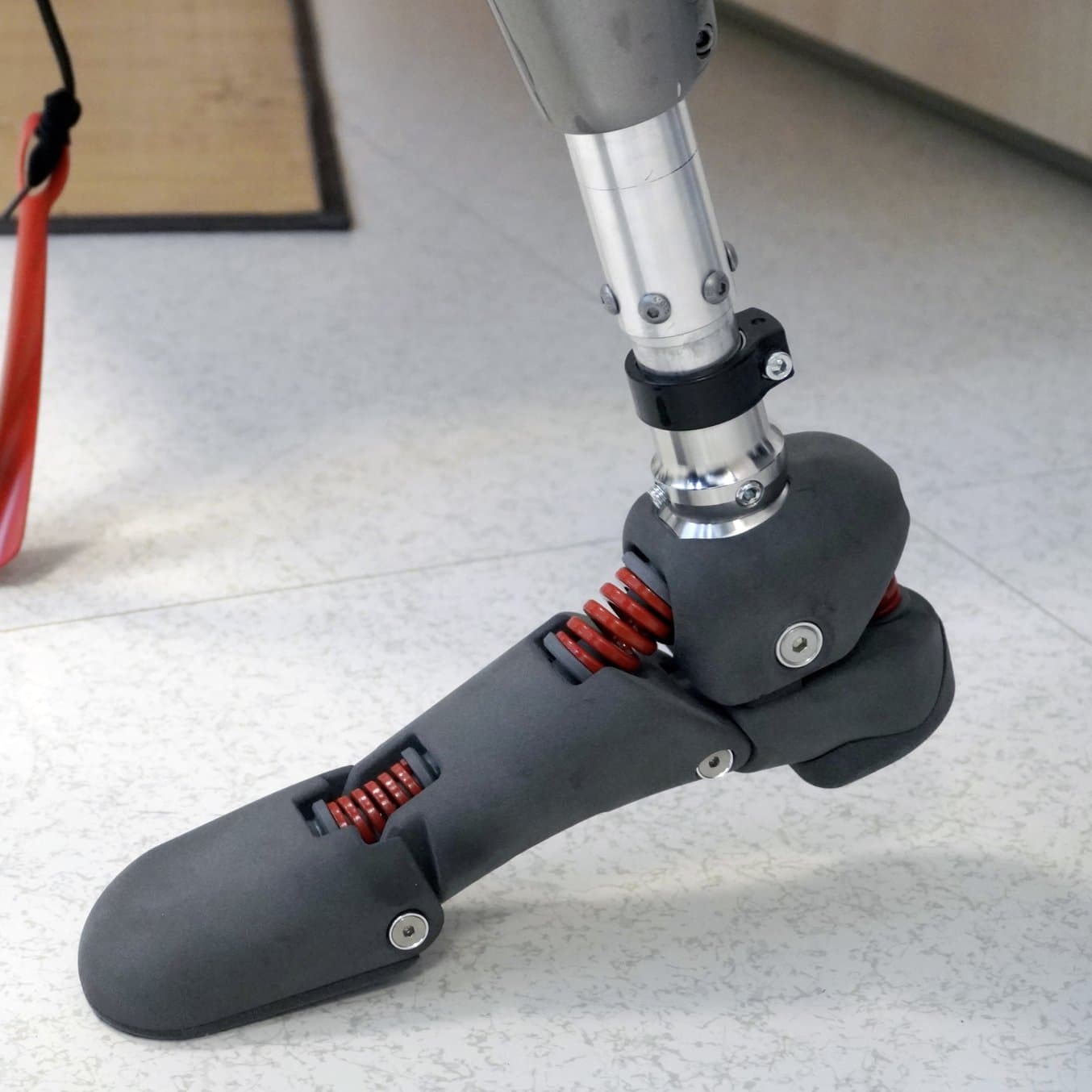
The springs in NOVA Foot, shown here in red, can be changed out for softer or stiffer springs, customizing the response of the NOVA Foot.
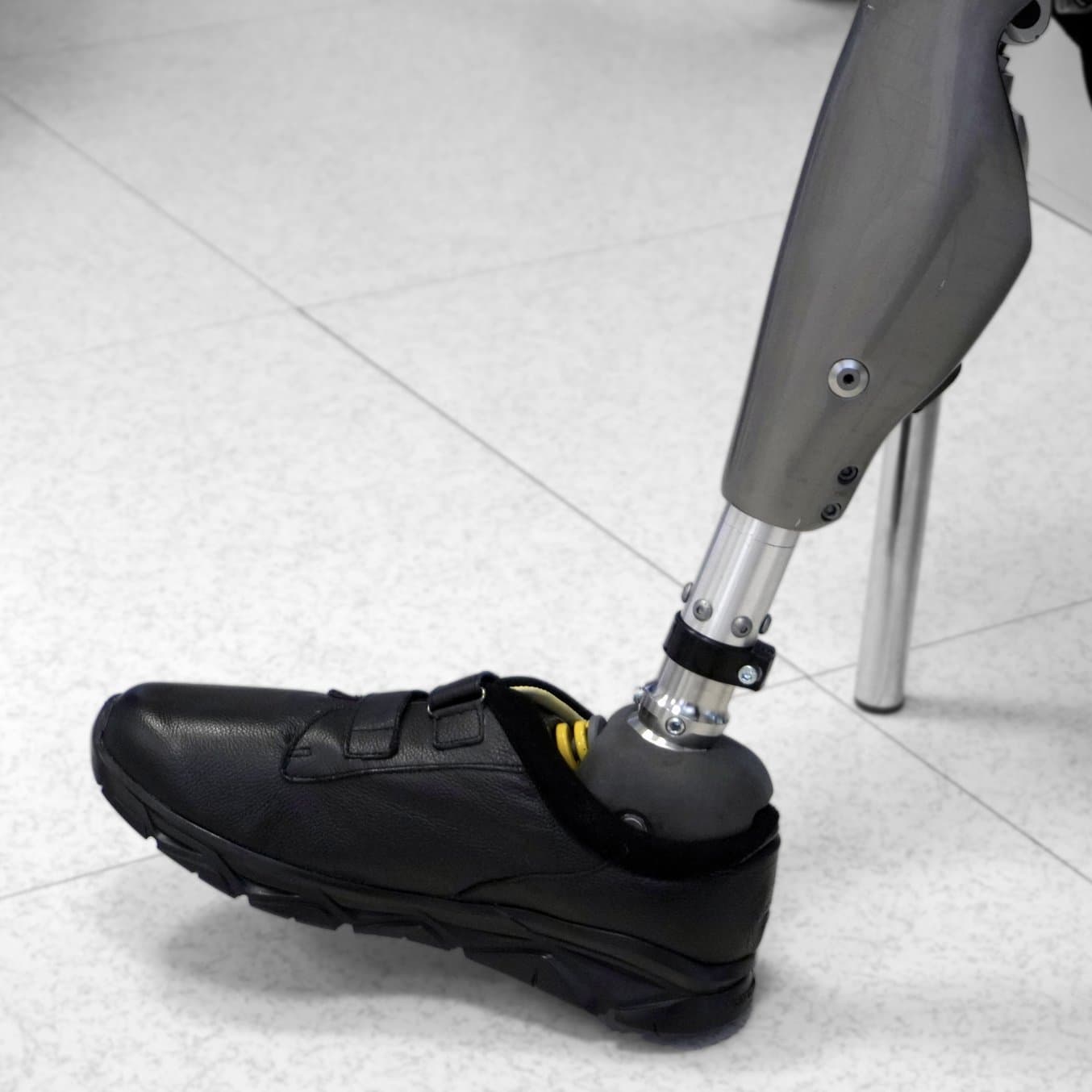
NOVA Foot was designed to fill shoes as well as function uncovered.
Three springs allow the 3D printed foot sections to move. The flexion of the foot can be customized with softer or more rigid springs. Allowing the replacement of the three springs at any time, NOVA Foot is ideal for less active patients who prefer a prosthesis that offers smooth movement and comfort, as well as for more active patients who need a responsive prosthesis that returns energy during short sporting activities. Changing the three springs also helps new amputees to follow a rehabilitation path after leg amputation.
For example, if a patient prefers greater comfort during the heel strike phase and greater push during the toe-off phase, a softer spring can be installed in the heel and two stiffer ones in the forefoot to tailor the response of the NOVA Foot.
Why Manufacture With 3D Printing?
“Using 3D printing, we are able to produce the parts internally in a very short time. This allows us to go from the idea to the prototype and from the prototype to production very quickly. 3D printing also allows us to create complex geometries that wouldn’t be possible with traditional production technologies.”
Marco Garano, CEO, C.P.T.
Producing the NOVA Foot would not be possible with another method of production. The high level of customization of so many elements would be prohibitively expensive to produce via another production method, including injection molding or machining. Additionally, Marco Garano says, “making the parts with the Fuse 1+ 30W allowed us to create very complex geometries, internally hollow, with reinforcements in specific points studied with the FEM. This made the parts light but at the same time tough and functional. Another example is the heel support insole, using TPU, creating an internal hollowing to reduce the density in that specific point.”
“We chose 3D printing to produce NOVA Foot parts because we have full control of the production process. Furthermore, if we need to modify the parts to customize them based on patient needs, we can do it without having to incur the costs of modifying molds.”
Valentina Garano, Sales & Marketing Manager, Protosystem
The cost of an injection mold to manufacture all the NOVA Foot parts can be estimated at €50,000-60,000 per size, with a minimum of six sizes. This would put molds alone for the six sizes at a minimum of €300,000, which is prohibitively expensive.
In-house 3D printing also offers supply chain resilience, decreasing risk, and quick turnaround times for both prototyping and production. Additionally, powder refresh rates with SLS minimize waste. Currently, a single NOVA Foot takes about five hours to print in Fuse 1+ 30W, and up to four prostheses can be included in a single build.
“From our point of view, the advantages of the Formlabs ecosystem (SLS and SLA) are the possibility of estimating costs in real time, the simplicity of the workflow from loading the material to post-processing, and the very precise analysis of printing times that PreForm performs.”
Marco Garano, CEO, C.P.T.
Protosystem uses both a Fuse 1+ 30W SLS 3D printer and a Form 3B+ stereolithography (SLA) 3D printer for both prototyping and production, and PreForm, Formlabs’ print preparation software. PreForm allows Marco Garano to see accurate time estimates and material usage in real time, for full control of production.
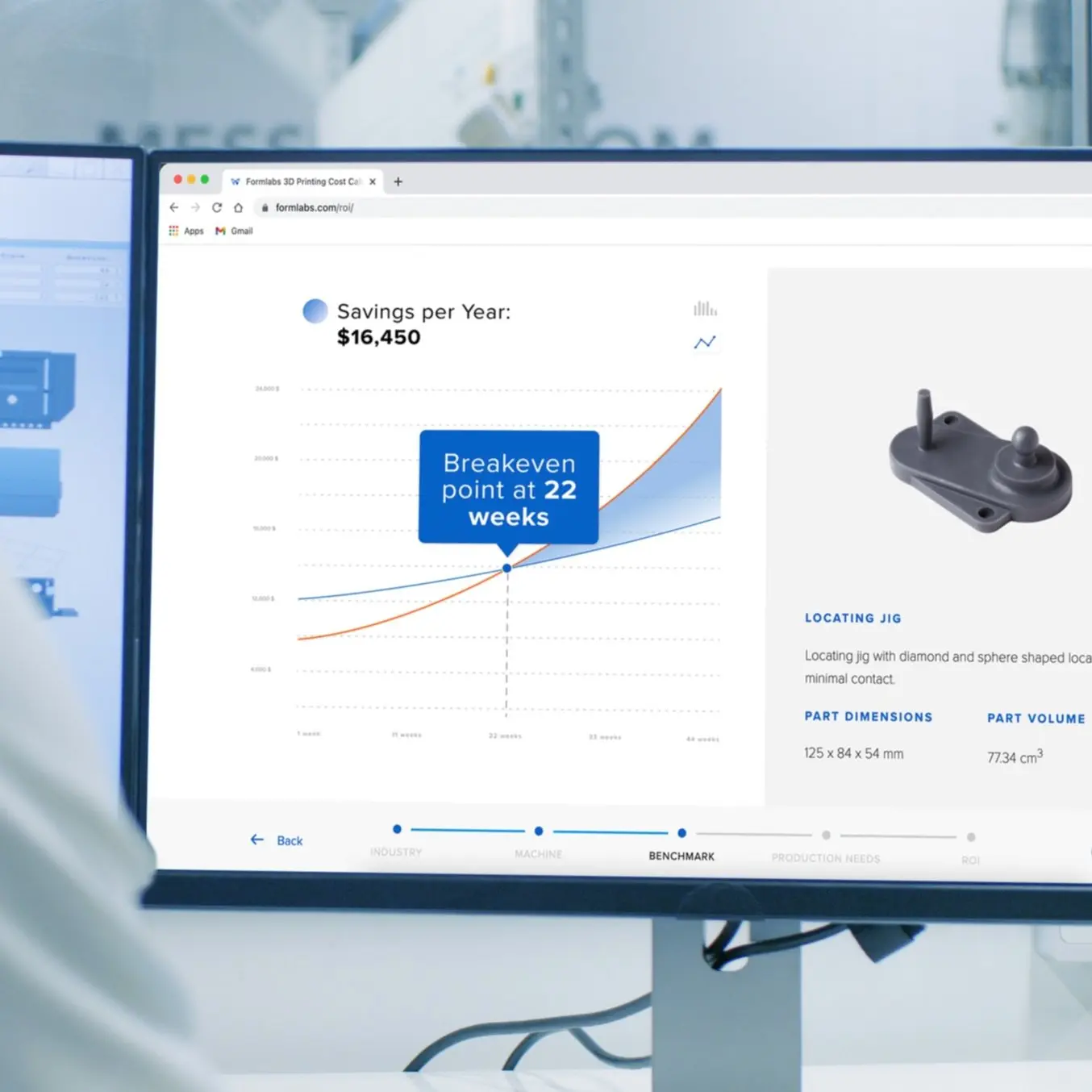
Calculate Your Time and Cost Savings
Try our interactive ROI tool to see how much time and cost you can save when 3D printing on Formlabs 3D printers.
“An advantage offered by Formlabs is the amount of materials available to create and test different parts.”
Valentina Garano, Sales & Marketing Manager, Protosystem
Access to Formlabs’ extensive catalog of over 40 high-performance materials was a key advantage in meeting the demanding requirements of this project. The NOVA Foot had a number of requirements for material properties; it needed to be durable, lightweight, waterproof, aesthetically pleasing, affordable, and hold up to repetitive use for a load-bearing application. Marco Garano worked with SLS materials, starting with Nylon 11 Powder for prototyping and then moving to Nylon 12 Powder for production.
Nylon 12 Powder is used for the bulk of the foot as it is light while being resistant to compression and impact, and has high environmental stability. Marco Garano says, “We chose to make the parts in Nylon 12 Powder mainly because the printing tolerances are better with this material, the parts in contact with each other do not require manual adjustment, and the cost of the final parts is slightly lower than Nylon 11 Powder.”
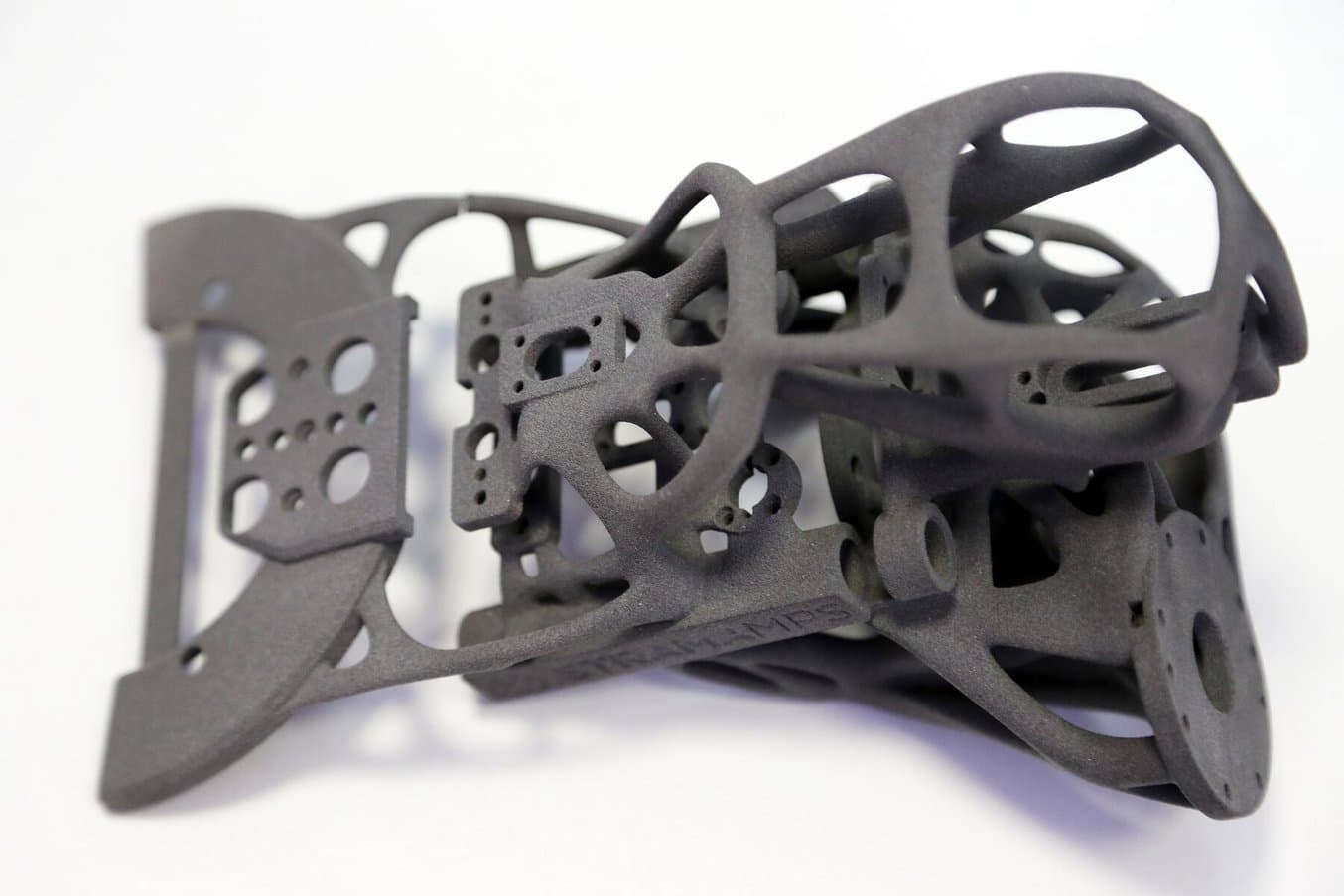
Fuse Series Design Guide
In this design guide, you’ll learn about some of the important considerations for designing for SLS 3D printing on the Fuse Series, and how you can leverage these practices to create successful parts.
TPU 90A Powder is used for a heel strike cushion and a forefoot cushion, as well as spring covers, which require ductility. The heel strike cushion has an internal lattice structure that provides comfort during daily use of the foot. Lattice structures are not possible to produce with manufacturing methods other than 3D printing.
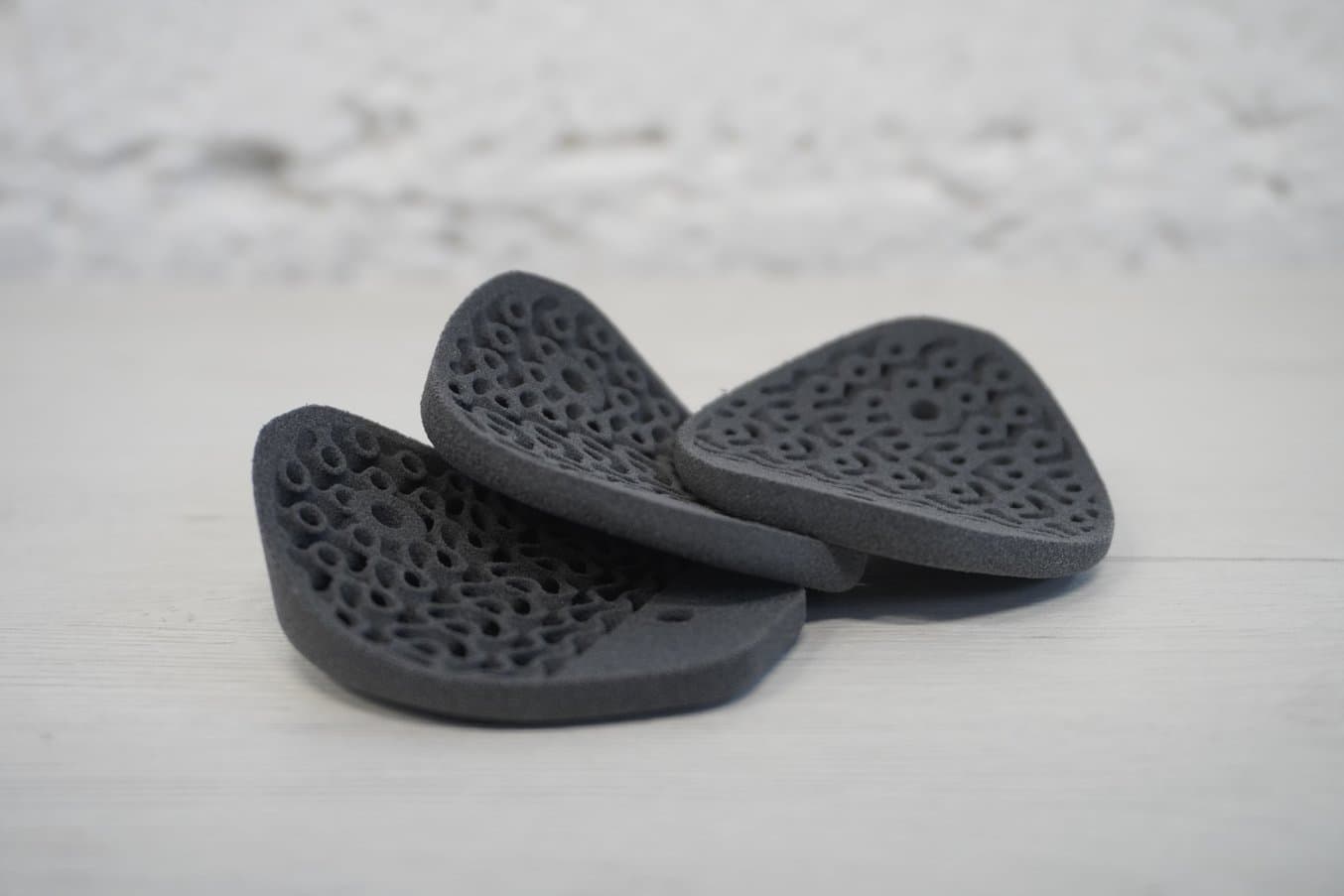
The lattice structure of the heel cushions absorb impact. These internal structures would be impossible to create with a manufacturing method other than 3D printing.
The cushions not only absorb impact, but they also give grip while walking. Marco Garano says, “Two insoles allowed us to avoid creating a cover like in traditional carbon fiber prostheses, therefore significantly containing the final weight of the prosthesis.”
Traditional carbon fiber prosthesis use covers to provide grip, protect the foot from wet environments, and fill the shoe. The design of the NOVA Foot fills shoes without the need of a cover. Additionally, the materials used to produce NOVA Foot do not need to be protected from water, and the TPU 90A Powder cushions provide traction.
On average, a carbon fiber prosthesis for adults weighs from 400 to 600 grams, with an additional ~200 grams of aesthetic cover. By contrast, the NOVA Foot weighs 550 grams and does not need an aesthetic cover, making it lighter than a carbon fiber prosthesis.
In addition to SLS 3D printed parts, SLA parts are used to hold the springs in place. These spring holders must have a very smooth surface because they slide, and must be highly accurate because they mate in the Nylon 12 Powder parts with minimum play. The spring holders are printed in Tough 2000 Resin, an ABS-like material for strong and sturdy parts that hold up to extended use.
“The joining between the Tough 2000 Resin spring holders and the Nylon 12 Powder foot parts demonstrates the high precision of Formlabs 3D printers.”
Valentina Garano, Sales & Marketing Manager, Protosystem
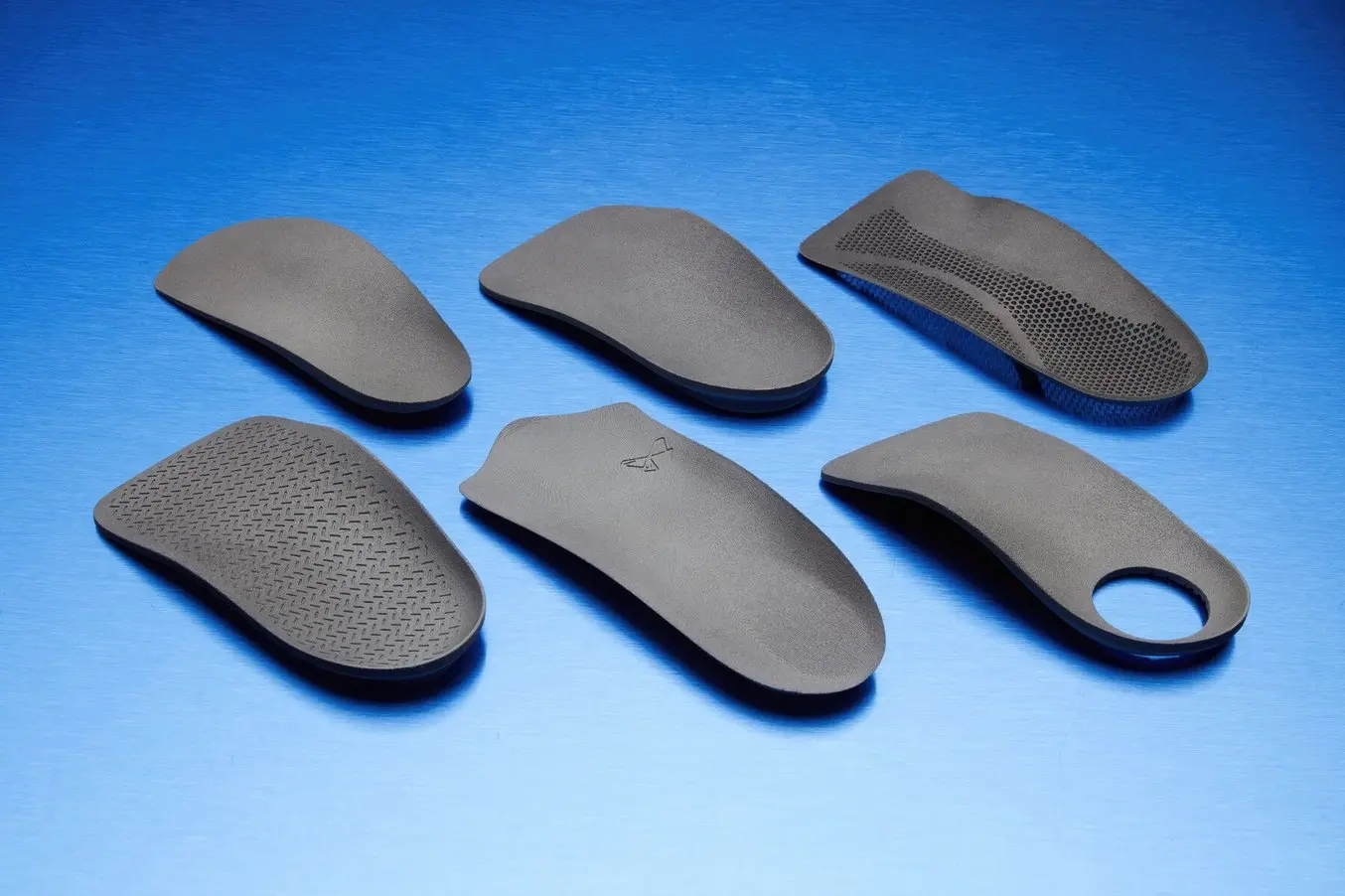
Custom Orthotics With 3D Printing
You can now produce custom orthotics easily and affordably in-house with a simple and clean digital workflow, reducing costs and labor needs, and improving turnaround time and comfort for your customers.
Testing the NOVA Foot
Initial testing is done with Finite Element Analysis (FEA) in Solidworks. Then, once the design is tested, it’s printed for physical testing. Machines are used to simulate the mechanical movement of different actions, stress-testing the foot, which must be able to withstand repetitive, weight-bearing movement. By prototyping using the same method of production as manufacturing, the results of these tests show exactly how the NOVA Foot will perform.
Users will need to replace the springs in the NOVA Foot every year to maintain full functionality, but as the Nylon 12 Powder parts are only subject to compression, they are expected to last for over three years.
After internal testing, Protosystem works with orthopedic specialists and centers for real-world testing. Prior to release, NOVA Foot was tested by volunteer patients at a gym for amputees and in daily use. Protosystem has found that users are amazed by how fluid NOVA Foot feels while walking up or down a ramp. Patients also reported that NOVA Foot returns a lot of energy while walking, supporting the patient with every step.
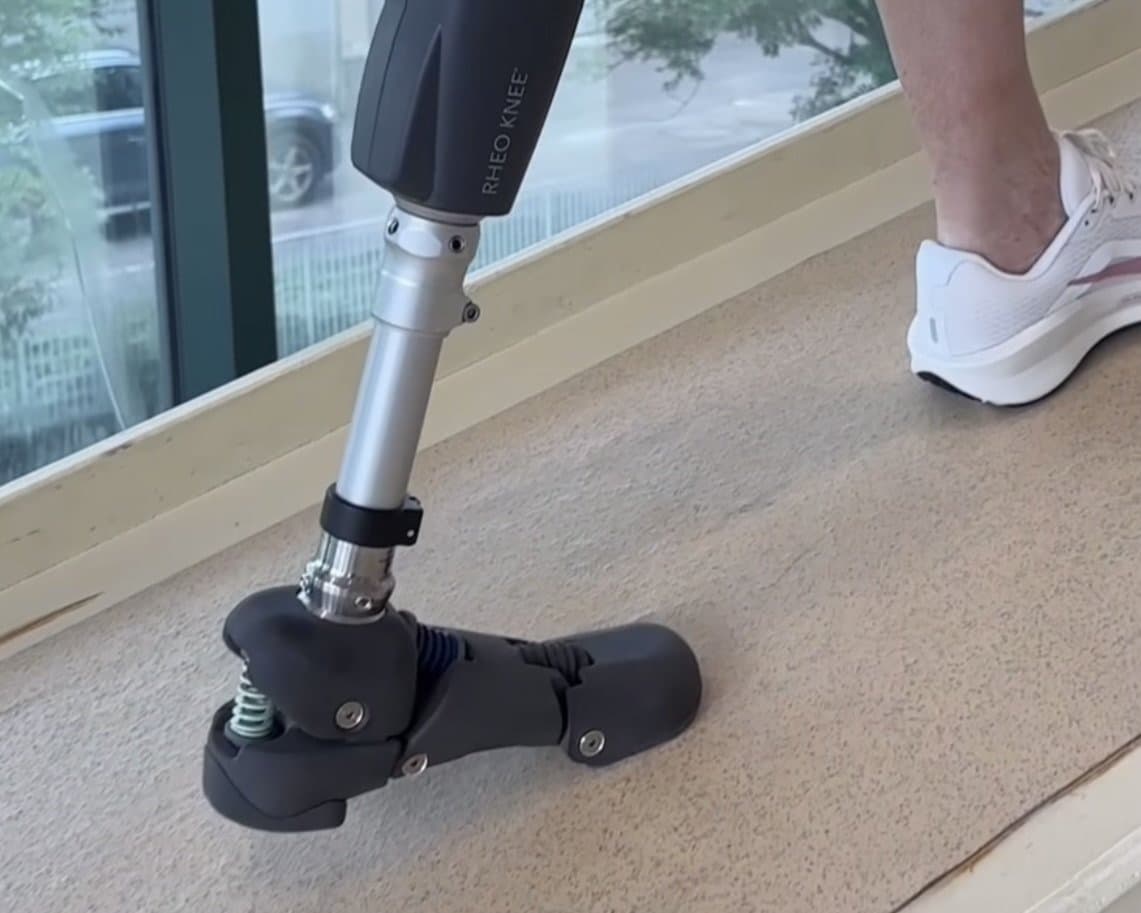
NOVA Foot has been tested in gyms as well as normal life, with users remarking on the fluidity of walking up a ramp.
Thanks to 3D printing, as patients use NOVA Foot and provide feedback, changes and customizations can continue to be made without interrupting production. For example, one amputee needed additional support in the heel strike phase and more shock absorption. Marco Garano was able to customize the model in a few hours, modifying the upper part of the foot and the foot attachment to improve support and provide more shock absorption. Once modifications are made, it takes five hours to print the foot, enabling customization in a day.
After a year of study and various prototypes, NOVA Foot was released at the beginning of March 2025 and, to date, the patients who have tried it have greatly appreciated the prosthesis for its unique characteristics.