
금속 주조는 아직 500억 달러 규모의 산업이고 미국에서만 단독으로 160,000여 개의 직접 고용을 창출하고 있지만, 미국 내 주조 공장의 생산 물량은 10년 전 물량의 절반에도 미치지 않습니다. 이런 생산 물량의 하락은 해외 생산으로 얻는 비용 절감, 금속 대체제의 성능 향상, 실제 생산 공정 각 단계의 숙련된 기술 인력 부족 등 다양한 요소에서 기인한 것일 수 있습니다. 그러면, 항공우주, 자동차, 에너지 등 중장비 산업 내 제조업체가 금속 파트를 빠르고 경제적으로 조달하는 방법은 무엇일까요?
아직 해당 분야에 금속 파트를 공급하고 있는 주조 공장은 지금껏 새로운 생산 공법을 채택하고 부상하는 기술을 실험해 온 덕분에 호황을 누려왔습니다. 저희는 Diversified Metalsmiths, Inc.의 존 파(John Farr) 부사장과 대담을 나눠 Diversified사가 자사의 금속 주조 워크플로에 최신 기술을 도입하여 비용 절감, 리드 타임 개선, 민첩성 향상의 효과를 거둔 방법을 알아 보았습니다.
Form 시리즈 광경화성 수지 조형 방식(SLA) 3D 프린터와 신소재인 Clear Cast Resin을 도입한 Diversified사는 주조용 패턴을 신속하고 경제적인 방법으로 직접 프린팅해 왔지만 자사의 주조 워크플로에는 전혀 변화가 없었을 뿐더러 외부 공급 업체에서 문제를 해결해야 했던 문제도 전혀 발생하지 않았습니다.
“저희가 Form 3L구매한 주된 이유는 패턴 비용 때문이었습니다… Form 3L과 관련 장비 비용을 분할 상환해도 현재 주문 비용의 최소 손익 분기점에는 도달할 것이고 향후 주문에서는 파트당 $200 이상 절약할 수 있을 것입니다. PMMA와 Clear Cast Resin으로 제작한 SLA 패턴 사이에는 공정 상의 변화가 거의 없고, 주조 전후 모두 마찬가지입니다."
존 파(John Farr), Diversified Metalsmiths 기술 부사장
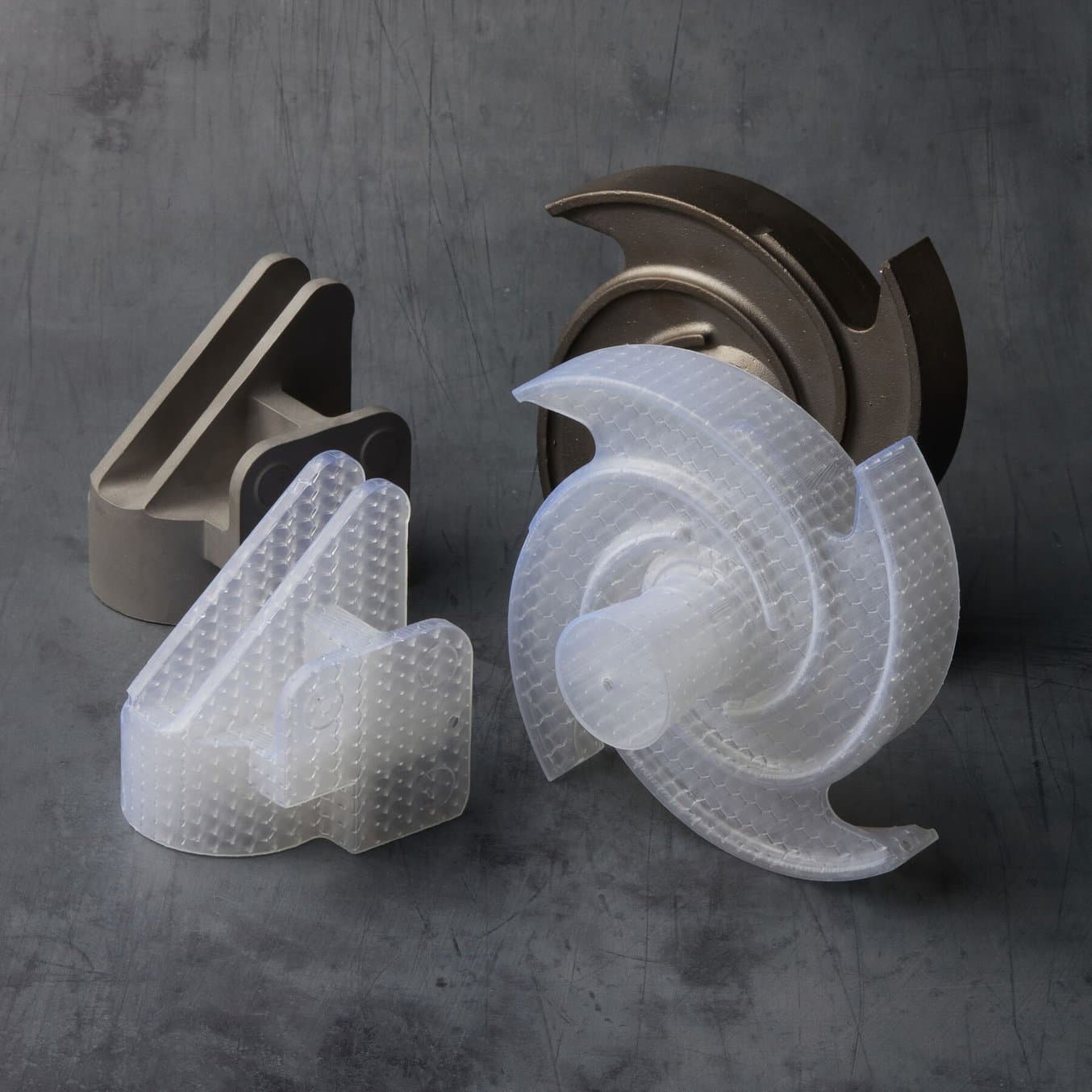
주조 공정의 정밀도와 비용 효율성: 금속 파트 제작에서 활용 가능한 3D 프린팅의 레버리징 효과
본 웨비나에서는 몇몇 기존 주조 업체가 금속 파트를 주조하면서 Formlabs의 3D 프린터로 프린팅한 패턴을 활용할 수 있었던 공법을 안내해 드립니다. Formlabs의 Clear Cast Resin과 Materialise Magics의 격자 생성 기능을 기존 주조 공법에 접목시켜 비용 절감, 처리 시간 단축, 금속 파트의 품질 개선의 효과를 거두고 있는 주조 업체의 비법을 알아보세요.
Diversified의 다양한 고객 계층
Diversified사(社)는 대량 물량 생산 시설 보다는 ‘주문형 생산 시설 ’ 형태로 운영되는 기업이며 이런 곳이 Diversified사(社)만은 아닙니다. 미국에는 전국적으로 생산 규모가 이들과 유사하고 정확도는 떨어져도 빠른 납품을 원하는 고정 고객을 유치하여 비슷한 물량을 생산하면서 규모는 더 작은 주조 공장이 많습니다. Farr 부사장은 “저희 고객은 다른 공장에서 견적을 받지 않습니다. 원하는 것을 우리가 정확하게 제공할 수 있다는 것을 아니까요.”라며 자부심을 드러냈습니다.
공차가 정확한 금속 파트를 중소 물량으로 주문하면서 리드 타임은 짧아야 한다면 이런 주문을 처리할 수 있는 곳은 Diversified사(社) 뿐입니다. 주문량의 약 70%는 임펠러, 펌프 하우징, 밸브, 드레인, 화격자 외 산업용 유체 컴포넌트 같은 유체 제어 응용 분야가 차지합니다. 작업 분야의 나머지 30%에는 드론 제조에서 자동차 컴포넌트, 의료 기기, 심지어 순수 예술 분야도 있습니다.
물량은 미세한 차이로 다양하지만 Diversified사(社)는 주물을 매달 약 3톤 정도 생산합니다. 공장에는 각기 다른 작업 처리용으로 가마가 몇 개 있습니다. 대부분 180kg 정도 되는 가마를 운용하지만 대형 파트 제작에는 500kg 정도 되는 가마도 사용합니다.
Diversified사에서 꾸준히 받는 주문에는 티타늄 임펠러가 있는데, 연간 주문량이 100개 정도 됩니다. 티타늄 가격이 상승하면서부터는 워크플로의 다른 부분에서 비용을 절감할 대체 방법을 찾아야 했습니다. 주조용 패턴을 SLA 3D 프린팅하는 것도 이런 대체 방법 중 하나로 티타늄 가격의 상승분을 상쇄시킬 수 있었습니다.
전통과 현대의 어울림
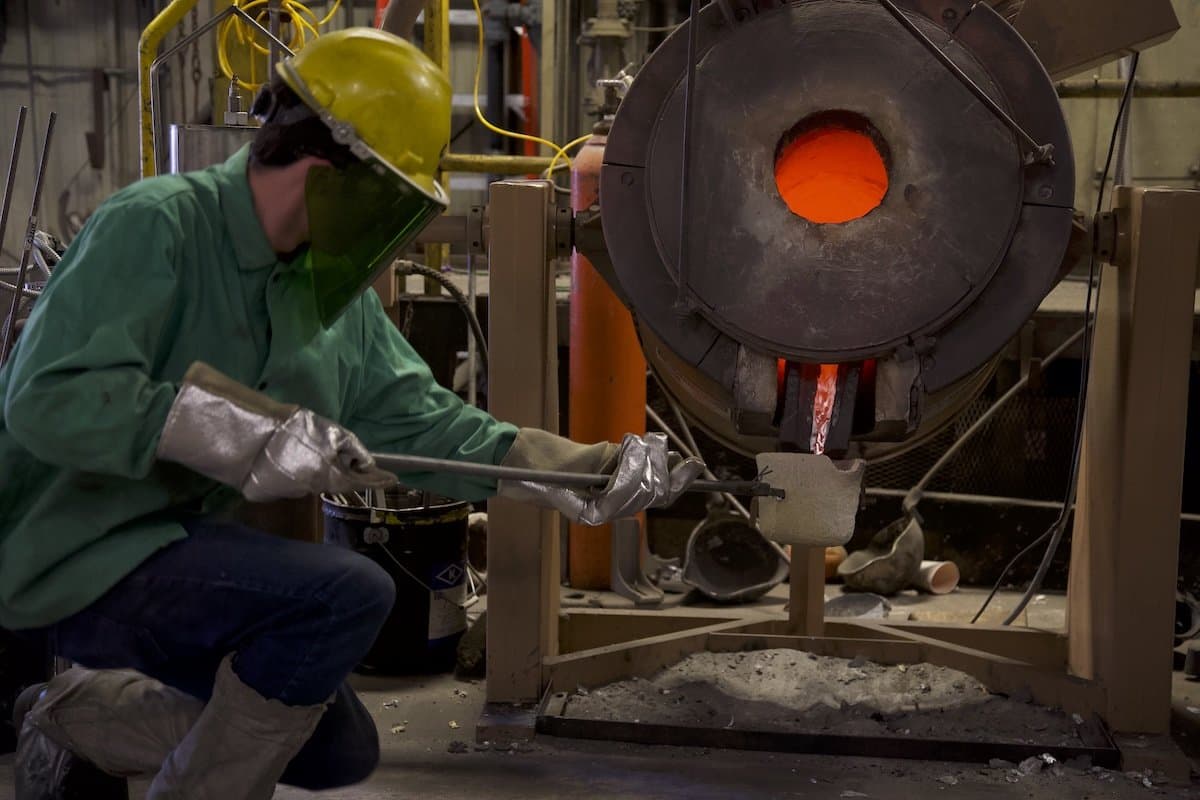
산업용 인베스트먼트 주조 업계에서는 아직도 워크플로의 많은 부분을 전통적인 공정으로 처리합니다. 예를 들어, 위에 보이는 것과 같이 용융된 알루미늄일 빈 거푸집에 부어넣는 작업이 그 한 가지 예입니다.
금속 주조는 어떤 면에서는 대단히 전통적인 산업이어서 그 핵심에는 수천 년을 변함 없이 전해 내려오는 워크플로가 있습니다. 또 어떤 면으로는 현대 제조 공정의 선구자 역할을 하는 주조 공장도 있습니다. Diversified사의 경우, Farr 부사장 외 직원들 덕분에 3D 프린팅 기술을 빠르게 도입한 얼리 어답터에 속합니다. Farr 부사장은 “3D 프린팅으로 제작된 인베스트먼트 패턴에 어떤 형태로는 관여해 왔습니다. 시작은, 그러니까 90년 대 중반이었다고 할 수 있죠.”라며 회상했습니다.
그 시작은 (속이 빈 금속 공구에 액상 왁스를 주입하는) 전통적인 왁스 패턴 제작에 시간과 비용이 너무 많이 들어서 엄두가 나지 않았을 때 왁스 3D 프린터를 사용한 것이었습니다. 어떤 프로젝트에는 용해되는 왁스 코어, 냉각용 왁스, 용해되는 냉각용 왁스, 완전 조립 파트를 주입하는 데 사용되는 도구 등 네 가지 개별 도구를 사용해야 했습니다. 도구는 모두 맞춤형으로 제작하여 왁스를 부어 넣은 후 조립해야 했고, 부족한 부분이 있다면 그것이 어떤 것이든 (빈번하게) 다시 작업해야 제거할 수 있었습니다. Farr 부사장은 “왁스 인베스트먼트 패턴 하나를 만드는 데도 인시(한 사람이 한 시간 동안 일하였을 때의 일의 양을 나타내는 단위)가 너무 많이 들었습니다. 그날 더 우수하게 제작된 파트를 가져오는 것이어서, 노동의 관점에서 보면 그리 오래가지 못했죠.”라며 회상했습니다.
Diversified의 직원들은 3D Systems의 왁스 프린터와 ThermoJet 3D 프린터를 도입하여 전통적인 사출 워크플로의 1대1 대체품 역할을 하도록 자사의 워크플로에 통합했습니다. 몇 년 후 한 고객사에서 신제품을 소개했는데 PMMA 폴리머를 VoxelJet 바인더 제팅 프린터로 3D 프린팅한 것이었고 그때까지 이용했던 왁스 프린터와 비교하면 번아웃이 깔끔했고 치수적으로도 안정적이었습니다.
업계 어디서든 가격은 상승하고, 심지어 다른 폴리머 3D 프린터 업체에 아웃소싱해도 비용이 많이 들게 되면서 Diversified은 패턴마다 대략 $300를 지출해야 했고 장비를 인하우스에 도입하는 데 필요한 비용은 억대를 훌쩍 뛰어넘었습니다.
Farr 부사장은 “가격이 상승하자 마자 다른 방법을 찾아야 했습니다. FDM과 SLA 장비를 살펴 보았고 처음에는 FDM 프린터 다섯 대를 도입했습니다. 해당 장비의 서포트 구조는 용해할 수 있었기 때문입니다. 그때는 다른 것이 필요하지 않았죠.”라며 소회를 전합니다.
그러나 한 고객사에서 임펠러 100개의 연간 주문을 시도했을 때 Farr 부사장 팀은 새로운 솔루션이 필요해졌고 Formlabs과 Form 3L 대형 포맨 SLA 3D 프린터에 관해 다시 상담하게 되었습니다.
Formlabs 에코시스템을 이용한 금속 주조
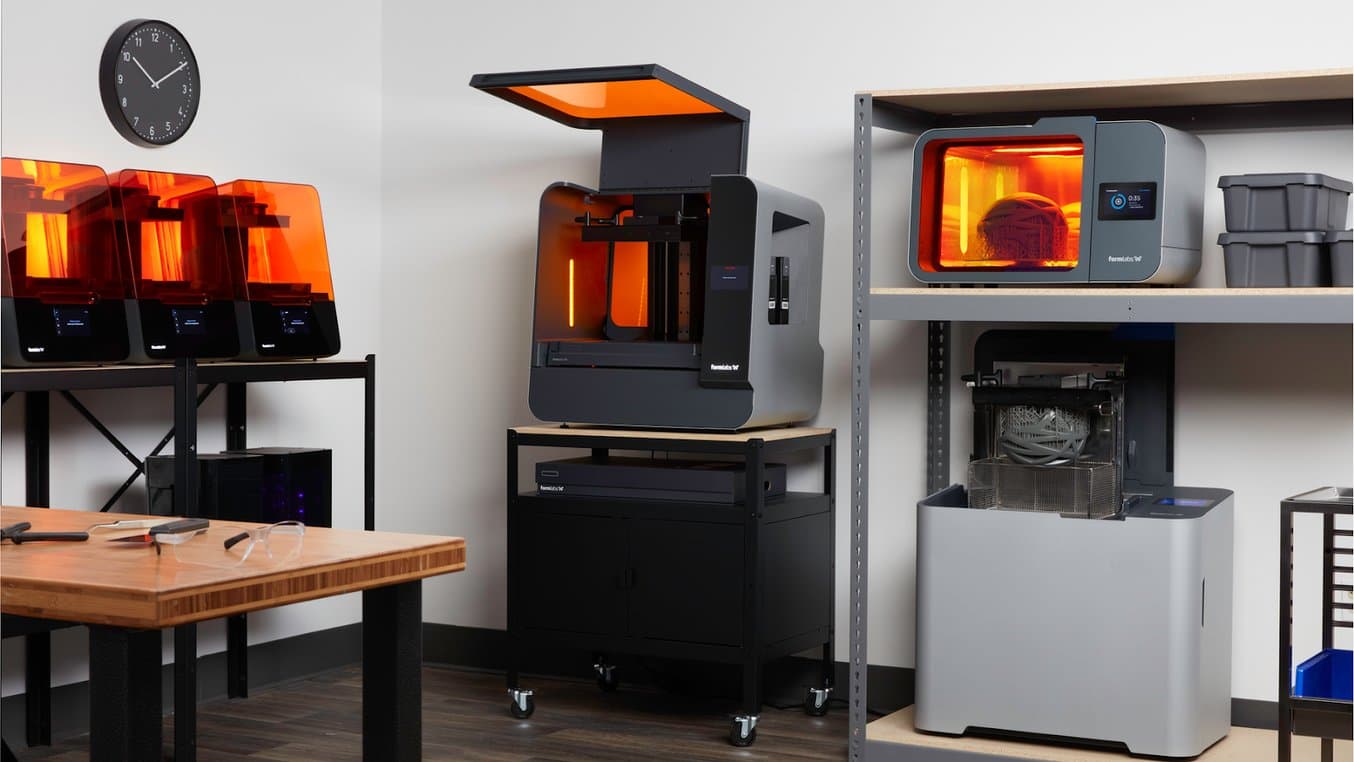
Form 3L, 후처리 솔루션 Form Wash L과 Form Cure L을 이용하면 취미용 데스크톱 3D 프린터로는 대응할 수 없는 대형 파트를 처리할 수 있는 데다, 워크플로 접근성이 우수하며 프린트물 품질도 극도로 우수합니다.
Diversified사는 몇 가지 사항을 새로운 3D 프린팅 솔루션에 요구했는데 이들은 번아웃이 깔끔하게 되는 소재, 안정적이고 사용하기 쉬운 에코시스템, 임펠러 프로젝트에 필요한 크기였습니다. Farr 부사장은 “우리가 보기에 전체 에코시스템과 지원 시스템이 타당했습니다. 프린터의 피팅과 마감 상태, 소프트웨어. 가격대가 비슷한 제품 사이에서 드물게 가장 우수했습니다”라며 설명합니다.Formlabs에서 프린팅한 테스트 파트를 받아 본 후, Farr 부사장은 Form 3L과 Clear Cast Resin을 즉시 자사의 워크플로에 도입할 수 있음을 알 수 있었습니다. 즉, 기존의 번아웃 온도, 슬러리 배합, 파트 설계를 변경할 필요가 없었던 것입니다. Formlabs 프린터로 제작한 패턴을 이용하자 파트에 게이팅 시스템을 직접 추가할 수 있게 되어 공정은 살짝 개선되기까지 했습니다.
“Clear Cast Resin으로 제작된 파트를 워크플로에 바로 도입했습니다. 좋은 점 하나는 게이팅 시스템을 파트에 직접 프린팅하여 정렬할 수 있다는 것입니다. PMMA로는 할 수 없었던 것이죠."
존 파(John Farr), Diversified Metalsmiths 기술 부사장
워크플로로 변경이 쉽다는 점이 증명되어 가장 마지막에 검증할 것은 번아웃 공정이었습니다. 여기서도 마찬가지로, Clear Cast Resin은 아웃소싱하던 PMMA 패턴을 효율적으로 대체할 수 있음이 증명되었고 심지어 비용은 그 일부에 불과했습니다. Farr 부사장은 “번아웃 공정은 PMMA를 사용할 때와 정확히 동일합니다. PMMA를 다루듯 하는 데 문제가 전혀 없어요.”라며 설명합니다 .
Diversified사에서는 Clear Cast Resin을 Form 3L 3D 프린팅으로 제작한 단일 임펠러 개당 소재비와 인건비로 $80을 지출하고 있습니다. 아웃소싱 비용인 $300와 비교하면 빠르게 프린터의 ROI에 도달하는 한편 사용 사례는 확장하고 신규 응용 분야도 개척했습니다. 주당 정확히 세 배를 프린팅하자 9개월도 채 지나지 않아 프린터 비용을 회수할 수 있었습니다.
아웃 소싱으로 제작한 PMMA 패턴 | 인하우스 제작 Clear Cast Resin 패턴 | |
---|---|---|
비용 | $300 | $80 |
리드 타임 | 2주 | 24시간 |
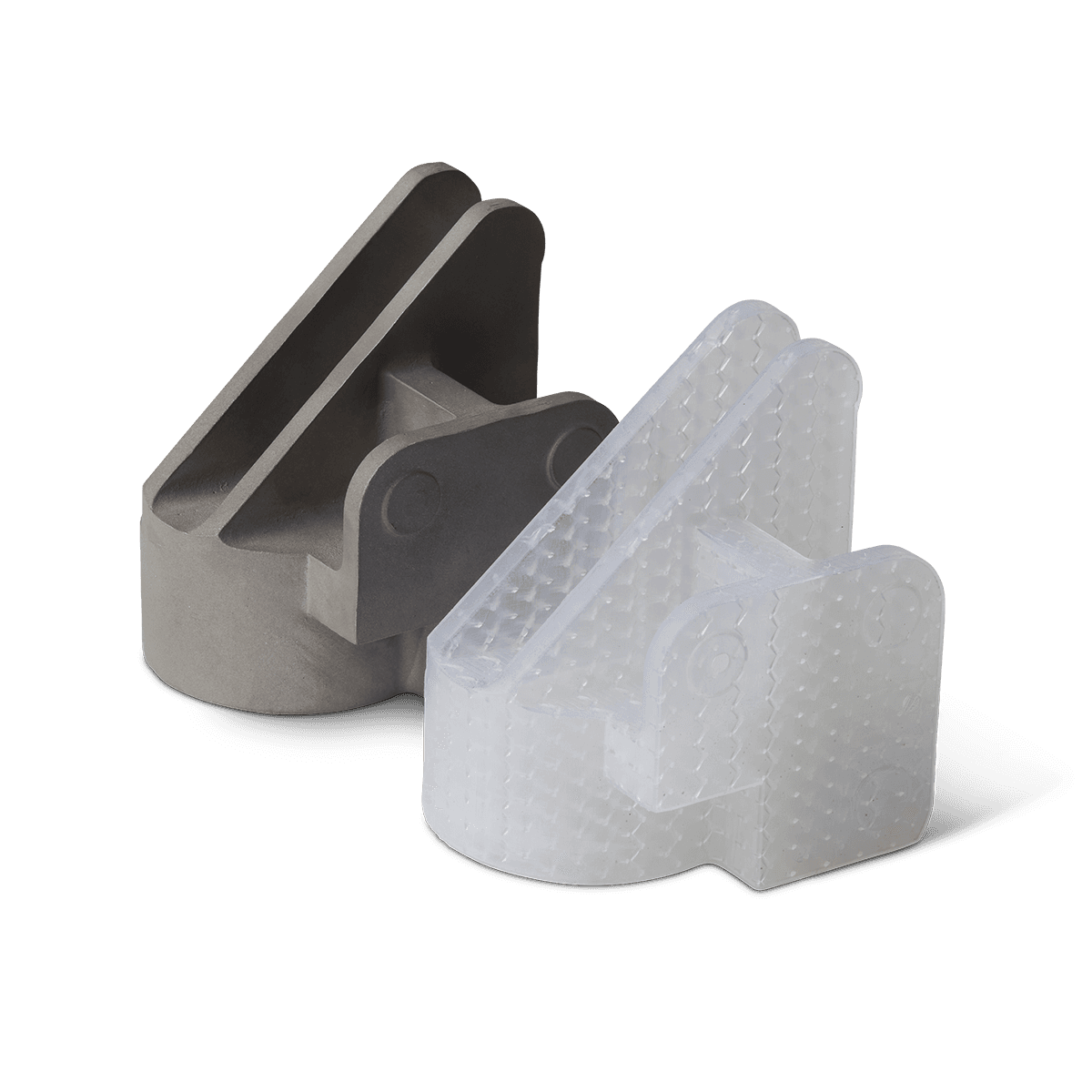
Formlabs의 Clear Cast Resin 3D 프린팅 패턴을 이용한 산업용 인베스트먼트 주조
본 백서는 몇몇 기존 주조업체에서 금속 파트 주조에 Formlabs의 광경화성 수지 조형 방식(SLA) 3D 프린터로 프린팅한 패턴을 활용한 공법을 제시합니다.
필요 물량에 정확히 맞아 떨어지는 도구
인베스트먼트 주조용 패턴은 공정마다 망가지게 되는 것이고 물량이 증가했을 때는 생산용 패턴을 예외 없이 모두 3D 프린팅으로 제작하는 방법이 항상 옳은 것은 아닙니다. 그렇지만 Form 3L과 Clear Cast Resin이 이상적인 도구로서 작용할 수 있는 '달콤한 지점'이 생산 물량에는 엄연히 존재합니다. Farr 부사장은 “한 고객사에서 문의하여 이런 파트를 천 개 요청한다면 그때가 툴링(공구 제작)을 할 시점입니다. 그렇지만 이런 공구를 제작하려면 $30,000이 들 수 있으니 그 비용을 정당화하려면 많이 만들어야 합니다.”라고 설명합니다.
Form 3L과 Clear Cast Resin 같은 인하우스 프린터와 소재를 보유하면 전체 작업 시간을 단축할 수 있고 복잡한 형상과 처음부터 정확한 치수를 얻을 수 있습니다.
Farr 부사장은 “모래로 제작된 패턴은 인베스트먼트 주조만큼 정확하지 않아서 3D 프린팅 인베스트먼트 주조 공정으로 생성된 완벽에 가까운 형상이 필요할 수 있습니다. 그런 공정을 이용하면 뭔가를 갈아내야 하는 공정 전후의 작업에 필요한 시간을 절약할 수 있습니다. 3D 프린팅을 이용하면 시간을 절약할 수 있습니다. 버튼 하나만 누르고 작업장을 떠나 다른 작업을 하고 주조 후에는 기계 가공과 수작업을 건너뛸 수 있습니다. 이렇게 절약한 시간으로 3D 프린팅 비용을 보상해 줄 것입니다.”라고 설명합니다.
Clear Cast Resin 프린팅 첫 걸음
업계에서는 수십 년간 3D 프린팅을 인베스트먼트 주조 워크플로에 사용해 왔습니다. 물론 상황에 따라서 적합한 솔루션이 아닐 수도 있지만 소재 과학의 진보와 프린트물의 정확도 덕분에 특정한 작업에서는 더 효율적인 도구로 작용할 수 있습니다.
Form 시리즈 SLA 3D 프린터와 Clear Cast Resin 3D 프린팅 패턴을 이용하면 프린트전 공정의 작업량을 축소하고 제작 후 파트를 연삭하거나 손수 기계 가공할 필요성을 경감하는 방식으로 전반적인 파트당 비용을 절감할 수 있을 뿐 아니라 워크플로의 변경 없이 새로운 기술을 도입할 수 있습니다.
Clear Cast Resin을 작업에 도입하려면 지금 주문해 보세요. 저희가 마련해 둔 백서에서는 3D 프린팅으로 제작된 패턴을 이용한 금속 파트의 인베스트먼트 주조법을 자세히 확인하실 수 있습니다.