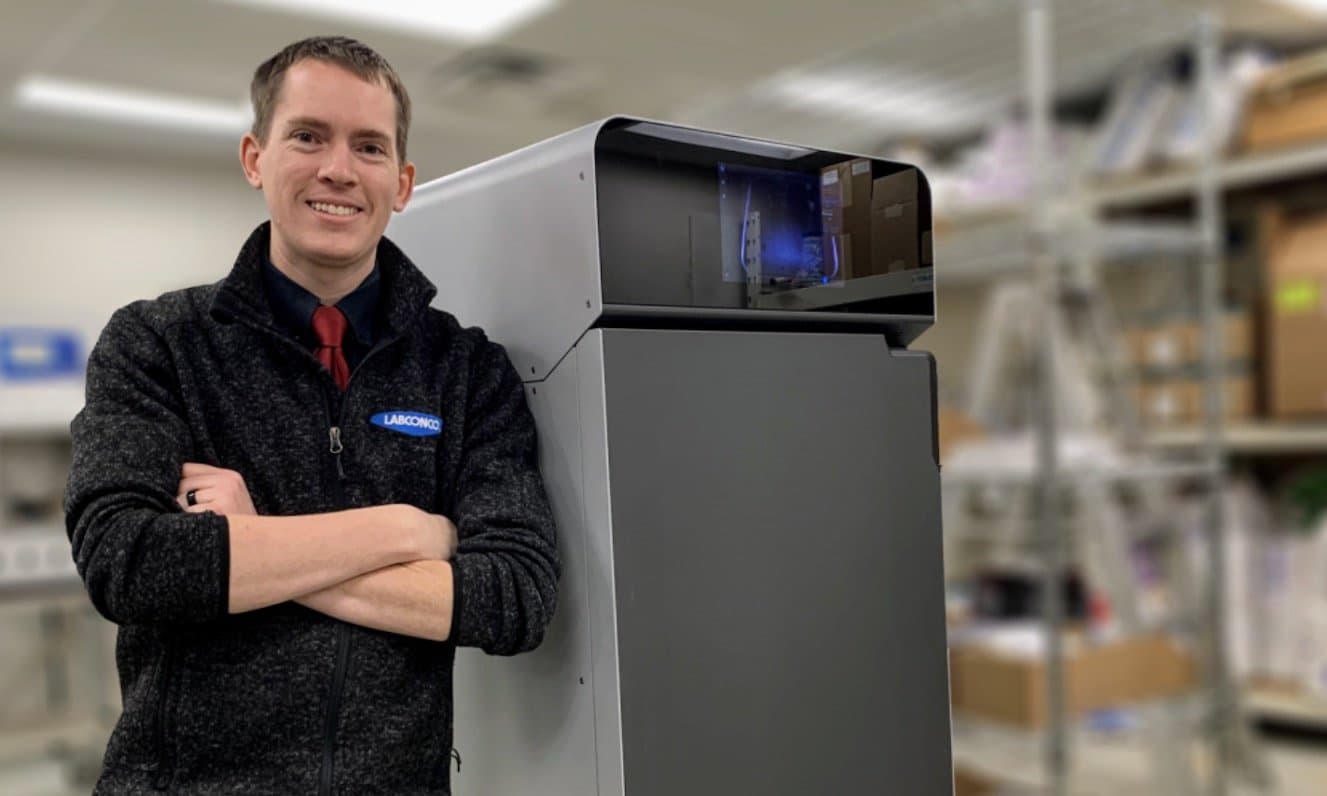
브렌트 그리피스(Brent Griffith) 씨가 2020년 초 Labconco에서 첫 번째 회의를 진행했을 때, 3D 프린팅은 회의실을 발칵 뒤집어 놓았습니다. 원래는 사출 성형으로 제작할 새로운 Logic Vue 제품의 작은 팬 스테이크를 두고 논의하기 위해 모인 자리였습니다. 신제품이고 아직 납품 수량이 정해지지 않았기 때문에 15,000달러가 넘는 장비를 들여 놓고 첫해에 100개의 파트만 생산해야 할 수도 있었습니다. 그 결과 파트당 비용이 상승하자 그룹은 새로운 솔루션을 찾게 되었습니다. Labconco 제품 엔지니어 브렌트 그리피스 씨는 “저는 '저기, 저걸 3D 프린팅하면 내일까지 1년치 분량을 완성할 수 있을 것 같습니다'라고 했죠. 그리고 갑자기 회의실이 조용해졌습니다,”라며 회상했습니다.
당시, Labconco에는 인하우스 3D 프린터가 한 대도 없었습니다. 그리피스 씨가 다음 날 집에 있던 프린터로 프린팅한 다양한 버전의 파트를 들고 출근했을 때, 3D 프린팅 비즈니스 사례는 그 자체로 빛을 발했습니다.
오늘날 그리피스 씨는 Labconco에서 Fuse 1+ 30W 선택적 레이저 소결(SLS) 프린터 세 대 , Fuse Sift와 Fuse Blast, Form 3L 광경화성 수지 조형(SLA) 프린터 한 대, 여러 대의 융합 증착 모델링(FDM) 프린터를 갖추고 성장 중인 실험실을 감독하고 있습니다. Labconco는 식품 테스트에서 의약품 개발, 종양학 진단 및 법의학에 이르기까지 다양한 산업 분야의 실험실 장비를 제조 및 공급하는 기업입니다. 그리피스 씨는 현재 일주일에 수백 개의 파트를 프린팅하고 있으며, 이는 기계 가공 또는 성형으로 제조하는 부속품을 개선하고, 공급망 문제가 생산에 영향을 미칠 때 임시방편으로 사용되며, Labconco의 다양한 신제품 개발 단계에 보조적 역할을 합니다.
사례 구축
그리피스 씨가 처음 3D 프린팅으로 팬 스테이크 파트로 비즈니스 사례를 입증한 후에는 사무실 내 엔지니어들의 개발 작업을 지원하기 위해 다른 파트를 프린팅하기 시작했고, 대기열이 빠르게 늘어났습니다. 그리피스 씨는 “정말 너무 빨리 바빠졌어요.”라며 당시의 분위기를 설명했습니다.
3D 프린팅으로 또 어떤 것이 가능한지 알아보기 위해 그는 동료 엔지니어인 오스틴 오름(Austin Orme) 씨와 함께 Labconco 제품에 들어가는 수천 개의 부속품, 도구, 구성 품을 검사하기 시작했습니다. 그리피스 씨는 "빌드 볼륨이 뛰어나고 프로토타입과 생산 모두에 사용할 수 있는 고품질 파트를 프린팅할 수 있는 장비를 찾으라는 구체적인 지침이 있었습니다."라고 말합니다. “장비 한 대로는 성공에 필요한 광범위한 기능과 유연성을 활용할 수 없으니 한 대 가지고 작업을 수행하기에는 충분하지 않다는 것을 금방 알아차렸죠.” 연구실은 결국 Fuse 1+ 30W SLS 프린터 3대와 Form 3L 대형 포맷 SLA 프린터 1대를 포함하여 총 6대의 프린터를 추가로 구비했습니다.
“Formlabs의 레진 라이브러리를 활용하고 싶어서 Form 3L을 구매했습니다. 유연성을 확보하고 새로운 기회를 열 수 있을 거라고 생각했거든요. 그리고 우리가 기대했던 바를 정확히 실현했죠."
브렌트 그리피스(Brent Griffith), 제품 엔지니어
Form 3L로 이용 가능한 소재의 다양성과 Fuse 시리즈 프린터 3대의 중대 물량 생산량 덕분에 그리피스 씨는 기존 제품 개선, 수만 달러에 이르는 툴링 비용 절감, 기존 프로젝트의 개발 속도 향상, 온디맨드 방식 파트 교체 등의 효과를 모두 거두어 오고 있습니다.
Replace, Improve, Scale: 3D Printing Applications at Labconco
SLS 충전 센서: 성형으로 제작된 어셈블리를 대체
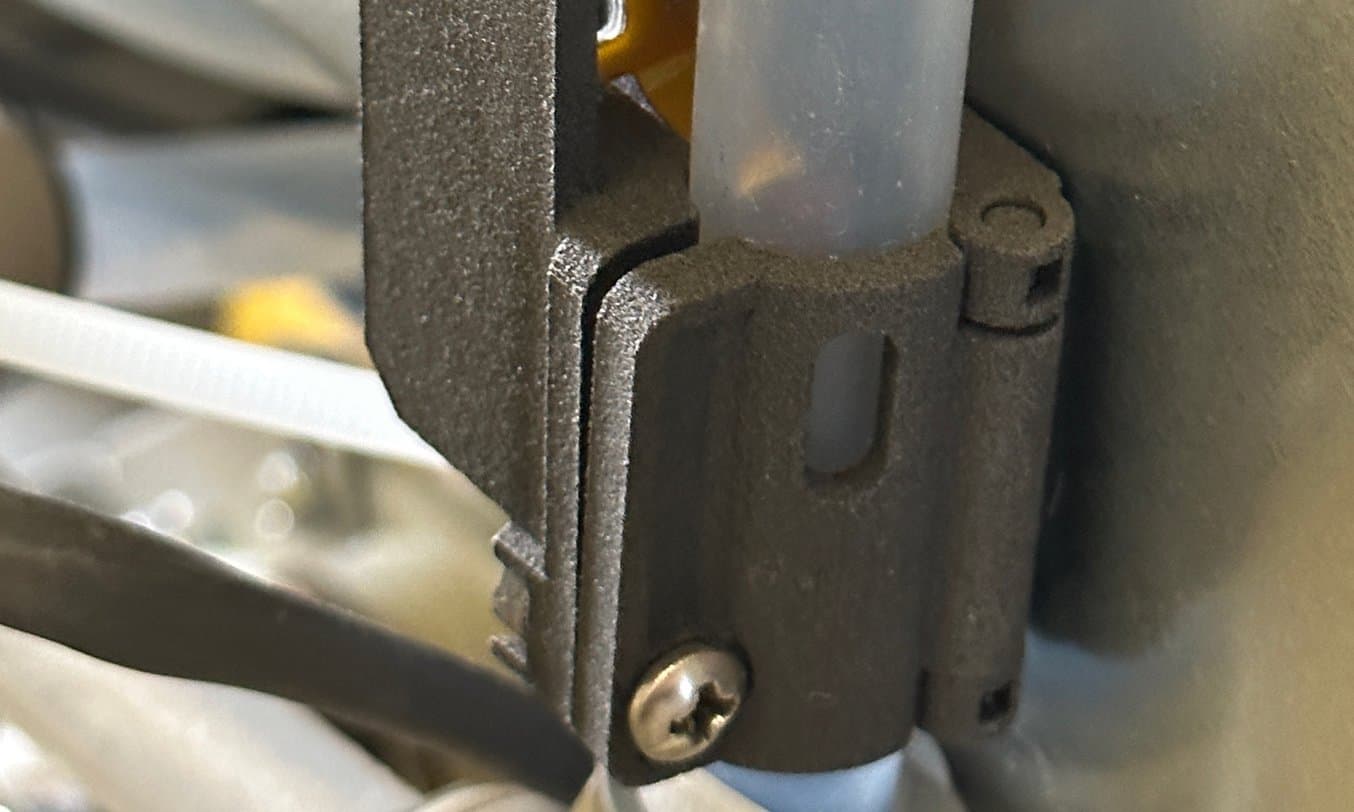
이 충전 센서 구성품에는 Labconco 제품 엔지니어 Tim Grove가 Nylon 12 Powder 표준 샘플을 보고 설계한 힌지 피처가 있습니다. 이 피처를 사용하면 부속품을 여러 부품으로 구성된 어셈블리 형태가 아니라 단일 파트로 프린팅할 수 있어 노동 시간과 재료 비용을 절감할 수 있습니다.
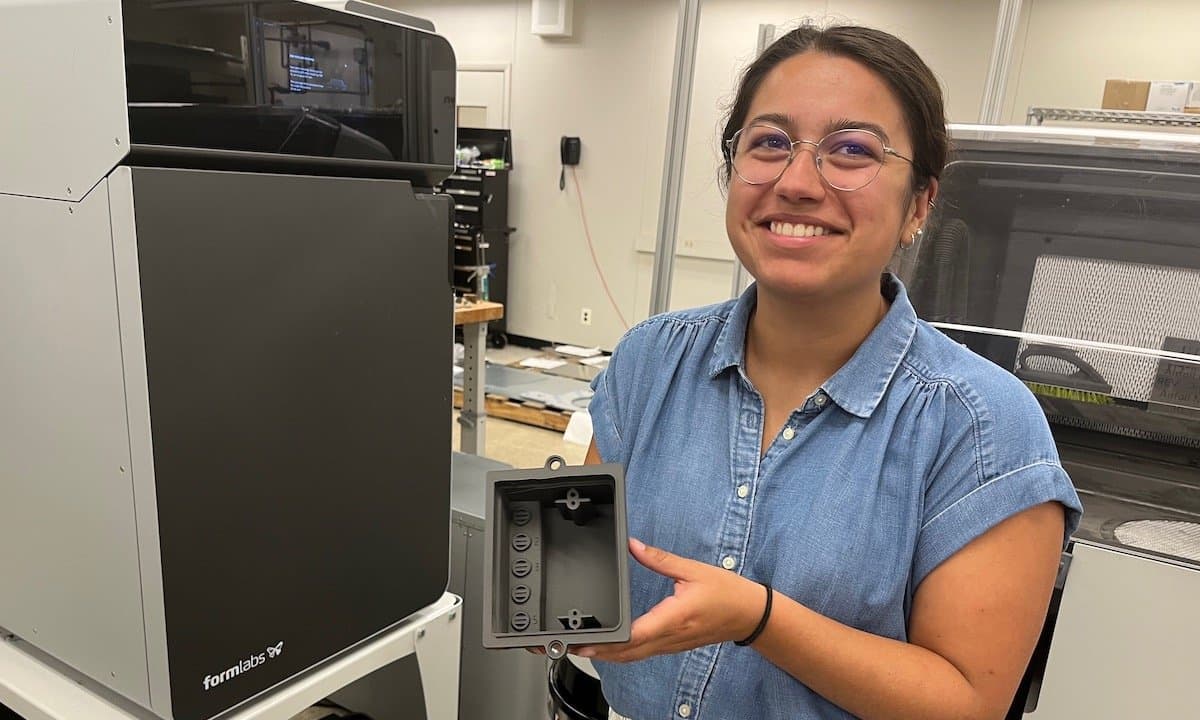
Labconco의 제품 엔지니어링 팀은 3D 프린팅 공간을 매우 효과적으로 확장할 수 있었기 때문에 많은 팀원들이 Fuse 시리즈 SLS 프린터 같은 산업용 기술에 접근하기가 쉬웠습니다. 그리피스 씨에 따르면 현재 Labconco의 여러 부서에서 3D 프린팅을 일반적인 워크플로에 통합하여 비용 절감, 유연성 확보, 공급망 보호 등을 실현할 방법을 고민하기 시작했다고 합니다.
Labconco의 유리 기기 세척기 라인은 적층 제조(AM) 파트를 비롯하여 최첨단 엔지니어링 혁신을 도입한 제품 라인입니다. 하나의 구성 요소인 충전 센서 마운트는 넘치는 것을 방지하려고는 예비 부품 역할을 합니다. 기존 방식으로 제작했다면 두 개의 개별 부품을 사출 성형한 후 핀으로 조립하여 서로 고정하는 방식을 채택했을 것입니다.
그러나 Labconco의 제품 디자이너 Tim Grove는 SLS 3D 프린팅으로 제작하면 비용과 시간을 절약할 수 있을 것으로 생각했습니다. Formlabs의 자체 Nylon 12 Powder 표준 샘플에 사용된 힌지 디자인에서 영감을 받은 Grove는 조립을 간소화하고 다양한 공구 주문과 관련된 비용을 없애기 위해 충전 센서 마운트를 재구상하는 작업에 착수했습니다.
그리피스 씨와 반복적으로 협업을 진행하던 Grove는 파트를 다양한 버전으로 프린팅하고 검토하여 완벽한 기능과 성능 저하 없는 파트를 개발했습니다.
그리피스 씨는 “힌지가 프린터 안에서부터 이미 작동하는 데다 준비된 상태로 프린터에서 나옵니다. 여기서 비용을 절감하고 생산 유연성을 확보할 수 있습니다. Fuse에서 막 꺼낸 Nylon 12 Powder 파트는 중간 정도 등급의 훌륭한 폴리머입니다. 여러 가지 응용 분야를 찾아냈고, 작동도 잘 합니다."라며 만족감을 드러냈습니다.
SLS 충전 센서 | Number of Components | Assembly Labor Time (per 50 components) | Cost Per Finished Part (with labor) | |
---|---|---|---|---|
Molded | 3 | 1시간 | $4.45/ea + tooling | |
SLS 3D Printed | 1 | 0 | $2.56/ea |
SLA Blower Wheel: Solving for Supplier Obsolescence
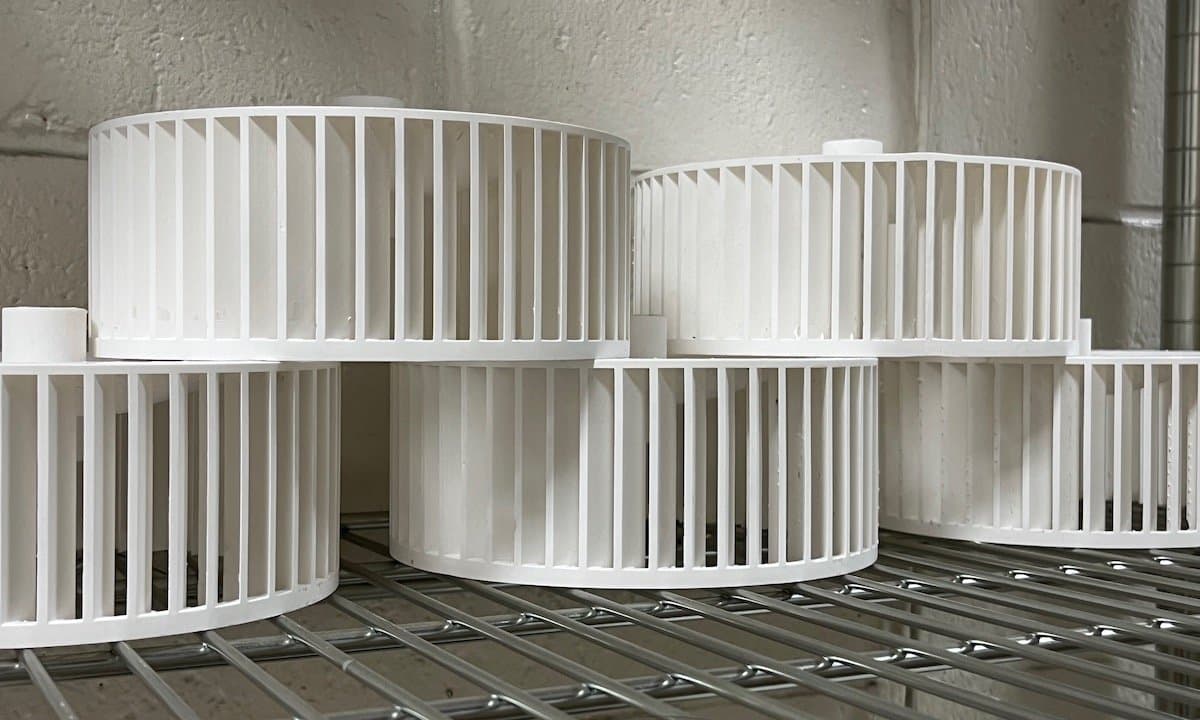
Labconco의 Kjeldahl 곡물 분석 제품에 사용되는 이 구성 요소는 이전에 외부 공급업체에서 구매했는데, 해당 공급업체가 부품 단종을 결정하기에 이르렀습니다. 그리피스 씨는 부품을 리버스 엔지니어링한 다음, 한 달 이상 매일 Rigid 10K Resin 을 Form 3L에서 프린팅하여 새 버전을 제작했습니다. 마침내 교체용 부품 재고를 확보하고 향후 공급망 문제로부터 부품을 보호할 수 있었습니다.
곡물 분석에 사용되는 Labconco의 Kjeldahl 장비에서 팀은 중요한 블로워 휠 부품용 공구를 생산하는 외부 공급업체와 협력하고 있었습니다. 수량이 적었고 공급업체는 제작용 공구의 수명이 다해 부품을 폐기하기로 결정했습니다.
Labconco는 새로운 툴과 금형의 설계 및 생산, 높은 자재 및 인건비가 예상되지만 새로운 공급업체를 찾아야 하는 상황에 직면했습니다. 그리피스 씨는 “수십 가지 솔루션을 검토했지만, 특히 화학적 호환성 측면에서 우리의 사양을 충족하는 솔루션은 없었습니다. 그래서 결국 사본을 가져와서 부품을 리버스 엔지니어링하고 최적화한 다음 Rigid 10K Resin으로 프린팅했습니다.”라고 설명했습니다. 그리피스 씨는 “테스트를 통해 견딜 수 있는지 확인한 결과, 최고의 솔루션이라고 판단했습니다.”
새롭게 출시된 대형 포맷 SLA 프린터인 Form 3L이 때마침 도착했고, 리버스 엔지니어링된 블로워 휠을 40일 동안 연속으로 프린팅하여 부품 재고를 다시 확보했습니다
그리피스 씨는 “Rigid 10K Resin을 여러 구성 요소에 꼭 맞는 소재로 사용해 왔습니다. 화학적 호환성은 산, 특히 이 경우 기화 황산과 관련하여 우리가 필요에 맞아 떨어졌습니다. 적층 가공으로 전환하자 공급업체와 재료를 검증하는 데 드는 수백 시간을 절약할 수 있습니다. 이런 점을 볼 때 정말 강력한 비즈니스 사례죠.”라고 단언했습니다.
SLA Blower Wheel | 비용 |
---|---|
Original Molded | $178.77 |
Redesigned and Printed in Rigid 10K Resin | $52.65 |
SLS Bearing Cage Separator: From $500 to $20
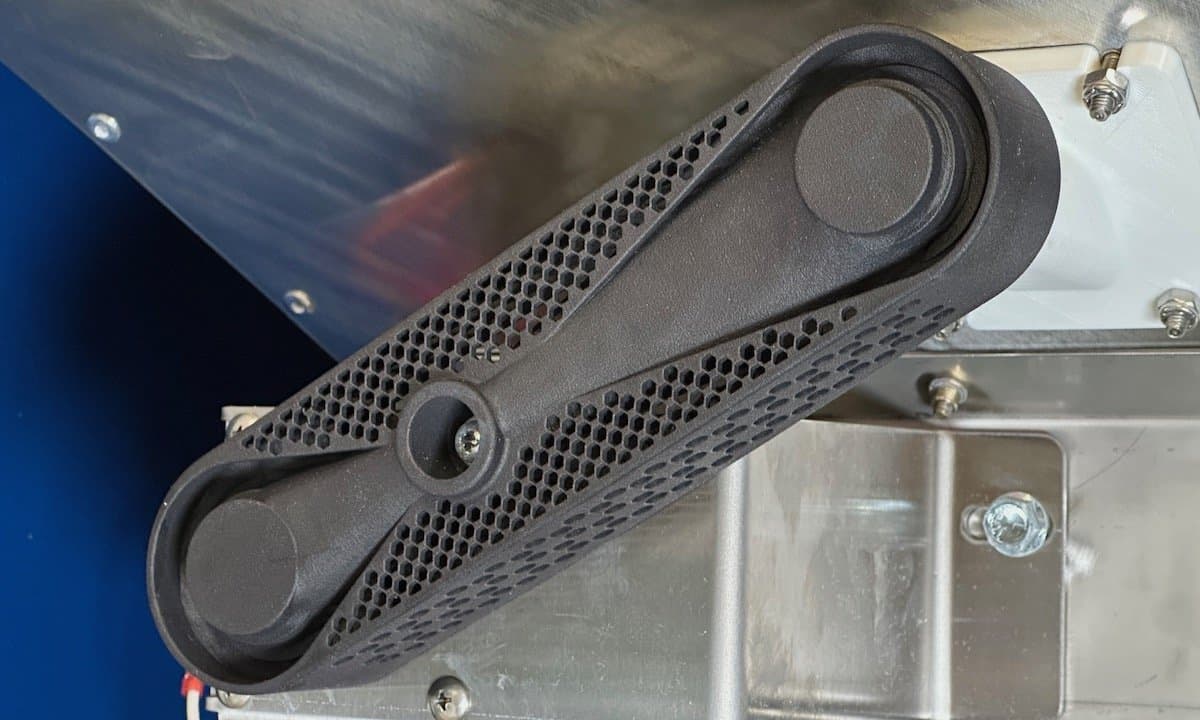
그리피스 씨는 외부 기계공이 약 $500에 견적한 베어링 케이지 분리기 구성품과 완전히 일치하는 파트를 프린팅할 수 있었습니다. 대신 그는 펜실베니아 주립대 적층 제조 및 설계 프로그램에서 배운 원리를 적용하고 SLS 3D 프린팅이 제공하는 기하학적 가능성을 활용하기 위해 파트를 재설계했습니다. 새로운 구성품의 가격은 약 $21였으며 Labconco는 수백 달러를 절약하고 리드 타임을 2일 이내로 단축할 수 있었습니다.
어떤 구성품은 구조가 비교적 간단할 수 있지만, 전통적인 제작 방식으로 제작하면 여전히 비용이 많이 들 수 있습니다. 한 기계공이 두 개의 베어링을 분리하고 베어링이 서로 잡아당겨지는 것을 방지하는 분리기 부품에 개당 약 $500의 견적가를 제시했습니다. 이 부품은 신제품에 들어가는 것이었고, Labconco는 이미 3D 프린팅 실험실에서 사용 사례를 입증한 바 있었습니다. 그리피스 씨는 즉시 Fuse 1+ 30W로 분리기를 프린팅하기 시작했고, 기계공에게 아웃소싱할 때 드는 비용의 10분의 1 수준인 약 $45로 가격을 낮췄습니다.
개선 프로세스는 여기서 멈추지 않았습니다. 그리피스 씨는 펜실베이니아 주립대학교의 적층 제조 및 설계 프로그램을 통해 대학원 과정에서 습득한 원리를 적용하여 단순한 일대일 교체에서 전체 최적화 점검으로 프로세스를 재구성했습니다
“적층 제조의 기회주의적 측면과 제한적 측면을 적용하는 방법을 배우던 중 바로 이런 점을 발견했습니다. ‘AM으로 할 수 있을까?' 라고 묻는 대신, ‘AM으로 해야 할까?’라고 묻는 거죠. 이 경우 1:1 교체를 할 수 있지만, 그렇게 하면 AM이 제공하는 기회를 활용하지 못합니다. 실제로 프린팅 가능한 형상에 제약이 거의 없는 Fuse 시리즈 프린터사용했기 때문에 새로운 것을 시도할 수 있었습니다."
브렌트 그리피스(Brent Griffith), 제품 엔지니어
제너레이티브 설계를 사용하여 부품 전체의 소재를 줄이면서도 작업자를 보호하는 분리기의 안전 기능을 유지하는 실험을 했습니다. 하루 만에 그는 최적화된 설계를 수정했고, Labconco는 부품을 인하우스 SLS 3D 프린팅으로 제작하기 시작했습니다. 개당 단가가 약 $20이었습니다.
그리피스 씨는 “3D 프린팅은 지오메트리로 할 수 있는 일의 측면에서 엄청난 이점을 제공합니다. 부품을 경량화하거나 다른 설계 기법을 적용하면 이전에는 없었던 방식으로 부품을 결합할 수 있습니다. 제조를 사내로 가져와서 많은 비용을 절감할 수 있습니다."라고 합니다.
SLS Bearing Cage Separator | Cost (Including Labor) | 리드 타임 |
---|---|---|
Machined | $485.82 | 2~3주 |
1:1 SLS Replacement | $43.50 | 29 hours |
Optimized for SLS | $21.08 | 28 hours |
SLS Parts in Testing: Reducing Component Counts and Improving Functionality
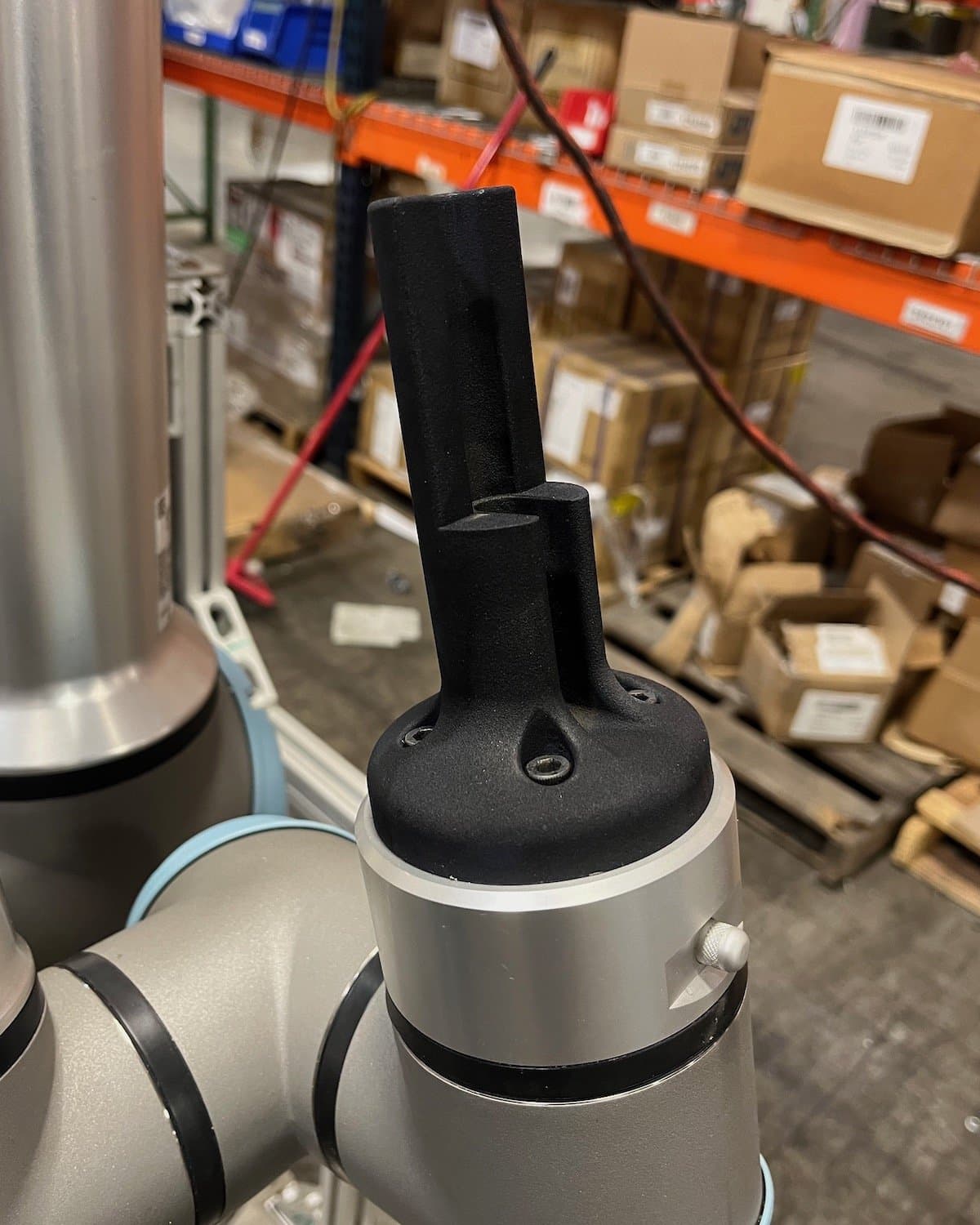
Labconco가 수작업과 로봇 액추에이터를 결합한 하이브리드 워크플로로 원활하게 전환할 수 있도록 그리피스 씨와 팀은 맞춤형 툴링과 이펙터를 설계한 후 Fuse 시리즈 프린터 대열에서 Nylon 12 Powder로 프린팅했습니다.
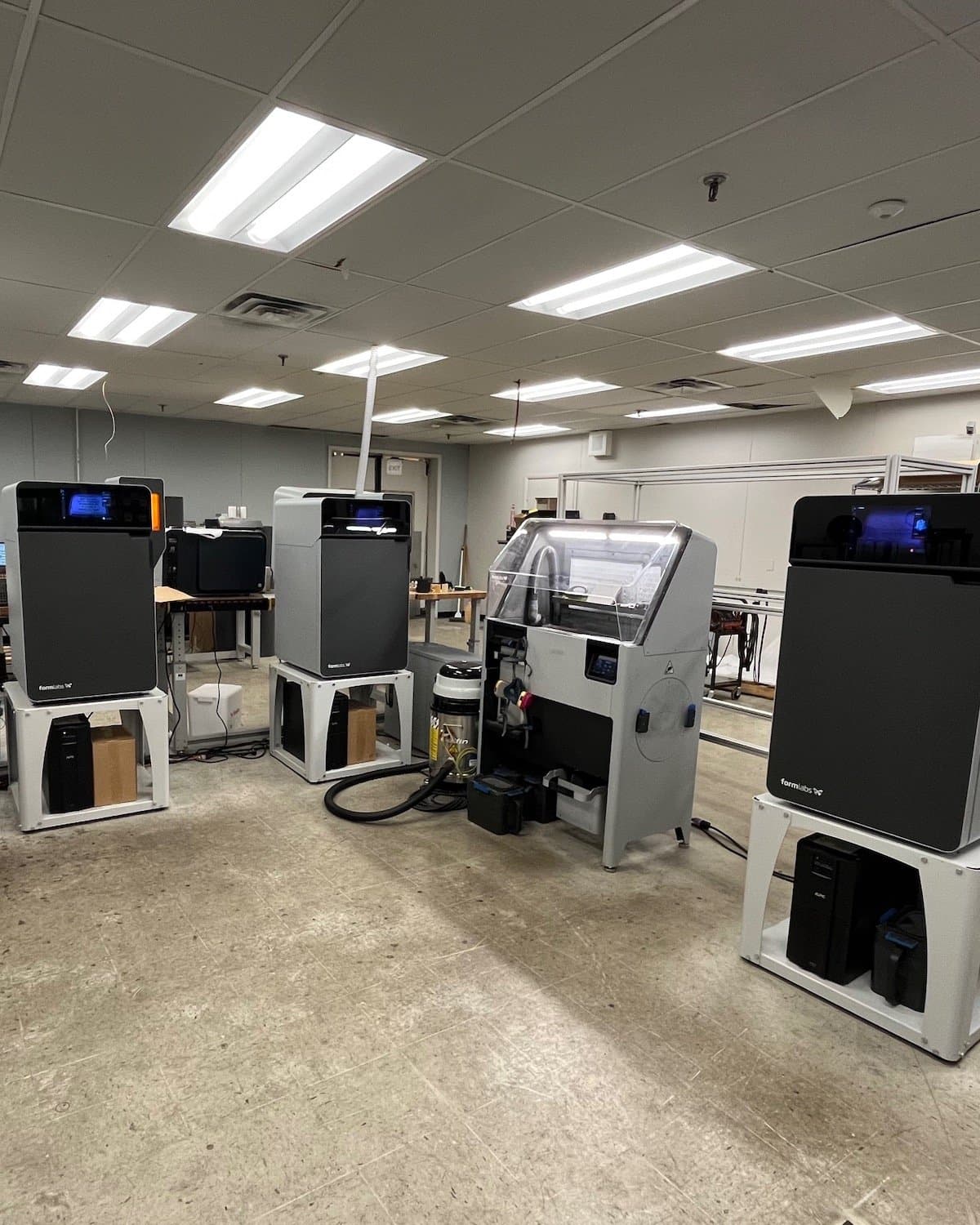
The compact size and low energy footprint of the Fuse Series SLS 3D printers means that as Griffith and the team expanded their range of applications for rugged, durable SLS parts, they could match it by scaling up their SLS operations.
Labconco의 타협 없는 우수성 추구는 주력 제품 중 하나인 생물학적 안전 캐비닛에 사용되는 핵심 부품 테스트까지 확장됩니다. 이러한 캐비닛은 특정 공기 흐름 패턴과 HEPA 필터에 의존하여 직원과 그 안에서 취급되는 제품을 보호하는 데 필수적입니다. 이러한 필터는 최고 수준의 성능을 보장하기 위해 엄격한 테스트와 인증을 거친 후 테스트가 완료된 것으로 표시됩니다.
과거에는 이러한 테스트 프로세스가 작업자에게 크게 의존했기 때문에 잠재적인 변동성과 한계가 있었습니다. 그러나 Labconco는 로봇 시스템의 성능을 활용하여 각 필터의 스캔을 완벽하게 정밀하게 자동화하는 혁신적인 접근 방식을 채택했습니다. 자동화로 전환하면서 테스트를 담당하는 로봇 팔 제작에 필요한 맞춤형 공구와 엔드 이펙터를 개발해야 했습니다. 기존 제작 방식은 비용이 엄청나게 많이 들고 수개월이 걸릴 수 있으며, 필요한 부품의 양이 적기 때문에 Fuse 시리즈 장비로 부품을 3D 프린팅하는 것은 혁신적인 접근 방식의 중요한 부분이었습니다.
Labconco는 Fuse 1+ 30W 에서 자체 생산한 SLS 부품을 사용하여 제품 안전 테스트의 정확성과 신뢰성을 높임으로써 이러한 부품의 일상적인 활용도를 획기적으로 향상시켰습니다. 이처럼 적층 가공을 중추적으로 도입한 덕분에 운영이 간소화되었을 뿐만 아니라 Labconco는 제품의 안전성과 성능을 보장할 수 있게 되었습니다
Effector Components | 비용 |
---|---|
Machined | $508.32 |
SLS 3D Printed | $73.44 |
Fume Hood Component: Mid Volume SLS Production for Increased Agility
Labconco는 퓸 후드 생산을 최초로 상용화한 회사로, 퓸 후드는 현재 가장 중요한 제품 사업부 중 하나입니다. 퓸 후드는 대규모 화학, 제약 또는 농업 벤처에 없어서는 안 될 필수 요소입니다.
사용자가 지정된 지점을 지나서 후드 새시를 열지 못하게 하는(따라서 에너지 비용을 절감하는) 기계식 새시 스톱 역할을 하는 한 구성 요소는 이전에는 사출 성형으로 제작했습니다. 단일 도구로 대량 주문을 진행하다 보니 대규모 고객을 위해 주문을 변경하거나 맞춤화할 수 있는 기능이 제한적이었습니다. 도구가 마모되면 공급업체는 교체 신뢰도가 떨어지기도 합니다. 그리피스 씨는 공급망 문제에 대응하기 위해 Fuse 1+ 30W로 이러한 새시 스톱을 프린팅하기 시작했고, 현재는 매주 50~100개의 부품을 Nylon 12 Powder로 생산하고 있습니다.
그리피스 씨는 “해당 부품을 성형하면 쉽게 수정할 수 없습니다. 흔한 일은 아니지만, 과거에 사출 성형 방식으로 부품을 만들었는데, 부품을 다시 가져와서 사용해보니 파손되거나 의도한 대로 작동하지 않아서 속이 상한 적이 있었습니다. 엔지니어들은 이제 일부 부품을 3D 프린팅으로 전환하면 필요 시 재설계하는 수고를 훨씬 덜 수 있고, 변경할 수 있는 옵션이 더 많아진다는 점을 염두에 두고 있습니다. 항상 달러 가치를 매길 수는 없지만, 적층 제조에는 종종 간과되는 '무형의' 이점이 상당히 많다고 생각합니다."라고 그리피스는 말합니다.”라고 합니다.
3D 프린팅 기술을 사내에 도입했을 대 얻을 수 있는 또 다른 이점은 이제 막 경력을 쌓기 시작한 젊은 직원들에게 자신감을 심어줄 수 있다는 점입니다. 새로운 도구를 주문할 때 필요한 절대적인 완벽함이 없어도 되기 때문에 새로운 것을 시도하거나 새로운 아이디어를 내놓을 의향이 더 많습니다. 그리피스 씨는 “젊은 엔지니어들은 부품을 보고 '이거면 되겠다'고 말할 수 있는 20년 경력의 엔지니어가 아닙니다 3D 프린팅을 통해 무언가, 심지어 많은 것을 시도해보고 실패하더라도 크게 상처받지 않고 오히려 힘을 얻을 수 있습니다."라고 합니다. “주어진 문제를 가장 창의적으로 해결할 수 있는 최선의 해결책을 찾는 데 집중하는 것이 우리가 원하는 인재상이며, 3D 프린팅은 이를 실현하는 데 큰 역할을 합니다.”
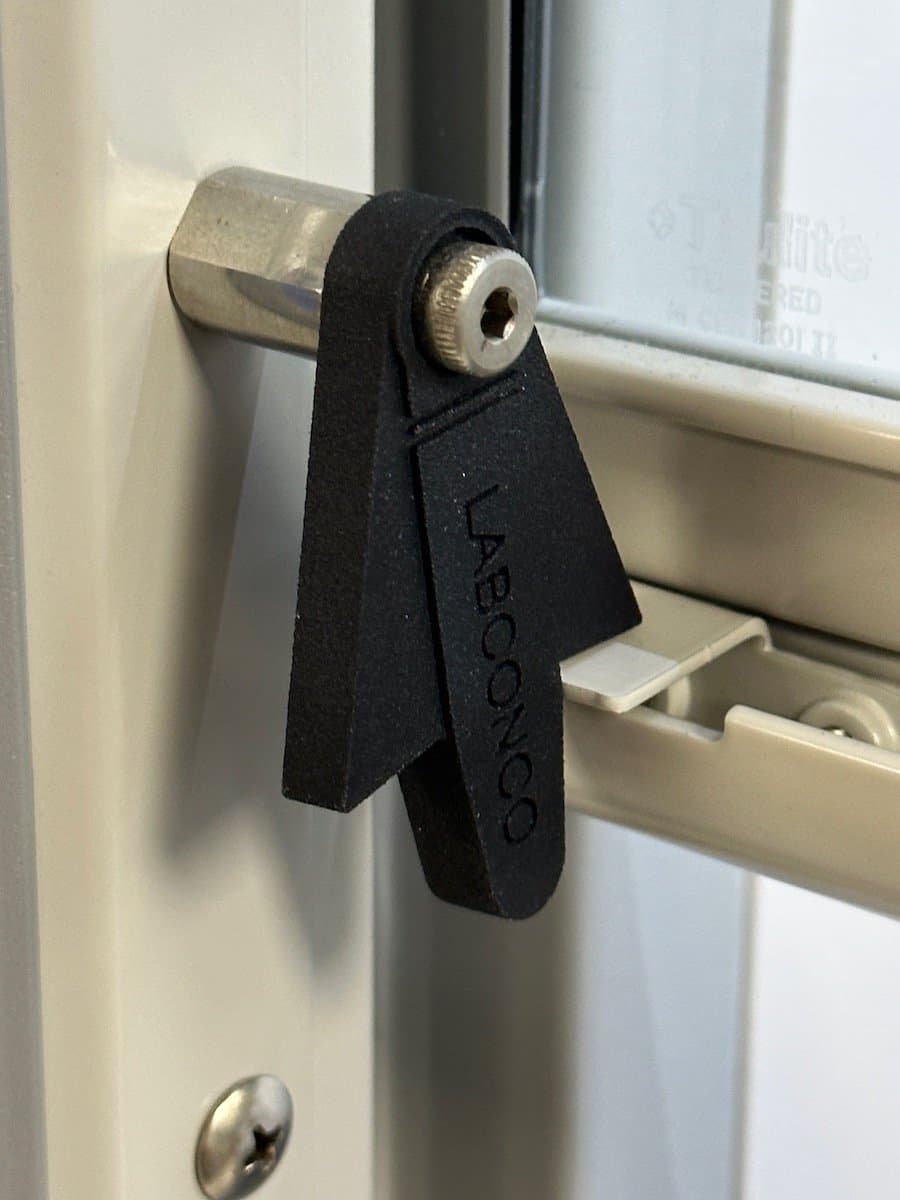
그리피스 씨는 Fuse 1+ 30W에서 Nylon 12 Powder를 프린팅하여 매주 50~100개의 새시 스톱 부품을 제작합니다. 이렇게 하면 하나의 툴링 워크플로에 고정되는 비용과 위험을 모두 피할 수 있습니다.
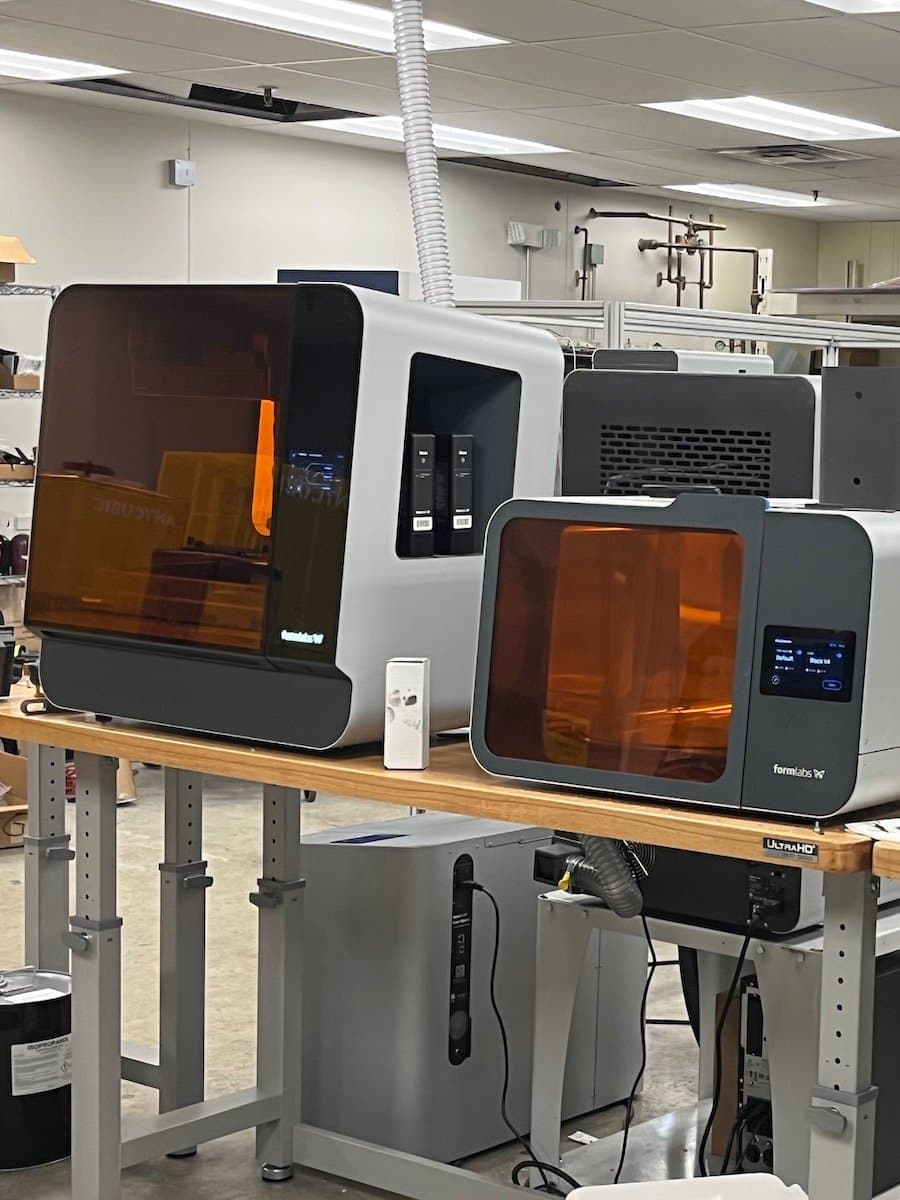
The ease of use of the SLS and SLA printers (like the Form 3L and Form Cure L shown here), mean that young employees just starting their careers can gain confidence in new technology and feel empowered to bring forth new ideas.
Labconco’s Fuse Blast Completes Their SLS Ecosystem
매주 100개 이상의 SLS 부품을 생산해야 하는 상황에서 미디어 블라스팅과 청소 같은 수동 후처리 단계에는 몇 시간의 수작업이 필요했으며, 이 시간을 더 가치 있는 설계 및 엔지니어링 작업에 투자하는 것이 더 효율적이었습니다. 그리피스 씨는 “회사는 우리가 가만히 앉아서 파트를 수작업으로 청소하기 보다는 새로운 비즈니스 기회를 찾고 파트를 재설계하고 비용 절감 방법을 찾는 데 집중하기를 바랍니다.”라고 설명했습니다.
고비용 자동화 블라스팅 시스템을 사용하던 Labconco는 Fuse Blast를 추가하여 Fuse SLS 에코시스템을 완성하고자 했습니다. 단 십 분 만에 설치를 끝낸 그리피스 씨는 가득 찬 Fuse 시리즈 빌드 챔버 두 개 분량의 파트를 청소한 후 미디어 블라스팅까지 마쳤습니다. 그리피스 씨는 “설치는 아주 쉬웠습니다…크기는 수동 블라스팅 시스템과 거의 같았죠. 그러니 SLS 시스템을 갖춘 회사라면 누구나 하나 쯤은 갖추고 있는 수동 블라스팅 시스템을 비치할 공간이 있다면 문제 없이 도입할 수 있는 시스템입니다."라며 장비의 첫인상을 복기했습니다.
더 우수해진 파트 품질과 성능
Labconco의 담당팀은 단박에 매끄러워진 표면과 파트 품질에 차이가 생겨난 것을 알아챌 수 있었습니다.
“Blast는 즉각적으로 커다한 변화를 가져왔습니다. 그리고 엔지니어들, 제가 프로토타입을 제작하며 파트를 건네준 엔지니어들은 하나 같이 바로 파트가 바뀌었다는 점을 알아채기 시작했죠. 심지어 후처리를 자동화했다는 점을 말하지도 않았는데 말이죠. 파트에 분말 잔여물이 거의 남지 않아 표면이 매끄러워졌거든요. 촉감도 더 좋아지고 보기에도 좋아졌습니다. 당장에 알아챌 수 밖에 없었어요. 파트 품질에 일어난 변화를 간과하기가 어려웠죠”
브렌트 그리피스, Labconco 제품 엔지니어
표면이 매끄러워지고 분말 잔여물이 사라지자 저희가 생산한 파트의 성능에 기대하지 않았던 효과가 생겼습니다. SLS 방식으로 프린팅한 부속품을 Fuse Blast로 청소하자 기계가 더 부드럽게 작동했거든요. 그리피스 씨는 “실제로 우리가 생산한 일부 부속품에서 약간의 성능 향상을 확인했습니다. 전과 비교했을 때 너무 깨끗해졌어요. 특히 우리 제품을 초기에 시운전할 때 확연히 드러났죠.
결과는 고가의 자동 블라스팅 시스템으로 청소한 파트를 사용했을 때와 흡사했습니다. 그리피스 씨는 “두 제품 사이에서 큰 차이를 발견했다고는 말하기 어려워요. [Fuse Blast]는 자기 체급보다 강한 펀치를 날리는 권투 선수 같습니다.”라며 이어갔습니다.
후처리에 쓰는 시간은 더 짧게, 설계 최적화에 쓰는 시간은 더 길게
Fuse Blast로 이룩한 자동화는 직접 수작업으로 파트를 블라스팅하며 시간을 보내지 않게 해주었을 뿐만 아니라 그리피스 씨와 팀이 Fuse Sift에 소비하던 시간도 줄여주었습니다. 블라스팅 시간을 줄여 Fuse Sift를 작동하며 소비하던 시간의 일부를 보상하는 셈이었습니다. 이제 Fuse Blast에서 자동으로 사이클이 돌아가 깨끗한 파트가 생산되고 심지어 분말에 파묻혀 있던 파트도 자동으로 청소합니다. 그리피스 씨는 “[Sift 안에서] 분말을 얼마나 많이 털어낼 수 있을지 걱정하지 않습니다. 왜냐면 Blast의 성능을 파악하고 있으니까요. 이제는 Sift 안에서 파트를 청소한다는 것이 시간을 절약할 수 있다는 의미는 아니에요. 선별 작업을 좀 더 철저하게 했더라면 얻을 수 있었던 사소한 분말 회수 작업은 추가 인건비로는 정당화할 수 없습니다.”라며 차이를 설명했습니다.
매주 50개를 꾸준히 생산하는 파트를 그리피스 씨가 수작업으로 블라스팅하면 파트당 구멍 세 개를 파이프 크리너로 청소해야 합니다. Fuse Blast를 도입한 지금은 자동 사이클만 설정해두고 자리를 비웠다가 20~30분 후에 돌아오면 완벽하게 청소가 끝난 파트를 만져볼 수 있습니다. 그리피스 씨는 “Blast는 큰 반향을 불러왔습니다. 구멍을 정말 환상적으로 청소했어요. 저로서는 시간을 제일 많이 절약하게 된 부분이죠.”라며 만족감을 드러냈습니다.
Scaling 3D Printing Operations
그리피스 씨와 그의 동료는 3D 프린팅에 체계적으로 접근했으며, 초기 감사를 통해 처음 도입한 6대의 장비에 대한 사용 사례를 입증했습니다. 광범위한 부품 카탈로그에 대한 비용 절감, 노동력 절감, 디자인 개선 효과를 지속적으로 발견하면서 3D 프린팅 기능을 확장할 방법을 모색하고 있습니다.
그리피스 씨는 “어떤 부품이 제 책상에 올라올 때마다 제가 가장 먼저 하는 질문은 '이걸 개선할 수 있을까, 적층 가공을 통해 좀 더 개선할 수 있을까'입니다 이러한 기회를 찾는 것이야말로 우리가 가장 많은 비용을 절감하고 많은 구성 요소에서 가장 많은 비용을 절감할 수 있었던 부분이라고 생각합니다.”라며 이어갔습니다.
그 이점은 회사 전체에 명확하게 드러납니다. 특정 응용 분야나 틈새 응용분야가 필요한 고객과 협력하는 팀은 사내 소량 생산의 힘 덕분에 비용 효율적인 솔루션을 자신 있게 제안할 수 있습니다. 그리피스 씨는 “심지어 맞춤형 부품이 5개, 10개 또는 50개만 필요한 고객도 비용 효율적으로 이러한 수요를 충족할 수 있습니다. 이렇게 시장의 요구에 신속하게 대응할 수 있죠.”라며 이야기를 마쳤습니다.
그리피스 씨는 회의실 안을 조용하게 만든 첫 번째 사례부터 모든 규모의 제조업체를 위한 비즈니스 사례를 구축해 왔습니다. SLA 및 SLS 3D 프린팅을 통한 인하우스 생산은 새로운 응용 분야를 지원하고 비즈니스에 성공할 수 있도록 개선할 뿐만 아니라 제품 성능을 최적화하고 공급망 중단을 방지하며 비용을 절감할 수 있습니다.
SLS 및 SLA 인하우스 도입을 자세히 알아보려면 제조 영업팀과 상담 일정을 잡으세요.