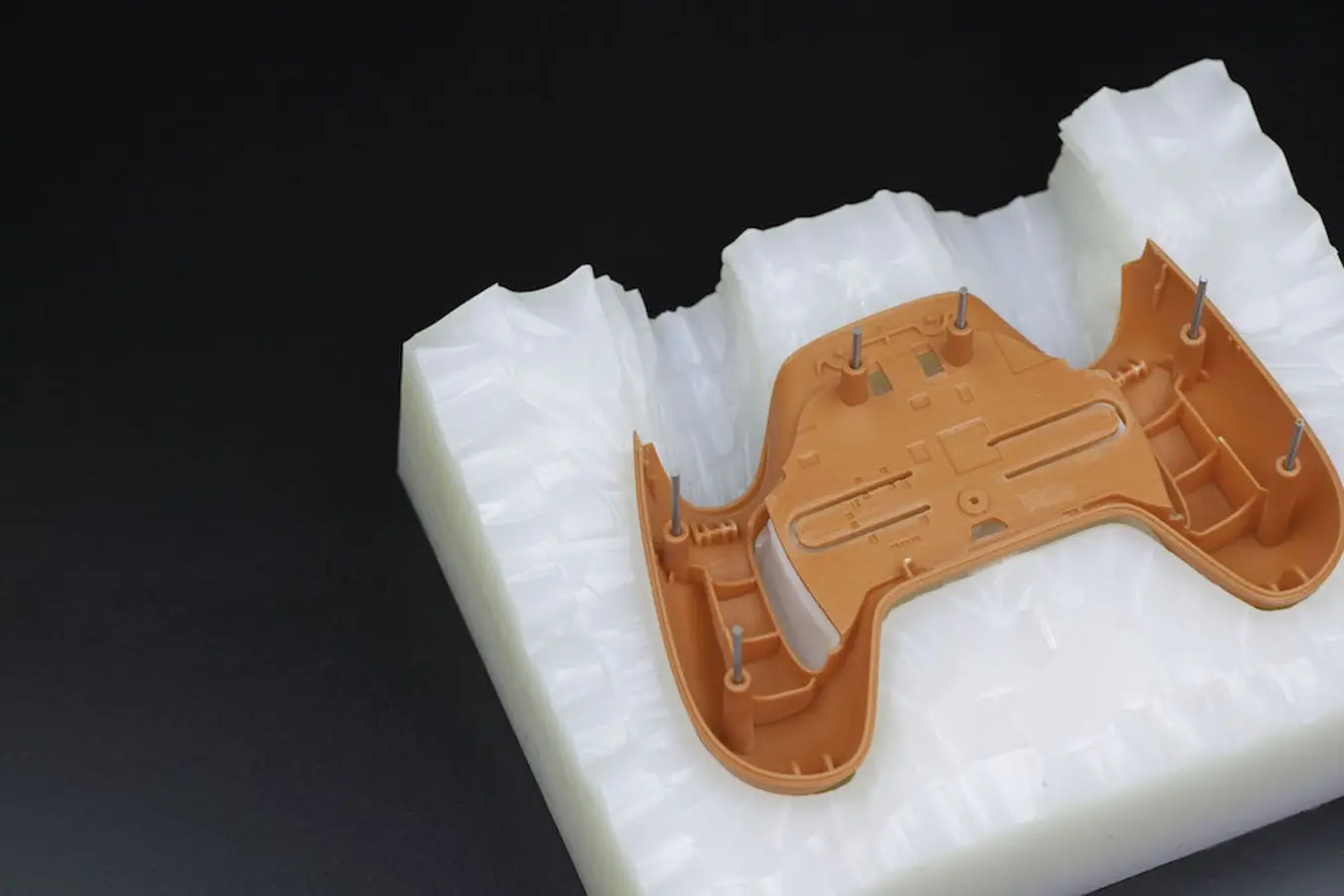
우레탄 주조로 제작된 프로토타입. 출처: Fictiv
진공 주조는 시장성 테스트용 프로토타입, 개인 맞춤형 제품, 환자 맞춤형 의료 기기 등의 소량 일괄 생산 실행에 흔히 사용되는 제조 공법입니다.
본 가이드에서는 진공 주조 공정의 구체적인 방법과 다른 생산 기술과의 비교, 최고의 우레탄 주조 장비, 그리고 진공 주조용 3D 프린팅 패턴 제작 방법까지 자세히 살펴보겠습니다.
진공 주조, 즉 우레탄 주조는 무엇인가요?
진공 주조는 사출 성형과 유사한 제조 공정으로 두 부분으로 구성된 실리콘 몰드 사이 캐비티(cavity, 동공)에 우레탄 레진을 주입해서 주조하는 방식입니다.
공정에서는 마스터 모델 주위에 실리콘을 부어 몰드를 만든 후 마스터 모델을 복제합니다. 고도로 숙련된 기술로 몰드를 두 개의 반쪽으로 잘라 마스터 모델을 꺼낸 다음에는 게이트 및 배기구 시스템을 구현합니다. 이어서 우레탄 기반 레진을 몰드에 생긴 캐비티에 부어넣고 진공 상태에서 경화하여 공기 방울이 생기는 것을 방지합니다.
결과적으로 원래 개체(마스터 모델)와 똑같은 개체를 우수한 정확도로 재생산하게 됩니다.
주의: 미국에서는 진공주조가 우레탄주조나 폴리우레탄 주조로 더 많이 알려져 있습니다. 이 글에서는 두 용어를 번갈아가며 사용할 예정입니다.
진공 주조 응용 분야
진공 주조는 생산 등급 품질과 흡사한 품질을 갖춘 품목을 소량으로 일괄 생산하는 데 잘 어울리는 제조 공정입니다.
공정을 거치면 최종 제품과 사실상 구분할 수 없을 만큼 고도의 디테일을 갖춘 모델을 만들 수 있습니다. 이런 이유로 우레탄 주조로 제작된 모델은 투자자 프레젠테이션, 무역 박람회, 상업용 사진 촬영에서 두드러지게 시선을 사로잡을 수 있습니다. 하나의 실리콘 몰드로 약 50개의 주물을 생산할 수 있으므로 개발 초기에 진공 주조를 이용하면 첫 번째 제품 시리즈를 출시하여 시장성을 테스트해 볼 수도 있습니다.
프로젝트에서 수요가 늘어나면 고객은 다음 몇 가지 옵션 중에서 골라 수요에 대응할 수 있습니다.
-
동일한 마스터 모델을 재사용하여 실리콘 몰드 여러 개를 제작할 수 있습니다.
-
마스터 모델 여러 개로 다중 캐비티 몰드를 제작할 수 있습니다.
-
실온 가황(RTV) 실리콘 대신 고온 가황(HTV) 실리콘 또는 고무를 사용할 수 있습니다. 이렇게 하면 내구성이 더 좋은 몰드를 제작할 수 있어 몰드당 300~500개의 주물을 제작할 수 있을 만큼 몰드의 수명이 늘어납니다.
마스터 몰드 제작 후 고작 10일의 리드타임으로, 사출 성형, 열성형, 원심주조 등 산업 등급 제조 공정에서 요하는 상당한 금액의 선행 투자 없이 주물 제품을 생산할 수 있는 진공 주조는 신속 프로토타입 제작 뿐만 아니라 브릿지 생산에도 유용합니다.
진공 주조를 이용하면 기계적 물성이 다양한 소재를 폭넓게 사용하여 표면 마감이 완벽하고 극도로 세밀한 모델을 제작할 수 있어 다음 최종 사용 제품을 소량 생산하는 데 적합합니다.
-
보철, 보조기, 청각 보조기 등 맞춤형 의료 기기
-
자동차 부품: 대시보드 패널, 손잡이, 게이지, 엠블럼, 후드 장식, 조명 렌즈, 인렛 매니폴드
-
소비자 가전: 인클로저, 컨트롤러, 사용자 인터페이스 패널, 센서 통합
-
로봇 및 산업 기계용 핵심 부품 및 예비 부품
-
소비재: 한정판 선글라스, 펜, 휴대폰 케이스
-
악기
-
과학 기기
-
스포츠 장비 애드온
-
예술, 피규어, 축소 모형, 소품
진공 주조는 또한, 복잡한 리버스 엔지니어링 워크플로에 의지하지 않고도 기존 객체를 복제할 때 흔히 사용되는 공정입니다. 조각품, 화석, 역사적 유물, 골동품, 수집품, 공예품 모델과 같이 희귀하거나 단종된 품목은 CAD 모델이나 다른 형태로도 도면이 없는 경우가 많습니다.
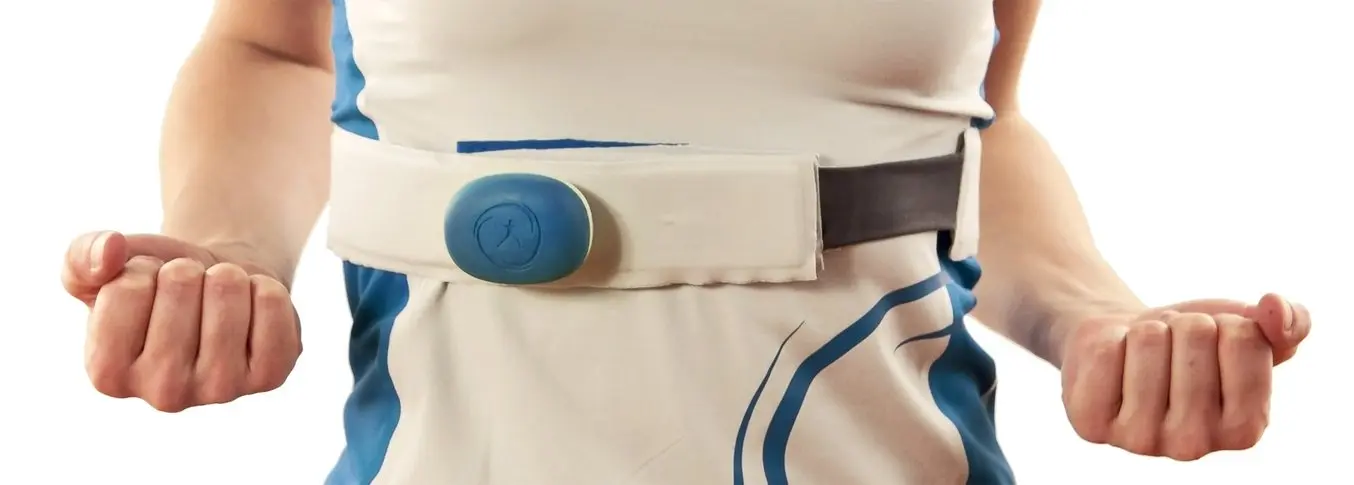
진공 주조로 제작된 실리콘 주형을 이용해 오버몰딩으로 제작된 웨어러블 호흡 센서용 전자기기 하우징. 출처: IDZone Product Design. 주조: Venture Rapid Technologies.
우레탄 주조 vs. 대체 공정
진공 주조 vs. 사출 성형
Product designers and engineers often turn to 3D printing for design validation, and make the immediate leap to injection molding for production validation. But the problem is that the cost of an injection mold, made out of CNC machined high-grade steel and good for millions of parts, can cost between $5,000 and $100,000 depending on part size and complexity.
That’s why lower-grade tools are often used as an intermediate step to hard tooling. An aluminum mold still ensures up to 1,000-5,000 molding cycles at a much-reduced cost. Because soft tooling processes are much faster and allow for a simplified mold design, they also roughly halves the lead time when compared to injection molding.
An acrylic mold or low-volume injection molding with 3D printed molds can be an option, depending on the quantities and part quality needed. A 3D printed mold created with a Formlabs SLA printer typically costs under $100 and delivers 100+ pieces without significant loss of quality.
However, product developers regularly overlook the fact that vacuum casting is often a smarter approach to cross the bridge from prototyping to production. Of all early-stage prototyping methods, the resin casting process bears the most similarities to injection molding. Additionally, it’s highly cost-effective; molds cost between $200 and $1,000, and a typical per-unit price is $10-$100.
A silicone mold for urethane casting is constructed in a similar fashion to an injection mold in that it has two halves—one forming the core, the other the cavity, and the liquefied material is injected in between those to form the final product. However, there are a few differences:
-
In injection molding, molten polymer is pushed into the mold cavity under high pressure and high temperature using a hopper and lead screw. Vacuum casting operates at low temperatures. Instead of molten plastic, it works with liquid resins that are drawn into the mold under a vacuum, much like the capillary action inside a plant stem. So while there are many different resins available to mimic various polymers, prototyping in the final injection-molded material is not possible.
-
After oven-curing, parts still undergo some post-curing for up to a week and remain vulnerable to UV radiation and high temperatures.
-
Because the mold is flexible, there are limits to part size and shape. Still, there are specific techniques to enable exceptions. For example, phased casting is the use of metal supports to counteract gravity for casting elongated parts in a three or four-part mold.
-
Vacuum casting handles variable wall thickness better than injection molding, because there is no heating-cooling cycle of the cast material. This results in less part distortion.
-
A silicone mold allows for significant undercuts in the part design. However, when testing for injection molding, it’s recommended to stick to the injection molded design as much as possible and build in the required draft angles of the final product.
-
Vacuum casting results in nearly zero waste, whereas in injection molding up to 20% of the used polymer is lost due to scrap rates, residues, and overproduction.
The high fidelity between a vacuum-cast model and a final product that pops out of an injection mold allows engineers to optimize the design for manufacturing. It provides them with a high-quality product preview without having to burden upper management with the astronomical fixed costs that can come with contract manufacturing at an injection molding factory.
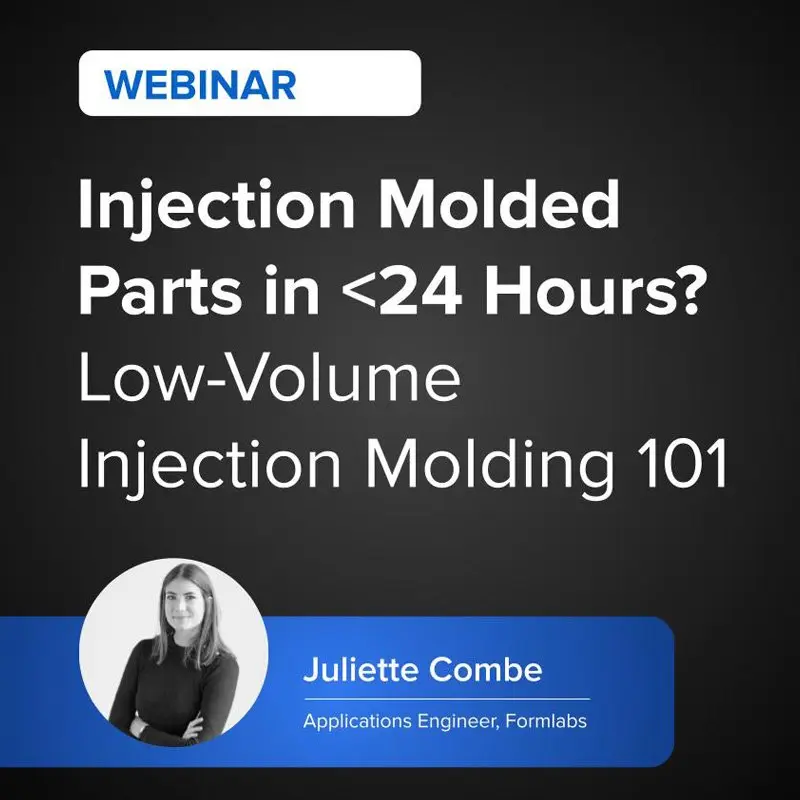
24시간 안에 제작하는 사출 성형 파트 소량 사출 성형에 관한 기본 사항
본 웨비나에서는 사출 성형 공정에서 광경화성 수지 조형 방식(SLA) 3D 프린팅 금형을 사용하여 비용은 절감하고 리드 타임은 단축하며 더 나은 제품을 출시하는 방법을 살펴보겠습니다.
진공 주조 vs. 3D 프린팅
흔히 3D 프린팅은 일회성 제작에 국한되어 있다고 오해합니다. 이와 반대로 3D 프린팅은 최종 사용 파트의 소량 생산에 사용할 수 있는 제조 방법입니다. 또한, 인하우스 프린트 팜에 투자하는 기업도 점점 늘어나고 있습니다. 줄지어 늘어선 3D 프린터로 소량 일괄 생산을 거치면 제품을 수백에서 심지어 수천 개까지 생산할 수 있습니다.
3D 프린팅과 진공 주조 사이에서 선택을 좌우하는 주요 요인은 제품의 기하학적 형상입니다. 진공 주조를 진행하는 목적은 명백하게도 사출 성형으로 제작된 파트를 시뮬레이션하는 것입니다. 본격적인 사출 성형을 대체할 수 있는 저비용 대안으로 오버몰드에 유연성과 강성을 결합하거나 인서트 몰딩을 통해 프로토타입에 직접 금속 부품을 추가할 수도 있습니다. 사출 성형이 가능한 소형 시리즈를 제작할 때는 진공 주조가 3D 프린팅보다 비용 효율적입니다.
진공 주조의 또 다른 장점은 3D 프린팅보다 훨씬 빠르고 저렴하게 대형 부품을 제작할 수 있다는 점입니다. 가장 긴 치수를 몰드로 만들면 약 50 cm이고 무게는 1.5kg까지 나갑니다.
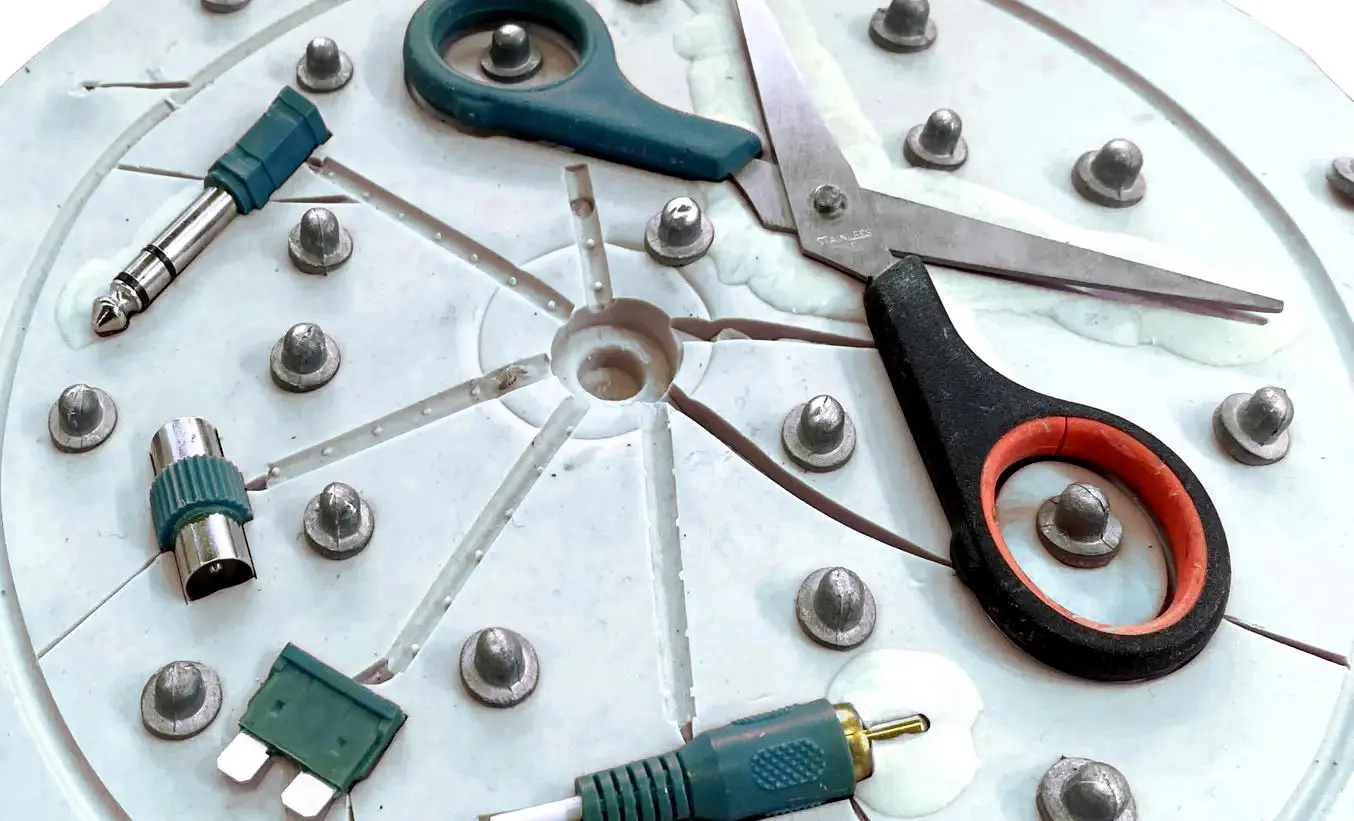
금속 인서트품와 실리콘 몰드를 사용한 진공 주조
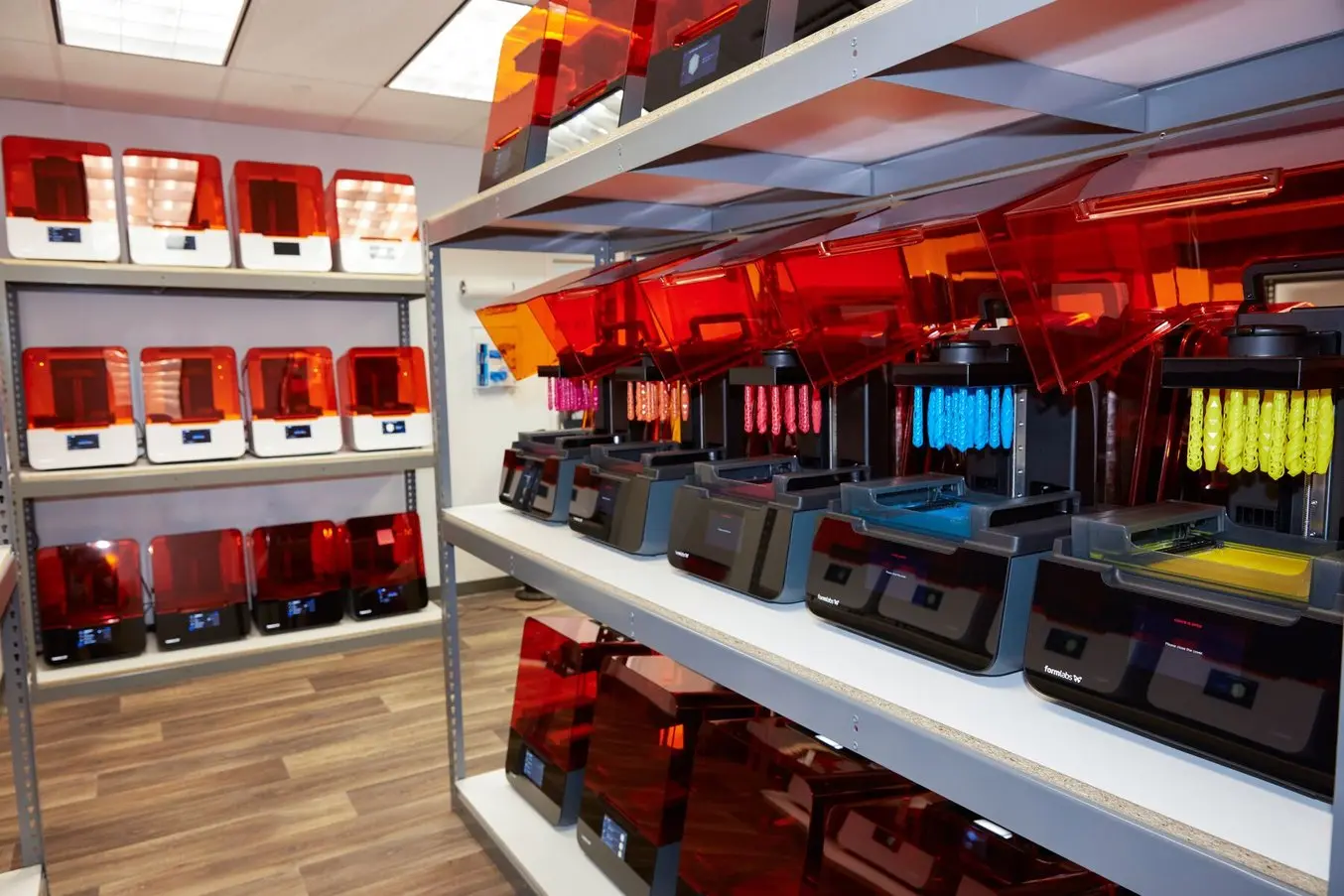
3D 프린팅 최종 사용 파트로 소량 생산과 맞춤형 제작 분야를 개척한 방법
웨비나에서 3D 프린팅을 이용해 맞춤형 생산과 최종 사용 파트 소량 생산을 신속하고 비용효율적으로 진행한 방법을 알아보세요.
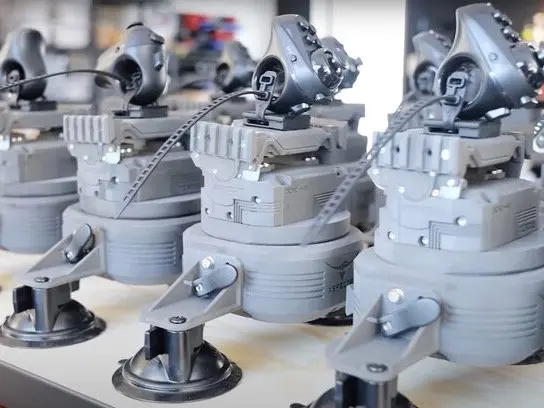
최종 사용 응용 분야용 3D 프린팅 파트의 피로 시험
이 백서에서는 사례 연구 및 피로 시험 결과를 포함하여 최종 사용 부품을 생산할 수 있는 Formlabs 3D 프린팅 하드웨어와 재료 솔루션을 소개하여 최종 사용 응용 분야에 대한 3D 프린팅 소재의 적합도를 검증해 봅니다.
비교: 진공 주조 vs. 대체 생산 방법
다음 다양한 제작 기술의 장단점을 살펴보겠습니다.
진공 주조 | 사출 성형 | 3D 프린팅 | 신속 툴링 | 기계 가공 | 수작업 | ||
---|---|---|---|---|---|---|---|
자유로운 설계 | ★★★☆☆ | ★★☆☆☆ | ★★★★★ | ★★☆☆☆ | ★★★★☆ | ★★★☆☆ | |
파트 크기 | ★★★★☆ | ★★★★☆ | ★★★☆☆ | ★★★☆☆ | ★★★★☆ | ★★★★★ | |
처리량 | ★★★☆☆ | ★★★★★ | ★★★☆☆ | ★★★★☆ | ★★☆☆☆ | ★☆☆☆☆ | |
가용 소재 범위 | ★★★☆☆ | ★★★★☆ | ★★★★☆ | ★★★★☆ | ★★★★★ | ★★★☆☆ | |
투자 비용 | ★★★☆☆ | ★☆☆☆☆ | ★★★☆☆ | ★★☆☆☆ | ★★★★★ | ★★☆☆☆ | |
파트 단가 | ★★★★☆ | ★★★★★ | ★★★☆☆ | ★★★★☆ | ★★★☆☆ | ★★★☆☆ | |
리드 타임 | ★★★★☆ | ★☆☆☆☆ | ★★★★★ | ★★★☆☆ | ★★★★☆ | ★★☆☆☆ |
진공 주조 공정
진공 주조는 4단계로 구성되어 있으며 고도로 숙련된 기술을 요합니다.
1. CAD 디자인
디자이너나 엔지니어가 Fusion 360이나 SolidWorks 같은 CAD 소프트웨어 환경에서 제작할 개체를 디지털 방식으로 표현합니다. 우레탄 주조로 제작할 파트를 설계할 때는 다음 지침을 염두에 두어야 합니다.
-
벽 두께 1.5 mm~4 mm. 절대적인 최소 두께는 1 mm입니다.
-
리브는 벽 두께의 60% 두께로 더 얇게 만들 수 있습니다.
-
3 mm를 초과하는 여유 반경을 사용합니다.
-
벽과 벽의 각도가 90 도가 되지 않도록 하여 파트 강도를 개선합니다.
-
두 쉘 사이에 0.5mm 홈을 제작하여 제품의 외관을 개선합니다.
-
나사 보스 벽 두께는 구멍 직경과 동일해야 합니다.
-
문자 음각 작업은 깊이가 0.25 mm일 때 가장 효과가 좋습니다.
작업이 끝나면, CAD 모델 데이터를 STL 형식으로 내보내 패턴을 제작합니다.
2. 마스터 패턴 제작
마스터 패턴은 주조 작업을 통해 도출될 복제품의 양각 모델입니다. 마스터 패턴은 실리콘 진공 주조 몰드와 정확하게 일치하는 복제품과 같으므로 3D 프린팅으로 제작된 패턴으로 원래 CAD 모델을 정확하게 구현할 수 있는 점은 특히 극도로 매끄러운 표면 품질을 얻을 수 있다는 측면에서 막대한 장점으로 작용합니다. 마스터 패턴을 잘 만들면 경도, 내화학성, 내열성 뿐만 아니라 내구성까지 갖추게 되어 시간이 흘러도 분해되지 않는다는 부차적인 특성도 있습니다.
지금까지는 CNC-가공으로 제작된 마스터 패턴이 표준이었지만 이 방식은 비용도, 시간도 많이 들었습니다. 게다가 구멍, 채널, 내부 직경, 유기체적인 곡선 표면을 구현하기 어렵다는 제약도 있습니다. 대조적으로 3D 프린팅은 현재 마스터 모델 제작에 지배적으로 사용되고 있는 첨단 기법입니다.
주류 분야에서도, 상업 분야에서도 사용할 수 있는 3D 프린터가 여러 기종이 있지만 우레탄 주조에 가장 흔히 사용되는 프린터 기종은 SLA와 SLS 방식 3D 프린터입니다.
SLA 3D 프린팅을 이용하면 표면 마감이 매끄러운 파트를 생산할 수 있어 진공 주조용 패턴에 아주 잘 어울립니다. SLA 방식 프린트는 올바른 프린트 설정이 갖춰져 있어 이미 표면이 매끄럽지만 사포와 광택 작업을 약간 더 하면 서포트 흔적을 제거하고 완벽하게 흠집이 없는 표면으로 마무리할 수 있습니다. Rigid 10K Resin 같은 일부 첨단 소재를 이용해도 탁월한 기계적 물성, 내열성, 내구성을 얻을 수 있습니다.
나일론을 SLS 방식으로 3D 프린팅하면 강도, 내열성, 정밀도를 모두 갖춘 프린트물을 얻을 수 있습니다. 이런 테크닉에는 서포트 구조가 필요하지 않아 파트에 박벽, 음각 디테일, 스냅핏, 힌지, 중첩 구조 또는 인터로킹 같은 정교한 피처를 구현하기에도 안성맞춤입니다. SLS 방식으로 프린팅된 파트의 표면은 우레탄 주조용 마스터 패턴으로 사용하기에 다소 거칠 수 있으나 미디어 블라스팅이나 진동 텀블링을 거치면 표면 거칠기가 줄어듭니다.
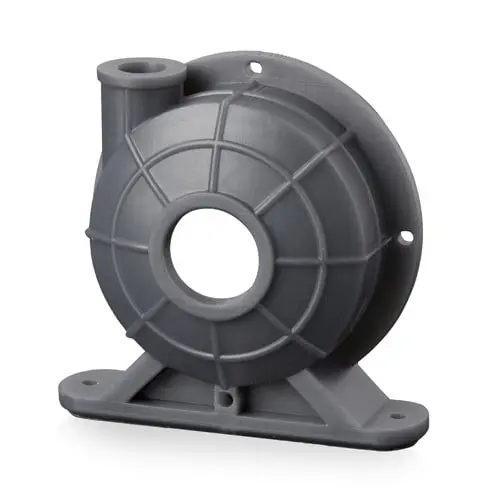
3. 몰드 제작
공정에서 가장 노동 집약적인 단계로 멜라민 보드와 열간 접착제로 몰드 상자를 제작해야 합니다. 그런 다음 마스터 패턴을 CA 접착제 몇 방울로 바닥에 고정합니다. 어떤 때는 마스터 모델 형태 대로 절삭날을 설계한 회전 공구로 포켓을 만들어 더 안정적으로 고정합니다.
반쪽 짜리 금형 두 개 사이에 분할선이 꼭 들어맞게 하려면 마스터 패턴과 하단 패널 사이의 구멍을 모두 메워야 합니다. 이런 작업에는 스티렌(Styrene) 블록과 플라스탈리나(Plastalina) 모델링 클레이 같은 소재를 선호합니다. 그런 다음 다월 핀과 레지스터바를 사용하면 나머지 반쪽 몰드와 완벽하게 맞아 떨어집니다.
2 액형 실리콘을 격렬하게 혼합한 후 진공 챔버 안에 부어 넣고 기체를 제거합니다. 그러나 그 전에 공기가 끼지 않도록 산(acid)성 브러시로 마스터 패턴의 작은 틈을 모두 실리콘 혼합물로 꼼꼼하게 채운 다음 실리콘을 다시 부어 주형의 첫 번째 절반을 만듭니다.
몇 시간 동안 경화한 후 주형 상자에서 주형 절반을 꺼내 거꾸로 뒤집습니다. 몰드 작업자가 숙련된 솜씨로 아크릴 통기구, 라이저(수직관), 충전 포트를 설치하여 공정의 나머지 반을 진행합니다. 실리콘 상단 표면에 이형제를 스프레이한 후 안쪽 깊숙한 곳까지 브러시로 펴바릅니다. 그런 다음 새 몰드 박스를 만들어서 두 번째 몰드 반쪽에 같은 방법으로 실리콘을 부어넣습니다.
진공 주조용 몰드를 준비하려면 몰드 상자에서 몰드를 떼어내 E236 우레탄 주형 이형제를 골고루 스프레이합니다. 반쪽 금형 두 개를 다시 모아 한 덩어리로 만든 후 다월핀과 레지스터 키로 정렬합니다.
4. 진공 우레탄 주조
이 단계에서는 진공 챔버에서 주조를 진행해 원래 마스터 패턴을 복제합니다. 먼저 몰드를 나무판에 테이프로 붙이고 통기용 빨대와 주입용 깔때기를 추가합니다.
2액형 레진을 계량하고 염료와 혼합하여 색상을 표현합니다. 그런 다음 진공 챔버에서 몇 분간 주조 재료에서 기체를 빼냅니다.
이제 폴리우레탄 혼합물을 주입할 준비가 되었습니다. 라이저 스트로로 캐비티가 가득 찼는지 알 수 있습니다. 70˚C에서 경화한 후, 몰드를 열면 원래 몰드의 디테일과 표면 텍스쳐가 구현된 복제품이 드러납니다.
마무리 작업은 주형 가장자리로 밀려 나온 과도한 재료 다듬기, 1000그릿 사포를 사용한 추가 연마 사이클, 오븐 경화로 이루어져 파트의 물성을 향상합니다.
전문가 팁
상기 공정은 대부분 전자기기 하우징, 보관용기, 기타 케이스 등 제품의 심미성이 중요한 표면에서 가시적으로 드러나는 분리선을 만들고 싶지 않은 박벽형 프로토타입을 제조할 때 사용합니다.
분리선이 비교적 덜 중요한 품목을 제작할 때는 마스터 패턴을 실리콘 블록으로 캡슐처럼 감싸고 수작업으로 잘라서 여는 것만으로도 충분합니다. 사인파 방식으로 잘라야 해서 경험과 손재주가 어느 정도는 필요합니다.
다음은 우레탄 주조에서 더 좋은 결과를 얻을 수 있는 몇 가지 모범 사례입니다.
-
스프레이형 이형제를 직접 모델에 분사할 때는 주의를 기울여야 합니다. 표면에 있는 미세한 텍스처를 메워 주조 시 표현이 안 될 수가 있기 때문입니다.
-
되도록이면 사용 전날 레진을 40˚C로 예열하고 가끔 병을 뒤집어 놓아 결정이 생기는 것을 방지합니다.
-
레진 병에 수분이 스며들지 않도록 주의합니다. 수분은 폴리우레탄에서 발포제 역할을 하기 때문입니다. 한 가지 방법으로 레진 사용 직후 아르곤 기체를 사용량 만큼 채우면 레진 안에 수분이 스며드는 것을 방지할 수 있습니다.
-
2액형 화학물질을 혼합할 때는 언제나 두 개의 컵을 사용해 고르게 혼합합니다. 첫 번째 용기에서 혼합된 레진을 직접 주입하면 혼합되지 않은 물질이 줄무늬를 만들어 주형이 망가집니다.
-
몰드 상자를 나중에 사용하기 위해 분해할 때 소독용 알코올로 열간 접착제를 느슨하게 만들어 줍니다.
-
파트의 다른 섹션까지 평균 거리가 가장 짧은 제품 모서리에 충전 포트를 설치합니다. 이렇게 하면 모든 영역을 채울 수 있습니다.
-
기포가 생기는 것을 방지하려면 한 지점에서 디테일한 표현이 많은 섬세한 영역 주변으로 부어넣고 그 위에 직접 부어넣지 마십시오.
-
주입구는 낮게 통기구는 높게 배치합니다.
-
화려한 광채가 나도록 마감하려면 금속성 분말을 추가하거나 전기 전도성이 필요하면 폴리피롤 또는 흑연 분말 사용을 고려합니다.
-
우레탄을 혼합할 때는 표면 위에 공간을 넉넉히 할애합니다. 액체 혼합물이 진공 챔버 안에서 전자레인지 속의 마시멜로 처럼 거품을 일으키며 올라오기 때문입니다.
-
전문적인 진공 주조기를 사용하면 공정 속도를 높이고 더 안정적인 결과를 얻을 수 있습니다.
진공 주조기
복잡한 공정 때문에 기업들은 대부분 우레탄을 주조하는 타사에 하청을 맡깁니다.
인하우스 진공 주조를 계획하는 기업이라면, 통합 솔루션으로 전문 진공 주조기를 사용하여 프로토타입 제작에 드는 노력을 한 단계 축소하고 공정을 가속화하여 생산량을 확대할 수 있습니다. 필요에 따라 소재와 색상이 다양한 주물 50개를 이틀 안에도 제작할 수 있습니다.
진공 레진 주조기는 냉장고 크기의 장치로 혼합에서 주조, 경화까지 모든 과정을 자동화할 수 있는 장비입니다. 장비를 이용하면 작업자가 챔버 압력, 혼합 속도, 컵 가열, 오븐 가열 같은 파라미터를 제어할 수 있습니다. 최신 시스템은 프로그래밍 기능이 있어 작업자가 맞춤형 단계를 생성하여 특정 소재와 제품 유형의 주조 주기를 최적화할 수 있습니다.
진공 주조기는 크기가 다양하여 제작할 수 있는 몰드의 크기도 다양합니다. 장비 모델 대부분에 레진 뿐만 아니라 사출 성형 수준의 나일론, 세라믹, 왁스, 심지어 저융점 금속 합금으로 주조하도록 설정하는 기능이 있습니다.
우레탄 주조기는 짧은 시간 안에 진공 상태를 만들어 수작업을 최소화하므로 선행 생산을 실행하기에 좋은 장비입니다. 단점은 비용이 수만 달러나 든다는 점입니다. 주얼리 진공 주조기는 크기가 한참이나 작고 가격은 대개 수천 달러입니다.
여기에서 성능 좋은 진공 주조기 몇 가지를 소개합니다.
-
Renishaw 5/01 PLC: 최대 몰드 크기 530 x 450 x 420 mm, 대략적인 가격 $45k. 이 기종보다 더 큰 5/04 모델은 최대 몰드 크기가 750 x 750 x 900 mm이며 유리 섬유 강화 나일론과 왁스 같은 소재도 사용 가능하지만 가격이 거의 두 배에 달합니다.
-
SLM VCM 04: 최대 몰드 크기 750 x 750 x 900 mm, 주조 부피 2.2L, 나일론과 왁스 주조도 가능합니다.
-
MCP 5/01: 최대 파트 크기 400 x 400 x 400 mm. MCP에는 파트 크기가 560 x 600 x 600 mm인 MCP 003, 파트 크기가 900 x 750 x 600 mm인 MCP 4/04 , 파트 크기가 1300 x 750 x 800 mm인 MCP 4/05 등 규모가 더 큰 기종이 많이 있습니다. MCP 장비는 모두 프로그래밍이 가능하며 폴리우레탄 이외에도 왁스, 실리콘, 나일론을 다양한 압력으로 주조할 수 있습니다. 3D 프린팅으로 제작된 사출 금형과 함께 사용할 수도 있습니다.
-
Scott AM 1000: 최대 몰드 크기 500 x 450 x 425 mm, 주물 무게 1 kg. 4000 모델은 최대 몰드 크기 750 x 750 x 900 mm, 주물 무게 5 kg. 레진 외에도 세라믹과 금속으로 진공 인베스트먼트 주조를 진행할 수 있는 장비입니다.
-
Multistation CSV 340: 최대 몰드 크기 340 x 340 x 435 mm, 주조 부피 600 mL. CSV500 모델은 최대 몰드 크기가 500 x 500 x 635 mm이며 주조 부피는 최고 1 L입니다.
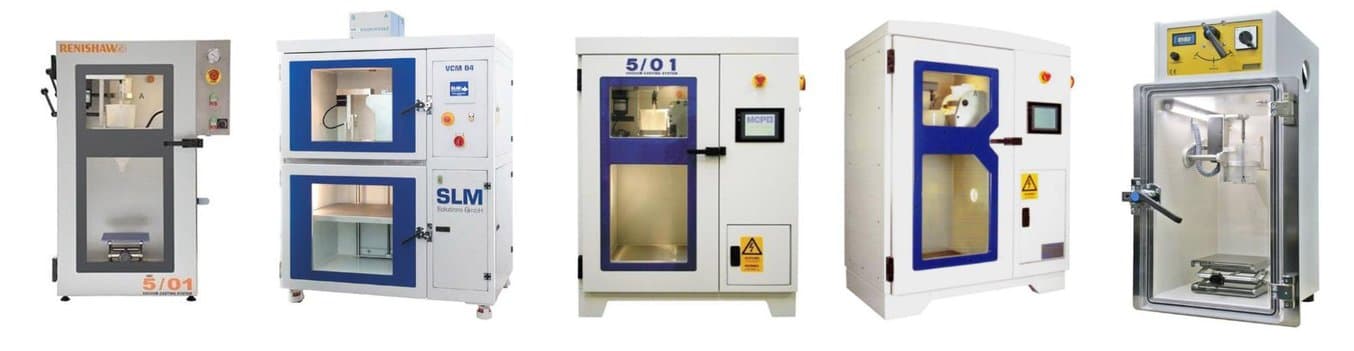
Renishaw, SLM, MCP, Scott AM, Multistation의 진공 주조기 라인.
진공 주조기 vs. 압력 챔버
저예산 대안으로 진공 중력 주조기를 직접 제작하는 것도 가능합니다. 몰드 내부에 기포 하나만 남아 있어도 전체 주조를 망칠 수 있기 때문에 기포 제거는 레진 주조 공정의 근본적인 과제입니다.
혼합물에서 기포를 모두 제거하려면 DIY 진공 주조기를 만들 때 진공 챔버 또는 가압기를 두 가지 기포 방지책으로 사용할 수 있습니다.
진공 챔버는 주형을 만들기 전에 실리콘 고무에서 공기를 제거할 때 사용할 수 있는 통입니다. 진공 흡입 방식은 고압 방식보다 경화 속도가 느리기 때문에 진공 챔버로는 경화 시간이 20분 이상인 저속 경화 레진만 작업할 수 있습니다.
진공 챔버에는 레버가 공기 흡입구용과 진공 펌프용으로 두 개 있고 진공에 도달했는지 확인할 수 있는 게이지와 탈기 상태를 확인할 수 있는 투명한 아크릴 뚜껑이 있습니다. 강화 유리 뚜껑은 플라스틱 뚜껑과는 반대로 시간이 흘러도 흠집이 생기지 않아 고가인 만큼 가치가 있습니다.
가압기는 조금 더 고가인데 이는 공기 압축기가 필요하기 때문입니다. 그러나 다른 한편으로 가압기가 기포가 없는 레진 혼합물과 주물을 제작하기에 가장 좋은 수단임에는 논란의 여지가 없습니다. 진공 챔버와 달리 몰드와 함께 사용할 수 있으며, 작업 기간이 짧은 속경화 레진으로 작업할 수 있으며, 기포가 100% 제거된 결과물을 얻을 수 있습니다.
진공 챔버는 석고, 콘크리트 또는 목재 주입물의 탈기 등 많은 응용 분야에 유용하다는 장점이 있는 반면 가압기는 일반적으로 실리콘 배치의 기체 제거에만 사용됩니다
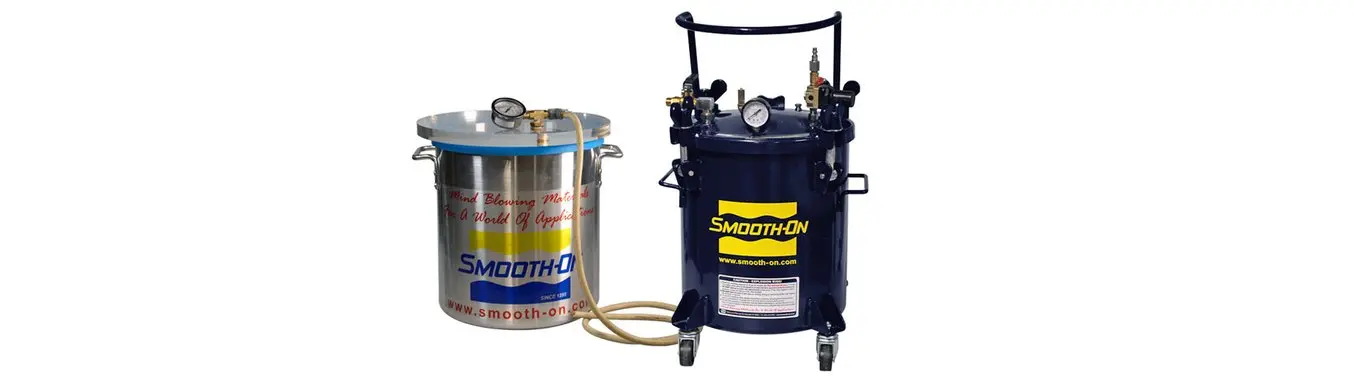
진공 챔버(좌측)와 가압기(우측).
진공 주조 소재
실리콘 몰드 소재
주조용 실리콘은 주석 경화 실리콘과 백금 경화 실리콘으로 나눌 수 있습니다. 주석 경화 실리콘, 즉 축합형 경화 실리콘은 1~4%의 수축을 보입니다. 모델 제조업체는 수축률을 보정하기 위해 최선을 다하지만, 공차가 큰 응용 분야에서는 품질이 우수한 백금 경화 실리콘 또는 고온 가황(HTV) 고무를 사용하는 것이 좋습니다.
쇼어 경도 A가 40~50이므로 내구성이 좋은 몰드를 제작하여 수십 번 재사용할 수 있으며 탈형이 쉽고 역류 문제로 인해 단단한 몰드로 둘러싸인 파트도 쉽게 탈형할 수 있습니다. 반투명 실리콘은 공기 트랩, 기포, 오염 물질과 금형 내부에서 일어나는 모든 일을 볼 수 있으므로 권장 소재입니다.
우수한 2액형 실리콘 브랜드로 SmoothOn, Elastosil, V-Sure, Silicones and More(S.A.M.)가 있습니다. 해외 화학 공장에서 직접 주문하면 특히 대량 주문의 경우 구매자의 사양에 정확하게 맞춘 전문가 수준의 제품을 낮은 가격에 수급할 수 있습니다.
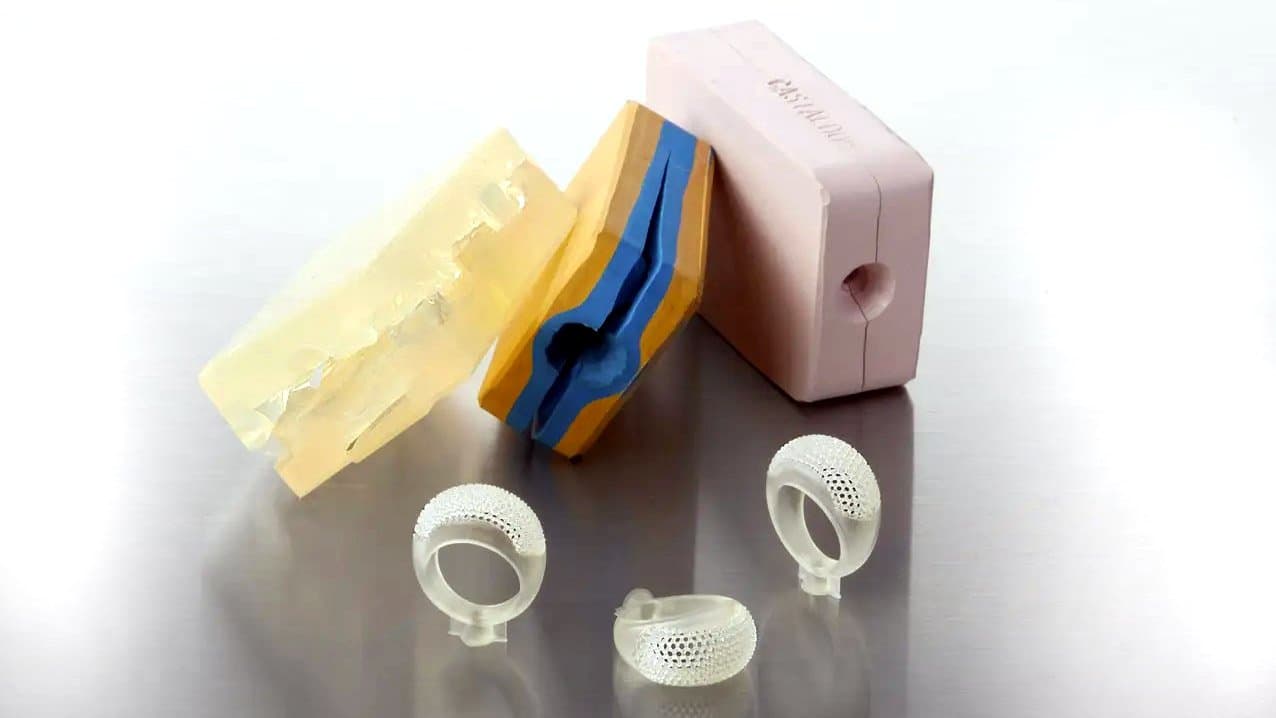
RTV 및 HTV 주얼리 몰드는 주얼리 업계에서 생산용으로 사용되며 복잡한 선조 세공의 디테일을 표현할 수 있습니다.
주조용 우레탄 레진
유연성, 탄성, 강성, 경도 측면에서 다양한 특성을 가진 진공 주조 재료가 다음과 같이 무수히 많습니다.
-
ABS 유사 범용 레진
-
탁월한 강성을 얻을 수 있는 유리 충전 나일론 유사 소재
-
웨어러블, 핸드 그립, 그립, 버튼, 개스킷, 씰 제작용 엘라스토머 TPE 유사 소재
-
PC 유사(폴리카보네이트)
-
반투명 또는 무색 투명 주조 우레탄(PMMA 유사)
-
POM 유사 또는 PU 유사 내열성 소재
스매시 유리, 왁스, 에폭시, 세라믹, 복합재뿐만 아니라 식품 등급, 전도성, 저밀도, 난연성 옵션과 같은 몇 가지 이색적인 우레탄 주조 재료도 있습니다. 잘 알려진 브랜드로는 FastCast 우레탄 주조 레진, Smooth-On, SRC 특수 레진 등이 있습니다.
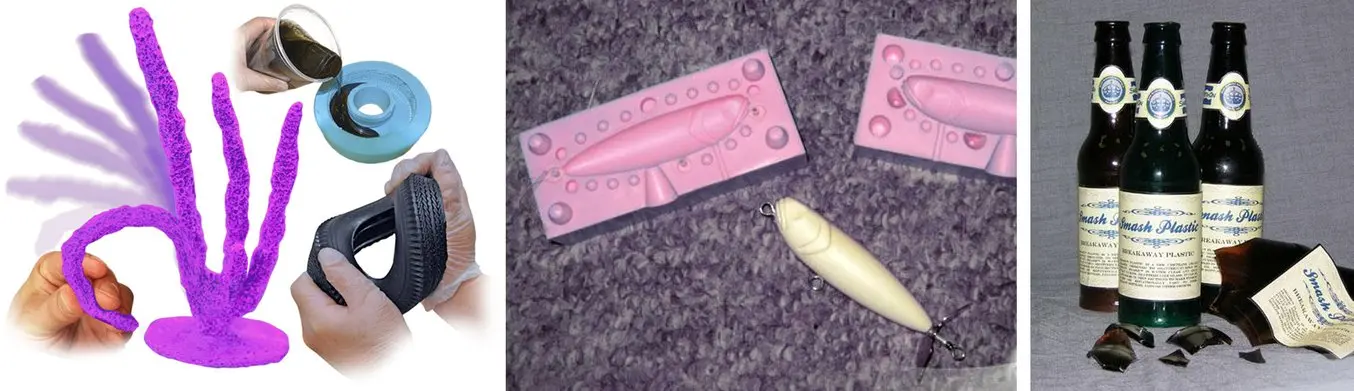
고무와 유사한 레진에서 물에 뜨는 레진, 유리와 유사한 레진까지 다양한 우레탄 레진.
사례 연구: 3D 프린팅 패턴을 이용한 우레탄 주조
칼리버 펜싱(Calibur Fencing)
진공 주조는 사출 성형용 공구 제작에 거액을 투자하기 전에 최종 제품을 테스트하고 조정하는 선행 생산 실행에 적합한 공정입니다.
성공적인 사례 중 하나로 펜싱에서 점수를 기록하는 무선 웨어러블 디바이스인 칼리버 펜싱(Calibur Fencing)이 있습니다.디자이너들이 간단한 프로토타입을 제작하여 디바이스의 기능을 테스트하는 데서 시작한 후, 적합한 폼 팩터를 찾기 위해 FDM 프린팅으로 대략적인 목업을 제작했습니다. 최종적으로는 Formlabs의 Form 3 SLA 프린터가 필수적인 장비임을 확인했는데 최종 제품과 흡사한 고품질 프로토타입을 제작할 수 있었기 때문입니다.
당시 팀은 SLA 3D 프린팅으로 제작된 파트를 패턴으로 사용하려고 진공 주조 외주 업체로 보내 고객용 장치를 제작 및 베타 테스트했습니다. 이후 최고의 품질은 그대로 유지하면서 최종 제품까지 빠르게 개발할 수 있었습니다.
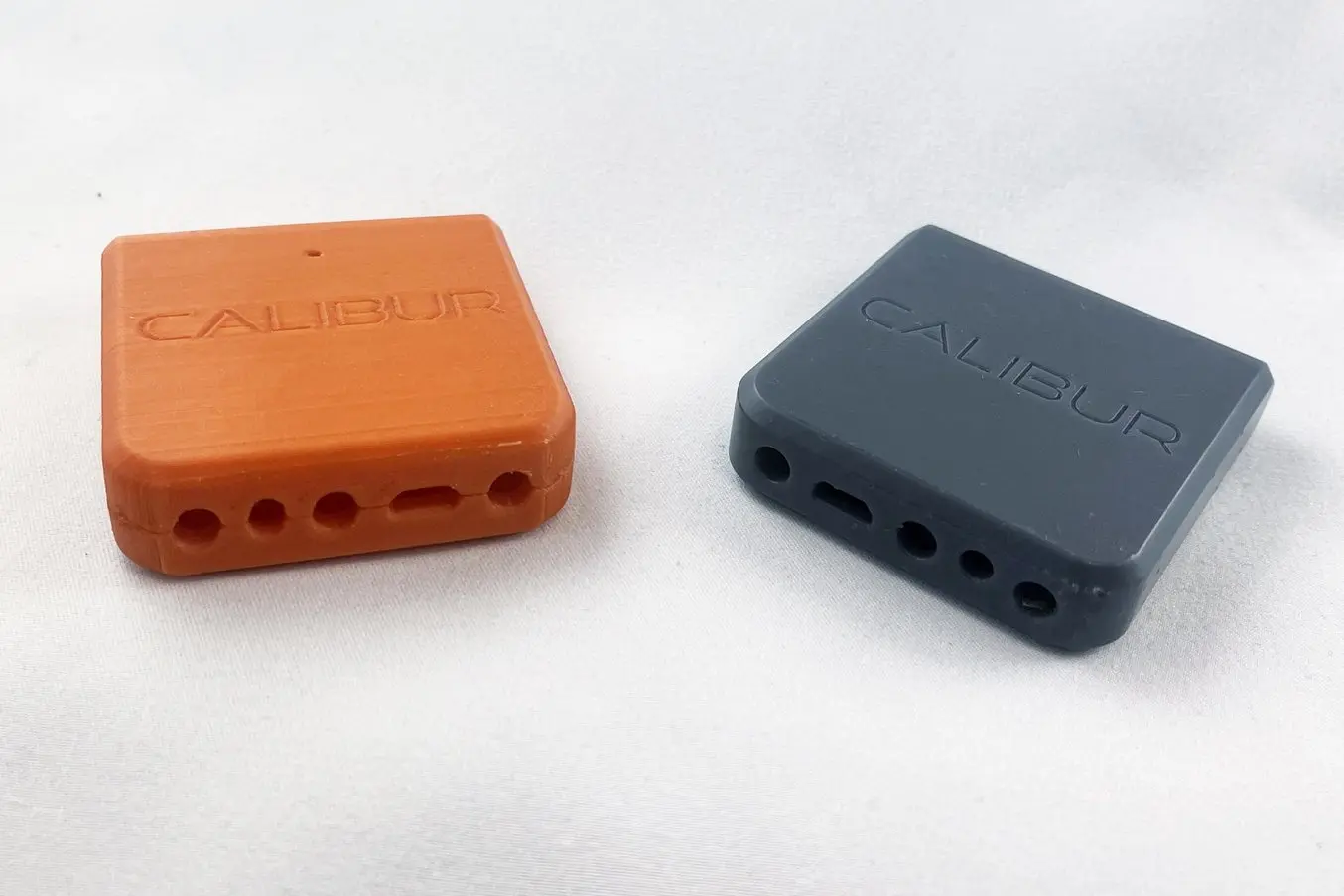
칼리버의 팀은 첫 번째 목업 제작에 FDM 3D 프린팅을 사용한 후 사실적이고 기능적인 프로토타입을 제작하기 위해 장비를 SLA 3D 프린터로 교체했습니다.
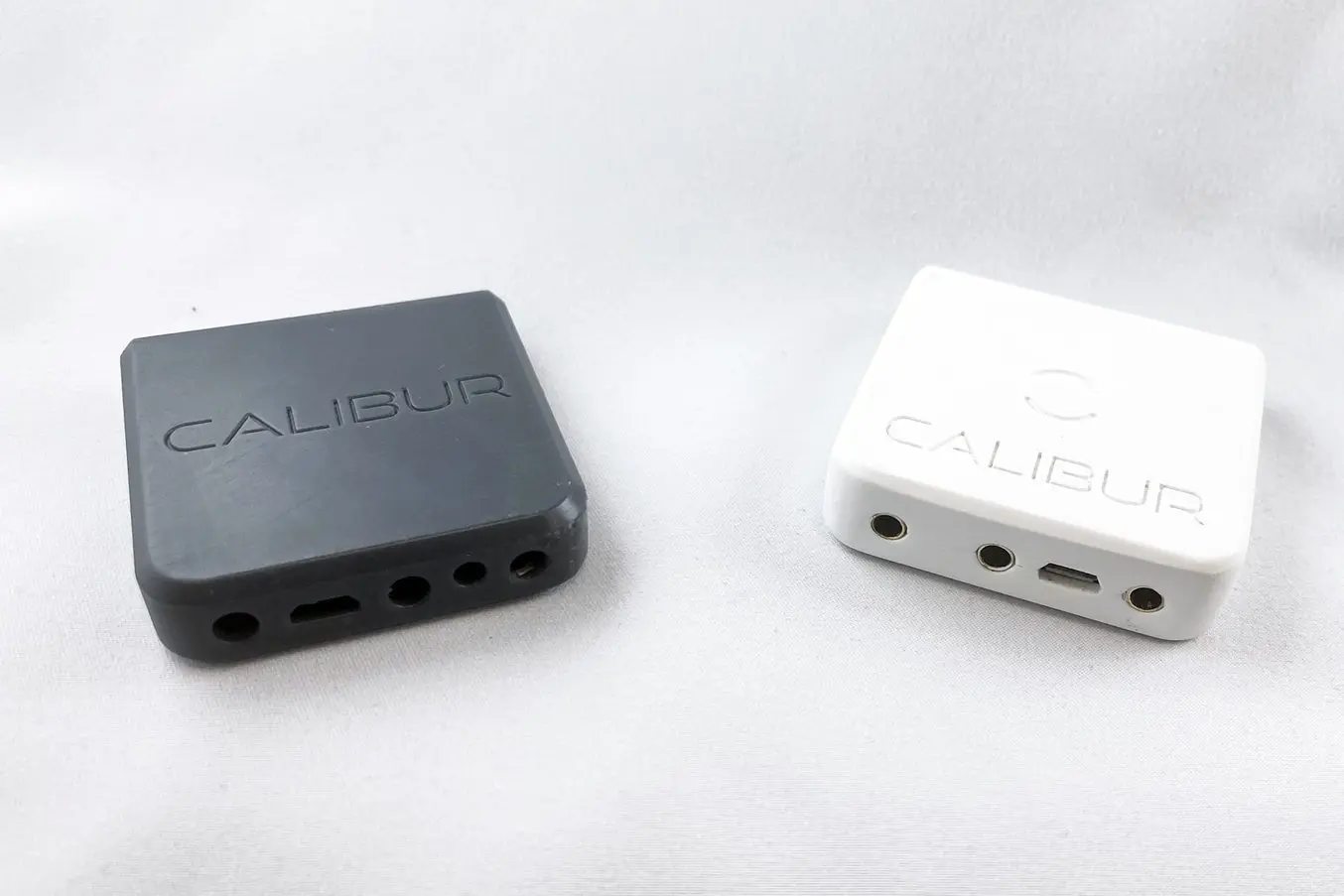
그런 다음 팀은 최종 사용 테스트 유닛 중 첫 번째 소량 시리즈용 진공 주조에서 SLA 3D 프린팅으로 제작된 파트를 패턴으로 사용했습니다.
루이빌 슬러거(Louisville Slugger)
루이빌 슬러거 이노베이션 센터의 팀은 작은 것이 큰 차이를 만들 수 있다는 사실을 깨달았습니다 1884년부터 야구 배트를 생산해 온 이들은 더욱 빠르고 강력한 스윙을 만들어내는 요소를 훤히 꿰뚫고 있습니다.
슬러거 혁신 센터의 직원들은 스포츠 디자인에 대한 분석적 접근 방식을 유지해 왔으며 Formlabs 3D 프린팅 솔루션의 도움을 받아 그립 애드온을 제작했습니다. 계단식 지오메트리는 타자가 가장 확실하게 타격할 수 있도록 완벽한 그립감을 느끼게 해 줍니다.
다른 사례와 마찬가지로 루이빌 슬러거의 디자인 팀도 3D 프린팅과 진공 주조 기능을 한 지붕 아래로 통합하면 디자인 반복 작업의 속도가 빨라지고 지식 창출이 빨라진다는 사실을 깨달았습니다. Form 3 SLA 프린터에서 50μm 레이어 높이로 프린팅한 세밀한 프로토타입 모델을 양각 몰드 제작에 사용했습니다. 우레탄 주조의 힘으로 실리콘 사출 성형 최종 제품의 품질에 가까운 내구성을 갖춰 테스트가 가능한 모델을 만들 수 있었습니다.
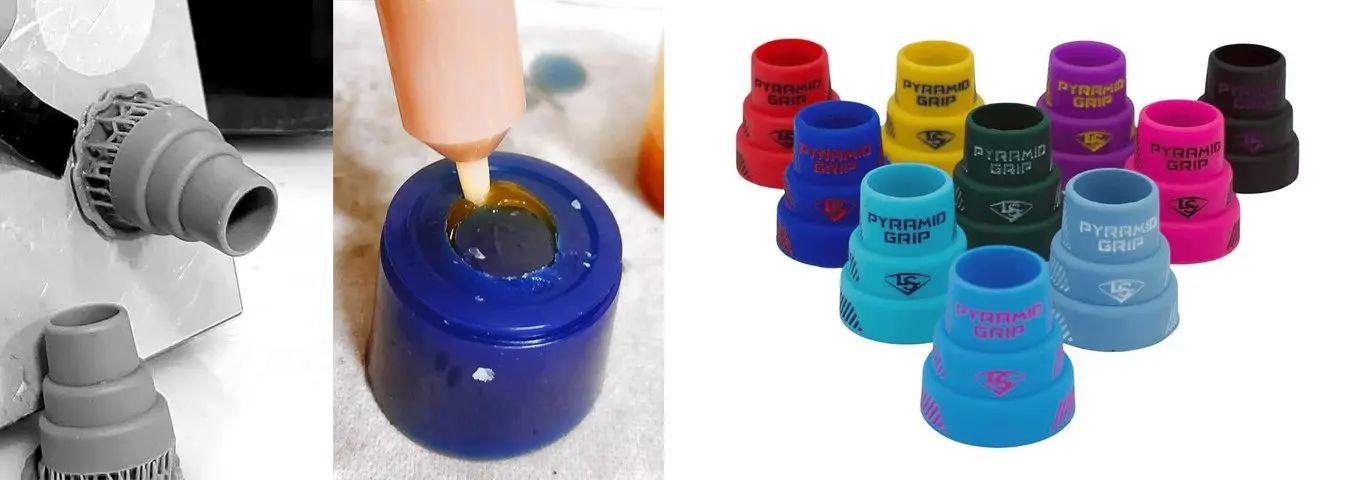
3D 프린팅 양각 모델에서 인하우스 주조까지, 그리고 최종 제품까지.
SiOCAST
SiOCAST는 3D 프린팅과 레진 주조의 통합에 관한 독특한 스토리를 보유하고 있습니다. MMORPG 온라인 게임과 RPG 보드 게임의 등장으로 맞춤형 미니어처 피규어에 대한 수요가 급증하고 있습니다. 비용이 많이 드는 원심 주조나 진공 주조 실리콘 몰드가 있어야 제작 가능한 제한된 시리즈 대신, 이 회사는 자체 개발 장비 및 HTV 고무 몰드와 함께 사용할 수 있는, 특허받은 레진 주입 시스템을 개발했습니다.
회사의 독점 소재인 SiOres는 최고 240˚C의 액화 열가소성 레진과 함께 사용할 수 있습니다. SiOCAST 장비는 기존 레진 주조 장비보다 최대 20배 빠르며 자동화 및 회전식 멀티 캐비티 몰드를 통해 시간당 1,000개의 부품을 생산할 수 있습니다.
마스터 패턴은 모두 Formlabs SLA 프린터로 3D 프린팅한 후 Formlabs의 자동 세척 및 경화 시스템인 Form Wash와 Form Cure에서 후처리합니다. SLS 3D 프린팅으로 재사용 가능한 러너를 제작하면 공정 속도가 더욱 빨라져 주조당 최대 64개의 미니어처를 제작할 수 있습니다.
사출 성형은 더 까다로운 조건과 점성이 있는 재료를 다루기 때문에 가끔 오류가 발생하는 반면, 진공 주조로 제작한 모델은 예외 없이 원본 조형물을 완벽하게 복제해 놓은 것으로 수많은 게이머의 디지털 영혼을 만족시키기에 충분합니다.
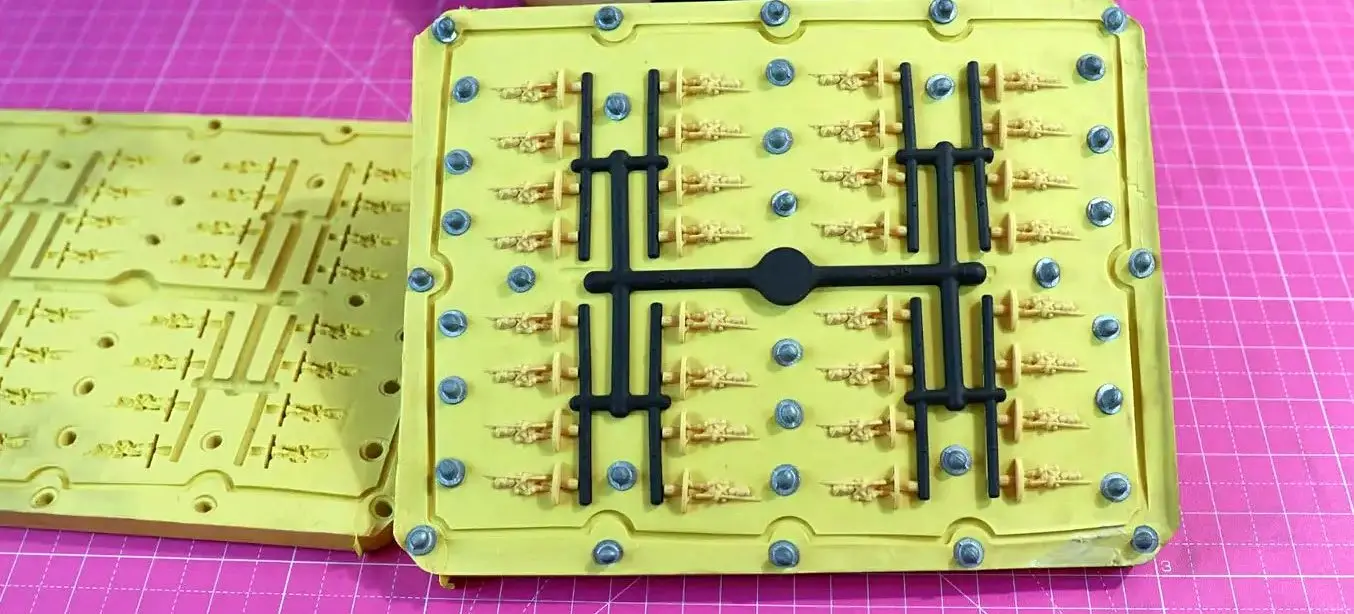
SiOCAST는 독점적인 HTV 실리콘, SLA 마스터 모델, 재사용 가능한 SLS 나일론 러너를 사용하여 미니어처를 최대 10,000개까지 연속으로 복제할 수 있습니다.
진공 주조와 3D 프린팅 시작하기
진공 주조는 산업 레벨 생산 방식에서 요구되는 대규모 초기 투자 없이 제품을 성형하기에 이상적인 공정으로, 프로토타입, 유사 모델, 사전 제작 시리즈는 물론 거의 모든 응용 분야의 최종 제품 제작에 사용할 수 있습니다. 주조로 제작한 모델은 제품의 기하학적 형상이 탈형 가능한 형상이고 진공 주조에 대한 특정 설계 지침을 준수하는 한 마스터 패턴을 정확하게 복제한 것입니다.
진공 주조는 또한 3D 프린팅의 새로운 발전으로 인해 매우 부드럽고 완벽한 마감으로 매우 상세한 마스터 모델을 만들 수 있어 진공 주조 공정과 완벽한 조화를 이룹니다.
그러나 3D 프린팅과 달리 DIY 진공 주조는 인하우스로 진행하기가 쉽지 않고 엄격한 절차를 따라야 합니다. 3D 프린팅은 높은 정밀도, 간단한 워크플로, 짧은 리드 타임으로 프로토타입 제작과 소량 생산에 있어 진공 주조를 대체할 수 있는 대안으로 떠오르고 있습니다.