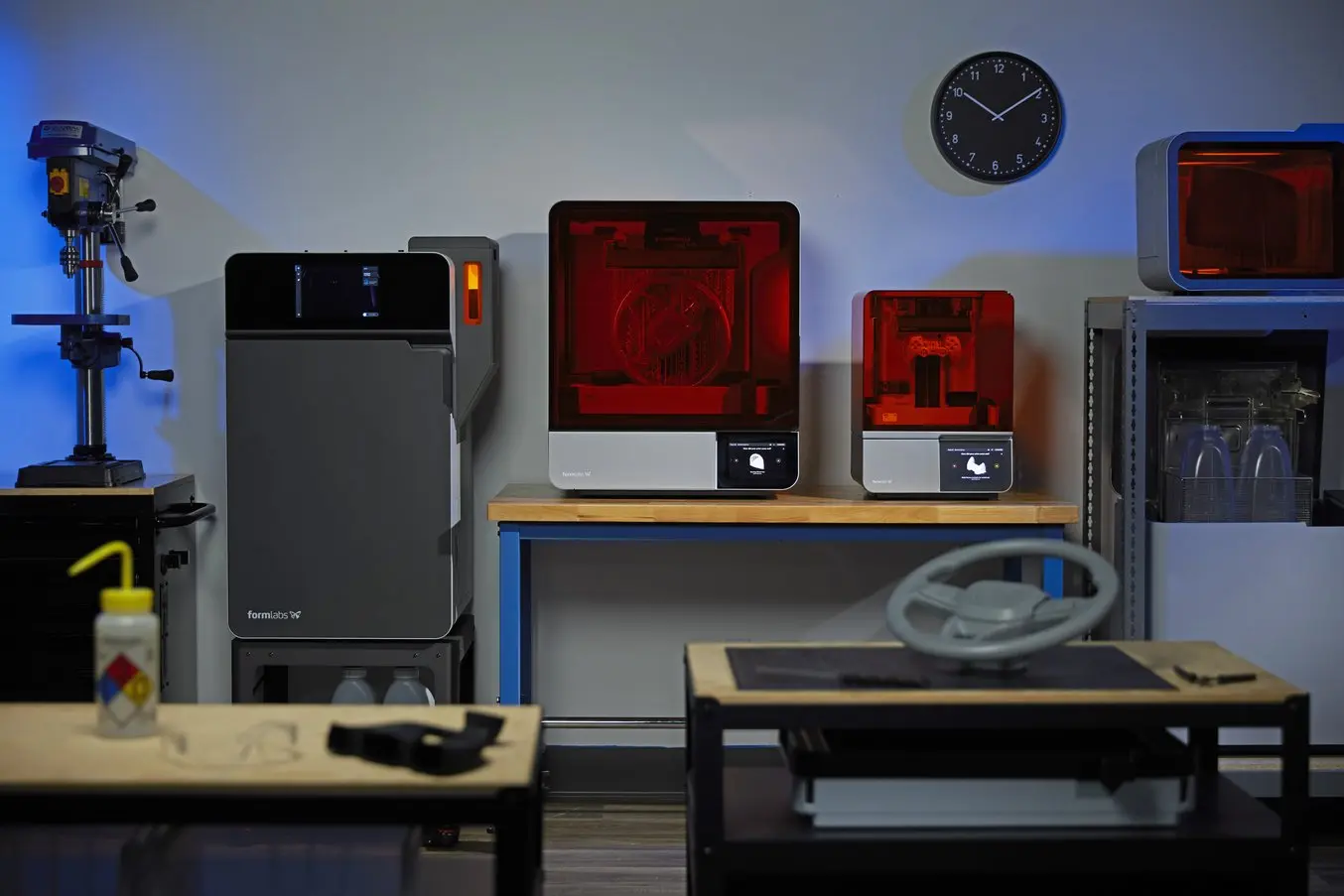
3D printing, or additive manufacturing, is revolutionizing industries, offering opportunities for improving sustainability. By rethinking traditional manufacturing processes, 3D printing enables resource efficiency, waste reduction, and localized production, contributing to a more environmentally responsible future.
Resource Efficiency and Waste Reduction
Traditional subtractive manufacturing often involves removing excess material, leading to significant waste. In the case of selective laser sintering (SLS), 3D printing uses only the necessary material, drastically reducing waste and minimizing the environmental impact of raw material extraction and processing. In SLS 3D printing, unused powder is cleaned from parts and reused in later printing batches.
Waste is further reduced through:
-
Material Optimization: Advanced designs, like lattice structures, optimize material use while maintaining strength, which is particularly valuable in industries like aerospace and automotive where weight reduction saves fuel (Hopkinson et al).
-
On-Demand Production: 3D printing enables on-demand manufacturing, reducing the need for large inventories and minimizing waste from obsolete or unsold products. This is ideal for spare parts and customized items (Khajavi et al). Producing goods closer to consumers also reduces transportation distances and the need for large warehouses, lowering carbon emissions and strengthening supply chain resilience (Berman et al).
“With powder and TPU there's very, very little waste and that's the way forward environmentally.”
Mark Joyce, General Manager, MAG Orthotics
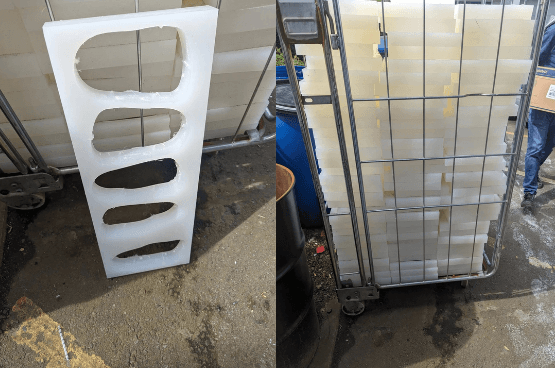
Reducing the accumulated waste of polypropylene from CNC manufacturing was a primary reason MAG Orthotics adopted 3D printing.
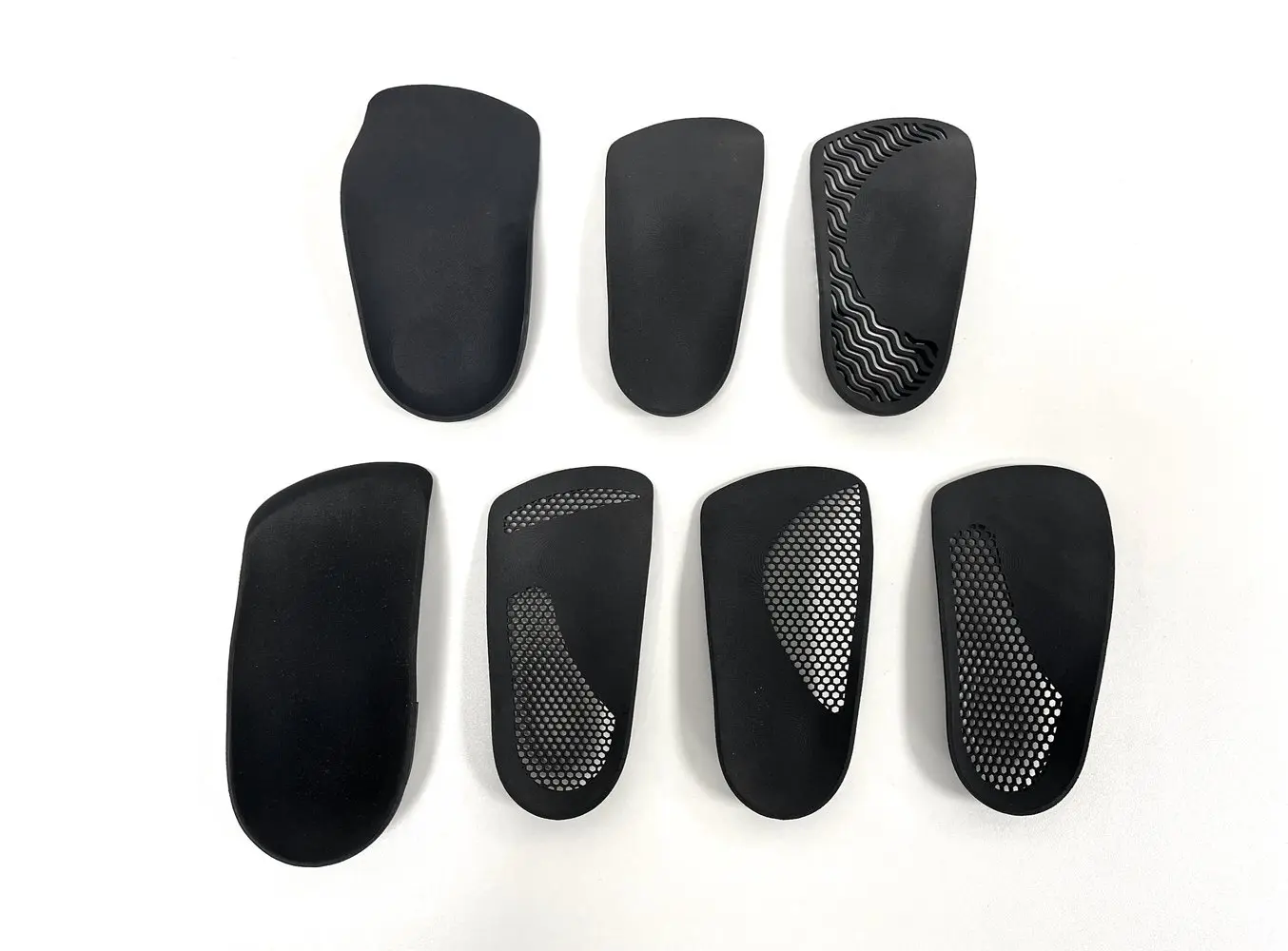
3D printing uses only the necessary material, drastically reducing waste.
Decreasing Waste With 3D Printed Prototypes & Production
Prototyping products with 3D printing versus traditional methods can save on transportation costs and excess material waste. However, there’s an even bigger potential reduction in waste: by prototyping products with 3D printing, manufacturers can reduce the possibility of product recalls or design changes at later stages of product development or production, both of which would result in waste.
"Printing parts in-house and with material we already have on site, rather than having different components delivered that may not work at all, can really make a difference in terms of sustainability.”
Samantha Melnyk, Sustainability & Communications Designer, KORG Berlin
Additionally, moving from a prototype to production with 3D printing makes it easy to continue optimizing a product — without having a stock of obsolete products. This enables refinement of a product without resulting waste from unsold products.
Localized Production and Reduced Transportation
3D printing can be deployed in localized production facilities, reducing the need for long-distance transportation of goods. Known as distributed manufacturing, this model involves the manufacture of products closer to the point of consumption for reduced transportation costs and emissions. Additionally, this reduces reliance on global supply chains, increasing supply chain resilience.
On-demand production reduces inventory, eliminating the need for large warehouses and the associated climate control, materials, and infrastructure required to support them. An added bonus is that more types of products or customized products can be produced than if warehousing were needed.
In producing desktop and benchtop 3D printers, Formlabs is making it easier for small businesses to produce goods locally, minimizing transportation and its associated environmental impact.
Sustainability Efforts at Formlabs
Formlabs is deeply committed to integrating sustainability into our core operations, focusing on three key areas: our products, our supply chain, and our sites.
"As Formlabs continues to transform the additive manufacturing industry, we must do so in an environmentally and socially responsible manner. We will continue to invest time, people, and money to support sustainability efforts and look to the global Formlabs team to engage and help drive positive changes in the impact we have on the environment. This will not be a task, but a continuous journey of improvement to lead the industries we serve in sustainability efforts."
Jason Fullmer, COO, Formlabs
Sustainable Products
The environmental impact of our products extends beyond the manufacturing process to development, with a focus on:
-
Material Innovation: Investing in research and development to create more sustainable resin formulations and reduce the amount of waste generated by the support structures required by resin printing.
-
Product Durability: Designing durable and long-lasting 3D printers and hardware accessories to extend product lifecycles and reduce the need for frequent replacements.
-
Responsible Resin Disposal: Providing clear guidelines and resources for customers on the safe and responsible disposal of resin waste, minimizing environmental contamination.
-
Packaging Optimization: Reducing packaging waste through efficient design and materials.
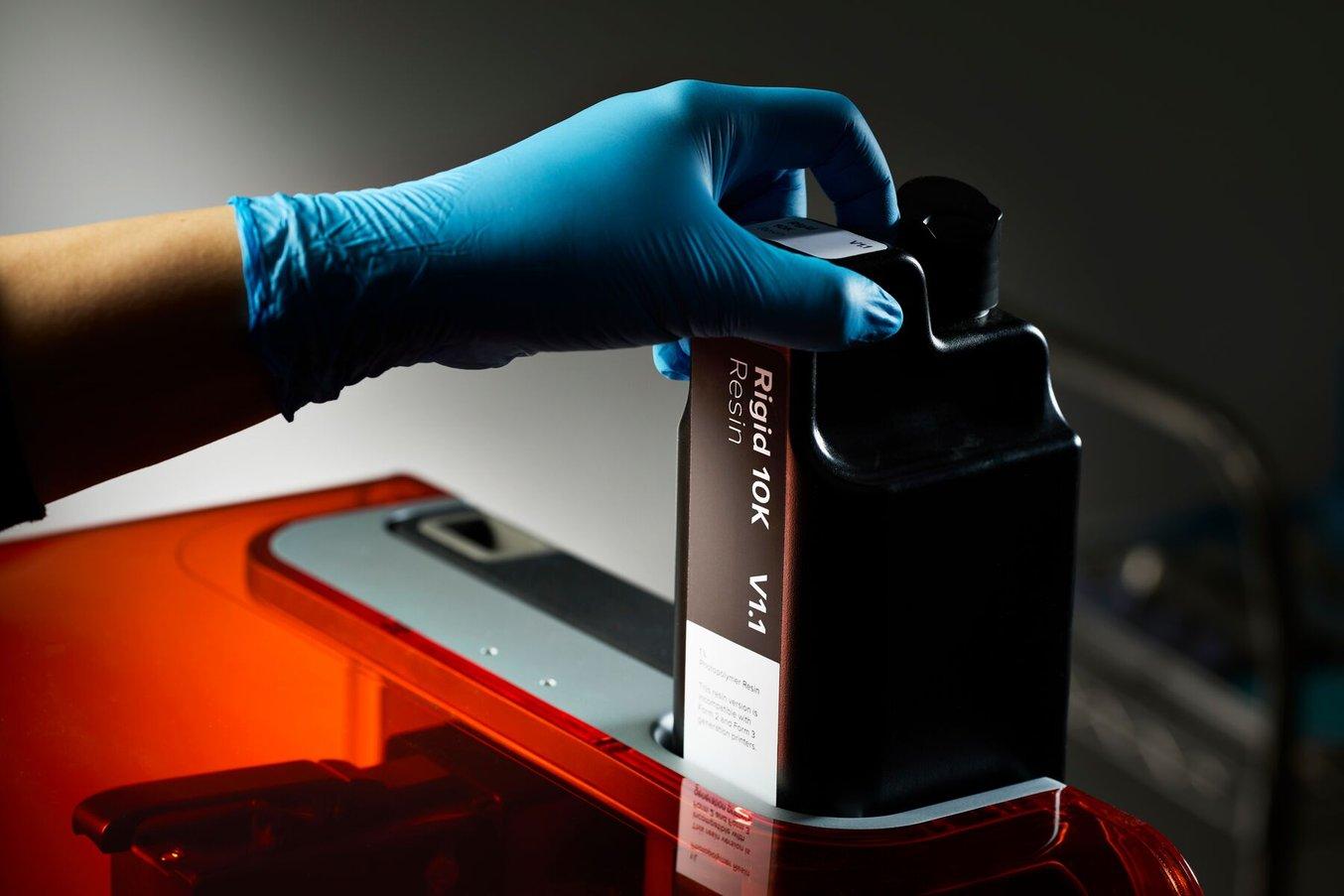
The next-generation resin cartridge for Form 4 Series 3D printers uses 66% less plastic than precious designs while still delivering one full liter of material.
Examples of innovations with an eye toward sustainability include:
-
Form 4 Series resin cartridge design reduces plastic use by 66% compared to previous designs
-
Reduced packaging waste on resin tanks and powders for selective laser sintering (SLS)
-
Lower refresh rates for Nylon 12 Tough Powder to increase material reuse
-
Improved resin tank lifetime for Form 4 Series 3D printers
Sustainable Supply Chain
Formlabs is building a sustainable supply chain by partnering with ethical suppliers and practicing responsible sourcing of raw materials. Additionally, logistics optimization and container shipment consolidation reduces the impact of transportation. By performing lifecycle assessments, we’re gaining visibility of each step in the creation of our products so we can continue to improve the sustainability of our supply chain.
Sustainable Sites
One focus is minimizing the environmental impact of our physical operations around the world. Formlabs implements energy-efficient technologies and practices within our facilities that reduce greenhouse gas emissions, including LED lighting and efficient HVAC systems. We also have comprehensive waste reduction and recycling programs to minimize landfill waste. When expanding or renovating facilities, we strive to incorporate sustainable building practices, such as the use of eco-friendly materials and designs that optimize natural light and ventilation. These efforts are further supported by the promotion and execution of eco-conscious behaviors by Formlabs employees.
Working Toward a Sustainable Future
3D printing offers a powerful tool for advancing sustainability by minimizing waste, optimizing resource utilization, and enabling localized production. As 3D printing technology continues to evolve, its potential to address environmental challenges will only grow.
From building durable products with replaceable parts to developing a sustainable supply chain, companies like Formlabs are playing a crucial role in driving this transformation. Through continued innovation and collaboration, 3D printing will continue to become more sustainable while powering more environmentally conscious production.
To learn more, explore Formlabs 3D printers or contact sales.
Works Cited:
Hopkinson, N., Hague, R. J. M., & Dickens, P. M. (2006). Rapid manufacturing: an industrial revolution for the digital age. John Wiley & Sons.
Khajavi, S. H., Partanen, J., Holmström, J., & Tuomi, T. (2014). Additive manufacturing in the spare parts supply chain. Computers in Industry, 65(1), 96-107.
Ligon, S. C., Liska, R., Stampfl, J., Gurr, M., & Mülhaupt, R. (2017). Polymers for 3D printing and customized additive manufacturing. Chemical Reviews, 117(15), 10212-10290.
Berman, B. (2012). 3-D printing: The new revolution. Business Horizons, 55(2), 155-162.