How to 3D Print Soft Anatomical Models Using BioMed Flex 80A Resin and BioMed Elastic 50A Resin
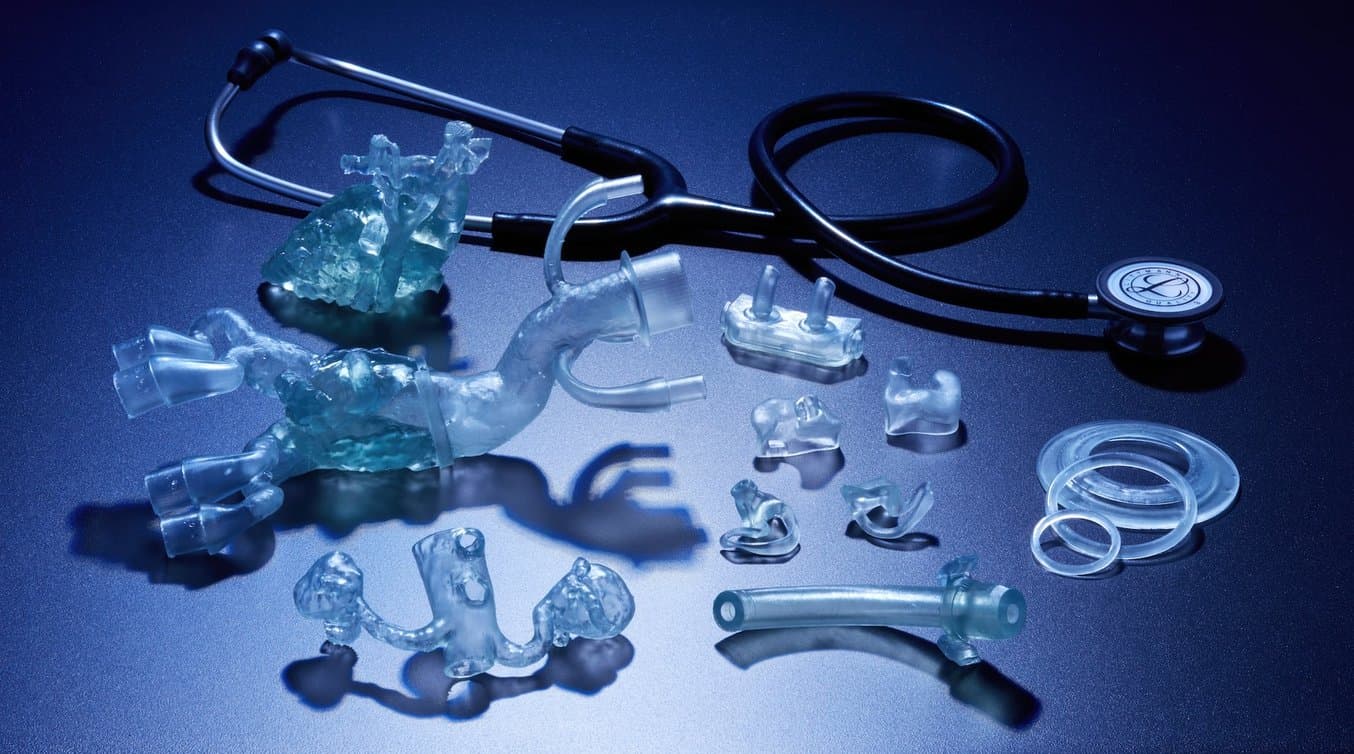
Formlabs is excited to introduce two novel materials designed for the direct 3D printing of elastomeric, biocompatible medical devices and models: BioMed Flex 80A Resin and BioMed Elastic 50A Resin. These new materials represent a significant expansion in medical application areas, particularly in the realm of anatomical modeling.
Traditionally, professionals looking to create soft anatomical models have grappled with the challenges of multi-step silicone molding processes, labor-intensive procedures resulting in limited geometries, messy outcomes, and excessive time and money spent. Alternatively, they have settled for costly contract manufacturing or rigid models.
Enter BioMed Flex 80A Resin and BioMed Elastic 50A Resin, which offer healthcare professionals the unprecedented ability to merge the advantages of traditional elastomeric and biocompatible materials with the user-friendly experience and streamlined workflows inherent to Formlabs resin 3D printers.
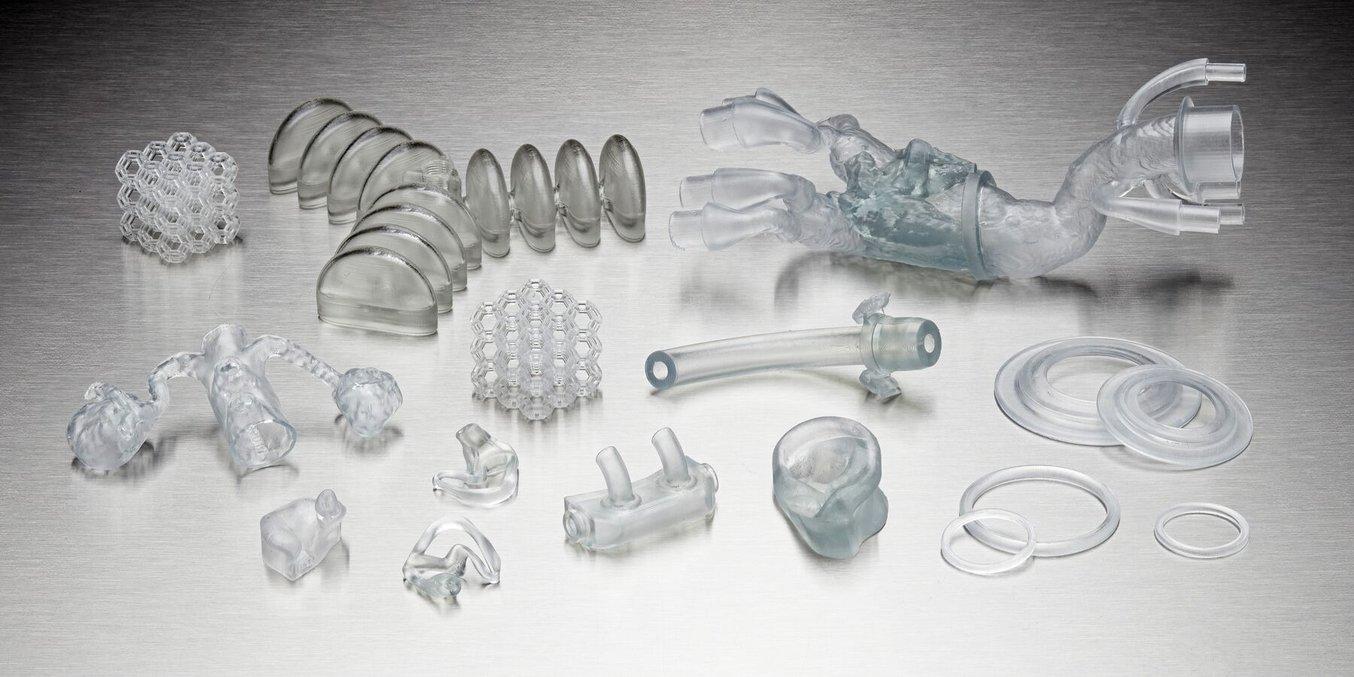
Printing Soft Anatomical Models Using BioMed Flex 80A Resin and BioMed Elastic 50A Resin
This comprehensive application guide walks through elastomeric material options for stereolithography (SLA) 3D printing and the entire in-house manufacturing process for soft anatomical models.
Why Use Soft Anatomical Models?
Soft anatomical models offer a great value to healthcare providers and patients alike. As cases become more complex, and interventions more unique, anatomical models can be used by healthcare providers to map pathology, plan interventions, gain a three-dimensional understanding of anatomical spatial relationships, pre-fit medical equipment, and practice approaches, all before the patient enters the operating room (OR).
Soft models in particular pose a great advantage to surgical training by providing medical residents, fellows, and students with the ability to cut directly into tissue-simulating material. Because BioMed Flex 80A Resin and BioMed Elastic 50A Resin are biocompatible and sterilizable, models can also be taken directly into the OR while surgery is underway to be used as an anatomical reference or sizing tool.
Anatomical model of a heart printed in BioMed Elastic 50A Resin.
The use of soft anatomical models offers advantages to patients as well. Not only are patient outcomes better when the physician has the opportunity to plan using a patient-specific model, but patient consent is enhanced when an anatomical model is used to inform them about the solution being offered. With an anatomical model, patients gain insights into the scale and scope of the issue as well as gain a more comprehensive understanding of what proposed treatments entail.
Read on to walk through the elastomeric material options for directly printing soft anatomical models using SLA printing, as well as the steps associated for printing them in-house.
BioMed Flex 80A Resin vs. BioMed Elastic 50A Resin
BioMed Flex 80A Resin and BioMed Elastic 50A Resin are similar in that they are both clear, biocompatible elastomers. However, differences in mechanical properties result in one often being preferred over the other for certain applications. When it comes to anatomical modeling, both materials are suitable and the optimal material depends on the mechanical properties of the anatomy that you’re aiming to simulate, and the forces that the model needs to withstand.
BioMed Flex 80A Resin | BioMed Elastic 50A Resin | |
---|---|---|
Color | Clear with a blue tint | Clear with a yellow tint |
Hardness Shore A | 80A | 50A |
Ultimate Tensile Strength | 7.2 MPa | 2.3 MPa |
Stress at 50% Elongation | 2.6 MPa | 1 MPa |
Stress at 100% Elongation | 4.5 MPa | 1.3 MPa |
Elongation | 135% | 150% |
Tear Strength | 22 kN/m | 11 kN/m |
BioMed Elastic 50A Resin is softer, similar to a pencil eraser or rubber stamp, whereas BioMed Flex 80A Resin is stiffer, similar to a leather belt or shoe heel. When using these materials for anatomical modeling, the effective resistance provided by the material can be varied by modifying the dimensions of the model (i.e. a part can be made easier to cut through by making the walls of that part thinner, even if the durometer is fixed).
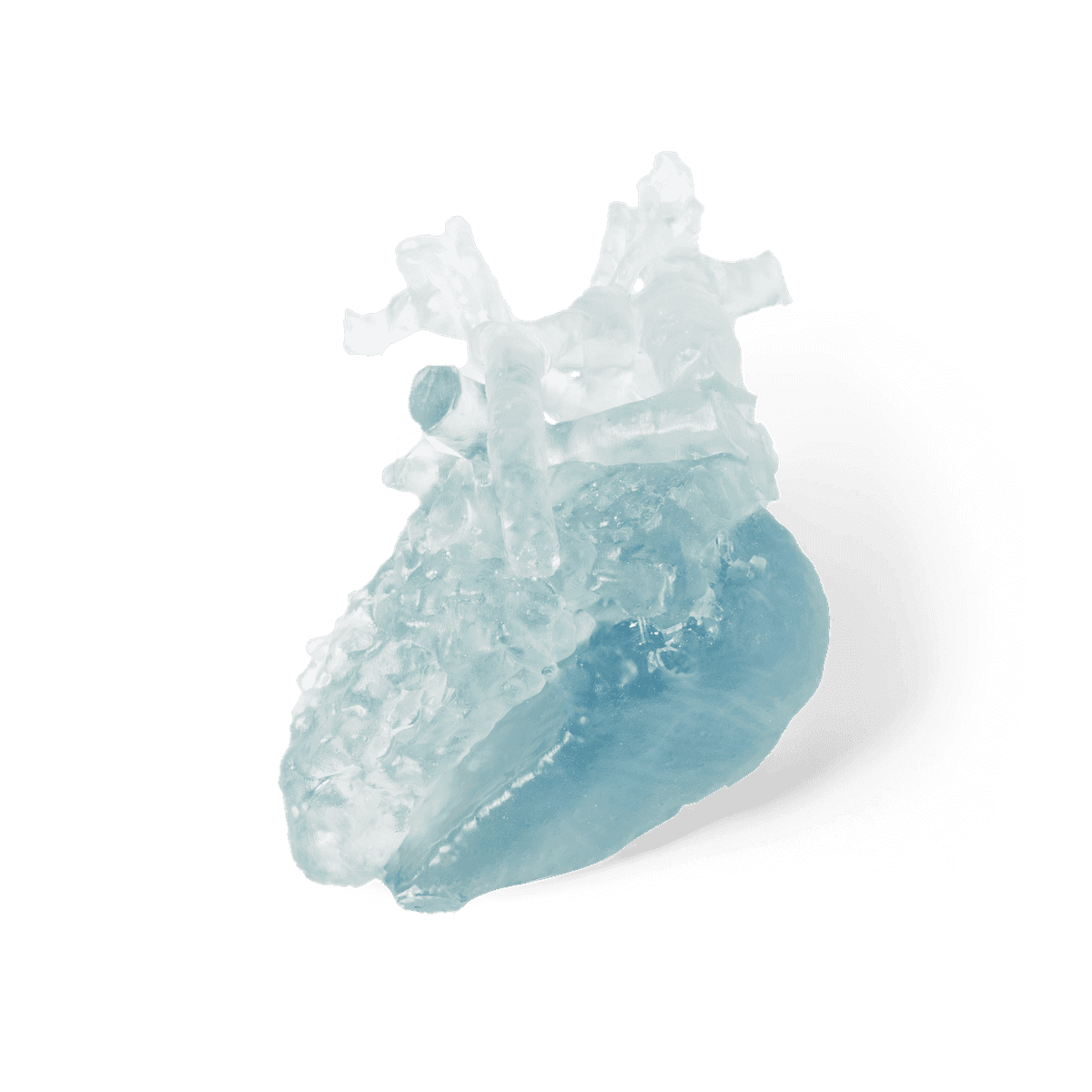
Anatomical model of a heart printed in BioMed Flex 80A Resin.
BioMed Flex 80A Resin is more rugged and is preferable for anatomical models with delicate geometries, or that are expected to resist larger amounts of force. BioMed Elastic 50A Resin, on the other hand, is less rugged but can experience more stretch before breaking.
Biocompatibility
Traditionally, professionals in medical device and medical component manufacturing, as well as at the point of care in hospitals and in medical service bureaus, have had to rely on multi-step silicone molding processes, which are often labor-intensive and messy or which must be outsourced to expensive contract manufacturers.
With BioMed Flex 80A Resin and BioMed Elastic 50A Resin, professionals can combine the benefits of traditional elastomeric and biocompatible materials with the ease of use and streamlined workflow of Formlabs resin printers.
Both BioMed Flex 80A Resin and BioMed Elastic 50A Resin are ISO 10993 and USP Class VI certified materials. They are made in an FDA-registered, ISO 13485 facility and can be used in applications for long-term skin contact (>30 days), and short-term mucosal membrane contact (≤24 hours).
"The BioMed Flex 80A Resin is a great tool to have in that it is flexible and has all the ingredients to be biocompatible for different clinical indications, and it really gives us more options in our arsenal to help surgeons out in the field.”
Dr. Prashanth Ravi, an Assistant Professor in the Department of Radiology at the University of Cincinnati
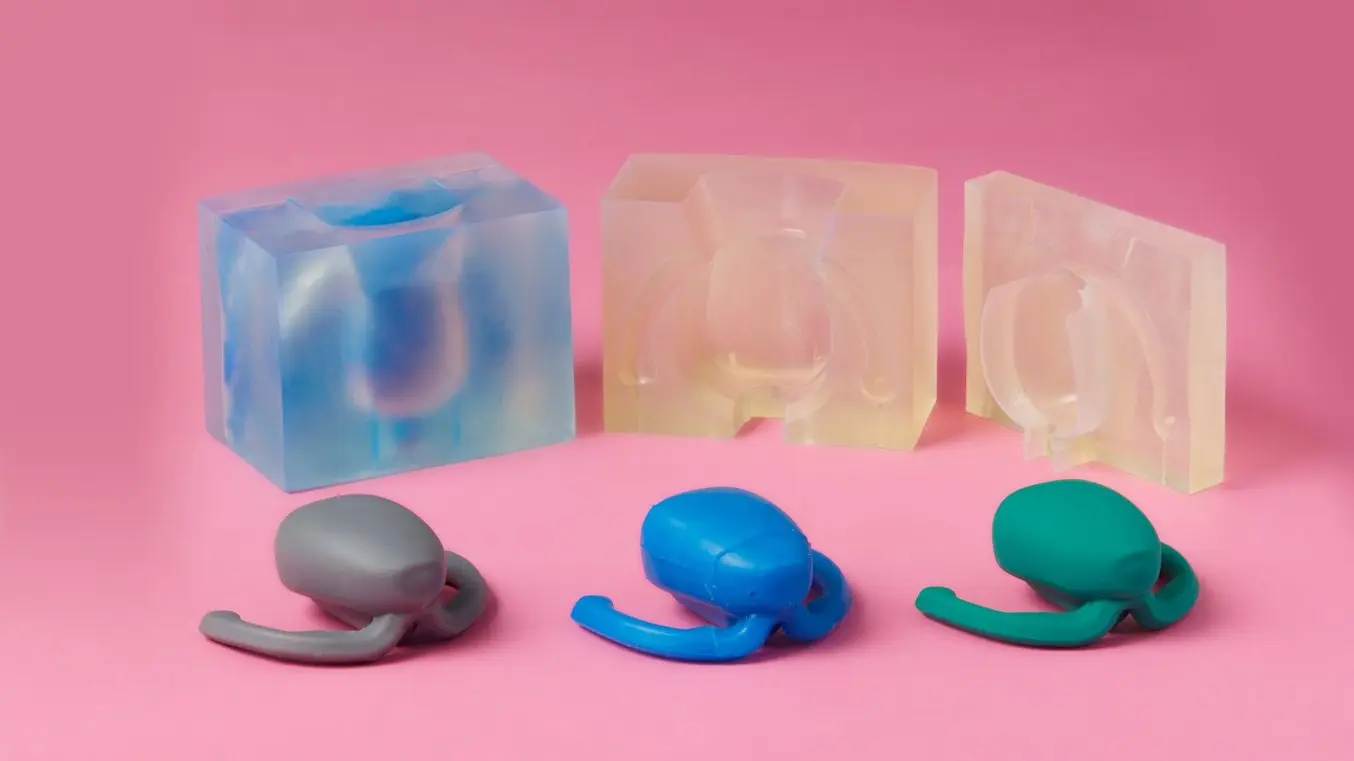
Creating Silicone Medical Devices
This guide aims to help the user decide on the best method of silicone part production for their intended use, and provides step-by-step instructions for both printing with Silicone 40A, and molding silicone using SLA 3D printed tooling (including two-part injection molds, overmolds, and compression molds).
Feedback From Medical Professionals
BioMed Flex 80A Resin and BioMed Elastic 50A Resin have been used by healthcare providers and clinical researchers, who share their feedback on both material and applications.
Dr. Prashanth Ravi, an Assistant Professor in the Department of Radiology at the University of Cincinnati, has utilized Formlabs' array of biocompatible resins extensively over the years. He identified the perfect application for the new material: an anatomical model used for device sizing, right in the OR.
He states, “one clear application is in device sizing for left atrial appendage closure planning to treat atrial fibrillation. If the cardiologist wants to take the sterilized 3D printed anatomic model into the operating room to actually size the device and communicate with the surgical team prior to the intervention, the BioMed Elastic 50A Resin is the material we would be using.”
Additional information on using 3D printed anatomical models for cardiological applications is available in this Medical 3D Printing Literature Roundup: Cardiology.
At Northwell Health, a leading provider of cutting-edge medical services, 3D printing has become a standard part of their workflow. Before the release of these two new materials, Allison Neuwirth, a project manager at Northwell Health, had to undergo a labor-intensive, multi-step silicone molding process to create biocompatible, personalized medical devices. She states, “in our hospital serving environment, this material excels in producing custom malleable parts which interface with the body. It also eliminates the need for prototyping via silicone molding which is labor-intensive and wasteful.”
Neurovasculature printed with BioMed Elastic 50A.
At Baystate Health, Greg Gagnon is a specialist in 3D printing and is responsible for preparing 3D printed bolus devices and other medical tools for physicians. It wasn't until the launch of BioMed Elastic 50A Resin that he was able to utilize direct 3D printing of elastomeric material in his workflow. He says that he “really enjoyed the material. Relative electron density was almost identical to water which is 1.0 g/cm3 and is great for 3D printing patient boluses. [We] already have some designs completed to start testing and expand our use cases into our surgical field."
“Formlabs BioMed Flex 80A Resin is a robust, durable addition to the company’s suite of material offerings. It offers high precision accuracy, and small-feature generation capability, in conjunction with a high durometer while being Biocompatible.”
Brian Powell, Medical Device Consultant
The Pennsylvania-based medical consultant Brian Powell notes that, “even in view of the additional water immersion UV cure step, I found this material to be compliant with my needs for high-resolution net shape generation and general ease of post-processing. I view this offering as a welcome addition to Formlabs BioMed material line-up which opens up an array of options resultant of flexible biocompatible component generation. Its introduction along with BioMed Elastic 50A Resin is definitely worth the wait.”
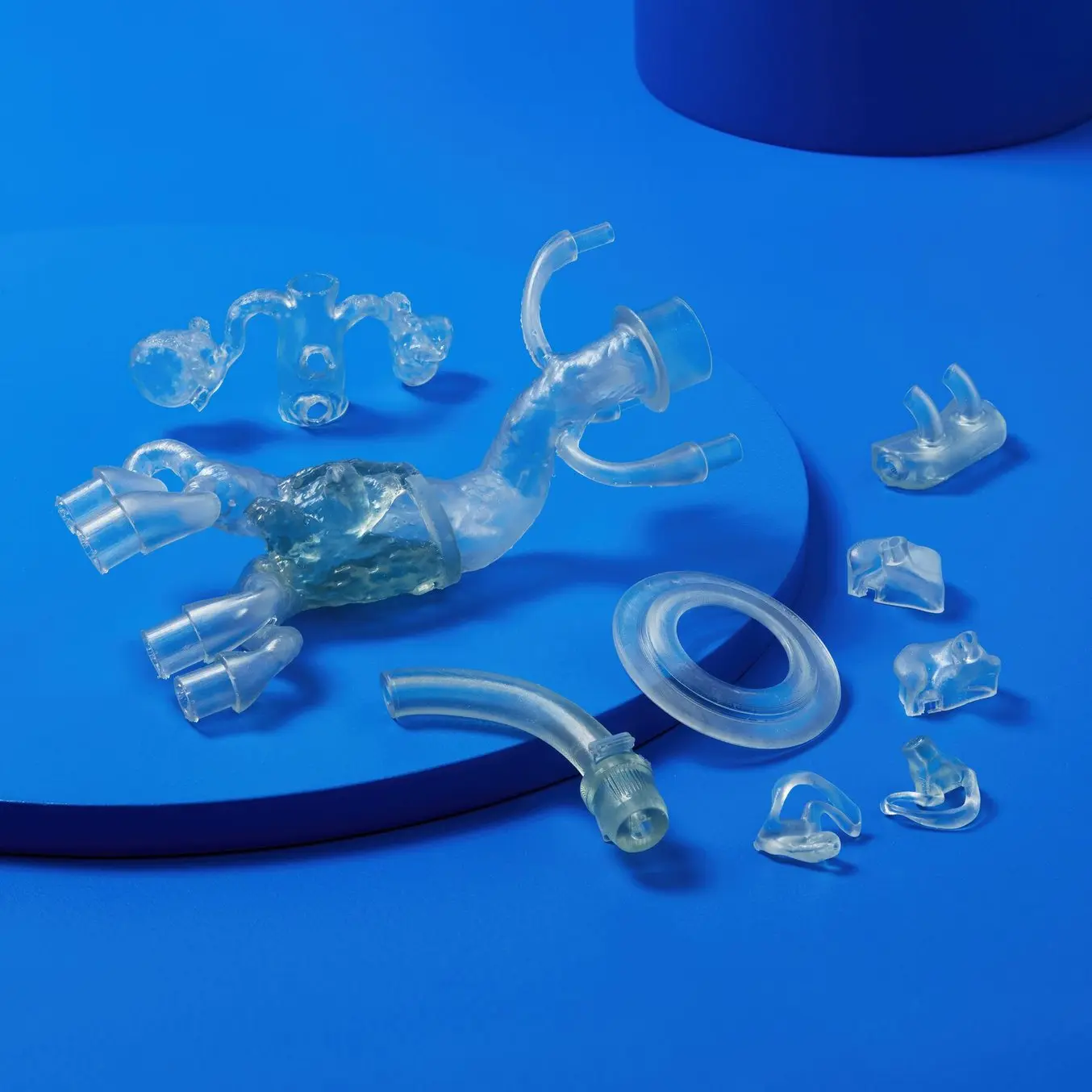
Leveraging Formlabs’ Biocomp Elastomers for Vascular Anatomical Models
Learn how medical professionals can incorporate elastomeric and biocompatible materials into innovative 3D printing workflows using Formlabs’ newest BioMed Flex 80A and BioMed Elastic 50A Resins.
Steps for Printing With Elastomers
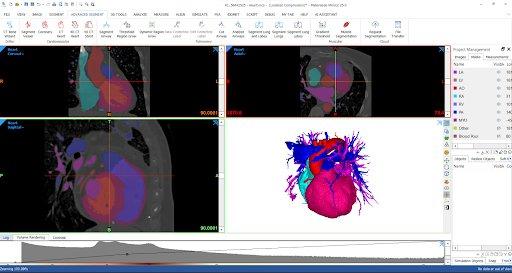
1. Scanning
To begin, start with a CT, MRI, 3D Ultrasound, or surface scanner image of the anatomy of interest. The quality of this image is key as higher quality imaging will result in better resolution of the printed part.
Some specific considerations need to be taken into account when choosing a surface scanner for healthcare applications. This article may be helpful when determining the best surface scanner for your general application, and this article may be helpful when determining the best scanner for podiatry applications.
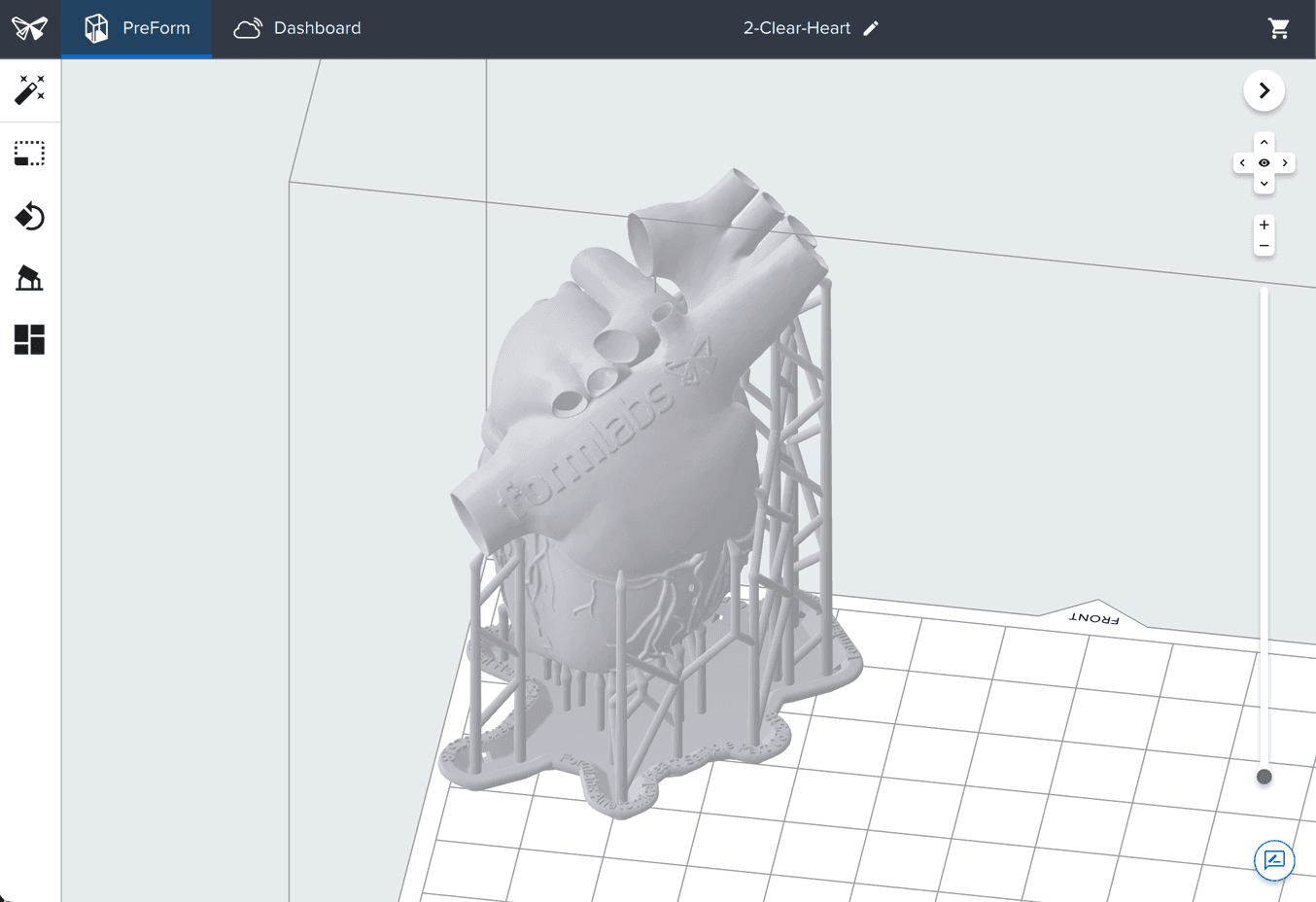
2. Designing
Some anatomical models may require modifications in order to print successfully. Make sure that the finished model adheres to Formlabs’ design guidelines. Edits to your scanned model should be made either in your segmentation software, or your CAD software of choice.
In point-of-care settings, a virtual surgical planning (VSP) session may be advisable at this stage. This is a meeting where the physician and segmentation team analyze the model and make necessary adjustments.
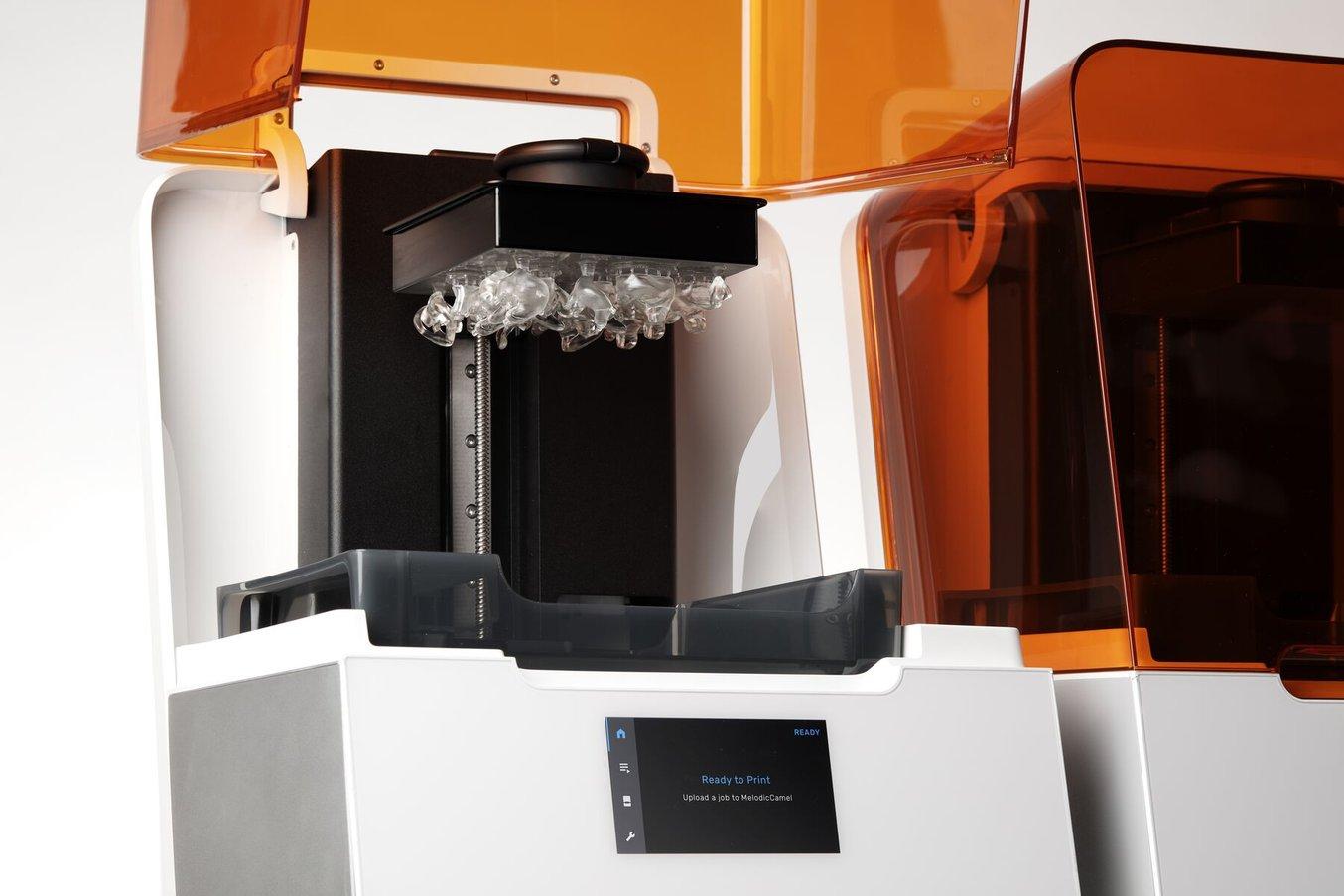
3. 3D Printing
Once the model is complete and saved, it’s time to move to printing. For full compliance and biocompatibility, BioMed Flex 80A Resin and BioMed Elastic 50A Resin require dedicated resin tanks and build platforms and must be printed on a dedicated biocompatible printer, either the Form 3B+ or Form 3BL.
Formlabs printers utilize PreForm software for printing. Before printing, check that your version is up to date and open your part file. Select BioMed Flex 80A Resin or BioMed Elastic 50A Resin as your print material and orient your part. PreForm can auto-orient based on Formlabs best practices or you can manually orient.
At this point, you may need to add supports. Elastomeric parts should be printed without supports whenever possible but you may auto-generate supports based on material properties in PreForm. Lastly, orient your part on the build platform and send your job to the printer.
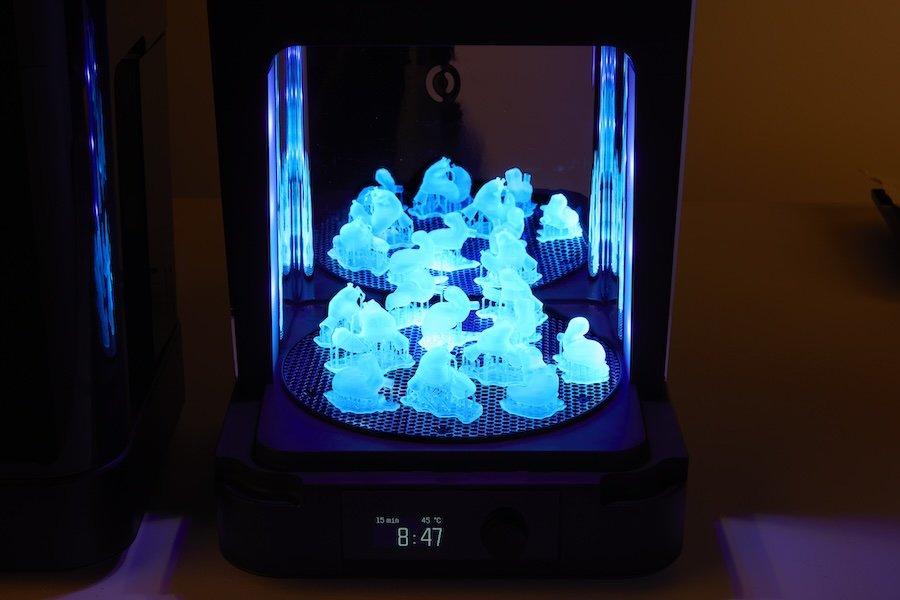
4. Post-Processing
Once printing is complete, the anatomical model must undergo proper post-processing procedures. First, remove the part from the build platform, leaving supports on the print for now. Then place the part in the Form Wash and wash using the recommended settings for BioMed Flex 80A Resin and BioMed Elastic 50A Resin found here.
Once the part has been washed, fully submerge it in a beaker (or other UV-transparent container) of water, and place the beaker of water containing the part into the Form Cure. Cure the parts according to the time and temperature settings found here. Leave the parts in the water until the water reaches room temperature. Once the water is room temperature, remove the parts and let them dry.
For a materials list and detailed workflow, download the white paper.
Formlabs Biocompatible Resins for Soft Anatomical Models
Formlabs' complete, easy-to-use ecosystem makes it simple to create soft anatomical models by directly 3D printing with BioMed Flex 80A Resin and BioMed Elastic 50A Resin. In-house manufacturing of soft anatomical models has proven invaluable for aiding surgical planning, bolstering medical training, and enhancing patient consent. With Formlabs BioMed Flex 80A Resin and BioMed Elastic 50A Resin, you can take a patient scan to a realistic, 3D printed model for use in or out of the operating room.
Do you have questions about using SLA printing for soft anatomical models, or finding the right 3D printing solution for your business? Set up a meeting with a Formlabs expert who can answer your questions.