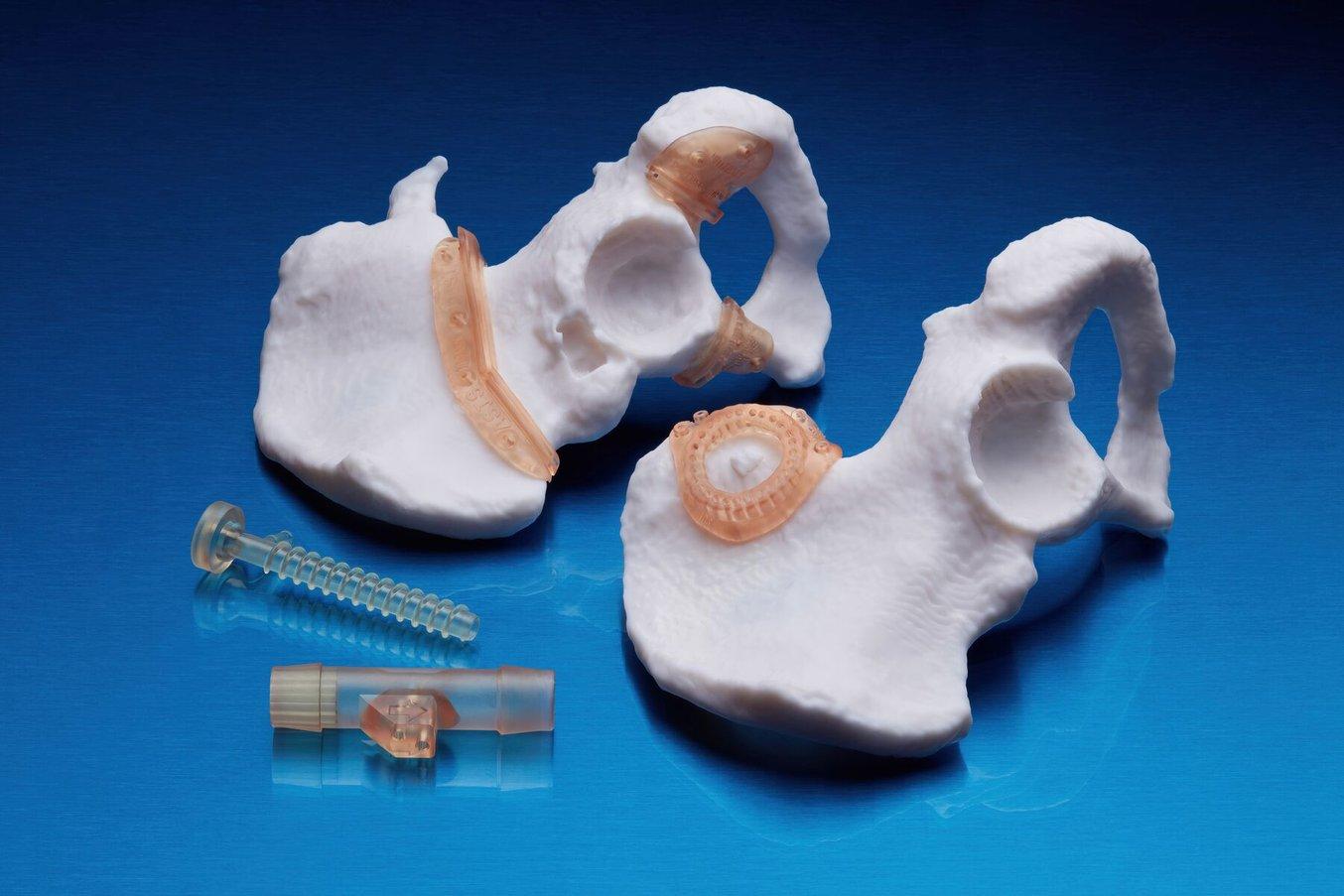
There is mounting evidence that in-house 3D printing labs at the point of care are scalable, affordable, and improve patient outcomes. From anatomical models for patient education, to patient-specific cutting guides, to biocompatible parts and components for equipment, 3D printing in-house makes a positive difference in patient care as well as the hospital’s bottom line. However, despite the clear benefits, many hospitals run into obstacles gaining the necessary support and funding to build an in-house medical 3D printing lab.
For that reason, Formlabs Medical hosted a roundtable with three leaders who have been through the process of building and running hospital-based 3D print labs to share their experience on what it takes to be successful. The roundtable includes:
-
Brian Albers: 3D Printing Engineer, St. Louis Children’s Hospital
-
Amy Alexander: Unit Head, Biomechanical Development and Applied Computational Engineering, Mayo Clinic
-
Dr. Summer Decker: Director of 3D Clinical Applications, USF Health/Tampa General Hospital
In this post, we recap some of the main insights from the webinar. To gain access to all of the learnings, watch the roundtable for free at the link below.
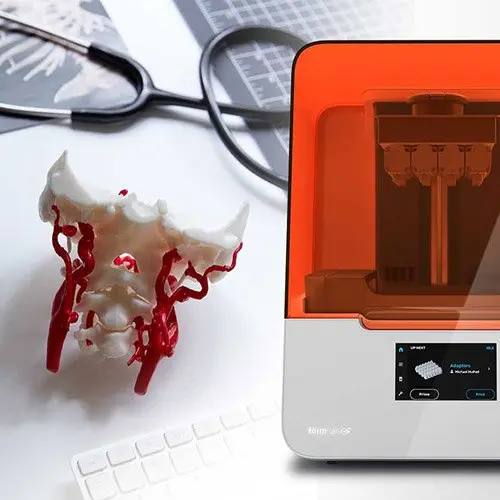
Planning & Considerations for Building a Medical 3D Printing Lab
Learn how medical professionals from USF Health, Saint Louis Children’s Hospital, and Mayo Clinic successfully built their medical 3D printing labs.
Purpose and Resources of a Hospital 3D Print Lab
Brian Albers, the 3D printing engineer at St. Louis Children’s Hospital, has developed quality-managed 3D printing protocols for multiple children’s hospitals. As an expert in 3D printing in a point-of-care deployment, his experience is invaluable to the thousands of hospitals and practitioners looking to harness the benefits of 3D printing in their own facilities.
Albers started the roundtable off by digging into key considerations that must be addressed when building hospital-based 3D printing labs from scratch. He pointed out that oftentimes, just a few physicians will be highly interested in using 3D printing. They will effectively become power users, working closely with 3D printing engineers on most, if not all, of their surgeries and seeking ways to improve operational workflows and patient outcomes. Albers feels this is the perfect place to start when scaling a lab, telling us that, “the first step is finding and targeting specific specialties and their physicians, and finding the physicians to actually champion these [3D printing] projects. The ones that come and say, ‘can I 3D print’, every time they interact with the patien, every time they're trying to come up with a plan for treatment.”
He continued, saying, “These are the people putting this on the front burner and it’s important to keep that in mind and keep the patients flowing. And then ultimately we need to figure out what kind of models that they're going to require. What do we need to produce for them? From there, you can take that and figure out the technology that you're going to need to adopt to make these models happen.”
Once you have a better understanding of which models will be requested most often, and have taken feedback from potential power users, it’s time to make smart investments in the right technology for your new lab. Albers focused in on three different 3D printing technologies:
-
Selective laser sintering (SLS) – SLS is capable of producing high-quality 3D printed parts at low tolerances, making them optimal for developing professional-grade solutions for patients. SLS is used for producing precision parts that require enhanced durability and ductility. Another advantage of SLS is the lack of support material and post-processing is generally considered to be more streamlined than other technologies.
-
Polyjet – PolyJet 3D printers work similarly to traditional inkjet printers, but cure drops of photopolymer plastic instead of jetting droplets of ink. Polyjet is used in medical settings due to its ability to mix multiple materials together to achieve unique material properties and colors. A key consideration of Polyjet 3D printing is the high cost associated with this technology. Individual prints are often ten times more expensive than competing technologies, therefore Polyject printing tends to serve a more niche category of applications and should be employed selectively.
-
Stereolithography (SLA) – SLA is the most commonly used 3D printing technology in the healthcare space and produces production-quality 3D-printed parts that meet the demands of a wide range of applications. Healthcare providers may choose to leverage SLA to produce low-cost items such as surgical jigs or guides, anatomical visualization models, assistive or adaptive devices, and a variety of other game-changing medical devices.
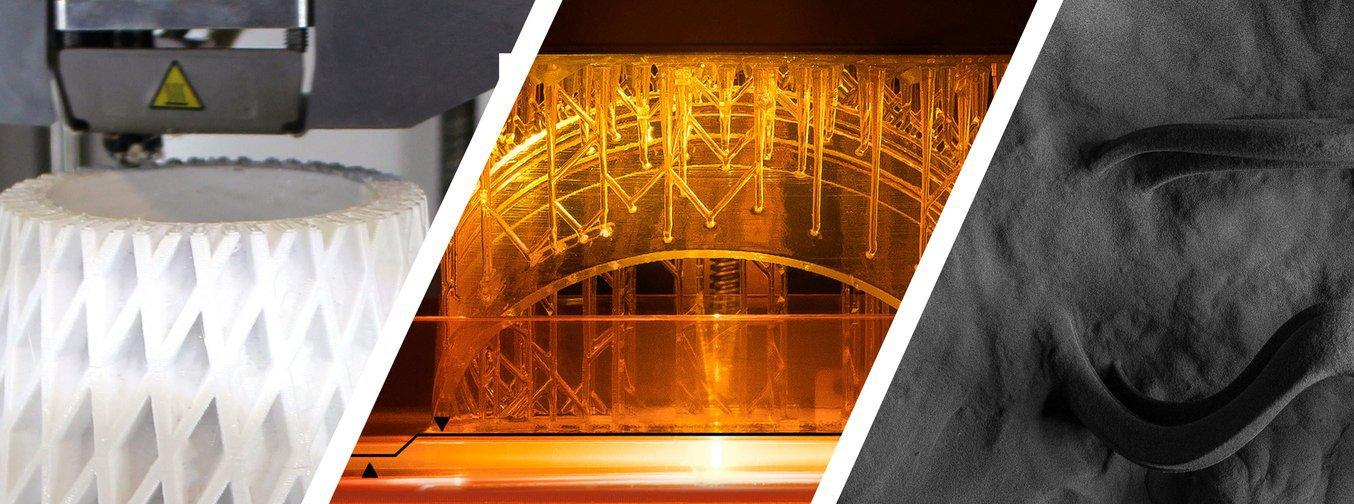
Albers explained, “So to jump into some of the technologies, I have not personally used JetFusion, although it is a promising technology so I’ll mostly describe Polyjet to start. It's great because it gives you quick and easy distinction between the structures by just being able to break the model into as many pieces as you want and assigning different colors so that, at a quick glance, you can see boundaries and borders on part of the plan.”
One downside to PolyJet printers are the upfront and annual maintenance costs, along with high cost per print which can run in the hundreds of dollars. SLS is the technology most often compared to PolyJet printers, and one of the major benefits of SLS is the high-quality, high-performance nylon powder, especially on a cost per print basis. Alders told us that “when we printed some spines, we're using about $1,600 in materials on the PolyJet. And now with SLS, we are at the price point of about $85 dollars per spine in materials.” At St. Louis Children’s Hospital, spines are being printed on the Fuse 1 with Nylon 12 Powder.
He continued, “the second benefit [of SLS] is strength. You know, we had a lot of issues with having to add all these extra supports and scaffoldings into these [PolyJet] prints to make sure they were going to survive. And honestly, I got most of my spines back broken, you know, because they're long. And so by moving it to the durable thermoplastics, these are significantly stronger and I'm not getting broken spines back anymore. And it also is giving our physicians more confidence when they're manipulating it to bend a plate, drill into it, to screw trajectories and fixturing.”
Albers added one final point regarding fused deposition modeling (FDM) technologies. He said, “A lot of people in 3D printing may notice that I haven't really included FDM. They are great printers, but I haven't been able to find a great fit for that technology. However, we are always open and keep it in mind.”
If you'd like to learn more about the cost and benefits of each major 3D printing technology mentioned here, Formlabs has created multiple in-depth guides to explain the difference. You can find them here:
-
SLA vs Polyjet: In this comprehensive guide, we take a closer look at PolyJet and SLA 3D printers, and how they compare in terms of costs, print quality, materials, applications, workflow, speed, and more, to help you decide which technique is ideal for your hospital.
-
SLA vs SLS vs FDM: In this article, we’ll take a closer look at the three most established plastic 3D printing processes today: fused deposition modeling (FDM), stereolithography (SLA), and selective laser sintering (SLS).
On the low-cost hobby market, LCD 3D printers are yet another option. While these printers are similar in technology to SLA and offer some speed benefits, they are generally more difficult to maintain and require more overall attention. This comes from the fact that they often require manual resin dispensing which poses a problem for scalability and changing from one material to another generally takes more work.
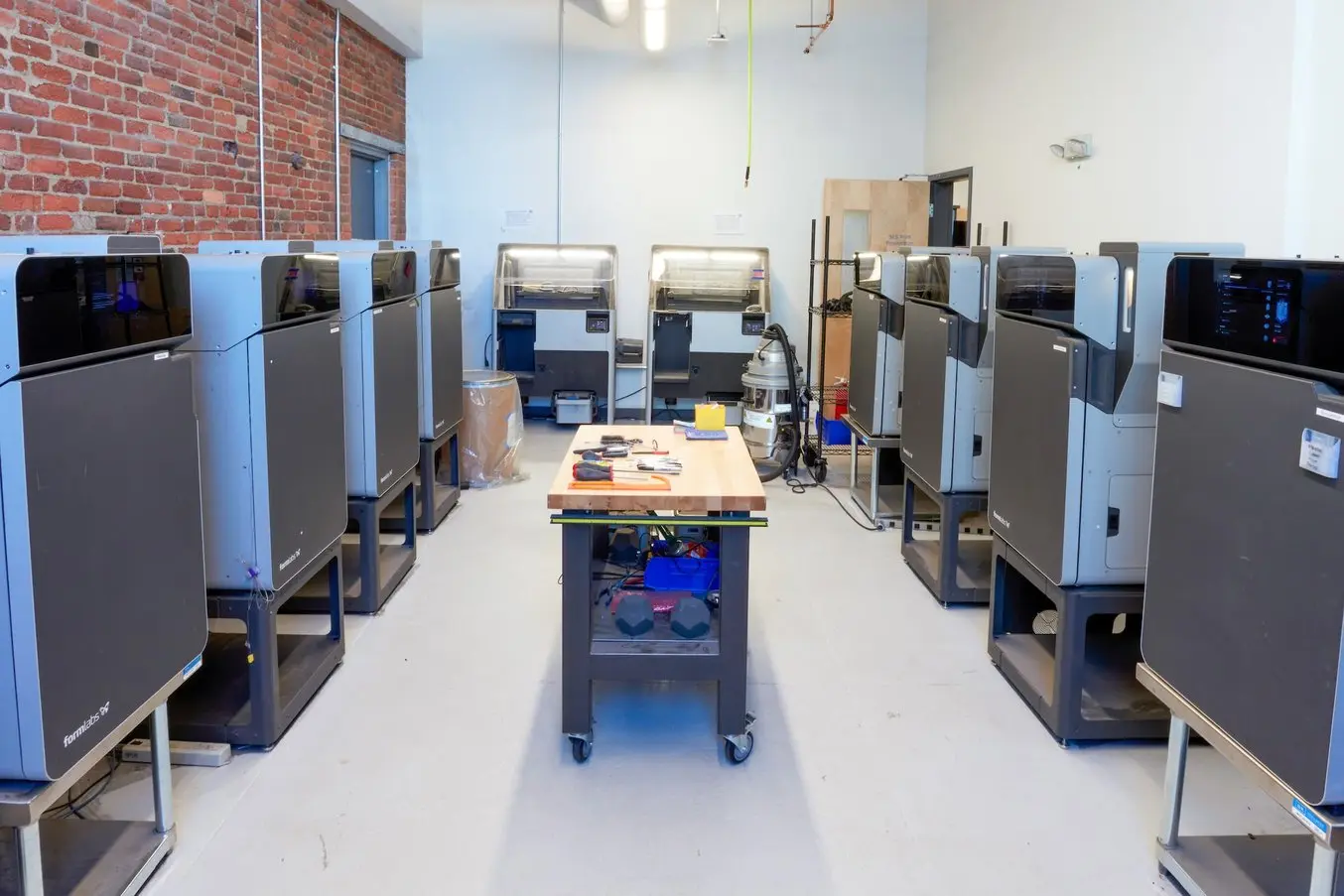
Managing 3D Printer Fleets
Managing multiple SLA and SLS printers doesn’t have to be complicated — any business can get a fleet of SLA and SLS printers up and running in just a day or two. By reviewing four different successful multi-printer scenarios, this guide will help you set up an efficient workflow for any volume or part type.
Growing Your Team and Compliance
Summer Decker recently won the Patents for Humanity 2023 award for her work on COVID-19 test swabs. She is an expert in additive manufacturing and Director of 3D Clinical Applications within the USF Health Department of Radiology.
Her advice for setting up a lab is simple: Get help from everyone you can. This will include finding internal champions, like Albers mentioned, but also medical students who are eager to find new and innovative ways to improve patient outcomes. Many medical students will be quick to pick up on 3D printing, and will be fully trained in the technology as they become residents.
Decker emphasized this point by saying, “I cannot stress any more fervently to get help from your med students and residents. A lot of our team started out as our medical students. They started out in that first lecture of medical school saying, ‘hey I want to be doing 3D work,’ and we got them involved and now they're my residents. I love that because now we have enthusiastic help, and we have people that come up with the most amazing ideas.”
Getting help and buy-in for a lab is also going to include educational content. This includes educating and working with your radiology team, since those teams are generally very good at reading 2D scans, but not at facilitating the creation of the best possible 3D model. Decker had to spend extra time making sure radiology was onboard, walking them through why a decent diagnostic image may not be sufficient for 3D modeling. She added, “I'd spend a lot of my time educating my organization trying to manage expectations. We've had people want stuff within a few hours, that's like a full liver, I mean we have to really educate. I had to really go in [to radiology] and explain this is why we got to work together. When I first got started it took me some time to educate the department of radiology on image quality and slice thickness and contras. We were so fervent about this we wrote a paper about the importance of that.”
Quality control is another huge theme across the hospital — but especially within 3D printing departments. Decker added that, “another big suggestion, when you're building quality assurance, is always trying to make sure that you're doing what you can as a lab to have very strict QA policies, such as modeler reliability maintenance on your printers, testing phantoms, and following all the ISO FDA guidelines. A lot of times people think it's as simple as putting a printer in a room and just starting.”
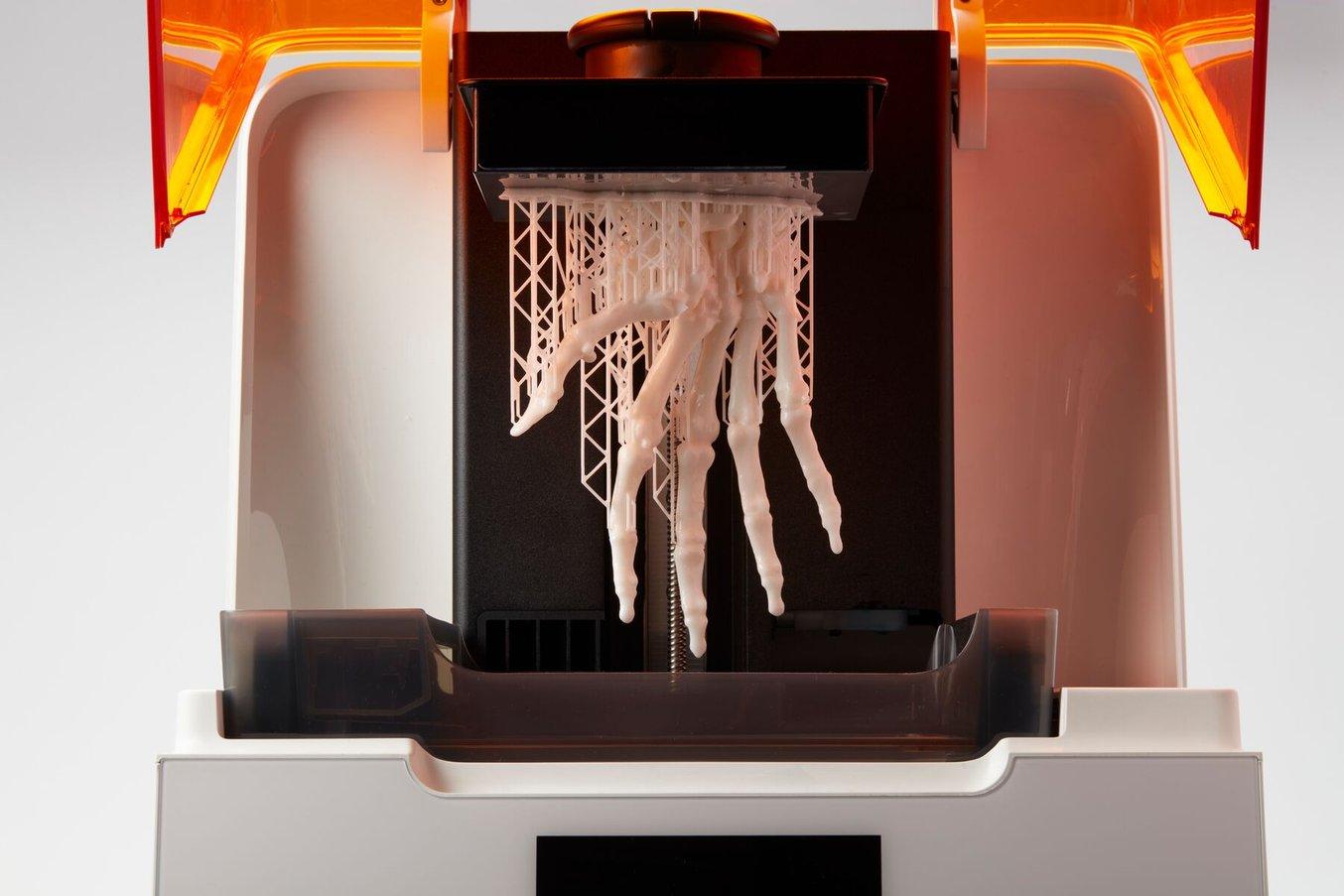
The Ultimate Guide to Quality Assurance and Regulatory Affairs in Medical 3D Printing
This document aims to guide users in the medical device industry through every stage of the product development process.
Scope Determination
Amy Alexander is the Unit Head of Biomechanical Development & Applied Computational Engineering at the Mayo Clinic Division of Engineering, and has extensive knowledge of what it takes to be successful with 3D printing.
During her talk, she offered advice around scope determination and evaluating the comparative benefits of in-house 3D printing and outsourcing. The team at Mayo Clinic started small with in-house printing; they were determined to not take on more than they could handle, and instead focused on executing at a high level with a more narrow scope of applications.
Alexander covered a total of five different elements of success when creating a 3D printing lab, the first being scope determination. She said that, “The first [element] is truly understanding what your scope is. You think, ‘oh wow I work at a hospital and I think 3D printing is amazing, I have a 3D printer in my house, I'm tech savvy, I think this would greatly help my physicians and my patients, and I want to do this.’ But you really need to think about what problems are you solving, what gap is there in the practice that you would like to fill, what gap is there that your surgeons are having that you can help them with. In biomedical engineering there's kind of this historical issue where engineers come up with a solution without talking to the people who are using the tool and they show up all happy, and the surgeons go who are you, you don't know my practice, you don't know my procedure how do you think you know what I need.”
Today, the Mayo Clinic has emerged as one of the leading 3D printing hospitals in the world, thanks in part to the team's relentless focus on scope and growing their 3D printing applications slowly.
Learn More to Get Started With In-House 3D Printing
If you want to hear about what Summer Decker, Brian Albers, and Amy Alexander have to say about setting up a 3D printing lab at their hospitals, you can click the link below to watch our free, on-demand webinar and hear from the experts directly.
Formlabs offers an end-to-end 3D printing solution for any anatomy that comes in the door, with a wide variety of materials and applications available on a single 3D printer, the Form 3B. Our technology has been validated in FDA-cleared workflows and we develop and manufacture our own materials. To learn more about Formlabs, visit our medical website or contact one of our medical experts.