How PMRobotics Accelerates Drone Production With Fuse Series SLS 3D Printing

Drone are one of the fastest growing segments in manufacturing by any measure. Unlike many of the world’s other high-growth industries, however, the competitive landscape is highly fragmented. While there are some massive companies, like DJI, or California-based Skydio that own large portions of the market share, there are still hundreds of small and medium-sized drone manufacturers who have been able to carve out their own niche.
PMRobotics, a Swiss drone manufacturer, is part of that upswell in small, independent manufacturers gaining traction in the industry. Their success, in part, has been made possible by their adoption of selective laser sintering (SLS) 3D printing for everything from end-use components to manufacturing aids and prototypes.
We spoke to co-founder Niklaus Hagen about how working with Formlabs and Swiss partner 3D-EDU has made integrating the Fuse Series SLS ecosystem easy, and how the printer has allowed them to reduce their development timeline for a new drone from almost three years to just nine months.
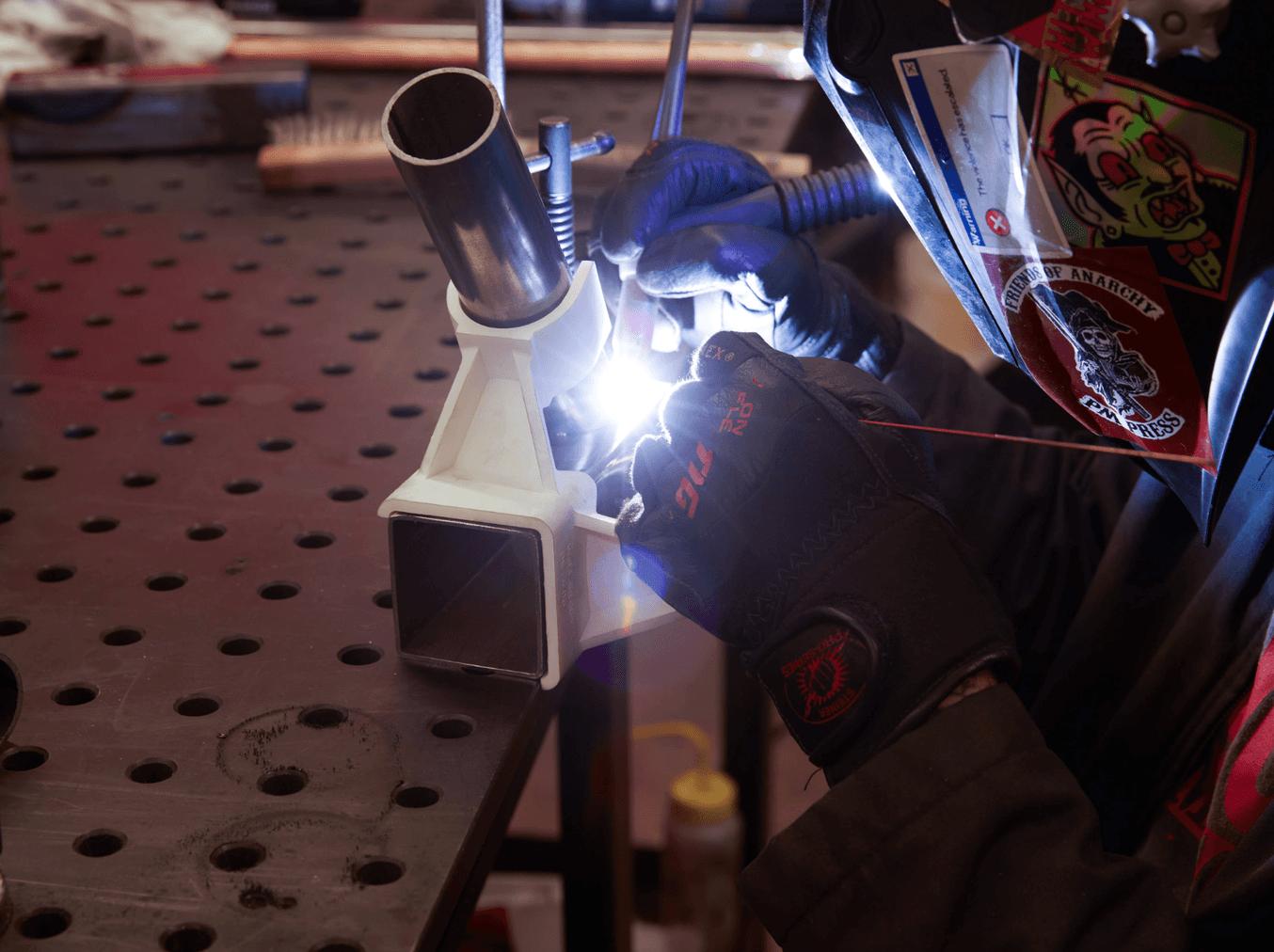
Low-Cost and Rapid Jigs and Fixtures for Metal Fabrication
This white paper outlines a methodology for using 3D printers to produce jigs, fixtures, and other tools for metalworking. Real-world case studies show how Formlabs printers create durable, precise, and heat-resistant tools that perform well in demanding environments. It highlights how companies can cut lead times and costs by up to 90% while improving tool customization and complexity.
Keeping Operating Costs Low to Gain Traction
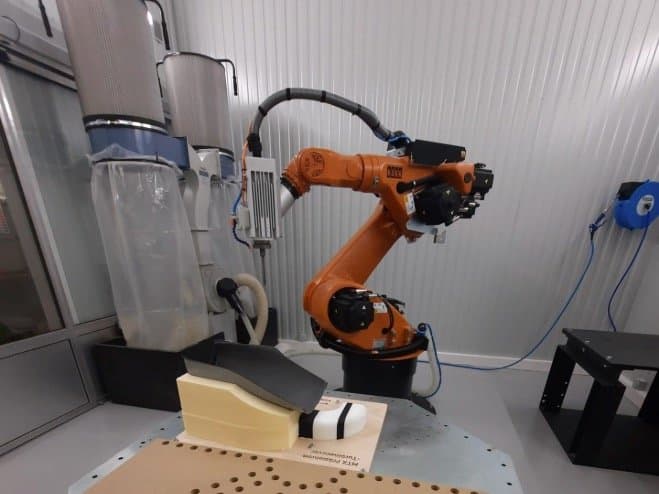
The integration of automation tools promises rapid returns in productivity, but the machines need extensive tooling and customization in order to work with new products and iterations, which is where SLS 3D printing gives PMRobotics an advantage.
Getting a new drone in the air, let alone to market, can seem like an insurmountable task for a small company. Manufacturing high-performance drones requires heavy investment and expertise in software programming, hardware design and development, and production capacity. Hagen, recognizing that reality, invested in building a team of multi-functional experts and where they needed help, automation machinery. “100% of the development, design, and production is actually done in-house. I try to opt for an automated version when I can, so that I only need to add staff as necessary,” he says.
Ensuring that the automation equipment can continuously adapt to new designs and updates requires an agile approach to production. With automation as a cornerstone of his business model, Hagen needed to find a way to ensure that adaptation could happen smoothly, without putting undue pressure on his small team.
"In the past, we used to glue together small, complex holder constructions made of milled wooden parts and fiberglass for our CNC milling machine. We had so many of these assemblies that had to be fitted or where brackets had to be glued together from small parts," he recalls.
Manual fabrication to support prototyping, testing, and production, were adding months to the development process for new drones. Hagen brought in 3D printing to speed up design, but his first printer, a model using fused deposition modeling (FDM) technology, wasn’t able to create parts with the strength and surface finish necessary. They needed a solution that combined the ease of use and accessibility of FDM with the reliability and part quality of more industrial systems. After touring the 3D EDU showroom and demoing the Fuse Series, they decided to bring SLS in-house.
"Not a great deal has happened in the FDM sector in recent years, but for SLS, the development has been rapid. When we started 3D printing nine years ago, it was unimaginable that you could have your own SLS printer in your workshop at this price."
Niklaus Hagen, Co-Owner, PMRobotics
Since the addition of in-house SLS, PMRobotics has put the printer to use improving their operations through on-demand manufacturing aids, functional prototyping, and end-use component production.
On-Demand Manufacturing Aids
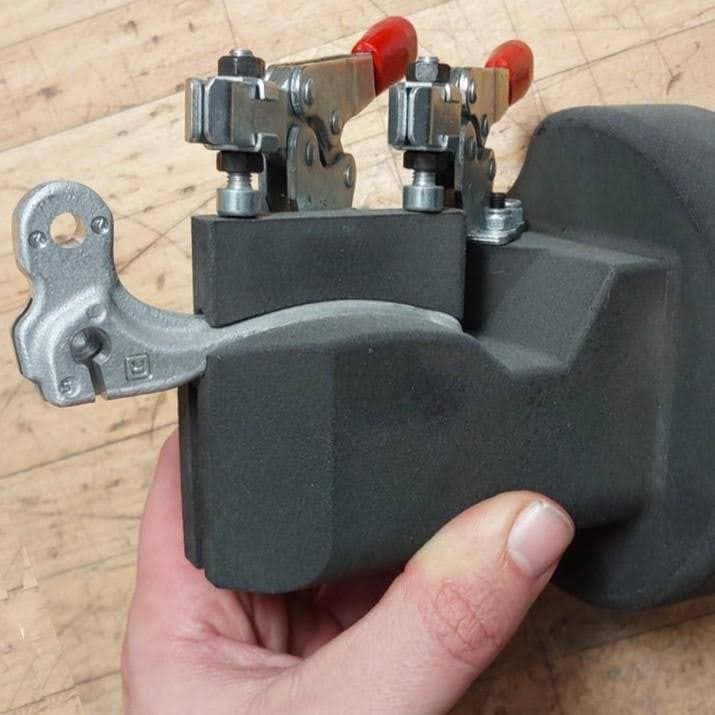
This CNC milling jig holds a metal component firmly in place during the milling process, improving the CNC machine’s accuracy and avoiding potential costly damages or inaccuracies.
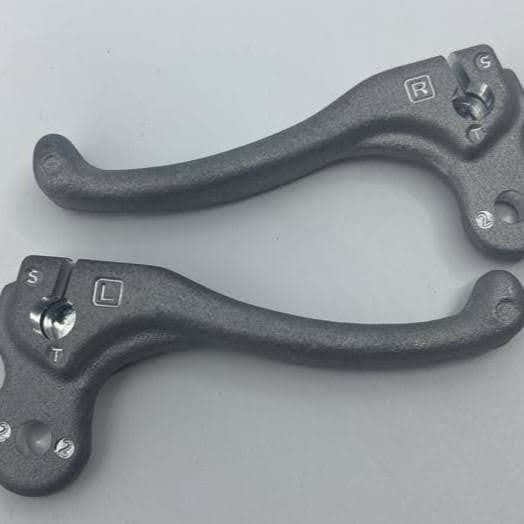
The holding gauges with bolted clamping levers are attached to the fourth axis of the milling machine to enable optimum machining.
Adapting automation tools to new products and processes requires quick, durable, highly accurate brackets, grippers, fixtures, and more. Because of PMRobotics’ reliance on complicated automation machinery, they need to be able to quickly design parts that can fit tightly onto or into existing equipment. Nylon 12 GF Powder parts from the Fuse Series have the dimensional tolerance that makes it possible.
"With the Fuse [1+ 30W], there are so many more possible applications. Be it adapters for vacuum hoses [of vacuum tables], holding gauges, production gauges, production equipment, aids, brackets, or small details on our CNC machines," says Hagen.
With only six people on the team, all of their efforts should be focused on the design and production of the end-use drones, rather than optimizing the tools needed to make those drones. Having access to a fast fabrication method in-house frees up the designers’ time for higher-value tasks. Every member of the team can identify problems they face in their daily tasks and send parts to the printer immediately, solving their issue with a same-day delivery jig, bracket, hose, or attachment.
"With the Fuse, I can solve many, many daily problems much more flexibly. For example, I have self-built vacuum tables with large air hoses for our KUKA robots. Instead of spending hours looking for a hose connection and then having to order it, I can design it myself in CAD and have my hose connection with a quick-release fastener the day after, exactly as I want it," says Hagen.
Fast, Functional Prototyping Shortens Production Timelines
Without in-house 3D printing | In-house 3D printing | Time saved with 3D printing | |
---|---|---|---|
Time-to-market of the drone | 2 years and 9 months | 2 years | 9 months or 27% |
Lead time / part | 4 days | 1 day | 3 days or 75% |
A major advantage of scaling with SLS rather than FDM is the increased functionality of the parts. Ideating, prototyping, testing, and low-volume production with the same technology, print parameters, and material shortens development timelines and improves the reliability of preliminary results.
A customer order for a large target drone — used for defensive practice — had an even shorter delivery timeline than the PMRobotics team was used to. Development processes for multiple components were happening in parallel with functional testing, and outsourcing certain parts was adding four days to their schedule for every order or iteration.
For the next order, they brought in the Fuse Series ecosystem and started printing overnight. Working hours were spent testing functional parts and tweaking designs while the printer churned out parts every night. Without any time spent waiting for parts, the overall development timeline was reduced by 30%.
"In the same time it takes others to order and receive a part, I have already fitted it perfectly with the Fuse. Others need six or seven weeks for this and I'm done in a week, thanks to the in-house workflow. In total, I've saved three quarters of a year in development time compared to external deliveries."
Niklaus Hagen, Co-Owner, PMRobotics
Taking Flight With Fuse Series End-Use Parts
Once the PMRobotics team finished designing and testing their model, they moved seamlessly into production, printing all the drone’s plastic components in the same Nylon 12 GF Powder they used for prototyping. To fulfill the batch order of eight drones, the PMRobotics team leveraged the production capacity of the Fuse Series.
"The Fuse ran almost continuously every day, with full build chambers and a 30% pack density…the printer was worth it from this one product alone, because we wouldn't have finished it so quickly and professionally if we hadn't bought the Fuse [1+ 30W].”
Niklaus Hagen, Co-Owner, PMRobotics
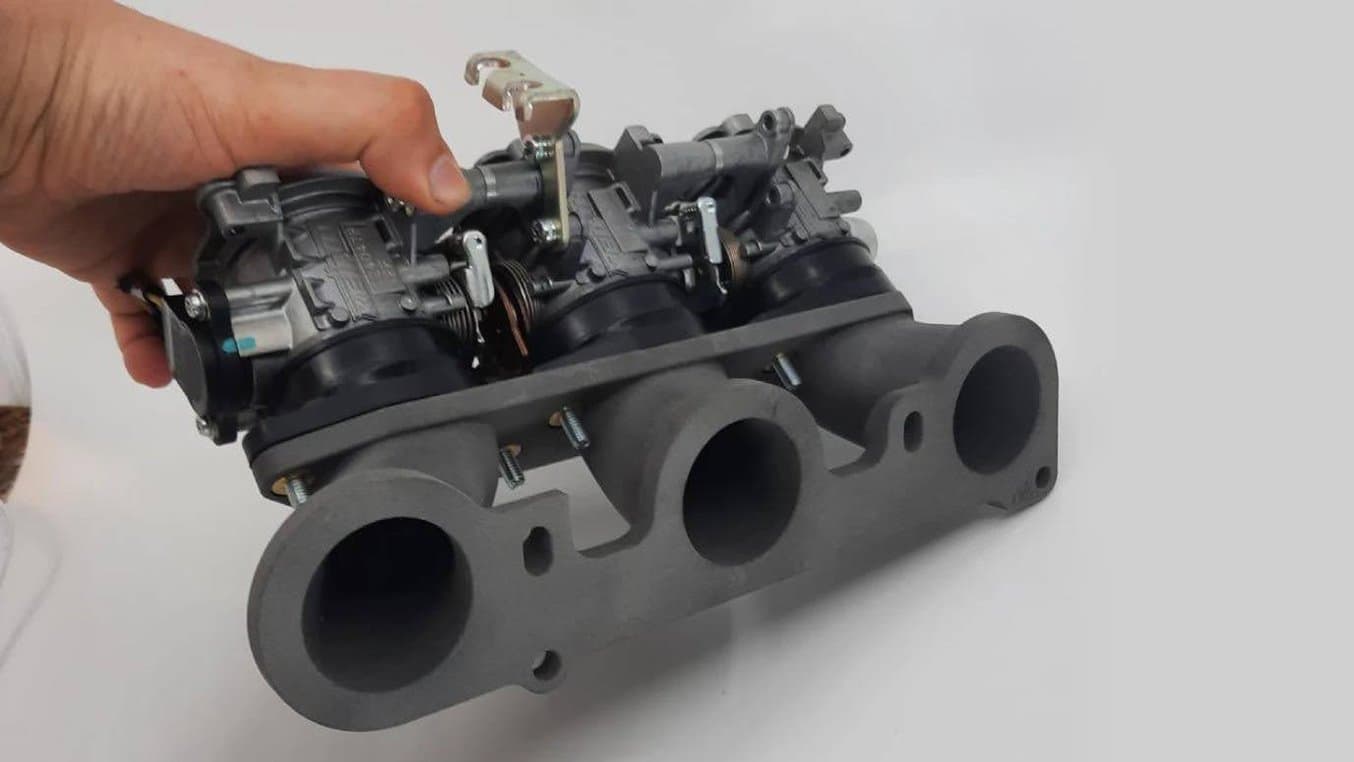
Having the Fuse Series in-house also gives the team the flexibility to take on lucrative side projects that draw on their 3D design and printing expertise, as well as the end-use capacity of the Fuse Series.
Other profitable side projects have spun off the team’s success with drone production. Recently, the Fuse Series and Nylon 12 GF Powder were put to use on the ground for the re-manufacturing of an intake manifold on a classic car engine. SLS 3D printing presents an ideal solution for antique or classic designs that may no longer have tooling available. With the Fuse Series, Hagen printed a manifold with the necessary chemical and temperature resistance.
“The intake manifold is continuously exposed to engine heat and fuel vapors from the fuel injection system. In contrast to FDM, the Fuse Series enables a nice, homogenous material with sufficient thermal stability. Additionally, it’s also petrol-resistant,” says Hagen.
Between prototyping, manufacturing aids, end-of-arm-tooling for automation machinery, and end-use production, the Fuse Series helped PMRobotics achieve an almost immediate ROI. Side projects like the engine manifold are able to create new profit streams for PMRobotics, without adding too much to the team’s workload.
“We can simply print custom solutions. It’s cheaper and above all, faster. The Fuse 1+ 30W is the simplest printer we have. There’s nothing to adjust, there’s nothing to mess up. That’s what I appreciate most about the Formlabs’ system: that it simply works and is stable,” says Hagen.
To learn more about SLS 3D printing, visit our product page. To see the thermal properties of Nylon 12 GF Powder for yourself, request a free 3D printed sample.