Formlabs is proud to introduce Flame Retardant Resin, our first self-extinguishing and UL 94 V-0 certified material for stereolithography (SLA) 3D printing. Designed specifically for the transportation, aviation, manufacturing, electronics, medical and aerospace industries, Flame Retardant Resin enables new applications for customers with tightly regulated workflows, such as:
-
Low-volume production parts for aerospace, aviation, automotive, and medical environments
-
Tooling and manufacturing aids for high temperature environments or near ignition sources
-
Electronics enclosures, connector housings and covers
-
High-power electrical applications (e.g. transformer bobbins and relays)
-
Maintenance, Repair, and Overhaul (MRO) applications
Users can now leverage the speed and design freedom of 3D printing while maintaining regulatory compliance. Formlabs’ powerful SLA technology coupled with Flame Retardant Resin is an end-to-end solution for the design and manufacturing of parts that require UL 94 flame retardant properties.
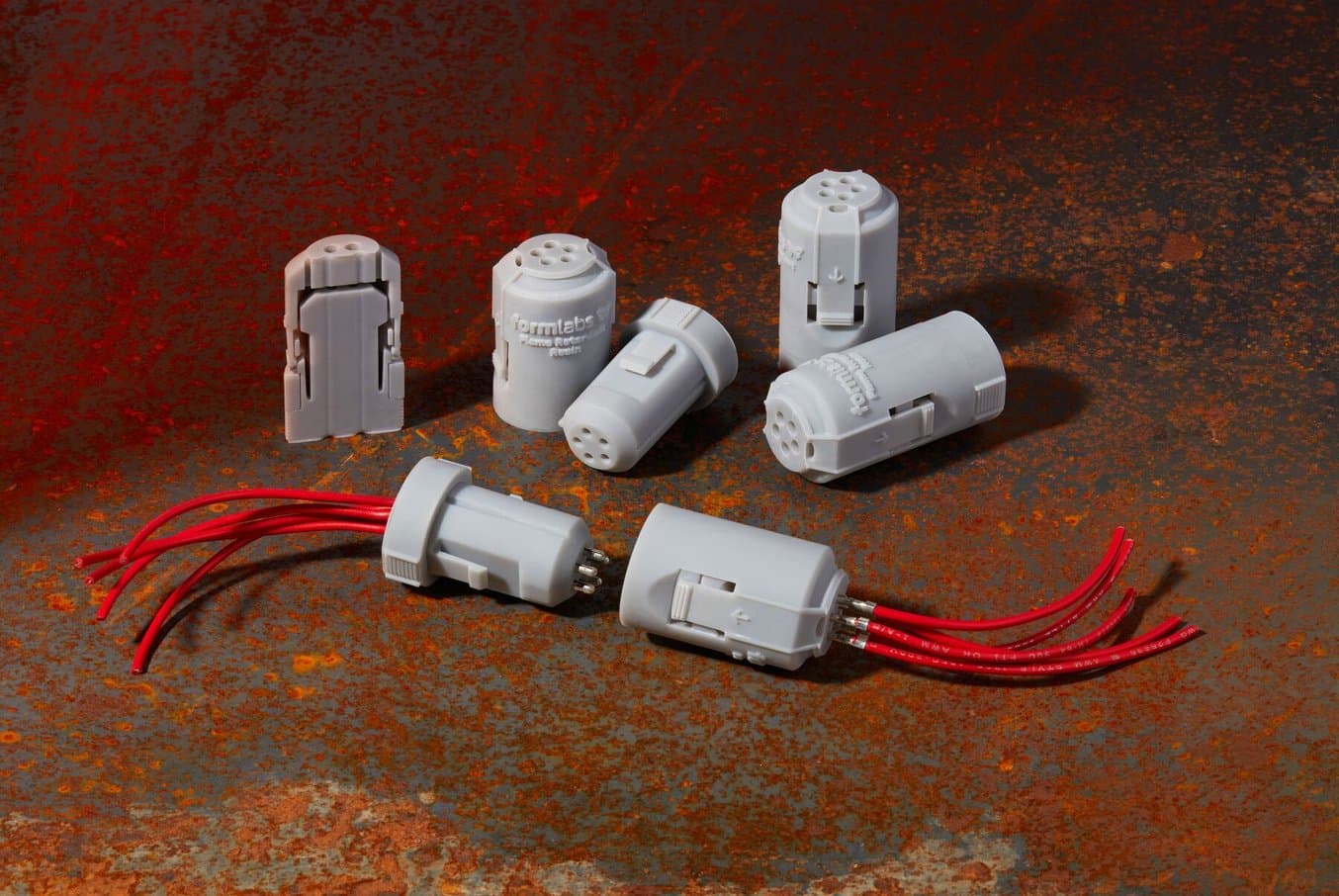
How Flame Retardant Resin Unlocks New Applications for Avance Design
Learn how you can use Flame Retardant Resin to easily 3D print flame retardant, heat-resistant, stiff, and creep-resistant parts that will perform well long-term in indoor and industrial environments with high temperatures or ignition sources.
Why Flame Retardant 3D Printing?
Combine Benefits of Traditional and 3D Printing Workflows
For manufacturers in industries like aviation, electronics, medical devices, and transportation, requiring flame retardant parts is nothing new. These environments, where either sparks, ether, or other fuel sources are commonly found, necessitate strict regulatory oversight to keep workplaces and products safe. The gold standard certification in these disciplines is UL 94 — a plastics flammability certification that determines a material’s tendency to either extinguish or spread the flame once ignited. Formlabs Flame Retardant Resin possesses UL 94 V-0 Blue Card certification, passes FAR 25.853(a) flame standards and smoke and toxicity tests, and can endure hazardous environments with open flames, ignition sources, and high temperatures.

Flame Retardant Resin is self-extinguishing once the flame source is removed.
Traditionally, plastics that can meet these standards are either machined, injection molded, or cast. These processes often require expensive industrial equipment or hours of hands-on labor. Many businesses outsource to machine shops or molding operations, but run into weeks-long lead times or high expedition fees. More affordable in-house processes, such as casting, require users to perform a multi-step process of silicone and polyurethane casting based on machined or 3D printed patterns. Traditionally, both outsourced or in-house workflows are either expensive or inefficient and labor-intensive to rely on consistently, keeping them out of potential applications where UL 94 rating is necessary.
Developments in some 3D printing materials have made high temperature resistant or flame retardant materials available, but there have been drawbacks. Many fused deposition modeling (FDM) 3D printer manufacturers offer flame retardant filaments, but these parts aren’t appropriate for functional testing, customer facing end-use parts, or for maintenance and repair applications. Other technologies, like SLA, have previously offered high temperature resistant 3D printing materials that are isotropic, strong, and have a superior surface finish, but have lacked a UL 94 certification.
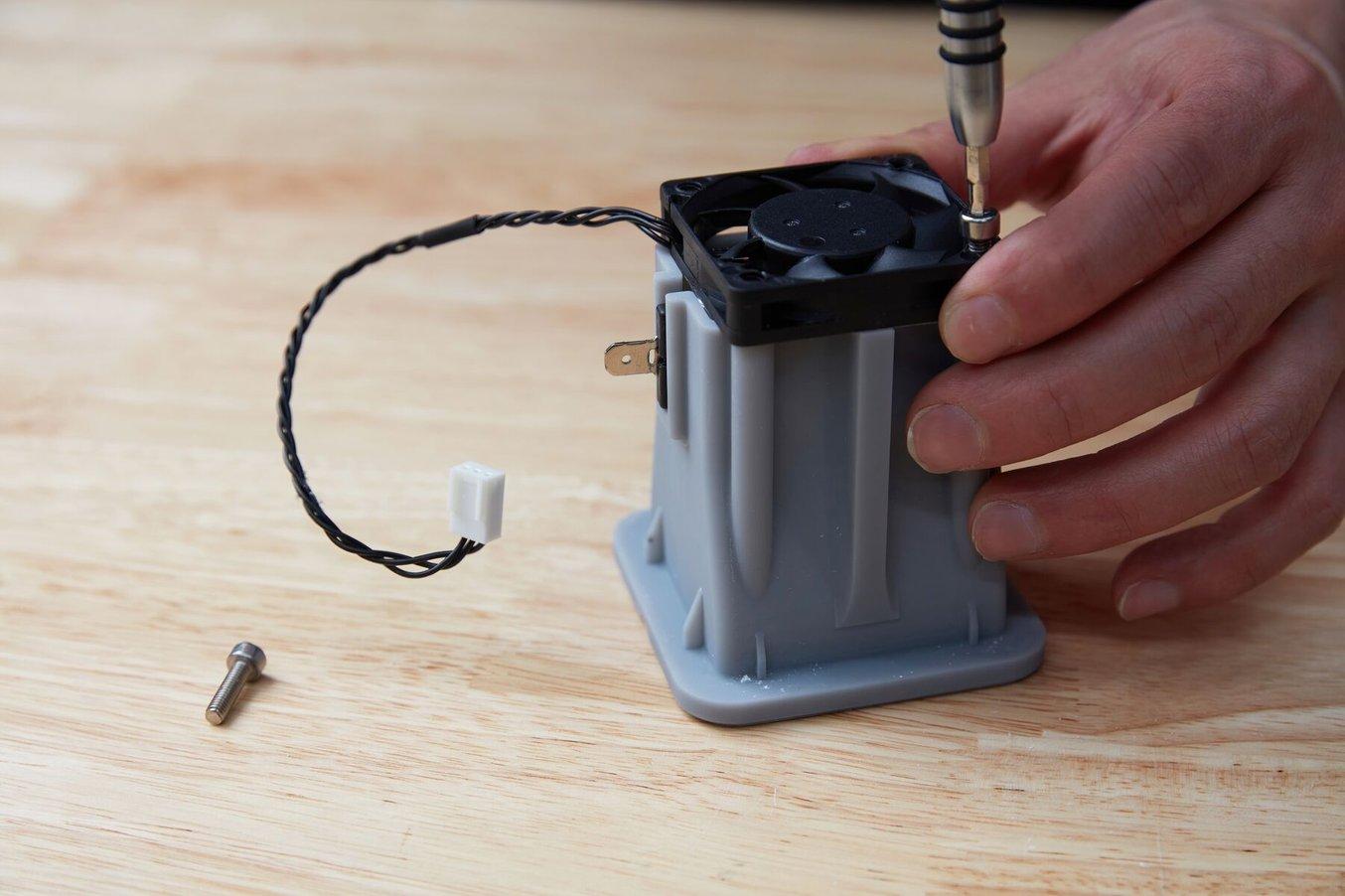
Flame Retardant Resin parts (light grey) can perform as components in functional assemblies, and can handle post-fabrication operations such as tapping, trimming, and drilling.
Flame Retardant Resin combines each facet to enable high performance applications and certified, safe workflows, all with the accessibility and power of Formlabs’ SLA platform. After post-curing at 80°C for 120 minutes, Flame Retardant Resin parts have a heat deflection temperature (HDT) of 111°C @ 0.45 MPa and a tensile modulus of 3.1 GPa. Other materials designed for high temperatures can be brittle, but Flame Retardant Resin can perform as a component in a functional assembly and be drilled for screw threads. Parts are stiff and resistant to creep, making them reliable and consistent in indoor and industrial environments. Unlike many FDM parts, Flame Retardant Resin exhibits a smooth, matte surface finish with clean lines and high dimensional accuracy, making parts suitable for end-use products or components in assemblies that require tight tolerances.
Fracture Toughness (KIC) | Fracture Toughness (Wf) | Impact Strength | Tensile Modulus | Ultimate Tensile Strength | Elongation at Break | Heat Deflection Temperature (HDT) @ 0.45 MPa | |
---|---|---|---|---|---|---|---|
Flame Retardant Resin | 2.17 | 848 | 22 J/m | 3.1 GPa, 2.9 GPa* | 41 MPa, 39 MPa* | 7.1%, 9.4%* | 111°C, 94°C* |
High Temp Resin | 0.55 | 47 | 18 J/m | 2.8 GPa | 58 MPa | 3.3% | 142°C |
Tough 2000 Resin | 3.61 | 3060 | 40 J/m | 2.2 GPa | 46 MPa | 48% | 63°C |
Grey Pro Resin | 1.76 | 541 | 19 J/m | 2.6 GPa | 61 MPa | 13% | 78°C |
Clear Resin | N/A | N/A | 25 J/m | 2.8 GPa | 65 MPa | 6.2% | 73°C |
*There are two post-curing options for FR Resin. Refer to the technical data sheet to understand how different options affect mechanical properties, and choose the post-cure option that is best suited to the intended application. To achieve the highest HDT of 111 °C @ 0.45 MPa: Post-cure parts in Form Cure for 120 min at 80 °C. For applications that do not require the maximum heat resistance but can benefit from more toughness, post-cure parts in Form Cure for 60 min at 70 °C.
Enable New Applications and Workflows
Industries like aerospace and automotive commonly integrate some type of 3D printing into their prototyping workflows, but often have to move to traditional manufacturing methods while still in the development stage in order to comply with regulatory requirements for flammability. Typical 3D printing materials might have the strength and heat deflection temperatures to perform in the functional testing phases, but not the UL rating. Now, with Flame Retardant Resin, large businesses can not only improve their development timelines, but use a common material across teams, from design to maintenance and repair operations and manufacturing fixtures.
For many industries, maintenance and repair parts have to be ordered from the OEM to ensure the product remains compliant. SLA 3D printing has not traditionally been a viable option, despite its low cost per part and efficiency. With Flame Retardant Resin, SLA 3D printing can finally be deployed as an on-demand repair part manufacturing solution.
Relying on a scalable platform like the Form 3+ and Form 3L enables large teams to increase their 3D printer fleet capacity without heavy investment, giving every team member access to a flame retardant, self-extinguishing, tough, and rugged material that can be used in real-world environments.
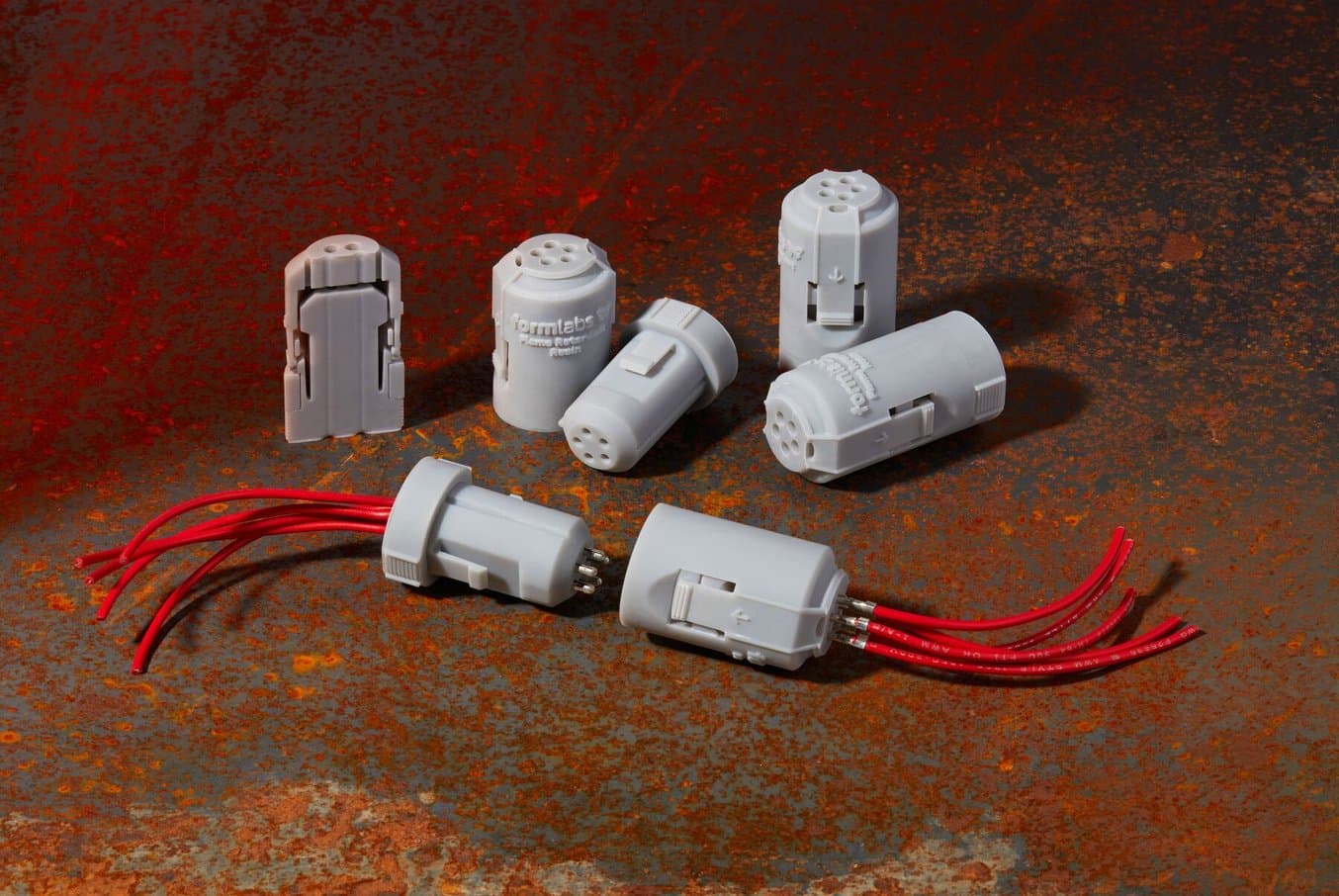
Flame Retardant parts open up new opportunities for 3D printing in the transportation, aviation, manufacturing, electronics, and aerospace industries.
Accelerate Time To Market
Flame Retardant Resin can streamline the workflow for products moving from the iterative design phase to end-use parts in low volumes. Using Flame Retardant Resin and the Formlabs Form 3+ or Form 3L, users are able to rapidly prototype with the same material they’ll use in functional and environmental testing and early-adopter low- to mid-volume production runs. Using one material throughout the process can help reduce the instances of redesigns and allow product managers to fully focus on performance and user feedback. Strong, functional parts that can pass any regulatory hurdle help companies get their products in the hands of consumers and capitalize on market opportunities.
Case Studies: Applications of Flame Retardant 3D Printing
NZ Technologies: End-Use Medical Devices
NZ Technologies (NZTech) specializes in the design and manufacture of advanced human machine interaction (HMI) products, such as touchless visualization platforms for medical and surgical applications. For many of their end-use environments, these products need to be completely UL certified from start to finish. For medical applications such as medical devices, the products will need to be made of flame retardant and self-extinguishing materials to meet the requirements of the operating room setting. To streamline the design process, even the looks-like prototypes are made with the same materials.
The NZTech team had been using an FDM printer filament to prototype their TIPSO® AirPad product, a touchless interface for surgeons, however the parts were lacking resolution and accuracy. As such, NZTech’s lead hardware engineer Jordan Karyanto required the resolution and on-demand power of his Form 3+, as well as the UL 94 rating to comply with both the IEC60601-1 (International) and EN60601-1 (European) regulations for their product certifications. With early access to Flame Retardant Resin, he has been able to combine these advantages into one powerful workflow.
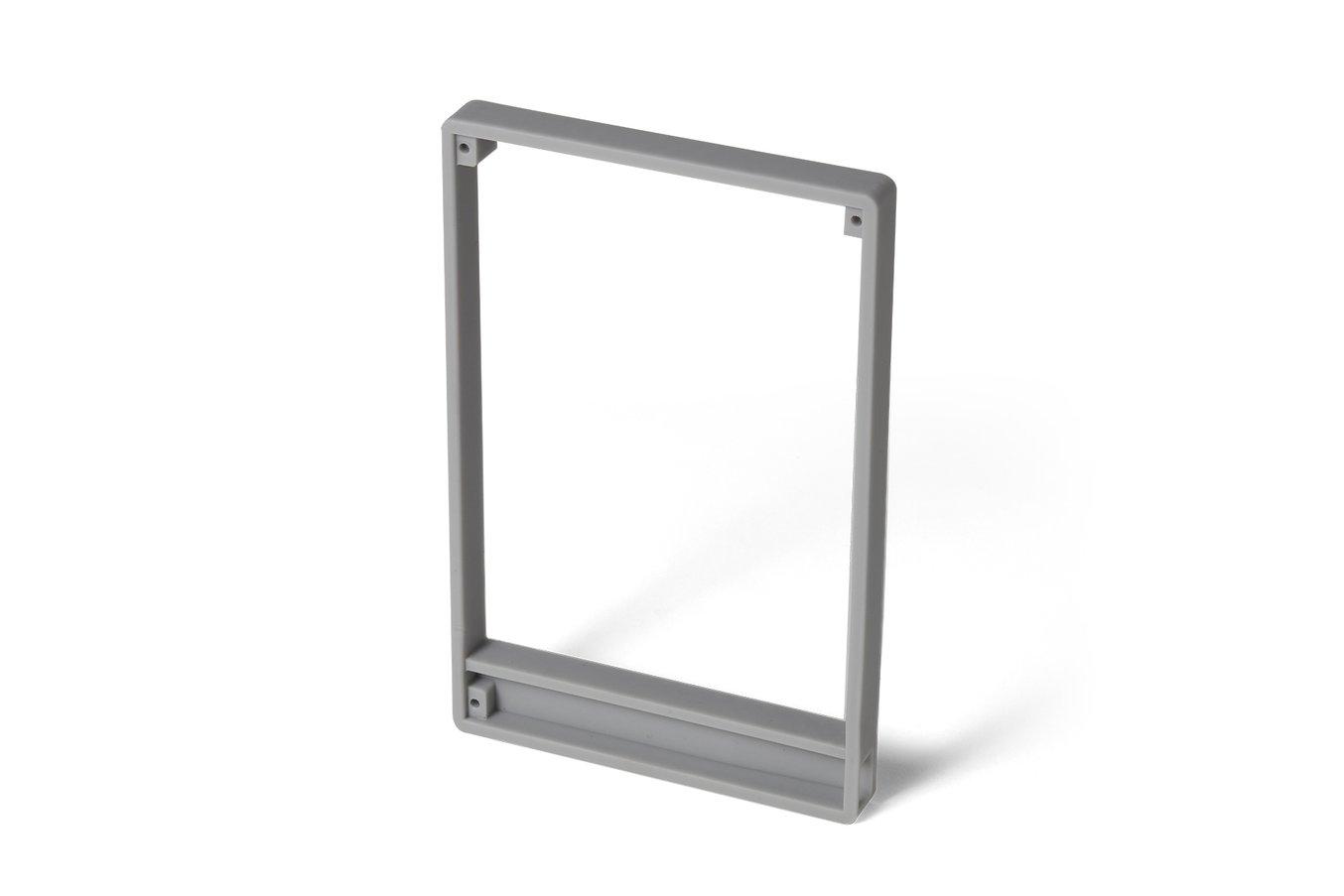
NZ Technologies printed this enclosure in Flame Retardant Resin for their TIPSO® AirPad product, a visualization device used by surgeons in operating rooms, that requires a UL rating.
Karyanto and his team have relied on the Form 3+ for accurate parts that require little post-processing work to get them ready for testing and certification in other industries. “If we’re making a part for testing, we need it to look like and function like the final product. We want to be able to easily mesh an electronic component into an enclosure, which requires dimensional accuracy. As soon as the enclosure is made with FR materials, it’s accepted during the testing phase, so we get both functionality and compliance,” says Karyanto.
We do a lot of demo testing, so having this resin is really helpful. If we need to build any device that will eventually be used in an OR, Flame Retardant Resin is useful for these functional prototypes and testing situations where a fire is present.
Jordan Karyanto, Lead Hardware Engineer at NZTech
Avance: Low Volume End-Use Parts
Avance Design, a product development and engineering consulting firm in Indianapolis, Indiana, USA, has been using 3D printing technology for over a decade, but they still see new opportunities and applications open up with every new 3D printing material development. We spoke with Tony Parker, principal at Avance Design, about his workflow with Flame Retardant Resin.
Along with casting, molding, machining, and FDM printing, Avance uses three Form 3+ and two Form 3L SLA printers to develop products for medical, robotics, architectural, and electronics industries. Manufacturing parts for one of their electronics industry customers traditionally required Avance to do a polyurethane casting process. Parker would 3D print or machine a mold pattern, construct a silicone mold around it, find a commercially available UL-rated polyurethane and pour it into the silicone mold, then extract the casted polyurethane part and post-process it. “It would take days for each part, and if we had to do an order of 20 of them, it would take about three weeks,” says Parker.
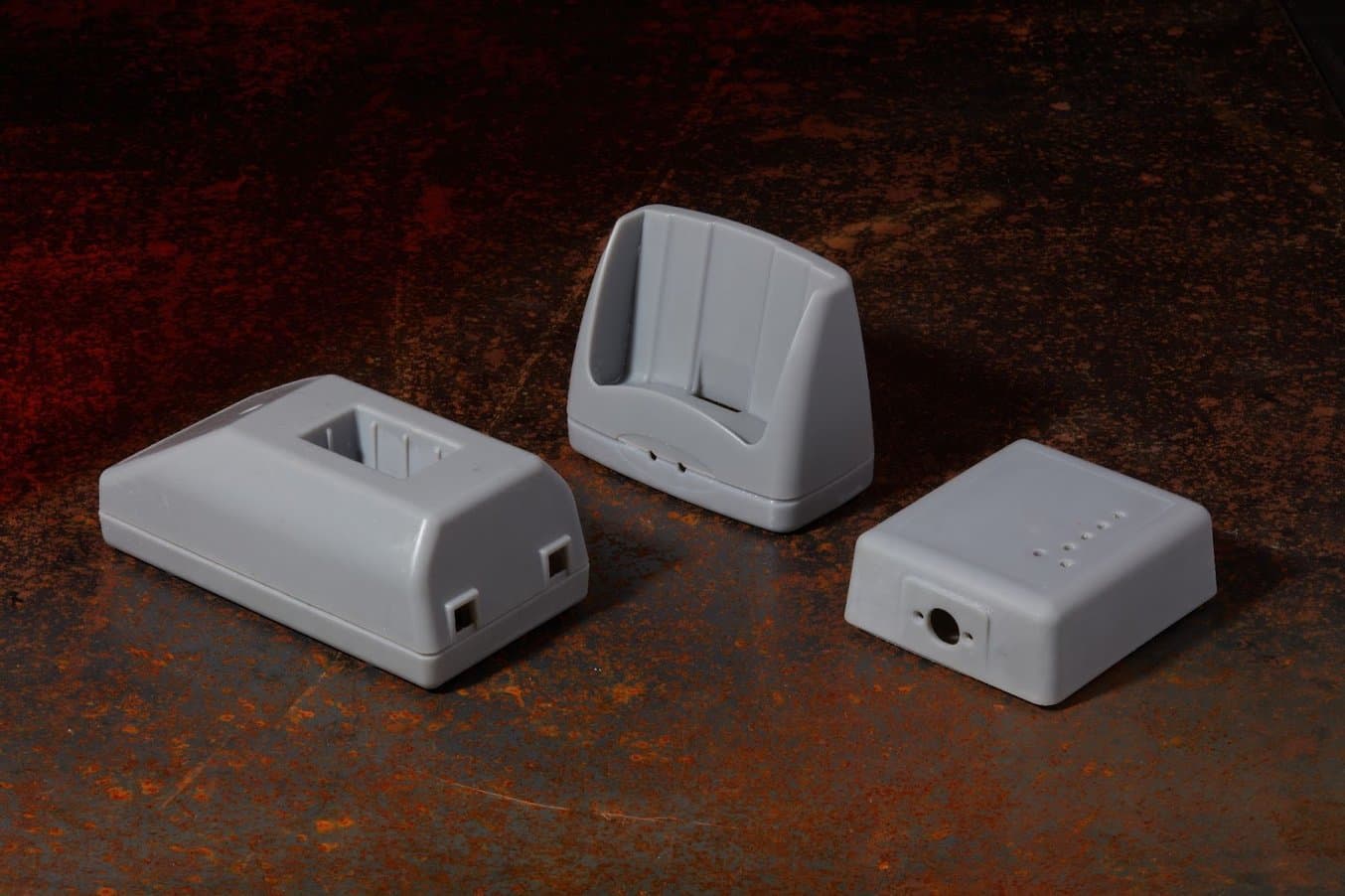
Avance relies on Flame Retardant Resin for parts, like these, requested by clients in the transportation, aviation, manufacturing, electronics, medical and aerospace industries.
Now, with Formlabs Flame Retardant Resin, Parker can cut out multiple steps and go from CAD design to finished part much quicker. “Being able to directly 3D print that part in Flame Retardant Resin cuts that time down to maybe one week for all 20 parts,” Parker says.
In addition to reducing the time and labor required to make UL certified parts, the Formlabs SLA workflow with Flame Retardant Resin provides design freedom, superior surface finish, and a strong, durable part that can withstand additional stressors like screws.
Being able to get a 3D printed part that truly mimics a thermoplastic, finishes well, has fine feature details, and behaves mechanically similar to molded parts is a huge benefit and time saver. With Flame Retardant Resin we can go from CAD design to finished part without the additional work we had to do with other methods.
Tony Park, Principal at Avance
Get Started With 3D Printing Flame Retardant Parts
For highly regulated industries where safety is a primary concern, 3D printing has already improved the iterative design cycle and enabled innovation through geometric freedom and accessible production tools. Now, with materials like Flame Retardant Resin, Formlabs is focusing specifically on the roadblocks that have either created barriers to entry for small businesses or slowed progress for large companies.
Flame Retardant Resin removes some of the obstacles product designers have faced when moving from looks-like models to functional testing or short-run end-use products. With the certifications necessary for use in manufacturing, aerospace, automotive, and electronics environments, Flame Retardant Resin streamlines workflows and helps shorten the iterative loop.
To learn more about material properties or to test the part for yourself, contact our sales team or request a 3D printed sample.