Every day, thousands and thousands of parts are produced using additive manufacturing. Over the years, billions of dollars and countless hours of development have gone into the hardware that produces these parts — making them more reliable, more accurate, faster, and better able to create complex and intricate geometries.
But 3D printers are only half of the equation. Sophisticated CAD programs and powerful 3D printers allow organizations of all sizes to produce incredibly detailed, custom parts — but what are those parts made of? What are they good for? The material properties of those parts are just as important as their form, but for too long, material science for additive manufacturing has taken a backseat to hardware and software. As Drew Prindle of Digital Trends put it, “Additive manufacturing has been hamstrung by a lack of variety in material options.” You can print anything you want, he added, as long as it’s made out of simple plastic.
At Formlabs, we think differently about materials. Since our earliest days, we have placed as much emphasis on the groundbreaking material science that opens up advanced applications as we have on our easy-to-use professional printers. In fact, over time, our emphasis on materials has only grown. With well over 45 materials in our library, we are as much a materials company as we are a hardware company, and we’re proud to say it.
From elastic and flexible to extremely rigid, from flame retardant to static-dissipative, Formlabs has pushed the additive industry forward by building a comprehensive library of powerful materials. Now, with two new groundbreaking chemistries just added to that library — Alumina 4N Resin and Silicone 40A Resin — we’re continuing to unlock critical new applications all the time. Walk through our headquarters and you’ll find dozens of materials scientists in lab coats working on the next generation of advanced 3D printing materials. On days like today, when these carefully formulated and immensely useful materials make it to our customers, it’s easy to see why we are much more than a hardware company — we are truly a materials company.
It is the breadth and unique capabilities of these materials that have helped our customers (more than 100,000 of them!) drive innovation, efficiency, and performance at their organizations. We’re incredibly proud of our material science program, so we’d like to give you a peek behind the curtain.
Read on to learn more about our:
- History of materials development
- Industry-leading materials library
- Best-in-class material science team
- Vertically integrated materials manufacturing
- Plans for providing even more material flexibility and freedom to our customers
Democratizing Access to Industrial Power
From day one, materials development has been central to our mission. At first, we focused on all-purpose materials that printed fast and performed well in a wide variety of applications. Early materials like our General Purpose Clear Resin, Grey Resin, Black Resin, and White Resin were the ideal way for customers to see that high-accuracy 3D printing was possible on a desktop printer. As engineers and manufacturers began to rely on our products for more than just looks-like prototypes, our materials team rose to the challenge, developing our first engineering materials like Flexible Resin, Tough Resin, and Durable Resin. Each of these materials was designed from the ground up to hold up to the most critical and common engineering needs. And they were tuned and tested extensively so they worked every time, right out of the box.
These materials made it possible for early adopters to move to functional testing and even end-use parts. Enabling businesses to bring more and more pieces of their workflow that had traditionally been outsourced empowered them to innovate, and made us realize how expanding our materials library opened up new opportunities for our customers. Businesses that had traditionally been confined to (slow, expensive, rigid) traditional manufacturing processes, were suddenly freed to leverage 3D printing.
Seeing this, we doubled down on materials development and ramped up our R&D efforts to make more high-performance materials.
The Widest Range of Materials
Many engineers, product developers, and designers are now approaching their projects through the lens of 3D printing. Now, 3D printing is often the default option for production, and material variety is the deciding factor.
For more and more customers, like industrial lab equipment manufacturer Labconco, the breadth of material options is the main draw to Formlabs. “The whole reason we bought the Form 3L was because we wanted access to Formlabs’ resin library. I knew it was going to grant me the flexibility and open up new opportunities and possibilities,” said Labconco Product Development Engineer Brent Griffith.
A library of over 45 materials opens up every application, including secondary fabrication techniques like 3D printed rapid tooling for injection molding, thermoforming, and more. Being able to 3D print injection molds in Rigid 10K Resin instead of expensive metal machining can represent cost savings in the hundreds of thousands of dollars for many manufacturers.
In September 2023, Formlabs launched a pure ceramic material, Alumina 4N Resin, making accessible, 3D printed ceramics in aerospace, automotive, and industrial casting applications possible at a 10x lower price than the leading alternatives. With an affordable desktop 3D printer, businesses as small as one-person consulting firms or as large as NASA can both have access to technology that’s been out of reach for so long.
Silicone is a material that is immediately recognizable to engineers and manufacturers — it’s already in use all over the world and in products we interact with on a daily basis. For 3D printing, however, it’s been elusive — available only on a few extremely expensive and complicated 3D printing. Powered by Formlabs’ new patent-pending Pure Silicone Technology™, Silicone 40A Resin is the first accessible 100% silicone 3D printing material. When paired with the affordability and design freedom of Form 3 Series desktop resin 3D printers, these materials open up new pathways for development and low volume production that were out of reach for many manufacturers before.
The healthcare industry, from orthopedics to dental surgery, has the highest barriers to entry for 3D printing manufacturers. Every step of a product’s lifecycle is regulated and has to go through an approval process — for good reason. From our first Dental SG Resin material approved for intraoral surgical guides to long-term materials like Dental LT Comfort Resin, our biocompatible materials have unlocked indications one by one. These specialized materials enable healthcare providers to focus on their work, without worrying about the safety of their products or appliances.
Investment Into Research and Development
To reach these milestones, Formlabs invests deeply in our materials development — by using our materials ourselves for our own product development and production and by working closely with customers, we know that materials are the gateway to their continued success.
A Team of 60+ Chemical Engineers and Developers
To create industry-changing materials, you need the best and the brightest. Formlabs has built a team of 40+ materials scientists and engineers to research, develop, and test the materials that turn our desktop and benchtop 3D printers into powerful engines of innovation. Our close proximity to juggernauts of research, education, and manufacturing like MIT, Harvard, and life sciences institutes helps foster an environment where leading minds come to learn, collaborate, and challenge each other.
In addition to the 40 chemical engineers working on the formulation of new materials, Formlabs has a team of 20 settings optimization specialists who ensure that the printers and materials work seamlessly together. Many manufacturers can create materials that perform in a lab under perfect conditions. Formlabs goes above and beyond to make sure that our materials have the same level of performance in the field, even under extreme conditions.
Custom Settings: The Key to Consistent Printing
When 3D printers and materials are developed separately, there’s absolutely no guarantee that the material will work consistently on different printer models from various manufacturers. This means that customers often have to troubleshoot issues themselves and search online forums to find the best settings.
Uniquely in our business, Formlabs’ settings optimization team develops print settings and validates them on each of our printer models to ensure the highest print success rate and save you the trouble of experimentation. This is the key to making every customer’s experience consistent, whether you are printing one or 100 parts a day.
“From the beginning, it’s been important that Formlabs provides a reliable and accessible printing process. Supporting a successful print process meant rigorous engineering, innovative material development, and enabling a seamless end-to-end process for our users.”
Max Lobovsky, CEO and co-founder of Formlabs
Formlabs has invested in not only the recruiting, but also the development of the engineering and materials teams, and worked hard to nurture a culture of innovation that supports each team member to do their best work. Our efforts haven’t gone unnoticed, and we were elated to be recognized in 2023 as one of the Best Workplaces for Innovators globally. By creating a cutting-edge wet lab that is central to the physical layout of our headquarters, we keep materials design top of mind.
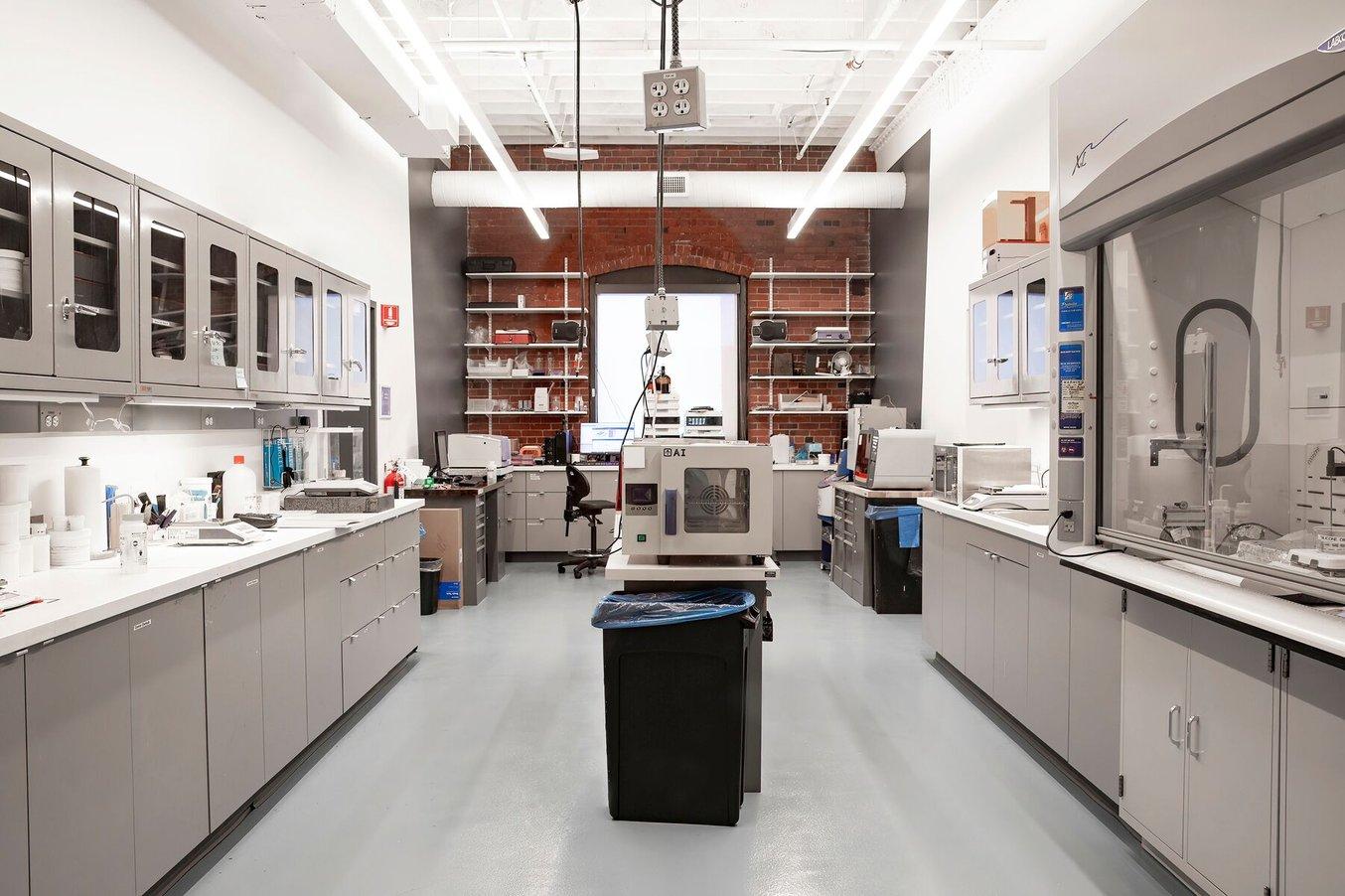
Controlling an Expanding Materials Supply Chain
Though innovation starts in the lab, it has to be carried throughout each stage of the manufacturing process to ensure that the mechanical properties we validate in our labs are the same ones our customers can rely on for their production. Our emphasis on quality and reliability doesn’t stop at our printers, it extends to the last drop of our materials. And doing this means we rely on our own quality standards and operational excellence in our materials manufacturing.
In fact, it’s why we made the rare decision to vertically integrate our business and buy one of the best materials manufacturing companies in the world to ensure that our materials meet our incredibly rigorous standards.
Formlabs Ohio
To that end, Formlabs acquired our longtime partner Spectra, bringing the production of our materials under one umbrella and streamlining the process from validation to distribution. Now part of Formlabs Ohio, the facility not only manufactures our materials, they also print thousands of parts each week for our sample program, and serve as one of the best use cases for mid- to high-volume production of 3D printed parts, in each of our 45+ materials.
“Most 3D printing companies are not vertically integrated and don’t have access to their own resin manufacturing, but we believe materials are critical components in opening up new applications, workflows and disrupting industries.”
Max Lobovsky, CEO and co-founder of Formlabs
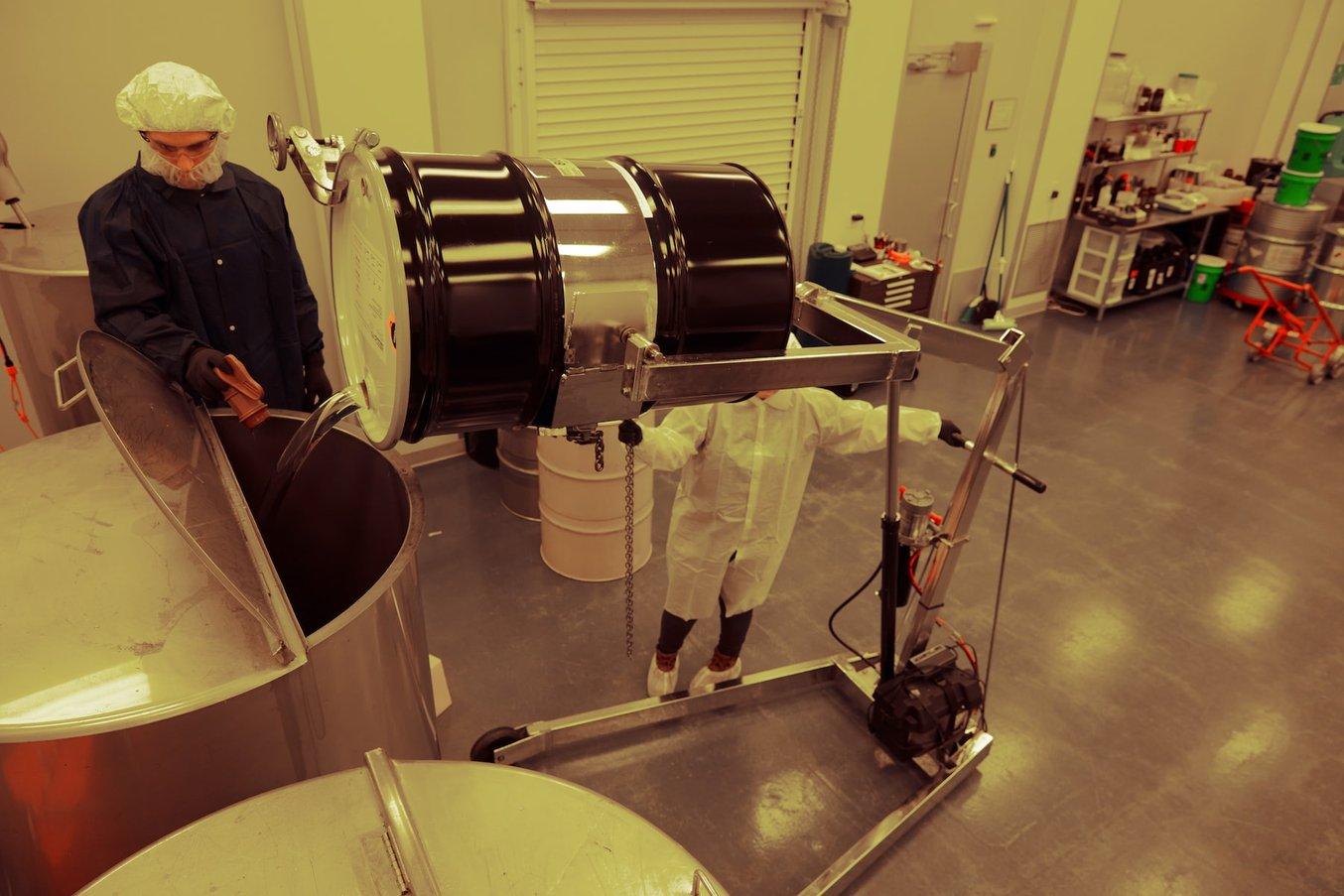
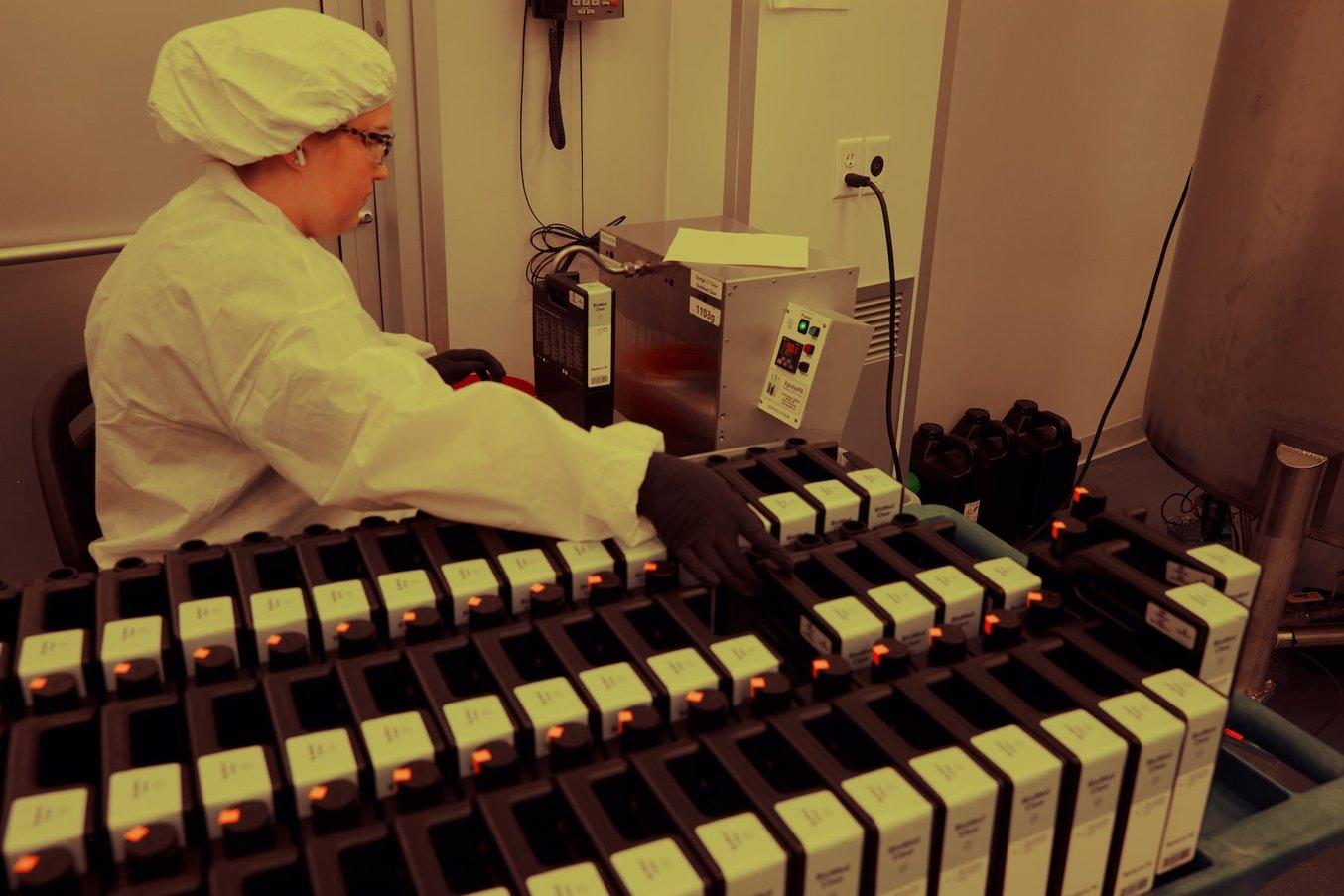
Some of those materials have specific requirements that have a real-life impact on end-use workflows. Our biocompatible materials have helped healthcare professionals for the last decade improve their standard of care by digitalizing their workflow. Resins approved for intraoral use, mucosal membrane exposure and contact, skin-safe applications, medium- to long-term implant applications, and end-use intraoral uses like surgical guides are all materials that are improving patient outcomes, bringing down costs for both provider and patient, and streamlining traditional workflows that often required days of manual labor.
Our biocompatible materials are produced in a completely regulated environment from start to finish so that our customers (and their patients) can feel secure in their workflow safety, health, and regulatory adherence. To consistently and safely produce these materials in high volumes, Formlabs invested time and effort into becoming a certified ISO 13485 facility for dental and medical materials development and developing an ISO Class 8-certified clean room for experimentation.
Formlabs’ efforts to build out the regulatory side of our materials production paid off during the COVID-19 pandemic. Thanks to a pre-approved and certified workflow, Formlabs, in collaboration with the University of South Florida and Northwell Health, was able to quickly pivot and begin mass-production of millions of nasopharyngeal swabs in response to the testing swab shortage faced across the country.
From the Source: Working With Experts for Specialized Formulations
As we add new materials and iterate on our existing materials, our team works closely with customers to identify new segments. This type of collaboration will only become more important as 3D printing becomes more widely adopted. For many, the affordable price of the hardware is not the barrier to entry — it’s the need for a specialized material.
Businesses that simply needed the design freedom or in-house fabrication of 3D printing have already integrated it; the businesses still waiting to begin are those that require high performance materials not currently available. As the entire industry looks to gain market share and attract new customers, Formlabs can rely on over a decade of proven workflows for identifying applications and working closely with experts to develop the perfect formulations.
With the latest materials such as Silicone 40A Resin and Alumina 4N Resin, as well as earlier releases like our polyurethane resins, Formlabs has a track record of creating specialized formulas for demanding industries and high performance applications. Our materials team researches extensively to determine which mechanical and aesthetic qualities are most important for our customers.
Adding Flexibility and Freedom
We put a lot of thought (and development work) into our proprietary resins, making them as reliable and effective as possible. But we know that some of our customers want as much freedom as possible to test new applications, find new routes to production, and more. That’s why we’ve also added new ways to make the Formlabs ecosystem as versatile as possible.
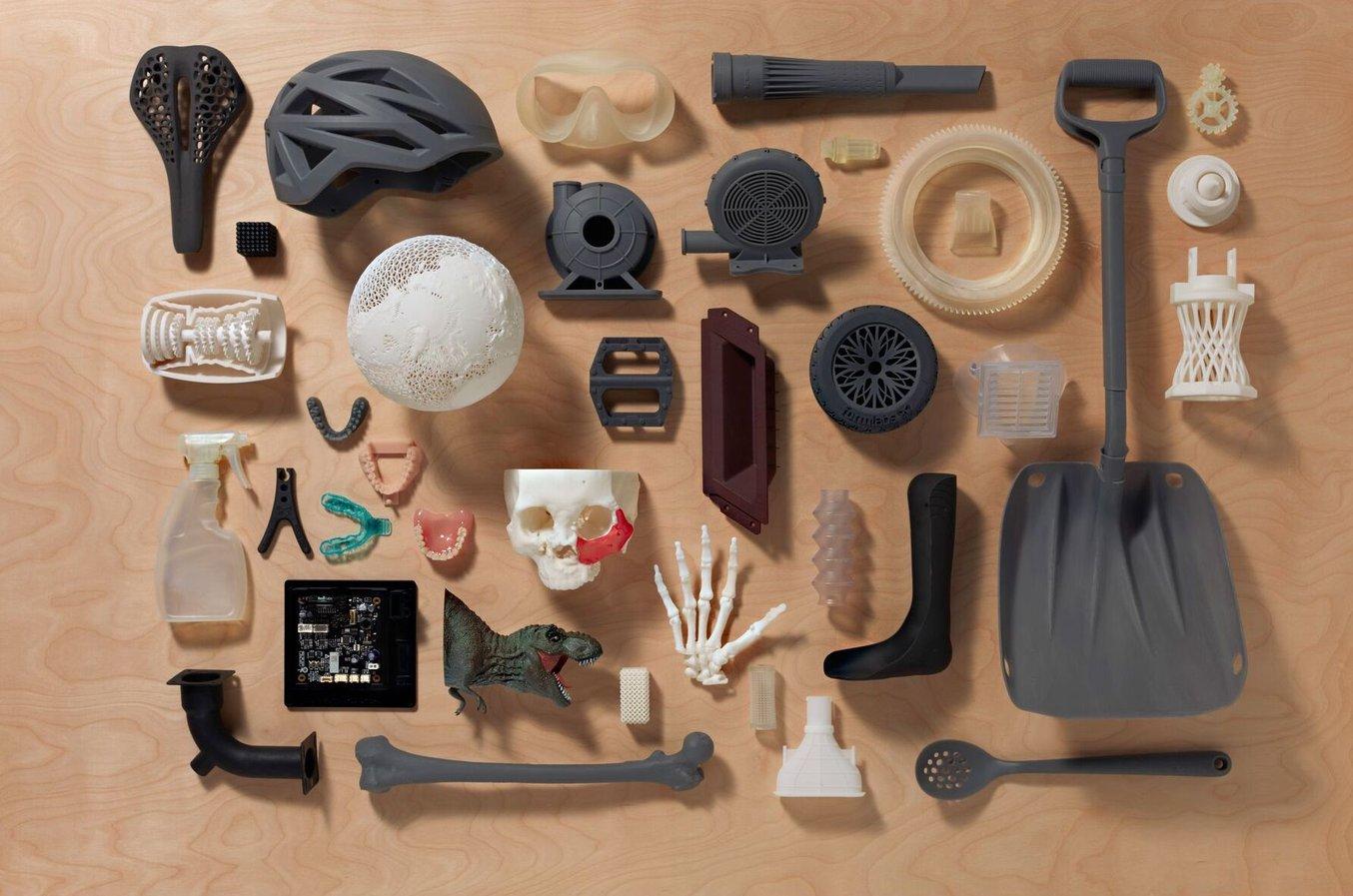
Recently, we did this by introducing Open Material Mode, a new way for Formlabs customers to expand their material options. Users can now personalize print settings to tailor performance and access a selection of curated, high-performance third-party resins from top-tier manufacturers. Open Material Mode unlocks the reliability of Formlabs' printers, enabling advanced users to print with any third-party 405 nm photopolymer resin. New materials available with Open Material Mode will suit unique requirements or tailored properties of specialized industries.
We’re incredibly proud of the materials we’ve developed, but we’re also excited to give even more freedom to our Formlabs community so they can take ownership of their own work.
Looking Forward
By focusing efforts and investment into developing new stereolithography (SLA) resins and selective laser sintering (SLS) powders, Formlabs has become the best-selling professional 3D printer manufacturer in the world. As the industry looks forward, we’re confident that continuing to expand material capability will be a driving force in the next industrial revolution.