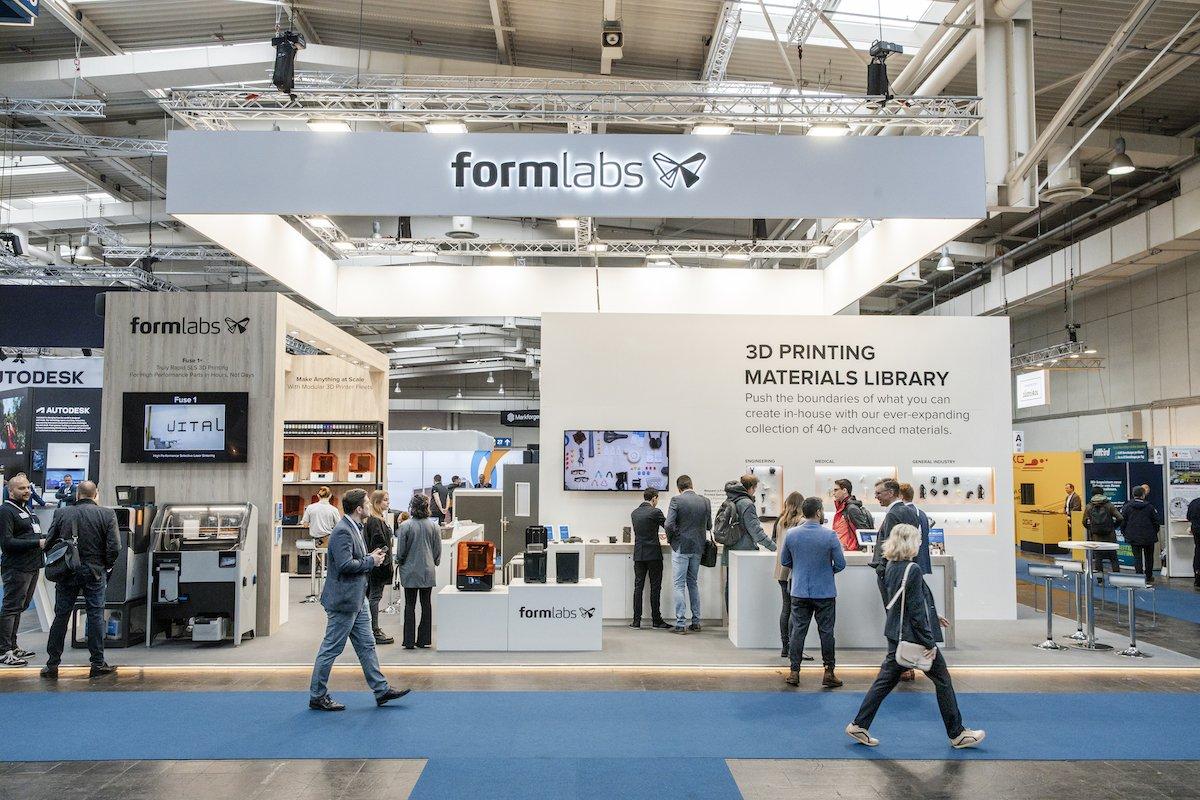
Though businesses have had to get comfortable with the realities of remote work, there are certain events that have proven the value of in-person interaction. Formnext is the premiere European additive manufacturing event, and every year serves as a locus for innovation and growth in our industry. There is no substitute for seeing the physical products that move our industry forward, testing new materials in action, and meeting fellow manufacturers and suppliers in person.
In previous years Formlabs has demonstrated printers that changed the AM paradigm, materials that unlock new 3D printing applications, and post-processing solutions that make workflows accessible. Over the past year, we’ve been hard at work, and with over 22 new products launched since the last Formnext event, we’ve got a lot to share. We'll also be launching exciting new hardware for our SLS line — to get a live demo, come see us in Booth E11 in Hall 11.1, or schedule time to speak with a member of our team.
The Automation Ecosystem
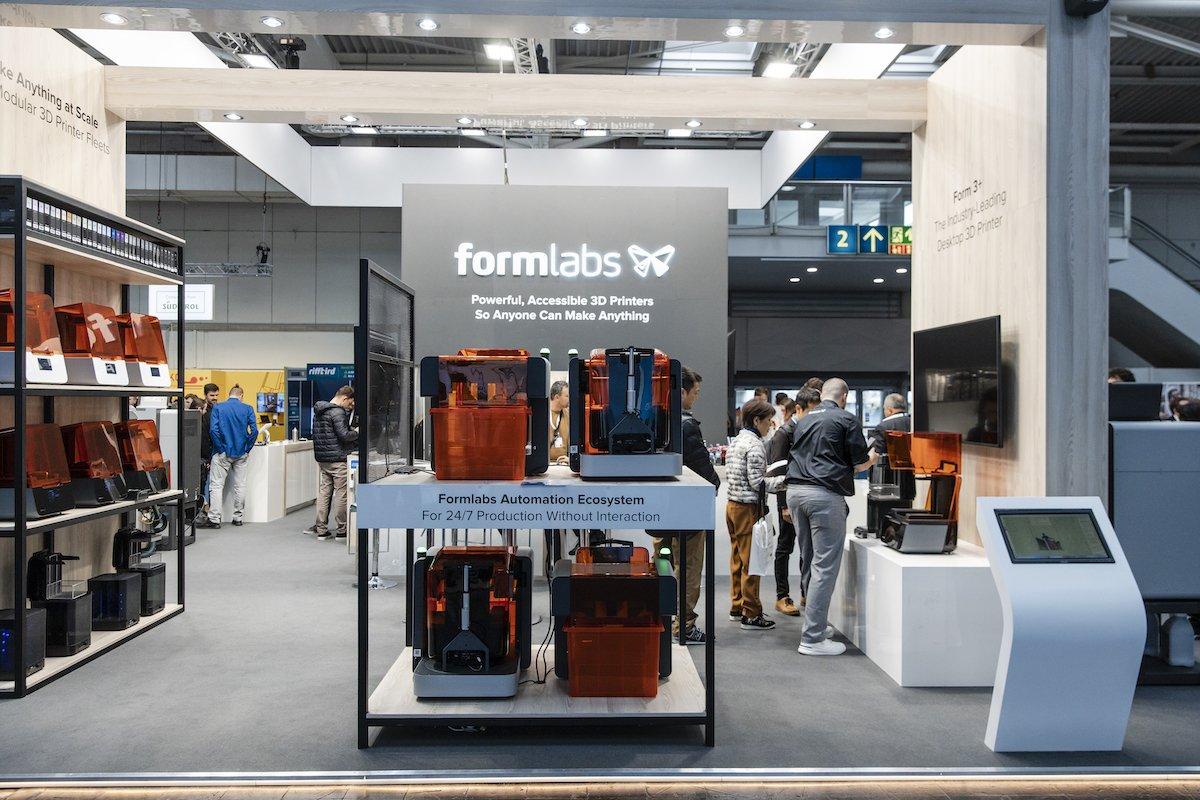
Additive manufacturing and automation are two trends pushing the manufacturing to grow in leaps and bounds, and together present enormous potential for increasing productivity, improving sustainability, and enabling new innovations in the way we make things.
The Formlabs Automation Ecosystem is comprised of a Formlabs SLA printer with Build Platform 2’s patented Quick Release Technology, the Form Auto hardware extension, and the High Volume Resin System. These components work together to nearly eliminate necessary printer interactions, freeing up users’ time for higher value tasks.
Formlabs user Mackart Additive, an engineering and manufacturing sub-contract facility based in Staffordshire, England that works with Formula 1 teams, touts the ability of the Form Auto to create a ‘third shift,’ of overnight part production. “With the Form Auto, you get that third and weekend shift going, and you don’t have to plan swapovers or any changes of build platforms. It runs nicely and it’s great for small components, and mid-size batch production runs of up to 1000 parts and beyond,” says Mackart Additive managing director and founder Steven McCarthy.
New Materials Capabilities Unlock Manufacturing Possibilities
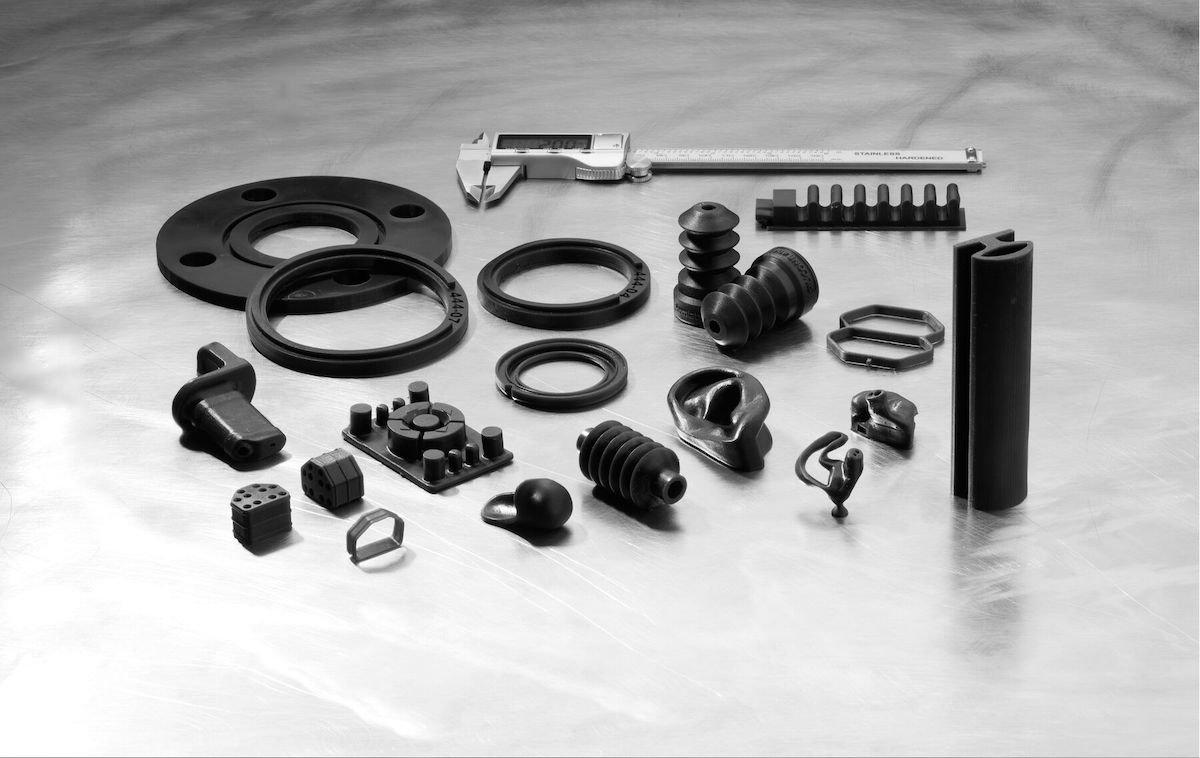
Though Formlabs has been at the forefront of hardware development for over a decade by bringing industrial power to an accessible price point with the Form Series SLA printers and Fuse Series SLS printers, our materials development team has matched the pace of innovation by developing over 40 proprietary materials and unlocking new applications for every industry.
With our two new SLA resin materials, Silicone 40A Resin and Alumina 4N Resin, we’re challenging the idea of what 3D printed parts can do.
Silicone 40A Resin is the first accessible pure silicone 3D printing material made possible by our patent-pending Pure Silicone Technology™, that combines the outstanding material properties of cast silicone with the benefits of 3D printing. Though pure silicone materials have existed for 3D printers for years, their exorbitant price or low-quality have limited the possibilities for functional prototypes or high-quality end-use parts. Silicone 40A Resin brings the accessibility and affordability that Formlabs is know for together with the reliability, consistency, and familiarity of pure silicone made through traditional methods. To test out the material properties for yourself, come try a free sample at our Formnext booth E11.
Technical ceramics are used everywhere in manufacturing and engineering. And though 3D printing is becoming nearly as ubiquitous, combining the two technologies has been all but impossible. With Alumina 4N Resin, Formlabs is introducing a 99.99% purity alumina material, opening doors to intuitive and cost-effect ceramic part production through 3D printing.
The United States Air Force Research Laboratory has been testing the new material by printing prototypes parts for turbine engines and materials research that are very difficult to make through traditional ceramic manufacturing techniques. Materials Research Engineer Benjamin Lam reported, “Alumina 4N Resin is remarkably easy to work with and plugs into our workflow seamlessly. It fits a need in the market, with a low barrier of entry that allows us to rapidly iterate on designs and produce parts at a comparably low cost.” Alumina 4N sample parts will be available at Formnext 2023 for you to bring home and temperature, pressure, and strength test yourself.
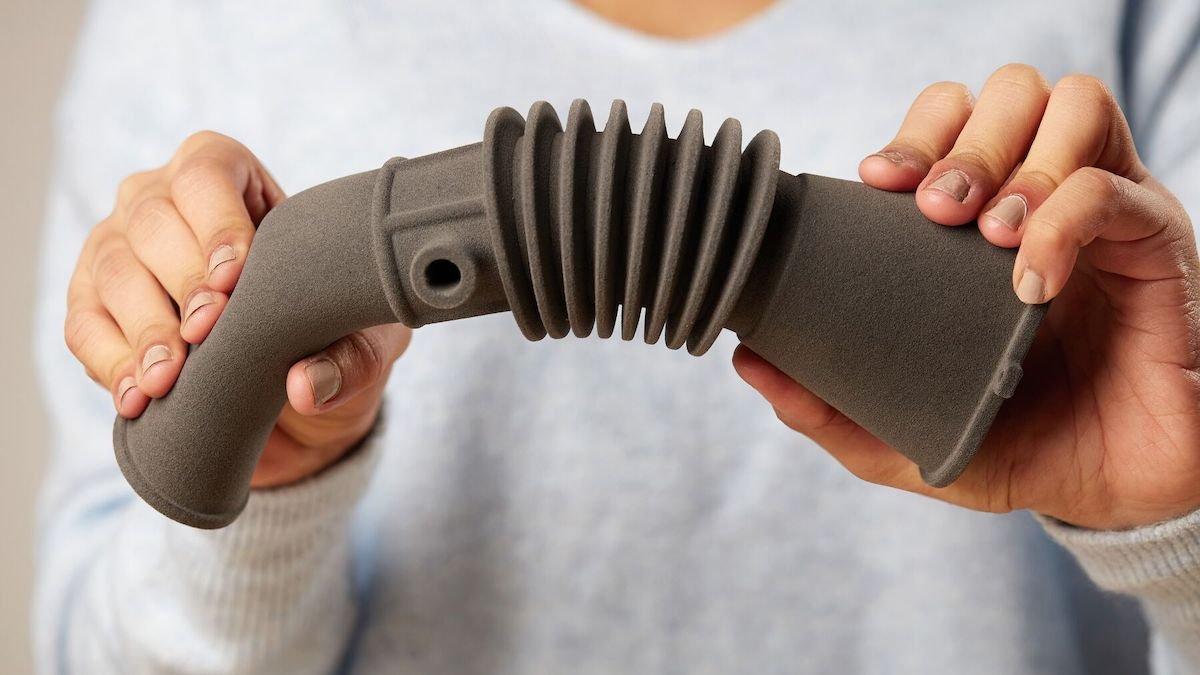
SLA resins haven't been the only big news since the last Formnext, however. We've released new SLS materials like TPU 90A Powder, our first flexible material for the Fuse Series SLS ecosystem. The Fuse 1+ 30W SLS printer was the first system to offer industrial power at an accessible price, and has been empowering Formlabs SLS customers to improve their design, engineering, and manufacturing workflows. It's versatility is only becoming more and more impactful as new, powerful materials become available.
TPU, or thermoplastic polyurethane, is one of the most commonly used elastomeric thermoplastics in the engineering, design, and manufacturing disciplines. This rubbery, durable material is everywhere: from sporting goods to medical devices, and the soles of the shoes on your feet.
There are proven workflows for the traditional manufacturing of TPU parts — and these workflows are still ideal for mass-produced rubber products. The advantages of printing TPU 90A Powder on the Fuse Series are found in the system’s ease of use for rapid prototyping, on-demand manufacturing aids, and customization possibilities. To try out TPU 90A Powder for yourself or speak to one of our SLS experts, visit our booth at Formnext.
Discuss Open Platform With Specialists
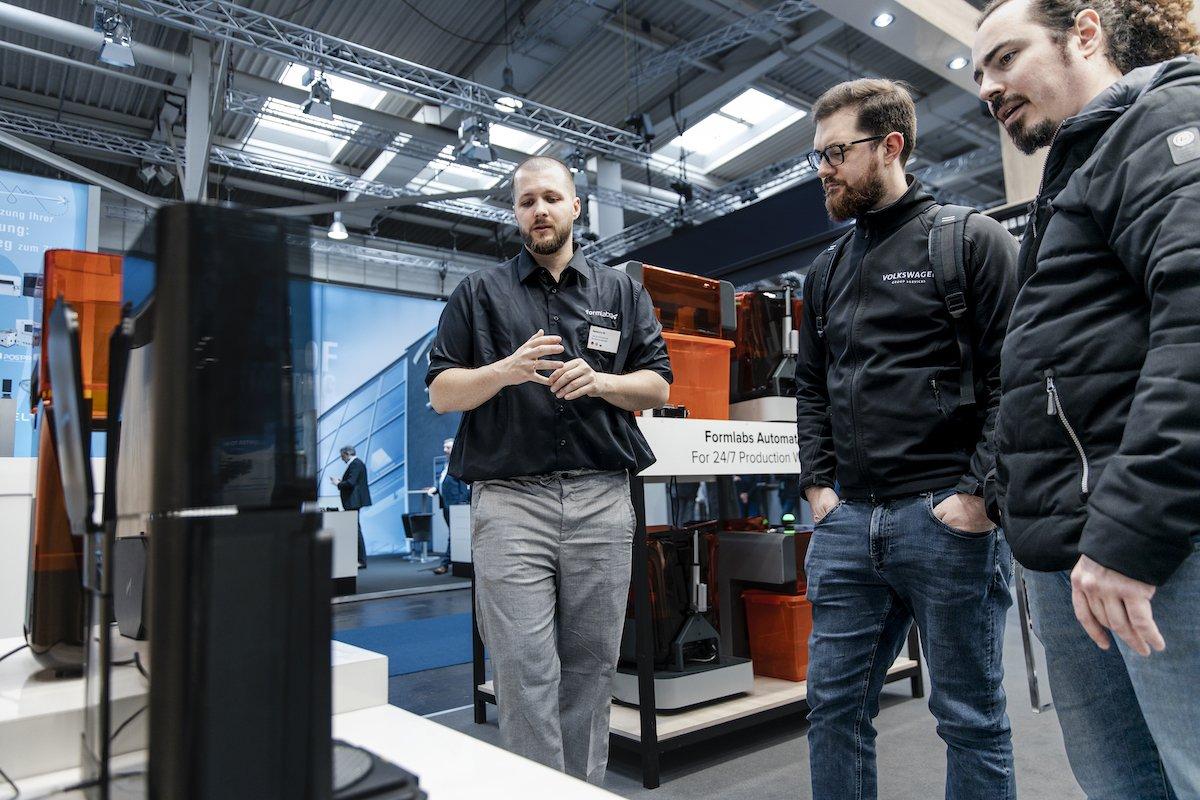
We’ve spent years honing our ecosystem of industry-leading 3D printers and materials that enable engineers, designers, and manufacturers to achieve the highest quality parts possible. We know that our intrepid customers are capable of even more when given the right tools and support.
To support our customers that want to further push the boundaries of what our printers and resins can do, we introduced Open Platform. With new features, users can have more control over print settings, try other manufacturers’ materials, and experiment with new print parameters to dial in your parts, your way. If you’re not sure that Open Platform will deliver value for you, our experts can walk you through how it works and its potential benefits for your workflow at the Formnext booth.
Deep Dive With Our Experts Across Industries
Events like Formnext aren’t just about evaluating new technologies, they’re also about learning how others are leveraging those technologies and integrating them into their workflows. At our booth we’ll be hosting several presentations from leading experts across many of the industries 3D printing can revolutionize (if it hasn’t already).
From subject-matter experts like Formlabs Materials Lead Sharon Soong to 3D printing media moguls like 3D Printing Nerd, our presentations aim to go deeper into the biggest trends in the industry and where Formlabs fits in.
Soong’s presentation will detail the work that Formlabs does to explore the boundaries of polymer science and develop resins and powders that help our customers create better solutions to the problems they face. Other presentations will cover the advantages and workflow for ceramic coating of 3D printed parts, as well as how to successfully investment cast with 3D printed rapid tooling. These workflow-centered demonstrations aim to help our customers expand what they can do with the tools we manufacture, and show that beyond best-in-class 3D printers, we support them through every step in their process.
Two exciting customer-led presentations include Hunt Bike Wheels and Deutsche Bahn GmBH. From Hunt Bike Wheels, we’ll learn how large-format resin 3D printing with the Form 3L has enabled them to ride to the front of trends in bike development for commuters, athletes, and leisure-riders. By shortening the iterative loop with in-house 3D printing, Hunt Bike Wheels engineers have been able to iterate and test almost daily, and they’ll walk us through their functional testing workflow and how they’ve dialed in their Form 3L to become a team-favorite tool in their making process.
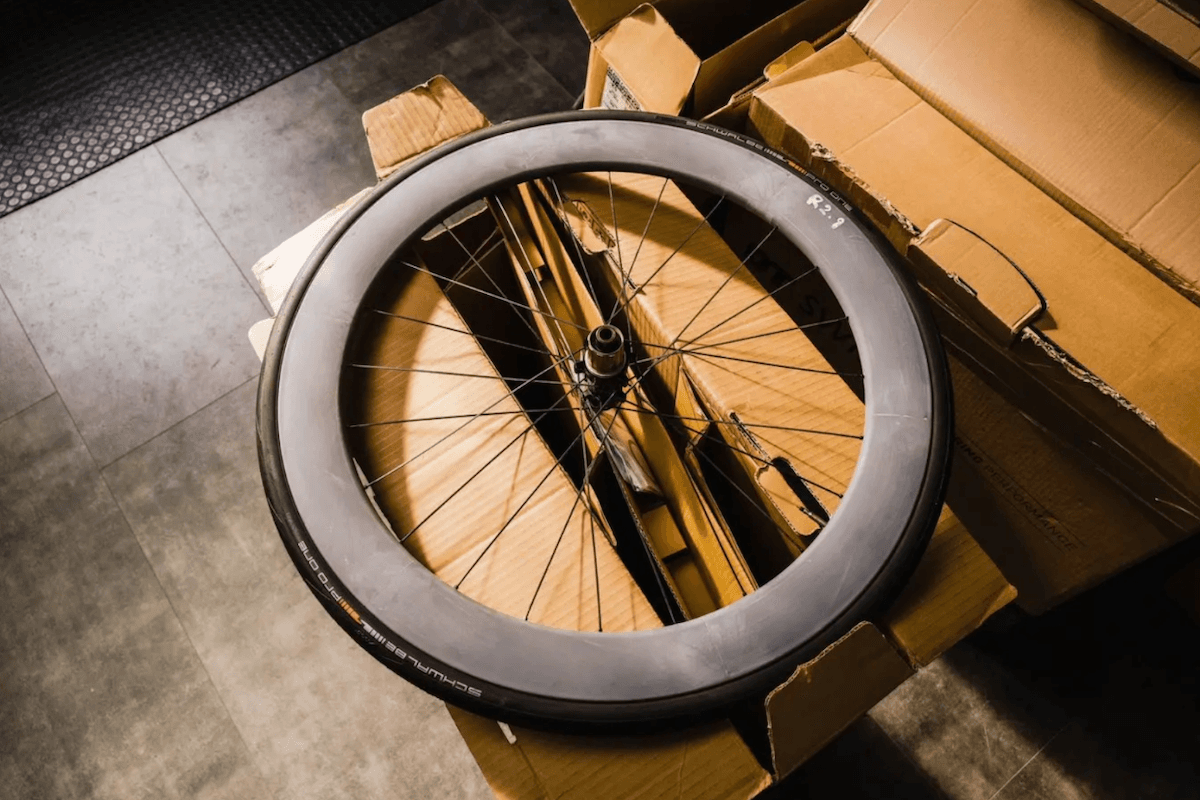
From Deutsche Bahn, giant of the European railway system, the focus will be less on product development and more on how 3D printing has improved their ongoing maintenance operations. As large manufacturers are starting to catch on that 3D printing is no longer just a prototyping tool, but an essential part of manufacturing at every stage, presentations like these are integral in sharing information and spreading knowledge from the best in the business.
Meet Us At Formnext
With new materials that have to be seen, felt, and tested to be believed, we know that Formnext is the place to be. 3D printing users across every industry are engaged, hungry to learn, and communicative about what they need from manufacturers. Formnext is the forum to learn from each other, see what’s new, and share insights and knowledge about your specific workflow.
We can’t wait to hear from experts both in our booth and on the main stage, and get a chance to share what we’ve been working so hard on since last year. Visit us at Booth E11 in Hall 11.1 or schedule a time to meet with an expert.