The design and fabrication of musical instruments are where technology and art can truly work together to create something beautiful. At S-Mute, Nathan Sobieralski has fused 3D printing with his extensive background in the world of classical trumpet to build a successful, fast-growing, one-man manufacturing company.
With the help of the Fuse Series selective laser sintering (SLS) ecosystem, Sobieralski developed innovative new trumpet and trombone mutes, and started producing them at scale. He’s built up a strong customer base and an agile manufacturing platform, all as a single designer, operator, and fulfillment team.
“I’ve always been interested in product design and production engineering. What’s amazing about the age we live in is that I had an idea, and now I’m holding it in my hands! The Fuse Series ecosystem is really great at producing professional stuff.”
Nathan Sobieralski, Owner, S-Mute
Playing, Pivoting, Product Engineering
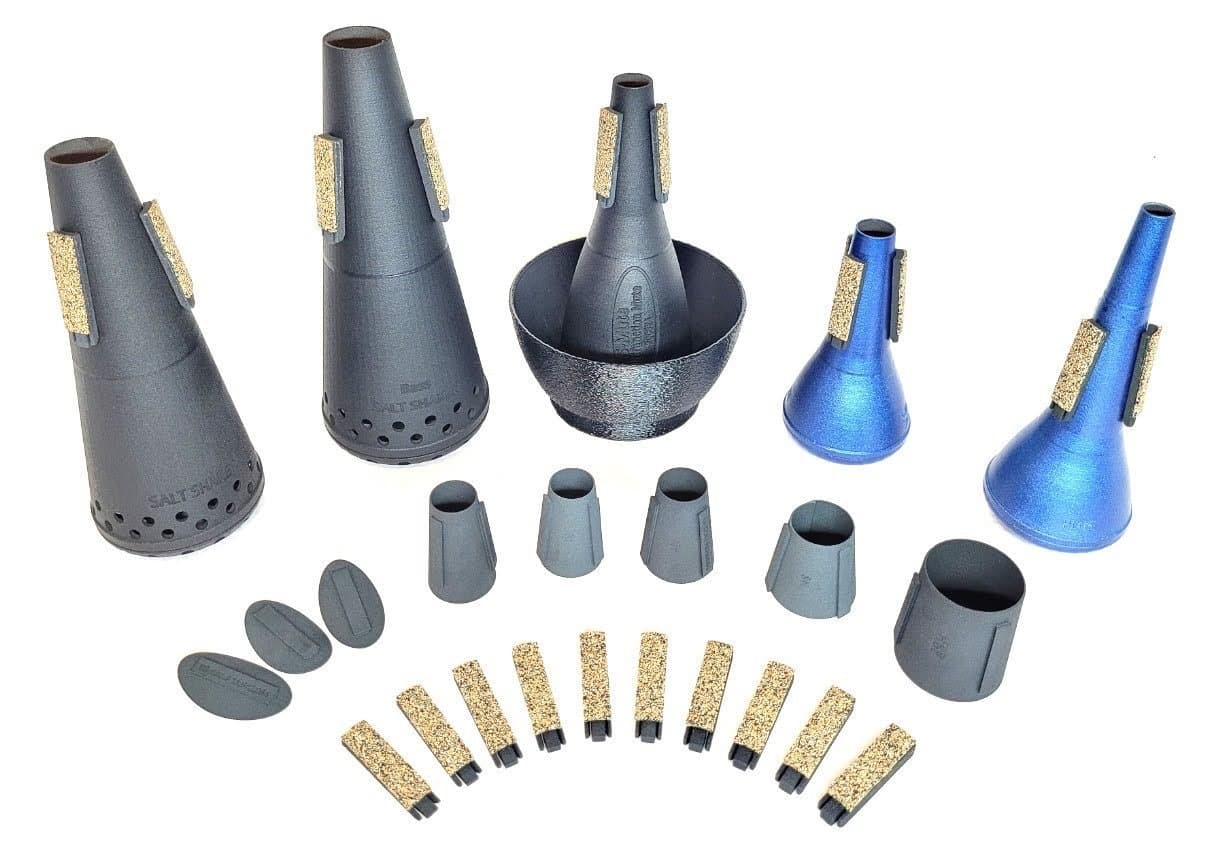
Sobieralski has built up an extensive product catalog, and SLS 3D printing has enabled him to batch produce the thousands of individual components necessary to keep up with growing demand.
Sobieralski has been playing trumpet since childhood and has the doctorate degree to prove it. Mastering the art and expanding access to it are two of his great passions — he’s a Professor of Trumpet at California State University, Fresno and plays in both the Fresno Philharmonic and the Sequoia Symphony.
Though his interests and career have been focused on the artistry of musical performance, he’s always had an interest in how things are made, how they’re put together, and ways to improve upon existing designs. Like many great engineering ideas, S-Mute started out as an inefficiency impacting Sobieralski’s day-to-day life.
When playing a brass instrument, you sometimes have to use a mute, a device inserted into the bell that alters the sound — but that can also change the tuning or pitch in an undesirable way. To fix this problem of tuning, brass instrument players would manually alter the thickness of the corks on the mute to change the depth of the mute within the bell of the instrument, and thereby its pitch. Until S-Mute, players would file down the cork and hope for the best that the deeper position of the mute had the right effect. Too often, they would find their estimation wrong, and would have to restart this process from the beginning with new corks.
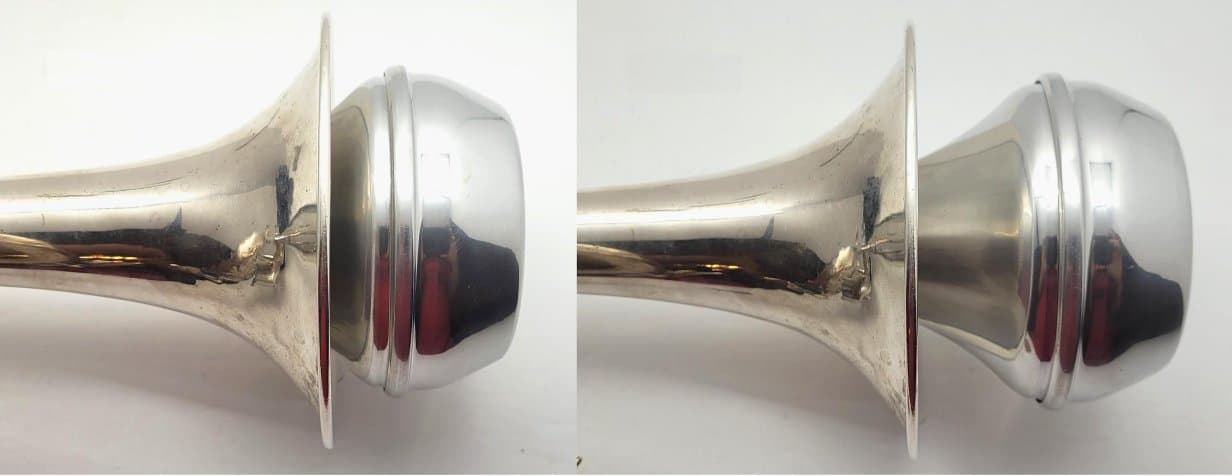
Mutes are devices inserted into the bells of brass instruments that alter the sound they produce, but they can often negatively impact the tuning or pitch if they are inserted to the incorrect depth.
“So, my idea for a long time was, ‘it would be great if we could just pop these off and pop on different thicknesses, and be able to make exact adjustments as needed, without having to whittle down new corks,” says Sobieralski. And so a new product, and product engineer, was born.
Developing Early Stage Designs
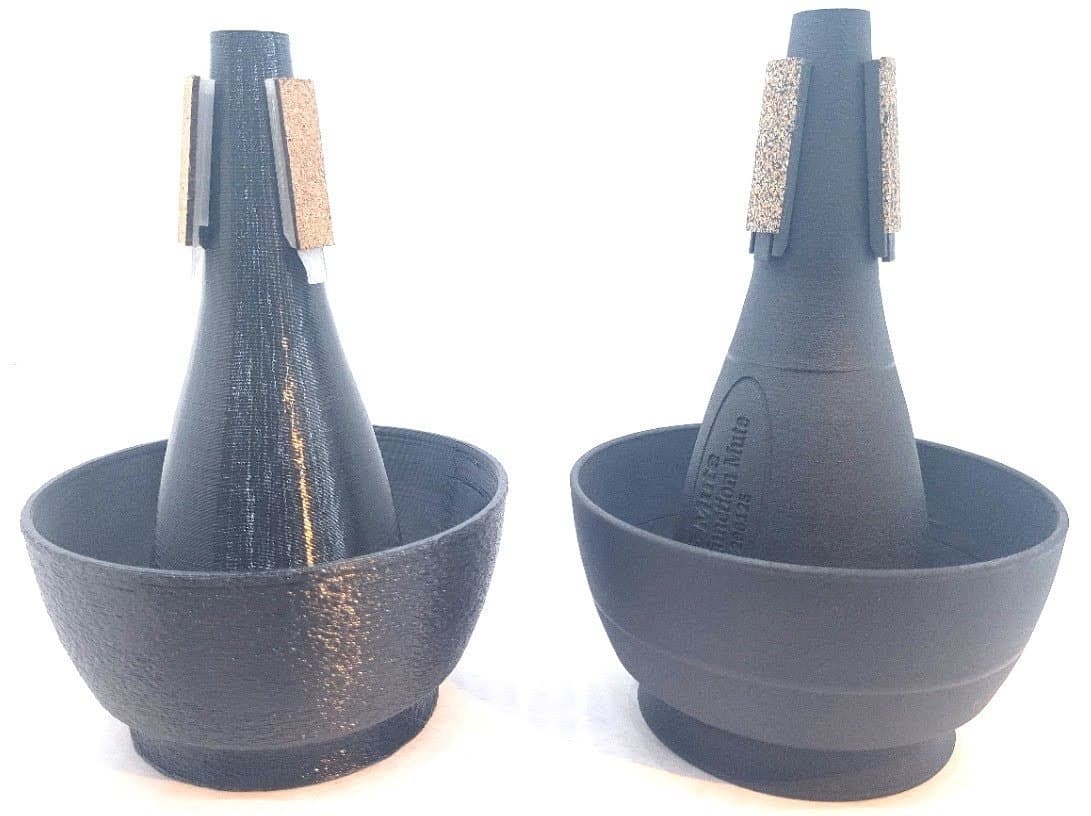
Sobieralski’s first designs were printed on an FDM 3D printer (left), which required extensive post-processing. His SLS 3D printed mutes (right) provided the design freedom and dimensional accuracy he needed, without obvious layer lines to sand away.
Sobieralski had CAD experience, so he started testing some early designs on a fused deposition modeling (FDM) printer he had originally bought for his son during the pandemic. Other people in the brass instrument industry had tried 3D printing mutes, the vast majority using inexpensive FDM printers, but no one had come up with the modular, innovative approach that Sobieralski could envision.
“I came up with a system that seemed to work pretty well, and within a year of starting, I was granted a patent. Since then, we’ve been producing end-use mutes, first with entry-level FDM, then a big Core XY FDM system, and now with SLS and the Fuse,” says Sobieralski.
Inexpensive and well-known even among 3D printing newcomers, FDM was an easy way for Sobieralski to prototype and get his initial concepts in front of other players. But soon the lack of consistency became an impediment as S-Mute grew quickly and higher volume production runs were necessary. “It was a lot of me tweaking firmware and doing stuff to get it dialed in. I know you can make FDM work, but I spent a lot of time tinkering around and doing a lot of post-processing, even with the more expensive system,” says Sobieralski.
Mutes are professional tools used by musicians during performances in a range of environments, including symphonic performances and other very formal settings. Every piece of the instrument needs to look professional and blend into the symphonic experience. The FDM printed mutes were doing the job, but Sobieralski had spent too much time ensuring they worked well and looked good, despite variances in filament or manufacturer. “I’d get different-looking batches, and deal with water getting into them, and the consistency was really bad. They were slow to make and had to be flat to print on the print bed,” says Sobieralski.
SLS and the Freedom to Innovate
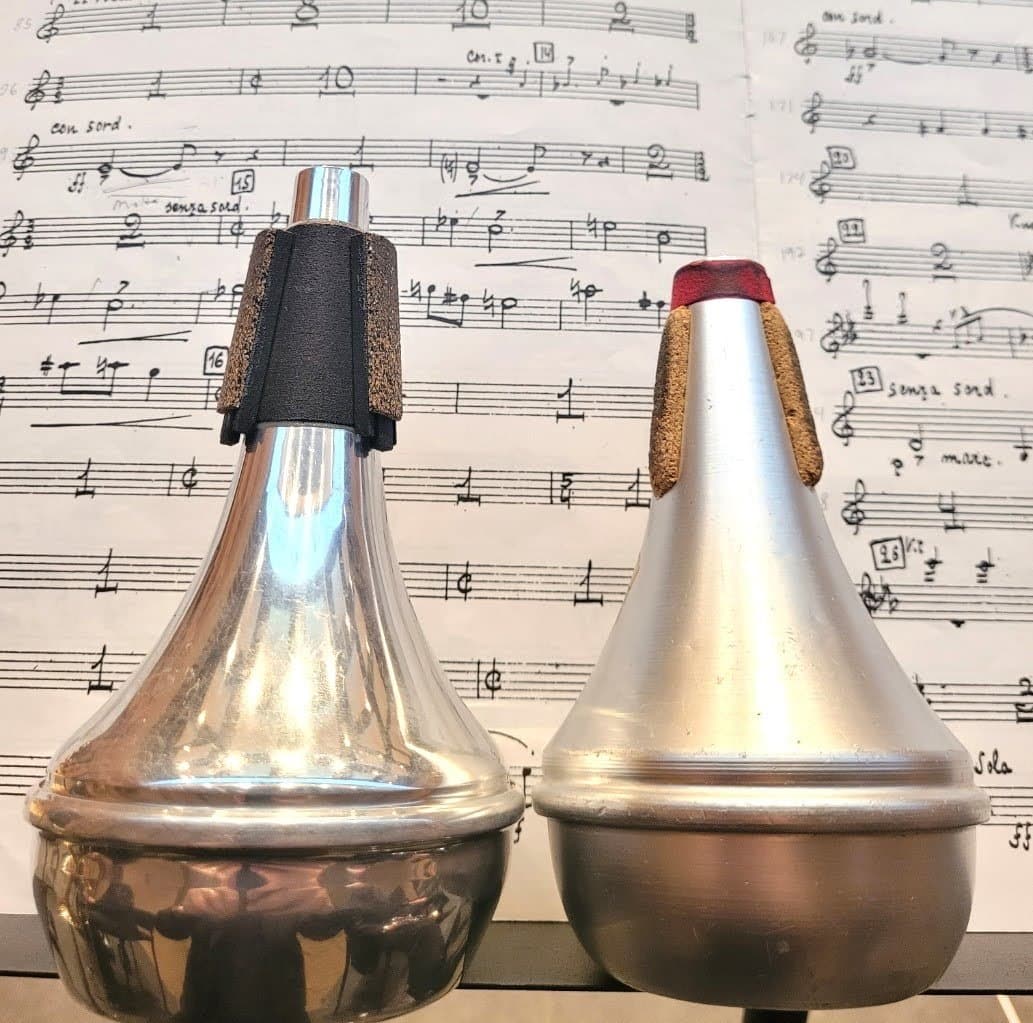
On the left is a traditional mute with an SLS printed removable cork adapter installed. On the right is a traditional mute with its non-removable factory corks in poor condition.
As he looked into other 3D printing solutions, one advantage of SLS caught his eye; the self-supporting nature of the powder bed made it possible to print organic, curved shapes like the inside of the bell of a trumpet.
“I learned about SLS — and that you could print any shape, any geometry whatsoever, within this medium. I saw how it worked, and the material you’d have to use… What struck me about Formlabs was that it was a very well thought-out workflow. One of my hesitations was about dealing with powder, but with the Sift it seemed like the most logical solution.”
Nathan Sobieralski, Owner, S-Mute
The Fuse Series, though an accessible option when compared to traditional powder bed fusion 3D printers, was not an easy decision for Sobieralski to make. His business was just getting off the ground, and everything would be a personal investment. However, after receiving samples and getting a business loan, Sobieralski installed his first Fuse Series printer and Fuse Sift at his residential address in 2022.
Though the workflow is more complex than an average FDM print, Sobieralski leaned on the Formlabs Services team for onboarding and optimization.
“Service is outstanding. Any issues I've encountered have been addressed swiftly and effectively. In my experience, the team goes above and beyond, doing everything they can to resolve the problem—even when an immediate solution isn't available. I can’t praise the service team enough; they are truly outstanding.”
Nathan Sobieralski, Owner, S-Mute
Scaling to Production Volumes With Fuse
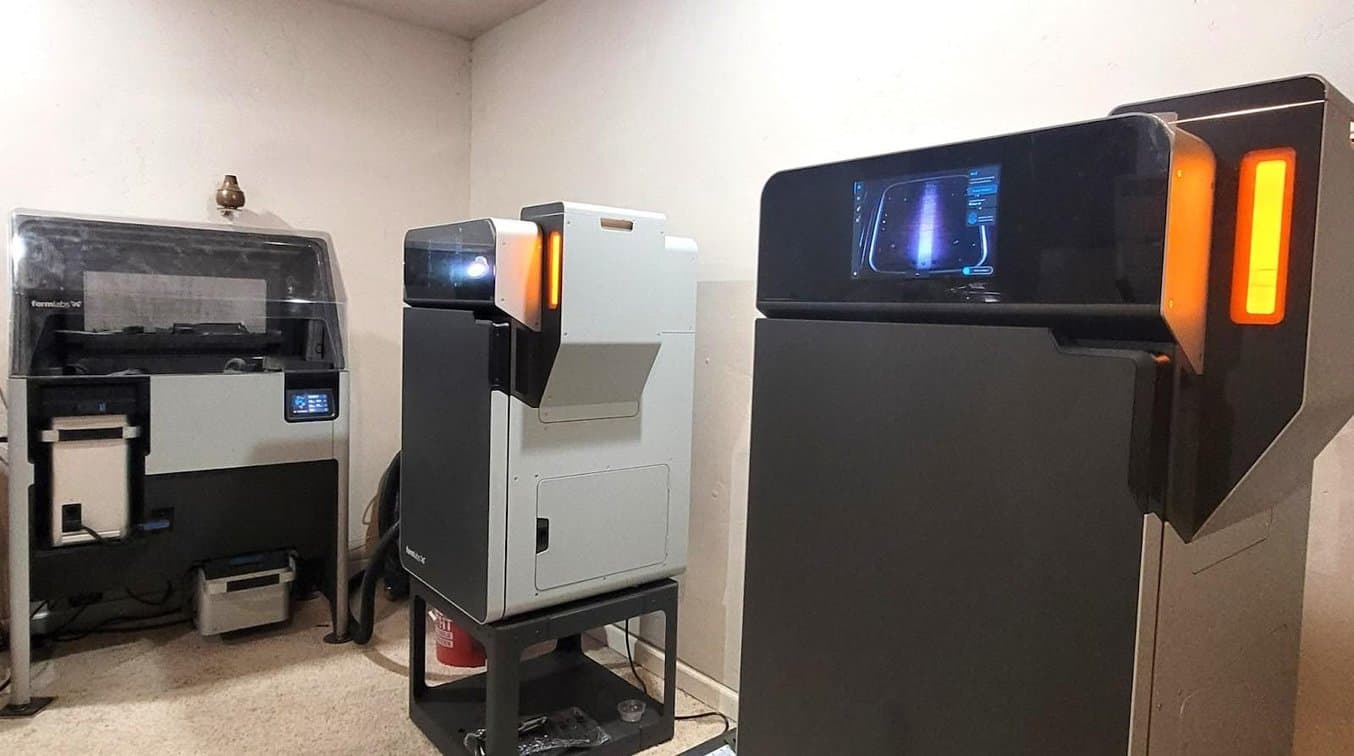
The compact size of the Fuse Series ecosystem means that Sobieralski could get a fully operational manufacturing facility up and running without investing heavily into an existing manufacturing facility.
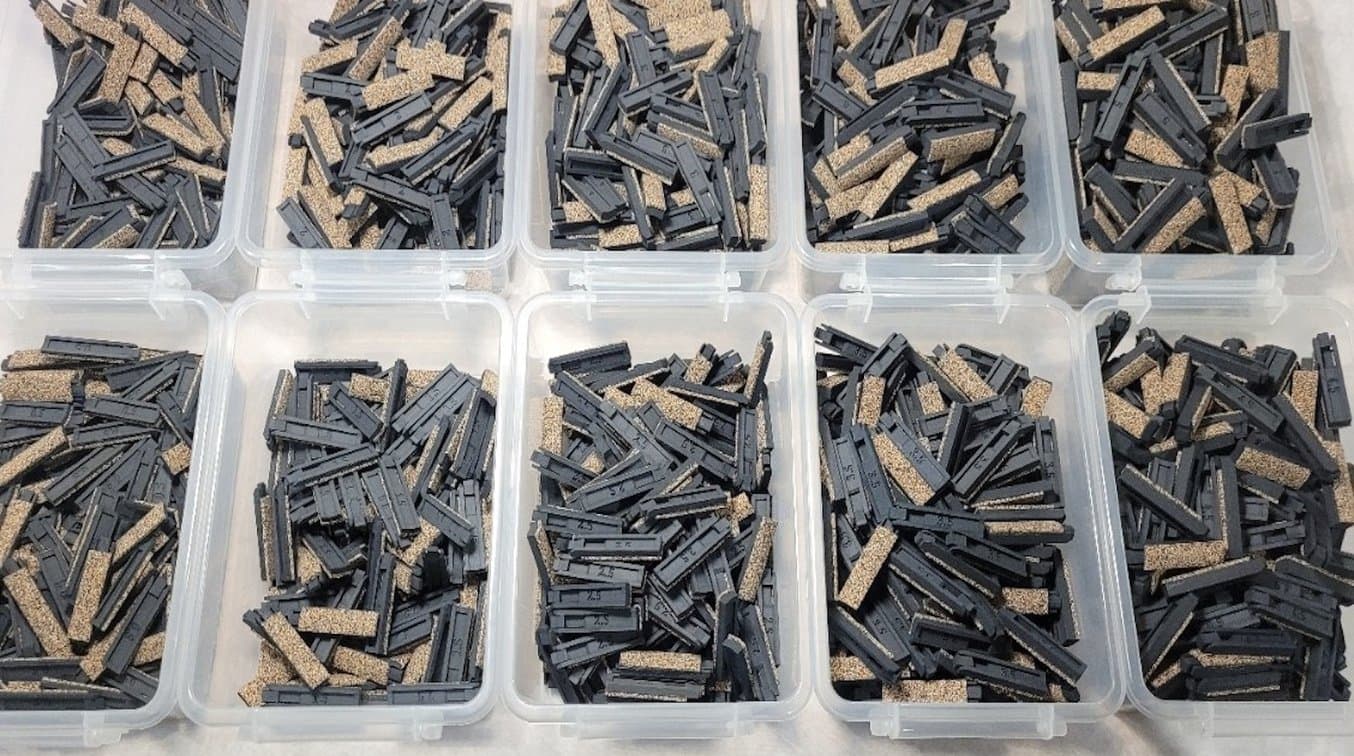
The Fuse Series Ecosystem makes it possible to batch produce thousands of end-use parts each week, with no additional employees and the accompanying labor costs.
As Sobieralski’s design became more well-known in his community and the global brass instrument industry, he learned how to optimize his Fuse workflow. Printing both the mute shell and the cork pieces means his products are functional fit assemblies and have to fit easily together. “When I sell a mute, they can buy up to 10 different cork thicknesses, and there’s three corks per thickness, so that’s where a lot of my volume comes from. I’m printing 1,600 of these corks at a time,” says Sobieralski.
In 2024, the volume and increasing demand warranted an additional investment — he added a second Fuse Series printer, completely bootstrapped by his success so far. Sobieralski has expanded into trombone mute design as well. “That’s starting to take off, and I’m making a lot of trombone mutes. As far as serious volume, I can make 40 of those mutes in two full-build chambers.”
PreForm's array and packing features make it easy to batch produce parts and use powder as efficiently as possible.
The tight tolerances and high accuracy possible on the Fuse Series make it easy to print interlocking parts and slide features like this.
Even with two printers running it’s still a one-man operation. The Fuse Series workflow makes it possible to be a one-man factory, fulfillment provider, advertising group, and sales team. On a recent Formlabs Forum review, Sobieralski said it best, “I am not a large corporation with a massive R&D budget and tons of employees, my requirement is for the machines to be efficient and produce quality parts with minimal downtime. Formlabs has delivered on this requirement for me.”
To learn more about the Fuse Series Ecosystem, visit our page. To test a material for yourself, request a free 3D printed sample.