
Selective laser sintering (SLS) 3D printing is trusted by engineers and manufacturers across different industries for its ability to produce strong, functional parts.
In this extensive guide, we’ll cover the selective laser sintering process, the different systems and materials available on the market, the workflow for using SLS printers, the various applications, and when to consider using SLS 3D printing over other additive and traditional manufacturing methods.
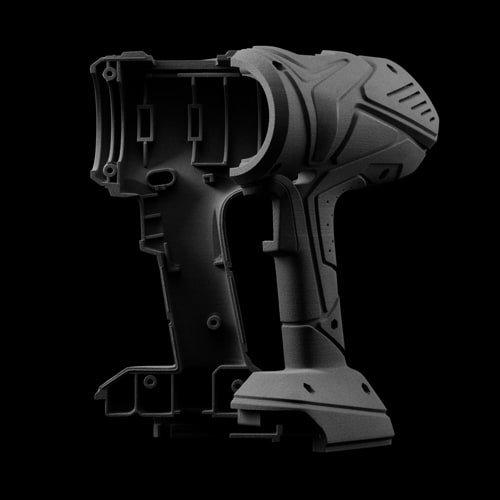
Introduction to Selective Laser Sintering (SLS) 3D Printing
Looking for a 3D printer to create strong, functional parts? Download our white paper to learn how SLS printing works and why it's a popular 3D printing process for functional prototyping and end-use production.
What is Selective Laser Sintering 3D Printing?
Selective laser sintering is an additive manufacturing (AM) technology that uses a high-power laser to sinter small particles of polymer powder into a solid structure based on a 3D model.
SLS 3D printing has been a popular choice for engineers and manufacturers for decades. Low cost per part, high productivity, and established materials make the technology ideal for a range of applications from rapid prototyping to small-batch, bridge, or custom manufacturing.
Recent advances in machinery, materials, and software have made SLS printing accessible to a wider range of businesses, enabling more and more companies to use these tools that were previously limited to a few high-tech industries.
Introducing the Formlabs Fuse Series SLS 3D printers, bringing high-performance SLS 3D printing finally within reach.
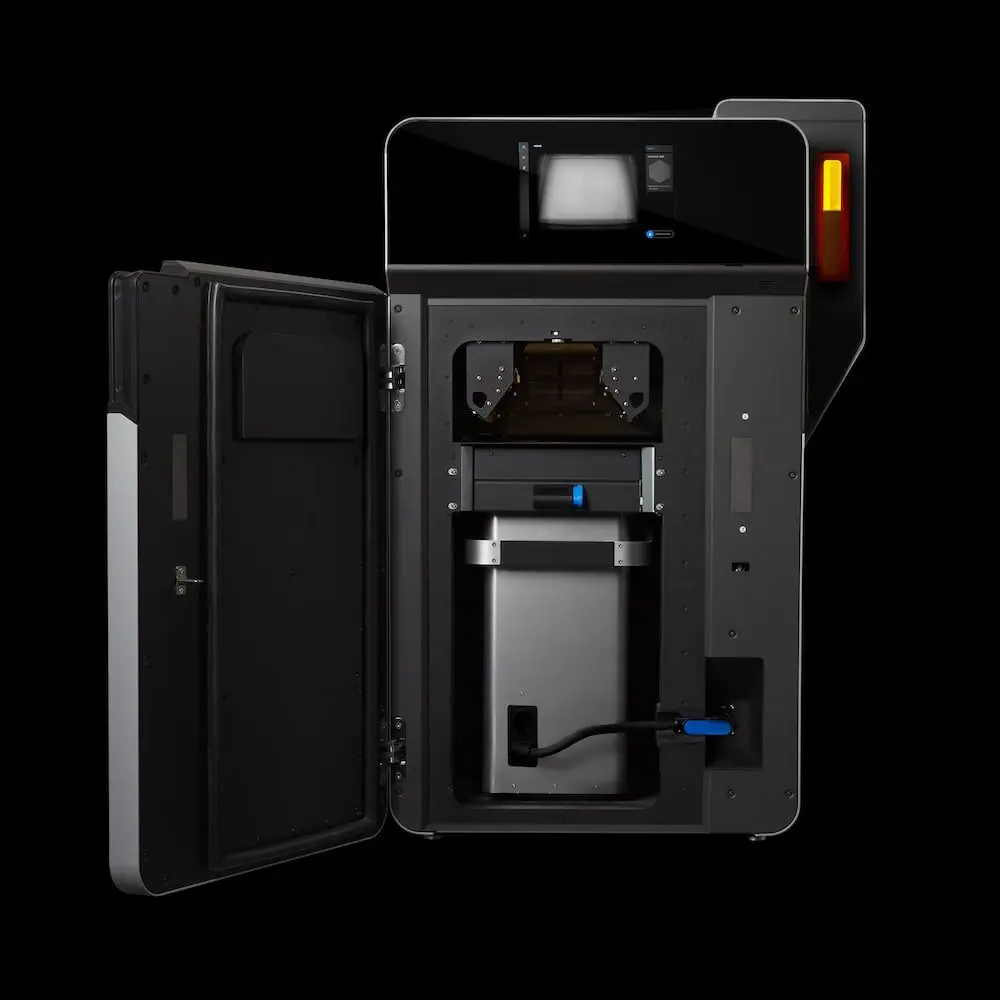
Rapid SLS Production of High Performance Parts with the New Fuse 1+ 30W
Watch our product demo for a walkthrough of the Fuse 1+ 30W and SLS 3D printing with Formlabs experts.
How SLS 3D Printing Works
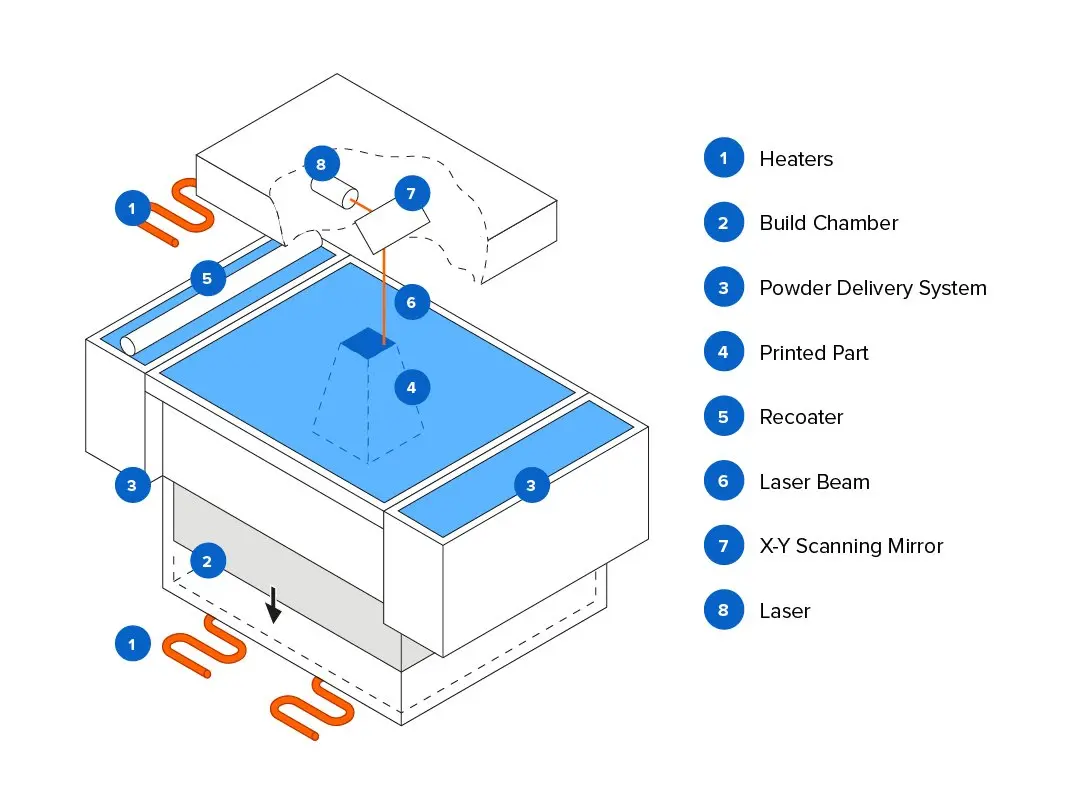
Schematic of the selective laser sintering process. SLS 3D printing uses a high-power laser to sinter small particles of polymer powder into a solid structure based on a 3D model.
-
Printing: The powder is dispersed in a thin layer on top of a platform inside of the build chamber. The printer preheats the powder to a temperature somewhat below the melting point of the raw material, which makes it easier for the laser to raise the temperature of specific regions of the powder bed as it traces the model to solidify a part. The laser scans a cross-section of the 3D model, heating the powder to just below or right at the melting point of the material. This fuses the particles together mechanically to create one solid part. The unfused powder supports the part during printing and eliminates the need for dedicated support structures. The platform then lowers by one layer into the build chamber, typically between 50 to 200 microns, and the process repeats for each layer until parts are complete.
-
Cooling: After printing, the build chamber needs to slightly cool down inside the print enclosure and then outside the printer to ensure optimal mechanical properties and avoid warping in parts.
-
Post-processing: The finished parts need to be removed from the build chamber, separated, and cleaned of excess powder. The powder can be recycled and the printed parts can be further post-processed by media blasting or media tumbling.
For the detailed workflow, see the “SLS 3D Printing Workflow” section below.
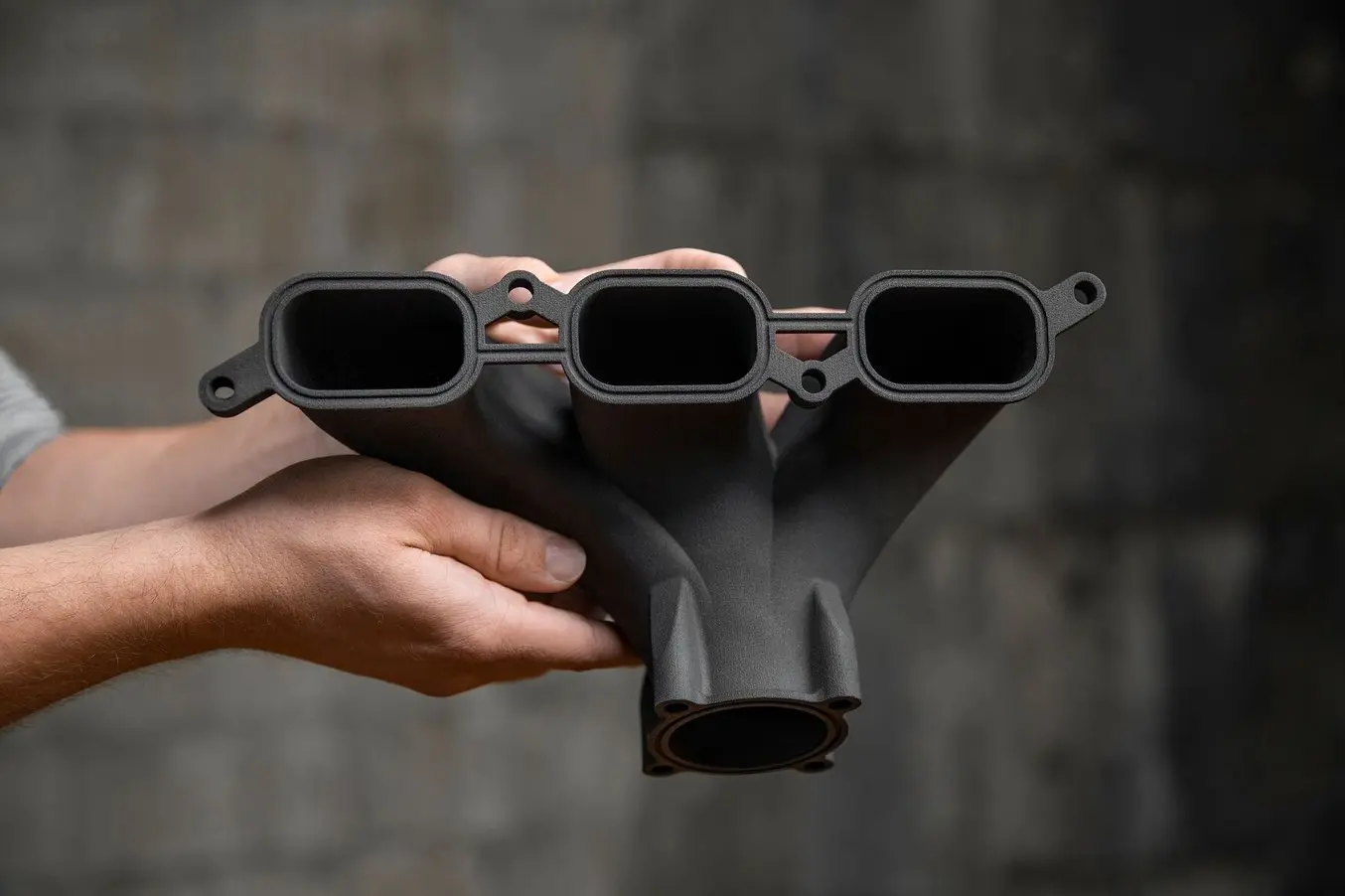
SLS parts have a slightly grainy surface finish, but almost no visible layer lines. Media blasting or media tumbling SLS parts is recommended for a smoother surface finish. This example part was printed on a Formlabs Fuse 1+ 30W benchtop industrial SLS 3D printer.
As the unfused powder supports the part during printing, there’s no need for dedicated support structures. This makes SLS ideal for complex geometries, including interior features, undercuts, thin walls, and negative features.
Parts produced with SLS 3D printing have excellent mechanical characteristics, with strength resembling injection molded parts.
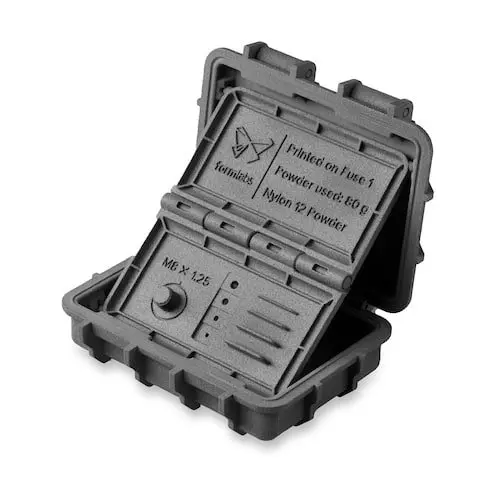
Request a Free SLS Sample Part
See and feel Formlabs quality firsthand. We’ll ship a free SLS sample part printed on the Fuse 1+ 30W to your office.
A Brief History of SLS 3D Printing
Selective laser sintering was one of the first additive manufacturing techniques, developed in the mid-1980s by Dr. Carl Deckard and Dr. Joe Beaman at the University of Texas at Austin. Their method has since been adapted to work with a range of materials, including plastics, metals, glass, ceramics, and various composite material powders. Today, these technologies are collectively categorized as powder bed fusion — additive manufacturing processes in which thermal energy selectively fuses regions of a powder bed.
The two most common powder bed fusion 3D printing systems today are plastic-based, commonly referred to as SLS, and metal-based, known as direct metal laser sintering (DMLS) or selective laser melting (SLM). Until recently, both plastic and metal powder bed fusion systems have been prohibitively expensive and complex, limiting their use to small quantities of high-value or custom parts, such as aerospace components or medical devices.
Innovation in the field has surged recently, and plastic-based SLS is now poised to follow other 3D printing technologies like stereolithography (SLA) and fused deposition modeling (FDM) to gain widespread adoption with accessible, compact systems.
Types of SLS 3D Printers
All selective laser sintering 3D printers are built around the process described in the previous section. The main differentiators are the type of laser, the size of the build volume, and the complexity of the system. Different machines use different solutions for temperature control, powder dispensing, and layer deposition.
Selective laser sintering requires a high level of precision and tight control throughout the printing process. The temperature of the powder along with the (incomplete) parts must be controlled within 2 °C during the three stages of preheating, sintering, and storing before removal to minimize warping, stresses, and heat-induced distortion.
Traditional Industrial SLS 3D Printers
Selective laser sintering has been one of the most popular 3D printing technologies for professionals for decades, but its complexity, requirements, and high price have limited its use to service bureaus and large enterprises.
These machines require special HVAC and industrial power, and even the smallest industrial machines take up at least 10 m² of installation space. Setting them up takes multiple days with on-site installation and training. The complex workflow and the steep learning curve also mean that these systems require a skilled technician in-house to operate and maintain.
With a starting price of around $200,000 that goes well beyond that for complete solutions, traditional industrial SLS has been inaccessible for many businesses.
Fuse Series: The First Benchtop Industrial SLS 3D Printers
Just like with other 3D printing technologies like FDM or SLA, lower-cost, compact SLS systems have recently started to emerge on the market, but initially, these solutions came with considerable trade-offs, including lower part quality and complex, manual workflows resulting from the lack of post-processing solutions, which limited their use in industrial and production settings.
The Formlabs Fuse 1 bridged that gap and created its own category as the first benchtop industrial SLS 3D printer that offered high quality, compact footprint, and a complete, simplified workflow at a fraction of the cost of traditional industrial SLS systems. Now, the next generation Fuse 1+ 30W extends that category with a more powerful laser, improved powder handling features, and new material capabilities for industrial quality parts and high throughput.

The Fuse Series ecosystem requires no specialized infrastructure, and can easily fit into your workspace.
Fuse Series SLS 3D printers use a single laser and a smaller build chamber that requires less heating. The lower energy consumption means that they can run on standard AC power without requiring specialized infrastructure. An optional nitrogen feature for the Fuse 1+ 30W printer creates an inert gas environment, preserving the quality of the unsintered powder for a lower refresh rate (more recycled powder than new powder in consecutive builds), minimizing waste, and enabling a better surface finish on sintered parts.
Fuse Series printers also feature a patent-pending solution called Surface Armor—a semi-sintered shell that keeps the area around the parts evenly heated as they print, ensuring great surface finish, consistent mechanical properties, high reliability, and better refresh rates.
To offer a compact, contained ecosystem and end-to-end powder handling, Fuse Series printers also come with Fuse Sift, which combines part extraction, powder recovery, storage, and mixing in a single free-standing device, and Fuse Blast, a fully automated cleaning and polishing solution.
Overall, benchtop industrial SLS 3D printing with Fuse Series printers offers a slightly smaller build volume compared to the entry-level traditional SLS systems, in return for a substantially smaller footprint, simplified workflow, and lower cost.
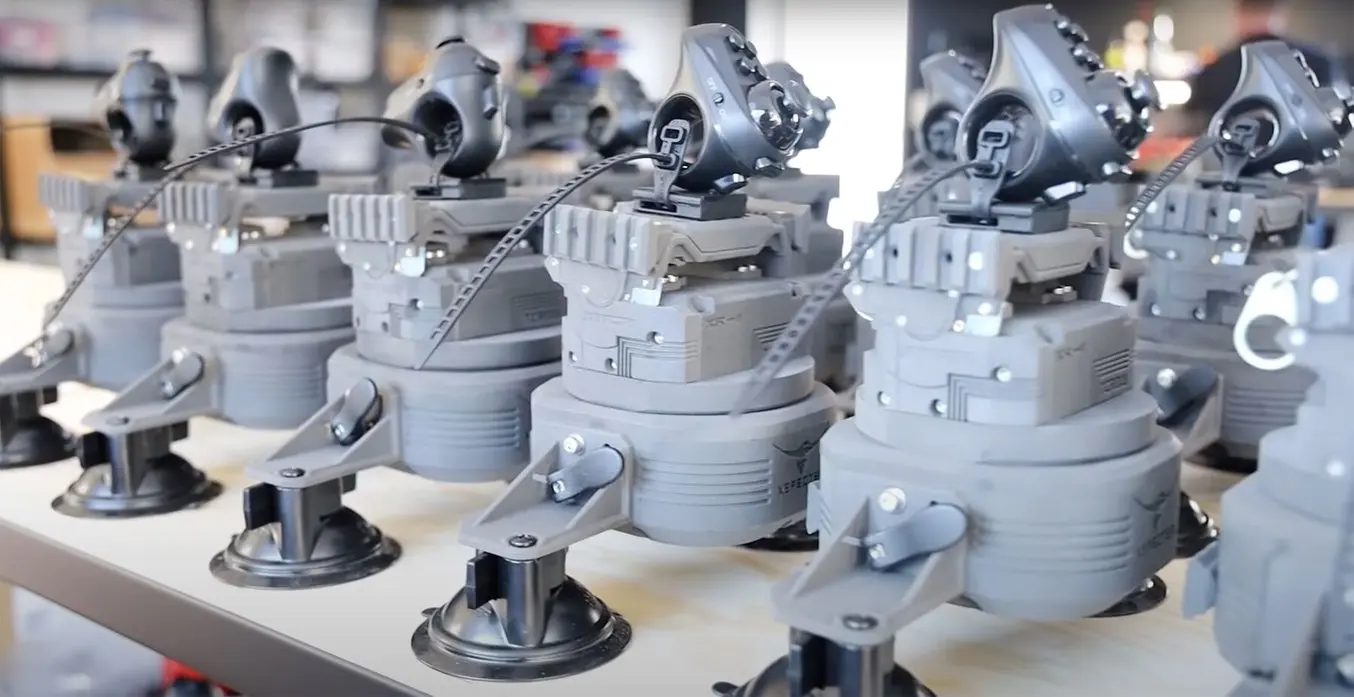
SLS for End-Use Production
3D printing for end-use production is not only possible, it's more affordable, agile, and scalable than ever with the Fuse SLS Ecosystem. Compare production methods, learn about bulk powder pricing, and see production in action for 15 different manufacturers currently using the Fuse Series.
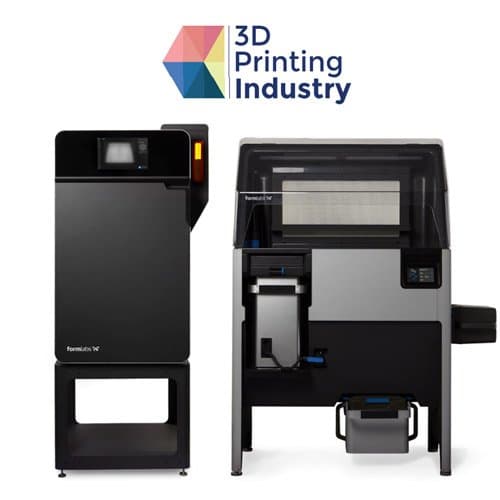
3D Printing Industry: Formlabs Fuse 1 & Sift In-Depth Review
Read this in-depth engineer's report by 3D Printing Industry that includes a review of Formlabs' SLS 3D printers and detailed results of accuracy testing.
Compare SLS 3D Printers
Fuse Series: Benchtop Industrial SLS 3D Printers | Traditional Industrial SLS 3D Printers | |
---|---|---|
Price | Starting just under $30,000 for the printer and $60,000 for the entire ecosystem | $200,000-$500,000+ |
Print Volume | 165 x 165 x 300 mm | Up to 550 x 550 x 750 mm |
Pros | Affordable High-quality parts High throughput Multiple material options Simplified workflow Small footprint Low maintenance | Large build volume High-quality parts High throughput Multiple material options |
Cons | Smaller build volume | Expensive machinery Large footprint Facility requirements High maintenance Requires a dedicated operator |
The comparison is based on the Formlabs Fuse Series benchtop industrial SLS system and traditional industrial SLS systems by EOS and 3D Systems.
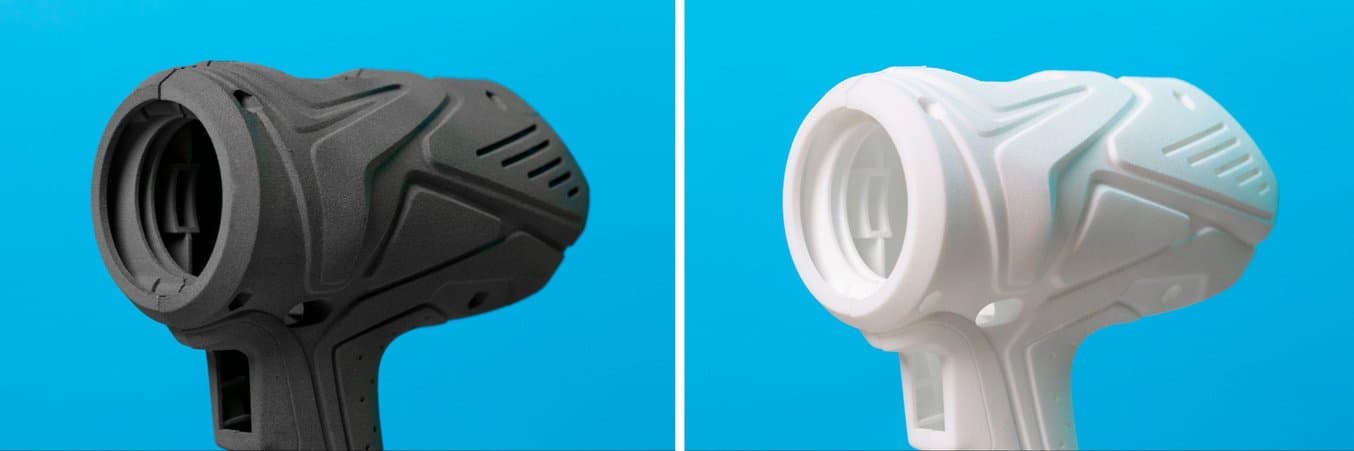
A drill prototype printed on the Fuse 1+ 30W (left) and on an EOS printer (right), with comparable quality but a vastly different machine price point.
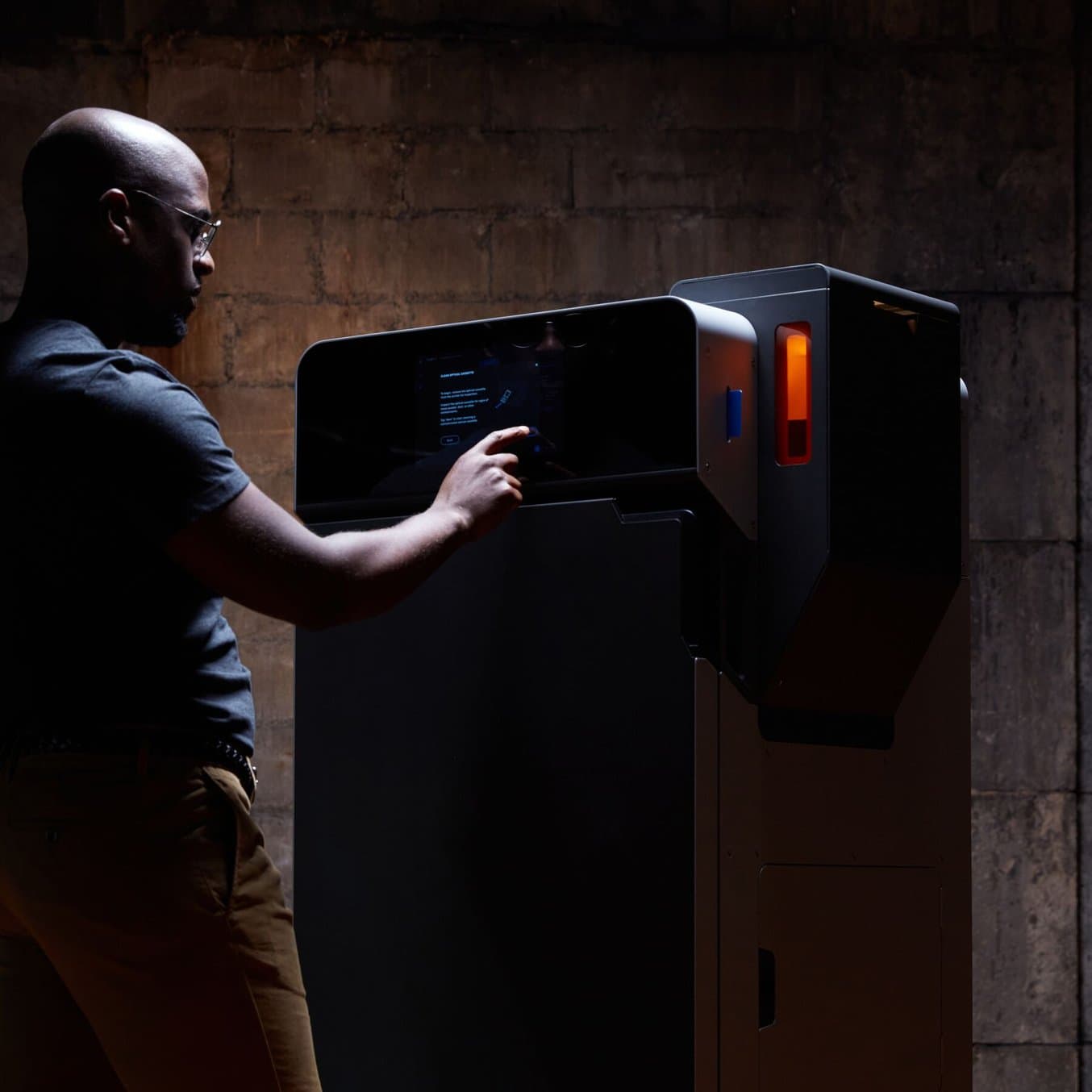
Outsourcing vs. In-House: When Does it Make Sense to Bring SLS 3D Printing In-House?
In this white paper, we evaluate the value proposition of bringing SLS 3D printers in-house, in comparison with outsourcing SLS parts from a service bureau.
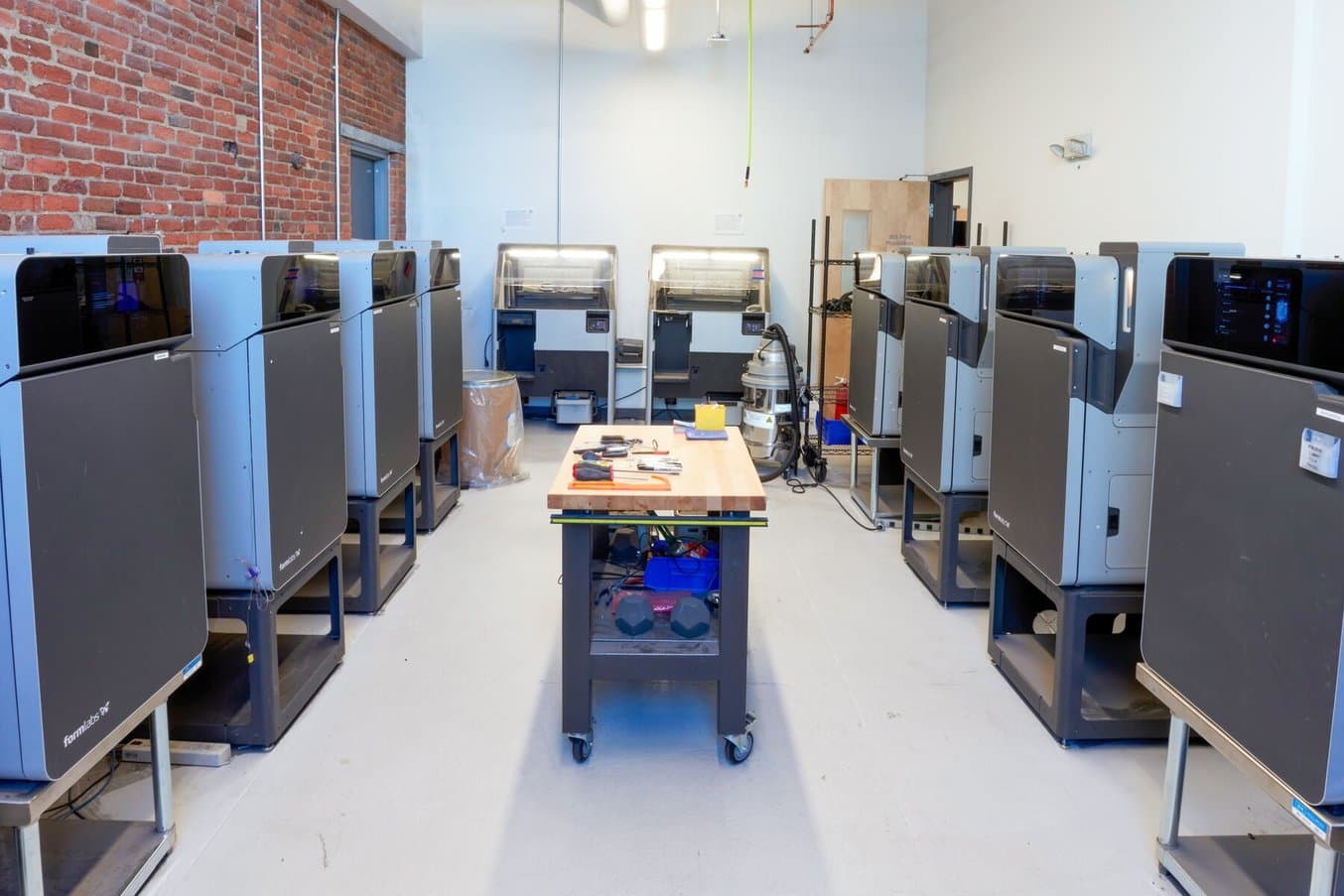
Fuse Series SLS Printers vs. Traditional Powder Bed Fusion Systems
This comparison guide will cover the main differences between compact SLS printers such as Formlabs Fuse Series and traditional large footprint machines.
SLS 3D Printing Materials
The most common material for selective laser sintering is nylon, a highly capable engineering thermoplastic for both functional prototyping and end-use production. Nylon is ideal for complex assemblies and durable parts with high environmental stability.
SLS 3D printed nylon parts are strong, stiff, sturdy, and durable. The final parts are impact-resistant and can endure repeated wear and tear. Nylon is resistant to UV, light, heat, moisture, solvents, temperature, and water. 3D printed nylon parts can also be biocompatible and not sensitizing, which means that they are ready to wear and safe to use in many contexts.
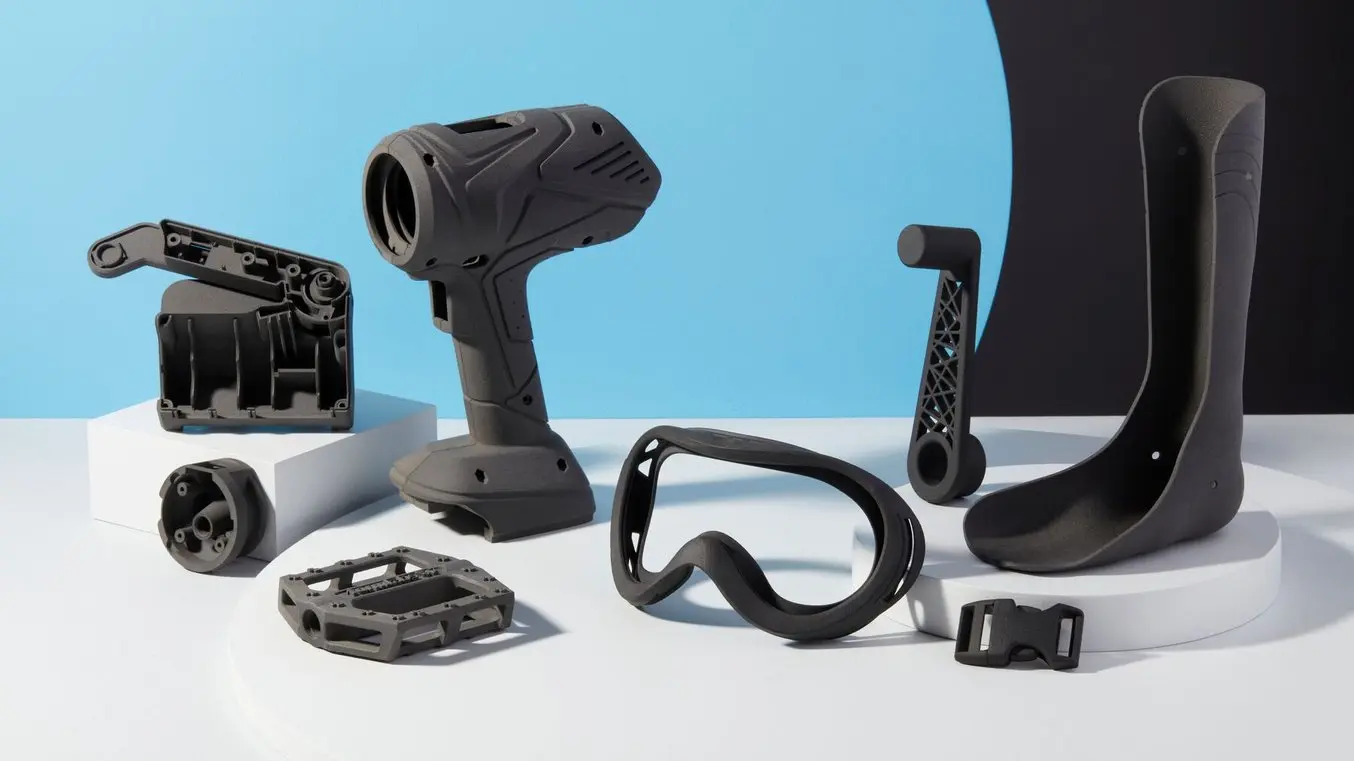
Nylon is ideal for a range of functional applications, from engineering consumer products to healthcare.
Nylon is a synthetic thermoplastic polymer that belongs to the family of polyamides. It is available in multiple variants, each tailored to different applications. Nylon 12 and nylon 11 are the most common single-component powders, and both can also be reinforced with other materials like glass or carbon fiber to create composites with specific properties, like added strength and rigidity.
Besides nylon, polypropylene (PP) is another popular SLS 3D printing material. PP is ideal for producing fully functional, lightweight parts that offer the mechanical properties of common injection molded polypropylenes, ensuring durability in demanding environments for prototypes or end-use applications.
SLS 3D printers can also create flexible TPU parts with unmatched design freedom and ease. Combining the high tear strength and elongation at break of rubber materials with the versatility of SLS 3D printing, TPU is ideal for producing flexible, skin-safe prototypes and end-use parts that withstand the demands of everyday use.
The specific material selection is dependent on the printer model. The following materials are compatible with the Fuse 1+ 30W:
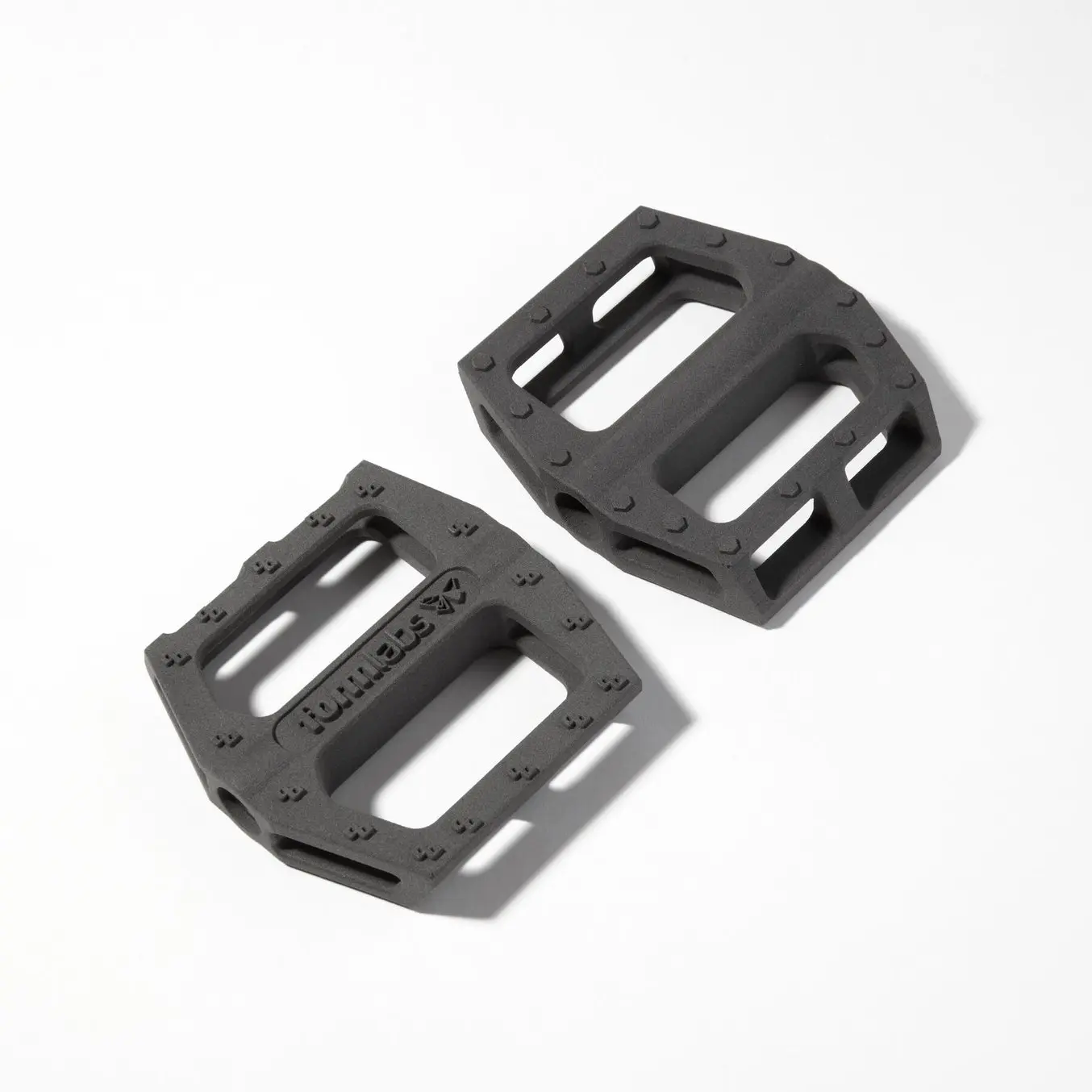
Nylon 12 Powder
General purpose, versatile material with high detail and great dimensional accuracy.
- High performance prototyping
- Small batch manufacturing
- Permanent jigs, fixtures, and tooling
- Biocompatible, sterilizable parts*
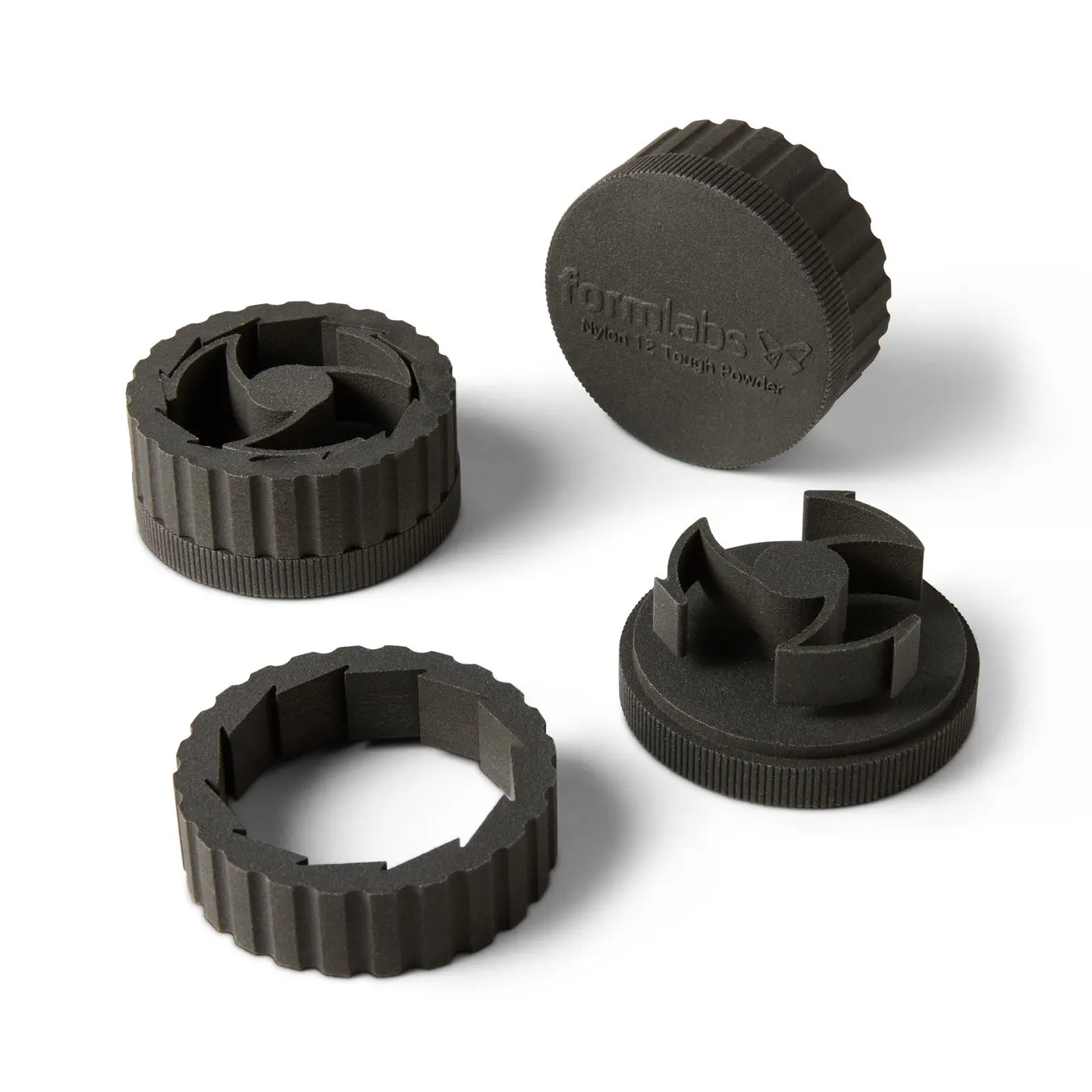
Nylon 12 Tough Powder
Best-in-class ductility, lowest refresh rate, and great dimensional accuracy.
- High performance, impact-resistant prototypes
- Parts requiring ductility; snaps, ratchets, hinges
- Long parts, susceptible to warping
- End-use parts in high-impact or high-wear environments
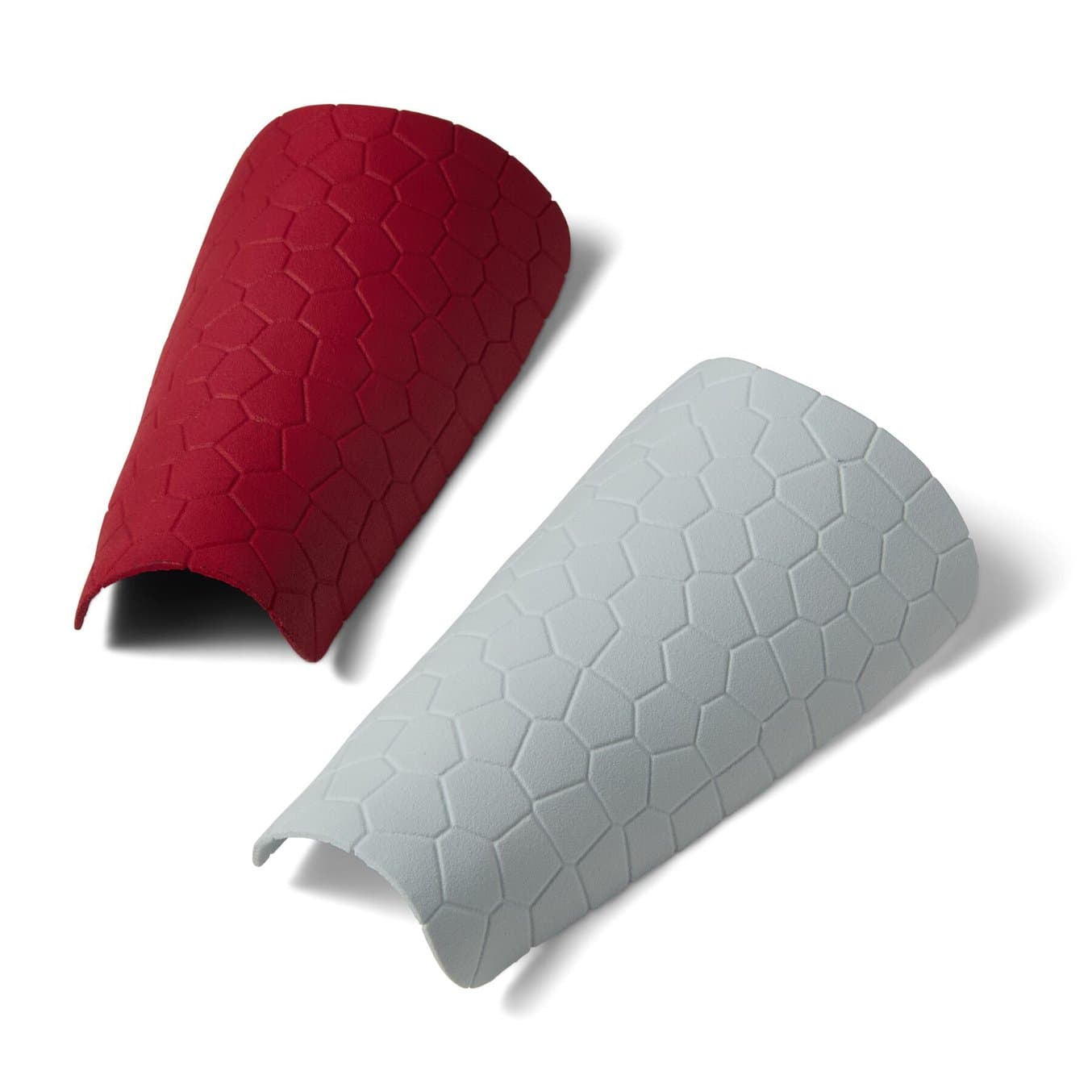
Nylon 12 White Powder
Leverage the reliability, durability, and strength of Nylon 12 Powder with the added benefit of an easy dyeing or coloring workflow.
- Dyed, painted, or otherwise colored parts
- Branded, looks-like prototypes
- Biocompatible medical devices and surgical guides*
- Small batch manufacturing
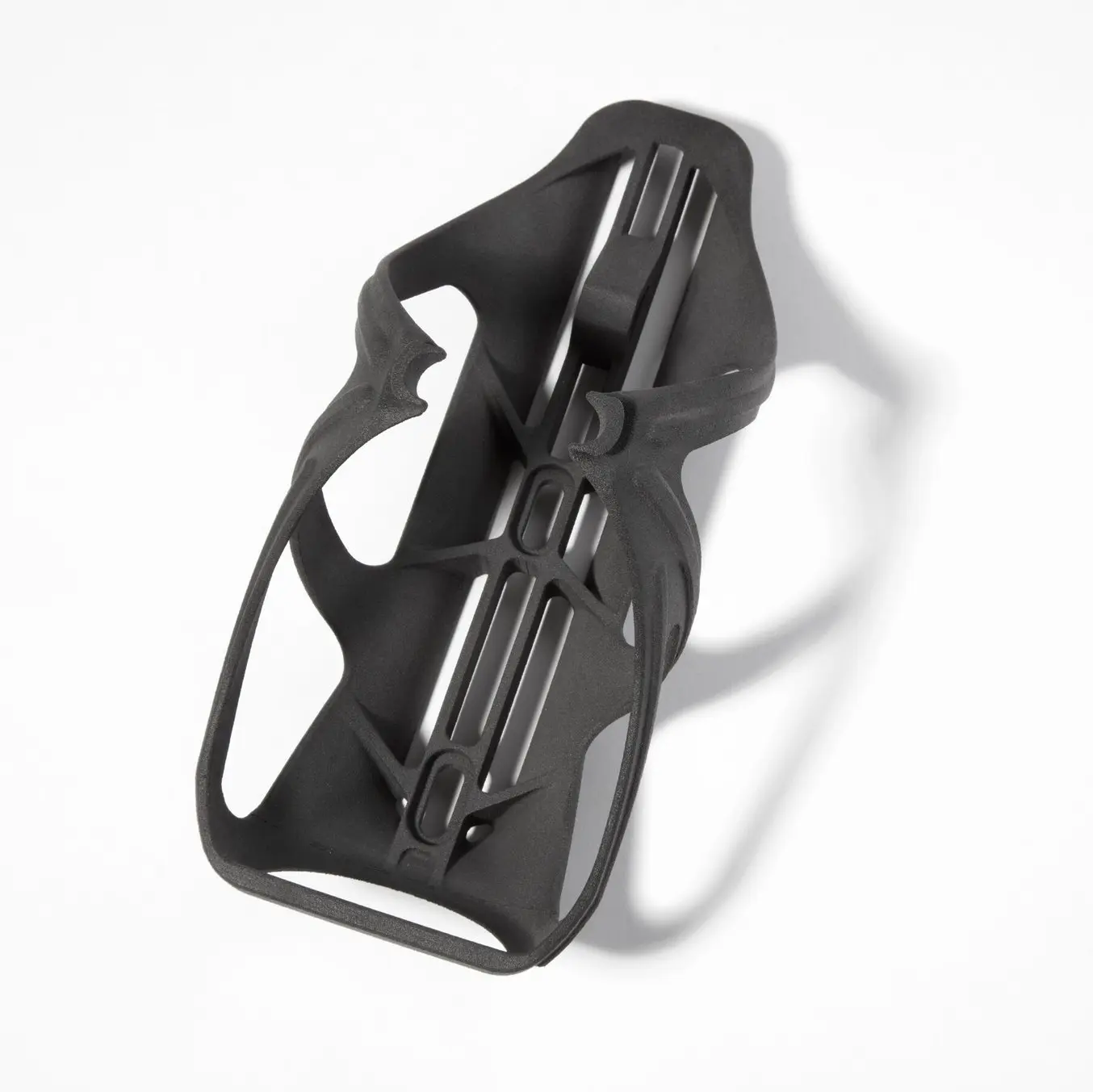
Nylon 11 Powder
Highly ductile, robust, and strong material for when durability and performance are key.
- Impact-resistant prototypes, jigs, and fixtures
- Thin-walled ducts and enclosures
- Snaps, clips, and hinges
- Orthotics and prosthetics*
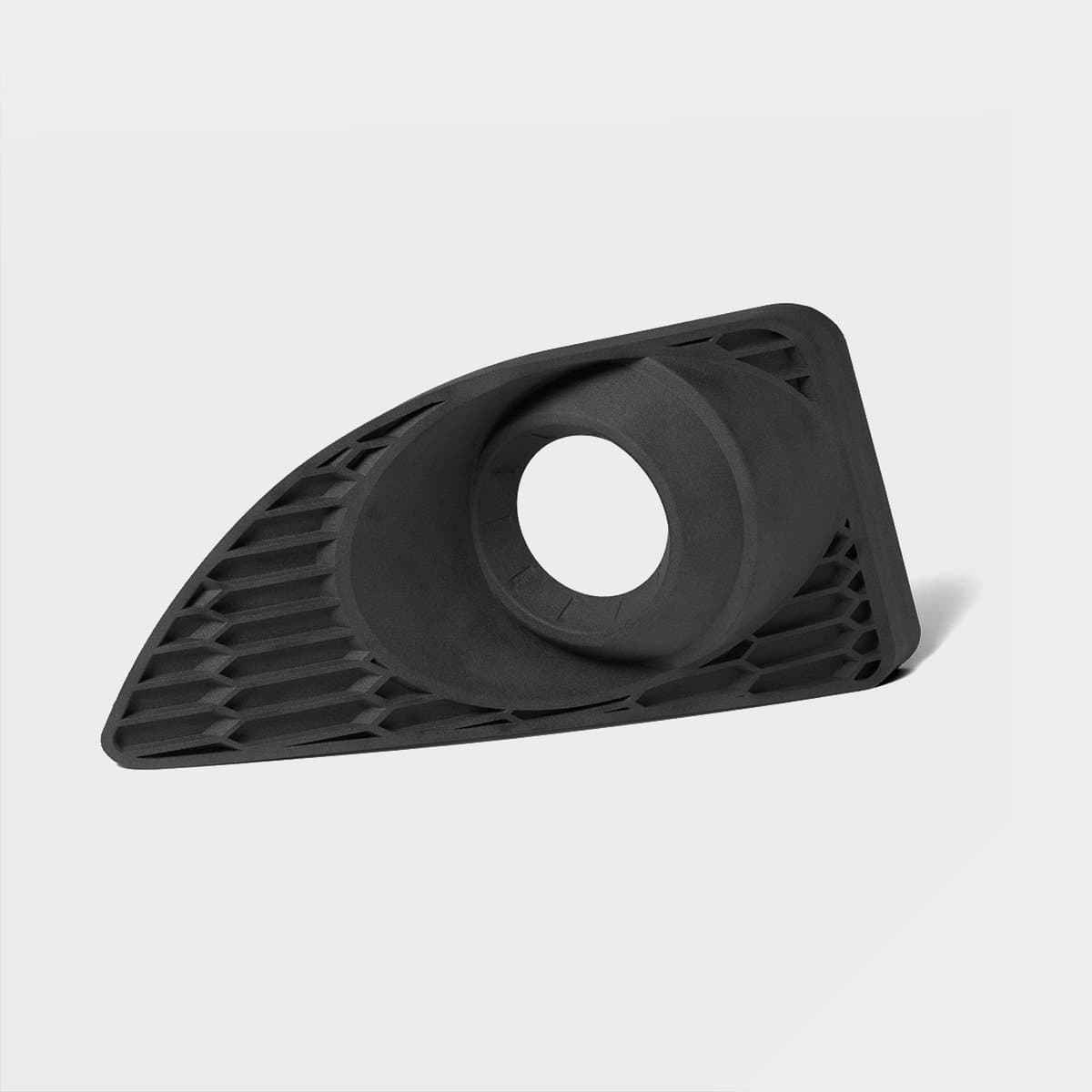
Nylon 12 GF Powder
A glass-filled material with enhanced stiffness and thermal stability for demanding industrial environments.
- Robust jigs and fixtures and replacement parts
- Parts undergoing sustained loading
- Threads and sockets
- Parts subjected to high temperature
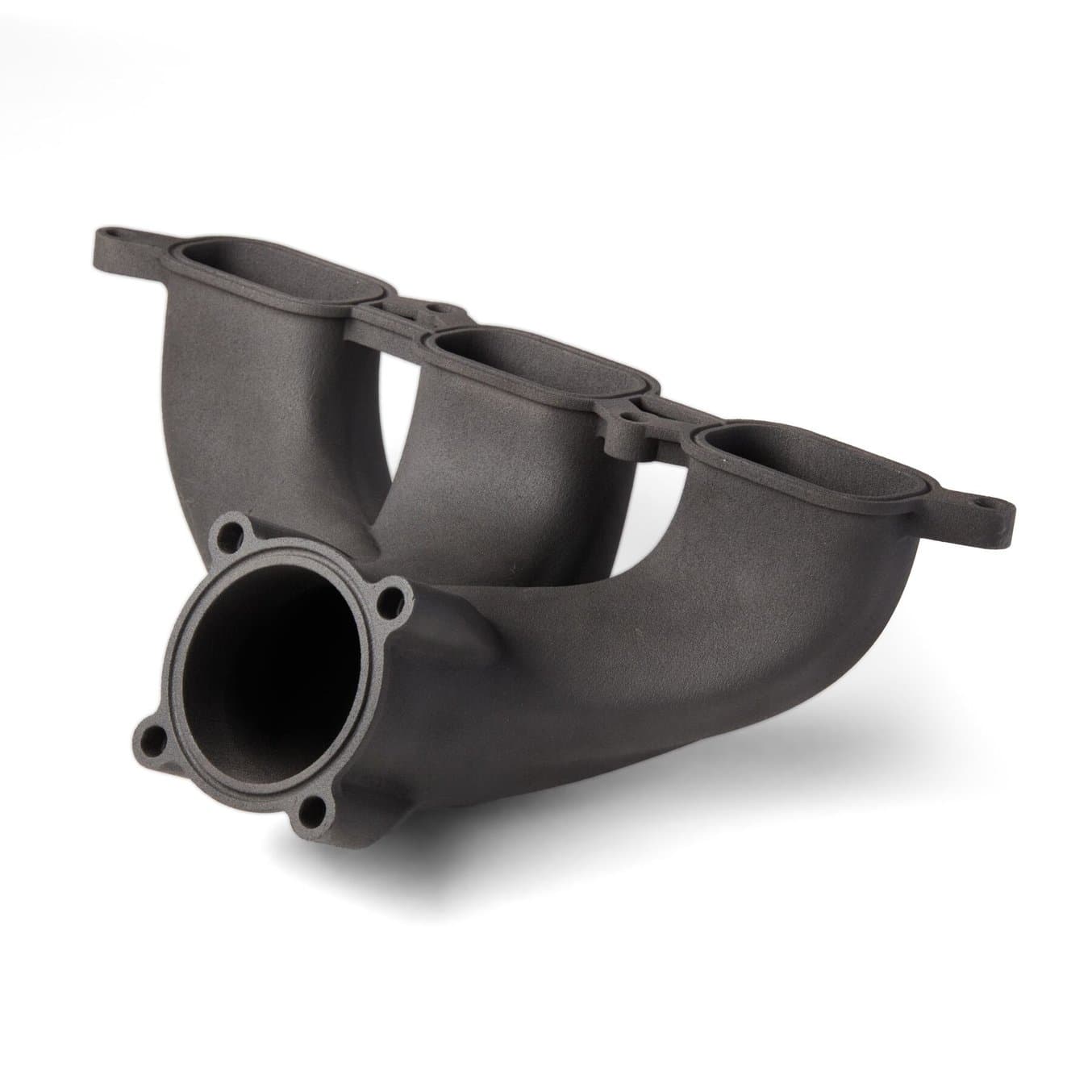
Nylon 11 CF Powder
Get the best of nylon and carbon fiber with this highly stable, lightweight, high-performance material.
- Replacement and spare alternatives to metal parts
- Tooling, jigs, fixtures
- High-impact equipment
- Functional composite prototypes
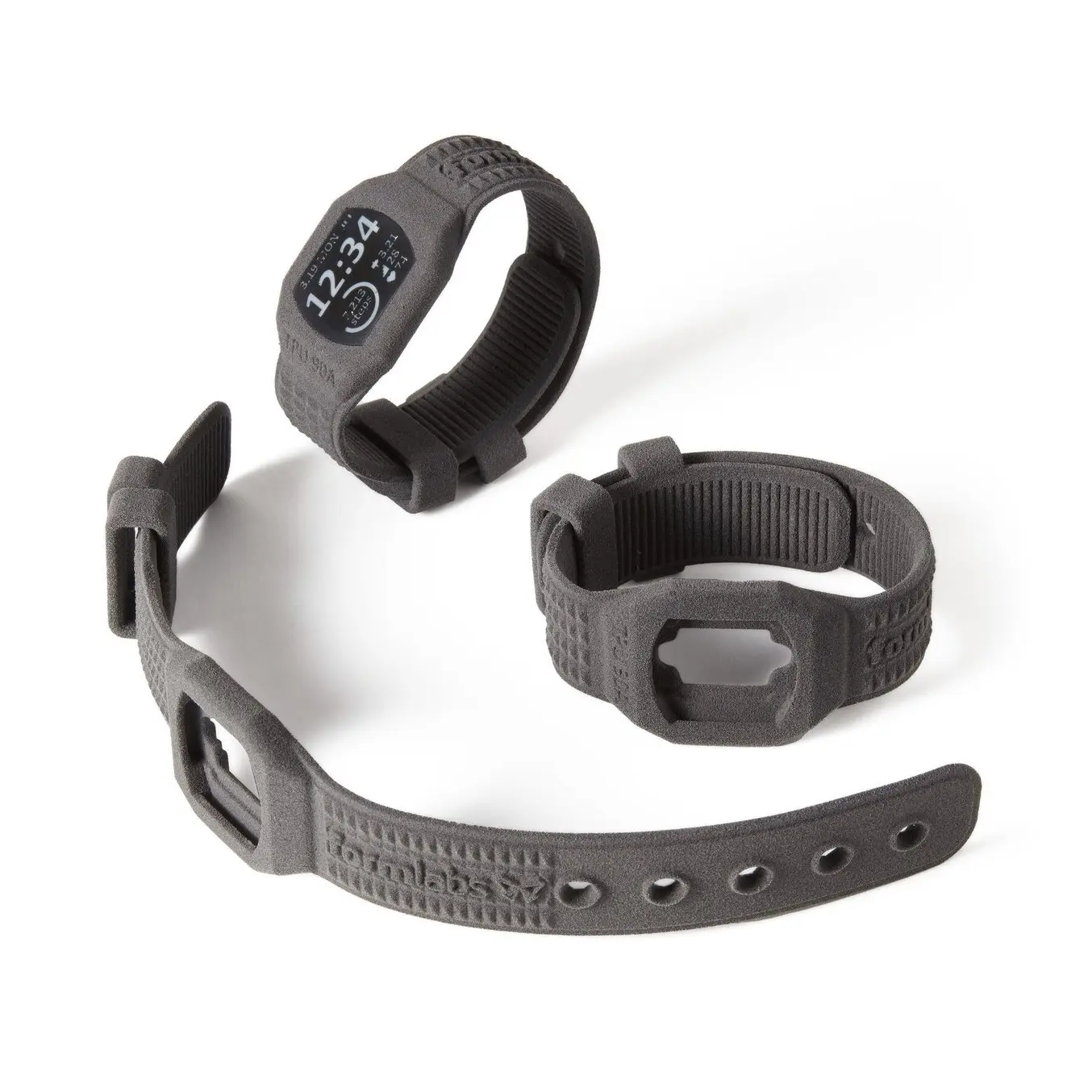
TPU 90A Powder
An elastomer with high elongation at break and superior tear strength for flexible, skin-safe prototypes and end-use parts.
- Wearables and soft-touch elements
- Padding, dampers, cushions, and grippers
- Gaskets, seals, masks, belts, plugs, and tubes
- Soles, splints, orthotics, and prosthetics*
* Material properties may vary based on part design and manufacturing practices. It is the manufacturer’s responsibility to validate the suitability of the printed parts for the intended use.
Compare Formlabs SLS 3D Printing Powders Material Properties
Materials | Nylon 12 Powder | Nylon 12 Tough Powder | Nylon 12 White Powder | Nylon 11 Powder | Nylon 12 GF Powder | Nylon 11 CF Powder | TPU 90A Powder |
---|---|---|---|---|---|---|---|
Ultimate Tensile Strength X (MPa) | 50 | 42 | 47 | 49 | 38 | 69 | 8.7 |
Ultimate Tensile Strength Y (MPa) | N/A | N/A | N/A | N/A | N/A | 52 | 8.7 |
Ultimate Tensile Strength Z (MPa) | N/A | N/A | N/A | N/A | N/A | 38 | 7.2 |
Tensile Modulus X (MPa) | 1850 | 1450 | 1950 | 1600 | 2800 | 5300 | N/A |
Elongation at Break, X/Y (%) | 11 | 25 | 8 | 40 | 4 | 9 / 15 | 310 |
Elongation at Break, Z (%) | 6 | 15 | 6 | N/A | 3 | 5 | 110 |
Heat Deflection Temperature @ 0.45 MPa (°C) | 171 | 161 | 177 | 182 | 170 | 188 | N/A |
Notched Izod (J/m) | 32 | 60 | 28 | 71 | 36 | 74 | N/A |
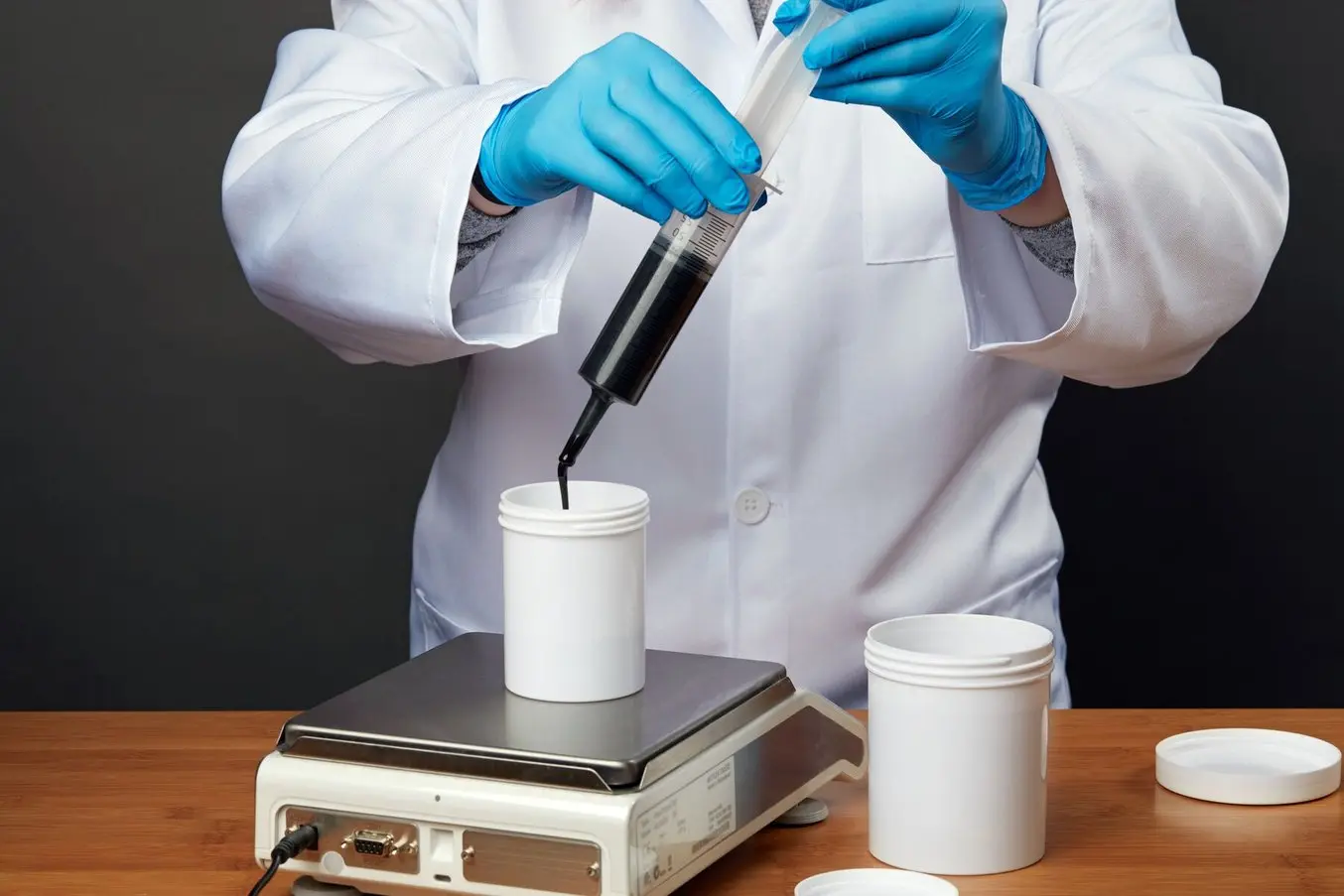
Formlabs is Open
Maximize your 3D printer’s potential with Formlabs Developer Platform. Unlock the possibility of printing with any 405 nm photopolymer resin or 1064 nm powder on Formlabs 3D printers, customize your print settings, or build software integrations.
SLS 3D Printing Applications
SLS 3D printing accelerates innovation and supports businesses across a wide range of industries, including engineering, manufacturing, and healthcare.
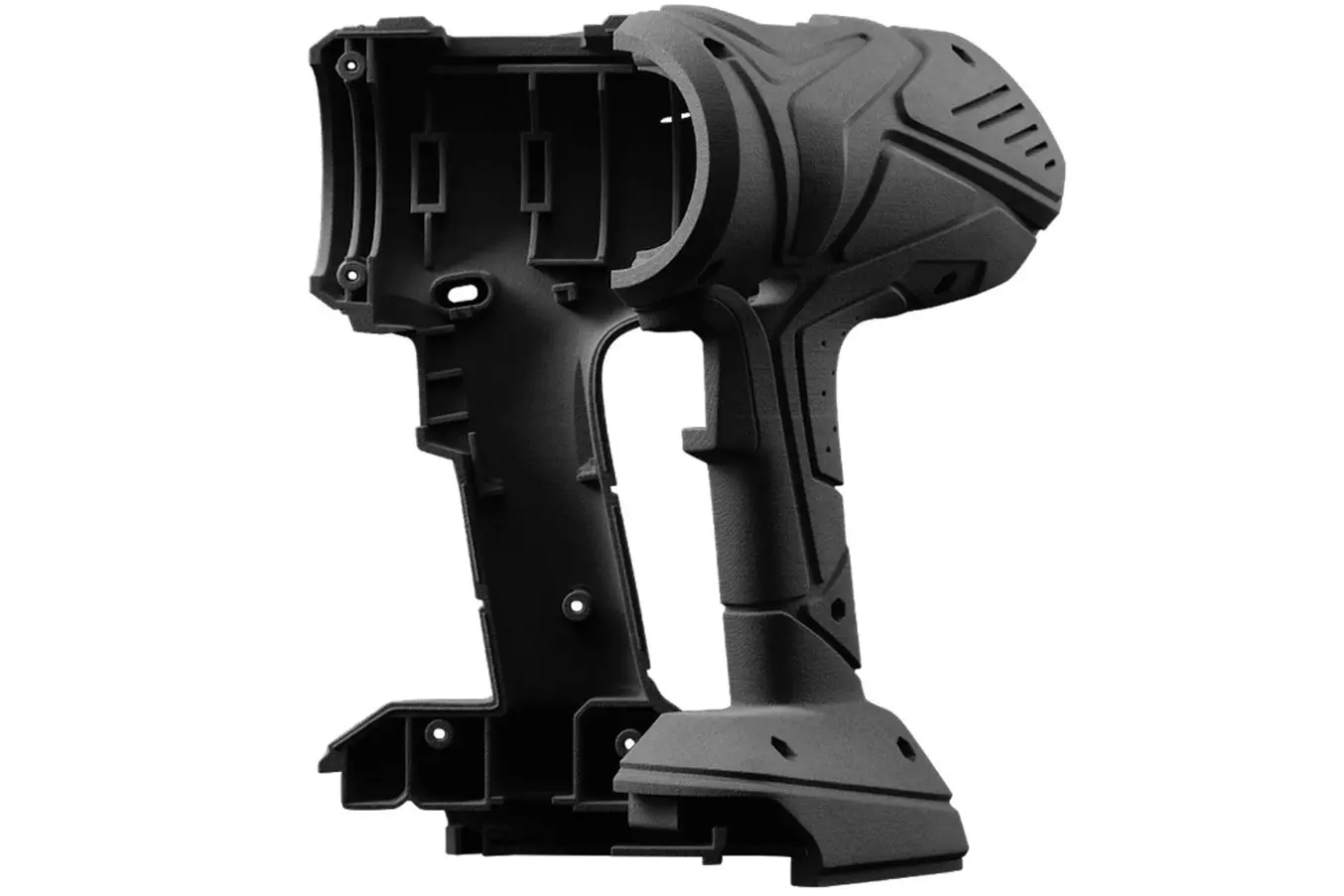
Engineering
Take control of your entire product development process, from iterating on your first concept design to manufacturing ready-to-use products:
- Rapid prototyping
- Mockups of products for in-field customer feedback
- Functional prototyping
- Rigorous functional testing of products (e.g. ductwork, brackets)
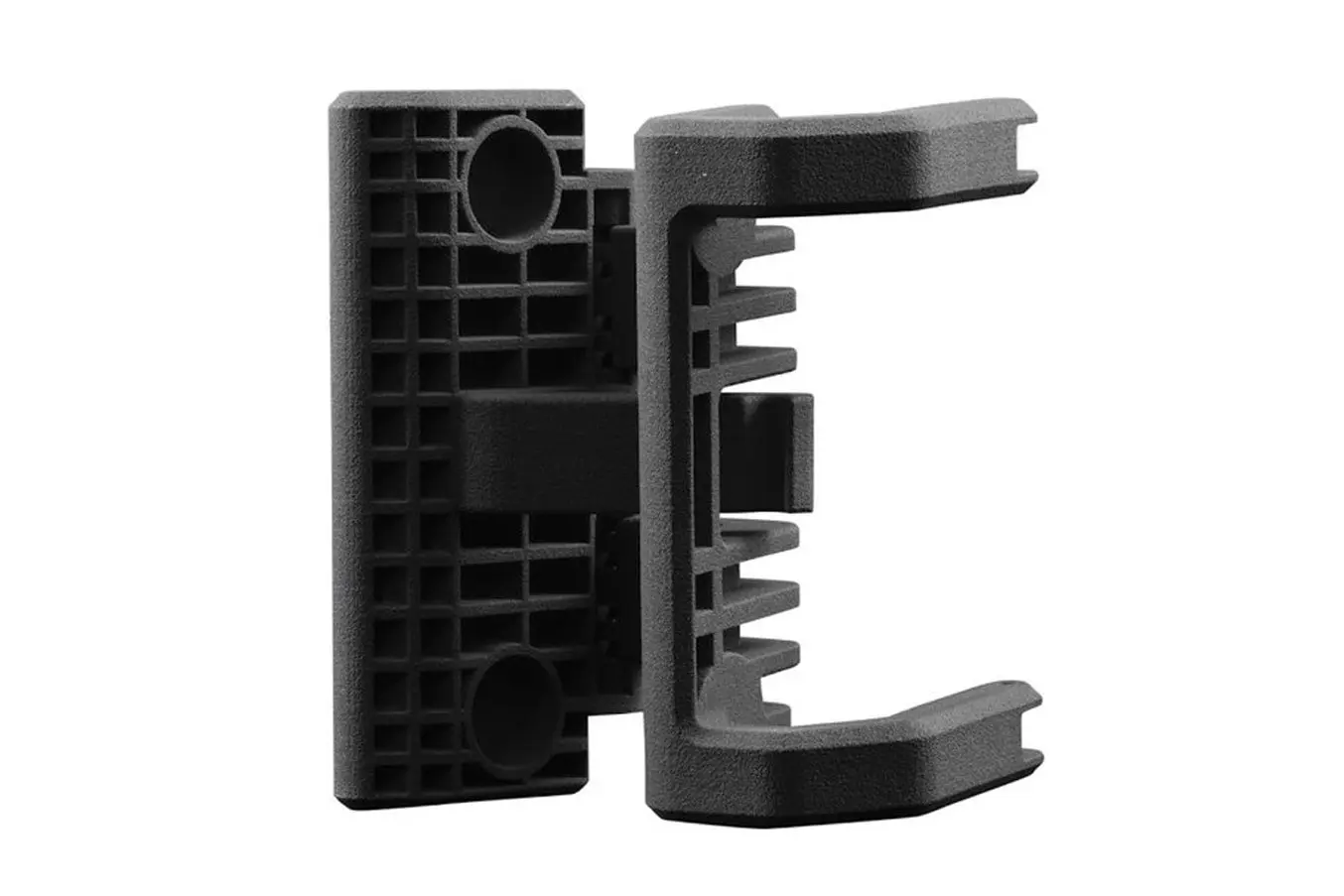
Manufacturing
Own your supply chain and respond quickly to changing demands:
- End-use part production
- Small batch, stop-gap, and bridge manufacturing
- Mass customized consumer products
- Replacement parts, aftermarket parts, spare parts
- Long-lasting, durable manufacturing aids, jigs, fixtures, and tooling
- Custom automotive or motorcycle parts, marine equipment, military ‘resupply on-demand’
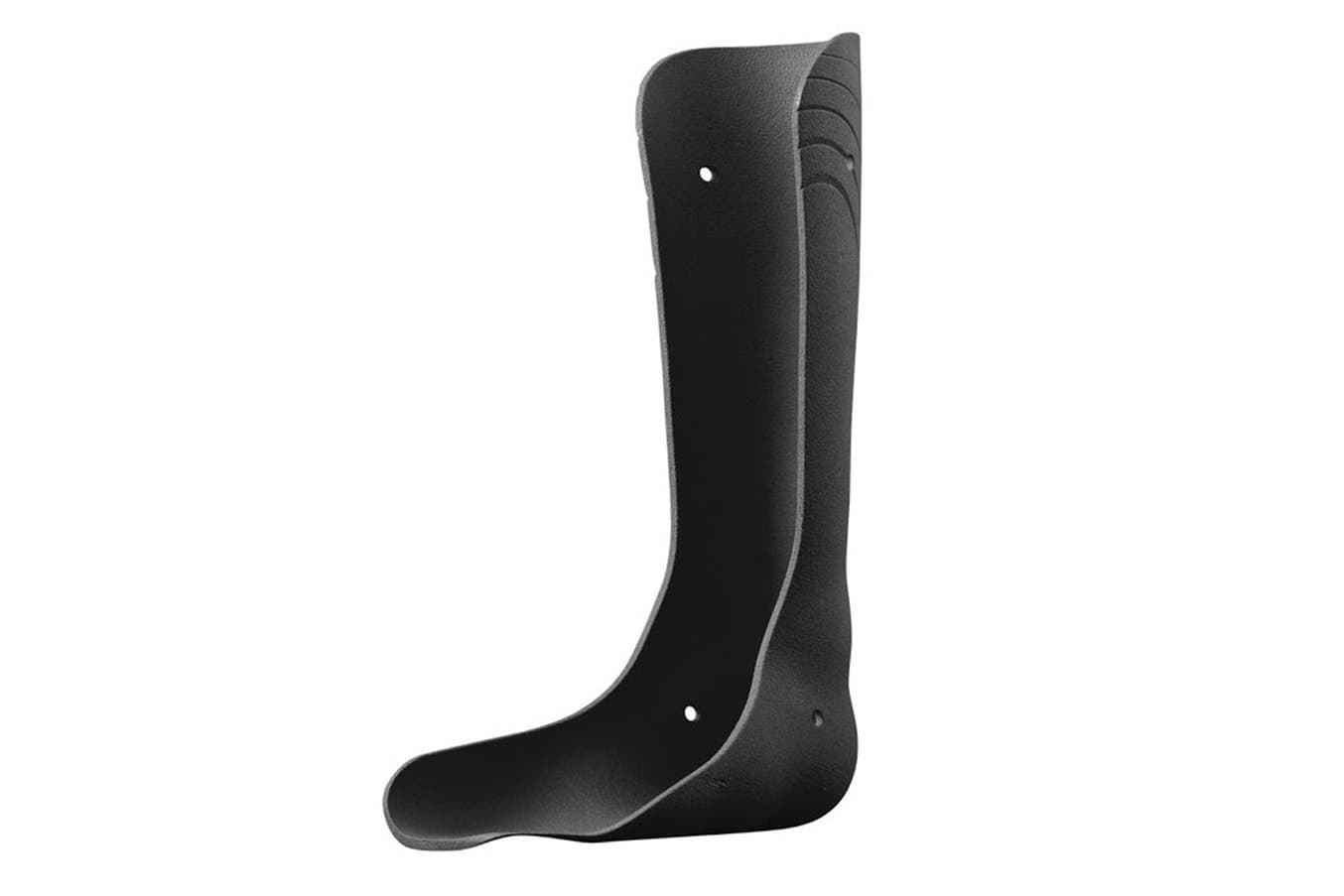
Healthcare
Manufacture ready-to-use, patient-specific medical devices in-house:
- Medical device prototyping
- Prosthetics and orthotics (i.e. limb replacements + braces)
- Surgical models and tools
- End-use parts*
* Material properties may vary based on part design and manufacturing practices. It is the manufacturer’s responsibility to validate the suitability of the printed parts for the intended use.
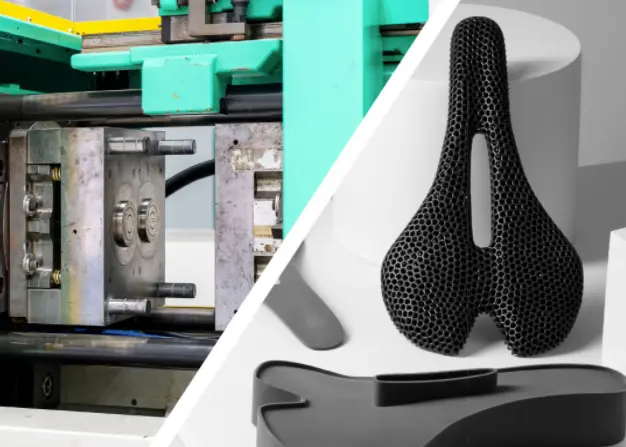
SLS 3D Printing vs. Injection Molding: When to Replace Molded Parts With 3D Printing?
This white paper showcases the cost-dynamics for real-life use cases, and presents guidelines for using SLS 3D printing, injection molding, or both.
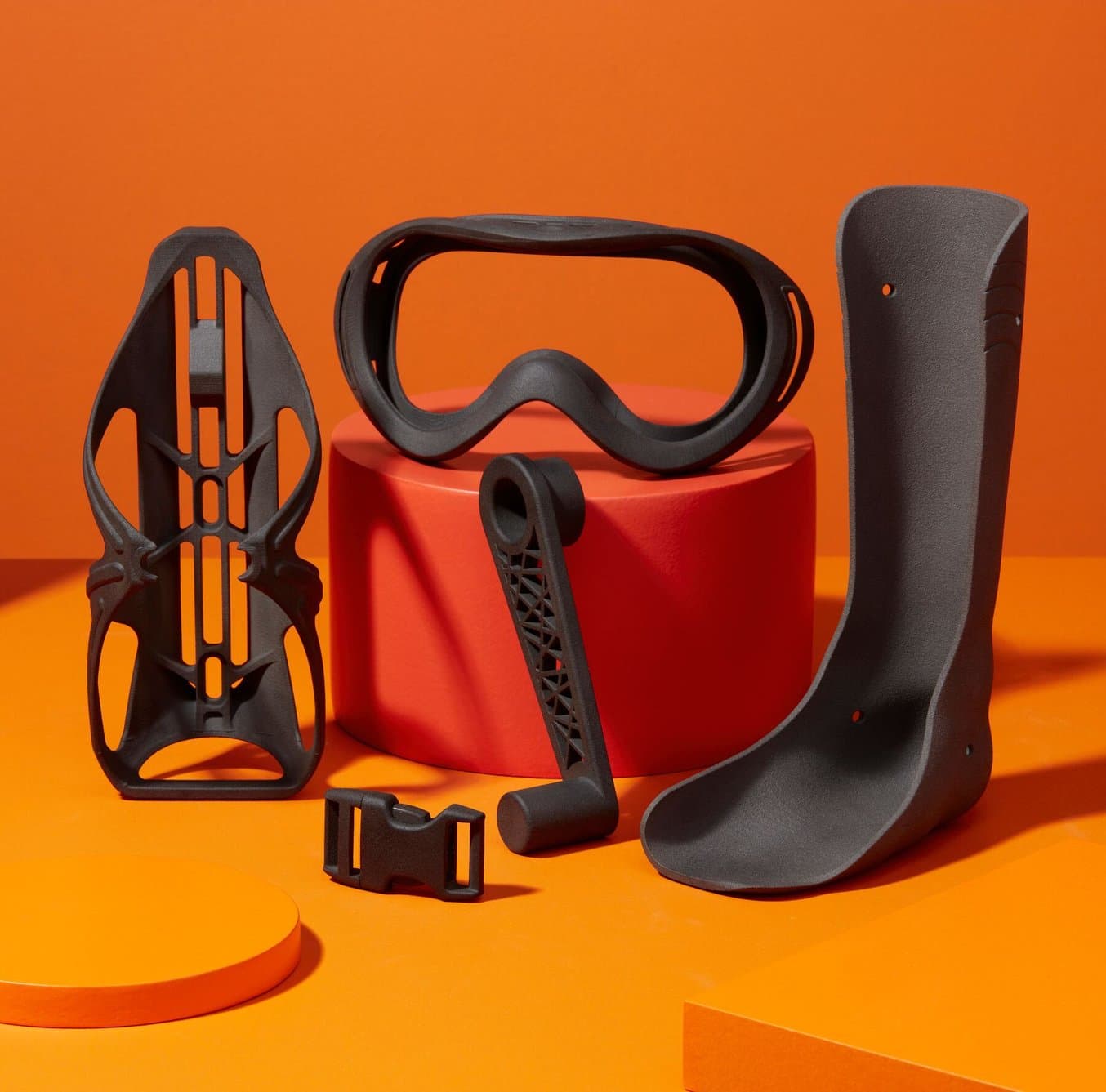
How to Identify the Right Applications for SLS Printing
In this webinar, learn how affordable industrial-quality SLS 3D printers are making additive manufacturing a viable choice for end-use production and mass customization.
SLS 3D Printing Workflow
Watch this video to see the step by step process of using a Fuse Series selective laser sintering (SLS) 3D printer and the Fuse Sift powder recovery station.
1. Design and Prepare the File
Use any CAD software or 3D scan data to design your model, and export it in a 3D printable file format (STL, OBJ or 3MF). Each SLS printer includes software with fine-tuned print settings, that assist you in orienting and arranging models, as well as estimating print times, and slicing the digital model into layers for printing. Once setup is complete, the print preparation software sends the instructions to the printer via a wireless or cable connection.
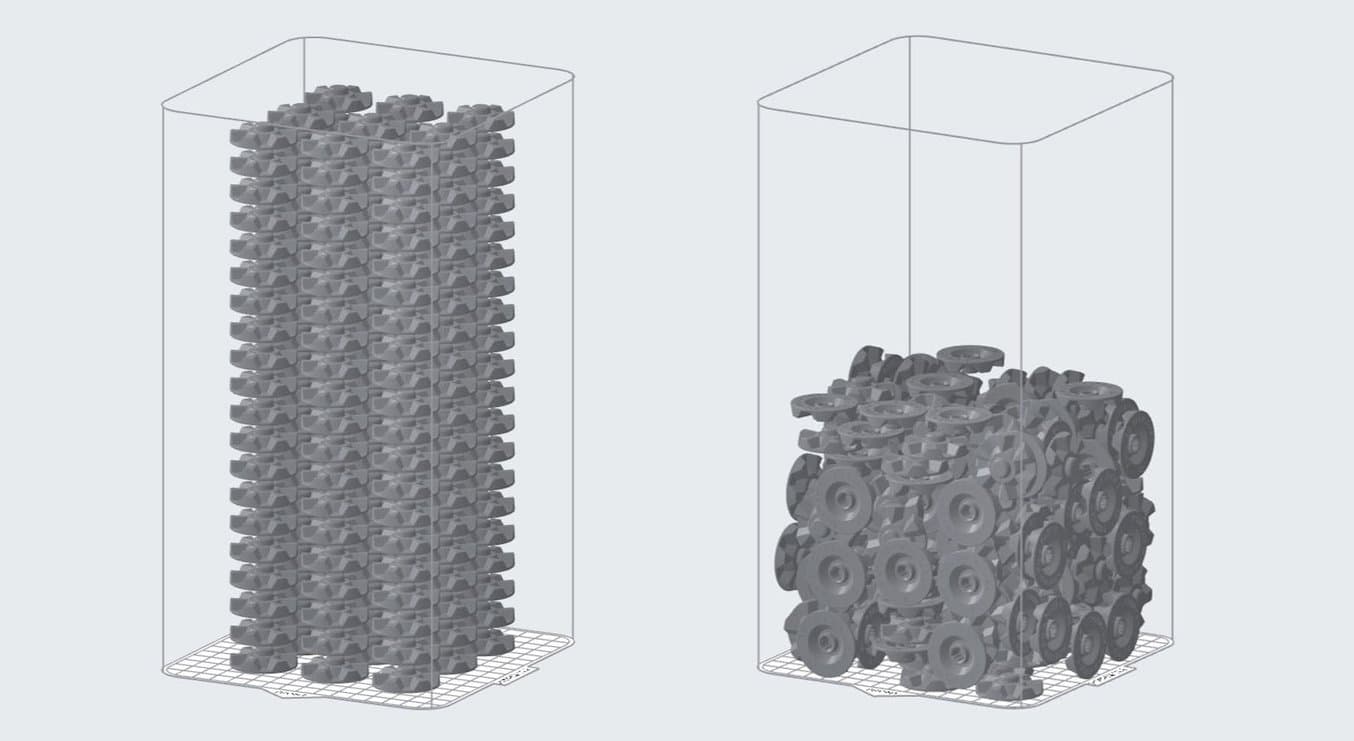
Fuse Series printers use PreForm print preparation software (free to download) that allows you to seamlessly duplicate and organize multiple parts within a 3D grid to use as much of the build space as possible for a single print. PreForm automatically suggests optimal orientation and part packing, with the ability to manually refine as needed.
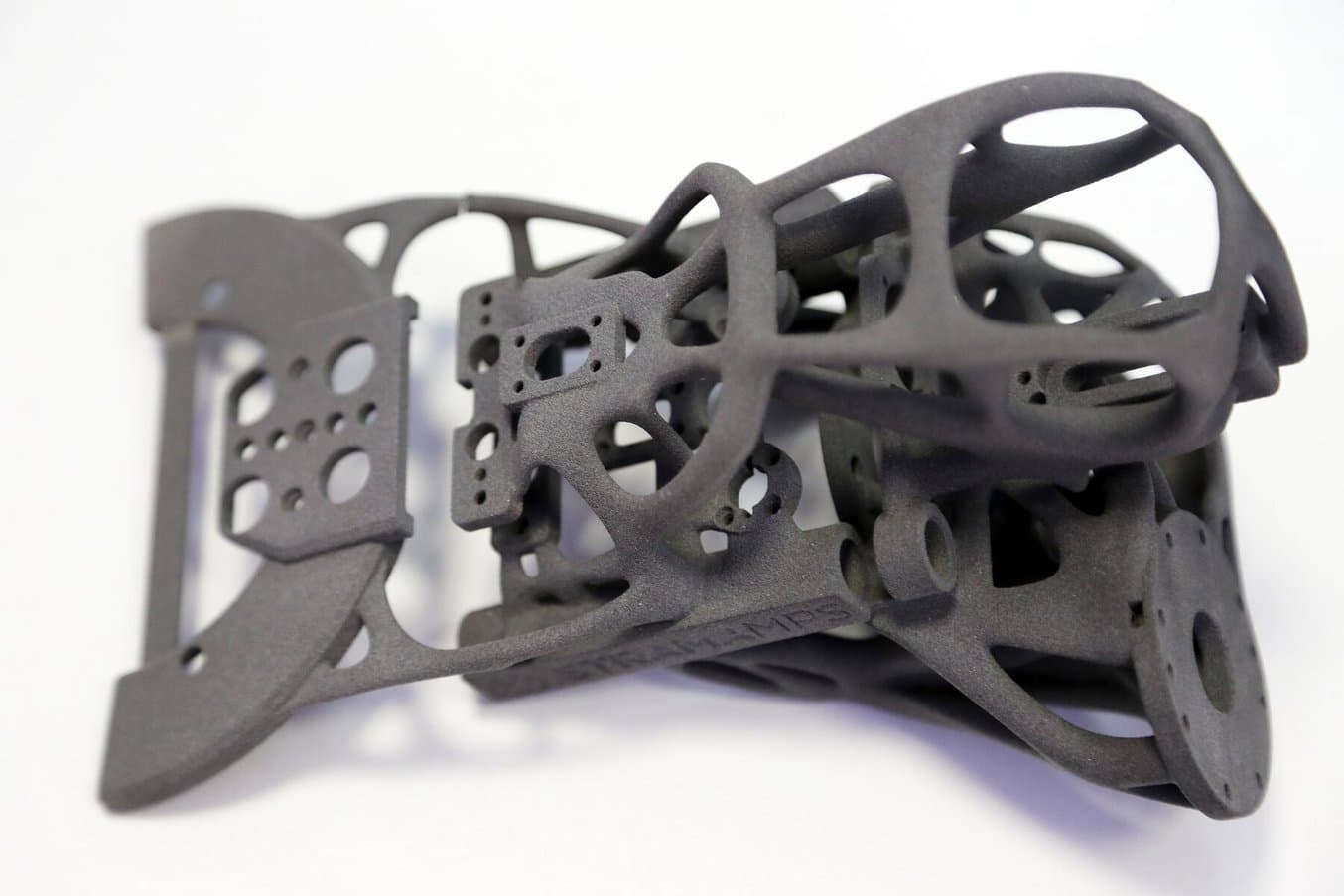
Fuse Series Design Guide
In this design guide, you’ll learn about some of the important considerations for designing for SLS 3D printing on the Fuse Series, and how you can leverage these practices to create successful parts.
2. Prepare the Printer
The workflow for preparing the printer varies by system. Most traditional SLS systems require extensive training, tools, and physical effort to prepare and maintain.
Fuse Series printers reimagine the SLS workflow for simplicity and efficiency, with modular components to enable nonstop printing and end-to-end powder handling.
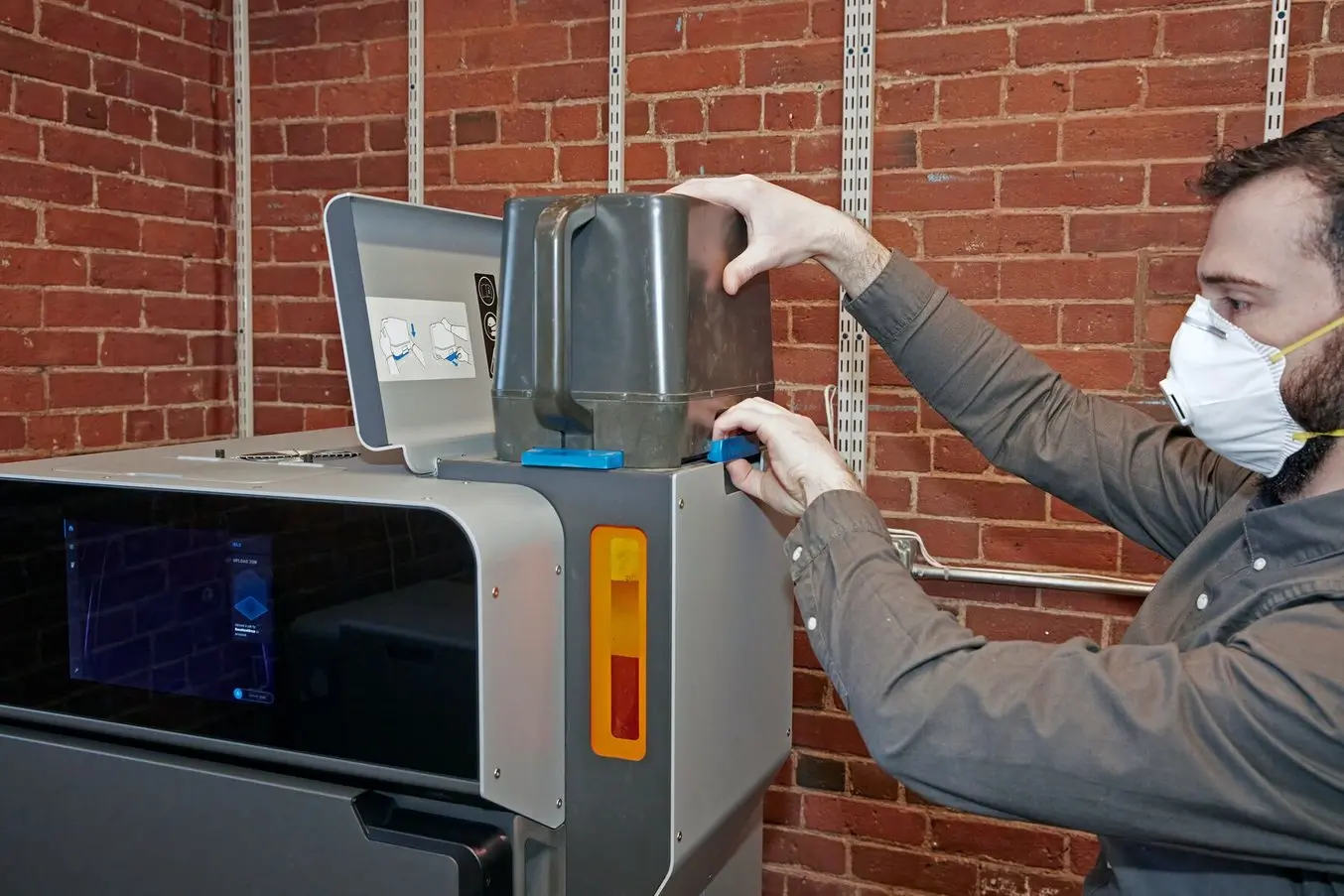
On Fuse Series printers, you can load powder easily using the powder cartridge.
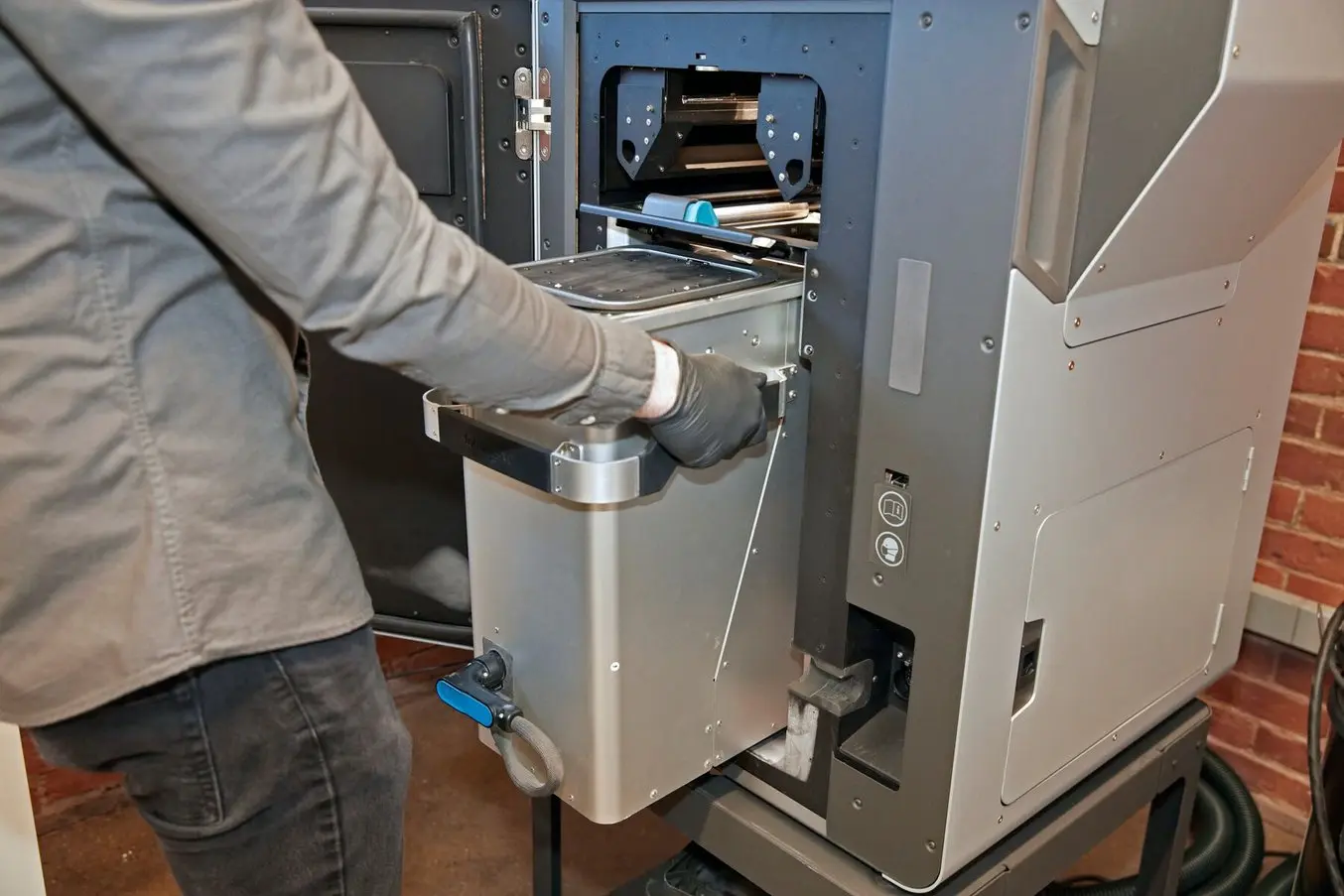
Fuse Series printers use a removable build chamber so you can run another print while a previous one is still cooling.
3. Print
Once all pre-print checks have been completed, the machine is ready to print. SLS 3D prints can take anywhere from a few hours to multiple days depending on the size and complexity of parts, as well as the part density. Thanks to its high-power laser, even full builds on the Fuse 1+ 30W generally finish within 24 hours.
Once the print is finished, the build chamber needs to slightly cool down in the print enclosure before moving to the next step. After that, the build chamber can be removed and a new one inserted to run another print.
The build chamber with the printer parts then has to cool down even further before post-processing to ensure the optimal mechanical properties and avoid warping in parts. This may take up to half of the print time.
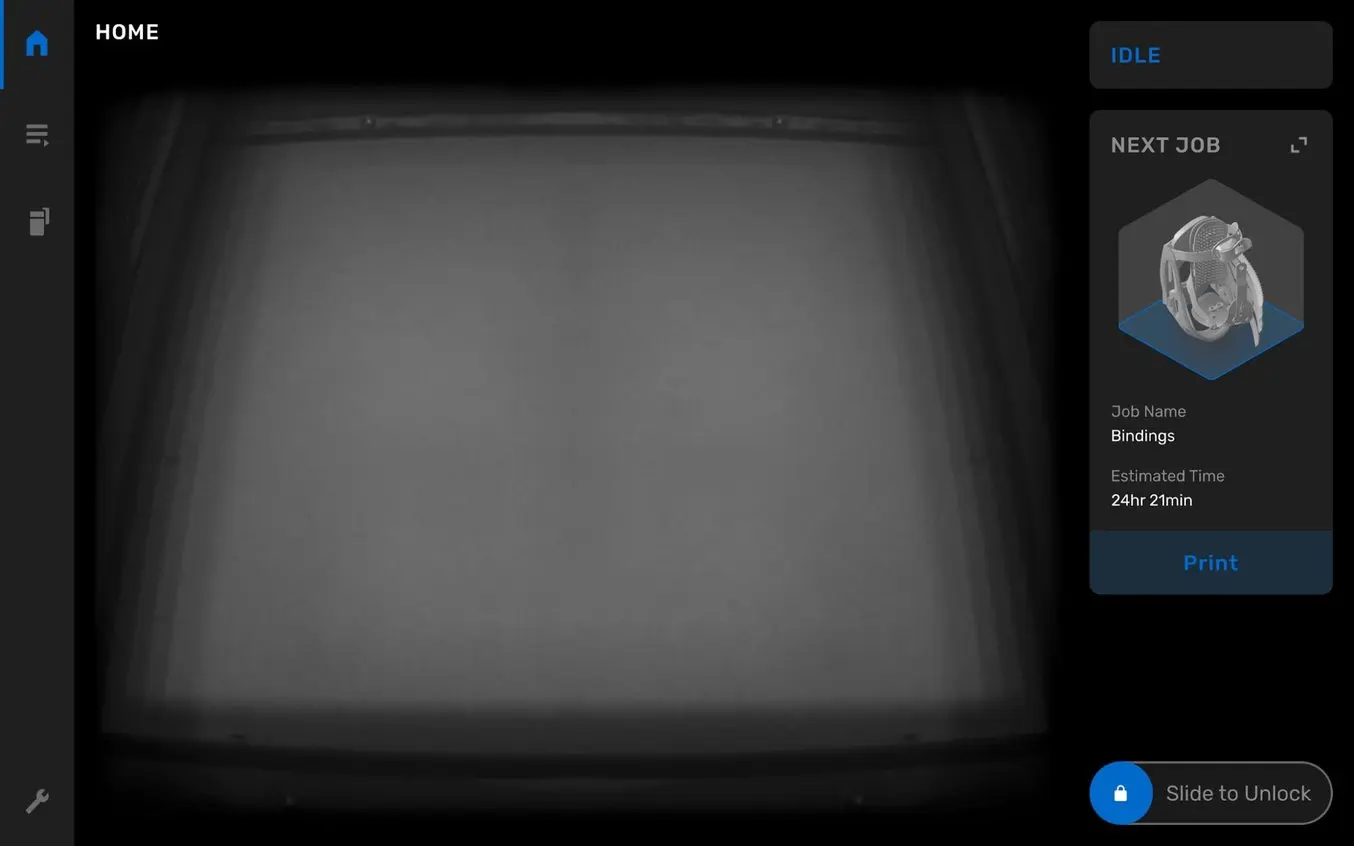
On Fuse Series printers, the touchscreen displays a live stream of the print bed during printing so you can watch each new layer take shape. This camera view is also available from your computer in PreForm so you can monitor your print without leaving your desk.
4. Part Extraction and Powder Recovery
Post-processing SLS parts requires minimal time and labor compared to other 3D printing processes. It is easily scalable and yields consistent results for batches of parts thanks to the lack of support structures.
After build cooled down, the finished parts can be removed from the build chamber and extracted from the unsintered powder. Solutions for this can range from more affordable manual powder recovery solutions, such as Fuse Depowdering Kit to all-in-one powder recovery stations, such as Fuse Sift, that handles the extraction of parts and unsintered powder, as well as storing, dosing, and mixing of powder.
Any excess powder remaining after part recovery is filtered to remove larger particles and can be recycled. Unfused powder degrades slightly with exposure to high temperatures, so it should be refreshed with new material for subsequent print jobs. This ability to re-use the material for subsequent jobs makes SLS one of the least wasteful manufacturing methods.
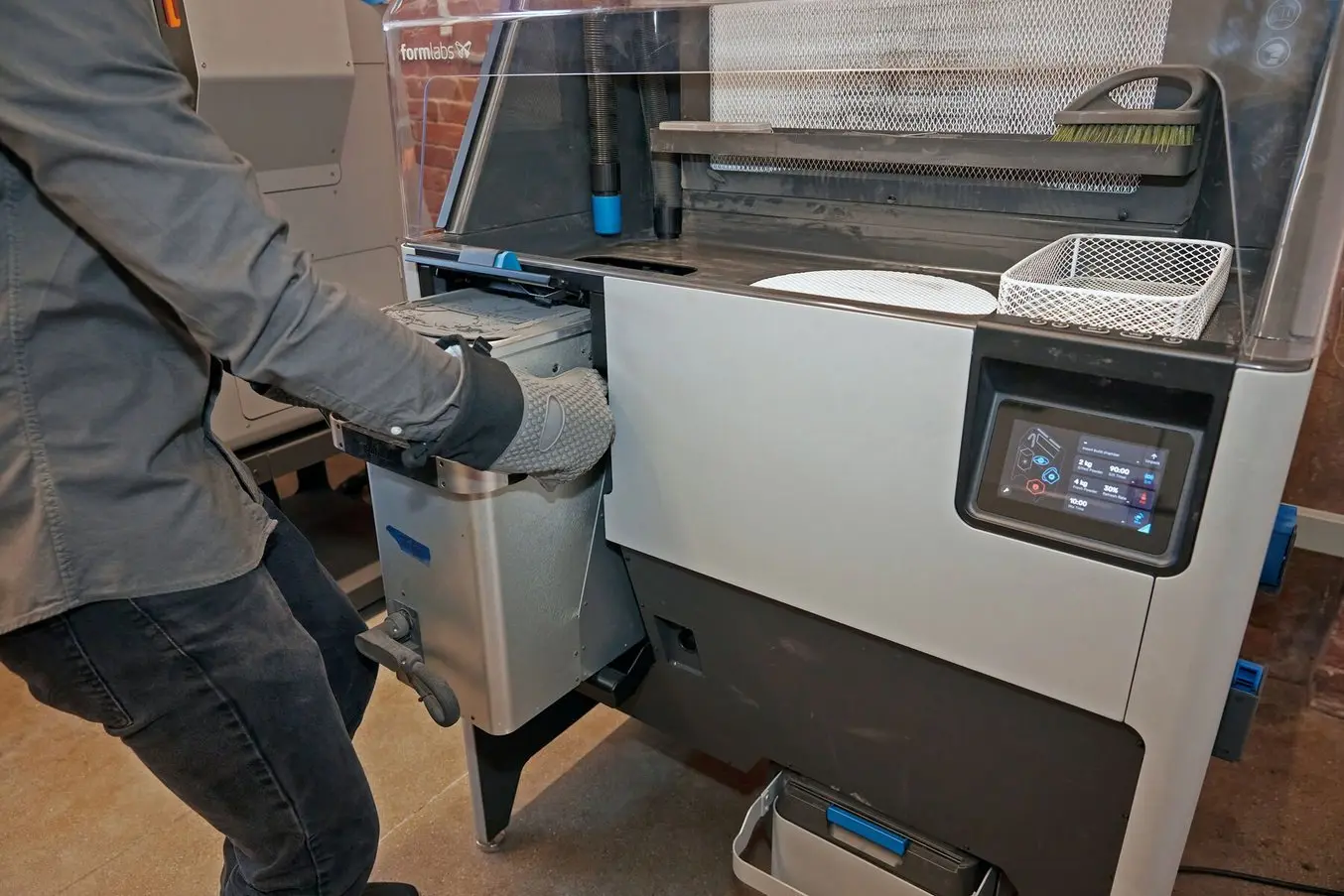
For Fuse Series printers, Fuse Sift completes the SLS printing workflow. It offers a safe and efficient system for extracting prints and recycling powder.
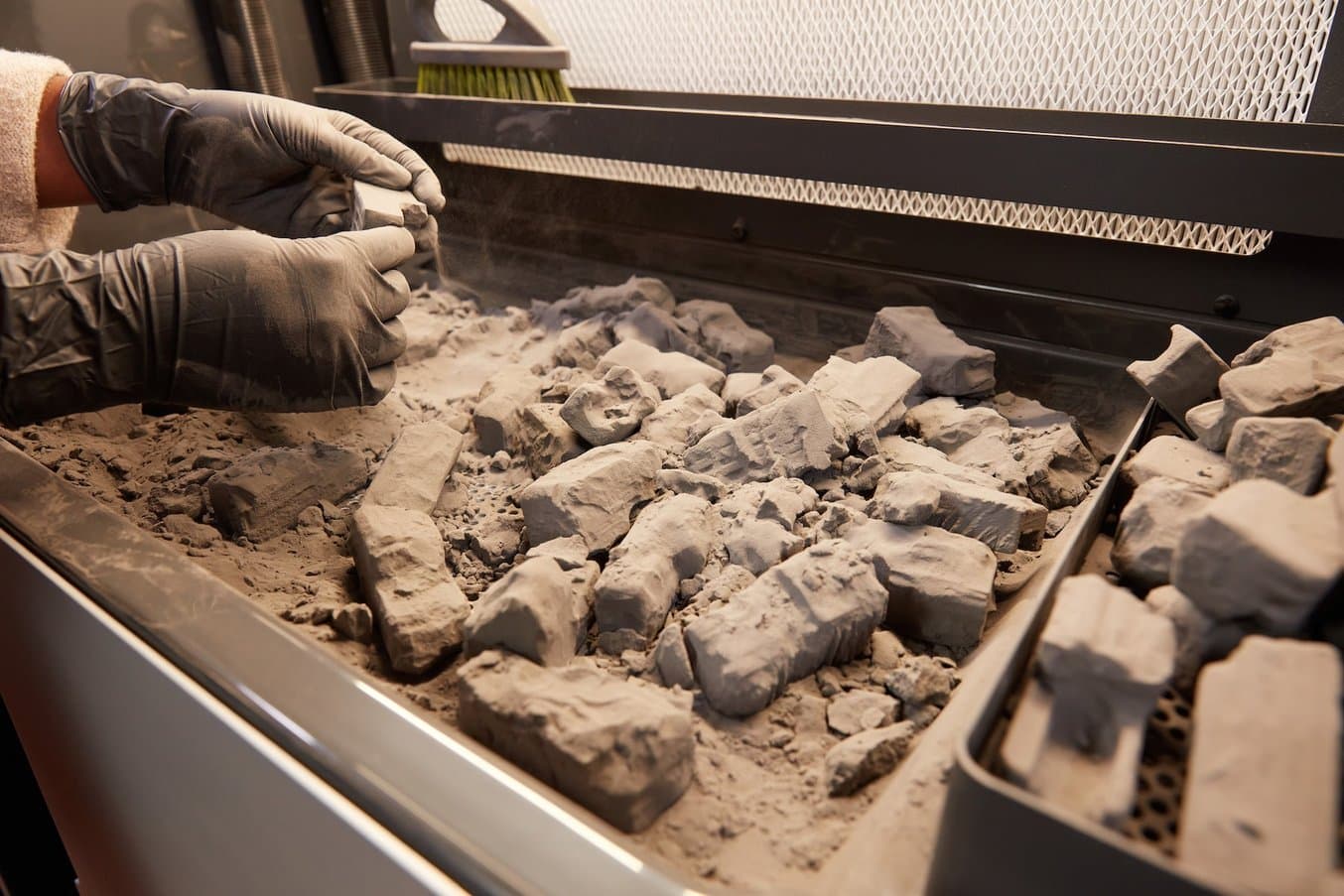
Fuse Sift can dispense and mix used and new powder automatically so you can reduce waste and control your powder supply.
5. Post-Processing
After extracting the parts, media blasting is a critical step to fully depowder SLS 3D printed parts and achieve a smooth, powder-free finish. This will remove the loose powder and clear the semi-sintered Surface Armor from your printed parts.
There are multiple manual and automated blasting solutions on the market for a variety of price ranges. The Formlabs Fuse Blast is the first affordable, automated media blasting solution that can complete either a Fuse Series SLS ecosystem or act as a printer-agnostic media blaster for other types of powder bed fusion 3D printers.
Media blasting can also drastically reduce the most time-consuming and physically demanding part of the SLS workflow. Adding Fuse Blast as a complement to Fuse Sift in the post-processing workflow reduces cleaning time to as little as 15 minutes overall — an 80% reduction in average hands-on labor time.
With Fuse Blast’s optional polishing system upgrade, you can go beyond cleaning to surface finishing with an all-in-one system. After polishing in Fuse Blast, parts are not only powder-free, but also smooth, scuff-resistant, and dye-ready with a professional semi-gloss finish in as little as 15 minutes. The concentrated beads of media effectively grind down the microscopic ridges that create the typical rough feel of SLS parts, smoothing the surface and removing much of the surface porosity.
Beyond the standard post-processing steps, there are a multitude of advanced SLS post-processing techniques to achieve a smoother surface finish, improve chemical resistance, reduce surface hardness, change color, make parts conductive, and more.
Read our article, where we discuss each option separately. If you are interested in stacking post-processing techniques to achieve a specific outcome, contact our team to speak with a specialist who can consult on your use case.
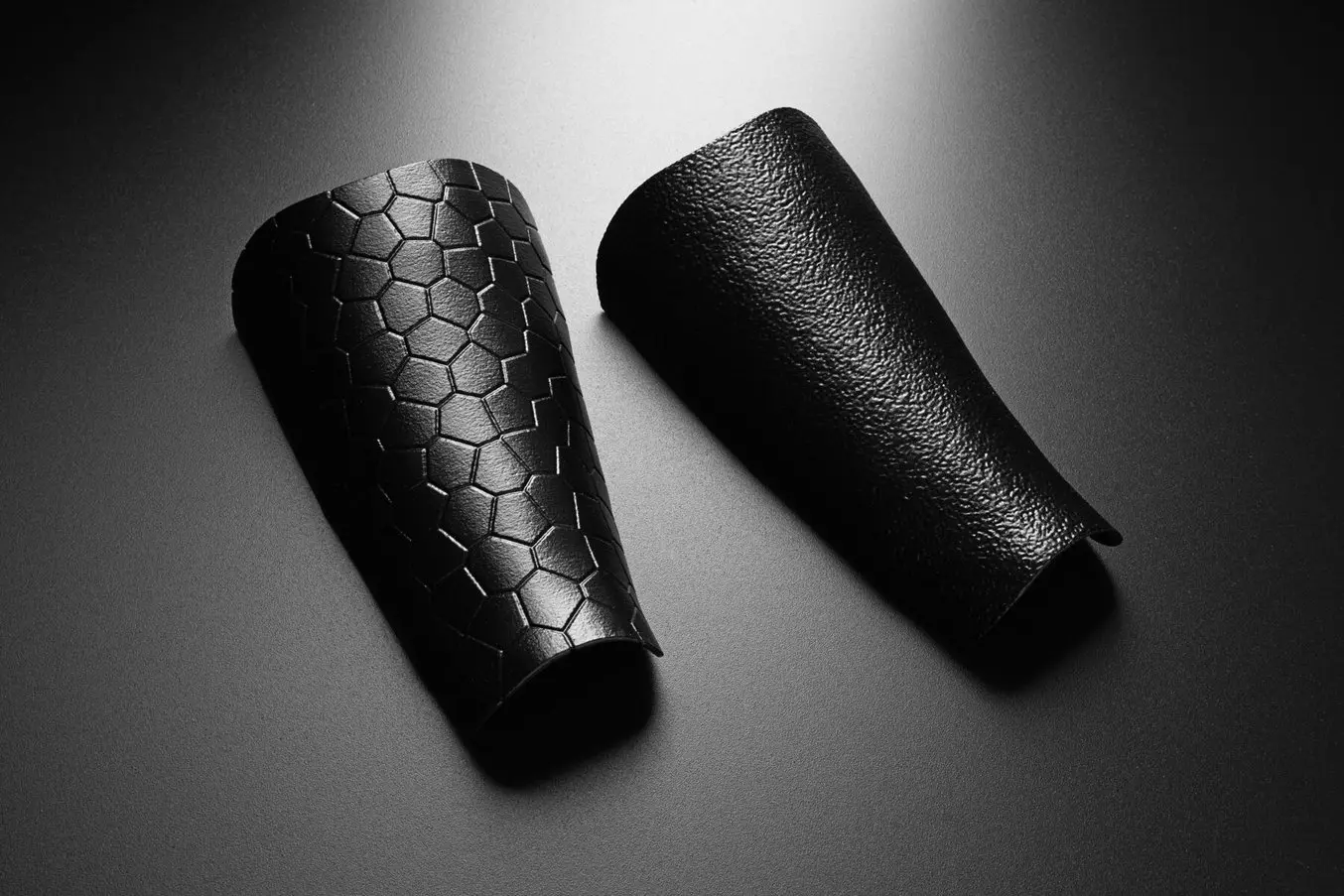
Through vapor smoothing, SLS parts can achieve surface quality and durability comparable to injection molded parts.
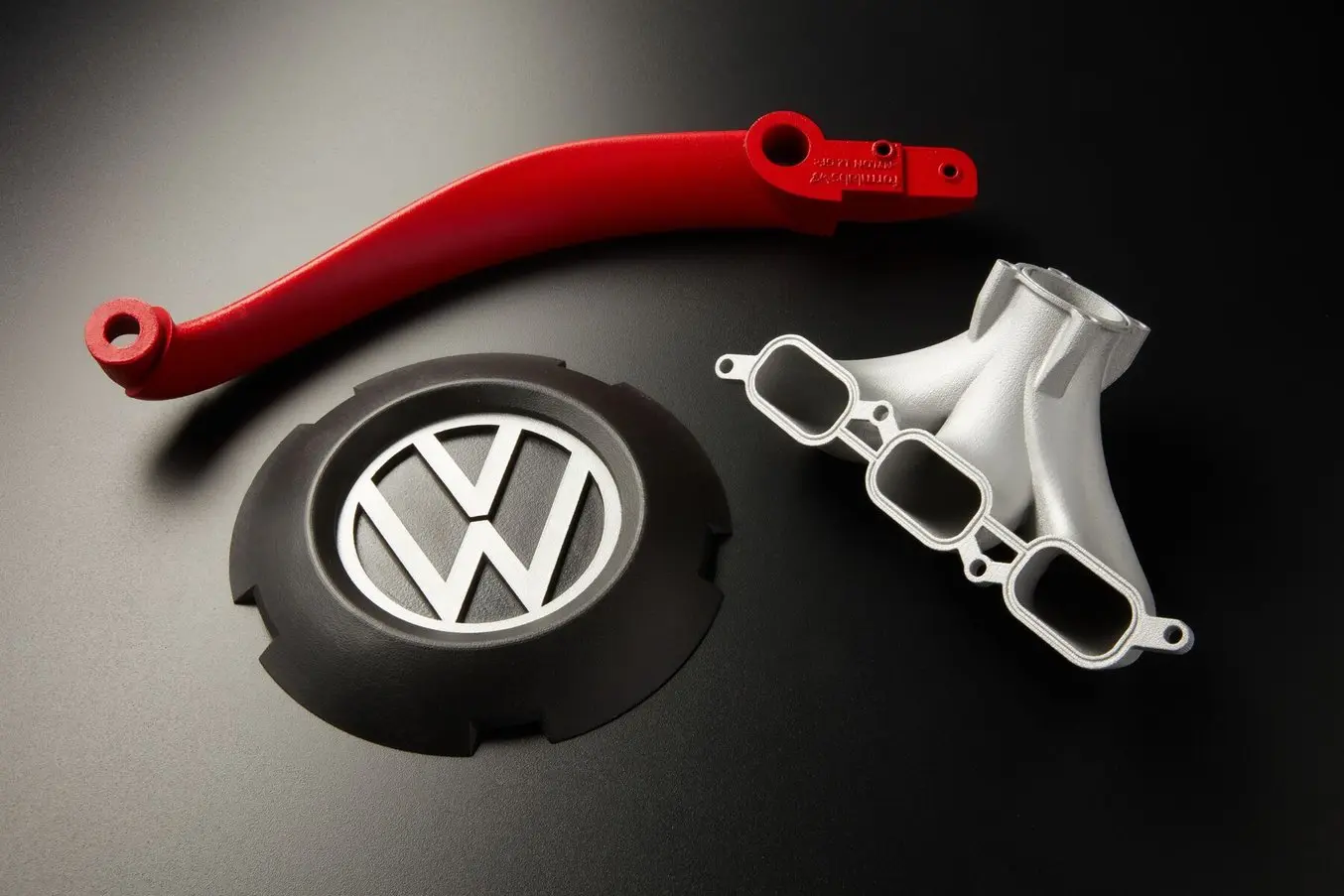
Ceramic coatings, like those made by Cerakote, provide both performance and aesthetic benefits, such as vibrant colors.
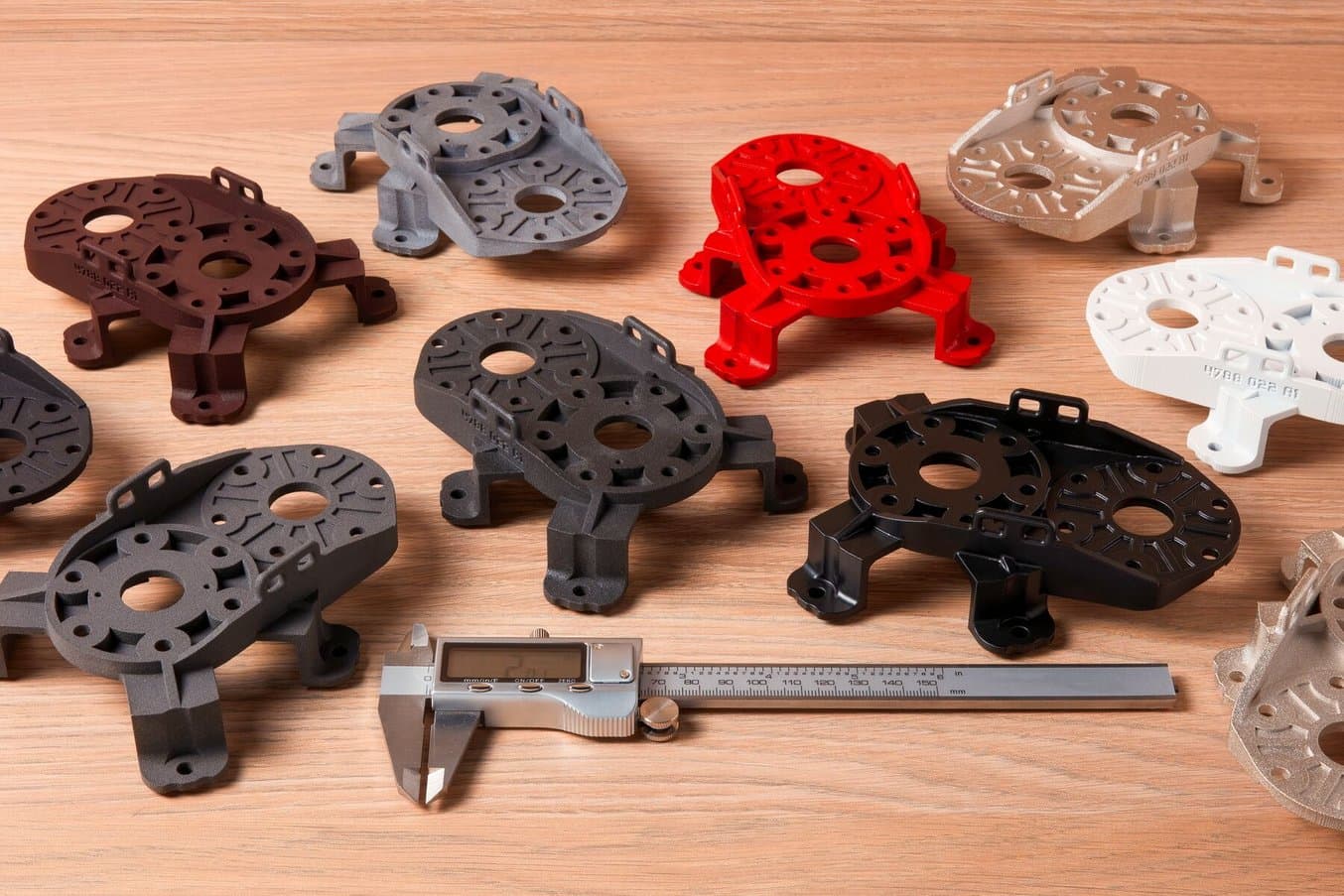
Advanced Post-Processing Techniques for 3D Printing
Watch this webinar to learn about 11+ advanced post-processing techniques for 3D printing, including Cerakote, electroplating, vapor smoothing, and more.
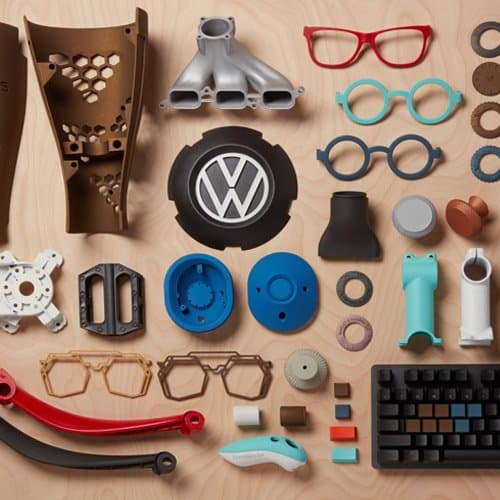
How to Create High Performance 3D Printed Parts with Advanced Ceramic Coatings
Watch our webinar now to discover how applying Cerakote ceramic coatings can enhance the performance of your 3D printed parts.
Why Choose SLS?
Engineers and manufacturers choose selective laser sintering for its design freedom, high productivity and throughput, low cost per part, and proven, end-use materials.
Design Freedom
Most additive manufacturing processes, such as stereolithography (SLA) and fused deposition modeling (FDM), require specialized support structures to fabricate designs with overhanging features.
Selective laser sintering does not require support structures because unsintered powder surrounds the parts during printing. SLS printing can produce previously impossible complex geometries, such as interlocking or moving parts, parts with interior components or channels, and other highly complex designs.
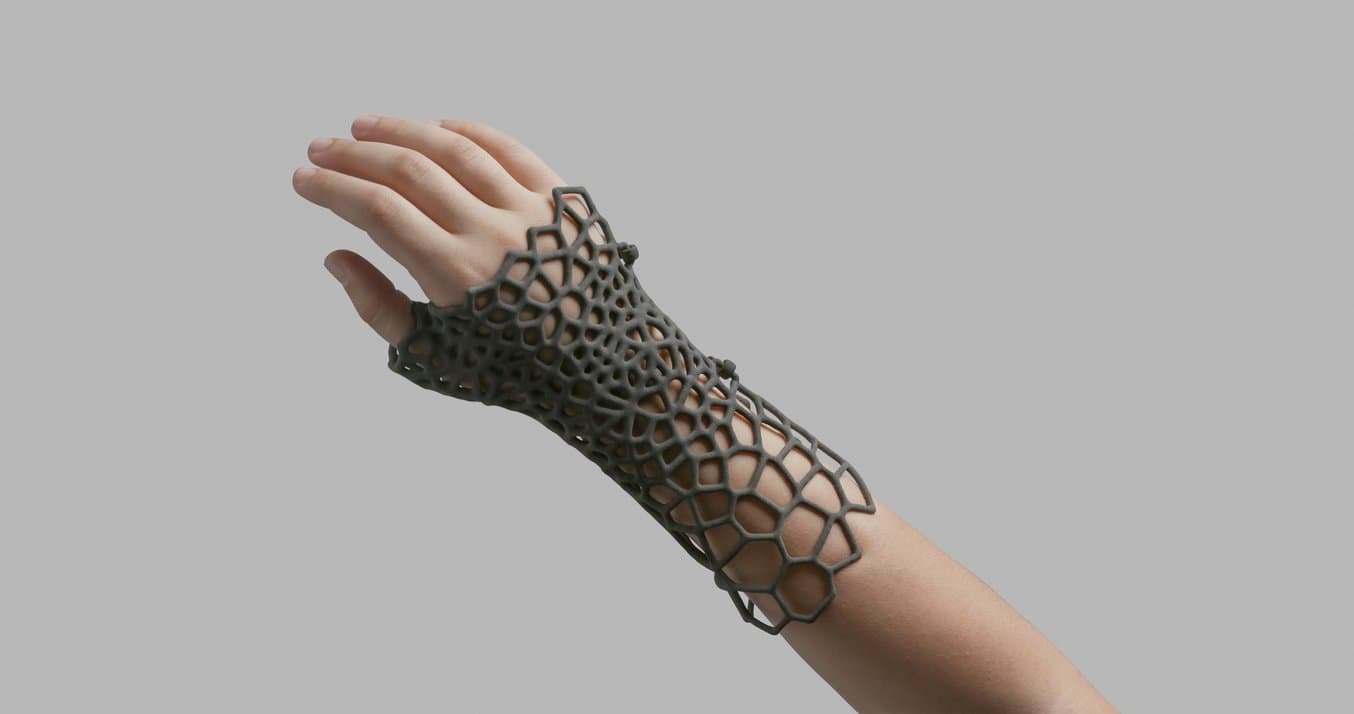
Hand splint designed with a complex pattern to reduce weight.
Engineers generally design parts with the capabilities of the final manufacturing process in mind, also known as design for manufacturing (DFM). When additive manufacturing is used for prototyping alone, it is limited to parts and designs that conventional manufacturing tools can ultimately reproduce during production.
As selective laser sintering becomes a viable rapid manufacturing method for an increasing number of end-use applications, it has the potential to unleash new possibilities for design and engineering. SLS 3D printers can produce complex geometries that are impossible or prohibitively costly to manufacture with traditional processes. SLS also empowers designers to consolidate complex assemblies that would normally require multiple parts into a single part. This helps alleviate weak joints and cuts down on assembly time.
Selective laser sintering can take generative design to its full potential by enabling lightweight designs that employ complex lattice structures impossible to manufacture with traditional methods.
High Productivity and Throughput
SLS printing is the fastest additive manufacturing technology for functional, durable prototypes and end-use parts. The lasers that fuse the powder have a much faster scanning speed and are more accurate than the layer deposition methods used in other processes like industrial FDM.
Multiple parts can be tightly arranged during printing to maximize the available build space in each machine. Operators use software to optimize each build for the highest productivity leaving only minimal clearance between parts.
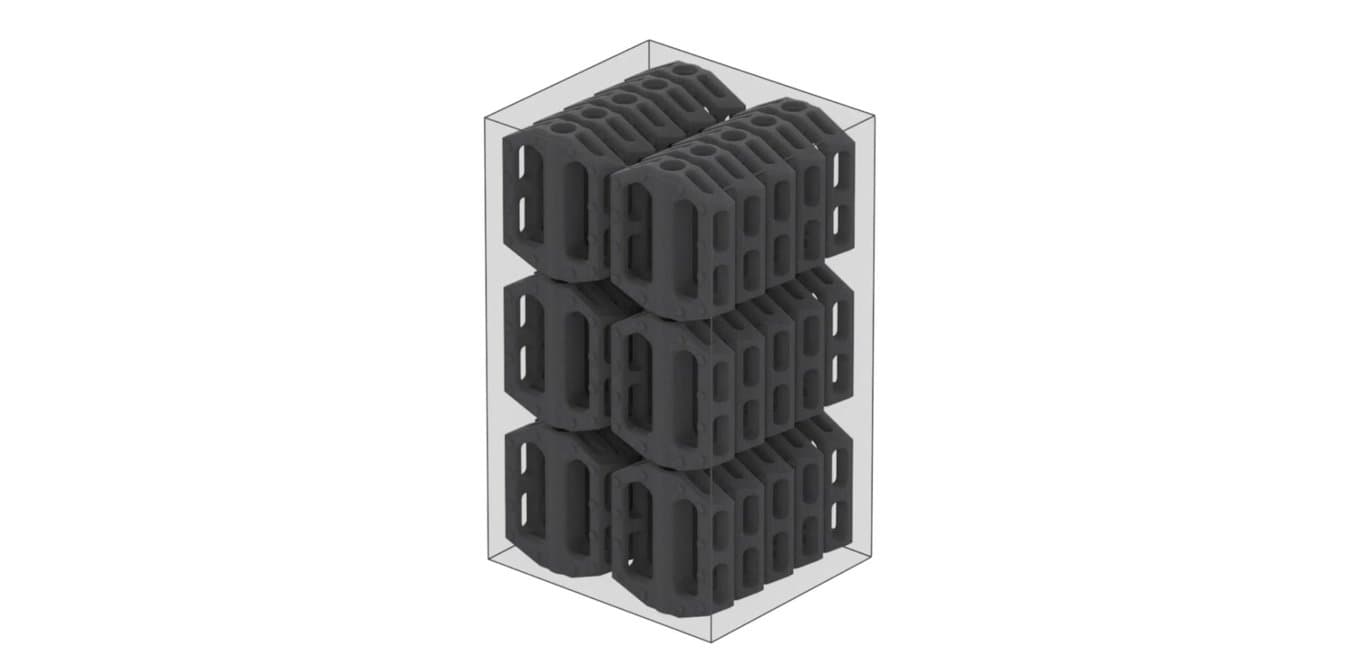
SLS allows operators to pack the build chamber with as many parts it can fit and print them without supports to save time in post-processing.
Proven, End-Use Materials
The key to SLS 3D printing’s functionality and versatility is the materials. Nylon, nylon composites, and TPU are proven, high-quality thermoplastics. Laser-sintered nylon parts have close to 100 percent density with mechanical properties comparable to parts created with conventional manufacturing methods like injection molding.
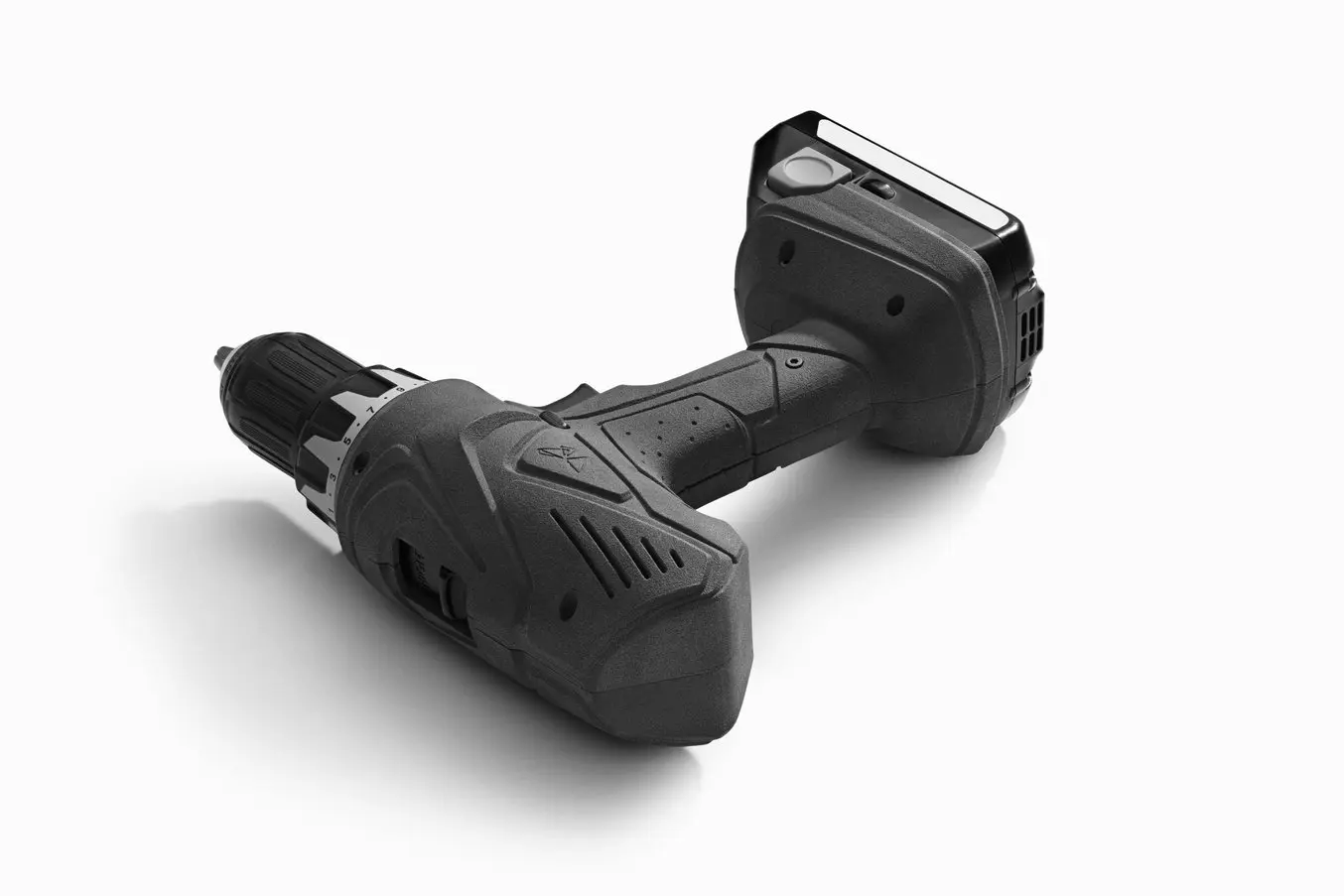
Drill assembly printed in Nylon 12 Powder. Nylon parts can be easily post-processed to achieve smooth, professional surface finishes.
SLS nylon and polypropylene are great substitutes for common injection molded plastics. They offer superior snap fits and mechanical joints compared to any other additive manufacturing technology. They are ideal for functional applications requiring plastic parts that will last where parts produced with other additive manufacturing methods would degrade and become brittle over time.
SLS TPU provides a great alternative to traditional molding workflows and a superior solution to other 3D printing methods for producing tough and long-lasting flexible parts. It is ideal for rapid prototyping, on-demand manufacturing aids, and custom or low-volume end-use parts.
Competitive Cost Per Part
Calculating cost per part usually requires accounting for equipment ownership, material, and labor costs:
-
Equipment ownership: The more parts a machine can produce over its lifetime, the lower the costs attributable to each individual part. Consequently, higher productivity leads to lower equipment ownership costs on a per-part basis. Given the fast scanning speed of the laser, the nesting of parts to maximize build capacity, and simple post-processing, SLS 3D printing offers the highest productivity and throughput of all plastic additive manufacturing techniques.
-
Material: While most 3D printing technologies use proprietary materials, nylon is a common thermoplastic produced in large quantities for industrial purposes, making it one of the least expensive raw materials for additive manufacturing. As SLS 3D printing doesn’t require support structures and allows for printing with recycled powder, the process produces minimal waste.
-
Labor: The Achilles heel of many 3D printing solutions is labor. Most processes have complex workflows that are hard to automate, which can substantially influence the cost per part. The simple post-processing workflow of SLS printing means less labor is required and the process is easy to scale.
An SLS 3D printer represents a substantial initial investment, but it can often recoup the initial investment even faster than smaller machines. Benchtop SLS significantly reduces this barrier to entry and also the per part cost for most applications.
Outsourcing production to service bureaus is recommended when your business requires 3D printing only occasionally, but it also comes with higher costs and long lead times. One of the greatest benefits of 3D printing is its speed compared to traditional manufacturing methods, which quickly diminishes when an outsourced part takes a week or even multiple weeks to arrive.
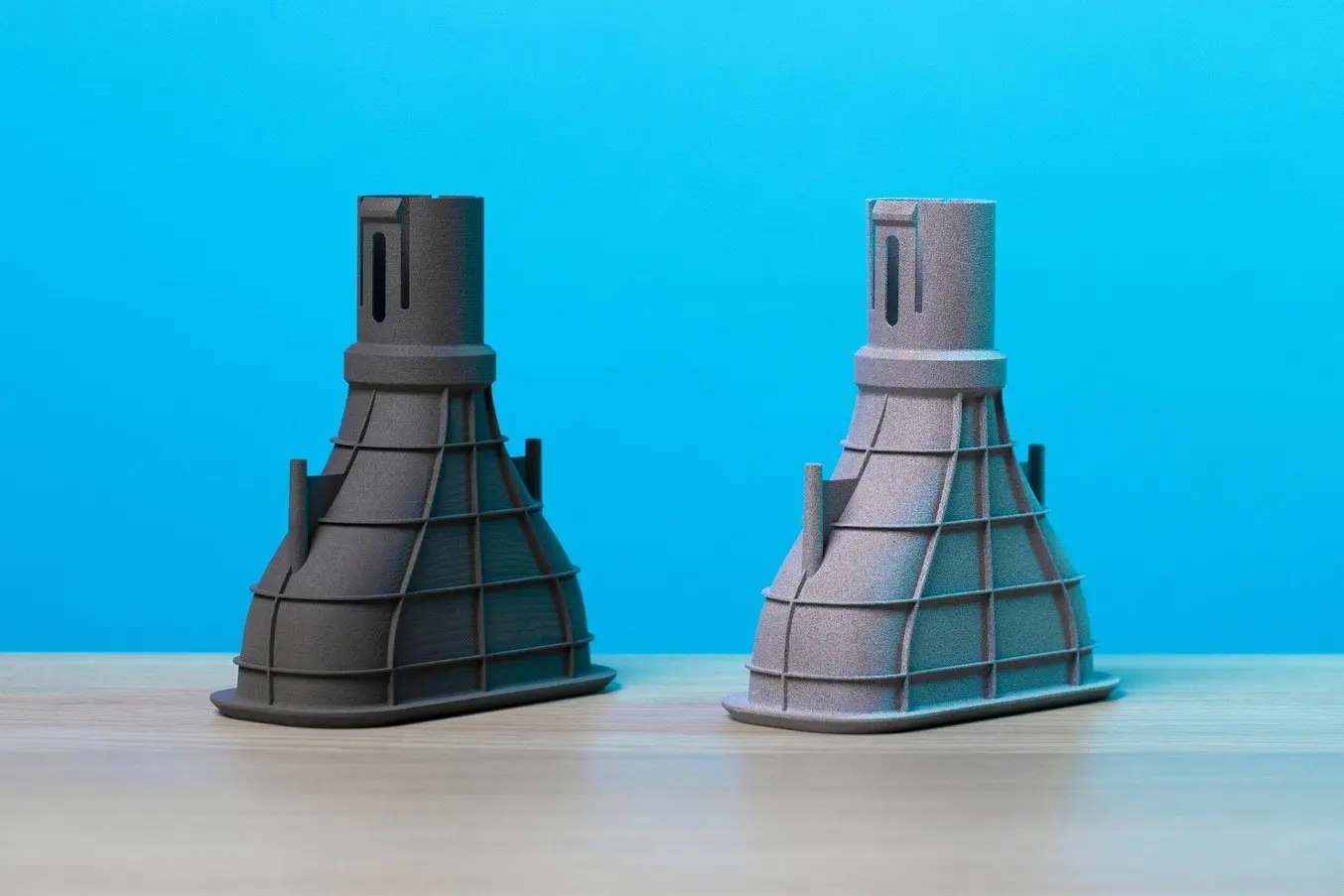
Automotive Manifold Prototype
Cost | Lead Time | |
Service Bureau | $118.33 | 7-10 days |
Fuse 1+ 30W | $9.02 | 13 hours |
Contact our team for a detailed analysis of your part files to find out where you can reduce costs and improve your workflow.
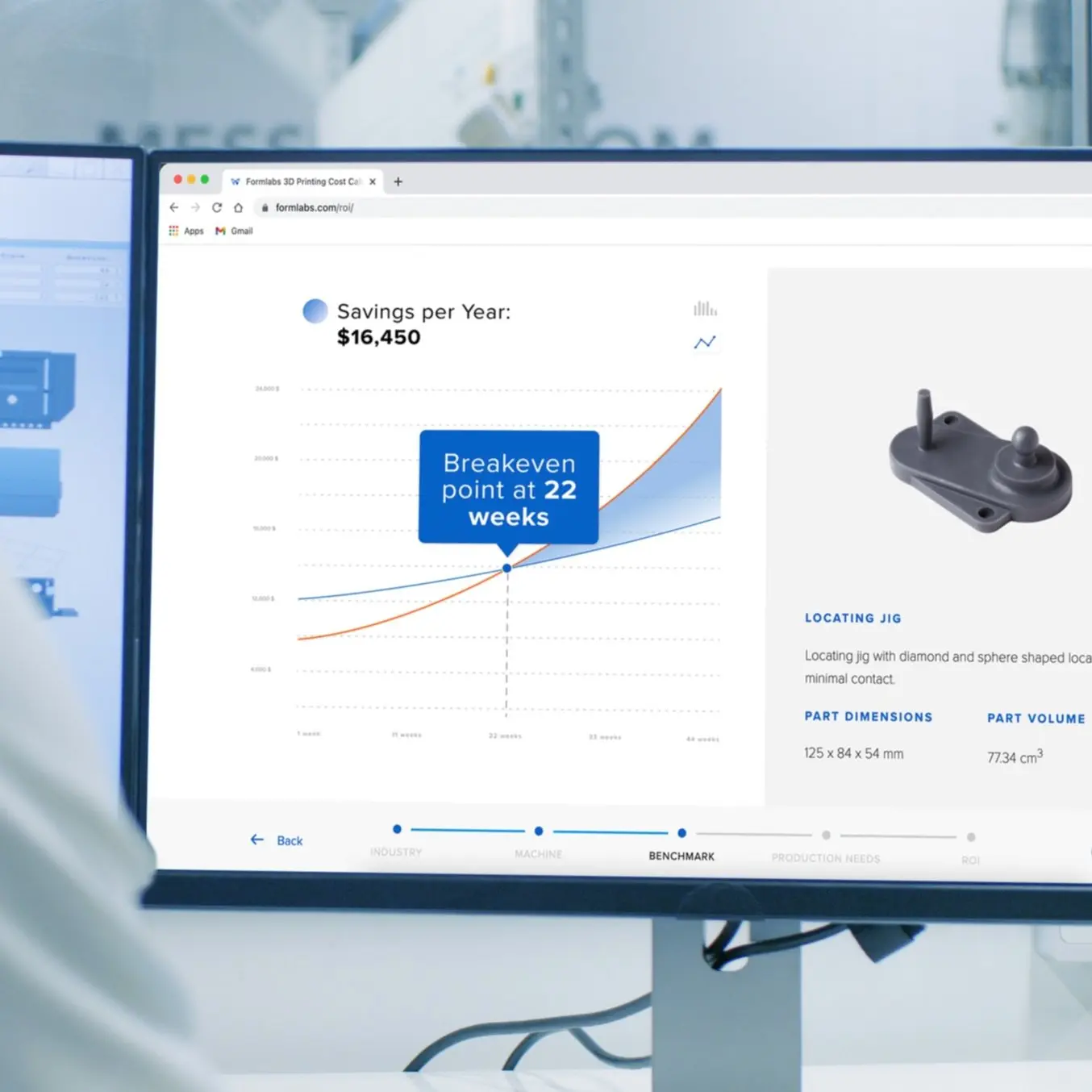
Calculate Your Time and Cost Savings
Try our interactive ROI tool to see how much time and cost you can save when 3D printing on Formlabs 3D printers.
Reduced Product Development Cycles
Selective laser sintering enables engineers to prototype parts early in the design cycle, then use the same machine and material to produce end-use parts. SLS 3D printing does not require the same expensive and time-consuming tooling as traditional manufacturing, so prototypes of parts and assemblies can be tested and easily modified over the course of a few days. This drastically reduces product development time.
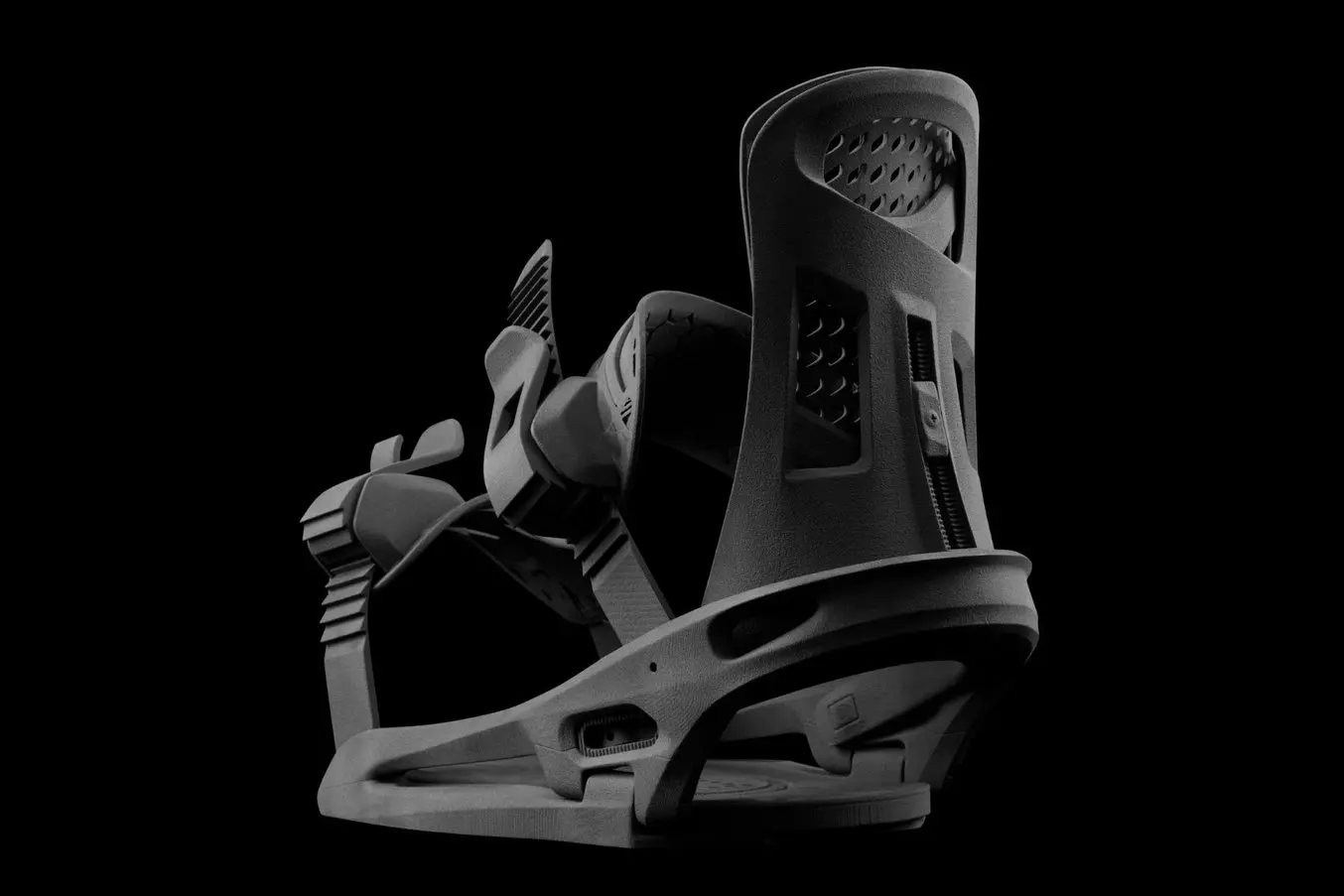
SLS 3D is ideal for creating durable, functional prototypes that are ready to undergo rigorous functional testing or to ship to customers as replacement parts or products that are ready to use.
Given its low cost per part and durable materials, SLS 3D printing is an economical way to produce complex, custom parts, or a series of small components for end products. In many cases, laser sintering is a cost-effective alternative to injection molding for limited-run or bridge manufacturing.
Meet the Fuse 1+ 30W SLS 3D Printer
Until now, industrial SLS 3D printers have been prohibitively costly for most businesses, with a single machine running over $200,000.
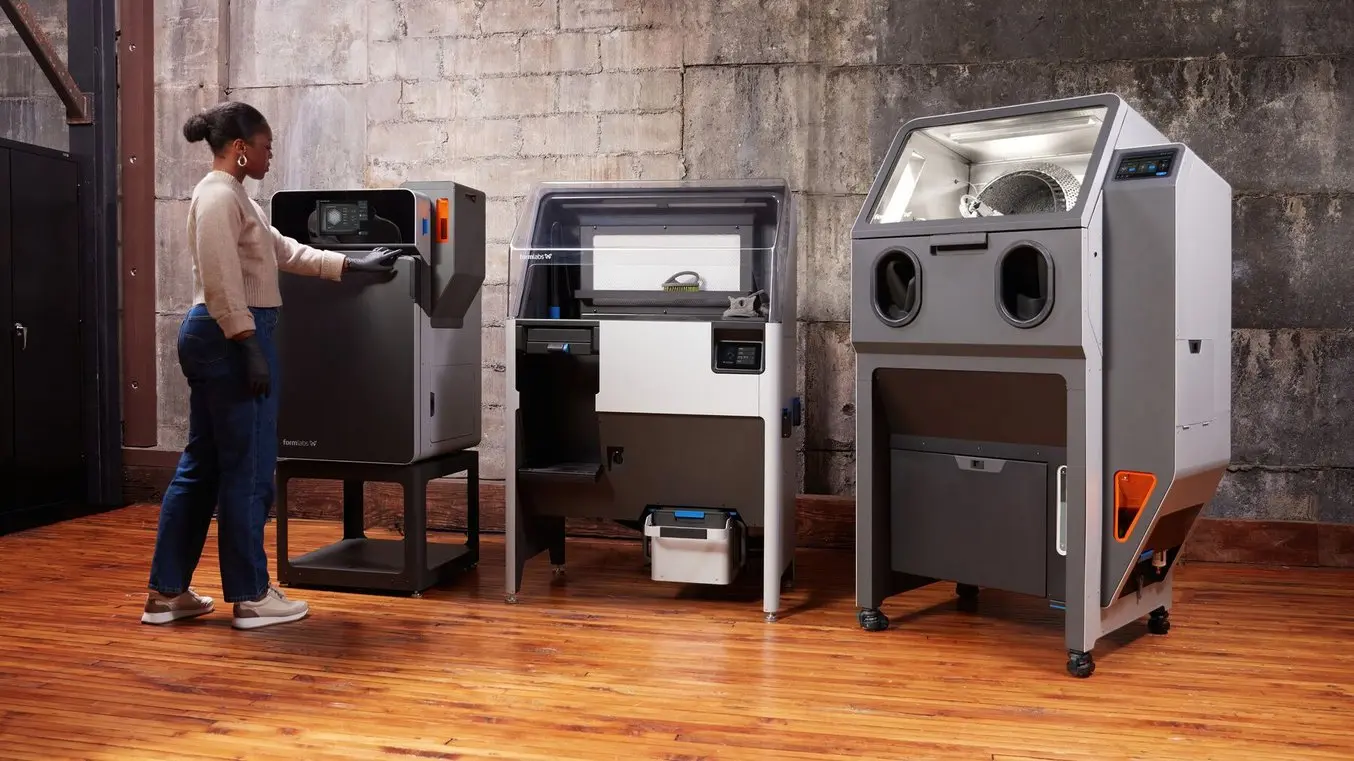
With the Fuse 1+ 30W, Formlabs is bringing the industrial power of selective laser sintering to the benchtop, offering high-performance materials at the lowest cost per part, with a compact footprint and simple workflow.
A new wave of independent manufacturing and prototyping starts now with the Fuse 1+ 30W.