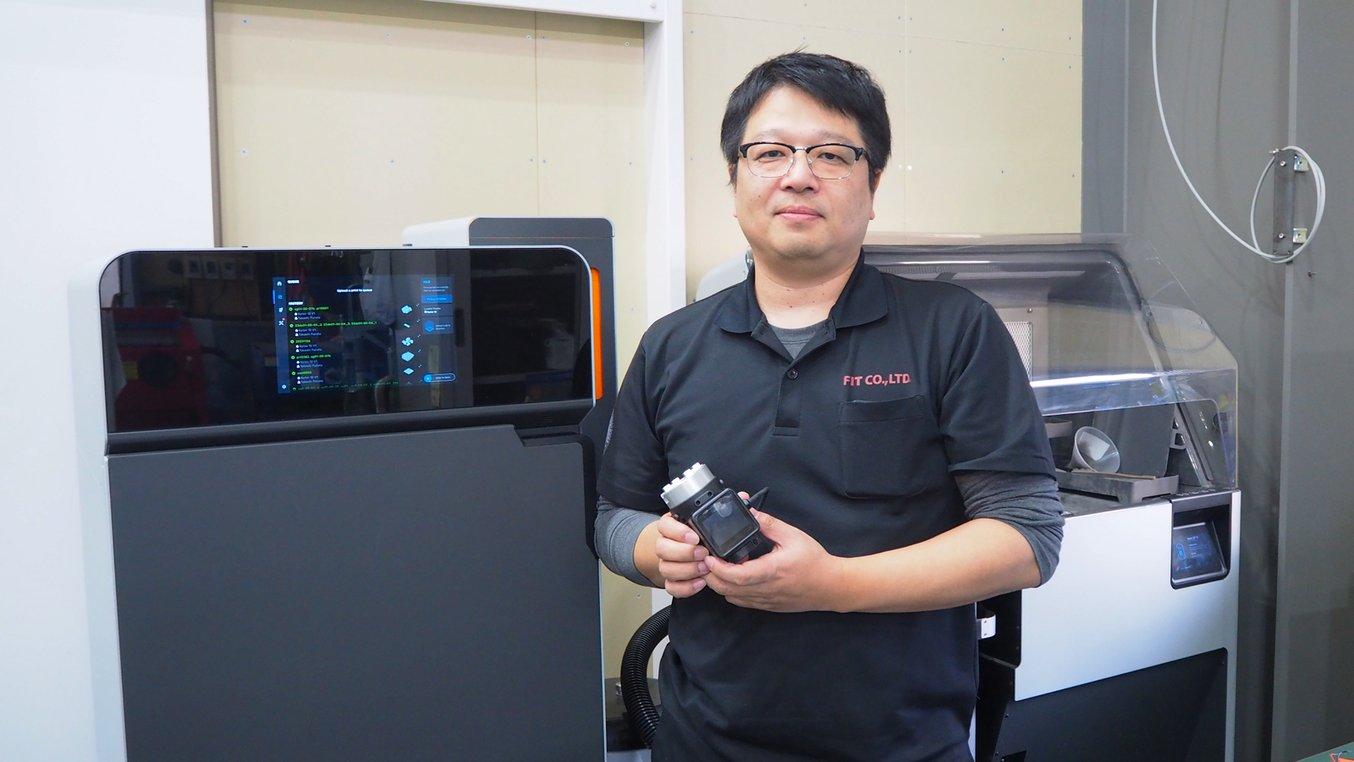
The successful integration of automation tools — both hardware and software — is key for manufacturers looking to remain successful in a globalized and hyper-competitive network.
Robotics solutions are one of the most complex parts of that equation. Their components need to be strong enough to manage the weight of the products they handle, yet lightweight enough to maneuver. Additionally, robotics must be customized to ensure they can manipulate differently shaped products dexterously.
FIT Co., based in Gifu, Japan found a solution that enabled the company to not only manufacture robotics components successfully, but to build an entire business around end-of-arm tooling (EOAT). FIT’s new robotics branch, ARMA, has leveraged the unique capabilities of Fuse Series’ selective laser sintering (SLS) technology to manufacture robotics components that can not only replace traditional metal end-of-arm tooling, but improve upon it.
End-of-Arm Tooling Requirements
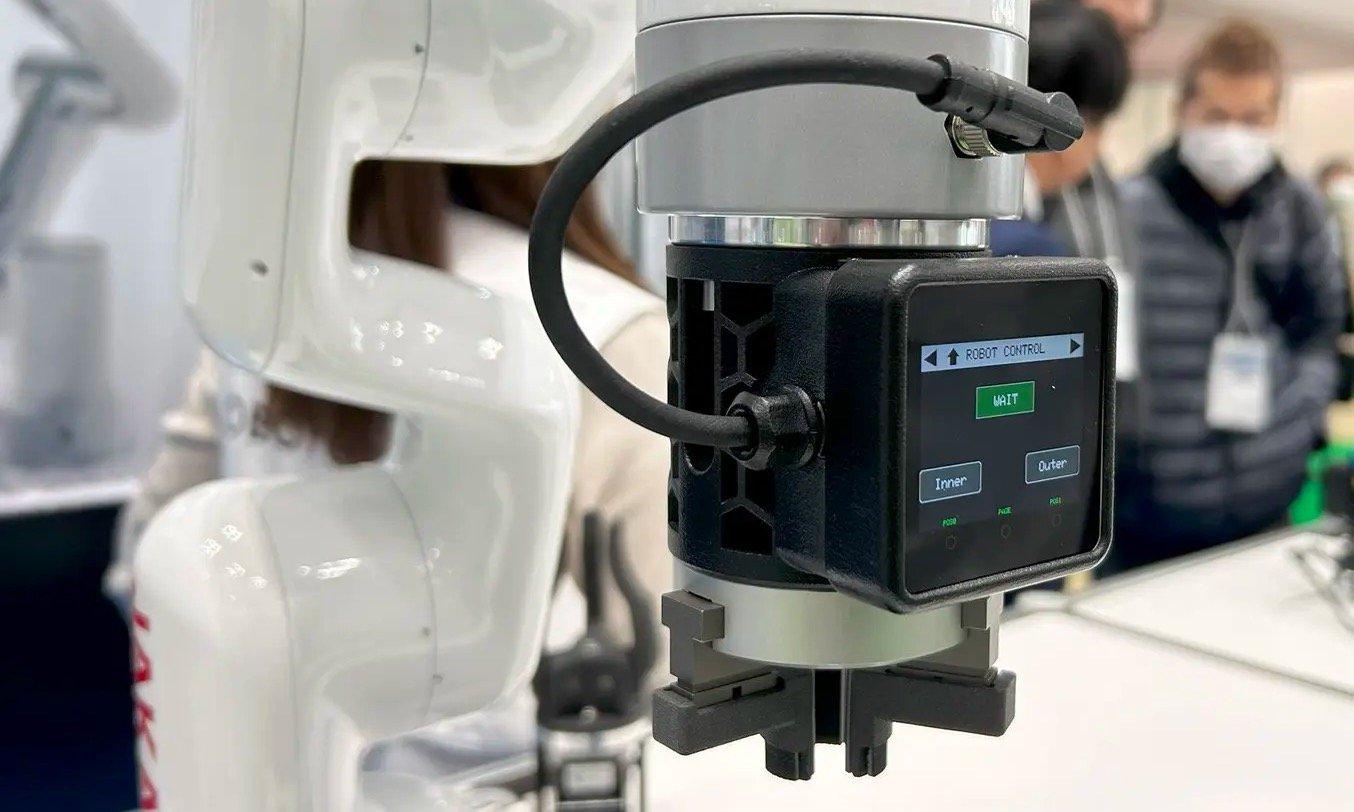
This gripper component, printed on ARMA's Fuse Series SLS 3D printer in Nylon 12 Powder, is strong, durable, and lightweight. 3D printed end-of-arm tooling components like this gripper enable companies to create on-demand robotics solutions for a variety of products with different shapes and weights.
As online shopping and a large warehouse distribution model have become the dominant way products reach consumers, pick-and-place robotics are in especially high demand. The wide range of products — hundreds of thousands of different SKUs — can each have different weights, shapes, and packaging types, making customized end-of-arm tooling for robots paramount. However, designing each customized piece involves complex engineering.
Though the robotics field is moving fast, they still often rely on traditional methods of metal fabrication for all components, including end-of-arm tooling. After all, these robots need to be strong, durable, and have the dexterity necessary to handle products of different shapes and sizes.
Traditional fabrication methods like machining or molding make it difficult to fulfill those requirements, so end-of-arm tooling is often made from multiple components that work as assemblies. The more components, the greater the risk of supply chain disruption for robotics manufacturers.
With SLS 3D printing, however, ARMA can design components with greater freedom. The self-supporting powder bed of the Fuse Series printers means parts can be built without support structures, and complex shapes like lattices, internal channels, honeycomb patterns, or generative designs are possible. By taking advantage of these design possibilities, ARMA optimizes parts to be lightweight while still maintaining strength and dexterity.
By using the Fuse Series and printing in Nylon 12 Powder, ARMA was able to reduce the weight of grippers and end effector parts by 40%. Both replacing metal components with nylon and the use of honeycomb structures within the parts contributed to the success of parts. “For ARMA’s grippers, the strength that Nylon 12 Powder offers is more than sufficient,” says Takashi Furuta, CEO of FIT and ARMA.
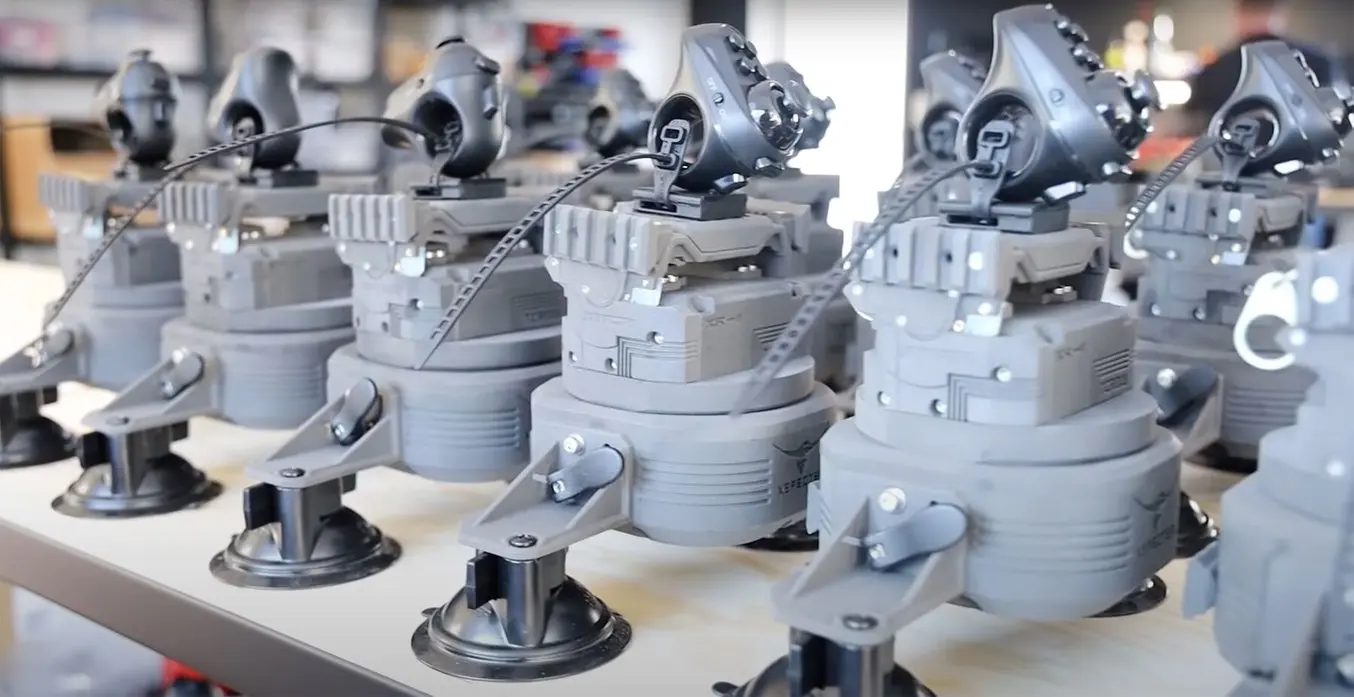
SLS for End-Use Production
3D printing for end-use production is not only possible, it's more affordable, agile, and scalable than ever with the Fuse SLS Ecosystem. Visit our SLS for Production page to compare production methods, learn about bulk powder pricing, and see production in action for 15 different manufacturers currently using the Fuse Series.
The Advantages of a Multi-Method Approach
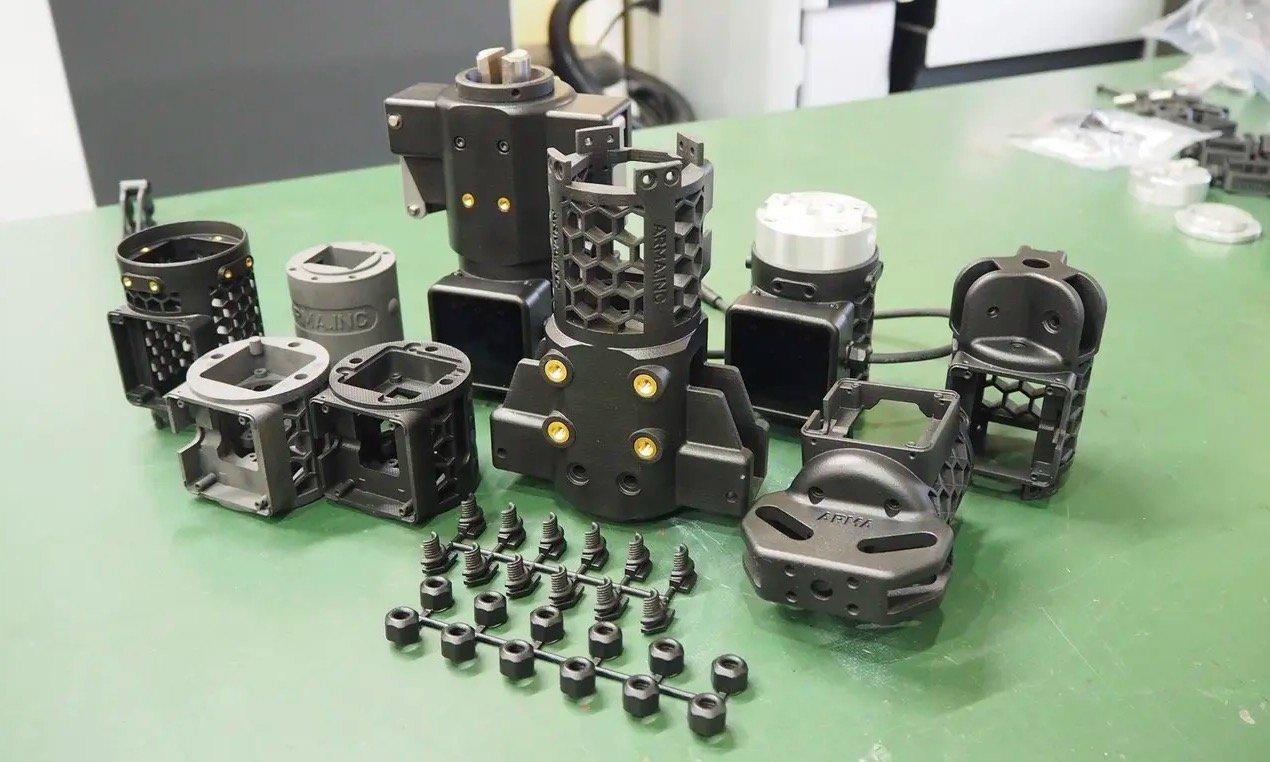
These components were all printed on the Fuse 1 in Nylon 12 Powder by Furuta’s team, and some were vapor smoothed to improve their aesthetics and durability, creating truly end-use quality products.
Furuta has found enormous success in combining traditional fabrication methods with modern tools, and has incorporated 3D printing into his company’s design and manufacturing processes since 2016. The company produces many metal components alongside various 3D printing technologies. Different 3D printing methods confer different advantages to the process. “We use FDM for quickly producing one item. For manufacturing in volume, we use the Fuse 1,” Furuta says.
When FIT began printing with the Fuse Series printer in 2022, he realized that the strength and quality of finished SLS parts would open up new opportunities for his business. “[Other technologies] can't match the quality of Fuse 1, especially when it comes to design freedom, isotropy, surface finish, and strength,” says Furuta.
The dimensional accuracy that the Fuse Series printers offer allows Furuta to easily design parts for assemblies because he has confidence in the reliability and consistent tolerancing of the Fuse Series. They combine their SLS printed Nylon 12 Powder parts with traditional metal components to create robotics systems that are lighter in weight than previous iterations, yet still incredibly strong and durable — all at a lower cost than relying on traditional machining for each part.
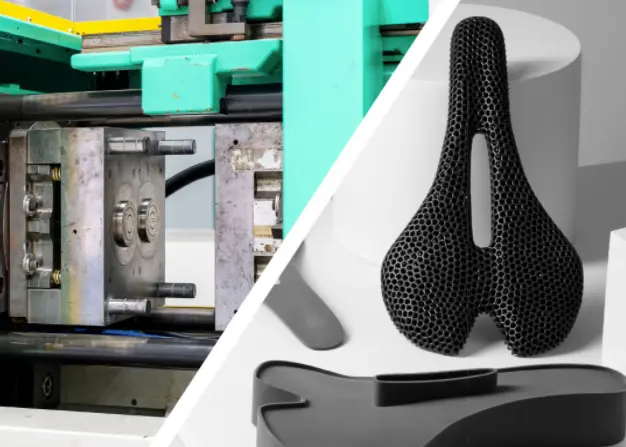
SLS 3D Printing vs. Injection Molding: When to Replace Molded Parts With 3D Printing?
This white paper showcases the cost-dynamics for real-life use cases, and presents guidelines for using SLS 3D printing, injection molding, or both.
Vapor Smoothing for Aesthetic Quality and Ease of Assembly
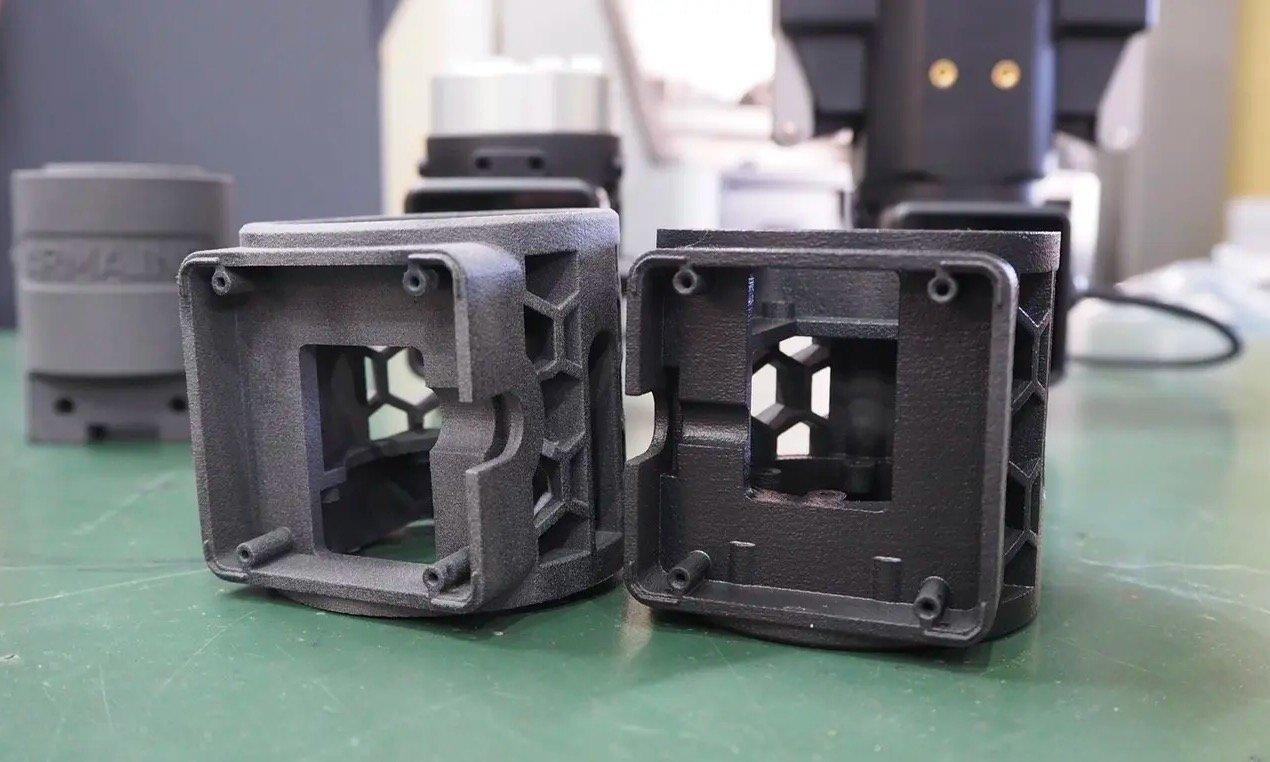
Vapor smoothing can improve the surface quality of SLS 3D printed parts as well as help make them more durable in end-use environments where they may be exposed to light, liquids, or chemicals.
SLS parts are end-use quality in terms of strength, but many customers prefer to use advanced post-processing methods to alter the surface of the parts, and remove some of the surface roughness that comes with SLS technology.
ARMA utilizes vapor smoothing, a technique where parts are bathed in a vaporized chemical solvent that creates a controlled chemical melt of the 3D printed material, filling minute cavities and forming a smooth, glossy shell around the part. Notably, the smoothing effect is not limited to line-of-sight geometries, making it suitable for complex parts with internal channels or other negative features. ARMA uses the AMT PostPro SF50 to achieve a smooth surface finish, making it even easier to integrate Nylon 12 Powder components into assemblies.
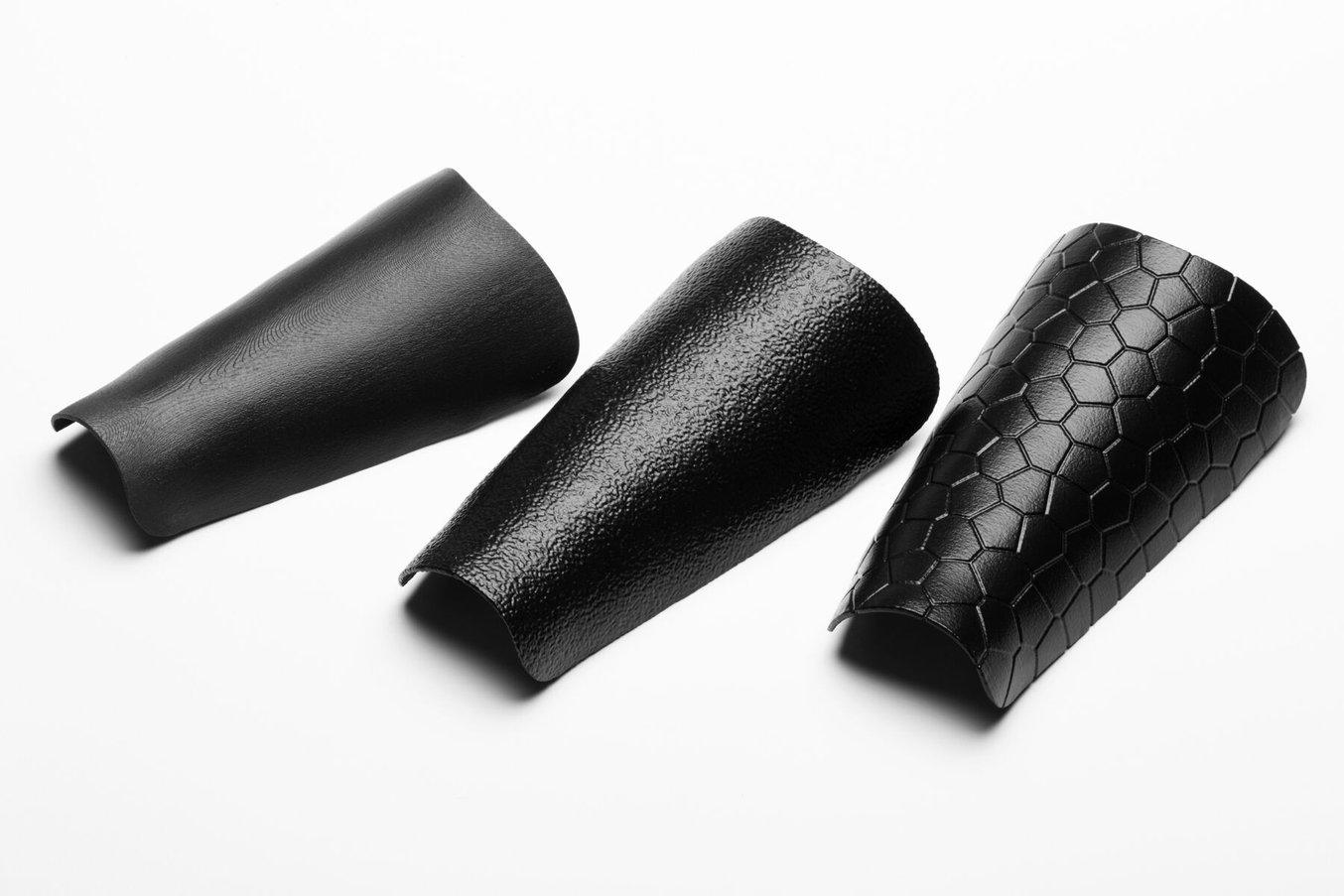
Enhancing the Surface Quality of SLS 3D Printed Parts With Vapor Smoothing: A Collaborative Study by Formlabs and AMT
In this white paper, we will review the considerations and benefits of vapor smoothing, report results from testing Formlabs SLS powders with AMT Vapor Smoothing System.
Reducing the Number of Components to Insulate the Supply Chain
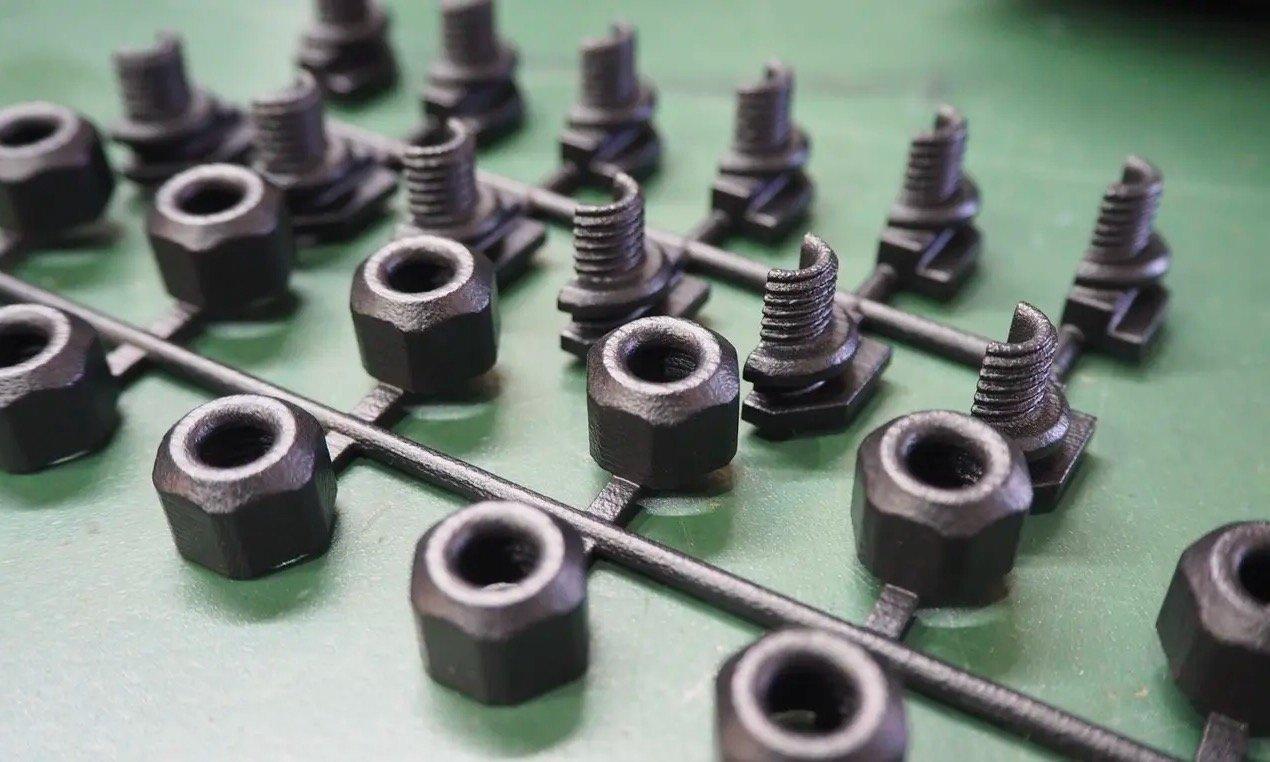
SLS printers have self-supporting print beds, so parts can be creatively designed as one piece, reducing the reliance on external contractors to supply multiple parts and insulating ARMA’s supply chain.
By limiting the number of individual components that make up an end-of-arm gripper or robotic component, ARMA can mitigate the risk of supply chain snarls affecting the production or distribution of their products. Bringing 3D printing in-house with the Fuse Series is one way they’re taking control over their means of production. “Grippers and end effectors we make on Fuse 1 are designed to be customized, as the needs vary depending on the company and production site,” says Furuta. If each of those custom orders requires the assembly of multiple components and the use of varied materials, lead times to deliver customer orders can quickly get out of control.
The Fuse SLS Ecosystem is compact, requires very little infrastructure, and can be used in an office or factory setting. Bringing it in-house as a production solution is possible — even for a company like ARMA that is just beginning to find their customer base. For low volume production where mass manufacturing methods are too costly and complicated, in-house SLS 3D printing is the perfect solution.
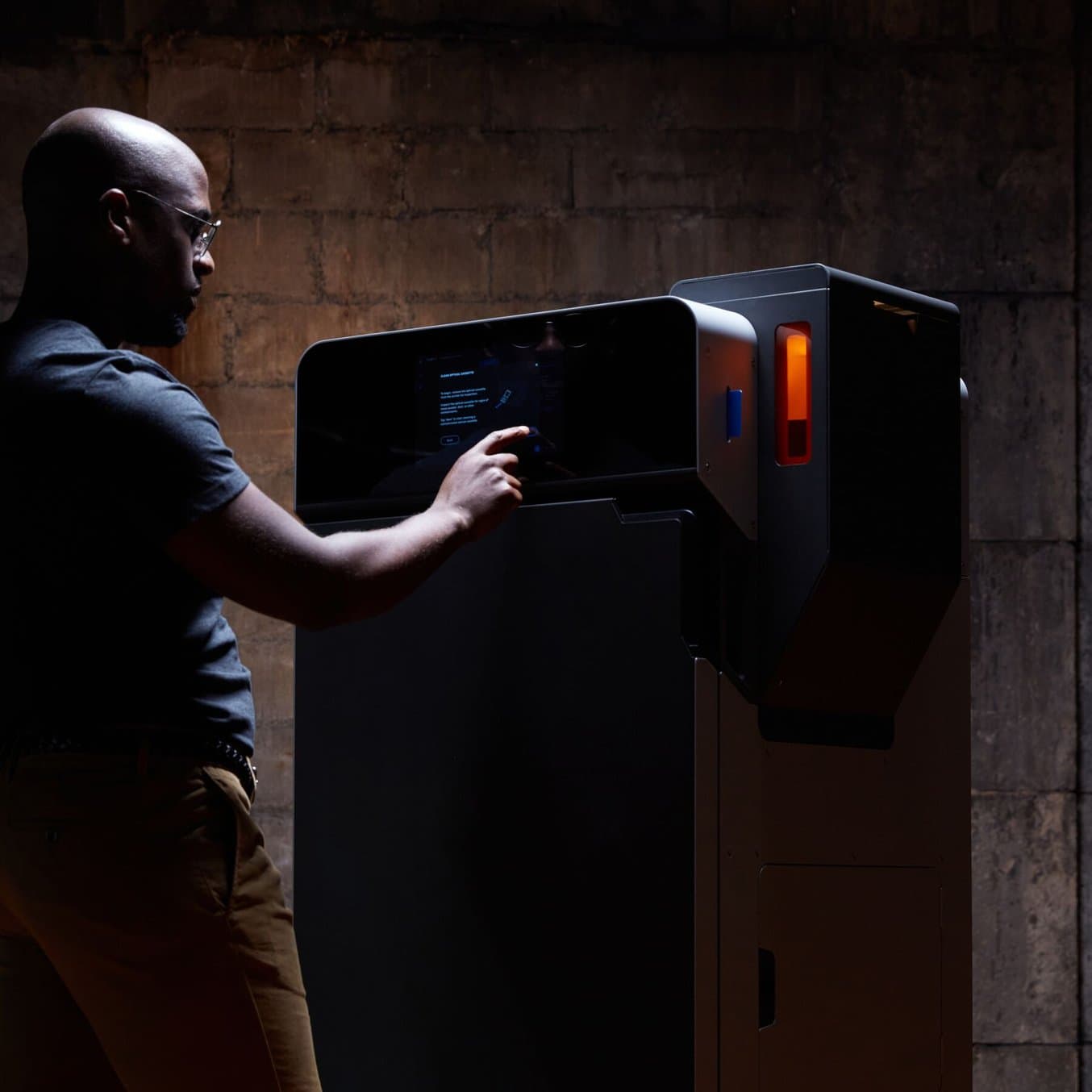
Outsourcing vs. In-House: When Does it Make Sense to Bring SLS 3D Printing In-House?
In this white paper, we evaluate the value proposition of bringing SLS 3D printers in-house, in comparison with outsourcing SLS parts from a service bureau.
Functionality and Aesthetics Combine at ARMA
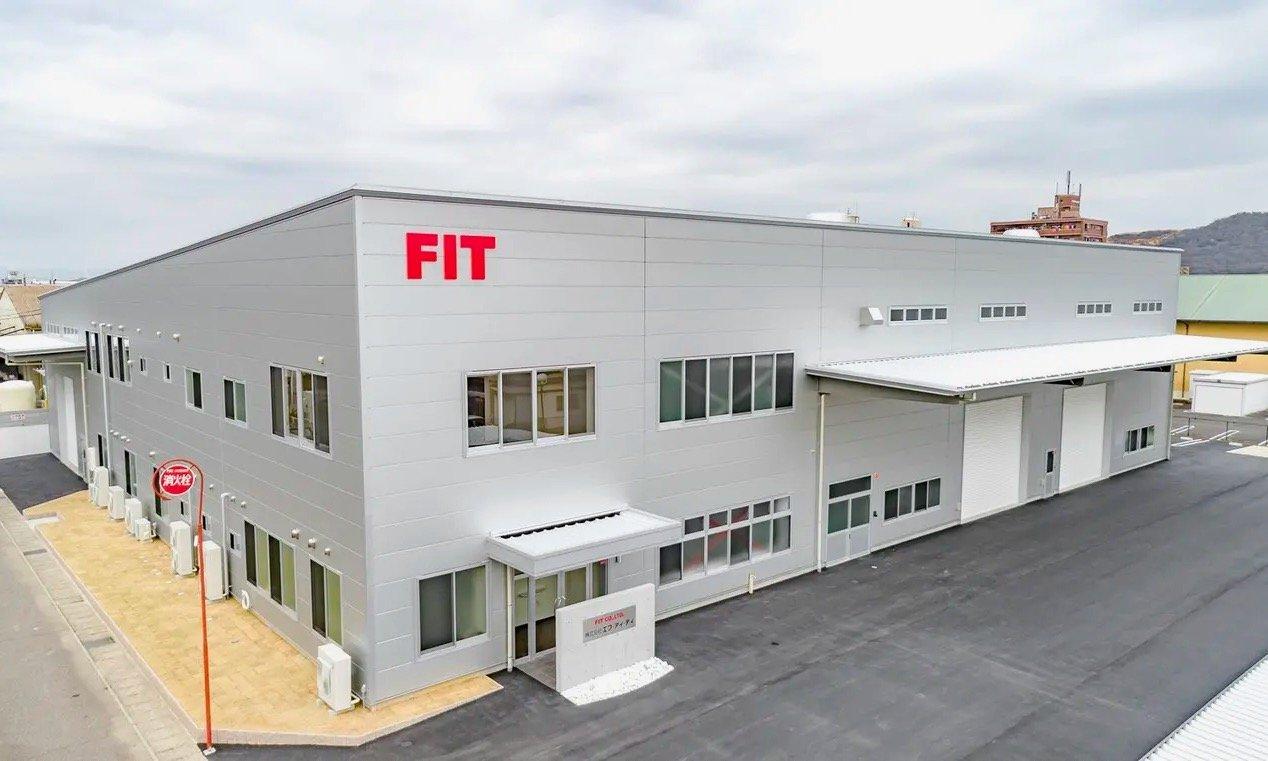
Integrating the Fuse Series into FIT’s manufacturing workflow helped them grow so successfully that they were able to dedicate an entire division, ARMA, to the manufacturing of these end-of-arm tooling components.
Furuta, who is typically reserved, had a smile on his face when asked about the Fuse, saying simply, “It’s fun.” The removal of design limitations with SLS technology, and the streamlined industrial power of the entire SLS ecosystem, are appealing to Furuta, who spends his energy turning clunky components into smoothly integrated and high-performancing robotics systems. With the Fuse, Furuta says he is looking to continue “pursuing functionality and eliminating unnecessary features.”
SLS 3D printing is opening up possibilities for manufacturing strong, durable, end-use parts that can replace metal components. By bringing the means of production in-house and controlling your supply chain, you can be more agile, protected from risk, and better positioned to capture new opportunities.
Explore manufacturing applications powered 3D printing or learn more about Fuse Series SLS 3D printers and post-processing solutions.