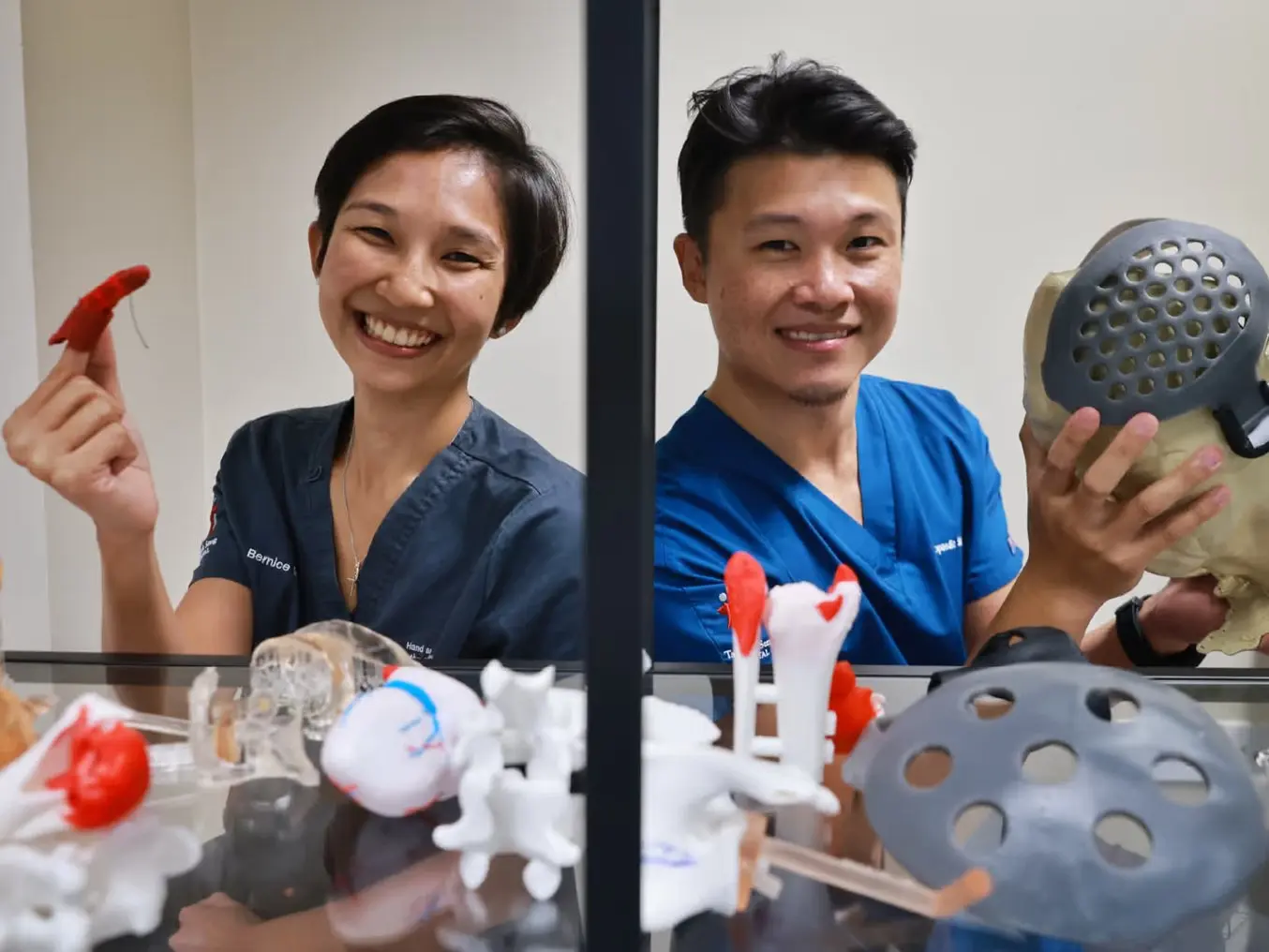
In the pursuit of patient-centric care, planning, and treatment, healthcare providers and hospitals have been increasingly turning to 3D printing as a valuable resource to elevate training, optimize pre-surgical preparation, and craft personalized surgical instruments and guides. For Tan Tock Seng Hospital (TTSH) in Singapore, the versatility of resins used for 3D printing has helped create realistic prostheses.
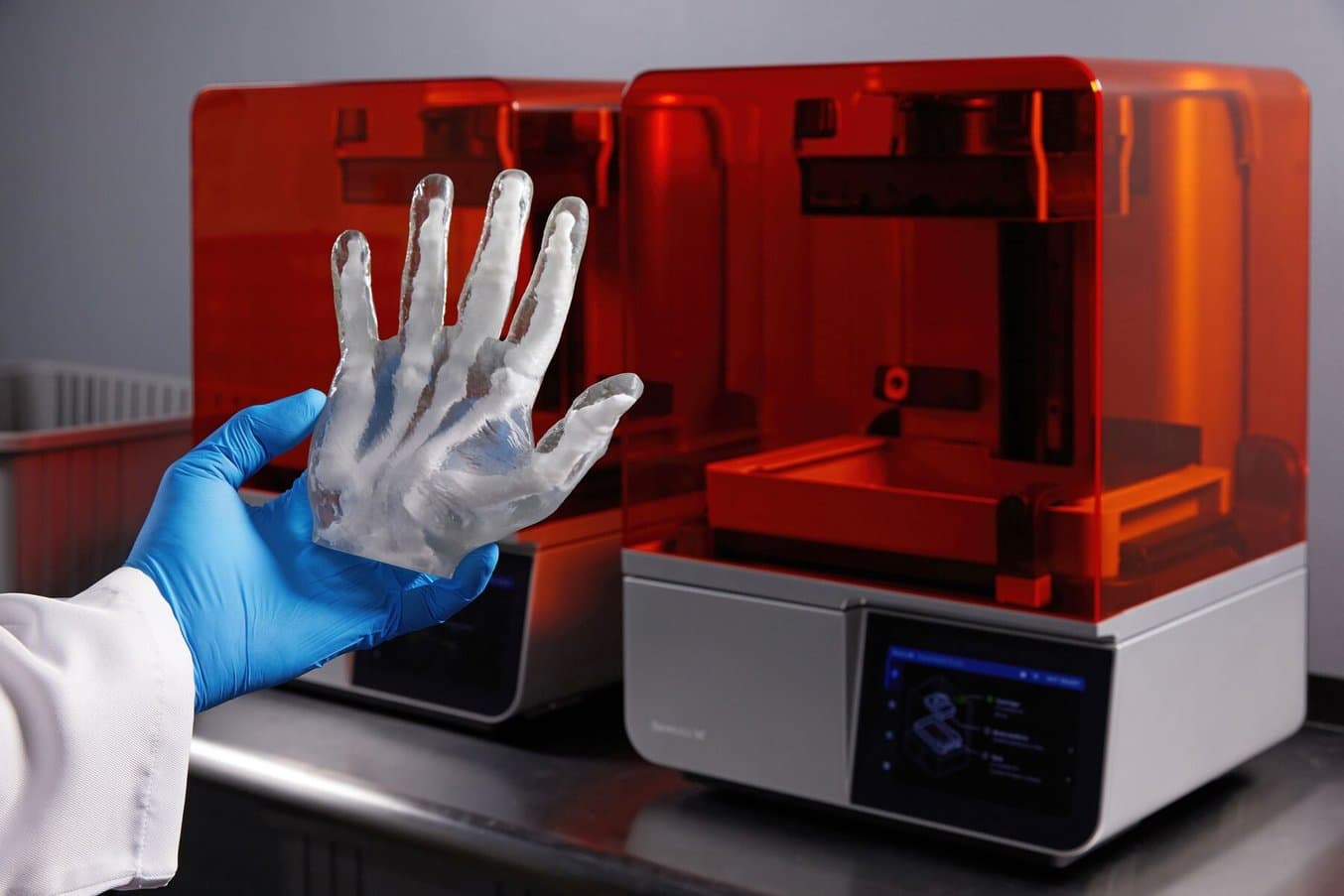
Formlabs Biocompatible Resins: A Comprehensive Guide To Choosing the Right Material
Formlabs currently offers more than 40 unique materials for stereolithography (SLA) 3D printing. This paper helps users compare and contrast our biocompatible offerings, and determine the best fit for their medical applications.
Transforming Patient Care at Tan Tock Seng Hospital’s Medical 3D Printing Centre
Emergency surgeries, a frequent occurrence in hospitals, demand swift response times that often render reliance on third-party vendors for anatomical models and surgical guides impractical, especially for larger institutions, making the dependence on third-party vendors for anatomical models and surgical guides less practical, particularly for larger institutions. This prompted TTSH to establish an in-house 3D printing lab, guaranteeing timely and accurate solutions for their patients.
“In the past, to obtain a 3D print or a 3D model, we had to look for a vendor. Finding vendors is not easy. And, with clinicians already having a busy schedule, it made things difficult.”
Dr. Michael Yam, Orthopaedic Surgeon and Head Clinical Director, TTSH Medical 3D Printing Centre
The Centre functions as a clinical service for the hospital, its departments, and patients. While officially launched in November 2022, it has been operational since 2020. It 3D prints models of patients' organs from medical scans, enabling attending doctors to provide clearer explanations of conditions and necessary treatments. Surgeons also use the centre to print jigs or custom tools to aid in surgery, or models to practice complex procedures on.
The Centre is well equipped with Formlabs’ Form 3B+ and Form 3BL 3D printers as well as a variety of biocompatible materials.
“Formlabs’ 3D printers work well with biocompatible resin, which is useful for our surgical procedures. It improves the accuracy and precision of our surgery. This has made our lives easy because if we need to do surgery on a patient and we need the scans soon, the in-house facility will take care of this process and ensure it’s done quickly.”
Dr. Michael Yam, Orthopaedic Surgeon and Head Clinical Director, TTSH Medical 3D Printing Centre
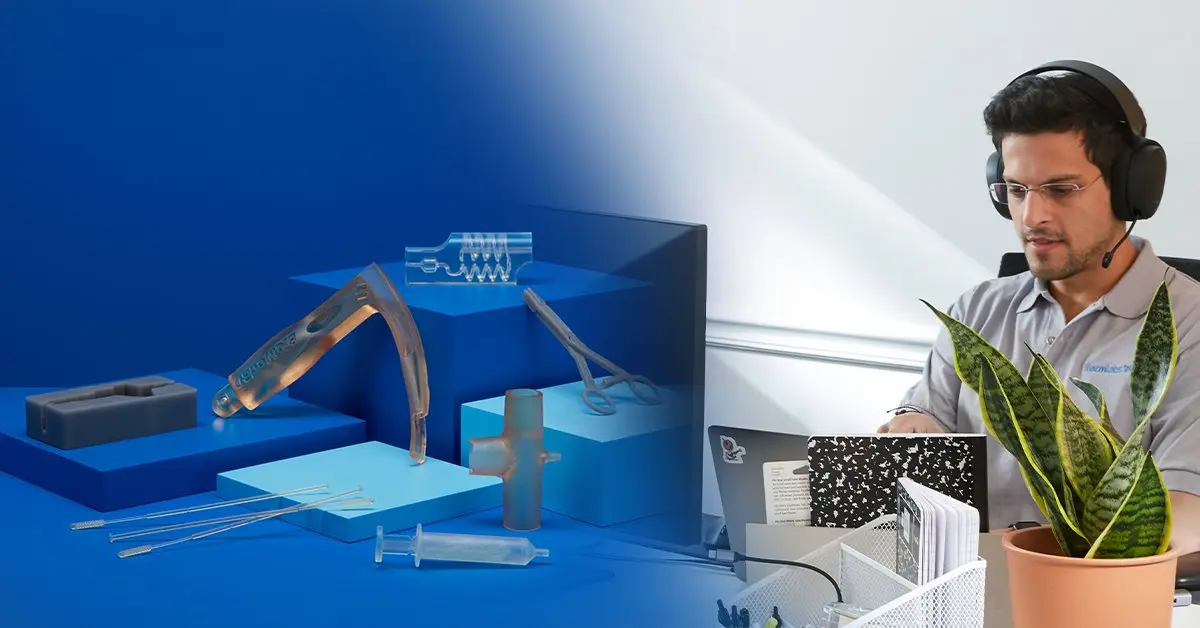
Talk to Our Medical Sales Team
Whether you need to make patient-matched surgical tools or are prototyping for a cardiac medical device, we’re here to help. Formlabs Medical team are dedicated specialists who know exactly how to support you and your company's needs.
The Challenge
In 2022, while battling skin cancer, 73-year-old J. F. Lian had most of his external nose removed. Lian said he had come to terms with living with a hole in the middle of his face and was pleasantly surprised when TTSH offered him the chance to receive a 3D printed nose that would be practically identical to the original organ. 3D printing a prosthetic nose for Lian was a pilot project for the centre.
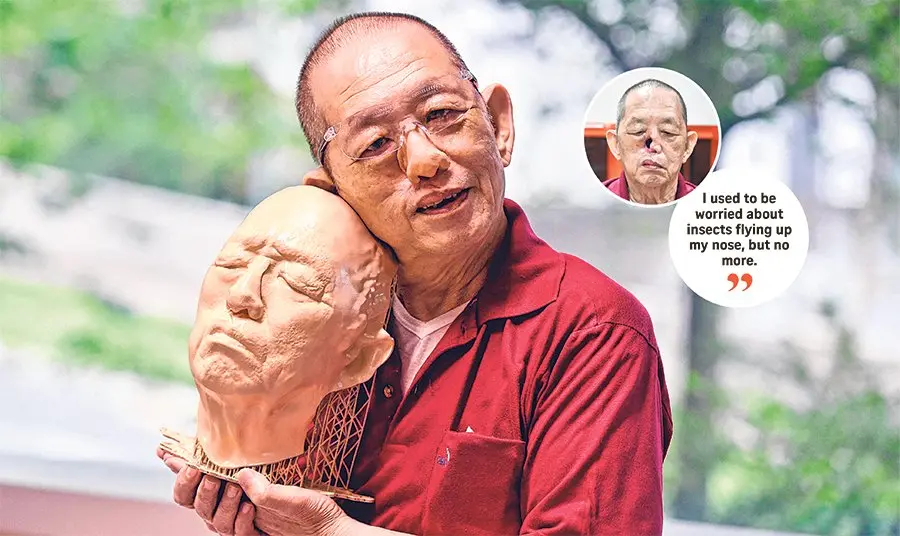
Skin cancer survivor Mr. J. F. Lian with his 3D printed face model and prosthetic nose.
The Solution
A colleague suggested to Dr. Yam that the centre design and 3D print a prosthetic nose for Lian. “I know how useful 3D printing can be, and I’m always looking to push the boundaries,” says Dr. Yam. So, in November 2022, the Medical 3D Printing Centre at TTSH offered to custom-design and 3D print a prosthetic nose made of resin for Lian, based on scans of his face.
The first step was to create a 3D print file, which was derived from the CT scans taken of Lian’s face prior to surgery. The images were cleaned up by the 3D printing engineers and “sliced” into files that the printer could read. Printing the prosthetic nose in surgical guide resin on Formlabs’ Form 3B+ 3D printer took about an hour. Next, the 3D print was soaked in isopropyl alcohol to remove excess resin. The 3D model was then put in a curing machine, where it was hardened under UV light. Finally, it was trimmed, sanded, and polished to ready it for painting.
As 3D printing can be a solution to many medical problems, Dr. Yam says, “We want to make 3D printing more accessible to patients.”
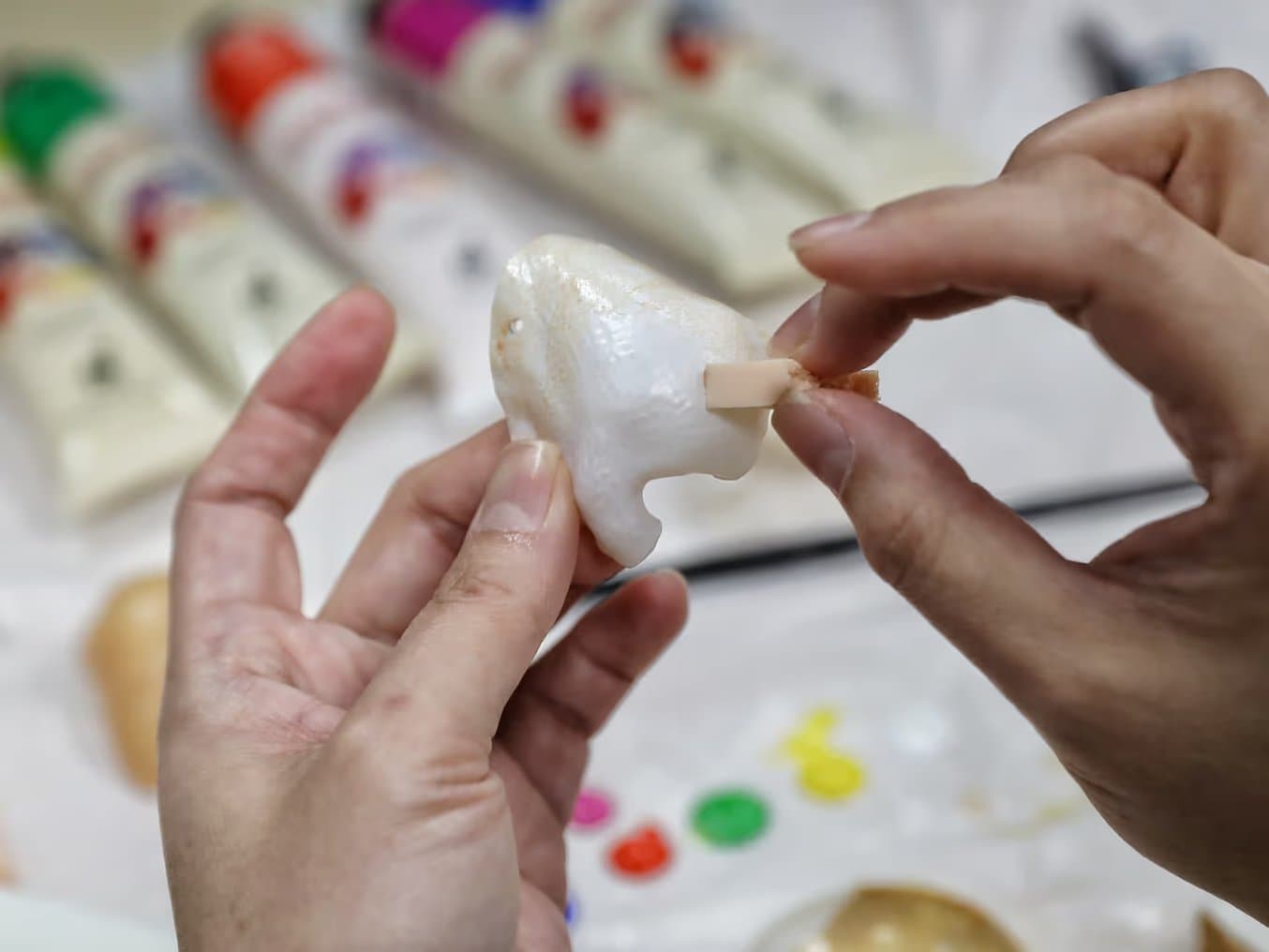
Dr. Michael Yam's team experimented with painting on different types of material.
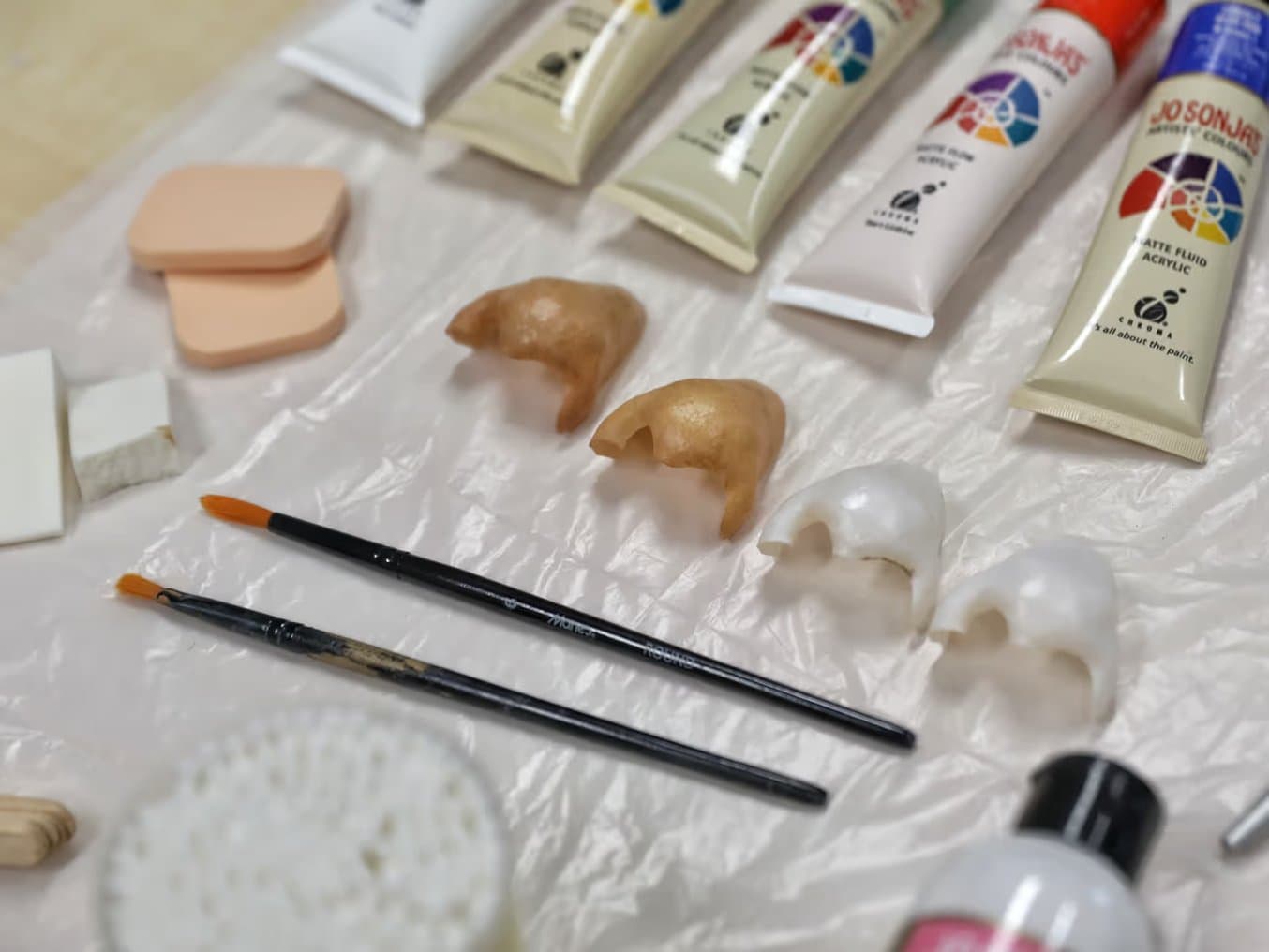
It took several trials and attempts to get the skin tone right.
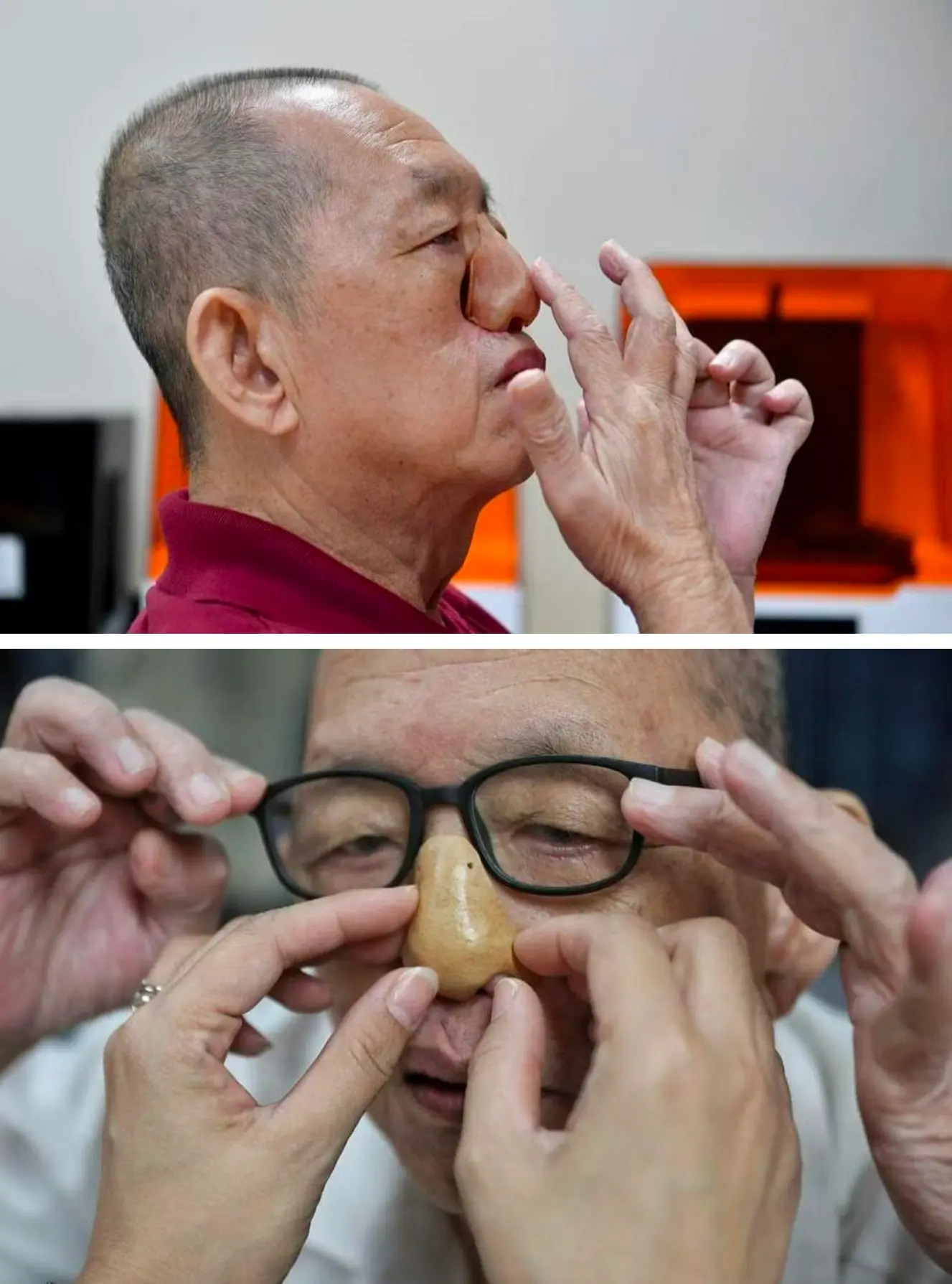
Form, fit, and function testing of the 3D printed nose prosthetic on Mr. Lian.
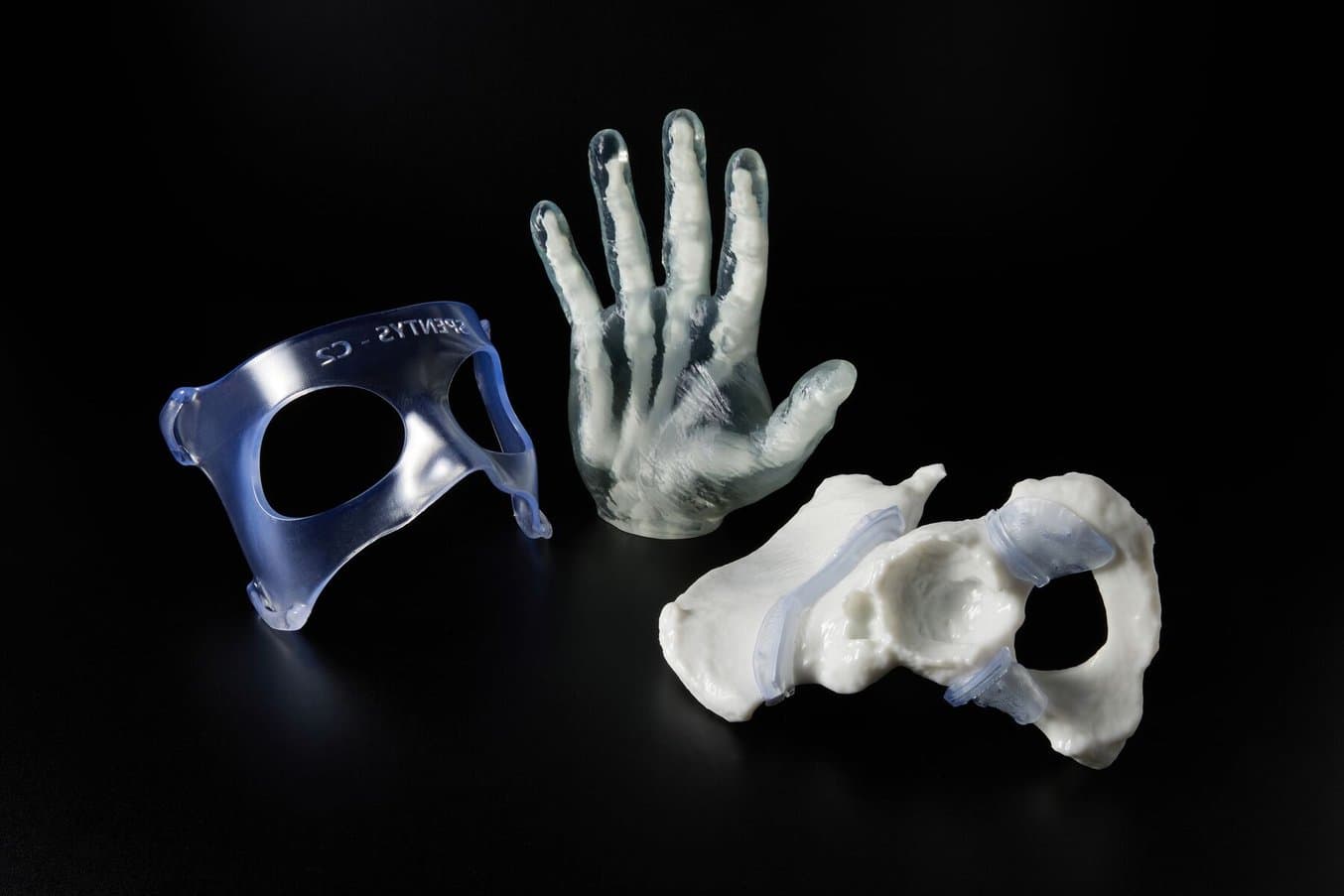
3D Printing Applications for Hospitals and Patient-Specific Procedures
This report looks at five different ways the recent adoption of affordable in-house printing is impacting hospital and device manufacturers.
The Outcome
Creating a 3D printed prosthetic nose for Mr. Lian began with CT scans of his face, which were processed and printed. After initial fitting issues due to weight loss and facial changes, new scans were taken. Realistic color printing was challenging until Dr. Yam collaborated with cosmetic experts Ms. Goh and Madam Ho from the Institute of Technical Education (ITE), Singapore. Despite their stage makeup experience, painting the resin prosthesis to match skin tones required significant experimentation. They painted fine details and applied a finishing coat, though concerns about sun exposure and fit persisted. Ultimately, transparent tape and the strategic use of glasses helped secure the prosthesis comfortably.

Dr. Michael Yam, head of the TTSH 3D printing team, first used 3D printing to assist in surgery in 2019.
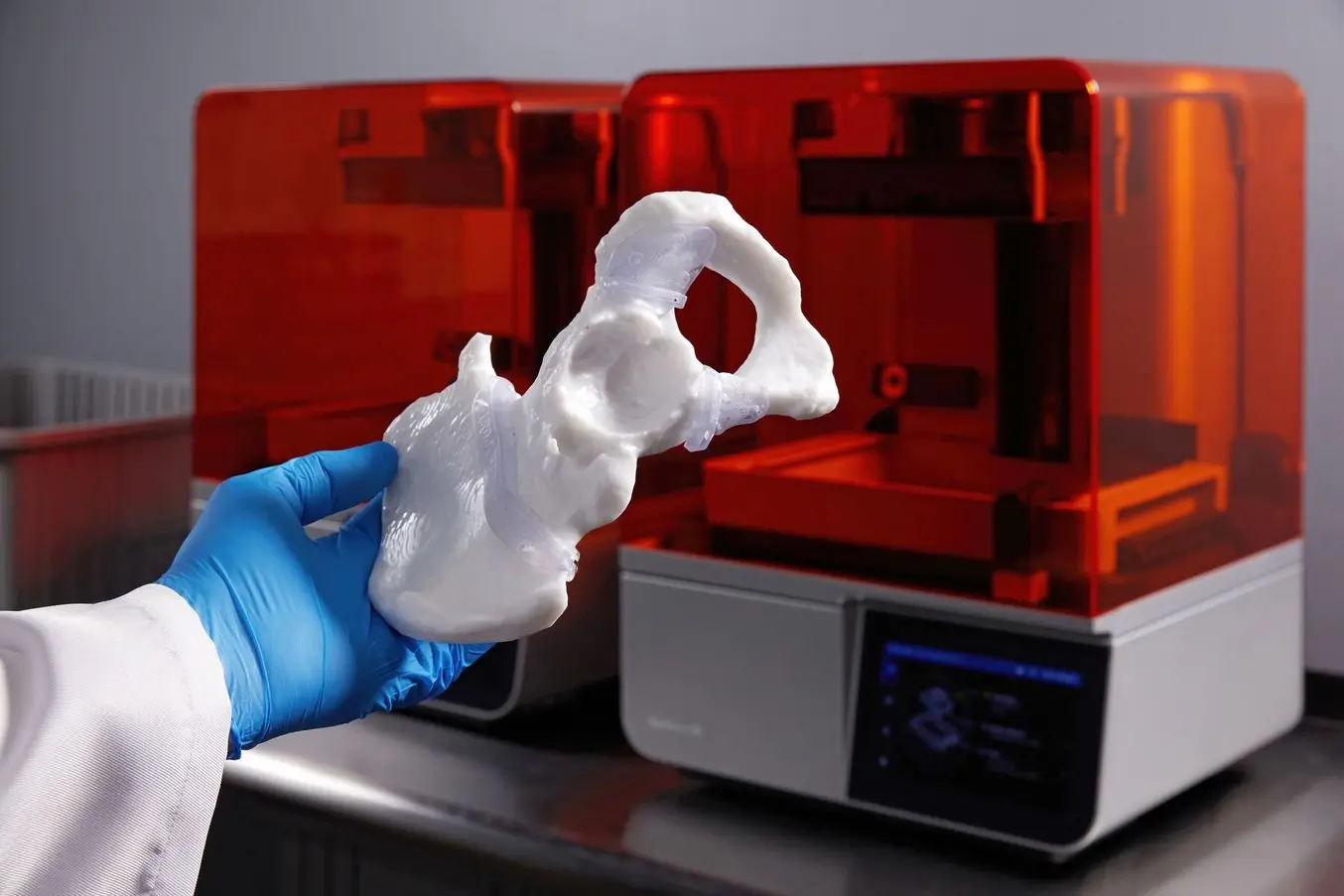
3D Printing in the Hospital
This report reviews the clinical and economic impacts of 3D printing, as well as challenges and opportunities for 3D printing technology as its use expands across healthcare delivery settings.
Surgical Guides for Accurate Results
Dr. Yam also shared various applications of Formlabs’ 3D printing technology at the hospital, including surgical guides. They have performed numerous operations utilizing 3D printed surgical guides, leading to better results, higher accuracy, and time-savings.
Elaborating on a recent case involving the use of a surgical guide, Dr. Yam said, “A man in his 60s came to our hospital after a road traffic accident. He had an unusual-shaped defect in his femur, requiring a bone graft. We began by performing a CT scan to examine the bone. Using the scan data, we designed a customized jig to match the shape of the defect. This jig was then 3D printed using Formlabs’ technology, followed by post-processing and sterilization for surgical use. With the help of a surgical guide designed by our 3D printing centre, I was able to precisely cut the graft to fit the defect. This streamlined the process, reducing both bone shaping and operative time. It also reduced the anesthesia time, potentially lowering the infection rate.”
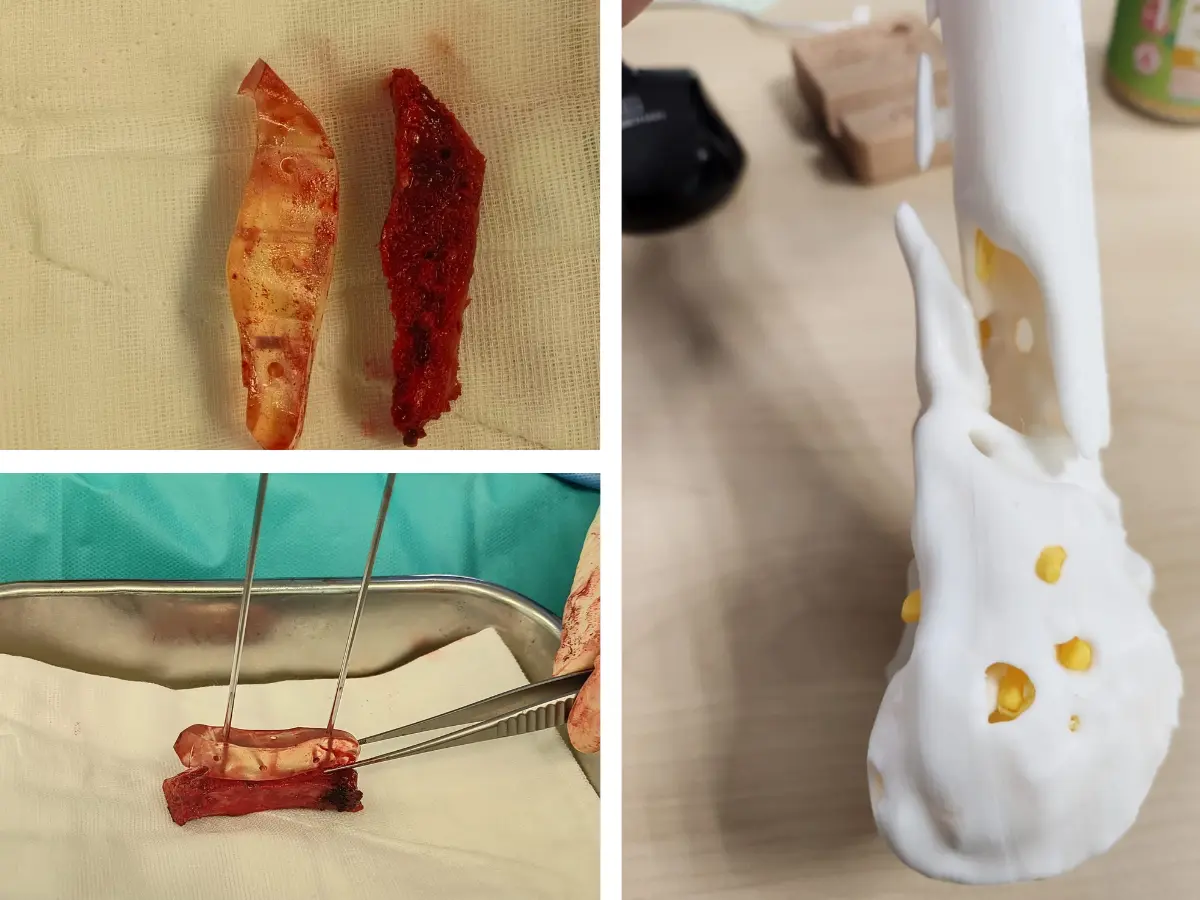
Examples of patient-specific surgical guides and 3D models printed by TTSH, achieving remarkable accuracy and efficiency in numerous operations.
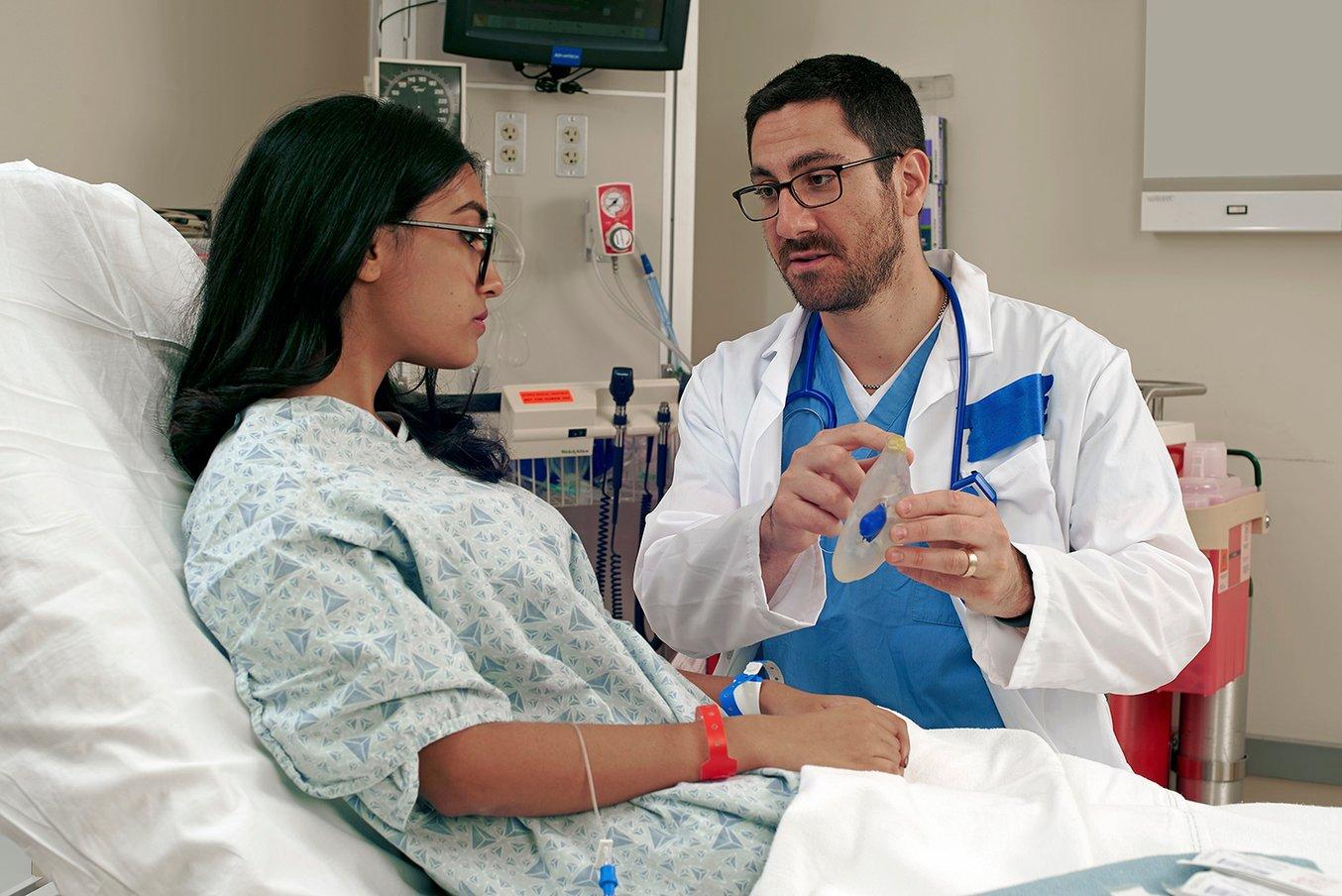
How to 3D Print Anatomical Models for Preoperative Planning and Enhanced Patient Consent
This white paper offers a practical walkthrough for physicians and technologists to get started creating 3D printed anatomical models from patient scans, reviewing best practices for setting up a CT/MRI scan, segmenting datasets, and converting files to a 3D printable format.
Future 3D Printing Projects
TTSH is currently working on a project dealing with implantable printing, i.e. printing implants. When queried about the materials being explored for this groundbreaking endeavor, Dr. Yam explained, “We plan to use traditional materials such as titanium and stainless steel, as well as explore PEEK and silicone resin printing for these purposes, particularly for prosthetics where silicone is being considered.”
The hospital is also working on a project to combine augmented reality with 3D printing for teaching purposes. “It’s not feasible to print everything. So, augmented reality can help here. This will improve the training and boost the confidence of the people involved,” added Dr. Yam.
In addition to implants and educational tools, TTSH is expanding its focus on printing more and more prosthetics and surgical guides. These efforts aim to produce highly customized prosthetic limbs and devices that perfectly match individual patient needs. Moreover, surgical guides created through 3D printing will provide surgeons with precise templates for complex procedures, enhancing accuracy and outcomes. By continuing to innovate in the field of 3D printing, TTSH hopes to push the boundaries of personalized medicine and improve patient care.
Reach out to our medical experts to learn more about in-house 3D printing, or request a free sample part to evaluate Formlabs BioMed resins for yourself.