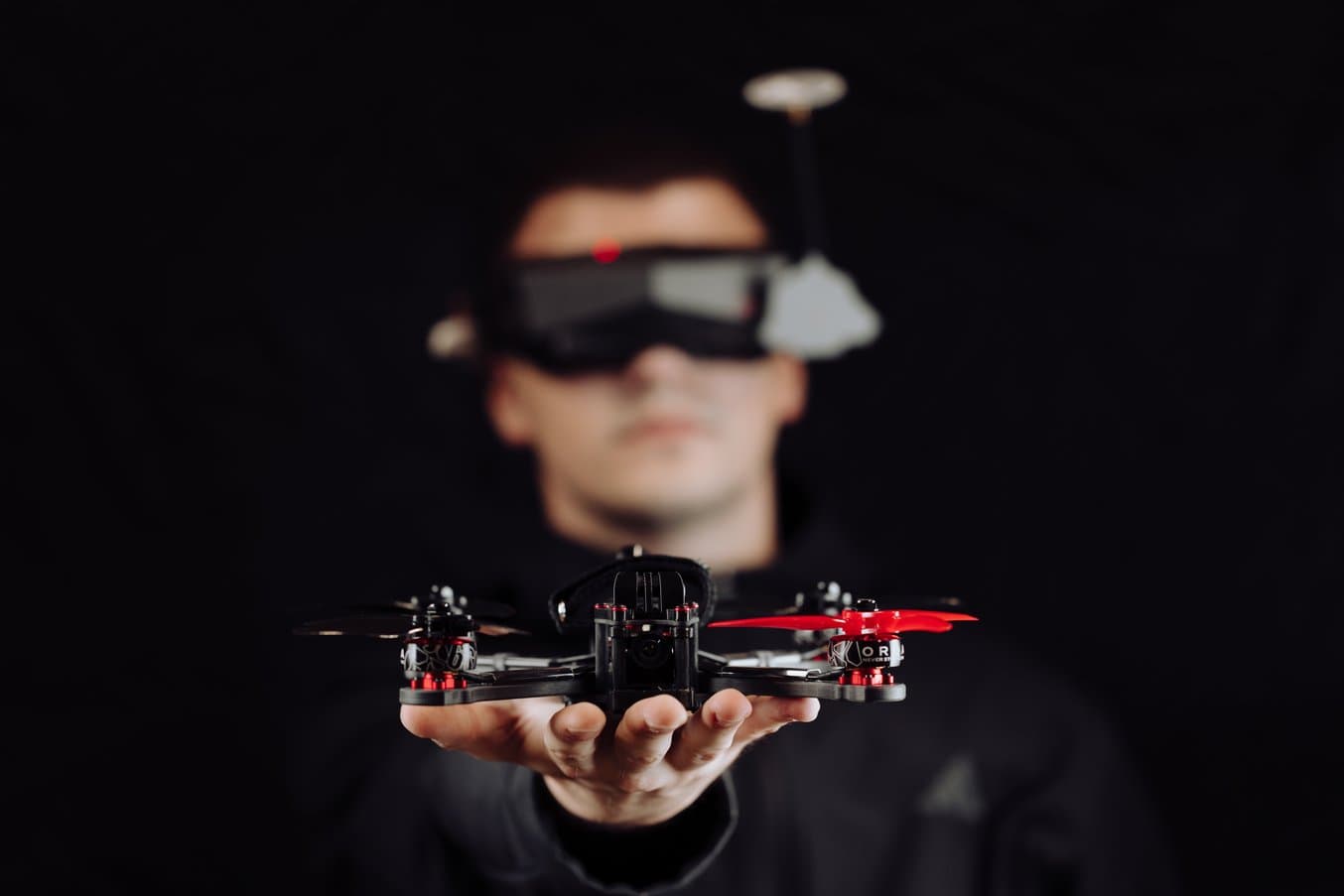
Trade regulations and tariffs affect some industries more than others. Relatively young markets, like drone manufacturing, can get squeezed harder than more established ones, due to their relative lack of supply chain diversity.
ORQA FPV, a drone manufacturer based in Croatia, recognized that years before the trade wars of 2025. Now, the supply chain and manufacturing base they’ve built in the EU has put them in the perfect position to provide timely solutions for those looking for alternatives to big offshore manufacturers.
Part of building their secure supply chain has been leveraging the power of in-house selective laser sintering (SLS) 3D printing with their two Fuse Series SLS printers and both Nylon 12 Powder and TPU 90A Powder. SLS 3D printing has enabled a cost-efficient and agile workflow that helps them get to market faster and provide the full range of high-quality components needed for drone manufacturing and services.
Incubator to Open Skies
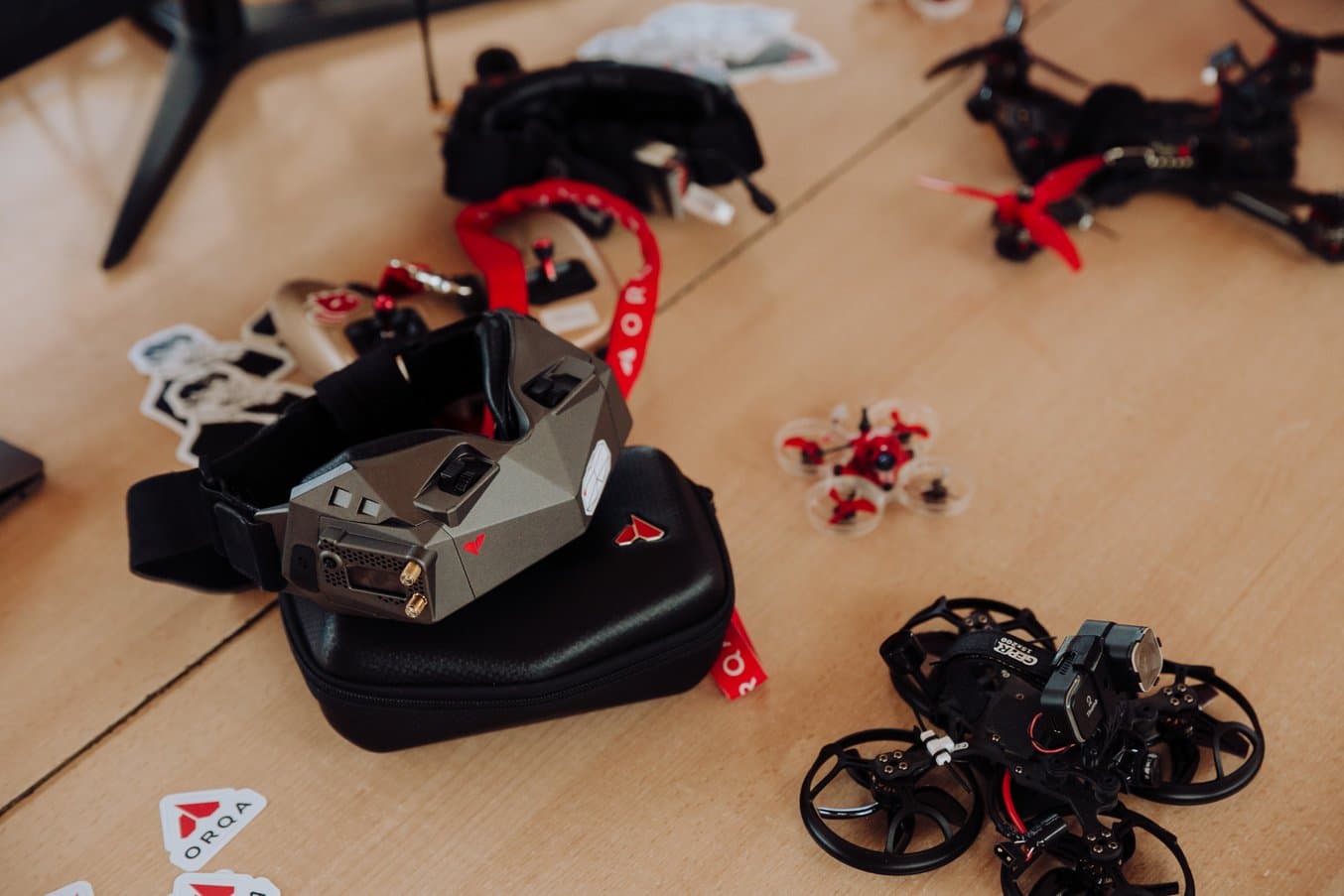
Prototyping goggles, drone frames, and controllers requires meticulous detail and tight tolerances. The ORQA team started with large format industrial 3D printers that were available in the common incubator space.
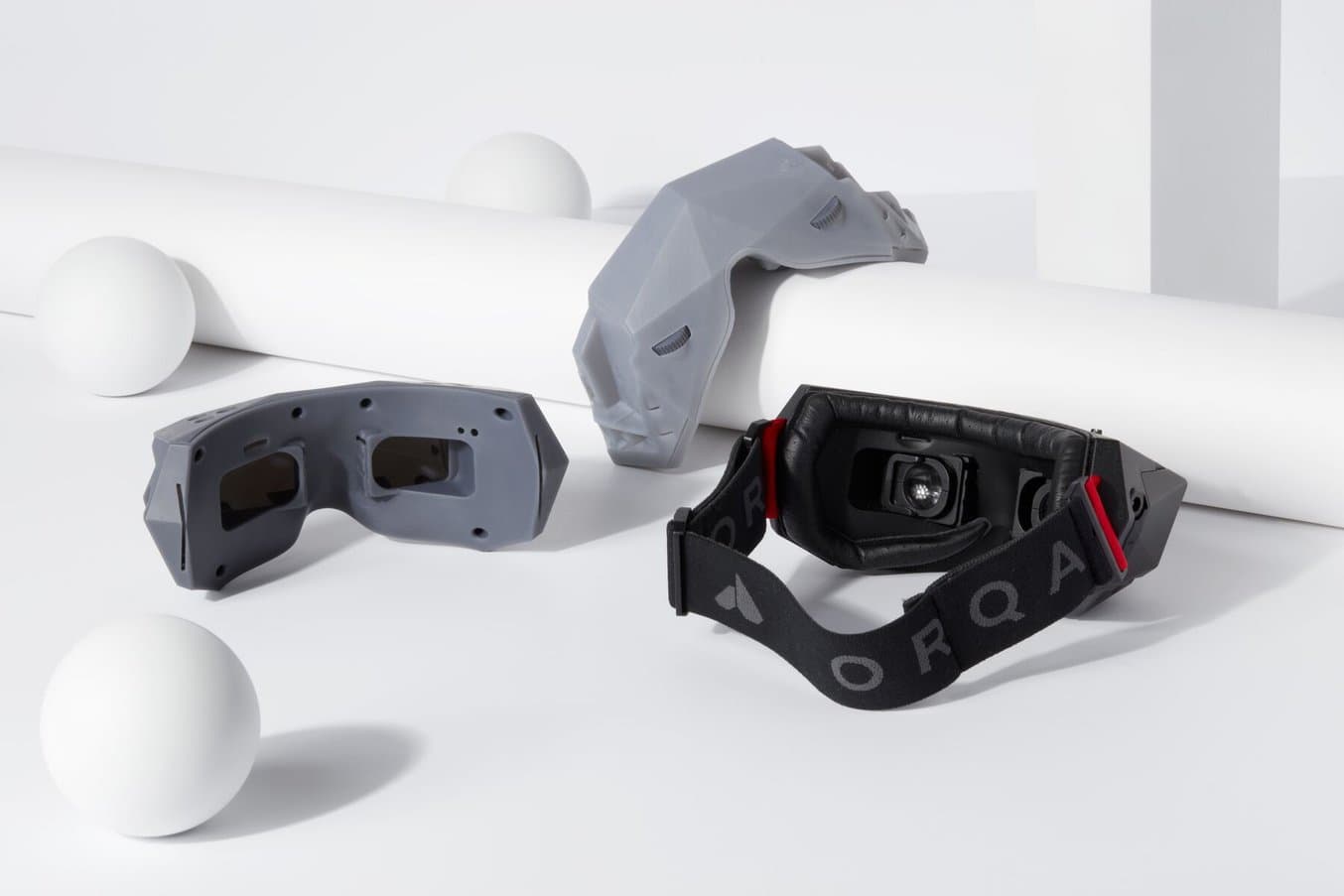
Once ORQA's product catalog began to expand, the team knew they needed their own high-quality fabrication technologies in-house.
ORQA was started in an entrepreneurial incubator space in 2018 by three young founders who saw a gap in the drone supply chain for the EU. “EU and US operators in the public safety sector cannot use cutting-edge technologies because the market leaders have been blacklisted for security reasons,” says Antonio Kovac, ORQA’s lead mechanical design engineer.
Though foreign companies can sell low-cost FPV drones and components to the average consumer in the US and EU, the military and public safety sectors are often barred from using these same companies. Publicly funded businesses and teams must rely on a constrained supply chain to access cutting-edge drone technology. ORQA’s founders recognized this disparity and began developing prototypes, taking them to CES in 2019, just as the drone frenzy was beginning.
Their prototypes at CES helped drive a successful Kickstarter campaign — selling 600 pairs of flight goggles with advanced displays. Those prototypes were made largely on a legacy SLS machine, the EOS Formiga. “For the first two or three years of designing and testing, we were using the incubator’s printing lab, which had FDM, SLA, and a big EOS Formiga machine. It helped us get our first orders, but was too expensive and big for us to consider getting one ourselves,” says Kovac.
As ORQA grew their product offering — racing goggles, PCBs, antennas, bases, propellers, and fully-assembled drones — the team realized they needed their own 3D printer that could handle the volume of constant iteration as well as functional testing parts.
Why ORQA Added the Fuse Series
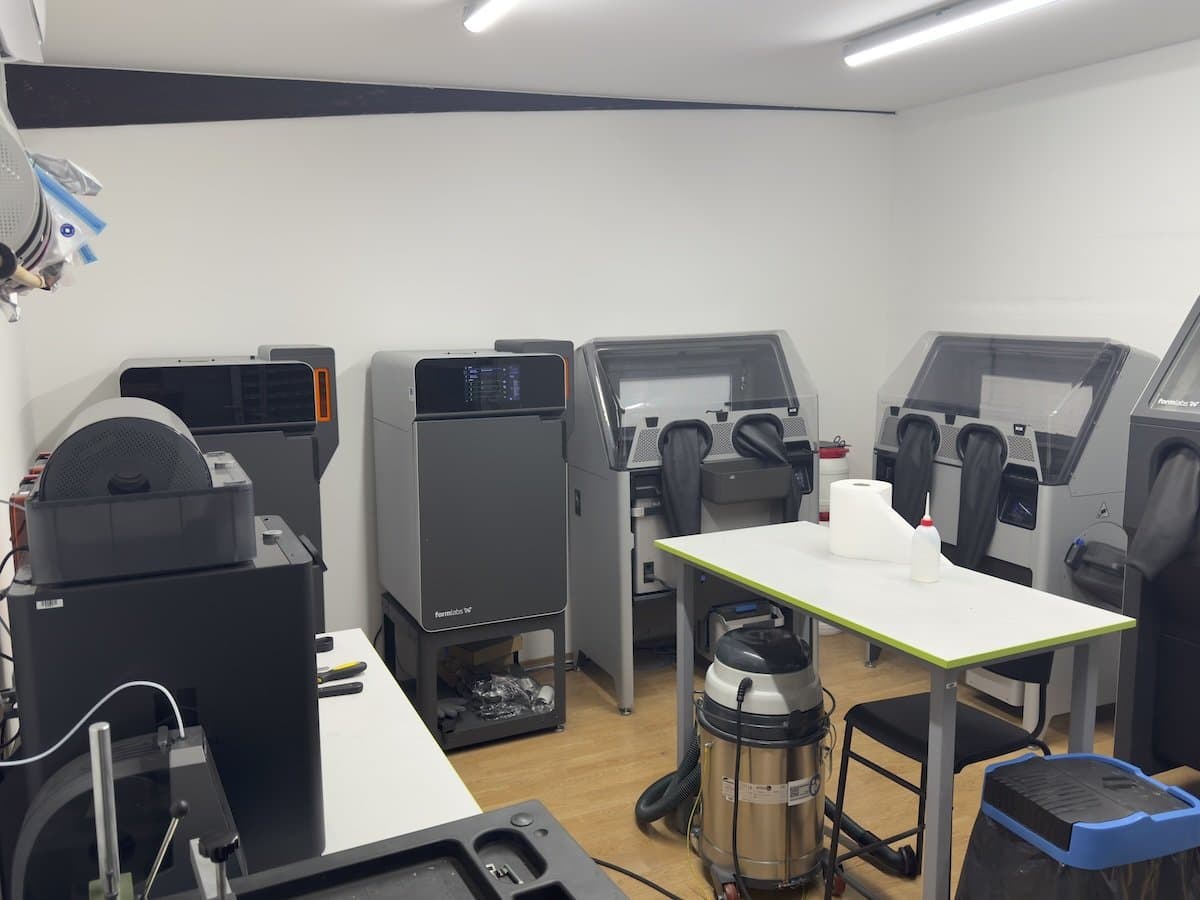
The compact size of the Fuse Series has made it possible to scale up as demand as grown.
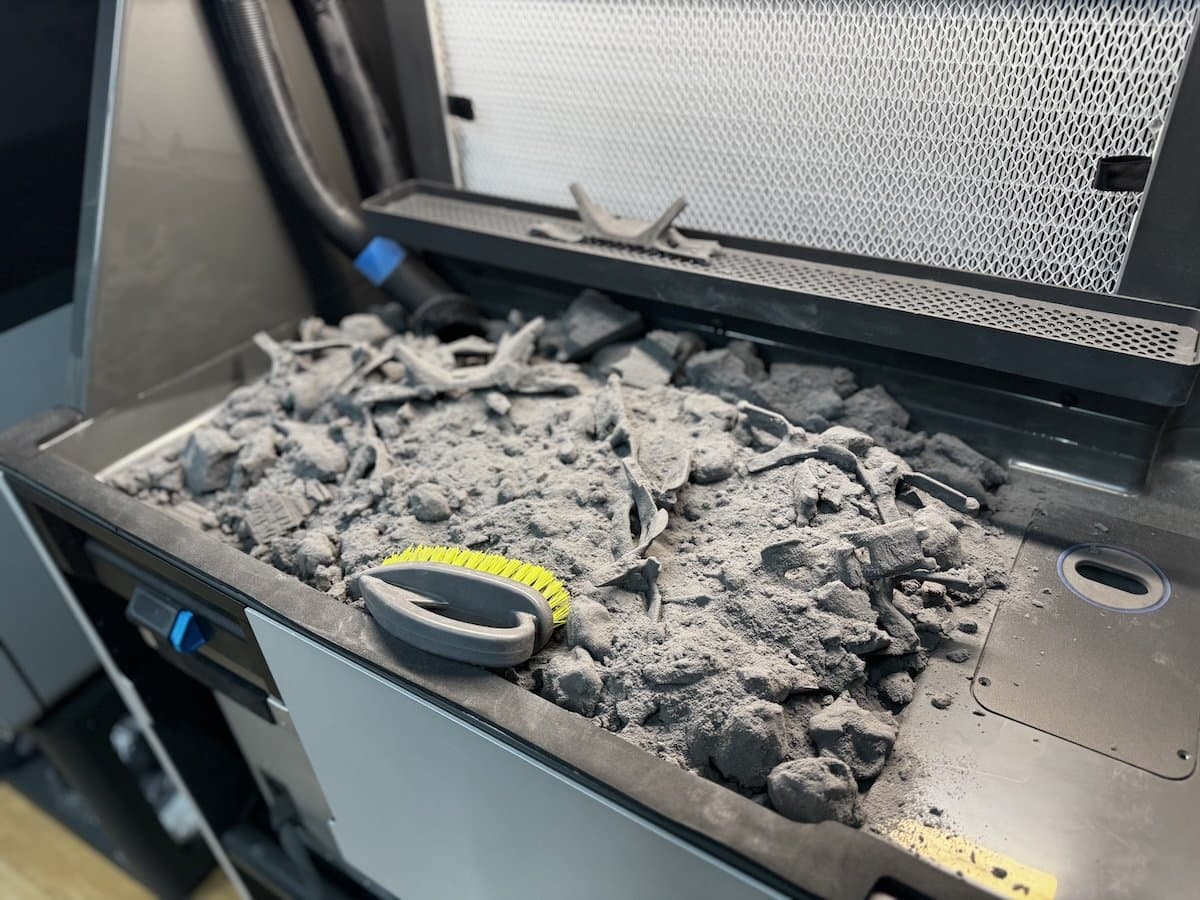
The Fuse Sift and Fuse Blast make post-processing mostly automated and fast, enabling higher volumes of parts to be produced every day.
Building a wider customer base and adding new products was good for business, but the ORQA team was being held back by having to share the 3D printing lab. They had extra space in their offices for a 3D printer, but not enough for a legacy SLS machine like a Formiga.
After years of printing with the shared EOS machine, ORQA decided to use their personal office space for a powerful option that could scale with them as they grew — the Fuse Series. “For the Formiga, you need probably 10 square meters, but the Fuse is quite compact. The Formiga would take a full day to do a print, but the Fuse is faster and it’s an overall cleaner system,” says Kovac. Taking up only 64.5 × 68.5 × 107 cm, the Fuse 1 could fit easily into the ORQA space in the incubator’s offices and they could get functional parts every day, speeding up the iterative cycle and supercharging growth.
"At that point, especially from the mechanical side, it was a must if we wanted to grow. If we had tried to get parts from Shapeways, it would have taken two months to try out an idea. Now we’re getting prints same day.”
Antonio Kovac, Mechanical Designer, ORQA FPV
Speed, Scale, Switching Materials
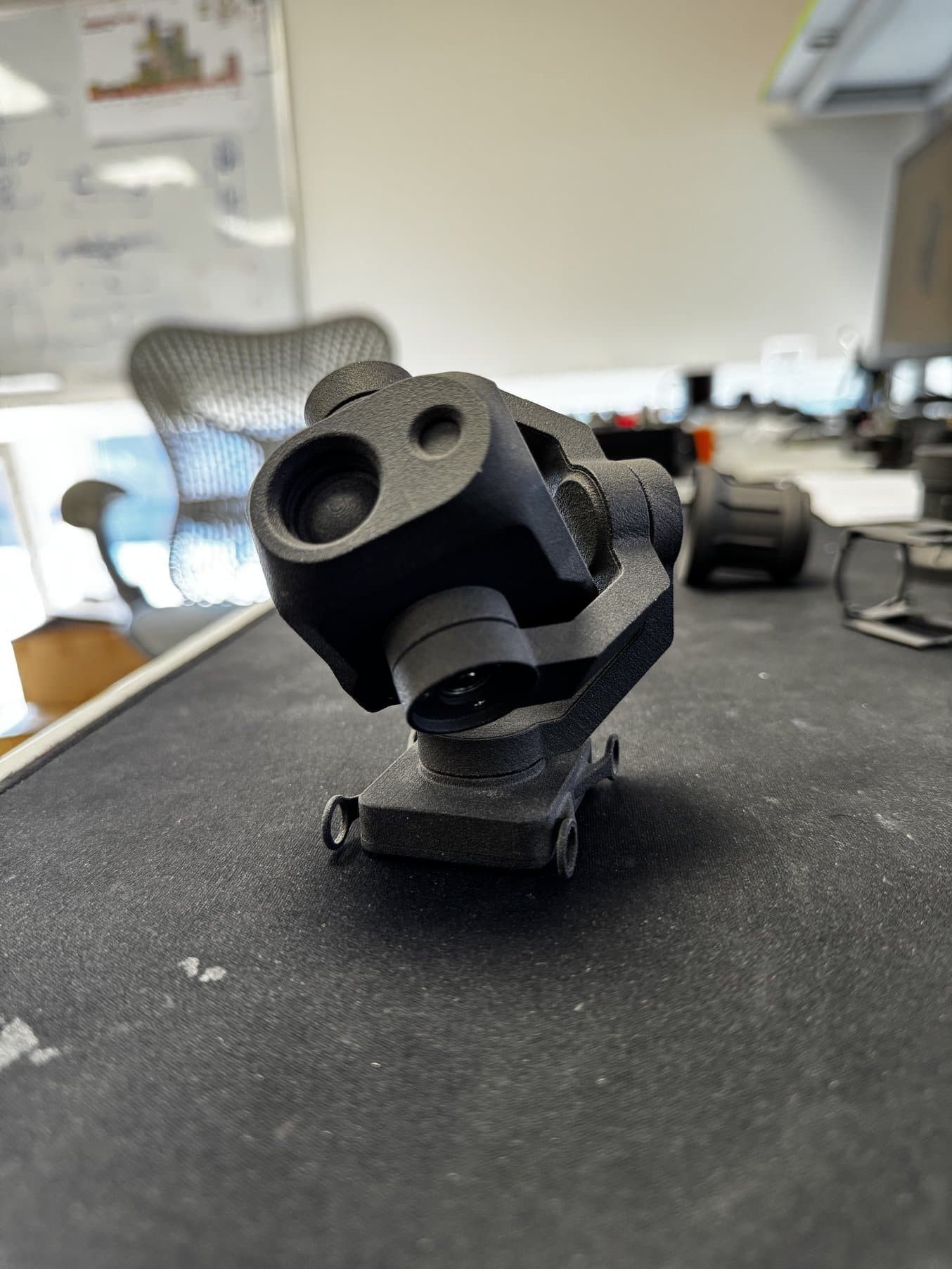
As demand surged, ORQA tried out different materials, like TPU 90A Powder, but realized they needed Nylon 12 Powder for more components, like this camera mount with interlocking parts and tight tolerances.
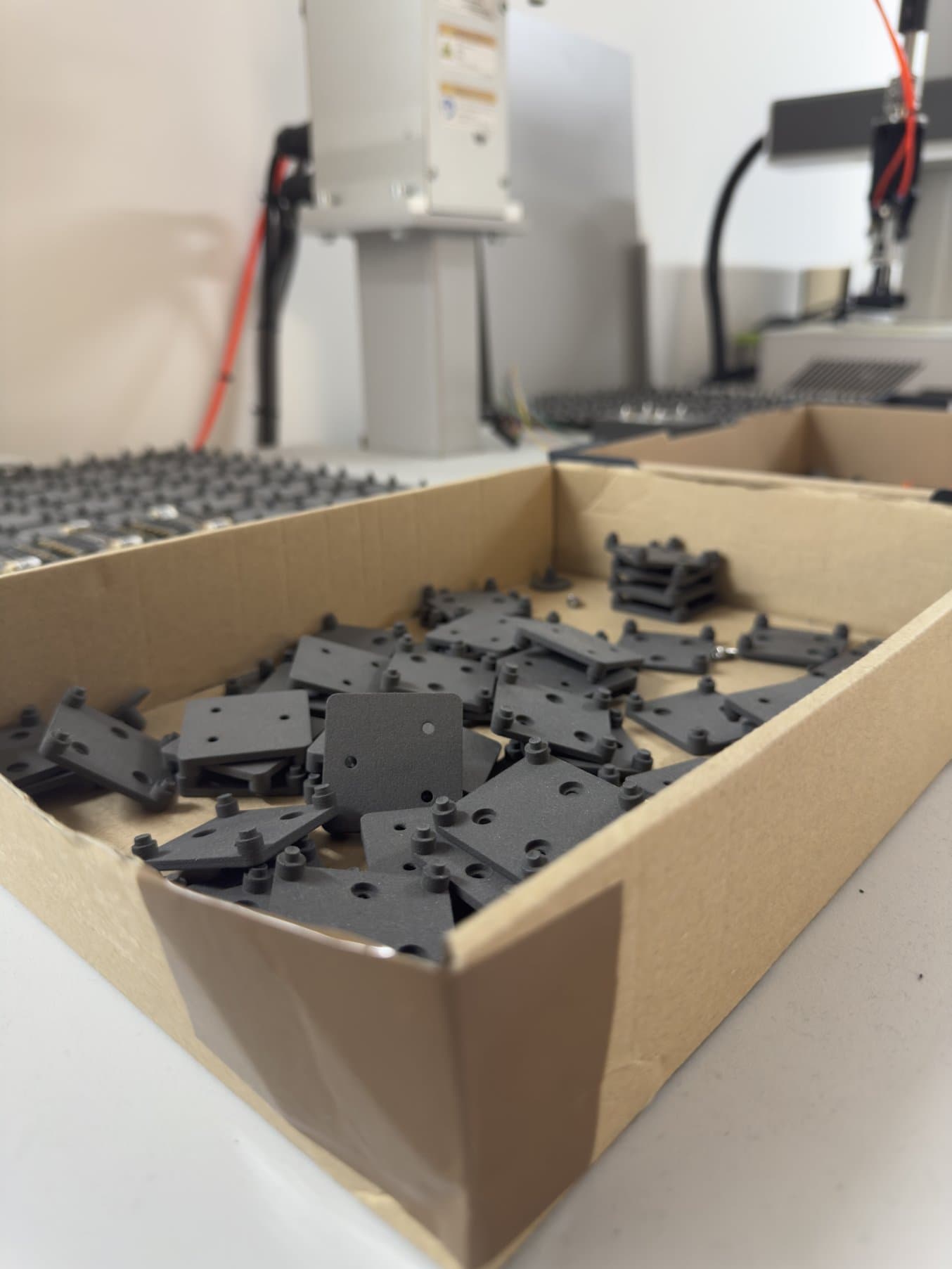
The Fuse Series enables low-volume production for end-use parts through the self-supporting technology and the large build chamber. Small businesses can avoid the costs and lead times of tooling by SLS 3D printing end-use parts in-house.
With the Fuse 1 turning out parts every day, ORQA started growing even faster. From three founders in 2019 to 140 people currently, the company’s growth matched that of the overall drone industry. US and EU drone manufacturers needed components without security concerns, and drone service industries (like construction monitoring, offshore wind maintenance, and more) needed high-quality drones themselves. ORQA was able to answer, designing and producing all their components, like electric speed controllers (ESCs), antennae, flight controls, goggles, and fully-assembled drones, in Croatia.
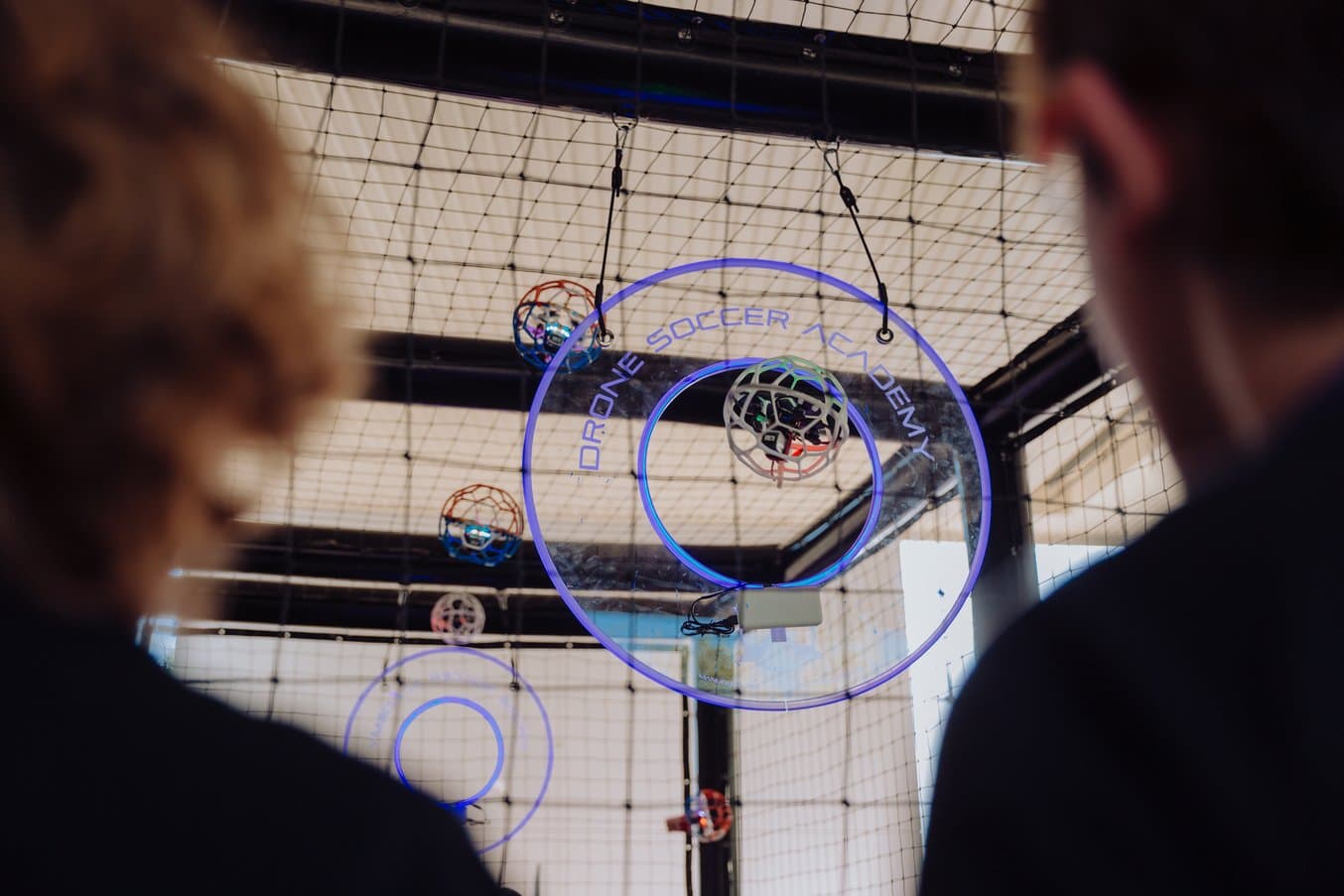
With the explosion of sports like drone racing and 'drone soccer,' the demand for high-performance drones like ORQA's surged, leading to an influx of orders and a need for larger scale production capabilities.
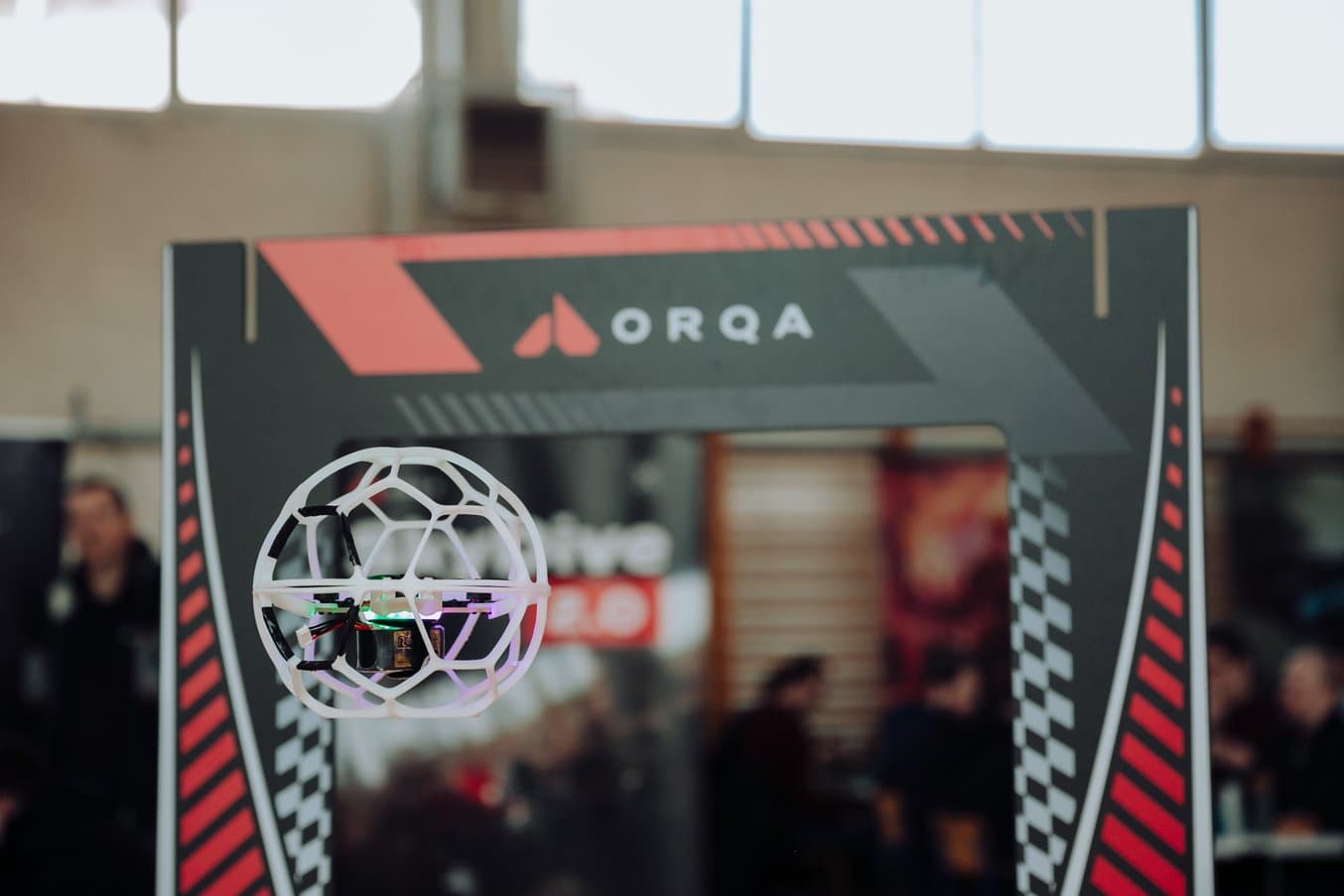
A combination of SLA and SLS technologies help make ORQA's drones agile, responsive, and light weight - ideal for competitive racing sports like these.
Quickly, ORQA needed even more 3D printing power. They brought in the Fuse 1+ 30W for faster printing and a greater variety of SLS materials in 2024. With two printers in-house, they were able to use one printer for TPU 90A Powder, perfect for impact-resistant components on drones. “When you test drones, you need major parts to survive, and for that you need impact protection. We like the TPU for cushioning features and fixtures for delicate parts like GPS modules. The TPU is really good and super durable,’ says Kovac.
For one soft part that would have required a change in injection molding tooling, the ORQA team even decided to go with SLS 3D printed TPU for end-use production. They needed several hundred TPU parts, and printed them on the Fuse 1+ 30W in just a few days. “With the Fuse 1+ we can get prints the same day. We don’t need to wait for changes in tooling,” says Kovac.
Once that batch production was finished, however, the demands for Nylon 12 Powder parts became more urgent, and ORQA decided to switch the powders on their two Fuse Series printers. “Cleaning the printers and switching from Nylon 12 to TPU only took a few hours, and made more sense for the volume of parts we needed from each to put Nylon 12 on the Fuse 1+ because of its speed,” says Kovac.
The ORQA team orders 50 kg of each material at a time, relying on the bulk powder pricing available for production customers to make their operation as efficient as possible. “We have 100 kg of powder ready to go, it just makes sense cost-wise to order in bulk and we know we won’t run out in the middle of a production batch,” says Kovac.
To learn about what kind of bulk discount you qualify for, contact our team.
Surprised by the Fuse Series
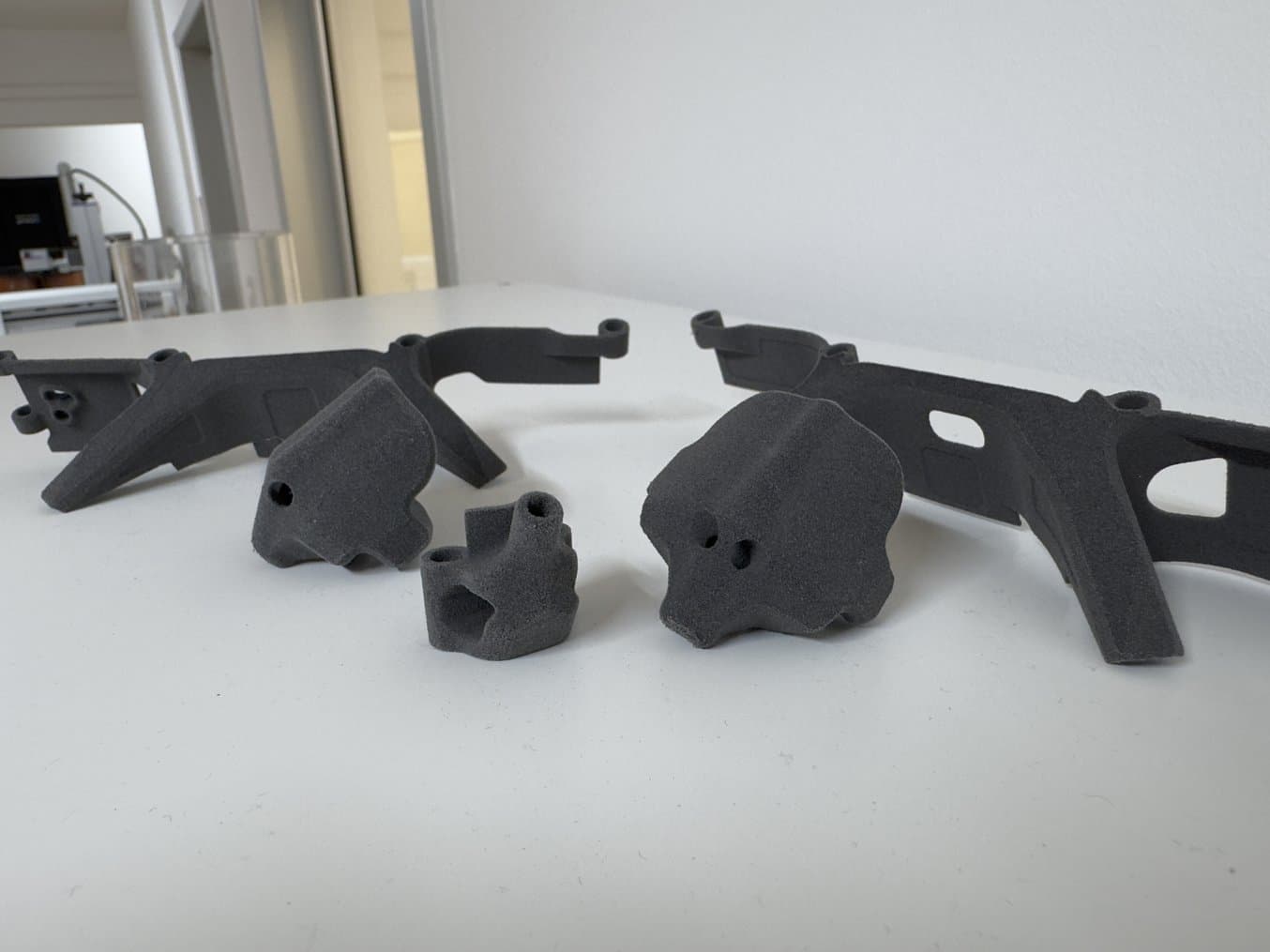
These flexible parts, printed in TPU 90A Powder on the Fuse 1+ 30W, are used for prototyping goggle components. The soft-touch material is crucial for functional prototypes of wearables like goggles.
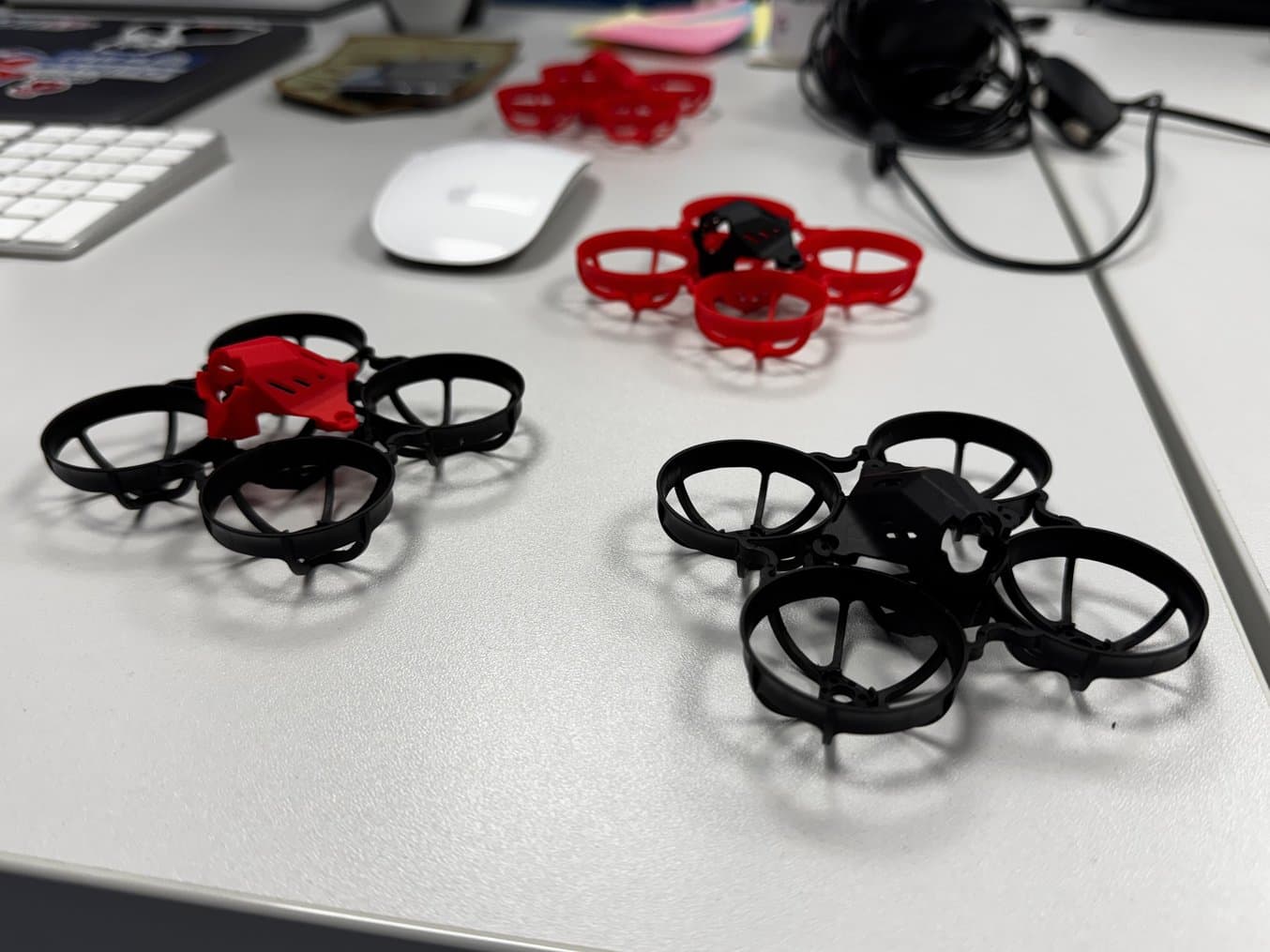
These quadcopter drone frames and propeller guards utilize the durability of Nylon 12 Powder (black parts) and SLA 3D printed components (red parts).
In such a hyper-speed growth industry, a stable supply chain and the ability to quickly scale is the key to staying ahead of the competition. Though it’s only been two years since the ORQA team has moved to their own facility, their growth has been hypercharged by in-house SLS 3D printing with the Fuse Series.
“We’ve been so surprised at how much the Fuse 1+ 30W has had an impact. It’s so fast and the whole system is so very well designed. We’re really satisfied with it and expanding to a fleet is in our future.”
Antonio Kovac, Mechanical Designer, ORQA FPV
To learn how to assemble a drone step by step using SLS 3D printing, read our step-by-step guide. To learn how you can scale with the Fuse Series, contact our team.