오늘날 조립 라인에서 나오는 신차 3대 중 1대는 Brose에서 제조한 구성품을 최소한 하나는 장착하고 있습니다. Brose는 세계 5대 가족 소유 자동차 공급업체 중 하나입니다. 100여 년 전 베를린에서 Max Brose가 설립한 이 회사는 자동차 파트 거래 사업에서 시작하여 메카트로닉스 시스템 분야의 시장 선도 기업으로 성장했습니다. 그들의 제품(대부분 시트, 리프트게이트, 도어 조립품)은 자동차 업계의 BMW, 볼보, 포드, 메르세데스, 지프 등. 가장 큰 이름을 위해 설계 및 생산됩니다.
Brose의 꾸준한 성장과 이들 OEM과의 장기적인 성공적인 파트너십은 부분적으로 회사의 지속적인 혁신과 개선에 대한 노력 덕분입니다. 3D 프린팅은 Brose의 설계 및 최종 사용 제조 공정에서 다양한 계획의 핵심이며 Brose가 빠르게 변화하는 자동차 산업의 모든 변화에 적응하고 대응하는 데 도움이 되었습니다.
우리는 미시간 주 오번 힐스에 있는 Brose North America 본사와 미시간 주 뉴 보스턴에 있는 가장 큰 최종 사용 제조 시설 중 하나인 Brose New Boston을 방문하여 강력한 광경화성 수지 조형(SLA) 및 선택적 레이저 소결(SLS) 3D 프린터를 실제로 사용하는 방법을 살펴보았습니다. 이 지역의 적층 기술을 이끌고 있는 시트 사업부 프로토타입 관리자 Matthias Schulz는 Brose가 OEM을 위해 촉박한 일정에 맞춰 설계부터 제조, 최종 사용 파트에 이르기까지 전체 프로세스에 3D 프린팅을 어떻게 활용하는지에 대해 이야기했습니다.
“우리는 자동차 산업, 특히 지난 5년 동안의 빠른 변화를 목격했습니다. 새로운 제품을 개발하는 데 걸리는 시간이 크게 단축되고 있습니다. 따라서 우리도 이에 맞춰 행동해야 합니다. 적층 기술을 점점 더 많이 구현해야 합니다. 이것은 우리에게 이익이 됩니다. 왜냐하면 툴링 등의 리드 타임도 단축되고 나중에 생산을 통해 파트를 더 빨리 공급하는 데 도움이 되기 때문입니다.”
Matthias Schulz, Brose North America, 시트 프로토타이핑 관리자
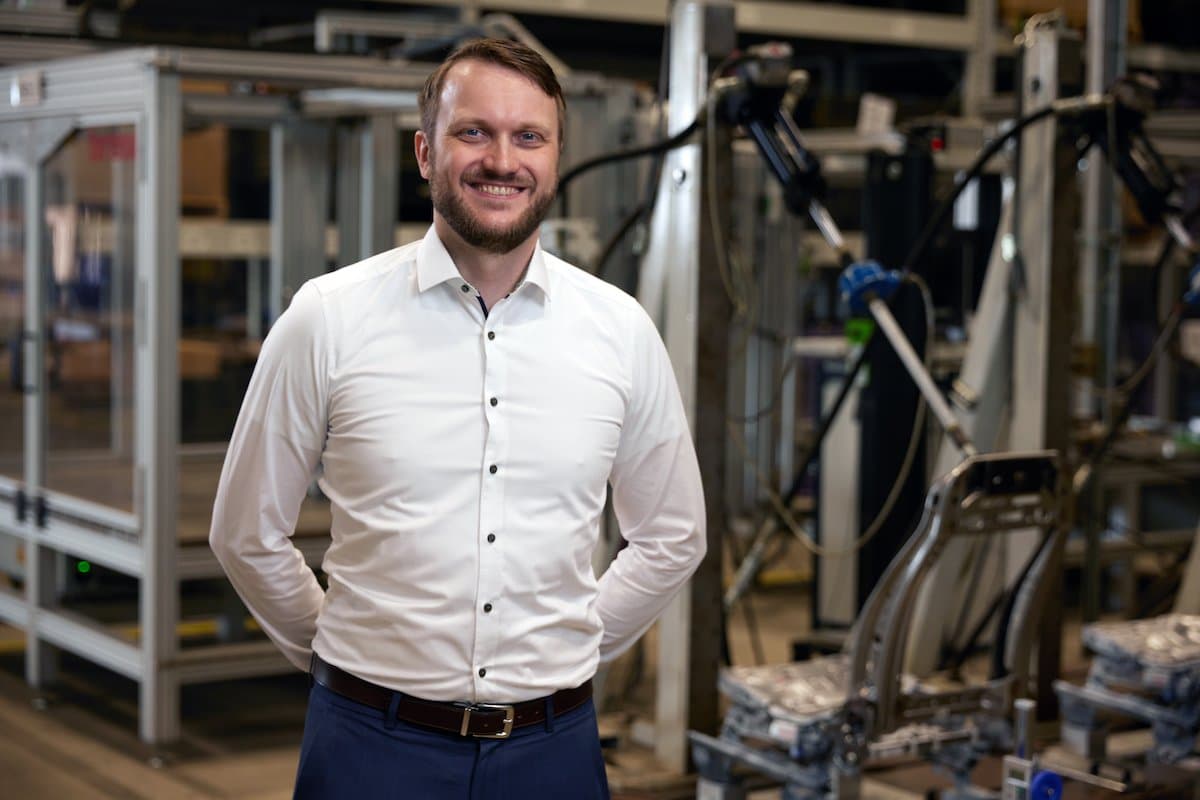
주문형 웨비나: 최종 사용 자동차 생산에 쓰이는 Brose의 SLS
이 주문형 웨비나에서는 Brose North America의 시트 프로토타입 관리자인 Matthias Schulz는 Brose가 간단한 용접 지그부터 250,000개의 최종 사용 파트 생산에 이르기까지 모든 것에 SLA 및 SLS 기술을 사용하는 방법을 설명합니다.
프로토타입 제작이 일회성 작업을 넘어설 때
프로토타입을 응용 프로그램으로 사용하는 것은 3D 프린팅에 완벽하고도 친숙한 방식입니다. Brose는 프로토타입을 위해 다양한 용융 증착 모델링 방식(FDM), SLA, SLS 3D 프린터를 사용하지만, 그 처리량이 반드시 개념 증명 파트에 대해 기대하는 바와 같은 것은 아닙니다. 경우, 프로토타입의 일반적인 볼륨은 500~1000에 가깝습니다.
Schulz 씨는 “우리는 더 큰 규모로 3D 프린팅을 사용합니다. '프로토타입 제작'은 수백 개의 파트를 프린트해야 한다는 것을 의미하는데, 이는 주로 우리가 해야 하는 테스트 횟수와 관련이 있습니다. 우리는 내부 및 외부 기준을 충족할 뿐만 아니라 연방 요구 사항도 충족합니다. 물론, 이를 위해서는 일정량의 파트를 만들어야 하며, 일반적으로 프로토타입을 위해 프린트해야 할 파트가 700~800개 정도 됩니다."라고 슐츠는 말합니다.”라고 합니다
해외 주문 수량으로 인해 SLA가 최상의 옵션: 고무 시트 길이 조절 댐퍼
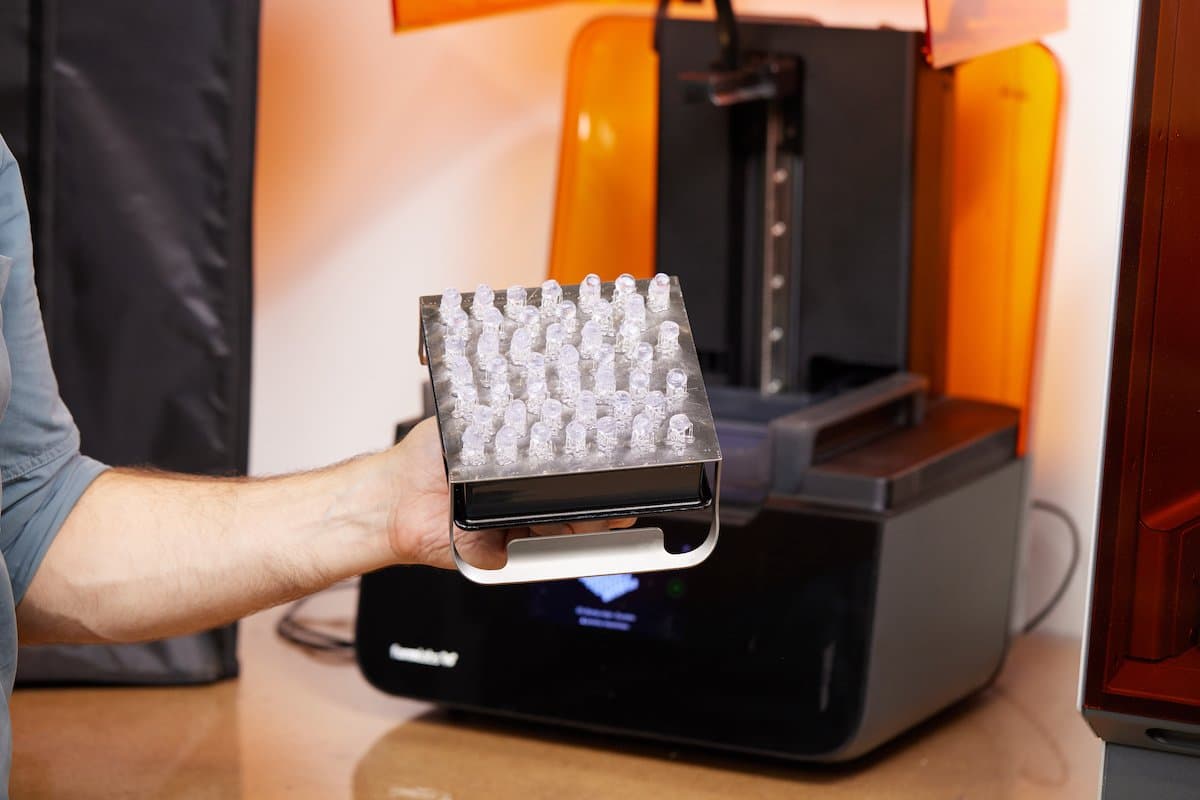
이러한 프로토타입은 금속 시트 조립체가 시트 프레임에 부딪히는 소리와 느낌을 줄이기 위해 만든 작은 댐퍼입니다. 해외에서 주문하려면 최소 수백만 개의 주문 수량이 필요했기 때문에 슐츠와 그의 팀은 테스트를 위해 Form 시리즈 프린터로 프린트했습니다.
한 프로젝트에서 프로토타입 팀은 좌석 조립체에 설치하는 부드러운 실리콘 댐퍼를 사용해야 했습니다. 좌석이 프레임 위에서 앞으로 이동함에 따라 해당 파트은 소리를 완화하고 좌석 조립 동작에 따른 촉각적, 음향적 피드백을 개선합니다. 해외 Brose 직렬 공급업체에서 이러한 파트를 주문하려면 최소 주문 수량이 수백만 개에 달했고, 브로세는 예비 설계 테스트에 사용하기 위해 수백 개만 필요했습니다.
수백만 개의 파트를 주문하고 해외로 배송하는 데 드는 높은 비용 외에도 리드 타임이 몇 주가 걸렸고, 필요하지 않은 수백만 개의 파트은 궁극적으로 낭비되기 전에 보관해야 했습니다. 파트를 주문하는 대신, 기존 CAD를 사용하여 Form 4에서 수백 개의 파트를 빠르게 3D로 프린트했습니다. 그들은 일주일 만에 준비가 되었고, 이 솔루션은 전체 프로젝트의 전반적인 비용과 리드 타임을 단축시켰습니다.
“우리는 이 파트를 여기로 비행기로 보내 최소 주문 수량 재고를 주문하는 것보다 훨씬 저렴한 비용으로 Form 4에 프린트할 수 있었습니다. 최소 주문 수량 재고를 주문하려면 수백만 개의 파트를 주문해야 했습니다. 우리는 그것들을 신속하게 이용할 수 있었고 아무것도 기다릴 필요가 없었습니다.”
Matthias Schulz, Brose North America, 시트 프로토타이핑 관리자
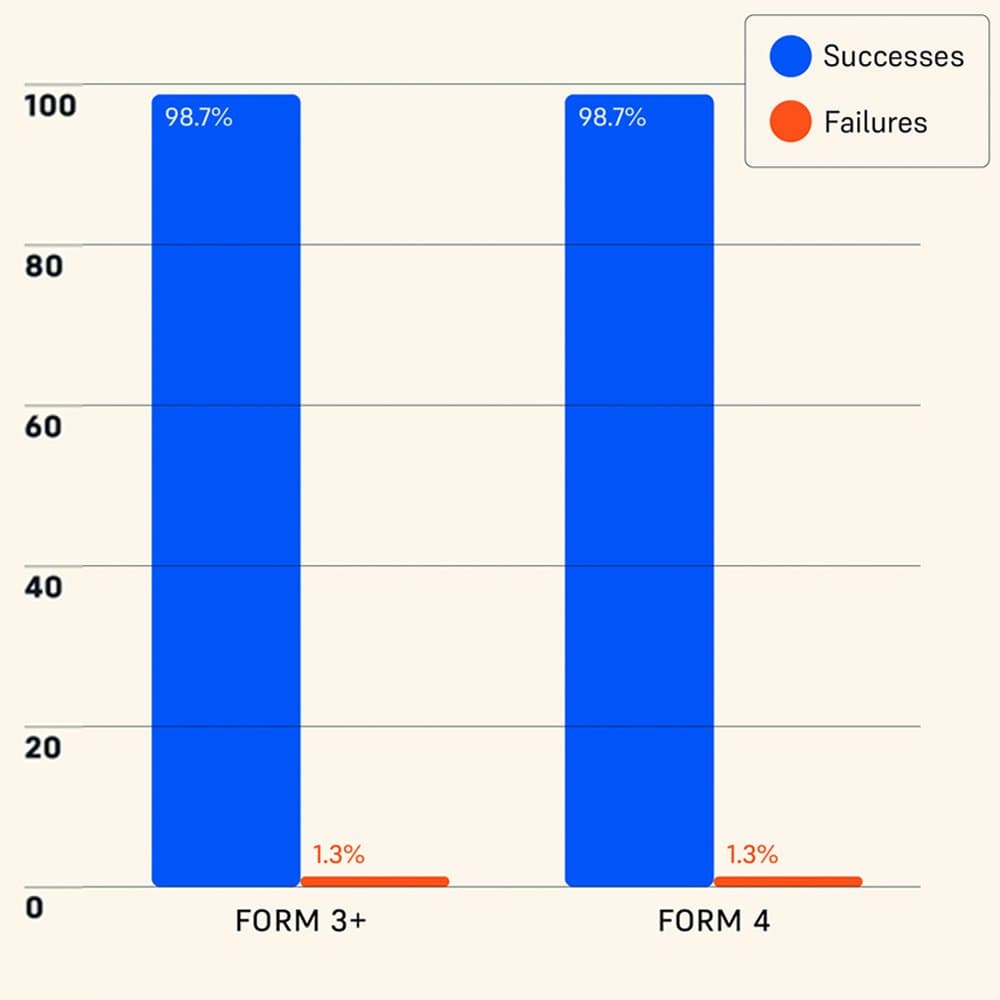
Form 4 및 기타 레진 3D 프린터의 안정성을 독립적으로 테스트한 결과
제품 테스트 분야를 선도하는 글로벌 기업에서 Form 4의 프린트 성공률을 독립적으로 측정한 결과 98.7%의 성공률을 얻었습니다. 당사의 백서에서 시험 방법 설명 전문과 시험 결과를 확인해 보세요.
대량 프로토타입을 위한 SLA와 SLS 결합
파트의 복잡성, 크기, 필요한 부피가 증가하면 Brose는 프로토타입과 생산을 위해 3대의 Fuse 시리즈 SLS 3D 프린터를 사용합니다 자체 지지형 프린트 베드를 갖춘 SLS 3D 프린팅은 완벽한 포장의 생산 볼륨 빌드를 가능하게 하며, 소결 나일론의 강도와 기계적 특성 덕분에 이 기술은 최종 사용 구성 요소에 이상적입니다. 최근 프로젝트에서 Brose의 적층 기술 팀은 시트 서스펜션 매트의 프로토타입을 만드는 데 SLA와 SLS 기술을 모두 사용했습니다.
Form 시리즈 SLA 3D 프린터에서 Durable Resin 로 반투명하고 유연한 파트를 프린팅했고, Fuse 시리즈 프린터에서 Nylon 12 GF Powder로 매트의 연결 튜빙을 프린트했습니다. 각 매트 프로토타입에는 SLS 파트가 6개, SLA 파트가 3개 있었지만, 팀은 전체 매트 150개를 조립하여 완전한 시트 조립의 일부로 테스트했습니다.
Brose는 자체적으로 신속한 프로토타입 제작 도구를 사용하여 툴링이나 아웃소싱 없이도 좌석 조립 제품의 중요한 구성 요소를 설계, 테스트하고 반복할 수 있었습니다. Schulz는 “때로는 SLA와 SLS를 결합하는 것이 답입니다. 이 시트 서스펜션 매트처럼요. 오버몰드 도구는 매우 복잡하고 비싸기 때문에 SLS를 위해 와이어 위에 파트를 끼울 수 있도록 설계하고 와이어에 "그린 상태"의 SLA 파트를 설치하여 그 방식으로 경화시켰습니다.”라고 합니다.
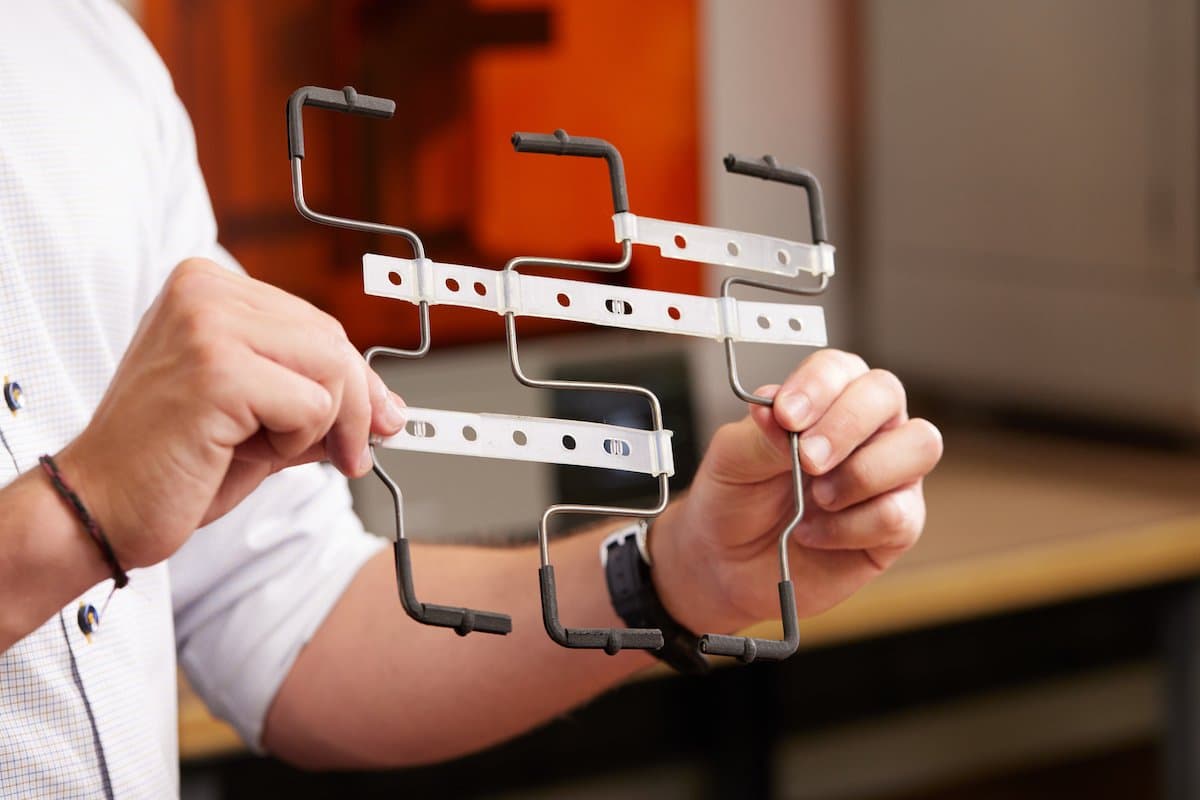
이 시트 서스펜션 매트는 SLA 파트(Durable Resin, translucent material)와 SLS 파트(Nylon 12 GF Powder, 진한 회색 소재)로 구성되어 있습니다. 테스트에는 SLS 파트 900개와 SLA 파트 450개를 포함하여 전체 어셈블리 150개가 필요했습니다.
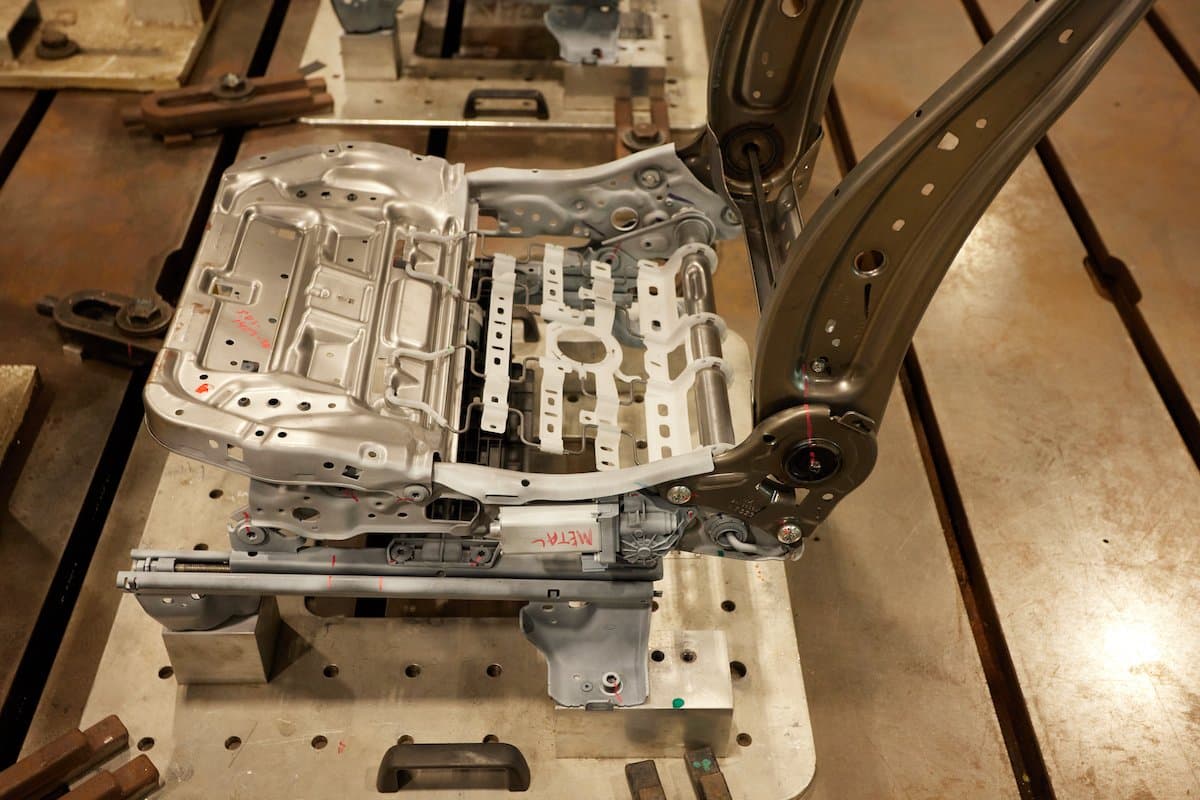
프로토타입과 최종 사용 생산 버전(위와 같은)은 수년간의 사용을 모방한 피로 테스트를 거칩니다.
제조 보조 도구를 이용한 생산 간소화
Brose에서는 적층 제조를 프로토타입 제작 도구로만 사용하는 것이 아니라 2022년에 출시된 Plant Goes Additive 이니셔티브의 일환으로 모든 부서에 기술을 통합하고 있습니다. 자동차 제조는 끊임없이 진행되고 엄격한 통제가 이루어집니다. 모든 공정이 효율과 안전성, 그리고 제품 우수성을 위해 간소하고 최적화되었습니다.
Form 4L에 올려진 당일 제작 로봇 용접 고정 장치
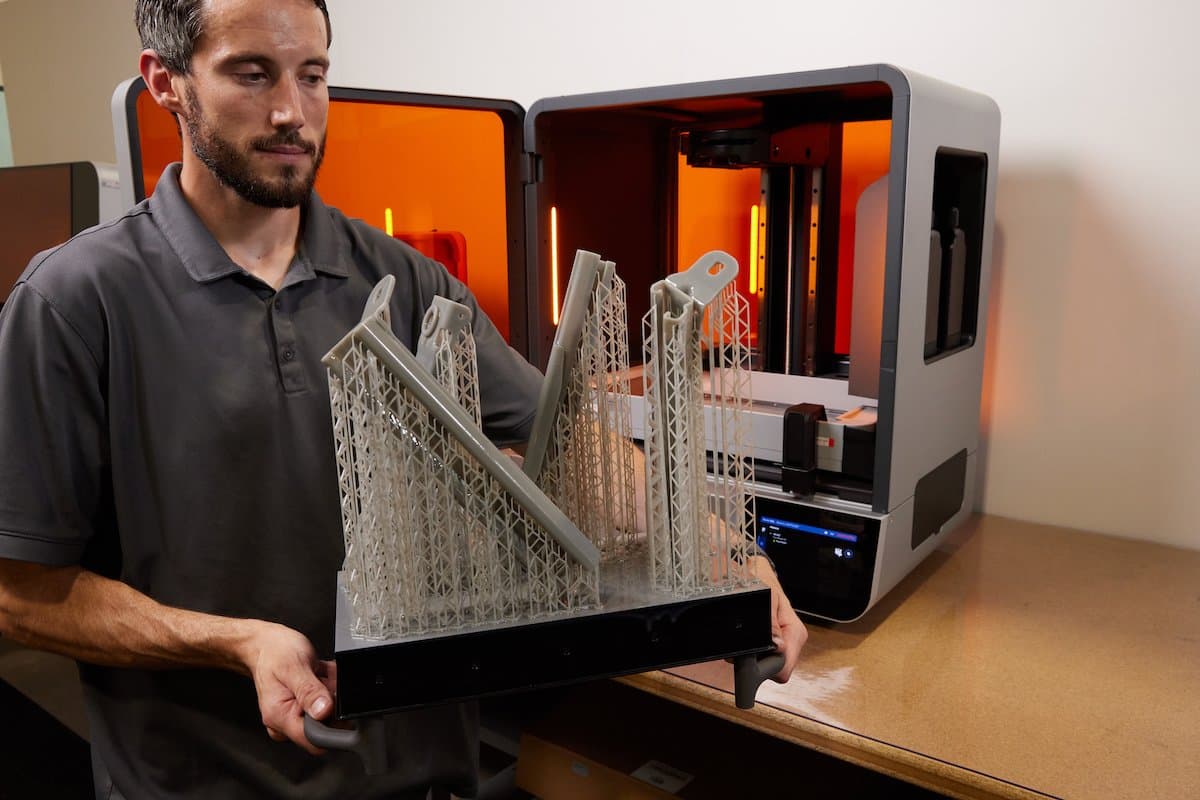
Form 4L을 사용하면 Fast Model Resin으로 프린트된 이 용접 맞춤 장치처럼 당일 대형 파트 생산이 가능합니다.
Form 4L을 사용하면 Fast Model Resin으로 프린트된 이 용접 맞춤 장치처럼 당일 대형 파트 생산이 가능합니다. 당연히 용접은 조립 과정에서 매우 큰 부분을 차지합니다. Brose의 Additive Technology 팀이 SLA 및 SLS 프린터를 운영하는 Brose North America에서 용접 로봇은 다양한 제품 라인 간에 지속적으로 전환해야 합니다. 공장에서는 용접 기계가 하나의 제품 라인에 맞게 프로그래밍되어 있는 반면, 본사에서는 두 대의 로봇 기계가 각기 다른 제품 라인의 시트 프로토타입을 용접하는 작업을 담당합니다.
로봇이 새로운 제품 라인으로 전환해야 할 때마다 용접 부서에서는 매개변수를 다시 프로그래밍해야 합니다. 프로토타입 금속 레일을 사용하여 용접 로봇을 프로그래밍하는 작업은 비용이 많이 들고, 용접 스테이션이 장비를 교육할 준비가 되었을 때 이러한 레일을 사용할 수 없는 경우가 많습니다. 3D 프린팅은 설치 파트에 속도와 치수 정확성이 필요하므로 빠르고 저렴한 솔루션을 제공합니다.
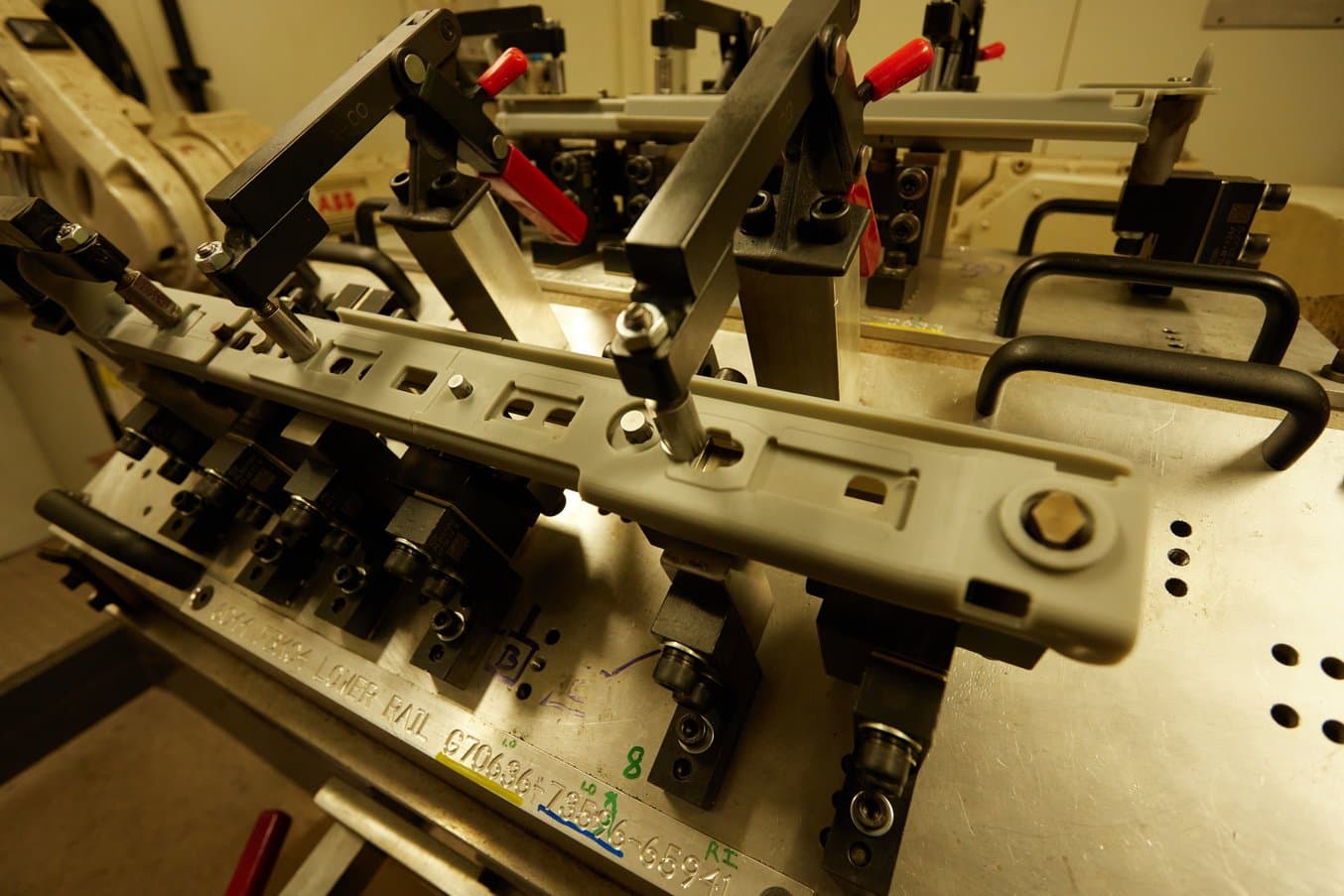
이 좌석 부분은 Fast Model Resin을 Form 4L에서 프린팅한 후 세척, 경화 과정을 거쳐 3시간 이내에 로봇 용접기에서 조립되었습니다. 이를 통해 팀은 로봇의 동작을 빠르게 가르칠 수 있습니다.
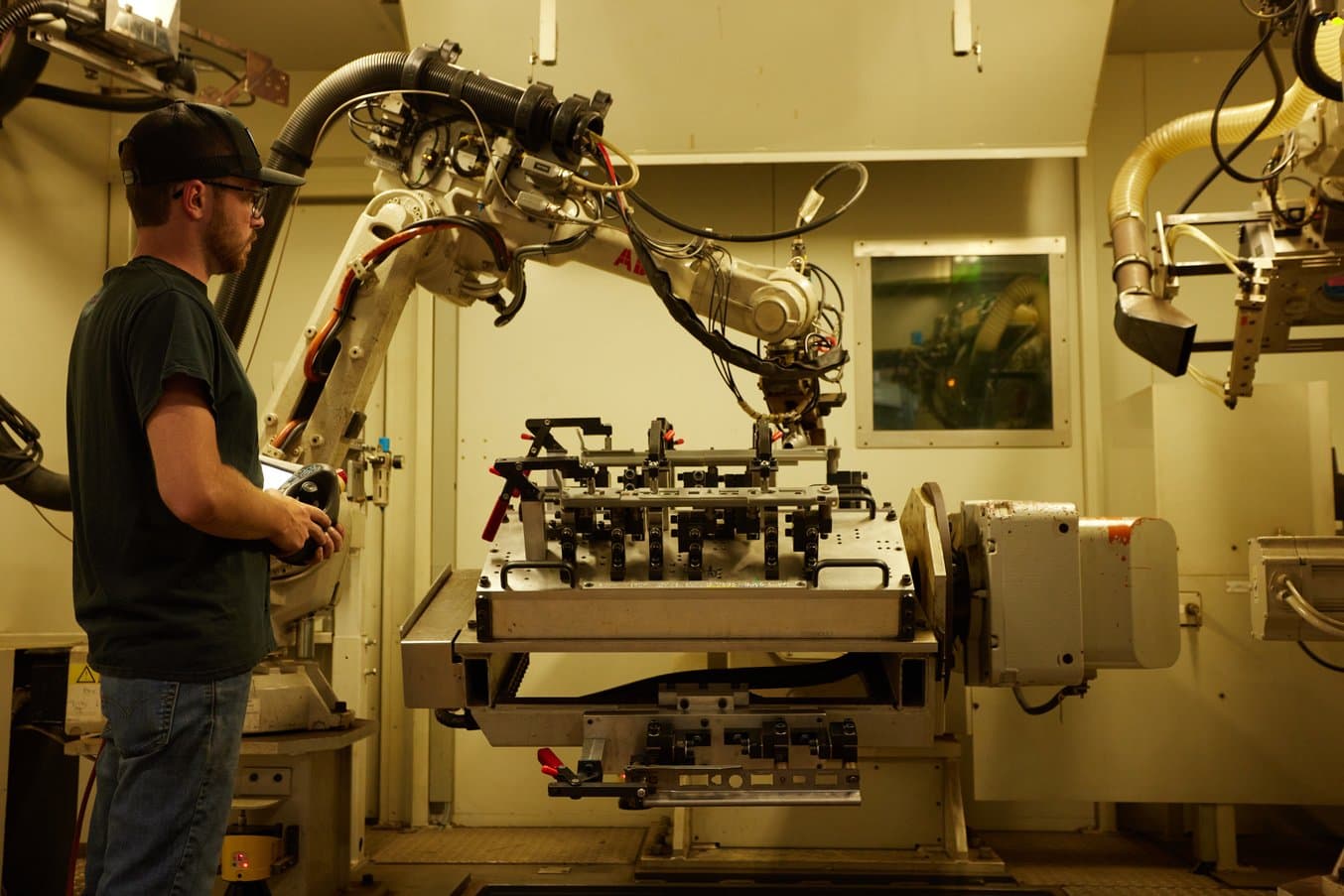
이러한 고정구는 용접팀이 제품군 간에 빠르고 효율적으로 전환하는 데 도움이 됩니다. 이러한 제품은 정확도가 높고 저렴하며, 변경이나 교체가 필요한 경우 무한정 복제가 가능합니다.
The Brose팀은 화요일 아침에 새로 도착한 대형 레진 3D 프린터인 Form 4L을 공개했습니다. 설치에 걸린 시간은 불과 30분이었고, 곧 Fast Model Resin을 사용하여 대형 용접 설치 파트를 프린팅하기 시작했습니다. 4개의 조각으로 나뉜 파트는 빌드 볼륨 전체를 거의 다 채웠습니다. 크기에도 불구하고 Form 4L로 2시간도 안 걸려 프린트했고, 간단한 세척과 후경화 과정을 거친 후 불과 45분 만에 용접 로봇에 고정물을 장착했습니다.
“새로운 Formlabs 4L을 사용하면 대형 파트를 빠르게 프린트할 수 있습니다. 예를 들어, 우리는 Form 4L로 밤새 프린트하는 대신 단 몇 시간 만에 용접 셀의 설정 파트를 프린트합니다. 이렇게 해서 Brose의 용접 전문가가 금속 스탬핑 구성 요소가 도착하기 전에 로봇을 프로그래밍할 수 있습니다. 새로운 Fast Model Resin을 사용하면 이전보다 훨씬 짧은 시간 안에 필요한 디테일과 강성을 얻을 수 있습니다.”
Matthias Schulz, Brose North America, 시트 프로토타이핑 관리자
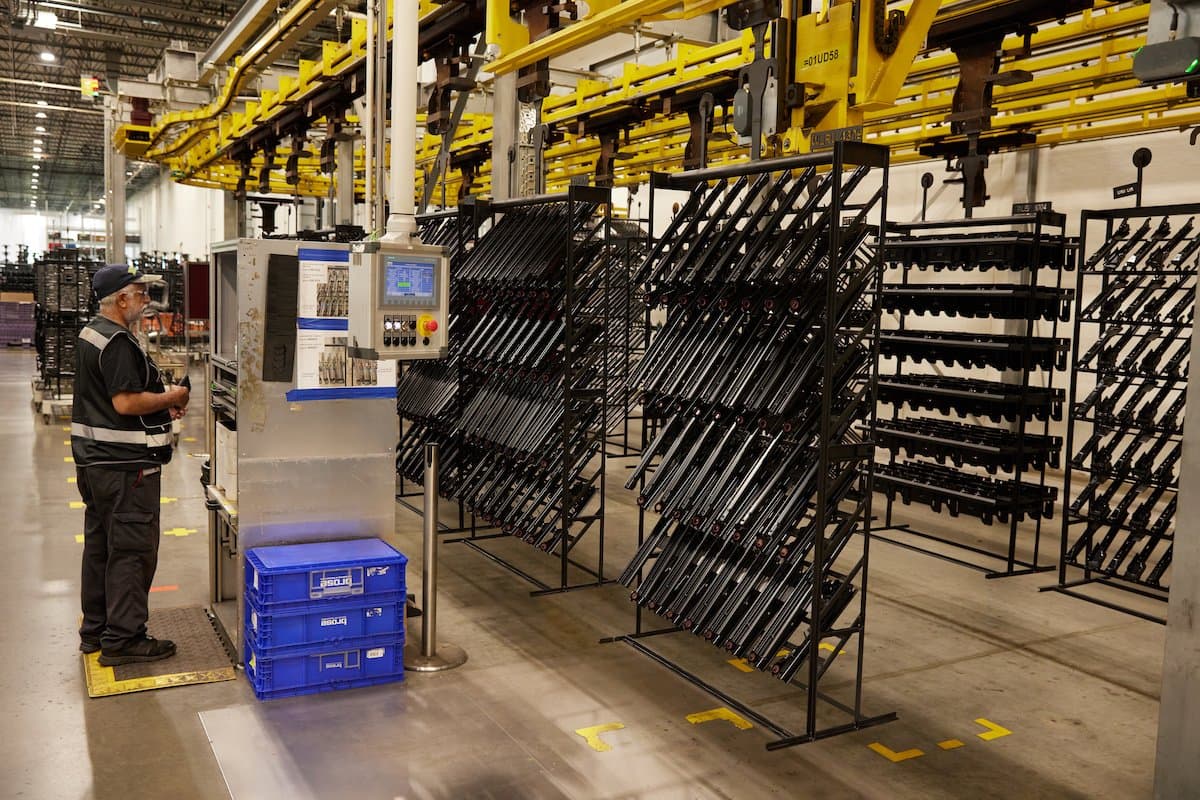
Brose New Boston에서는 위에 보이는 수천 개의 좌석 레일을 용접하여 좌석 조립체의 바닥을 형성합니다. 용접 파라미터 테스트는 제조 공정에 필수적입니다.
Brose North America에서 프로토타입과 3D 프린팅 설치 파트를 사용하여 결정된 용접 파라미터는 용접 시트 프레임의 대량 생산에 사용됩니다. 위의 시트 레일은 Brose New Boston에서 대형 로봇 용접 기계를 이용해 조립됩니다.
End-of-Line(EOL) 커넥터를 이용한 Brose New Boston의 운영 비용 절감
디트로이트 도심에서 서쪽으로 약 30분 거리에 있는 브로즈의 뉴보스턴 공장에서 팀은 3D 프린팅을 활용하여 조립 공정을 간소화하는 맞춤형 제조 보조 도구를 만듭니다. 3D 프린팅 파트는 생산에 통합되기 전에 엄격한 테스트를 거치며, 승인을 받으면 낭비를 줄이고, 생산 일정을 개선하고, 기계를 일관되게 작동하는 데 도움이 됩니다.
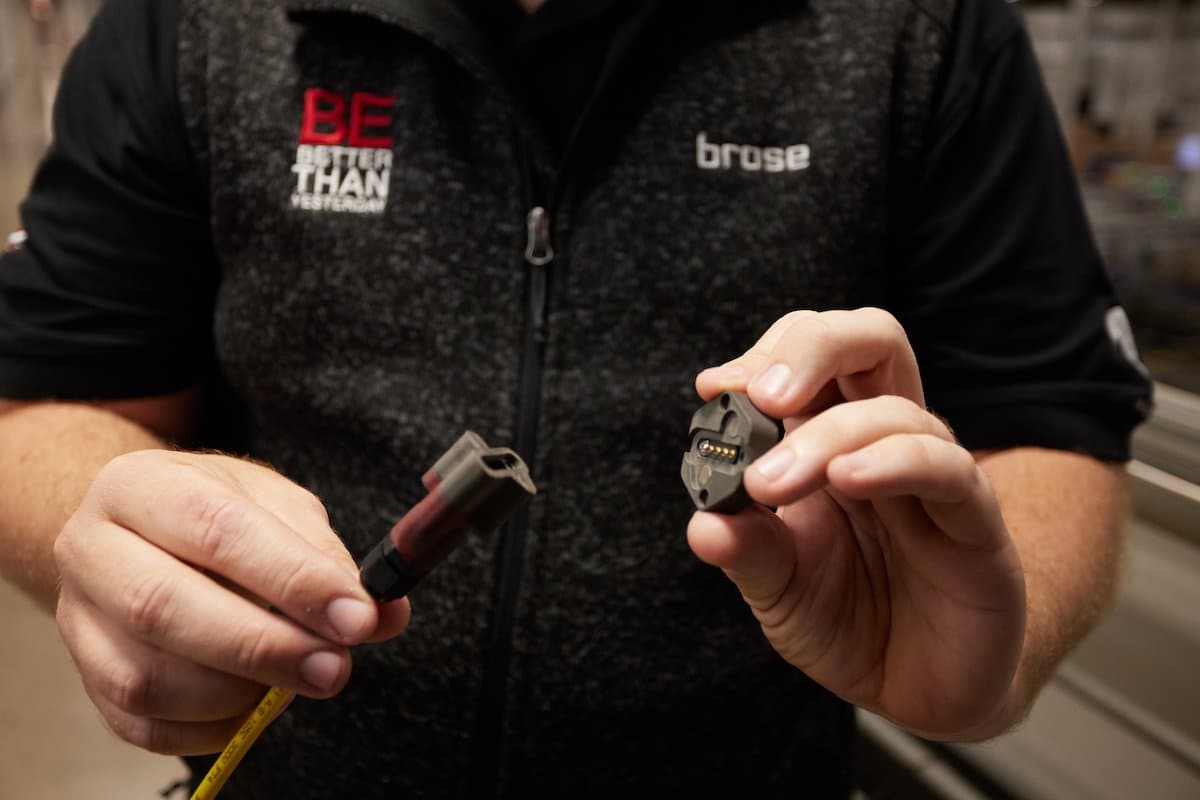
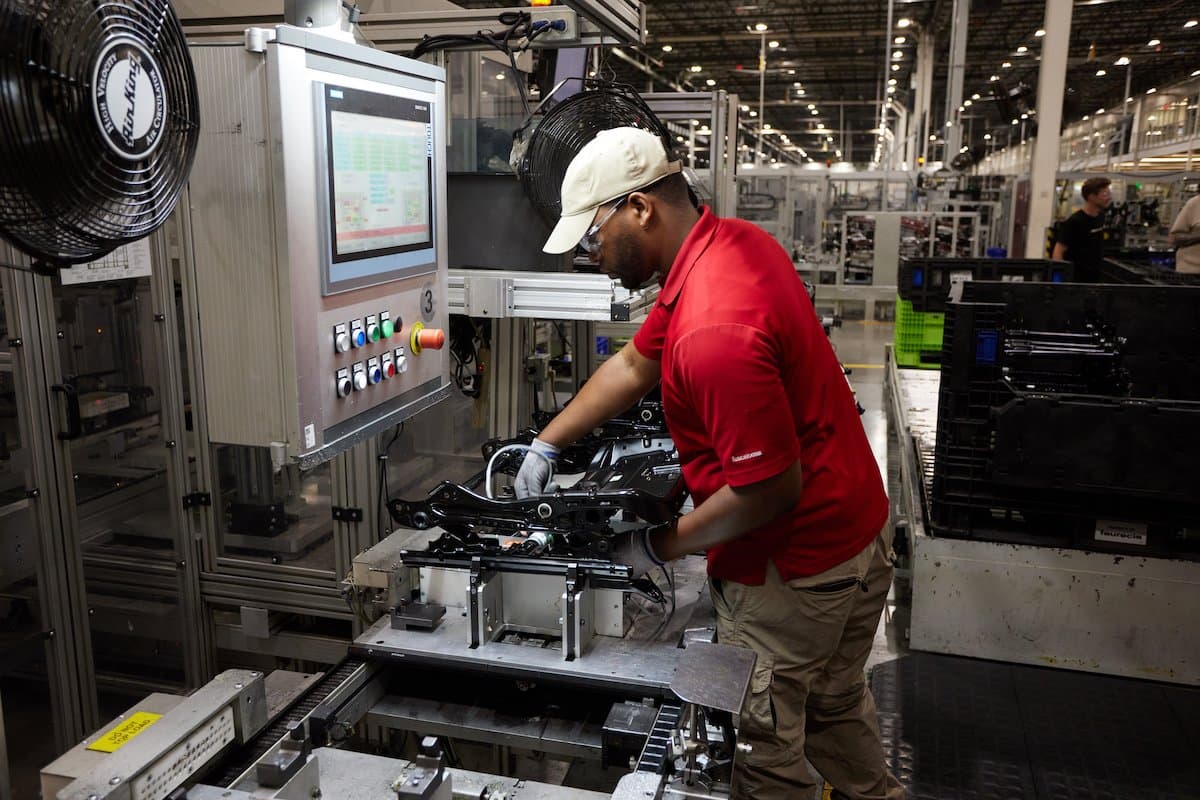
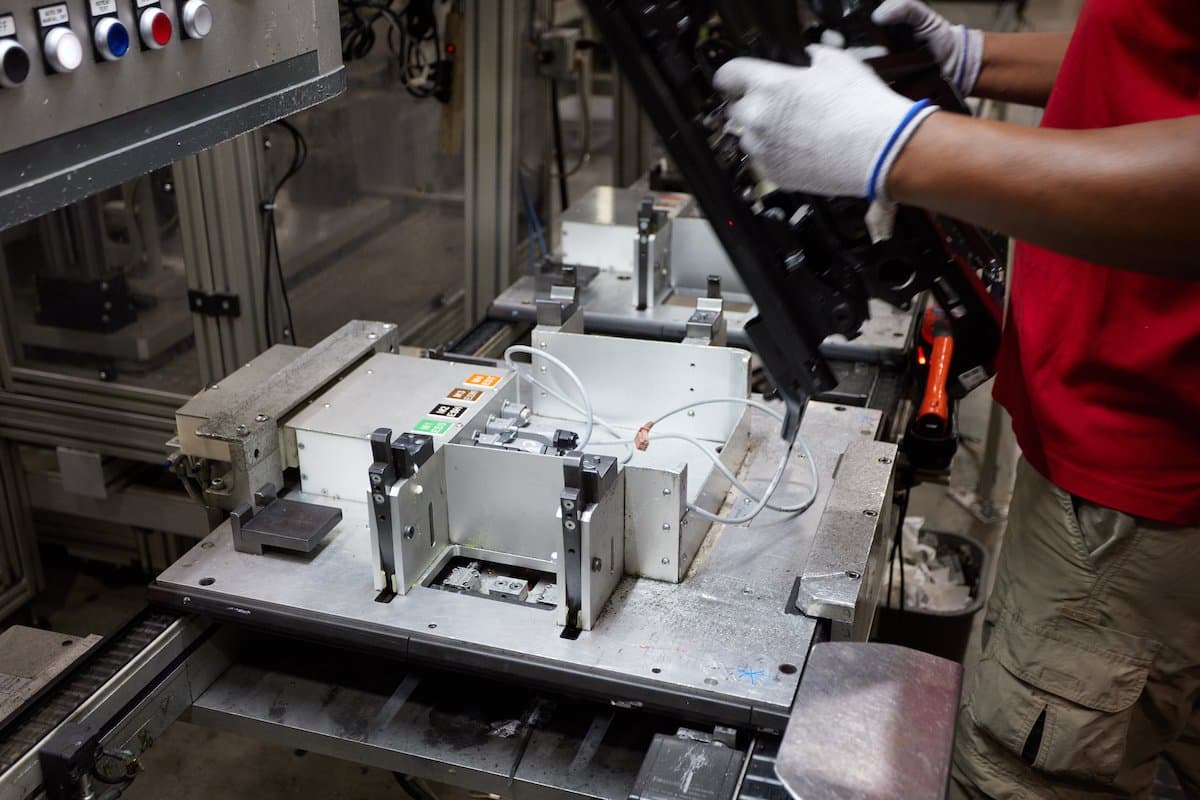

이 EOL(end-of-line)커넥터 조각은 시트 조립 공정의 마지막 단계에 구현되었습니다. 기술자가 좌석 프레임을 전원에 연결하고 최종 검사를 수행한 후, 좌석 프레임을 제거하여 다음 공정 단계로 넘어갑니다. 기술자들이 전기 연결을 잊어버린 채 좌석을 제거하는 과정에서 코드가 끊어지는 일이 많았고, 조립 라인에 수백 달러 상당의 피해가 발생하여 생산이 중단되기도 했습니다.
적층 기술 팀은 뉴보스턴 팀과 협력하여 자기 커넥터 라인을 설계했습니다. 기술자가 코드를 수동으로 제거하지 않고 좌석 프레임을 잡아당기면 코드와 좌석 프레임에 쉽게 부착되지만, 아무런 손상 없이 끊어집니다. Schulz는 “우리는 기계의 마모와 파손을 줄이기 위해 3D 프린팅 제조 보조 도구를 사용합니다. 이를 통해 생산 라인에서 더 빠른 수리가 가능해졌습니다. 이를 통해 생산 중단 시간이 줄어들고 전체 생산량도 늘어나는 데 도움이 됩니다.”라고 합니다.
최종 사용 자동차 파트를 위한 직렬 갭 생산
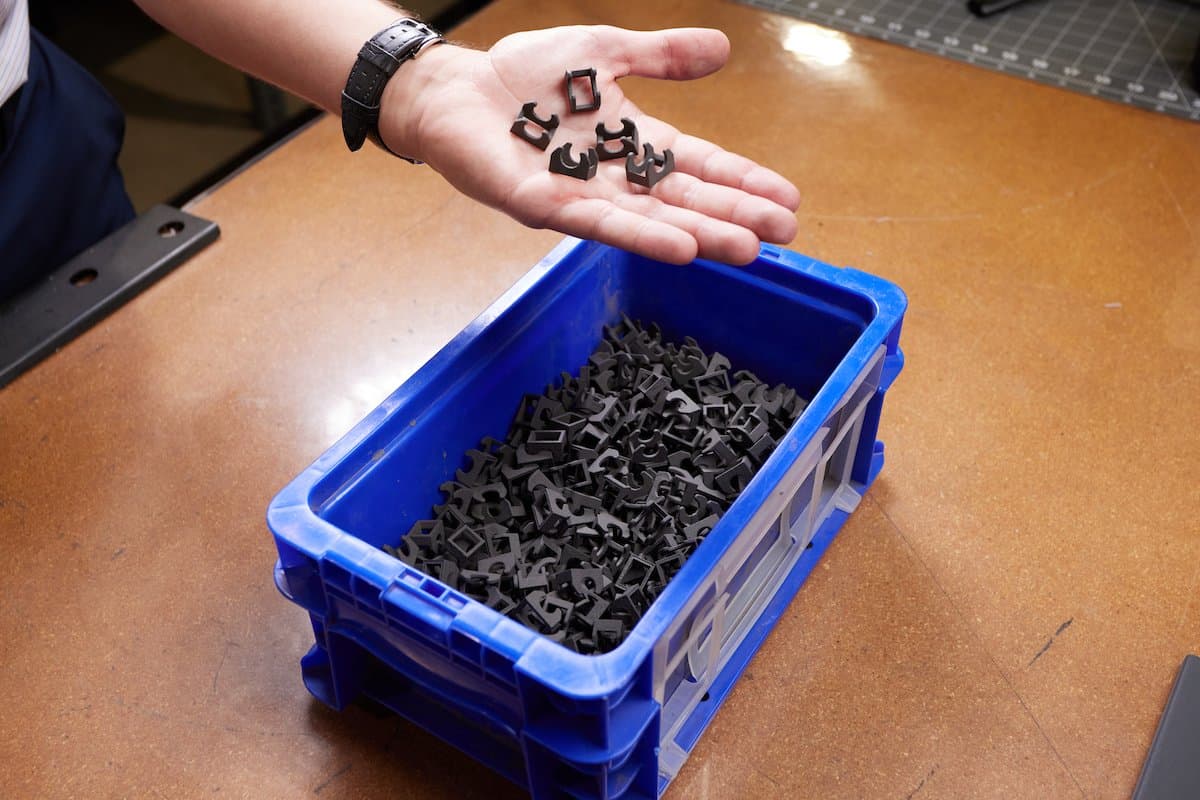
Brose는 BMW X7의 시트 조립을 위해 이 클립 25만 개를 3D로 프린트할 예정입니다.
Schulz가 말했듯이 자동차 산업은 특히 지난 5년 동안 빠르게 변화하고 있습니다. 전기 자동차의 부상, 맞춤형 기능에 대한 수요 증가, 공급망에 대한 우려 등으로 인해 OEM은 생산을 위한 신뢰할 수 있는 대안으로 적층 제조에 더 많은 투자를 하게 되었습니다.
“적층 기술을 요청하는 고객이 점점 늘어나고 있습니다. 또한 최종 사용 고객을 위한 고객 인터페이스에서도 역할을 합니다. 최종 사용 고객은 차량에 더 많은 개인화를 원하기 때문에 OEM에서 적층 기술을 점점 더 많이 요구하고 있기 때문입니다."라고 Schulz 씨는 말합니다.
특히 규제가 엄격한 자동차 산업에서 최종 사용 파트를 항상 3D 프린팅할 수 있었던 것은 아닙니다. Brose의 적층 제조 팀은 하드웨어와 재료의 품질이 고성능 파트를 안정적으로 제공할 수 있는 경우에만 최종 사용 생산으로 전환하도록 했습니다.
“우리는 여기서 Formlabs 보트에 뛰어들기로 결정했습니다. 우리가 그렇게 한 이유는 재료의 가용성과 프린트물의 일관성이 크게 개선되어 이 기술이 이제 자동차 산업에 도움이 될 준비가 되었기 때문입니다. 우리에게 문제가 되는 것은, 특히 OEM의 경우 안전성과 내구성에 대한 우려가 존재한다는 것입니다. 이 문제를 배제하려고 했습니다. 그리고 Formlabs와 협력하여 현재의 BMW X7에서와 같은 파트를 구현할 수 있다는 것을 증명했습니다."
Matthias Schulz, Brose North America, 시트 프로토타이핑 관리자
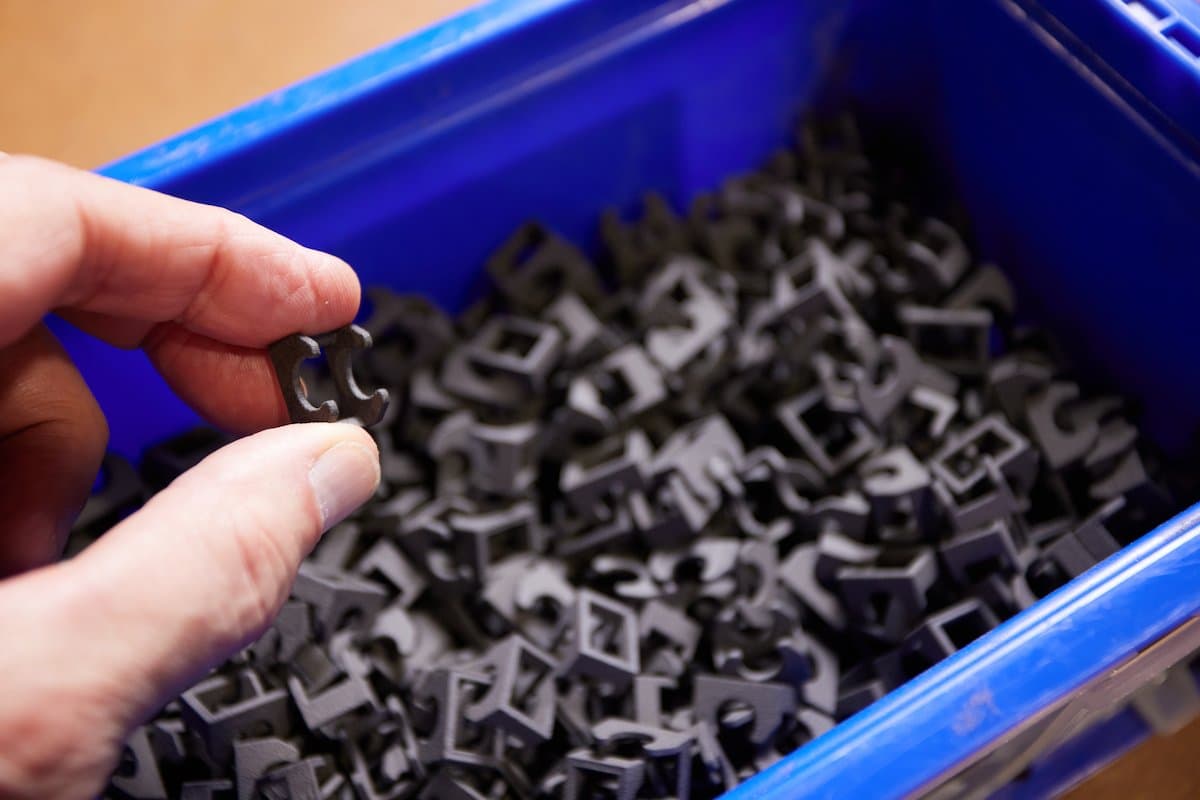
응용 분야: BMW X7 시트 컴포넌트
워크플로: 3D 스캐닝, 반복 설계, 최종 사용 생산을 위한 Fuse 시리즈 SLS 3D 프린터로 3D 프린팅
물량: 250,000
빌드 세부사항:
- 프린터: Fuse 1와 Fuse 1+ 30W
- 소재: Nylon 12 GF Powder
- 빌드 볼륨: 빌드 챔버당 파트 1,440개
- 월간 파트 생산량: 16,000개
3D 프린팅의 목적은?
- 공구 확보까지 전환 시간 확보용 갭 프린팅
Brose는 기존 제조 방식에 비해 저렴하고 빠른 대안으로 3D 프린팅을 최종 생산에 활용합니다. OEM이 툴링 및 대량 생산이 어려운 파트를 요청하거나 기존 파트를 변경해 달라고 요청하면 브로제의 적층 사업부에서 3D 프린팅이 적합한지 평가합니다. 그 중 큰 부분은 기존 구성 요소의 역엔지니어링과 스캐닝입니다.
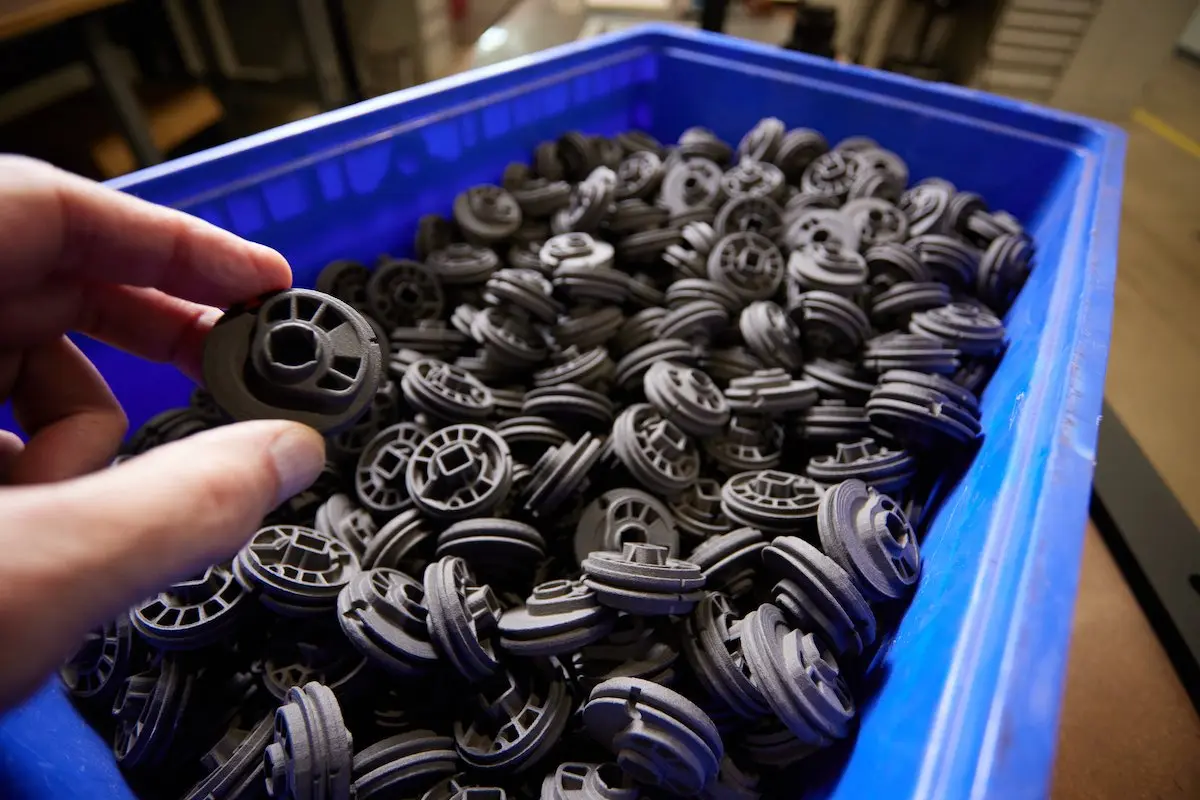
응용 분야: 보우덴 릴리스
워크플로: 3D 스캐닝, 반복 설계, 최종 사용 생산을 위한 Fuse 시리즈 SLS 3D 프린터로 3D 프린팅
물량: 20,000
빌드 세부사항:
- 프린터: Fuse 1와 Fuse 1+ 30W
- 소재: Nylon 12 GF Powder
- 처리량: 챔버당 144개 파트, 주당 1000개 파트
왜 3D 프린팅인가?
- 공구를 사용할 수 있는 시간까지의 전환 시간 확보용 갭 프린팅
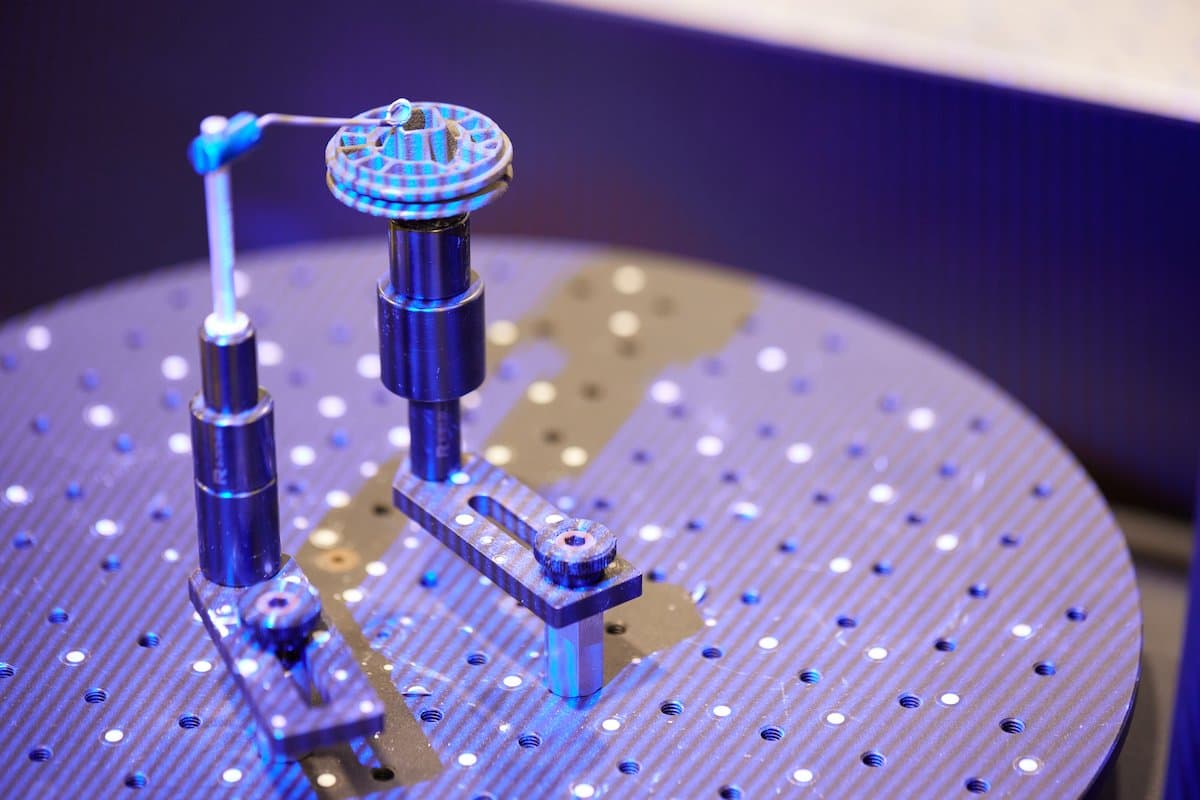
Brose는 기존 구성 요소나 이전 반복 작업을 스캔하여 CAD에서 변경 사항을 적용하고 같은 날 업데이트된 버전을 3D 프린팅합니다.
이 구성 요소는 Bowden 릴리스입니다. 이 파트 20,000개가 Brose의 Fuse Series SLS 3D 프린터에 프린트되어 유명 대형 OEM의 최종 시트 조립에 포함됩니다.
Schulz는 “Brose는 Formlabs에서 SLS를 도입하기로 결정했습니다. SLS 기술은 SLA에서 보는 것보다 후처리 요구 사항이 적은 빠르고 신속한 3D 프린트를 가능하게 하기 때문입니다. 우리는 갭 프린팅이나 기타 OEM 관련 최종 사용 고객 파트를 지원하는 데 필요한 대량 프린트가 가능합니다.”라고 합니다.
3대의 Fuse 시리즈 SLS 3D 프린터가 쉬지 않고 작동하여 프로토타입, 제조 보조 도구 및 수십만 개의 최종 사용 구성 요소를 생산하기 때문에 안정성과 일관성이 중요합니다. 이 팀에서는 사출 성형 나일론과의 유사성과 치수 정확성이 뛰어나 대량 생산에서도 Nylon 12 GF Powder를 사용합니다. 풀 빌드가 매번 완료된 후, Fuse 1 또는 Fuse 1 30W에 대한 간단한 유지 관리 점검을 수행하는 데 걸리는 시간은 약 15분으로, 지속적이고 효율적인 생산이 보장됩니다.
Schulz는 “Formlabs는 유지 관리가 쉬운 프린터를 만드는 방법을 알고 있습니다. 장비가 매우 안정적이고 프린트 실패가 거의 발생하지 않아 더 많은 양의 파트를 프린트하고 생산에 나설 수 있는 자신감을 가질 수 있었습니다.”라며 만족스러워했습니다.
0에서 60까지: 자동차 분야에서 속도가 빨라진 3D 프린터
Brose는 지속적인 개선에 대한 의지를 바탕으로 적층 제조 및 자동화와 같은 신기술에 투자하여 프로세스를 간소화하고 각 고객에게 혁신적인 솔루션을 제공했습니다. 3D 프린팅이 회사에서 점점 더 큰 역할을 하게 되면서, 슐츠와 같은 옹호자들은 빠른 처리 시간과 (대부분의) 더 낮은 비용을 활용할 수 있는 새로운 방법을 찾는 데 전념하고 있습니다.
Form 4, Form 4L, Fuse 시리즈와 같은 빠르고 강력한 도구를 사용하면 프로토타입, 제조 지원 도구, 최종 사용 구성 요소를 몇 주 또는 몇 달이 아닌 몇 시간 또는 며칠 만에 완료할 수 있습니다. “Formlabs은 협력하기에 꼭 맞는 파트너입니다. 우리는 엔지니어링 지원을 덜 받으면서 더 많은 양의 파트를 생산할 수 있는 턴키 솔루션이 필요했습니다. Formlabs의 소프트웨어, 지원 및 프린터는 모두 적합합니다.”
자동차 산업에서의 3D 프린팅을 자세히 알아보려면 당사 웹사이트를 방문하세요. SLS 3D 프린팅 품질을 직접 알아보려면 샘플을 요청해 주세요.