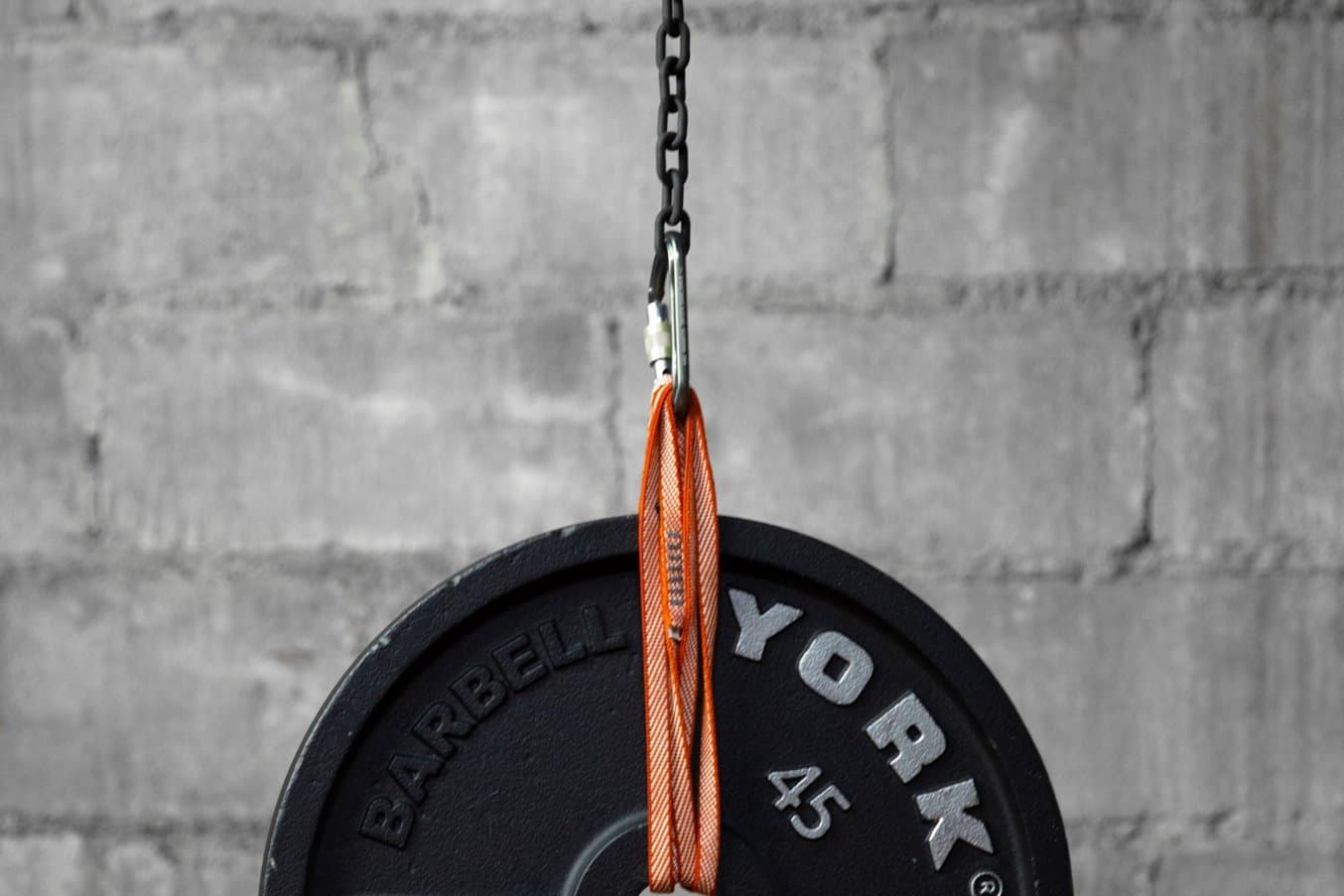
자전거, 경주용 자동차, 드론, 테니스 라켓 등은 용도가 다양한 제품이지만 모두 무게는 늘리지 않으면서도 높은 강도와 내구성을 필요로 합니다. 이러한 물성의 조합은 포뮬러 1 경주용 자동차의 섀시부터 경량 로드 자전거의 프레임에 이르기까지 어느 곳에서나 사용되는 탄소 섬유 복합 소재에서 찾을 수 있습니다.
보통 다양한 복합재 등 고분자 기반 소재를 사용하는 전문 3D 프린터도 많아서 "탄소 섬유를 3D 프린트할 수 있나요?"라고 묻는 사람도 많습니다.
사실, 3D 프린팅으로 탄소 섬유 파트를 만드는 방법에는 두 가지가 있습니다. 3D 프린팅 금형을 사용하여 전통적인 제조 방법을 보조하거나 탄소 섬유 복합재를 직접 3D 프린팅하는 것입니다. 이 글에서는 전통적인 제작 방법과 3D 프린팅 탄소 섬유 금형 및 탄소 섬유 복합재 파트를 직접 3D 프린팅하는 새로운 워크플로를 살펴봅니다.
전통적인 방법과 3D 프린팅의 결합으로 탄소 섬유 파트 제작하기
탄소 섬유는 전통적으로 긴 탄소 섬유 가닥을 엮은 다음 더 결합하여 폴리머 형태로 제조하는 복합 소재입니다. 섬유 가닥은 강도가 하나의 특정 벡터를 따라 정렬되도록 전략적으로 직조하거나 최종 제품이 모든 방향에서 다각적인 강도를 갖도록 직조할 수 있습니다. 그런 다음 결과물은 일반적으로 습식 레이업, 프리프레그 라미네이션 또는 레진 트랜스퍼 몰딩성형(RTM)의 세 가지 공정 중 하나를 통해 원하는 최종 제품으로 성형합니다.
습식 레이업
습식 레이업 제조에서는 탄소 섬유 시트를 절단하여 금형에 압착한 다음 액체 레진으로 도장하여 경화 및 응고되면서 시트를 원하는 최종 모양으로 결합합니다. 이 방법은 필요한 장비가 가장 적고 초보자도 가장 쉽게 마스터할 수 있습니다. 대부분 수작업으로 할 수 있기 때문에 비용이 가장 적게 드는 방법 중 하나이지만, 다른 방법으로 생산된 파트에 비해 금형 마스터의 충실도가 떨어진다는 단점이 있습니다.
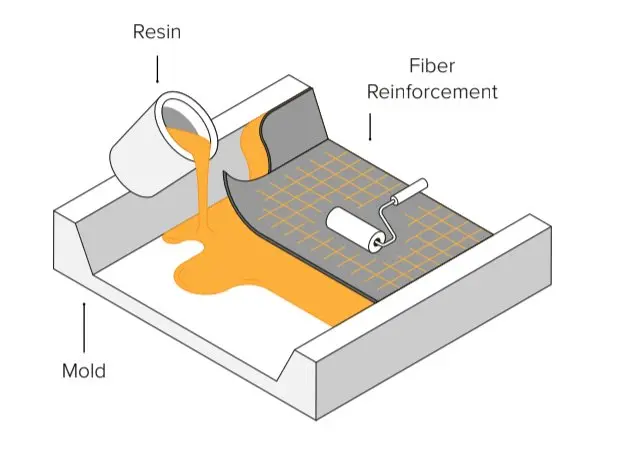
프리프레그 라미네이션
이 방법에서는 탄소 섬유에 이미 수지를 주입한 다음 압력과 열을 사용하여 최종 모양을 형성하는 금형에 삽입합니다. 이 방법은 가열 및 가압 성형기뿐만 아니라 미리 주입된 시트를 보관하고 취급하는 특수 장비가 필요하기 때문에 가장 비용이 많이 듭니다. 이러한 요소는 반복성과 일관성이 가장 뛰어나 탄소 섬유 파트의 일괄 생산에 가장 적합한 요소이기도 합니다.
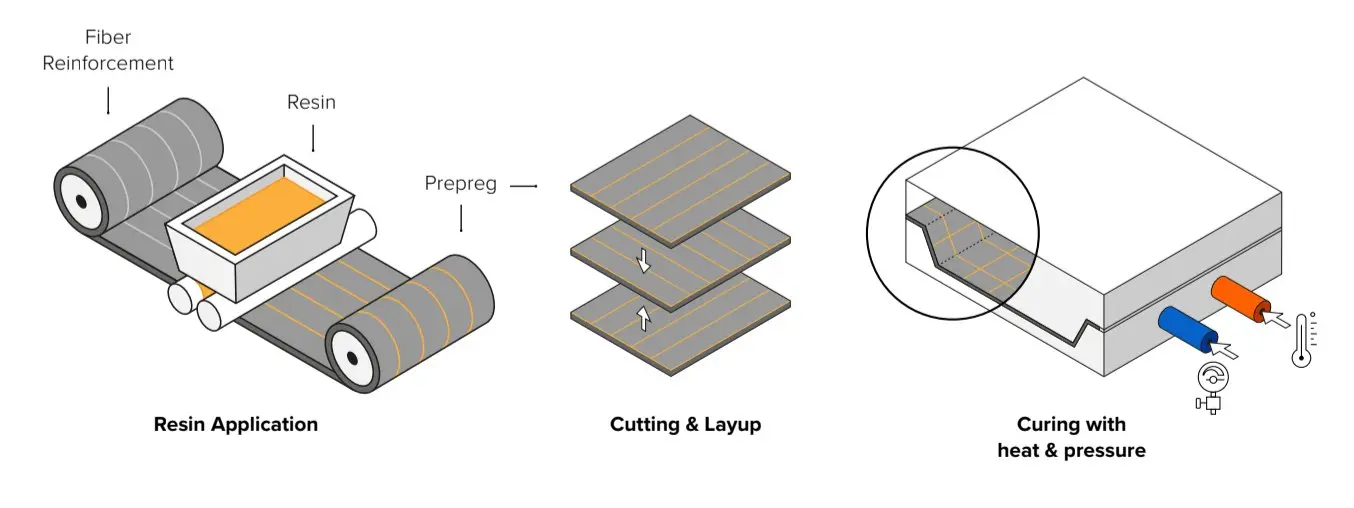
레진 트랜스퍼 성형(RTM)
RTM 성형의 경우, 건식 섬유를 이부 금형에 삽입합니다. 금형을 클램핑된 상태로 닫은 후 고압에서 공동(cavity)에 레진을 밀어넣습니다. RTM은 일반적으로 대량 생산에 사용되는 자동화된 공정입니다.
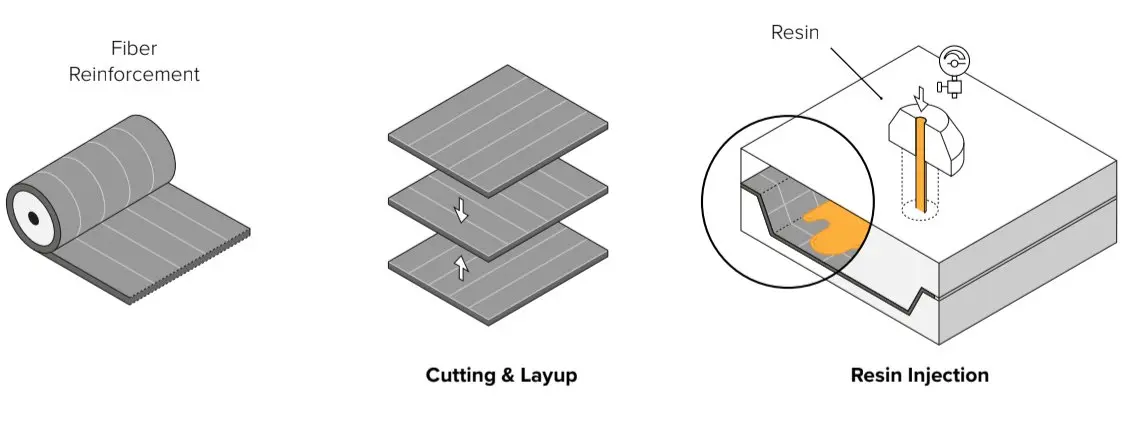
3D 프린트 금형으로 탄소 섬유 파트 제조
앞의 세 가지 방법에 각각 3D 프린팅을 사용하면 비용을 절감하고 리드 타임을 개선할 수 있습니다. 세 가지 전통적인 제조 방법 모두 금형을 하나 또는 여러 개 사용해야 하며, 이러한 금형은 전통적으로 목재, 폼, 금속, 플라스틱 또는 왁스 가공과 같이 시간이 많이 소요되는 서브트랙티브법을 통해 만들어졌습니다. 3D 프린팅은 이러한 금형 제작의 대안이 될 수 있습니다. 3D 프린팅으로 제작된 금형은 맞춤형 제작이 가능할 뿐만 아니라 소량 생산이나 맞춤형 제작에 더 효율적이고 비용 효율적입니다.
자동차 및 항공우주 산업과 같이 제대로 작동하는 프로토타입이 필요한 애플리케이션의 경우 반복적인 공정에 수백 개의 다양한 금형이 필요할 수 있습니다. 전통적인 제조 방법을 사용하여 이러한 반복 작업을 수행하려면 많은 비용과 시간이 소요될 수 있으므로 3D 프린팅은 소량 생산을 위한 효율적인 수단이 될 수 있습니다. 3D 프린트 금형은 금속 금형만큼 대량 생산에 적합하지는 않지만 인하우스에서 저렴하게 제작할 수 있어 제품 개발 및 검증, 단기 생산 속도를 높일 수 있습니다.
탄소섬유 파트 생산용 금형은 다양한 기술로 제작할 수 있지만, 광경화성 수지 조형 방식(SLA) 레진3D 프린터 의 매끄러운 표면 마감과 광범위한 소재 라이브러리는 인하우스 금형 생산 에 일반적으로 선택됩니다. SLA 파트는 레이어 분리선이나 다공성이 거의 없으므로 탄소 섬유 시트를 금형에 단단히 압착하여 표면 질감이 생길 염려 없이 제작할 수 있습니다.
레이싱 및 스포츠카 제조업체인 파노즈는 실내 공기를 배출하고 내부 온도를 낮추기 위해 레이싱카 조종석에 맞춤형 공기 배출 덕트가 필요했습니다. DeltaWing Manufacturing과 협력한 이들은 Formlabs 3D 프린터를 사용하여 High Temp Resin으로 패턴을 프린트한 다음 고온 툴링 에폭시를 사용하여 프린팅된 패턴으로 수작업으로 금형을 주조했습니다. 델타윙은 3D 프린트를 사용하여 이 맞춤형 탄소 섬유 파트에 값비싼 금속 금형을 아웃소싱하지 않음으로써 전체 비용과 납기를 모두 줄일 수 있었습니다.
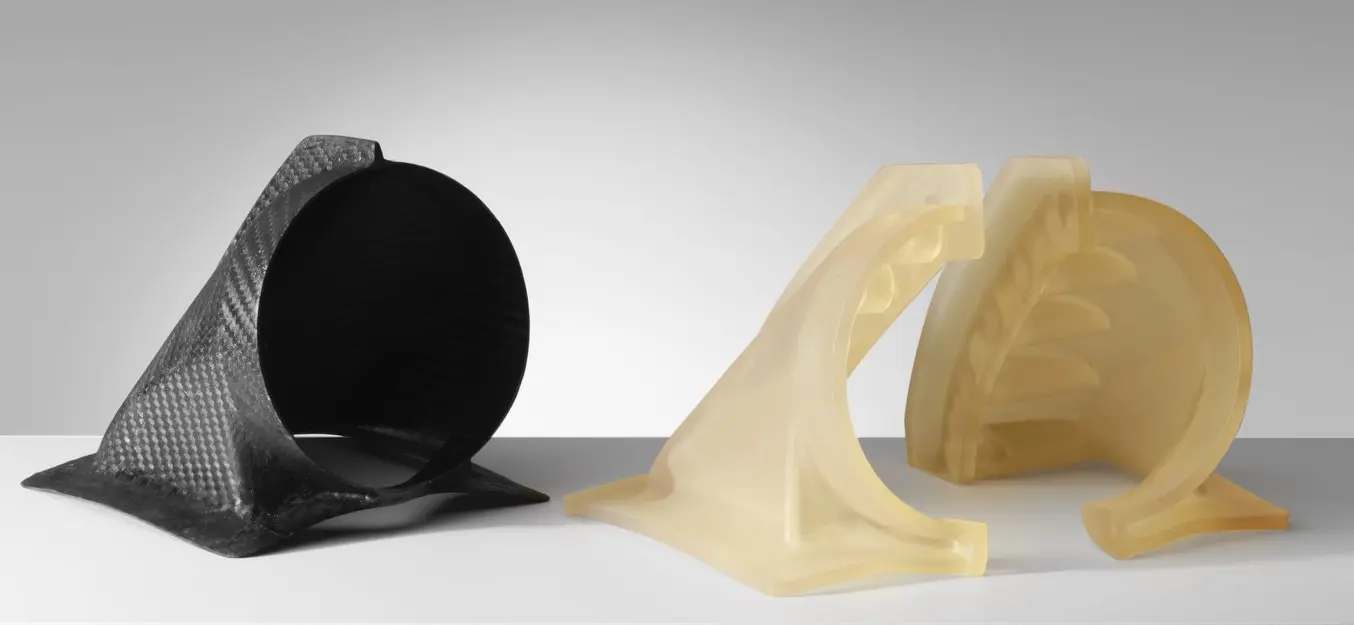
DeltaWing Manufacturing에서 High Temp Resin으로 프린팅한 이분(二分) 금형과 탄소 섬유 펜더 에어 덕트(fender air duct).
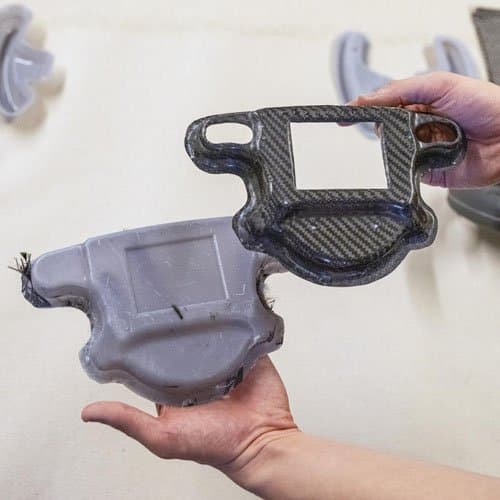
3D 프린팅 금형을 사용한 탄소 섬유 파트 제작
탄소 섬유 파트 제작에 사용되는 프리프레그 및 핸드 라미네이팅 방법에 관한 단계별 지침과 복합 금형 설계 지침을 확인하려면 본 백서를 다운로드하세요.
직접 탄소 섬유 3D 프린트
최고의 탄소 섬유 3D 프린터를 찾고 계신가요? 전통적인 탄소 섬유 파트의 강도, 내구성, 견고성과 3D 프린팅의 민첩성, 기하학적 가능성, 반복성을 결합한 워크플로에 대한 수요가 많습니다. 따라서 탄소 섬유 3D 프린팅을 제공하는 3D 프린팅 기업이 많은 것이 그다지 놀라운 사실은 아닙니다. 현재 이들이 처리할 수 있는 공정은 절단 섬유를 이용하는 방법이나 연속 섬유를 이용하는 방법입니다.
잘게 잘린 탄소 섬유 3D 프린트
잘게 잘린 섬유는 작은 탄소 섬유 조각이 스며든 3D 프린팅 복합 플라스틱 소재를 말합니다. 이렇게 잘게 잘린 섬유는 합성 복합재에 추가적인 강도를 부여하며, 용융 적층 모델링(FDM)을 위한 탄소 섬유 필라멘트 또는 선택적 레이저 소결(SLS) 3D 프린팅을 위한 나일론 분말이 될 수 있습니다.
다른 유형의 폴리머 기반 3D 프린트 재료에 비해 잘게 잘린 탄소섬유 강화 3D 프린트 재료의 주요 장점은 강하고 가벼우며 내열성이 뛰어나고 크리프 현상이 적다는 것입니다. 전통적으로 성형된 탄소 섬유 부품과 비교할 때, 3D 프린팅된 잘게 잘린 섬유는 특히 SLS 3D 프린팅을 통해 파트 설계의 기하학적 유연성이 향상되어 기존 성형과 관련된 많은 노동력을 제거하거나 사용자가 이 재료를 워크플로에 통합할 수 있는 새로운 혁신적인 가능성을 열어줍니다.
Formlabs Fuse 1+ 30W SLS 3D 프린터를 사용하면 이러한 유형의 탄소 섬유 3D 프린팅이 가능하며, Formlabs SLS 재료 라이브러리에서 가장 강력한 소재인 Nylon 11 CF Powder를 사용할 수 있습니다. Fuse 1+ 30W는 잘게 잘린 탄소 섬유를 사용한 SLS 프린팅을 위한 가장 경제적인 고성능 옵션을 제공합니다. 기존 산업용 SLS 장비도 일부 탄소 섬유 소재를 제공하지만, 도입 초기 비용 때문에 RTM 또는 프리프레그 라미네이션 방식과 비교할 때 탄소 섬유 파트의 3D 프린팅에 대한 추가 이점이 많이 상쇄됩니다.
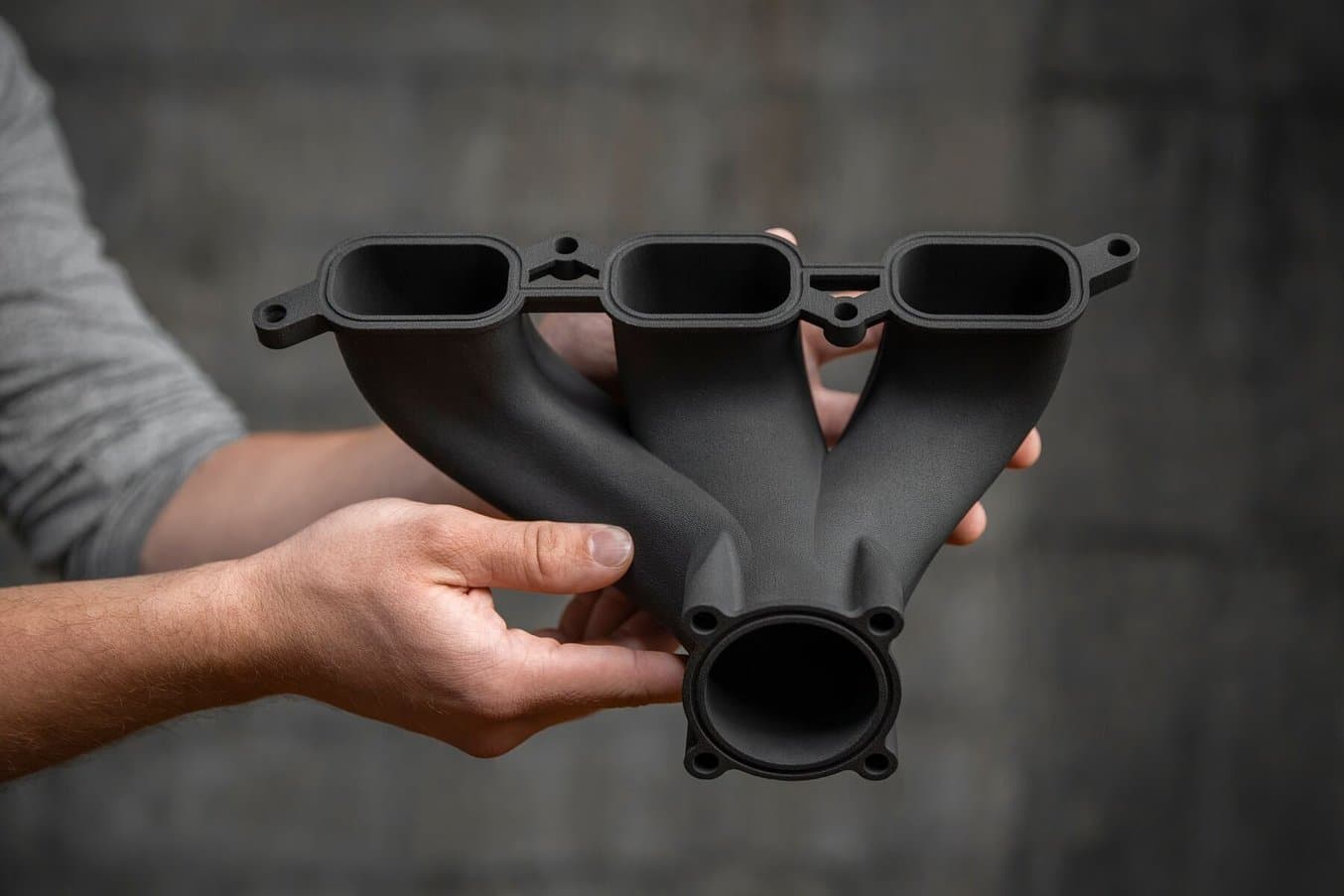
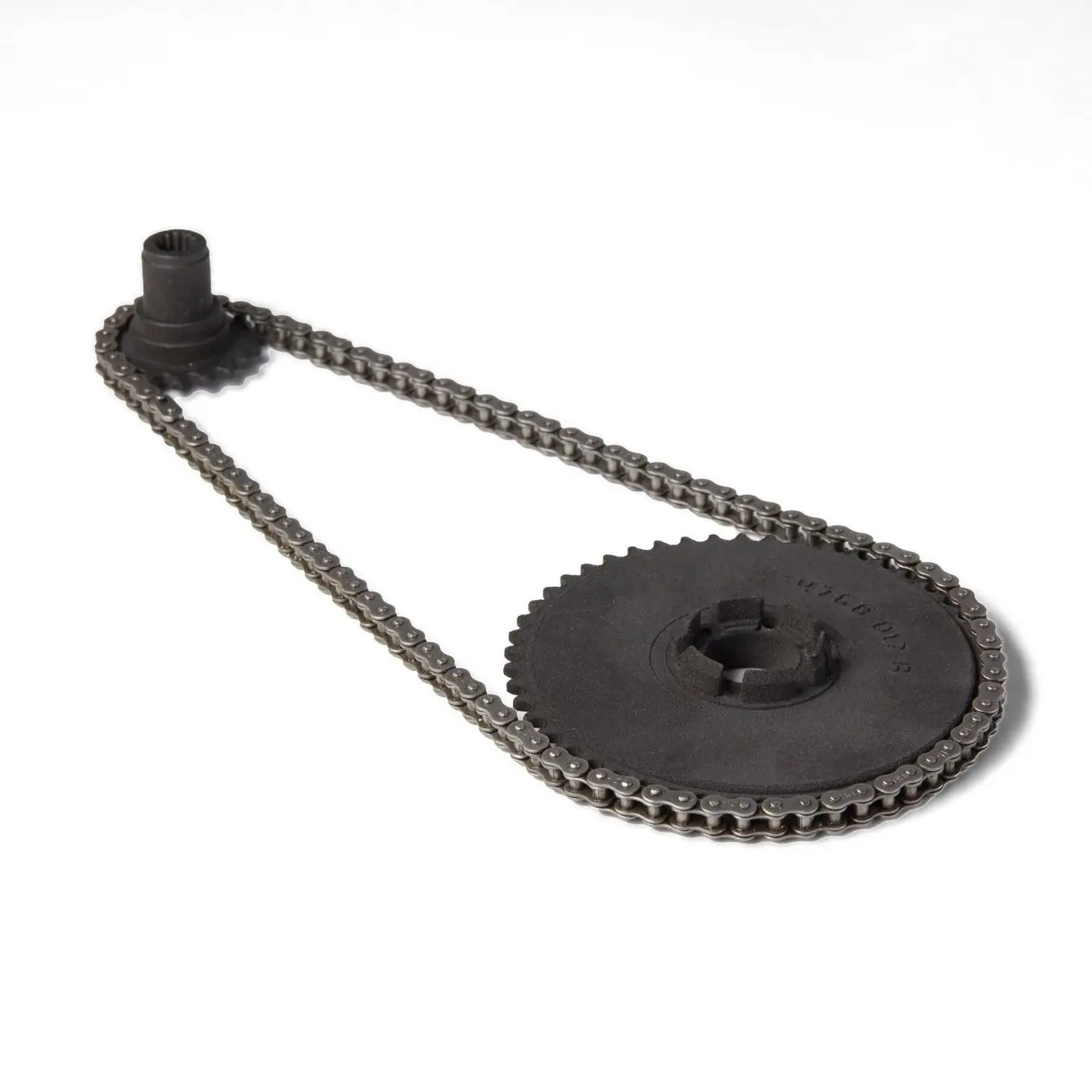
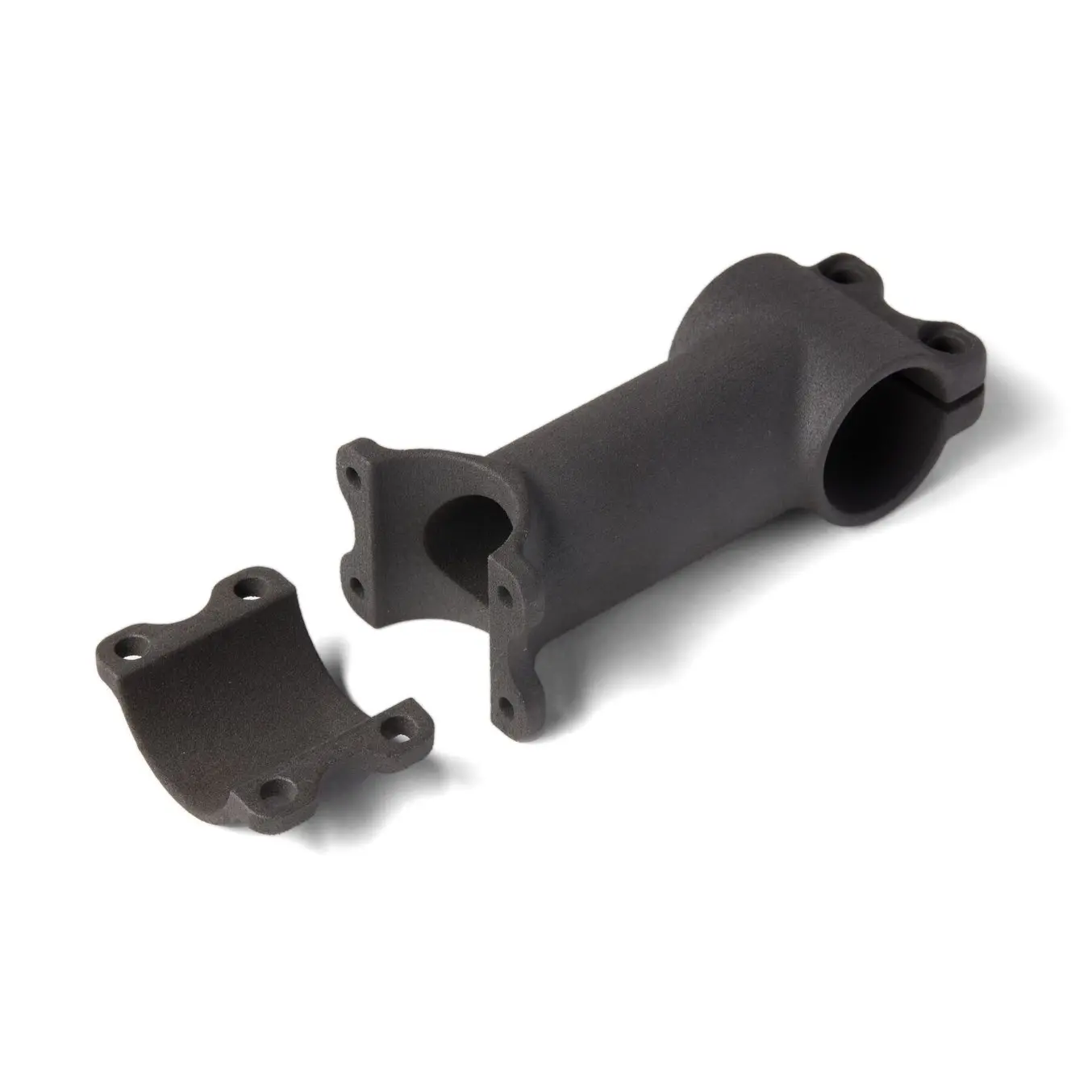
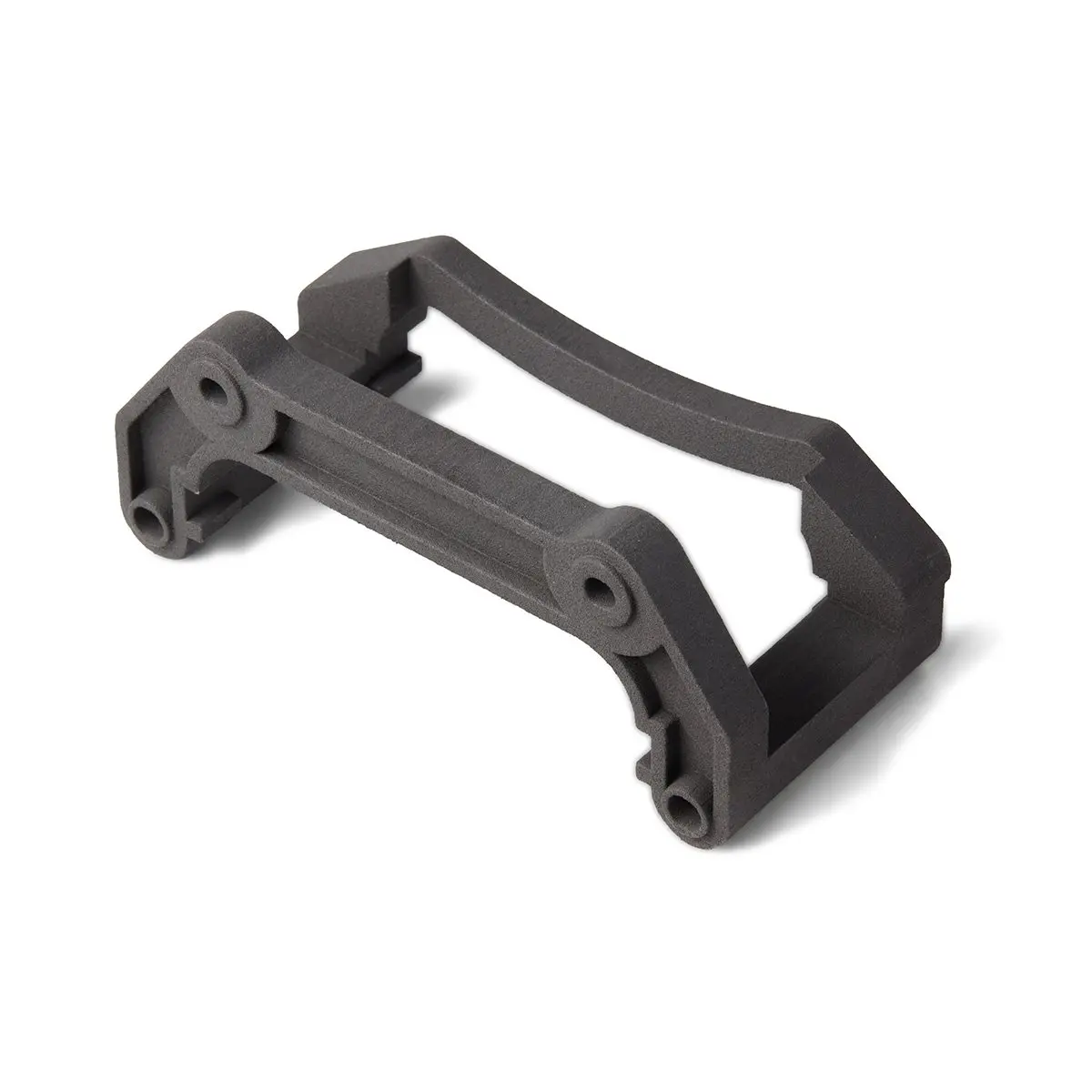
Formlabs의 Nylon 11 CF Powder는 튼튼하고, 가볍고, 내열성이 뛰어나 자동차, 항공우주 및 제조 분야에 적합합니다.
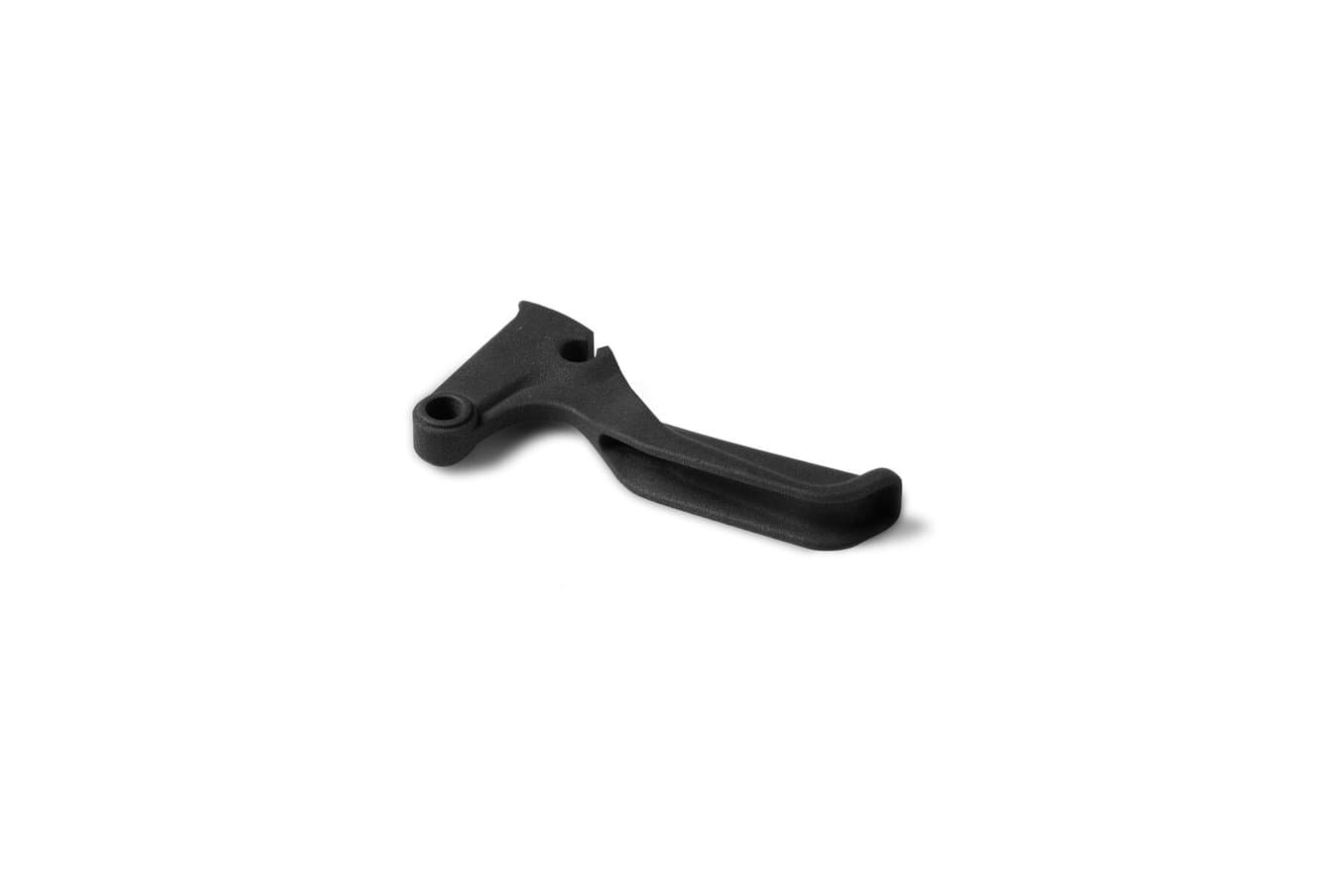
많은 FDM 3D 프린터는 탄소 섬유 필라멘트로 작동할 수 있지만 이러한 재료를 사용한 프린팅은 표준 ABS 또는 PLA 필라멘트보다 더 복잡하기 때문에 연마 필라멘트가 황동 노즐을 마모시켜 잦은 막힘과 유지 관리가 더 필요합니다. 탄소 섬유 필라멘트 절단용으로 특별히 설계된 용융 적층 모델링 방식의 3D 프린터도 사용할 수 있지만 가격이 비쌉니다.
SLS 및 용융 적층 모델링 방식의 3D 프린트 부품의 주요 한계는 모두 직조 및 연속 섬유를 사용한 기존 탄소 섬유 부품의 진정한 대안이 아닌 강력한 3D 프린트 부품으로 간주해야 한다는 것입니다. 또한 3D 프린트 시 누워있는 방향에 따라 강도가 가장 크게 증가하는데, SLS 파트의 경우 X 방향, 용융 적층 모델링 방식 파트의 경우 XY 방향이 가장 강합니다. 기존의 탄소 섬유 파트 제작 방식은 프리몰드 설정에서 다양한 탄소 섬유 시트를 신중하게 계획하고 배치하여 다방향 강도를 구현할 수 있습니다.
연속 탄소 섬유 3D 프린트
연속 탄소 섬유 3D 프린팅은 일부 특수 FDM 3D 프린터에서 사용할 수 있으며 생산되는 파트는 강도 측면에서 기존 탄소 섬유 부품에 근접할 수 있지만 XY 평면에서만 절단 섬유 FDM 프린터와 유사합니다. 이 프린터를 사용하면 연속적인 탄소 섬유 가닥을 열가소성 플라스틱과 혼합하고, 가닥을 전략적으로 적용하여 특정 평면이나 축에 선택적으로 압력을 가할 수 있습니다. 이 방법은 이중 압출기 노즐을 사용하여 탄소 섬유 실과 폴리머를 조합하여 놓거나, 한 노즐이 탄소 섬유 실을 증착하고 다른 노즐이 필라멘트를 가열하여 압출하는 투인원을 사용할 수 있습니다.
연속 탄소 섬유 3D 프린팅은 설계 자유도가 제한적이기는 하지만 기존의 성형 탄소 섬유 부품에 필적하는 대안을 제공합니다. 이 파트는 매우 강하지만 그 강도는 XY 평면에서만 발생하며, 인쇄물은 그 강도와 가해지는 힘의 방향이 일치하도록 방향을 지정해야 합니다. 이것이 가능한 설계의 경우 이 방법을 사용하여 알루미늄 부품을 대체하고 견고한 제조 보조 도구 또는 최종 사용 부품을 만들 수 있습니다.
비교: 전통적인 탄소 섬유 제조와 탄소 섬유 3D 프린트 워크플로 비교
습식 레이업 | 프리프레그 라미네이션 | 레진 트랜스퍼 몰딩 | 잘게 잘린 섬유 용융 적층 모델링 방식 3D 프린팅 | 촙섬유 SLS 3D 프린팅 | 연속 섬유 FDM 3D 프린팅 | |
---|---|---|---|---|---|---|
제조업체 및 모델 | 다양 | 다양 | 다양 | 마크포지드 오닉스, 마크포지드 X3 | Formlabs Fuse 1+ 30W | Markforged Mark Two, 데스크톱 금속 섬유, Markforged X7 |
정확도 | ★★★☆☆ | ★★★★★ | ★★★★★ | ★★★☆☆ | ★★★★★ | ★★★☆☆ |
표면 마감 | ★★★☆☆ | ★★★★★ | ★★★★★ | ★★★☆☆ | ★★★★☆ | ★★★☆☆ |
설계 자유도 | ★★★☆☆ | ★★★☆☆ | ★★★☆☆ | ★★★★☆ | ★★★★★ | ★★★★☆ |
경량 | ★★★★★ | ★★★★★ | ★★★★★ | ★★★★☆ | ★★★★☆ | ★★★★☆ |
강도 | ★★★★★ | ★★★★★ | ★★★★★ | ★★★☆☆ | ★★★☆☆ | ★★★★★ |
강도의 방향 | XYZ | XYZ | XYZ | XY | X(Y) | XY |
처리량 | ★☆☆☆☆ | ★★★☆☆ | ★★★★★ | ★★★☆☆ | ★★★★☆ | ★★★☆☆ |
장비 비용(특정) | 가변, <$100부터 시작 | 가변, 시작가 <$3000 | 가변, 일반적으로 $100,000 이상 | 데스크톱 솔루션은 $5,000부터, 산업용 솔루션은 약 $40,000부터 시작합니다. | 39,243달러부터 시작하는 완벽한 산업 솔루션 | 데스크톱 솔루션은 $20,000부터, 산업용 솔루션은 약 $70,000부터 시작합니다. |
파트 당 비용 | $$$$ | $$$ | $$ | $$$ | $$ | $$$$ |
적정 용도 | 맞춤형 고성능 제품, 진입 수준 워크플로 | 중저용량 생산 | 대량 생산 | 빠른 반복, 강력한 3D 프린트 파트 | 빠른 반복, 복잡한 형상, 강력한 3D 프린트 파트의 소량 생산 | 빠른 반복, 3D 프린트 파트 기존 탄소섬유 합성 복합재만큼 강함(XY 방향) |
장점 | 높은 강도 저렴한 장비 비용 | 고강도 | 높은 강도 정밀도 및 반복성 자동화 가능성 | 저렴 툴링 필요 없음 | 정밀도 및 반복성 설계의 자유 툴링 필요 없음 | 고강도 툴링 필요 없음 |
단점 | 노동 집약적 높은 품질 유지가 어려움 | 노동 집약적 | 고가의 툴링 및 기계 | 이방성 강도 낮은 강도 인쇄하기 어려움 | 이방성 강도 낮은 강도 | 이방성 강도 |
3D 프린트 탄소 섬유는 얼마나 강할까요?
3D 프린팅 탄소 섬유 복합재의 기계적 물성은 강도와 온도 저항성 측면에서 거의 모든 다른 3D 프린팅 플라스틱을 능가합니다. 참고로 잘게 잘린 섬유가 연속 섬유 3D 프린트와 일반적인 재료와 어떻게 비교되는지 살펴보겠습니다.
제조 공정 | SLS - 촙섬유 | FDM - 촙섬유 | 용융 적층 모델링 방식 - 연속 섬유 | 용융 적층 모델링 방식 - 연속 섬유 | 사출 성형 | 주조 또는 가공 |
---|---|---|---|---|---|---|
소재 | 폼랩스 Nylon 11 CF 파우더 | 탄소 섬유 충전 나일론 필라멘트 | 나일론 6 필라멘트 + 탄소 섬유 | PEEK 필라멘트 + 탄소 섬유 | ABS | 알루미늄 |
인장 탄성계수(GPa) | 1.6 - 5.3 | 2.4 | 60 - 100 | 145 | 2.3 | 70 |
극한 인장 강도 (MPa) | 38 - 69 | 40 | 800 - 1000 | 2400 | 39 | 310 |
굴곡 탄성계수(GPa) | 4.2 | 3.0 | 51 - 71 | 124 | 2.4 | 70 |
굽힘 강도(MPa) | 110 | 71 | 540 - 800 | 13:00 | 74 | 310 |
파단 시 연신율 | 5 - 15% | 25% | 1.5% | 해당사항 없음 | 6 - 15% | 해당사항 없음 |
노치 아이조드 충격강도(J/m) | 74 | 330 | 960 | 해당사항 없음 | 200 | 해당사항 없음 |
열변형 온도 @ 0.45MPa (°C) | 188 | 145 | 105 | 해당사항 없음 | 70 - 107 | 해당사항 없음 |
탄소 섬유 3D 프린트 파트의 응용 분야
탄소 섬유 3D 프린트 파트의 높은 강도와 가벼운 무게, 내충격성, 내열성, 내화학성 덕분에 이전에는 3D 프린팅을 고려하지 않았던 다양한 응용 분야에 이상적입니다. 이제 플라스틱 및 탄소 섬유 합성 복합재 3D 프린트 부품은 자동차 또는 항공 우주 엔진 컴포넌트에서 발생하는 열을 견딜 수 있고, 가공된 알루미늄 부품 및 제조 보조 도구의 대체품으로 사용되며, 오래 지속되고 충격에 강한 장비를 생산할 수 있습니다.
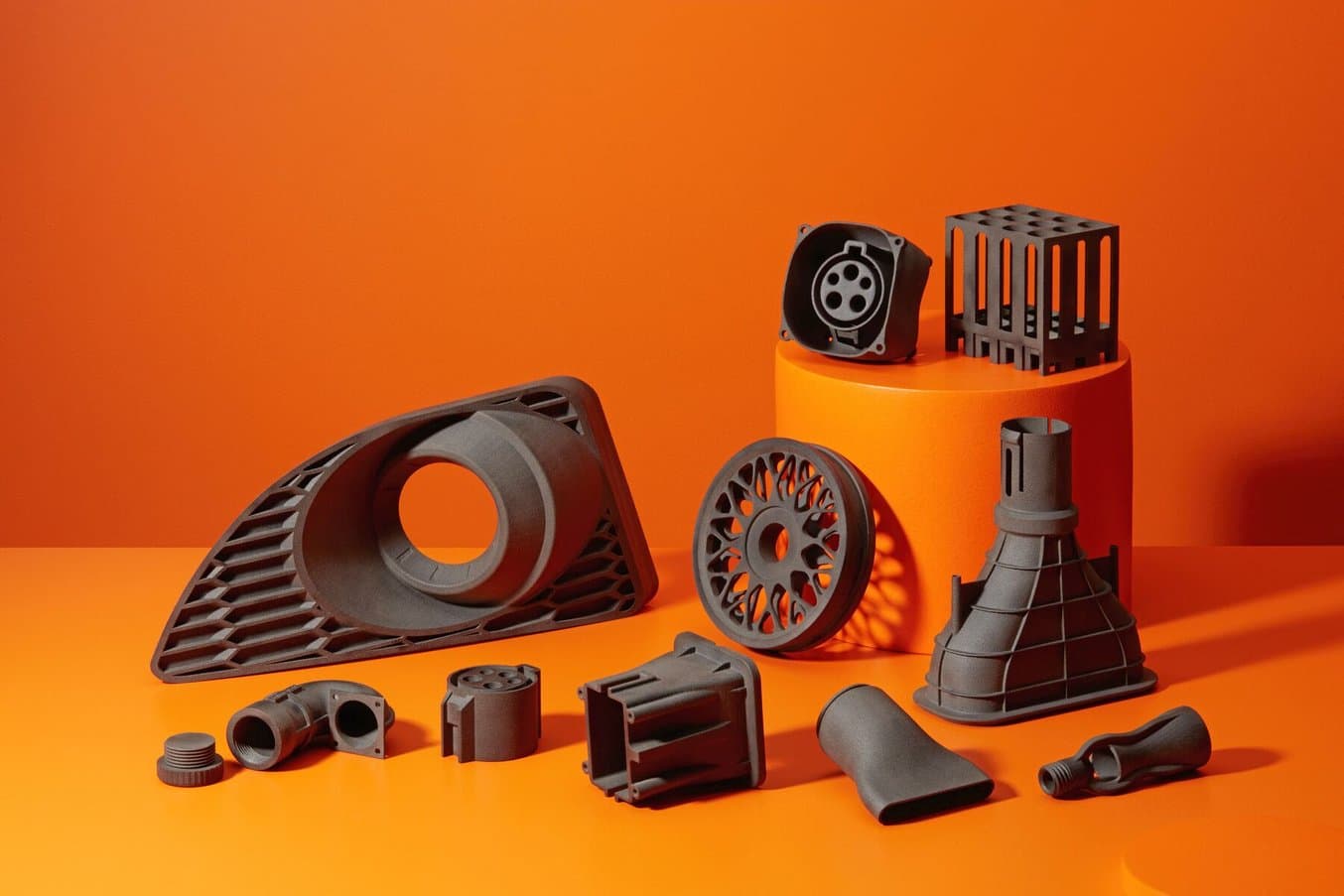
탄소 섬유 3D 프린팅 파트는 신속 프로토타이핑, 지그 및 픽스처와 같은 내마모성 및 내구성 제조 보조 도구, 복잡한 형상을 가진 강력한 최종 사용 부품의 소량 생산에 이상적입니다.
3D 프린팅 기술은 설계 및 제조 분야에서 새로운 가능성을 열었으며, 3D 프린팅 탄소 섬유 합성 복합재는 이를 더욱 발전시켜 자동차, 항공 우주, 방위 및 제조 산업의 사용자가 기하학적 유연성을 갖춘 고강도 내열 부품을 빠르고 효율적으로 생산할 수 있게 해줍니다. 이러한 사용자는 기존의 가공 또는 성형 공정을 우회하여 맞춤형 부품, 교체 파트 및 기능성 프로토타입을 더 쉽게 제작할 수 있습니다. 3D 프린팅 탄소 섬유 부품은 단일한 강도가 추가되어 기존 기술을 완전히 대체할 수는 없지만, 거의 대부분의 다른 플라스틱보다 강도가 높기 때문에 많은 응용 분야에서 독보적으로 유용합니다.
성형 또는 3D 프린트로 직접 탄소 섬유 부품을 생산하는 데 적합한 공정은 특정 응용 분야와 파트 설계, 생산량 등과 같은 요소에 따라 크게 달라집니다. 촙섬유를 사용한 SLS 3D 프린팅은 기존의 성형 탄소 섬유 파트 수준은 아니지만 견고한 파트를 제조하고자 하는 사람들에게 적합한 솔루션입니다.
Formlabs Fuse 1+ 30W와 Nylon 11 CF Powder를 사용하면 자금이 많지 않고 일정이 촉박한 기업도 기존 플라스틱과 달리 강도와 기계적 물성이 뛰어난 최종 사용 파트를 빠르게 반복하여 생산할 수 있습니다. 또한 부품을 기능적으로 테스트한 다음 약간의 CAD 수정만으로 설계를 변경하여 제품의 성능을 개선하고 출시 시기를 앞당길 수 있습니다.
지금 무료 샘플 파트를 요청하여 SLS 3D 프린트 절단 섬유 부품의 품질과 강도를 직접 확인하거나 전문가와 상담하여 귀사의 애플리케이션에 적합한 솔루션을 찾아보세요.