사출 성형은 어디서나 손쉽게 볼 수 있을 만큼 널리 사용되는 제조 공정입니다. 사실 오늘날 전 세계 플라스틱 제품의 대부분은 사출 성형 방식으로 제조됩니다. 기존 CNC 기계 가공 금속 금형은 대규모 생산 요건에는 이상적인 기술이지만, 소량 생산의 경우 비용이 지나치게 많이 소요되며 리드 타임이 길다는 단점이 있습니다.
프로토타입 제작 및 소량 생산(약 10~1000개 부품)의 경우 3D 프린팅 사출 금형은 시간 및 비용 효율적인 솔루션을 제공합니다. 또한 엔지니어 및 설계자가 금형 설계를 테스트하고 간편하게 수정한 후 신속하게 설계를 반복할 수 있으므로 보다 민첩한 제작 방식을 채택할 수 있습니다. 동시에 이 과정은 기존의 CNC 가공보다 훨씬 저렴한 비용으로 진행됩니다.
Form 3+와 같은 광경화성 수지 조형 방식 (SLA) 3D 프린터를 사용하면 간단하고 편리한 방식으로 맞춤 금형을 제작할 수 있기에 3D 프린팅과 기존 사출 성형 기술의 이점을 모두 활용할 수 있습니다.
본 가이드에서는 DIY 사출 성형 과정을 단계별로 상세히 안내하며, 인하우스에서 3D 프린팅 금형을 이용한 플라스틱 사출 성형 공정을 활용하는 데 필요한 모든 도구와 팁을 살펴보겠습니다.
자세한 지침, 설계 권장 사항 및 실제 사례 연구를 확인하려면 백서를 다운로드하세요.
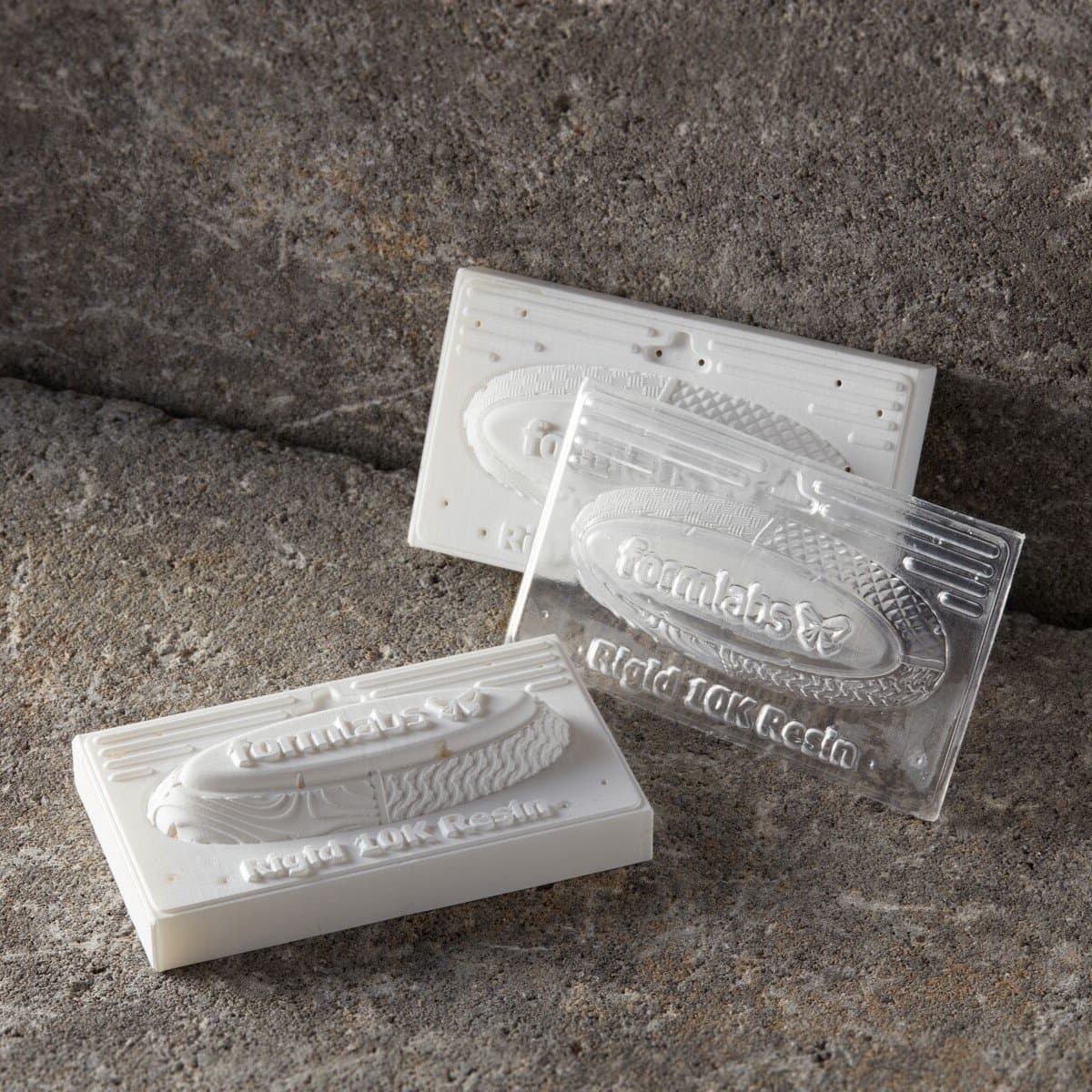
DIY 사출 성형에 필요한 것
DIY 플라스틱 금형 제작 환경을 조성하려면 어느 정도 투자가 필요합니다. 적합한 장비를 구입하고 사용법을 익히는 데는 시간과 돈이 들죠. 그러나 이러한 비용은 대부분 단일 금속 금형 제작 비용보다 적게 소요됩니다. 따라서 일단 장비를 갖추고 사용법을 익히면, 시간 및 비용 절감 효과로 초기 노력을 쉽게 상쇄할 수 있습니다.
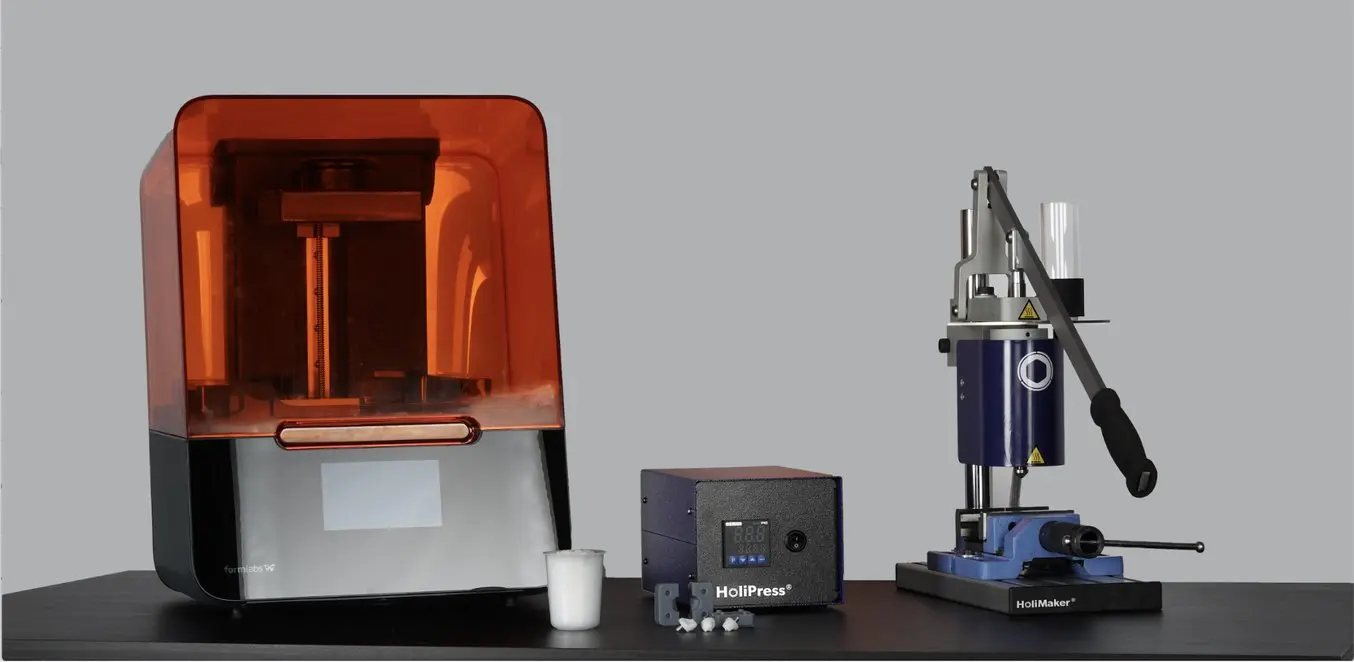
Holipress 데스크톱 사출 성형기 옆에 있는 Form 3 SLA 3D 프린터.
시작하기에 앞서 구비해야 할 품목:
-
Formlabs의 Form 3+와 같은 고성능 데스크톱 SLA 3D 레진 프린터. Form 3+는 고품질 최종 성형 부품의 제작에 적합하도록 디테일이 명료하며 매끄러운 표면 마감을 갖춘 정교한 금형을 프린팅할 수 있습니다. SLA 3D 프린터는 DIY 플라스틱 성형 외에도 제품 개발 과정 전반에 걸쳐 시제품 제작 및 기타 응용 분야에 다양하게 활용할 수 있는 유용한 자산입니다.
-
사출 성형 공정 중 금형에 가해지는 온도와 압력을 견딜 수 있는 3D 프린팅 재료. Formlabs SLA 3D 프린터에는 다음 재료를 사용하시도록 권장합니다.
-
Rigid 10K Resin은 산업 등급의 유리 성분 비율이 높게 충전된 재료로, 보다 다양한 기하학적 구조와 사출 성형 공정에 활용할 수 있는 솔루션을 제공합니다. 열변형 온도(HDT)는 0.45 MPa 하중에서 218°C이고 인장 탄성율은 10,000 MPa로 우수한 강도와 강성, 열안정성을 자랑합니다.
-
High Temp Resin은 사출 성형에 적합한 0.45 MPa 하중에서 열변형온도가 238 °C입니다. High Temp Resin은 취성(brittleness)이 좀 더 강한 재료이지만 성형 온도가 높고 냉각 시간을 줄여야 할 경우에 사용을 권장합니다.
-
Grey Pro Resin은 High Temp Resin이나 Rigid Resin보다 열전도율이 낮아 냉각 시간이 더 길지만, 더 부드러우며 수백 번의 사이클에도 견딜 수 있습니다.
-
-
Galomb Model-B100 또는 Holipress와 같은 벤치톱 사출 성형기. 시중에서 판매되고 있는 벤치톱 사출 성형기는 가격이 다양합니다. 저가의 성형기는 대부분 수동식 플런저를 사용하는 반면, 고가 장치는 나사형 또는 공압식 시스템을 사용합니다.일부 고객은 Minijjector, Morgan, APSX, 또는 Micromolder의 시스템도 추천했습니다. Babyplast의 제품군과 같은 데스크톱 자동 성형기는 소형 파트를 대량으로 생산하기에 좋은 대안입니다.
-
선호하는 플라스틱 펠렛
-
무료로 다운로드할 수 있는 Blender 등의 금형 인서트 설계용 CAD 소프트웨어 도구.
구입하기 전에 사출 성형기가 생산 필요 사항에 맞는지 신중하게 평가하시기 바랍니다. 대형 부품의 경우, 여전히 산업 공정이 필요로 합니다. DIY 사출 성형 기술은 소량 생산에 최적화되어 있습니다.
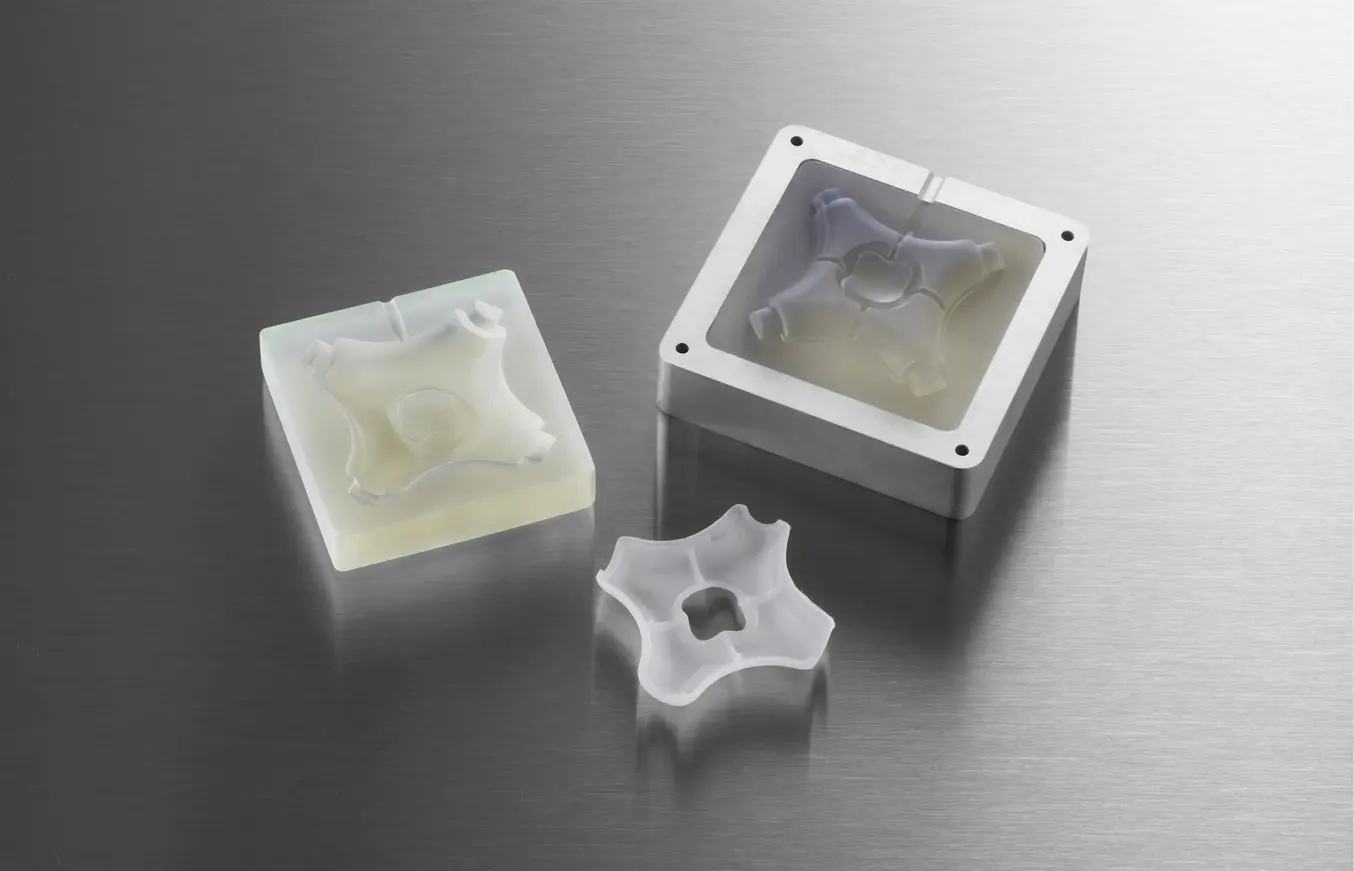
이 DIY 사출 성형 공정으로 제작한 Formlabs 3D 프린팅 금형 및 캡슐화된 컴포넌트.
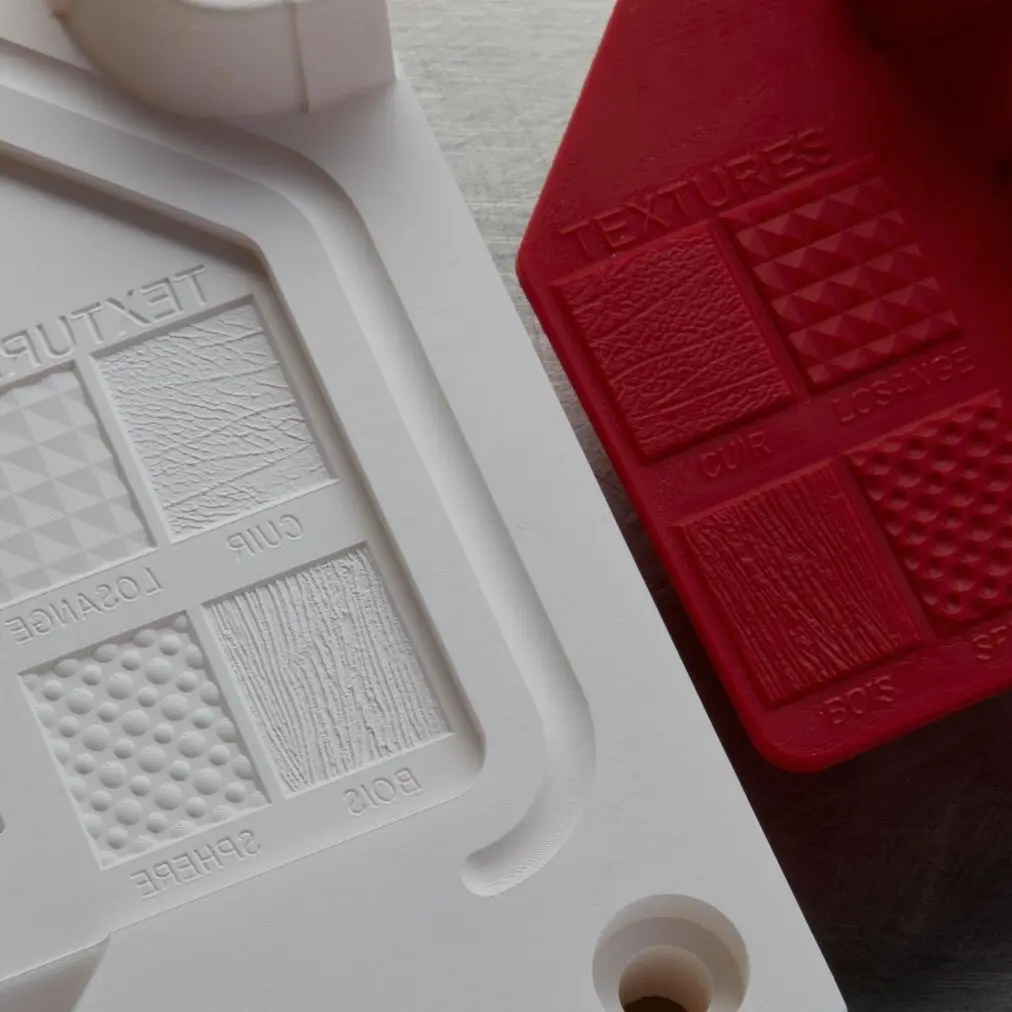
24시간 안에 제작하는 사출 성형 파트 소량 사출 성형에 관한 기본 사항
저희 3D 프린팅 전문가와의 1:1 상담하시면 귀사의 비즈니스에 적합한 솔루션을 결정하고 ROI 분석, 테스트 프린트, 외 다양한 것을 받아보실 수 있습니다.
단계별 DIY 사출 성형
1. CAD에서 금형을 디자인합니다
먼저 원하는 CAD 소프트웨어 도구를 선택하여 금형 인서트를 설계합니다. 당사는 오픈 소스 Blender를 사용하지만, 워크플로는 다른 CAD 소프트웨어에서도 상당히 유사합니다.
기본 금형 인서트 설계 파일을다운로드합니다. 이 파일을 사용하여 사출 금형을 설계하려고 합니다. 또한 대부분의 사출 금형 및 금형 프레임을 수용하도록 설계를 쉽게 조정할 수 있습니다. 또는 마스터 금형 프레임의 공동(cavity) 다이어그램을 사용하여 자체 금형 인서트를 설계하는 것도 가능합니다.
금형 코어의 금형 반쪽과 제작하고자 하는 3D 설계를 모두 CAD 도구로 가져옵니다.
블렌더에서 장면 탐색기의 눈 아이콘을 사용하여 금형의 절반을 끕니다. 작업 환경을 원하는 대로 설정했으면 아래 이미지와 같이 객체 메뉴에서 금형의 양쪽 절반을 '선' 그리기 유형으로 설정합니다.
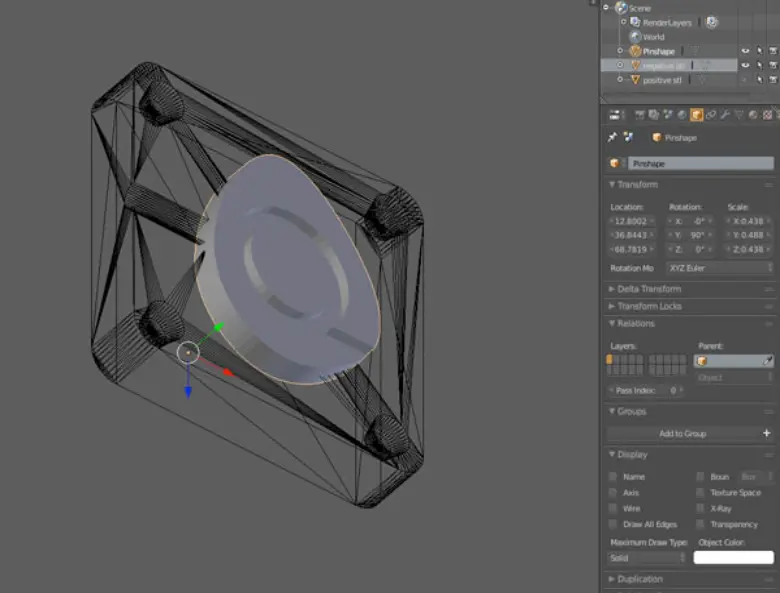
이제 금형을 배치할 수 있습니다. 사출 성형 공정 중에 개체가 용융 플라스틱 입구와 완전히 교차하는지 확인하세요. '원근/직교 전환 모드'를 통해 보다 쉽게 사용할 수 있습니다.
현재 금형 코어의 가시성(visibility)을 끄고 다른 쪽을 켭니다. 본 과정의 반복을 통해 개체가 금형 코어의 나머지 절반 입구와 완전히 교차하는지 확인합니다. 개체 정렬 시 Blender의 '부울 차이' 기능을 사용하여 교차하는 두 개체의 면적을 차감할 수 있습니다.
개체의 전반부를 선택하고 수정자 메뉴(Modifiers Menu)에서 부울 옵션을 선택합니다. 절단할 개체를 선택하고 '차이' 작업이 선택되어 있는지 확인합니다. 연산자를 적용하고 반대쪽도 동일하게 수행합니다. 아래 이미지와 비슷하게 나타나야 합니다. 여기서 막힌다면, 설계에 연동 구성 요소를 추가하는 방법에 대한 튜토리얼을 보는 것이 도움이 될 수 있습니다.
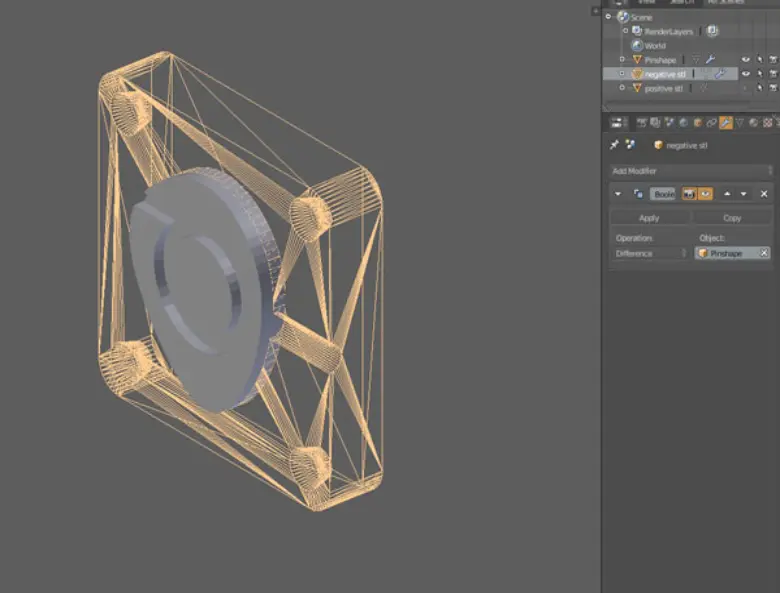
이제 금형을 프린팅할 준비가 되었습니다. Blender 내보내기에서 '선택한 부분만(Selection Only)' 체크박스를 선택하여 각 절반을 내보냅니다.
2. 금형 3D 프린팅
금형을 3D 프린팅하려면 사출 성형 과정에서 금형에 가해지는 온도와 압력을 견딜 수 있는 재료를 선택해야 합니다.
당사는 내부 테스트 및 고객사와의 사례 연구를 바탕으로 아래 표의 기준에 따라 3D 프린팅 레진의 선택을 권장합니다. 별 세 개는 레진이 해당 분야에서 기능이 우수하다는 의미이며, 별 한 개는 상대적으로 그렇지 못하다는 의미입니다.
기준 | High Temp Resin | Grey Pro Resin | Rigid 10K Resin | |
---|---|---|---|---|
높은 금형 온도 | ★★★ | ★ | ★★ | |
짧은 쿨링 시간 | ★★★ | ★ | ★★ | |
높은 압력 | ★ | ★★ | ★★★ | |
복잡한 기하학 부품에 대한 사이클 횟수 증가 | ★ | ★★ | ★★★ |
Setting up the print only takes a few seconds in PreForm, the print preparation software for Formlabs professional 3D printers. If your mold design requires support structures for printing, make sure to orient the mold halves in PreForm so that the cavity faces up. This will simplify post-processing and ensure a high-quality surface for your molded parts.
Depending on the geometry and the size, multiple molds can be printed at once on a build platform to increase printing efficiency.
3. 플라스틱 부품 사출 성형
Now that you’ve designed and 3D printed your mold, you can mold the parts on your benchtop plastic injection molding machine.
You have a wide variety of materials to choose from for injection molding. Formlabs and our customers have tested the following materials with 3D printed injection molds:
- LDPE
- PP
- PA
- PE
- TPE
- TPU
- PLA
- ABS
- ASA
- HDPE
- EVA
- PS
- POM
Consider the desired properties of your object and the capabilities of your injection molder before you make your choice. From there, simply follow the bespoke instructions on your injection molder to quickly and efficiently produce your parts.
Depending on the injected material, adhesion of the part to the mold can cause deterioration of the mold during extraction, in particular with flexible 3D printing materials such as TPUs or TPEs. Using a mold release agent is a good solution to help separate the part from the mold. Silicone mold release agents are compatible with Formlabs Grey Pro Resin, High Temp Resin, and Rigid 10K Resin.
If you have more questions about the workflow, make make sure to check our article FAQ: Injection Molding With 3D Printed Molds.
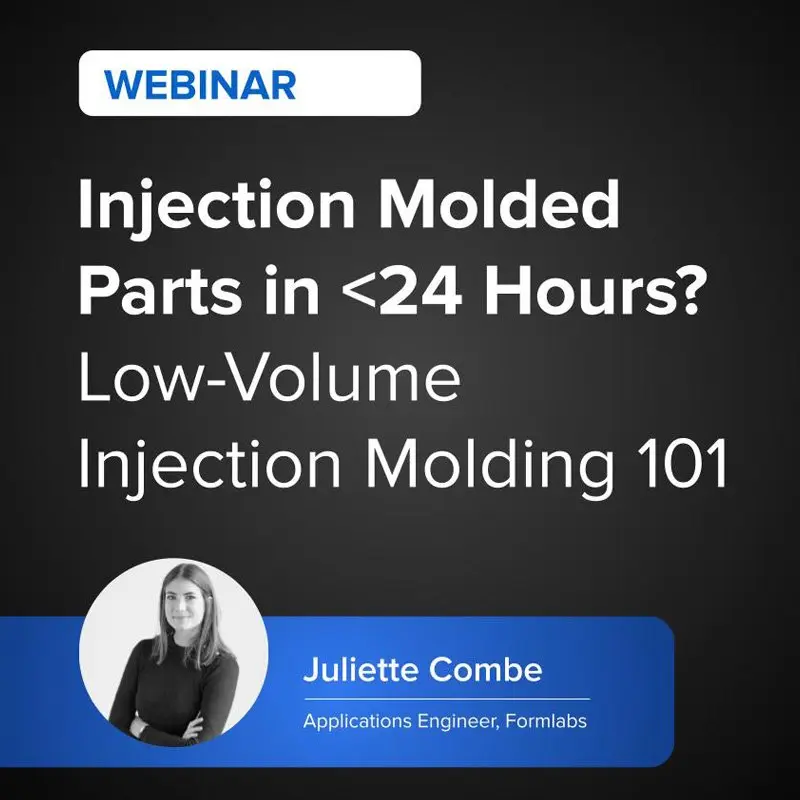
24시간 안에 제작하는 사출 성형 파트 소량 사출 성형에 관한 기본 사항
본 웨비나에서는 사출 성형 공정에서 광경화성 수지 조형 방식(SLA) 3D 프린팅 금형을 사용하여 비용은 절감하고 리드 타임은 단축하며 더 나은 제품을 출시하는 방법을 살펴보겠습니다.
DIY 사출 성형에 도전하는 설계자를 위한 도움말
When designing your mold, consider what will 3D print successfully, as well as what will mold successfully.
The exact approach to DIY injection molding will vary based on your desired design and volume, but these tips and tricks will help increase your success rate.
-
To reduce the visibility of print lines on the finished part, print the mold with a smaller layer height (50 or 25 microns per layer instead of the default 100). Note that this increases print time.
-
Adding two to five degrees of draft on surfaces perpendicular to the direction of pull will allow the part to be removed more easily and will minimize degradation of the mold.
-
You can polish split-plane surfaces with fine-grit sandpaper to reduce flash.
-
Consider using a water bath to more rapidly cool your part and reduce warping.
-
Embossed and engraved details should be offset from the surface by at least 1 mm.
-
If designing for an aluminum mold frame, add .125 mm of extra thickness to the back of the mold plates to account for compression forces and to ensure a complete seal.
For the complete process workflow and other best practices, download our white paper.
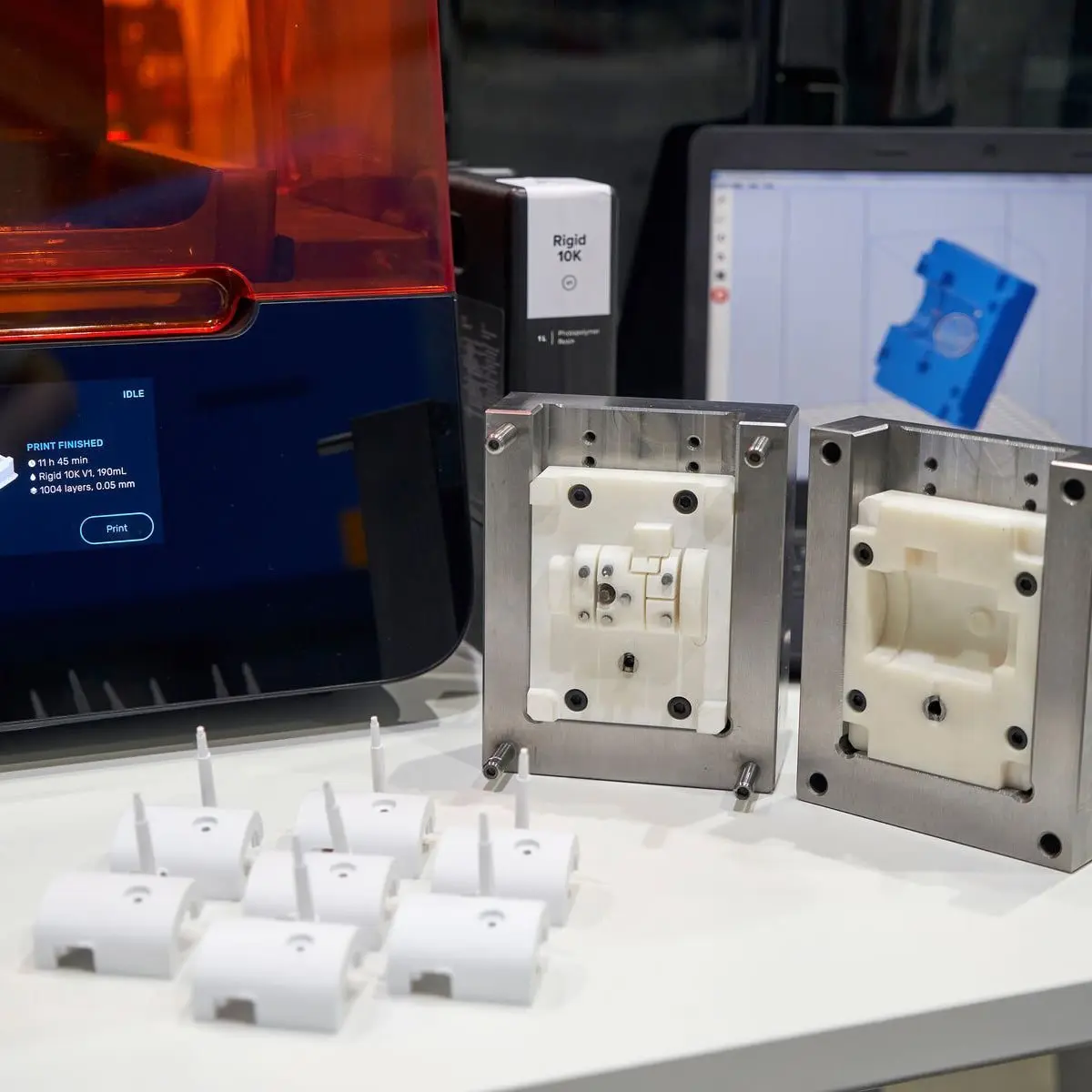
3D 프린팅 금형을 사용한 소량 고속 사출성형
백서를 다운로드하여 사출성형 공정에서 3D 프린팅 금형으로 비용과 리드 타임을 절감하는 방법과 관련한 지침을 확인하고, 브라스켐과 홀리메이커, 노버스 애플리케이션스의 실제 사례 연구를 살펴보세요.
3D 프린팅을 이용한 고정관념 타파
The conversation around 3D printing and injection molding is often oppositional, but it’s not always a question of one versus the other. By directly 3D printing parts or using 3D printed molds for injection molding for prototyping and low-volume production, you can leverage the benefits of both technologies. This will make your manufacturing process more time- and cost-efficient and allow you to bring products to the market faster.
Want to learn more about injection molding with 3D printed molds? Download our white paper for detailed guidelines for using 3D printed molds in the injection molding process and see real-life case studies with Braskem, Holimaker, and Novus Applications.
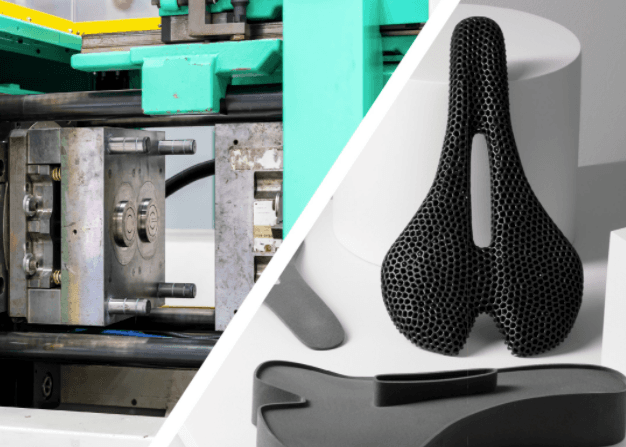
SLS 3D 프린팅 vs. 사출 성형: 사출 성형을 3D 프린팅 방식으로 전환해야 하는 시점
본 백서에서는 실제 사용 사례의 비용 역학과 SLS 3D 프린팅, 사출 성형 또는 두 가지 모두를 함께 사용하는 데 필요한 지침을 제시합니다.